rack INFINITI FX35 2004 Service Manual
[x] Cancel search | Manufacturer: INFINITI, Model Year: 2004, Model line: FX35, Model: INFINITI FX35 2004Pages: 4449, PDF Size: 99.66 MB
Page 3020 of 4449
![INFINITI FX35 2004 Service Manual FRONT WHEEL HUB AND KNUCKLE
FAX-11
[AWD]
C
E
F
G
H
I
J
K
L
MA
B
FA X
Revision: 2004 November 2004 FX35/FX45
6. Use a ball joint remover (SST) to remove steering outer socket
from steering knuckle. Be INFINITI FX35 2004 Service Manual FRONT WHEEL HUB AND KNUCKLE
FAX-11
[AWD]
C
E
F
G
H
I
J
K
L
MA
B
FA X
Revision: 2004 November 2004 FX35/FX45
6. Use a ball joint remover (SST) to remove steering outer socket
from steering knuckle. Be](/img/42/57021/w960_57021-3019.png)
FRONT WHEEL HUB AND KNUCKLE
FAX-11
[AWD]
C
E
F
G
H
I
J
K
L
MA
B
FA X
Revision: 2004 November 2004 FX35/FX45
6. Use a ball joint remover (SST) to remove steering outer socket
from steering knuckle. Be careful not to damage ball joint boot.
CAUTION:
Tighten temporarily mounting nut to prevent damage to
threads and to prevent ball joint remover (SST) from com-
ing off.
7. Remove cotter pin at transverse link, then loosen mounting nut.
8. Use a ball joint remover (SST) to remove transverse link from
steering knuckle. Be careful not to damage ball joint boot.
CAUTION:
Tighten temporarily mounting nut to prevent damage to
threads and to prevent ball joint remover (SST) from com-
ing off.
9. Remove cotter pin, then remove lock nut from drive shaft with
power tool.
10. Remove steering knuckle from drive shaft.
CAUTION:
When removing steering knuckle, do not apply an exces-
sive angle to drive shaft joint. Also be careful not to excessively extend slide joint.
Do not hang over drive shaft without support.
11. Remove fixing bolts and nuts between strut assembly and steering knuckle with power tool.
12. Remove steering knuckle from vehicle.
13. Remove fixing bolts between steering knuckle and wheel hub and bearing assembly with power tool.
14. Remove splash guard and wheel hub and bearing assembly from steering knuckle.
INSPECTION AFTER REMOVAL
Check for deformity, cracks and damage on each parts, replace if necessary.
Ball Joint Inspection
Check for boot breakage, axial looseness, and torque of transverse link and steering outer socket ball joint.
Refer to FSU-14, "
TRANSVERSE LINK" , PS-19, "POWER STEERING GEAR AND LINKAGE" .
INSTALLATION
Refer to FAX-10, "Removal and Installation" for tightening torque. Install in the reverse order of removal.
NOTE:
Refer to component parts location and do not reuse non-reusable parts.
After removing/installing or replacing axle components, check wheel alignment. Refer to FSU-6, "Wheel
Alignment Inspection" .
After adjusting wheel alignment, adjust neutral position of steering angle sensor. Refer to BRC-6, "Adjust-
ment of Steering Angle Sensor Neutral Position" .
Check the following item after service.
–Installation condition of wheel sensor harness.
SDIA1434E
SDIA1435E
Page 3021 of 4449
![INFINITI FX35 2004 Service Manual FAX-12
[AWD]
FRONT DRIVE SHAFT
Revision: 2004 November 2004 FX35/FX45
FRONT DRIVE SHAFTPFP:39100
Removal and Installation (Left Side)ADS000ON
REMOVAL
1. Remove tire from vehicle with power tool.
2. Re INFINITI FX35 2004 Service Manual FAX-12
[AWD]
FRONT DRIVE SHAFT
Revision: 2004 November 2004 FX35/FX45
FRONT DRIVE SHAFTPFP:39100
Removal and Installation (Left Side)ADS000ON
REMOVAL
1. Remove tire from vehicle with power tool.
2. Re](/img/42/57021/w960_57021-3020.png)
FAX-12
[AWD]
FRONT DRIVE SHAFT
Revision: 2004 November 2004 FX35/FX45
FRONT DRIVE SHAFTPFP:39100
Removal and Installation (Left Side)ADS000ON
REMOVAL
1. Remove tire from vehicle with power tool.
2. Remove undercover with power tool.
3. Remove cotter pin. Then remove lock nut from drive shaft with power tool.
4. Remove wheel sensor harness from strut assembly. Refer to BRC-57, "
WHEEL SENSORS" .
CAUTION:
Do not pull on wheel sensor harness.
5. Remove brake hose lock plate. Then remove brake hose from strut assembly. Refer to BR-11, "
BRAKE
PIPING AND HOSE" .
6. Remove fixing bolts and nuts between strut assembly and steering knuckle with power tool.
7. Remove drive shaft from steering knuckle.
CAUTION:
When removing drive shaft, do not apply an excessive angle to drive shaft joint. Also be careful
not to excessively extend slide joint.
8. Remove fixing bolt of front final drive side assembly drive shaft with power tool, then remove drive shaft
from vehicle.
INSPECTION AFTER REMOVAL
Move joint up/down, left /right, and in the axial direction. Check for any rough movement or significant
looseness.
Check boot for cracks or other damage, and also for grease
leakage.
If a trouble is found, disassemble drive shaft, and then replace
with new one.
INSTALLATION
Refer to FA X - 1 2 , "Removal and Installation (Left Side)" for tightening torque. Install in the reverse order of
removal.
NOTE:
Refer to component parts location and do not reuse non-reusable parts.
Check the following item after service.
–Installation condition of wheel sensor harness
1. Cotter pin 2. Washer
SDIA1441E
SDIA1046J
Page 3022 of 4449
![INFINITI FX35 2004 Service Manual FRONT DRIVE SHAFT
FAX-13
[AWD]
C
E
F
G
H
I
J
K
L
MA
B
FA X
Revision: 2004 November 2004 FX35/FX45
Removal and Installation (Right Side)ADS000OO
REMOVAL
1. Remove tire from vehicle with power tool.
2. INFINITI FX35 2004 Service Manual FRONT DRIVE SHAFT
FAX-13
[AWD]
C
E
F
G
H
I
J
K
L
MA
B
FA X
Revision: 2004 November 2004 FX35/FX45
Removal and Installation (Right Side)ADS000OO
REMOVAL
1. Remove tire from vehicle with power tool.
2.](/img/42/57021/w960_57021-3021.png)
FRONT DRIVE SHAFT
FAX-13
[AWD]
C
E
F
G
H
I
J
K
L
MA
B
FA X
Revision: 2004 November 2004 FX35/FX45
Removal and Installation (Right Side)ADS000OO
REMOVAL
1. Remove tire from vehicle with power tool.
2. Remove undercover with power tool.
3. Remove cotter pin. Then remove lock nut from drive shaft with power tool.
4. Remove wheel sensor harness from strut assembly. Refer to BRC-57, "
WHEEL SENSORS" .
CAUTION:
Do not pull on wheel sensor harness.
5. Remove brake hose lock prate. Then remove brake hose from strut assembly. Refer to BR-11, "
BRAKE
PIPING AND HOSE" .
6. Remove fixing bolts and nuts between strut assembly and steering knuckle with power tool.
7. Remove drive shaft from steering knuckle.
CAUTION:
When removing drive shaft, do not apply an excessive angle to drive shaft joint. Also be careful
not to excessively extend slide joint.
8. Pry off drive shaft from front final drive assembly side as shown
in the figure.
INSPECTION AFTER REMOVAL
Move joint up/down, left/right, and in the axial direction. Check for any rough movement or significant
looseness.
Check boot for cracks or other damage, and also for grease
leakage.
If a trouble is found, disassemble drive shaft, and then replace
with new one.
1. Cotter pin 2. Washer
SDIA1442E
SDIA1489E
SFA108A
Page 3024 of 4449
![INFINITI FX35 2004 Service Manual FRONT DRIVE SHAFT
FAX-15
[AWD]
C
E
F
G
H
I
J
K
L
MA
B
FA X
Revision: 2004 November 2004 FX35/FX45
4. Put matching marks on spider assembly and shaft.
CAUTION:
Use paint for matching mark, but don’t INFINITI FX35 2004 Service Manual FRONT DRIVE SHAFT
FAX-15
[AWD]
C
E
F
G
H
I
J
K
L
MA
B
FA X
Revision: 2004 November 2004 FX35/FX45
4. Put matching marks on spider assembly and shaft.
CAUTION:
Use paint for matching mark, but don’t](/img/42/57021/w960_57021-3023.png)
FRONT DRIVE SHAFT
FAX-15
[AWD]
C
E
F
G
H
I
J
K
L
MA
B
FA X
Revision: 2004 November 2004 FX35/FX45
4. Put matching marks on spider assembly and shaft.
CAUTION:
Use paint for matching mark, but don’t damage to spider
assembly and drive shaft.
5. Remove snap ring, then remove spider assembly from shaft.
6. Remove boot from shaft.
7. Remove old grease on slide joint assembly with paper towels.
Wheel Side
1. Place drive shaft in a vice.
CAUTION:
When retaining drive shaft in a vice, always use copper or aluminum plates between a vise and
shaft.
2. Remove boot bands. Then remove boot from joint sub-assembly.
3. Screw a drive shaft puller (suitable tool) 30 mm (1.18 in) or more
into threaded part of joint sub-assembly. Pull joint sub-assembly
out of shaft.
CAUTION:
If joint sub-assembly cannot be removed after five or
more unsuccessful attempts, replace shaft and joint sub-
assembly as a set.
Align sliding hammer and drive shaft and remove them
by pulling directly.
4. Remove boot from shaft.
5. Remove circular clip from shaft.
6. While rotating ball cage, remove old grease on joint sub-assembly with paper towels.
INSPECTION AFTER DISASSEMBLY
Shaft
Replace shaft if there is any runout, cracking, or other damage.
Joint Sub-Assembly
Make sure there is no rough rotation or unusual axial looseness.
Make sure there is no foreign material inside joint sub-assembly.
Check joint sub-assembly for compression scar, cracks or fractures.
CAUTION:
If there are any irregular conditions of joint sub-assembly components, replace the entire joint
sub-assembly.
Slide Joint Side
Housing and spider assembly
If roller or roller surface of spider assembly has scratch or wear, replace housing and spider assembly.
SFA963
SFA612
SDIA0606E
Page 3029 of 4449
![INFINITI FX35 2004 Service Manual FAX-20
[AWD]
FRONT DRIVE SHAFT
Revision: 2004 November 2004 FX35/FX45
3. Put matching marks on spider assembly and shaft.
CAUTION:
Use paint for matching mark, but don’t damage to spider
assembly an INFINITI FX35 2004 Service Manual FAX-20
[AWD]
FRONT DRIVE SHAFT
Revision: 2004 November 2004 FX35/FX45
3. Put matching marks on spider assembly and shaft.
CAUTION:
Use paint for matching mark, but don’t damage to spider
assembly an](/img/42/57021/w960_57021-3028.png)
FAX-20
[AWD]
FRONT DRIVE SHAFT
Revision: 2004 November 2004 FX35/FX45
3. Put matching marks on spider assembly and shaft.
CAUTION:
Use paint for matching mark, but don’t damage to spider
assembly and shaft.
4. Remove snap ring, then remove spider assembly from shaft.
5. Remove boot from shaft.
6. Remove old grease on slide joint assembly with paper towels.
Wheel Side
1. Place drive shaft in a vice.
CAUTION:
When retaining drive shaft in a vice, always use copper or aluminum plates between vise a and
shaft.
2. Remove boot bands. Then remove boot from joint sub-assembly.
3. Screw a drive shaft puller (suitable tool) 30 mm (1.18 in) or more
into threaded part of joint sub-assembly. Pull joint sub-assembly
out of shaft.
CAUTION:
If joint sub-assembly cannot be removed after five or
more unsuccessful attempts, replace shaft and joint sub-
assembly as a set.
Align sliding hammer and drive shaft and remove them
by pulling directly.
4. Remove boot from shaft.
5. Remove circular clip from shaft.
6. While rotating ball cage, remove old grease on joint sub-assembly with paper towels.
INSPECTION AFTER DISASSEMBLY
Shaft
Replace shaft if there is any runout, cracking, or other damage.
Joint sub-assembly
Make sure there is no rough rotation or unusual axial looseness.
Make sure there is no foreign material inside joint sub-assembly.
Check joint sub-assembly for compression scar, cracks or fractures.
If there are any irregular conditions of joint sub-assembly components, replace the entire joint sub-assem-
bly.
Slide Joint Side
Housing and spider assembly
If roller or roller surface of spider assembly has scratch or wear, replace housing and spider assembly.
SFA963
SFA612
SDIA0606E
Page 3045 of 4449
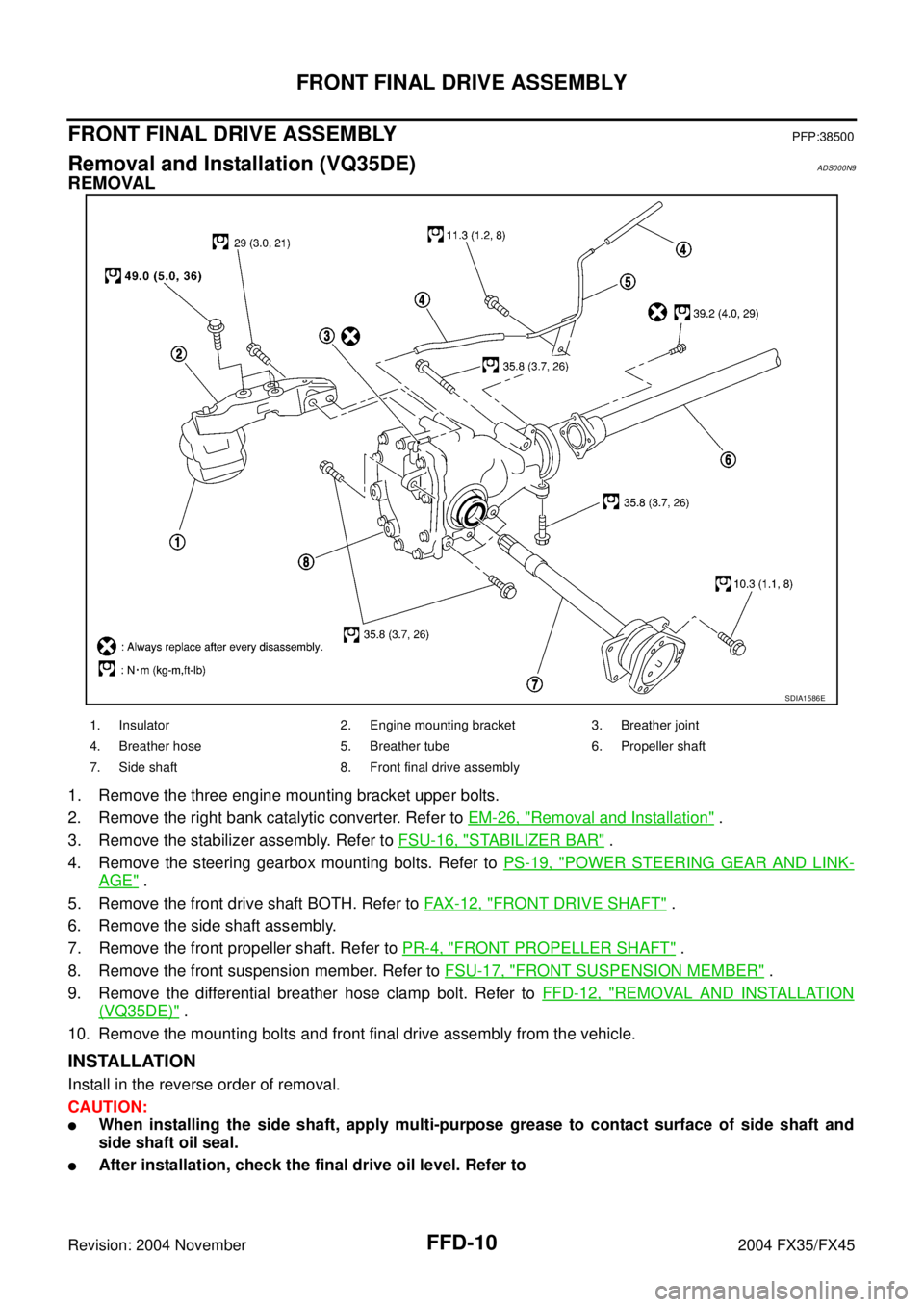
FFD-10
FRONT FINAL DRIVE ASSEMBLY
Revision: 2004 November 2004 FX35/FX45
FRONT FINAL DRIVE ASSEMBLYPFP:38500
Removal and Installation (VQ35DE)ADS000N9
REMOVAL
1. Remove the three engine mounting bracket upper bolts.
2. Remove the right bank catalytic converter. Refer to EM-26, "
Removal and Installation" .
3. Remove the stabilizer assembly. Refer to FSU-16, "
STABILIZER BAR" .
4. Remove the steering gearbox mounting bolts. Refer to PS-19, "
POWER STEERING GEAR AND LINK-
AGE" .
5. Remove the front drive shaft BOTH. Refer to FAX-12, "
FRONT DRIVE SHAFT" .
6. Remove the side shaft assembly.
7. Remove the front propeller shaft. Refer to PR-4, "
FRONT PROPELLER SHAFT" .
8. Remove the front suspension member. Refer to FSU-17, "
FRONT SUSPENSION MEMBER" .
9. Remove the differential breather hose clamp bolt. Refer to FFD-12, "
REMOVAL AND INSTALLATION
(VQ35DE)" .
10. Remove the mounting bolts and front final drive assembly from the vehicle.
INSTALLATION
Install in the reverse order of removal.
CAUTION:
When installing the side shaft, apply multi-purpose grease to contact surface of side shaft and
side shaft oil seal.
After installation, check the final drive oil level. Refer to
SDIA1586E
1. Insulator 2. Engine mounting bracket 3. Breather joint
4. Breather hose 5. Breather tube 6. Propeller shaft
7. Side shaft 8. Front final drive assembly
Page 3047 of 4449
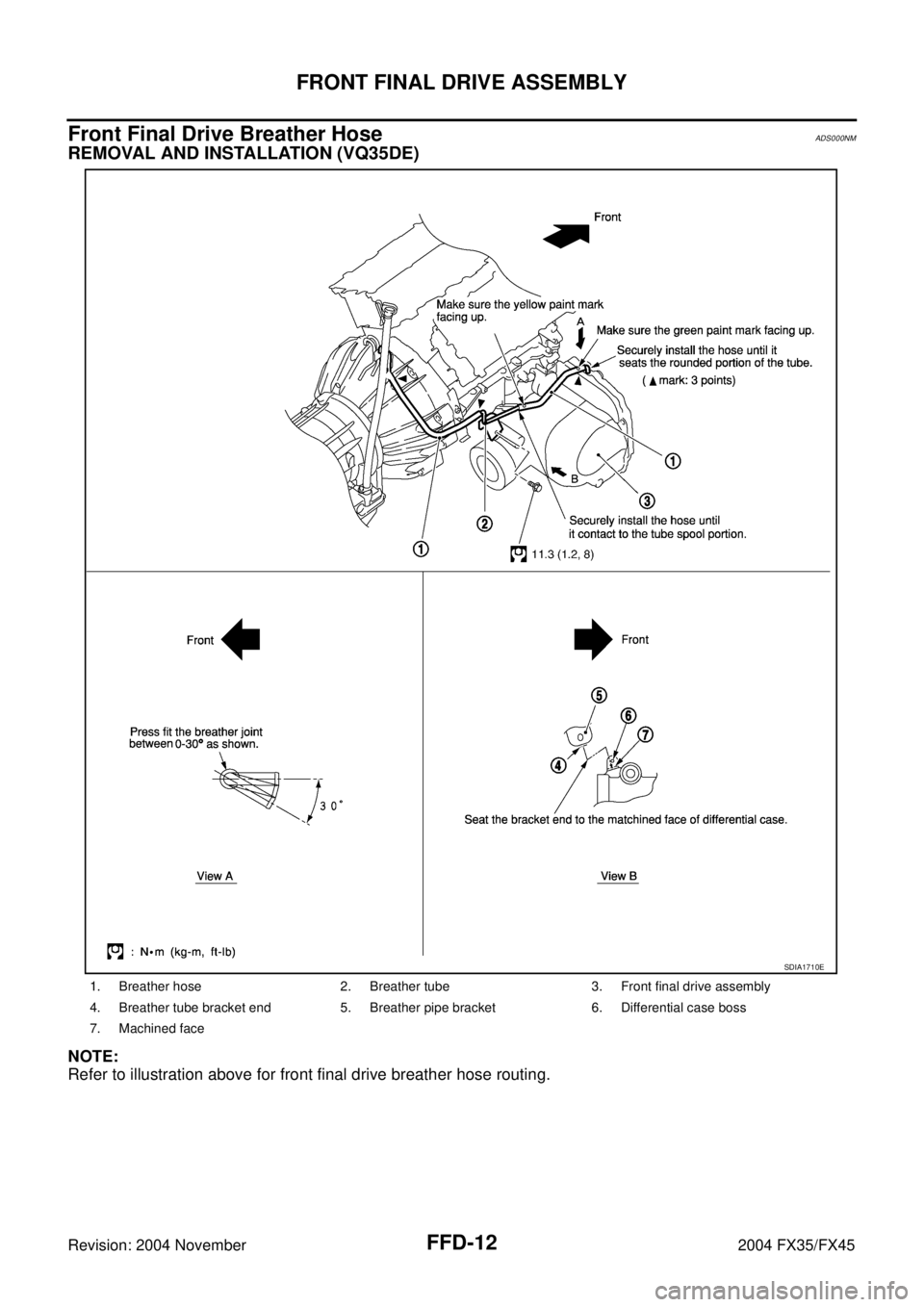
FFD-12
FRONT FINAL DRIVE ASSEMBLY
Revision: 2004 November 2004 FX35/FX45
Front Final Drive Breather HoseADS000NM
REMOVAL AND INSTALLATION (VQ35DE)
NOTE:
Refer to illustration above for front final drive breather hose routing.
1. Breather hose 2. Breather tube 3. Front final drive assembly
4. Breather tube bracket end 5. Breather pipe bracket 6. Differential case boss
7. Machined face
SDIA1710E
Page 3059 of 4449
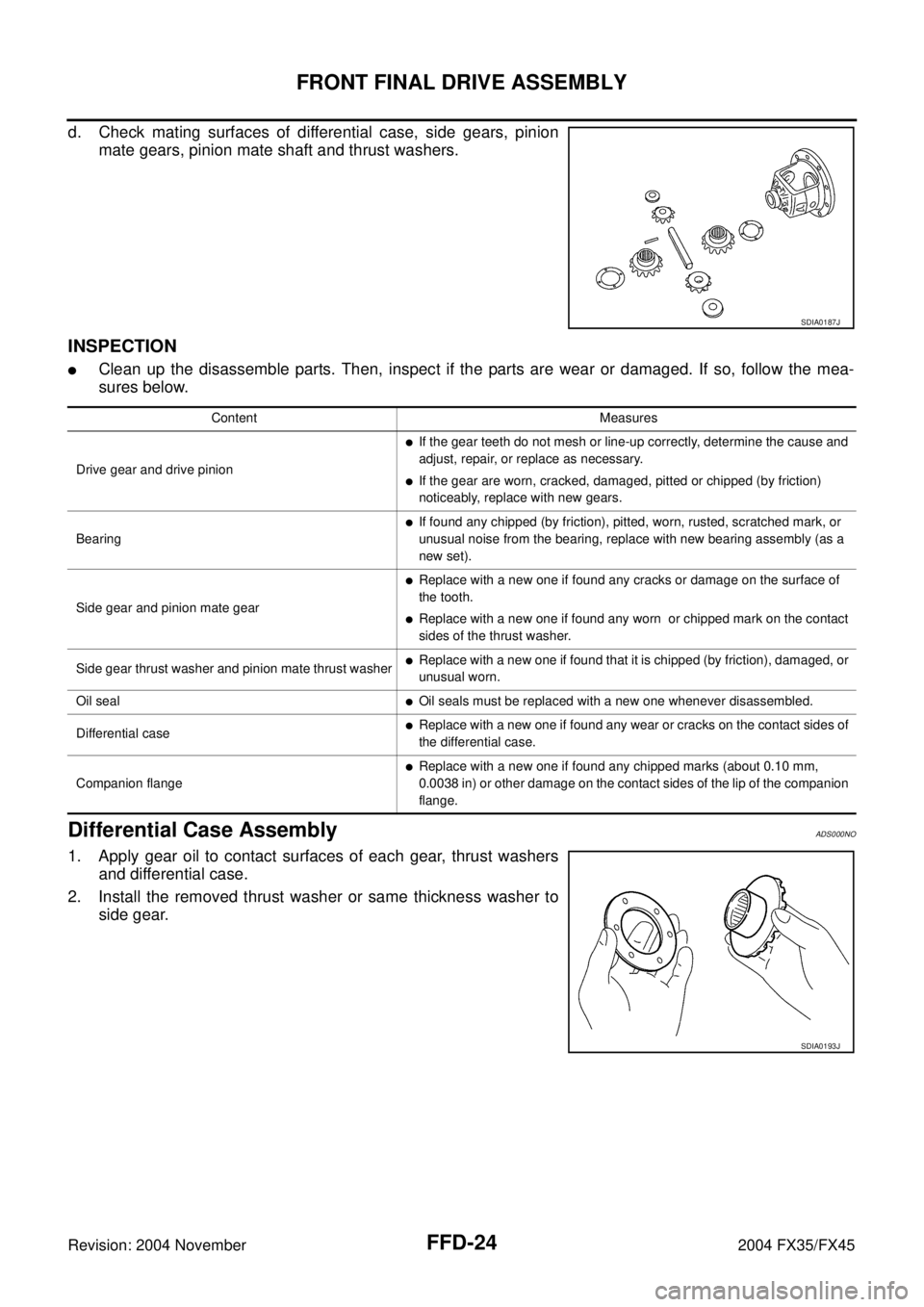
FFD-24
FRONT FINAL DRIVE ASSEMBLY
Revision: 2004 November 2004 FX35/FX45
d. Check mating surfaces of differential case, side gears, pinion
mate gears, pinion mate shaft and thrust washers.
INSPECTION
Clean up the disassemble parts. Then, inspect if the parts are wear or damaged. If so, follow the mea-
sures below.
Differential Case AssemblyADS000NO
1. Apply gear oil to contact surfaces of each gear, thrust washers
and differential case.
2. Install the removed thrust washer or same thickness washer to
side gear.
SDIA0187J
Content Measures
Drive gear and drive pinion
If the gear teeth do not mesh or line-up correctly, determine the cause and
adjust, repair, or replace as necessary.
If the gear are worn, cracked, damaged, pitted or chipped (by friction)
noticeably, replace with new gears.
Bearing
If found any chipped (by friction), pitted, worn, rusted, scratched mark, or
unusual noise from the bearing, replace with new bearing assembly (as a
new set).
Side gear and pinion mate gear
Replace with a new one if found any cracks or damage on the surface of
the tooth.
Replace with a new one if found any worn or chipped mark on the contact
sides of the thrust washer.
Side gear thrust washer and pinion mate thrust washer
Replace with a new one if found that it is chipped (by friction), damaged, or
unusual worn.
Oil seal
Oil seals must be replaced with a new one whenever disassembled.
Differential case
Replace with a new one if found any wear or cracks on the contact sides of
the differential case.
Companion flange
Replace with a new one if found any chipped marks (about 0.10 mm,
0.0038 in) or other damage on the contact sides of the lip of the companion
flange.
SDIA0193J
Page 3076 of 4449
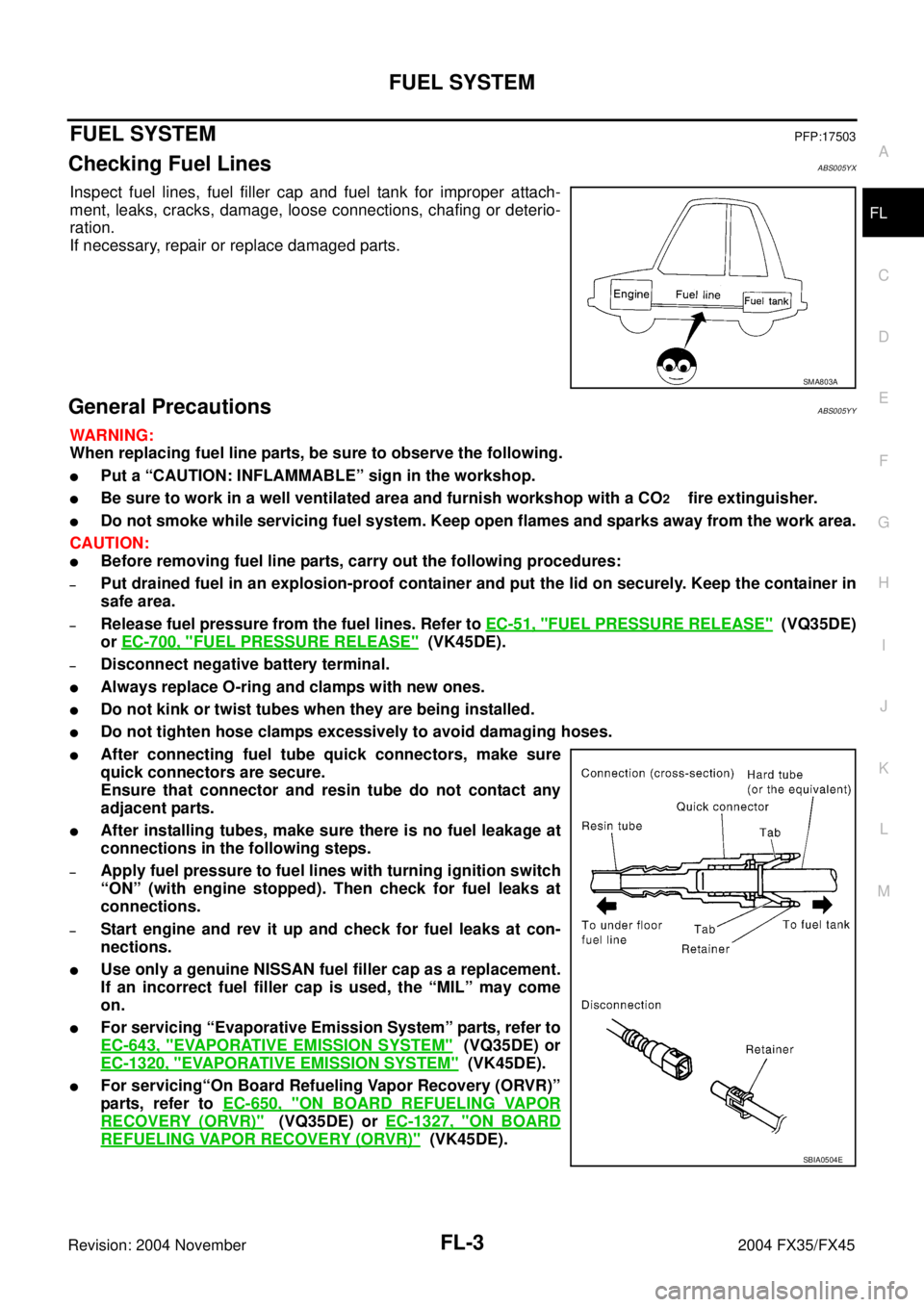
FUEL SYSTEM
FL-3
C
D
E
F
G
H
I
J
K
L
MA
FL
Revision: 2004 November 2004 FX35/FX45
FUEL SYSTEMPFP:17503
Checking Fuel LinesABS005YX
Inspect fuel lines, fuel filler cap and fuel tank for improper attach-
ment, leaks, cracks, damage, loose connections, chafing or deterio-
ration.
If necessary, repair or replace damaged parts.
General PrecautionsABS005YY
WARNING:
When replacing fuel line parts, be sure to observe the following.
Put a “CAUTION: INFLAMMABLE” sign in the workshop.
Be sure to work in a well ventilated area and furnish workshop with a CO2 fire extinguisher.
Do not smoke while servicing fuel system. Keep open flames and sparks away from the work area.
CAUTION:
Before removing fuel line parts, carry out the following procedures:
–Put drained fuel in an explosion-proof container and put the lid on securely. Keep the container in
safe area.
–Release fuel pressure from the fuel lines. Refer to EC-51, "FUEL PRESSURE RELEASE" (VQ35DE)
or EC-700, "
FUEL PRESSURE RELEASE" (VK45DE).
–Disconnect negative battery terminal.
Always replace O-ring and clamps with new ones.
Do not kink or twist tubes when they are being installed.
Do not tighten hose clamps excessively to avoid damaging hoses.
After connecting fuel tube quick connectors, make sure
quick connectors are secure.
Ensure that connector and resin tube do not contact any
adjacent parts.
After installing tubes, make sure there is no fuel leakage at
connections in the following steps.
–Apply fuel pressure to fuel lines with turning ignition switch
“ON” (with engine stopped). Then check for fuel leaks at
connections.
–Start engine and rev it up and check for fuel leaks at con-
nections.
Use only a genuine NISSAN fuel filler cap as a replacement.
If an incorrect fuel filler cap is used, the “MIL” may come
on.
For servicing “Evaporative Emission System” parts, refer to
EC-643, "
EVAPORATIVE EMISSION SYSTEM" (VQ35DE) or
EC-1320, "
EVAPORATIVE EMISSION SYSTEM" (VK45DE).
For servicing“On Board Refueling Vapor Recovery (ORVR)”
parts, refer to EC-650, "
ON BOARD REFUELING VAPOR
RECOVERY (ORVR)" (VQ35DE) or EC-1327, "ON BOARD
REFUELING VAPOR RECOVERY (ORVR)" (VK45DE).
SMA803A
SBIA0504E
Page 3091 of 4449
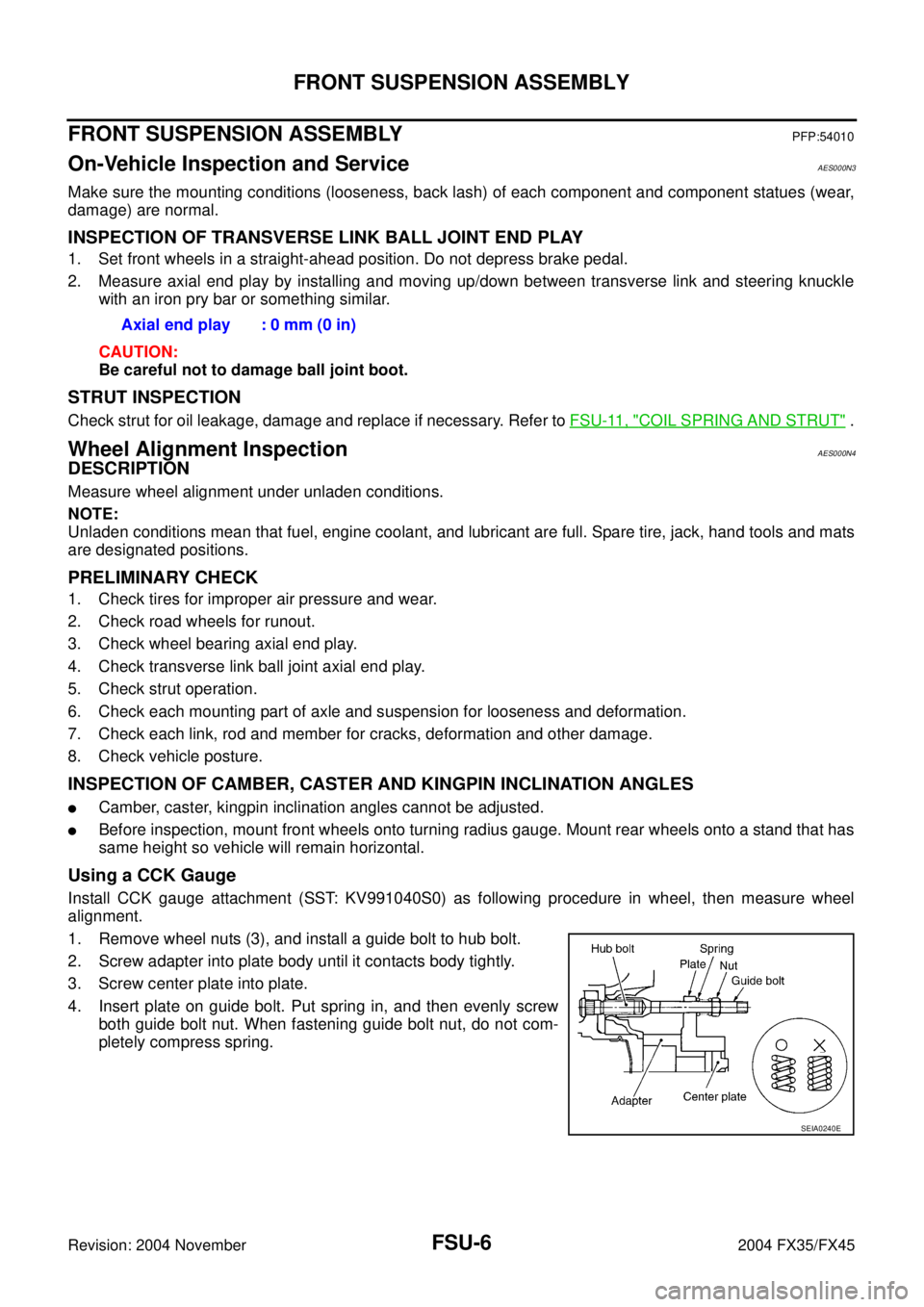
FSU-6
FRONT SUSPENSION ASSEMBLY
Revision: 2004 November 2004 FX35/FX45
FRONT SUSPENSION ASSEMBLYPFP:54010
On-Vehicle Inspection and ServiceAES000N3
Make sure the mounting conditions (looseness, back lash) of each component and component statues (wear,
damage) are normal.
INSPECTION OF TRANSVERSE LINK BALL JOINT END PLAY
1. Set front wheels in a straight-ahead position. Do not depress brake pedal.
2. Measure axial end play by installing and moving up/down between transverse link and steering knuckle
with an iron pry bar or something similar.
CAUTION:
Be careful not to damage ball joint boot.
STRUT INSPECTION
Check strut for oil leakage, damage and replace if necessary. Refer to FSU-11, "COIL SPRING AND STRUT" .
Wheel Alignment InspectionAES000N4
DESCRIPTION
Measure wheel alignment under unladen conditions.
NOTE:
Unladen conditions mean that fuel, engine coolant, and lubricant are full. Spare tire, jack, hand tools and mats
are designated positions.
PRELIMINARY CHECK
1. Check tires for improper air pressure and wear.
2. Check road wheels for runout.
3. Check wheel bearing axial end play.
4. Check transverse link ball joint axial end play.
5. Check strut operation.
6. Check each mounting part of axle and suspension for looseness and deformation.
7. Check each link, rod and member for cracks, deformation and other damage.
8. Check vehicle posture.
INSPECTION OF CAMBER, CASTER AND KINGPIN INCLINATION ANGLES
Camber, caster, kingpin inclination angles cannot be adjusted.
Before inspection, mount front wheels onto turning radius gauge. Mount rear wheels onto a stand that has
same height so vehicle will remain horizontal.
Using a CCK Gauge
Install CCK gauge attachment (SST: KV991040S0) as following procedure in wheel, then measure wheel
alignment.
1. Remove wheel nuts (3), and install a guide bolt to hub bolt.
2. Screw adapter into plate body until it contacts body tightly.
3. Screw center plate into plate.
4. Insert plate on guide bolt. Put spring in, and then evenly screw
both guide bolt nut. When fastening guide bolt nut, do not com-
pletely compress spring.Axial end play : 0 mm (0 in)
SEIA0240E