torque DATSUN 610 1969 Owner's Guide
[x] Cancel search | Manufacturer: DATSUN, Model Year: 1969, Model line: 610, Model: DATSUN 610 1969Pages: 171, PDF Size: 10.63 MB
Page 92 of 171
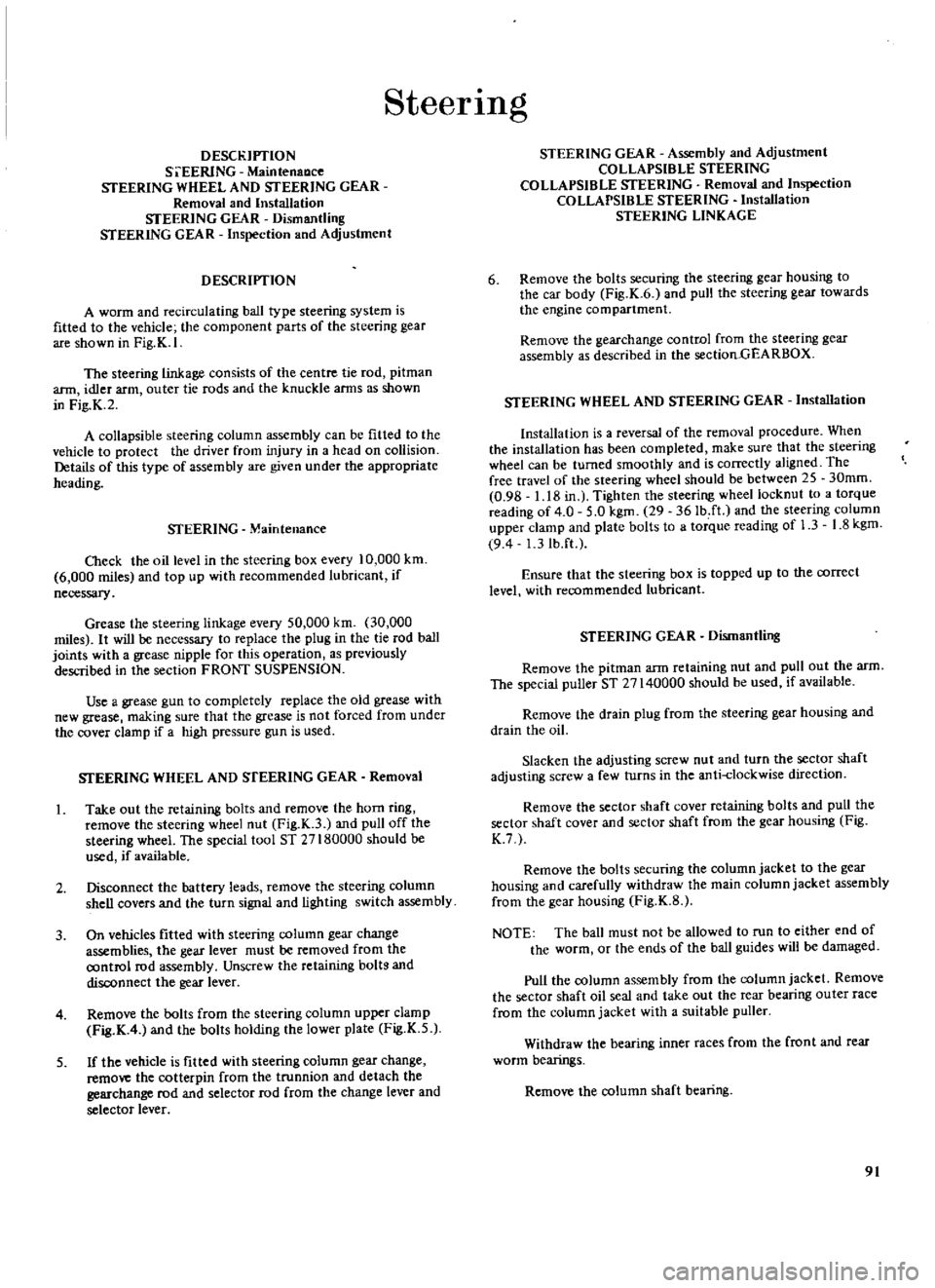
SteerIng
DEsn
IPTION
S
i
EERlNG
MaintenaDce
STEERING
WHEEL
AND
STEERING
GEAR
Removal
and
Installation
STEERING
GEAR
Dismantling
STEERING
GEAR
Inspection
and
Adjustment
DESCRIPTION
A
worm
and
recirculating
ball
type
steering
system
is
fitted
to
the
vehicle
the
component
parts
of
the
steering
gear
are
shown
in
Fig
K
I
The
steering
linkage
consists
of
the
centre
tie
rod
pitman
ann
idler
arm
outer
tie
rods
and
the
knuckle
arms
as
shown
in
Fig
K
2
A
collapsible
steering
column
assembly
can
be
fitted
to
the
vehicle
to
protect
the
driver
from
injury
in
a
head
on
collision
Details
of
this
type
of
assembly
are
given
under
the
appropriate
heading
STEERING
Maintenance
O1eck
the
oil
level
in
the
steering
box
every
10
000
km
6
000
miles
and
top
up
with
recommended
lubricant
if
necessary
Grease
the
steering
linkage
every
50
000
km
30
OOO
miles
It
will
be
necessary
to
replace
the
plug
in
the
tie
rod
ball
joints
with
a
grease
nipple
for
this
operation
as
previously
described
in
the
section
FRONT
SUSPENSION
Use
a
grease
gun
to
completely
replace
the
old
grease
with
new
grease
making
SUfe
that
the
grease
is
not
forced
from
under
the
cover
clamp
if
a
high
pressure
gun
is
used
STEERING
WHEEL
AND
STEERING
GEAR
Removal
1
Take
out
the
retaining
bolts
and
remove
the
horn
ring
remove
the
steering
wheel
nut
Fig
K
3
and
pull
off
the
steering
wheel
The
special
tool
ST
27180000
should
be
used
if
available
2
Disconnect
the
battery
leads
remove
the
steering
column
shell
covers
and
the
turn
signal
and
lighting
switch
assembly
3
On
vehicles
fitted
with
steering
column
gear
change
assemblies
the
gear
lever
must
be
removed
from
the
control
rod
assembly
Unscrew
the
retaining
boltg
and
disconnect
the
gear
lever
4
Remove
the
bolts
from
the
steering
column
upper
clamp
Fig
K
4
and
the
bolts
holding
the
lower
plate
Fig
K
5
5
If
the
vehicle
is
fitted
with
steering
column
gear
change
remove
the
cotterpin
from
the
trunnion
and
detach
the
gearchange
rod
and
selector
rod
from
the
change
lever
and
selector
lever
STEERING
GEAR
Assembly
and
Adjustment
COLLAPSIBLE
STEERING
COLLAPSIBLE
STEERING
Removal
and
Inspection
COLLAPSIBLE
STEERING
Installation
STEERING
LINKAGE
6
Remove
the
bolts
securing
the
steering
gear
housing
to
the
car
body
Fig
K
6
and
pull
the
steering
gear
towards
the
engine
compartment
Remove
the
gearchange
control
from
the
steering
gear
assembly
as
described
in
the
section
GEARBOX
STEERING
WHEEL
AND
STEERING
GEAR
Installation
Installation
is
a
reversal
of
the
removal
procedure
When
the
installation
has
been
completed
make
sure
that
the
steering
wheel
can
be
turned
smoothly
and
is
correctly
aligned
The
free
travel
of
the
steering
wheel
should
be
between
2S
30mm
0
9B
1
18
in
Tighten
the
steering
wheel
locknut
to
a
torque
reading
of
4
0
5
0
kgm
29
36Ib
ft
and
the
steering
column
upper
clamp
and
plate
bolts
to
a
torque
reading
of
1
3
1
8
kgm
94
1
3
Ib
ft
Ensure
that
the
steering
box
is
topped
up
to
the
correct
level
with
recommended
lubricant
STEERING
GEAR
Dismantling
Remove
the
pitman
arm
retaining
nut
and
pull
out
the
arm
The
special
puller
ST
27140000
should
be
used
if
available
Remove
the
drain
plug
from
the
steering
gear
housing
and
drain
the
oil
Slacken
the
adjusting
screw
nut
and
turn
the
sector
shaft
adjusting
screw
a
few
turns
in
the
anti
clockwise
direction
Remove
the
sector
shaft
cover
retaining
bolts
and
pull
the
sector
shaft
cover
and
sector
shaft
from
the
gear
housing
Fig
K
7
Remove
the
bolts
securing
the
column
jacket
to
the
gear
housing
and
carefully
withdraw
the
main
column
jacket
assembly
from
the
gear
housing
Fig
K
B
NOTE
The
ball
must
not
be
allowed
to
run
to
either
end
of
the
worm
or
the
ends
of
the
ball
guides
will
be
damaged
Pull
the
column
assembly
from
the
column
jacket
Remove
the
sector
shaft
oil
seal
and
take
out
the
rear
bearing
outer
race
from
the
column
jacket
with
a
suitable
puller
Withdraw
the
bearing
inner
races
from
the
front
and
fear
worm
bearings
Remove
the
column
shaft
bearing
91
Page 94 of 171
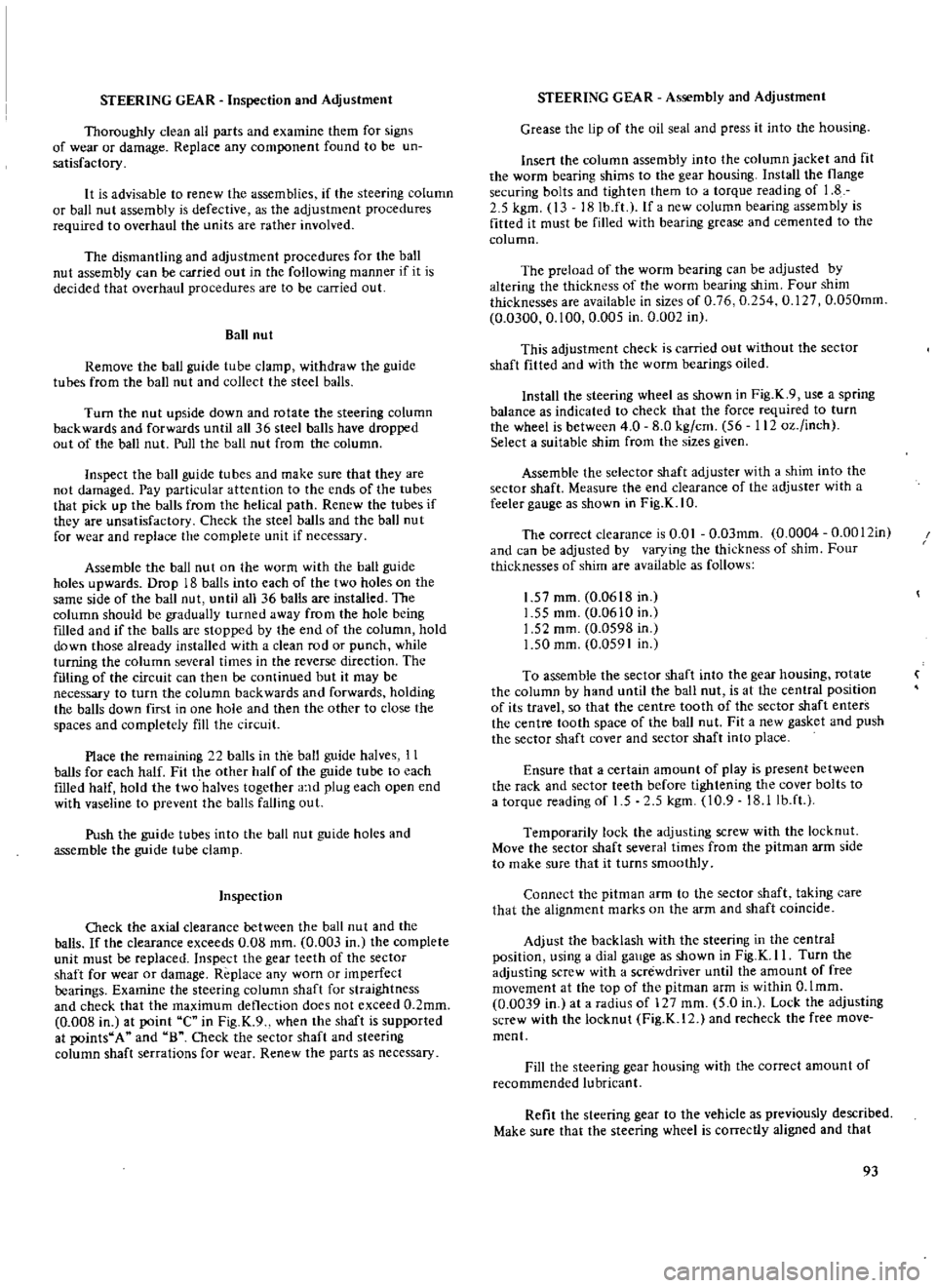
STEERING
GEAR
Inspection
and
Adjustment
Thoroughly
clean
all
parts
and
examine
them
for
signs
of
wear
or
damage
Replace
any
comIK
nent
found
to
be
un
satisfactory
It
is
advisable
to
renew
the
assemblies
if
the
steering
column
or
ball
nut
assembly
is
defective
as
the
adjustment
procedures
required
to
overhaul
the
units
are
rather
involved
The
dismantling
and
adjustment
procedures
for
the
ball
nut
assembly
can
be
carried
out
in
the
following
manner
if
it
is
decided
that
overhaul
procedures
are
to
be
carried
out
Ball
nut
Remove
the
ball
guide
tube
clamp
withdraw
the
guide
tubes
from
the
ball
nut
and
collect
the
steel
balls
Turn
the
nut
upside
down
and
rotate
the
steering
column
backwards
and
forwards
until
all
36
steel
balls
have
dropped
out
of
the
ball
nut
Pull
the
ball
nut
from
the
column
Inspect
the
ball
guide
tubes
and
make
sure
that
they
are
not
damaged
Pay
particular
attention
to
the
ends
of
the
tubes
that
pick
up
the
balls
from
the
helical
path
Renew
the
tubes
if
they
are
unsatisfactory
Check
the
steel
balls
and
the
ball
nut
for
wear
and
replace
the
complete
unit
if
necessary
Assemble
the
ball
nut
on
the
worm
with
the
ball
guide
holes
upwards
Drop
18
balls
into
each
of
the
two
holes
on
the
same
side
of
the
ball
nut
until
all
36
balls
are
installed
The
column
should
be
gradually
turned
away
from
the
hole
being
filled
and
if
the
balls
are
stopped
by
the
end
of
the
column
hold
down
those
already
installed
with
a
clean
rod
or
punch
while
turning
the
column
several
times
in
the
reverse
direction
The
filling
of
the
circuit
can
then
be
continued
but
it
may
be
necessary
to
turn
the
column
backwards
and
forwards
holding
the
balls
down
first
in
one
hole
and
then
the
other
to
close
the
spaces
and
completely
fill
the
circuit
Place
the
remaining
22
balls
in
the
ball
guide
halves
11
balls
for
each
half
Fit
the
other
half
of
the
guide
tube
to
each
f11led
half
hold
the
two
halves
together
a
ld
plug
each
open
end
with
vaseline
to
prevent
the
balls
falling
out
Push
the
guide
tubes
into
the
ball
nut
guide
holes
and
assemble
the
guide
tube
clamp
Inspection
Oteck
the
axial
clearance
between
the
ball
nut
and
the
balls
If
the
clearance
exceeds
0
08
mrn
0
003
in
the
complete
unit
must
be
replaced
Inspect
the
gear
teeth
of
the
sector
shaft
for
wear
or
damage
Replace
any
worn
or
imperfect
bearings
Examine
the
steering
column
shaft
for
straightness
and
check
that
the
maximum
deflection
does
not
exceed
0
2mm
0
008
in
at
point
C
in
Fig
K
9
when
the
shaft
is
supported
at
points
A
and
B
Check
the
sector
shaft
and
steering
column
shaft
serrations
for
wear
Renew
the
parts
as
necessary
STEERING
GEAR
Assembly
and
Adjustment
Grease
the
lip
of
the
oil
seal
and
press
it
into
the
housing
Insert
the
column
assembly
into
the
column
jacket
and
fit
the
worm
bearing
shims
to
the
gear
housing
Install
the
flange
securing
bolts
and
tighten
them
to
a
torque
reading
of
1
8
2
5
kgm
13
18lb
ft
If
a
new
column
bearing
assembly
is
fitted
it
must
be
filled
with
bearing
grease
and
cemented
to
the
column
The
preload
of
the
worm
bearing
can
be
adjusted
by
altering
the
thickness
of
the
worm
bearing
shim
Four
shim
thicknesses
are
available
in
sizes
of
0
76
0
254
0
127
0
050mm
0
0300
0
100
0
005
in
0
002
in
This
adjustment
check
is
carried
out
without
the
sector
shaft
fitted
and
with
the
worm
bearings
oiled
Install
the
steering
wheel
as
shown
in
Fig
K
9
use
a
spring
balance
as
indicated
to
check
that
the
force
required
to
turn
the
wheel
is
between
4
0
8
0
kg
cm
56
l120z
inch
Select
a
suitable
shim
from
the
sizes
given
Assemble
the
selector
shaft
adjuster
with
a
shim
into
the
sector
shaft
Measure
the
end
clearance
of
the
adjuster
with
a
feeler
gauge
as
shown
in
Fig
K
1
O
The
correct
clearance
is
0
01
0
03mm
0
0004
O
0012in
and
can
be
adjusted
by
varying
the
thickness
of
shim
Four
thicknesses
of
shim
are
available
as
follows
1
57
mm
0
0618
in
1
55
mm
0
0610
in
1
52
mm
0
0598
in
1
50
mm
0
0591
in
To
assemble
the
sector
shaft
into
the
gear
housing
rotate
the
column
by
hand
until
the
ball
nut
is
at
the
central
position
of
its
travel
so
that
the
centre
tooth
of
the
sector
shaft
enters
the
centre
tooth
space
of
the
ball
nut
Fit
a
new
gasket
and
push
the
sector
shaft
cover
and
sector
shaft
into
place
Ensure
that
a
certain
amount
of
play
is
present
between
the
rack
and
sector
teeth
before
tightening
the
cover
bolts
to
a
torque
reading
of
1
5
2
5
kgm
10
9
18
llb
ft
Temporarily
lock
the
adjusting
screw
with
the
locknut
Move
the
sector
shaft
several
times
from
the
pitman
arm
side
to
make
sure
that
it
turns
smoothly
Connect
the
pitman
arm
to
the
sector
shaft
taking
care
that
the
alignment
marks
on
the
arm
and
shaft
coincide
Adjust
the
backlash
with
the
steering
in
the
central
position
using
a
dial
gauge
as
shown
in
Fig
K
II
Turn
the
adjusting
screw
with
a
screwdriver
until
the
amount
of
free
movement
at
the
top
of
the
pitman
arm
is
within
O
lmm
0
0039
in
at
a
radius
of
127
mm
5
0
in
Lock
the
adjusting
screw
with
the
locknut
Fig
K
12
and
recheck
the
free
move
ment
Fill
the
steering
gear
housing
with
the
correct
amount
of
recommended
lubricant
Refit
the
steering
gear
to
the
vehicle
as
previously
described
Make
sure
that
the
steering
wheel
is
correctly
aligned
and
that
93
Page 98 of 171
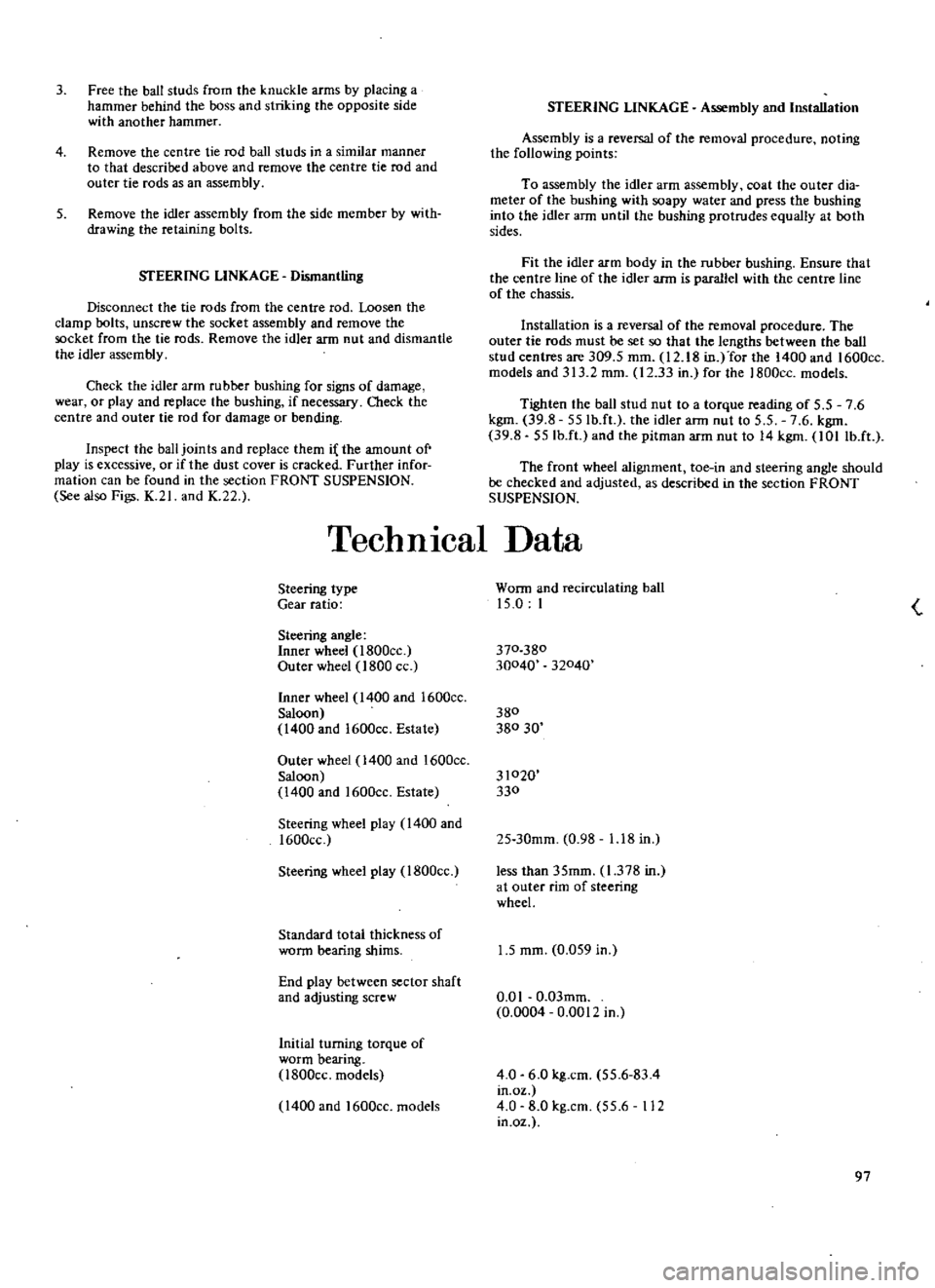
3
Free
the
ball
studs
from
the
knuckle
arms
by
placing
a
hammer
behind
the
boss
and
striking
the
opposite
side
with
another
hammer
4
Remove
the
centre
tie
rod
ball
studs
in
a
similar
manner
to
that
described
above
and
remove
the
centre
tie
rod
and
outer
tie
rods
as
an
assembly
5
Remove
the
idler
assembly
from
the
side
member
by
with
drawing
the
retaining
bolts
SfEERING
LINKAGE
Dismantling
Disconnect
the
tie
rods
from
the
centre
rod
Loosen
the
clamp
bolts
unscrew
the
socket
assembly
and
remove
the
socket
from
the
tie
rods
Remove
the
idler
arm
nut
and
dismantle
the
idler
assembly
Check
the
idler
arm
rubber
bushing
for
signs
of
damage
wear
or
play
and
replace
the
bushing
if
necessary
Oteck
the
centre
and
outer
tie
rod
for
damage
or
bending
Inspect
the
ball
joints
and
replace
them
i
the
amount
of
play
is
excessive
or
if
the
dust
cover
is
cracked
Further
infor
mation
can
be
found
in
the
section
FRONT
SUSPENSION
See
also
Figs
K
21
and
K
22
STEERING
LINKAGE
Assembly
and
Installation
Assembly
is
a
reversal
of
the
removal
procedure
noting
the
following
points
To
assembly
the
idler
arm
assembly
coat
the
outer
dia
meter
of
the
bushing
with
soapy
water
and
press
the
bushing
into
the
idler
arm
until
the
bushing
protrudes
equally
at
both
sides
Fit
the
idler
arm
body
in
the
rubber
bushing
Ensure
that
the
centre
line
of
the
idler
arm
is
parallel
with
the
centre
line
of
the
chassis
Installation
is
a
reversal
of
the
removal
procedure
The
outer
tie
rods
must
be
set
so
that
the
lengths
between
the
ball
stud
centres
are
309
5
mm
12
18
in
for
the
1400
and
1600cc
models
and
313
2
mm
12
33
in
for
the
1800cc
models
Tighten
the
ball
stud
nut
to
a
torque
reading
of
5
5
7
6
kgm
39
8
55Ib
ft
the
idler
ann
nut
to
5
5
7
6
kgm
39
8
55Ib
ft
and
the
pitman
arm
nut
to
14
kgm
lOllb
ft
The
front
wheel
alignment
toe
in
and
steering
angle
should
be
checked
and
adjusted
as
described
in
the
section
FRONT
SUSPENSION
TechnIcal
Data
Steering
type
Gear
ratio
Steering
angle
Inner
wheel
l800cc
Outer
wheel
1800
cc
Inner
wheel
1400
and
1600cc
Saloon
1400
and
1600cc
Estate
Outer
wheel
1400
and
1600cc
Saloon
1400
and
1600cc
Estate
Steering
wheel
play
1400
and
1600cc
Steering
wheel
play
1800cc
Standard
total
thickness
of
worm
bearing
shims
End
play
between
sector
shaft
and
adjusting
screw
Initial
turning
torque
of
worm
bearing
l800cc
models
1400
and
1600cc
models
Worm
and
recirculating
ball
15
0
I
370
380
30040
32040
380
380
30
31020
330
25
30mm
0
98
1
18
in
less
than
35mm
1
378
in
at
outer
rim
of
steering
wheel
1
5
mm
0
059
in
0
0
I
0
03mm
0
0004
0
0012
in
4
0
6
0
kg
cm
55
6
83
4
in
oz
4
0
8
0
kg
cm
55
6
112
in
oz
97
Page 100 of 171
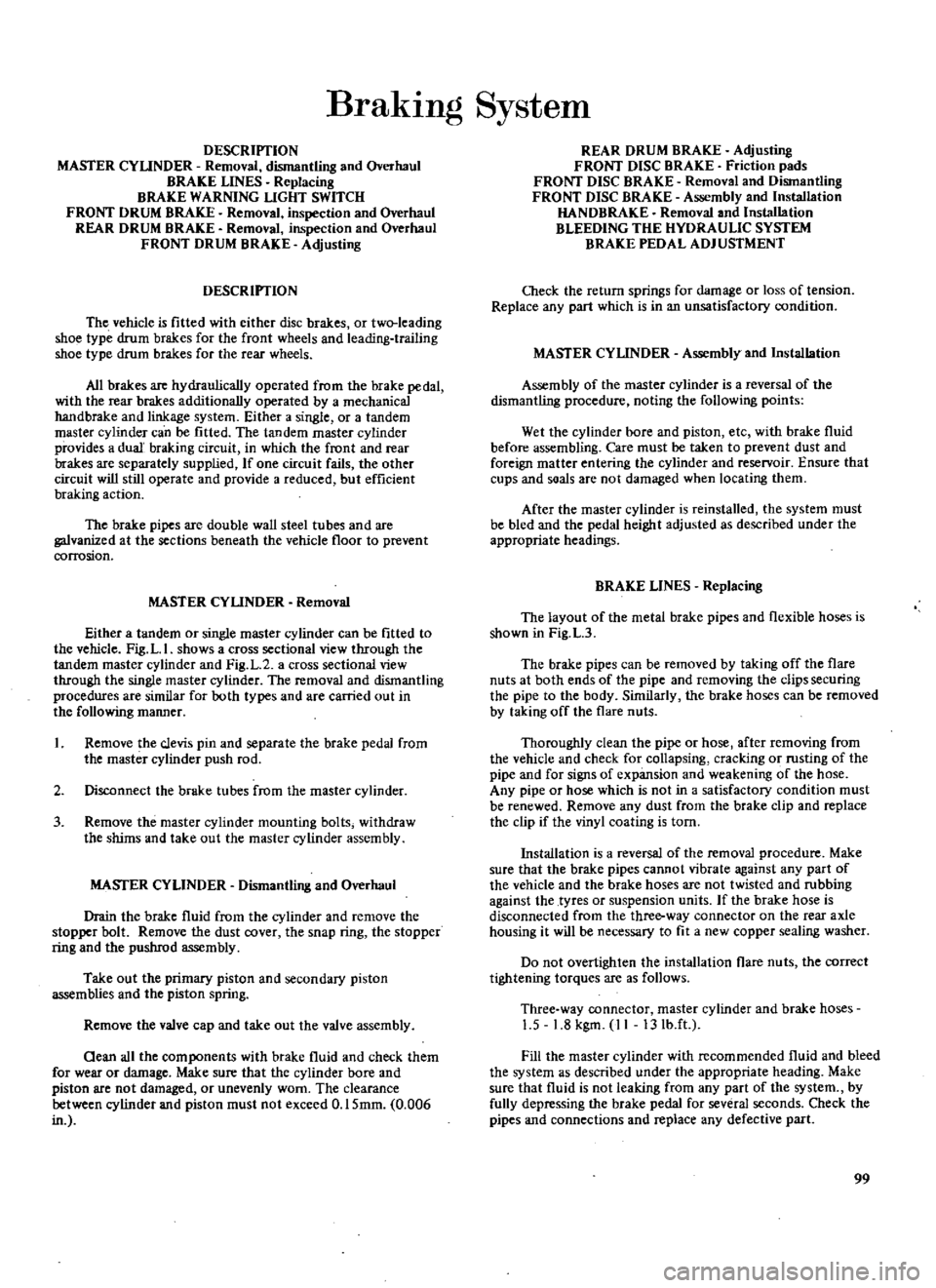
BrakIng
System
DESCRIPTION
MASTER
CYLINDER
Removal
dismantling
and
Overhaul
BRAKE
LINES
Replacing
BRAKE
WARNING
LIGHT
SWITCH
FRONT
DRUM
BRAKE
Removal
inspection
and
Overhaul
REAR
DRUM
BRAKE
Removal
inspection
and
Overhaul
FRONT
DRUM
BRAKE
Adjusting
DESCRIPTION
The
vehicle
is
fitted
with
either
disc
brakes
or
two
leading
shoe
type
drum
brakes
for
the
front
wheels
and
leading
trailing
shoe
type
drum
brakes
for
the
rear
wheels
All
brakes
are
hydraulically
operated
from
the
brake
pedal
with
the
rear
brakes
additionally
operated
by
a
mechanical
handbrake
and
linkage
system
Either
a
single
or
a
tandem
master
cylinder
can
be
fitted
The
tandem
master
cylinder
provides
a
dual
braking
circuit
in
which
the
front
and
rear
brakes
are
separately
supplied
If
ODe
circuit
fails
the
other
circuit
will
still
operate
and
provide
a
reduced
but
efficient
braking
action
The
brake
pipes
are
double
wall
steel
tubes
and
are
galvanized
at
the
sections
beneath
the
vehicle
floor
to
prevent
corrosion
MASTER
CYLINDER
Removal
Either
a
tandem
or
single
master
cylinder
can
be
fitted
to
the
vehicle
Fig
L
I
shows
a
cross
sectional
view
through
the
tandem
master
cylinder
and
Fig
L
2
a
cross
sectional
view
through
the
single
master
cylinder
The
removal
and
dismantling
procedures
are
similar
for
both
types
and
are
carried
out
in
the
following
manner
1
Remove
the
clevis
pin
and
separate
the
brake
pedal
from
the
master
cylinder
push
rod
2
Disconnect
the
brake
tubes
from
the
master
cylinder
3
Remove
the
master
cylinder
mounting
bolts
withdraw
the
shims
and
take
out
the
master
cylinder
assembly
MASfER
CYLINDER
Dismantling
and
Overhaul
Drain
the
brake
fluid
from
the
cylinder
and
remove
the
stopper
bolt
Remove
the
dust
cover
the
snap
ring
the
stopper
ring
and
the
pusbrod
assembly
Take
out
the
primary
piston
and
secondary
piston
assemblies
and
the
piston
spring
Remove
the
valve
cap
and
take
out
the
valve
assembly
Oean
all
the
components
with
brake
fluid
and
check
them
for
wear
or
damage
Make
sure
that
the
cylinder
bore
and
piston
are
not
damaged
or
unevenly
worn
The
clearance
between
cylinder
and
piston
must
not
exceed
0
15mm
0
006
in
REAR
DRUM
BRAKE
Adjusting
FRONT
DISC
BRAKE
Friction
pads
FRONT
DISC
BRAKE
Removal
and
Dismantling
FRONT
DISC
BRAKE
Assembly
and
Installation
HANDBRAKE
Removal
and
Installation
BLEEDING
THE
HYDRAULIC
SYSTEM
BRAKE
PEDAL
ADJUSTMENT
Check
the
return
springs
for
damage
or
loss
of
tension
Replace
any
part
which
is
in
an
unsatisfactory
condition
MASfER
CYLINDER
Assembly
and
Installation
Assembly
of
the
master
cylinder
is
a
reversal
of
the
dismantling
procedure
noting
the
following
points
Wet
the
cylinder
bore
and
piston
etc
with
brake
fluid
before
assembling
Care
must
be
taken
to
prevent
dust
and
foreign
matter
entering
the
cylinder
and
reservoir
Ensure
that
cups
and
soals
are
not
damaged
when
locating
them
After
the
master
cylinder
is
reinstalled
the
system
must
be
bled
and
the
pedal
height
adjusted
as
described
under
the
appropriate
headings
BRAKE
LINES
Replacing
The
layout
of
the
metal
brake
pipes
and
flexible
hoses
is
shown
in
Fig
L
3
The
brake
pipes
can
be
removed
by
taking
off
the
flare
nuts
at
both
ends
of
the
pipe
and
removing
the
clips
securing
the
pipe
to
the
body
Similarly
the
brake
hoses
can
be
removed
by
taking
off
the
flare
nuts
Thoroughly
clean
the
pipe
or
hose
after
removing
from
the
vehicle
and
check
for
collapsing
cracking
or
rusting
of
the
pipe
and
for
signs
of
expansion
and
weakening
of
the
hose
Any
pipe
or
hose
which
is
not
in
a
satisfactory
condition
must
be
renewed
Remove
any
dust
from
the
brake
clip
and
replace
the
clip
if
the
vinyl
coating
is
torn
Installation
is
a
reversal
of
the
removal
procedure
Make
sure
that
the
brake
pipes
cannot
vibrate
against
any
part
of
the
vehicle
and
the
brake
hoses
are
not
twisted
and
rubbing
against
the
tyres
or
suspension
units
If
the
brake
hose
is
disconnected
from
the
three
way
connector
on
the
rear
axle
housing
it
will
be
necessary
to
fit
a
new
copper
sealing
washer
Do
not
overtighten
the
installation
flare
nuts
the
correct
tightening
torques
are
as
follows
Three
way
connector
master
cylinder
and
brake
hoses
1
5
1
8
kgm
II
13Ib
ft
Fill
the
master
cylinder
with
recommended
fluid
and
bleed
the
system
as
described
under
the
appropriate
heading
Make
sure
that
fluid
is
not
leaking
from
any
part
of
the
system
by
fully
depressing
the
brake
pedal
for
several
seconds
Check
the
pipes
and
connections
and
replace
any
defective
part
99
Page 102 of 171
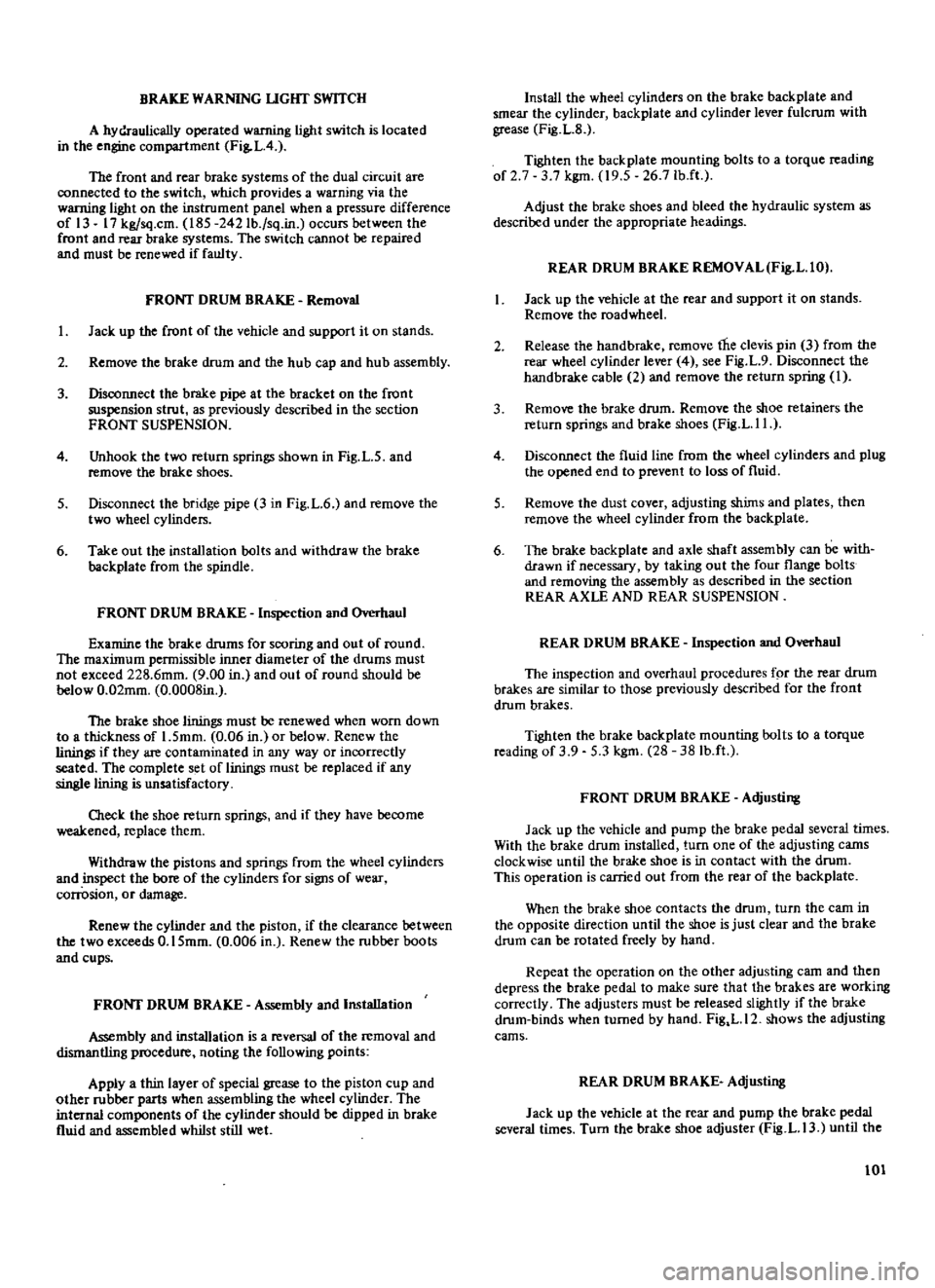
BRAKE
WARNING
UGHT
SWITCH
A
hydraulically
operated
warning
light
switch
is
located
in
the
engine
compartment
Fig
LA
The
front
and
rear
brake
systems
of
the
dual
circuit
are
connected
to
the
switch
which
provides
a
warning
via
the
warning
light
on
the
instrument
panel
when
a
pressure
difference
of
13
17
kg
sq
cm
185
242Ib
sq
in
occurs
between
the
front
and
rear
brake
systems
The
switch
cannot
be
repaired
and
must
be
renewed
if
faulty
FRONT
DRUM
BRAKE
Removal
1
Jack
up
the
front
of
the
vehicle
and
support
it
on
stands
2
Remove
the
brake
drum
and
the
hub
cap
and
hub
assembly
3
Disconnect
the
brake
pipe
at
the
bracket
on
the
front
suspension
strut
as
previously
described
in
the
section
FRONT
SUSPENSION
4
Unhook
the
two
return
springs
shown
in
Fig
L
5
and
remove
the
brake
shoes
5
Disconnect
the
bridge
pipe
3
in
Fig
L
6
and
remove
the
two
wheel
cylinders
6
Take
out
the
installation
bolts
and
withdraw
the
brake
backplate
from
the
spindle
FRONT
DRUM
BRAKE
Inspection
and
Overhaul
Examine
the
brake
drums
for
scoring
and
out
of
round
The
maximum
permissible
inner
diameter
of
the
drums
must
not
exceed
228
6mm
9
00
in
and
out
of
round
should
be
below
0
02mm
0
0008in
The
brake
shoe
linings
must
re
renewed
when
worn
down
to
a
thickness
of
1
5mm
0
06
in
or
below
Renew
the
linings
if
they
are
contaminated
in
any
way
or
incorrectly
seated
The
complete
set
of
linings
must
be
replaced
if
any
single
lining
is
unsatisfactory
O1eck
the
shoe
return
springs
and
if
they
have
become
weakened
replace
them
Withdraw
the
pistons
and
springs
from
the
wheel
cylinders
and
inspect
the
bore
of
the
cylinders
for
signs
of
wear
corrosion
or
damage
Renew
the
cylinder
and
the
piston
if
the
clearance
between
the
two
exceeds
O
15mm
0
006
in
Renew
the
rubber
boots
and
cups
FRONT
DRUM
BRAKE
Assembly
and
Installation
Assembly
and
installation
is
a
reversal
of
the
removal
and
dismantling
procedure
noting
the
fOllowing
points
Apply
a
thin
layer
of
special
grease
to
the
piston
cup
and
other
rubber
parts
when
assembling
the
wheel
cylinder
The
internal
components
of
the
cylinder
should
be
dipped
in
brake
fluid
and
assembled
whilst
still
wet
Install
the
wheel
cylinders
on
the
brake
backplate
and
smear
the
cylinder
backplate
and
cylinder
lever
fulcrum
with
grease
Fig
L
8
Tighten
the
backplate
mounting
bolts
to
a
torque
reading
of
2
7
3
7
kgm
19
5
26
71b
ft
Adjust
the
brake
shoes
and
bleed
the
hydraulic
system
as
described
under
the
appropriate
headings
REAR
DRUM
BRAKE
REMOVAL
Fig
L
IO
Jack
up
the
vehicle
at
the
rear
and
support
it
on
stands
Remove
the
road
wheel
2
Release
the
handbrake
remove
the
clevis
pin
3
from
the
rear
wheel
cylinder
lever
4
see
Fig
L
9
Disconnect
the
handbrake
cable
2
and
remove
the
return
spring
I
3
Remove
the
brake
drum
Remove
the
shoe
retainers
the
return
springs
and
brake
shoes
Fig
L
II
4
Disconnect
the
fluid
line
from
the
wheel
cylinders
and
plug
the
opened
end
to
prevent
to
loss
of
fluid
5
Remove
the
dust
cover
adjusting
shims
and
plates
then
remove
the
wheel
cylinder
from
the
backplate
6
The
brake
backplate
and
axle
shaft
assembly
can
be
with
drawn
if
necessary
by
taking
out
the
four
flange
bolts
and
removing
the
assembly
as
described
in
the
section
REAR
AXLE
AND
REAR
SUSPENSION
REAR
DRUM
BRAKE
Inspection
and
Overhaul
The
inspection
and
overhaul
procedures
fpr
the
rear
drum
brakes
are
similar
to
those
previously
described
for
the
front
drum
brakes
Tighten
the
brake
backplate
mounting
bolts
to
a
torque
reading
of
3
9
5
3
kgm
28
38Ib
ft
FRONT
DRUM
BRAKE
Adjusting
Jack
up
the
vehicle
and
pump
the
brake
pedal
several
times
With
the
brake
drum
installed
turn
one
of
the
adjusting
cams
clockwise
until
the
brake
shoe
is
in
contact
with
the
drum
This
operation
is
carried
out
from
the
rear
of
the
backplate
When
the
brake
shoe
contacts
the
drum
turn
the
cam
in
the
opposite
direction
until
the
shoe
is
just
clear
and
the
brake
drum
can
be
rotated
freely
by
hand
Repeat
the
operation
on
the
other
adjusting
cam
and
then
depress
the
brake
pedal
to
make
sure
that
the
brakes
are
working
correctly
The
adjusters
must
be
released
slightly
if
the
brake
drum
binds
when
turned
by
hand
Fig
L
12
shows
the
adjusting
cams
REAR
DRUM
BRAKE
Adjusting
Jack
up
the
vehicle
at
the
rear
and
pump
the
brake
pedal
several
times
Turn
the
brake
shoe
adjuster
Fig
L
13
until
the
101
Page 116 of 171
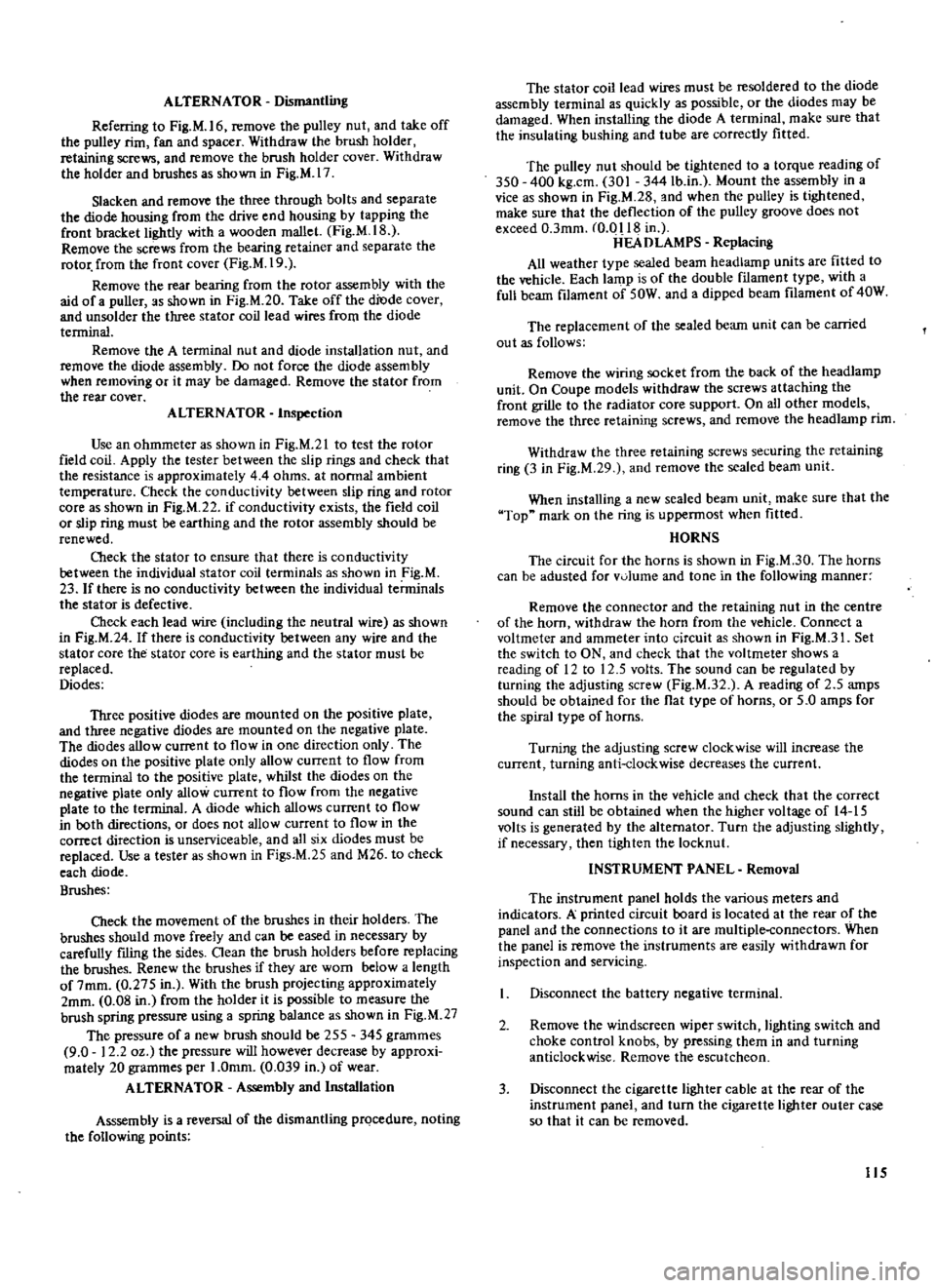
ALTERNATOR
Dismantling
Refening
to
Fig
M
16
remove
the
pulley
nut
and
take
off
the
pulley
rim
fan
and
spacer
Withdraw
the
brush
holder
retaining
screws
and
remove
the
brush
holder
cover
Withdraw
the
holder
and
brushes
as
shown
in
Fig
M
17
Slacken
and
remove
the
three
through
bolts
and
separate
the
diode
housing
from
the
drive
end
housing
by
tapping
the
front
bracket
lightly
with
a
wooden
mallet
Fig
M
18
Remove
the
screws
from
the
bearing
retainer
and
separate
the
rotor
from
the
front
cover
Fig
M
19
Remove
the
rear
bearing
from
the
rotor
assembly
with
the
aid
of
a
puller
as
shown
in
Fig
M
2D
Take
off
the
diode
cover
and
unsolder
the
three
stator
coil
lead
wires
from
the
diode
terminal
Remove
the
A
terminal
nut
and
diode
installation
nut
and
remove
the
diode
assembly
Do
not
force
the
diode
assembly
when
removing
or
it
may
be
damaged
Remove
the
stator
from
the
rear
cover
ALTERNATOR
Inspection
Use
an
ohmmeter
as
shown
in
Fig
M
21
to
test
the
rotor
field
coil
Apply
the
tester
between
the
slip
rings
and
check
that
the
resistance
is
approximately
4
4
ohms
at
normal
ambient
temperature
Check
the
conductivity
between
slip
ring
and
rotor
core
as
shown
in
Fig
M
22
if
conductivity
exists
the
field
coil
or
slip
ring
must
be
earthing
and
the
rotor
assembly
should
be
renewed
Cbeck
the
stator
to
ensure
that
there
is
conductivity
retween
the
individual
stator
coil
terminals
as
shown
in
Fig
M
23
If
there
is
no
conductivity
between
the
individual
terminals
the
stator
is
defective
Check
each
lead
wire
including
the
neutral
wire
as
shown
in
Fig
M
24
If
there
is
conductivity
between
any
wire
and
the
stator
COTe
the
stator
core
is
earthing
and
the
stator
must
be
replaced
Diodes
Three
positive
diodes
are
mounted
on
the
positive
plate
and
three
negative
diodes
are
mounted
on
the
negative
plate
The
diodes
allow
current
to
flow
in
one
direction
only
The
diodes
on
the
positive
plate
only
allow
current
to
flow
from
the
terminal
to
the
positive
plate
whilst
the
diodes
on
the
negative
plate
only
allow
current
to
flow
from
the
negative
plate
to
the
terminal
A
diode
which
allows
current
to
flow
in
ooth
directions
or
does
not
allow
current
to
flow
in
the
correct
direction
is
unserviceable
and
all
six
diodes
must
be
replaced
Use
a
tester
as
shown
in
Figs
M
25
and
M26
to
check
each
diode
Brushes
Check
the
movement
of
the
brushes
in
their
holders
The
brushes
should
move
freely
and
can
be
eased
in
necessary
by
carefully
ming
the
sides
Oean
the
brush
holders
before
replacing
the
brushes
Renew
the
brushes
if
they
are
worn
below
a
length
of
7mm
0
275
in
With
the
brush
projecting
approximately
2mm
0
08
in
from
the
holder
it
is
possible
to
measure
the
brush
spring
pressure
using
a
spring
balance
as
shown
in
Fig
M
27
The
pressure
of
a
new
brush
should
be
255
345
grammes
9
0
12
2
oz
the
pressure
will
however
decrease
by
approxi
mately
20
grammes
per
I
amm
0
039
in
of
wear
ALTERNATOR
Assembly
and
Installation
Asssembly
is
a
reversal
of
the
dismantling
prQcedure
noting
the
following
points
The
stator
coil
lead
wires
must
be
resoldered
to
the
diode
assembly
terminal
as
quickly
as
possible
or
the
diodes
may
be
damaged
When
installing
the
diode
A
tenninal
make
sure
that
the
insulating
bushing
and
tube
are
correctly
fitted
The
pulley
nut
should
he
tightened
to
a
torque
reading
of
350
400
kg
cm
301
344Ib
in
Mount
the
assembly
in
a
vice
as
shown
in
Fig
M
28
and
when
the
pulley
is
tightened
make
sure
that
the
deflection
of
the
pulley
groove
does
not
exceed
O
3mm
m
o
118
in
ilEA
D
LAMPS
Replacing
All
weather
type
sealed
beam
headlamp
units
are
fitted
to
the
vehicle
Each
lamp
is
of
the
double
fIlament
type
with
a
full
beam
filament
of
50W
and
a
dipped
beam
filament
of
40W
The
replacement
of
the
sealed
beam
unit
can
be
carried
out
as
follows
Remove
the
wiring
socket
from
the
back
of
the
headlamp
unit
On
Coupe
models
withdraw
the
screws
attaching
the
front
grille
to
the
radiator
core
support
On
all
other
models
remove
the
three
retaining
screws
and
remove
the
headlamp
rim
Withdraw
the
three
retaining
screws
securing
the
retaining
ring
3
in
Fig
M
29
and
remove
the
sealed
beam
unit
When
installing
a
new
sealed
beam
unit
make
sure
that
the
Top
mark
on
the
ring
is
uppennost
when
fitted
HORNS
The
circuit
for
the
horns
is
shown
in
Fig
M
30
The
horns
can
be
adusted
for
v01ume
and
tone
in
the
following
manner
Remove
the
connector
and
the
retaining
nut
in
the
centre
of
the
horn
withdraw
the
horn
from
the
vehicle
Connect
a
voltmeter
and
ammeter
into
circuit
as
shown
in
Fig
M
3I
Set
the
switch
to
ON
and
check
that
the
voltmeter
shows
a
reading
of
12
to
12
5
volts
The
sound
can
be
regulated
by
turning
the
adjusting
screw
Fig
M
32
A
reading
of
2
5
amps
should
be
obtained
for
the
flat
type
of
horns
or
5
0
amps
for
the
spiral
type
of
horns
Turning
the
adjusting
screw
clockwise
will
increase
the
current
turning
anti
clockwise
decreases
the
current
Install
the
horns
in
the
vehicle
and
check
that
the
correct
sound
can
still
be
obtained
when
the
higher
voltage
of
14
15
volts
is
generated
by
the
alternator
Turn
the
adjusting
slightly
if
necessary
then
tighten
the
locknut
INSTRUMENT
PANEL
Removal
The
instrument
panel
holds
the
various
meters
and
indicators
A
printed
circuit
board
is
located
at
the
rear
of
the
panel
and
the
connections
to
it
are
multiple
connectors
When
the
panel
is
remove
the
instruments
are
easily
withdrawn
for
inspection
and
servicing
Disconnect
the
battery
negative
terminal
2
Remove
the
windscreen
wiper
switch
lighting
switch
and
choke
control
knobs
by
pressing
them
in
and
turning
anticlockwise
Remove
the
escutcheon
3
Disconnect
the
cigarette
lighter
cable
at
the
rear
of
the
instrument
panel
and
turn
the
cigarette
lighter
outer
case
so
that
it
can
be
removed
115
Page 118 of 171
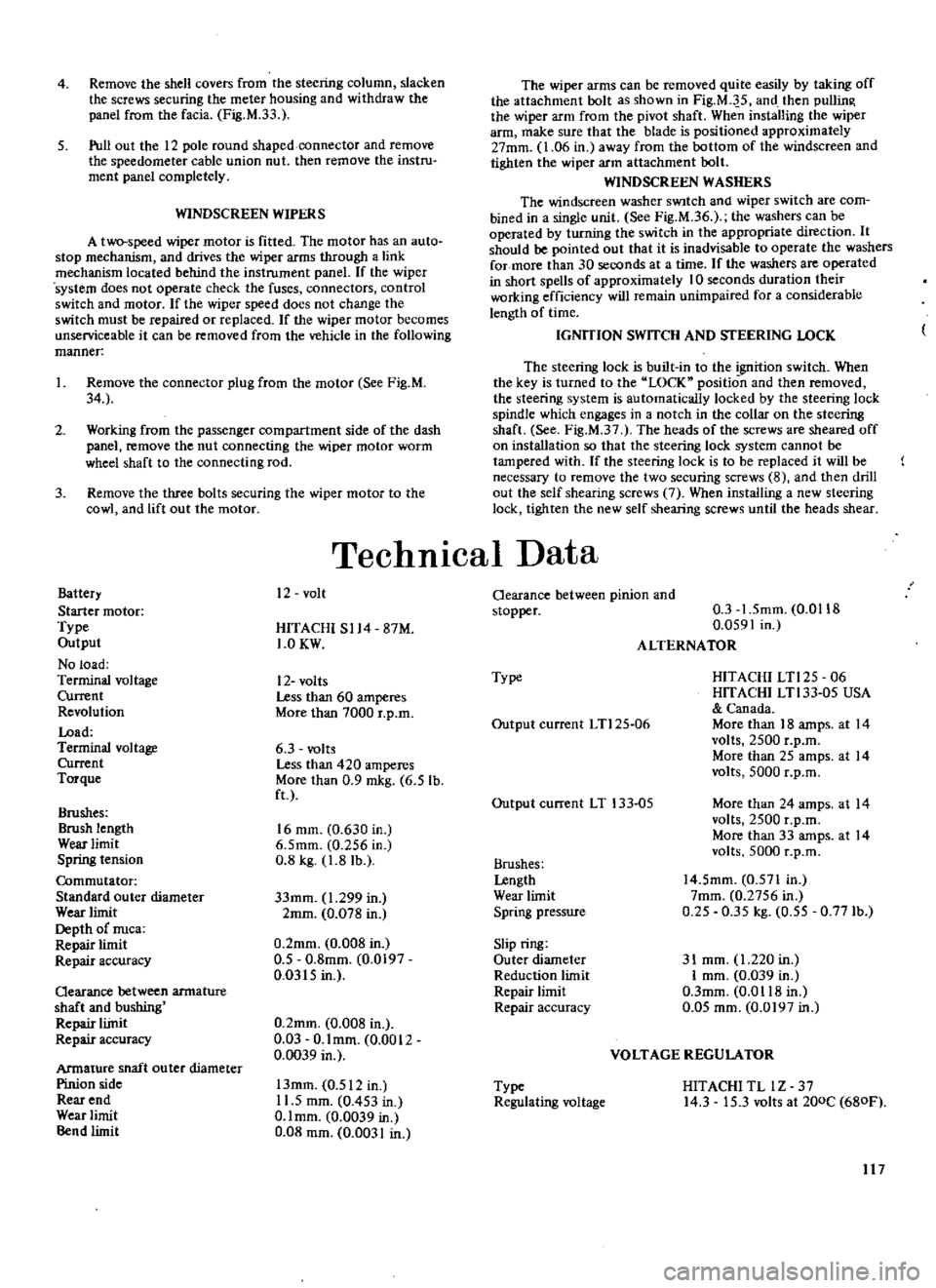
4
Remove
the
shell
covers
from
the
steering
column
slacken
the
screws
securing
the
meter
housing
and
withdraw
the
panel
from
the
facia
Fig
M
33
5
Pull
out
the
12
pole
round
shaped
connector
and
remove
the
speedometer
cable
union
nut
then
remove
the
instru
ment
panel
completely
WINDSCREEN
WIPERS
A
two
speed
wiper
motor
is
fitted
The
motor
has
an
auto
stop
mechanism
and
drives
the
wiper
arms
through
a
link
mechanism
located
behind
the
instrument
panel
If
the
wiper
system
does
not
operate
check
the
fuses
connectors
control
switch
and
motor
If
the
wiper
speed
does
not
change
the
switch
must
be
repaired
or
replaced
If
the
wiper
motor
becomes
unserviceable
it
can
be
removed
from
the
vehicle
in
the
fOllowing
manner
I
Remove
the
connector
plug
from
the
motor
See
Fig
M
34
2
Working
from
the
passenger
compartment
side
of
the
dash
panel
remove
the
nut
connecting
the
wiper
motor
worm
wheel
shaft
to
the
connecting
rod
3
Remove
the
three
bolts
securing
the
wiper
motor
to
the
cowl
and
lift
out
the
motor
Battery
Starter
motor
Type
Output
No
load
Terminal
voltage
Current
Revolution
Load
Terminal
voltage
Current
Torque
Brushes
Brush
length
Wear
limit
Spring
tension
Commutator
Standard
outer
diameter
Wear
limit
Depth
of
nuca
Repair
limit
Repair
accuracy
Qearance
between
armature
shaft
and
bushing
Repair
liinit
Repair
accuracy
Armature
shaft
ou
ter
diameter
Pinion
side
Rear
end
Wear
limit
Bend
limit
The
wiper
arms
can
be
removed
quite
easily
by
taking
off
the
attachment
bolt
as
shown
in
Fig
M
J
5
and
then
pullin
the
wiper
arm
from
the
pivot
shaft
When
installing
the
wiper
arm
make
sure
that
the
blade
is
positioned
approximately
27mm
1
06
in
away
from
the
bottom
of
the
windscreen
and
tighten
the
wiper
arm
attachment
bolt
WINDSCREEN
WASHERS
The
windscreen
washer
SWItch
and
wiper
switch
are
com
bined
in
a
single
unit
See
Fig
M
36
the
washers
can
be
operated
by
turning
the
switch
in
the
appropriate
direction
It
should
be
pointed
out
that
it
is
inadvisable
to
operate
the
washers
for
more
than
30
seconds
at
a
time
If
the
washers
are
operated
in
short
spells
of
approximately
10
seconds
duration
their
working
efficiency
will
remain
unimpaired
for
a
considerable
length
of
time
IGNITION
SWITCH
AND
STEERING
LOCK
The
steering
lock
is
built
in
to
the
goition
switch
When
the
key
is
turned
to
the
LOCK
position
and
then
removed
the
steering
system
is
automatically
locked
by
the
steering
lock
spindle
which
engages
in
a
notch
in
the
collar
on
the
steering
shaft
See
Fig
M
37
The
heads
of
the
screws
are
sheared
off
on
installation
so
that
the
steering
lock
system
cannot
be
tampered
with
If
the
steering
lock
is
to
be
replaced
it
will
be
necessary
to
remove
the
two
securing
screws
8
and
then
drill
out
the
self
shearing
screws
7
When
installing
a
new
steering
lock
tighten
the
new
self
shearing
screws
until
the
heads
shear
TechnICal
Data
12
volt
HITACHI
S114
87M
1
0KW
12
volts
Less
than
60
amperes
More
than
7000
r
p
m
6
3
volts
Less
than
420
amperes
More
than
0
9
mkg
6
5
lb
ft
16
mm
0
630
in
6
5mm
0
256
in
0
8
kg
1
8
lb
33mm
1
299
in
2mm
0
078
in
0
2mm
0
008
in
0
5
0
8mm
0
0197
0
0315
in
0
2mm
0
008
in
0
03
O
lmm
0
0012
0
0039
in
13mm
0
512
in
11
5
mm
0
453
in
O
lmm
0
0039
in
0
08
mm
0
0031
in
Oearance
between
pinion
and
stopper
0
3
1
5mm
0
0118
0
0591
in
ALTERNATOR
Type
HITACHI
LTl25
06
HITACHI
LTl33
05
USA
Canada
More
than
18
amps
at
14
volts
2500
r
p
m
More
than
25
amps
at
14
volts
5000
r
p
m
Output
current
LTl25
06
Output
current
LT
133
05
More
than
24
amps
at
14
volts
2500
r
p
m
More
than
33
amps
at
14
volts
5000
r
p
m
Brushes
Lengtb
Wear
limit
Spring
pressure
14
5mm
0
571
In
7mm
0
2756
in
0
25
0
35
kg
0
55
0
771b
Slip
ring
Outer
diameter
Reduction
limit
Repair
limit
Repair
accuracy
31
mm
1
220
in
I
mm
0
039
in
O
3mm
0
0118
in
0
05
mm
0
0197
in
VOLTAGE
REGULATOR
Type
Regulating
voltage
HITACHI
TL
lZ
37
14
3
15
3
volts
at
200C
680F
117
Page 128 of 171
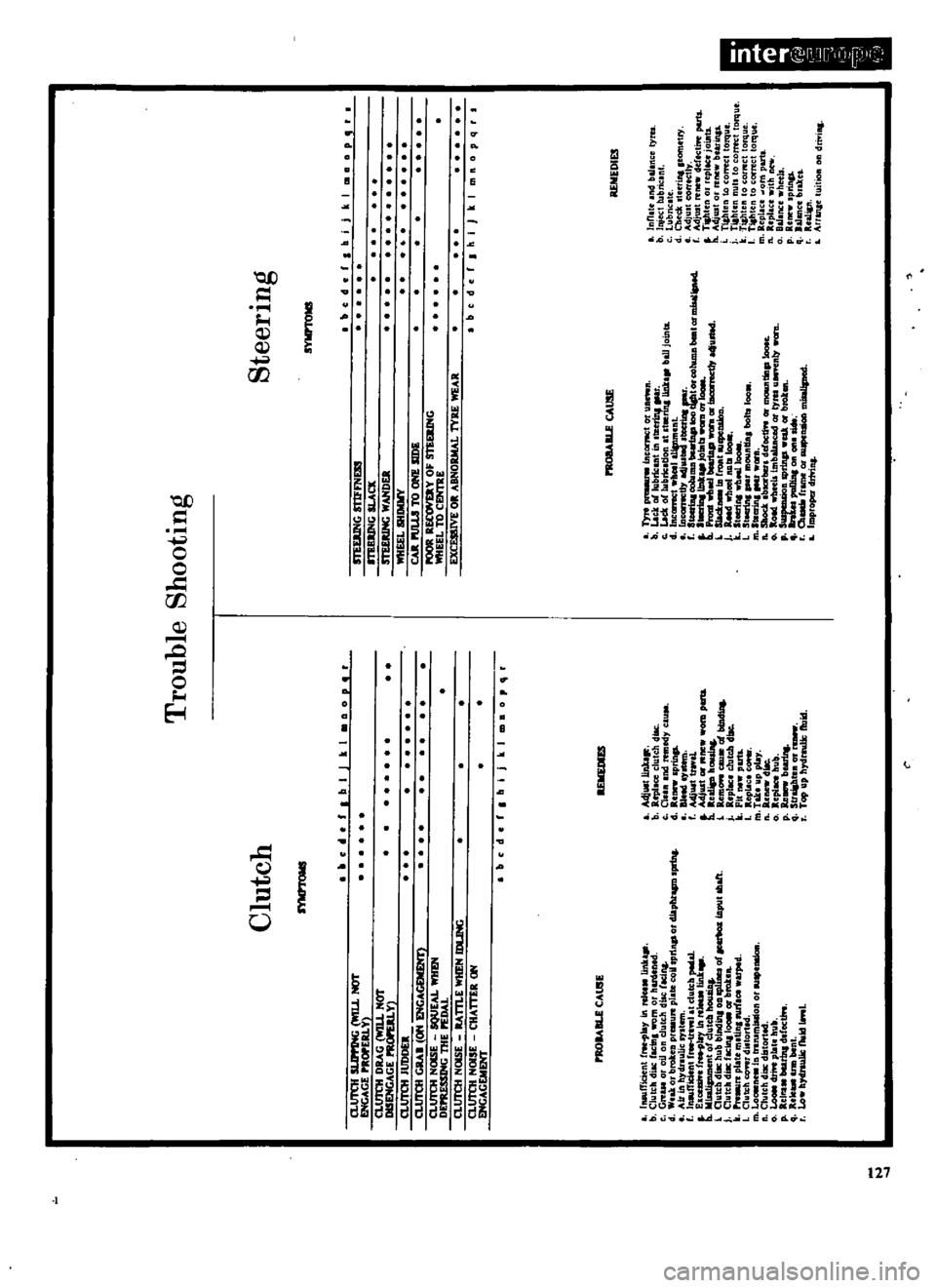
Clutch
MIPTOOlS
Trouble
Shootmg
Steering
IYMmlMS
mDING
S1
1FFNESS
ITIBJJNG
IIl
ACJt
STEEIUNG
WANDER
WHEEL
SHIIlOlY
CAR
PUl
U
TO
ONE
IIDE
POOR
RECa
Dy
OF
STEERING
WHEEL
10
CENl1tE
EXCESSIVE
01
ABNORMAL
TYKE
WEAR
It
d
e
f
I
II
J
e
It
b
I
J
k1
D
0
P
41
r
nUTCH
SI
IPPING
WIu
NOT
ENGAGE
PROPERLY
CLUfCHDRAG
WILLNOT
DISENGAGE
PROf
ERL
Yl
a
1JTCH
JUDDE
a
tn
CII
eRA
fON
ENCAGEMDIT
CLIJfCH
NOISE
SQUEAL
DEl
ltESSlNG
nlE
PEDAL
nUTCH
NOISE
RATTLE
WHEN
IDI
ING
CLUTCH
NOISE
CHATTER
ON
a
GAGEMENI
I
I
j
ILlm
ROUBLE
CAUSE
I
hllUtrident
f
lay
In
RIM
link
Ia
CllIlclldilC
facbllWl
lmorlludlned
t
Gt
dM
01
oil
cluu
h
d
ana
d
Wellk
or
brotell
pralure
plate
coilsprinp
or
diapht
m
IprIzlf
to
Alrinhydr
lIlie
tma
r
l
ffid
n
r
I
tc
hltcbped
Elc
c
frw
plly
kft
Iink
h
MlIali
DIIleruofdutdabOUJ
i
a
L
ctutcb
dlx
hllb
blndinl
011
of
FctJoz
laput
matt
J
Clutch
dilc
faclnf
10
or
brot
II
Pn
n
pllte
malin
Nrflet
w
d
L
ClukIl
CO
Ierdl
lorl
d
m
Lo
nttl
It
tnlllmblllon
or
rlIkm
Ii
Clutch
d
4i1torWd
LoC
drift
plate
hub
p
Relr
a
ba
tIn
d
rcc
q
Reina
UlIl
Mnt
r
l
o
b
Vau1lcf
luld
l
I
b
OE
1
R08A1LE
CAUSE
I
Adj
t
IinbF
tI
Replace
elutchdlK
c
CIUlllnd
l
eIlIedy
CIII
d
ae
prln
lInSl
llem
f
AdJ
t
tnweL
Niju
st
gII
It
Irom
put
lLaealipll
ReIl
CIU
gfbUadiJll
j
aepllC
t1utdl
dK
11
Pit
ne
puta
1
lI
epla
c
m
TIk
lIp
pia
ae
dK
aepl
cellub
p
Reiin
b
4
Strlilhtenor
f
To
I
p
hy4rw1k
ftuid
Tyre
pnlUUI1IIlncoo
ct
or
un
no
b
Lec1l
oIJ
l
brk
l
ltlnltlt
r
Co
uck
oflubric
t1on
t
t
lU
IliDt
p
ball
Joillta
4
Inc
t
Mil
a1
aNM
nt
laeomctl
adj
ma
tccriaI
pr
f
StMrbtloobuMb
IrtJlptooaptorcohuMbcalor
aUalllipMd
I
na
UU
JobltJ
u1I
or
Joe
b
Proal
lrbtd
artap
or
116
4
L
sacu
1Il
frollt
lUlptlllioa
J
d
boolnallloo
t
It
Ill
wb
100II
L
StMdn
plr
mountiJl
both
100
m
ltleerina
I
U
om
II
SIlock
IblOl
WI
defoc
or
ItlOUfttinp
IGolC
0
ll
oIId
wbedJ
lmbllancedor
t
tu
l
lIImitltr
x
D
p
S
IIPIUioa
IPrInp
e
Ik
01
blOt
CII
IrUd
paDiq
Oft
Oft
r
aa
frllJlt
or
AlIPfaaoa
mbaIlpcd
llllproperobtriftJ
II
I
ma
P
l
f
Il
i
I
II
I
m
JtE
lIED1D
I
Inn
te
Ind
balln
t
ra
b
Inject
lIItln
nl
C
Lubnclte
4
Check
1
rifla
tOll
t
ry
e
djUlt
QOlTectly
I
djuttrelll
defe
t
pIrtI
Ti
ht
n
r
pllCe
joints
h
t
ilDtor
renc
bannp
i
Ttchtentoco
cttorqu
j
Tiaht
n
correct
torque
t
fiahten
con
ttO
lIe
I
Tiahtcn
correct
torque
m
Jlepl
c
om
putl
II
aepl
c
ith
nC
Ballonce
h
p
Rene
prinp
q
laJan
bnltct
r
lI
eaJian
Ull
Ielllllion
drio
Page 130 of 171
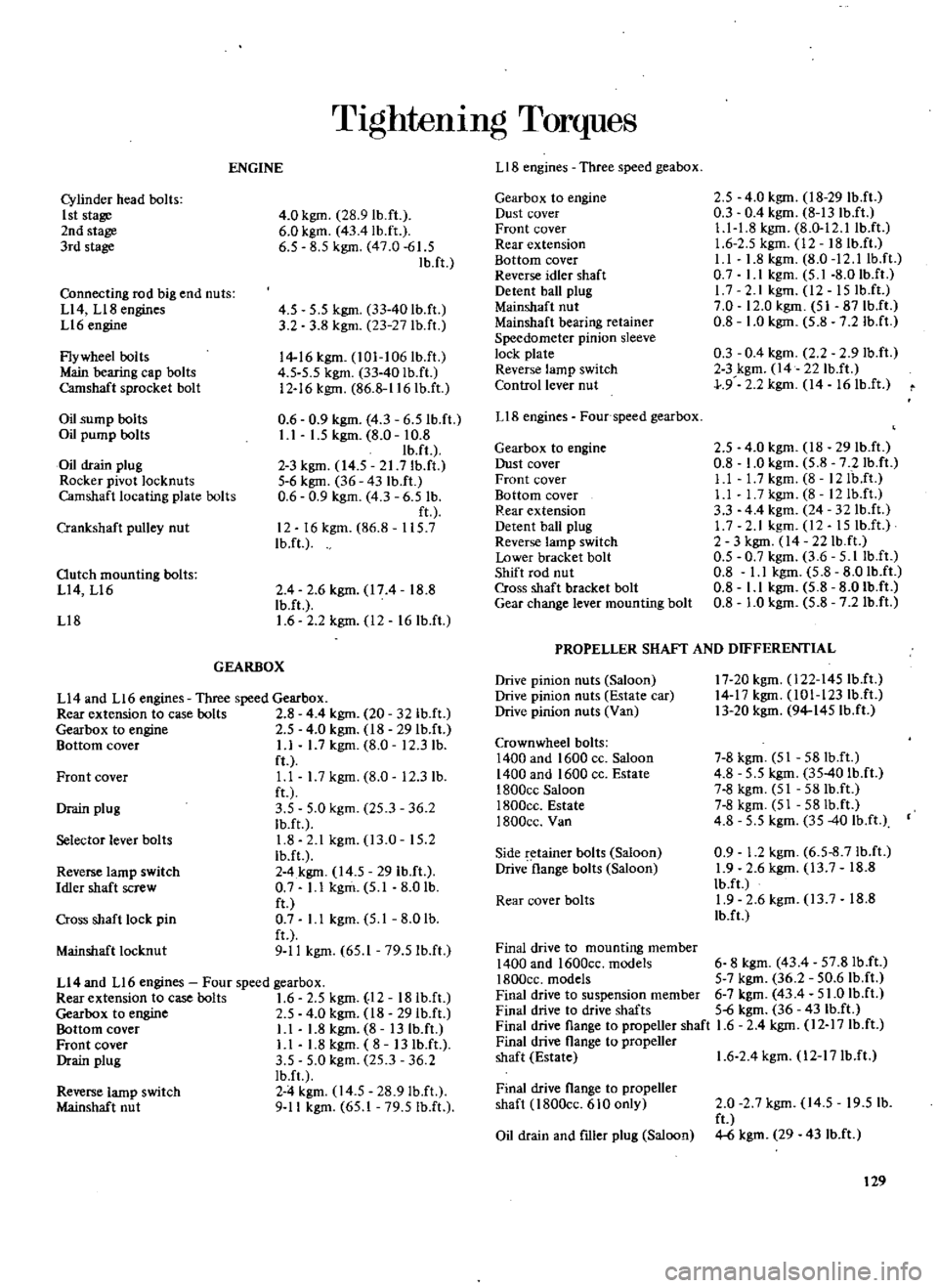
TIghtenIng
Torques
LIB
engines
Three
speed
geabox
ENGINE
2
5
4
0
kgm
18
29
Ib
ft
0
3
0
4
kgm
8
13
IbJI
Ll
1
8
kgm
8
0
12
llbJt
1
6
2
5
kgm
12
18Ib
ft
I
I
1
8
kgm
8
0
12
llbJt
0
7
I
I
kgm
5
1
8
0
IbJt
17
2
lkgm
l2
15IbJI
7
0
12
0
kgm
51
87IbJI
0
8
1
0
kgm
5
8
7
2
IbJI
0
3
0
4
kgm
2
2
2
9Ib
ft
2
3
kgm
14
22IbJI
J
9
2
2
kgm
14
16IbJI
Gearbox
to
engine
Dust
cover
Front
cover
Rear
extension
Bottom
cover
Reverse
idler
shaft
Detent
ball
plug
Mainshaft
nut
Mainshaft
bearing
retainer
Speedometer
pinion
sleeve
lock
plate
Reverse
lamp
switch
Control
lever
nut
Cylinder
head
bolts
1st
stage
2nd
stage
3rd
slage
4
0
kgm
28
9Ib
ft
6
0
kgm
43
4lb
ft
6
5
8
5
kgm
47
0
61
5
Ib
ft
Connecting
rod
big
end
nuts
Ll4
Ll8
engines
Ll6
engine
Flywheel
bolls
Main
bearing
cap
bolts
Camshaft
sprocket
bolt
4
5
5
5
kgm
33
40
Ib
fl
3
2
3
8
kgm
23
27
lb
ft
14
16
kgm
l01
106Ib
ft
4
5
5
5
kgm
33
40Ib
ft
12
16
kgm
86
8
116IbJt
0
6
0
9
kgm
4
3
6
5IbJt
I
I
1
5
kgm
8
0
10
8
Ib
fl
2
3
kgm
14
5
21
7Ib
ft
5
6
kgm
36
43
Ib
ft
0
6
0
9
kgm
4
3
6
5
Ib
ft
12
16kgm
86
8
115
7
IbJt
LIB
engines
Four
speed
gearbox
Oil
sump
bolts
Oil
pump
bolts
Oil
drain
plug
Rocker
pivot
locknuts
Camshaft
locating
plate
bolts
2
5
4
0
kgm
18
29
IbJt
0
8
1
0
kgm
5
8
7
2Ib
ft
Ll
l
7kgm
8
12IbJt
Ll
I
7kgm
8
12Ib
ft
3
3
44
kgm
24
32IbJI
1
7
2
1
kgm
12
15
IbJt
2
3
kgm
14
22Ib
ft
0
5
0
7
kgm
3
6
5
IlbJI
0
8
I
I
kgm
5
8
8
0Ib
ft
0
8
Ll
kgm
5
8
8
01b
ft
0
8
1
0
kgm
5
8
7
2Ib
ft
Gearbox
to
engine
Dust
cover
Front
cover
Bottom
cover
Rear
extension
Detent
ball
plug
Reverse
lamp
switch
Lower
bracket
bolt
Shift
rod
nut
Cross
shaft
bracket
bolt
Gear
change
lever
mounting
bolt
Crankshaft
pulley
nut
Outch
mounting
bolts
L14
Ll6
Ll8
2
4
2
6kgm
174
18
8
Ib
ft
1
6
2
2
kgm
12
16Ib
fl
PROPELLER
SHAFf
AND
DIFFERENTIAL
GEARBOX
17
20kgm
l22
145IbJI
14
17
kgm
101
123Ib
ft
13
20
kgm
94
145Ib
fI
Drive
pinion
nuts
Saloon
Drive
pinion
nuts
Estate
car
Drive
pinion
nuts
Van
Ll4
and
L16
engines
Three
speed
Gearbox
Rear
extension
to
case
bolts
2
8
4
4
kgm
20
32lb
ft
Gearbox
10
engine
2
5
4
0
kgm
18
29Ib
fI
Bnttom
cover
L1
1
7
kgm
8
0
12
3
lb
ft
Ll
1
7
kgm
8
0
12
3
lb
fl
3
5
5
0
kgm
25
3
36
2
Ib
ft
1
8
2
1
kgm
13
0
15
2
Ib
ft
2
4
kgm
14
5
29
Ib
ft
0
7
L1
kgm
5
1
8
0
lb
ft
0
7
Ll
kgm
5
1
8
0
lb
fl
9
11
kgm
65
1
79
51b
ft
Crown
wheel
bolts
1400
and
1600
cc
Saloon
1400
and
1600
cc
Eslale
1800ce
Saloon
I800cc
Estate
1800cc
Van
7
8
kgm
51
58Ib
ft
4
8
5
5
kgm
35
40
Ib
ft
7
8
kgm
51
58Ib
ft
7
8
kgm
51
58Ib
ft
4
8
5
5
kgm
35
40
Ib
ft
0
9
1
2
kgm
6
5
8
7Ib
ft
1
9
2
6
kgm
13
7
18
8
IbJI
1
9
2
6
kgm
13
7
18
8
Ib
f
Front
cover
Drain
plug
Selector
lever
bolts
Side
retainer
bolts
Saloon
Drive
flange
bolts
Saloon
Reverse
lamp
switch
Idler
shaft
screw
Rear
cover
bolts
Cross
shaft
lock
pin
Final
drive
to
mounting
member
1400
and
1600cc
models
6
8
kgm
43
4
57
8IbJI
1800cc
models
5
7
kgm
36
2
50
6Ib
fI
Final
drive
to
suspension
member
6
7
kgm
43
4
51
0
Ib
ft
Final
drive
to
drive
shafls
5
6
kgm
36
431b
ft
Final
drive
flange
to
propeller
shaft
1
6
2
4
kgm
12
17
Ib
ft
Final
drive
flange
to
propeller
shaft
Eslale
1
6
2
4
kgm
l2
17Ib
ft
Mainshafl
locknut
Ll4
and
L16
engines
Four
speed
gearbox
Rearexlension
to
case
bolts
1
6
2
5
kgm
12
18Ib
ft
Gearbox
to
engine
2
5
4
0
kgm
18
29Ib
ft
Bottnm
cnver
L1
1
8
kgm
8
13
Ib
ft
Fronl
cover
L1
1
8
kgm
8
13
IbJI
Drain
plug
3
5
5
0
kgm
25
3
36
2
Ib
f
2
4
kgm
14
5
28
9IbJt
9
11
kgm
65
1
79
5Ib
ft
Final
drive
flange
to
propeller
shaft
l800cc
610
only
Reverse
lamp
switch
Mainshaft
nut
2
0
2
7
kgm
14
5
19
5
lb
ft
4
6
kgm
29
43
Ib
ft
Oil
drain
and
flller
plug
Saloon
129
Page 132 of 171
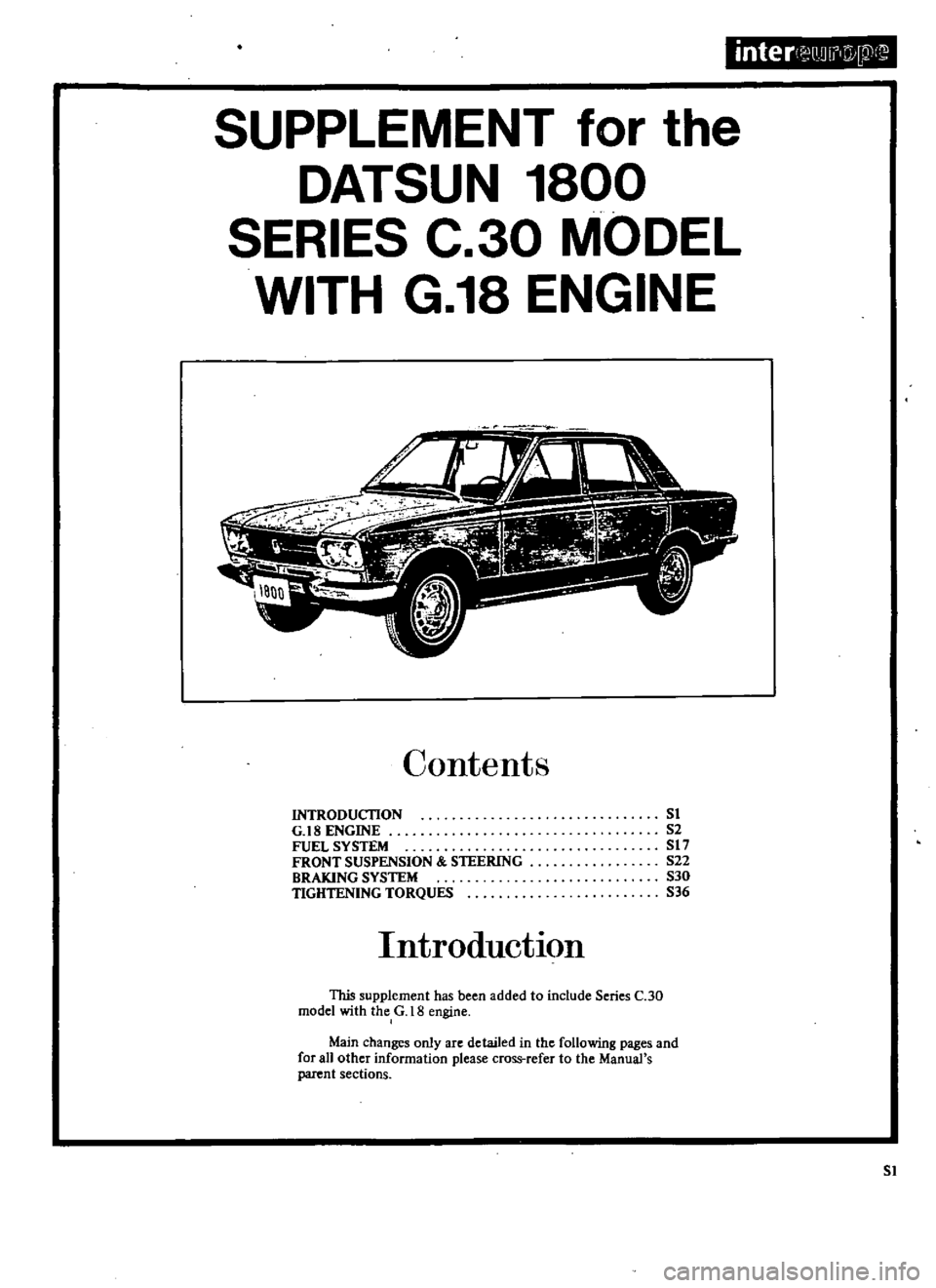
inter
QDu
w
P1
SUPPLEMENT
for
the
DATSUN
1800
SERIES
C
30
MODEL
WITH
G
18
ENGINE
Contents
INTRODUCTION
G
18
ENGINE
FUEL
SYSTEM
FRONT
SUSPENSION
STEERING
BRAKING
SYSTEM
TIGhlGJ
u
GTORQUES
SI
S2
SI7
S22
S30
S36
IntroductIon
This
supplement
has
been
added
to
include
Series
C
30
model
with
the
G
18
engine
Main
changes
only
are
detailed
in
the
following
pages
and
for
aU
other
information
please
CI
to
the
Manual
s
parent
sections
SI