alternator DATSUN PICK-UP 1977 Service Manual
[x] Cancel search | Manufacturer: DATSUN, Model Year: 1977, Model line: PICK-UP, Model: DATSUN PICK-UP 1977Pages: 537, PDF Size: 35.48 MB
Page 19 of 537
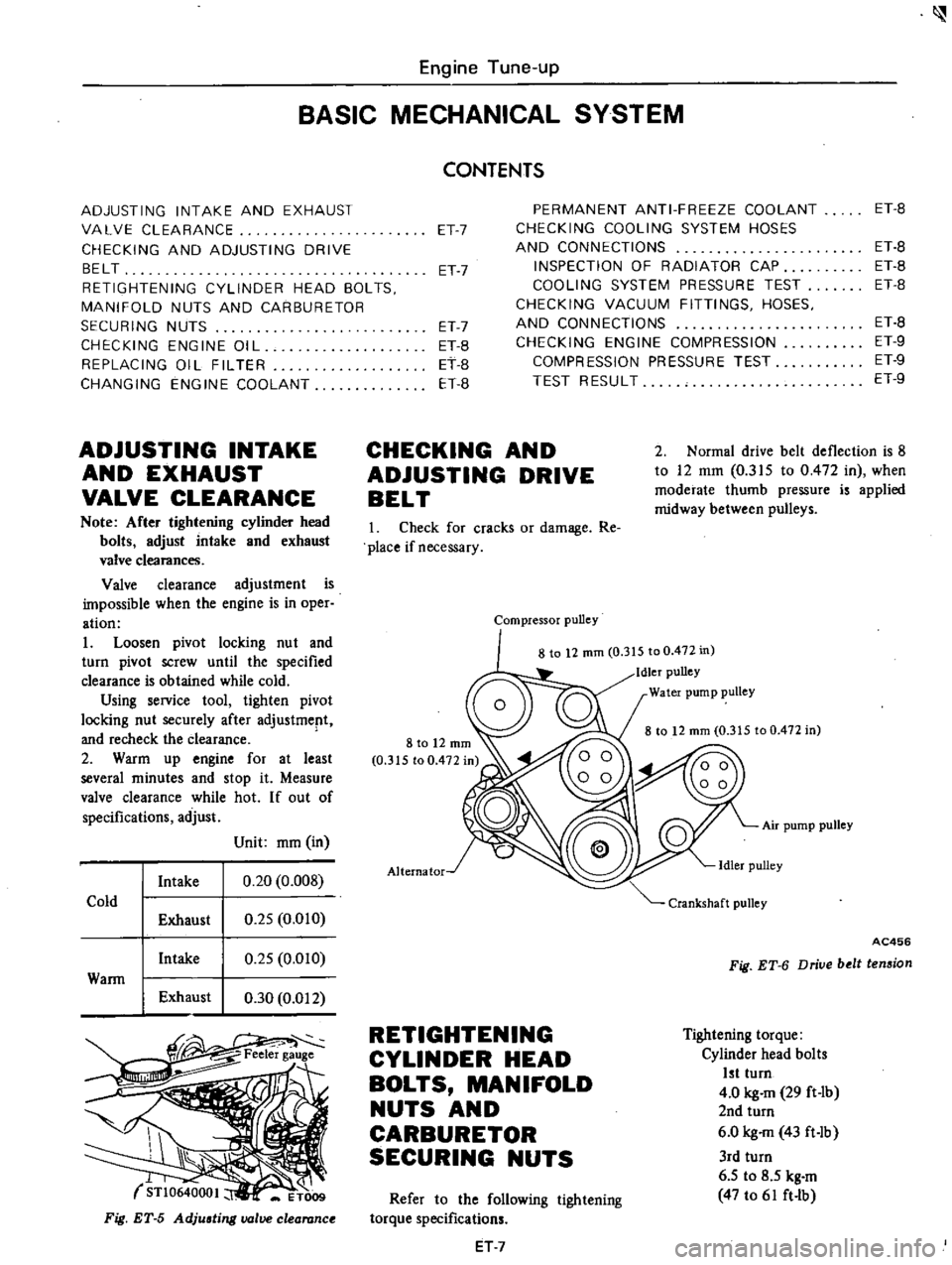
Engine
Tune
up
BASIC
MECHANICAL
SYSTEM
ADJUSTING
INTAKE
AND
EXHAUST
VALVE
CLEARANCE
CHECKING
AND
ADJUSTING
DRIVE
BELT
RETIGHTENING
CYLINDER
HEAD
BOLTS
MANIFOLD
NUTS
AND
CARBURETOR
SECURING
NUTS
CHECKING
ENGINE
OIL
REPLACING
OIL
FILTER
CHANGING
ENGINE
COOLANT
ADJUSTING
INTAKE
AND
EXHAUST
VALVE
CLEARANCE
Note
After
tightening
cylinder
head
bolts
adjust
intake
and
exhaust
valve
clearances
Valve
clearance
adjustment
is
impossible
when
the
engine
is
in
oper
ation
1
Loosen
pivot
locking
nu
t
and
turn
pivot
screw
until
the
specified
clearance
is
obtained
while
cold
Using
service
tool
tighten
pivot
locking
nut
securely
after
adjustment
and
recheck
the
clearance
2
Warm
up
engine
for
at
least
several
minutes
and
stop
it
Measure
valve
clearance
while
hot
If
out
of
specifications
adjust
Unit
mm
in
Intake
0
20
0
008
Cold
Exhaust
0
25
0
010
Intake
0
25
OmO
Wann
I
Exhaust
0
30
0
012
STl
064000
I
ET009
Fig
ET
5
Adjusting
valve
clearance
CONTENTS
ET
7
PERMANENT
ANTI
FREEZE
COOLANT
CHECKING
COOLING
SYSTEM
HOSES
AND
CONNECTIONS
INSPECTION
OF
RADIATOR
CAP
COOLING
SYSTEM
PRESSURE
TEST
CHECKING
VACUUM
FITTINGS
HOSES
AND
CONNECTIONS
CHECKING
ENGINE
COMPRESSION
COMPRESSION
PRESSURE
TEST
TEST
RESULT
ET
7
ET7
ET
B
ET
B
ET
B
CHECKING
AND
ADJUSTING
DRIVE
BELT
ET
B
ET
B
ET
B
ET
B
ET
B
ET
9
ET
9
ET
9
2
Normal
drive
belt
deflection
is
8
to
12
mm
0
315
to
0
472
in
when
moderate
thumb
pressure
is
applied
midway
between
pulleys
1
Check
for
cracks
or
damage
Re
place
if
necessary
Compressor
pulley
8
to
12
mm
0
315
to
0
472
in
Idler
pulley
Water
pump
pulley
8
to
12
mm
0
315
to
0
472
in
Air
pump
pulley
Alternator
AC456
Fig
ET
6
Driue
belt
tension
RETIGHTENING
CYLINDER
HEAD
BOLTS
MANIFOLD
NUTS
AND
CARBURETOR
SECURING
NUTS
Tightening
torque
Cylinder
head
bolts
1st
turn
4
0
kg
m
29
ft
Ib
2nd
turn
6
0
kg
m
43
ft
Ib
3rd
turn
6
5
to
8
5
kg
m
47
to
61
ft
lb
Refer
to
the
following
tightening
torque
specifications
ET
7
Page 49 of 537
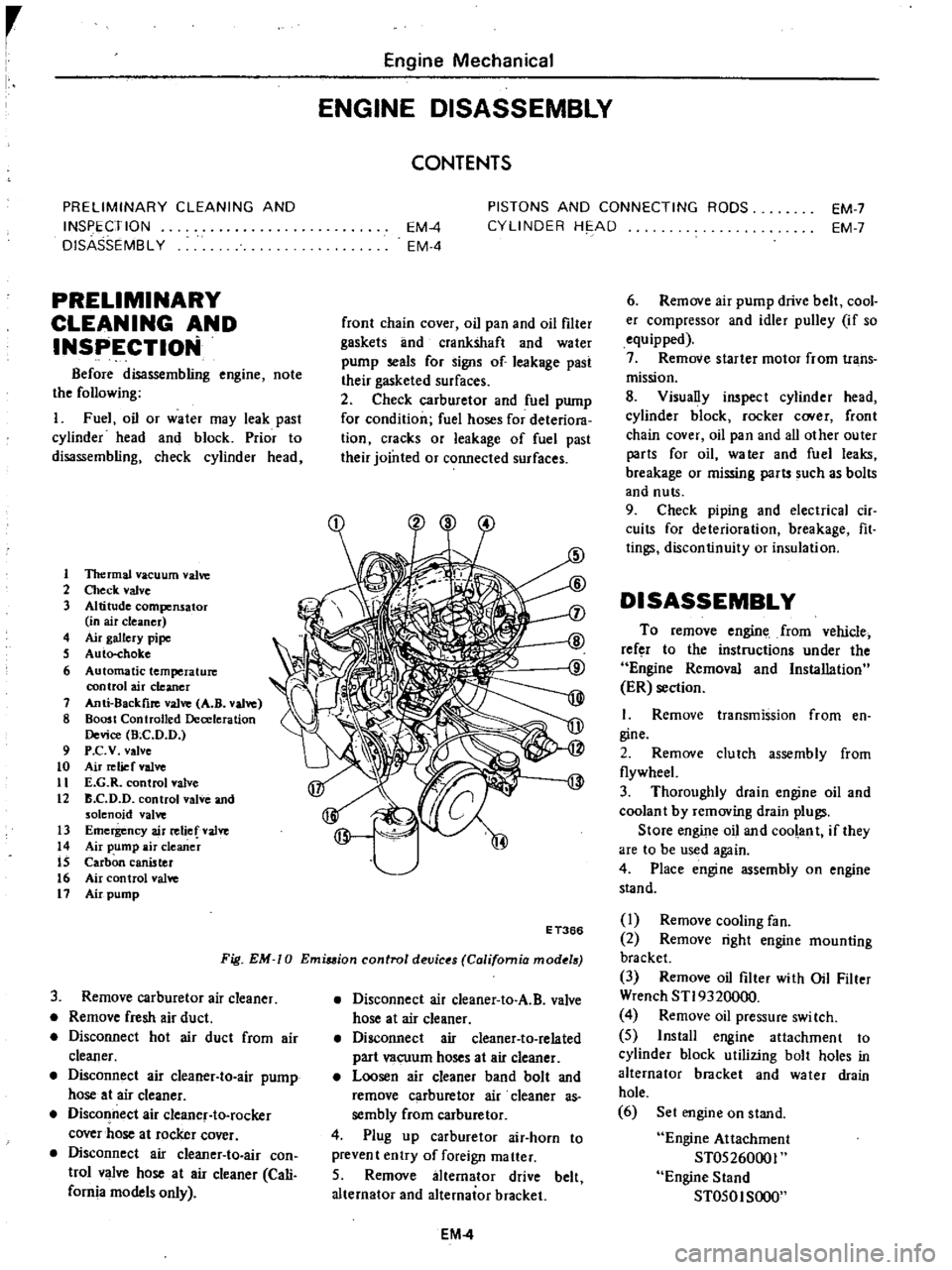
r
I
I
PRELIMINARY
CLEANING
AND
INSPECTION
DISASSEMBL
Y
PRELIMINARY
CLEANING
AND
INSt
ECTION
Before
disassembling
engine
note
the
following
I
Fuel
oil
or
water
may
leak
past
cylinder
head
and
block
Prior
to
disassembling
check
cylinder
head
1
1ltermal
vacuum
valve
2
Check
valve
3
Altitude
compensator
in
air
cleaner
4
Air
gallery
pipe
S
Auto
choke
6
Automatic
temperature
control
air
cleaner
7
Anti
8ackfire
valve
A
B
valve
8
Boost
Controlled
Deceleration
Device
Bee
D
D
9
P
c
v
valve
to
Air
relief
valve
11
E
G
R
control
valve
12
B
C
D
D
control
valve
and
solenoid
valve
13
Emergency
air
relief
valve
14
Air
pump
air
cleaner
IS
Carbon
canister
16
Air
control
valve
11
Air
pump
Engine
Mechanical
ENGINE
DISASSEMBLY
CONTENTS
EM
4
EM
4
PISTONS
AND
CONNECTING
RODS
CYLINDER
HE
AD
EM
7
EM
7
front
chain
cover
oil
pan
and
oil
filter
gaskets
lInd
crankshaft
and
water
pump
seals
for
signs
of
leakage
past
their
gasketed
surfaces
2
Check
carburetor
and
fuel
pump
for
condition
fuel
hoses
for
deteriora
tion
cracks
or
leakage
of
fuel
past
their
jointed
or
connected
surfaces
Fig
EM
0
Emiuion
control
devic
s
California
mod
18
E
T366
3
Remove
carburetor
air
cleaner
Remove
fresh
air
duct
Disconnect
hot
air
duct
from
air
cleaner
Disconnect
air
cleaner
to
air
pump
hose
at
air
cleaner
Disconnect
air
cleanef
to
rocker
cover
hose
at
rocker
cover
Disconnect
air
cIeaner
to
air
con
trol
valve
hose
at
air
cleaner
Cali
fornia
models
only
Disconnect
air
cleaner
to
A
B
valve
hose
at
air
cleaner
Disconnect
air
cleaner
to
related
part
vacuum
hoses
at
air
cleaner
Loosen
air
cleaner
band
bolt
and
remove
carburetor
air
cleaner
as
sembly
from
carburetor
4
Plug
up
carburetor
air
horn
to
prevent
entry
of
foreign
matter
5
Remove
alternator
drive
belt
alternator
and
alternator
bracket
EM
4
6
Remove
air
pump
drive
belt
cool
er
compressor
and
idler
pulley
if
so
equipped
7
Remove
starter
motor
from
trans
mission
8
Visually
inspect
cylinder
head
cylinder
block
rocker
C
Ner
front
chain
cover
oil
pan
and
all
other
outer
parts
for
oil
water
and
fuel
leaks
breakage
or
missing
parts
such
as
bolts
and
nuts
9
Check
piping
and
electrical
cir
cuits
for
deterioration
breakage
fit
tings
discontinuity
or
insulation
DISASSEMBLY
To
remove
engine
from
vehicle
refer
to
the
instructions
under
the
Engine
Removal
and
Installation
ER
section
I
Remove
transmission
from
en
gine
2
Remove
clutch
assembly
from
flywheeL
3
Thoroughly
drain
engine
oil
and
coolan
t
by
removing
drain
plugs
Store
engine
oil
and
coolant
if
they
are
to
be
used
again
4
Place
engine
assembly
on
engine
stand
I
Remove
cooling
fan
2
Remove
right
engine
mounting
bracket
3
Remove
oil
filter
with
Oil
Filter
Wrench
STI9320000
4
Remove
oil
pressure
swi
tch
5
Install
engine
attachment
to
cylinder
block
utilizing
bolt
holes
in
alternator
bracket
and
water
drain
hole
6
Set
engine
on
stand
Engine
Attachment
ST05260001
Engine
Stand
ST050I
SOOO
Page 71 of 537
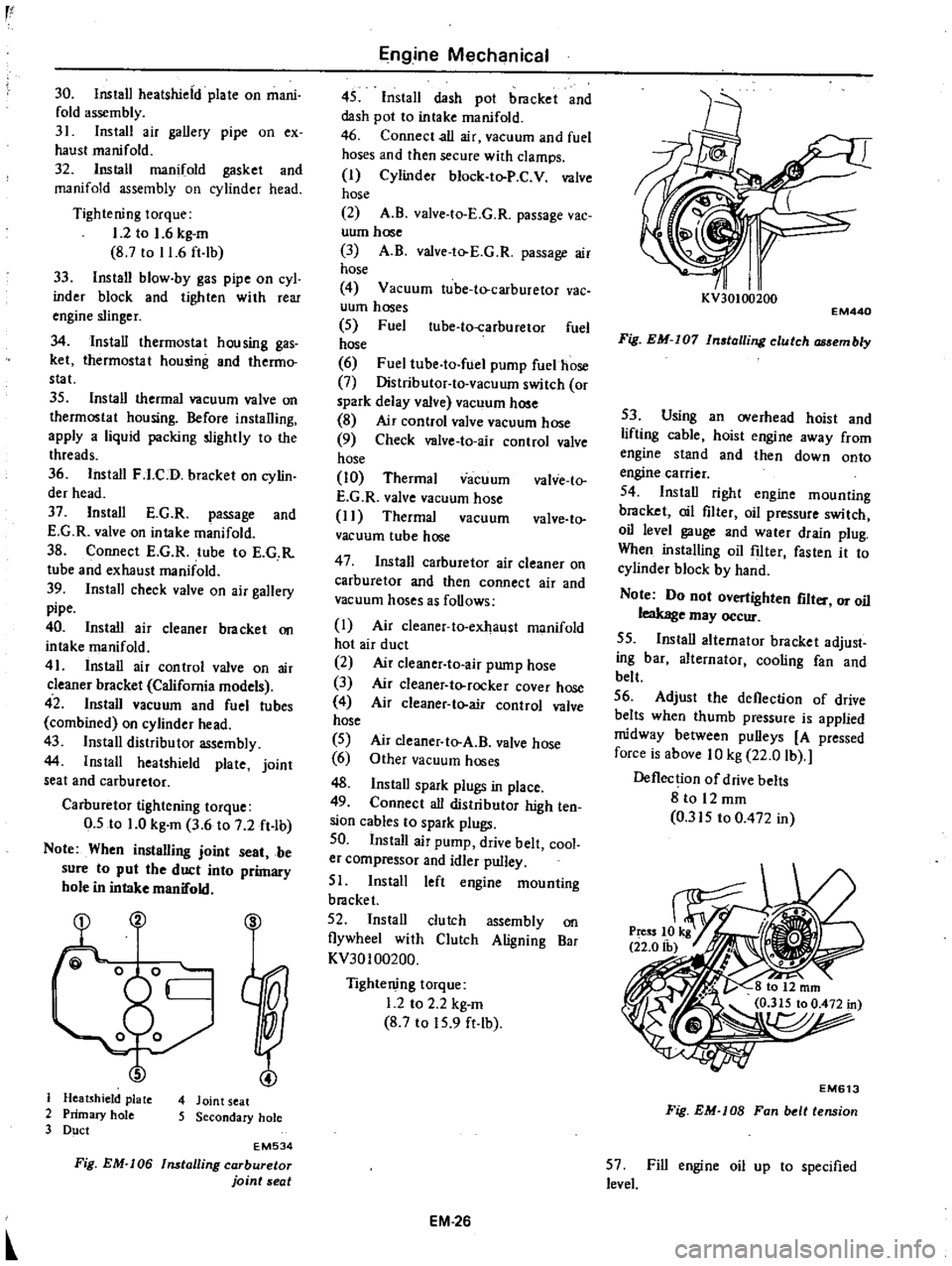
30
Install
heatshieid
plate
on
mani
fold
assembly
31
Install
air
gallery
pipe
on
ex
haust
manifold
32
Install
manifold
gasket
and
manifold
assembly
on
cylinder
head
Tightening
torque
1
2to
1
6kg
m
8
7
to
11
6
ft
lb
33
Install
blow
by
gas
pipe
on
cyl
inder
block
and
tighten
with
rear
engine
slinger
34
Install
thermostat
housing
gas
ket
thermostat
housing
and
thermo
stat
35
Install
thermal
vacuum
valve
on
thermostat
housing
Before
installing
apply
a
liquid
packing
slightly
to
the
threads
36
Install
FJ
C
D
bracket
on
cylin
der
head
37
Install
E
G
R
passage
and
E
G
R
valve
on
intake
manifold
38
Connect
E
G
R
tube
to
E
G
R
tube
and
exhaust
manifold
39
Install
check
valve
on
air
gallery
pipe
40
Install
air
cleaner
bracket
on
intake
manifold
41
Install
air
control
valve
on
air
cleaner
bracket
California
models
42
Install
vacuum
and
fuel
tubes
combined
on
cylinder
head
43
Install
distributor
assembly
44
Install
heatshield
plate
joint
seat
and
carburetor
Carbure10r
tightening
torque
0
5
to
1
0
kg
m
3
6
to
7
2
ft
lb
Note
When
instalUng
joint
seat
be
sure
to
put
the
duct
into
primary
hole
in
intake
manifold
S
J
Heatshield
plate
4
Joint
seat
2
Primary
hole
5
Secondary
hole
3
Duct
EM534
Fig
EM
I06
Installing
carburetor
joint
seat
Engine
Mechanical
45
Install
dash
pot
bracket
and
dash
pot
to
intake
manifold
46
Connect
all
air
vacuum
and
fuel
hoses
and
then
secure
with
clamps
I
Cylinder
block
to
P
C
V
valve
hose
2
A
B
valve
to
E
G
R
passage
vac
uum
hose
3
A
B
valve
to
E
G
R
passage
air
hose
4
Vacuum
tube
to
carburetor
vac
uum
hoses
5
Fuel
ube
to
carburetor
fuel
hose
6
Fuel
tube
to
fuel
pump
fuelhose
7
Distributor
to
vacuum
switch
or
spark
delay
valve
vacuum
hose
8
Air
control
valve
vacuum
hose
9
Check
valve
to
air
control
valve
hose
10
Thermal
vacuum
valve
to
E
G
R
valve
vacuum
hose
I
I
Thermal
vacuum
valve
to
vacuum
tube
hose
47
Install
carburetor
air
cleaner
on
carburetor
and
then
connect
air
and
vacuum
hoses
as
follows
I
Air
cleaner
to
exhaust
manifold
hot
air
duct
2
Air
c1eaner
to
air
pump
hose
3
Air
cleaner
to
rocker
cover
hose
4
Air
cleaner
to
air
control
valve
hose
5
6
48
Install
spark
plugs
in
place
49
Connect
all
distributor
high
ten
sion
cables
to
spark
plugs
50
Install
air
pump
drive
belt
cool
er
compressor
and
idler
pulley
51
Install
left
engine
mounting
bracket
52
Install
clutch
assembly
on
flywheel
with
Clutch
Aligning
Bar
KV30100200
Air
cleaner
to
A
B
valve
hose
Other
vacuum
hoses
Tightening
torque
1
2
to
2
2
kg
m
8
7
to
15
9
ft
lb
EM
26
I
I
KV30100200
EM440
Fig
EM
I07
In
talling
clutch
embly
53
Using
an
overhead
hoist
and
lifting
cable
hoist
engine
away
from
engine
stand
and
then
down
onto
engine
carrier
54
Install
right
engine
mounting
bracket
oil
filter
oil
pressure
switch
oil
level
gauge
and
water
drain
plug
When
installing
oil
filter
fasten
it
to
cylinder
block
by
hand
Note
Do
not
overtighten
flit
or
oil
leakage
may
occur
55
Install
alternator
bracket
adjust
ing
bar
alternator
cooling
fan
and
belt
56
Adjust
the
deflection
of
drive
belts
when
thumb
pressure
is
applied
midway
between
pulleys
A
pressed
force
is
above
10
kg
22
0
lb
Deflection
of
drive
belts
8
to
12
mm
0
315
to
0
472
in
EM613
Fig
EM
lOB
Fan
belt
tension
57
Fill
engine
oil
up
to
specified
level
Page 92 of 537
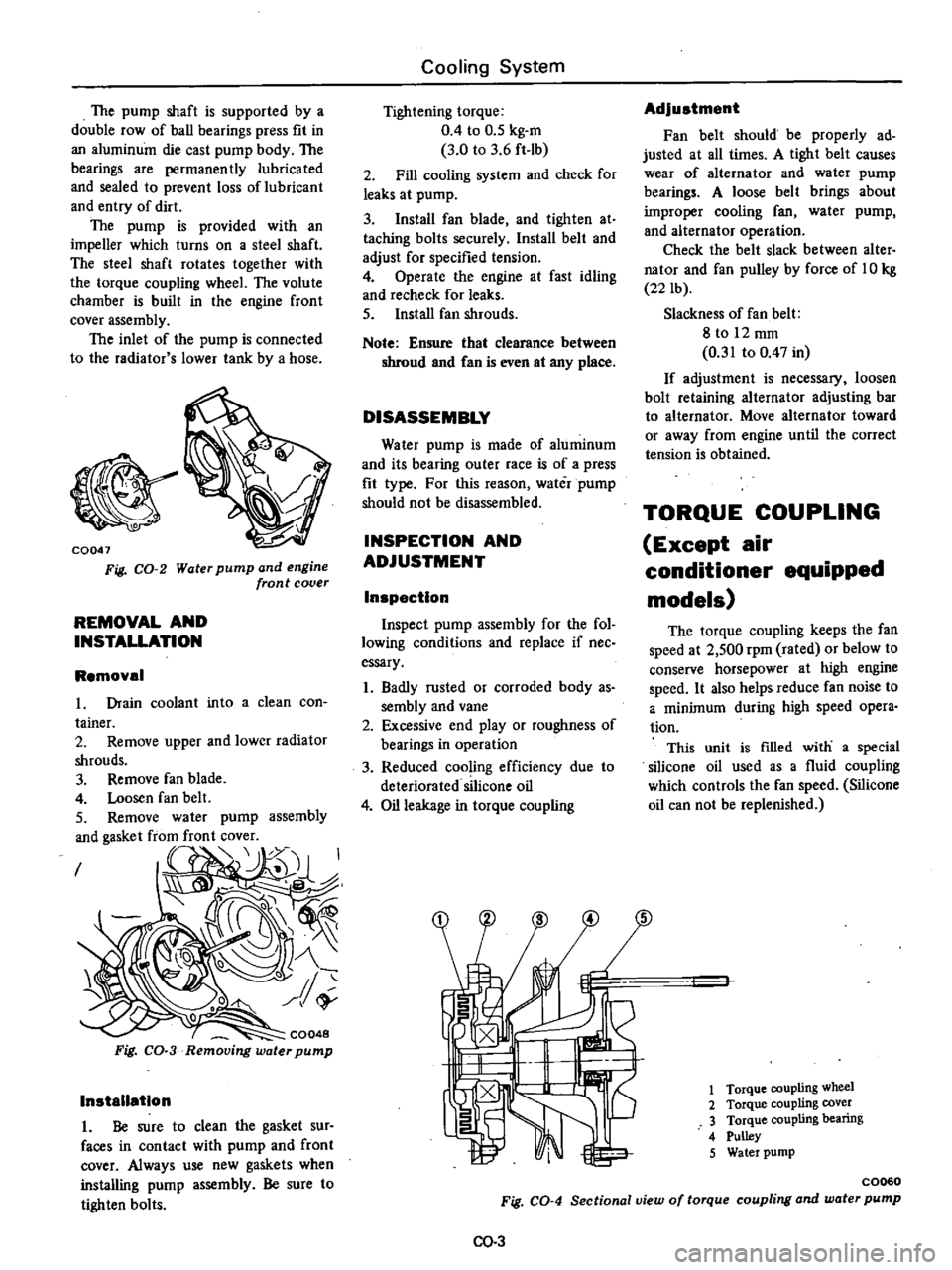
The
pump
shaft
is
supported
by
a
double
row
of
ball
bearings
press
fit
in
an
aluminum
die
cast
pump
body
The
bearings
are
permanently
lubricated
and
sealed
to
prevent
loss
of
lubricant
and
entry
of
dirt
The
pump
is
provided
with
an
impeller
which
turns
on
a
steel
shaft
The
steel
shaft
rotates
together
with
the
torque
coupling
wheeL
The
volute
chamber
is
built
in
the
engine
front
cover
assembly
The
inlet
of
the
pump
is
connected
to
the
radiator
s
lower
tank
by
a
hose
i
o
CQ047
Fig
CO
2
Water
pump
and
engine
front
cover
REMOVAL
AND
INSTALLATION
Removal
in
to
a
clean
con
assembly
I
CQ048
Fig
CO
3
Removing
water
pump
Installation
1
Be
sure
to
clean
the
gasket
sur
faces
in
contact
with
pump
and
front
cover
Always
use
new
gaskets
when
installing
pump
assembly
Be
sure
to
tighten
bolts
Cooling
System
Tightening
torque
0
4
to
0
5
kg
m
3
0
to
3
6
ft
lb
2
Fill
cooling
system
and
check
for
leaks
at
pump
3
Install
fan
blade
and
tighten
at
taching
bolts
securely
Install
belt
and
adjust
for
specified
tension
4
Operate
the
engine
at
fast
idling
and
recheck
for
leaks
5
Install
fan
shrouds
Note
Ensure
that
clearance
between
shroud
and
Can
is
even
at
any
place
DISASSEMBLY
Water
pump
is
made
of
aluminum
and
its
bearing
outer
race
is
of
a
press
fit
type
For
this
reason
water
pump
should
not
be
disassembled
INSPECTION
AND
ADJUSTMENT
Inspection
Inspect
pump
assembly
for
the
fol
lowing
conditions
and
replace
if
nee
essary
1
Badly
rusted
or
corroded
body
as
sembly
and
vane
2
Excessive
end
play
or
roughness
of
bearings
in
operation
3
Reduced
cooling
efficiency
due
to
deteriorated
silicone
oil
4
Oil
leakage
in
torque
coupling
Adjustment
Fan
belt
should
be
properly
ad
justed
at
all
times
A
tight
belt
causes
wear
of
alternator
and
water
pump
bearings
A
loose
belt
brings
about
improper
cooling
fan
water
pump
and
alternator
operation
Check
the
belt
slack
between
alter
nator
and
fan
pulley
by
force
of
10
kg
22
lb
Slackness
of
fan
belt
8
to
12
mm
0
31
to
0
47
in
If
adjustment
is
necessary
loosen
bolt
retaining
alternator
adjusting
bar
to
alternator
Move
alternator
toward
or
away
from
engine
until
the
correct
tension
is
obtained
TORQUE
COUPLING
Except
air
conditioner
equipped
models
The
torque
coupling
keeps
the
fan
speed
at
2
500
rpm
rated
or
below
to
conserve
horsepower
at
high
engine
speed
It
also
helps
reduce
fan
noise
to
a
minimum
during
high
speed
opera
tion
This
unit
is
filled
with
a
special
silicone
oil
used
as
a
fluid
coupling
which
controls
the
fan
speed
Silicone
oil
can
not
be
replenished
1
Torque
coupling
wheel
2
Torque
coupling
cover
3
Torque
coupling
bearing
4
Pulley
5
Water
pump
C0060
Fig
CO
4
Sectional
view
of
torque
coupling
and
water
pump
00
3
Page 116 of 537
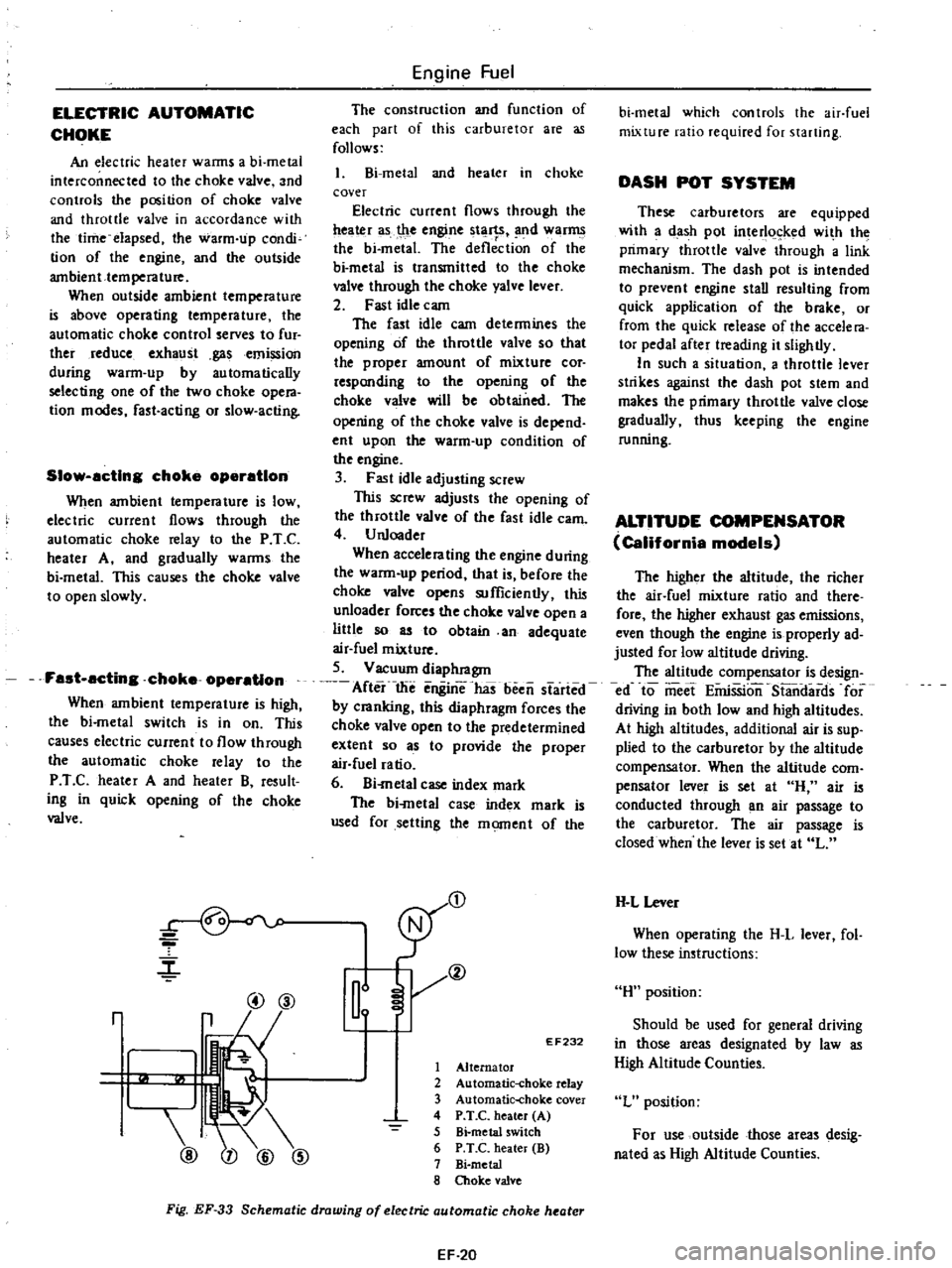
ELECTRIC
AUTOMATIC
CHOKE
An
electric
heater
wanns
a
bi
metal
interconnected
to
the
choke
valve
and
controls
the
position
of
choke
valve
and
throttle
valve
in
accordance
with
the
time
elapsed
the
warm
up
condi
tion
of
the
engine
and
the
outside
ambient
temperature
When
outside
ambient
temperature
is
above
operating
temperature
the
automatic
choke
control
serves
to
fur
ther
reduce
exhaust
gasemission
during
warm
up
by
automatically
selecting
one
of
the
two
choke
opera
tion
modes
fast
acting
or
slow
acting
Slow
acting
choke
operation
When
ambient
temperature
is
low
electric
current
flows
through
the
automatic
choke
relay
to
the
P
T
C
heater
A
and
gradually
warms
the
bi
metal
This
causes
the
choke
valve
to
open
slowly
Fast
acting
choke
operation
When
ambient
temperature
is
high
the
bi
metal
switch
is
in
on
This
causes
electric
current
to
flow
through
the
automatic
choke
relay
to
the
P
T
C
heater
A
and
heater
B
result
ing
in
quick
opening
of
the
choke
valve
r
@@
r
@
Engine
Fuel
The
construction
and
function
of
each
part
of
this
carburetor
are
as
follows
l
Bi
metal
and
heater
in
choke
cover
Electric
current
flows
through
the
ttea
r
as
t
le
engine
tl
1
SI
nd
war
the
bi
metal
The
deflection
of
the
bi
metal
is
transmitted
to
the
choke
valve
through
the
choke
yalve
lever
2
Fast
idle
cam
The
fast
idle
cam
determines
the
opening
of
the
throttle
valve
so
that
the
proper
amount
of
mixture
cor
responding
to
the
opening
of
the
choke
valve
will
be
obtained
The
opening
of
the
choke
valve
is
depend
ent
upon
the
warm
up
condition
of
the
engine
3
Fast
idle
adjusting
screw
This
screw
adjusts
the
opening
of
the
throttle
valve
of
the
fast
idle
earn
4
U
nloader
When
accelerating
the
engine
during
the
warm
up
period
that
is
before
the
choke
valve
opens
sufficiently
this
unloader
forces
the
choke
valve
open
a
liUle
so
as
to
obtain
an
adequate
air
fuel
mixture
5
Vacuum
diaphragm
After
the
enginThas
been
started
by
cranking
this
diaphragm
forces
the
choke
valve
open
to
the
predetermined
extent
so
as
to
provide
the
proper
air
fuel
ratio
6
Bi
metal
case
index
mark
The
bi
metal
case
index
mark
is
used
for
setting
the
moment
of
the
D
Il
EF232
1
Alternator
2
Automatic
choke
relay
3
Automatic
choke
cover
4
P
T
C
heater
A
5
Bi
metal
switch
6
P
T
C
heater
B
7
Bi
metal
8
Choke
valve
Fig
EF
33
Schematic
drawing
of
electric
automatic
choke
heater
EF
20
bi
metal
which
controls
the
air
fuel
mixture
ratio
required
for
starting
DASH
POT
SYSTEM
These
carburetors
are
equipped
with
a
dash
pot
interl
ked
wi
h
the
primary
throttle
valve
through
a
link
mechanism
The
dash
pot
is
intended
to
prevent
engine
stall
resulting
from
quick
application
of
the
brake
or
from
the
quick
release
of
the
accele
ra
tor
pedal
after
treading
it
slightly
In
such
a
situation
a
throttle
lever
strikes
against
the
dash
pot
stem
and
makes
the
primary
throttle
valve
close
gradually
thus
keeping
the
engine
running
ALTITUDE
COMPENSATOR
California
models
The
higher
the
altitude
the
richer
the
air
fuel
mixture
ratio
and
there
fore
the
higher
exhaust
gas
emissions
even
though
the
engine
is
properly
ad
justed
for
low
altitude
driving
The
altitude
compensator
is
design
ed
to
meet
EiiriSSion
S13ndards
for
driving
in
both
low
and
high
altitudes
At
high
altitudes
additional
air
is
sup
plied
to
the
carburetor
by
the
altitude
compensator
When
the
altitude
com
pensator
lever
is
set
at
H
air
is
conducted
through
an
air
passage
to
the
carburetor
The
air
passage
is
closed
when
the
lever
is
set
at
L
H
L
Lever
When
operating
the
H
L
lever
fol
low
these
instructions
H
position
Should
be
used
for
general
driving
in
those
areas
designated
by
law
as
High
Altitude
Counties
L
position
For
use
outside
those
areas
desig
nated
as
High
Altitude
Counties
Page 168 of 537
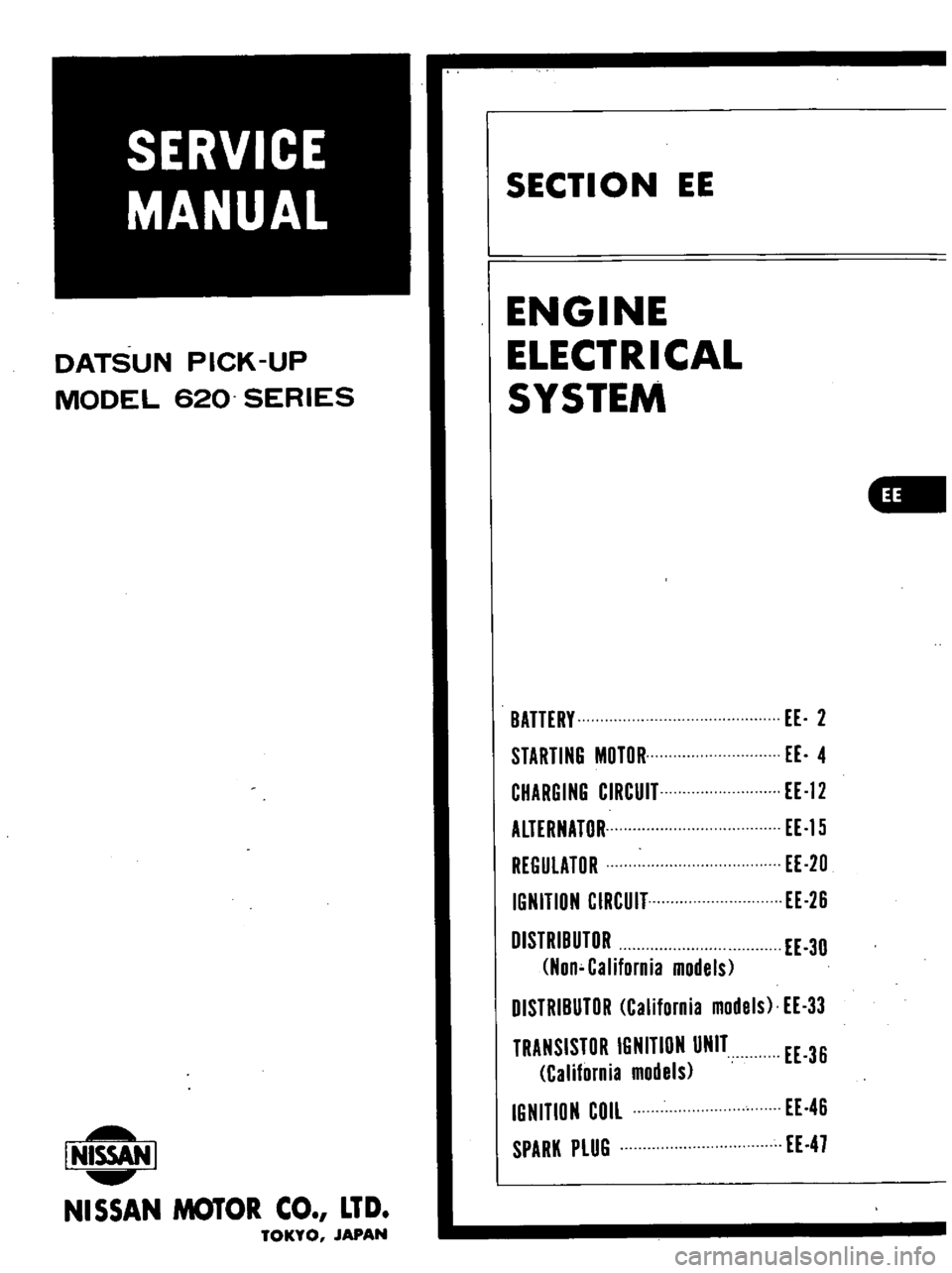
DATSUN
PICK
UP
MODEL
620
SERIES
I
NISSAN
I
NISSAN
MOTOR
CO
LTD
TOKYO
JAPAN
SECTION
EE
ENGINE
ELECTRICAL
SYSTEM
BATTERY
EE
2
STARTING
MOTOR
EE
4
CHARGING
CIRCUIT
EE
12
ALTERNATOR
EE
15
REGULATOR
EE
20
IGNITION
CIRCUIT
EE
26
DISTRIBUTOR
EE
30
Non
California
models
DISTRIBUTOR
California
models
EE
33
TRANSISTOR
IGNITION
UNIT
California
models
IGNITION
COIL
SPARK
PLUG
EE
36
EE
46
EE
47
Page 179 of 537
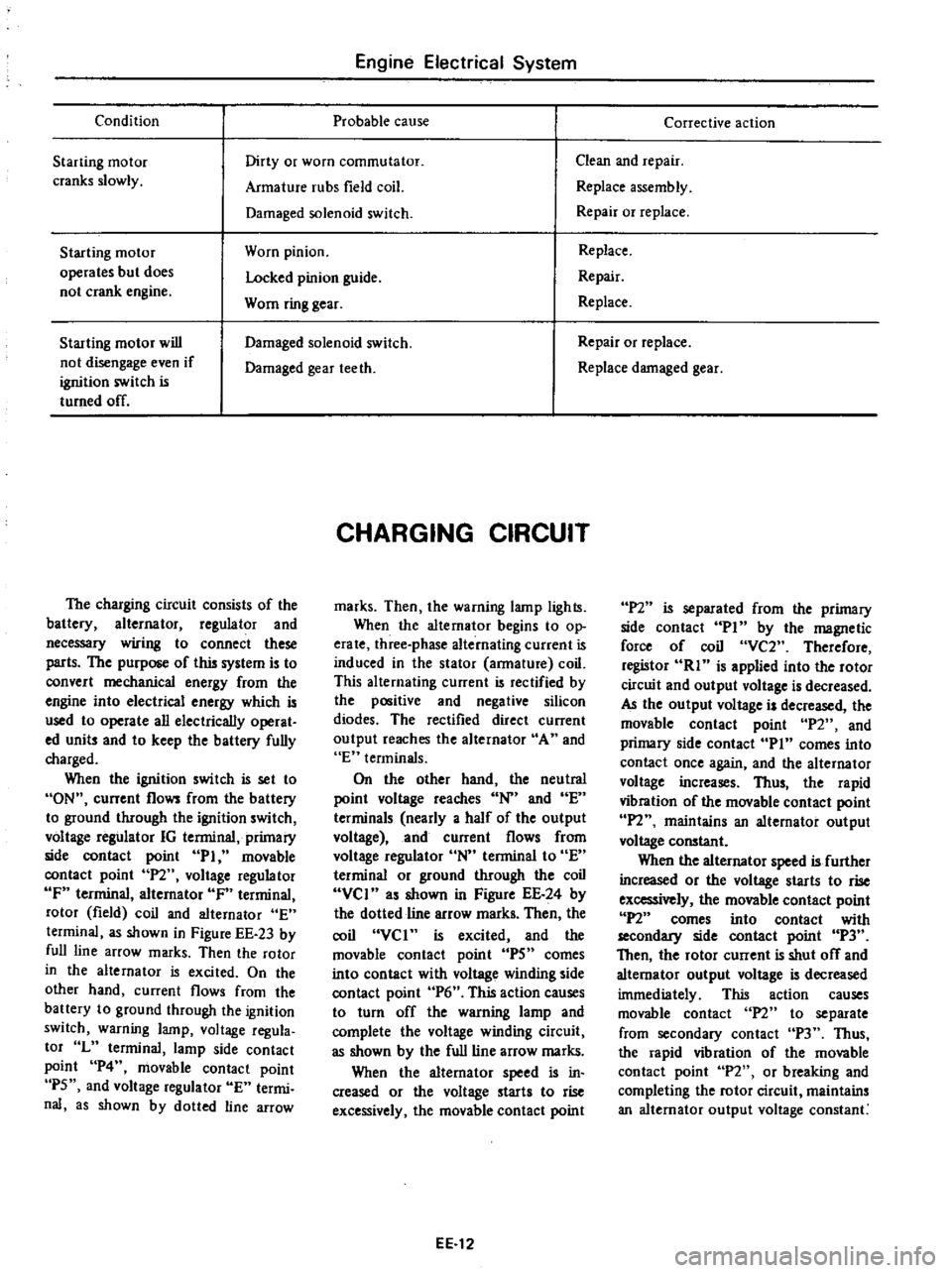
Condition
Engine
Electrical
System
Probable
cause
Starting
motor
cranks
slowly
Dirty
or
worn
commutator
Armature
rubs
field
coil
Damaged
solenoid
switch
Starting
motor
operates
but
does
not
crank
engine
Worn
pinion
Locked
pinion
guide
Worn
ring
gear
Starting
motor
will
not
disengage
even
if
ignition
switch
is
turned
off
Damaged
solenoid
switch
Damaged
gear
teeth
The
charging
circuit
consists
of
the
battery
alternator
regulator
and
necessary
wiring
to
connect
these
parts
The
purpose
of
this
system
is
to
convert
mechanical
energy
from
the
engine
into
electrical
energy
which
is
used
to
operate
all
electrically
operat
ed
units
and
to
keep
the
battery
fully
charged
When
the
ignition
switch
is
set
to
ON
current
flows
from
the
battery
to
ground
through
the
ignition
switch
voltage
regulator
IG
terminal
primary
side
contact
point
PI
movable
contact
point
P2
voltage
regulator
IF
terminal
alternator
IF
terminal
rotor
field
coil
and
alternator
E
terminal
as
shown
in
Figure
EE
23
by
full
line
arrow
marks
Then
the
rotor
in
the
alternator
is
excited
On
the
other
hand
current
flows
from
the
battery
to
ground
through
the
ignition
switch
warning
lamp
voltage
regula
tor
L
terminal
lamp
side
contact
point
P4
movable
contact
point
P5
and
voltage
regulator
E
termi
nal
as
shown
by
dotted
line
arrow
CHARGING
CIRCUIT
marks
Then
the
warning
lamp
lights
When
the
alternator
begins
to
op
erate
three
phase
alternating
current
is
induced
in
the
stator
armature
coil
This
alternating
current
is
rectified
by
the
positive
and
negative
silicon
diodes
The
rectified
direct
current
output
reaches
the
alternator
A
and
E
terminals
On
the
other
hand
the
neutral
point
voltage
reaches
N
and
E
terminals
nearly
a
half
of
the
output
voltage
and
current
flows
from
voltage
regulator
N
terminal
to
E
terminal
or
ground
through
the
coil
VCI
as
shown
in
Figure
EE
24
by
the
dotted
line
arrow
marks
Then
the
coil
VCI
is
excited
and
the
movable
contact
point
IPS
comes
into
contact
with
voltage
winding
side
contact
point
P6
This
action
causes
to
turn
off
the
warning
lamp
and
complete
the
voltage
winding
circuit
as
shown
by
the
full
line
arrow
marks
When
the
alternator
speed
is
in
creased
or
the
voltage
starts
to
rise
excessively
the
movable
contact
point
EE
12
Corrective
action
Clean
and
repair
Replace
assembly
Repair
or
replace
Replace
Repair
Replace
Repair
or
replace
Replace
damaged
gear
P2
is
separated
from
the
primary
side
contact
PI
by
the
magnetic
force
of
coil
VC2
Therefore
registor
RI
is
applied
into
the
rotor
circuit
and
output
voltage
is
decreased
AJ
the
output
voltage
is
decreased
the
movable
contact
point
P2
and
primary
side
contact
Pin
comes
into
contact
once
again
and
the
alternator
voltage
increases
Thus
the
rapid
vibration
of
the
movable
contact
point
IPl
maintains
an
alternator
output
voltage
constant
When
the
alternator
speed
is
further
increased
or
the
voltage
starts
to
rise
excessively
the
movable
contact
point
P2
comes
into
contact
with
secondllJ
side
contact
point
P3
Then
the
rotor
current
is
shut
off
and
alternator
output
voltage
is
decreased
immediately
This
action
causes
movable
contact
n
to
separate
from
secondary
contact
P3
Thus
the
rapid
vibration
of
the
movable
contact
point
P2
or
breaking
and
completing
the
rotor
circuit
maintains
an
alternator
output
voltage
constant
Page 180 of 537
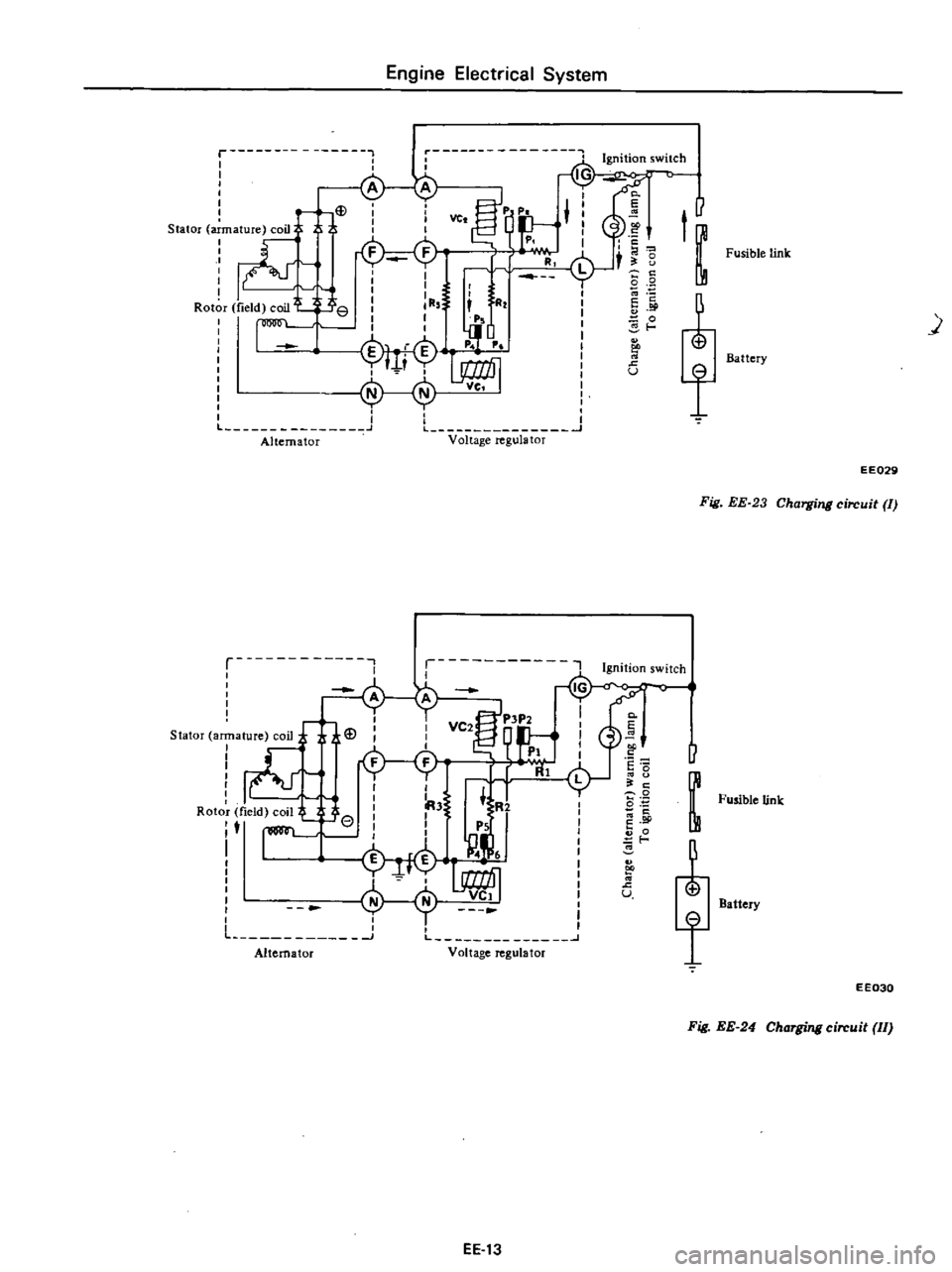
Engine
Electrical
System
r
l
I
I
I
i
r
Ye
Ff
p
Stator
ma
ture
coiJ
FF
vw
I
I
RI
L
Rot
r
field
C
oil
e
R
I
I
I
I
I
J
1
J
Alternator
Voltage
regulator
11
t
c
I
Fusible
link
t
8
c
J
5
9
i
c
c
0
Battery
t
u
J
EE029
Fig
EE
23
Charging
circuit
II
p
ns
1
Slator
ar
ature
coil
teJ
U
2iI
I
r
R
l
I
I
A3
R2
0
Fusible
link
Roto
field
coil
e
I
I
t
I
I
PS
M
g
j
t
i
H
U
Battery
Lh
A
l
a
o
J
L
V
It
g
t
f
EE030
Fig
EE
24
Charging
circuit
II
EE
13
Page 181 of 537
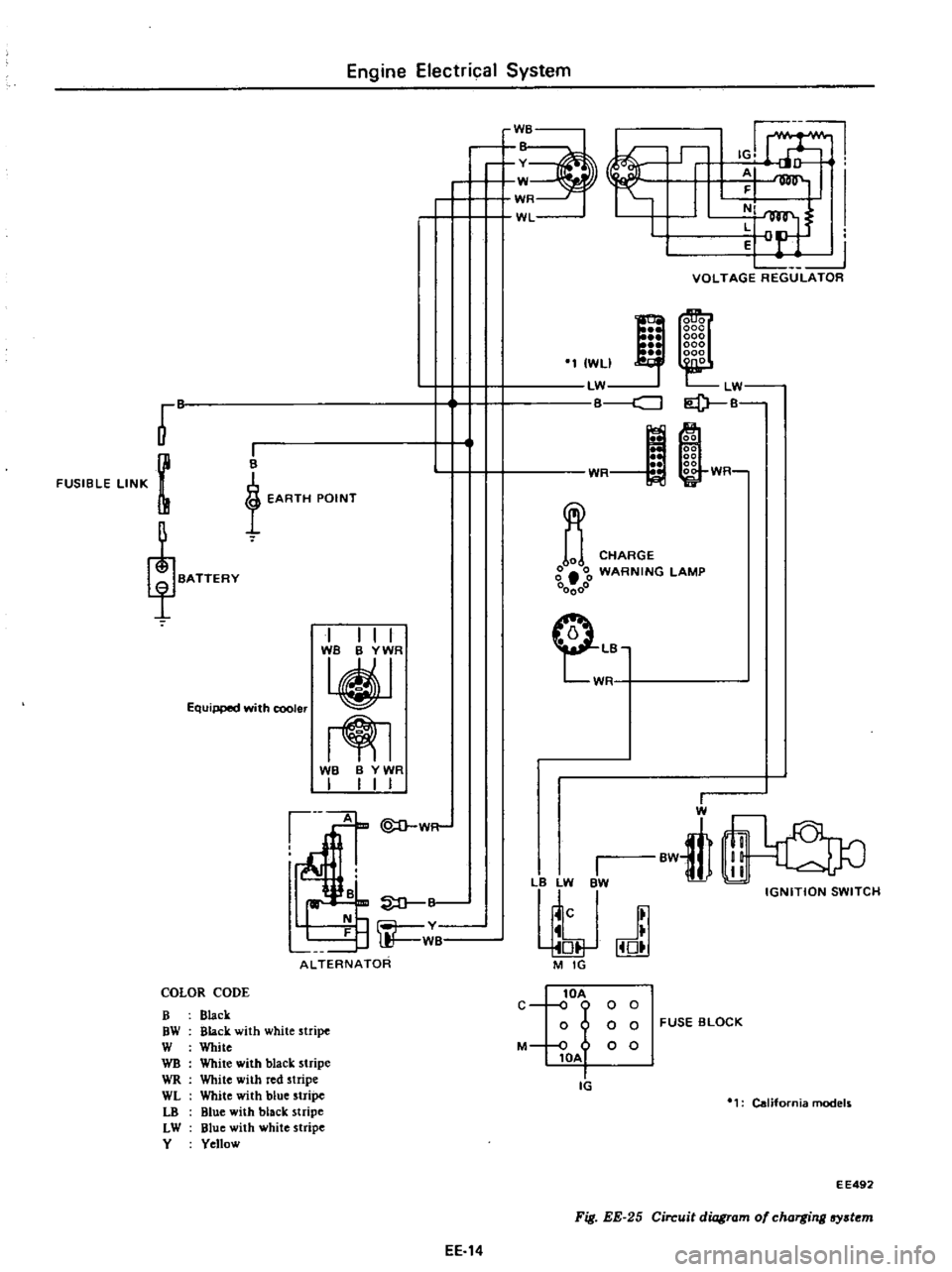
Engine
Electrical
System
B
v
W
WR
WL
L2
VOLTAGE
REGULATOR
co
LW
I
P
B
r
FUSIBLE
LINK
m
I
WLI
LW
cJ
I
B
t
EARTH
POINT
m
WR
WR
CHARGE
g
00
WARNING
lAMP
00000
Equipped
with
cooler
I
I
I
I
TjT
m
CLB
W
WB
B
YWR
I
I
I
I
1
W
B
rn
ALTERNATOR
I
l
LW
BW
j
J
M
IG
I
W
BwtIl
IGNITION
SWITCH
COLOR
CODE
B
Black
OW
Black
with
white
stripe
W
White
WB
White
with
black
stripe
WR
White
with
red
stripe
WL
White
with
blue
stripe
LO
Blue
with
black
stripe
LW
Blue
with
white
stripe
Y
Yellow
lOA
C
o
0
0
0
o
0
0
FUSE
BLOCK
M
0
0
0
lOA
Ii
California
models
E
E492
Fig
EE
25
Circuit
diagram
of
charging
lfY
t
m
EE
14
Page 182 of 537
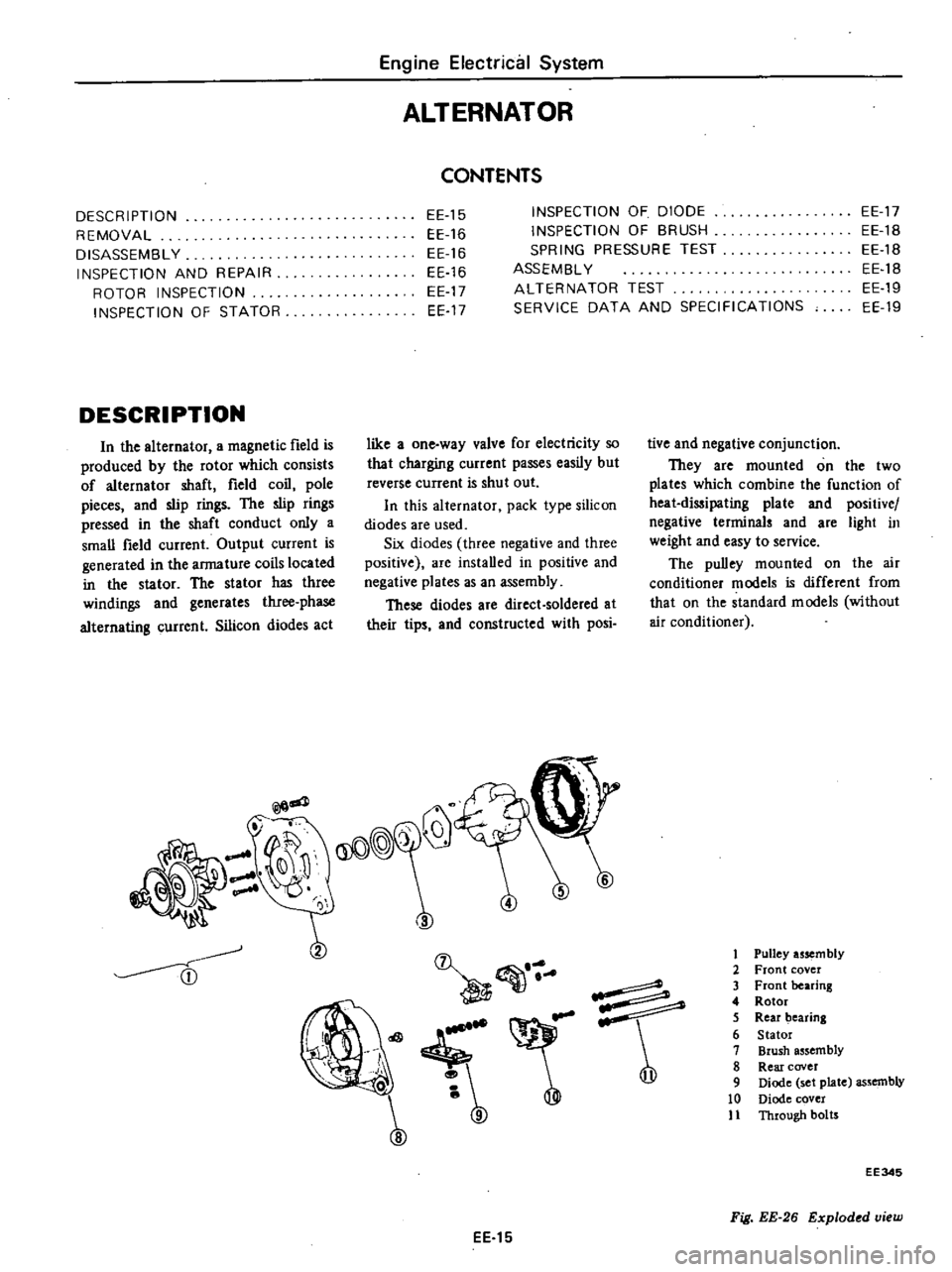
DESCRIPTION
REMOVAL
DISASSEMBLY
INSPECTION
AND
REPAIR
ROTOR
INSPECTION
INSPECTION
OF
STATOR
DESCRIPTION
In
the
alternator
a
magnetic
field
is
produced
by
the
rotor
which
consists
of
alternator
shaft
field
coil
pole
pieces
and
slip
rings
The
slip
rings
pressed
in
the
shaft
conduct
only
a
small
field
current
Output
current
is
generated
in
the
armature
coils
located
in
the
stator
The
stator
has
three
windings
and
generates
three
phase
alternating
current
Silicon
diodes
act
@God
A
tfff
Engine
Electrical
System
ALTERNATOR
CONTENTS
EE
15
EE
16
EE
16
EE
16
EE
17
EE
17
INSPECTION
OF
DIODE
INSPECTION
OF
BRUSH
SPRING
PRESSURE
TEST
ASSEMBL
Y
ALTERNATOR
TEST
SERVICE
DATA
AND
SPECIFICATIONS
EE
17
EE
1B
EE1B
EE
1B
EE19
EE
19
like
a
one
way
valve
for
electricity
so
that
charging
current
passes
easily
but
reverse
current
is
shut
out
In
this
alternator
pack
type
silicon
di
odes
are
used
Six
diodes
three
negative
and
three
positive
are
installed
in
positive
and
negative
plates
as
an
assembly
These
diodes
are
direct
soldered
at
their
tips
and
constructed
with
posi
3
2
I
4
e
o
e
9
tive
and
negative
conjunction
They
are
mounted
on
the
two
plates
which
combine
the
function
of
heat
dissipating
plate
and
positive
negative
terminals
and
are
light
in
weight
and
easy
to
service
The
pulley
mounted
on
the
air
conditioner
models
is
different
from
that
on
the
standard
models
without
air
conditioner
1
Pulley
usem
bly
2
Front
cover
3
Front
bearing
4
Rotor
5
Rear
bearing
6
Stator
7
Brush
assembly
8
Rear
cover
9
Diode
set
plate
assembly
10
Diode
cover
11
Through
botrs
EE
15
EE345
Fig
EE
26
Exploded
view