check engine HONDA CIVIC 2003 7.G Workshop Manual
[x] Cancel search | Manufacturer: HONDA, Model Year: 2003, Model line: CIVIC, Model: HONDA CIVIC 2003 7.GPages: 1139, PDF Size: 28.19 MB
Page 367 of 1139
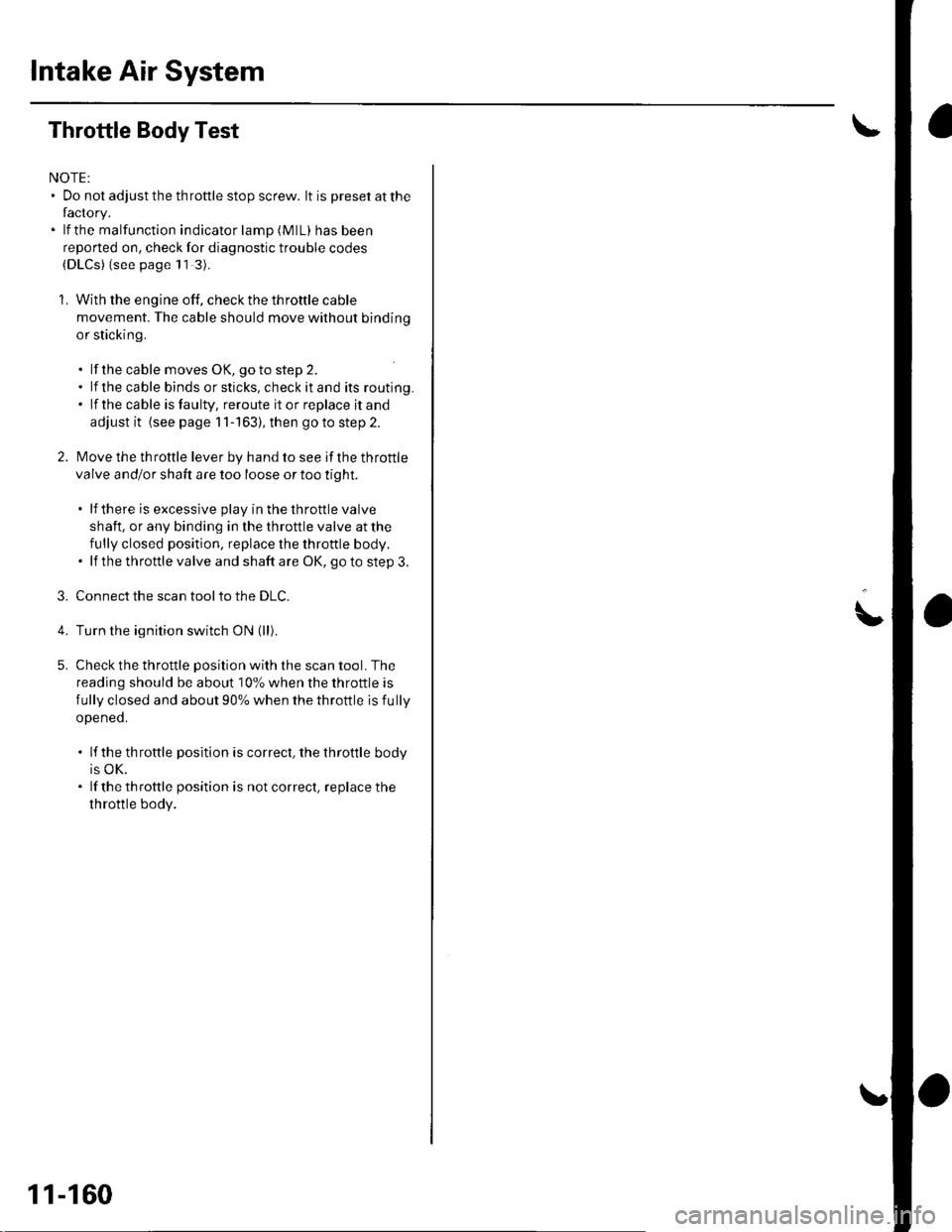
Intake Air System
Throttle Body Test
NOTE:. Do not adjust the throttle stop screw. lt is preset at the
factory.. lf the malfunction indicator lamp (MlL) has been
reported on, check for diagnostic trouble codes(DLCS) (see page 11 3).
1. With the engine off, check the throttle cable
movement. The cable should move without binding
or sticking.
. lf lhe cable moves OK, goto step 2.. lf the cable binds or sticks, check it and its routing.. lf the cable isfaulty, reroute itor replace itand
adjust it (see page 11-163), then go to step 2.
2. l\4ove the throttle lever by hand to see if the throftle
valve and/or shaft are too loose or too tight.
. lf there is excessive play in the throttle valve
shaft, or any binding in the throttle valve at the
fully closed position, replace the throttle body.. lf thethrottlevalve and shaft are OK, goto step3.
3. Connect the scan toolto the DLC.
Turn the ignition switch ON (ll).
Check the throttle position with the scan tool. The
reading should be about 10% when the throttle is
fully closed and about 90% when the throttle is fully
openeo.
. lf the throttle position is correct, the throttle body
is OK.. lf thethrottle position is notcorrect, replace the
throttle body.
5.
11-160
!
Page 368 of 1139

Intake Air Bypass GontrolThermalValve Test
Special Tools Required
Vacuum Pump/Gauge,0 30 in. Hg A973X-041-XXXXX
1. Stan the engine. Then let it idl€.
NOTE: The engine coolant temperature must be
below 149'F (65'C).
2. Remove the vacuum hose (A)from the intake air
duct, and connect a vacuum pump/gauge to the
nose.
3. Raise and lowerthe engine speed. and make sure
the vacuum gauge reading changes as the engine
speeo cnanges.
lf the vacuum reading does not change, check for
these problems:
. Misrouted, leaking, broken, or clogged intake air
bypass control system vacuum lines.. A cracked or damaged intake air bypass control
thermal valve.
4. Hold the engine at 3,000 rpm with no load (in
neutral) until the radiator fan comes on, then let it
id le.
5. Raise and lower the engine speed, and make sure
the vacuum gauge reading does not change as the
rpm cnanges.
lf the vacuum reading changes, check for these
proorems:
. l\4isrouted, leaking, broken, or clogged intake air
bypass control system vacuum lines.. A cracked or damaged intake air bypass control
thermal valve.
11-161
Page 371 of 1139
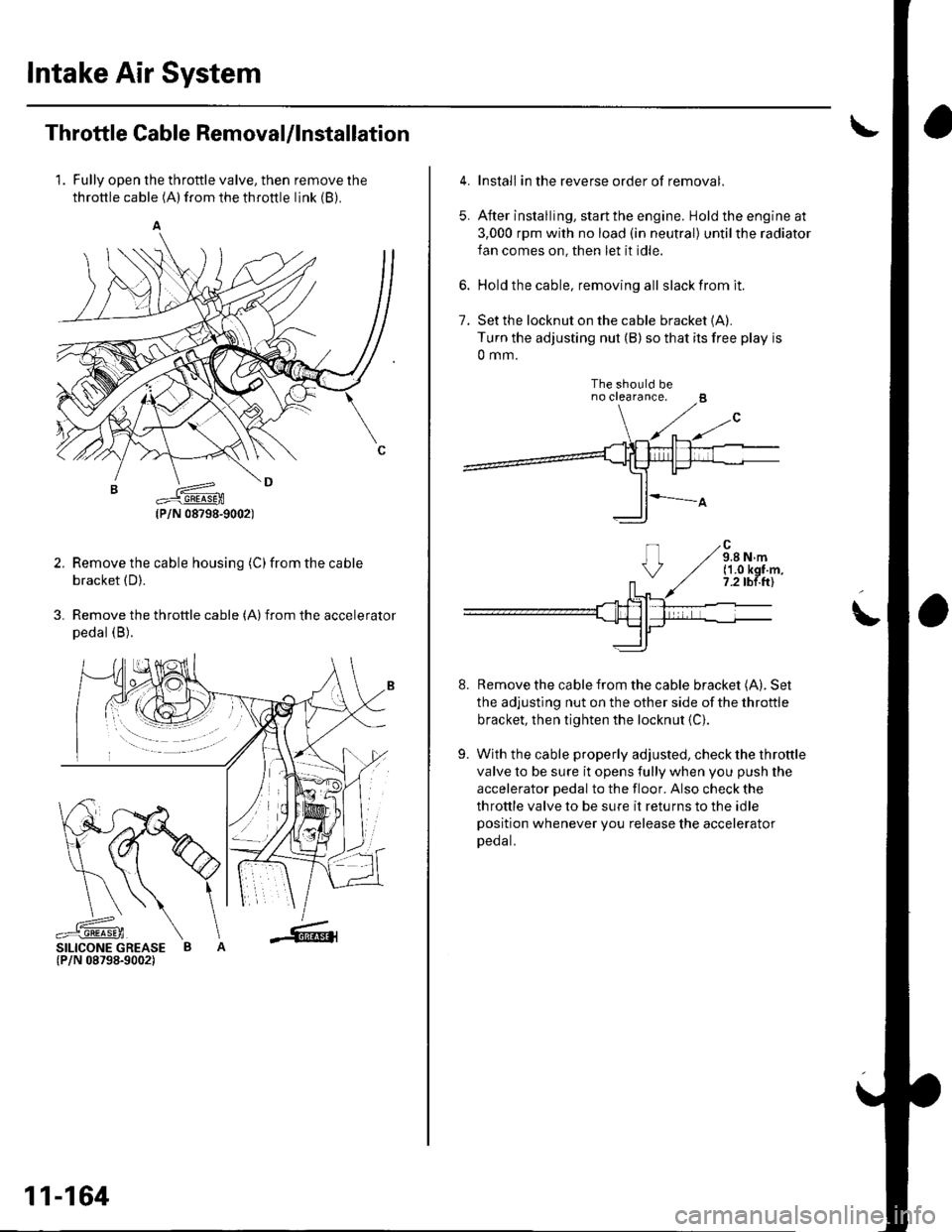
Intake Air System
Throttle Cable Removal/lnstallation
1. Fully open the throttle valve, then remove the
throttle cable (A) from the throttle link (B).
Remove the cable housing (C)from the cable
bracket (D).
Remove the throttle cable (A)from the accelerator
pedal (B).
2.
3.
SILICONE GREASE B(P/N 08798-9002)
(P/N 08?98-9002)
11-164
5.
Install in the reverse order of removal.
After installing, start the engine. Hold the engine at
3,000 rpm with no load (in neutral) untilthe radiator
fan comes on, then let it idle.
Hold the cable, removing all slack from it.
Set the locknut on the cable bracket {A).Turn the adjusting nut (B) so that its free play is
0 mm.
The should beno crearance.
Remove the cable from the cable bracket (A). Set
the adjusting nut on the other side of the throttle
bracket, then tighten the locknut {C}.
With the cable properly adjusted, check the throttle
valve to be sure it opens fully when you push the
accelerator pedal to the floor. Also check the
throttle valve to be sure it returns to the idle
position whenever you release the accelerator
Deoat.
7.
!
8.
9.
('1.0 kgf.m,7.2 tbf.ftl
Page 374 of 1139
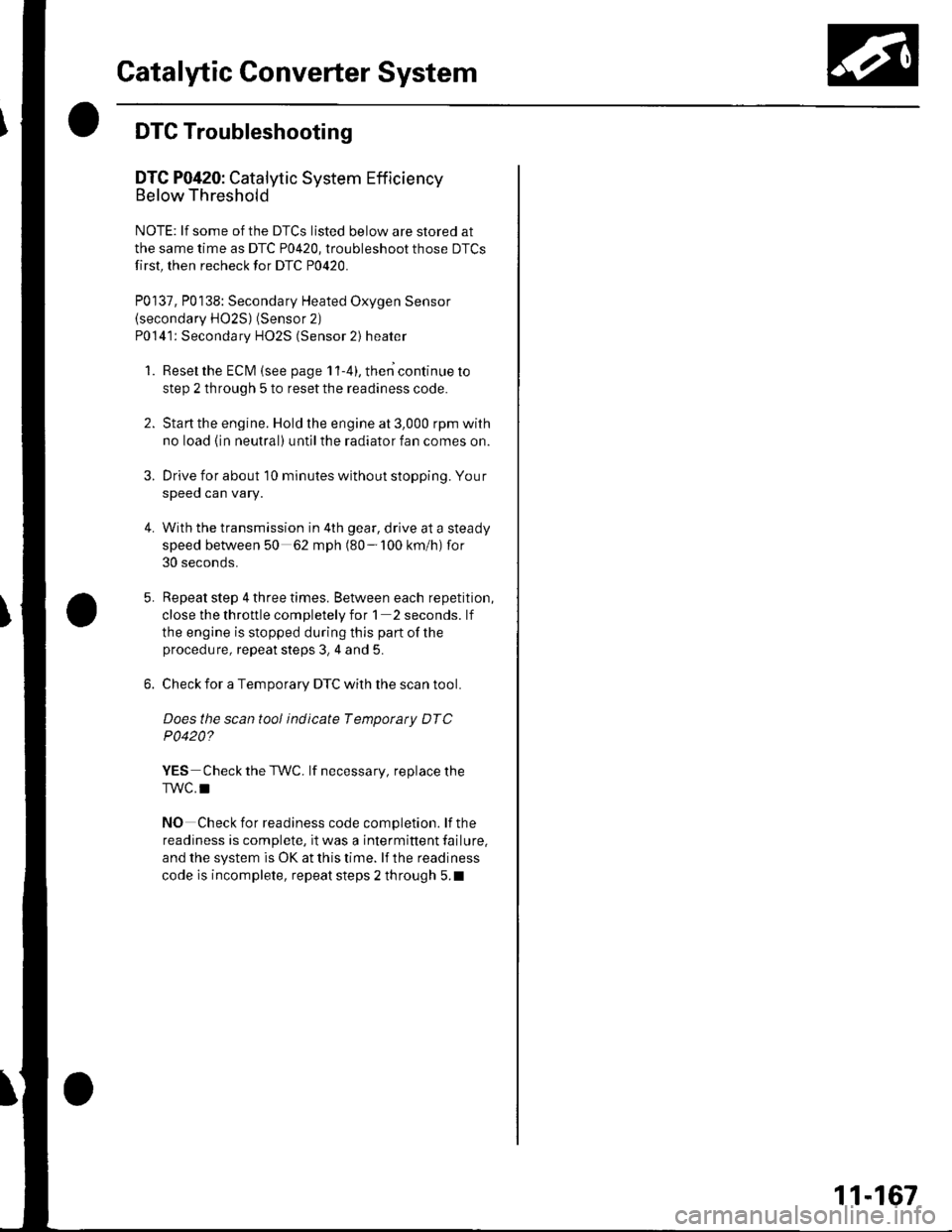
Catalytic Converter System
DTC Troubleshooting
DTC P0420: Catalytic System Efficiency
Below Threshold
NOTE: lf some of the DTCS listed below are stored at
the same time as DTC P0420, troubleshoot those DTCS
first, then recheck for DTC P0420.
P0137, P0138: Secondary Heated Oxygen Sensor(secondary HO2S) (Sensor 2)
P0141: Secondary HO2S (Sensor 2) heater
1. Reset the ECM {see page 1'l-4}, then continue to
step 2 through 5 to reset the readiness code.
2. Start the engine. Hold the engine at 3,000 rpm with
no load (in neutral) untilthe radiator fan comes on.
Drive for about l0 minutes without stopping. Your
speeo can vary.
With the transmission in 4th gear, drive at a steady
speed between 50 62 mph (80-'100 km/h) for
30 seconds.
Repeat step 4 three times. Between each repetition,
close the throttle completely for 1 2 seconds. lf
the engine is stopped during this part of the
procedure, repeat steps 3, 4 and 5.
Check for a Temporary DTC with the scan tool.
Does the scan tool indicate Temporaty DTC
P0420?
YES Check the TWC. lf necessary, replace the
TWC.I
NO Check for readiness code completion. lfthe
readiness is complete, it was a interminent failure,
and the system is OK at this time. lf the readiness
code is incomplete, repeat steps 2 through 5.1
4.
11-167
Page 375 of 1139
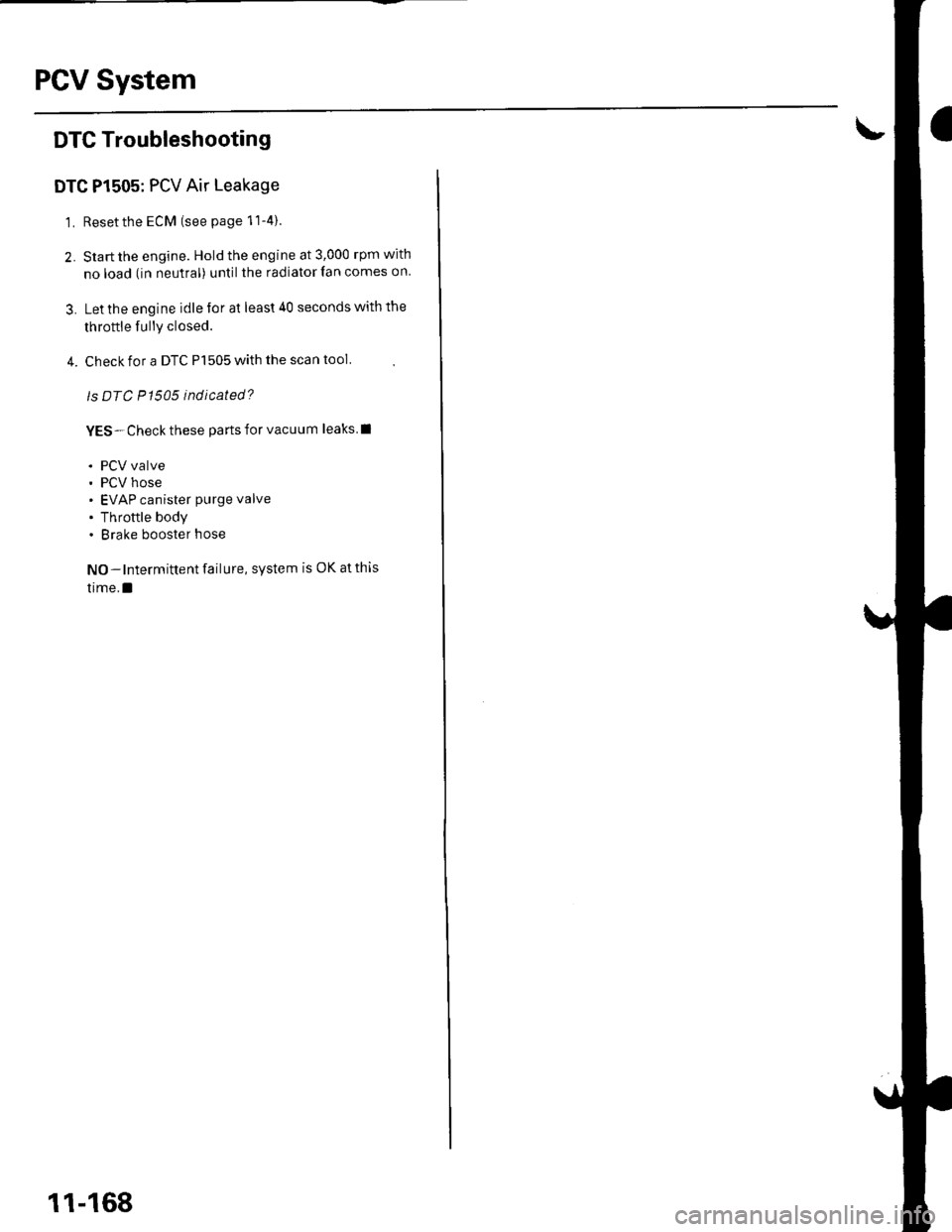
PCV System
DTC Troubleshooting
DTC P1505: PCV Air Leakage
1. Reset the ECM (see page 11-4).
2. Start the engine. Hold the engine at 3,000 rpm with
no load (in neutral) until the radiator fan comes on
3. Let the engine idle tor al least 40 seconds with the
throttle fully closed.
4. Check for a DTC P1505 with the scan tool
ls DTC P1505 indicated?
YES-Check these parts for vacuum leaks l
. PCV valve. PCV hose. EVAP canister purge valve
. Throttle body. Brake booster hose
NO - Intermittent failure, system is OK at this
time.l
11-168
Page 382 of 1139
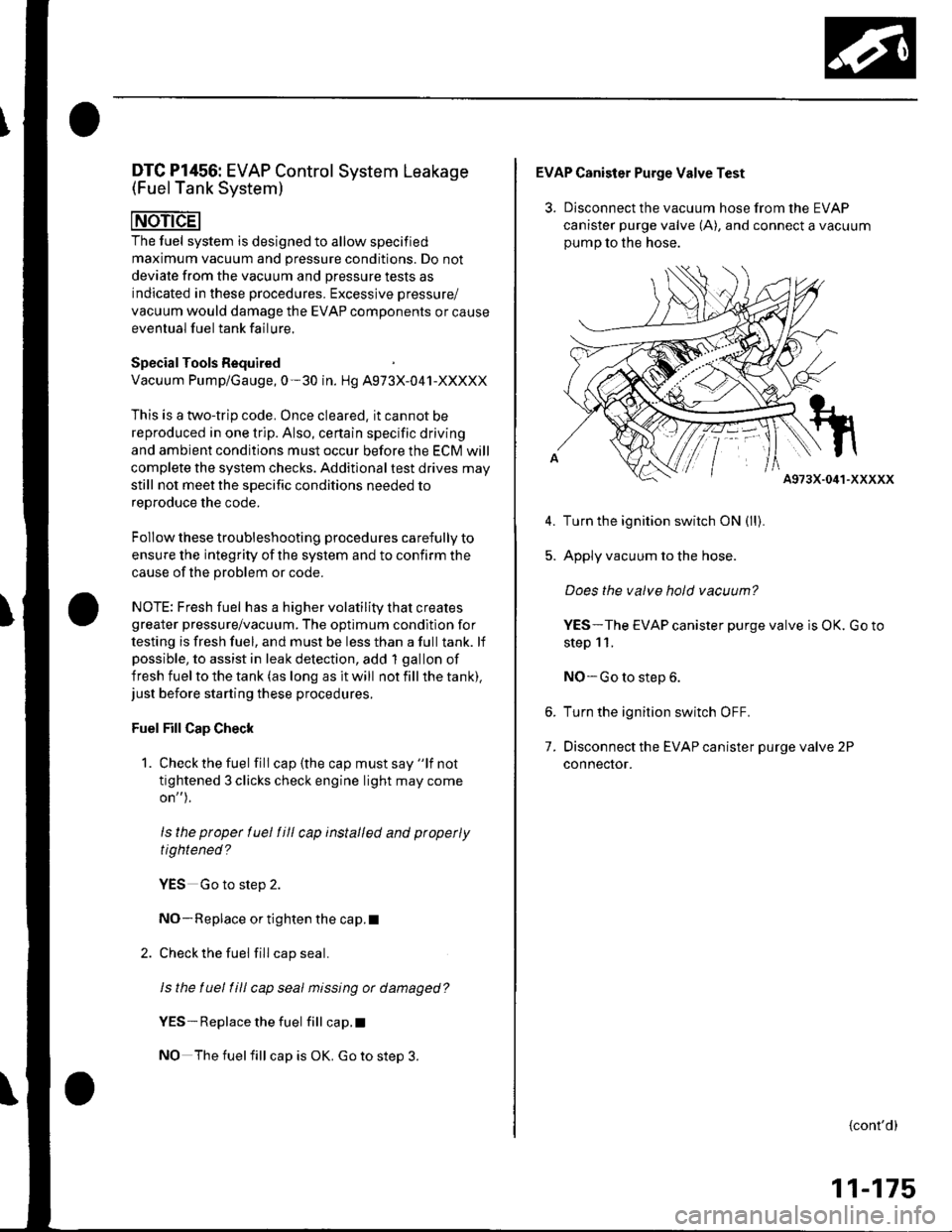
DTC Pl456: EVAP Control(Fuel Tank Svstem)
System Leakage
The fuel system is designed to allow specified
maximum vacuum and pressure conditions. Do not
deviate from the vacuum and pressure tests as
indicated in these procedures. Excessive pressure/
vacuum would damage the EVAP components or cause
eventual fuel tank failure.
Special Tools Required
Vacuum Pump/Gauge, 0-30 in. Hg A973X-041-XXXXX
This is a two-trip code. Once cleared, it cannot be
reproduced in one trip. Also, cenain specific driving
and ambient conditions must occur before the ECM will
complete the system checks. Additional test drives may
still not meet the specific conditions needed to
reproduce the code.
Follow these troubleshooting procedures carefully to
ensure the integrity of the system and to confirm the
cause of the problem or code.
NOTE: Fresh fuel has a higher volatility that createsgreater pressure/vacuum. The optimum condltlon for
testing is fresh fuel, and must be less than a full tank. lf
possible, to assist in leak detection, add 1 gallon of
fresh fuel to the tank (as long as it will not fill the tank).just before starting these procedures.
Fuel Fill Cap Check
1. Check the fuel fill cap (the cap must say "lf not
tightened 3 clicks check engine light may come
on" ).
ls the proper luel till cap installed and properly
tightened?
YES Go to step 2.
NO- Replace or tighten the cap.I
2. Check the fuel fill cap seal.
ls the tuel fill cap seal missing or damaged?
YES- Replace the fuel fill cap.I
NO The fuelfill cap is OK. Go to step 3.
EVAP Canister Purge Valve Test
3. Disconnect the vacuum hose from the EVAP
canister purge valve (A), and connect a vacuum
oumo to the hose.
A973X-041-XXXXX
Turn the ignition switch ON (ll).
Apply vacuum to the hose.
Does the valve hold vacuum?
YES-The EVAP canister purge valve is OK. Go to
step 11.
NO-Go to step 6.
Turn the ignition switch OFF.
Disconnect the EVAP canister purge valve 2P
connecror.
5.
7.
{cont'd)
11-175
Page 386 of 1139
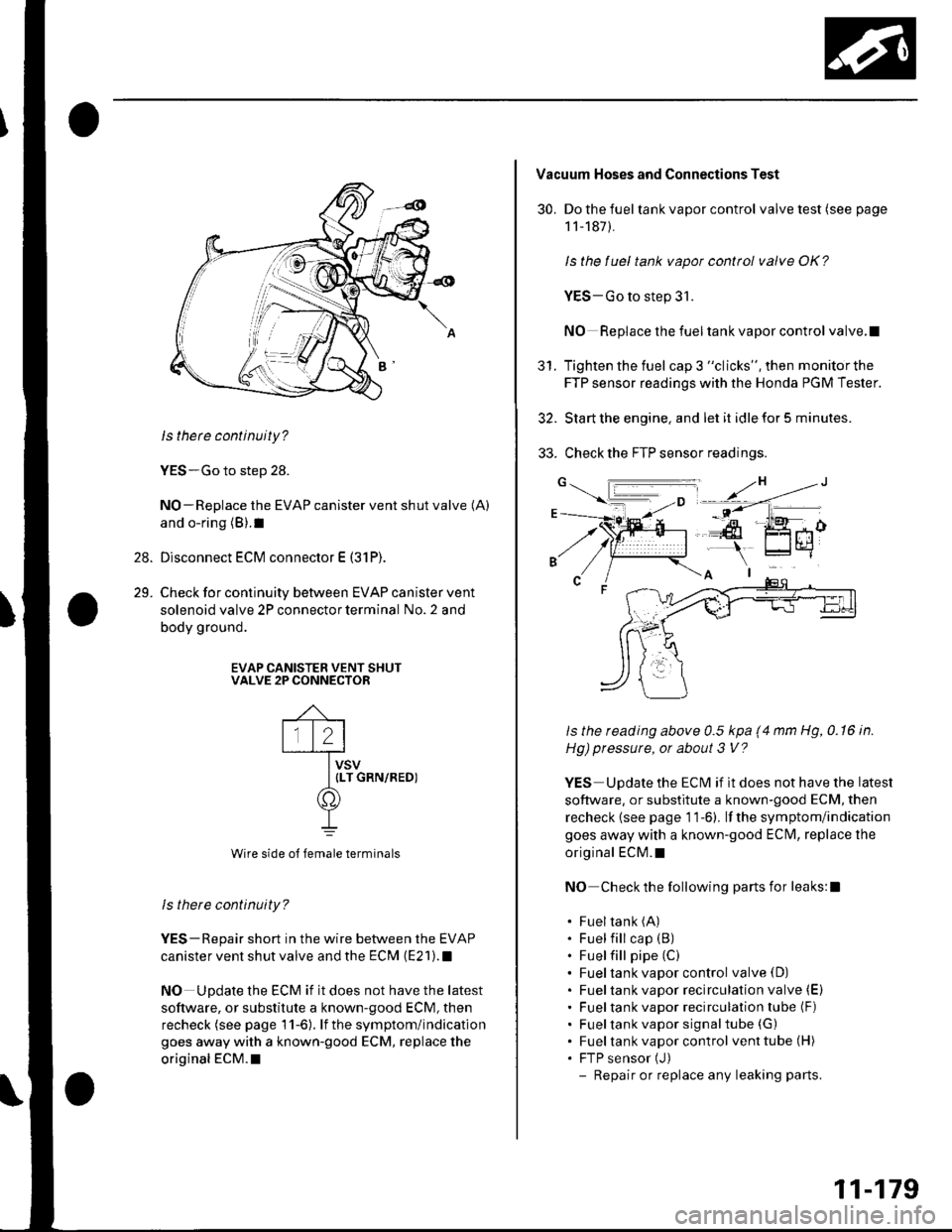
28.
29.
ls thete continuity?
YES-Go to step 28.
NO-Replace the EVAP canister vent shut valve (A)
and o-ring (B).1
Disconnect ECM connector E (31P).
Check for continuity between EVAP canister vent
solenoid valve 2P connector terminal No. 2 and
body ground.
EVAP CANISTER VENT SHUTVALVE 2P CONNECTOR
Wire side o{ female terminals
ls there continuity?
YES-Repair short in the wire between the EVAP
canister vent shut valve and the ECM (E21).1
NO Update the ECM if it does not have the latest
soflware, or substitute a known-good ECM, then
recheck (see page 11-6). lf the symptom/indication
goes away with a known-good ECM, replace the
original ECM.I
30.
Vacuum Hoses and Connections Test
Do the fuel tank vapor control valve test (see page
1 1-187).
ls the fuel tank vapot control valve OK?
YES-Go to step 31.
NO Replace the fueltank vapor control valve.l
Tighten the fuel cap 3 "clicks", then monitorthe
FTP sensor readings with the Honda PGM Tester.
Start the engine. and let it idle for 5 minutes.
Check the FTP sensor readings.
ls the reading above 0.5 kpa (4 mm Hg, 0.16 in.
Hg) pressure, or about 3 V?
YES Update the ECM if it does not have the latest
software, or substitute a known-good ECM, then
recheck {see page 1 1-6). lf the symptom/indication
goes away with a known-good ECfvl, replace the
original ECM.t
NO Check the following parts for leaks:l
. Fueltank (A)
. Fuel fill cap (B)
. Fuel fill pipe (C)
. Fueltank vapor control valve(D). Fueltank vapor recirculation valve (E)
. Fueltank vapor recirculation tube (F)
. Fueltank vapor signaltube (G)
. Fueltank vapor control venttube(H). FTP sensor (J)
- Repair or replace any leaking parts.
5t.
11-179
Page 401 of 1139

Clutch
Clutch Pedal, Clutch
Adjustment
NOTE:. To check the clutch pedal position switch(see page 4-45).. To check the clutch interlock switch (see page 4-6).. Remove the driver's side floor mat before adjusting
the clutch pedal.. The clutch is self-adjusting to compensate for wear.. lf there is no clearance betweenthe mastercylinderpiston and push rod, the release bearing will be held
against the diaphragm spring. which can result in
clutch slippage or other clutch problems.
1. Loosen the clutch pedal position switch locknut (A),
and back off the clutch pedal position switch (B)
until it no longer touches the clutch pedal (C).
J9.8 N.m(1.0 kgf.m,7.2 lbf.ft)
A9.8 N.m11.0 kgf.m, 7.2 lbf.ft)
o18 N.m{1.8 kgf.m,13 tbf.ftl
Loosen the clutch push-rod locknut (D). and turn
the push rod (E) in or out to get the specified height(F), stroke (G). free play (H) and disengagement
height (l) atthe clutch pedal.
Clutch PedalStroke: 130 140 mm(5.12 5.51 in.l
Clutch Pedal Free Play: l0 16 mm (0.39-0.63 in.)
Clutch Pedal Height: 193 mm (7.60 in.)
Disengagement
Height: 115 mm (4.53 in.)
Between Floor And
Carpet Height(Approximate Valuel: 38 mm {1.50 in.l
12-4
Pedal Position Switch, and Clutch Interlock Switch
3. Tighten the clutch push-rod locknut (D).
4. With the clutch pedal released. turn the clutchpedal position switch (B) in until it contacts the
clutch pedal (C).
5. Turn the clutch pedal position switch {B) in an
additional 3/4 to 1 turn.
6. Tighten the clutch pedal position switch locknut (A).
7. Loosen locknut (J)and the clutch interlock switch(K).
8. Press the clutch pedal to the floor.
9. Release the clutch pedal 10 'l6mm(0,39 0.63in.)
from the fully pressed position, and hold it there.
Adjust the position of the clutch interlock switch (K)
so that the engine will start with the clutch pedal in
thls position.
10. Tighten the clutch interlock switch locknut (J).
Page 413 of 1139
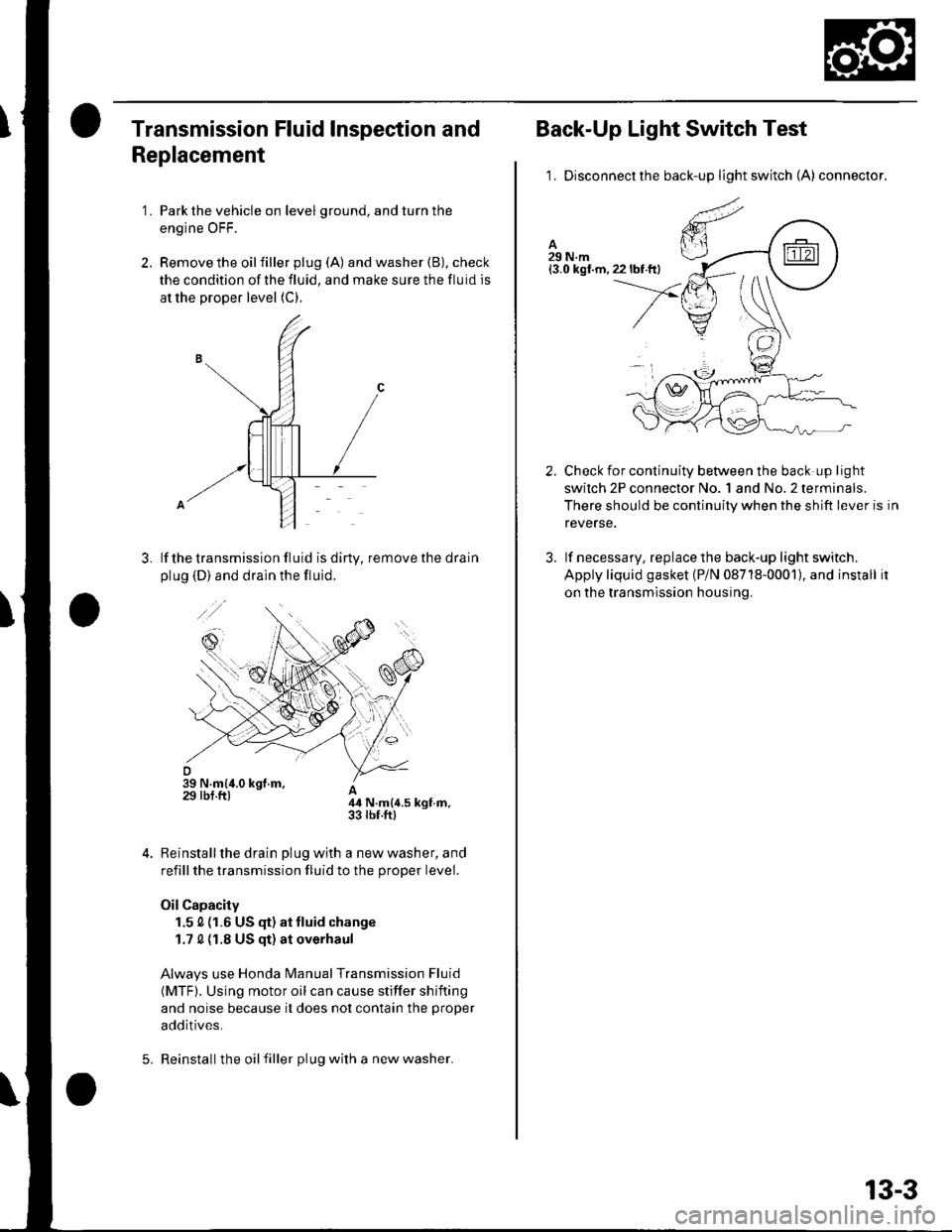
Transmission Fluid Inspection and
Replacement
'1. Park the vehicle on level ground, and turn the
engine OFF.
2. Remove the oilfiller plug (A) and washer (B), check
the condition of the fluid, and make sure the fluid is
at the proper level (C).
lf the transmission fluid is diny, remove the drain
plug (D) and drain the fluid.
A44 N.m{4.5 kgt.m,33 rbr.ftl
Reinstall the drain plug with a new washer, and
refill the transmission fluid to the proper level.
Oil Capacity
1.5 0 (1.6 US (F) at tluid change
1.7 0 {1.8 US qt) at overhaul
Always use Honda Manual Transmission Fluid
(MTF). Using motor oil can cause stiffer shifting
and noise because it does not contain the proper
additives.
Reinstall the oil filler plug with a new washer.5.
13-3
Back-Up Light Switch Test
1. Disconnectthe back-up light switch (A) connector.
Check for continuity between the back up light
swilch 2P connector No. 1 and No.2 terminals.
There should be continuity when the shift lever is in
reverse.
lf necessary, replace the back-up light switch.
Apply liquid gasket (P/N 08718-0001), and install it
on the transmission housing.
2.
3.
Page 418 of 1139
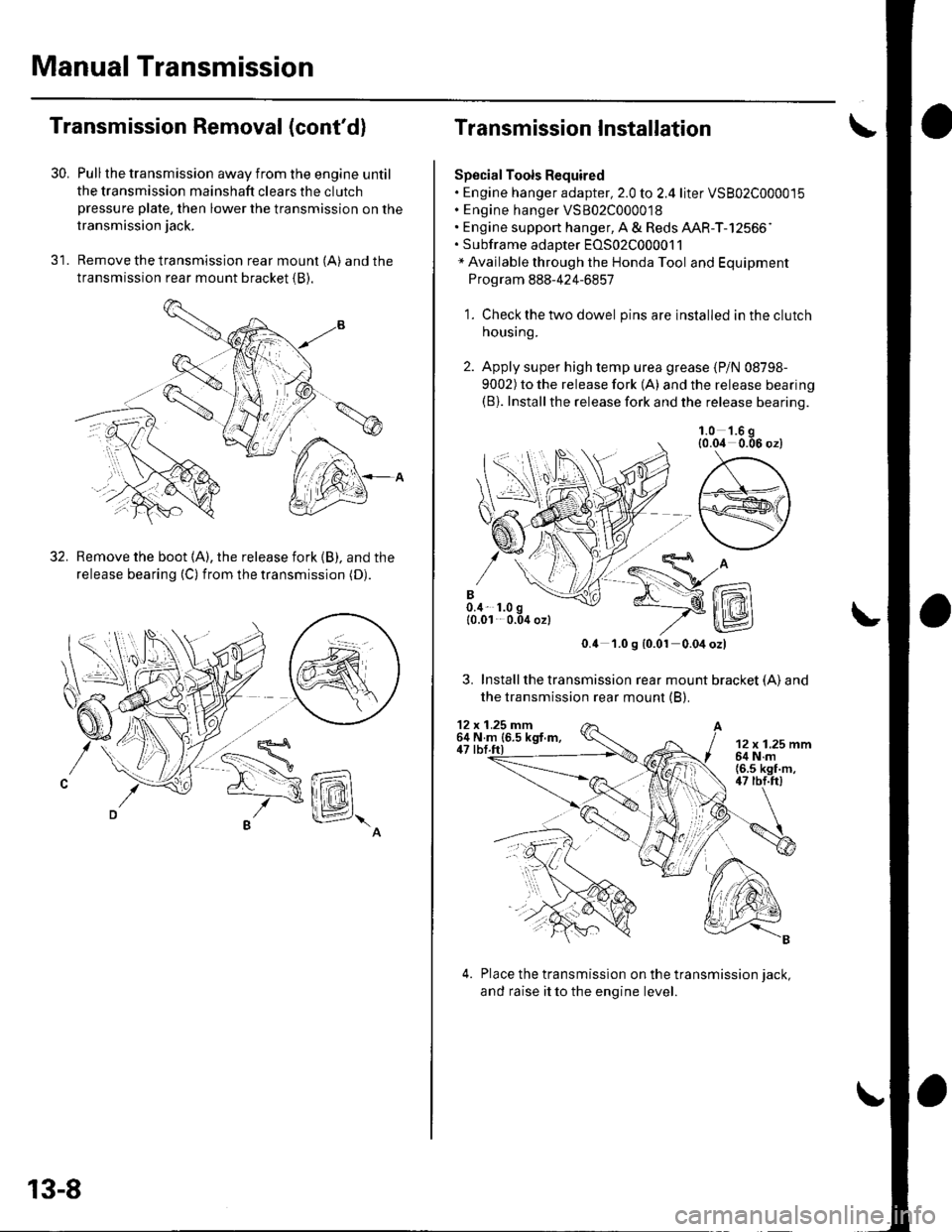
Manual Transmission
\
12 x 1.25 mm64 N.m{6.5 ksf.m,47 tbf.ft)
30.
Transmission Removal (cont'd)
Pull the transmission away from the engine until
the transmission mainshaft clears the clutchpressure plate, then lower the transmission on the
transmission jack.
Remove the transmission rear mount (A) and the
transmission rear mount bracket {B).
Remove the boot (A), the release fork {B). and the
release bearing (C) from the transmission (D).
32.
13-8
Transmission Installation
Special Tools Required. Engine hanger adapter, 2.0 to 2.4 liter VS802C000015. E ngine hanger VS802C000018. Engine support hanger, A & Reds AAR-T-12566". subframe adaDter EoS02c000011* Available through the Honda Tool and Equipment
Program 888-424-6857
1. Check the two dowel pins are installed in the clutch
housr ng.
Apply super high temp urea grease (P/N 08798-
9002) to the release fork (A) and the release bearing(B). Installthe release fork and the release bearing.
0.4 1.0 g {0.01 0.04 ozl
3. Installthe transmission rear mount bracket (A)and
the transmission rear mount (B).
x 1.25 mmN m {6.5 kgf.m,
Place the transmission on the transmission iack.
and raise it to the engine level.
't2
6447
1.0 '1.6 g{0.04 0.06 oz)