ECU DATSUN PICK-UP 1977 Repair Manual
[x] Cancel search | Manufacturer: DATSUN, Model Year: 1977, Model line: PICK-UP, Model: DATSUN PICK-UP 1977Pages: 537, PDF Size: 35.48 MB
Page 361 of 537
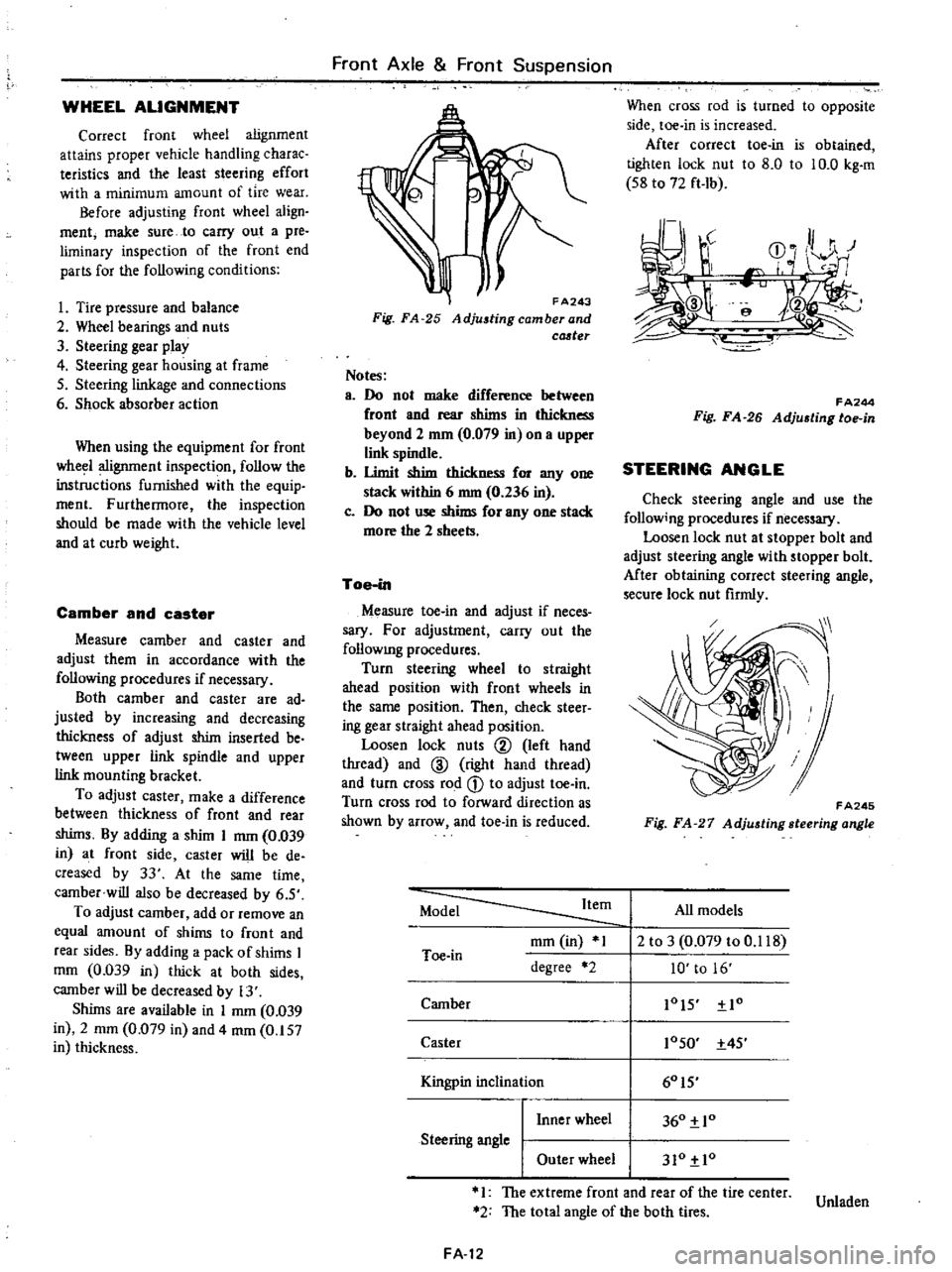
WHEEL
ALIGNMENT
Correct
front
wheel
alignment
attains
proper
vehicle
handling
charac
teristics
and
the
least
steering
effort
with
a
minimum
amount
of
tire
wear
Before
adjusting
front
wheel
align
ment
make
sure
to
carry
out
a
pre
liminary
inspection
of
the
front
end
parts
for
the
following
conditions
1
Tire
pressure
and
balance
2
Wheel
bearings
and
nuts
3
Steering
gear
play
4
Steering
gear
housing
at
frame
S
Steering
linkage
and
connections
6
Shock
absorber
action
When
using
the
equipment
for
front
wheel
alignment
inspection
follow
the
inst
c
tions
furnished
with
the
equip
ment
Furthennore
the
inspection
should
be
made
with
the
vehicle
level
and
at
curb
weight
Camber
and
caster
Measure
camber
and
caster
and
adjust
them
in
accordance
with
the
following
procedures
if
necessary
Both
camber
and
caster
are
ad
justed
by
increasing
and
decreasing
thickness
of
adjust
shim
inserted
be
tween
upper
link
spindle
and
upper
link
mounting
bracket
To
adjust
caster
make
a
difference
between
thickness
of
front
and
rear
shims
By
adding
a
shim
I
mm
0
039
in
at
front
side
caster
will
be
de
creased
by
33
At
the
same
time
camber
will
also
be
decreased
by
6
S
To
adjust
camber
add
or
remove
an
equal
amount
of
shims
to
front
and
rear
sides
By
adding
a
pack
of
shims
I
mOl
0
039
in
thick
at
both
sides
camber
will
be
decreased
by
13
Shims
are
available
in
I
mm
0
039
in
2
mOl
0
079
in
and
4
mOl
0
157
in
thickness
Front
Axle
Front
Suspension
FA243
Fig
FA
25
Adjustingcamberand
cCJ
ter
Notes
a
Do
not
make
difference
between
front
and
rear
shims
in
thickness
beyond
2
mm
0
079
in
on
a
upper
link
spindle
b
Umit
shim
thickness
for
anyone
stack
within
6
nun
0
236
in
c
Do
not
use
shims
for
anyone
stack
more
the
2
sheets
Toe
in
Measure
toe
in
and
adjust
if
neces
sary
For
adjustment
carry
out
the
follOWIng
procedures
Turn
steering
wheel
to
straight
ahead
position
with
front
wheels
in
the
same
position
Then
check
steer
ing
gear
straight
ahead
position
Loosen
lock
nuts
@
left
hand
thread
and
ID
right
hand
thread
and
turn
cross
rod
CD
to
adjust
toe
in
Turn
cross
rod
to
forward
direction
as
shown
by
arrow
and
toe
in
is
reduced
When
cross
rod
is
turned
to
opposite
side
toe
in
is
increased
After
correct
toe
in
is
obtained
tighten
lock
nut
to
8
0
to
10
0
kg
m
S8
to
72
ft
Ib
r
J
r
CD
0
HI
r
I
e
f
FA244
Fig
FA
26
Adju6ting
toe
in
STEERING
ANGLE
Check
steering
angle
and
use
the
follow
ng
procedures
if
necessary
Loosen
lock
nut
at
stopper
bolt
and
adjust
steering
angle
with
stopper
bolt
Mter
obtaining
correct
steering
angle
secure
lock
nut
firmly
FA245
Fig
FA
27
Adjusting
steering
angle
Model
Item
All
models
mOl
in
1
2
to
3
0
079
to
0
118
Toe
in
degree
2
10
to
16
Camber
lOIS
Io
Caster
10SO
4S
I
60IS
Kingpin
inc
inal10n
I
Inner
wheel
360
10
Steering
angle
I
Outer
wheel
310
10
1
The
extreme
front
and
rear
of
the
tire
center
Unladen
2
The
total
angle
of
the
both
tires
FA
12
Page 371 of 537
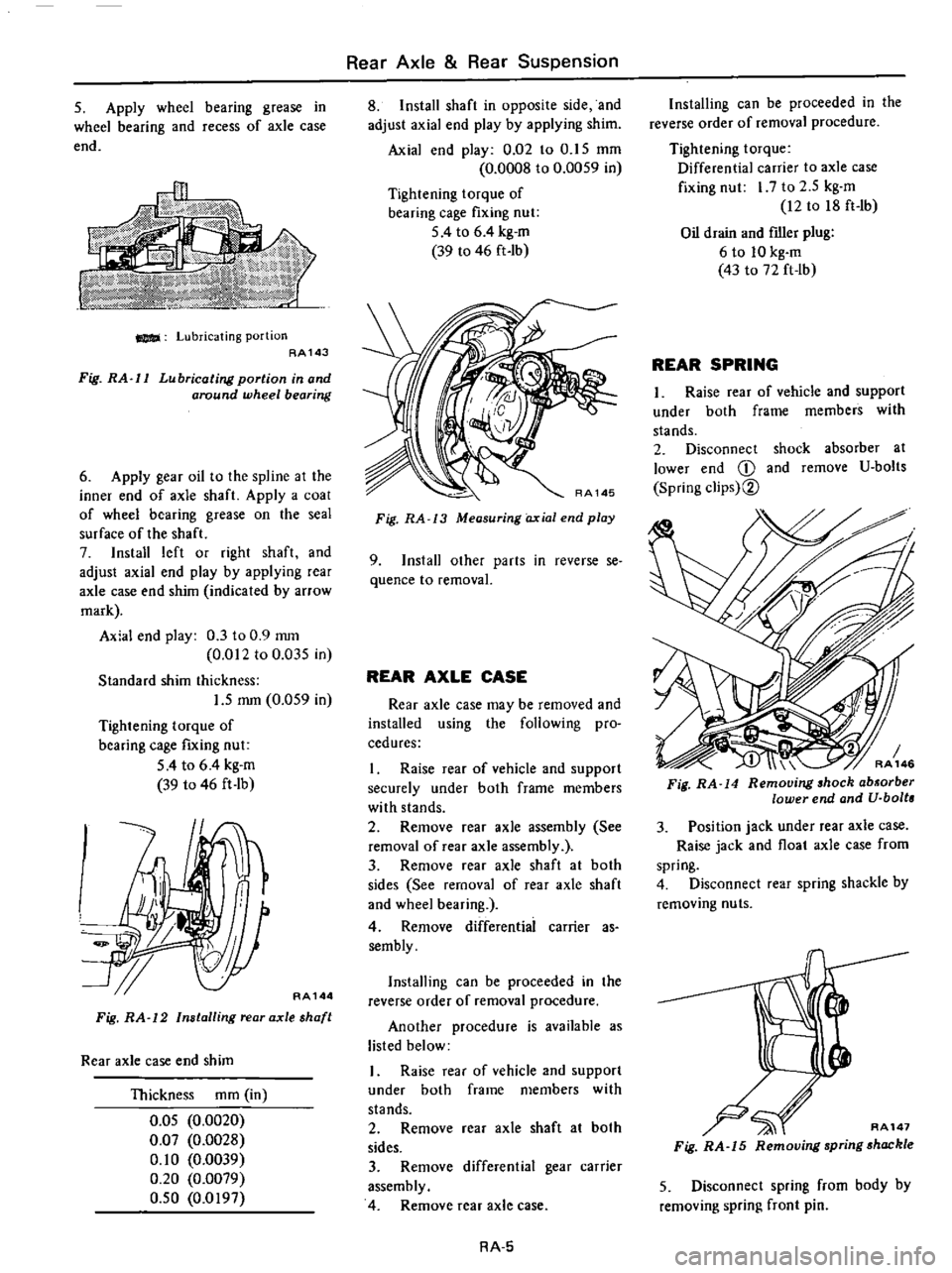
S
Apply
wheel
bearing
grease
in
wheel
bearing
and
recess
of
axle
case
end
Lubricating
portion
AA143
Fig
RA
l1
Lubricating
portion
in
and
around
wheel
bearing
6
Apply
gear
oil
to
the
spline
at
the
inner
end
of
axle
shaft
Apply
a
coal
of
wheel
bearing
grease
on
the
seal
surface
of
the
shaft
7
Install
left
or
right
shaft
and
adjust
axial
end
play
by
applying
rear
axle
case
end
shim
indicated
by
arrow
mark
Axial
end
play
0
3
to
0
9
mOl
0
012
to
0
035
in
Standard
shim
thickness
1
5
mm
0
059
in
Tightening
torque
of
bearing
cage
fIXing
nut
54
to
6
4
kg
m
39
to
46
ft
lb
w
AA144
Fig
RA
12
Installing
rear
axle
shaft
Rear
axle
case
end
shim
Thickness
mOl
in
O
OS
0
0020
0
07
0
0028
0
10
0
0039
0
20
0
0079
O
SO
0
0197
Rear
Axle
Rear
Suspension
8
Install
shaft
in
opposite
side
and
adjust
axial
end
play
by
applying
shim
Axial
end
play
0
02
to
O
IS
mOl
0
0008
to
0
0059
in
Tightening
torque
of
bearing
cage
fixing
nut
5
4
to
6
4
kg
m
39
to
46
ft
Ib
Fig
RA
13
Measuring
axial
end
play
9
Install
other
parts
in
reverse
se
quence
to
removal
REAR
AXLE
CASE
Rear
axle
case
may
be
removed
and
installed
using
the
following
pro
cedures
I
Raise
rear
of
vehicle
and
support
securely
under
both
frame
members
with
stands
2
Remove
rear
axle
assembly
See
removal
of
rear
axle
assembly
3
Remove
rear
axle
shaft
at
both
sides
See
removal
of
rear
axle
shaft
and
wheel
bearing
4
Remove
differentiai
carrier
as
sembly
Installing
can
be
proceeded
in
the
reverse
order
of
removal
procedure
Another
procedure
is
available
as
listed
below
I
Raise
rear
of
vehicle
and
support
under
both
frame
members
with
stands
2
Remove
ear
axle
shaft
at
both
sides
3
Remove
differential
gear
carrier
assembly
4
Remove
rear
axle
case
RA
5
Installing
can
be
proceeded
in
the
reverse
order
of
removal
procedure
Tightening
torque
Differential
carrier
to
axle
case
fixing
nut
I
7
to
2
5
kg
m
12
to
18
ft
Ib
Oil
drain
and
fIller
plug
6
to
10
kg
m
43
to
72
ft
lb
REAR
SPRING
1
Raise
rear
of
vehicle
and
support
under
both
frame
members
with
stands
2
Disconnect
shock
absorber
at
lower
end
CD
and
remove
U
bolts
Spring
clips
2
3
Position
jack
under
rear
axle
case
Raise
jack
and
float
axle
case
from
spring
4
Disconnect
rear
spring
shackle
by
removing
nuts
AA147
Fig
RA
15
Removing
spring
shackle
5
Disconnect
spring
from
body
by
removing
spring
front
pin
Page 374 of 537
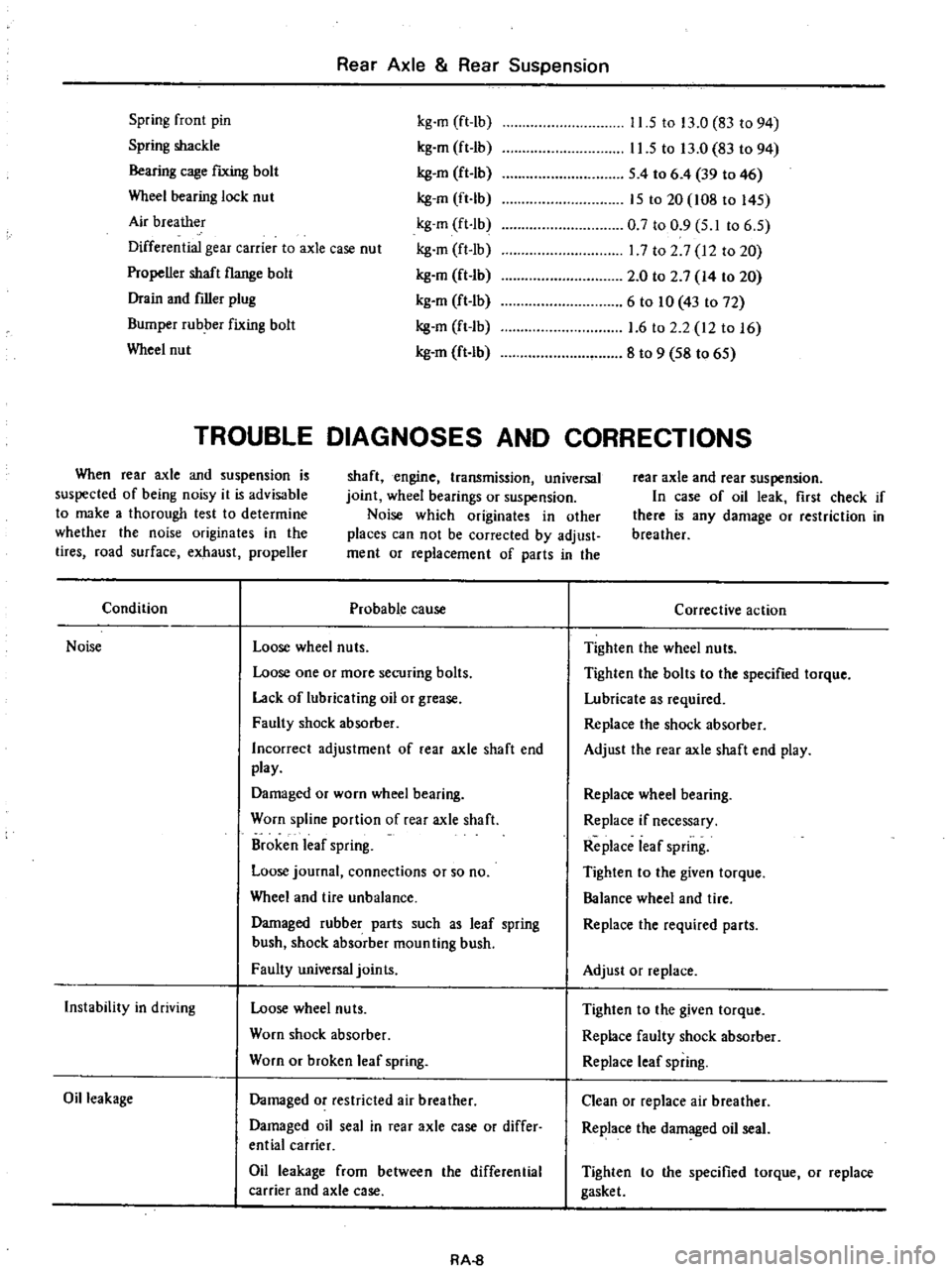
Rear
Axle
Rear
Suspension
Spring
front
pin
Spring
shackle
Bearing
cage
fIXing
bolt
Wheel
bearing
lock
nut
Air
breather
Differential
gear
carrier
to
axle
case
nut
Propeller
shaft
flange
bolt
Drain
and
filler
plug
Bumper
rubber
fixing
bolt
Wheel
nut
kg
m
ft
lb
kg
m
ft
Ib
kg
en
ft
lb
kg
m
ft
Ib
kg
m
ft
Ib
kg
m
ft
Ib
kg
en
ft
Ib
kg
m
ft
Ib
kg
m
ft
Ib
kg
m
ft
lb
11
5
to
13
0
83
to
94
11
5
to
13
0
83
to
94
S
4
to
6
4
39
to
46
IS
to
20
108
to
l4S
0
7
to
0
9
S
I
to
6
S
17
to
2
7
12
to
20
2
0
to
2
7
14
to
20
6
to
10
43
to
72
1
6
to
2
2
12
to
16
8
to
9
S8
to
6S
TROUBLE
DIAGNOSES
AND
CORRECTIONS
When
rear
axle
and
suspension
is
suspected
of
being
noisy
it
is
advisable
to
make
a
thorough
test
to
determine
whether
the
noise
originates
in
the
tires
road
surface
exhaust
propeller
shaft
engine
transmission
universal
joint
wheel
bearings
or
suspension
Noise
which
originates
in
other
places
can
not
be
corrected
by
adjust
ment
or
replacement
of
parts
in
the
rear
axle
and
rear
suspension
In
case
of
oil
leak
first
check
if
there
is
any
damage
or
restriction
in
breather
Condition
Probable
cause
Noise
Loose
wheel
nuts
Loose
one
or
more
securing
bolts
Lack
of
lubricating
oil
or
grease
Faulty
shock
absorber
Incorrect
adjustment
of
rear
axle
shaft
end
play
Damaged
or
worn
wheel
bearing
Worn
spline
portion
of
rear
axle
shaft
Broken
leaf
spring
Loose
journal
connections
or
so
no
Wheel
and
tire
unbalance
Damaged
rubber
parts
such
as
leaf
spring
bush
shock
absorber
moun
ting
bush
Faulty
universal
joints
Instability
in
driving
Loose
wheel
nuts
Worn
shock
absorber
Worn
or
broken
leaf
spring
Oil
leakage
Damaged
or
restricted
air
breather
Damaged
oil
seal
in
rear
axle
case
or
differ
ential
carrier
Oil
leakage
from
between
the
differential
carrier
and
axle
case
RA
8
Corrective
action
Tighten
the
wheel
nuts
Tighten
the
bolts
to
the
specified
torque
Lubricate
as
required
Replace
the
shock
absorber
Adjust
the
rear
axle
shaft
end
play
Replace
wheel
bearing
Replace
if
necessary
Replace
leaf
spring
Tighten
to
the
given
torque
Balance
wheel
and
tire
Replace
the
required
parts
Adjust
or
replace
Tighten
to
the
given
torque
Replace
faulty
shock
absorber
Replace
leaf
spring
Clean
or
replace
air
breather
Replace
the
damaged
oil
seal
Tighten
to
the
specified
torque
or
replace
gasket
Page 377 of 537
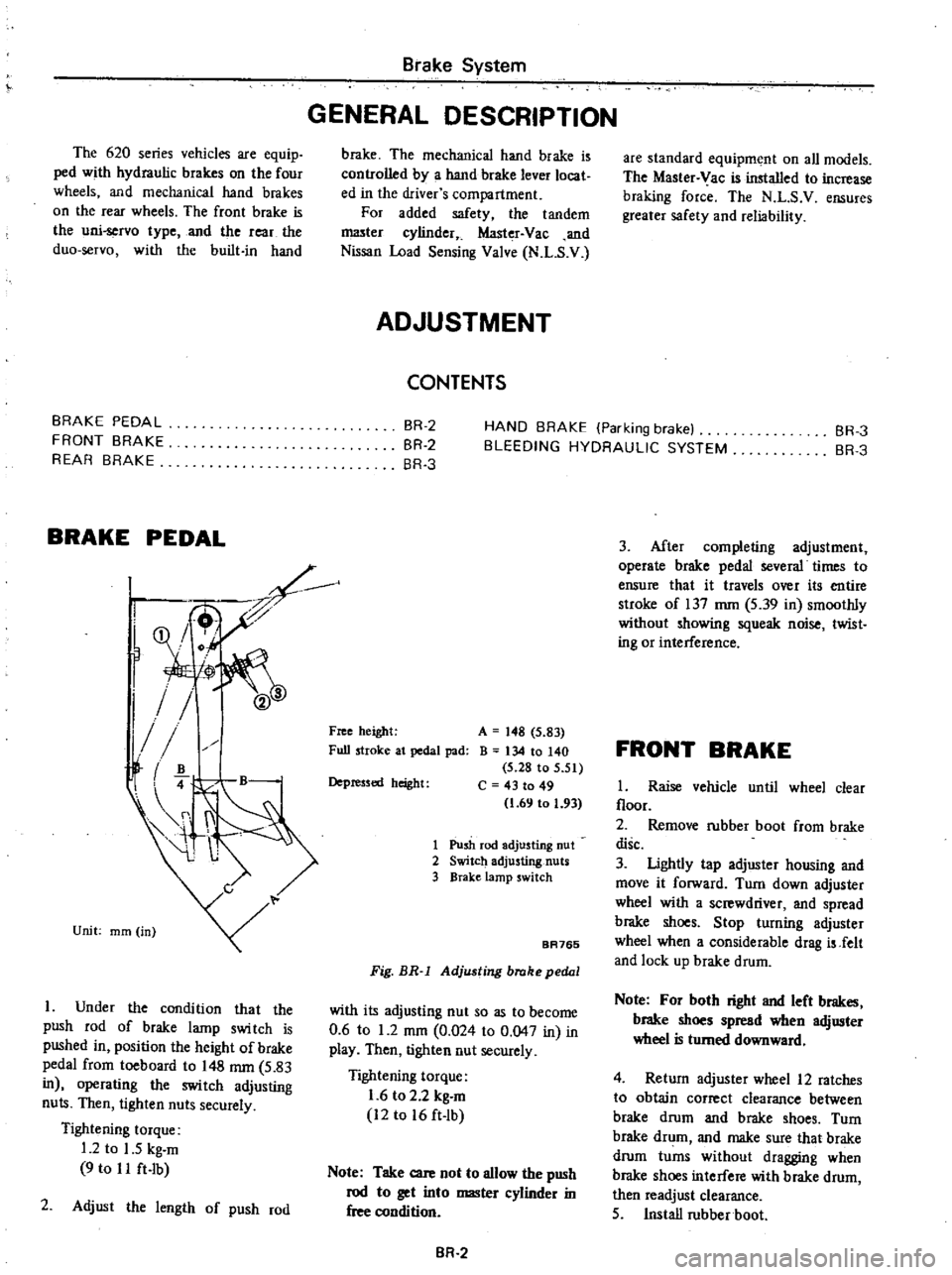
The
620
series
vehicles
are
equip
ped
with
hydraulic
brakes
on
the
four
wheels
and
mechanical
hand
brakes
on
the
rear
wheels
The
front
brake
is
the
uni
servo
type
and
the
rear
the
duo
servo
with
the
built
in
hand
BRAKE
PEDAL
FRONT
BRAKE
REAR
BRAKE
BRAKE
PEDAL
Qi
f
l
II
t
Unit
mm
in
I
Under
the
condition
that
the
push
rod
of
brake
lamp
swi
tch
is
pushed
in
position
the
height
of
brake
pedal
from
toeboard
to
148
mm
5
83
in
operating
the
switch
adjusting
nuts
Then
tighten
nuts
securely
Tightening
torque
1
2
to
1
5
kg
m
9
to
I
I
ft
Ib
2
Adjust
the
length
of
push
rod
Brake
System
GENERAL
DESCRIPTION
brake
The
mechanical
hand
brake
is
controlled
by
a
hand
brake
lever
locat
ed
in
the
driver
s
compartment
For
added
safety
the
tandem
I
1lI3ter
cylinder
Master
Vac
and
Nissan
Load
Sensing
Valve
N
L
S
V
ADJUSTMENT
CONTENTS
are
standard
equipment
on
all
models
The
Master
Vac
is
installed
to
increase
braking
force
The
N
L
S
V
ensures
greater
safety
and
reliability
BR
2
BR
2
BR
3
HAND
BRAKE
Parking
brake
BLEEDING
HYDRAULIC
SYSTEM
BR
3
BR
3
Free
height
Full
stroke
at
pedal
pad
A
148
5
83
B
134
10
140
5
28
to
5
51
C
43
to
49
1
69
to
1
93
Depressed
height
1
Push
rod
adjusting
nut
2
Switch
adjusting
nuts
3
BraKe
lamp
switch
BA765
Fig
BR
l
Adjusting
brake
pedal
with
its
adjusting
nut
so
as
to
become
0
6
to
1
2
mOl
0
024
to
0
047
in
in
play
Then
tigh1en
nut
securely
Tightening
torque
1
6
to
2
2
kg
m
12
to
16
ft
lb
Note
Take
care
not
to
allow
the
push
rod
to
get
into
master
cylinder
in
free
condition
BR
2
3
After
completing
adjustment
operate
brake
pedal
several
times
to
ensure
that
it
travels
over
its
entire
stroke
of
137
mm
5
39
in
smoothly
without
showing
squeak
noise
twist
ing
or
interference
FRONT
BRAKE
1
Raise
vehicle
until
wheel
clear
floor
2
Remove
rubber
boot
from
brake
disc
3
Ughtly
tap
adjuster
housing
and
move
it
forward
Turn
down
adjuster
wheel
with
a
screwdriver
and
spread
brake
shoes
Stop
turning
adjuster
wheel
when
a
considerable
drag
is
Jelt
and
lock
up
brake
drum
Note
For
both
right
and
left
brakes
brake
shoes
spread
when
adjuster
wheel
is
turned
downward
4
Return
adjuster
wheel
12
ratches
to
obtain
correct
clearance
between
brake
drum
and
brake
shoes
Turn
brake
drum
and
make
sure
that
brake
drum
turns
without
dragging
when
brake
shoes
interfere
with
brake
drum
then
readjust
clearance
5
Install
rubber
boot
Page 378 of 537
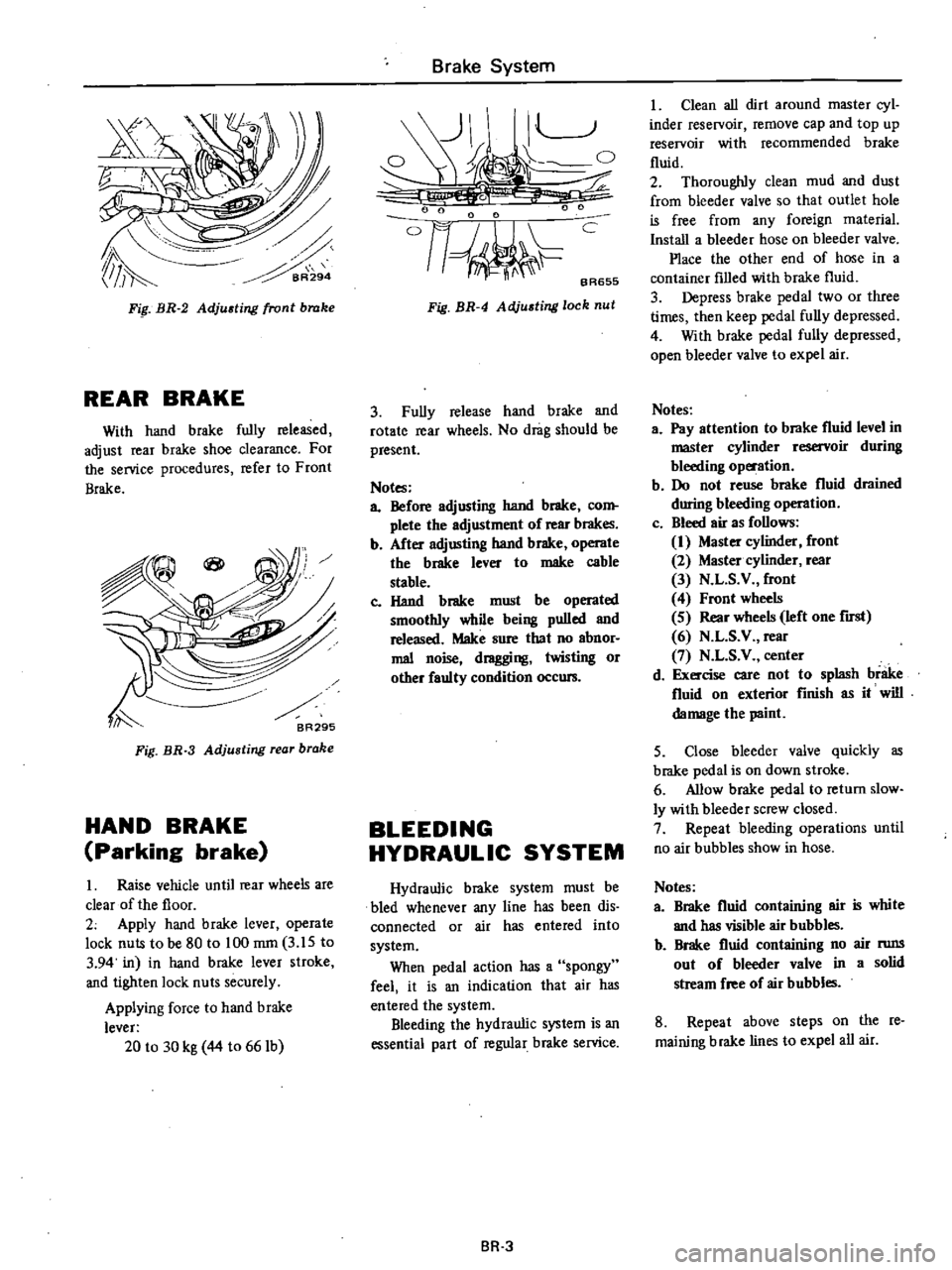
Fip
BR
2
Adjusting
front
brake
REAR
BRAKE
With
hand
brake
fully
released
adjust
rear
brake
shoe
clearance
For
the
service
procedures
refer
to
Front
Brake
Fig
BR
3
Adjusting
rear
brake
HAND
BRAKE
Parking
brake
I
Raise
vehicle
until
rear
wheels
are
clear
of
the
floor
2
Apply
hand
brake
lever
operate
lock
nuts
to
be
80
to
100
mrn
3
lS
to
3
94
in
in
hand
brake
lever
stroke
and
tighten
lock
nuts
securely
Applying
force
to
hand
brake
lever
20
to
30
kg
44
to
661b
Brake
System
1
t
0
t
6
0
I
o
nJ
c
BA655
Fig
BR
4
Adjusting
lock
nut
3
Fully
release
hand
brake
and
rotate
rear
wheels
No
drag
should
be
present
Notes
a
Before
adjusting
hand
brake
com
plete
the
adjustment
of
rear
brakes
b
After
adjusting
hand
brake
operate
the
brake
lever
to
make
cable
stable
c
Hand
brake
must
be
operated
smoothly
while
being
pulled
and
released
Make
sure
that
no
abnor
mal
noise
dragging
twisting
or
other
faulty
condition
occurs
BLEEDING
HYDRAUL
Ie
SYSTEM
Hydraulic
brake
system
must
be
bled
whenever
any
line
has
been
dis
connected
or
air
has
entered
into
system
When
pedal
action
has
a
spongy
feel
it
is
an
indication
that
air
has
entered
the
system
Bleeding
the
hydraulic
system
is
an
essential
part
of
regular
brake
service
BR
3
I
Clean
all
dirt
around
master
cyl
inder
reservoir
I
remove
cap
and
top
up
reservoir
with
recommended
brake
fluid
2
Thoroughly
clean
mud
and
dust
from
bleeder
valve
so
that
outlet
hole
is
free
from
any
foreign
material
Install
a
bleeder
hose
on
bleeder
valve
Place
the
other
end
of
hose
in
a
container
filled
with
brake
fluid
3
Depress
brake
pedal
two
or
three
times
then
keep
pedal
fully
depressed
4
With
brake
pedal
fully
depressed
open
bleeder
valve
to
expel
air
Notes
a
Pay
attention
to
brake
fluid
level
in
master
cylinder
reservoir
during
bleeding
operation
b
Do
not
reuse
brake
fluid
drained
during
bleeding
operation
c
Bleed
air
as
follows
1
Master
cylinder
front
2
Master
cylinder
rear
3
N
L
S
V
front
4
Front
wheels
S
Rear
wheels
left
one
first
6
N
L
S
V
rear
7
N
L
S
V
center
d
Exercise
care
not
to
splash
brake
fluid
on
exterior
finish
as
it
will
damage
the
paint
5
Close
bleeder
valve
quickly
as
brake
pedal
is
on
down
stroke
6
Allow
brake
pedal
to
return
slow
ly
with
bleeder
screw
closed
7
Repeat
bleeding
operations
until
no
air
bubbles
show
in
hose
Notes
a
Brake
fluid
containing
air
is
white
and
has
visible
air
bubbles
b
Brake
fluid
containing
no
air
nms
out
of
bleeder
valve
in
a
solid
stream
free
of
air
bubbles
8
Repeat
above
steps
on
the
re
maining
brake
lines
to
expel
all
air
Page 380 of 537
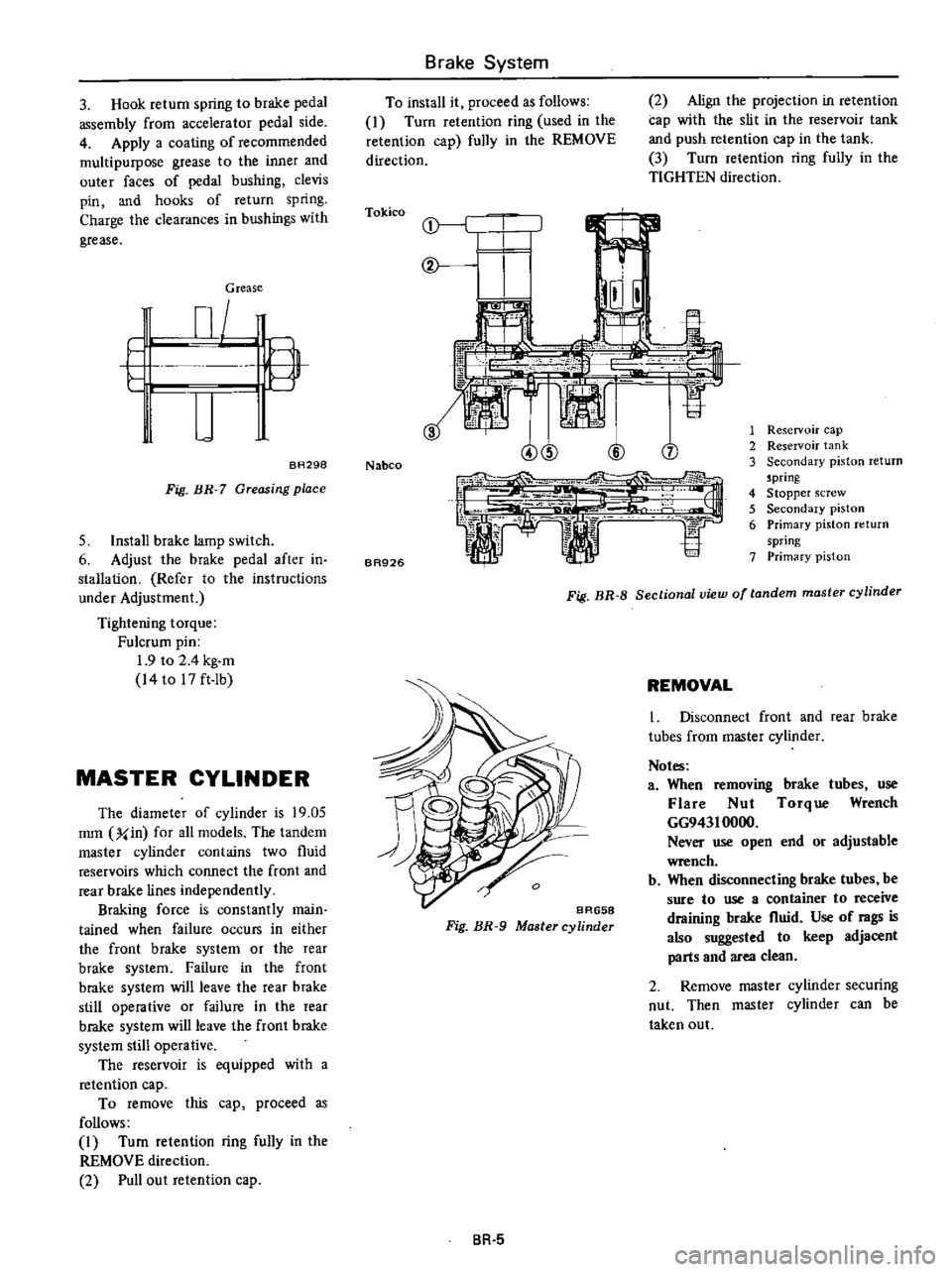
3
Hook
return
spring
to
brake
pedal
assembly
from
accelerator
pedal
side
4
Apply
a
coating
of
recommended
multipurpose
grease
to
the
inner
and
outer
faces
of
pedal
bushing
clevis
pin
and
hooks
of
return
spring
Charge
the
clearances
in
bushings
with
grease
Grease
m
n
L
g
U
BR298
Fig
BH
7
Greasing
place
5
lnstali
brake
lamp
switch
6
Adjust
the
brake
pedal
after
in
stallation
Refer
to
the
instructions
under
Adjustment
Tightening
torque
Fulcrum
pin
1
9
to
2
4
kg
m
14to
17ft
ib
MASTER
CYLINDER
The
diameter
of
cylinder
is
19
05
mm
y
in
for
all
models
The
tandem
master
cylinder
contains
two
fluid
reservoirs
which
connect
the
front
and
rear
brake
lines
independently
Braking
force
is
constantly
main
tained
when
failure
occurs
in
either
the
front
brake
system
or
the
rear
brake
system
Failure
in
the
front
brake
system
will
leave
the
rear
brake
still
operative
or
failure
in
the
rear
brake
system
will
leave
the
front
brake
system
still
operative
The
reservoir
is
eq
ui
pped
with
a
retention
cap
To
remove
this
cap
proceed
as
follows
I
Tum
retention
ring
fully
in
the
REMOVE
direction
2
Pull
out
retention
cap
Brake
System
To
install
it
proceed
as
follows
I
Turn
retention
ring
used
in
the
retention
cap
fully
in
the
REMOVE
direction
Tokico
@
1tr
I
I
I
j
1
Nabco
BR926
2
Align
the
projection
in
retention
cap
with
the
slit
in
the
reservoir
tank
and
push
retention
cap
in
the
tank
3
Turn
retention
ring
fully
in
the
TIGHTEN
direction
00
CD
1
Reservoir
cap
2
Reservoir
tank
3
Secondary
piston
return
5pring
4
Stopper
screw
5
Secondary
piston
6
Primary
piston
return
spring
7
Primary
piston
Fig
BR
B
Sectional
view
of
tandem
master
cylinder
o
BR658
Fig
BR
9
Master
cylinder
BR
5
REMOVAL
1
Disconnect
front
and
rear
brake
tubes
from
master
cylinder
Notes
a
When
removing
brake
tubes
use
Flare
Nut
Torque
Wrench
GG94310000
Never
use
open
end
or
adjustable
wrench
b
When
disconnecting
brake
tubes
be
sure
to
use
a
container
to
receive
draining
brake
flnid
Use
of
rags
is
also
suggested
to
keep
adjacent
parts
and
area
clean
2
Remove
master
cylinder
securing
nut
Then
master
cylinder
can
be
taken
out
Page 383 of 537
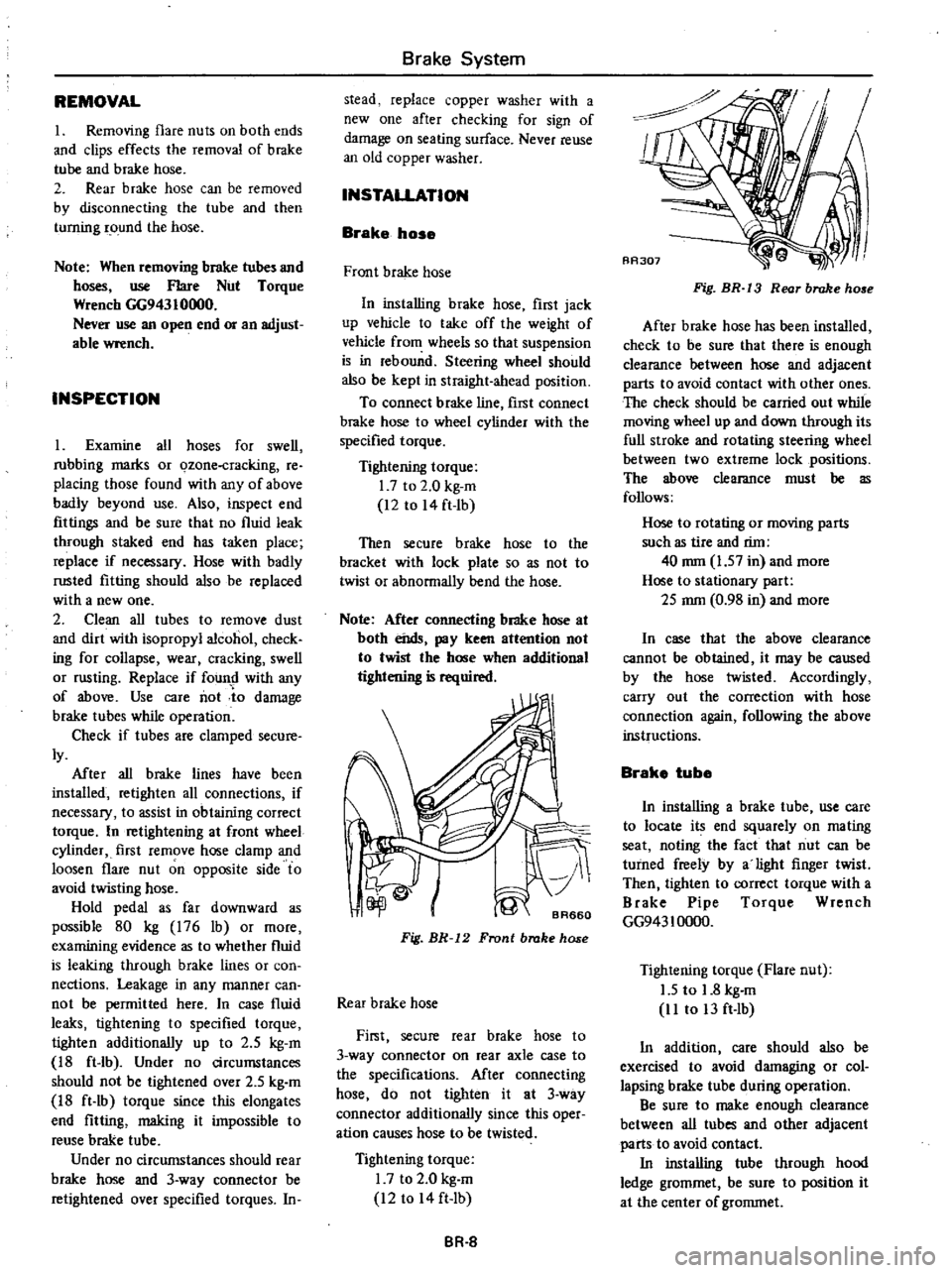
REMOVAL
1
Removing
flare
nuts
on
both
ends
and
clips
effects
the
removal
of
brake
tube
and
brake
hose
2
Rear
brake
hose
can
be
removed
by
disconnecting
the
tube
and
then
turning
round
the
hose
Note
When
removing
brake
tubes
and
hoses
use
Flare
Nut
Torque
Wrench
GG943IOOOO
Never
use
an
OpeD
end
or
an
adjust
able
wrench
INSPECTION
1
Examine
all
hoses
for
swell
rubbing
marks
or
ozone
cracking
re
placing
those
found
with
any
of
above
badly
beyond
use
Also
inspect
end
fittings
and
be
sure
that
no
fluid
leak
through
staked
end
has
taken
place
replace
if
necessary
Hose
with
badly
rusted
fitting
should
also
be
replaced
with
a
new
one
2
Clean
all
tubes
to
remove
dust
and
dirt
with
isopropyl
alcohol
check
ing
for
collapse
wear
cracking
swell
or
rusting
Replace
if
foun
d
with
any
of
wove
Use
care
not
to
damage
brake
tubes
while
operation
Check
if
tubes
are
clamped
secure
ly
Mter
all
brake
lines
have
been
installed
retighten
aU
connections
if
necessary
to
assist
in
obtaining
correct
torque
In
retightening
at
front
wheel
cylinder
first
remove
hose
clamp
and
loosen
flare
nut
on
opposite
side
to
avoid
twisting
hose
Hold
pedal
as
far
downward
as
possible
80
kg
176
lb
or
more
examining
evidence
as
to
whether
fluid
is
leaking
through
brake
lines
or
con
nections
Leakage
in
any
manner
can
not
be
permitted
here
In
case
fluid
leaks
tightening
to
specified
torque
tighten
additionally
up
to
2
5
kg
m
J
8
ft
lb
Under
no
circumstances
should
not
be
tightened
over
2
5
kg
m
18
ft
Ib
torque
since
this
elongates
end
fitting
making
it
impossible
to
reuse
brake
tube
Under
no
circumstances
should
rear
brake
hose
and
3
way
connector
be
retightened
over
specified
torques
In
Brake
System
stead
replace
copper
washer
with
a
new
one
after
checking
for
sign
of
damage
on
seating
surface
Never
reuse
an
old
copper
washer
INSTALLATION
Brake
hose
Front
brake
hose
In
installing
brake
hose
first
jack
up
vehicle
to
take
off
the
weight
of
vehicle
from
wheels
so
that
suspension
is
in
rebound
Steering
wheel
should
also
be
kept
in
straight
ahead
position
To
connect
brake
line
first
connect
brake
hose
to
wheel
cylinder
with
the
specified
torque
Tightening
torque
1
7
to
2
0
kg
m
12
to
14
ft
Ib
Then
secure
brake
hose
to
the
bracket
with
lock
plate
so
as
not
to
twist
or
abnormally
bend
the
hose
Note
After
connecting
brake
hose
at
both
eiuIs
pay
keen
attention
not
to
twist
the
hose
when
additional
tightening
is
required
Fig
BR
12
Front
brake
hose
Rear
brake
hose
First
secure
rear
brake
hose
to
3
way
connector
on
rear
axle
case
to
the
specifications
Mter
connecting
hose
do
not
tighten
it
at
3
way
connector
additionally
since
this
oper
ation
causes
hose
to
be
twisted
Tightening
torque
I
7
to
2
0
kg
m
12
to
14
ft
Ib
BR
8
Fig
BR
13
Rear
brake
ho
e
After
brake
hose
has
been
installed
check
to
be
sure
that
there
is
enough
clearance
between
hose
and
adjacent
parts
to
avoid
contact
with
other
ones
The
check
should
be
carried
out
while
moving
wheel
up
and
down
through
its
full
stroke
and
rotating
steering
wheel
between
two
extreme
lock
positions
The
wow
clearance
must
be
as
follows
Hose
to
rotating
or
mOving
parts
such
as
tire
and
rim
40
mm
1
57
in
and
more
Hose
to
stationary
part
2S
mm
0
98
in
and
more
In
case
that
the
above
clearance
cannot
be
obtained
it
may
be
caused
by
the
hose
twisted
Accordingly
carry
out
the
correction
with
hose
connection
again
following
the
above
instructions
Brake
tube
In
installing
a
brake
tube
use
care
to
locate
its
end
squarely
on
mating
seat
noting
the
fact
that
nut
can
be
turned
freely
by
a
light
finger
twist
Then
tighten
to
correct
torque
with
a
Brake
Pipe
Torque
Wrench
GG943
10000
Tightening
torque
Flare
nut
1
5
to
1
8
kg
m
11
to
13
ft
Ib
In
addition
care
should
also
be
exercised
to
avoid
damaging
or
col
lapsing
brake
tube
during
operation
Be
sure
to
make
enough
clearance
between
all
tubes
and
other
adjacent
parts
to
avoid
contact
In
installing
tube
through
hood
ledge
grommet
be
sure
to
position
it
at
the
center
of
grommet
Page 384 of 537
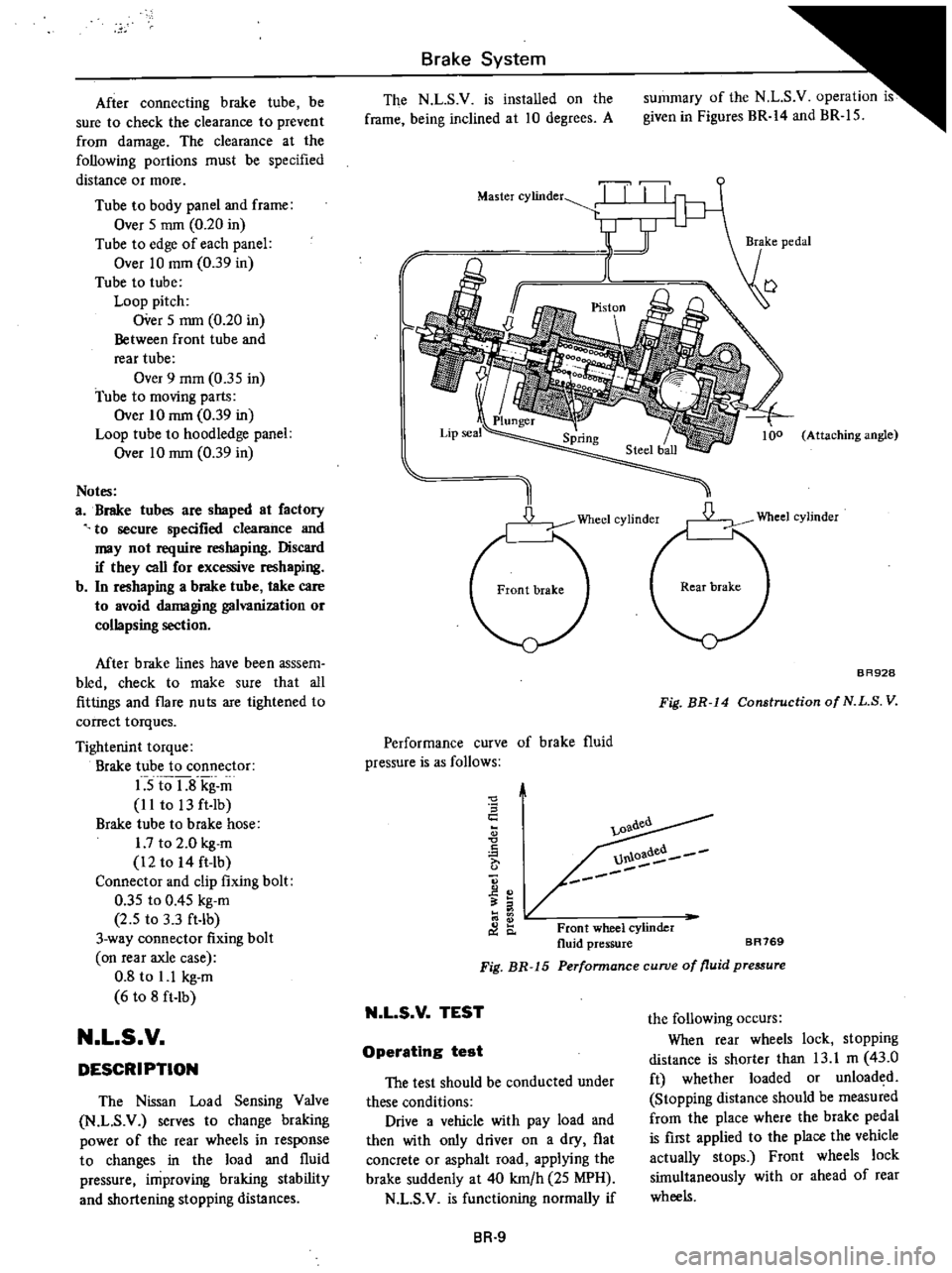
After
connecting
brake
tube
be
sure
to
check
the
clearance
to
prevent
from
damage
The
clearance
at
the
following
portions
must
be
specified
distance
or
more
Tube
to
body
panel
and
frame
Over
5
mm
0
20
in
Tube
to
edge
of
each
panel
Over
10
mm
0
39
in
Tube
to
tube
Loop
pitch
OVer
5
mm
0
20
in
Between
front
tube
and
rear
tube
Over
9
mOl
0
35
in
Tube
to
moving
parts
Over
10
mm
0
39
in
Loop
tube
to
hood
ledge
panel
Over
10
mm
0
39
in
Notes
a
Brake
tubes
are
shaped
at
factory
to
secure
specified
clearance
and
may
not
require
reshaping
Discard
if
they
call
for
excessive
reshaping
b
In
reshaping
a
brake
tube
take
care
to
avoid
damaging
galvanization
or
collapsing
section
Mter
brake
lines
have
been
asssem
bled
check
to
make
sure
that
all
fittings
and
flare
nu
Is
ale
lightened
to
correct
torques
Tightenint
torque
Brake
tube
to
connector
I
Ston
kg
m
II
to
13
ft
Ib
Brake
tube
to
brake
hose
1
7
to
2
0
kg
m
12
to
14
ft
lb
Connector
and
clip
fixing
bolt
O
3S
to
O
4S
kg
m
2
5
to
3
3
ft
lb
3
way
connector
fixing
bolt
on
rear
axle
case
0
8
to
1
1
kg
m
6
to
8
ft
lb
N
L
S
V
DESCRIPTION
The
Nissan
Load
Sensing
Valve
N
L
S
V
serves
to
change
braking
power
of
the
rear
wheels
in
response
to
changes
in
the
load
and
fluid
pressure
improving
braking
stability
and
shortening
stopping
distances
Brake
System
The
N
L
S
V
is
installed
on
the
frame
being
inclined
at
10
degrees
A
summary
of
the
N
L
S
v
operation
is
given
in
Figures
BR
14
and
BR
15
r
Master
cylinder
TI
II
I
y
1
J
I
l
Attaching
angle
D
Wheel
cylinder
BR928
Fig
BR
14
Construction
of
N
L
S
V
Performance
curve
of
brake
fluid
pressure
is
as
follows
0
S
c
A
0
C
o
l
0
oadea
U1U
Front
wheel
cylinder
fluid
pressure
BR769
Perfonnance
curve
of
fluid
pressure
Fig
BR
15
N
L
S
V
TEST
the
following
occurs
When
rear
wheels
lock
stopping
distance
is
shorter
than
13
1
m
43
0
ft
whether
loaded
or
unloaded
Stopping
distance
should
be
measured
from
the
place
where
the
brake
pedal
is
first
applied
to
the
place
the
vehicle
actually
stops
Front
wheels
lock
simultaneously
with
or
ahead
of
rear
wheels
Operating
test
The
test
should
be
conducted
under
these
conditions
Drive
a
vehicle
with
pay
load
and
then
with
only
driver
on
a
dry
flat
concrete
or
asphalt
road
applying
the
brake
suddenly
at
40
km
h
25
MPH
N
L
S
V
is
functioning
normally
if
BR
9
Page 385 of 537
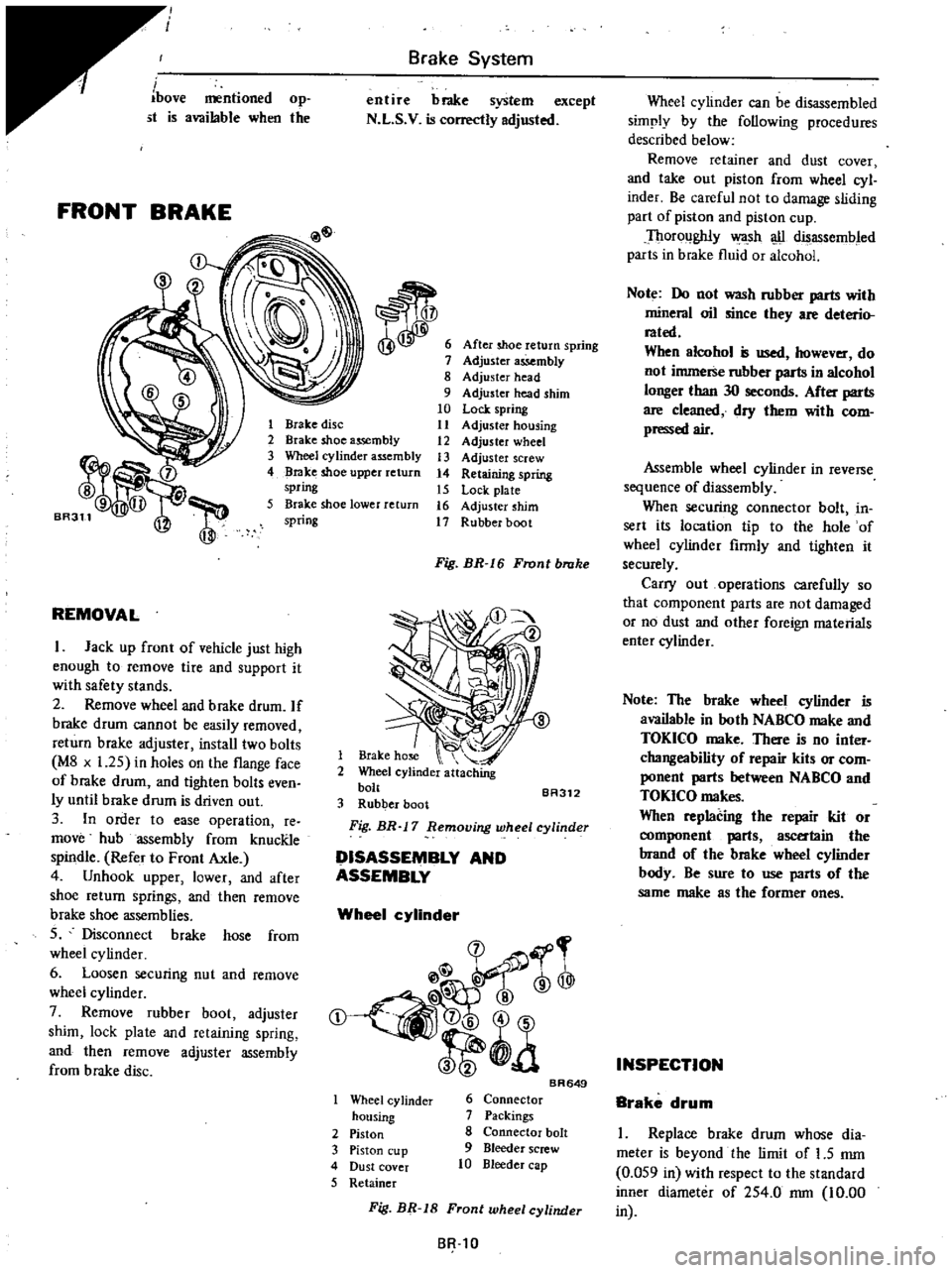
Ibove
mentioned
st
is
available
when
op
the
FRONT
BRAKE
Brake
System
entire
brake
system
except
N
L
S
V
is
correctly
adjusted
After
shoe
return
spring
Adjuster
assembly
8
Adjuster
head
9
Adjuster
head
shim
10
Lock
spring
11
Adjuster
housing
12
Adjuster
wheel
13
Adjuster
screw
14
Retaining
spring
15
Lock
plate
16
Adjuster
shim
17
Rubber
boot
1
Brake
disc
2
Brake
shoe
assembly
3
Wheel
cylinder
assembly
4
Brake
shoe
upper
return
spring
5
Brake
shoe
lower
return
spring
REMOVAL
I
Jack
up
front
of
vehicle
just
high
enough
to
remove
tire
and
support
it
with
safety
stands
2
Remove
wheel
and
brake
drum
If
brake
drum
cannot
be
easily
removed
return
brake
adjuster
install
two
bolts
M8
x
1
25
in
holes
on
the
flange
face
of
brake
drum
and
tighten
bolts
even
ly
until
brake
drum
is
driven
out
3
In
order
to
ease
operation
re
move
hub
assembly
from
knucRle
spindle
Refer
to
Front
Axle
4
Unhook
upper
lower
and
after
shoe
return
springs
and
then
remove
brake
shoe
assemblies
S
Disconnect
brake
hose
from
wheel
cy
linder
6
Loosen
securing
nut
and
remove
wheel
cylinder
7
Remove
rubber
boot
adjuster
shim
lock
plate
and
retaining
spring
and
then
remove
adjuster
assembly
from
brake
disc
Fig
BR
I
6
Front
brake
1
Brake
hose
2
Wheel
cylinder
attaching
bolt
BA312
3
Rubber
boot
Fig
BR
17
Removing
wheel
cylinder
DISASSEMBLY
AND
ASSEMBLY
Wheel
cylinder
@
rr
l
@
t
a
Wheel
cy
linder
housing
2
Piston
3
Piston
cup
4
Dust
cover
5
Retainer
BR649
6
Connector
7
Packings
8
Connector
bolt
9
Bleeder
screw
10
Bleeder
cap
Wheel
cylinder
can
be
disassembled
simply
by
the
following
procedures
described
below
Remove
retainer
and
dust
cover
and
take
out
piston
from
wheel
cyl
inder
Be
careful
not
to
damage
sliding
part
of
piston
and
piston
cup
Thoroughly
wa
sh
u
disassembled
parts
in
brake
fluid
or
alcohol
Note
Do
not
wash
rubber
parts
with
mineral
oil
since
they
are
deterio
rated
When
alcohol
is
used
however
do
not
immerse
rubber
parts
in
alcohol
longer
than
30
seconds
After
parts
are
cleaned
dry
them
with
com
pressed
air
Assemble
wheel
cylinder
in
reverse
sequence
of
diassembly
When
securing
connector
bolt
in
sert
its
location
tip
to
the
hole
of
wheel
cylinder
firmly
and
tighten
it
securely
Carry
out
operations
carefully
so
that
component
parts
are
not
damaged
or
no
dust
and
other
foreign
materials
enter
cylinder
Note
The
brake
wheel
cylinder
is
available
in
both
NABCO
make
and
TOKICO
make
There
is
no
inter
changeability
of
repair
kits
or
com
ponent
parts
between
NABCO
and
TOKICO
makes
When
replacing
the
repair
kit
or
ent
parts
ascertain
the
brand
of
the
brake
wheel
cylinder
body
Be
sure
to
use
parts
of
the
same
make
as
the
former
ones
INSPECTION
Brake
drum
I
Replace
brake
drum
whose
dia
meter
is
beyond
the
limit
of
1
5
mm
0
OS9
in
with
respect
to
the
standard
inner
diameter
of
2S4
0
rom
10
00
SR
tO
Fig
BR
18
Front
wheel
cylinder
in
Page 386 of 537
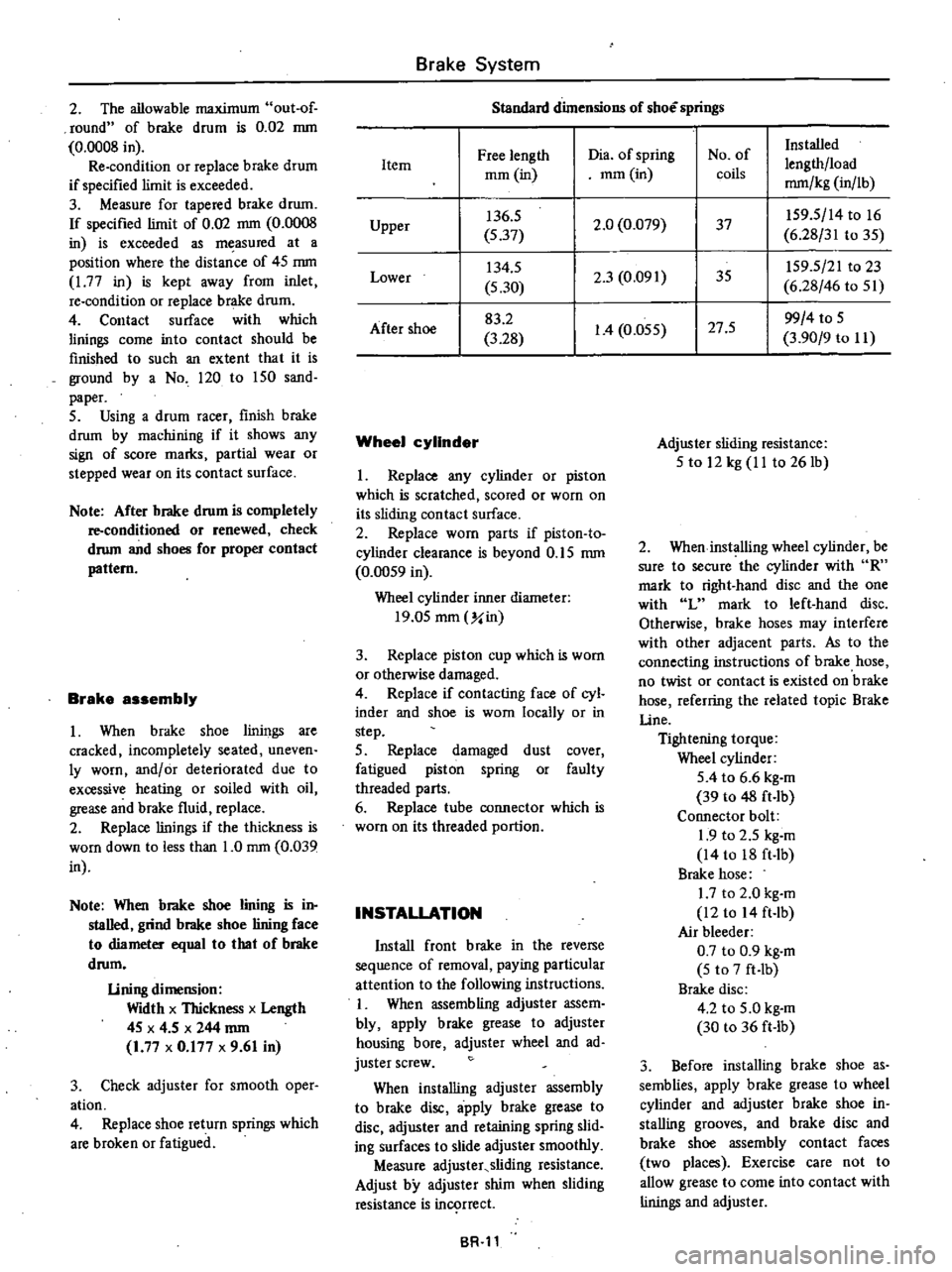
2
The
allowable
maximum
out
of
round
of
brake
drum
is
0
02
mm
0
0008
in
Re
condition
or
replace
brake
drum
if
specified
limit
is
exceeded
3
Measure
for
tapered
brake
drum
If
specified
limit
of
0
02
mm
0
0008
in
is
exceeded
as
measured
at
a
position
where
the
distance
of
4S
mm
177
in
is
kept
away
from
inlet
re
condition
or
replace
brake
drum
4
Contact
surface
with
which
linings
come
into
contact
should
be
finished
to
such
an
extent
that
it
is
ground
by
a
No
120
to
150
sand
paper
S
Using
a
drum
racer
finish
brake
drum
by
machining
if
it
shows
any
sign
of
score
marks
partial
wear
or
stepped
wear
on
its
contact
surface
Note
After
brake
drum
is
completely
re
conditioned
or
renewed
check
drum
and
shoes
for
proper
contact
pattern
Brake
assembly
I
When
brake
shoe
linings
are
cracked
incompletely
seated
uneven
Iy
worn
andlor
deteriorated
due
to
excessive
heating
or
soiled
with
oil
grease
and
brake
fluid
replace
2
Replace
linings
if
the
thickness
is
worn
down
to
less
than
1
0
mm
0
039
in
Note
When
brake
shoe
lining
is
in
stalled
grind
brake
shoe
lining
face
to
diameter
equal
to
that
of
brake
drum
lining
dimension
Width
x
Thickness
x
Length
4S
x
4
S
x
244
mm
1
77
x
0
177
x
9
61
in
3
Check
adjuster
for
smooth
oper
ation
4
Replace
shoe
return
springs
which
are
broken
or
fatigued
Brake
System
Standard
dimensions
of
shoe
springs
Free
length
Dia
of
spring
No
of
Installed
Item
lengthlload
mOl
in
mOl
in
coils
mm
kg
in
lb
Upper
136
5
2
0
0
079
37
IS9
S
14
to
16
S
37
6
28
31
to
3S
Lower
134
S
2
3
0
091
35
IS9
5
21
to
23
5
30
6
28
46
to
Sl
After
shoe
83
2
1
4
O
OSS
27
S
99
4
to
S
3
28
3
90
9
to
II
Wheel
cylinder
I
Replace
any
cylinder
or
piston
which
is
scratched
scored
or
worn
on
its
sliding
contact
surface
2
Replace
worn
parts
if
piston
to
cylinder
clearance
is
beyond
O
IS
mm
0
OOS9
in
Wheel
cylinder
inner
diameter
19
0S
mOl
Y
in
3
Replace
piston
cup
which
is
worn
or
otherwise
damaged
4
Replace
if
contacting
face
of
cyl
inder
and
shoe
is
worn
locally
or
in
step
S
Replace
damaged
dust
cover
fatigued
piston
spring
or
faulty
threaded
parts
6
Replace
tube
connector
which
is
worn
on
its
threaded
portion
INSTALLATION
Install
front
brake
in
the
reverse
sequence
of
removal
paying
particular
attention
to
the
following
instructions
I
When
assembling
adjuster
assem
bly
apply
brake
grease
to
adjuster
housing
bore
adjuster
wheel
and
ad
juster
screw
When
installing
adjuster
assembly
to
brake
disc
apply
brake
grease
to
disc
adjuster
and
retaining
spring
slid
ing
surfaces
to
slide
adjuster
smoothly
Measure
adjuster
sliding
resistance
Adjust
by
adjuster
shim
when
sliding
resistance
is
in
rrect
BR
ll
Adjuster
sliding
resistance
S
to
12
kg
II
to
261b
2
When
installing
wheel
cylinder
be
sure
to
secure
the
cylinder
with
R
mark
to
right
hand
disc
and
the
one
with
L
mark
to
left
hand
disc
Otherwise
brake
hoses
may
interfere
with
other
adjacent
parts
As
to
the
connecting
instructions
of
brake
hose
no
twist
or
contact
is
existed
on
brake
hose
referring
the
related
topic
Brake
line
Tightening
torque
Wheel
cylinder
SA
to
6
6
kg
m
39
to
48
ft
lb
Connector
bolt
1
9
to
2
5
kg
m
14
to
18
ft
Ib
Brake
hose
1
7
to
2
0
kg
m
12
to
14
ft
lb
Air
bleeder
0
7
to
0
9
kg
m
5
to
7
ft
Ib
Brake
disc
4
2
to
S
O
kg
m
30
to
36
ft
lb
3
Before
installing
brake
shoe
as
semblies
apply
brake
grease
to
wheel
cylinder
and
adjuster
brake
shoe
in
stalling
grooves
and
brake
disc
and
brake
shoe
assembly
contact
faces
two
places
Exercise
care
not
to
allow
grease
to
come
into
contact
with
linings
and
adjuster