ECU DATSUN PICK-UP 1977 Service Manual
[x] Cancel search | Manufacturer: DATSUN, Model Year: 1977, Model line: PICK-UP, Model: DATSUN PICK-UP 1977Pages: 537, PDF Size: 35.48 MB
Page 518 of 537
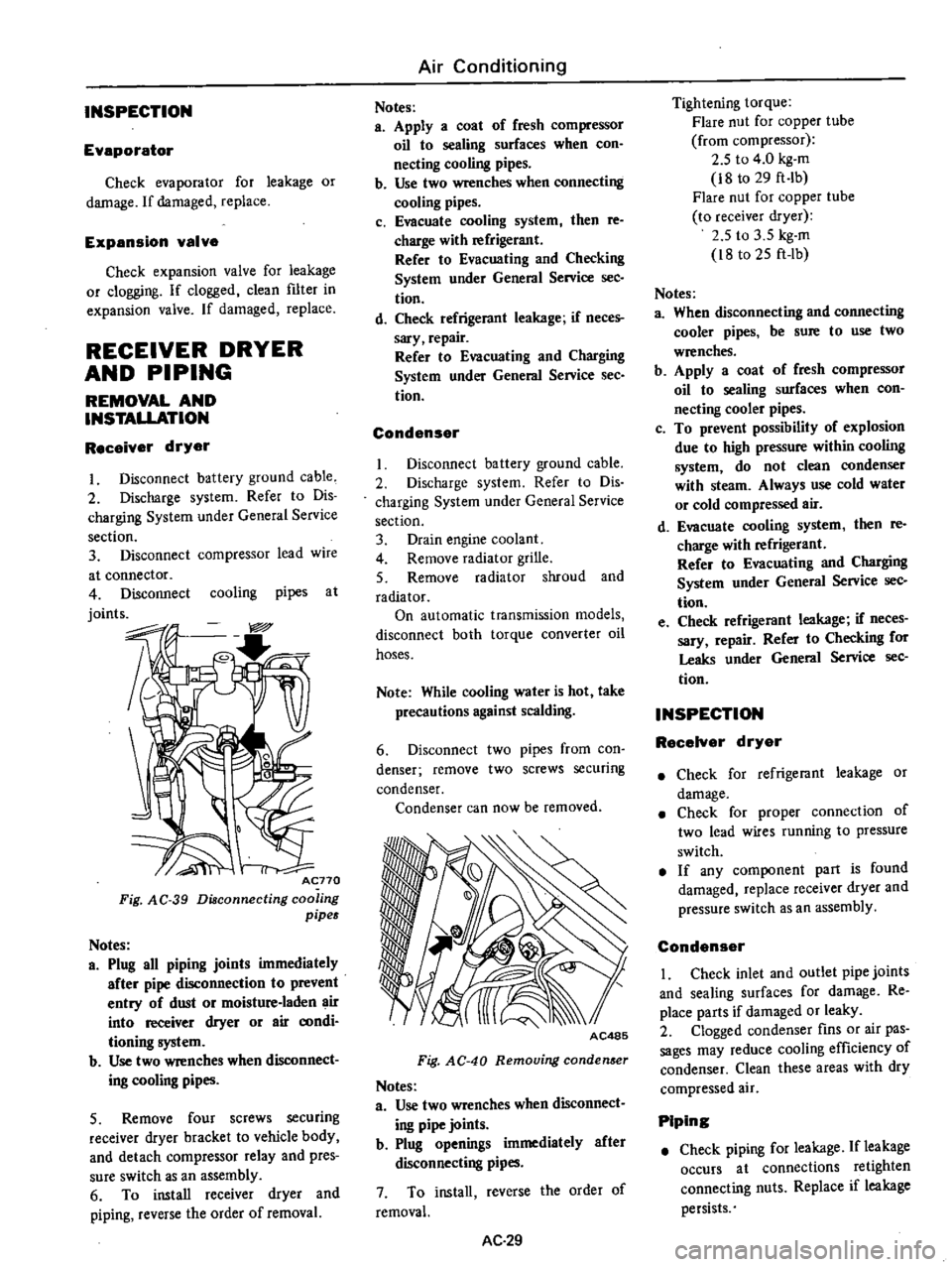
INSPECTION
Evaporator
Check
evaporator
for
leakage
or
damage
If
damaged
replace
Expansion
valve
Check
expansion
valve
for
leakage
or
clogging
If
clogged
clean
filter
in
expansion
valve
If
damaged
replace
RECEIVER
DRYER
AND
PIPING
REMOVAL
AND
INSTAUATION
Receiver
dryer
I
Disconnect
battery
ground
cable
2
Discharge
system
Refer
to
Dis
charging
System
under
General
Service
section
3
Disconnect
compressor
lead
wire
at
connector
4
Disconnect
cooling
pipes
at
joints
Acno
Fig
AC
39
Diaconnecting
coo
ing
pipes
Notes
a
Plug
all
piping
joints
immediately
after
pipe
disconnection
to
prevent
entry
of
dust
or
moisture
laden
air
into
receiver
dryer
or
air
aJOdi
tioning
system
b
Use
two
wrenches
when
dIsconnect
ing
cooling
pipes
5
Remove
four
screws
securing
receiver
dryer
bracket
to
vehicle
body
and
detach
compressor
relay
and
pres
sure
switch
as
an
assembly
6
To
install
receiver
dryer
and
piping
reverse
the
order
of
removal
Air
Conditioning
Notes
a
Apply
a
coat
of
fresh
compressor
oil
to
sealing
surfaces
when
con
necting
cooling
pipes
b
Use
two
wrenches
when
connecting
cooling
pipes
c
Evacuate
cooling
system
then
re
charge
with
refrigerant
Refer
to
Evacuating
and
Checking
System
under
General
Service
sec
tion
d
Check
refrigerant
leakage
if
neces
sary
repair
Refer
to
Evacuating
and
Charging
System
under
General
Service
See
tion
Condenser
Disconnect
battery
ground
cable
2
Discharge
system
Refer
to
Dis
charging
System
under
General
Service
section
3
Drain
engine
coolant
4
Remove
radiator
grille
5
Remove
radiator
shroud
and
radiator
On
automatic
transmission
models
disconnect
both
torque
converter
oil
hoses
Note
While
cooling
water
is
hot
take
precautions
against
scalding
6
Disconnect
two
pipes
from
con
denser
remove
two
screws
securing
condenser
Condenser
can
now
be
removed
AC485
Fig
AC
40
Removing
conden
er
Notes
a
Use
two
wrenches
when
disconnect
ing
pipe
joints
b
Plug
openings
immediately
after
disconnecting
pipes
7
To
install
reverse
the
order
of
removal
AC
29
Tightening
torque
Flare
nut
for
copper
tube
from
compressor
2
5
to
4
0
kg
m
i8
to
29
ft
Ib
Flare
nut
for
copper
tube
to
receiver
dryer
2
5
to
3
5
kg
m
i8
to
25
ft
lb
Notes
a
When
disconnecting
and
connecting
cooler
pipes
be
sure
to
use
two
wrenches
b
Apply
a
coat
of
fresh
compressor
oil
to
sealing
surfaces
when
con
necting
cooler
pipes
c
To
prevent
possibility
of
explosion
due
to
high
pressure
within
cooling
system
do
not
clean
condenser
with
steam
Always
use
cold
water
or
cold
compressed
air
d
Evacuate
cooling
system
then
re
charge
with
refrigerant
Refer
to
Evacuating
and
Charging
System
under
General
Service
sec
tion
e
Check
refrigerant
leakage
if
neces
sary
repair
Refer
to
Checking
for
Leaks
under
General
Service
sec
tion
INSPECTION
RecelYer
dryer
Check
for
refrigerant
leakage
or
damage
Check
for
proper
connection
of
two
lead
wires
running
to
pressure
switch
If
any
component
part
is
found
damaged
replace
receiver
dryer
and
pressure
switch
as
an
assembly
Condenser
I
Check
inlet
and
outlet
pipe
joints
and
sealing
surfaces
for
damage
Re
place
parts
if
damaged
or
leaky
2
Clogged
condenser
fins
or
air
pas
sages
may
reduce
cooling
efficiency
of
condenser
Clean
these
areas
with
dry
compressed
air
Piping
Check
piping
for
leakage
If
leakage
occurs
at
connections
retighten
connecting
nuts
Replace
if
leakage
persists
Page 520 of 537
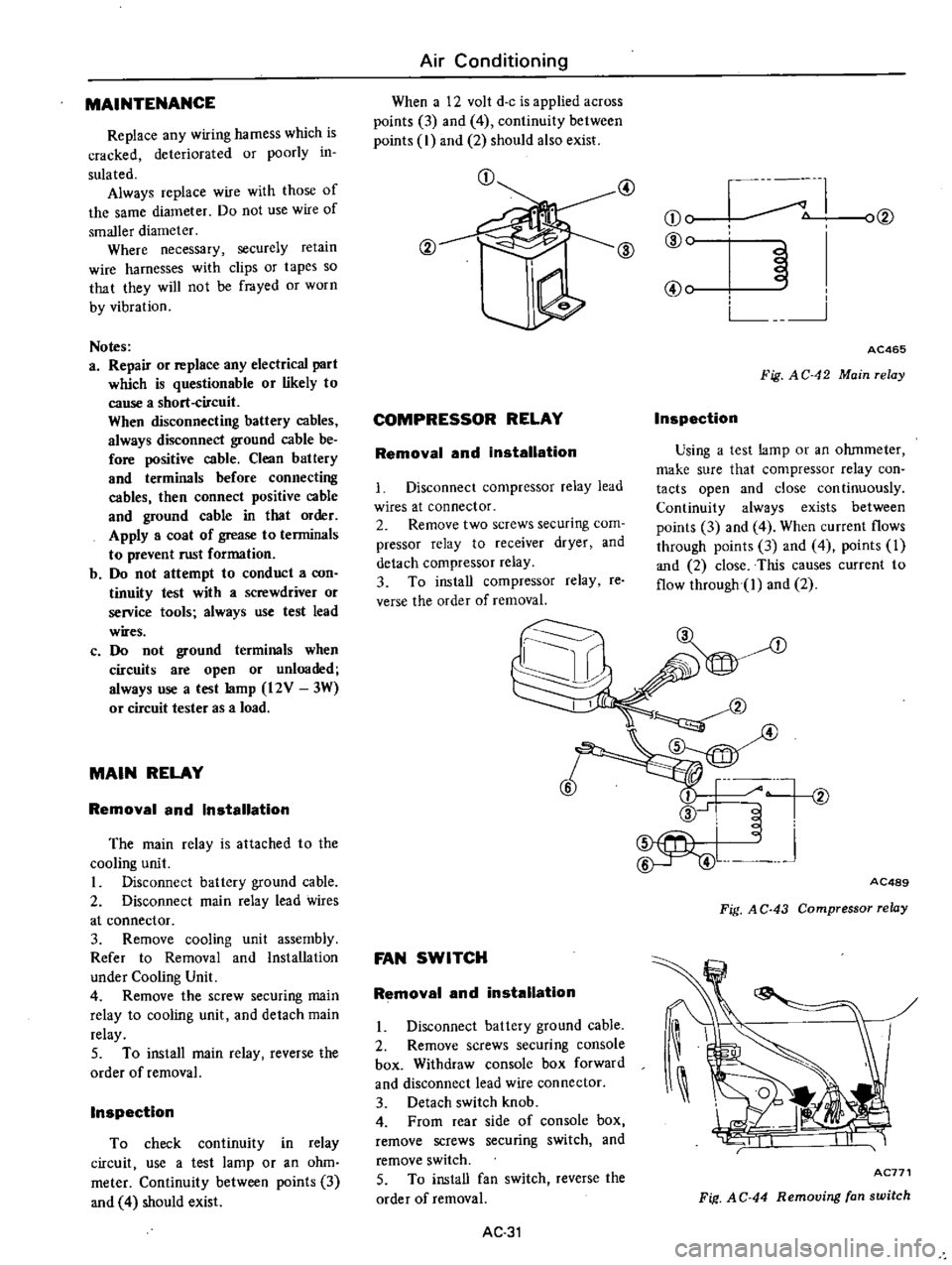
MAINTENANCE
Replace
any
wiring
harness
which
is
cracked
deteriorated
or
poorly
in
sulated
Always
replace
wire
with
those
of
the
same
diameter
Do
not
use
wire
of
smaller
diameter
Where
necessary
securely
retain
wire
harnesses
with
clips
or
tapes
so
that
they
will
not
be
frayed
or
worn
by
vibration
Notes
a
Repair
or
replace
any
electrical
part
which
is
questionable
or
likely
to
cause
a
short
circuit
When
disconnecting
battery
cables
always
disconnect
ground
cable
be
fore
positive
cable
Clean
battery
and
terminals
before
connecting
cables
then
connect
positive
cable
and
ground
cable
in
that
order
Apply
a
coat
of
grease
to
terminals
to
prevent
rust
formation
b
Do
not
attempt
to
conduct
a
con
tinuity
test
with
a
screwdriver
or
service
tools
always
use
test
lead
wires
c
Do
not
ground
terminals
when
circuits
are
open
or
unloaded
always
use
a
test
lamp
12V
3W
or
circuit
tester
as
a
load
MAIN
RELAY
Removal
and
Installation
The
main
relay
is
attached
to
the
cooling
unit
I
Disconnect
battery
ground
cable
2
Disconnect
main
relay
lead
wires
at
connector
3
Remove
cooling
unit
assembly
Refer
to
Removal
and
Installation
under
Cooling
Unit
4
Remove
the
screw
securing
main
relay
to
cooling
unit
and
detach
main
relay
5
To
install
main
relay
reverse
the
order
of
removal
Inspection
To
check
continuity
in
relay
circuit
use
a
test
lamp
or
an
ohm
meter
Continuity
between
points
3
and
4
should
exist
Air
Conditioning
When
a
12
volt
d
c
is
applied
across
points
3
and
4
continuity
between
points
I
and
2
should
also
exist
CD
00
COMPRESSOR
RELAY
Removal
and
installation
Disconnect
compressor
relay
lead
wires
at
connector
2
Remove
two
screws
securing
com
pressor
relay
to
receiver
dryer
and
detach
compressor
relay
3
To
install
compressor
relay
reo
verse
the
order
of
removal
@
I
ul
CDe
JOO
ID
IDe
@e
L
AC465
Fig
AC
42
Main
relay
Inspection
Using
a
test
lamp
or
an
ohmmeter
make
sure
that
compressor
relay
con
tacts
open
and
close
con
tinuously
Continuity
always
exists
between
points
3
and
4
When
current
flows
through
points
3
and
4
points
1
and
2
close
This
causes
current
to
flow
through
1
and
2
FAN
SWITCH
Removal
and
installation
1
Disconnect
battery
ground
cable
2
Remove
screws
securing
console
box
Withdraw
console
box
forward
and
disconnect
lead
wire
connector
3
Detach
switch
knob
4
From
rear
side
of
console
box
remove
screws
securing
switch
and
remove
switch
5
To
install
fan
switch
reverse
the
order
of
removal
AC
31
i
t
v
J
AC489
Fig
A
C
43
Compressor
relay
AC771
Fif
AC
44
Removing
fan
switch
Page 521 of 537
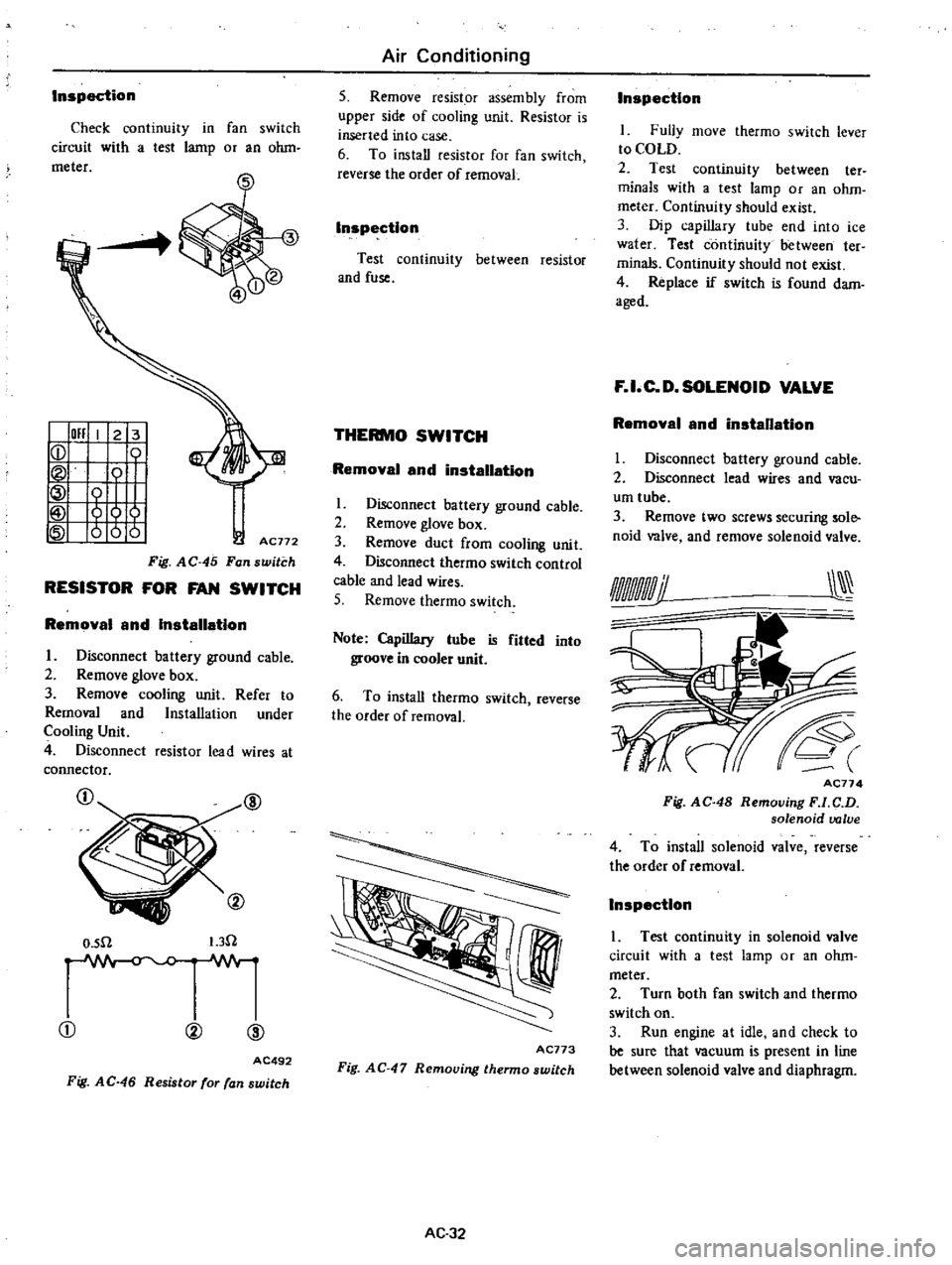
Inspection
Check
continuiry
in
fan
switch
circuit
with
a
test
lamp
or
an
ohm
meter
I
011
I
2
3
ICD
Tt
tt
AC772
Fig
AC
45
Fan
switch
RESISTOR
FOR
FAN
SWITCH
Removal
and
Installation
I
Disconnect
battery
ground
cable
2
Remove
glove
box
3
Remove
cooling
unit
Refer
to
Removal
and
Installation
under
Cooling
Unit
4
Disconnect
resistor
lead
wires
at
connector
@
O
sn
I
3n
CD
00
@
AC492
Fig
AC
46
Resistor
for
fan
switch
Air
Conditioning
5
Remove
resistor
assembly
from
upper
side
of
cooling
unit
Resistor
is
inserted
into
case
6
To
install
res
istor
for
fan
switch
reverse
the
order
of
removaL
Inspection
Test
continuity
between
resistor
and
fuse
THERMO
SWITCH
Removal
and
installation
1
Disconnect
battery
ground
cable
2
Remove
glove
box
3
Remove
duct
from
cooling
unit
4
Disconnect
thermo
switch
control
cable
and
lead
wires
5
Remove
thermo
switch
Note
Capillary
lube
is
fitted
into
groove
in
cooler
unit
6
To
install
thermo
switch
reverse
the
order
of
removal
I
I
AC773
Fig
AC
47
Removing
thermo
switch
AC
32
Inspection
I
Fully
move
thermo
swirch
lever
to
COLD
2
Test
continuity
between
ter
minals
with
a
test
tamp
or
an
ohm
meter
Continuity
should
exist
3
Dip
capillary
tube
end
into
ice
water
Test
continuity
between
ter
minals
Continuity
should
not
exist
4
Replace
if
switch
is
found
dam
aged
F
I
C
D
SOLENOID
VALVE
Removal
and
installation
I
Disconnect
battery
ground
cable
2
Disconnect
lead
wires
and
vacu
um
tube
3
Remove
two
screws
securing
sole
noid
valve
and
remove
solenoid
valve
AC77
4
Fig
AC
48
Removing
F
l
C
D
solenoid
valve
4
To
install
solenoid
valve
reverse
the
order
of
removal
Inspection
1
Test
continuity
in
solenoid
valve
circuit
with
a
test
lamp
or
an
ohm
meter
2
Turn
both
fan
switch
and
thermo
switch
on
3
Run
engine
at
idle
and
check
to
be
sure
that
vacuum
is
present
in
line
between
solenoid
valve
and
diaphragm
Page 523 of 537
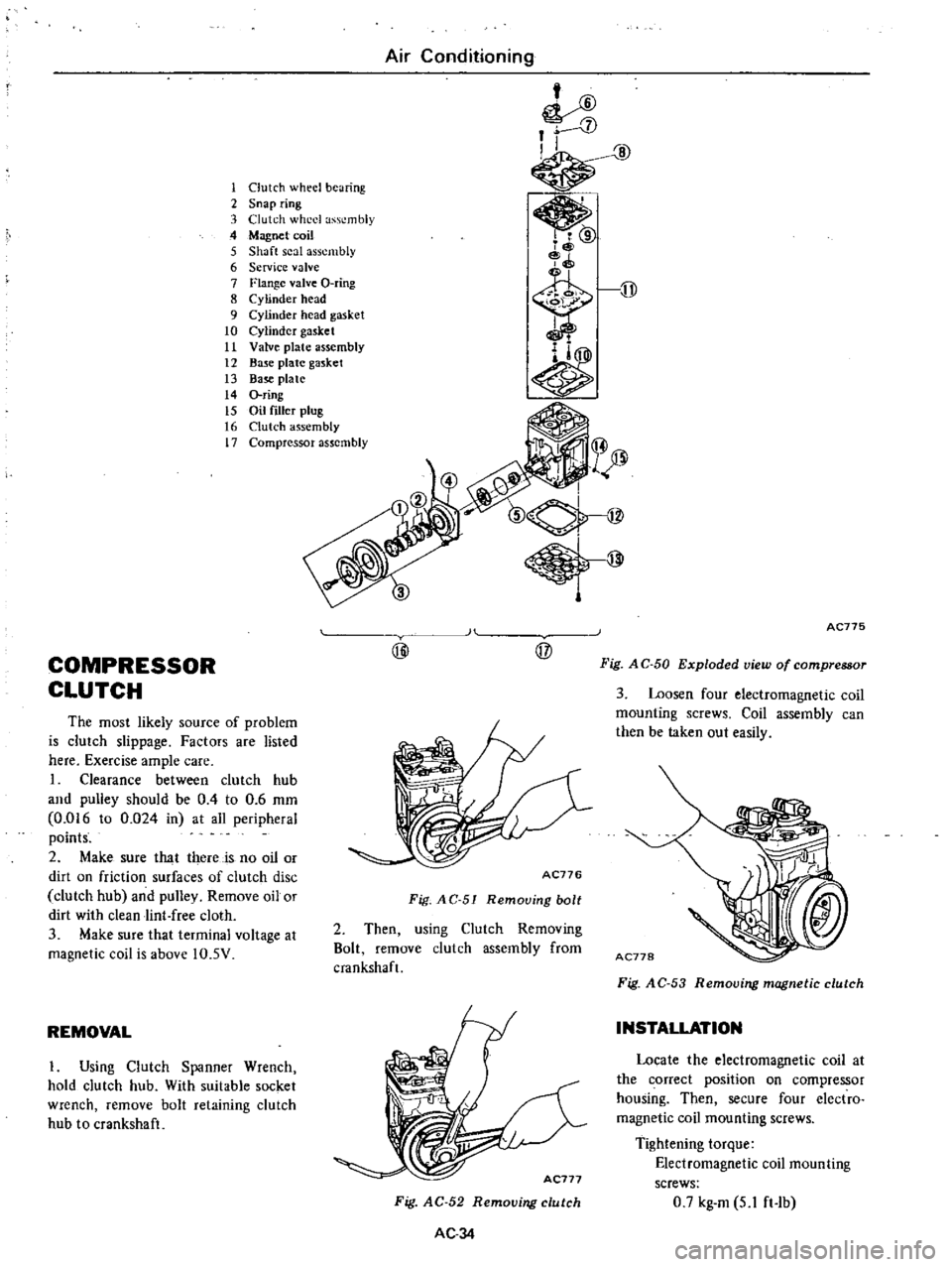
Air
Conditioning
1foo
1t
1
t7
LV
I
1
Clutch
wheel
bearing
2
Snap
ring
3
Clutch
wheel
assembly
4
Magnet
coil
5
Shaft
seal
assembly
6
Service
valve
7
Flange
valve
O
ring
8
Cylinder
head
9
Cylinder
head
gasket
10
Cylinder
gasket
11
Valve
plate
assembly
12
Base
plate
gasket
13
Base
plate
14
O
ring
15
Oil
filler
plug
16
Clutch
assembly
17
Compressor
assembly
COMPRESSOR
CLUTCH
The
most
likely
source
of
problem
is
clutch
slippage
Factors
are
listed
here
Exercise
ample
care
I
Clearance
between
clutch
hub
and
pulley
should
be
0
4
to
0
6
mm
0
016
to
0
024
in
at
all
peripheral
points
2
Make
sure
that
there
is
no
oil
or
dirt
on
friction
surfaces
of
clutch
disc
clutch
hub
and
pulley
Remove
oil
or
dirt
with
clean
lint
free
cloth
3
Make
sure
that
terminal
voltage
at
magnetic
coil
is
above
IO
5V
REMOVAL
I
Using
Clutch
Spanner
Wrench
hold
clutch
hub
With
suitable
socket
wrench
remove
bolt
retaining
clutch
hub
to
crankshaft
H
@
@
AC776
Fig
AC
51
Remouing
bolt
2
Then
using
Clutch
Removing
Bolt
remove
clutch
assembly
from
cmnkshaft
Fig
AC
52
Removing
clutch
AC34
AC775
Fig
A
C
50
Exploded
view
of
compressor
3
Loosen
four
electromagnetic
coil
mounting
screws
Coil
assembly
can
then
be
taken
out
easily
Fig
A
C
53
Removing
magnetic
clutch
INSTALLATION
Locate
the
electromagnetic
coil
at
the
correct
position
on
compressor
housing
Then
secure
four
electro
magnetic
coil
mounting
screws
Tightening
torque
Electromagnetic
coil
mounting
screws
0
7
kg
m
5
1
ft
Ib
Page 524 of 537
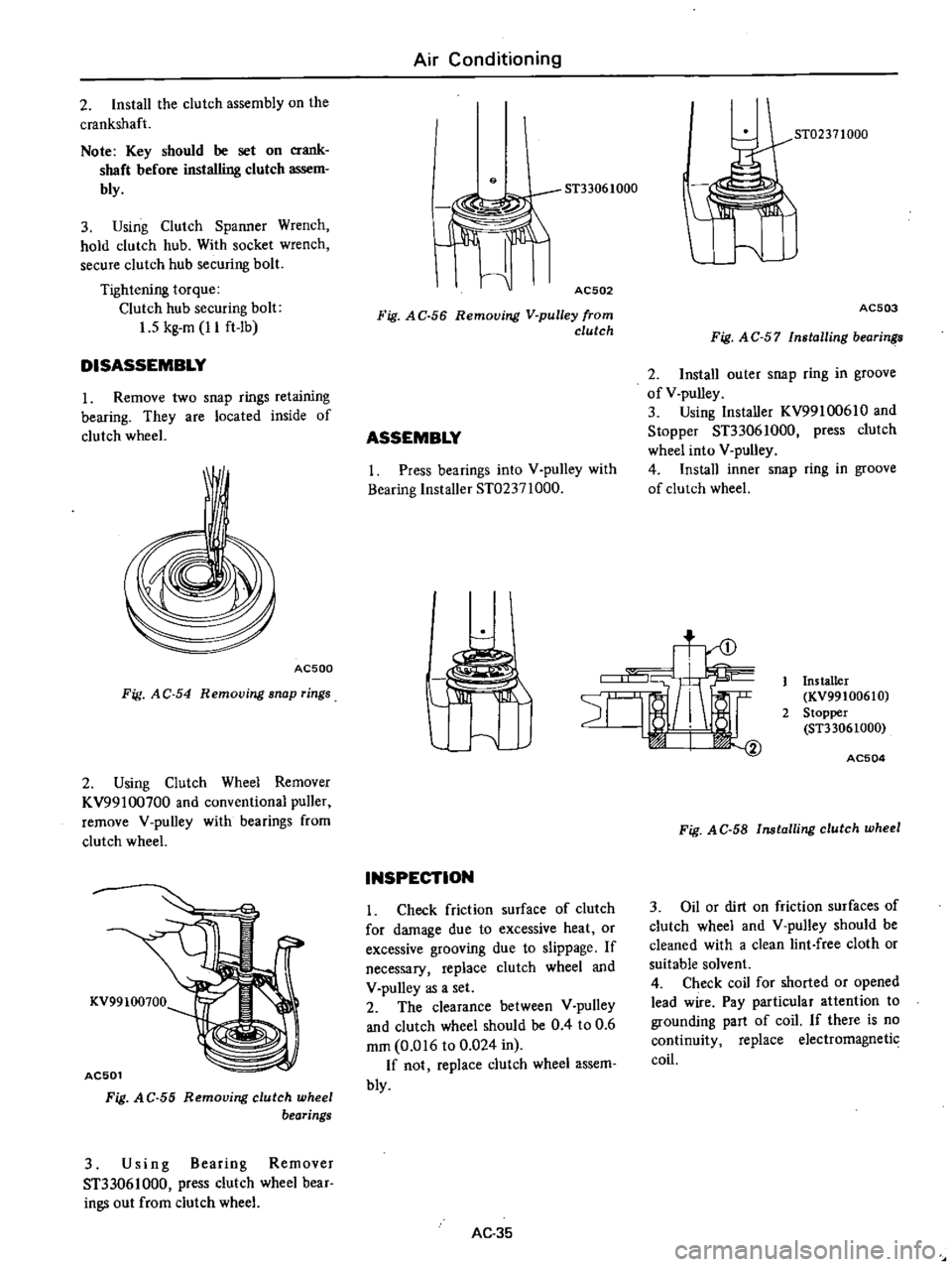
2
Install
the
clutch
assembly
on
the
crankshaft
Note
Key
should
be
set
on
crank
shaft
before
installing
clutch
assem
bly
3
Using
Clutch
Spanner
Wrench
hold
clutch
hub
With
socket
wrench
secure
clutch
hub
securing
bolt
Tightening
torque
Clutch
hub
securing
bolt
1
5
kg
m
II
ft
lb
DISASSEMBLY
1
Remove
two
snap
rings
retaining
bearing
They
are
located
inside
of
clutch
wheel
AC500
Fig
AC
54
Removing
snap
rings
2
Using
Clutch
Wheel
Remover
KV99100700
and
conventional
puller
remove
V
pulley
with
bearings
from
clutch
wheel
KV99100700
AC501
Fig
A
C
55
Removing
clutch
wheel
bearings
3
Using
Bearing
Remover
ST33061000
press
clutch
wheel
bear
ings
out
from
clutch
wheel
Air
Conditioning
9
AC502
Fig
AC
56
Removing
V
pulley
from
clutch
ASSEMBLY
I
Press
bearings
into
V
pulley
with
Bearing
Installer
ST02371000
ST02371000
AC503
Fig
A
C
57
Installing
bearin
2
Install
outer
snap
ring
in
groove
of
V
pulley
3
Using
Installer
KV99100610
and
Stopper
ST33061000
press
clutch
wheel
into
V
pulley
4
Install
inner
snap
ring
in
groove
of
clutch
wheel
t
INSPECTION
Check
friction
surface
of
clutch
for
damage
due
to
excessive
heat
or
excessive
grooving
due
to
slippage
If
necessary
replace
clutch
wheel
and
V
pulley
as
a
set
2
The
clearance
between
V
pulley
and
clutch
wheel
should
be
0
4
to
0
6
mm
0
016
to
0
024
in
If
not
replace
clutch
wheel
assem
bly
AC
35
Installer
KV99100610
2
Stopper
ST33061000
AC504
Fig
AC
58
Installing
clutch
wheel
3
Oil
or
dirt
on
friction
surfaces
of
clutch
wheel
and
V
pulley
should
be
cleaned
with
a
clean
lint
free
cloth
or
suitable
solvent
4
Check
coil
for
shorted
or
opened
lead
wire
Pay
particular
attention
to
grounding
part
of
coil
If
there
is
no
continuity
replace
electromagnetic
coil
Page 525 of 537
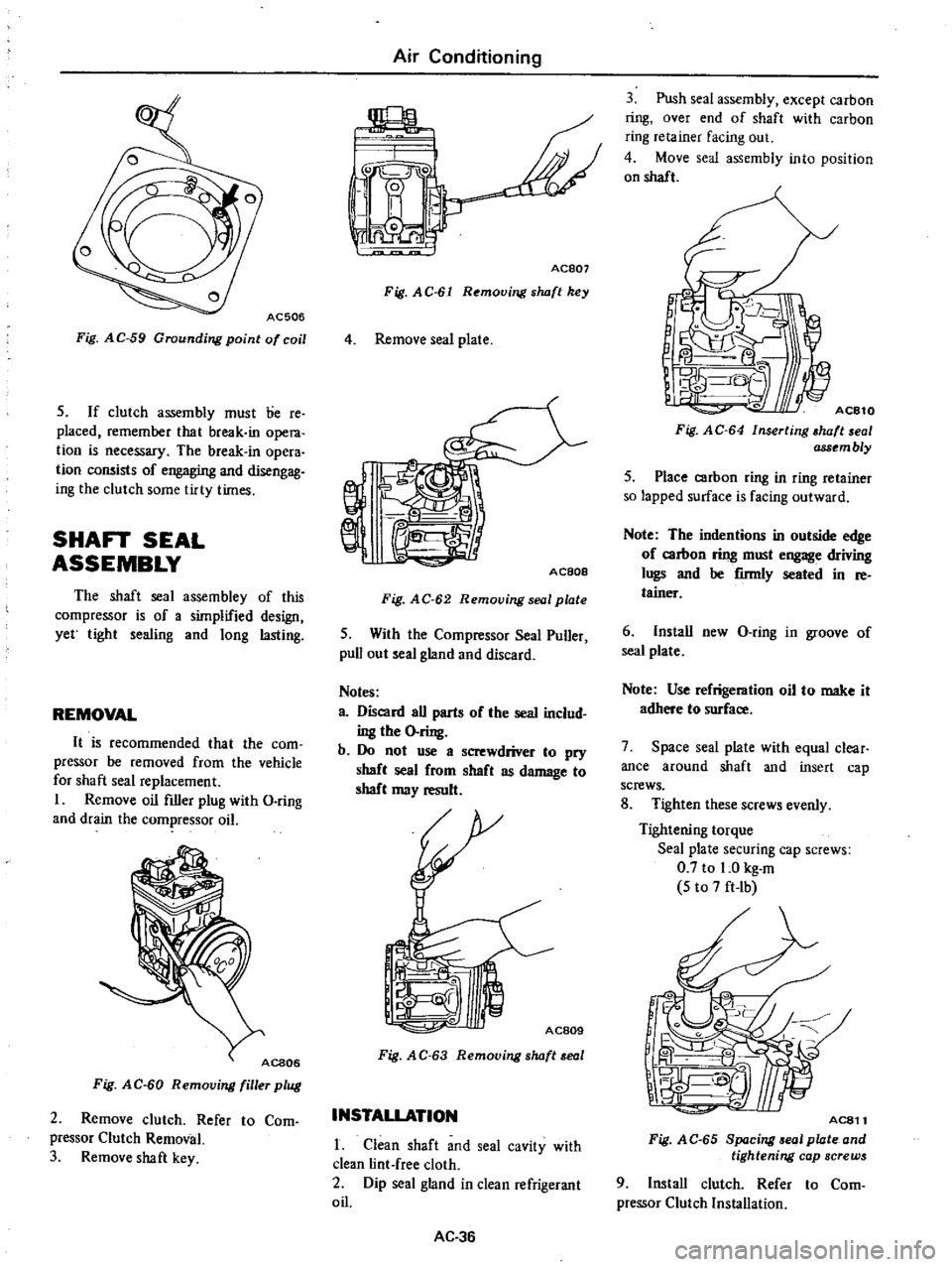
AC506
Fig
AC
59
Grounding
point
of
coil
5
If
clutch
assembly
must
lie
re
placed
remember
that
break
in
opera
tion
is
necessary
The
break
in
opera
tion
consists
of
engaging
and
disengag
ing
the
clutch
some
tirty
times
SHAFT
SEAL
ASSEMBLY
The
shaft
seal
assembley
of
this
compressor
is
of
a
simplified
design
yet
tight
sealing
and
long
lasting
REMOVAL
It
is
recommended
that
the
com
pressor
be
removed
from
the
vehicle
for
shaft
seal
replacement
I
Remove
oil
filler
plug
with
D
ring
and
drain
the
compressor
oil
Fig
AC
60
Removing
filler
plug
2
Remove
clutch
Refer
to
Com
pressor
Clutch
Removal
3
Remove
shaft
key
Air
Conditioning
jpL
Y
L
I
i
0
I
I
0
Ace07
Fig
AC
61
Removing
s
wft
key
4
Remove
seal
plate
AC80e
Fig
AC
62
Removing
seal
plate
5
With
the
Compressor
Seal
Puller
pull
out
seal
gland
and
discard
Notes
a
Discard
all
parts
of
the
seal
includ
ing
the
O
ring
b
Do
not
use
a
screwdriver
to
pry
shaft
seal
from
shaft
as
damage
to
shaft
may
result
AC809
Fig
A
C
63
Removing
s
wft
eal
INSTALLATION
1
Clean
shaft
and
seal
cavity
with
clean
lint
free
cloth
2
Dip
seal
gland
in
clean
refrigerant
oil
AC
36
3
Push
seal
assembly
except
carbon
ring
over
end
of
shaft
with
carbon
ring
retainer
facing
out
4
Move
seal
assembly
into
position
on
shaft
1
I
Fig
AC
64
Inserting
wft
al
ass
mbly
5
Place
carbon
ring
in
ring
retainer
so
lapped
surface
is
facing
outward
Note
The
indentions
in
outside
edge
of
carbon
ring
must
engage
driving
lugs
and
be
firmly
seated
in
re
tainer
6
Install
new
D
ring
in
groove
of
seal
plate
Note
Use
refrigeration
oil
to
make
it
adhere
to
surface
7
Space
seal
plate
with
equal
clear
ance
around
shaft
and
insert
cap
screws
8
Tighten
these
screws
evenly
Tightening
torque
Seal
plate
securing
cap
screws
0
7
to
1
0
kg
m
5
to
7
ft
Ib
AC811
Fig
AC
65
8p
cing
01
plate
and
tightening
cap
screws
9
Install
clutch
Refer
to
Com
pressor
Clutch
Installation