torque DATSUN PICK-UP 1977 Service Manual
[x] Cancel search | Manufacturer: DATSUN, Model Year: 1977, Model line: PICK-UP, Model: DATSUN PICK-UP 1977Pages: 537, PDF Size: 35.48 MB
Page 429 of 537
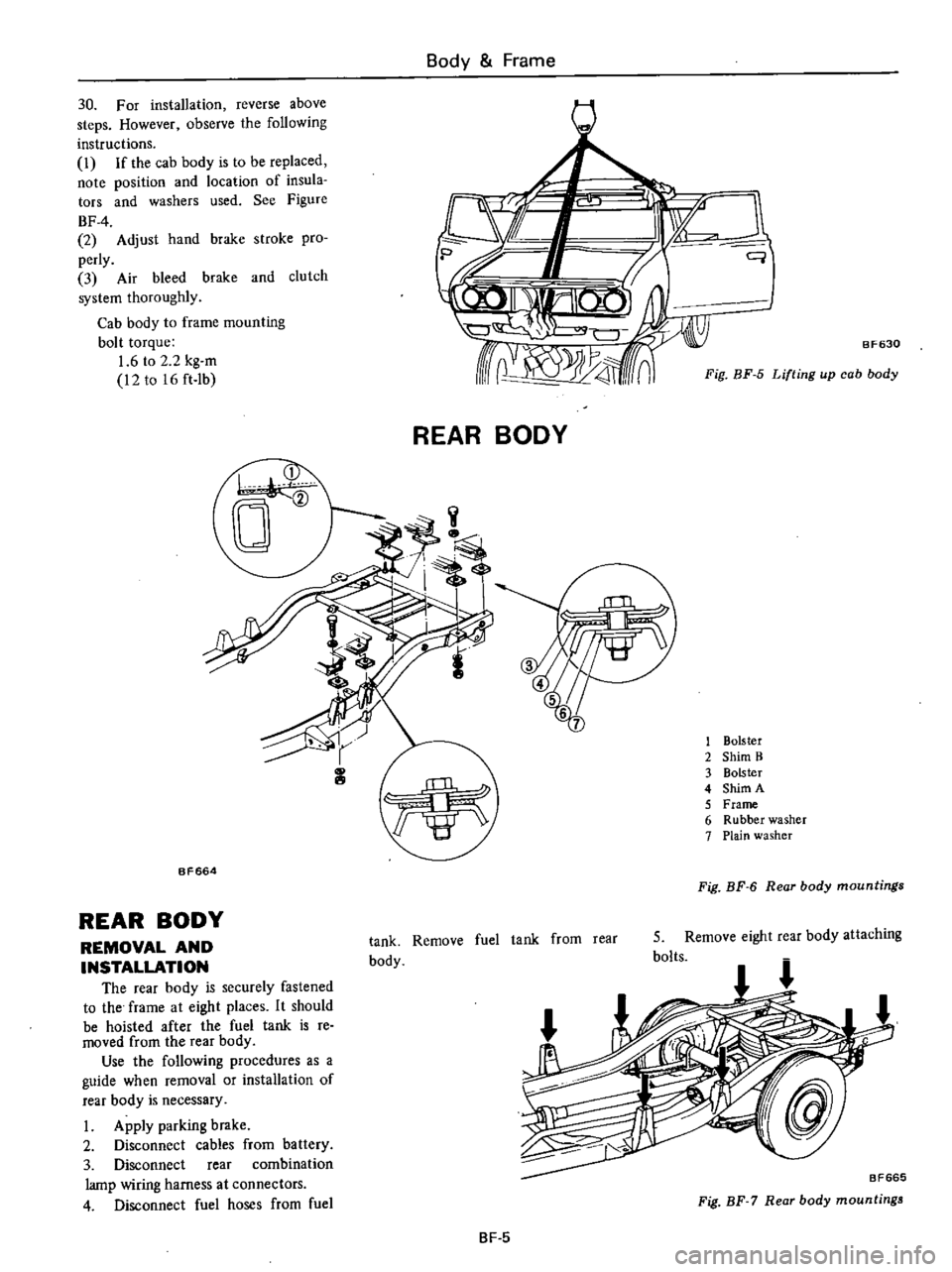
Body
Frame
30
For
installation
reverse
above
steps
However
observe
the
following
instructions
i
If
the
cab
body
is
to
be
replaced
note
position
and
location
of
insula
tors
and
washers
used
See
Figure
BF
4
2
Adjust
hand
brake
stroke
pro
perly
3
Air
bleed
brake
and
clutch
system
thorougWy
Cab
body
to
frame
mounting
bolt
torque
1
6
to
2
2
kg
m
12
to
16
ft
Ib
o
i
k
q
1Q
j
b
crru
V
J
8F630
rr
1
4
n
Fig
BF
5
Lifting
up
cab
body
REAR
BODY
1
Bolster
2
Shim
B
3
Bolster
4
Shim
A
5
Frame
6
Rubber
washer
7
Plain
washer
BF664
Fig
BF
6
Rear
body
mountings
REAR
BODY
REMOVAL
AND
INSTALLATION
The
rear
body
is
securely
fastened
to
the
frame
at
eight
places
It
should
be
hoisted
after
the
fuel
tank
is
re
moved
from
the
rear
body
Use
the
following
procedures
as
a
guide
when
removal
or
installation
of
rear
body
is
necessary
I
Apply
parking
brake
2
Disconnect
cables
from
battery
3
Disconnect
rear
combination
lamp
wiring
harness
at
connectors
4
Disconnect
fuel
hoses
from
fuel
tank
Remove
fuel
tank
from
rear
body
5
Remove
eight
rear
body
attaching
bolts
BF665
Fig
BF
7
Rear
body
mountings
BF
5
Page 430 of 537
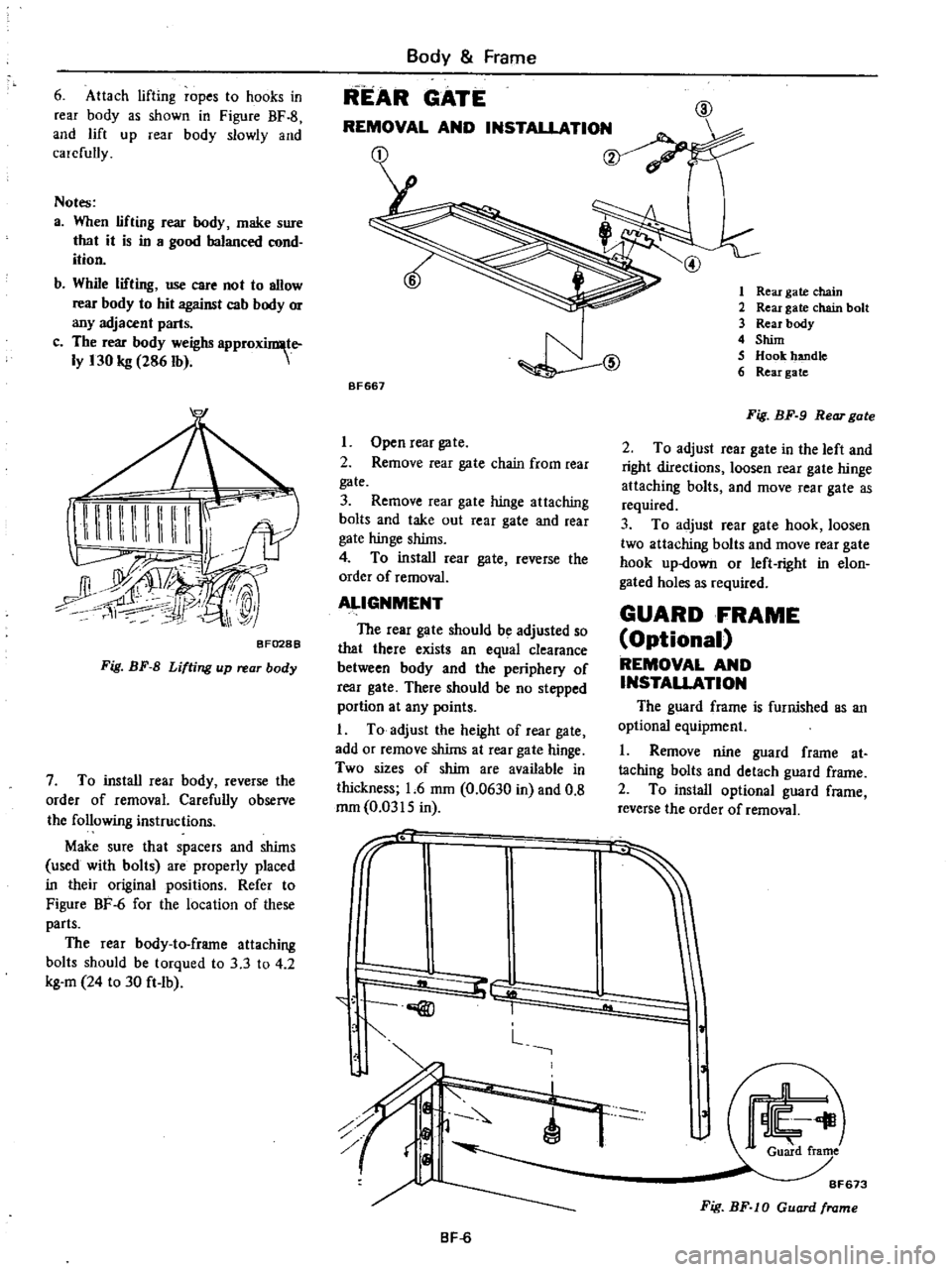
6
Attach
lifting
ropes
to
hooks
in
rear
body
as
shown
in
Figure
BF
8
and
lift
up
rear
body
slowly
and
carefully
Notes
a
When
lifting
rear
body
make
sure
that
it
is
in
a
good
balanced
cond
ition
b
While
lifting
use
care
not
to
allow
rear
body
to
hit
against
cab
body
or
any
adjacent
parts
c
The
rear
body
weighs
approxillll
te
Iy
130
kg
286
Ib
BF0288
Fig
BF
8
Lifting
up
rear
body
7
To
install
rear
body
reverse
the
order
of
removal
Carefully
observe
the
following
instructions
Make
sure
that
spacers
and
shims
used
with
bolts
are
properly
placed
in
their
original
positions
Refer
to
Figure
BF
6
for
the
location
of
these
parts
The
rear
body
to
frame
attaching
bolts
should
be
torqued
to
3
3
to
4
2
kg
m
24
to
30
ft
Ib
Body
Frame
REAR
GATE
00
REMOVAL
AND
INSTAllATION
1
W
@
BF661
I
Open
rear
gate
2
Remove
rear
gate
chain
from
ear
gate
3
Remove
rear
gate
hinge
attaching
bolts
and
take
out
rear
gate
and
rear
gate
hinge
shims
4
To
install
rear
gate
reverse
the
order
of
removal
ALIGNMENT
The
rear
gate
should
be
adjusted
so
that
there
exists
an
equal
clearance
between
body
and
the
periphery
of
rear
gate
There
should
be
no
stepped
portion
at
any
points
I
To
adjust
the
height
of
rear
gate
add
or
remove
shims
at
rear
gate
hinge
Two
sizes
of
shim
are
available
in
thickness
1
6
mm
0
0630
in
and
0
8
rom
0
0315
in
rr
r
f
r
@
C
L
i
BF
6
1
Rear
gate
chain
2
Rear
gate
chain
bolt
3
Rear
body
4
Shim
S
Hook
handle
6
Reargate
Fig
BF
9
Rear
gate
2
To
adjust
rear
gate
in
the
left
and
right
directions
loosen
rear
gate
hinge
attaching
bolts
and
move
rear
gate
as
required
3
To
adjust
rear
gate
hook
loosen
two
attaching
bolts
and
move
rear
gate
hook
up
down
or
left
right
in
elon
gated
holes
as
required
GUARD
FRAME
Optional
REMOVAL
AND
INSTAUATION
The
guard
frame
is
furnished
as
an
optional
equipment
I
Remove
nine
guard
frame
at
taching
bolts
and
detach
guard
frame
2
To
install
optional
guard
frame
reverse
the
order
of
removal
s
SF673
Fig
BF
lO
Guard
frame
Page 433 of 537
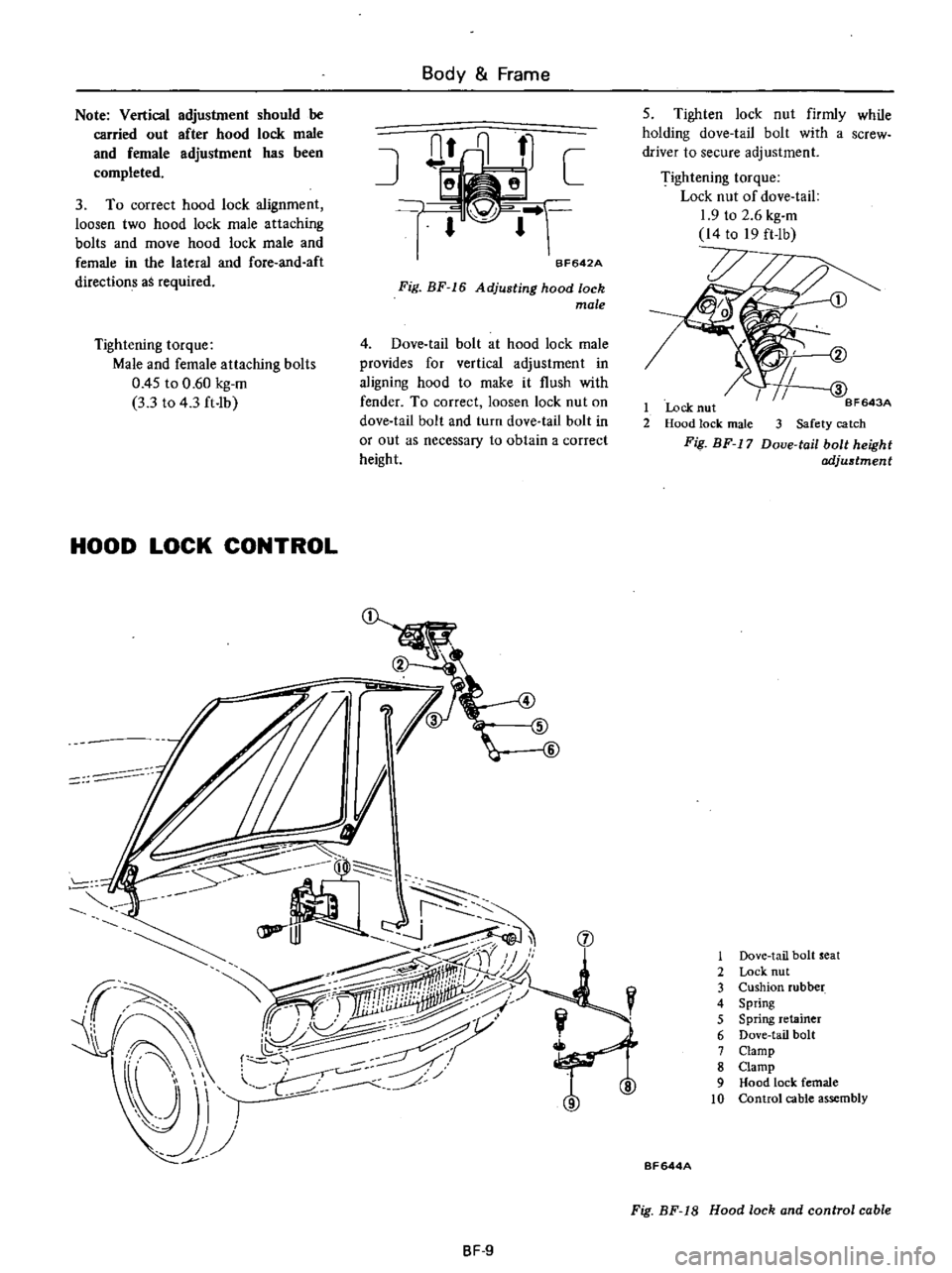
Body
Frame
Note
Vertical
adjustment
should
be
carried
out
after
hood
lock
male
and
female
adjustment
has
been
completed
3
To
correct
hood
lock
alignment
loosen
two
hood
lock
male
attaching
bolts
and
move
hood
lock
male
and
female
in
the
lateral
and
fore
and
aft
directions
as
required
D
1r
r
BF642A
Fig
BF
16
Adjusting
hood
lock
male
Tightening
torque
Male
and
female
attaching
bolts
0
45
to
0
60
kg
m
3
3
to
4
3
ft
Ib
4
Dove
tail
bolt
at
hood
lock
male
provides
for
vertical
adjustment
in
aligning
hood
to
make
it
flush
with
fender
To
correct
loosen
lock
nut
on
dove
tail
bolt
and
turn
dove
tail
bolt
in
or
out
as
necessary
to
obtain
a
correct
height
HOOD
LOCK
CONTROL
JI
I
i
I
r
lPP
J
jJ
J
Sr
aj
I
I
I
J
f
ifry
ff
I
ii1iiilliii
j
iW
r
U
I
j
Y
f
7
j
1
JJ
J
8F
9
5
Tighten
lock
nut
firmly
while
holding
dove
tail
bolt
with
a
screw
driver
to
secure
adjustment
Tightening
torque
Lock
nut
of
dove
tail
1
9
to
2
6
kg
m
14
to
19
ft
lb
BF643A
1
Lock
nut
2
Hood
lock
male
3
Safety
catch
Fig
BF
17
Doue
tail
bolt
height
adjustment
1
Dove
tail
bolt
seat
2
Lock
nut
3
Cushion
rubber
4
Spring
5
Spring
retainer
6
Dove
tail
bolt
7
Clamp
8
Clamp
9
Hood
lock
female
10
Control
cable
assembly
BF644A
Fig
BF
18
Hood
lock
and
control
cable
Page 444 of 537
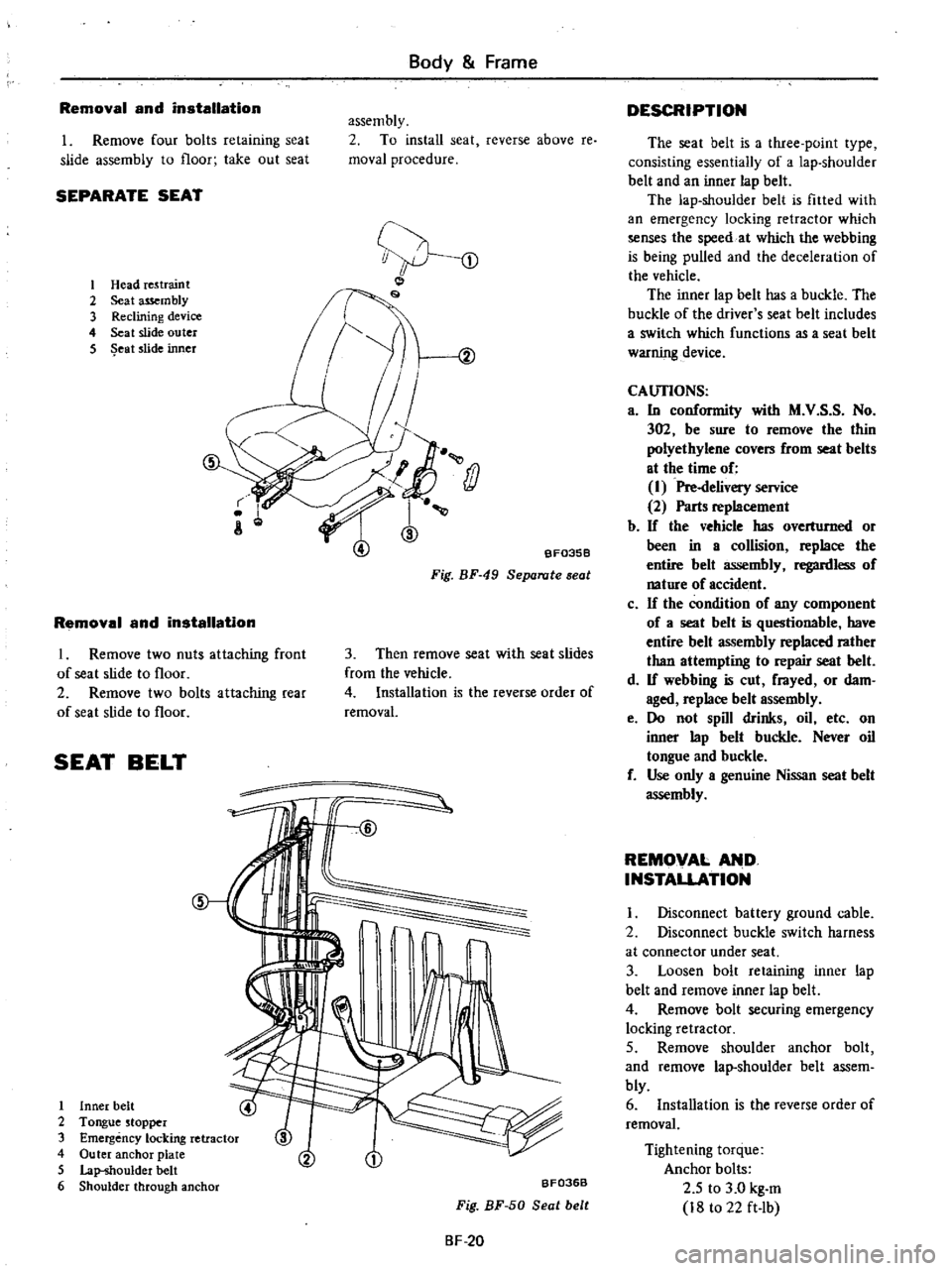
Body
Frame
Removal
and
installation
assembly
2
To
install
seat
reverse
above
re
moval
procedure
1
Remove
four
bolts
retaining
seat
slide
assembly
to
floor
take
out
seat
SEPARATE
SEAT
1
Head
re5traint
2
Seat
assembly
3
Reclining
device
4
Seat
slide
outer
5
eat
slide
inner
s
J
j
BF0358
Fig
BF
49
Separate
seat
Removal
and
installation
I
Remove
two
nuts
attaching
front
of
seat
slide
to
floor
2
Remove
two
bolts
attaching
rear
of
seat
slide
to
floor
3
Then
remove
seat
with
seat
slides
from
the
vehicle
4
Installation
is
the
reverse
order
of
removal
SEAT
BELT
1
Inner
belt
2
Tongue
stopper
3
Emergency
locking
retractor
4
Outer
anchor
plate
5
Lap
shoulder
belt
6
Shoulder
through
anchor
BF036B
Fig
BF
50
Seat
belt
BF
20
DESCRIPTION
The
seat
belt
is
a
three
point
type
consisting
essentiaily
of
a
lap
shoulder
belt
and
an
inner
lap
belt
The
lap
shoulder
belt
is
fitted
with
an
emergency
locking
retractor
which
senses
the
speed
at
which
the
webbing
is
being
pulled
and
the
deceleration
of
the
vehicle
The
inner
lap
belt
has
a
buckle
The
buckle
of
the
driver
s
seat
belt
includes
a
switch
which
functions
as
a
seat
belt
warning
device
CAlJI10NS
a
In
conformity
with
M
V
S
S
No
302
be
sure
to
remove
the
thin
polyethylene
covers
from
seat
belts
at
the
time
of
I
Pre
delivery
service
2
Parts
replacement
b
If
the
vehicle
has
overturned
or
been
in
a
collision
replace
the
entire
belt
assembly
regardless
of
nature
of
accident
c
If
the
condition
of
any
component
of
a
seat
belt
is
questionable
have
entire
belt
assembly
replaced
rather
than
attempting
to
repair
seat
belt
d
If
webbing
is
cut
frayed
or
dam
aged
replace
belt
assembly
e
Do
not
spill
drinks
oil
etc
on
inner
lap
belt
buckle
Never
oil
tongue
and
buckle
f
Use
only
a
genuine
Nissan
seat
belt
assembly
REMOVAL
AND
INSTAUATION
I
Disconnect
battery
ground
cable
2
Disconnect
buckle
switch
harness
at
connector
under
seat
3
Loosen
bolt
retaining
inner
lap
belt
and
remove
inner
lap
belt
4
Remove
bolt
securing
emergency
locking
retractor
5
Remove
shoulder
anchor
bolt
and
remove
lap
shoulder
belt
assem
bly
6
Installation
is
the
reverse
order
of
removal
Tightening
torque
Anchor
bolts
2
5
to
3
0
kg
m
18
to
22
ft
lb
Page 507 of 537
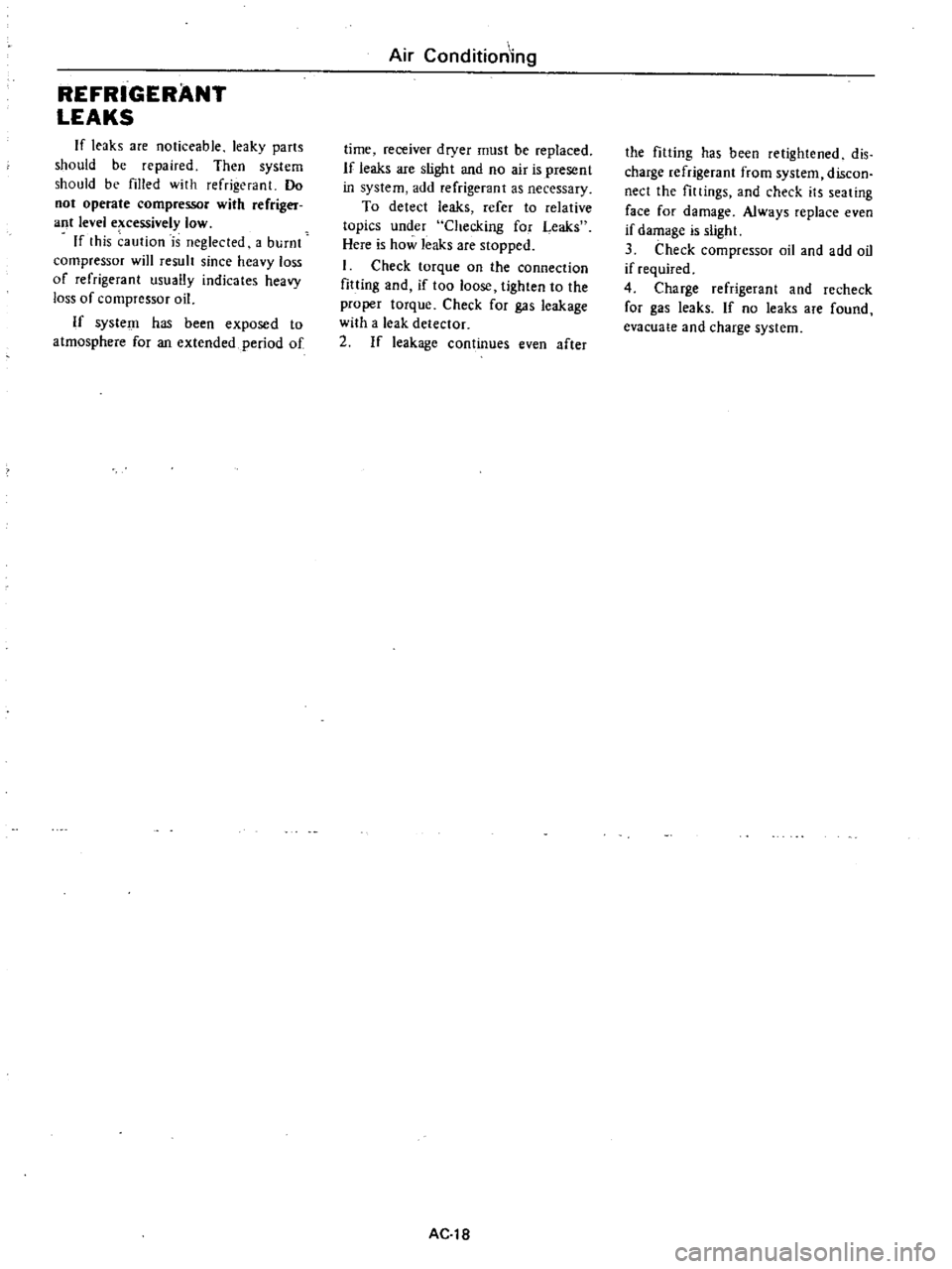
REFRIGERANT
LEAKS
If
leaks
are
noticeable
leaky
parts
should
be
repaired
Then
system
should
be
filled
with
refrigerant
Do
not
operate
compressor
with
refriger
ant
level
e
cessively
low
If
this
caution
is
neglected
a
burnt
compressor
will
result
since
heavy
loss
of
refrigerant
usually
indicates
heavy
loss
of
compressor
oil
If
system
has
been
exposed
to
atmosphere
for
an
extended
period
of
Air
Condition
ing
time
receiver
dryer
must
be
replaced
If
leaks
are
slight
and
no
air
is
present
in
system
add
refrigerant
as
necessary
To
detect
leaks
refer
to
relative
topics
under
Checking
for
Leaks
Here
is
how
leaks
are
stopped
I
Check
torque
on
the
connection
fitting
and
if
too
loose
tighten
to
the
proper
torque
Check
for
gas
leakage
with
a
leak
detector
2
If
leakage
continues
even
after
AC
18
the
fitting
has
been
retightened
dis
charge
refrigerant
from
system
discon
nect
the
fittings
and
check
its
seating
face
for
damage
Always
replace
even
if
damage
is
slight
3
Check
compressor
oil
and
add
oil
if
required
4
Charge
refrigerant
and
recheck
for
gas
leaks
If
no
leaks
are
found
evacuate
and
charge
system
Page 515 of 537
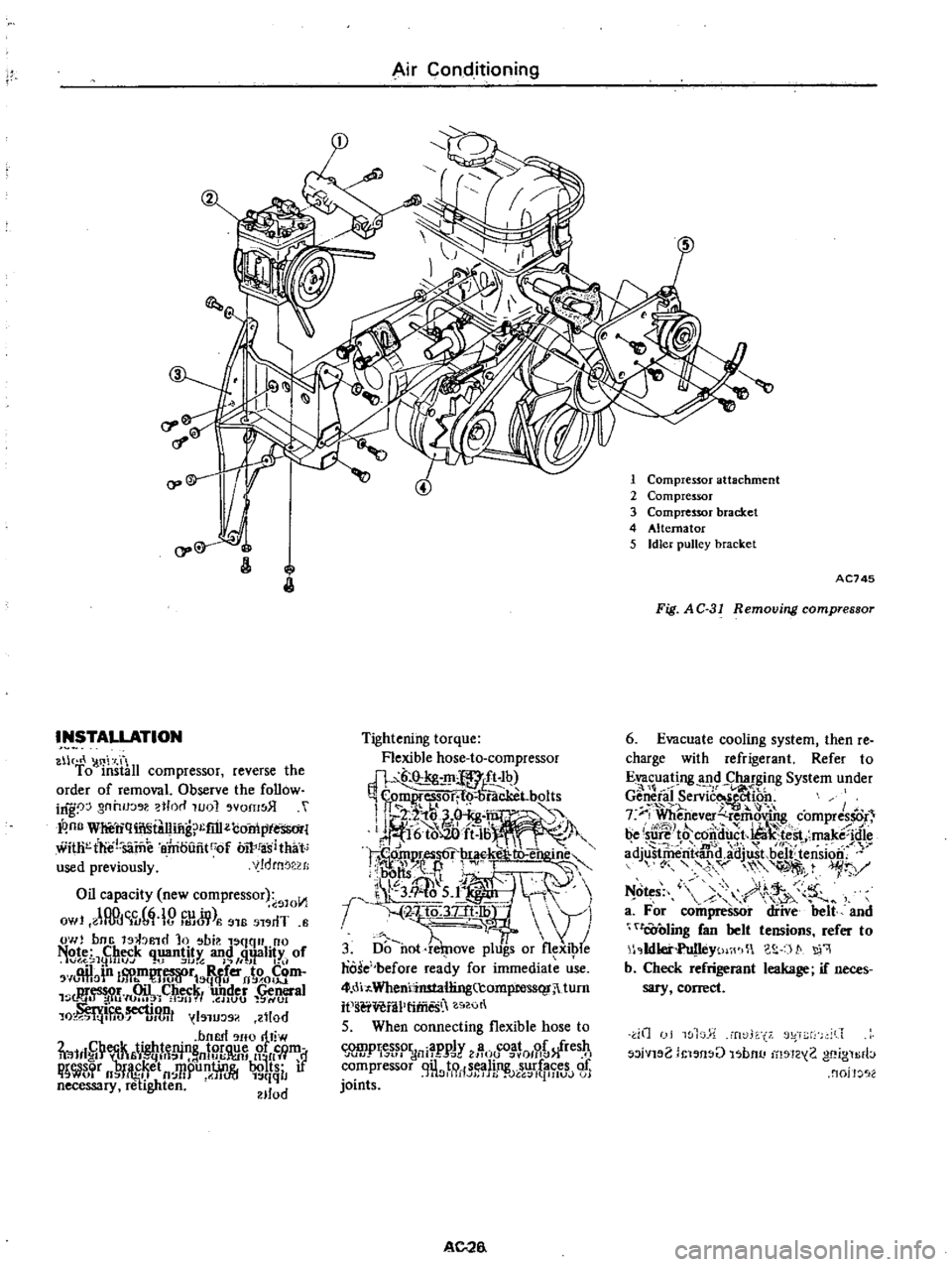
2
R
C7
c
L
PJJ
I
8
INSTALLATION
a
c
J
l
i
rp
To
install
compressor
reverse
the
order
of
removal
Observe
the
follow
ing
nhlJo
e
trorf
1001
vom
R
i
n3
Wheliqli
liiAniitg
fiil
l
in
pt
l
witlil
tiiel
sam
efuouiitITof
b11
1fasitlult
used
previously
v
d
rnl
2
Oil
capacity
new
compressor
O
910
1
owt
llllt
blj
f
H
w
s
013
5
rlT
s
0
111
boc
19
bB1rllo
bi2
qqll
no
e
l
bffik
kuanM
mpdi
x
of
Jli
oln
L
il
m
1IlffiiOrb
fler
ot
oldm
F
n
Cheo
f
undeF
r
n
al
1
aQ
r1tIU
Jt
t31
HClJI1
t
JIVU
i
rlUI
1o
ifm
ft
q
t
VI
31U
S
ltlod
bnM
UfO
l
W
kldf
CJiJi
ti
WIf
nl
L
llil
g
ncn
d
oressor
M
et
illpuntinl
botts
if
l9Wul
fb
i
l
fI
I
l
1Ttio
l
qqlJ
necessary
re
Ighten
I
d
210
Air
Conditioning
Tightening
torque
Flexible
hose
to
compressor
dl
t
kg
J
l
IQ
1
Tf
es
oriti
ra
Lbolts
IbP
fo
o15g
m
J
r
f6i
o
20
i
il
f
J
rt
I
r
aGket
engine
Dons
1
1
0
1
1
3
16
5
l11fd
1l
V
f
42
3
3U
llif
Yl
I
u
y
j
3
D
not
remove
IJgs
orflexibie
1i6
e
before
ready
for
immediate
use
4l
di
Wheniiinstallingccomptess
i
turn
it
serWfiPtiffies
SlOt
5
When
connecting
flexible
hose
to
9mPr
ssor
apD
v
a
coat
of
Hfresh
JU
UI
l1Il
t
2
JIUU
uOHltl
r
fl
compressor
0
1
to
fs
aHn
lurfaces
of
1n
1l11
JJ
J
f
PJU
Ht
UlUJ
jJ
joints
AC
26
5
1
Compressor
attachment
2
Compressor
3
Compressor
bracket
4
AHernator
5
Idler
pulley
bracket
AC745
Fig
AC
31
Removing
compressor
6
Evacuate
cooling
system
then
re
charge
with
refrigerant
Refer
to
Evacuating
and
Charging
System
under
l
r
Gen
efal
Servic
ectioo
f
iI
t
7
F
Whenever
remoV
J
compres
r
be
su
J
t8
C6itiu
t
Ua
t
st
make
idie
mV
i
1rJ
adjustril
rit
and
adjwt
beJf
tension
yv
1
r
Y
N
o
s
9
r
h
v
a
For
compressor
diive
belt
and
tOoling
fan
belt
tensions
refer
to
1
Ildlet
Yt
j
WI
c
S
t
q
b
Cheok
refrigerant
leakage
if
neces
sary
correct
dO
I
wl
Tw
l
rt
f
r2
iVl
2
i
l
n
U
l
bnu
1
1Z
2
gf
ign
rb
nojJ
2
Page 517 of 537
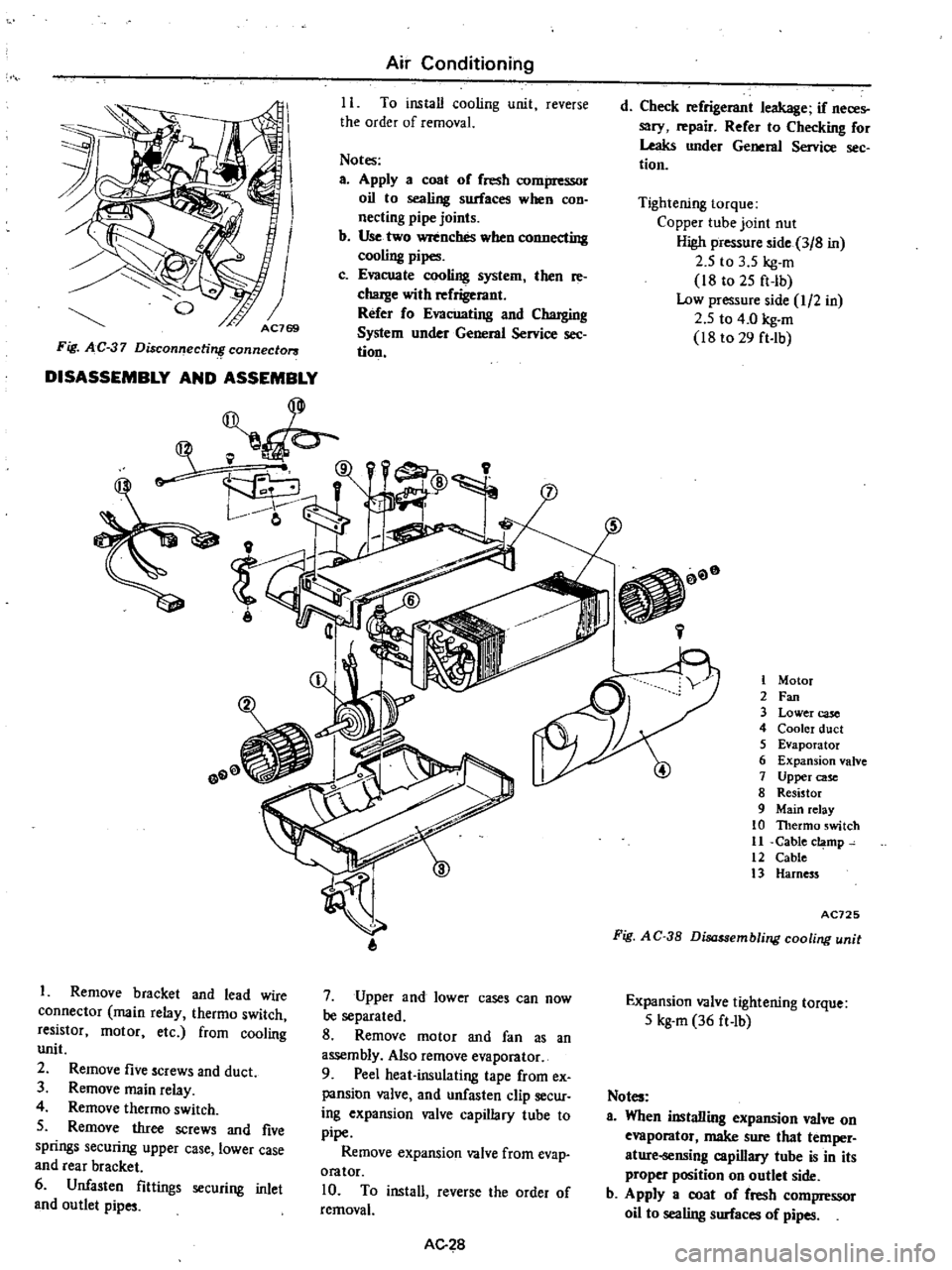
I
o
Fig
AC
37
Disconnectirt
connector
3
DISASSEMBLY
AND
ASSEMBLY
I
Remove
bracket
and
lead
wire
connector
main
relay
thermo
switch
resistor
motor
etc
from
cooling
unit
2
Remove
five
screws
and
duct
3
Remove
main
relay
4
Remove
thermo
switch
5
Remove
three
screws
and
five
springs
securing
upper
case
lower
case
and
rear
bracket
6
Unfasten
fittings
securing
inlet
and
outlet
pipes
Air
Conditioning
11
To
install
cooling
unit
reverse
the
order
of
removal
Notes
a
Apply
a
coat
of
fresh
compressor
oil
to
sealing
surfaces
when
COD
necting
pipe
joints
b
Use
two
wrenches
when
connecting
cooling
pipes
c
Evacuate
cooling
system
then
re
chaJge
with
refrigerant
Refer
fo
Evacuating
and
Charging
System
under
General
Service
see
tion
9
7
Upper
and
lower
cases
can
now
be
separated
8
Remove
motor
and
fan
as
an
assembly
Also
remove
evaporator
9
Peel
heat
insulating
tape
from
ex
pansion
valve
and
unfasten
clip
secur
ing
expansion
valve
capillary
tube
to
pipe
Remove
expansion
valve
from
evap
orator
10
To
install
reverse
the
order
of
removal
AG
28
d
Check
refrigerant
leakage
if
neces
sary
repair
Refer
to
Checking
for
Leaks
under
General
Service
sec
tion
Tightening
torque
Copper
tube
joint
nut
High
pressure
side
3
8
in
2
5
to
3
5
kg
m
18
to
25
ft
lb
Low
pressure
side
I
2
in
2
5
to
4
0
kg
m
18
to
29
ft
lb
00
L
1
Motor
2
Fan
3
Lower
case
4
Cooler
duct
5
Evaporator
6
Expansion
valve
7
Upper
case
8
Resistor
9
Main
relay
10
Thermo
switch
11
Cable
c
mp
12
Cable
3
Harness
AC725
Fig
A
C
38
Disassembling
cooling
unit
Expansion
valve
tightening
torque
5
kg
m
36
ft
Ib
Notes
a
When
installing
expansion
valve
on
evaporator
make
sure
that
temper
ature
oensing
capillary
tube
is
in
its
proper
position
on
outlet
side
b
Apply
a
coat
of
fresh
compressor
oil
to
sealing
surfaces
of
pipes
Page 518 of 537
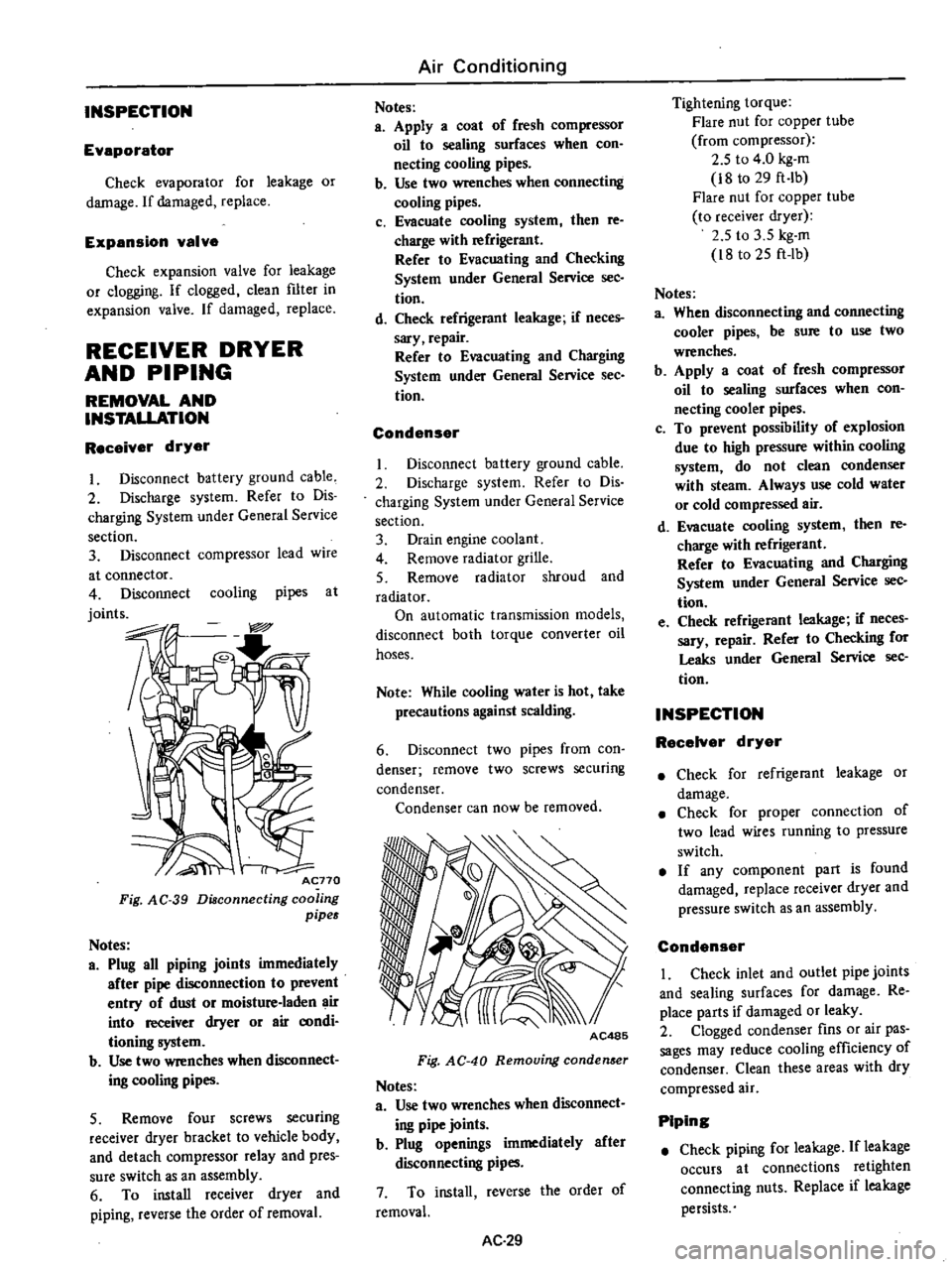
INSPECTION
Evaporator
Check
evaporator
for
leakage
or
damage
If
damaged
replace
Expansion
valve
Check
expansion
valve
for
leakage
or
clogging
If
clogged
clean
filter
in
expansion
valve
If
damaged
replace
RECEIVER
DRYER
AND
PIPING
REMOVAL
AND
INSTAUATION
Receiver
dryer
I
Disconnect
battery
ground
cable
2
Discharge
system
Refer
to
Dis
charging
System
under
General
Service
section
3
Disconnect
compressor
lead
wire
at
connector
4
Disconnect
cooling
pipes
at
joints
Acno
Fig
AC
39
Diaconnecting
coo
ing
pipes
Notes
a
Plug
all
piping
joints
immediately
after
pipe
disconnection
to
prevent
entry
of
dust
or
moisture
laden
air
into
receiver
dryer
or
air
aJOdi
tioning
system
b
Use
two
wrenches
when
dIsconnect
ing
cooling
pipes
5
Remove
four
screws
securing
receiver
dryer
bracket
to
vehicle
body
and
detach
compressor
relay
and
pres
sure
switch
as
an
assembly
6
To
install
receiver
dryer
and
piping
reverse
the
order
of
removal
Air
Conditioning
Notes
a
Apply
a
coat
of
fresh
compressor
oil
to
sealing
surfaces
when
con
necting
cooling
pipes
b
Use
two
wrenches
when
connecting
cooling
pipes
c
Evacuate
cooling
system
then
re
charge
with
refrigerant
Refer
to
Evacuating
and
Checking
System
under
General
Service
sec
tion
d
Check
refrigerant
leakage
if
neces
sary
repair
Refer
to
Evacuating
and
Charging
System
under
General
Service
See
tion
Condenser
Disconnect
battery
ground
cable
2
Discharge
system
Refer
to
Dis
charging
System
under
General
Service
section
3
Drain
engine
coolant
4
Remove
radiator
grille
5
Remove
radiator
shroud
and
radiator
On
automatic
transmission
models
disconnect
both
torque
converter
oil
hoses
Note
While
cooling
water
is
hot
take
precautions
against
scalding
6
Disconnect
two
pipes
from
con
denser
remove
two
screws
securing
condenser
Condenser
can
now
be
removed
AC485
Fig
AC
40
Removing
conden
er
Notes
a
Use
two
wrenches
when
disconnect
ing
pipe
joints
b
Plug
openings
immediately
after
disconnecting
pipes
7
To
install
reverse
the
order
of
removal
AC
29
Tightening
torque
Flare
nut
for
copper
tube
from
compressor
2
5
to
4
0
kg
m
i8
to
29
ft
Ib
Flare
nut
for
copper
tube
to
receiver
dryer
2
5
to
3
5
kg
m
i8
to
25
ft
lb
Notes
a
When
disconnecting
and
connecting
cooler
pipes
be
sure
to
use
two
wrenches
b
Apply
a
coat
of
fresh
compressor
oil
to
sealing
surfaces
when
con
necting
cooler
pipes
c
To
prevent
possibility
of
explosion
due
to
high
pressure
within
cooling
system
do
not
clean
condenser
with
steam
Always
use
cold
water
or
cold
compressed
air
d
Evacuate
cooling
system
then
re
charge
with
refrigerant
Refer
to
Evacuating
and
Charging
System
under
General
Service
sec
tion
e
Check
refrigerant
leakage
if
neces
sary
repair
Refer
to
Checking
for
Leaks
under
General
Service
sec
tion
INSPECTION
RecelYer
dryer
Check
for
refrigerant
leakage
or
damage
Check
for
proper
connection
of
two
lead
wires
running
to
pressure
switch
If
any
component
part
is
found
damaged
replace
receiver
dryer
and
pressure
switch
as
an
assembly
Condenser
I
Check
inlet
and
outlet
pipe
joints
and
sealing
surfaces
for
damage
Re
place
parts
if
damaged
or
leaky
2
Clogged
condenser
fins
or
air
pas
sages
may
reduce
cooling
efficiency
of
condenser
Clean
these
areas
with
dry
compressed
air
Piping
Check
piping
for
leakage
If
leakage
occurs
at
connections
retighten
connecting
nuts
Replace
if
leakage
persists
Page 523 of 537
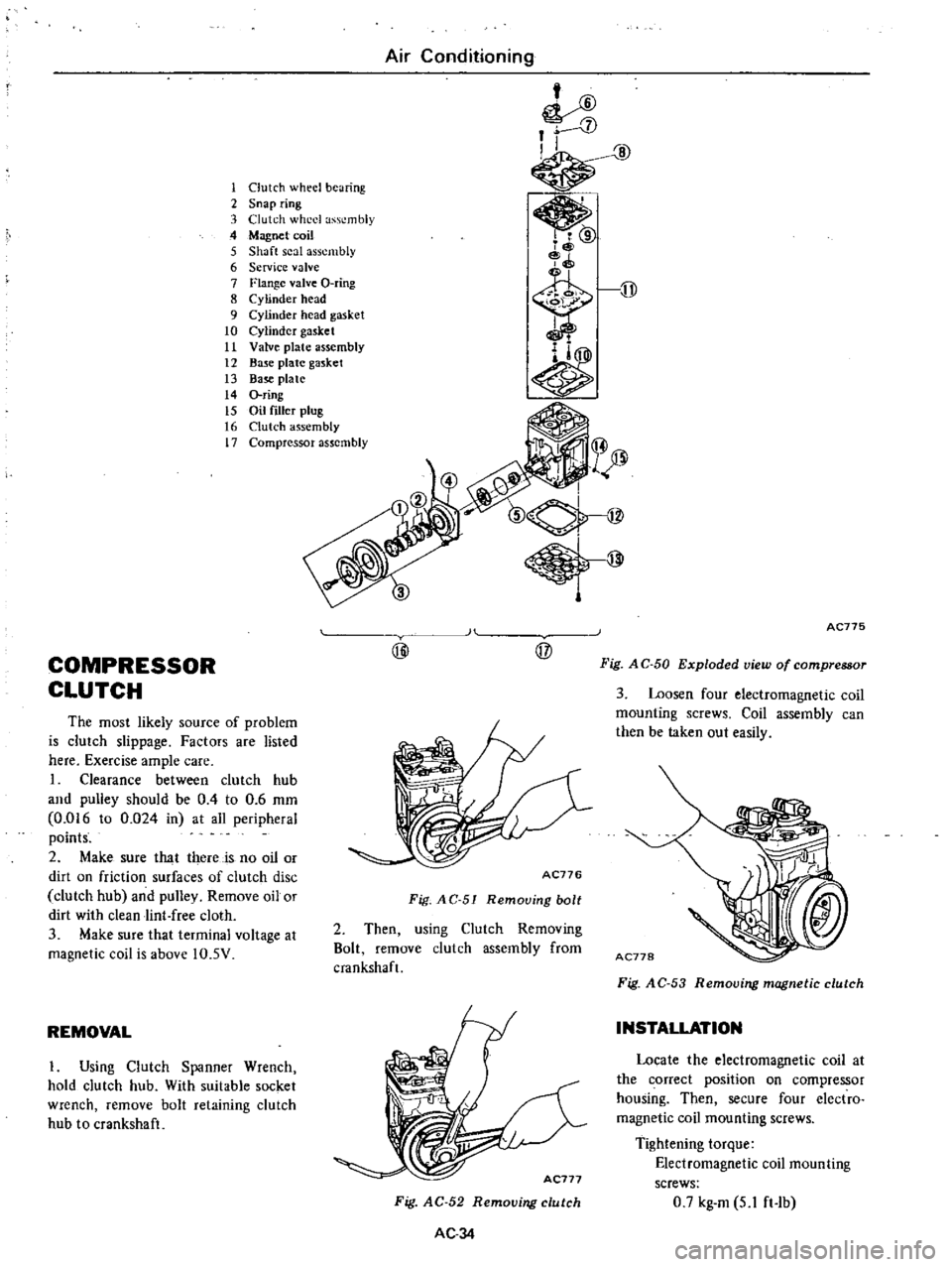
Air
Conditioning
1foo
1t
1
t7
LV
I
1
Clutch
wheel
bearing
2
Snap
ring
3
Clutch
wheel
assembly
4
Magnet
coil
5
Shaft
seal
assembly
6
Service
valve
7
Flange
valve
O
ring
8
Cylinder
head
9
Cylinder
head
gasket
10
Cylinder
gasket
11
Valve
plate
assembly
12
Base
plate
gasket
13
Base
plate
14
O
ring
15
Oil
filler
plug
16
Clutch
assembly
17
Compressor
assembly
COMPRESSOR
CLUTCH
The
most
likely
source
of
problem
is
clutch
slippage
Factors
are
listed
here
Exercise
ample
care
I
Clearance
between
clutch
hub
and
pulley
should
be
0
4
to
0
6
mm
0
016
to
0
024
in
at
all
peripheral
points
2
Make
sure
that
there
is
no
oil
or
dirt
on
friction
surfaces
of
clutch
disc
clutch
hub
and
pulley
Remove
oil
or
dirt
with
clean
lint
free
cloth
3
Make
sure
that
terminal
voltage
at
magnetic
coil
is
above
IO
5V
REMOVAL
I
Using
Clutch
Spanner
Wrench
hold
clutch
hub
With
suitable
socket
wrench
remove
bolt
retaining
clutch
hub
to
crankshaft
H
@
@
AC776
Fig
AC
51
Remouing
bolt
2
Then
using
Clutch
Removing
Bolt
remove
clutch
assembly
from
cmnkshaft
Fig
AC
52
Removing
clutch
AC34
AC775
Fig
A
C
50
Exploded
view
of
compressor
3
Loosen
four
electromagnetic
coil
mounting
screws
Coil
assembly
can
then
be
taken
out
easily
Fig
A
C
53
Removing
magnetic
clutch
INSTALLATION
Locate
the
electromagnetic
coil
at
the
correct
position
on
compressor
housing
Then
secure
four
electro
magnetic
coil
mounting
screws
Tightening
torque
Electromagnetic
coil
mounting
screws
0
7
kg
m
5
1
ft
Ib
Page 524 of 537
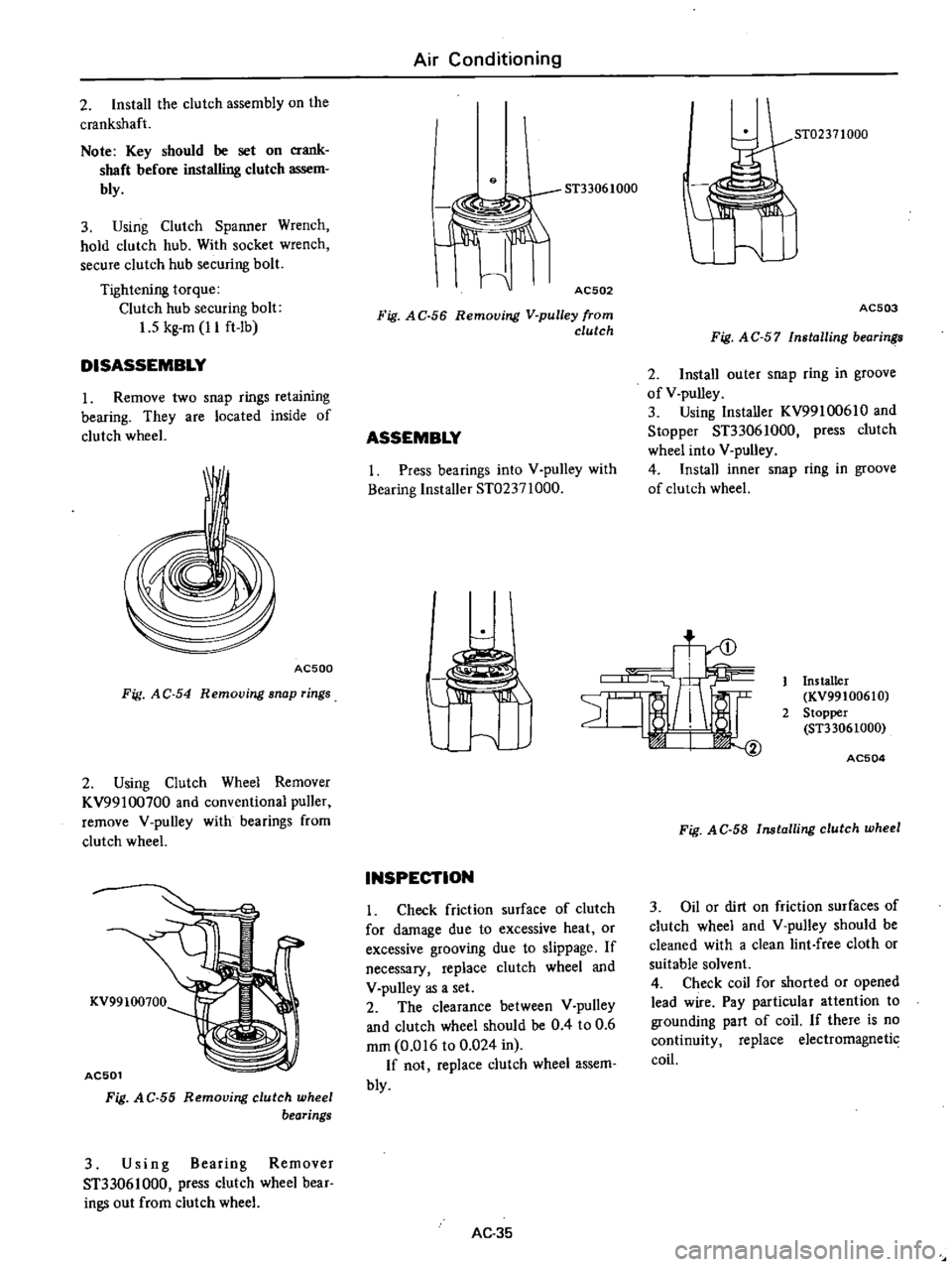
2
Install
the
clutch
assembly
on
the
crankshaft
Note
Key
should
be
set
on
crank
shaft
before
installing
clutch
assem
bly
3
Using
Clutch
Spanner
Wrench
hold
clutch
hub
With
socket
wrench
secure
clutch
hub
securing
bolt
Tightening
torque
Clutch
hub
securing
bolt
1
5
kg
m
II
ft
lb
DISASSEMBLY
1
Remove
two
snap
rings
retaining
bearing
They
are
located
inside
of
clutch
wheel
AC500
Fig
AC
54
Removing
snap
rings
2
Using
Clutch
Wheel
Remover
KV99100700
and
conventional
puller
remove
V
pulley
with
bearings
from
clutch
wheel
KV99100700
AC501
Fig
A
C
55
Removing
clutch
wheel
bearings
3
Using
Bearing
Remover
ST33061000
press
clutch
wheel
bear
ings
out
from
clutch
wheel
Air
Conditioning
9
AC502
Fig
AC
56
Removing
V
pulley
from
clutch
ASSEMBLY
I
Press
bearings
into
V
pulley
with
Bearing
Installer
ST02371000
ST02371000
AC503
Fig
A
C
57
Installing
bearin
2
Install
outer
snap
ring
in
groove
of
V
pulley
3
Using
Installer
KV99100610
and
Stopper
ST33061000
press
clutch
wheel
into
V
pulley
4
Install
inner
snap
ring
in
groove
of
clutch
wheel
t
INSPECTION
Check
friction
surface
of
clutch
for
damage
due
to
excessive
heat
or
excessive
grooving
due
to
slippage
If
necessary
replace
clutch
wheel
and
V
pulley
as
a
set
2
The
clearance
between
V
pulley
and
clutch
wheel
should
be
0
4
to
0
6
mm
0
016
to
0
024
in
If
not
replace
clutch
wheel
assem
bly
AC
35
Installer
KV99100610
2
Stopper
ST33061000
AC504
Fig
AC
58
Installing
clutch
wheel
3
Oil
or
dirt
on
friction
surfaces
of
clutch
wheel
and
V
pulley
should
be
cleaned
with
a
clean
lint
free
cloth
or
suitable
solvent
4
Check
coil
for
shorted
or
opened
lead
wire
Pay
particular
attention
to
grounding
part
of
coil
If
there
is
no
continuity
replace
electromagnetic
coil