check oil GEELY FC 2008 Service Manual
[x] Cancel search | Manufacturer: GEELY, Model Year: 2008, Model line: FC, Model: GEELY FC 2008Pages: 419, PDF Size: 13.87 MB
Page 133 of 419
 Assemble lower ball joint on lower suspension arm with the
bolts and screw caps.
Torque: 142 ± 10 N
⋅ ⋅⋅ GEELY FC 2008 Service Manual Drive shaft--Front drive shaft35. Assemble left lower control arm assembly [64000091](a) Assemble lower ball joint on lower suspension arm with the
bolts and screw caps.
Torque: 142 ± 10 N
⋅ ⋅⋅](/img/58/57161/w960_57161-132.png)
Drive shaft--Front drive shaft35. Assemble left lower control arm assembly [64000091](a) Assemble lower ball joint on lower suspension arm with the
bolts and screw caps.
Torque: 142 ± 10 N
⋅ ⋅⋅ ⋅
⋅m36. Assemble left transversal lever assembly.(a) Assemble transversal lever terminal to steering knuckle with
screw cap.
Torque: 49 ± 5 N
⋅ ⋅⋅ ⋅
⋅m
(b) Assemble new cotter pin.
Note: if hole position of cotter pin could not make a
line, lock the screw cap for 60.37. Assemble speed sensor assembly of left front
wheels (equipping with ABS) [67000020](a) Assemble speed sensor absorber with bolts.
Torque: 49 ± 5 N
⋅ ⋅⋅ ⋅
⋅m
(b) Assemble speed sensor on the steering knuckle with bolts.
Torque: 8 N
⋅ ⋅⋅ ⋅
⋅m
Note: zDo not damage speed sensor. zPrevent it from contacting with sundries. zWhen assembling the sensor, the wiring harness
of sensor could not bend.38. Assemble fixing nuts of drive shaft [68000083](a) Assemble fixing nuts.
Torque: 216 ± 15 N
⋅ ⋅⋅ ⋅
⋅m
(b) Use chisel and hammer to knock the fixing nuts concave
and fix them.39. Assemble front wheels.Torque: 103 ± 10 N
⋅ ⋅⋅ ⋅
⋅m40. Add the oil in gearbox.
41. Check and adjust the oil in gearbox.
42. Check and adjust wheel alignment (referring to page
87)
43. Check the ABS speed sensor (equipping with ABS).
44. Test on road.
122
Page 137 of 419
 Assemble lower ball head and locking nut.
Torque: 103
± ±± ±
± 10 N
⋅ ⋅⋅ ⋅
⋅m
(b) Assemble new cotter pin.
GEELY FC 2008 Service Manual 18. Assemble left front lower control arm ball head as-
sembly [64000093](a) Assemble lower ball head and locking nut.
Torque: 103
± ±± ±
± 10 N
⋅ ⋅⋅ ⋅
⋅m
(b) Assemble new cotter pin.](/img/58/57161/w960_57161-136.png)
18. Assemble left front lower control arm ball head as-
sembly [64000093](a) Assemble lower ball head and locking nut.
Torque: 103
± ±± ±
± 10 N
⋅ ⋅⋅ ⋅
⋅m
(b) Assemble new cotter pin.
If hole position of cotter pin could not make a line, lock the
screw cap for 60again.19. Assemble left front shaft hub assembly(a) Assemble two bolts and nuts, and assemble shaft hub as-
sembly on absorber.
Torque: 153
± ±± ±
± 10 N
⋅ ⋅⋅ ⋅
⋅m
Note: when the bolts and nuts should be used again,
spread engine oil on the thread of nuts.
(b) Push the front shaft hub assembly to the outside of
automobile, then assemble transmission shaft assembly
in the gear slot of front shaft hub assembly.
Note:
Front shaft assembly could not be pushed to outside
too much. zDo not damage the exterior joint dustproof cover of
drive shaft. zDo not damage the stator of speed sensor.20. Assemble left lower control arm assembly
[64000091]Assemble lower control arm and ball head with two nuts and
bolts.
Torque: 142
± ±± ±
± 10 N
⋅ ⋅⋅ ⋅
⋅m21. Assemble left transversal lever assembly(a) Connect transversal lever to steering knuckle.
(b) Assemble screw cap and new cotter pin.
Torque: 49
± ±± ±
± 5 N
⋅ ⋅⋅ ⋅
⋅m22. Assemble left front brake assembly [64000134]
23. Assemble front brake caliper assembly(a) Assemble brake caliper assemble on steering knuckle with
two bolts.
Torque: 106
± ±± ±
± 10 N
⋅ ⋅⋅ ⋅
⋅m24. Assemble fixing nuts of left front drive shaft
[64000083]Use torque wrench (30mm) to assemble new fixing nuts.25. Disassemble left front brake branch pump assembly
26. Disassemble left front brake assembly [64000134]
27. Check the axial clearance of bearingDrive shaft--Left front shaft hub assembly126
Page 144 of 419
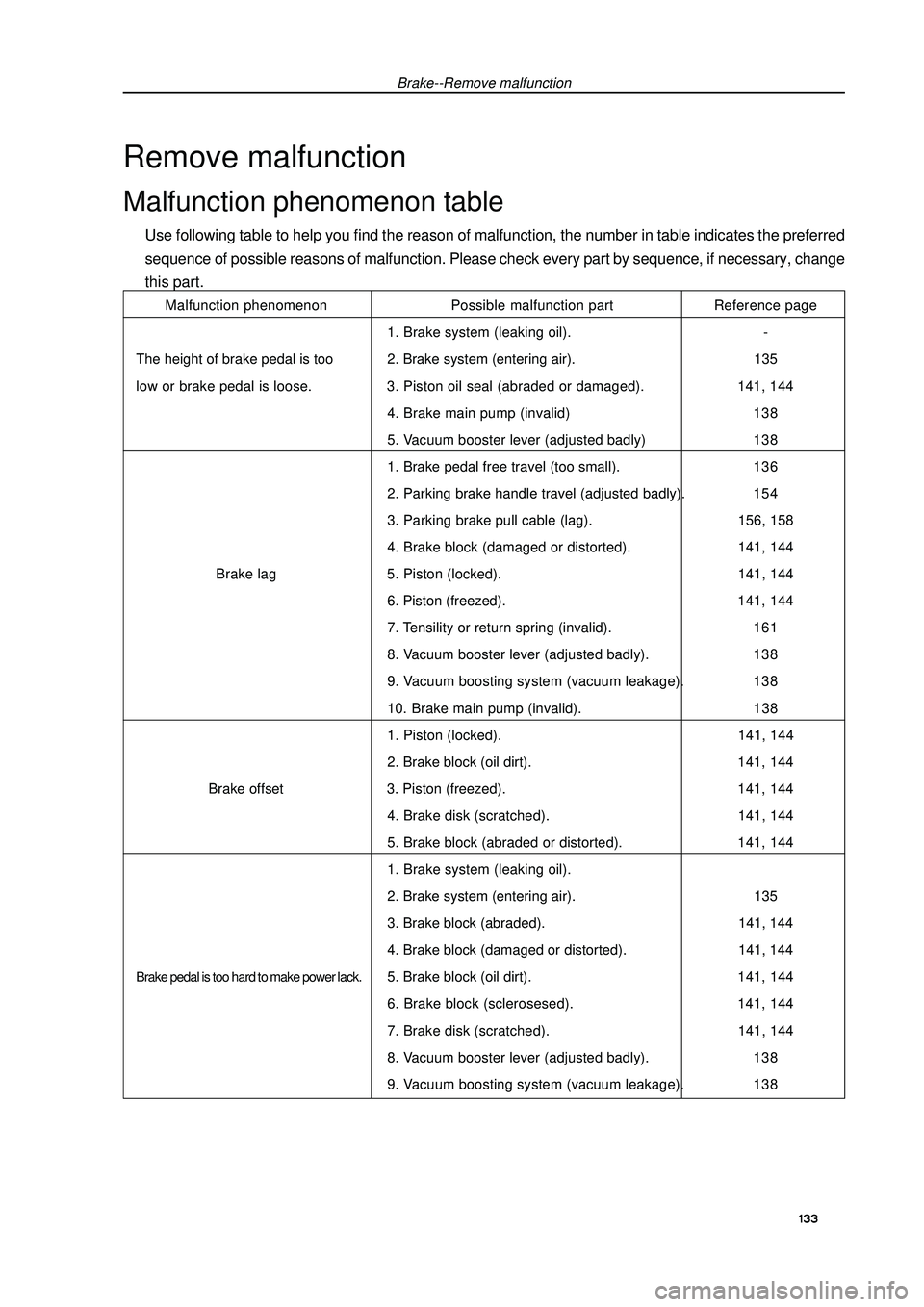
Brake--Remove malfunctionRemove malfunctionMalfunction phenomenon tableUse following table to help you find the reason of malfunction, the number in table indicates the preferred
sequence of possible reasons of malfunction. Please check every part by sequence, if necessary, change
this part.Malfunction phenomenon Possible malfunction part Reference page
1. Brake system (leaking oil). -
The height of brake pedal is too 2. Brake system (entering air). 135
low or brake pedal is loose. 3. Piston oil seal (abraded or damaged). 141, 144
4. Brake main pump (invalid) 138
5. Vacuum booster lever (adjusted badly) 138
1. Brake pedal free travel (too small). 136
2. Parking brake handle travel (adjusted badly). 154
3. Parking brake pull cable (lag). 156, 158
4. Brake block (damaged or distorted). 141, 144
Brake lag 5. Piston (locked). 141, 144
6. Piston (freezed).141, 144
7. Tensility or return spring (invalid). 161
8. Vacuum booster lever (adjusted badly). 138
9. Vacuum boosting system (vacuum leakage). 138
10. Brake main pump (invalid). 138
1. Piston (locked). 141, 144
2. Brake block (oil dirt).141, 144
Brake offset 3. Piston (freezed).141, 144
4. Brake disk (scratched). 141, 144
5. Brake block (abraded or distorted).141, 144
1. Brake system (leaking oil).
2. Brake system (entering air). 135
3. Brake block (abraded). 141, 144
4. Brake block (damaged or distorted). 141, 144Brake pedal is too hard to make power lack.5. Brake block (oil dirt).141, 144
6. Brake block (sclerosesed). 141, 144
7. Brake disk (scratched). 141, 144
8. Vacuum booster lever (adjusted badly). 138
9. Vacuum boosting system (vacuum leakage). 138133
Page 146 of 419
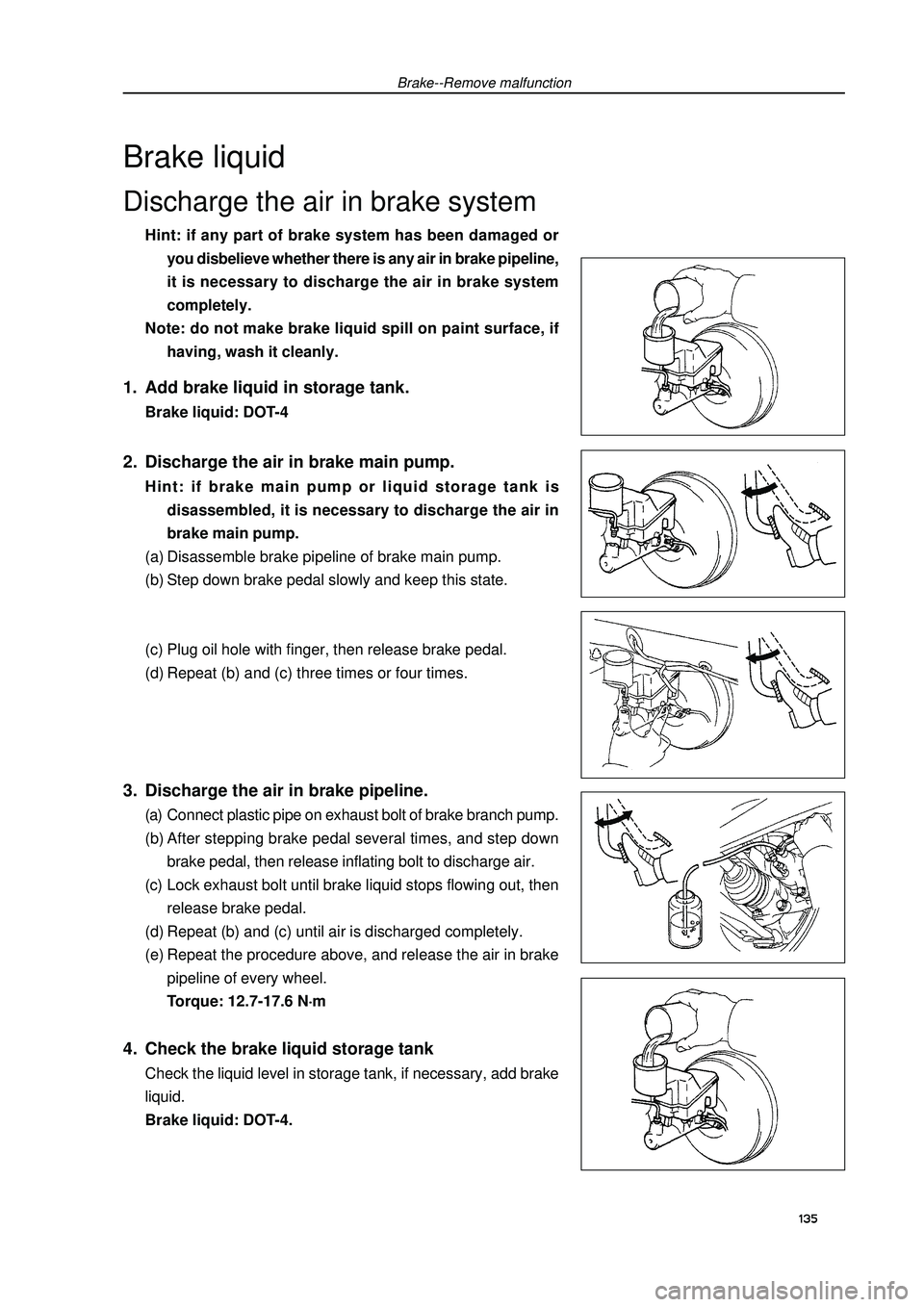
Brake--Remove malfunction1. Add brake liquid in storage tank.Brake liquid: DOT-42. Discharge the air in brake main pump.Hint: if brake main pump or liquid storage tank is
disassembled, it is necessary to discharge the air in
brake main pump.
(a) Disassemble brake pipeline of brake main pump.
(b) Step down brake pedal slowly and keep this state.
(c) Plug oil hole with finger, then release brake pedal.
(d) Repeat (b) and (c) three times or four times.3. Discharge the air in brake pipeline.(a) Connect plastic pipe on exhaust bolt of brake branch pump.
(b) After stepping brake pedal several times, and step down
brake pedal, then release inflating bolt to discharge air.
(c) Lock exhaust bolt until brake liquid stops flowing out, then
release brake pedal.
(d) Repeat (b) and (c) until air is discharged completely.
(e) Repeat the procedure above, and release the air in brake
pipeline of every wheel.
Torque: 12.7-17.6 N
⋅ ⋅⋅ ⋅
⋅m4. Check the brake liquid storage tankCheck the liquid level in storage tank, if necessary, add brake
liquid.
Brake liquid: DOT-4.Brake liquidDischarge the air in brake systemHint: if any part of brake system has been damaged or
you disbelieve whether there is any air in brake pipeline,
it is necessary to discharge the air in brake system
completely.
Note: do not make brake liquid spill on paint surface, if
having, wash it cleanly.135
Page 153 of 419
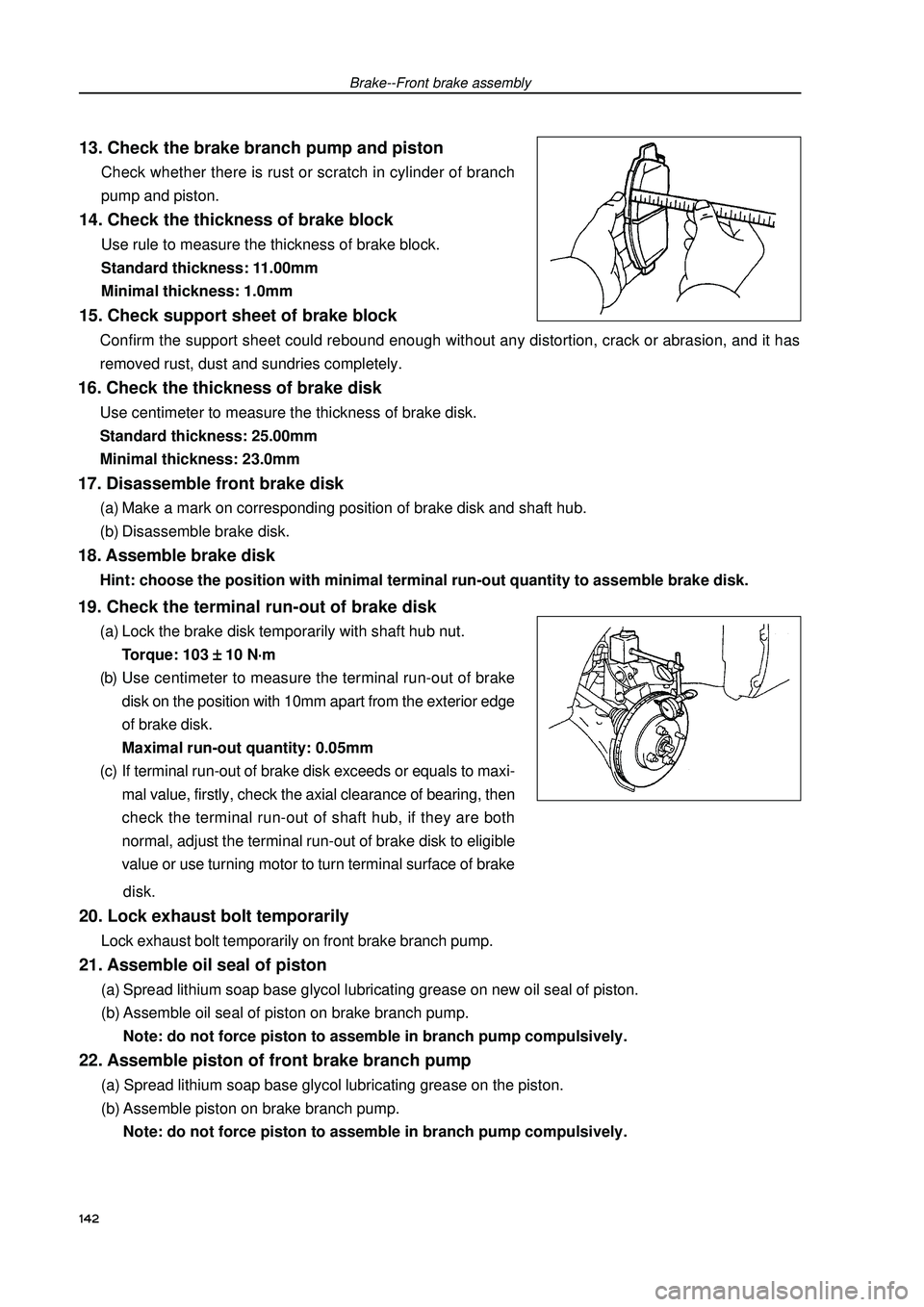
Brake--Front brake assembly13. Check the brake branch pump and pistonCheck whether there is rust or scratch in cylinder of branch
pump and piston.14. Check the thickness of brake blockUse rule to measure the thickness of brake block.
Standard thickness: 11.00mm
Minimal thickness: 1.0mm15. Check support sheet of brake block
142Confirm the support sheet could rebound enough without any distortion, crack or abrasion, and it has
removed rust, dust and sundries completely.16. Check the thickness of brake diskUse centimeter to measure the thickness of brake disk.
Standard thickness: 25.00mm
Minimal thickness: 23.0mm17. Disassemble front brake disk(a) Make a mark on corresponding position of brake disk and shaft hub.
(b) Disassemble brake disk.18. Assemble brake diskHint: choose the position with minimal terminal run-out quantity to assemble brake disk.19. Check the terminal run-out of brake disk(a) Lock the brake disk temporarily with shaft hub nut.
Torque: 103
± ± ± ±
± 10 N
⋅ ⋅⋅ ⋅
⋅m
(b) Use centimeter to measure the terminal run-out of brake
disk on the position with 10mm apart from the exterior edge
of brake disk.
Maximal run-out quantity: 0.05mm
(c) If terminal run-out of brake disk exceeds or equals to maxi-
mal value, firstly, check the axial clearance of bearing, then
check the terminal run-out of shaft hub, if they are both
normal, adjust the terminal run-out of brake disk to eligible
value or use turning motor to turn terminal surface of brake
disk.20. Lock exhaust bolt temporarilyLock exhaust bolt temporarily on front brake branch pump.21. Assemble oil seal of piston(a) Spread lithium soap base glycol lubricating grease on new oil seal of piston.
(b) Assemble oil seal of piston on brake branch pump.
Note: do not force piston to assemble in branch pump compulsively.22. Assemble piston of front brake branch pump(a) Spread lithium soap base glycol lubricating grease on the piston.
(b) Assemble piston on brake branch pump.
Note: do not force piston to assemble in branch pump compulsively.
Page 154 of 419
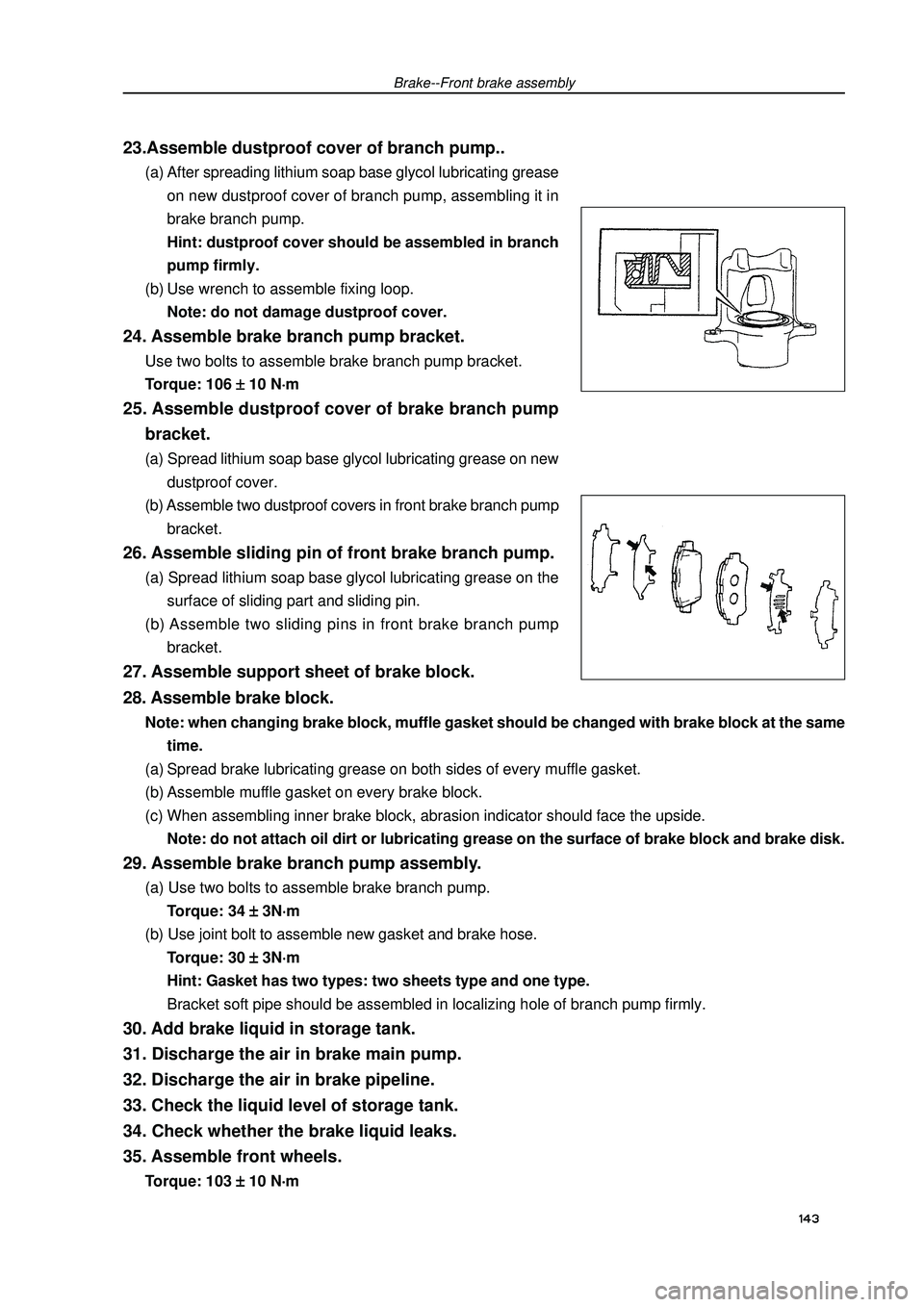
Brake--Front brake assembly23.Assemble dustproof cover of branch pump..(a) After spreading lithium soap base glycol lubricating grease
on new dustproof cover of branch pump, assembling it in
brake branch pump.
Hint: dustproof cover should be assembled in branch
pump firmly.
(b) Use wrench to assemble fixing loop.
Note: do not damage dustproof cover.24. Assemble brake branch pump bracket.Use two bolts to assemble brake branch pump bracket.
Torque: 106
± ±± ±
± 10 N
⋅ ⋅⋅ ⋅
⋅m25. Assemble dustproof cover of brake branch pump
bracket.(a) Spread lithium soap base glycol lubricating grease on new
dustproof cover.
(b) Assemble two dustproof covers in front brake branch pump
bracket.26. Assemble sliding pin of front brake branch pump.(a) Spread lithium soap base glycol lubricating grease on the
surface of sliding part and sliding pin.
(b) Assemble two sliding pins in front brake branch pump
bracket.27. Assemble support sheet of brake block.143 28. Assemble brake block.Note: when changing brake block, muffle gasket should be changed with brake block at the same
time.
(a) Spread brake lubricating grease on both sides of every muffle gasket.
(b) Assemble muffle gasket on every brake block.
(c) When assembling inner brake block, abrasion indicator should face the upside.
Note: do not attach oil dirt or lubricating grease on the surface of brake block and brake disk.29. Assemble brake branch pump assembly.(a) Use two bolts to assemble brake branch pump.
Torque: 34
± ±± ±
± 3N
⋅ ⋅⋅ ⋅
⋅m
(b) Use joint bolt to assemble new gasket and brake hose.
Torque: 30
± ±± ±
± 3N
⋅ ⋅⋅ ⋅
⋅m
Hint: Gasket has two types: two sheets type and one type.
Bracket soft pipe should be assembled in localizing hole of branch pump firmly.30. Add brake liquid in storage tank.
31. Discharge the air in brake main pump.
32. Discharge the air in brake pipeline.
33. Check the liquid level of storage tank.
34. Check whether the brake liquid leaks.
35. Assemble front wheels.Torque: 103
± ±± ±
± 10 N
⋅ ⋅⋅ ⋅
⋅m
Page 156 of 419
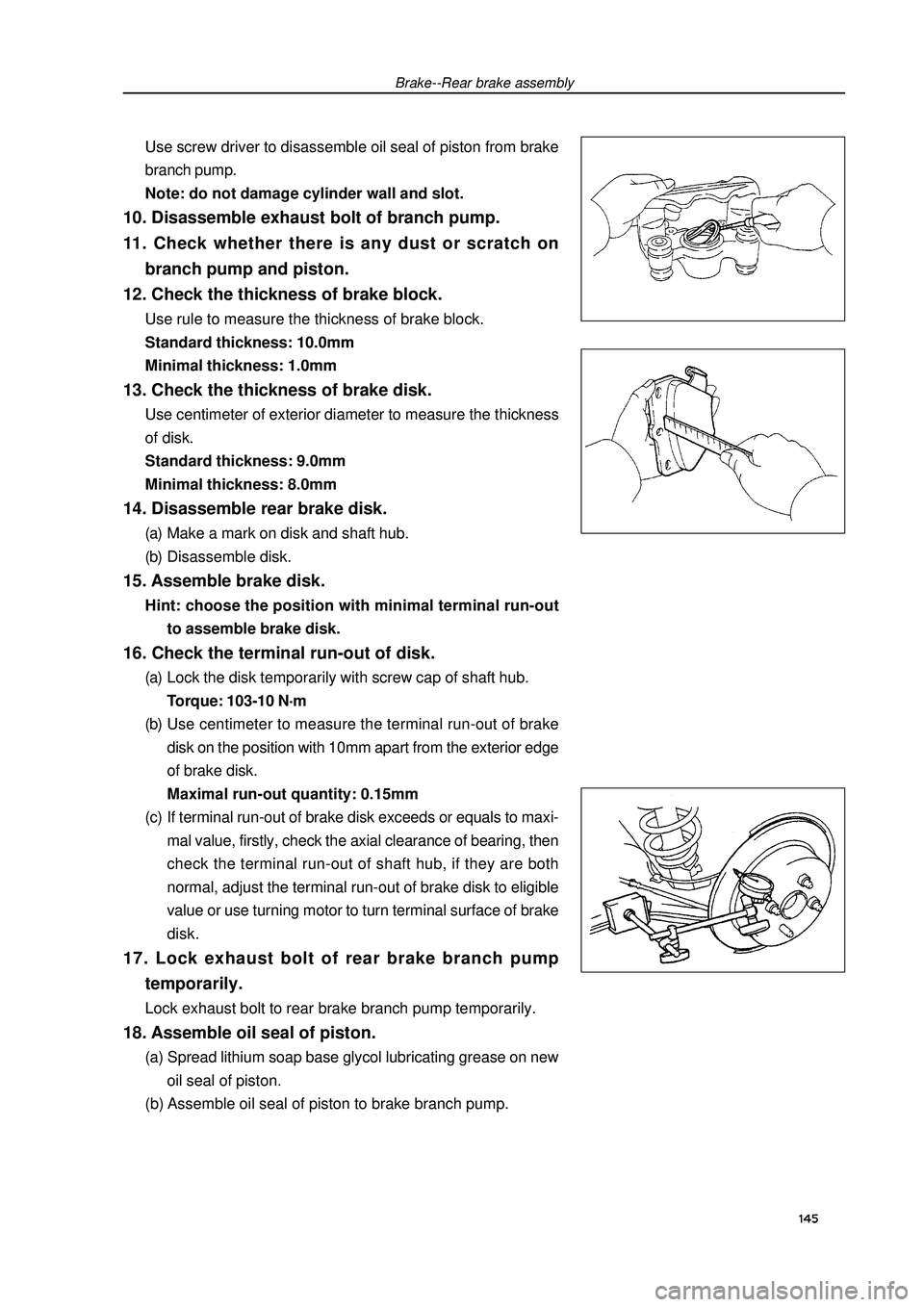
Brake--Rear brake assemblyUse screw driver to disassemble oil seal of piston from brake
branch pump.
Note: do not damage cylinder wall and slot.10. Disassemble exhaust bolt of branch pump.
11. Check whether there is any dust or scratch on
branch pump and piston.
12. Check the thickness of brake block.Use rule to measure the thickness of brake block.
Standard thickness: 10.0mm
Minimal thickness: 1.0mm13. Check the thickness of brake disk.Use centimeter of exterior diameter to measure the thickness
of disk.
Standard thickness: 9.0mm
Minimal thickness: 8.0mm14. Disassemble rear brake disk.(a) Make a mark on disk and shaft hub.
(b) Disassemble disk.15. Assemble brake disk.Hint: choose the position with minimal terminal run-out
to assemble brake disk.16. Check the terminal run-out of disk.(a) Lock the disk temporarily with screw cap of shaft hub.
Torque: 103-10 N
⋅ ⋅⋅ ⋅
⋅m
(b) Use centimeter to measure the terminal run-out of brake
disk on the position with 10mm apart from the exterior edge
of brake disk.
Maximal run-out quantity: 0.15mm
(c) If terminal run-out of brake disk exceeds or equals to maxi-
mal value, firstly, check the axial clearance of bearing, then
check the terminal run-out of shaft hub, if they are both
normal, adjust the terminal run-out of brake disk to eligible
value or use turning motor to turn terminal surface of brake
disk.17. Lock exhaust bolt of rear brake branch pump
temporarily.Lock exhaust bolt to rear brake branch pump temporarily.18. Assemble oil seal of piston.(a) Spread lithium soap base glycol lubricating grease on new
oil seal of piston.
(b) Assemble oil seal of piston to brake branch pump.145
Page 158 of 419
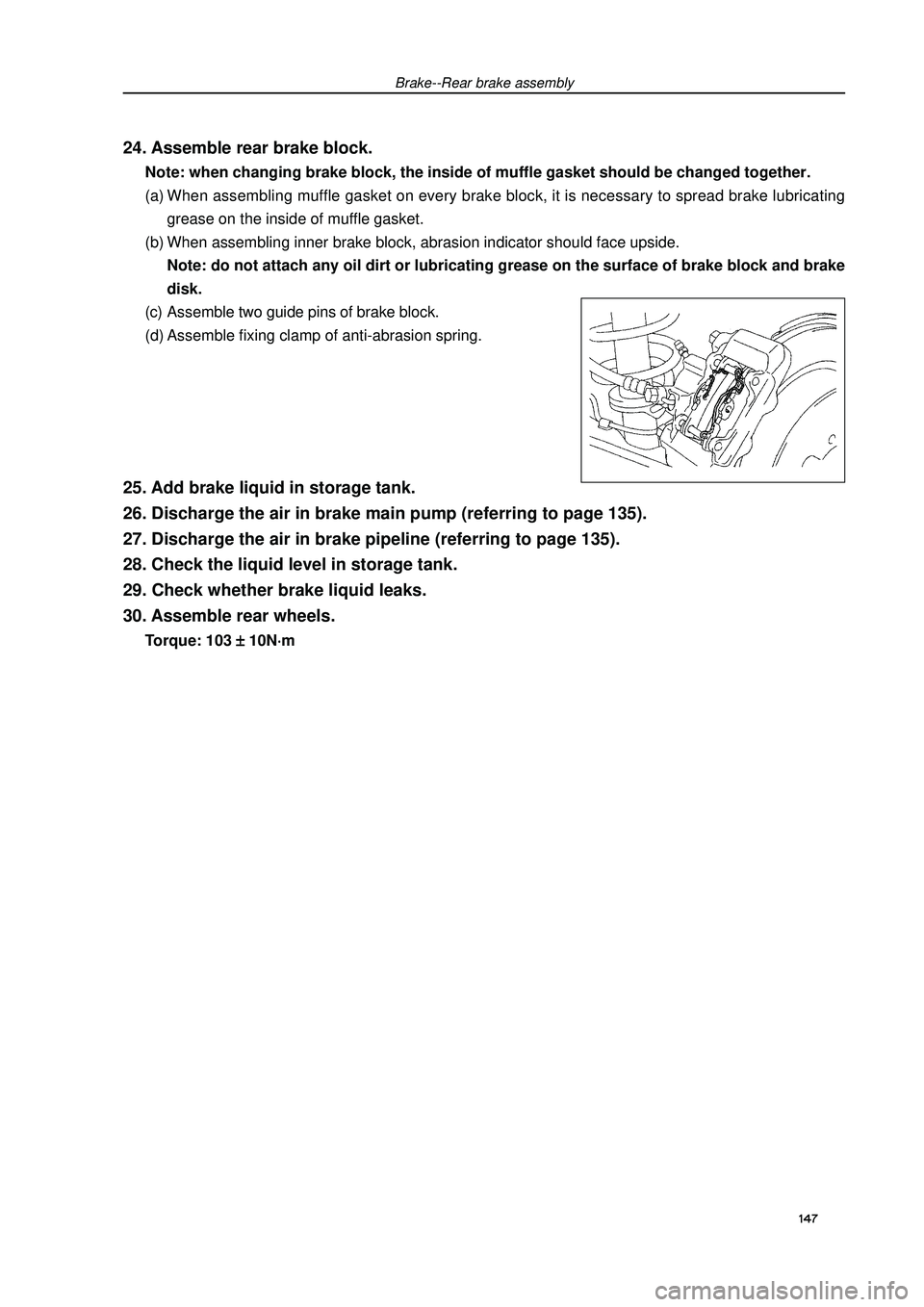
Brake--Rear brake assembly24. Assemble rear brake block.Note: when changing brake block, the inside of muffle gasket should be changed together.
(a) When assembling muffle gasket on every brake block, it is necessary to spread brake lubricating
grease on the inside of muffle gasket.
(b) When assembling inner brake block, abrasion indicator should face upside.
Note: do not attach any oil dirt or lubricating grease on the surface of brake block and brake
disk.
(c) Assemble two guide pins of brake block.
(d) Assemble fixing clamp of anti-abrasion spring.25. Add brake liquid in storage tank.
26. Discharge the air in brake main pump (referring to page 135).
27. Discharge the air in brake pipeline (referring to page 135).
28. Check the liquid level in storage tank.
29. Check whether brake liquid leaks.
30. Assemble rear wheels.Torque: 103
± ±± ±
± 10N
⋅ ⋅⋅ ⋅
⋅m147
Page 161 of 419
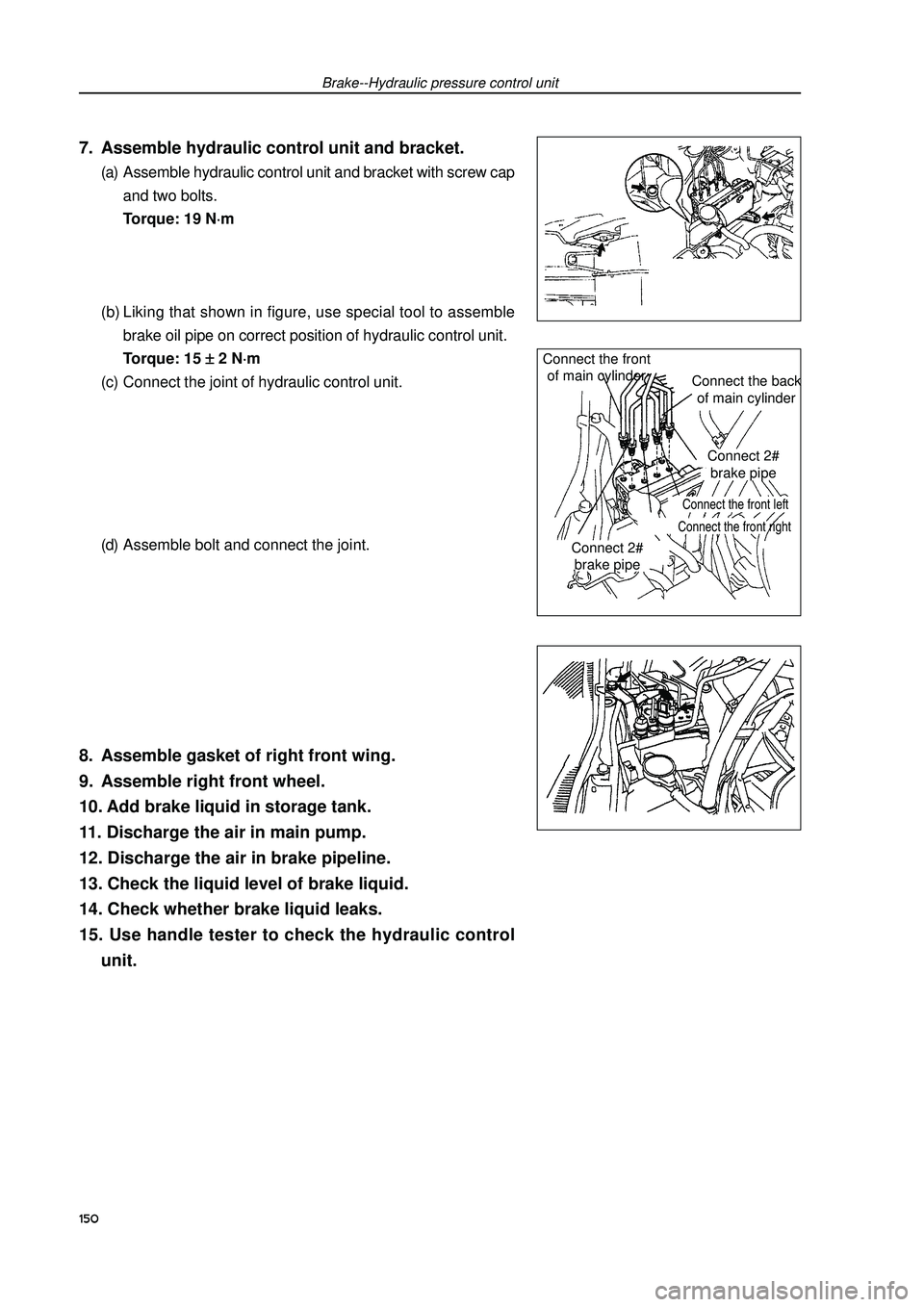
Brake--Hydraulic pressure control unit7. Assemble hydraulic control unit and bracket.(a) Assemble hydraulic control unit and bracket with screw cap
and two bolts.
Torque: 19 N
⋅ ⋅⋅ ⋅
⋅m
(b) Liking that shown in figure, use special tool to assemble
brake oil pipe on correct position of hydraulic control unit.
Torque: 15
± ±± ±
± 2 N
⋅ ⋅⋅ ⋅
⋅m
(c) Connect the joint of hydraulic control unit.
(d) Assemble bolt and connect the joint.8. Assemble gasket of right front wing.
9. Assemble right front wheel.
10. Add brake liquid in storage tank.
11. Discharge the air in main pump.
12. Discharge the air in brake pipeline.
13. Check the liquid level of brake liquid.
14. Check whether brake liquid leaks.
15. Use handle tester to check the hydraulic control
unit.150Connect the front
of main cylinder
Connect the back
of main cylinder
Connect 2#
brake pipe
Connect the front left
Connect 2#
brake pipeConnect the front right
Page 175 of 419

18. Check the assembly of parking brake system.
Check every part after assembly.
Note: do not attach oil dirt or lubricating grease on contacting surface between shoe friction
sheet and brake drum.
Parking brake--Parking brake assembly
19. Assemble the brake
20. Adjust the clearance of parking brake shoe.
(a) Lock screw cap of shaft hub temporarily.
(b) Disassemble hole plug, then use screw driver to turn the
adjustor until brake drum is locked by shoe.
(c) Return the adjustor for 8 gears.
(d) Check whether shoe has lag.
(e) Assemble hole plug.
21. Assemble rear disk type brake branch pump assem-
bly (LH).
22. Assemble rear wheels.
Torque: 103
± ±± ±
± 10N
⋅ ⋅⋅ ⋅
⋅m
23. Check the travel of parking brake drag lever.
24. Adjust the travel of parking brake drag lever.
Left
Right
Front
Front
Increase the
clearance
Decrease the
clearance
164