check oil GEELY CK 2008 Owner's Manual
[x] Cancel search | Manufacturer: GEELY, Model Year: 2008, Model line: CK, Model: GEELY CK 2008Pages: 392, PDF Size: 38.86 MB
Page 59 of 392
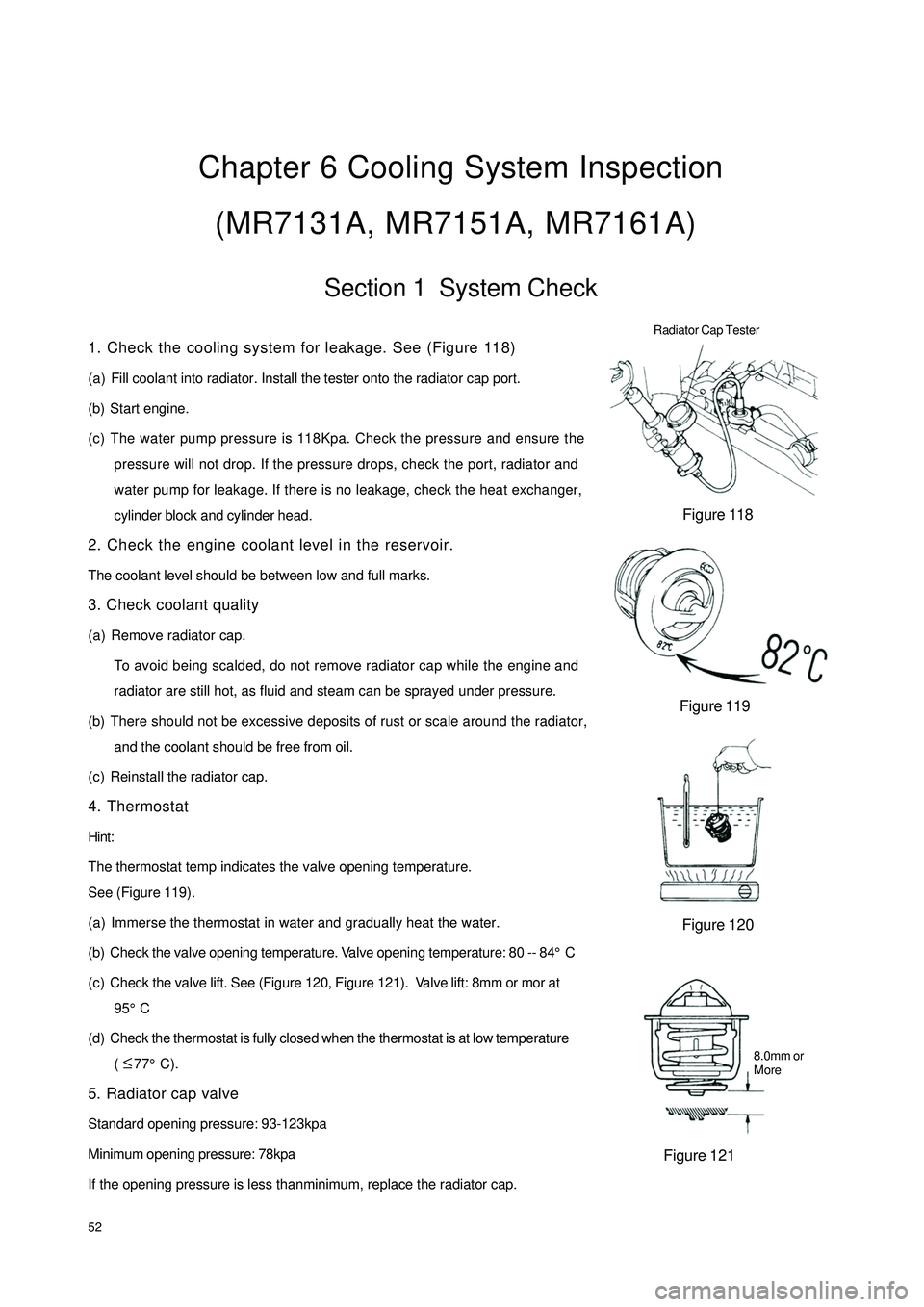
52Chapter 6 Cooling System Inspection
(MR7131A, MR7151A, MR7161A)Section 1 System Check1. Check the cooling system for leakage. See (Figure 118)
(a) Fill coolant into radiator. Install the tester onto the radiator cap port.
(b) Start engine.
(c) The water pump pressure is 118Kpa. Check the pressure and ensure the
pressure will not drop. If the pressure drops, check the port, radiator and
water pump for leakage. If there is no leakage, check the heat exchanger,
cylinder block and cylinder head.
2. Check the engine coolant level in the reservoir.
The coolant level should be between low and full marks.
3. Check coolant quality
(a) Remove radiator cap.
To avoid being scalded, do not remove radiator cap while the engine and
radiator are still hot, as fluid and steam can be sprayed under pressure.
(b) There should not be excessive deposits of rust or scale around the radiator,
and the coolant should be free from oil.
(c) Reinstall the radiator cap.
4. Thermostat
Hint:
The thermostat temp indicates the valve opening temperature.
See (Figure 119).
(a) Immerse the thermostat in water and gradually heat the water.
(b) Check the valve opening temperature. Valve opening temperature: 80 -- 84°C
(c) Check the valve lift. See (Figure 120, Figure 121). Valve lift: 8mm or mor at
95°C
(d) Check the thermostat is fully closed when the thermostat is at low temperature
( 77°C).
5. Radiator cap valve
Standard opening pressure: 93-123kpa
Minimum opening pressure: 78kpa
If the opening pressure is less thanminimum, replace the radiator cap.Figure 118
Figure 119
Figure 120
Figure 121 Radiator Cap Tester8.0mm or
More ≤
Page 72 of 392
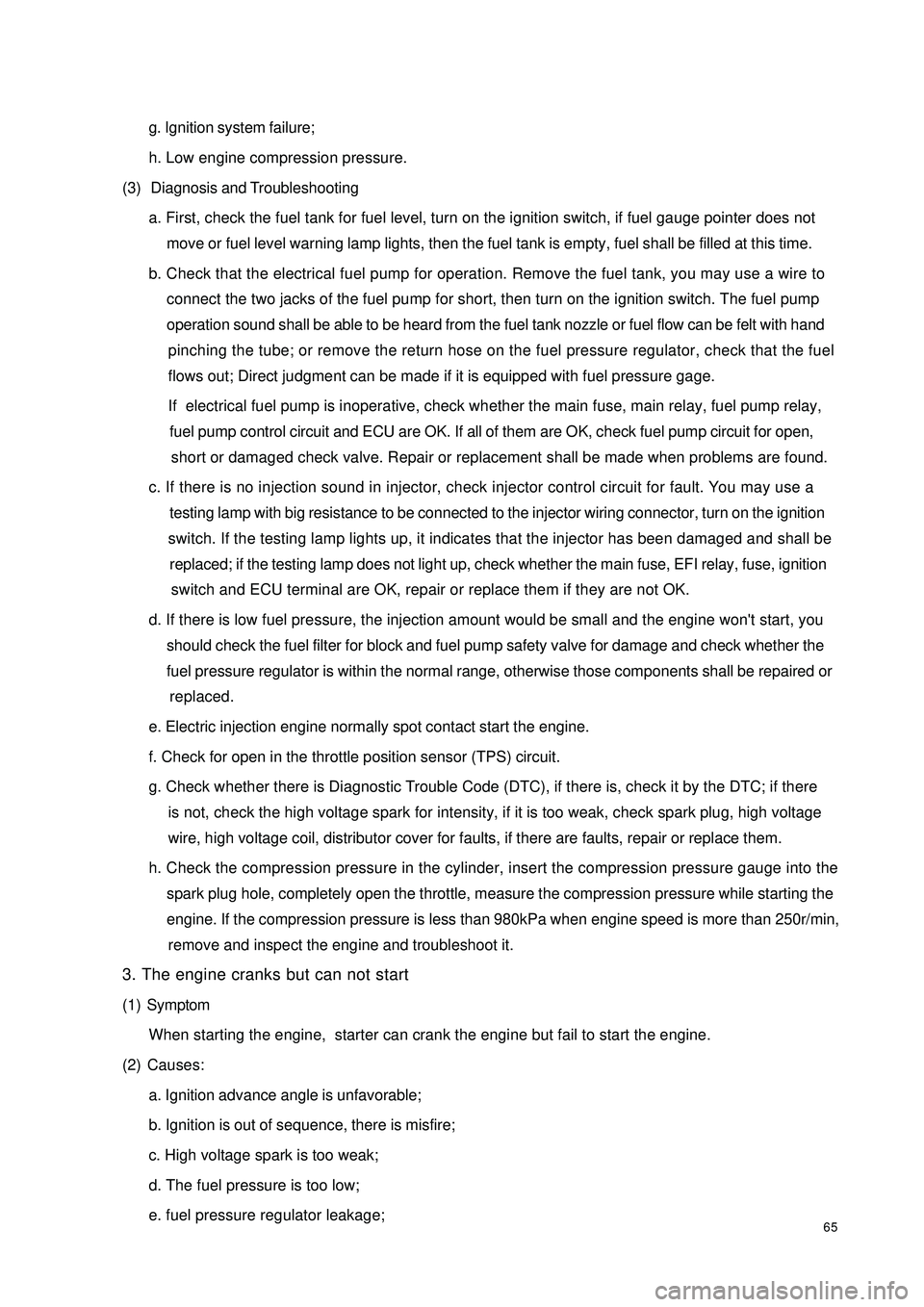
65g. Ignition system failure;
h. Low engine compression pressure.
(3) Diagnosis and Troubleshooting
a. First, check the fuel tank for fuel level, turn on the ignition switch, if fuel gauge pointer does not
move or fuel level warning lamp lights, then the fuel tank is empty, fuel shall be filled at this time.
b. Check that the electrical fuel pump for operation. Remove the fuel tank, you may use a wire to
connect the two jacks of the fuel pump for short, then turn on the ignition switch. The fuel pump
operation sound shall be able to be heard from the fuel tank nozzle or fuel flow can be felt with hand
pinching the tube; or remove the return hose on the fuel pressure regulator, check that the fuel
flows out; Direct judgment can be made if it is equipped with fuel pressure gage.
If electrical fuel pump is inoperative, check whether the main fuse, main relay, fuel pump relay,
fuel pump control circuit and ECU are OK. If all of them are OK, check fuel pump circuit for open,
short or damaged check valve. Repair or replacement shall be made when problems are found.
c. If there is no injection sound in injector, check injector control circuit for fault. You may use a
testing lamp with big resistance to be connected to the injector wiring connector, turn on the ignition
switch. If the testing lamp lights up, it indicates that the injector has been damaged and shall be
replaced; if the testing lamp does not light up, check whether the main fuse, EFI relay, fuse, ignition
switch and ECU terminal are OK, repair or replace them if they are not OK.
d. If there is low fuel pressure, the injection amount would be small and the engine won't start, you
should check the fuel filter for block and fuel pump safety valve for damage and check whether the
fuel pressure regulator is within the normal range, otherwise those components shall be repaired or
replaced.
e. Electric injection engine normally spot contact start the engine.
f. Check for open in the throttle position sensor (TPS) circuit.
g. Check whether there is Diagnostic Trouble Code (DTC), if there is, check it by the DTC; if there
is not, check the high voltage spark for intensity, if it is too weak, check spark plug, high voltage
wire, high voltage coil, distributor cover for faults, if there are faults, repair or replace them.
h. Check the compression pressure in the cylinder, insert the compression pressure gauge into the
spark plug hole, completely open the throttle, measure the compression pressure while starting the
engine. If the compression pressure is less than 980kPa when engine speed is more than 250r/min,
remove and inspect the engine and troubleshoot it.
3. The engine cranks but can not start
(1) Symptom
When starting the engine, starter can crank the engine but fail to start the engine.
(2) Causes:
a. Ignition advance angle is unfavorable;
b. Ignition is out of sequence, there is misfire;
c. High voltage spark is too weak;
d. The fuel pressure is too low;
e. fuel pressure regulator leakage;
Page 73 of 392
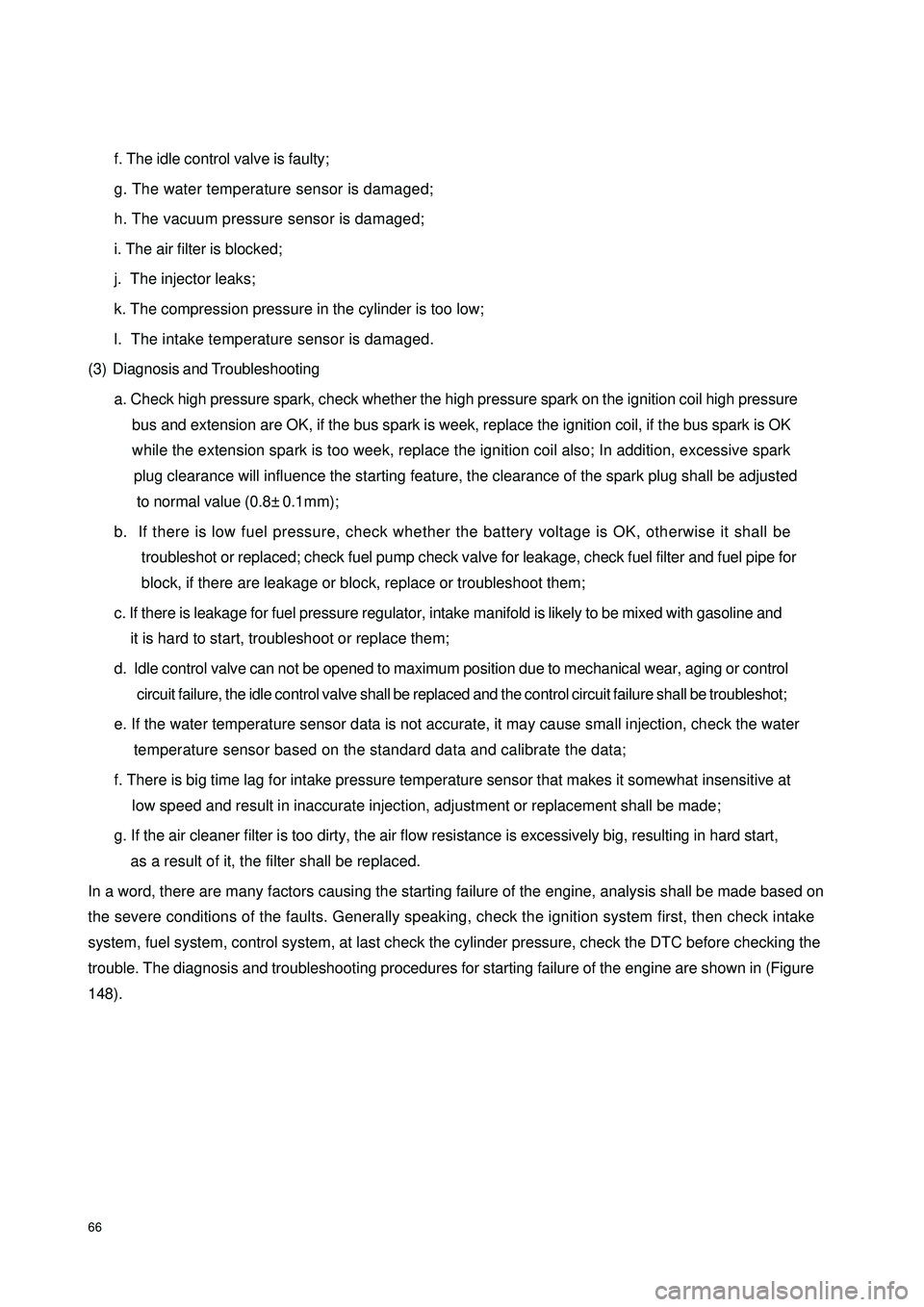
66f. The idle control valve is faulty;
g. The water temperature sensor is damaged;
h. The vacuum pressure sensor is damaged;
i. The air filter is blocked;
j. The injector leaks;
k. The compression pressure in the cylinder is too low;
l. The intake temperature sensor is damaged.
(3) Diagnosis and Troubleshooting
a. Check high pressure spark, check whether the high pressure spark on the ignition coil high pressure
bus and extension are OK, if the bus spark is week, replace the ignition coil, if the bus spark is OK
while the extension spark is too week, replace the ignition coil also; In addition, excessive spark
plug clearance will influence the starting feature, the clearance of the spark plug shall be adjusted
to normal value (0.8±0.1mm);
b. If there is low fuel pressure, check whether the battery voltage is OK, otherwise it shall be
troubleshot or replaced; check fuel pump check valve for leakage, check fuel filter and fuel pipe for
block, if there are leakage or block, replace or troubleshoot them;
c. If there is leakage for fuel pressure regulator, intake manifold is likely to be mixed with gasoline and
it is hard to start, troubleshoot or replace them;
d. Idle control valve can not be opened to maximum position due to mechanical wear, aging or control
circuit failure, the idle control valve shall be replaced and the control circuit failure shall be troubleshot;
e. If the water temperature sensor data is not accurate, it may cause small injection, check the water
temperature sensor based on the standard data and calibrate the data;
f. There is big time lag for intake pressure temperature sensor that makes it somewhat insensitive at
low speed and result in inaccurate injection, adjustment or replacement shall be made;
g. If the air cleaner filter is too dirty, the air flow resistance is excessively big, resulting in hard start,
as a result of it, the filter shall be replaced.
In a word, there are many factors causing the starting failure of the engine, analysis shall be made based on
the severe conditions of the faults. Generally speaking, check the ignition system first, then check intake
system, fuel system, control system, at last check the cylinder pressure, check the DTC before checking the
trouble. The diagnosis and troubleshooting procedures for starting failure of the engine are shown in (Figure
148).
Page 75 of 392
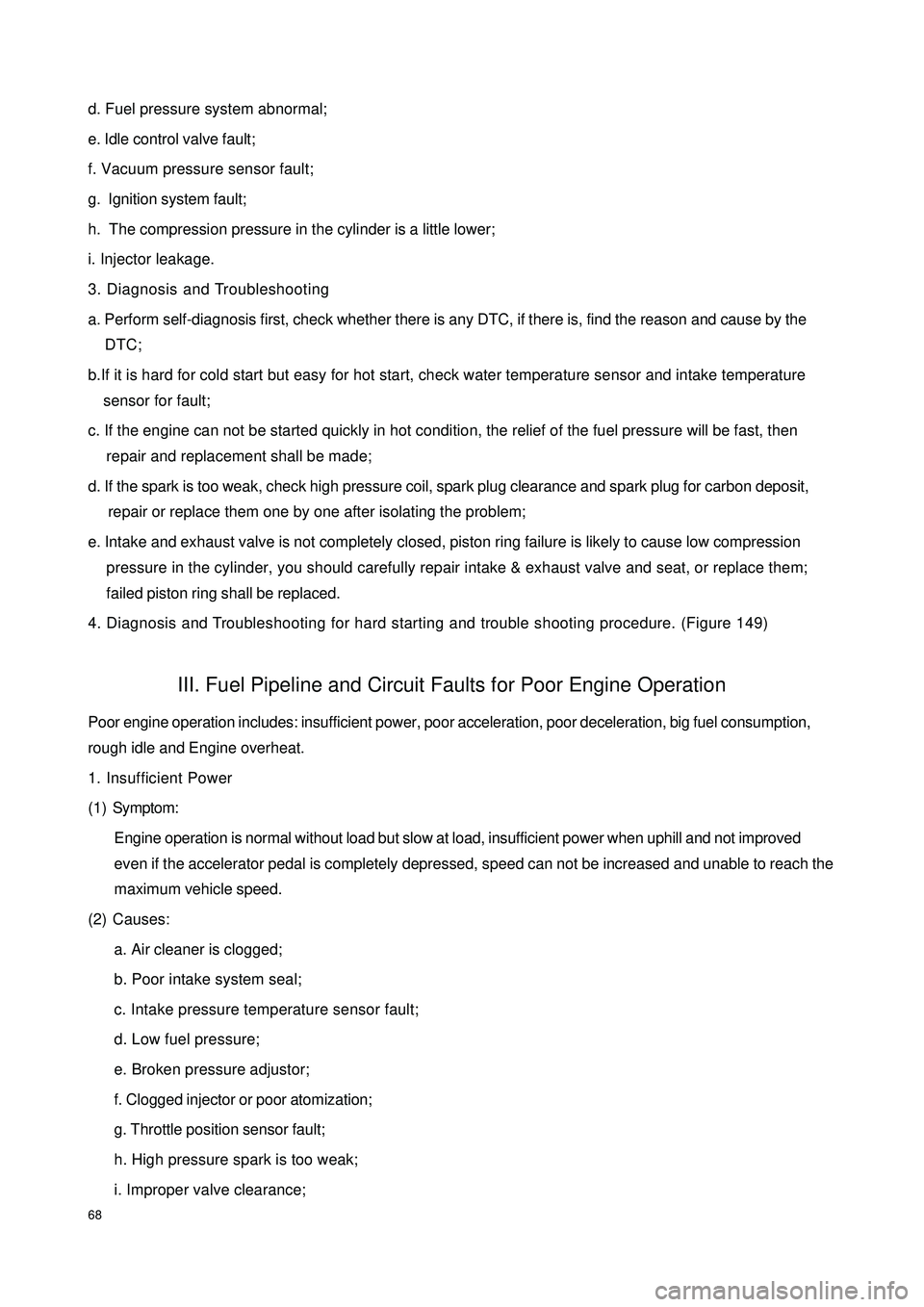
68d. Fuel pressure system abnormal;
e. Idle control valve fault;
f. Vacuum pressure sensor fault;
g. Ignition system fault;
h. The compression pressure in the cylinder is a little lower;
i. Injector leakage.
3. Diagnosis and Troubleshooting
a. Perform self-diagnosis first, check whether there is any DTC, if there is, find the reason and cause by the
DTC;
b.If it is hard for cold start but easy for hot start, check water temperature sensor and intake temperature
sensor for fault;
c. If the engine can not be started quickly in hot condition, the relief of the fuel pressure will be fast, then
repair and replacement shall be made;
d. If the spark is too weak, check high pressure coil, spark plug clearance and spark plug for carbon deposit,
repair or replace them one by one after isolating the problem;
e. Intake and exhaust valve is not completely closed, piston ring failure is likely to cause low compression
pressure in the cylinder, you should carefully repair intake & exhaust valve and seat, or replace them;
failed piston ring shall be replaced.
4. Diagnosis and Troubleshooting for hard starting and trouble shooting procedure. (Figure 149)III. Fuel Pipeline and Circuit Faults for Poor Engine OperationPoor engine operation includes: insufficient power, poor acceleration, poor deceleration, big fuel consumption,
rough idle and Engine overheat.
1. Insufficient Power
(1) Symptom:
Engine operation is normal without load but slow at load, insufficient power when uphill and not improved
even if the accelerator pedal is completely depressed, speed can not be increased and unable to reach the
maximum vehicle speed.
(2) Causes:
a. Air cleaner is clogged;
b. Poor intake system seal;
c. Intake pressure temperature sensor fault;
d. Low fuel pressure;
e. Broken pressure adjustor;
f. Clogged injector or poor atomization;
g. Throttle position sensor fault;
h. High pressure spark is too weak;
i. Improper valve clearance;
Page 77 of 392
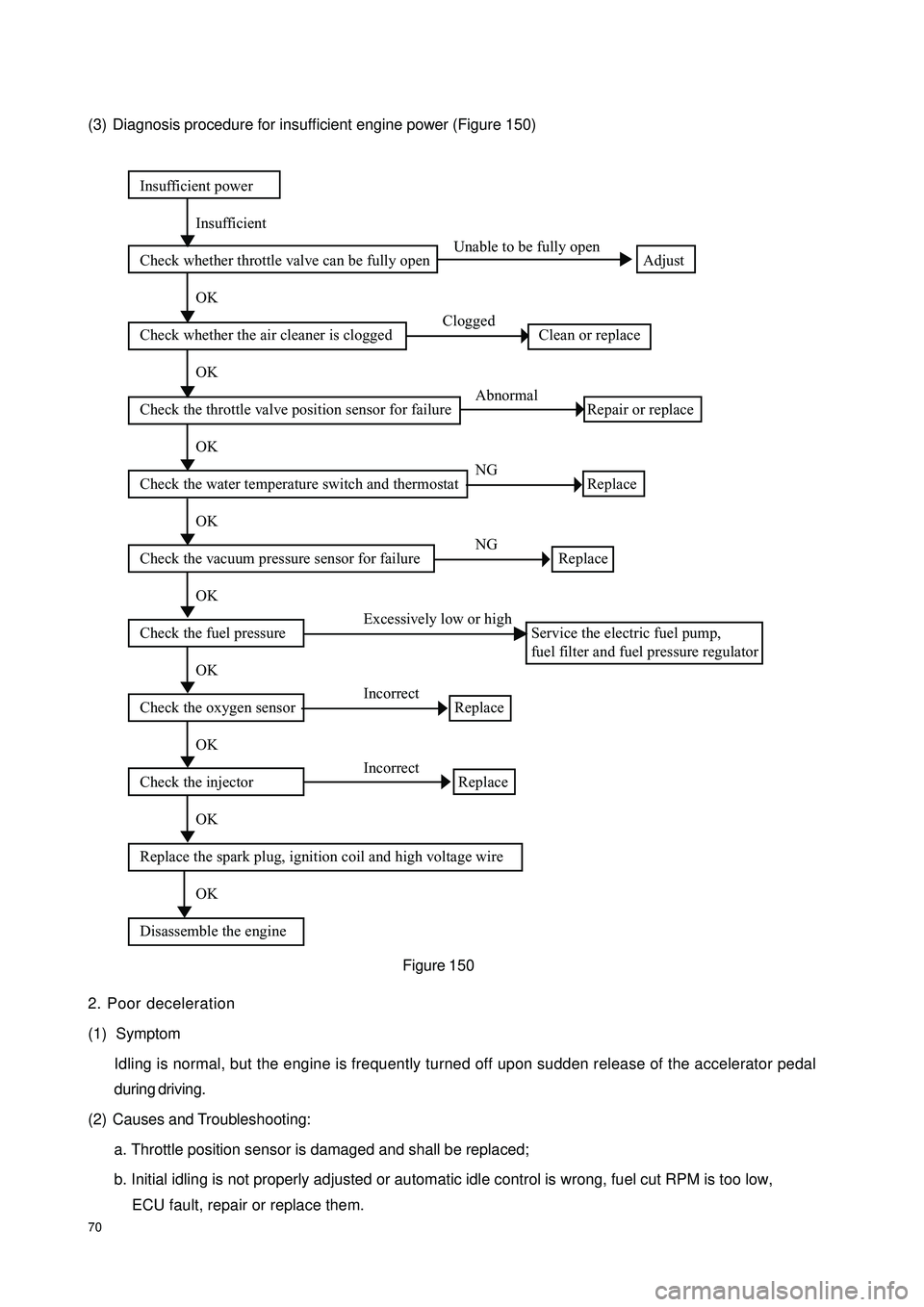
70(3) Diagnosis procedure for insufficient engine power (Figure 150)
2. Poor deceleration
(1) Symptom
Idling is normal, but the engine is frequently turned off upon sudden release of the accelerator pedal
during driving.
(2) Causes and Troubleshooting:
a. Throttle position sensor is damaged and shall be replaced;
b. Initial idling is not properly adjusted or automatic idle control is wrong, fuel cut RPM is too low,
ECU fault, repair or replace them.Insufficient power
Insufficient
Check whether throttle valve can be fully open Unable to be fully open
Adjust
OK
Check whether the air cleaner is clogged Clogged
Clean or replace
OK
Check the throttle valve position sensor for failure Abnormal
Repair or replace
OK
Check the water temperature switch and thermostat NG
Replace
OK
Check the vacuum pressure sensor for failure NG
Replace
OK
Check the fuel pressure Excessively low or high
Service the electric fuel pump,
fuel filter and fuel pressure regulator
OK
Check the oxygen sensor Incorrect
Replace
OK
Check the injector Incorrect
Replace
OK
Replace the spark plug, ignition coil and high voltage wire
OK
Disassemble the engineFigure 150
Page 84 of 392
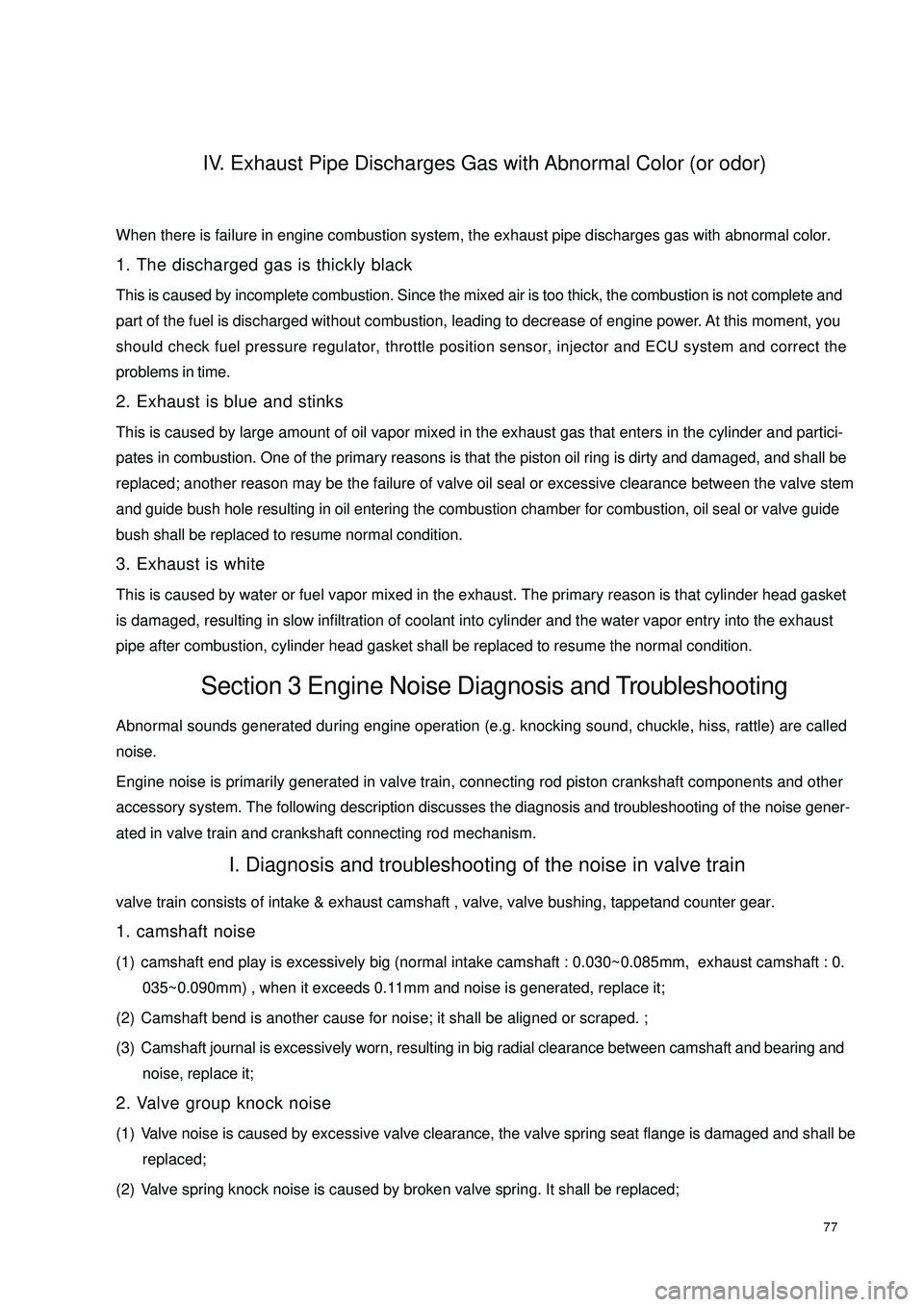
77IV. Exhaust Pipe Discharges Gas with Abnormal Color (or odor)When there is failure in engine combustion system, the exhaust pipe discharges gas with abnormal color.
1. The discharged gas is thickly black
This is caused by incomplete combustion. Since the mixed air is too thick, the combustion is not complete and
part of the fuel is discharged without combustion, leading to decrease of engine power. At this moment, you
should check fuel pressure regulator, throttle position sensor, injector and ECU system and correct the
problems in time.
2. Exhaust is blue and stinks
This is caused by large amount of oil vapor mixed in the exhaust gas that enters in the cylinder and partici-
pates in combustion. One of the primary reasons is that the piston oil ring is dirty and damaged, and shall be
replaced; another reason may be the failure of valve oil seal or excessive clearance between the valve stem
and guide bush hole resulting in oil entering the combustion chamber for combustion, oil seal or valve guide
bush shall be replaced to resume normal condition.
3. Exhaust is white
This is caused by water or fuel vapor mixed in the exhaust. The primary reason is that cylinder head gasket
is damaged, resulting in slow infiltration of coolant into cylinder and the water vapor entry into the exhaust
pipe after combustion, cylinder head gasket shall be replaced to resume the normal condition.Section 3 Engine Noise Diagnosis and TroubleshootingAbnormal sounds generated during engine operation (e.g. knocking sound, chuckle, hiss, rattle) are called
noise.
Engine noise is primarily generated in valve train, connecting rod piston crankshaft components and other
accessory system. The following description discusses the diagnosis and troubleshooting of the noise gener-
ated in valve train and crankshaft connecting rod mechanism.I. Diagnosis and troubleshooting of the noise in valve trainvalve train consists of intake & exhaust camshaft , valve, valve bushing, tappetand counter gear.
1. camshaft noise
(1) camshaft end play is excessively big (normal intake camshaft : 0.030~0.085mm, exhaust camshaft : 0.
035~0.090mm) , when it exceeds 0.11mm and noise is generated, replace it;
(2) Camshaft bend is another cause for noise; it shall be aligned or scraped. ;
(3) Camshaft journal is excessively worn, resulting in big radial clearance between camshaft and bearing and
noise, replace it;
2. Valve group knock noise
(1) Valve noise is caused by excessive valve clearance, the valve spring seat flange is damaged and shall be
replaced;
(2) Valve spring knock noise is caused by broken valve spring. It shall be replaced;
Page 106 of 392
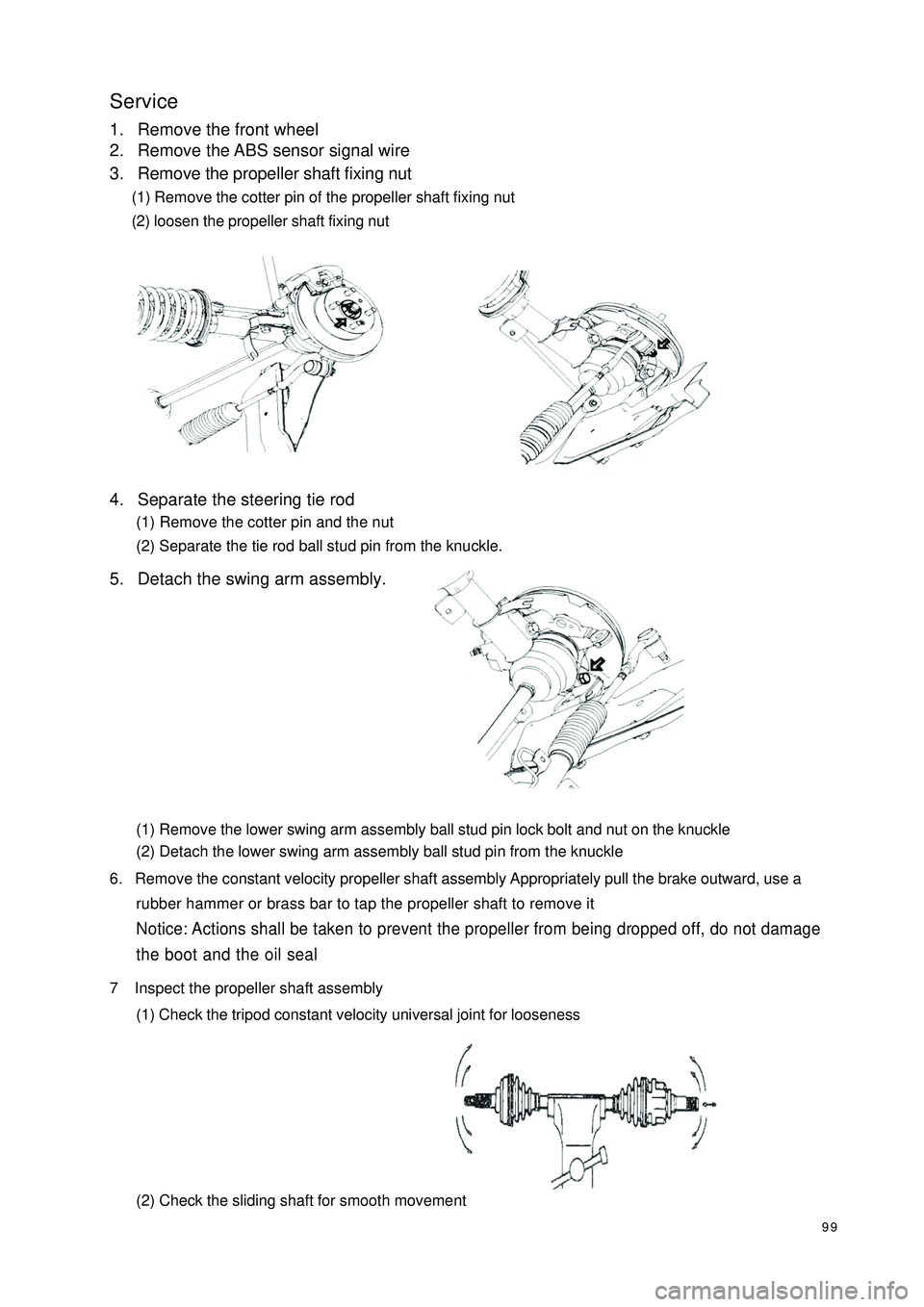
99Service1. Remove the front wheel
2. Remove the ABS sensor signal wire
3. Remove the propeller shaft fixing nut
(1) Remove the cotter pin of the propeller shaft fixing nut
(2) loosen the propeller shaft fixing nut
4. Separate the steering tie rod
(1) Remove the cotter pin and the nut
(2) Separate the tie rod ball stud pin from the knuckle.
5. Detach the swing arm assembly.
(1) Remove the lower swing arm assembly ball stud pin lock bolt and nut on the knuckle
(2) Detach the lower swing arm assembly ball stud pin from the knuckle
6. Remove the constant velocity propeller shaft assembly Appropriately pull the brake outward, use a
rubber hammer or brass bar to tap the propeller shaft to remove itNotice: Actions shall be taken to prevent the propeller from being dropped off, do not damage
the boot and the oil seal7 Inspect the propeller shaft assembly
(1) Check the tripod constant velocity universal joint for looseness
(2) Check the sliding shaft for smooth movement
Page 123 of 392
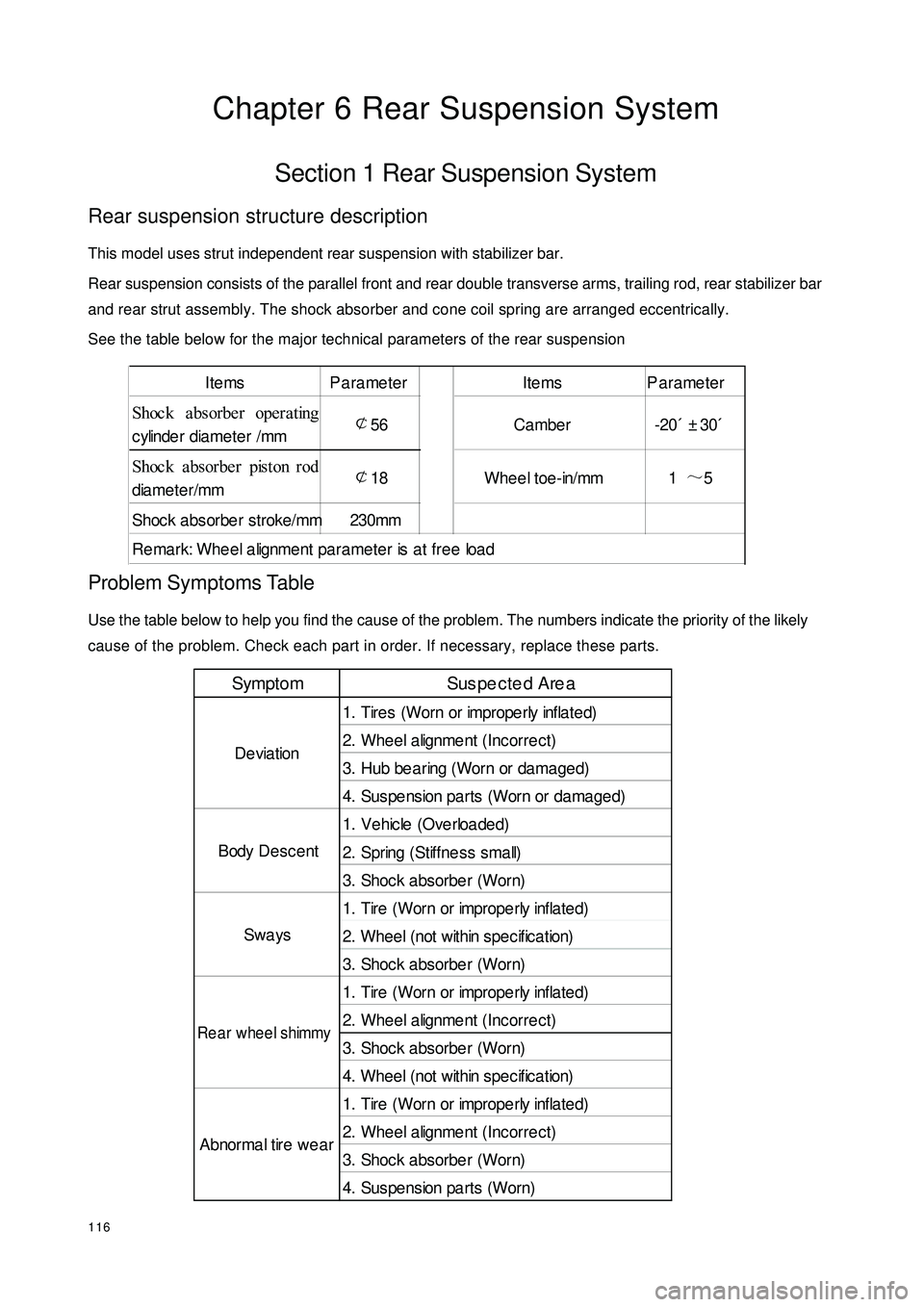
116Chapter 6 Rear Suspension SystemSection 1 Rear Suspension SystemRear suspension structure descriptionThis model uses strut independent rear suspension with stabilizer bar.
Rear suspension consists of the parallel front and rear double transverse arms, trailing rod, rear stabilizer bar
and rear strut assembly. The shock absorber and cone coil spring are arranged eccentrically.
See the table below for the major technical parameters of the rear suspensionProblem Symptoms TableUse the table below to help you find the cause of the problem. The numbers indicate the priority of the likely
cause of the problem. Check each part in order. If necessary, replace these parts.Items Parameter Items Parameter
Shoc k a bsorbe r operating
cylinder diameter /mm¢
56 Cambe r -20´±30´
Shoc k a bsorbe r piston rod
diameter/mm¢
18 Wheel toe-in/mm 1~
5
Shoc k absorbe r stroke/mm 230mm
Remark: Wheel alignment parameter is at free loadSympto m Sus pe cte d Are a
1. Tires (Worn or imprope rly infla te d)
2. Wheel alignment (Incorrect)
3. Hub be a ring (Worn or da ma ge d)
4. Suspe nsion pa rts (Worn or da ma ge d)
1. Ve hic le (Ove rloa de d)
2. Spring (Stiffness small)
3. Shoc k a bsorbe r (Worn)
1. Tire (Worn or imprope rly inflate d)
2. W he e l ( not w it hin s pe c if ic a t ion)
3. Shoc k a bsorbe r (Worn)
1. Tire (Worn or imprope rly inflate d)
2. Wheel alignment (Incorrect)
3. Shoc k a bsorbe r (Worn)
4. W he e l ( not w it hin s pe c if ic a t ion)
1. Tire (Worn or imprope rly inflate d)
2. Wheel alignment (Incorrect)
3. Shoc k a bsorbe r (Worn)
4. Sus pe nsion pa rts (Worn) Abnormal tire wearDeviation
Body Desc ent
SwaysRear wheel shimmy
Page 136 of 392
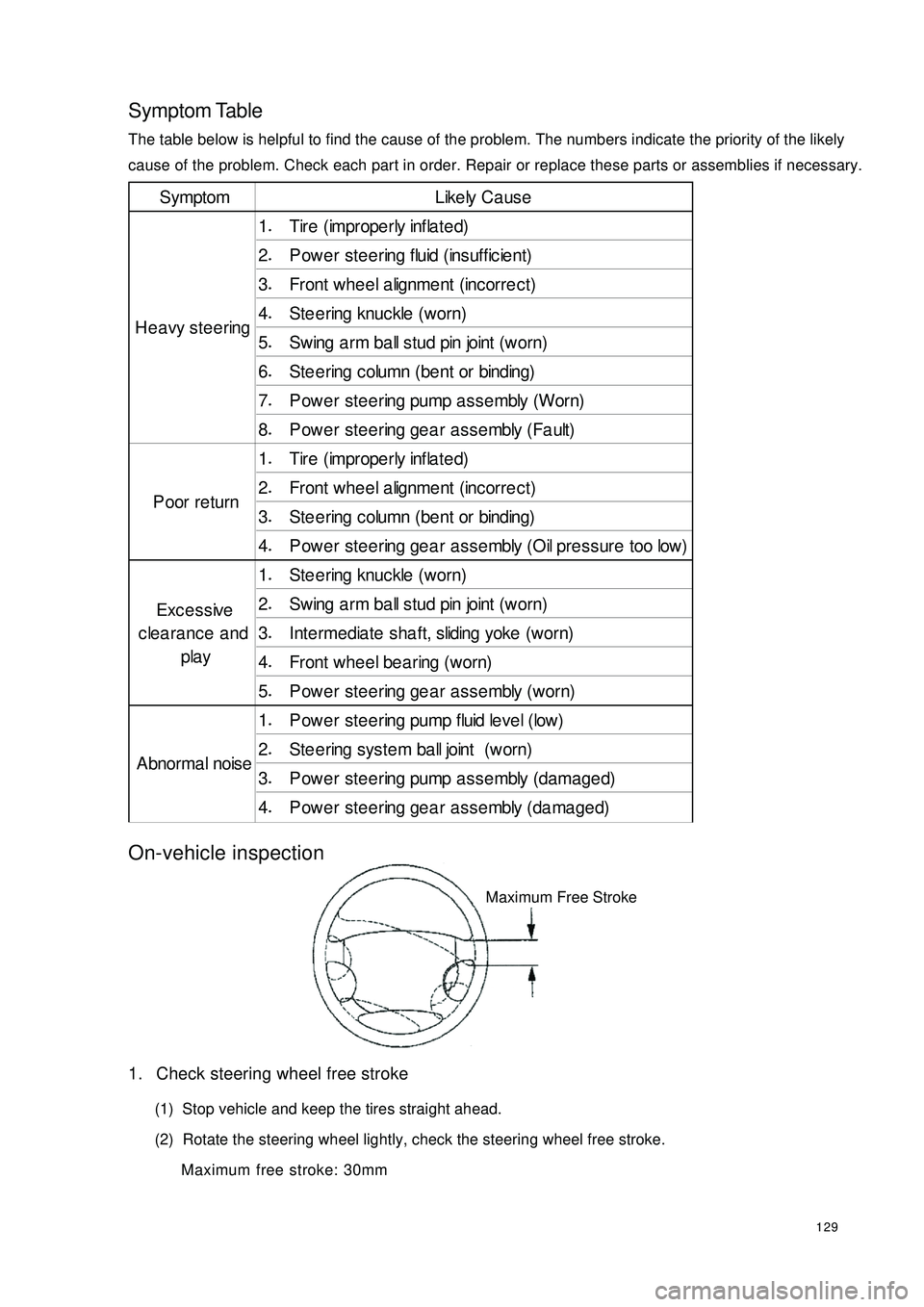
129Symptom TableThe table below is helpful to find the cause of the problem. The numbers indicate the priority of the likely
cause of the problem. Check each part in order. Repair or replace these parts or assemblies if necessary.On-vehicle inspection1. Check steering wheel free stroke
(1) Stop vehicle and keep the tires straight ahead.
(2) Rotate the steering wheel lightly, check the steering wheel free stroke.
Maximum free stroke: 30mmSymptom Like ly Ca us e
1.
Tire (imprope rly infla te d)
2.
P owe r ste ering fluid (insuffic ie nt)
3.
Front whe e l a lignme nt (inc orre c t)
4.
Ste e ring knuckle (worn)
5.
Swing a rm ba ll stud pin joint (worn)
6.
St e e r ing c olumn ( be nt or binding)
7.
P owe r ste ering pump a ssembly (Worn)
8.
Power steering gear assembly (Fault)
1.
Tire (imprope rly infla te d)
2.
Front whe e l a lignme nt (inc orre c t)
3.
St e e r ing c olumn ( be nt or binding)
4.
Power steering gear assembly (Oil pressure too low)
1.
Ste e ring knuckle (worn)
2.
Swing a rm ba ll stud pin joint (worn)
3.
Inte rmediate sha ft, sliding yoke (worn)
4.
Front whe e l be a ring (w orn)
5.
P owe r ste ering ge a r asse mbly (worn)
1.
P owe r ste ering pump fluid leve l (low)
2.
St e e r ing s ys t e m ba ll joint ( w or n)
3.
Power steering pump assembly (damaged)
4.
Power steering gear assembly (damaged) He avy ste eringPoor returnExcessive
clearance and
play
A bnor ma l nois eMaximum Free Stroke
Page 142 of 392
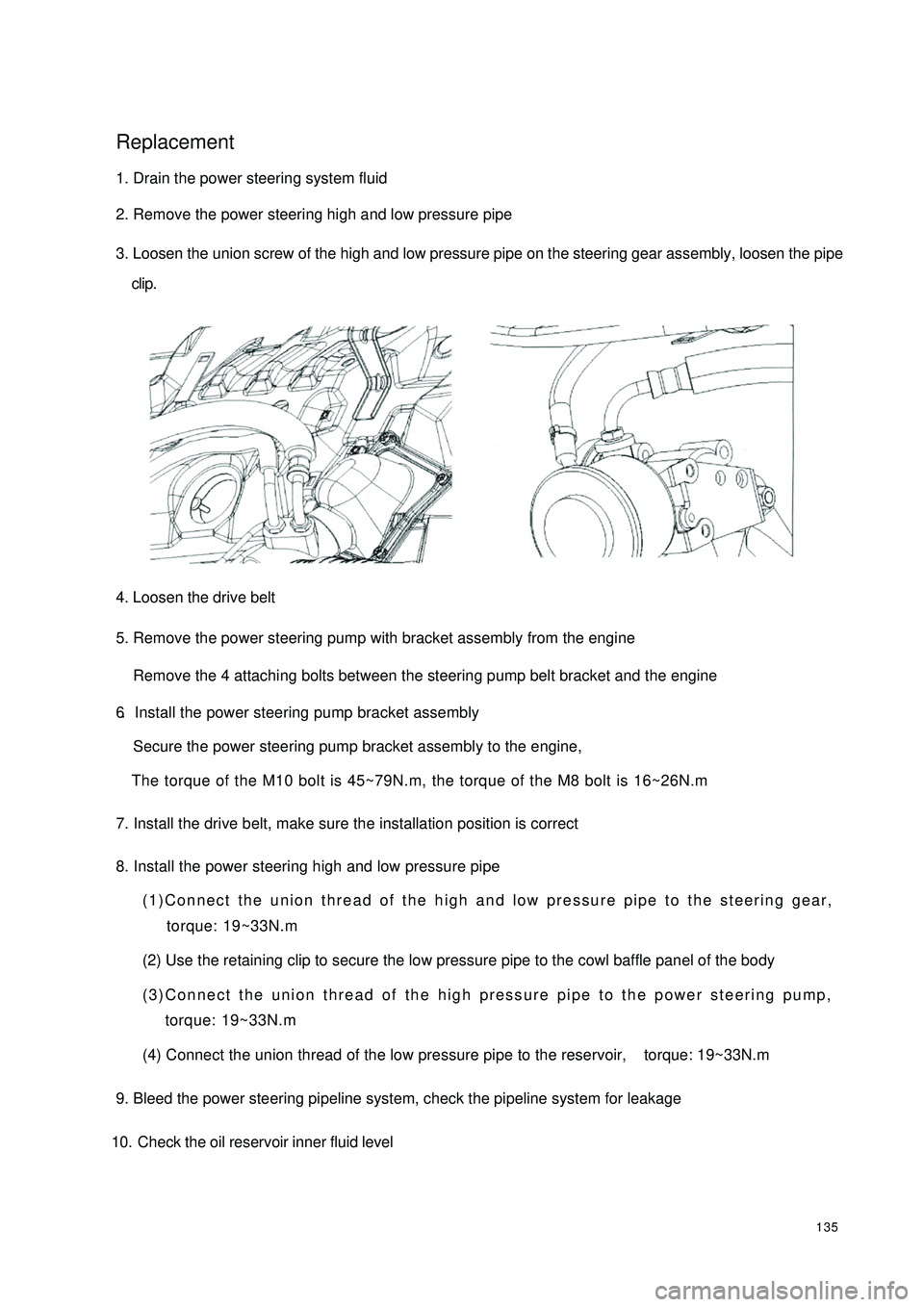
135Replacement1. Drain the power steering system fluid
2. Remove the power steering high and low pressure pipe
3. Loosen the union screw of the high and low pressure pipe on the steering gear assembly, loosen the pipe
clip.
4. Loosen the drive belt
5. Remove the power steering pump with bracket assembly from the engine
Remove the 4 attaching bolts between the steering pump belt bracket and the engine6.Install the power steering pump bracket assemblySecure the power steering pump bracket assembly to the engine,
The torque of the M10 bolt is 45~79N.m, the torque of the M8 bolt is 16~26N.m7. Install the drive belt, make sure the installation position is correct
8. Install the power steering high and low pressure pipe(1)Connect the union thread of the high and low pressure pipe to the steering gear,
torque: 19~33N.m
(2) Use the retaining clip to secure the low pressure pipe to the cowl baffle panel of the body
(3)Connect the union thread of the high pressure pipe to the power steering pump,
torque: 19~33N.m
(4) Connect the union thread of the low pressure pipe to the reservoir, torque: 19~33N.m
9. Bleed the power steering pipeline system, check the pipeline system for leakage
10. Check the oil reservoir inner fluid level