engine DATSUN PICK-UP 1977 Service Manual
[x] Cancel search | Manufacturer: DATSUN, Model Year: 1977, Model line: PICK-UP, Model: DATSUN PICK-UP 1977Pages: 537, PDF Size: 35.48 MB
Page 510 of 537
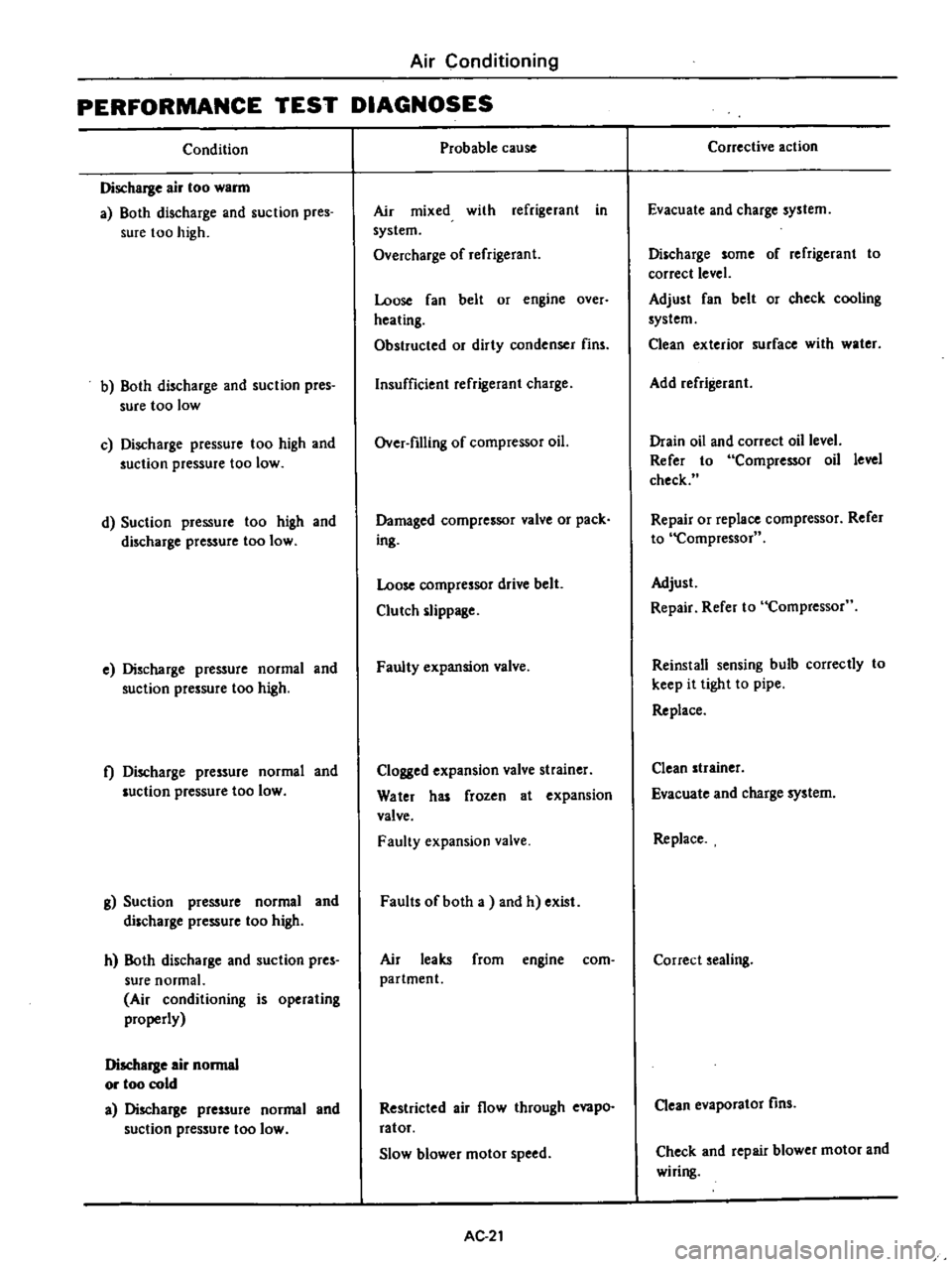
Air
Conditioning
PERFORMANCE
TEST
DIAGNOSES
Condition
Discharge
air
too
warm
a
Both
discharge
and
suction
pres
sure
too
high
b
Both
discharge
and
suction
pres
sure
too
low
c
Discharge
pressure
too
high
and
suction
pressure
too
low
d
Suction
pressure
too
high
and
discharge
pressure
too
low
e
Discharge
pressure
normal
and
suction
pressure
too
high
t
Discharge
pressure
normal
and
luction
pressure
too
low
g
Suction
pressure
normal
and
discharge
pressure
too
high
h
Both
discharge
and
suction
pres
sure
normal
Air
conditioning
is
operating
properly
Discharge
air
normal
or
too
cold
a
Discharge
pressure
normal
and
suction
pressure
too
low
Probable
cause
Air
mixed
with
refrigerant
in
system
Overcharge
of
refrigerant
Loose
fan
belt
or
engine
over
heating
Obstructed
or
dirty
condenser
fins
Insufficient
refrigerant
charge
Over
filling
of
compressor
oil
Damaged
compressor
valve
or
pack
ing
Loose
compressor
drive
belt
Clutch
slippage
Faulty
expansion
valve
Clogged
expansion
valve
strainer
Water
has
frozen
at
expansion
valve
Faulty
expansion
valve
Faults
of
both
a
and
h
exist
Air
leaks
from
engine
com
partment
Restricted
air
flow
through
evapo
ratof
Slow
blower
motor
speed
AC
21
Corrective
action
Evacuate
and
charge
system
Discharge
some
of
refrigerant
to
correct
level
Adjust
fan
belt
or
check
cooling
system
Clean
exterior
surface
with
water
Add
refrigerant
Drain
oil
and
correct
oil
level
Refer
to
Compressor
oil
level
check
Repair
or
replace
compressor
Refer
to
Compressor
Adjust
Repair
Refer
to
Compressor
Reinstall
sensing
bulb
correctly
to
keep
it
tight
to
pipe
Replace
Clean
strainer
Evacuate
and
charge
system
Replace
Correct
sealing
Clean
evaporator
fins
Check
and
repair
blower
motor
and
wiring
Page 512 of 537
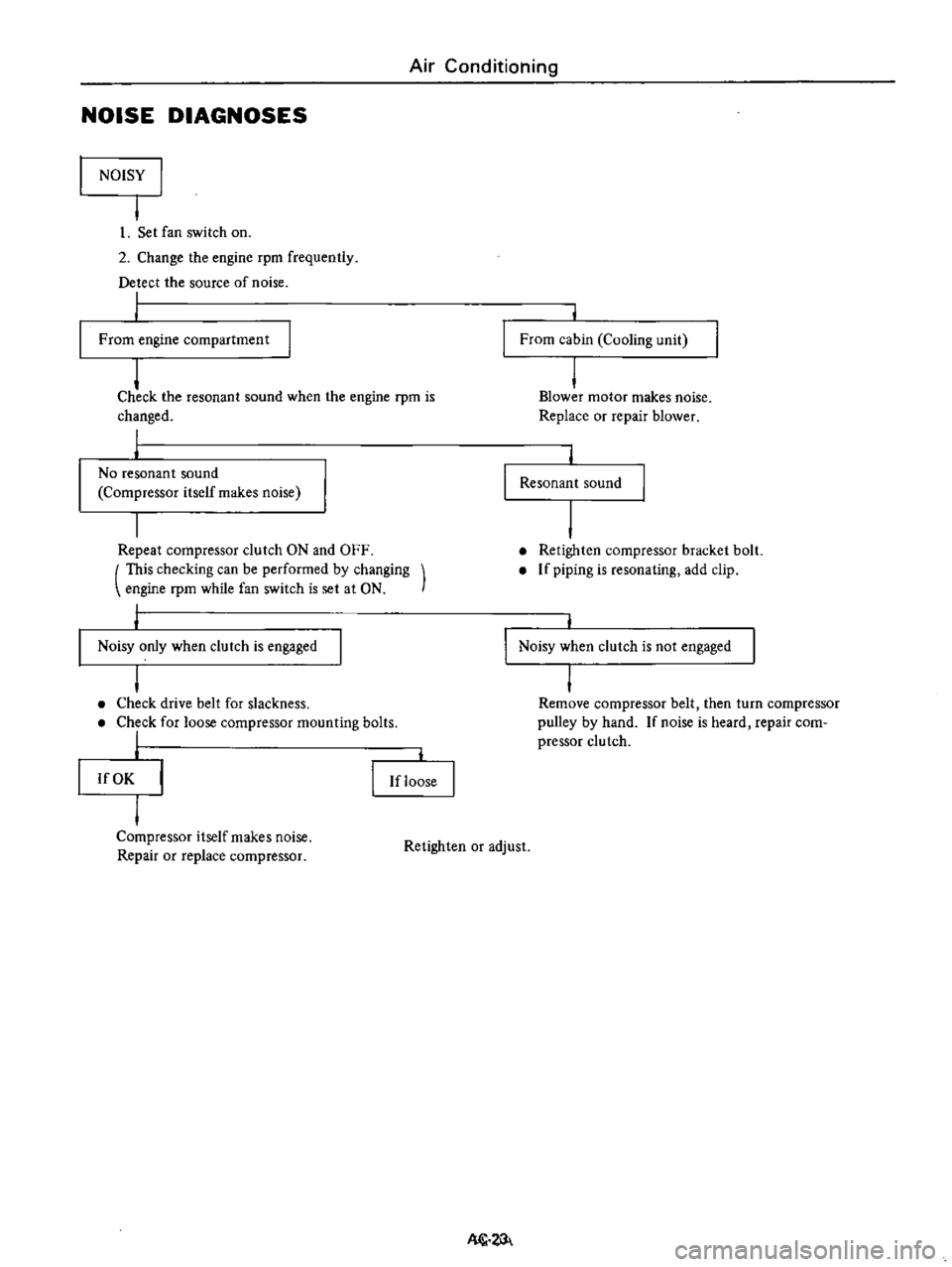
Air
Conditioning
NOISE
DIAGNOSES
NOISY
I
I
I
Set
fan
switch
on
2
Change
the
engine
rpm
frequently
Detect
the
source
of
noise
I
From
engine
compartment
From
cabin
Cooling
unit
j
Check
the
resonant
sound
when
the
engine
rpm
is
changed
I
I
No
resonant
sound
Compressor
itself
makes
noise
j
Blower
motor
makes
noise
Replace
or
repair
blower
Resonant
sound
Repeat
compressor
clutch
ON
and
OFF
This
checking
can
be
performed
by
changing
engine
rpm
while
fan
switch
is
set
at
ON
Retighten
compressor
bracket
bolt
If
piping
is
resonating
add
clip
Noisy
only
when
clutch
is
engaged
Noisy
when
clutch
is
not
engaged
I
Check
drive
belt
for
slackness
Check
for
loose
compressor
mounting
bolts
I
I
Remove
compressor
belt
then
turn
compressor
pulley
by
hand
If
noise
is
heard
repair
com
pressor
clutch
If
OK
If
loose
Compressor
itself
makes
noise
Repair
or
replace
compressor
Retighten
or
adjust
Nl1
Page 515 of 537
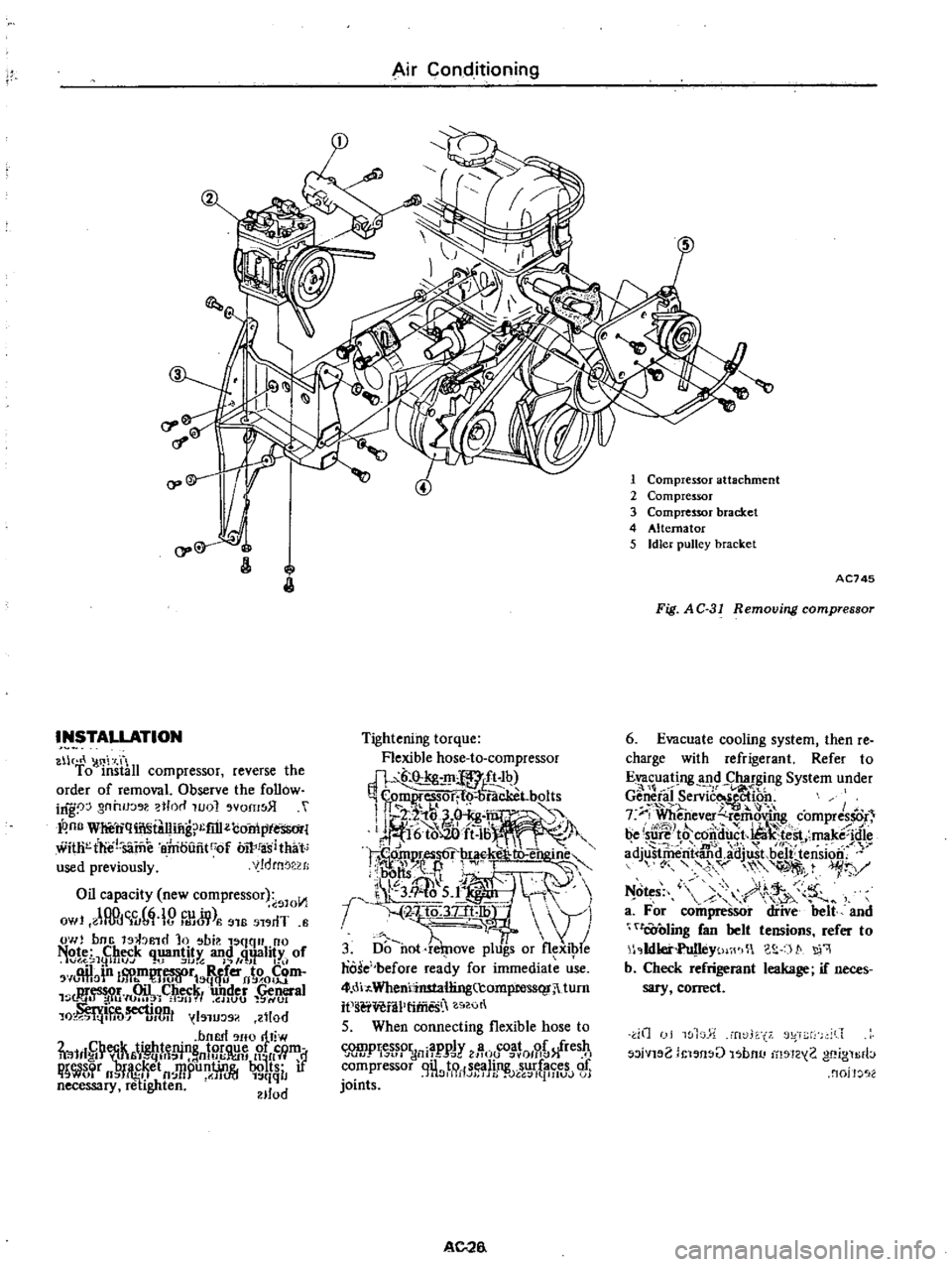
2
R
C7
c
L
PJJ
I
8
INSTALLATION
a
c
J
l
i
rp
To
install
compressor
reverse
the
order
of
removal
Observe
the
follow
ing
nhlJo
e
trorf
1001
vom
R
i
n3
Wheliqli
liiAniitg
fiil
l
in
pt
l
witlil
tiiel
sam
efuouiitITof
b11
1fasitlult
used
previously
v
d
rnl
2
Oil
capacity
new
compressor
O
910
1
owt
llllt
blj
f
H
w
s
013
5
rlT
s
0
111
boc
19
bB1rllo
bi2
qqll
no
e
l
bffik
kuanM
mpdi
x
of
Jli
oln
L
il
m
1IlffiiOrb
fler
ot
oldm
F
n
Cheo
f
undeF
r
n
al
1
aQ
r1tIU
Jt
t31
HClJI1
t
JIVU
i
rlUI
1o
ifm
ft
q
t
VI
31U
S
ltlod
bnM
UfO
l
W
kldf
CJiJi
ti
WIf
nl
L
llil
g
ncn
d
oressor
M
et
illpuntinl
botts
if
l9Wul
fb
i
l
fI
I
l
1Ttio
l
qqlJ
necessary
re
Ighten
I
d
210
Air
Conditioning
Tightening
torque
Flexible
hose
to
compressor
dl
t
kg
J
l
IQ
1
Tf
es
oriti
ra
Lbolts
IbP
fo
o15g
m
J
r
f6i
o
20
i
il
f
J
rt
I
r
aGket
engine
Dons
1
1
0
1
1
3
16
5
l11fd
1l
V
f
42
3
3U
llif
Yl
I
u
y
j
3
D
not
remove
IJgs
orflexibie
1i6
e
before
ready
for
immediate
use
4l
di
Wheniiinstallingccomptess
i
turn
it
serWfiPtiffies
SlOt
5
When
connecting
flexible
hose
to
9mPr
ssor
apD
v
a
coat
of
Hfresh
JU
UI
l1Il
t
2
JIUU
uOHltl
r
fl
compressor
0
1
to
fs
aHn
lurfaces
of
1n
1l11
JJ
J
f
PJU
Ht
UlUJ
jJ
joints
AC
26
5
1
Compressor
attachment
2
Compressor
3
Compressor
bracket
4
AHernator
5
Idler
pulley
bracket
AC745
Fig
AC
31
Removing
compressor
6
Evacuate
cooling
system
then
re
charge
with
refrigerant
Refer
to
Evacuating
and
Charging
System
under
l
r
Gen
efal
Servic
ectioo
f
iI
t
7
F
Whenever
remoV
J
compres
r
be
su
J
t8
C6itiu
t
Ua
t
st
make
idie
mV
i
1rJ
adjustril
rit
and
adjwt
beJf
tension
yv
1
r
Y
N
o
s
9
r
h
v
a
For
compressor
diive
belt
and
tOoling
fan
belt
tensions
refer
to
1
Ildlet
Yt
j
WI
c
S
t
q
b
Cheok
refrigerant
leakage
if
neces
sary
correct
dO
I
wl
Tw
l
rt
f
r2
iVl
2
i
l
n
U
l
bnu
1
1Z
2
gf
ign
rb
nojJ
2
Page 516 of 537
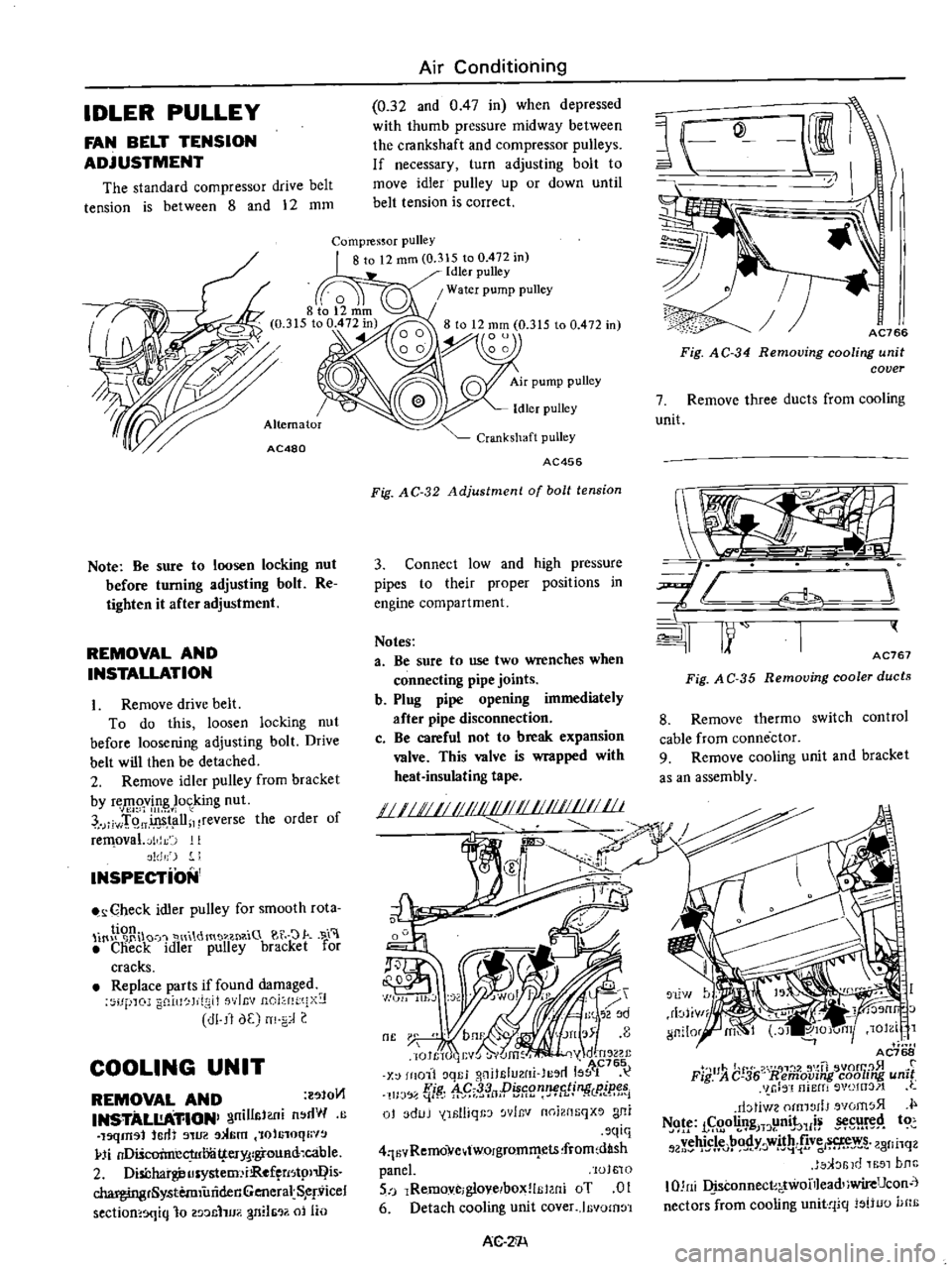
IDLER
PULLEY
FAN
BELT
TENSION
ADJUSTMENT
The
standard
compressor
drive
belt
tension
is
between
8
and
12
mm
AC480
Note
Be
sure
to
loosen
locking
nut
before
turning
adjusting
bolt
Re
tighten
it
after
adjustment
REMOVAL
AND
INSTALLATION
Remove
drive
belt
To
do
this
loosen
locking
nut
before
loosening
adjusting
bolt
Drive
belt
will
then
be
detached
2
Remove
idler
pulley
from
bracket
by
r
J1e
vM
or
king
nut
jiwT
9ff
t
llil
reverse
the
order
of
rerr
oval
jldJ
1
t
Jldr
J
I
INSPECTiON
Oheck
idler
pulley
for
smooth
rota
tion
G
0
llfHt
H
Y
d
H
u
t
1
W
n
l
ot
Jrk
H
l
Check
i
ler
pulley
bracket
for
cracks
Replace
arts
iffound
damaged
c
f
lOJ
gD
IlI
J
l
gtt
flvlnv
nOj
IH
q
g
cll
dE
m
J
COOLING
UNIT
REMOVAL
AND
oM1
INSTALl
A
1lIONI
gnillslUli
n
dW
C
19qm91
crft
llU2
3
6rn
f01
Gl0ql
pj
nDiScoimecprlY
i
ferY
lgroUR
hable
2
Disbhargiou
y
tem
iRefrflsll
Qis
chargingrSystemiillidenGeneral
S
ervicel
sectiom5qiq
10
2
9
fl
1U
n
1Ii
2
oj
liD
Air
Conditioning
0
32
and
0
47
in
when
depressed
with
thumb
pressure
midway
between
the
crankshaft
and
compressor
pulleys
If
necessary
turn
adjusting
bolt
to
move
idler
pulley
up
or
down
until
belt
tension
is
correct
Idler
pulley
Crankshaft
pulley
AC456
Fig
AC
32
Adjustment
of
bolt
tension
3
Connect
low
and
high
pressure
pipes
to
their
proper
positions
in
engine
compartment
Notes
3
Be
sure
to
use
two
wrenches
when
connecting
pipe
joints
b
Plug
pipe
opening
immediately
after
pipe
disconnection
c
Be
careful
not
to
break
expansion
valve
This
valve
is
wrapped
with
heat
insulating
tape
0
J
JWu
J
1
2
ld
m
bm
Ufl
J51
8
I
1
lEldgJ
v
Jwm
j
y
d
n
l2u
1
C765
X
fIlO
1i
qJ
j
gnjlcfu2fIJ
lc
rf
1551
1UJ
flip
1h
tqnPfffi2n
Wfi
i
V1c
ip
j
at
3duJ
lsIliqr
J
wlr
v
n
irWfiqX
ani
qiq
4q
v
Remo
e
tworgromll
ets
from
dash
panel
lots
n
5
lRemove
glovelbox
lBl
n1
oT
0
6
Detach
cooling
unit
cover
Icyom
n
AC
ZA
AC766
Fig
AC
34
Removing
cooling
unit
cover
7
Remove
three
ducts
from
cooling
unit
i
j
l
I
11
AC767
Fig
A
C
35
Removing
cooler
ducts
8
Remove
thermo
switch
control
cable
from
conne
ctor
9
Remove
cooling
unit
and
bracket
as
an
assembly
J
t
AC768
F
lIJAh
Cr
P
3
6
R
1
7
fi
vorr
l
l51
r
Ig
emo
vmg
coo
mg
um
r
n
I1iBITJ
0HJ
Jl
t
rbtivl2
Ofm
IIfj
wom
51
f
H
f
L
ol
IJgjjJpn
1I
SH
tc
vehicle
bn
y
with
five
rews
q
2tl
G
i
O
r
Jv
a8f1l1
J
a
I
ld
1
51
b
nc
IOJni
QisconnecEf
twonleadliwif
eUcon
1
nectars
from
cooling
unitqiq
s
iuo
UHf
Page 518 of 537
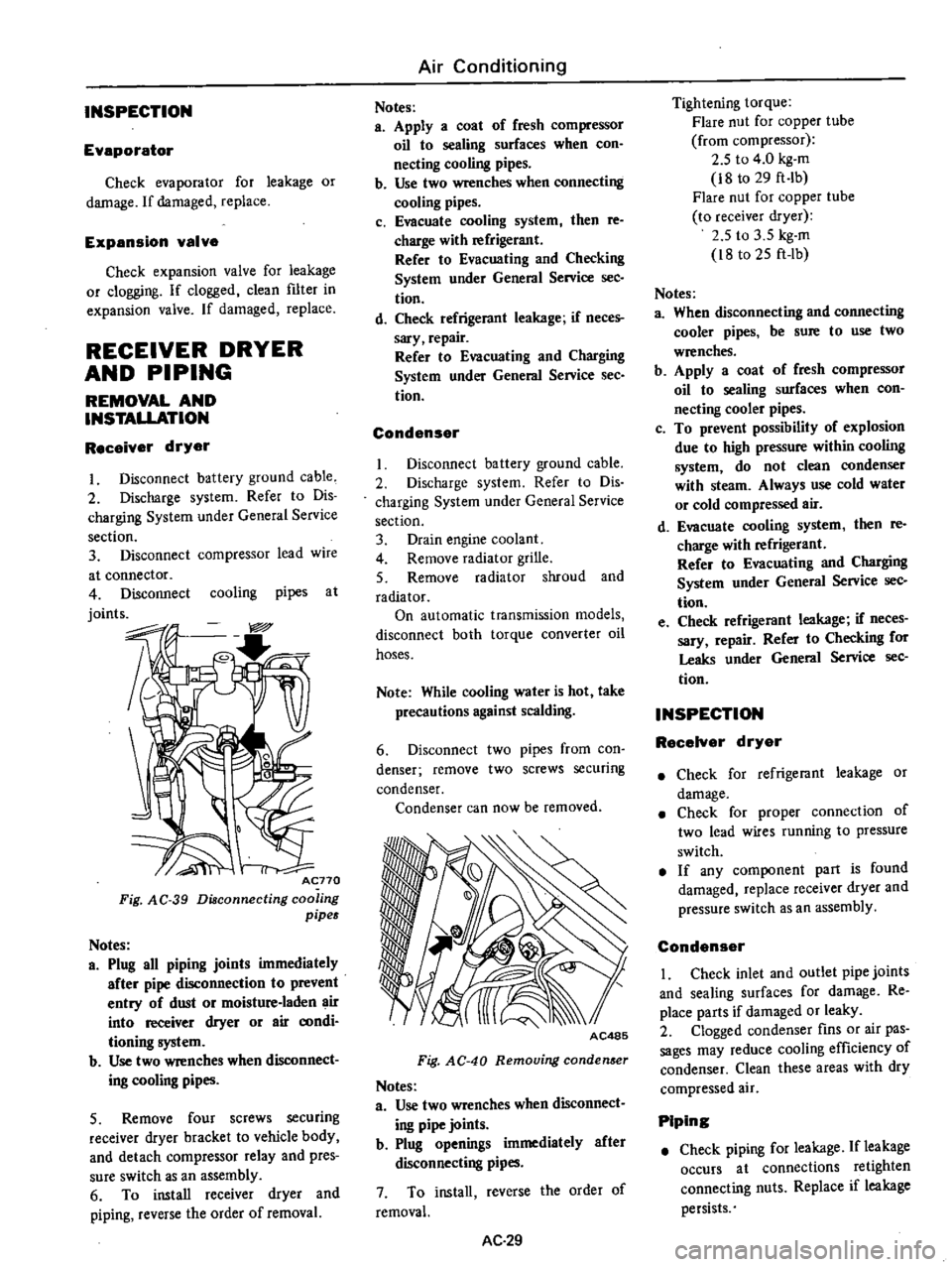
INSPECTION
Evaporator
Check
evaporator
for
leakage
or
damage
If
damaged
replace
Expansion
valve
Check
expansion
valve
for
leakage
or
clogging
If
clogged
clean
filter
in
expansion
valve
If
damaged
replace
RECEIVER
DRYER
AND
PIPING
REMOVAL
AND
INSTAUATION
Receiver
dryer
I
Disconnect
battery
ground
cable
2
Discharge
system
Refer
to
Dis
charging
System
under
General
Service
section
3
Disconnect
compressor
lead
wire
at
connector
4
Disconnect
cooling
pipes
at
joints
Acno
Fig
AC
39
Diaconnecting
coo
ing
pipes
Notes
a
Plug
all
piping
joints
immediately
after
pipe
disconnection
to
prevent
entry
of
dust
or
moisture
laden
air
into
receiver
dryer
or
air
aJOdi
tioning
system
b
Use
two
wrenches
when
dIsconnect
ing
cooling
pipes
5
Remove
four
screws
securing
receiver
dryer
bracket
to
vehicle
body
and
detach
compressor
relay
and
pres
sure
switch
as
an
assembly
6
To
install
receiver
dryer
and
piping
reverse
the
order
of
removal
Air
Conditioning
Notes
a
Apply
a
coat
of
fresh
compressor
oil
to
sealing
surfaces
when
con
necting
cooling
pipes
b
Use
two
wrenches
when
connecting
cooling
pipes
c
Evacuate
cooling
system
then
re
charge
with
refrigerant
Refer
to
Evacuating
and
Checking
System
under
General
Service
sec
tion
d
Check
refrigerant
leakage
if
neces
sary
repair
Refer
to
Evacuating
and
Charging
System
under
General
Service
See
tion
Condenser
Disconnect
battery
ground
cable
2
Discharge
system
Refer
to
Dis
charging
System
under
General
Service
section
3
Drain
engine
coolant
4
Remove
radiator
grille
5
Remove
radiator
shroud
and
radiator
On
automatic
transmission
models
disconnect
both
torque
converter
oil
hoses
Note
While
cooling
water
is
hot
take
precautions
against
scalding
6
Disconnect
two
pipes
from
con
denser
remove
two
screws
securing
condenser
Condenser
can
now
be
removed
AC485
Fig
AC
40
Removing
conden
er
Notes
a
Use
two
wrenches
when
disconnect
ing
pipe
joints
b
Plug
openings
immediately
after
disconnecting
pipes
7
To
install
reverse
the
order
of
removal
AC
29
Tightening
torque
Flare
nut
for
copper
tube
from
compressor
2
5
to
4
0
kg
m
i8
to
29
ft
Ib
Flare
nut
for
copper
tube
to
receiver
dryer
2
5
to
3
5
kg
m
i8
to
25
ft
lb
Notes
a
When
disconnecting
and
connecting
cooler
pipes
be
sure
to
use
two
wrenches
b
Apply
a
coat
of
fresh
compressor
oil
to
sealing
surfaces
when
con
necting
cooler
pipes
c
To
prevent
possibility
of
explosion
due
to
high
pressure
within
cooling
system
do
not
clean
condenser
with
steam
Always
use
cold
water
or
cold
compressed
air
d
Evacuate
cooling
system
then
re
charge
with
refrigerant
Refer
to
Evacuating
and
Charging
System
under
General
Service
sec
tion
e
Check
refrigerant
leakage
if
neces
sary
repair
Refer
to
Checking
for
Leaks
under
General
Service
sec
tion
INSPECTION
RecelYer
dryer
Check
for
refrigerant
leakage
or
damage
Check
for
proper
connection
of
two
lead
wires
running
to
pressure
switch
If
any
component
part
is
found
damaged
replace
receiver
dryer
and
pressure
switch
as
an
assembly
Condenser
I
Check
inlet
and
outlet
pipe
joints
and
sealing
surfaces
for
damage
Re
place
parts
if
damaged
or
leaky
2
Clogged
condenser
fins
or
air
pas
sages
may
reduce
cooling
efficiency
of
condenser
Clean
these
areas
with
dry
compressed
air
Piping
Check
piping
for
leakage
If
leakage
occurs
at
connections
retighten
connecting
nuts
Replace
if
leakage
persists
Page 521 of 537
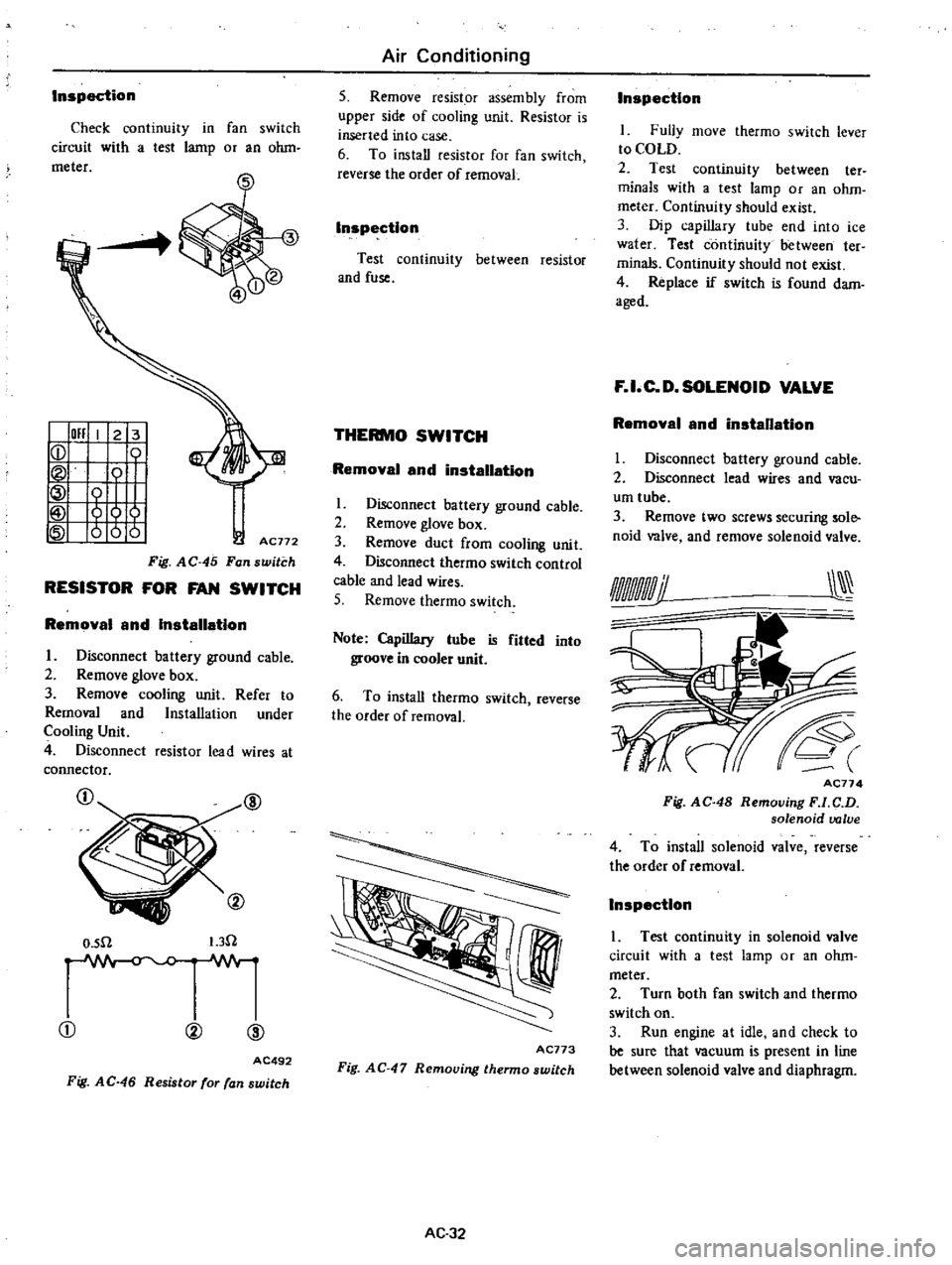
Inspection
Check
continuiry
in
fan
switch
circuit
with
a
test
lamp
or
an
ohm
meter
I
011
I
2
3
ICD
Tt
tt
AC772
Fig
AC
45
Fan
switch
RESISTOR
FOR
FAN
SWITCH
Removal
and
Installation
I
Disconnect
battery
ground
cable
2
Remove
glove
box
3
Remove
cooling
unit
Refer
to
Removal
and
Installation
under
Cooling
Unit
4
Disconnect
resistor
lead
wires
at
connector
@
O
sn
I
3n
CD
00
@
AC492
Fig
AC
46
Resistor
for
fan
switch
Air
Conditioning
5
Remove
resistor
assembly
from
upper
side
of
cooling
unit
Resistor
is
inserted
into
case
6
To
install
res
istor
for
fan
switch
reverse
the
order
of
removaL
Inspection
Test
continuity
between
resistor
and
fuse
THERMO
SWITCH
Removal
and
installation
1
Disconnect
battery
ground
cable
2
Remove
glove
box
3
Remove
duct
from
cooling
unit
4
Disconnect
thermo
switch
control
cable
and
lead
wires
5
Remove
thermo
switch
Note
Capillary
lube
is
fitted
into
groove
in
cooler
unit
6
To
install
thermo
switch
reverse
the
order
of
removal
I
I
AC773
Fig
AC
47
Removing
thermo
switch
AC
32
Inspection
I
Fully
move
thermo
swirch
lever
to
COLD
2
Test
continuity
between
ter
minals
with
a
test
tamp
or
an
ohm
meter
Continuity
should
exist
3
Dip
capillary
tube
end
into
ice
water
Test
continuity
between
ter
minals
Continuity
should
not
exist
4
Replace
if
switch
is
found
dam
aged
F
I
C
D
SOLENOID
VALVE
Removal
and
installation
I
Disconnect
battery
ground
cable
2
Disconnect
lead
wires
and
vacu
um
tube
3
Remove
two
screws
securing
sole
noid
valve
and
remove
solenoid
valve
AC77
4
Fig
AC
48
Removing
F
l
C
D
solenoid
valve
4
To
install
solenoid
valve
reverse
the
order
of
removal
Inspection
1
Test
continuity
in
solenoid
valve
circuit
with
a
test
lamp
or
an
ohm
meter
2
Turn
both
fan
switch
and
thermo
switch
on
3
Run
engine
at
idle
and
check
to
be
sure
that
vacuum
is
present
in
line
between
solenoid
valve
and
diaphragm
Page 531 of 537
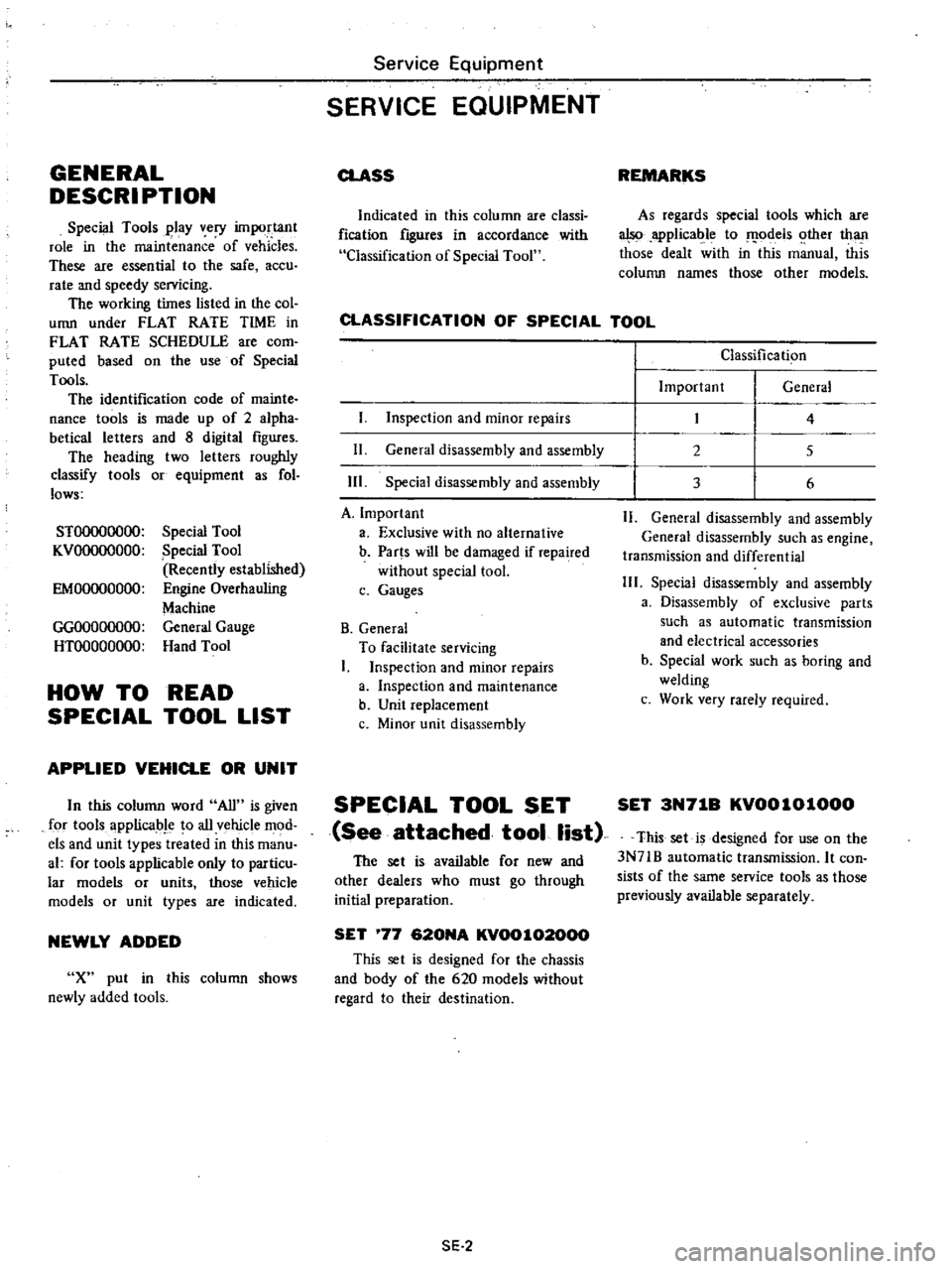
GENERAL
DESCRI
PTION
Special
Tools
play
very
important
role
in
the
maintenance
of
vehicles
These
are
essential
to
the
safe
accu
rate
and
speedy
servicing
The
working
times
listed
in
the
col
umn
under
FLAT
RATE
TIME
in
FLAT
RATE
SCHEDULE
are
com
puted
based
on
the
use
of
Special
Tools
The
identification
code
of
mainte
nance
tools
is
made
up
of
2
alpha
betical
letters
and
8
digital
figures
The
heading
two
letters
roughly
classify
tools
or
equipment
as
fol
lows
STOOOOOOOO
KVOOOOOOOO
Special
Tool
Special
Tool
Recently
established
Engine
Overhauling
Machine
General
Gauge
Hand
Tool
EMOOOOOOOO
GGOOOOOOOO
HTOOOOOOOO
HOW
TO
READ
SPECIAL
TOOL
LIST
APPLIED
VEHICLE
OR
UNIT
In
this
column
word
All
is
given
for
tools
applicable
to
all
vehicle
mod
els
and
unit
types
treated
in
this
manu
al
for
tools
applicable
only
to
particu
lar
models
or
units
those
vehicle
models
or
unit
types
are
indicated
NEWLY
ADDED
X
put
in
this
column
shows
newly
added
tools
Service
Equipment
SERVICE
EQUIPMENT
CLASS
Indicated
in
this
column
are
classi
fication
ftg1ll
es
in
accordance
with
Classification
of
Speciai
Tool
REMARKS
As
regards
special
tools
which
are
also
applicable
to
models
other
than
those
dealt
ith
U
this
m
inual
this
coluITUl
names
those
other
models
CLASSIFICATION
OF
SPECIAL
TOOL
I
Inspection
and
minor
repairs
11
General
disassembly
and
assembly
Ill
Special
disassembly
and
assembly
A
Important
a
Exclusive
with
no
alternative
b
Parts
will
be
damaged
if
repaired
without
special
tool
c
Gauges
B
General
To
facilitate
servicing
I
Inspection
and
minor
repairs
a
Inspection
and
maintenance
b
Unit
replacement
c
Minor
unit
disassembly
SPECIAL
TOOL
SET
See
attached
tool
list
The
set
is
available
for
new
and
other
dealers
who
must
go
through
initial
preparation
SET
77
620NA
KV00102000
This
set
is
designed
for
the
chassis
and
body
of
the
620
models
without
regard
to
their
destination
SE
2
Classification
Important
General
2
3
4
5
6
11
General
disassembly
and
assembly
General
disassembly
such
as
engine
transmission
and
differential
111
Special
disassembly
and
assembly
a
Disassembly
of
exclusive
parts
such
as
automatic
transmission
and
electrical
accessories
b
Special
work
such
as
boring
and
welding
c
Work
very
rarely
required
SET
3N71B
KV0010l000
This
set
is
designed
for
use
on
the
3N71B
automatic
transmission
It
con
sists
of
the
same
service
tools
as
those
previously
available
separately
Page 532 of 537
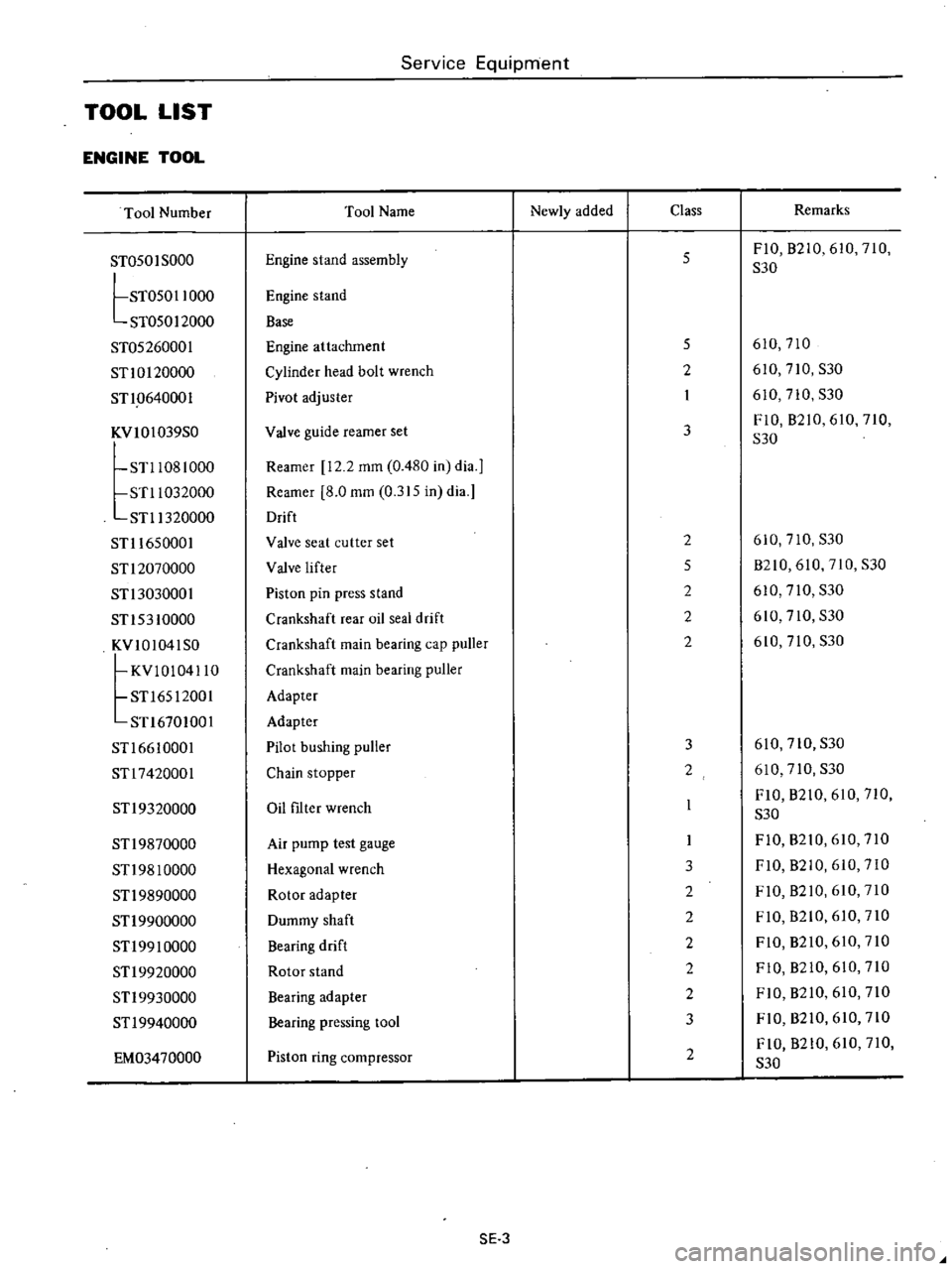
Service
Equipment
TOOL
LIST
ENGINE
TOOL
Tool
Number
Tool
Name
Newly
added
Class
Remarks
ST050
I
SODa
Engine
stand
assembly
5
FIO
B2iO
610
710
S30
tST05011000
Engine
stand
ST050
I
2000
Base
ST05260001
Engine
attachment
5
610
710
STlOl20000
Cylinder
head
bolt
wrench
2
610
710
S30
STl
0640001
Pivot
adjuster
I
610
710
S30
KVIOI039S0
Valve
guide
reamer
set
3
FiO
B210
610
710
S30
STl1081
000
Reamer
12
2
mffi
0
480
in
dia
J
STl1032000
Reamer
8
0
mffi
0
315
in
dia
STl1320000
Drift
STll650001
Valve
seat
cutter
set
2
610
710
S30
STl2070000
Valve
lifter
5
B210
610
710
S30
STl3030001
Piston
pin
press
stand
2
610
710
S30
STl53
10000
Crankshaft
rear
oil
seal
drift
2
610
710
S30
KVI01041S0
Crankshaft
main
bearing
cap
puller
2
610
710
S30
KVIOI04110
Crankshaft
main
bearing
puller
STl6512001
Adapter
STl6701001
Adapter
STl6610001
Pilot
bushing
puller
3
610
710
S30
STl7420001
Chain
stopper
2
610
710
S30
STl9320000
Oil
filter
wrench
FIO
B210
610
710
S30
STl9870000
Air
pump
test
gauge
FI0
B210
610
710
STl98
10000
Hexagonal
wrench
3
FIO
B2iO
610
710
STl9890000
Rotor
adapter
2
FIO
B210
610
710
STl9900000
Dummy
shaft
2
FIO
B210
610
710
STl99
10000
Bearing
drift
2
FIO
B210
610
710
STl9920000
Rotor
stand
2
FIO
B210
610
710
STl9930000
Bearing
adapter
2
FIO
B210
610
710
ST
I
9940000
Bearing
pressing
tool
3
FIO
B210
610
710
EM03470000
Piston
ring
compressor
2
FIO
B210
610
710
S30
SE
3