DODGE RAM 1500 1998 2.G Workshop Manual
Manufacturer: DODGE, Model Year: 1998, Model line: RAM 1500, Model: DODGE RAM 1500 1998 2.GPages: 2627
Page 1981 of 2627
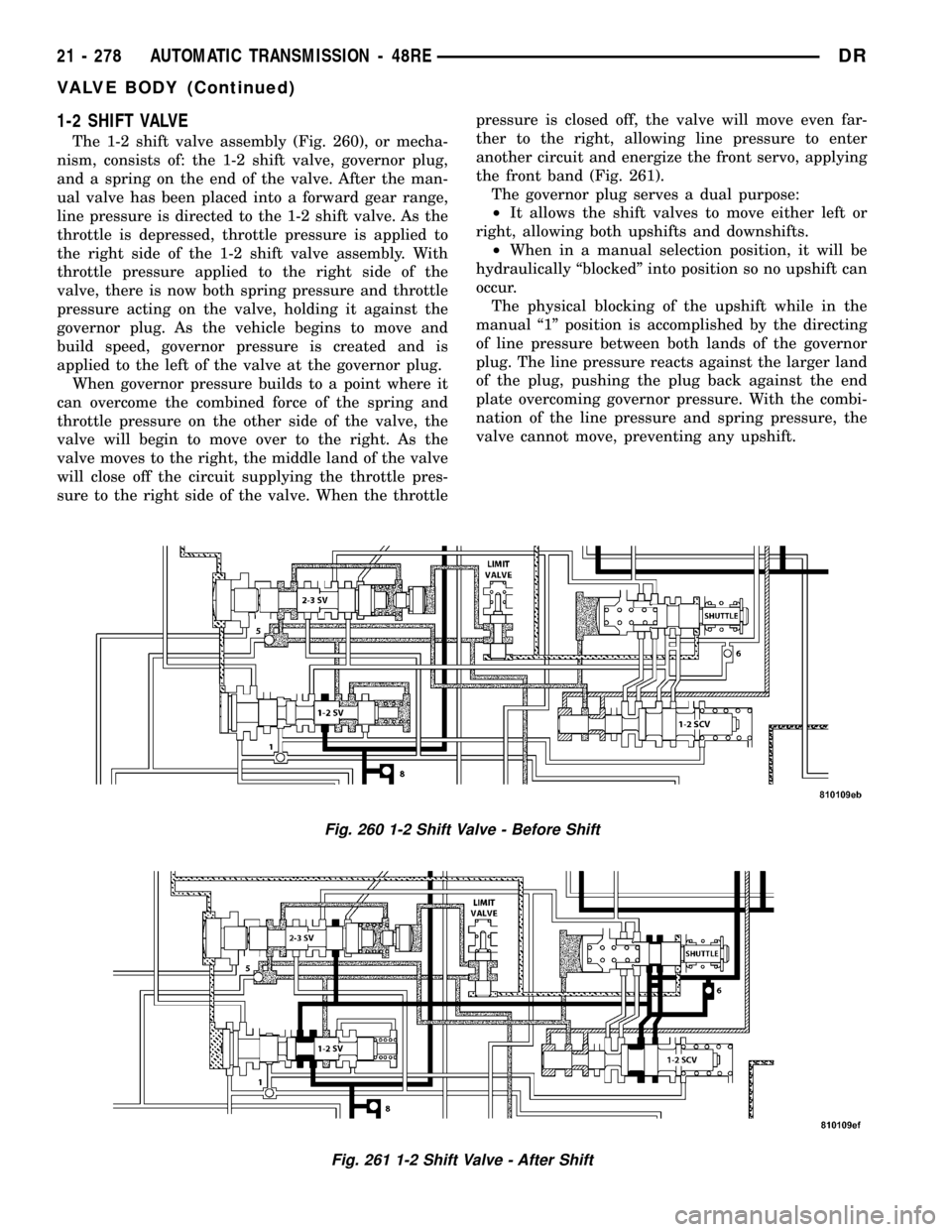
1-2 SHIFT VALVE
The 1-2 shift valve assembly (Fig. 260), or mecha-
nism, consists of: the 1-2 shift valve, governor plug,
and a spring on the end of the valve. After the man-
ual valve has been placed into a forward gear range,
line pressure is directed to the 1-2 shift valve. As the
throttle is depressed, throttle pressure is applied to
the right side of the 1-2 shift valve assembly. With
throttle pressure applied to the right side of the
valve, there is now both spring pressure and throttle
pressure acting on the valve, holding it against the
governor plug. As the vehicle begins to move and
build speed, governor pressure is created and is
applied to the left of the valve at the governor plug.
When governor pressure builds to a point where it
can overcome the combined force of the spring and
throttle pressure on the other side of the valve, the
valve will begin to move over to the right. As the
valve moves to the right, the middle land of the valve
will close off the circuit supplying the throttle pres-
sure to the right side of the valve. When the throttlepressure is closed off, the valve will move even far-
ther to the right, allowing line pressure to enter
another circuit and energize the front servo, applying
the front band (Fig. 261).
The governor plug serves a dual purpose:
²It allows the shift valves to move either left or
right, allowing both upshifts and downshifts.
²When in a manual selection position, it will be
hydraulically ªblockedº into position so no upshift can
occur.
The physical blocking of the upshift while in the
manual ª1º position is accomplished by the directing
of line pressure between both lands of the governor
plug. The line pressure reacts against the larger land
of the plug, pushing the plug back against the end
plate overcoming governor pressure. With the combi-
nation of the line pressure and spring pressure, the
valve cannot move, preventing any upshift.
Fig. 260 1-2 Shift Valve - Before Shift
Fig. 261 1-2 Shift Valve - After Shift
21 - 278 AUTOMATIC TRANSMISSION - 48REDR
VALVE BODY (Continued)
Page 1982 of 2627
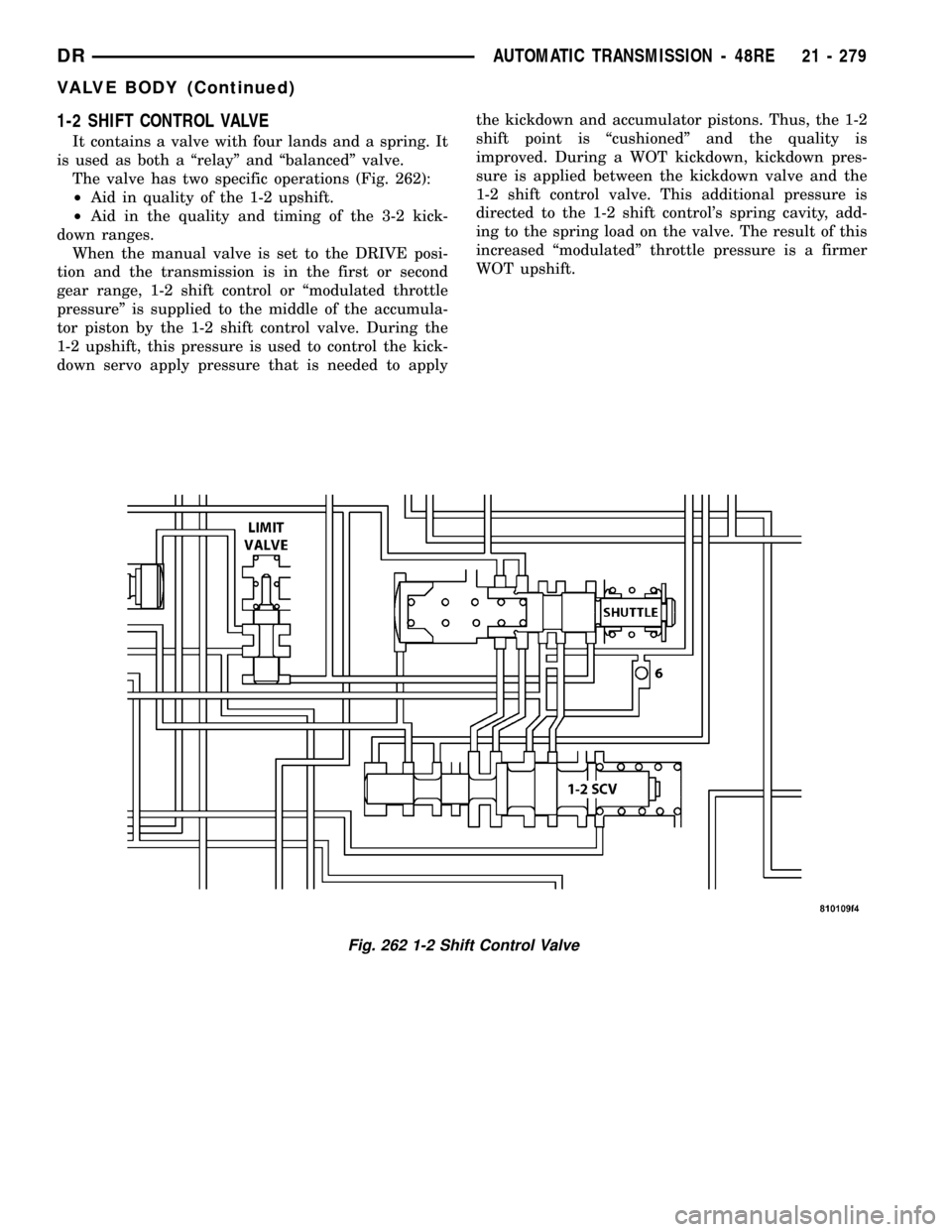
1-2 SHIFT CONTROL VALVE
It contains a valve with four lands and a spring. It
is used as both a ªrelayº and ªbalancedº valve.
The valve has two specific operations (Fig. 262):
²Aid in quality of the 1-2 upshift.
²Aid in the quality and timing of the 3-2 kick-
down ranges.
When the manual valve is set to the DRIVE posi-
tion and the transmission is in the first or second
gear range, 1-2 shift control or ªmodulated throttle
pressureº is supplied to the middle of the accumula-
tor piston by the 1-2 shift control valve. During the
1-2 upshift, this pressure is used to control the kick-
down servo apply pressure that is needed to applythe kickdown and accumulator pistons. Thus, the 1-2
shift point is ªcushionedº and the quality is
improved. During a WOT kickdown, kickdown pres-
sure is applied between the kickdown valve and the
1-2 shift control valve. This additional pressure is
directed to the 1-2 shift control's spring cavity, add-
ing to the spring load on the valve. The result of this
increased ªmodulatedº throttle pressure is a firmer
WOT upshift.
Fig. 262 1-2 Shift Control Valve
DRAUTOMATIC TRANSMISSION - 48RE 21 - 279
VALVE BODY (Continued)
Page 1983 of 2627
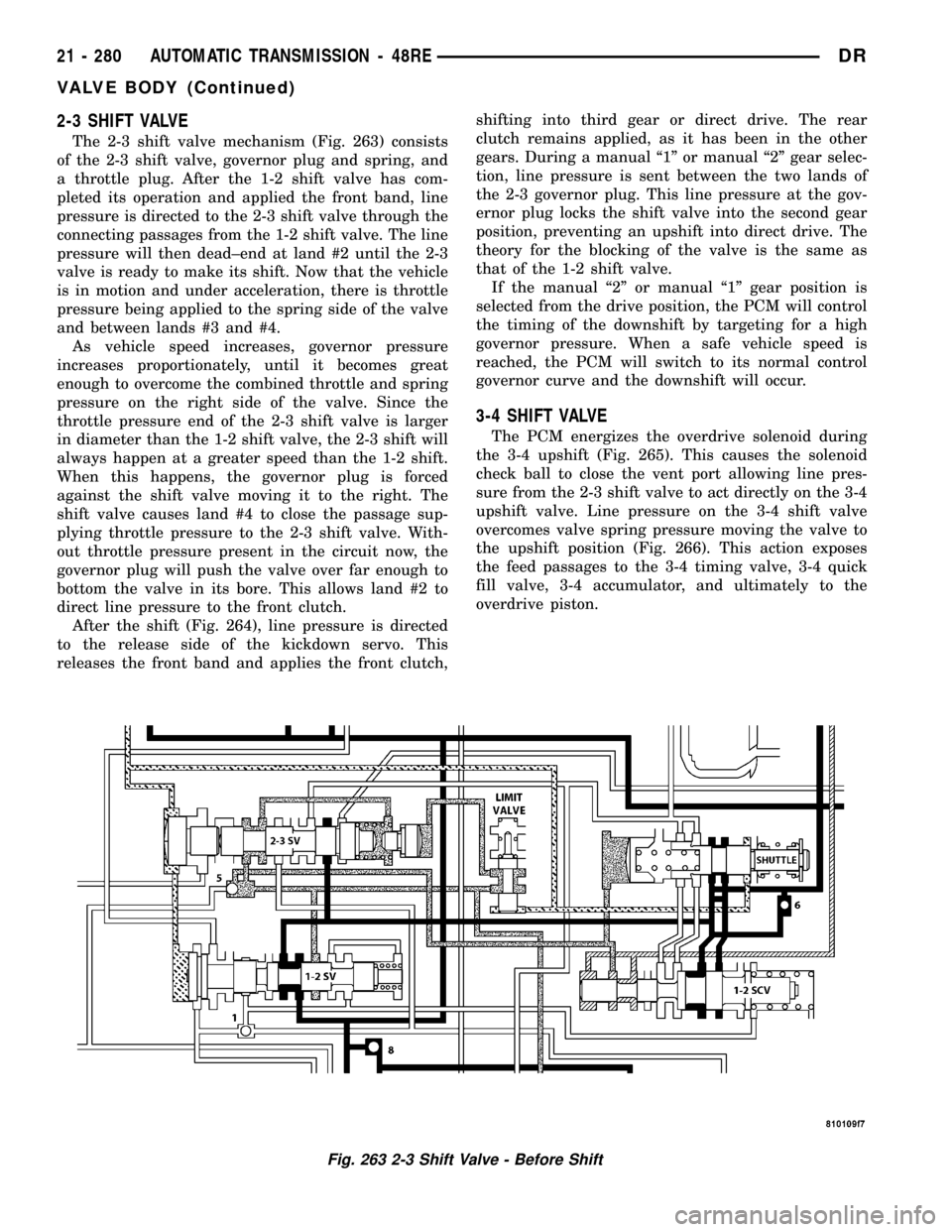
2-3 SHIFT VALVE
The 2-3 shift valve mechanism (Fig. 263) consists
of the 2-3 shift valve, governor plug and spring, and
a throttle plug. After the 1-2 shift valve has com-
pleted its operation and applied the front band, line
pressure is directed to the 2-3 shift valve through the
connecting passages from the 1-2 shift valve. The line
pressure will then dead±end at land #2 until the 2-3
valve is ready to make its shift. Now that the vehicle
is in motion and under acceleration, there is throttle
pressure being applied to the spring side of the valve
and between lands #3 and #4.
As vehicle speed increases, governor pressure
increases proportionately, until it becomes great
enough to overcome the combined throttle and spring
pressure on the right side of the valve. Since the
throttle pressure end of the 2-3 shift valve is larger
in diameter than the 1-2 shift valve, the 2-3 shift will
always happen at a greater speed than the 1-2 shift.
When this happens, the governor plug is forced
against the shift valve moving it to the right. The
shift valve causes land #4 to close the passage sup-
plying throttle pressure to the 2-3 shift valve. With-
out throttle pressure present in the circuit now, the
governor plug will push the valve over far enough to
bottom the valve in its bore. This allows land #2 to
direct line pressure to the front clutch.
After the shift (Fig. 264), line pressure is directed
to the release side of the kickdown servo. This
releases the front band and applies the front clutch,shifting into third gear or direct drive. The rear
clutch remains applied, as it has been in the other
gears. During a manual ª1º or manual ª2º gear selec-
tion, line pressure is sent between the two lands of
the 2-3 governor plug. This line pressure at the gov-
ernor plug locks the shift valve into the second gear
position, preventing an upshift into direct drive. The
theory for the blocking of the valve is the same as
that of the 1-2 shift valve.
If the manual ª2º or manual ª1º gear position is
selected from the drive position, the PCM will control
the timing of the downshift by targeting for a high
governor pressure. When a safe vehicle speed is
reached, the PCM will switch to its normal control
governor curve and the downshift will occur.
3-4 SHIFT VALVE
The PCM energizes the overdrive solenoid during
the 3-4 upshift (Fig. 265). This causes the solenoid
check ball to close the vent port allowing line pres-
sure from the 2-3 shift valve to act directly on the 3-4
upshift valve. Line pressure on the 3-4 shift valve
overcomes valve spring pressure moving the valve to
the upshift position (Fig. 266). This action exposes
the feed passages to the 3-4 timing valve, 3-4 quick
fill valve, 3-4 accumulator, and ultimately to the
overdrive piston.
Fig. 263 2-3 Shift Valve - Before Shift
21 - 280 AUTOMATIC TRANSMISSION - 48REDR
VALVE BODY (Continued)
Page 1984 of 2627
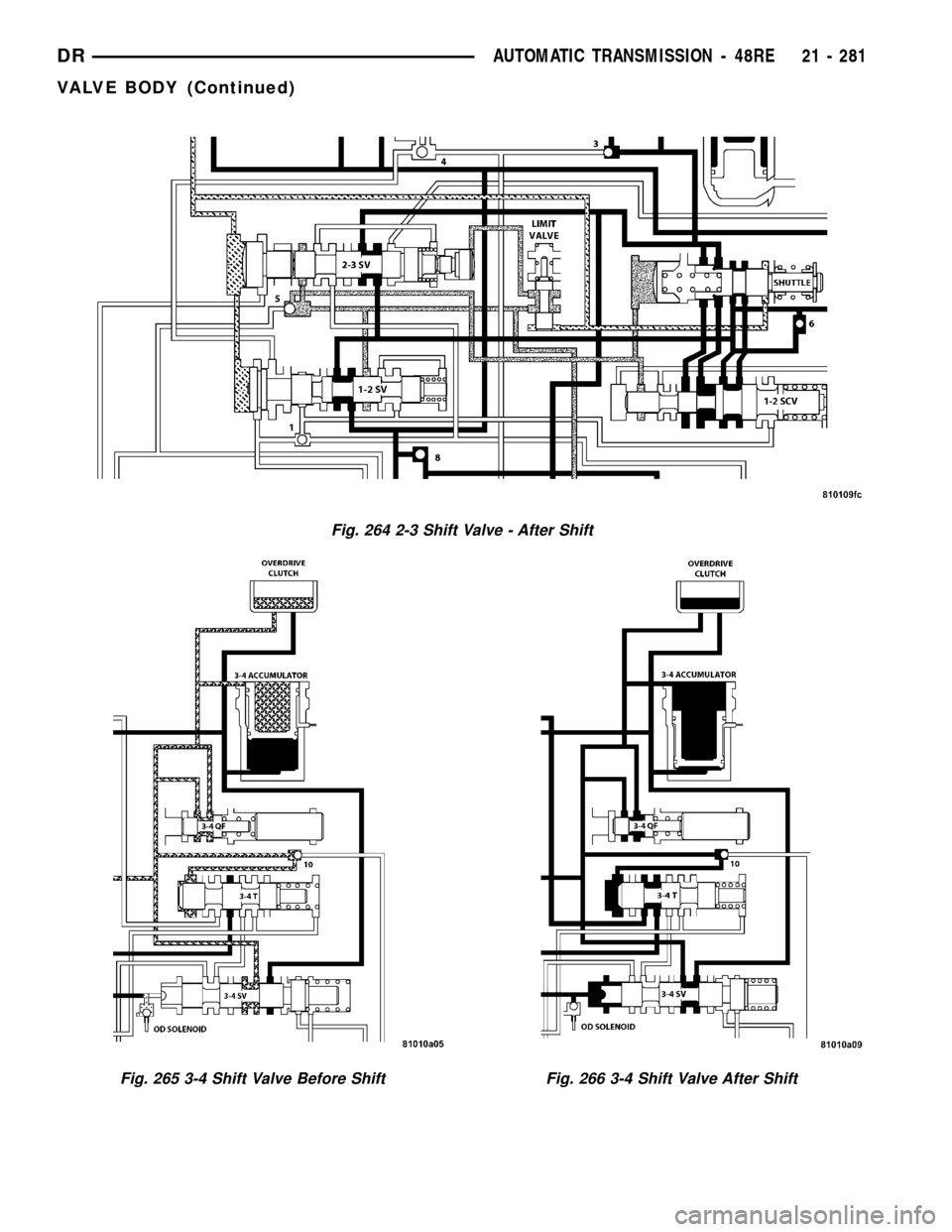
Fig. 264 2-3 Shift Valve - After Shift
Fig. 265 3-4 Shift Valve Before ShiftFig. 266 3-4 Shift Valve After Shift
DRAUTOMATIC TRANSMISSION - 48RE 21 - 281
VALVE BODY (Continued)
Page 1985 of 2627
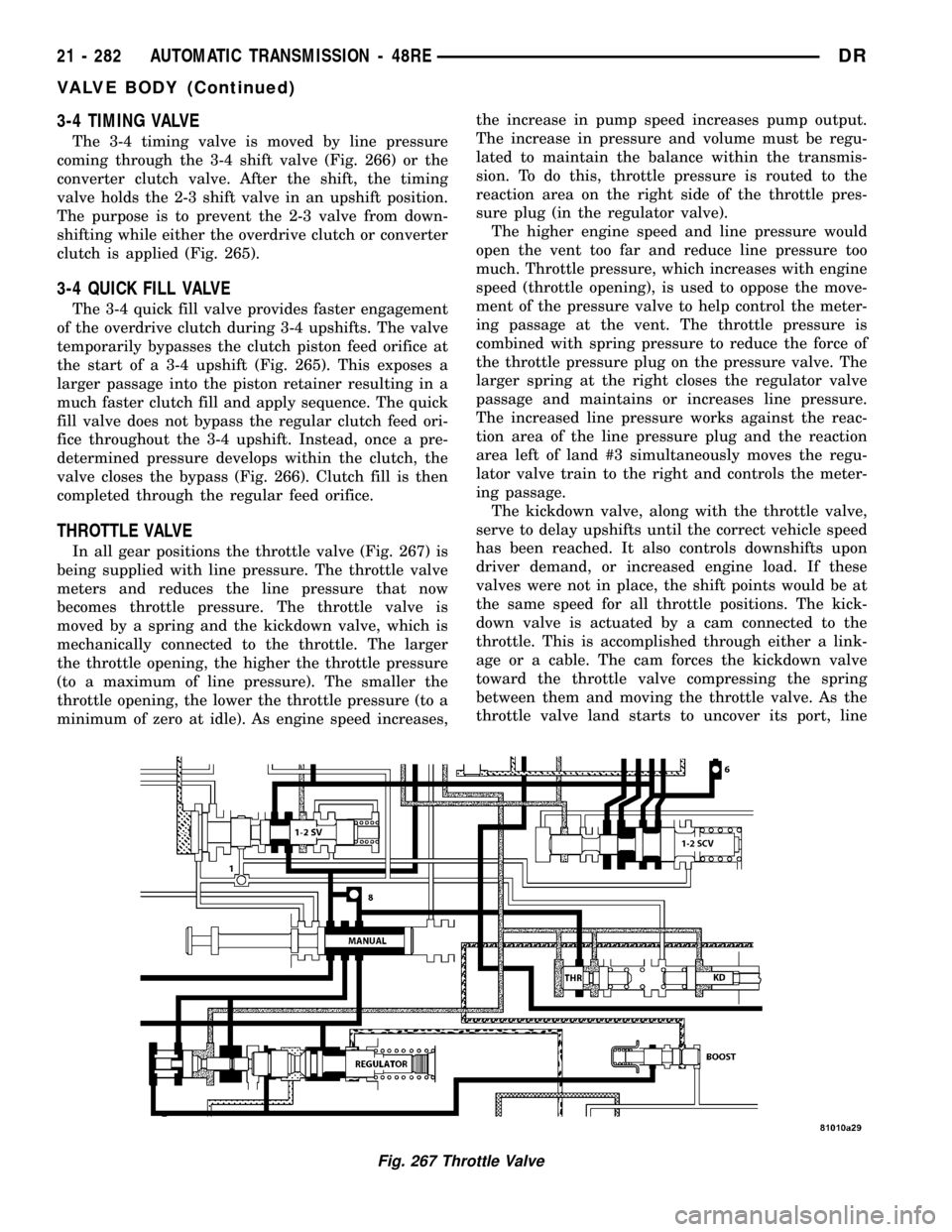
3-4 TIMING VALVE
The 3-4 timing valve is moved by line pressure
coming through the 3-4 shift valve (Fig. 266) or the
converter clutch valve. After the shift, the timing
valve holds the 2-3 shift valve in an upshift position.
The purpose is to prevent the 2-3 valve from down-
shifting while either the overdrive clutch or converter
clutch is applied (Fig. 265).
3-4 QUICK FILL VALVE
The 3-4 quick fill valve provides faster engagement
of the overdrive clutch during 3-4 upshifts. The valve
temporarily bypasses the clutch piston feed orifice at
the start of a 3-4 upshift (Fig. 265). This exposes a
larger passage into the piston retainer resulting in a
much faster clutch fill and apply sequence. The quick
fill valve does not bypass the regular clutch feed ori-
fice throughout the 3-4 upshift. Instead, once a pre-
determined pressure develops within the clutch, the
valve closes the bypass (Fig. 266). Clutch fill is then
completed through the regular feed orifice.
THROTTLE VALVE
In all gear positions the throttle valve (Fig. 267) is
being supplied with line pressure. The throttle valve
meters and reduces the line pressure that now
becomes throttle pressure. The throttle valve is
moved by a spring and the kickdown valve, which is
mechanically connected to the throttle. The larger
the throttle opening, the higher the throttle pressure
(to a maximum of line pressure). The smaller the
throttle opening, the lower the throttle pressure (to a
minimum of zero at idle). As engine speed increases,the increase in pump speed increases pump output.
The increase in pressure and volume must be regu-
lated to maintain the balance within the transmis-
sion. To do this, throttle pressure is routed to the
reaction area on the right side of the throttle pres-
sure plug (in the regulator valve).
The higher engine speed and line pressure would
open the vent too far and reduce line pressure too
much. Throttle pressure, which increases with engine
speed (throttle opening), is used to oppose the move-
ment of the pressure valve to help control the meter-
ing passage at the vent. The throttle pressure is
combined with spring pressure to reduce the force of
the throttle pressure plug on the pressure valve. The
larger spring at the right closes the regulator valve
passage and maintains or increases line pressure.
The increased line pressure works against the reac-
tion area of the line pressure plug and the reaction
area left of land #3 simultaneously moves the regu-
lator valve train to the right and controls the meter-
ing passage.
The kickdown valve, along with the throttle valve,
serve to delay upshifts until the correct vehicle speed
has been reached. It also controls downshifts upon
driver demand, or increased engine load. If these
valves were not in place, the shift points would be at
the same speed for all throttle positions. The kick-
down valve is actuated by a cam connected to the
throttle. This is accomplished through either a link-
age or a cable. The cam forces the kickdown valve
toward the throttle valve compressing the spring
between them and moving the throttle valve. As the
throttle valve land starts to uncover its port, line
Fig. 267 Throttle Valve
21 - 282 AUTOMATIC TRANSMISSION - 48REDR
VALVE BODY (Continued)
Page 1986 of 2627
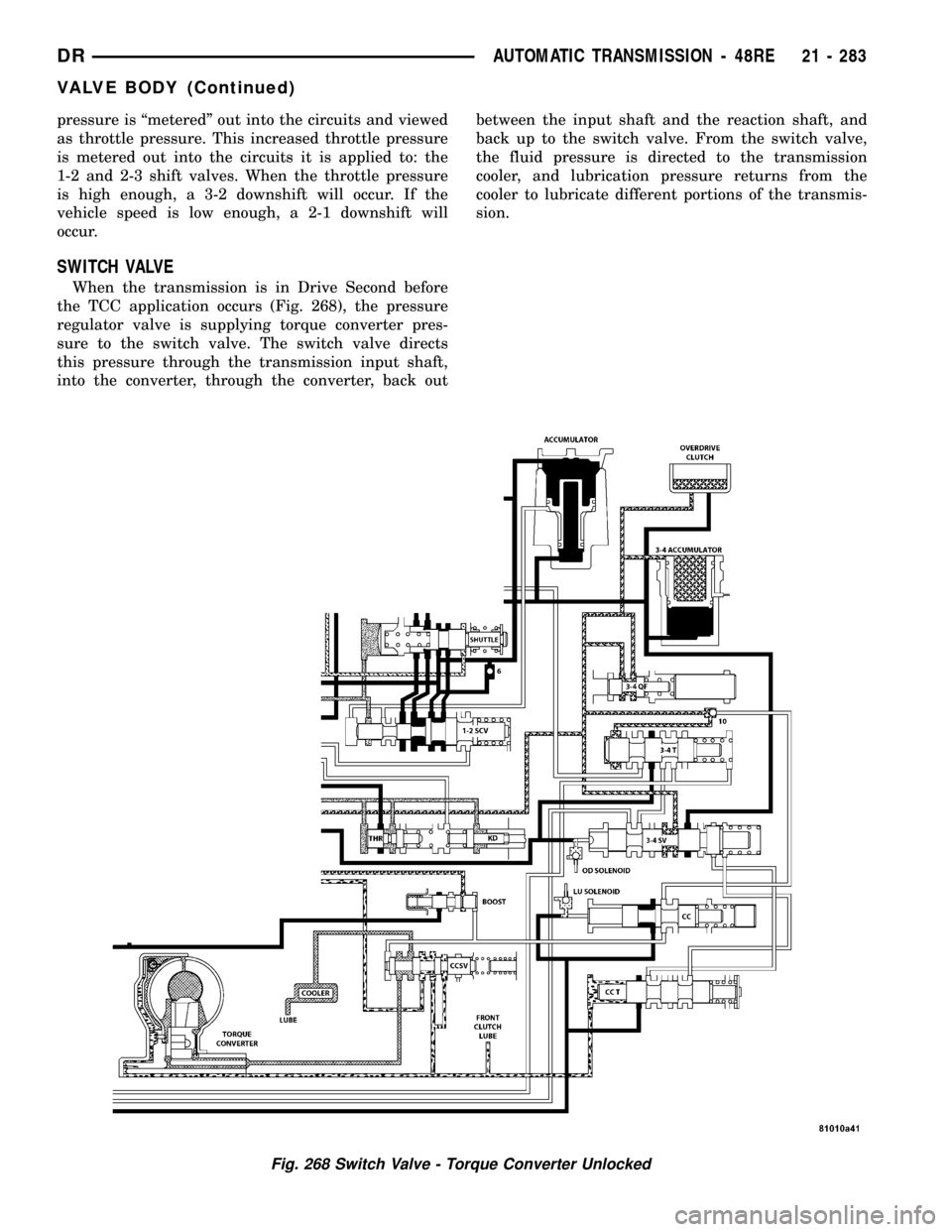
pressure is ªmeteredº out into the circuits and viewed
as throttle pressure. This increased throttle pressure
is metered out into the circuits it is applied to: the
1-2 and 2-3 shift valves. When the throttle pressure
is high enough, a 3-2 downshift will occur. If the
vehicle speed is low enough, a 2-1 downshift will
occur.
SWITCH VALVE
When the transmission is in Drive Second before
the TCC application occurs (Fig. 268), the pressure
regulator valve is supplying torque converter pres-
sure to the switch valve. The switch valve directs
this pressure through the transmission input shaft,
into the converter, through the converter, back outbetween the input shaft and the reaction shaft, and
back up to the switch valve. From the switch valve,
the fluid pressure is directed to the transmission
cooler, and lubrication pressure returns from the
cooler to lubricate different portions of the transmis-
sion.
Fig. 268 Switch Valve - Torque Converter Unlocked
DRAUTOMATIC TRANSMISSION - 48RE 21 - 283
VALVE BODY (Continued)
Page 1987 of 2627
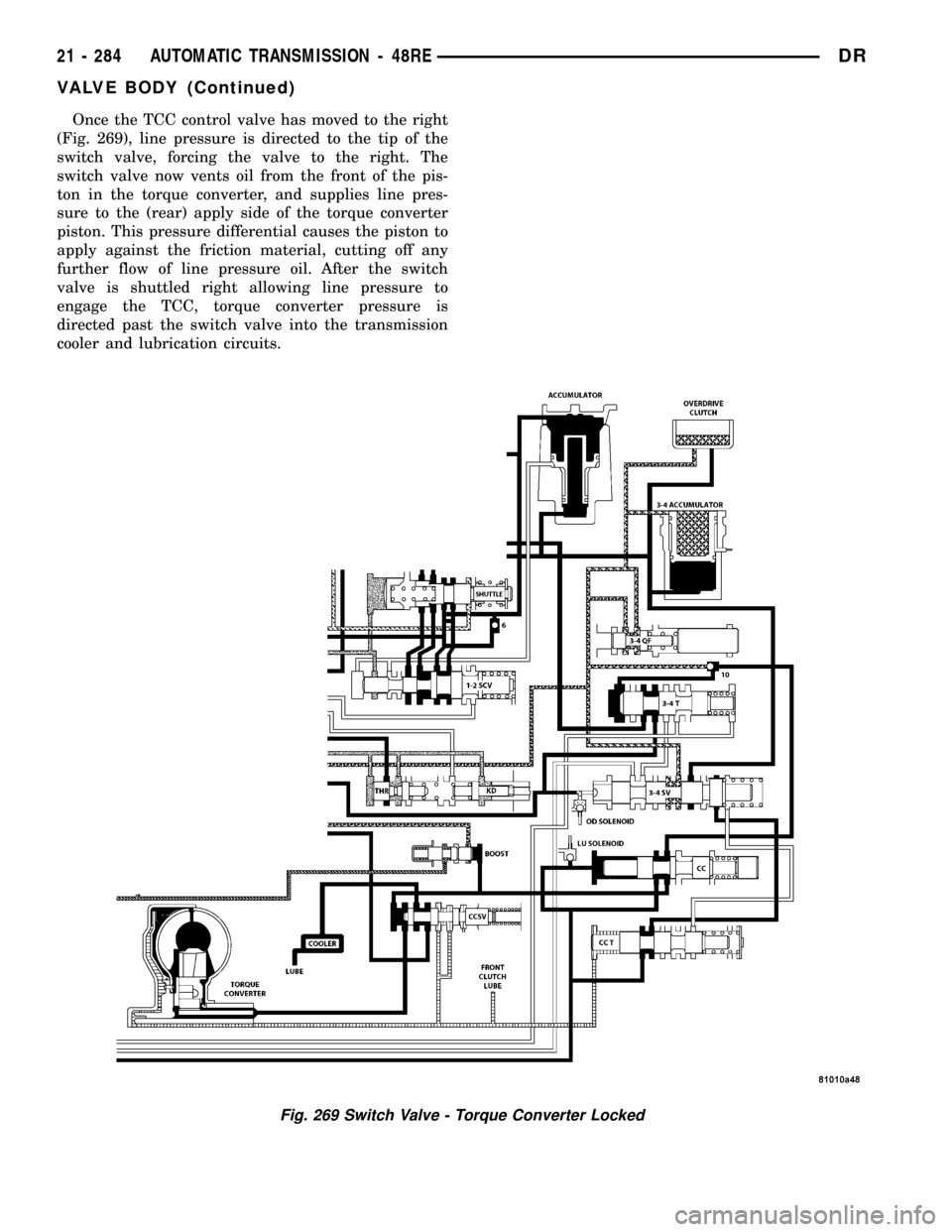
Once the TCC control valve has moved to the right
(Fig. 269), line pressure is directed to the tip of the
switch valve, forcing the valve to the right. The
switch valve now vents oil from the front of the pis-
ton in the torque converter, and supplies line pres-
sure to the (rear) apply side of the torque converter
piston. This pressure differential causes the piston to
apply against the friction material, cutting off any
further flow of line pressure oil. After the switch
valve is shuttled right allowing line pressure to
engage the TCC, torque converter pressure is
directed past the switch valve into the transmission
cooler and lubrication circuits.
Fig. 269 Switch Valve - Torque Converter Locked
21 - 284 AUTOMATIC TRANSMISSION - 48REDR
VALVE BODY (Continued)
Page 1988 of 2627
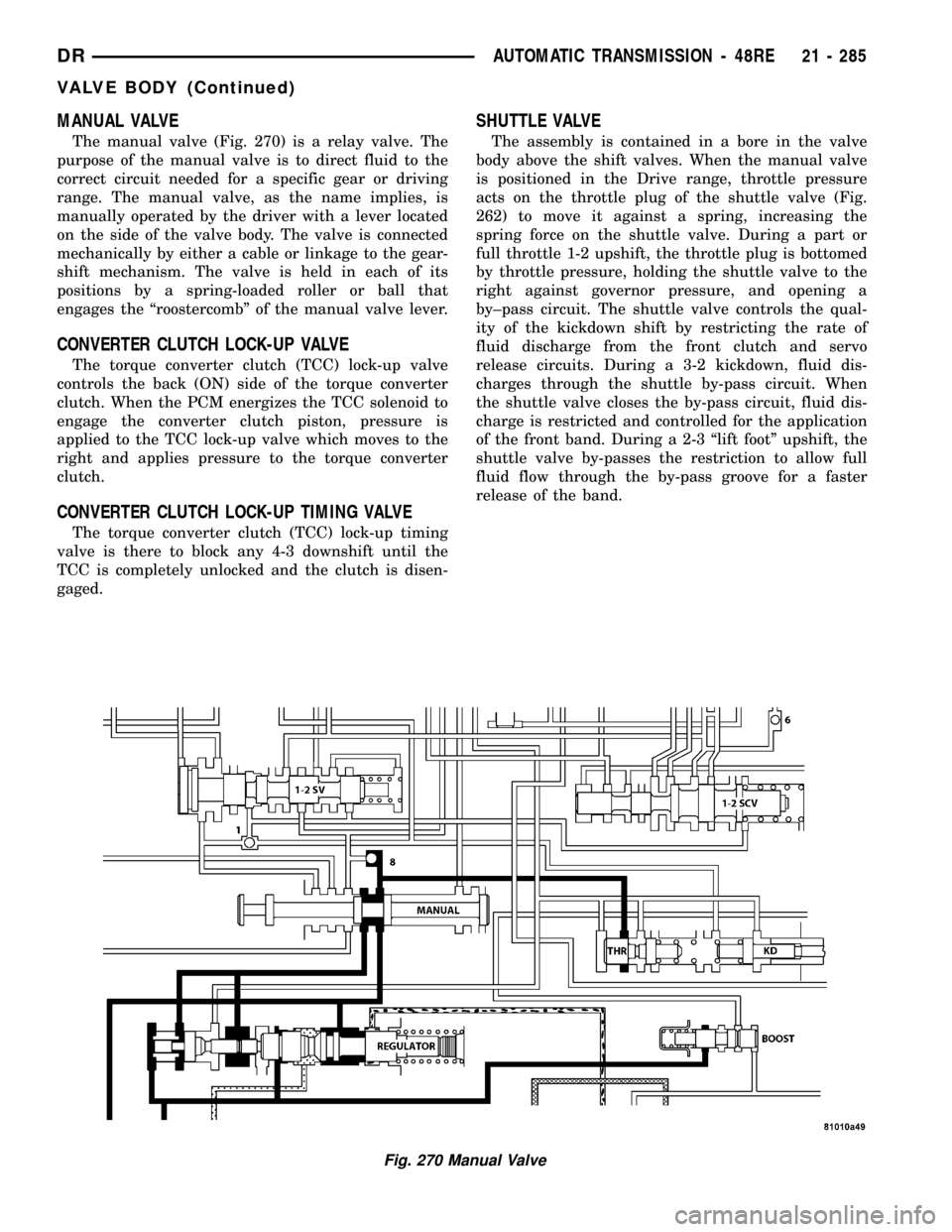
MANUAL VALVE
The manual valve (Fig. 270) is a relay valve. The
purpose of the manual valve is to direct fluid to the
correct circuit needed for a specific gear or driving
range. The manual valve, as the name implies, is
manually operated by the driver with a lever located
on the side of the valve body. The valve is connected
mechanically by either a cable or linkage to the gear-
shift mechanism. The valve is held in each of its
positions by a spring-loaded roller or ball that
engages the ªroostercombº of the manual valve lever.
CONVERTER CLUTCH LOCK-UP VALVE
The torque converter clutch (TCC) lock-up valve
controls the back (ON) side of the torque converter
clutch. When the PCM energizes the TCC solenoid to
engage the converter clutch piston, pressure is
applied to the TCC lock-up valve which moves to the
right and applies pressure to the torque converter
clutch.
CONVERTER CLUTCH LOCK-UP TIMING VALVE
The torque converter clutch (TCC) lock-up timing
valve is there to block any 4-3 downshift until the
TCC is completely unlocked and the clutch is disen-
gaged.
SHUTTLE VALVE
The assembly is contained in a bore in the valve
body above the shift valves. When the manual valve
is positioned in the Drive range, throttle pressure
acts on the throttle plug of the shuttle valve (Fig.
262) to move it against a spring, increasing the
spring force on the shuttle valve. During a part or
full throttle 1-2 upshift, the throttle plug is bottomed
by throttle pressure, holding the shuttle valve to the
right against governor pressure, and opening a
by±pass circuit. The shuttle valve controls the qual-
ity of the kickdown shift by restricting the rate of
fluid discharge from the front clutch and servo
release circuits. During a 3-2 kickdown, fluid dis-
charges through the shuttle by-pass circuit. When
the shuttle valve closes the by-pass circuit, fluid dis-
charge is restricted and controlled for the application
of the front band. During a 2-3 ªlift footº upshift, the
shuttle valve by-passes the restriction to allow full
fluid flow through the by-pass groove for a faster
release of the band.
Fig. 270 Manual Valve
DRAUTOMATIC TRANSMISSION - 48RE 21 - 285
VALVE BODY (Continued)
Page 1989 of 2627
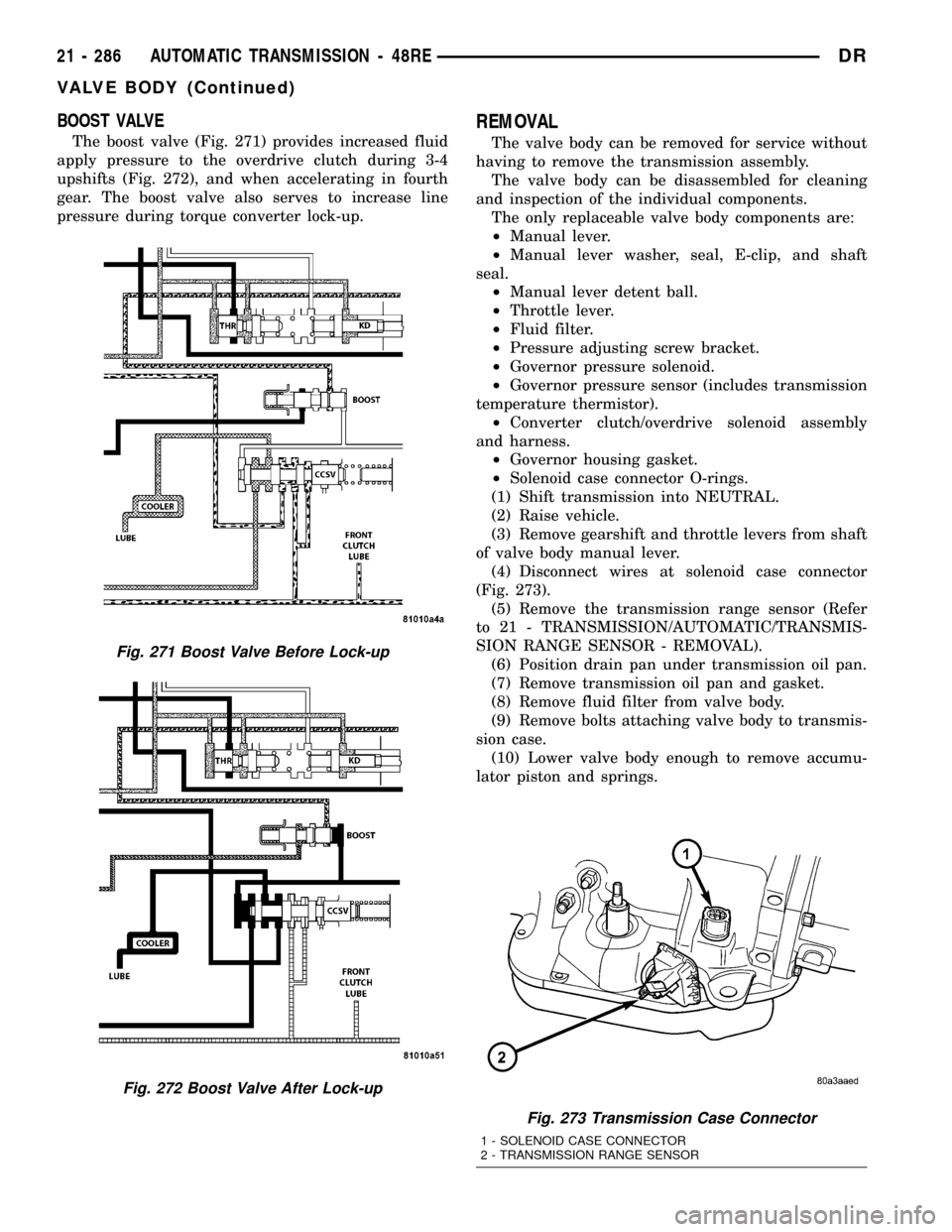
BOOST VALVE
The boost valve (Fig. 271) provides increased fluid
apply pressure to the overdrive clutch during 3-4
upshifts (Fig. 272), and when accelerating in fourth
gear. The boost valve also serves to increase line
pressure during torque converter lock-up.
REMOVAL
The valve body can be removed for service without
having to remove the transmission assembly.
The valve body can be disassembled for cleaning
and inspection of the individual components.
The only replaceable valve body components are:
²Manual lever.
²Manual lever washer, seal, E-clip, and shaft
seal.
²Manual lever detent ball.
²Throttle lever.
²Fluid filter.
²Pressure adjusting screw bracket.
²Governor pressure solenoid.
²Governor pressure sensor (includes transmission
temperature thermistor).
²Converter clutch/overdrive solenoid assembly
and harness.
²Governor housing gasket.
²Solenoid case connector O-rings.
(1) Shift transmission into NEUTRAL.
(2) Raise vehicle.
(3) Remove gearshift and throttle levers from shaft
of valve body manual lever.
(4) Disconnect wires at solenoid case connector
(Fig. 273).
(5) Remove the transmission range sensor (Refer
to 21 - TRANSMISSION/AUTOMATIC/TRANSMIS-
SION RANGE SENSOR - REMOVAL).
(6) Position drain pan under transmission oil pan.
(7) Remove transmission oil pan and gasket.
(8) Remove fluid filter from valve body.
(9) Remove bolts attaching valve body to transmis-
sion case.
(10) Lower valve body enough to remove accumu-
lator piston and springs.
Fig. 273 Transmission Case Connector
1 - SOLENOID CASE CONNECTOR
2 - TRANSMISSION RANGE SENSOR
Fig. 271 Boost Valve Before Lock-up
Fig. 272 Boost Valve After Lock-up
21 - 286 AUTOMATIC TRANSMISSION - 48REDR
VALVE BODY (Continued)
Page 1990 of 2627
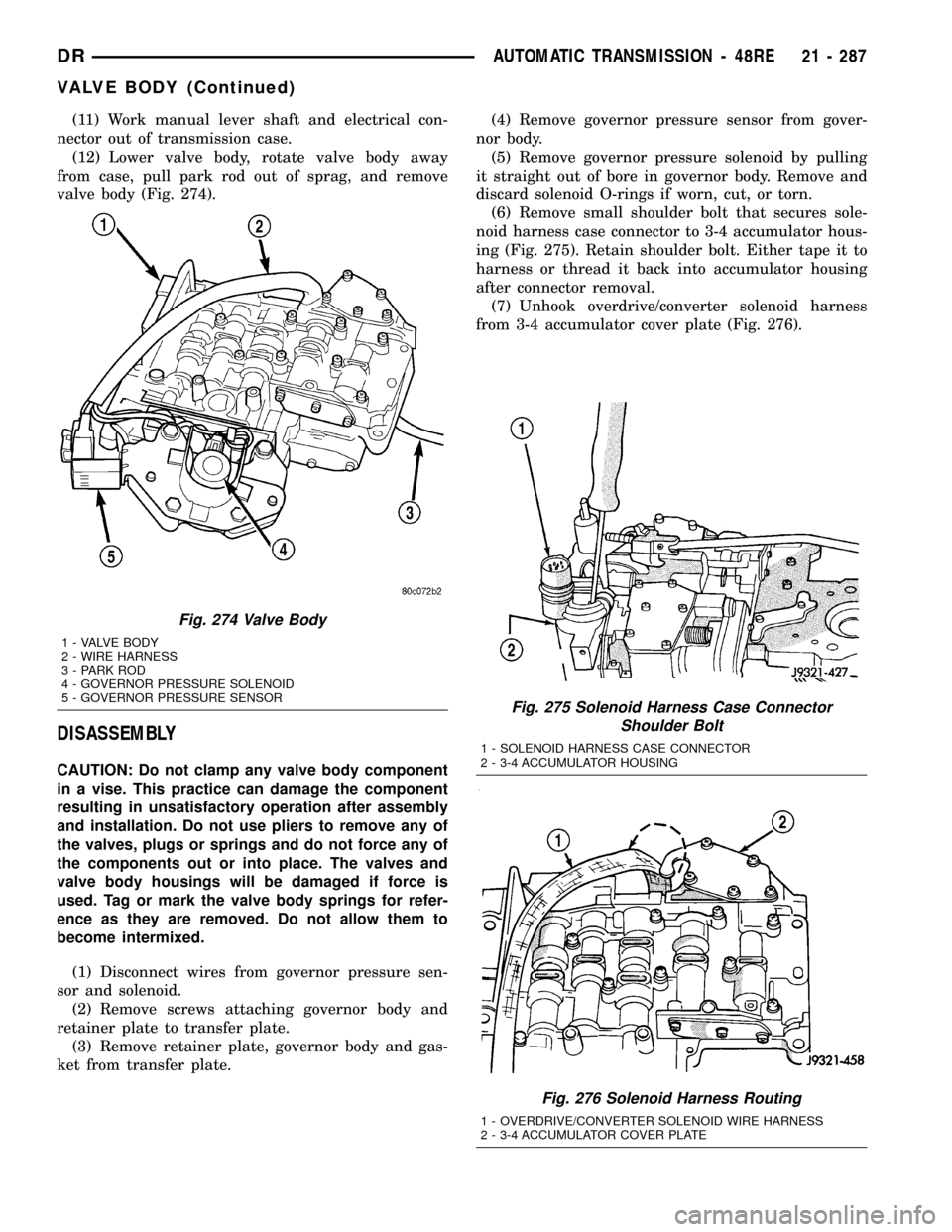
(11) Work manual lever shaft and electrical con-
nector out of transmission case.
(12) Lower valve body, rotate valve body away
from case, pull park rod out of sprag, and remove
valve body (Fig. 274).
DISASSEMBLY
CAUTION: Do not clamp any valve body component
in a vise. This practice can damage the component
resulting in unsatisfactory operation after assembly
and installation. Do not use pliers to remove any of
the valves, plugs or springs and do not force any of
the components out or into place. The valves and
valve body housings will be damaged if force is
used. Tag or mark the valve body springs for refer-
ence as they are removed. Do not allow them to
become intermixed.
(1) Disconnect wires from governor pressure sen-
sor and solenoid.
(2) Remove screws attaching governor body and
retainer plate to transfer plate.
(3) Remove retainer plate, governor body and gas-
ket from transfer plate.(4) Remove governor pressure sensor from gover-
nor body.
(5) Remove governor pressure solenoid by pulling
it straight out of bore in governor body. Remove and
discard solenoid O-rings if worn, cut, or torn.
(6) Remove small shoulder bolt that secures sole-
noid harness case connector to 3-4 accumulator hous-
ing (Fig. 275). Retain shoulder bolt. Either tape it to
harness or thread it back into accumulator housing
after connector removal.
(7) Unhook overdrive/converter solenoid harness
from 3-4 accumulator cover plate (Fig. 276).
Fig. 275 Solenoid Harness Case Connector
Shoulder Bolt
1 - SOLENOID HARNESS CASE CONNECTOR
2 - 3-4 ACCUMULATOR HOUSING
Fig. 276 Solenoid Harness Routing
1 - OVERDRIVE/CONVERTER SOLENOID WIRE HARNESS
2 - 3-4 ACCUMULATOR COVER PLATE
Fig. 274 Valve Body
1 - VALVE BODY
2 - WIRE HARNESS
3 - PARK ROD
4 - GOVERNOR PRESSURE SOLENOID
5 - GOVERNOR PRESSURE SENSOR
DRAUTOMATIC TRANSMISSION - 48RE 21 - 287
VALVE BODY (Continued)