tow DATSUN PICK-UP 1977 User Guide
[x] Cancel search | Manufacturer: DATSUN, Model Year: 1977, Model line: PICK-UP, Model: DATSUN PICK-UP 1977Pages: 537, PDF Size: 35.48 MB
Page 92 of 537
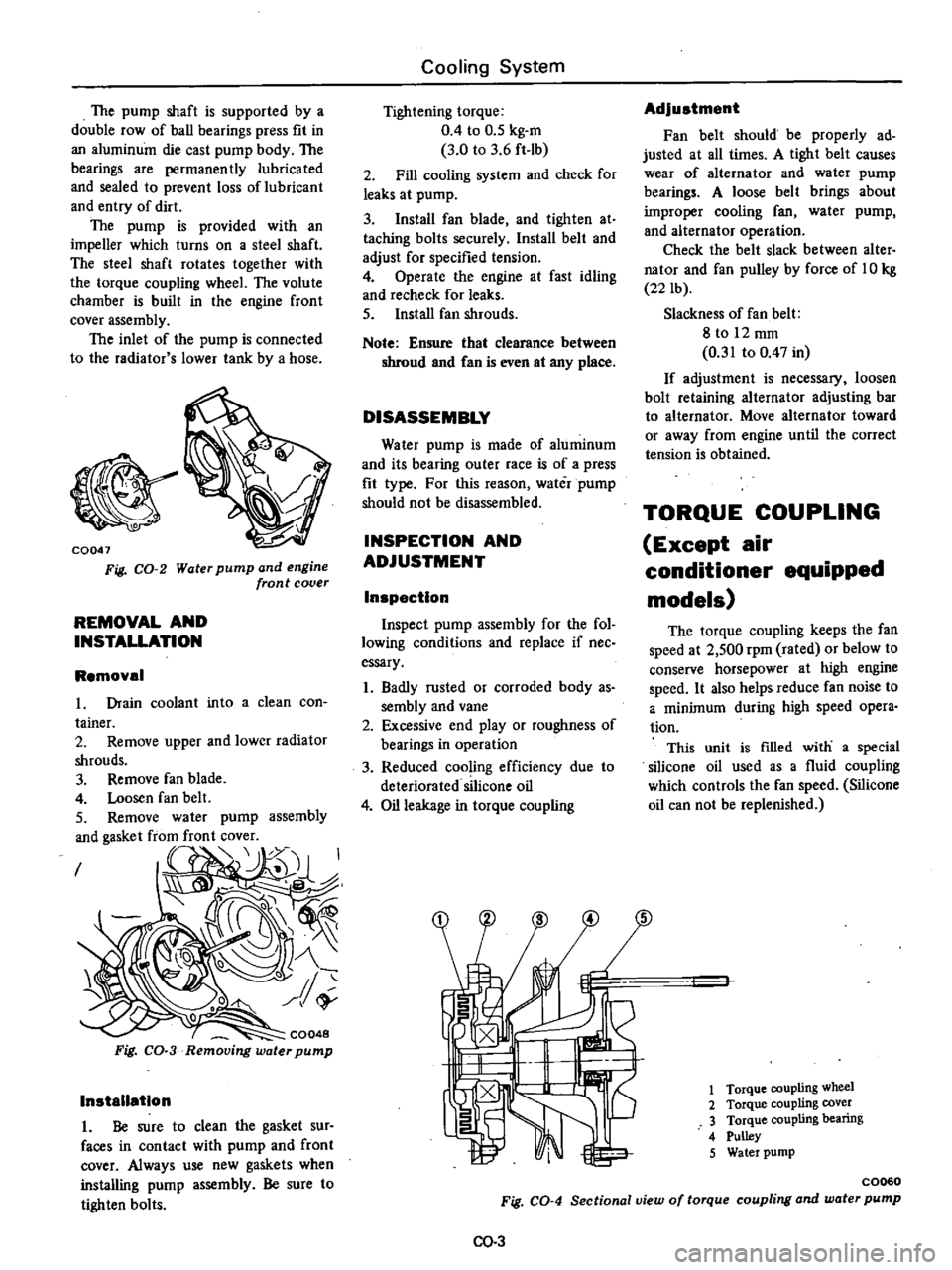
The
pump
shaft
is
supported
by
a
double
row
of
ball
bearings
press
fit
in
an
aluminum
die
cast
pump
body
The
bearings
are
permanently
lubricated
and
sealed
to
prevent
loss
of
lubricant
and
entry
of
dirt
The
pump
is
provided
with
an
impeller
which
turns
on
a
steel
shaft
The
steel
shaft
rotates
together
with
the
torque
coupling
wheeL
The
volute
chamber
is
built
in
the
engine
front
cover
assembly
The
inlet
of
the
pump
is
connected
to
the
radiator
s
lower
tank
by
a
hose
i
o
CQ047
Fig
CO
2
Water
pump
and
engine
front
cover
REMOVAL
AND
INSTALLATION
Removal
in
to
a
clean
con
assembly
I
CQ048
Fig
CO
3
Removing
water
pump
Installation
1
Be
sure
to
clean
the
gasket
sur
faces
in
contact
with
pump
and
front
cover
Always
use
new
gaskets
when
installing
pump
assembly
Be
sure
to
tighten
bolts
Cooling
System
Tightening
torque
0
4
to
0
5
kg
m
3
0
to
3
6
ft
lb
2
Fill
cooling
system
and
check
for
leaks
at
pump
3
Install
fan
blade
and
tighten
at
taching
bolts
securely
Install
belt
and
adjust
for
specified
tension
4
Operate
the
engine
at
fast
idling
and
recheck
for
leaks
5
Install
fan
shrouds
Note
Ensure
that
clearance
between
shroud
and
Can
is
even
at
any
place
DISASSEMBLY
Water
pump
is
made
of
aluminum
and
its
bearing
outer
race
is
of
a
press
fit
type
For
this
reason
water
pump
should
not
be
disassembled
INSPECTION
AND
ADJUSTMENT
Inspection
Inspect
pump
assembly
for
the
fol
lowing
conditions
and
replace
if
nee
essary
1
Badly
rusted
or
corroded
body
as
sembly
and
vane
2
Excessive
end
play
or
roughness
of
bearings
in
operation
3
Reduced
cooling
efficiency
due
to
deteriorated
silicone
oil
4
Oil
leakage
in
torque
coupling
Adjustment
Fan
belt
should
be
properly
ad
justed
at
all
times
A
tight
belt
causes
wear
of
alternator
and
water
pump
bearings
A
loose
belt
brings
about
improper
cooling
fan
water
pump
and
alternator
operation
Check
the
belt
slack
between
alter
nator
and
fan
pulley
by
force
of
10
kg
22
lb
Slackness
of
fan
belt
8
to
12
mm
0
31
to
0
47
in
If
adjustment
is
necessary
loosen
bolt
retaining
alternator
adjusting
bar
to
alternator
Move
alternator
toward
or
away
from
engine
until
the
correct
tension
is
obtained
TORQUE
COUPLING
Except
air
conditioner
equipped
models
The
torque
coupling
keeps
the
fan
speed
at
2
500
rpm
rated
or
below
to
conserve
horsepower
at
high
engine
speed
It
also
helps
reduce
fan
noise
to
a
minimum
during
high
speed
opera
tion
This
unit
is
filled
with
a
special
silicone
oil
used
as
a
fluid
coupling
which
controls
the
fan
speed
Silicone
oil
can
not
be
replenished
1
Torque
coupling
wheel
2
Torque
coupling
cover
3
Torque
coupling
bearing
4
Pulley
5
Water
pump
C0060
Fig
CO
4
Sectional
view
of
torque
coupling
and
water
pump
00
3
Page 174 of 537
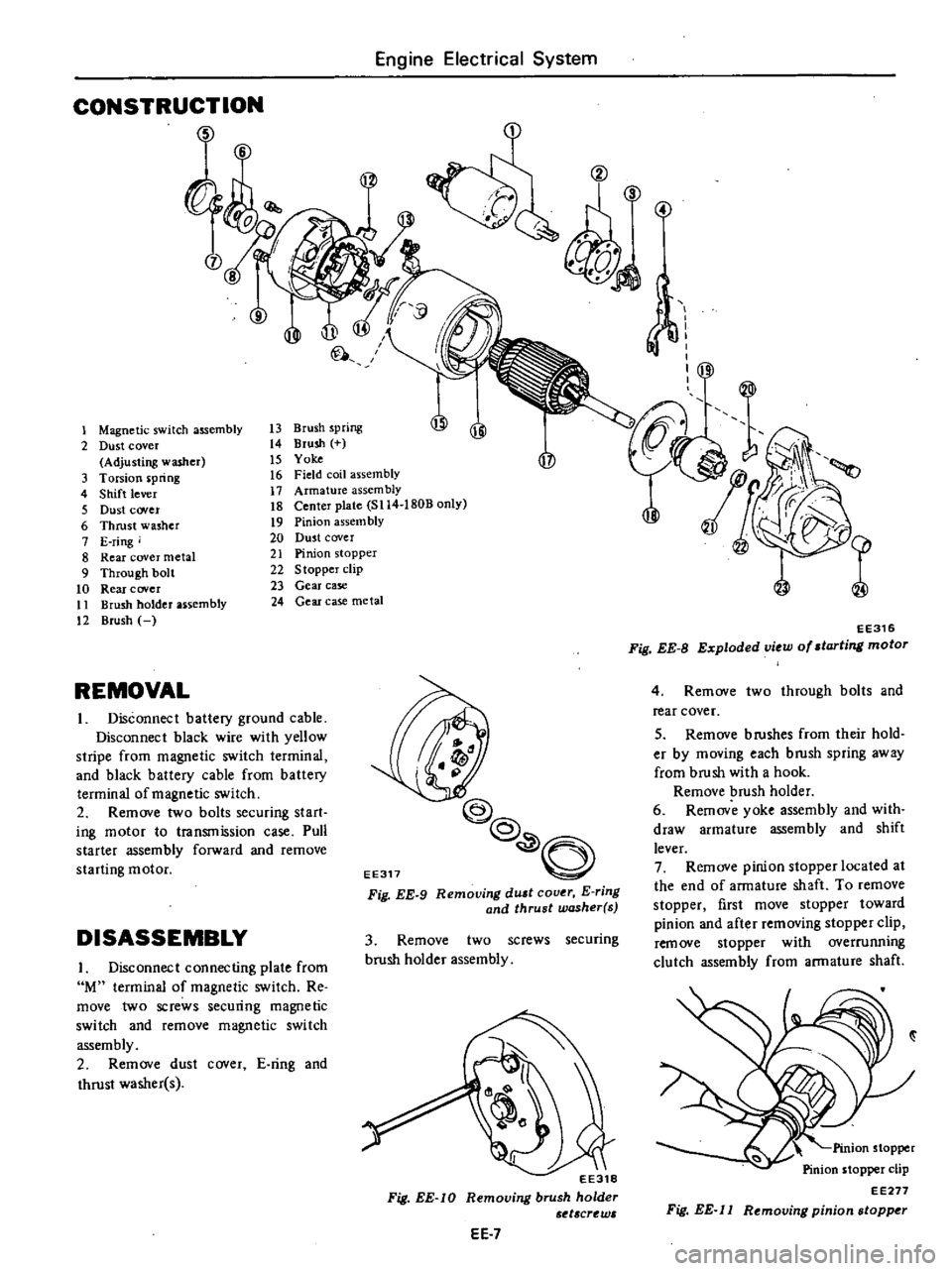
CONSTRUCTION
O
o
8
w
il
Engine
Electrical
System
V
1
Magnetic
switch
assembly
13
Brush
spring
jj
JI
2
Dust
cover
t4
Brush
Adjusting
washer
15
Yoke
P
3
Torsion
pring
t6
Field
coil
assembly
4
Shift
lever
17
Armature
assembly
5
Dust
cover
18
Center
plate
SI14
1808
only
6
Thrust
washer
19
Pinion
assem
bly
7
E
ring
20
Dust
cover
8
Rear
cover
metal
21
Pinion
stopper
9
Through
bolt
22
Stopper
clip
10
Rear
cover
23
Gear
case
tl
Brush
holder
assembly
24
Gear
case
metal
12
Brush
REMOVAL
Disconnect
battery
ground
cable
Disconnect
black
wire
with
yellow
stripe
from
magnetic
switch
terminal
and
black
battery
cable
from
battery
terminal
of
magnetic
switch
2
Remove
two
bolts
securing
start
ing
motor
to
transmission
case
Pull
starter
assembly
forward
and
remove
starting
motor
DISASSEMBLY
I
Disconnect
connecting
plate
from
M
terminal
of
magnetic
switch
Re
move
two
screws
securing
magnetic
switch
and
remove
magnetic
switch
assembly
2
Remove
dust
cover
E
ring
and
thrust
washer
s
EE317
@
@
O
Fig
EE
9
Remouing
dUlt
cover
E
ring
and
thrust
washer
s
3
Remove
two
screws
securing
brush
holder
assembly
EE318
Fig
EE
IO
Removing
brush
holder
d
crt
w
EE
7
S
4
f
I
jl
I
EE316
Fig
EE
B
Exploded
view
of
starting
motor
4
Remove
two
through
bolts
and
rear
cover
5
Remove
b
rushes
from
their
hold
er
by
moving
each
brush
spring
away
from
brush
with
a
hook
Remove
brush
holder
6
Remov
yoke
assembly
and
with
draw
armature
assembly
and
shift
lever
7
Remove
pinion
stopper
located
at
the
end
of
armature
shaft
To
remove
stopper
first
move
stopper
toward
pinion
and
after
removing
stopper
clip
remove
stopper
with
overrunning
clutch
assembly
from
armature
shaft
Pinion
stopper
Pinion
stopper
clip
EE277
Fig
EE
l1
Removing
pinion
stopper
Page 198 of 537
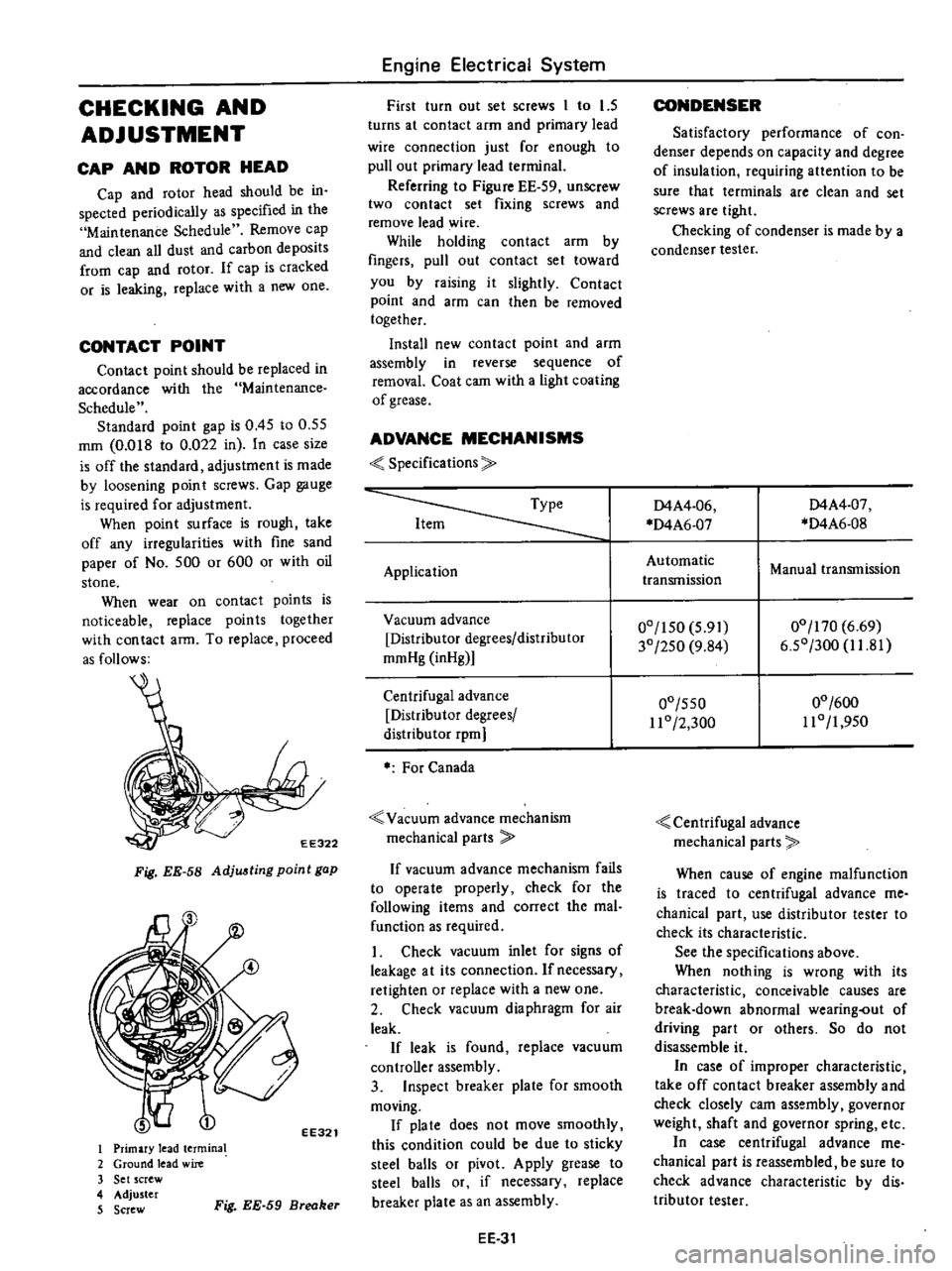
CHECKING
AND
ADJUSTMENT
CAP
AND
ROTOR
HEAD
Cap
and
rotor
head
should
be
in
spected
periodically
as
specified
in
the
Maintenance
Schedule
Remove
cap
and
clean
all
dust
and
carbon
deposits
from
cap
and
rotor
If
cap
is
cracked
or
is
leaking
replace
with
a
De
one
CONTACT
POINT
Contact
point
should
be
replaced
in
accordance
with
the
Maintenance
Schedule
Standard
point
gap
is
0
45
to
0
55
mm
O
OIS
to
0
022
in
In
case
size
is
off
the
standard
adjustment
is
made
by
loosening
point
screws
Gap
gauge
is
required
for
adjustment
When
point
surface
is
rough
take
off
any
irregularities
with
fine
sand
paper
of
No
500
or
600
or
with
oil
stone
When
wear
on
contact
points
is
noticeable
replace
points
together
with
contact
arm
To
replace
proceed
as
follows
EE322
Fig
EE
58
Adju
ting
point
gap
EE321
I
Primary
lead
termina
2
Ground
lead
wire
3
Set
screw
4
Adjuster
5
Screw
Fig
EE
59
Breaker
Engine
Electrical
System
First
turn
out
set
screws
1
to
1
5
turns
at
contact
arm
and
primary
lead
wire
connection
just
for
enough
to
pull
out
primary
lead
terminal
Referring
to
Figure
EE
59
unSCrew
two
contact
set
fixing
screws
and
remove
lead
wire
While
holding
contact
arm
by
fingers
pull
out
contact
set
toward
you
by
raising
it
slightly
Contact
point
and
afm
can
then
be
removed
together
Install
new
contact
point
and
arm
assembly
in
reverse
sequence
of
removal
Coat
cam
with
a
light
coating
of
grease
ADVANCE
MECHANISMS
Specifications
Application
Vacuum
advance
Distributor
degrees
distributor
mmHg
inHg
Centrifugal
advance
Distributor
degrees
distribu
tor
rpm
For
Canada
Vacuum
advance
mechanism
mechanical
parts
If
vacuum
advance
mechanism
fails
to
operate
properly
check
for
the
following
items
and
correct
the
mal
function
as
required
1
Check
vacuum
inlet
for
signs
of
leakage
at
its
connection
Ifnecessacy
retighten
or
replace
with
a
new
one
2
Check
vacuum
diaphragm
for
air
leak
If
leak
is
found
replace
vacuum
controller
assembly
3
Inspect
breaker
plate
for
smooth
moving
If
pia
te
does
not
move
smoothly
this
condition
could
be
due
to
sticky
steel
balls
or
pivot
Apply
grease
to
steel
balls
or
if
necessary
replace
breaker
plate
as
an
assembly
EE
31
CONDENSER
Satisfactory
performance
of
con
denser
depends
on
capacity
and
degree
of
insulation
requiring
attention
to
be
sure
that
terminals
are
clean
and
set
screws
are
tight
Checking
of
condenser
is
made
by
a
condenser
tester
D4A4
06
D4A6
07
D4A4
07
D4A6
0S
Automatic
transmission
Manual
transmission
00
150
5
91
30
250
9
S4
00
170
6
69
6
50
300
1I
S1
00
550
11
0
2
300
00
600
110
1
950
Centrifugal
advance
mechanical
parts
When
cause
of
engine
malfunction
is
traced
to
centrifugal
advance
me
chanical
part
use
distributor
tester
to
check
its
characteristic
See
the
specifications
above
When
nothing
is
wrong
with
its
characteristic
conceivable
causes
are
break
down
abnormal
wearing
out
of
driving
part
or
others
So
do
not
disassemble
it
In
case
of
improper
characteristic
take
off
contact
breaker
assembly
and
check
closely
cam
assembly
governor
weight
shaft
and
governor
spring
etc
In
case
centrifugal
advance
me
chanical
part
is
reassembled
be
sure
to
check
advance
characteristic
by
dis
tributor
tester
Page 202 of 537
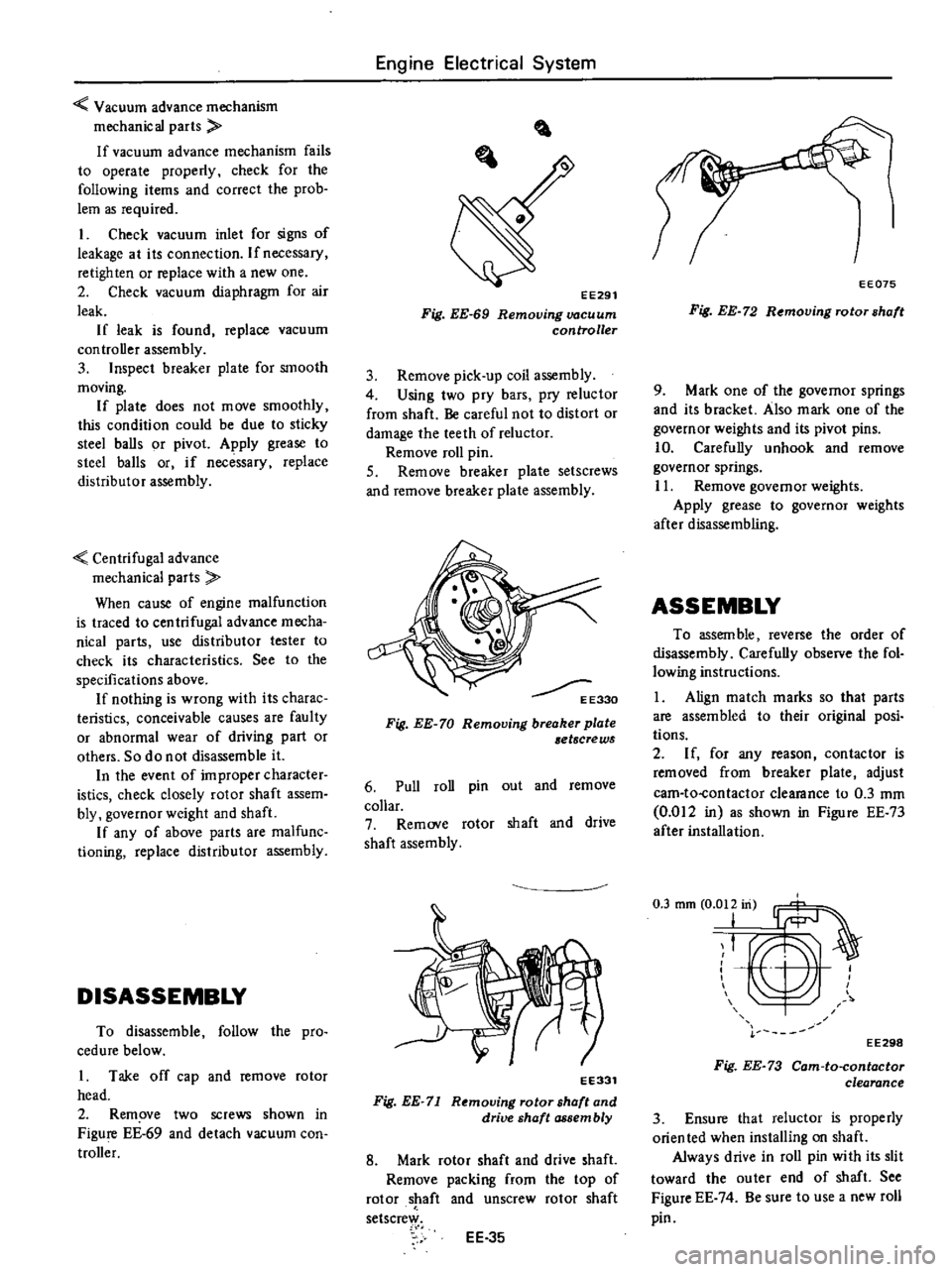
Vacuum
advance
mechanism
mechanical
parts
If
vacuum
advance
mechanism
fails
to
operate
properly
check
for
the
following
items
and
correct
the
prob
lem
as
required
1
Check
vacuum
inlet
for
signs
of
leakage
at
its
connection
If
necessary
retighten
or
replace
with
a
new
one
2
Check
vacuum
diaphragm
for
air
leak
If
leak
is
found
replace
vacuum
controller
assembly
3
Inspect
breaker
plate
for
smooth
moving
If
plate
does
not
move
smoothly
this
condition
could
be
due
to
sticky
steel
balls
or
pivot
Apply
grease
to
steel
balls
or
if
necessary
replace
distributor
assembly
Centrifugal
advance
mechanical
parts
When
cause
of
engine
malfunction
is
traced
to
centrifugal
advance
mecha
nical
parts
use
distributor
tester
to
check
its
characteristics
See
to
the
specifications
above
If
nothing
is
wrong
with
its
charac
teristics
conceivable
causes
are
faulty
or
abnormal
wear
of
driving
part
or
others
So
do
not
disassemble
it
In
the
event
of
improper
character
istics
check
closely
rotor
shaft
assem
bly
governor
weight
and
shaft
If
any
of
above
parts
are
malfunc
tioning
replace
distributor
assembly
DISASSEMBLY
To
disassemble
follow
the
pro
cedure
below
1
Take
off
cap
and
remove
rotor
head
2
Remove
two
screws
shown
in
Figure
EE
69
and
detach
vacuum
con
troller
Engine
Electrical
System
EE291
Fig
EE
69
Removing
vacuum
controller
3
Remove
pick
up
coil
assembly
4
Using
two
pry
bars
pry
reluctor
from
shaft
Be
careful
not
to
distort
or
damage
the
teeth
of
reluctor
Remove
roll
pin
S
Remove
breaker
plate
setscrews
and
remove
breaker
plate
assembly
E330
Fig
EE
70
Removing
breaker
plate
etscrews
6
Pull
roll
pin
out
and
remove
collar
7
Remove
rotor
shaft
and
drive
shaft
assembly
EE331
Fig
EE
71
Removing
rotor
shaft
and
drive
shaft
assembly
8
Mark
rotor
shaft
and
drive
shaft
Remove
packing
from
the
top
of
rotor
shaft
and
unscrew
rotor
shaft
setscrew
EE
35
EE075
Fig
EE
72
Removing
rotor
shaft
9
Mark
one
of
the
governor
springs
and
its
bracket
Also
mark
one
of
the
governor
weights
and
its
pivot
pins
10
Carefully
unhook
and
remove
governor
springs
11
Remove
governor
weights
Apply
grease
to
governor
weights
after
disassembling
ASSEMBLY
To
assem
ble
reverse
the
order
of
disassembly
Carefully
observe
the
fol
lowing
instructions
1
Align
match
marks
so
that
parts
are
assembled
to
their
original
posi
tions
2
If
for
any
reason
contactor
is
removed
from
breaker
plate
adjust
cam
to
contactor
clearance
to
0
3
mm
0
012
in
as
shown
in
Figure
EE
73
after
installation
T
EE298
Fig
EE
73
Cam
to
contactor
clearance
3
Ensure
that
reluctor
is
properly
orien
ted
when
installing
on
shaft
Always
drive
in
roll
pin
with
its
slit
toward
the
outer
end
of
shaft
See
Figure
EE
74
Be
sure
to
use
a
new
roll
pin
Page 220 of 537
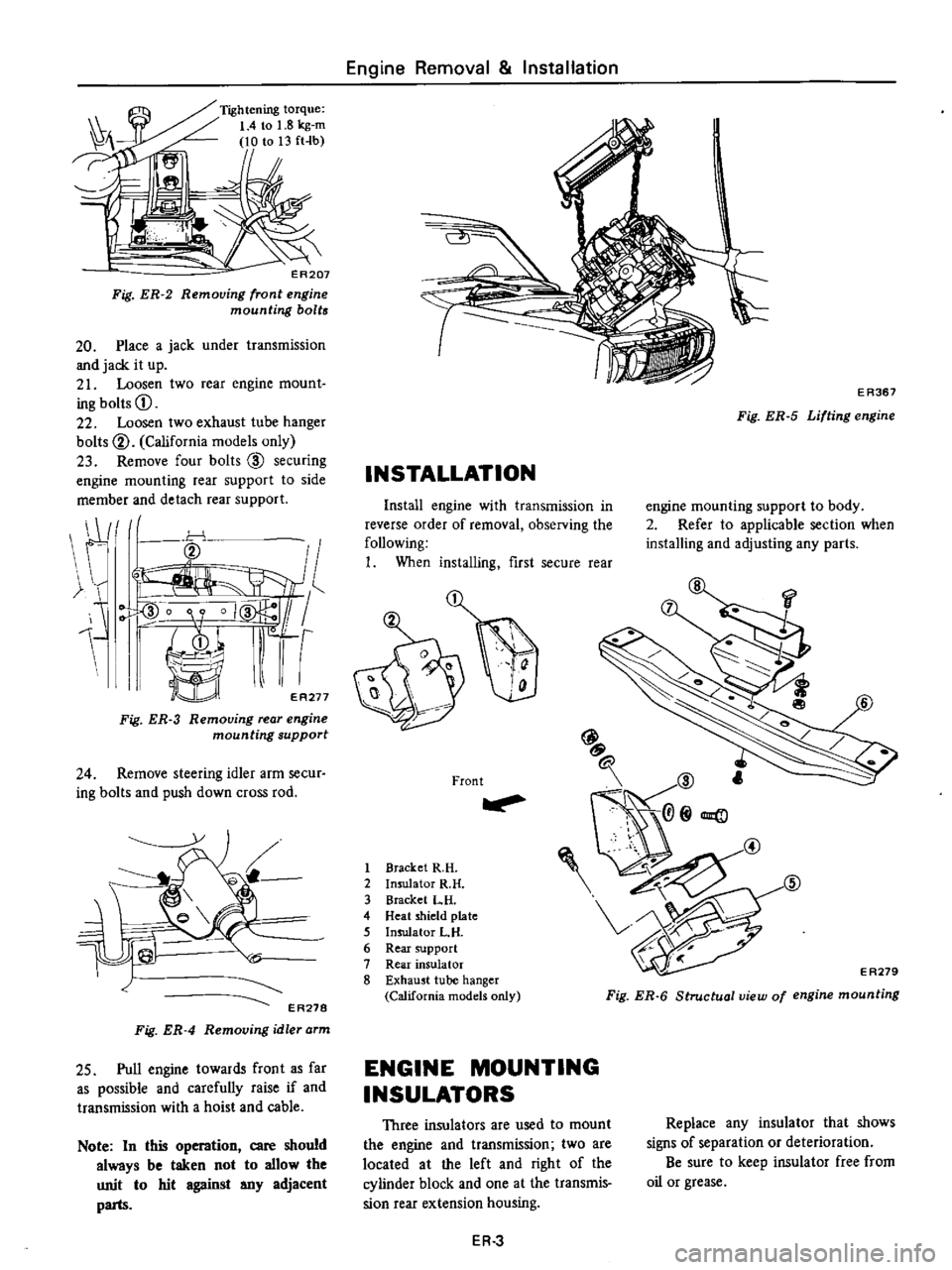
Fig
ER
2
ER207
Removing
front
engine
mounting
bolts
20
Place
a
jack
under
transmission
and
jack
it
up
21
Loosen
two
rear
engine
mount
ing
bolts
CD
22
Loosen
two
exhaust
tube
hanger
bolts
V
California
models
only
23
Remove
four
bolts
CID
securing
engine
mounting
rear
support
to
side
member
and
detach
rear
support
j
r
O
1
ER271
Fig
ER
3
Removing
rear
engine
mounting
support
24
Remove
steering
idler
arm
secur
ing
bolts
and
push
down
cross
rod
iC
EA278
Fig
ER
4
Removing
idler
arm
25
Pull
engine
towards
front
as
far
as
possible
and
carefully
raise
if
and
transmission
with
a
hoist
and
cable
Note
In
this
r
an
care
should
always
be
taken
not
to
allow
the
unit
to
hit
against
any
adjacent
parts
Engine
Removal
Installation
INSTALLATION
E
R367
Fig
ER
5
Lifting
engine
Install
engine
with
transmission
in
reverse
order
of
removal
observing
the
following
I
When
installing
first
secure
rear
2
Front
1
Bracket
R
H
2
Insulator
R
H
3
Bracket
LH
4
Heat
shield
plate
5
Insulator
L
H
6
Rear
support
7
Rear
insulator
8
Exhaust
tube
hanger
California
models
only
engine
mounting
support
to
body
2
Refer
to
applicable
section
when
installing
and
adjusting
any
parts
@
E
A279
Fig
ER
6
Structual
view
of
engine
mounting
ENGINE
MOUNTING
INSULATORS
Three
insulators
are
used
to
mount
the
engine
and
transmission
two
are
located
at
the
left
and
right
of
the
cylinder
block
and
one
at
the
transmis
sion
rear
extension
housing
Replace
any
insulator
that
shows
signs
of
separation
or
deterioration
Be
sure
to
keep
insulator
free
from
oil
or
grease
ER
3
Page 231 of 537
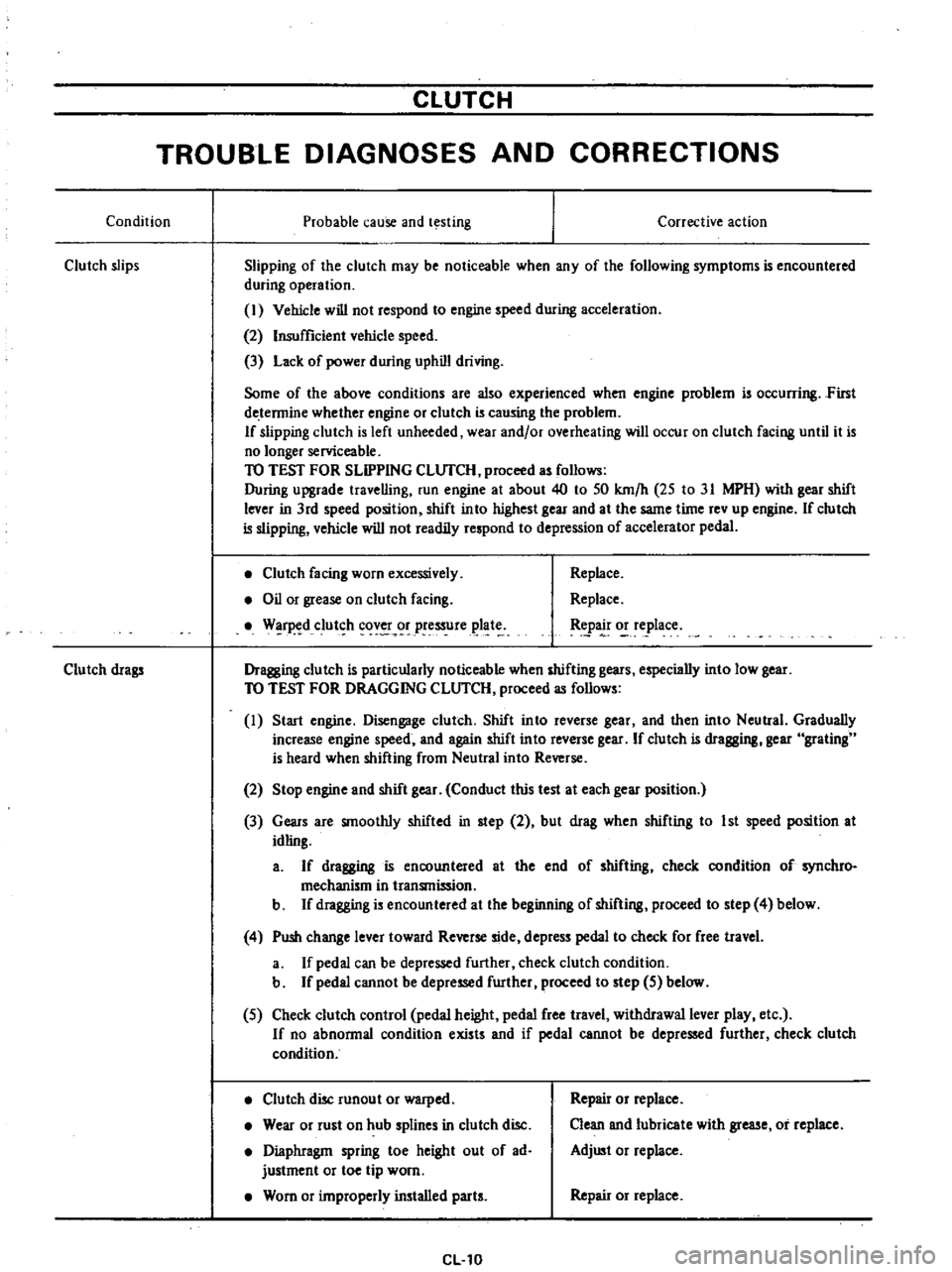
CLUTCH
TROUBLE
DIAGNOSES
AND
CORRECTIONS
Condition
Probable
cause
and
testing
Clutch
slips
Corrective
action
Slipping
of
the
clutch
may
be
noticeable
when
any
of
the
following
symptoms
is
encountered
during
operation
I
Vehicle
will
not
respond
to
engine
speed
during
acceleration
2
Insufficient
vehicle
speed
3
Lack
of
power
during
uphill
driving
Some
of
the
above
conditions
are
also
experienced
when
engine
problem
is
oc
urring
First
de
tennine
whether
engine
or
clutch
is
causing
the
problem
If
slipping
clutch
is
left
unheeded
wear
and
or
overheating
will
occur
on
clutch
facing
until
it
is
no
longer
serviceable
TO
TEST
FOR
SLIPPING
CLlJfCH
proceed
as
follows
During
upgrade
travelling
run
engine
at
about
40
to
50
km
h
25
to
31
MPH
with
gear
shift
lever
in
3rd
speed
position
shift
into
highest
gear
and
at
the
same
time
rev
up
engine
If
clutch
is
slipping
vehicle
will
not
readily
respond
to
depression
of
accelerator
pedal
Clutch
facing
worn
excessively
Oil
or
grease
on
clutch
facing
W
r
d
clut
h
cov
r
pressure
plat
Replace
Replace
tpa
o
e
lace
Dragging
clutch
is
particularly
noticeable
when
shifting
gears
especially
into
low
gear
TO
TEST
FOR
DRAGGING
CLlJfCH
proceed
as
follows
I
Start
engine
Disengage
clutch
Shift
into
reverse
gear
and
then
into
Neutral
Gradually
increase
engine
speed
and
again
shift
into
reverse
gear
If
clutch
is
dragging
gear
grating
is
heard
when
shifting
from
Neutral
into
Reverse
Clutch
drags
2
Stop
engine
and
shift
gear
Conduct
this
test
at
each
gear
position
3
Gears
are
smoothly
shifted
in
step
2
but
drag
when
shifting
to
1st
speed
position
at
idling
a
If
dragging
is
encountered
at
the
end
of
shifting
check
condition
of
synchro
mechanism
in
transmission
b
If
dragging
is
encountered
at
the
beginning
of
shifting
proceed
to
step
4
below
4
Push
change
lever
toward
Reverse
side
depress
pedal
to
check
for
free
travel
a
If
pedal
can
be
depressed
further
check
clutch
condition
b
If
pedal
cannot
be
depressed
further
proceed
to
step
5
below
5
Check
clutch
control
pedal
height
pedal
free
travel
withdrawal
lever
play
etc
If
no
abnonnal
condition
exists
and
if
pedal
cannot
be
depressed
further
check
clutch
condition
Clutch
disc
runout
or
warped
Wear
or
rust
on
hub
splines
in
clutch
disc
Diaphragm
spring
toe
height
out
of
ad
justment
or
toe
tip
worn
Worn
or
improperly
installed
parts
CL10
Repair
or
replace
Clean
and
lubricate
with
grease
or
replace
Adjust
or
replace
Repair
or
replace
Page 239 of 537
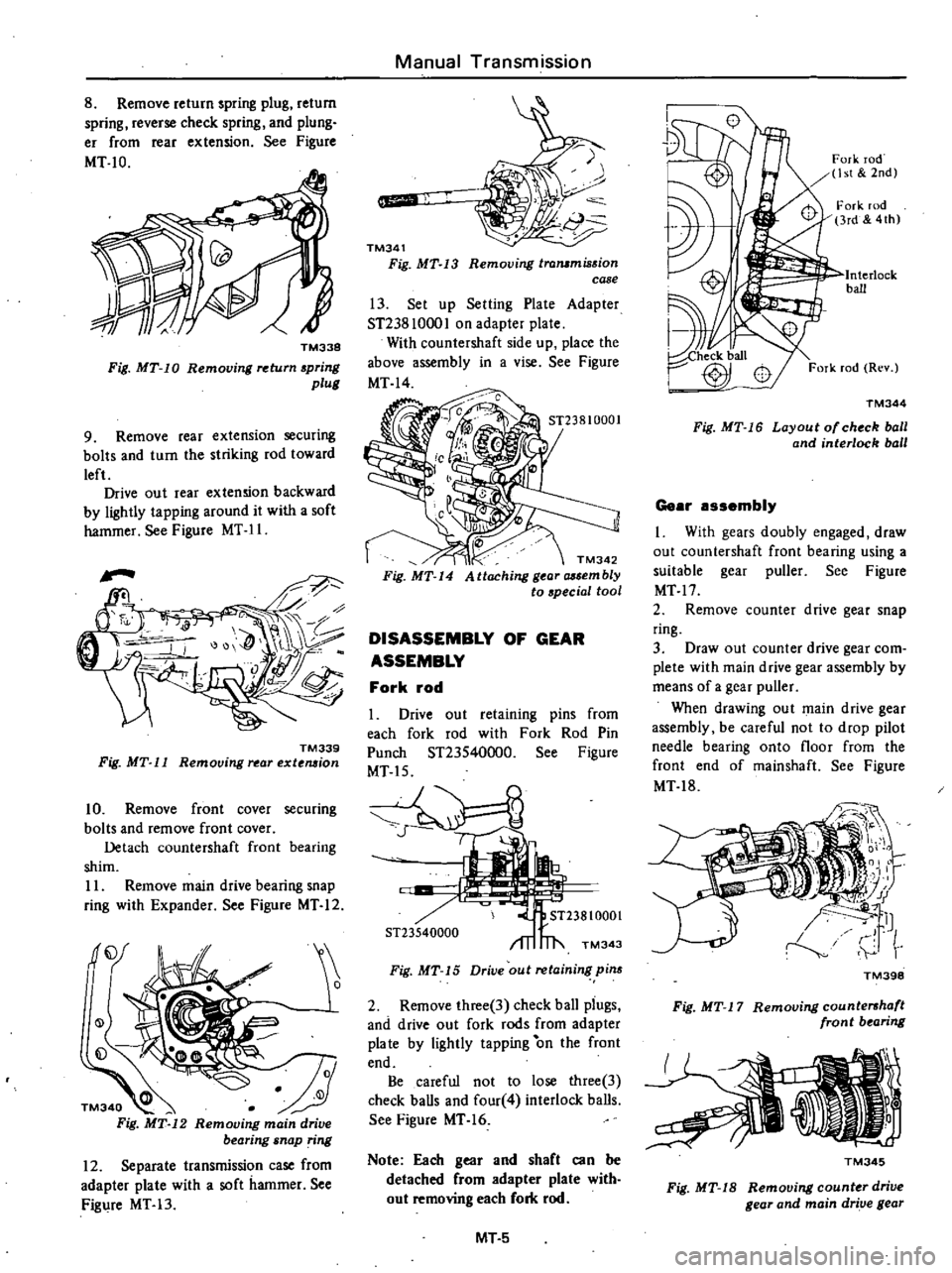
8
Remove
return
spring
plug
return
spring
reverse
check
spring
and
plung
er
from
rear
extension
See
Figure
MT
10
TM338
Fig
MT
10
Removing
return
spring
plull
9
Remove
rear
extension
securing
bolts
and
turn
the
striking
rod
toward
left
Drive
out
rear
extension
backward
by
lightly
tapping
around
it
with
a
soft
hammer
See
Figure
MT
11
TM339
Fig
MT
11
Removing
rear
extension
10
Remove
front
cover
securing
bolts
and
remove
front
cover
Detach
countershaft
front
bearing
shim
II
Remove
main
drive
bearing
snap
ring
with
Expander
See
Figure
MT
12
j
12
Separate
transmission
case
from
adapter
plate
with
a
soft
hammer
See
Figure
MT
13
Manual
Transmission
qJiiiiiI
TM341
Fig
MT
13
Removing
trammission
case
13
Set
up
Setting
Plate
Adapter
ST238
1000
I
on
adapter
plate
With
countershaft
side
up
place
the
above
assembly
in
a
vise
See
Figure
MT
14
TM342
Fig
MT
14
Attaching
l
or
mbly
to
special
tool
DISASSEMBLY
OF
GEAR
ASSEMBLY
Fork
rod
Drive
out
retaining
pins
from
each
fork
rod
with
Fork
Rod
Pin
Punch
ST23540000
See
Figure
MT
15
S
ST23540000
TM343
Fig
MT
15
Drive
out
retaining
pim
2
Remove
three
3
check
ball
piugs
and
drive
out
fork
rods
from
adapter
pia
te
by
lightly
tapping
on
the
front
end
Be
careful
not
to
lose
three
3
check
balls
and
four
4
interlock
balls
See
Figure
MT
16
Note
Each
gear
and
shaft
can
be
detached
from
adapter
plate
with
out
removing
each
fork
rod
MT
5
Fork
rod
ht
2nd
Interlock
ball
TM344
Fig
MT
16
Layout
o
ch
ck
boll
and
interlock
ball
Gear
assembly
I
With
gears
doubly
engaged
draw
out
countershaft
front
bearing
using
a
suitable
gear
puller
See
Figure
MT
17
2
Remove
counter
drive
gear
snap
ring
3
Draw
out
counter
drive
gear
com
plete
with
main
drive
gear
assembly
by
means
of
a
gear
puller
When
drawing
out
main
drive
gear
assembly
be
careful
not
to
drop
pilot
needle
bearing
onto
floor
from
the
front
end
of
mainshaft
See
Figure
MT
18
TM398
Fig
MT
17
Removing
countershaft
front
b
aring
TM345
Fig
MT
18
Removing
count
r
drive
gear
and
main
drive
gear
Page 265 of 537
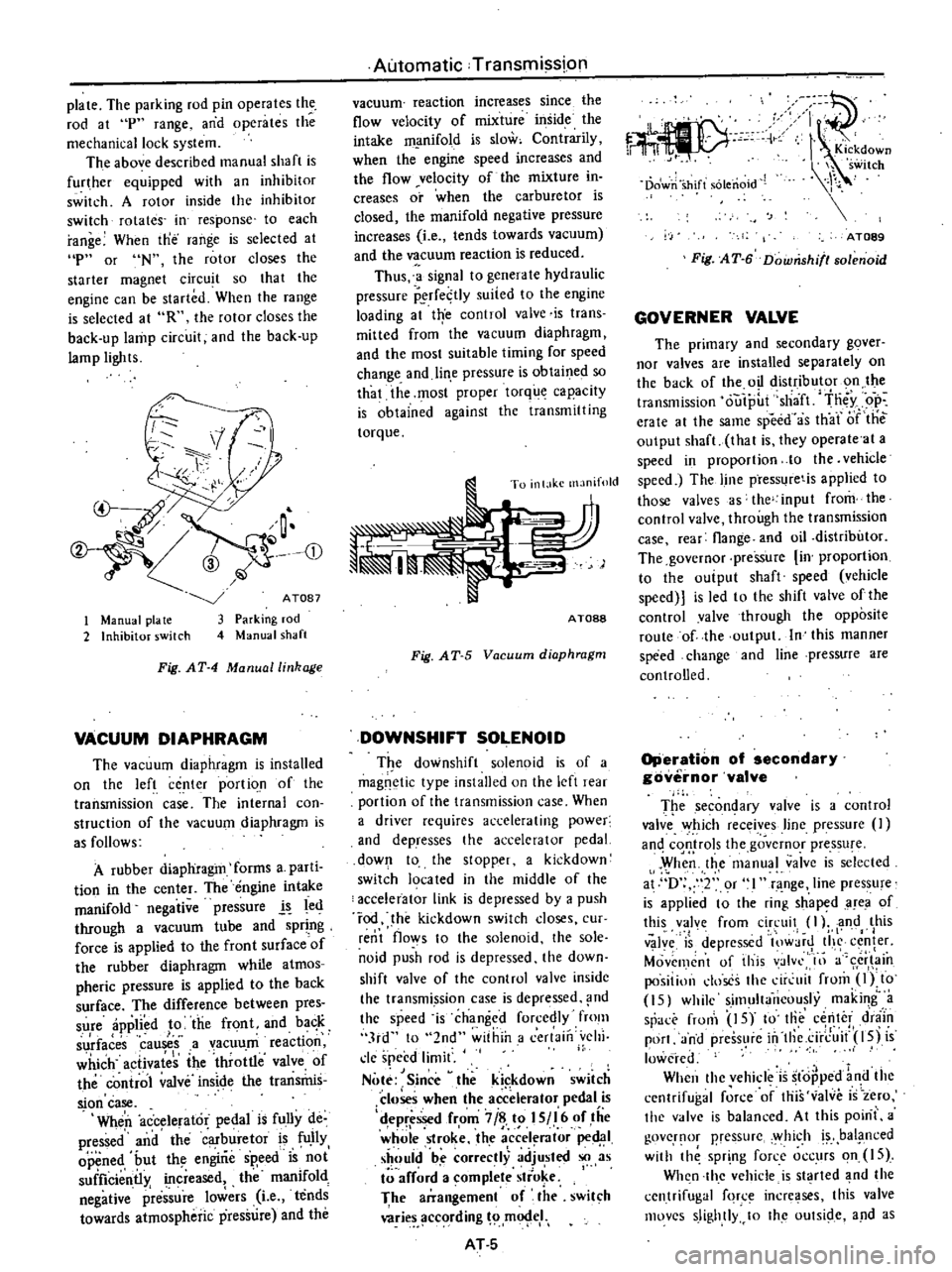
plate
The
parking
rod
pin
operates
the
rod
at
p
range
and
operates
the
mechanical
lock
system
The
above
described
manual
shaft
is
further
equipped
with
an
inhibitor
switch
A
rotor
inside
the
inhibitor
switch
rotates
in
response
to
each
range
When
tne
range
is
selected
at
p
or
N
the
rotor
closes
the
starter
magnet
circuit
so
that
the
engine
can
be
started
When
the
range
is
selected
at
R
the
rolor
closes
the
back
up
lamp
circuit
and
the
back
up
lamp
lights
CD
1
Manual
pia
te
2
Inhibitor
switch
ATOB7
Parking
rod
Manual
shaft
Fig
AT
4
Manual
linkage
VACUUM
DIAPHRAGM
The
vacuum
diaphragm
is
installed
on
the
left
center
portio
n
of
the
transmission
case
The
internal
con
struction
of
the
vacuum
diaphragm
is
as
follows
A
rubber
diaphragm
forms
a
parti
tion
in
the
center
The
engine
intake
manifold
negative
pressure
l
led
through
a
vacuum
tube
and
spring
force
is
applied
to
the
front
surfaceof
the
rubber
diaphragm
while
atmos
pheric
pressure
is
applied
to
the
back
surface
The
difference
between
pres
sure
applied
to
the
front
and
ba
K
I
surfaces
causes
a
vacuum
reactIOn
which
activates
the
throttle
valve
of
the
control
valve
inside
the
transrhis
sion
case
Wheri
accelerator
pedal
is
fully
de
pressed
and
the
buretor
is
fU
IIy
opened
but
th
engirie
sp
eed
is
not
suificientl
increased
the
manifold
negative
plre
sure
lowers
Le
tends
towards
atmospheric
pressure
and
the
Automatic
Transmission
vacuum
reaction
increases
since
the
flow
velocity
of
mixture
inside
the
intake
m
mifold
is
slow
Contrarily
when
the
engine
speed
increases
and
the
flow
velocity
of
the
mixture
in
creases
or
when
the
carburetor
is
closed
the
manifold
negative
pressure
increases
Le
tends
towards
vacuum
and
the
vacuum
reaction
is
reduced
Thus
a
signal
to
genera
Ie
hydraulic
pressure
P
rfe
tly
suited
to
the
engine
loading
at
trye
control
valve
is
trans
mitted
from
the
vacuum
diaphragm
and
the
most
suitable
timing
for
speed
change
and
lin
e
pressure
is
obtaine
so
that
the
most
proper
torque
capacity
is
obtained
against
the
transmitting
torque
To
inl
lkc
manifold
AT088
Fig
AT
5
Vacuum
diaphragm
DOWNSHIFT
SOLENOID
T
e
downshift
solenoid
is
of
a
magnetic
type
installed
on
the
left
re
r
portion
of
the
transmission
case
When
a
driver
requires
accelerating
power
and
dePresses
the
accelerator
pedal
down
to
the
stopper
a
kickdown
switch
19ca
ted
in
the
middle
of
the
accelerator
link
is
depressed
by
a
push
rod
he
kickdown
switch
doses
cur
rent
flows
to
the
solenoid
the
sole
noid
push
rod
is
depressed
the
down
shift
valve
of
the
control
valvc
insidc
the
transmi
ssion
case
is
depressed
nd
the
speed
is
changed
forcedly
fmm
3rd
to
2nd
within
a
cerlaill
vehi
cle
speed
limit
Note
Since
theki
kdown
switch
closes
when
the
accelerator
pedal
is
d
epr
ssed
from
7
i
t
I
S
I
6
of
tiie
whole
stroke
the
a
ccel
rator
ped
1
should
be
correctly
adjusted
so
as
arf
rd
a
omplete
stro
e
I
The
arrangement
of
the
swit
h
wries
ccording
m
eI
AT
S
c
C
r
11
I
Kickdown
h
switch
Dowri
shift
solenoid
AT089
Fig
AT
6
Downshifl80lenoid
GOVERNER
VALVE
The
primary
and
secondary
gover
nor
valves
are
installed
separately
on
the
back
of
the
oil
distributor
on
the
transmission
outp
t
sha
ft
tn
y
op
erate
al
the
same
speed
as
th
ar
iJf
tile
output
shaft
thai
is
they
operate
at
a
speed
in
proportion
10
the
vehicle
speed
The
line
press
retis
applied
to
those
valves
s
the
input
from
the
control
valve
through
the
transmission
case
rear
flange
and
oil
distributor
The
governor
pressure
in
proportion
to
the
ouiput
shaft
speed
vehicle
speed
is
led
to
the
shift
valve
ofthe
control
valve
through
the
opposite
route
of
the
output
In
this
manner
speed
change
and
line
pressure
are
controlled
Operation
of
secondary
governor
valve
T
e
secon
ary
valve
is
a
contro
valve
Y
hich
receives
line
pressure
an
cqQ
rols
the
governor
pressu
e
When
the
manual
valve
is
selected
at
D
2
or
l
range
line
pressure
is
applied
t
the
ri
g
sh
aped
area
of
this
valve
from
circuit
I
l
and
this
I
v
Jy
is
depressed
lOW
jr
tI
c
fer
Movemcnt
of
this
valvl
III
a
cr
in
positillll
doses
the
dr
uit
from
Olto
15
while
simultaneously
making
a
sr
rronl
IS
to
Iii
center
d
niin
port
and
press
re
in
tllc
ci
rJ
it
l5j
is
lowered
When
thc
vehicle
is
stopped
1
d
the
cenlrifugal
force
of
this
valve
is
zero
the
v
lve
is
balanced
At
this
poini
a
govcr
lOr
pressurc
y
hich
bal
i1
nced
with
th
spr
ng
force
occurs
on
IS
Wh
n
thc
vehicle
is
st
rted
nd
the
centrifugal
fqr
incre
ses
this
valve
movcs
slightly
10
Ihc
oUlSide
and
as
Page 266 of 537
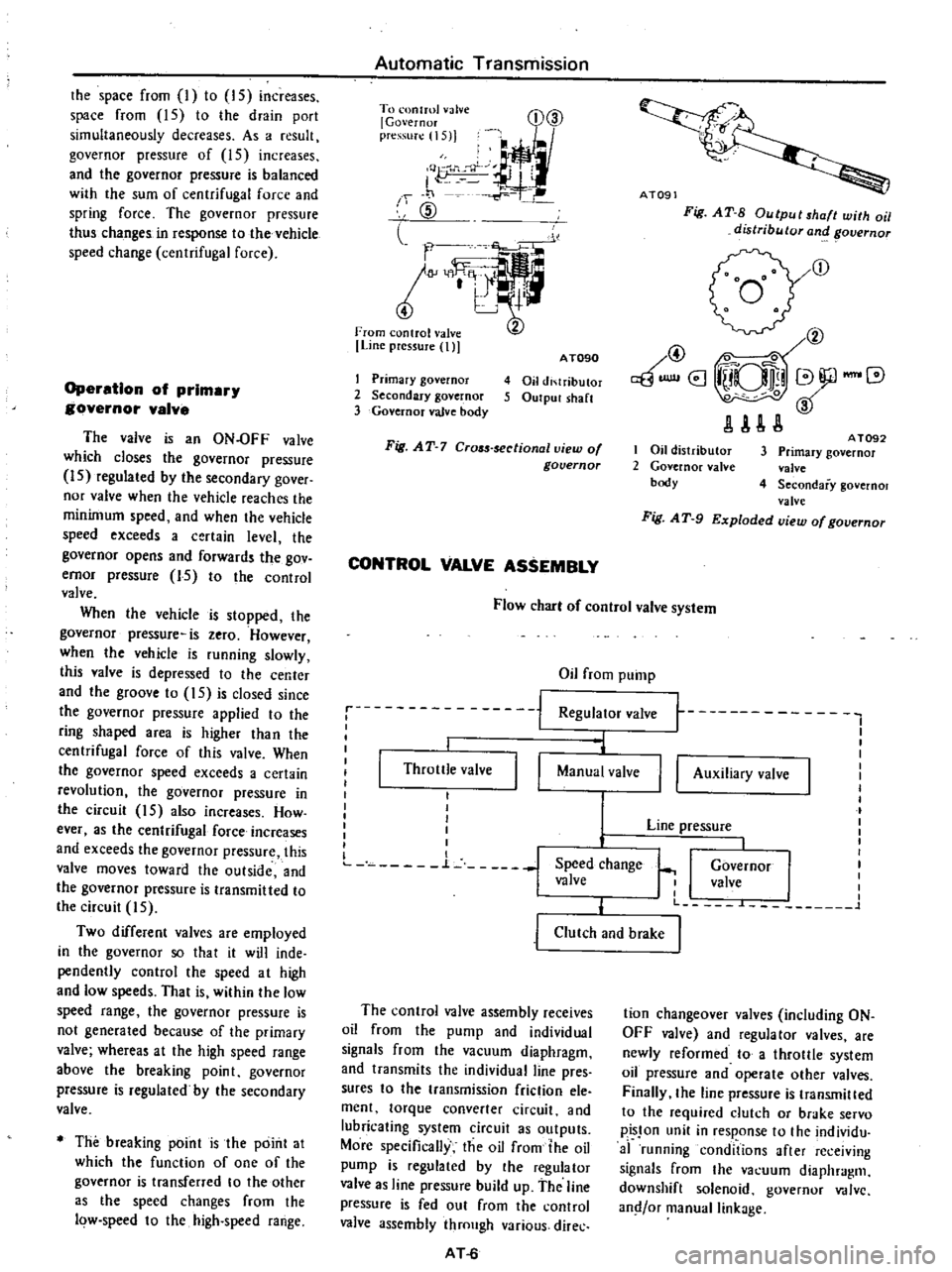
the
space
from
I
to
IS
increases
space
from
15
to
the
drain
port
simultaneously
decreases
As
a
resull
governor
pressure
of
15
increases
and
the
governor
pressure
is
balanced
with
the
sum
of
centrifugal
force
and
spring
force
The
governor
pressure
thus
changes
in
response
to
the
vehicle
speed
change
centrifugal
force
Operation
of
prlmar
governor
valve
The
valve
is
an
ON
OFF
valve
which
closes
the
governor
pressure
IS
regulated
by
the
secondary
gover
nor
valve
when
the
vehicle
reaches
the
minimum
speed
and
when
the
vehicle
speed
exceeds
a
certain
level
the
governor
opens
and
forwards
the
gov
ernor
pressure
15
to
the
control
valve
When
the
vehicle
is
stopped
the
governor
pressure
is
zero
However
when
the
vehicle
is
running
slowly
this
valve
is
depressed
to
Ihe
center
and
the
groove
to
15
is
closed
since
the
governor
pressure
applied
to
the
ring
shaped
area
is
higher
than
the
centrifugal
force
of
this
valve
When
the
governor
speed
exceeds
a
certain
revolution
the
governor
pressure
in
the
circuit
15
also
increases
How
ever
as
the
centrifugal
force
increases
and
exceeds
the
governor
pressure
this
valve
moves
toward
the
outside
and
the
governor
pressure
is
transmitted
to
the
circuil
5
Two
different
valves
are
employed
in
the
governor
so
that
it
will
inde
pendently
control
the
speed
at
high
and
low
speeds
That
is
within
the
low
speed
range
the
governor
pressure
is
not
generated
because
of
the
primary
valve
whereas
at
the
high
speed
range
above
the
breaking
point
governor
pressure
is
regulated
by
the
secondary
valve
The
breaking
point
is
the
point
at
which
the
function
of
one
of
the
governor
is
transferred
to
the
other
as
the
speed
changes
from
the
low
speed
to
the
high
speed
range
Automatic
Transmission
To
onlml
valve
l
Governor
pre
S1I
1I5
j
I
Q
J
J
f
1
1
CID
l
l
m
Line
pressure
t
D@
I
Primary
governor
2
Secondary
governor
3
Governor
valve
body
AT090
4
Oil
di
lributor
5
Output
sh
lft
Fig
AT
7
Cr05s
sectionallliew
of
governor
CONTROL
VALVE
ASSEMBLY
Ai09
Fig
AT
S
Output
shaft
with
oil
distributor
and
overnor
r
@
@
0
aBUlllI8
iUQlli
V
JlAU
I
Oil
distributor
2
Governor
nlve
body
A
T092
3
Primary
governor
valve
4
Secondary
governol
valve
Fig
A
T
9
Exploded
view
of
governor
Flow
cbar
of
control
valve
system
Oil
from
pump
Regulator
valve
1
I
i
j
Throttle
valve
I
I
l
Manual
valve
I
I
I
I
I
I
I
L
n
L
j
Speed
change
valve
I
I
t
t
I
I
I
I
I
I
Governor
I
I
valve
I
I
I
L
L
1
II
Auxiliary
valve
Line
pressure
j
Clutch
and
brake
The
control
valve
assembly
receives
oil
from
the
pump
and
individual
signals
from
the
vacuum
diaphragm
and
transmits
the
individual
line
pres
sures
to
the
transmission
friction
ele
ment
torque
converter
circuit
and
lubricating
system
circuit
as
outputs
More
specifically
the
oil
from
the
oil
pump
is
regulated
by
the
regulator
valve
as
line
pressure
build
up
the
line
pressure
is
fed
out
from
the
control
valve
assembly
through
various
direc
AT
6
tion
changeover
valves
including
ON
OFF
valve
and
regulator
valves
are
newly
reformed
to
a
throllle
system
oil
pressure
and
operate
other
valves
Finally
the
line
pressure
is
transmilled
to
the
required
dutch
or
brake
servo
pisJon
unit
in
response
to
the
individu
af
running
conditions
after
re
ejving
signals
from
the
va
uum
diaphragm
downshift
solenoid
governor
V
dlvc
and
or
manual
linkage
Page 268 of 537
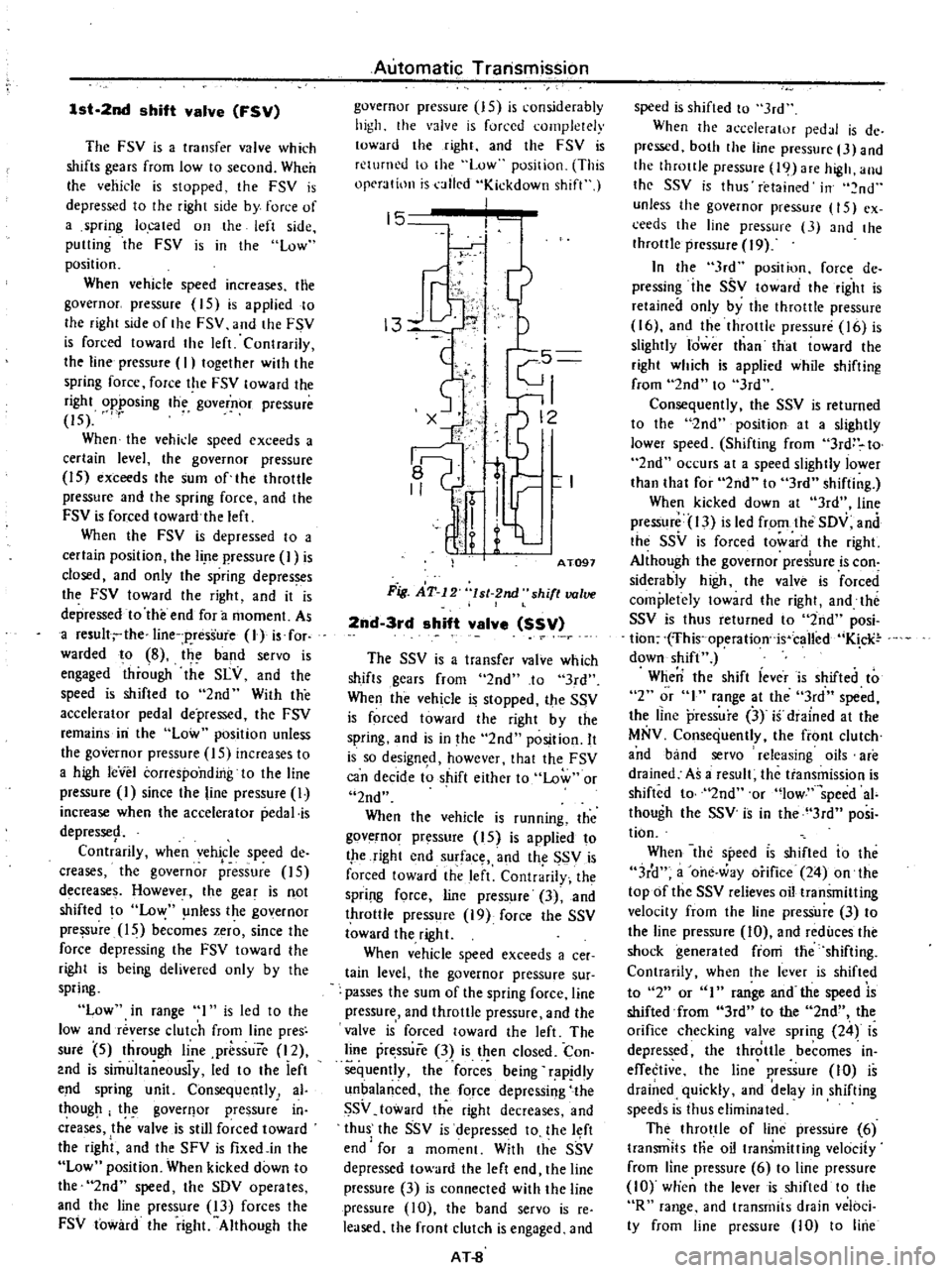
1st
2nd
shift
valve
FSV
The
FSV
is
a
transfer
valve
which
shifts
gears
from
low
to
second
When
Ihe
vehicle
is
stopped
the
FSV
is
depressed
to
the
right
side
by
force
of
a
spring
located
on
the
left
side
putting
the
FSV
is
in
the
low
position
When
vehicle
speed
increases
the
governor
pressure
15
is
applied
to
Ihe
right
side
of
the
FSV
and
the
FSV
is
forced
toward
the
left
Contrarily
the
line
pressure
I
togelher
with
the
spring
force
force
the
FSV
toward
the
right
opposing
the
governor
pressure
15
When
the
vehide
speed
exceeds
a
certain
level
the
governor
pressure
15
exceeds
the
sum
of
the
throttle
pressure
and
Ihe
spring
force
and
the
FSV
is
forced
toward
the
left
When
the
FSV
is
depressed
10
a
certain
position
the
lire
pressure
I
is
closed
and
only
the
spring
depresses
the
FSV
toward
the
right
and
it
is
depressed
to
the
end
for
a
moment
As
a
resull
the
line
p
ressure
lJ
is
for
warded
to
8
the
band
servo
is
engaged
through
the
SLY
and
the
speed
is
shifted
to
2nd
With
the
accelerator
pedal
depressed
the
FSV
remains
iIi
the
Low
position
unless
the
governor
pressure
IS
increases
to
a
high
leVel
corresponding
to
the
line
pressure
I
since
the
line
pressure
I
increase
when
the
accelerator
pedal
is
depresse9
Contrarily
when
vehicle
speed
de
creases
the
governor
pressure
15
decrease
Howeve
f
the
gear
is
not
shifted
to
Low
nless
the
governor
pressure
15
becomes
zero
since
the
force
depressing
the
FSV
toward
the
right
is
being
delivered
only
by
the
spring
Low
in
range
I
is
led
to
the
low
and
reverse
clutch
from
line
pres
sure
5
through
line
prbssure
12
2nd
is
simultaneousi
y
led
to
the
ieft
end
spring
unit
Consequently
al
thougp
the
goverflor
pressure
in
creases
the
valve
is
still
forced
toward
the
right
and
the
SFV
is
fixedjn
the
Low
position
When
kicked
down
to
the
2nd
speed
the
SDV
operates
and
the
line
pressure
13
forces
the
FSV
toward
the
right
Although
the
Automatic
Transmission
governor
pressure
15
is
considerably
high
the
valve
is
forced
completely
toward
the
right
and
the
FSV
is
returned
to
the
Low
position
This
operation
is
alled
Kickdown
shift
15
j
13
1
c5
I
0
t
r
I
I
q
1
AT091
Fig
AT
12
lsl
2nd
shift
valve
2nd
3rd
shift
valve
SSV
The
SSV
is
a
transfer
valve
which
shifts
gears
from
2nd
to
3rd
When
the
vehicle
is
stopped
the
SSV
is
forced
toward
the
right
by
the
spring
and
is
in
the
2nd
position
It
is
so
design
d
however
that
the
FSV
can
decide
to
shift
either
to
Low
or
2nd
When
the
vehicle
is
running
the
governor
pressure
15
is
applied
to
the
right
end
surface
and
th
SSV
is
forced
toward
the
left
Contrarily
the
Spri
l
force
line
pressure
3
and
throttle
press
re
19
force
the
SSV
toward
the
right
When
vehicle
speed
exceeds
a
cee
tain
level
the
governor
pressure
sur
passes
the
sum
of
the
spring
force
line
pressure
and
throttle
pressure
and
the
valve
is
forced
toward
the
left
The
line
pressure
3
is
then
closed
Con
sequently
the
forces
being
rapjdly
unbalanced
the
force
depressing
the
SSV
toward
the
right
decreases
and
thus
the
SSV
is
depressed
to
the
l
ft
end
for
a
moment
With
Ihe
SSV
depressed
toward
the
left
end
lhe
line
pressure
3
is
connected
with
the
line
pressure
10
the
band
servo
is
re
leased
the
front
clutch
is
engaged
and
AT
8
speed
is
shifted
to
3rd
When
the
accelerator
pedJI
is
de
prcssed
both
the
line
pressure
3
and
the
throttle
pressure
19
are
high
allll
the
SSV
is
thus
retained
in
nd
unless
the
governor
pressure
15
ex
ceeds
the
line
pressure
3
and
the
throttle
pressure
19
In
the
3rd
position
force
de
pressing
ihe
SSV
toward
the
right
is
retained
only
by
the
throttle
pressure
16
and
the
throttle
pressure
16
is
slightly
Idwer
than
that
toward
the
right
which
is
applied
while
shifting
from
2nd
to
3rd
Consequently
the
SSV
is
returned
to
the
2nd
position
at
a
slightly
lower
speed
Shifting
from
3rd
to
2nd
occurs
at
a
speed
slightly
lower
than
that
for
2nd
to
3rd
shifting
When
kicked
down
at
3rd
line
pressure
13
is
led
from
the
SDV
and
the
SSV
is
forced
toward
the
right
Although
the
governor
pres
ure
is
con
siderably
high
the
valve
is
forced
completely
loward
the
right
and
tht
SSV
is
thus
returned
to
2nd
posi
tion
fhis
operation
is
called
K
cli
down
shift
When
the
shift
iever
is
shifted
to
2
or
I
range
at
the
3rd
speed
the
line
pressure
3
if
diained
at
the
MNV
Consequently
the
front
clutch
and
band
servo
releasing
oils
are
drained
As
a
result
the
transmission
is
shifted
to
2nd
or
low
speed
ai
though
the
SSV
is
in
the
3rd
posi
tion
When
the
specd
IS
shifted
io
the
3r
1
a
one
way
orifice
24
on
the
topof
the
SSV
relieves
oil
transmitting
velocity
from
the
line
pressure
3
to
the
line
pressure
10
and
reduces
the
shock
generated
fioni
the
shifting
Contrarily
when
the
lever
is
shifted
to
2
or
I
range
and
the
speed
is
shifted
from
3rd
to
the
2nd
the
orifice
checking
valve
spring
24
is
depressed
the
throttle
becomes
in
effective
the
line
pressure
10
is
drained
quickly
and
delay
in
shifting
speeds
is
thus
eliminated
The
throttle
of
line
pressure
6
transmits
Hie
oil
transmitting
velocity
from
line
pressure
6
to
line
pressurc
10
wtien
the
lever
is
shifted
to
the
R
range
and
transmits
drain
veloci
ty
from
line
pressure
10
to
line