diagram DATSUN PICK-UP 1977 Service Manual
[x] Cancel search | Manufacturer: DATSUN, Model Year: 1977, Model line: PICK-UP, Model: DATSUN PICK-UP 1977Pages: 537, PDF Size: 35.48 MB
Page 57 of 537
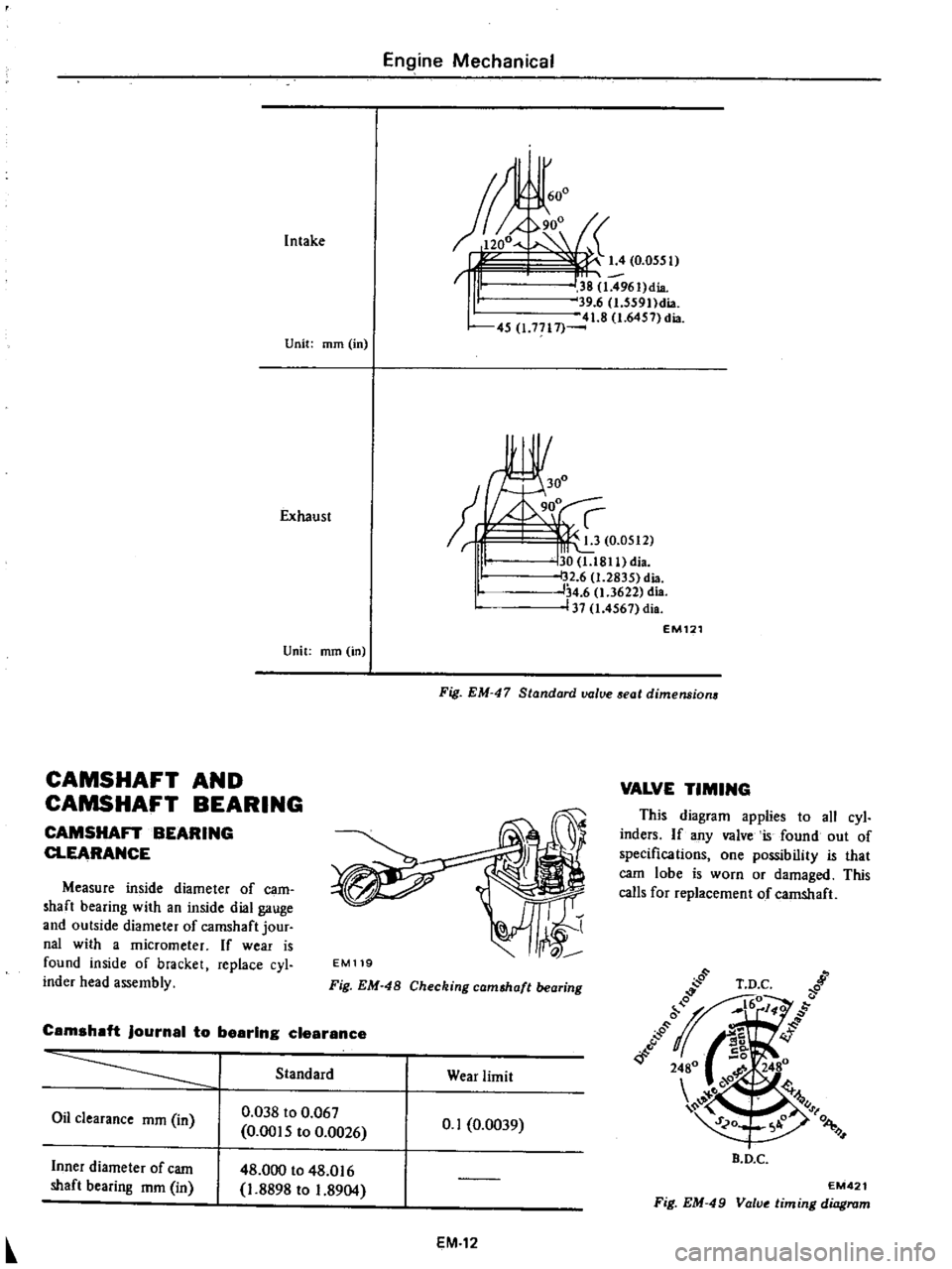
Intake
Engine
Mechanical
I
600
38
1
496I
dia
W
39
6
I
559Ildia
1
8
1
6457
dia
45
1
71l1
Unit
mm
in
Exhaust
30
30
1
l811
di
I
32
6
2835
dia
34
6
1
3622
dia
137
1
4567
dia
Unit
mm
m
CAMSHAFT
AND
CAMSHAFT
BEARING
CAMSHAnBEARING
CLEARANCE
Measure
inside
diameter
of
earn
haft
beating
with
an
inside
dial
gauge
and
outside
diameter
of
camshaft
jour
nal
with
a
micrometer
If
wear
is
found
inside
of
bracket
replace
cyl
inder
head
assembly
EM121
Fig
EM
47
Standard
value
aeat
dimensions
EM119
Fig
EM
48
Checking
cam
haft
bearing
Camshaft
journal
to
bearing
clearance
Standard
Wear
limit
Oil
clearance
mm
in
0
038
to
0
067
0
0015
to
0
0026
0
1
0
0039
Inner
diameter
of
earn
shaft
bearing
mm
in
48
000
to
48
016
1
8898
to
1
8904
EM
12
VALVE
TIMING
This
diagram
applies
to
all
cyl
inders
If
any
valve
is
found
out
of
specifications
one
possibility
that
carn
lobe
is
worn
or
damaged
This
calls
for
replacement
of
camshaft
B
D
C
EM421
Fig
EM
49
Value
timing
diagram
Page 160 of 537
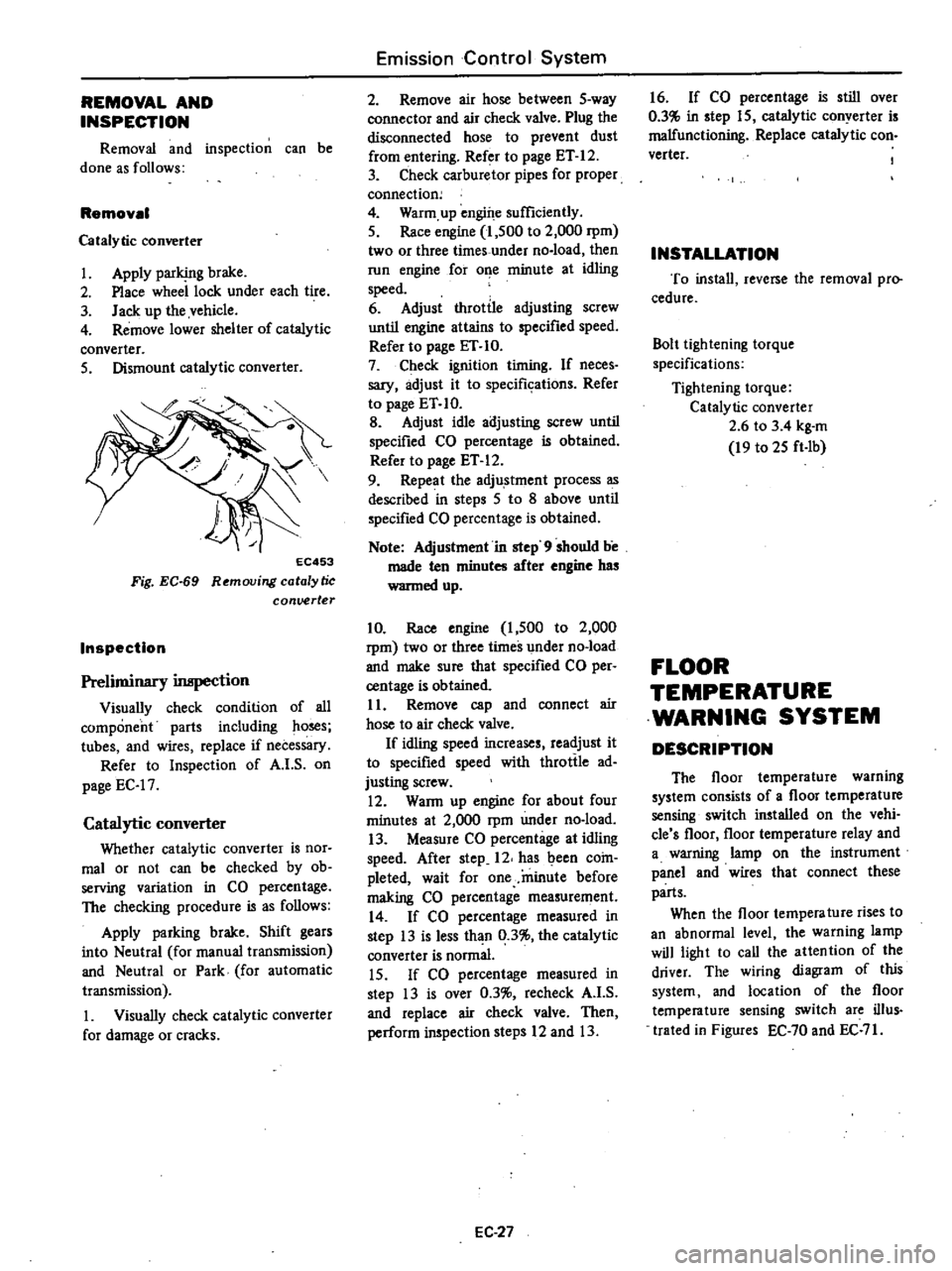
REMOVAL
AND
INSPECTION
Removal
and
inspection
can
be
done
as
follows
Removal
Catalytic
converter
1
Apply
parking
brake
2
Place
wheel
lock
under
each
tire
3
Jack
up
the
vehicle
4
Remove
lower
shelter
of
catalytic
converter
5
Dismount
catalytic
converter
EC453
Fig
EC
69
Removing
catalytic
conuerter
Inspection
Preliminary
inspection
Visually
check
condition
of
all
component
parts
including
ho
s
tubes
and
wires
replace
if
necessary
Refer
to
Inspection
of
A
I
S
on
page
EC
17
Catalytic
converter
Whether
catalytic
converter
is
nor
mal
or
not
can
be
checked
by
ob
serving
variation
in
CO
percentage
The
checking
procedure
is
as
follows
Apply
parking
brake
Shift
gears
into
Neutral
for
manual
transmission
and
Neutral
or
Park
for
automatic
transmission
1
Visually
check
catalytic
converter
for
damage
or
cracks
Emission
Control
System
2
Remove
air
hose
between
5
way
connector
and
air
check
valve
Plug
the
disconnected
hose
to
prevent
dust
from
entering
Refer
to
page
ET
12
3
Check
carburetor
pipes
for
proper
connection
4
Warm
up
engine
sufficiently
5
Race
engine
1
500
to
2
000
rpm
two
or
three
times
under
no
load
then
run
engine
for
o
e
minute
at
idling
speed
6
Adjust
throttle
adjusting
screw
until
engine
attains
to
specified
speed
Refer
to
page
ET
10
7
Check
ignition
timing
If
neces
sary
adjust
it
to
specifkations
Refer
to
page
ET
10
B
Adjust
idle
adjusting
screw
until
specified
CO
percentage
is
obtained
Refer
to
page
ET
12
9
Repeat
the
adju
stment
process
as
described
in
steps
5
to
8
above
until
specified
CO
percentage
is
obtained
Note
Adjustment
in
step
9
should
be
made
ten
minutes
after
engine
has
wanned
up
10
Race
engine
1
500
to
2
000
rpm
two
or
three
times
under
no
load
and
make
sure
that
specified
CO
per
centage
is
obtained
11
Remove
cap
and
connect
air
hose
to
air
check
valve
If
idling
speed
increases
readjust
it
to
specified
speed
with
throttle
ad
justing
screw
12
WaRn
up
engine
for
about
four
minutes
at
2
000
rpm
under
no
load
13
Measure
CO
percentage
at
idling
speed
After
step
12
has
been
coin
pleted
wait
for
one
minute
before
making
CO
percentage
measurement
14
If
CO
percentage
measured
in
step
13
is
less
than
0
3
the
catalytic
converter
is
normal
15
If
CO
percentage
measured
in
step
13
is
over
0
3
recheck
A
I
S
and
replace
air
check
valve
Then
perform
inspection
steps
12
and
13
EC
27
16
If
CO
percentage
is
still
over
0
3
in
step
15
catalytic
conyerter
is
malfunctioning
Replace
catalytic
con
verter
INSTALLATION
To
install
reverse
the
removal
pro
cedure
Bolt
lightening
torque
specifications
Tightening
torque
Catalytic
converter
2
6
to
3
4
kg
m
19
to
25
ft
Ib
FLOOR
TEMPERATURE
WARNING
SYSTEM
DESCRIPTION
The
floor
temperature
warning
system
consists
of
a
floor
temperature
sensing
switch
installed
on
the
vehi
cle
s
floor
floor
temperature
relay
and
a
warning
lamp
on
the
instrument
panel
and
wires
that
connect
these
parts
When
the
floor
tempera
ture
rises
to
an
abnormal
level
the
warning
lamp
will
light
to
call
the
attention
of
the
driver
The
wiring
diagram
of
this
system
and
location
of
the
floor
temperature
sensing
switch
are
ilIus
trated
in
Figures
EC
70
and
EC
71
Page 161 of 537
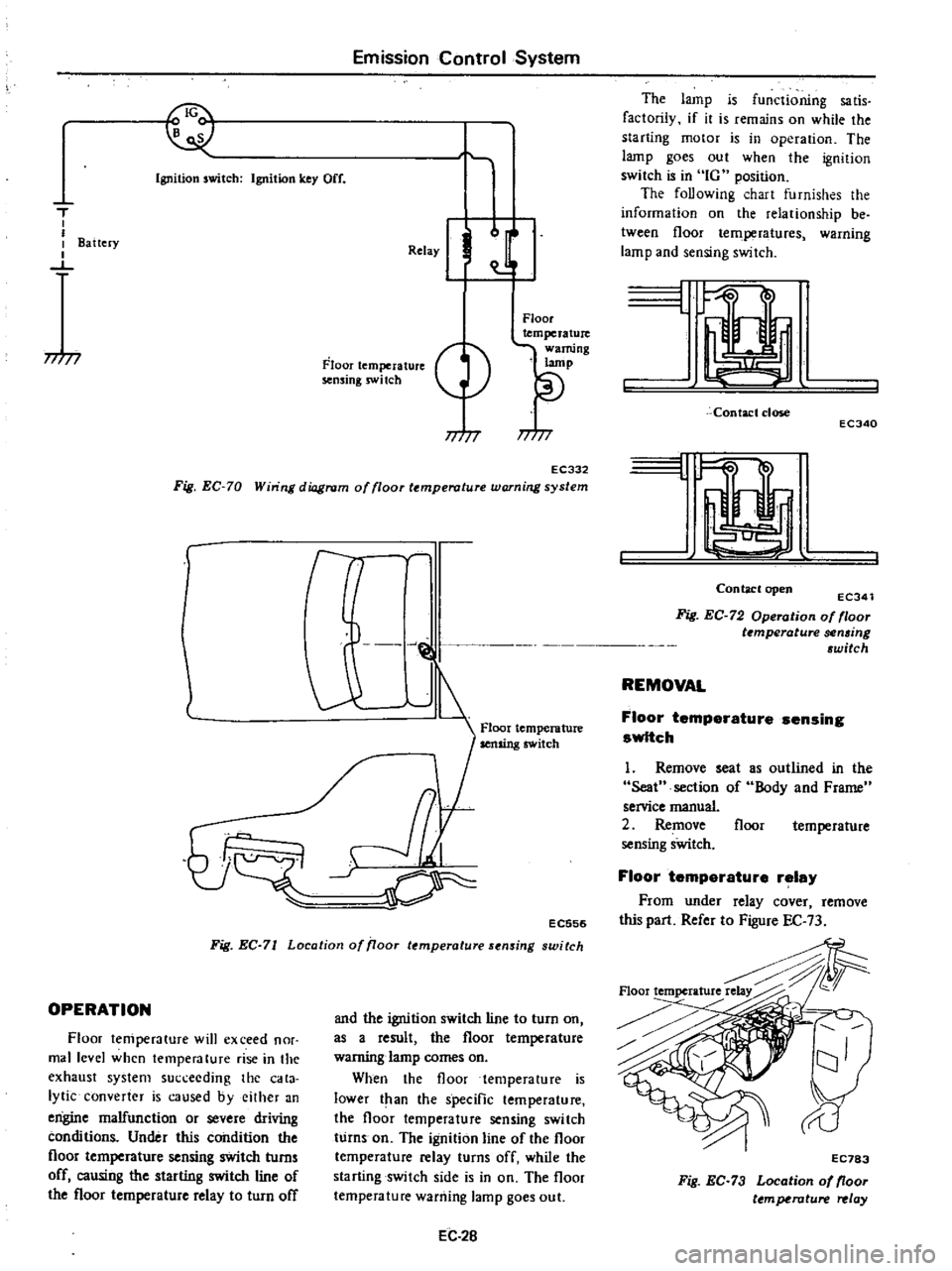
I
Emission
Control
System
Ignition
switch
Ignition
key
Off
T
I
I
I
Battery
I
J
77
77
Relay
J
Floor
temperature
sensing
swi
tch
Floor
temperature
warning
lamp
77
77
EC332
Fig
EC
70
Win
ng
diagram
of
floor
temperature
warning
system
r
l
J
@
1
Floor
temperature
Ij
cr
EC556
Fig
EC
71
Location
of
iJoor
temperature
sensing
switch
OPERATION
Floor
temperature
will
exceed
nor
mal
level
when
temperature
rise
in
the
exhaust
system
succeeding
the
cata
lytic
converter
is
caused
byeilher
an
engine
malfunction
or
severe
driving
conditions
Under
this
condition
the
floor
temperature
sensing
switch
turns
off
causing
the
starting
switch
line
of
the
floor
temperature
relay
to
turn
off
and
the
ignition
switch
line
to
turn
on
as
a
result
the
floor
temperature
warning
lamp
comes
on
When
the
floor
temperature
is
lower
t
an
the
specific
temperature
the
floor
temperature
sensing
switch
turns
on
The
ignition
line
of
the
floor
temperature
relay
turns
off
while
the
starting
switch
side
is
in
on
The
floor
temperature
warning
lamp
goes
out
EC
2B
The
lamp
is
functioning
sa
tis
factorily
if
it
is
remains
on
while
the
starting
motor
is
in
operation
The
lamp
goes
out
when
the
ignition
switch
is
in
IG
position
The
foUowing
chart
furnishes
the
information
on
the
relationship
be
tween
floor
temperatures
warning
lamp
and
sensing
switch
L
Contact
close
ECJ40
I
Contaclopen
ECJ41
Fig
EC
72
Operation
of
floor
t
mperature
sen6ing
6witch
REMOVAL
Floor
temperature
sensing
switch
1
Remove
seat
Seat
section
of
service
manual
2
Remove
sensing
sWitch
as
outlined
in
the
Body
and
Frame
floor
temperature
Floor
temperature
relay
From
under
relay
cover
remove
this
part
Refer
to
Figure
EC
73
Floortemperature
EC783
Fig
EC
73
Location
of
floor
ttmperature
relay
Page 172 of 537
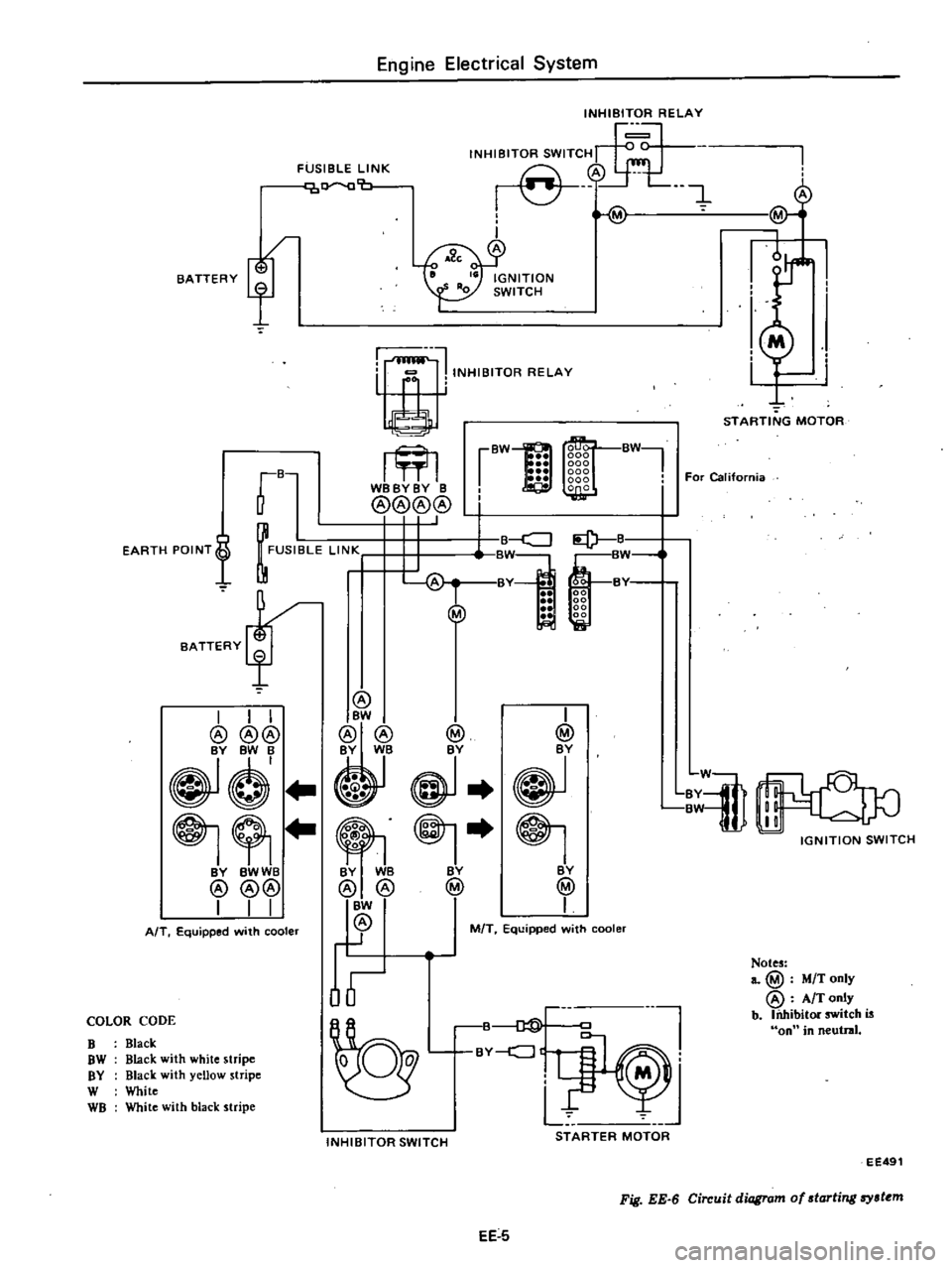
fB
WBBYBY
B
@@@@
I
I
FUSIBLE
lIN
r
T
H
BATTERY
rJ
BATTERY
f
EARTH
POINT
f
I
I
I
@@@
Y
BY
BWWB
@@@
I
I
I
AfT
E
quipped
with
cooler
COLOR
CODE
B
Black
OW
Black
with
white
stripe
BY
Black
with
yellow
stripe
W
White
WB
White
with
black
stripe
Engine
Electrical
System
FUSIBLE
LINK
1Y
O
b
INHIBITOR
RELAY
INHIBITOR
SWITCH
A
I
J
Y
@
I
A
l
rBW
j
CJ
B
W
BWI
000
000
ggg
For
California
I
Bd
f
00
00
00
00
Q
BW
B
Y
BY
WB
BY
@
@
@
BW
@
I
M
T
Equipped
with
cooler
@
I
@
BY
BY
@
I
STARTING
MOTOR
l
BY
BW
9
IGNITION
SWITCH
L
INHIBITOR
SWITCH
STARTER
MOTOR
Notes
a
@
M
T
only
@
A
T
only
b
Inhibitor
switch
is
on
in
neutral
EE
5
Fig
EE
6
Circuit
diagram
0
starting
systom
eE491
Page 181 of 537
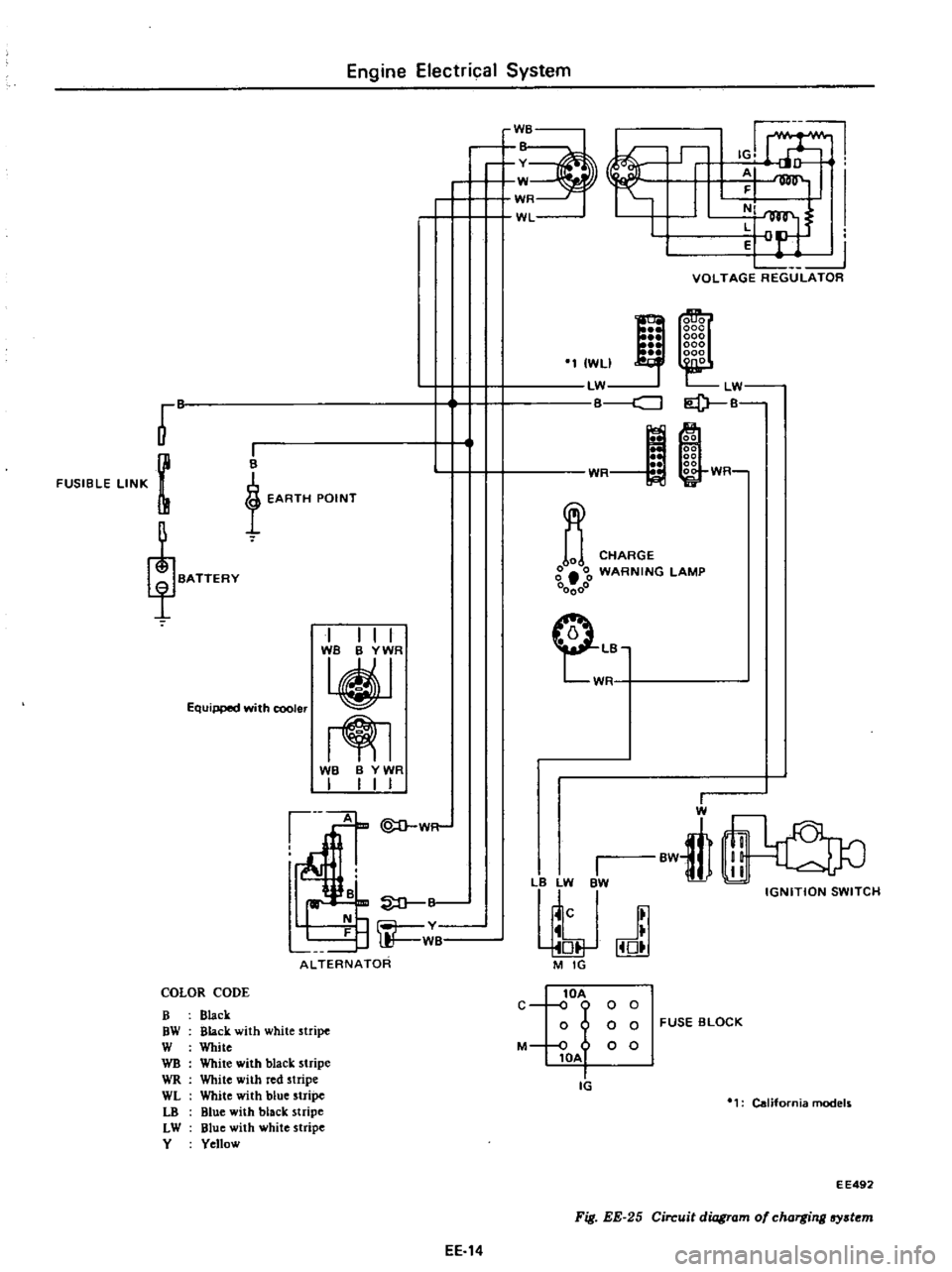
Engine
Electrical
System
B
v
W
WR
WL
L2
VOLTAGE
REGULATOR
co
LW
I
P
B
r
FUSIBLE
LINK
m
I
WLI
LW
cJ
I
B
t
EARTH
POINT
m
WR
WR
CHARGE
g
00
WARNING
lAMP
00000
Equipped
with
cooler
I
I
I
I
TjT
m
CLB
W
WB
B
YWR
I
I
I
I
1
W
B
rn
ALTERNATOR
I
l
LW
BW
j
J
M
IG
I
W
BwtIl
IGNITION
SWITCH
COLOR
CODE
B
Black
OW
Black
with
white
stripe
W
White
WB
White
with
black
stripe
WR
White
with
red
stripe
WL
White
with
blue
stripe
LO
Blue
with
black
stripe
LW
Blue
with
white
stripe
Y
Yellow
lOA
C
o
0
0
0
o
0
0
FUSE
BLOCK
M
0
0
0
lOA
Ii
California
models
E
E492
Fig
EE
25
Circuit
diagram
of
charging
lfY
t
m
EE
14
Page 193 of 537
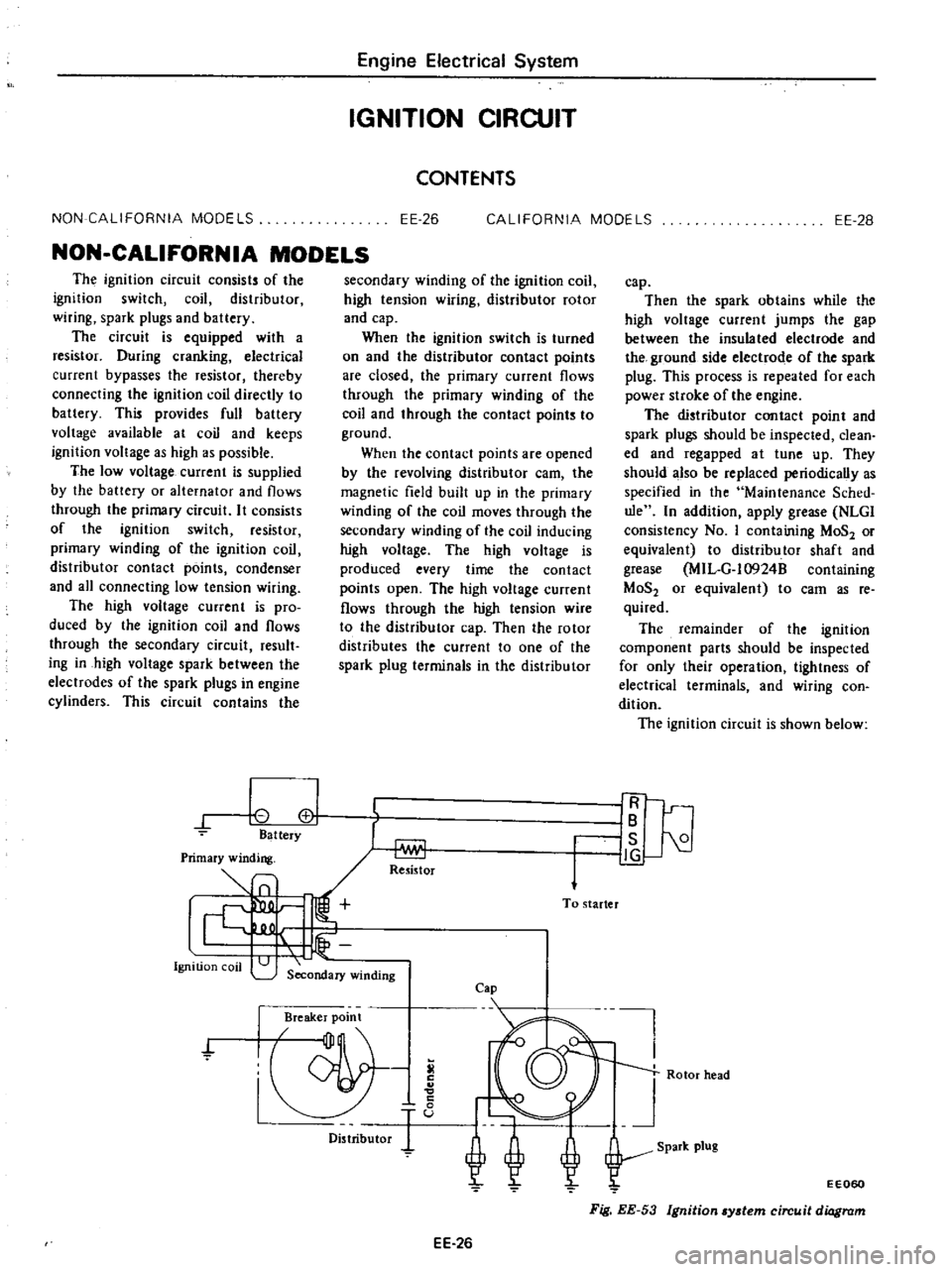
NON
CALIFORNIA
MODELS
Engine
Electrical
System
IGNITION
CIRCUIT
CONTENTS
EE
26
CALIFORNIA
MODELS
EE
2B
NON
CALIFORNIA
MODELS
The
ignition
circuit
consists
of
the
ignition
switch
coil
distributor
wiring
spark
plugs
and
battery
The
circuit
is
equipped
with
a
resistor
During
cranking
electrical
current
bypasses
the
resistor
thereby
connecting
the
ignition
coil
directly
to
battery
This
provides
full
battery
voltage
available
at
coil
and
keeps
ignition
voltage
as
high
as
possible
The
low
voltage
current
is
supplied
by
the
battery
or
alternator
and
flows
through
the
primary
circuit
It
consists
of
the
ignition
switch
resistor
primary
winding
of
the
ignition
coil
distributor
contact
points
condenser
and
all
connecting
low
tension
wiring
The
high
voltage
current
is
pro
duced
by
the
ignition
coil
and
flows
through
the
secondary
circuit
result
ing
in
high
voltage
spark
between
the
electrodes
of
the
spark
plugs
in
engine
cylinders
This
circuit
contains
the
0
cl
Battery
Ignition
coil
secondary
winding
of
the
ignition
coil
high
tension
wiring
distributor
rotor
and
cap
When
the
ignition
switch
is
turned
on
and
the
distributor
contact
points
are
closed
the
primary
current
flows
through
the
primary
winding
of
the
coil
and
through
the
contact
points
to
ground
When
the
contact
points
are
opened
by
the
revolving
distributor
earn
the
magnetic
field
built
up
in
the
primary
winding
of
the
coil
moves
through
the
secondary
winding
of
the
coil
inducing
high
voltage
The
high
voltage
is
produced
every
time
the
contact
points
open
The
high
voltage
current
flows
through
the
high
tension
wire
to
the
distributor
cap
Then
the
rotor
distributes
the
current
to
one
of
the
spark
plug
terminals
in
the
distributor
Re5istor
To
starter
Secondary
winding
Cap
Breaker
point
f
Distributor
EE
26
cap
Then
the
spark
obtains
while
the
high
voltage
current
jumps
the
gap
between
the
insulated
electrode
and
the
ground
side
electrode
of
the
spark
plug
This
process
is
repeated
for
each
power
stroke
of
the
engine
The
distributor
contact
point
and
spark
plugs
should
be
inspected
clean
ed
and
regapped
at
tune
up
They
should
also
be
replaced
periodically
as
specified
in
the
Maintenance
Sched
ule
In
addition
apply
grease
NLGl
consistency
No
I
containing
MoS2
or
equivalent
to
distributor
shaft
and
grease
MIL
G
l0924B
containing
MoS2
or
equivalent
to
cam
as
reo
quired
The
remainder
of
the
ignition
component
parts
should
be
inspected
for
only
their
operation
tightness
of
electrical
terminals
and
wiring
con
dition
The
ignition
circuit
is
shown
below
IR
IB
I
is
21
J
g
Rotor
head
EE060
Fig
EE
53
Ignition
ydem
circuit
diagram
Page 194 of 537
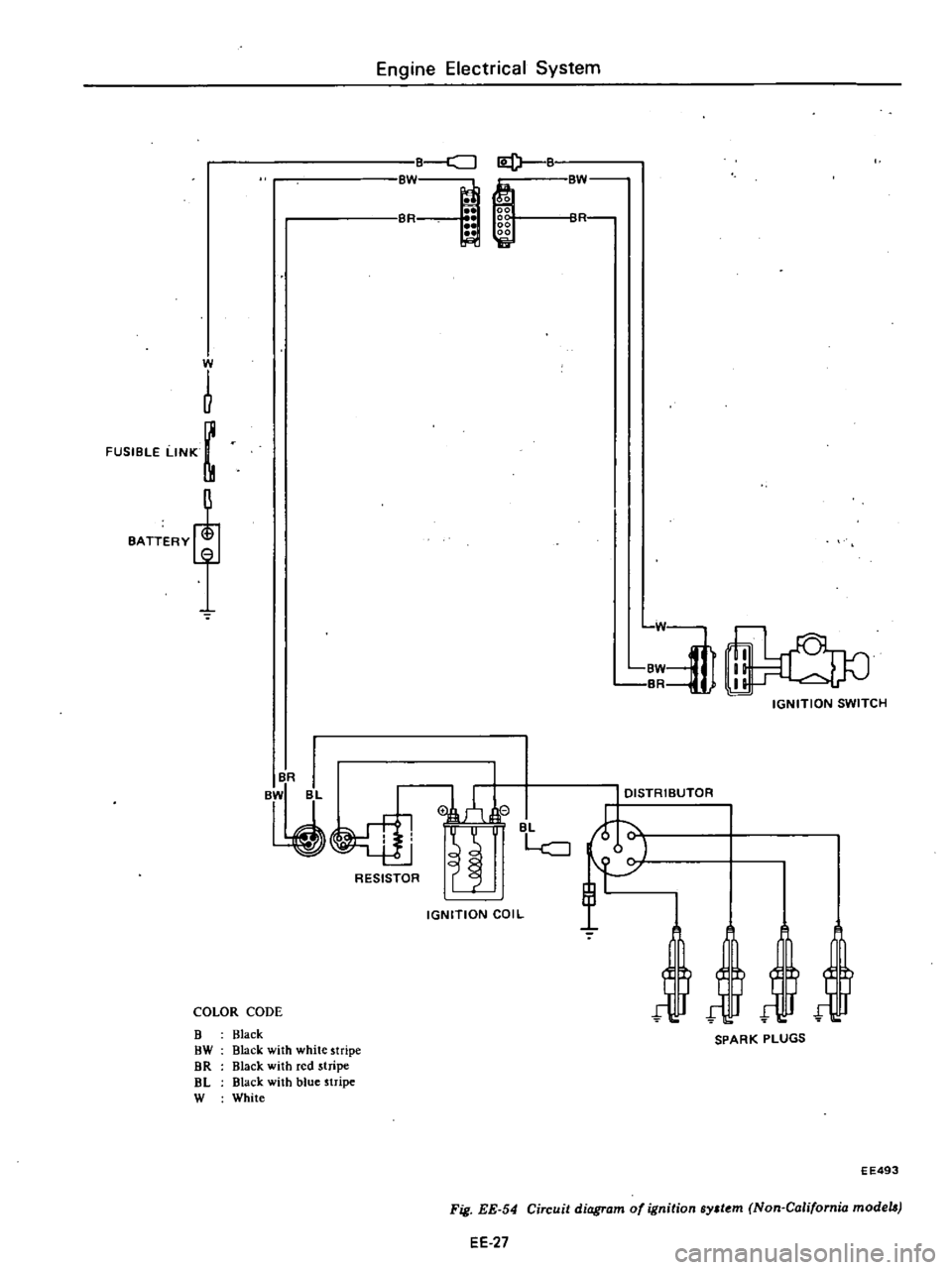
FUSIBLE
LtNK
m
Engine
Electrical
System
E
CJI2t
Bf
o
00
00
fOl
R
BL
I
ti
L
oj
L
C
J
RESISTOR
IGNITION
COIL
COLOR
CODE
B
Black
OW
Black
with
white
stripe
DR
Black
with
red
stripe
aL
Black
with
blue
stripe
W
White
W
R
Wj
BW
BR
IGNITION
SWtTCH
DISTRtBUTOR
jjj
SPARK
PLUGS
EE493
EE
27
Fig
EE
54
Circuit
diagram
of
ignition
ByJt
m
Non
California
models
Page 195 of 537
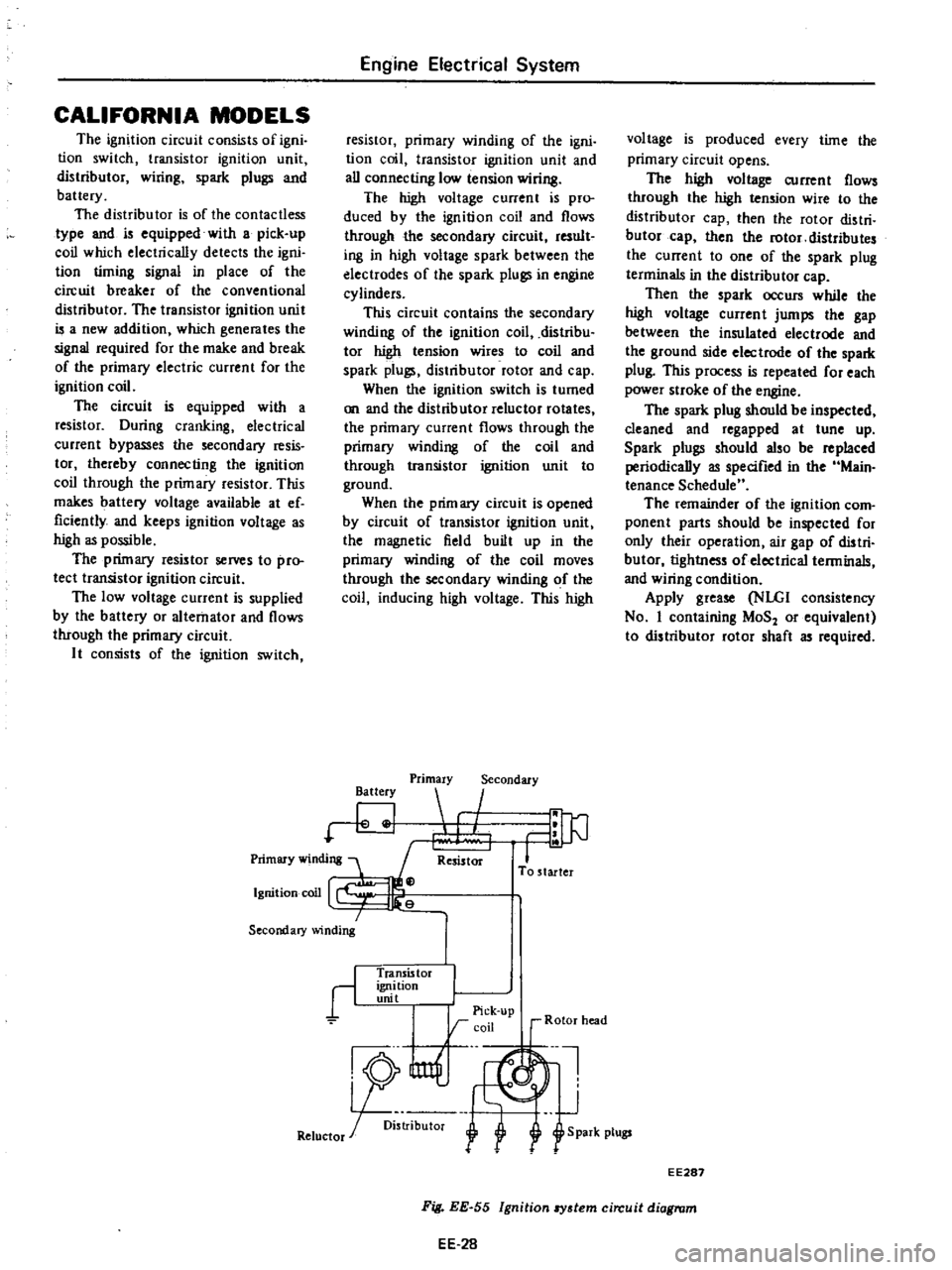
Primary
winding
1
Ignition
coo
I
Secondary
winding
CALIFORNIA
MODELS
The
ignition
circuit
consists
of
igni
tion
switch
transistor
ignition
unit
distributor
wiring
spark
plugs
and
battery
The
distributor
is
of
the
contactless
type
and
is
equipped
with
a
pick
up
coil
which
electrically
detects
the
igni
tion
timing
signal
in
place
of
the
circuit
breaker
of
the
conventional
distributor
The
transistor
ignition
unit
is
a
new
addition
which
generates
the
signal
required
for
the
make
and
break
of
the
primary
electric
current
for
the
ignition
coil
The
circuit
is
equipped
with
a
resistor
During
cranking
electrical
current
bypasses
the
secondary
resis
tor
thereby
connecting
the
ignition
coil
through
the
primary
resistor
This
makes
battery
voltage
available
at
ef
ficiently
and
keeps
ignition
voltage
as
high
as
possible
The
primary
resistor
selVeS
to
pro
tect
transistor
ignition
circuit
The
low
voltage
current
is
supplied
by
the
battery
or
alternator
and
flows
through
the
primary
circuit
It
consists
of
the
ignition
switch
Engine
Electrical
System
resistor
primary
winding
of
the
igni
tion
coil
transistor
ignition
unit
and
all
connecting
low
tension
wiring
The
high
voltage
current
is
pro
duced
by
the
ignition
coil
and
flows
through
the
secondary
circuit
result
ing
in
high
voltage
spark
between
the
electrodes
of
the
spark
plugs
in
engine
cylinders
This
circuit
contains
the
secondary
winding
of
the
ignition
coil
distribu
tor
high
tension
wires
to
coil
and
spark
plugs
distributor
rotor
and
cap
When
the
ignition
switch
is
turned
on
and
the
distributor
reluctor
rotates
the
primary
current
flows
through
the
primary
winding
of
the
coil
and
through
transistor
ignition
unit
to
ground
When
the
prim
ary
circuit
is
opened
by
circuit
of
transistor
ignition
unit
the
magnetic
field
built
up
in
the
primary
winding
of
the
coil
moves
through
the
secondary
winding
of
the
coil
inducing
high
voltage
This
high
Battery
Primary
Secondary
I
Resistor
To
starter
r
Transis
tor
ignition
unit
I
I
Pick
up
rcoil
r
Rotor
head
nl
J
R5
U1f
1
Retuctor
r
oi
l
f
S
park
plugs
voltage
is
produced
every
time
the
primary
circuit
opens
The
high
voltage
current
flows
through
the
high
tension
wire
to
the
distributor
cap
then
the
rotor
distri
butor
cap
then
the
rotor
distributes
the
current
to
one
of
the
spark
plug
terminals
in
the
distributor
cap
Then
the
spark
occurs
while
the
high
voltage
current
jumps
the
gap
between
the
insulated
electrode
and
the
ground
side
electrode
of
the
spark
plug
This
process
is
repeated
for
each
power
stroke
of
the
engine
The
spark
plug
should
be
inspected
cleaned
and
regapped
at
tune
up
Spark
plugs
should
also
be
replaced
periodically
as
specified
in
the
Main
tenance
Schedule
The
remainder
of
the
ignition
com
ponent
parts
should
be
inspected
for
only
their
operation
air
gap
of
distri
butor
tightness
of
electrical
terminals
and
wiring
condition
Apply
grease
NLGI
consistency
No
I
containing
MoS
or
equivalent
to
distributor
rotor
shaft
as
required
EE287
EE
28
Fig
EE
55
Ignition
8Y3tem
circuit
diagram
Page 196 of 537
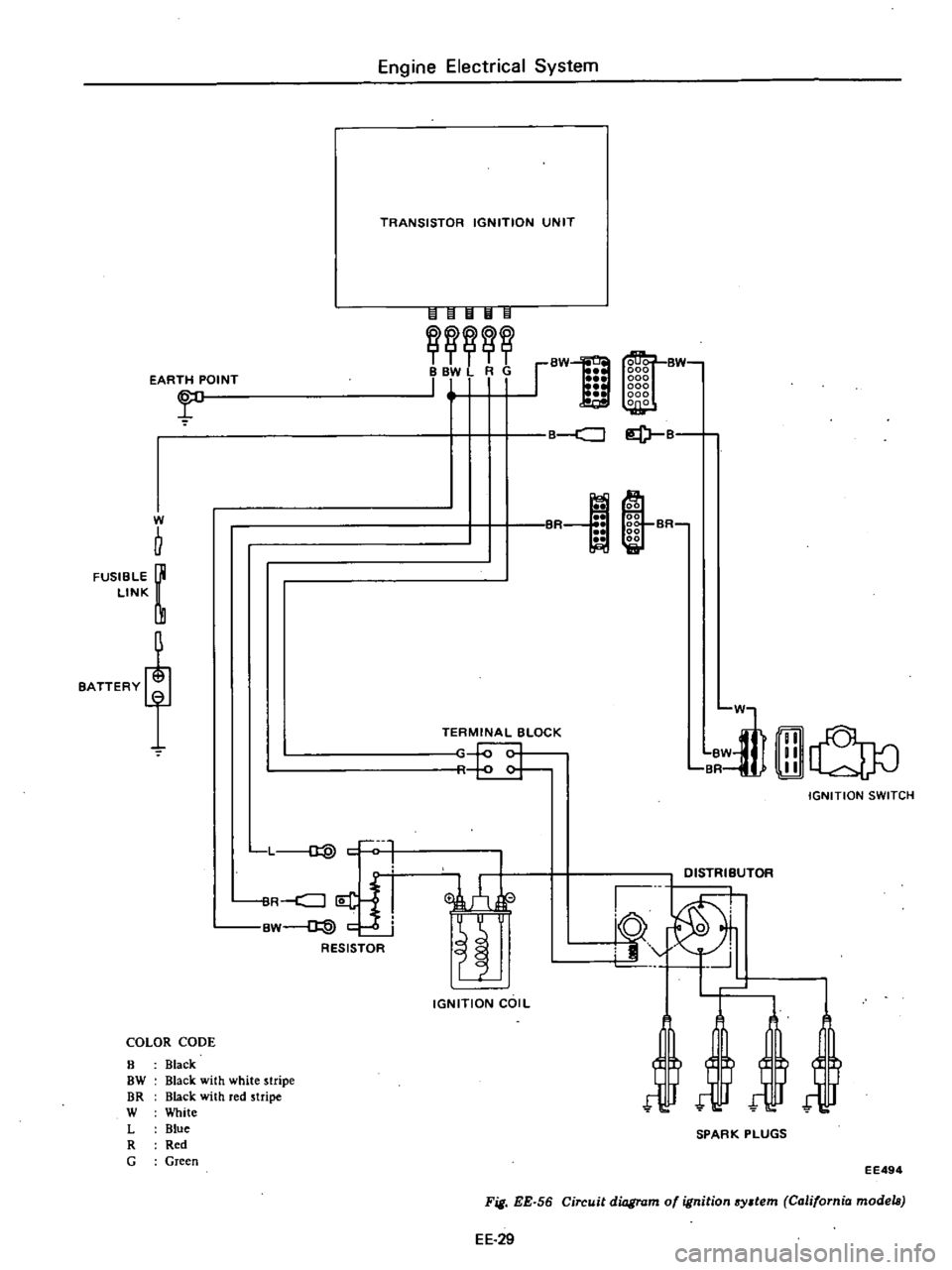
EARTH
POINT
r
W
b
FUSIBLE
LINK
BATTERY
L
d
l
ilR
j
i
BW
@
c
RESISTOR
COLOR
CODE
8
Black
OW
Black
with
white
stripe
DR
Black
with
red
stripe
W
White
L
Blue
R
Red
G
Green
Engine
Electrical
System
TRANSISTOR
IGNITION
UNIT
IHIIl
II
II
BW
BBV
RG
111
I
I
TERMINAL
BLOCK
r
c
IGNITION
COIL
BW
B
ml
BR
lliJ
LldJ0
IGNITION
SWITCH
EE
29
Fig
EE
56
Circuit
diagram
of
ignition
system
California
models
EE494
a
B
lof1
@
00
00
00
SR
00
00
Et
liiI
in
D1STRliUTOR
10
0
i9
J
SPARK
PLUGS
Page 204 of 537
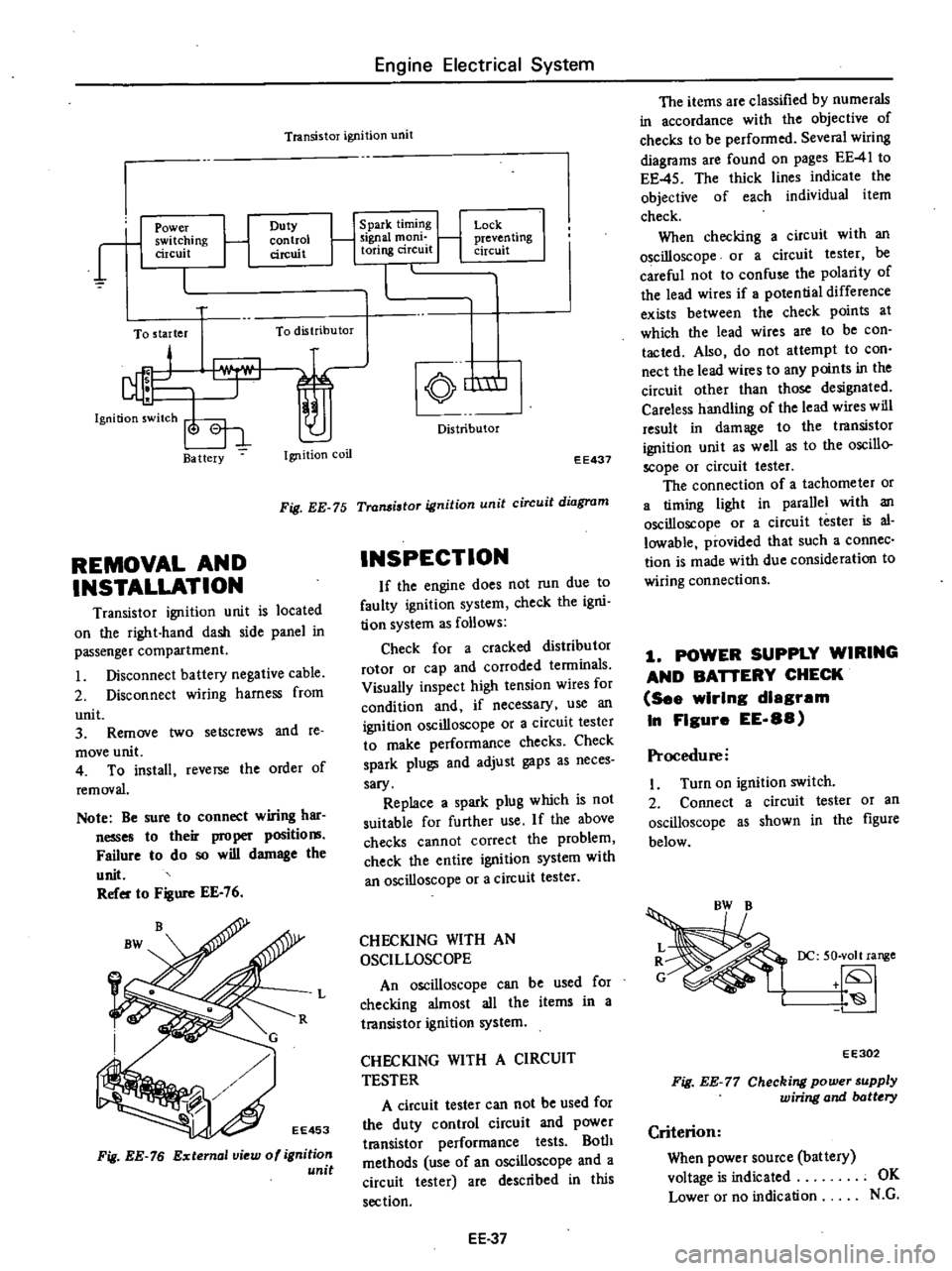
Engine
Electrical
System
Transistor
ignition
unit
r
1
Power
switching
circuit
Duty
control
circuit
To
starter
To
distributor
Ba
ttery
Ignition
coil
1
Spark
timing
1
Signal
mom
toring
circuit
Lock
j
preven
ling
circuit
nm
Distributor
EE437
Fig
EE
75
Transistor
ignition
unit
circuit
diagram
REMOVAL
AND
INSTALLATION
Transistor
ignition
unit
is
located
on
the
right
hand
dash
side
panel
in
passenger
compartment
Disconnect
battery
negative
cable
2
Disconnect
wiring
harness
from
unit
3
Remove
two
setscrews
and
te
move
unit
4
To
install
reverse
the
order
of
removal
Note
Be
sure
to
connect
wiring
har
nesses
to
their
proper
positio
Failure
to
do
so
will
damage
the
unit
Refer
to
Figure
EE
76
Fig
EE
76
External
view
of
ignition
unit
INSPECTION
If
the
engine
does
not
run
due
to
faulty
ignition
system
check
the
igni
tion
system
as
follows
Check
for
a
cracked
distributor
rotor
or
cap
and
corroded
tenninals
Visually
inspect
high
tension
wires
for
condition
and
if
necessary
use
an
ignition
oscilloscope
or
a
circuit
tester
to
make
performance
checks
Check
spark
plugs
and
adjust
gaps
as
neces
sary
Replace
a
spark
plug
which
is
not
suitable
for
further
use
If
the
above
checks
cannot
correct
the
problem
check
the
entire
ignition
system
with
an
oscilloscope
or
a
circuit
tester
L
CHECKING
WITH
AN
OSCILLOSCOPE
An
oscilloscope
can
be
used
for
checking
almost
all
the
items
in
a
transistor
ignition
system
CHECKING
WITH
A
CIRCUIT
TESTER
A
circuit
tester
can
not
be
used
for
the
duty
control
circuit
and
power
t18nsistor
performance
tests
Both
methods
use
of
an
oscilloscope
and
a
circuit
tester
are
described
in
this
section
EE
37
The
items
are
classified
by
numerals
in
accordance
with
the
objective
of
checks
to
be
performed
Several
wiring
diagrams
are
found
on
pages
EE
41
to
EE
45
The
thick
lines
indicate
the
objective
of
each
individual
item
check
When
checking
a
circuit
with
an
oscilloscope
or
a
circuit
tester
be
careful
not
to
confuse
the
polarity
of
the
lead
wires
if
potential
difference
exists
between
the
check
points
at
which
the
lead
wires
are
to
be
con
tacted
Also
do
not
attempt
to
con
nect
the
lead
wires
to
any
points
in
the
circuit
other
than
those
designated
Careless
handling
of
the
lead
wires
will
result
in
damage
to
the
transistor
ignition
unit
as
well
as
to
the
oscillo
scope
or
circuit
tester
The
connection
of
a
tachometer
or
a
timing
light
in
parallel
with
an
oscilloscope
or
a
circuit
tester
is
al
lowable
provided
that
such
a
connec
tion
is
made
with
due
consideration
to
wiring
connections
1
POWER
SUPPLY
WIRING
AND
BAnERY
CHECK
See
wIrIng
diagram
In
FIgure
EE
88
Procedure
I
Turn
on
ignition
switch
2
Connect
a
circuit
tester
or
an
oscilloscope
as
shown
in
the
figure
below
DC
50
volt
range
EE302
Fig
EE
77
Checking
power
supply
wiring
and
batt
ry
Criterion
When
power
source
battery
voltage
is
indicated
OK
Lower
or
no
indication
N
G