Fuel system FIAT MAREA 2000 1.G Repair Manual
[x] Cancel search | Manufacturer: FIAT, Model Year: 2000, Model line: MAREA, Model: FIAT MAREA 2000 1.GPages: 330
Page 107 of 330
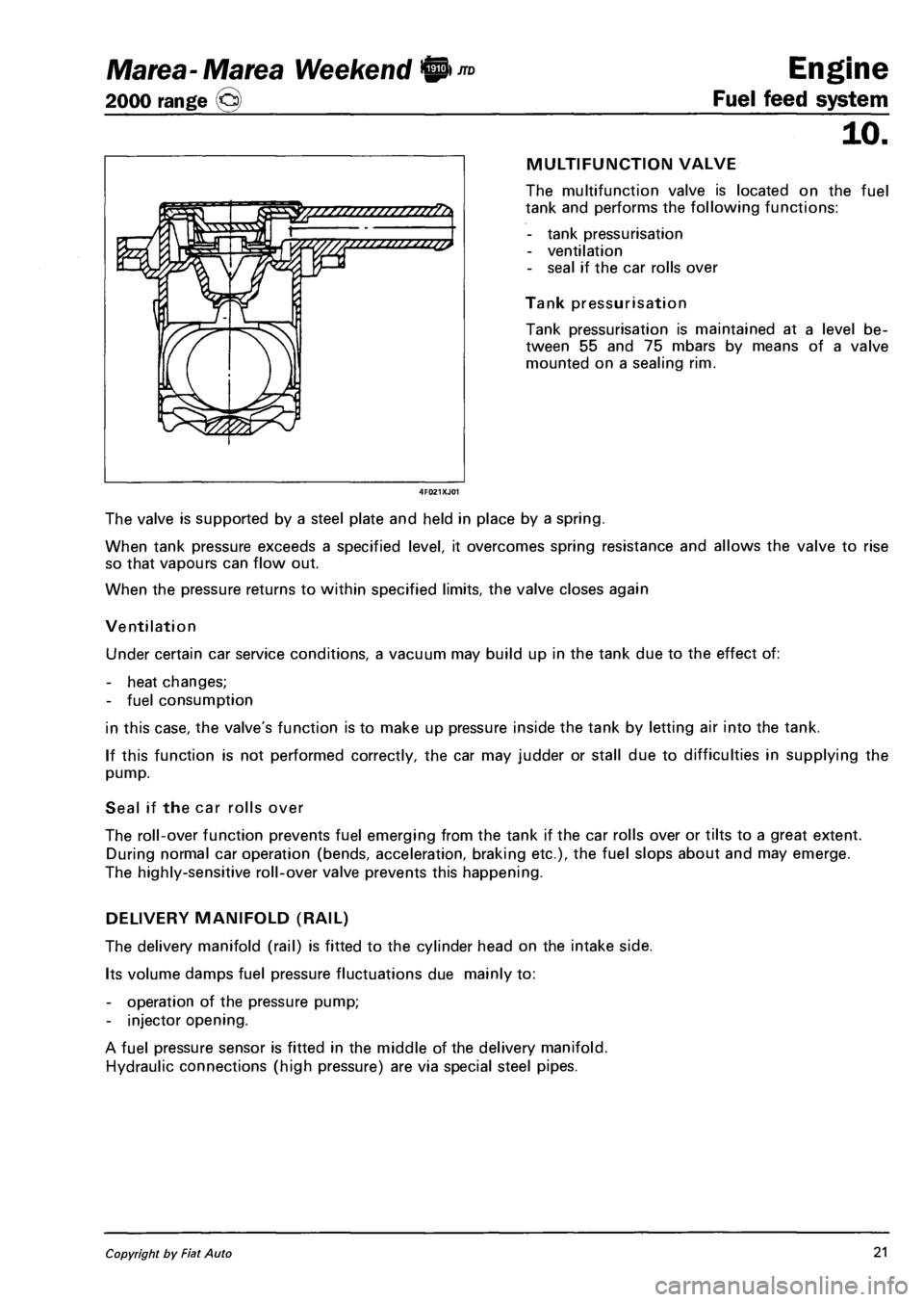
Marea- Marea Weekend <§l ™
2000 range ©
Engine
Fuel feed system
TZZZZZZZZZZZZZZZZZZb
TZZZZZZZZZZZZZZ*
10.
MULTIFUNCTION VALVE
The multifunction valve is located on the fuel
tank and performs the following functions:
- tank pressurisation
- ventilation
- seal if the car rolls over
Tank pressurisation
Tank pressurisation is maintained at a level be
tween 55 and 75 mbars by means of a valve
mounted on a sealing rim.
The valve is supported by a steel plate and held in place by a spring.
When tank pressure exceeds a specified level, it overcomes spring resistance and allows the valve to rise
so that vapours can flow out.
When the pressure returns to within specified limits, the valve closes again
Ventilation
Under certain car service conditions, a vacuum may build up in the tank due to the effect of:
- heat changes;
- fuel consumption
in this case, the valve's function is to make up pressure inside the tank by letting air into the tank.
If this function is not performed correctly, the car may judder or stall due to difficulties in supplying the
pump.
Seal if the car rolls over
The roll-over function prevents fuel emerging from the tank if the car rolls over or tilts to a great extent.
During normal car operation (bends, acceleration, braking etc.), the fuel slops about and may emerge.
The highly-sensitive roll-over valve prevents this happening.
DELIVERY MANIFOLD (RAIL)
The delivery manifold (rail) is fitted to the cylinder head on the intake side.
Its volume damps fuel pressure fluctuations due mainly to:
- operation of the pressure pump;
- injector opening.
A fuel pressure sensor is fitted in the middle of the delivery manifold.
Hydraulic connections (high pressure) are via special steel pipes.
Copyright by Fiat Auto 21
Page 108 of 330
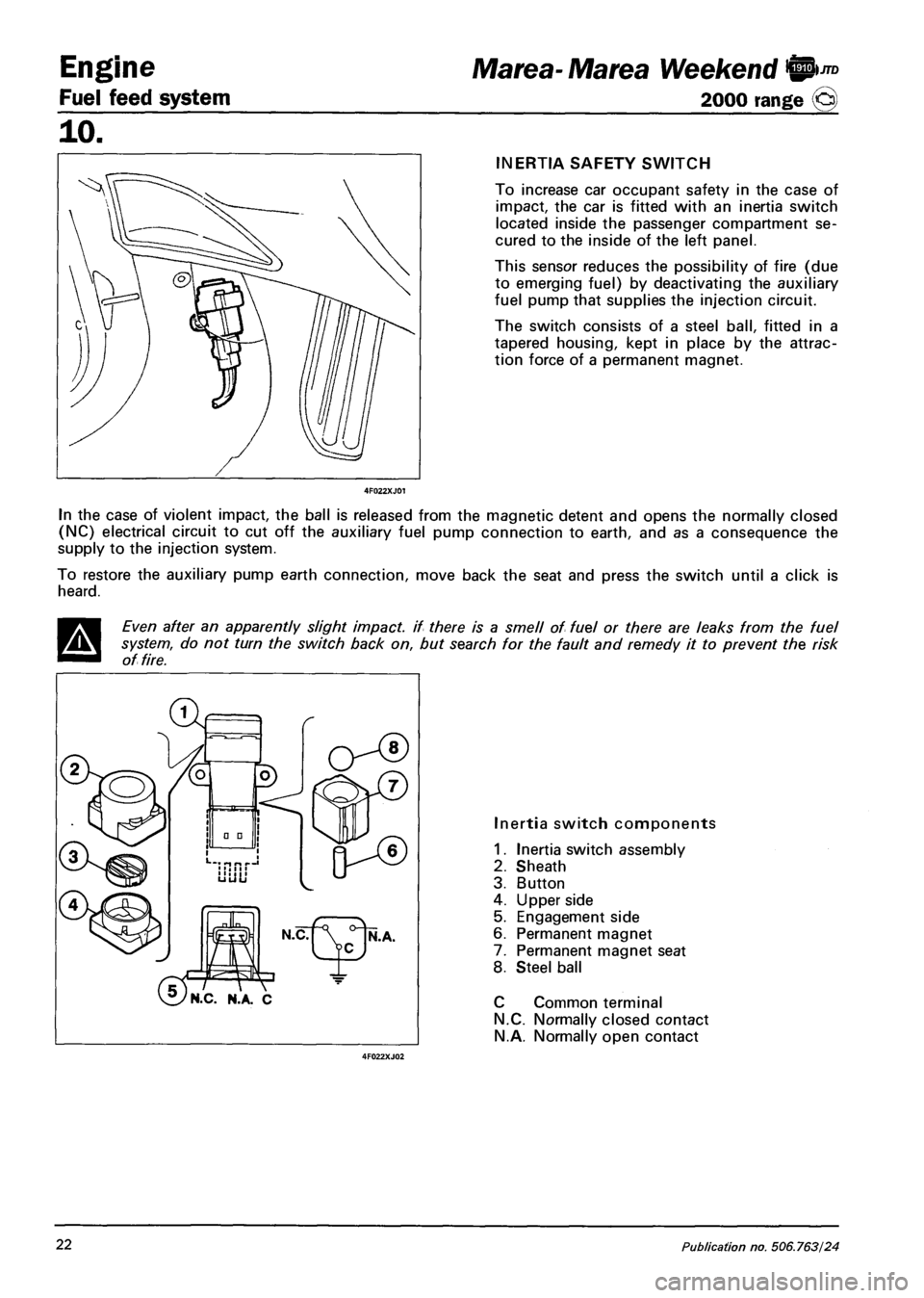
Engine
Fuel feed system
Marea- Marea Weekend W)JTD
2000 range ©
INERTIA SAFETY SWITCH
To increase car occupant safety in the case of
impact, the car is fitted with an inertia switch
located inside the passenger compartment se
cured to the inside of the left panel.
This sensor reduces the possibility of fire (due
to emerging fuel) by deactivating the auxiliary
fuel pump that supplies the injection circuit.
The switch consists of a steel ball, fitted in a
tapered housing, kept in place by the attrac
tion force of a permanent magnet.
In the case of violent impact, the ball is released from the magnetic detent and opens the normally closed
(NC) electrical circuit to cut off the auxiliary fuel pump connection to earth, and as a consequence the
supply to the injection system.
To restore the auxiliary pump earth connection, move back the seat and press the switch until a click is
heard.
Even after an apparently slight impact, if there is a smell of fuel or there are leaks from the fuel
system, do not turn the switch back on, but search for the fault and remedy it to prevent the risk
of fire.
'N.C. N.A. C
Inertia switch components
1. Inertia switch assembly
2. Sheath
3. Button
4. Upper side
5. Engagement side
6. Permanent magnet
7. Permanent magnet seat
8. Steel ball
C Common terminal
N.C. Normally closed contact
N.A. Normally open contact
22 Publication no. 506.763/24
Page 109 of 330
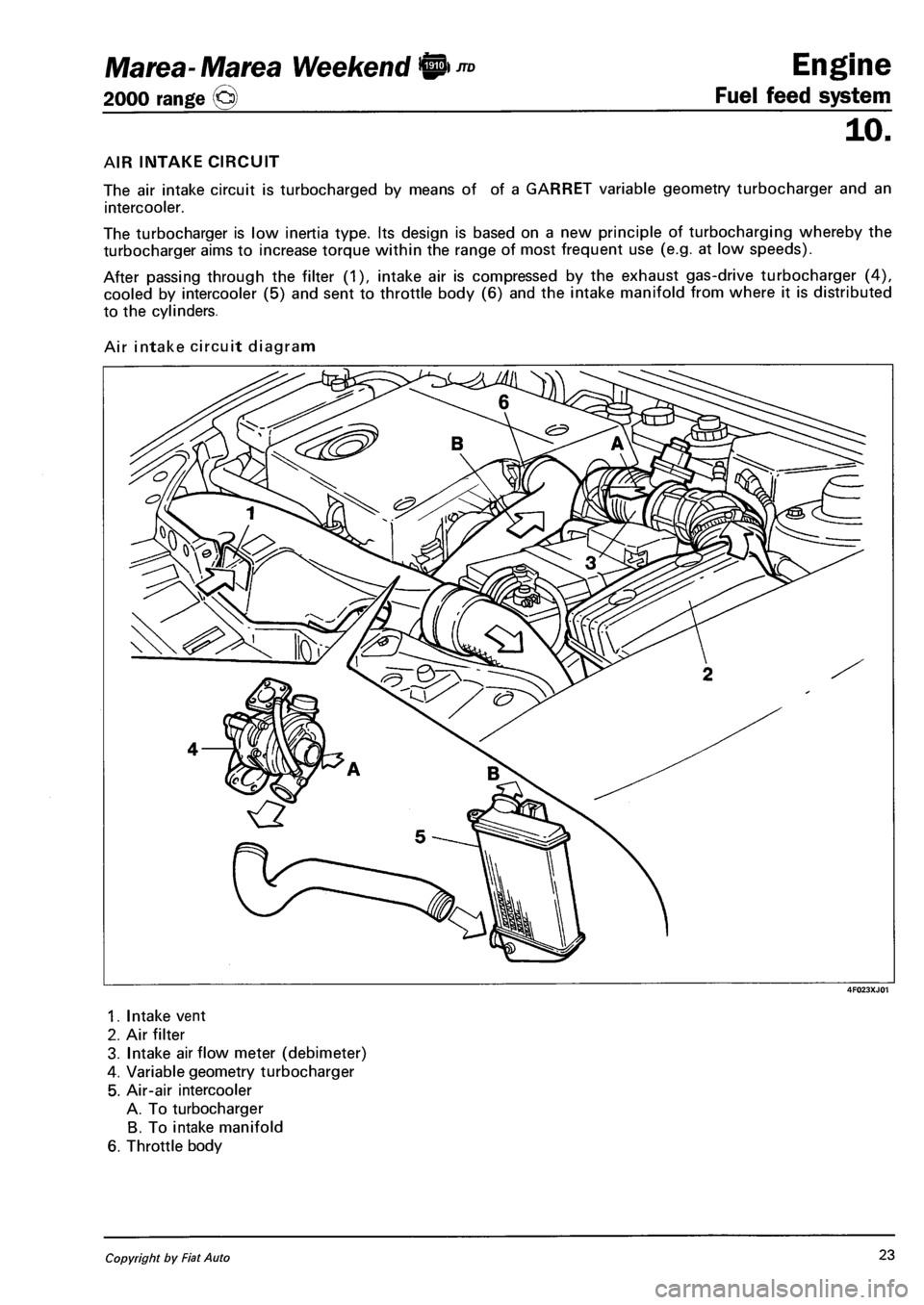
Marea-Marea Weekend 9 Engine
2000 range ©) Fuel feed system
10.
AIR INTAKE CIRCUIT
The air intake circuit is turbocharged by means of of a GARRET variable geometry turbocharger and an
intercooler.
The turbocharger is low inertia type. Its design is based on a new principle of turbocharging whereby the
turbocharger aims to increase torque within the range of most frequent use (e.g. at low speeds).
After passing through the filter (1), intake air is compressed by the exhaust gas-drive turbocharger (4),
cooled by intercooler (5) and sent to throttle body (6) and the intake manifold from where it is distributed
to the cylinders.
Air intake circuit diagram
4F023XJ01
1. Intake vent
2. Air filter
3. Intake airflow meter (debimeter)
4. Variable geometry turbocharger
5. Air-air intercooler
A. To turbocharger
B. To intake manifold
6. Throttle body
Copyright by Fiat Auto 23
Page 110 of 330
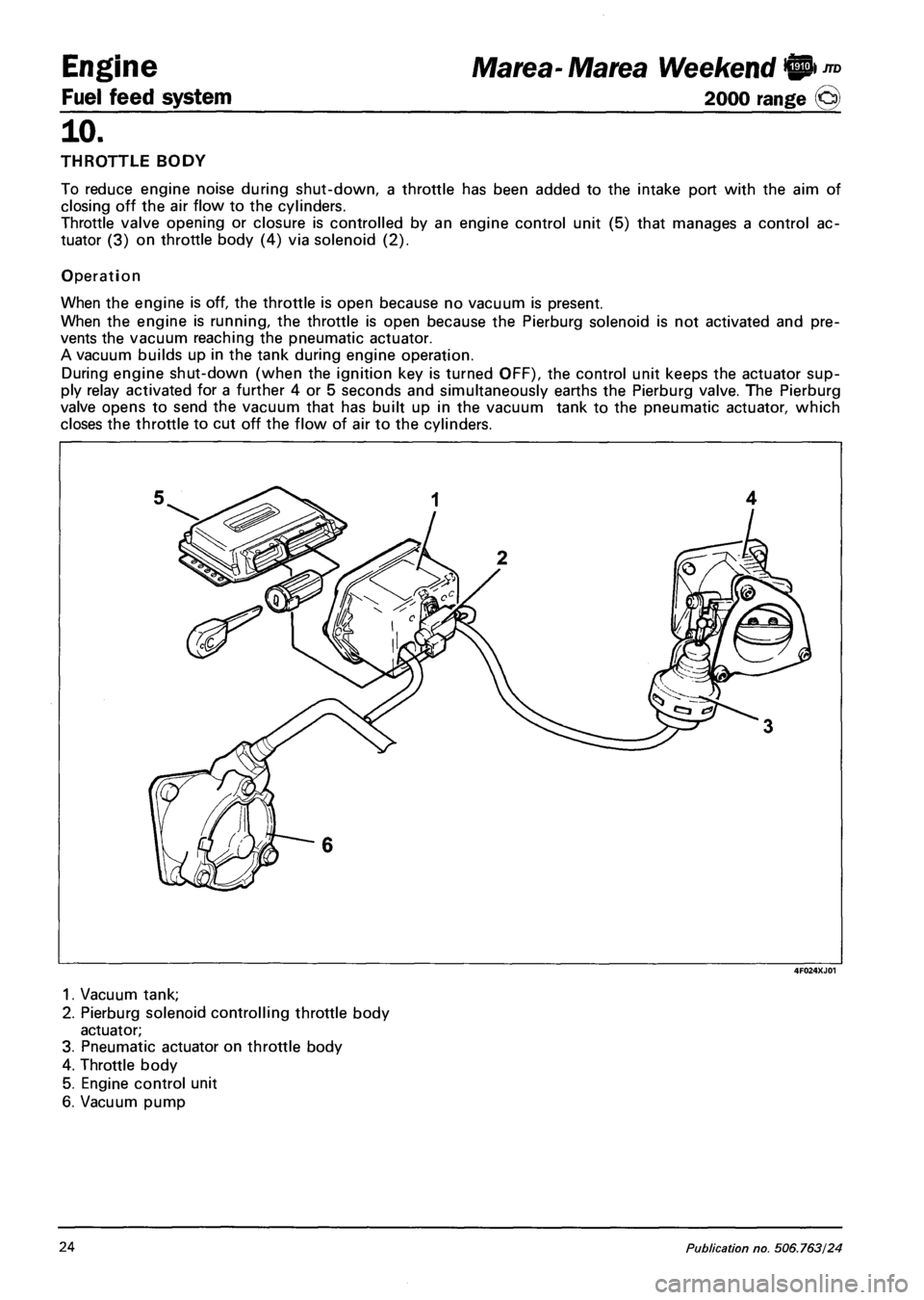
Engine Marea- Marea Weekend 9*nD
Fuel feed system 2000 range (§)
10.
THROTTLE BODY
To reduce engine noise during shut-down, a throttle has been added to the intake port with the aim of
closing off the air flow to the cylinders.
Throttle valve opening or closure is controlled by an engine control unit (5) that manages a control ac
tuator (3) on throttle body (4) via solenoid (2).
Operation
When the engine is off, the throttle is open because no vacuum is present.
When the engine is running, the throttle is open because the Pierburg solenoid is not activated and pre
vents the vacuum reaching the pneumatic actuator.
A vacuum builds up in the tank during engine operation.
During engine shut-down (when the ignition key is turned OFF), the control unit keeps the actuator sup
ply relay activated for a further 4 or 5 seconds and simultaneously earths the Pierburg valve. The Pierburg
valve opens to send the vacuum that has built up in the vacuum tank to the pneumatic actuator, which
closes the throttle to cut off the flow of air to the cylinders.
4F024XJ01
1. Vacuum tank;
2. Pierburg solenoid controlling throttle body
actuator;
3. Pneumatic actuator on throttle body
4. Throttle body
5. Engine control unit
6. Vacuum pump
24 Publication no. 506.763/24
Page 111 of 330
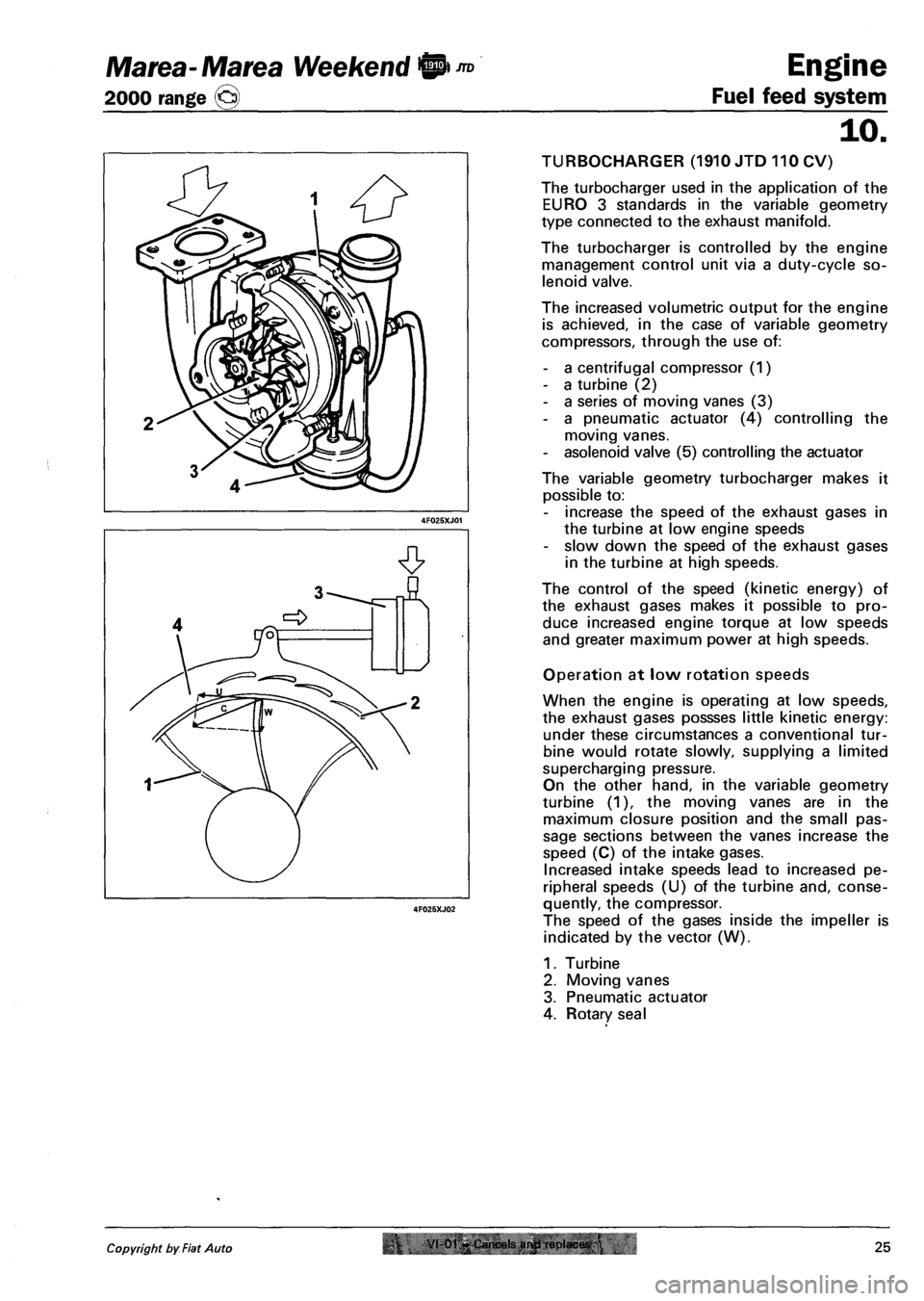
Marea- Marea Weekend 9
2000 range ©
Engine
Fuel feed system
10.
TURBOCHARGER (1910 JTD 110 CV)
The turbocharger used in the application of the
EURO 3 standards in the variable geometry
type connected to the exhaust manifold.
The turbocharger is controlled by the engine
management control unit via a duty-cycle so
lenoid valve.
The increased volumetric output for the engine
is achieved, in the case of variable geometry
compressors, through the use of:
- a centrifugal compressor (1)
- a turbine (2)
- a series of moving vanes (3)
- a pneumatic actuator (4) controlling the
moving vanes.
- asolenoid valve (5) controlling the actuator
The variable geometry turbocharger makes it
possible to:
- increase the speed of the exhaust gases in
the turbine at low engine speeds
- slow down the speed of the exhaust gases
in the turbine at high speeds.
The control of the speed (kinetic energy) of
the exhaust gases makes it possible to pro
duce increased engine torque at low speeds
and greater maximum power at high speeds.
Operation at low rotation speeds
When the engine is operating at low speeds,
the exhaust gases possses little kinetic energy:
under these circumstances a conventional tur
bine would rotate slowly, supplying a limited
supercharging pressure.
On the other hand, in the variable geometry
turbine (1), the moving vanes are in the
maximum closure position and the small pas
sage sections between the vanes increase the
speed (C) of the intake gases.
Increased intake speeds lead to increased pe
ripheral speeds (U) of the turbine and, conse
quently, the compressor.
The speed of the gases inside the impeller is
indicated by the vector (W).
1. Turbine
2. Moving vanes
3. Pneumatic actuator
4. Rotary seal
Copyright by Fiat Auto r VI-01-Cancels arwl replaces.25
Page 112 of 330
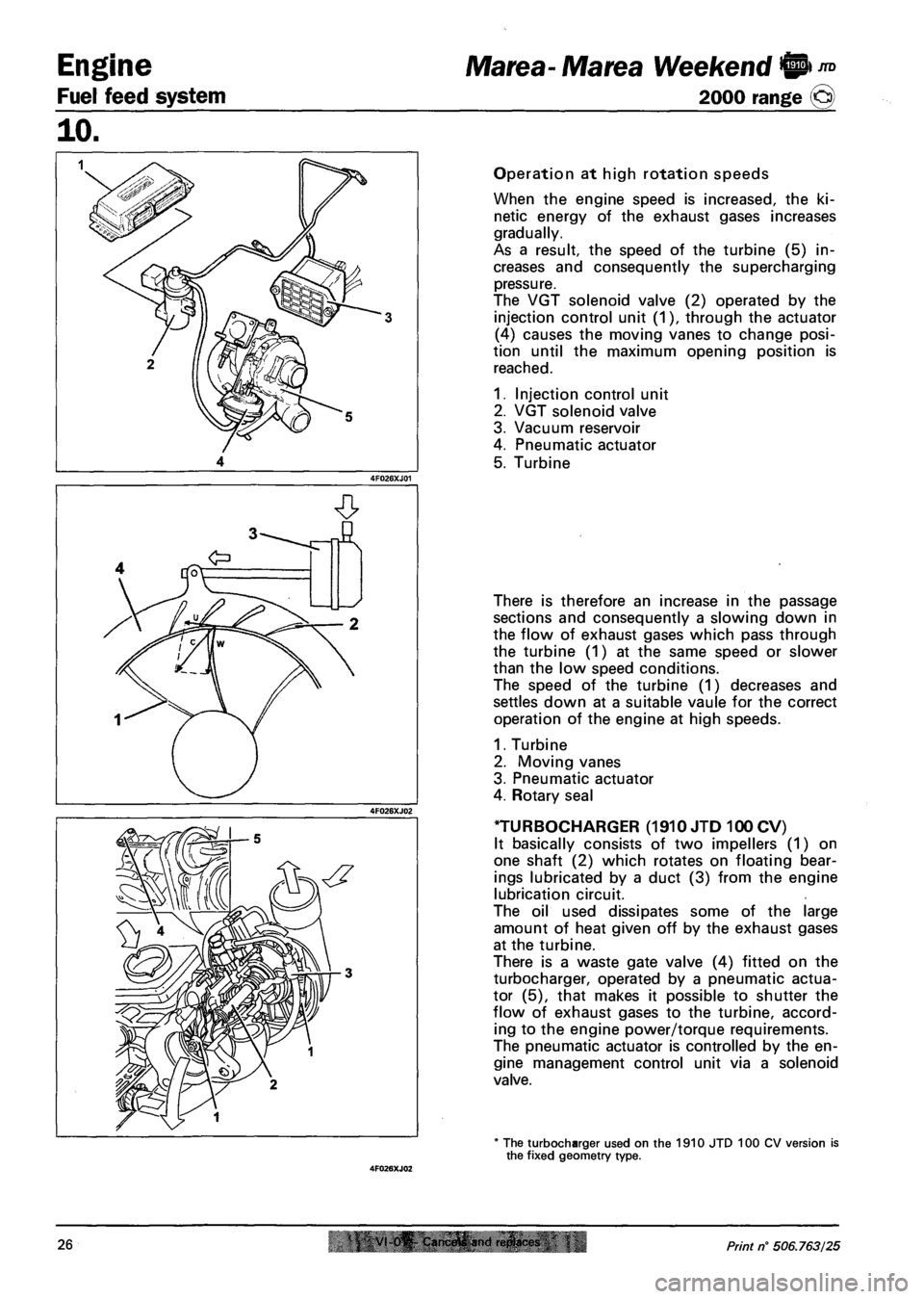
Engine
Fuel feed system
JTD Marea- Marea Weekend 9
2000 range @
10.
Operation at high rotation speeds
When the engine speed is increased, the ki
netic energy of the exhaust gases increases
gradually.
As a result, the speed of the turbine (5) in
creases and consequently the supercharging
pressure.
The VGT solenoid valve (2) operated by the
injection control unit (1), through the actuator
(4) causes the moving vanes to change posi
tion until the maximum opening position is
reached.
1. Injection control unit
2. VGT solenoid valve
3. Vacuum reservoir
4. Pneumatic actuator
5. Turbine
There is therefore an increase in the passage
sections and consequently a slowing down in
the flow of exhaust gases which pass through
the turbine (1) at the same speed or slower
than the low speed conditions.
The speed of the turbine (1) decreases and
settles down at a suitable vaule for the correct
operation of the engine at high speeds.
1. Turbine
2. Moving vanes
3. Pneumatic actuator
4. Rotary seal
TURBOCHARGER (1910 JTD 100 CV)
It basically consists of two impellers (1) on
one shaft (2) which rotates on floating bear
ings lubricated by a duct (3) from the engine
lubrication circuit.
The oil used dissipates some of the large
amount of heat given off by the exhaust gases
at the turbine.
There is a waste gate valve (4) fitted on the
turbocharger, operated by a pneumatic actua
tor (5), that makes it possible to shutter the
flow of exhaust gases to the turbine, accord
ing to the engine power/torque requirements.
The pneumatic actuator is controlled by the en
gine management control unit via a solenoid
valve.
* The turbocharger used on the 1910 JTD 100 CV version is the fixed geometry type.
26 VI 0^ Cam.frtfi and ri!plact<& Print n° 506.763/25
Page 113 of 330
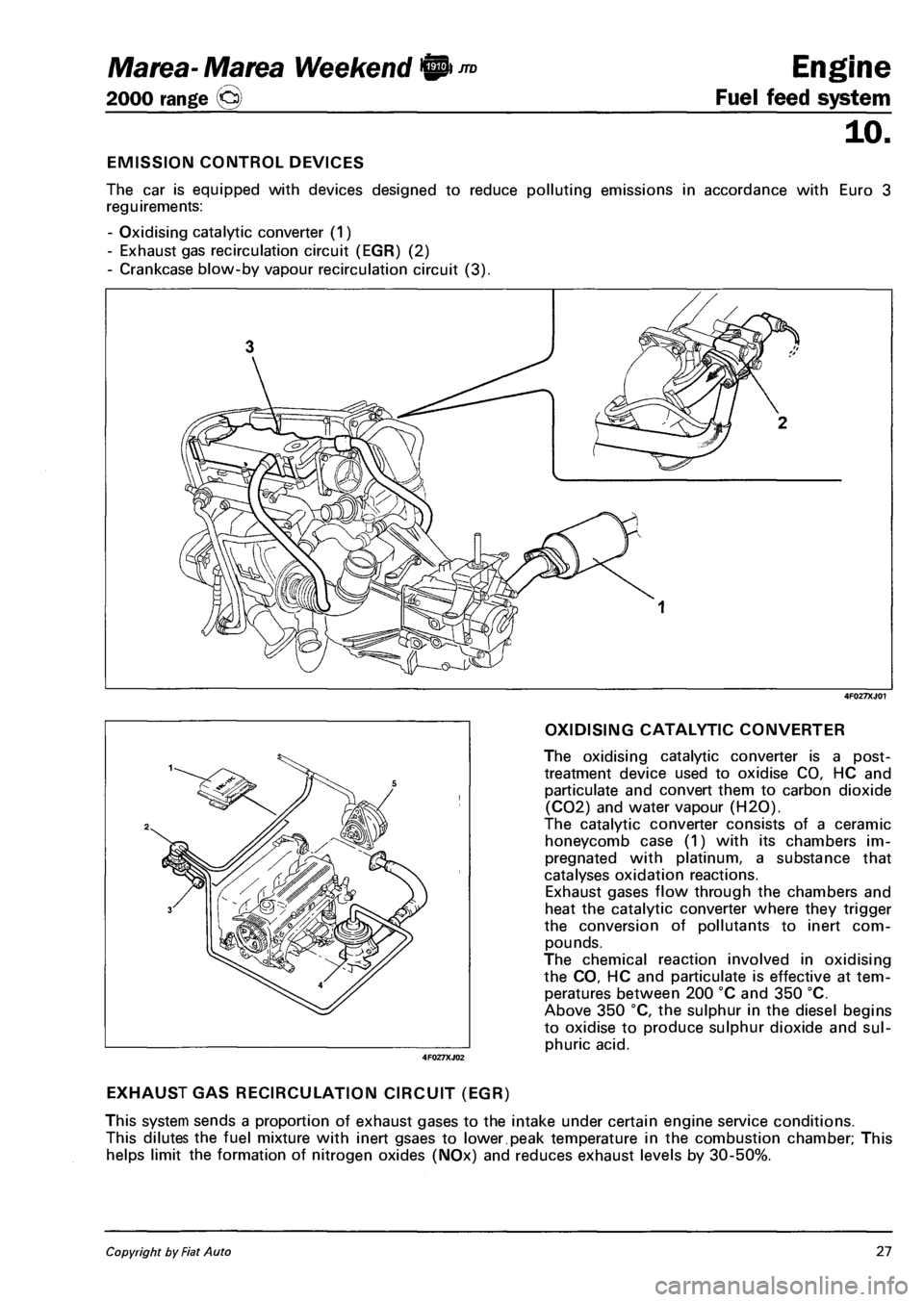
Marea- Marea Weekend 0 *° Engine
2000 range @ Fuel feed system
10.
EMISSION CONTROL DEVICES
The car is equipped with devices designed to reduce polluting emissions in accordance with Euro 3
reguirements:
- Oxidising catalytic converter (1)
- Exhaust gas recirculation circuit (EGR) (2)
- Crankcase blow-by vapour recirculation circuit (3).
4F027XJ01
OXIDISING CATALYTIC CONVERTER
The oxidising catalytic converter is a post-
treatment device used to oxidise CO, HC and
particulate and convert them to carbon dioxide
(C02) and water vapour (H20).
The catalytic converter consists of a ceramic
honeycomb case (1) with its chambers im
pregnated with platinum, a substance that
catalyses oxidation reactions.
Exhaust gases flow through the chambers and
heat the catalytic converter where they trigger
the conversion of pollutants to inert com
pounds.
The chemical reaction involved in oxidising
the CO, HC and particulate is effective at tem
peratures between 200 °C and 350 °C.
Above 350 °C, the sulphur in the diesel begins
to oxidise to produce sulphur dioxide and sul
phuric acid.
EXHAUST GAS RECIRCULATION CIRCUIT (EGR)
This system sends a proportion of exhaust gases to the intake under certain engine service conditions.
This dilutes the fuel mixture with inert gsaes to lower.peak temperature in the combustion chamber; This
helps limit the formation of nitrogen oxides (NOx) and reduces exhaust levels by 30-50%.
4F027XJ02
Copyright by Fiat Auto 27
Page 114 of 330
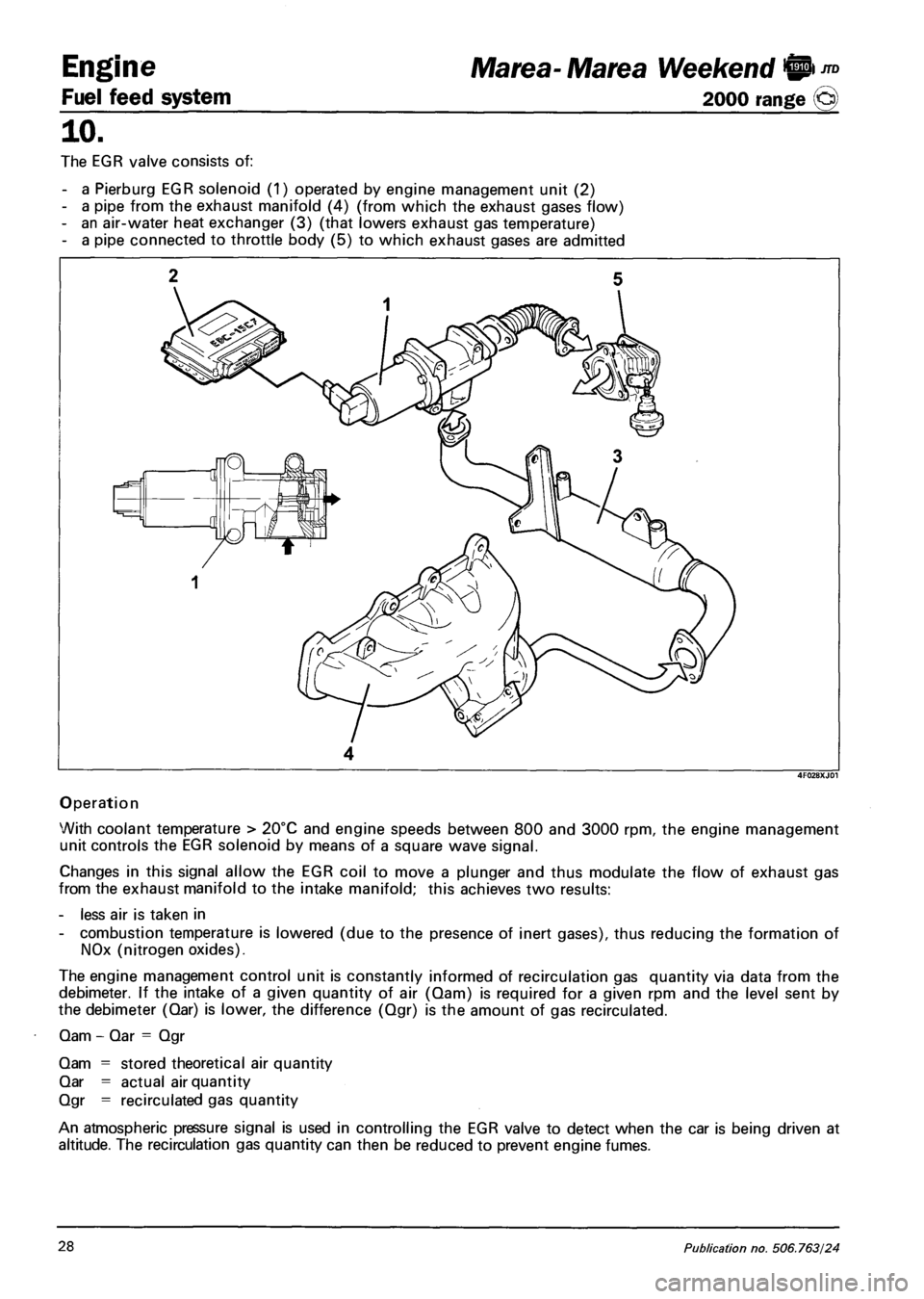
Engine Marea- Marea Weekend IP ™
Fuel feed system 2000 range o
10.
The EGR valve consists of:
- a Pierburg EGR solenoid (1) operated by engine management unit (2)
- a pipe from the exhaust manifold (4) (from which the exhaust gases flow)
- an air-water heat exchanger (3) (that lowers exhaust gas temperature)
- a pipe connected to throttle body (5) to which exhaust gases are admitted
4
Operation
With coolant temperature > 20°C and engine speeds between 800 and 3000 rpm, the engine management
unit controls the EGR solenoid by means of a square wave signal.
Changes in this signal allow the EGR coil to move a plunger and thus modulate the flow of exhaust gas
from the exhaust manifold to the intake manifold; this achieves two results:
- less air is taken in
- combustion temperature is lowered (due to the presence of inert gases), thus reducing the formation of
NOx (nitrogen oxides).
The engine management control unit is constantly informed of recirculation gas quantity via data from the
debimeter. If the intake of a given quantity of air (Qam) is required for a given rpm and the level sent by
the debimeter (Qar) is lower, the difference (Qgr) is the amount of gas recirculated.
Qam - Qar = Qgr
Qam = stored theoretical air quantity
Qar = actual air quantity
Qgr = recirculated gas quantity
An atmospheric pressure signal is used in controlling the EGR valve to detect when the car is being driven at
altitude. The recirculation gas quantity can then be reduced to prevent engine fumes.
28 Publication no. 506.763/24
Page 115 of 330
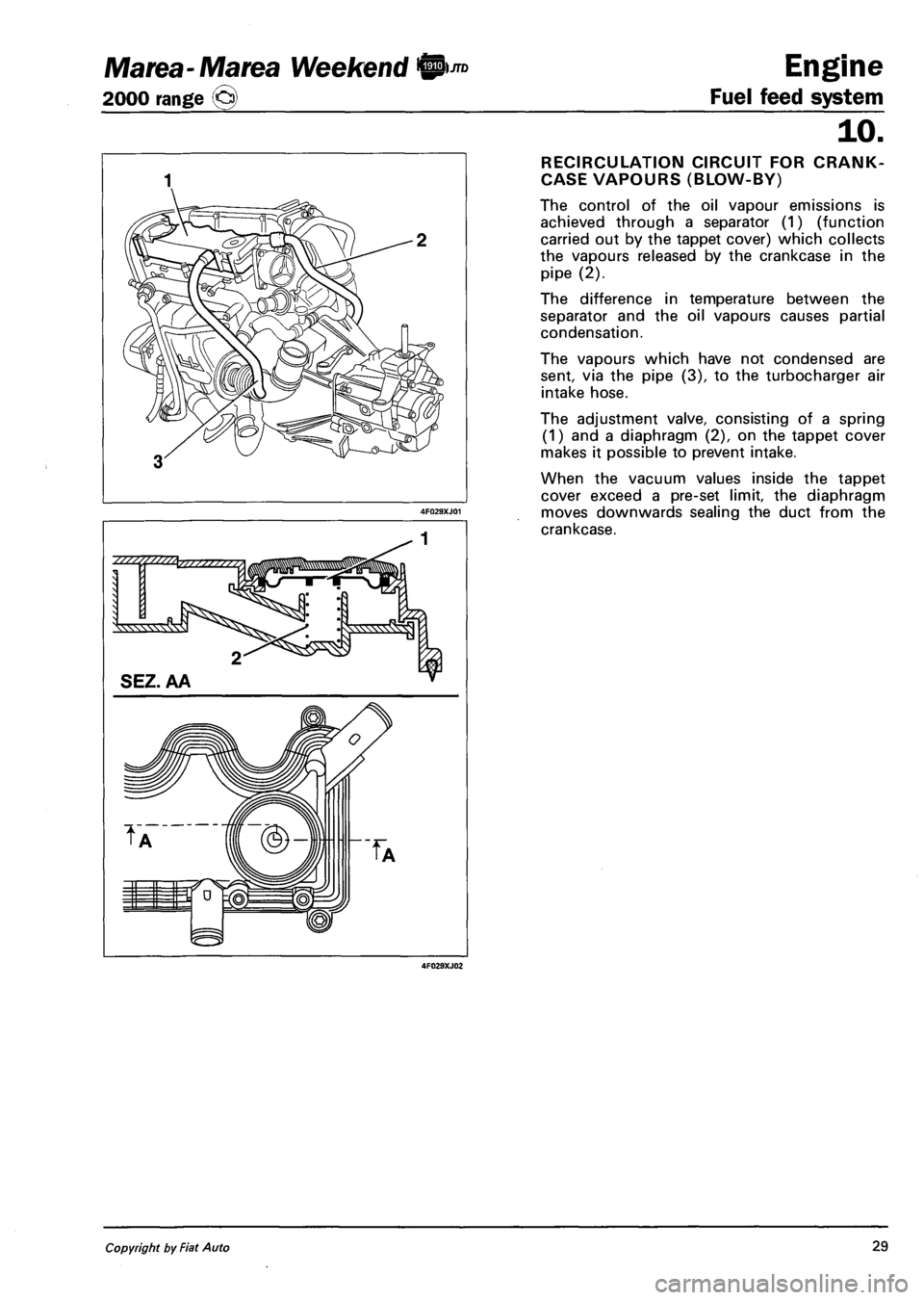
Marea-Marea Weekend
2000 range (j§)
1
4F029XJ02
Engine
Fuel feed system
10.
RECIRCULATION CIRCUIT FOR CRANK-
CASE VAPOURS (BLOW-BY)
The control of the oil vapour emissions is
achieved through a separator (1) (function
carried out by the tappet cover) which collects
the vapours released by the crankcase in the
pipe (2).
The difference in temperature between the
separator and the oil vapours causes partial
condensation.
The vapours which have not condensed are
sent, via the pipe (3), to the turbocharger air
intake hose.
The adjustment valve, consisting of a spring
(1) and a diaphragm (2), on the tappet cover
makes it possible to prevent intake.
When the vacuum values inside the tappet
cover exceed a pre-set limit, the diaphragm
moves downwards sealing the duct from the
crankcase.
Copyright by Fiat Auto 29
Page 116 of 330
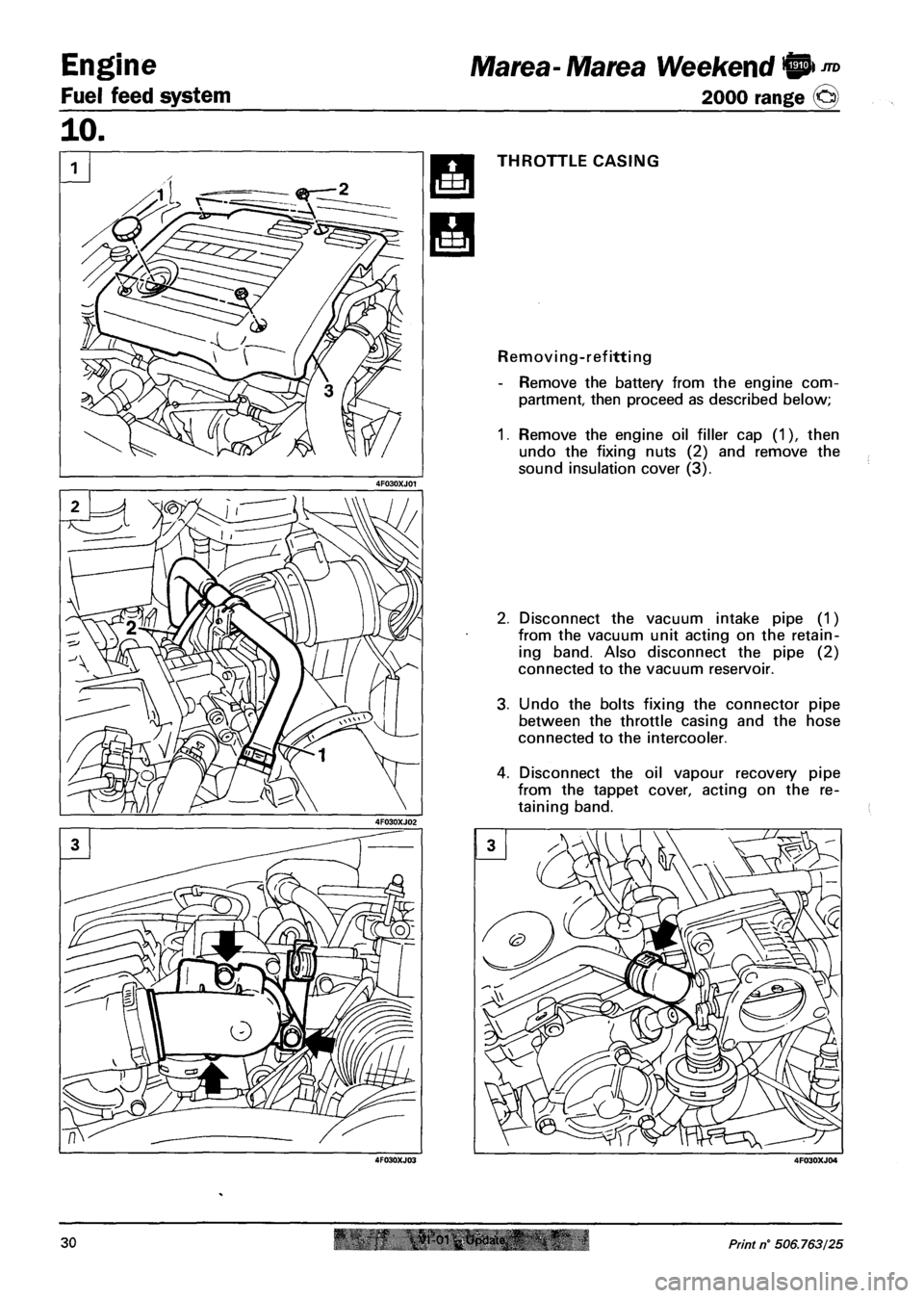
Engine
Fuel feed system
Marea-Marea Weekend
2000 range ©
THROTTLE CASING
Removing-refitting
- Remove the battery from the engine com
partment, then proceed as described below;
1. Remove the engine oil filler cap (1), then
undo the fixing nuts (2) and remove the
sound insulation cover (3).
2. Disconnect the vacuum intake pipe (1)
from the vacuum unit acting on the retain
ing band. Also disconnect the pipe (2)
connected to the vacuum reservoir.
3. Undo the bolts fixing the connector pipe
between the throttle casing and the hose
connected to the intercooler.
4. Disconnect the oil vapour recovery pipe
from the tappet cover, acting on the re
taining band.
30 Print n° 506.763/25