tire type INFINITI FX35 2005 Service Manual
[x] Cancel search | Manufacturer: INFINITI, Model Year: 2005, Model line: FX35, Model: INFINITI FX35 2005Pages: 4731, PDF Size: 60.13 MB
Page 4 of 4731
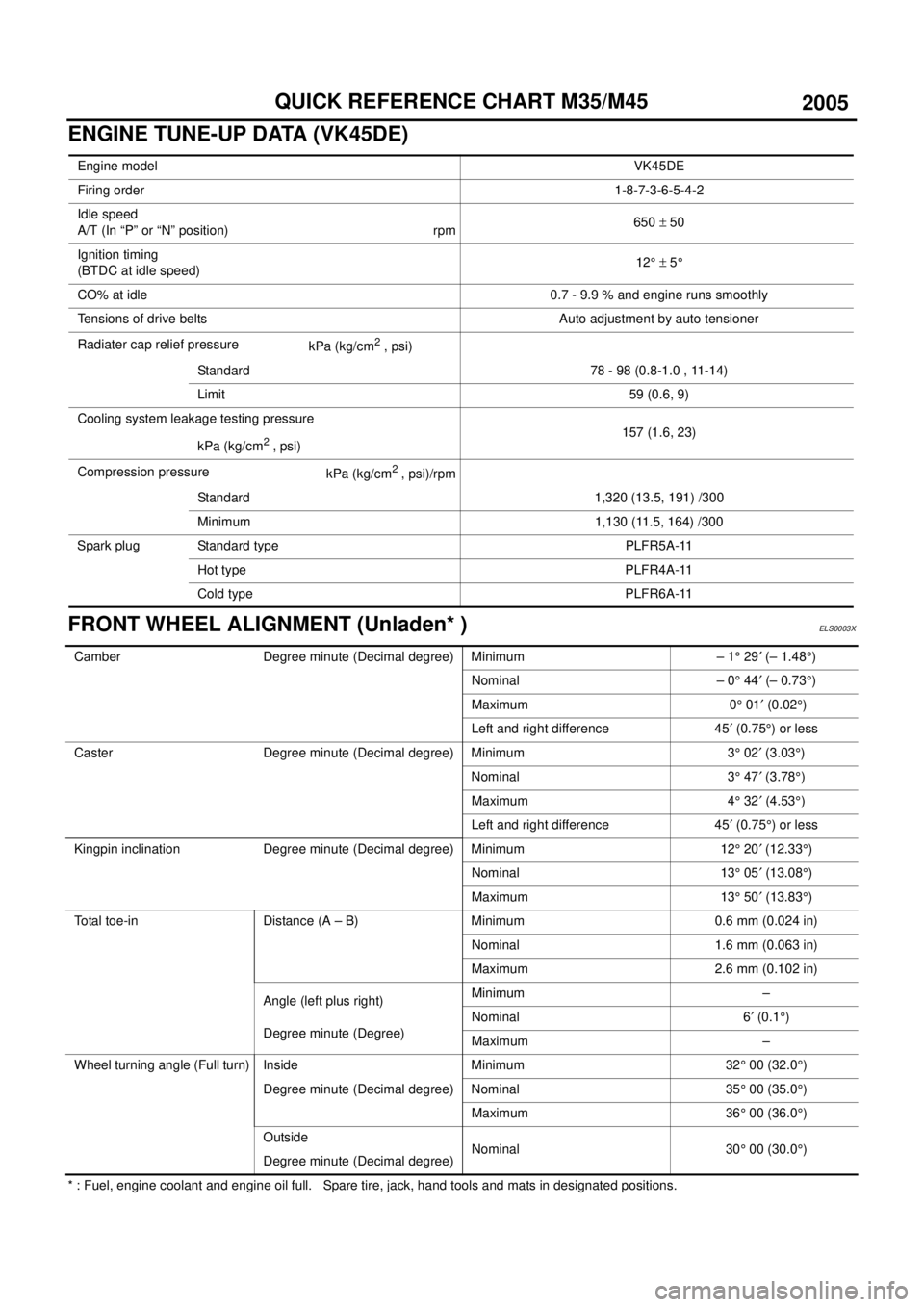
QUICK REFERENCE CHART M35/M45
ENGINE TUNE-UP DATA (VK45DE)
FRONT WHEEL ALIGNMENT (Unladen* )
ELS0003X
* : Fuel, engine coolant and engine oil full. Spare tire, jack, hand tools and mats in designated positions.Engine modelVK45DE
Firing order1-8-7-3-6-5-4-2
Idle speed
A/T (In “P” or “N” position) rpm650 ± 50
Ignition timing
(BTDC at idle speed)12° ± 5°
CO% at idle 0.7 - 9.9 % and engine runs smoothly
Tensions of drive belts Auto adjustment by auto tensioner
Radiater cap relief pressure
kPa (kg/cm
2 , psi)
78 - 98 (0.8-1.0 , 11-14) Standard
Limit 59 (0.6, 9)
Cooling system leakage testing pressure
157 (1.6, 23)
kPa (kg/cm
2 , psi)
Compression pressure
kPa (kg/cm
2 , psi)/rpm
1,320 (13.5, 191) /300 Standard
Minimum 1,130 (11.5, 164) /300
Spark plug Standard type PLFR5A-11
Hot type PLFR4A-11
Cold type PLFR6A-11
Camber Degree minute (Decimal degree) Minimum – 1° 29′ (– 1.48°)
Nominal – 0° 44′ (– 0.73°)
Maximum 0° 01′ (0.02°)
Left and right difference 45′ (0.75°) or less
Caster Degree minute (Decimal degree) Minimum 3° 02′ (3.03°)
Nominal 3° 47′ (3.78°)
Maximum 4° 32′ (4.53°)
Left and right difference 45′ (0.75°) or less
Kingpin inclination Degree minute (Decimal degree) Minimum 12° 20′ (12.33°)
Nominal 13° 05′ (13.08°)
Maximum 13° 50′ (13.83°)
Total toe-in Distance (A – B) Minimum 0.6 mm (0.024 in)
Nominal 1.6 mm (0.063 in)
Maximum 2.6 mm (0.102 in)
Angle (left plus right)
Degree minute (Degree)Minimum –
Nominal 6′ (0.1°)
Maximum –
Wheel turning angle (Full turn) Inside Minimum 32° 00 (32.0°)
Degree minute (Decimal degree) Nominal 35° 00 (35.0°)
Maximum 36° 00 (36.0°)
Outside
Nominal 30° 00 (30.0°)
Degree minute (Decimal degree)
2005
Page 686 of 4731
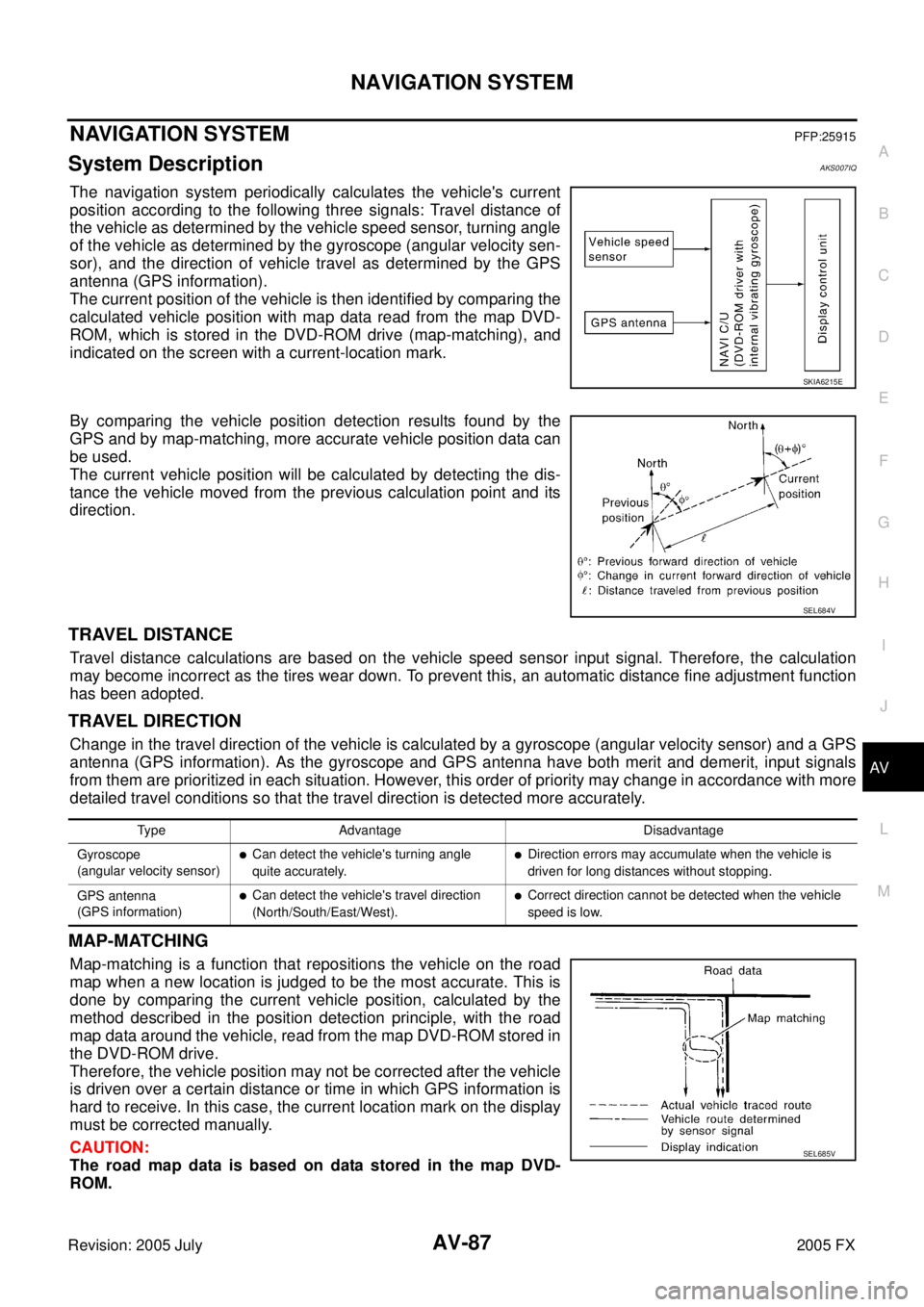
NAVIGATION SYSTEM AV-87
C
D E
F
G H
I
J
L
M A
B
AV
Revision: 2005 July 2005 FX
NAVIGATION SYSTEMPFP:25915
System DescriptionAKS007IQ
The navigation system periodically calculates the vehicle's current
position according to the following three signals: Travel distance of
the vehicle as determined by the vehicle speed sensor, turning angle
of the vehicle as determined by the gyroscope (angular velocity sen-
sor), and the direction of vehicle travel as determined by the GPS
antenna (GPS information).
The current position of the vehicle is then identified by comparing the
calculated vehicle position with map data read from the map DVD-
ROM, which is stored in the DVD-ROM drive (map-matching), and
indicated on the screen with a current-location mark.
By comparing the vehicle position detection results found by the
GPS and by map-matching, more accurate vehicle position data can
be used.
The current vehicle position will be calculated by detecting the dis-
tance the vehicle moved from the previous calculation point and its
direction.
TRAVEL DISTANCE
Travel distance calculations are based on the vehicle speed sensor input signal. Therefore, the calculation
may become incorrect as the tires wear down. To prevent this, an automatic distance fine adjustment function
has been adopted.
TRAVEL DIRECTION
Change in the travel direction of the vehicle is calculated by a gyroscope (angular velocity sensor) and a GPS
antenna (GPS information). As the gyroscope and GPS antenna have both merit and demerit, input signals
from them are prioritized in each situation. However, this order of priority may change in accordance with more
detailed travel conditions so that the travel direction is detected more accurately.
MAP-MATCHING
Map-matching is a function that repositions the vehicle on the road
map when a new location is judged to be the most accurate. This is
done by comparing the current vehicle position, calculated by the
method described in the position detection principle, with the road
map data around the vehicle, read from the map DVD-ROM stored in
the DVD-ROM drive.
Therefore, the vehicle position may not be corrected after the vehicle
is driven over a certain distance or time in which GPS information is
hard to receive. In this case, the current location mark on the display
must be corrected manually.
CAUTION:
The road map data is based on data stored in the map DVD-
ROM.
SKIA6215E
SEL684V
Type Advantage Disadvantage
Gyroscope
(angular velocity sensor)
Can detect the vehicle's turning angle
quite accurately.Direction errors may accumulate when the vehicle is
driven for long distances without stopping.
GPS antenna
(GPS information)
Can detect the vehicle's travel direction
(North/South/East/West).Correct direction cannot be detected when the vehicle
speed is low.
SEL685V
Page 807 of 4731
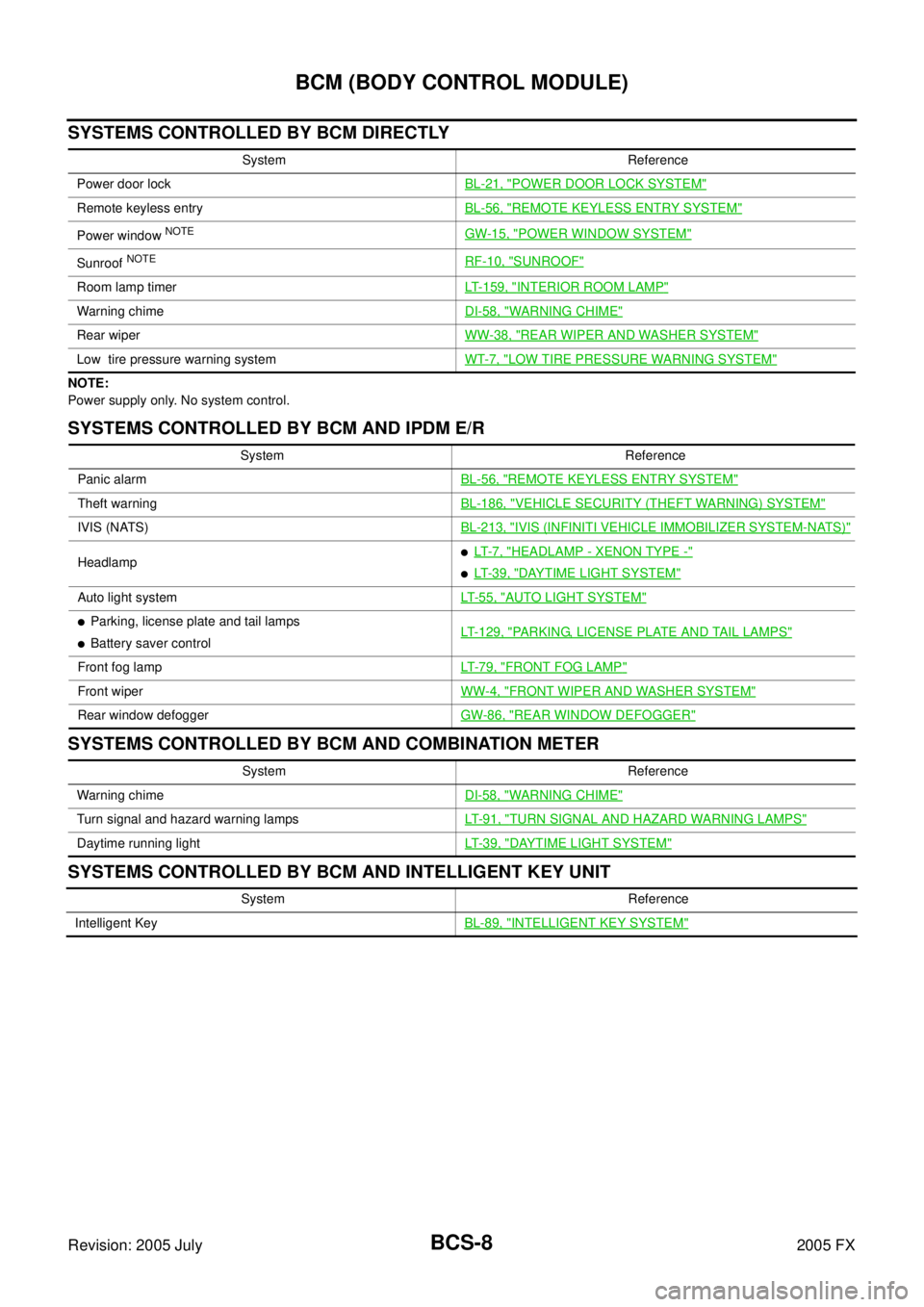
BCS-8
BCM (BODY CONTROL MODULE)
Revision: 2005 July 2005 FX
SYSTEMS CONTROLLED BY BCM DIRECTLY
NOTE:
Power supply only. No system control.
SYSTEMS CONTROLLED BY BCM AND IPDM E/R
SYSTEMS CONTROLLED BY BCM AND COMBINATION METER
SYSTEMS CONTROLLED BY BCM AND INTELLIGENT KEY UNIT
System Reference
Power door lock BL-21, "
POWER DOOR LOCK SYSTEM"
Remote keyless entryBL-56, "REMOTE KEYLESS ENTRY SYSTEM"
Power window NOTEGW-15, "POWER WINDOW SYSTEM"
Sunroof NOTERF-10, "SUNROOF"
Room lamp timerLT-159, "INTERIOR ROOM LAMP"
Warning chimeDI-58, "WARNING CHIME"
Rear wiperWW-38, "REAR WIPER AND WASHER SYSTEM"
Low tire pressure warning systemWT-7, "LOW TIRE PRESSURE WARNING SYSTEM"
System Reference
Panic alarm BL-56, "
REMOTE KEYLESS ENTRY SYSTEM"
Theft warningBL-186, "VEHICLE SECURITY (THEFT WARNING) SYSTEM"
IVIS (NATS)BL-213, "IVIS (INFINITI VEHICLE IMMOBILIZER SYSTEM-NATS)"
HeadlampLT- 7 , "HEADLAMP - XENON TYPE -"
LT- 3 9 , "DAYTIME LIGHT SYSTEM"
Auto light systemLT- 5 5 , "AUTO LIGHT SYSTEM"
Parking, license plate and tail lamps
Battery saver control LT-129, "PARKING, LICENSE PLATE AND TAIL LAMPS"
Front fog lamp
LT- 7 9 , "FRONT FOG LAMP"
Front wiperWW-4, "FRONT WIPER AND WASHER SYSTEM"
Rear window defoggerGW-86, "REAR WINDOW DEFOGGER"
System Reference
Warning chime DI-58, "
WARNING CHIME"
Turn signal and hazard warning lampsLT- 9 1 , "TURN SIGNAL AND HAZARD WARNING LAMPS"
Daytime running lightLT- 3 9 , "DAYTIME LIGHT SYSTEM"
System Reference
Intelligent Key BL-89, "
INTELLIGENT KEY SYSTEM"
Page 1144 of 4731
![INFINITI FX35 2005 Service Manual PRECAUTIONS BRC-3
[VDC/TCS/ABS]
C
D E
G H
I
J
K L
M A
B
BRC
Revision: 2005 July 2005 FX
[VDC/TCS/ABS]PRECAUTIONSPFP:00001
Precautions for Supplemental Restraint System (SRS) “AIR BAG” INFINITI FX35 2005 Service Manual PRECAUTIONS BRC-3
[VDC/TCS/ABS]
C
D E
G H
I
J
K L
M A
B
BRC
Revision: 2005 July 2005 FX
[VDC/TCS/ABS]PRECAUTIONSPFP:00001
Precautions for Supplemental Restraint System (SRS) “AIR BAG”](/img/42/57020/w960_57020-1143.png)
PRECAUTIONS BRC-3
[VDC/TCS/ABS]
C
D E
G H
I
J
K L
M A
B
BRC
Revision: 2005 July 2005 FX
[VDC/TCS/ABS]PRECAUTIONSPFP:00001
Precautions for Supplemental Restraint System (SRS) “AIR BAG” and “SEAT
BELT PRE-TENSIONER”
AFS00289
The Supplemental Restraint System such as “AIR BAG” and “SEAT BELT PRE-TENSIONER”, used along
with a front seat belt, helps to reduce the risk or severity of injury to the driver and front passenger for certain
types of collision. This system includes seat belt switch inputs and dual stage front air bag modules. The SRS
system uses the seat belt switches to determine the front air bag deployment, and may only deploy one front
air bag, depending on the severity of a collision and whether the front occupants are belted or unbelted.
Information necessary to service the system safely is included in the SRS and SB section of this Service Man-
ual.
WARNING:
To avoid rendering the SRS inoperative, which could increase the risk of personal injury or death
in the event of a collision which would result in air bag inflation, all maintenance must be per-
formed by an authorized NISSAN/INFINITI dealer.
Improper maintenance, including incorrect removal and installation of the SRS, can lead to per-
sonal injury caused by unintentional activation of the system. For removal of Spiral Cable and Air
Bag Module, see the SRS section.
Do not use electrical test equipment on any circuit related to the SRS unless instructed to in this
Service Manual. SRS wiring harnesses can be identified by yellow and/or orange harnesses or
harness connectors.
Precautions for Brake SystemAFS001S3
Recommended fluid is brake fluid “DOT 3”.
Do not reuse drained brake fluid.
Be careful not to splash brake fluid on painted areas such as body. If brake fluid is splashed, wipe it off
and flush area with water immediately.
Do not use mineral oils such as gasoline or kerosene to clean. They will ruin rubber parts and cause
improper operation.
Using a flare nut crowfoot and torque wrench, securely tighten
brake tube flare nuts.
Brake system is an important safety part. If a brake fluid leak is
detected, always disassemble the affected part. If a malfunction
is detected, replace part with a new one.
Before working, turn ignition switch OFF and disconnect electri-
cal connectors of ABS actuator and electric unit (control unit) or
battery negative terminal.
When installing brake piping, be sure to check torque.
WARNING:
Clean brake pads and shoes with a waste cloth, then wipe with
a dust collector.
Precautions for Brake ControlAFS001S4
During VDC/TCS/ABS operation, brake pedal lightly vibrates and a mechanical noise may be heard. This
is normal.
Just after starting vehicle after turning ignition switch ON, brake pedal may vibrate or motor operating
noise may be heard from engine room. This is a normal status of operation check.
Stopping distance may be longer than that of vehicles without ABS when vehicle drives on rough, gravel,
or snow-covered (fresh, deep snow) roads.
When an error is indicated by ABS or another warning lamp, collect all necessary information from cus-
tomer (what symptoms are present under what conditions) and check for simple causes before starting
diagnostic servicing. Besides electrical system inspection, check booster operation, brake fluid level, and
fluid leaks.
If tire size and type are used in an improper combination, or brake pads are not Genuine NISSAN parts,
stopping distance or steering stability may deteriorate.
SBR686C
Page 3219 of 4731
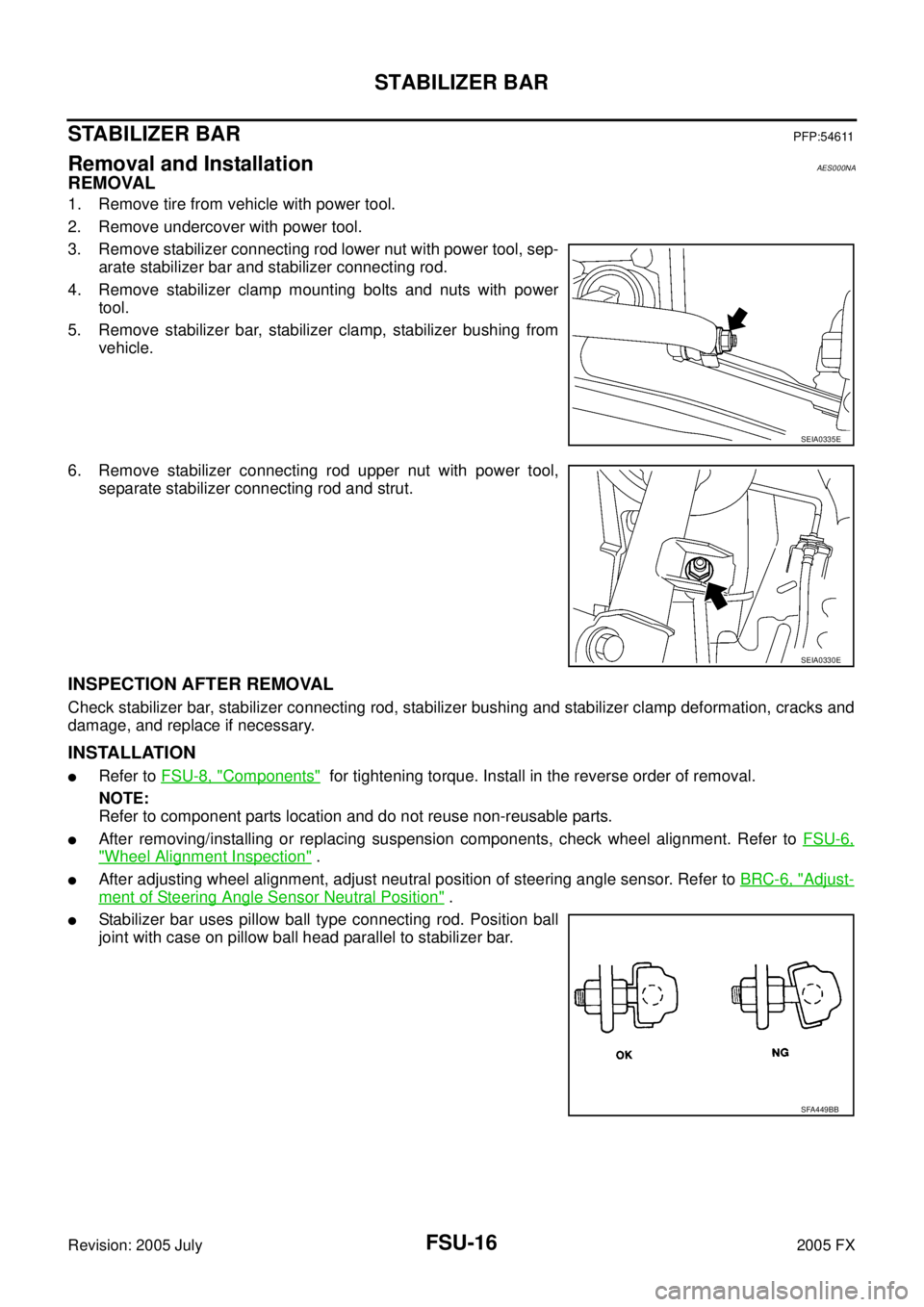
FSU-16
STABILIZER BAR
Revision: 2005 July 2005 FX
STABILIZER BARPFP:54611
Removal and InstallationAES000NA
REMOVAL
1. Remove tire from vehicle with power tool.
2. Remove undercover with power tool.
3. Remove stabilizer connecting rod lower nut with power tool, sep- arate stabilizer bar and stabilizer connecting rod.
4. Remove stabilizer clamp mounting bolts and nuts with power tool.
5. Remove stabilizer bar, stabilizer clamp, stabilizer bushing from vehicle.
6. Remove stabilizer connecting rod upper nut with power tool, separate stabilizer connecting rod and strut.
INSPECTION AFTER REMOVAL
Check stabilizer bar, stabilizer connecting rod, stabilizer bushing and stabilizer clamp deformation, cracks and
damage, and replace if necessary.
INSTALLATION
Refer to FSU-8, "Components" for tightening torque. Install in the reverse order of removal.
NOTE:
Refer to component parts location and do not reuse non-reusable parts.
After removing/installing or replacing suspension components, check wheel alignment. Refer to FSU-6,
"Wheel Alignment Inspection" .
After adjusting wheel alignment, adjust neutral position of steering angle sensor. Refer to BRC-6, "Adjust-
ment of Steering Angle Sensor Neutral Position" .
Stabilizer bar uses pillow ball type connecting rod. Position ball
joint with case on pillow ball head parallel to stabilizer bar.
SEIA0335E
SEIA0330E
SFA449BB
Page 3924 of 4731
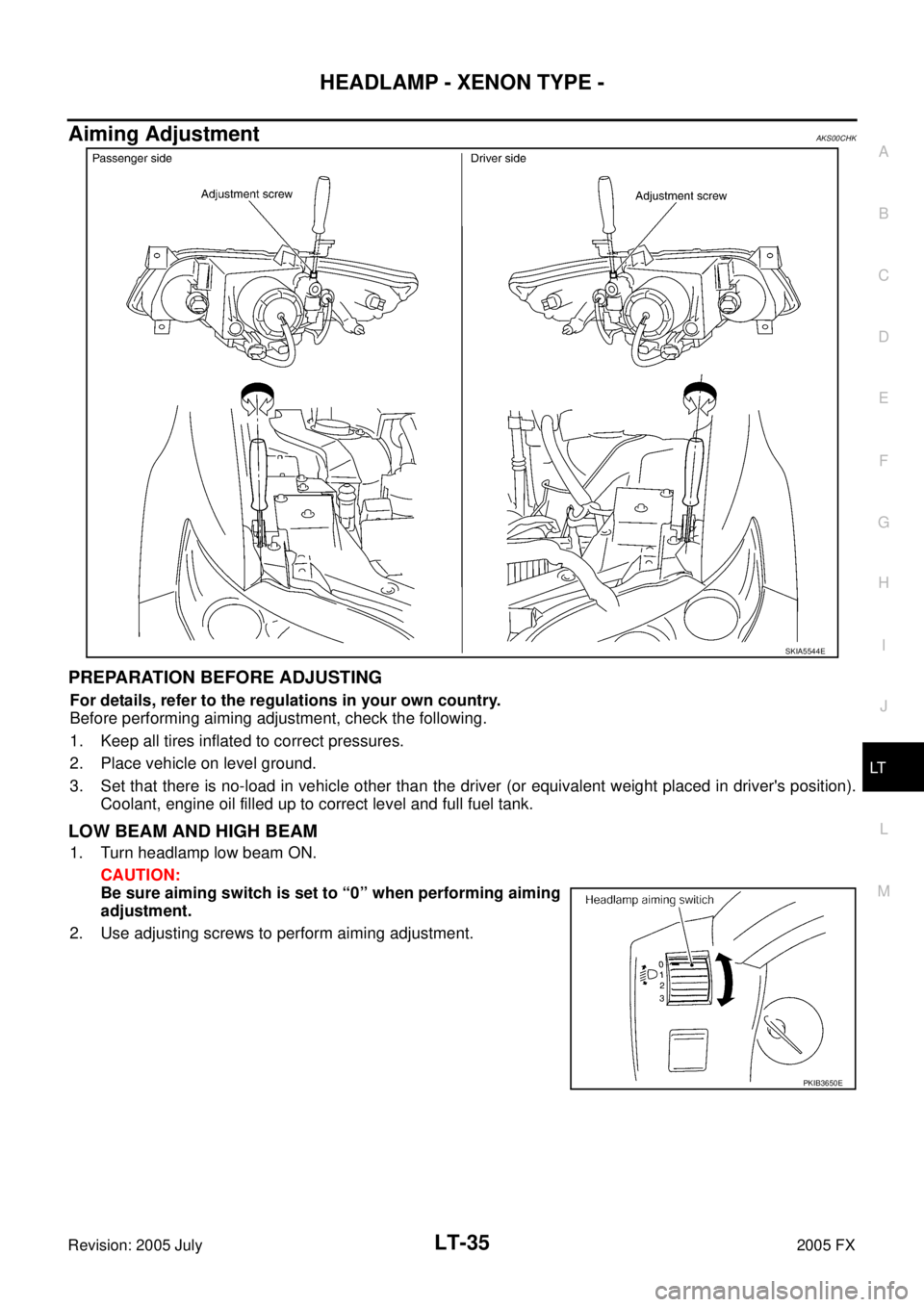
HEADLAMP - XENON TYPE - LT-35
C
D E
F
G H
I
J
L
M A
B
LT
Revision: 2005 July 2005 FX
Aiming AdjustmentAKS00CHK
PREPARATION BEFORE ADJUSTING
For details, refer to the regulations in your own country.
Before performing aiming adjustment, check the following.
1. Keep all tires inflated to correct pressures.
2. Place vehicle on level ground.
3. Set that there is no-load in vehicle other than the driver (or equivalent weight placed in driver's position). Coolant, engine oil filled up to correct level and full fuel tank.
LOW BEAM AND HIGH BEAM
1. Turn headlamp low beam ON.
CAUTION:
Be sure aiming switch is set to “0” when performing aiming
adjustment.
2. Use adjusting screws to perform aiming adjustment.
SKIA5544E
PKIB3650E
Page 3978 of 4731
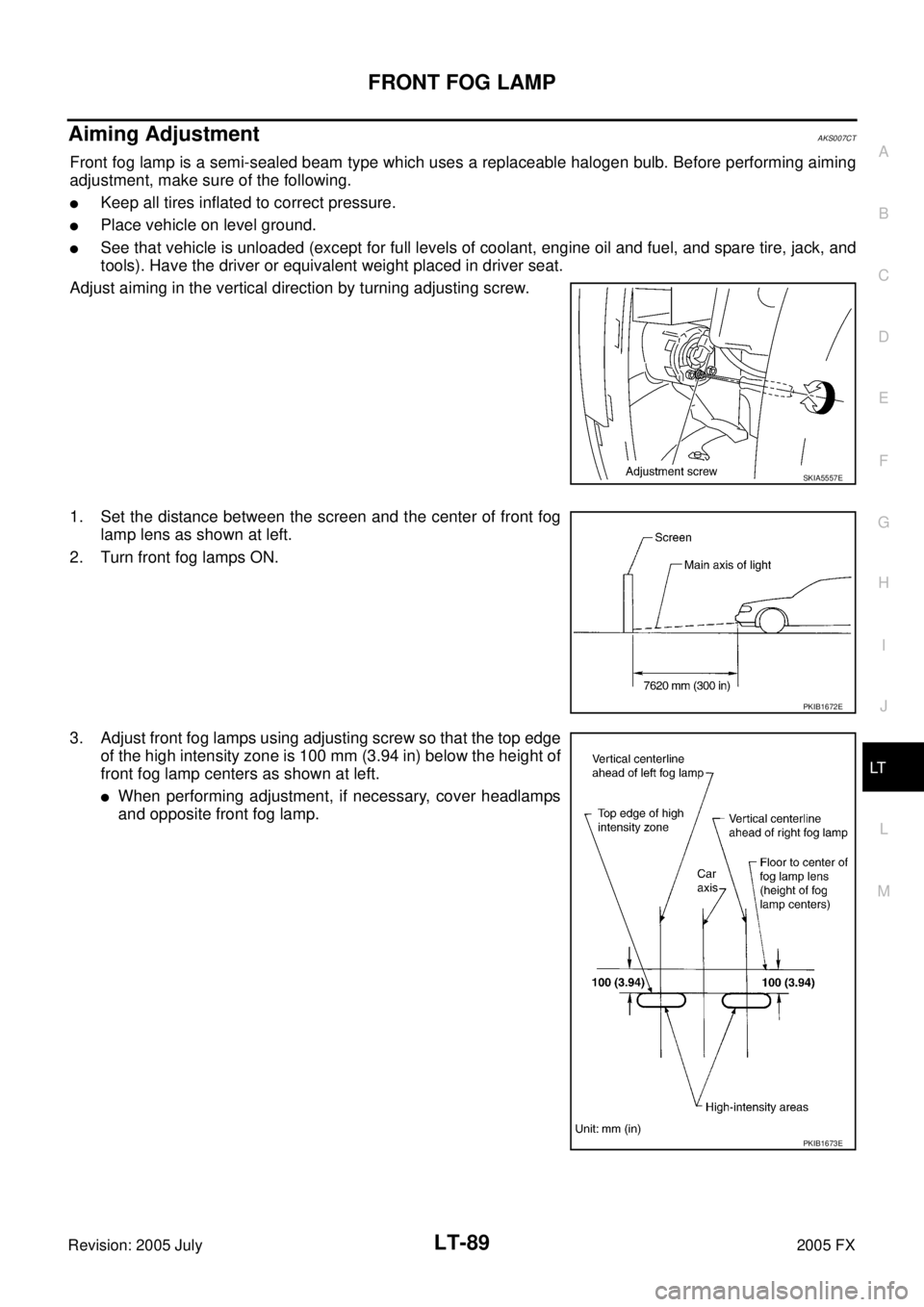
FRONT FOG LAMP LT-89
C
D E
F
G H
I
J
L
M A
B
LT
Revision: 2005 July 2005 FX
Aiming AdjustmentAKS007CT
Front fog lamp is a semi-sealed beam type which uses a replaceable halogen bulb. Before performing aiming
adjustment, make sure of the following.
Keep all tires inflated to correct pressure.
Place vehicle on level ground.
See that vehicle is unloaded (except for full levels of coolant, engine oil and fuel, and spare tire, jack, and
tools). Have the driver or equivalent weight placed in driver seat.
Adjust aiming in the vertical direction by turning adjusting screw.
1. Set the distance between the screen and the center of front fog lamp lens as shown at left.
2. Turn front fog lamps ON.
3. Adjust front fog lamps using adjusting screw so that the top edge of the high intensity zone is 100 mm (3.94 in) below the height of
front fog lamp centers as shown at left.
When performing adjustment, if necessary, cover headlamps
and opposite front fog lamp.
SKIA5557E
PKIB1672E
PKIB1673E
Page 4128 of 4731
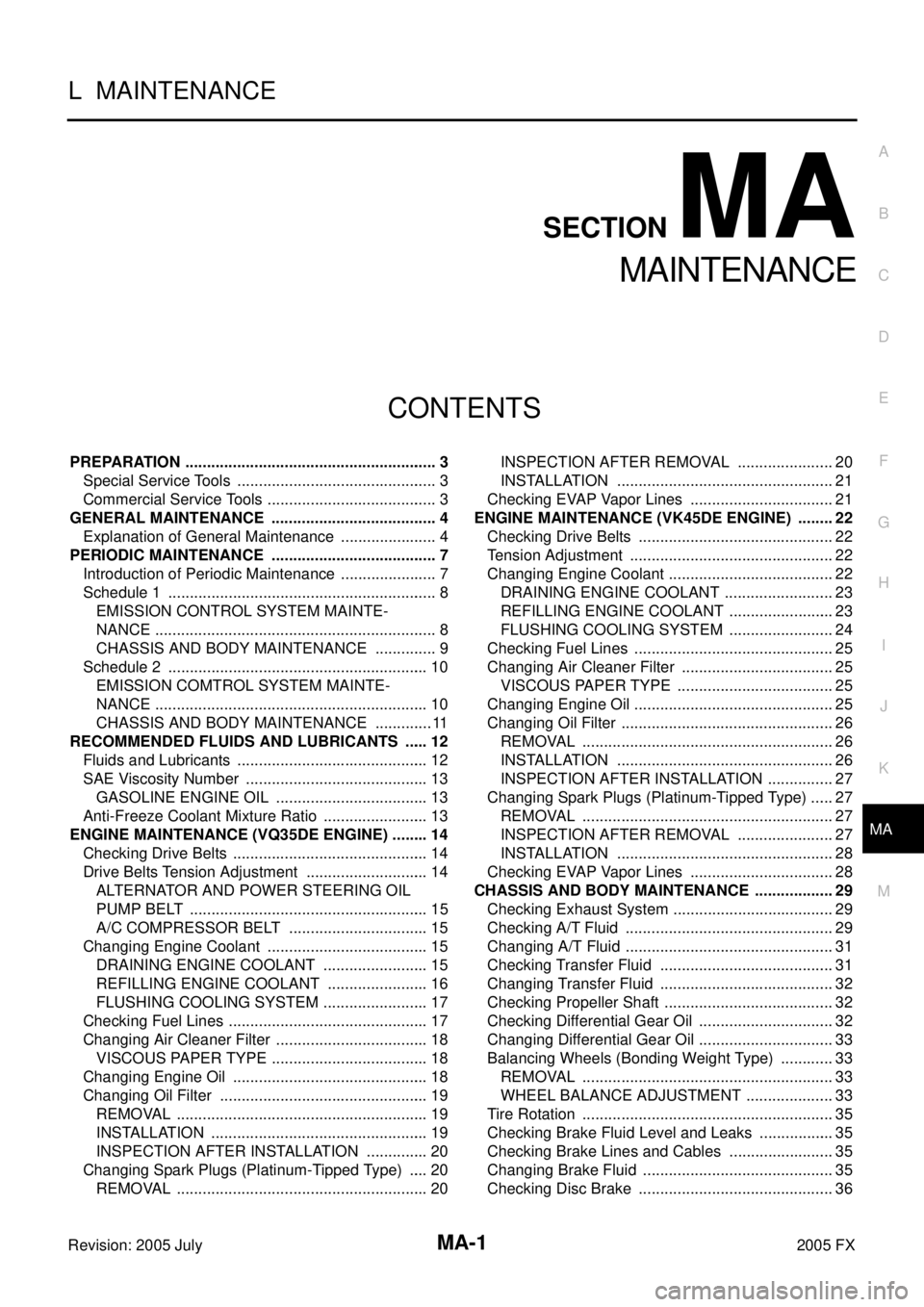
MA-1
MAINTENANCE
L MAINTENANCE
CONTENTS
C
D E
F
G H
I
J
K
M
SECTION MA
A
B
MA
Revision: 2005 July 2005 FX
MAINTENANCE
PREPARATION ........................................................... 3
Special Service Tools .......................................... ..... 3
Commercial Service Tools ................................... ..... 3
GENERAL MAINTENANCE .................................. ..... 4
Explanation of General Maintenance .................. ..... 4
PERIODIC MAINTENANCE .................................. ..... 7
Introduction of Periodic Maintenance .................. ..... 7
Schedule 1 .......................................................... ..... 8
EMISSION CONTROL SYSTEM MAINTE-
NANCE ............................................................. ..... 8
CHASSIS AND BODY MAINTENANCE .......... ..... 9
Schedule 2 .......................................................... ... 10
EMISSION COMTROL SYSTEM MAINTE-
NANCE ............................................................. ... 10
CHASSIS AND BODY MAINTENANCE .......... .... 11
RECOMMENDED FLUIDS AND LUBRICANTS ... ... 12
Fluids and Lubricants .......................................... ... 12
SAE Viscosity Number ........................................ ... 13
GASOLINE ENGINE OIL ................................. ... 13
Anti-Freeze Coolant Mixture Ratio ...................... ... 13
ENGINE MAINTENANCE (VQ35DE ENGINE) ...... ... 14
Checking Drive Belts ........................................... ... 14
Drive Belts Tension Adjustment .......................... ... 14
ALTERNATOR AND POWER STEERING OIL
PUMP BELT ..................................................... ... 15
A/C COMPRESSOR BELT .............................. ... 15
Changing Engine Coolant ................................... ... 15
DRAINING ENGINE COOLANT ...................... ... 15
REFILLING ENGINE COOLANT ..................... ... 16
FLUSHING COOLING SYSTEM ...................... ... 17
Checking Fuel Lines ............................................ ... 17
Changing Air Cleaner Filter ................................. ... 18
VISCOUS PAPER TYPE .................................. ... 18
Changing Engine Oil ........................................... ... 18
Changing Oil Filter .............................................. ... 19
REMOVAL ........................................................ ... 19
INSTALLATION ................................................ ... 19
INSPECTION AFTER INSTALLATION ............ ... 20
Changing Spark Plugs (Platinum-Tipped Type) .. ... 20
REMOVAL ........................................................ ... 20 INSPECTION AFTER REMOVAL ....................
... 20
INSTALLATION ................................................ ... 21
Checking EVAP Vapor Lines ............................... ... 21
ENGINE MAINTENANCE (VK45DE ENGINE) ...... ... 22
Checking Drive Belts ........................................... ... 22
Tension Adjustment ............................................. ... 22
Changing Engine Coolant .................................... ... 22
DRAINING ENGINE COOLANT ....................... ... 23
REFILLING ENGINE COOLANT ...................... ... 23
FLUSHING COOLING SYSTEM ...................... ... 24
Checking Fuel Lines ............................................ ... 25
Changing Air Cleaner Filter ................................. ... 25
VISCOUS PAPER TYPE .................................. ... 25
Changing Engine Oil ............................................ ... 25
Changing Oil Filter ............................................... ... 26
REMOVAL ........................................................ ... 26
INSTALLATION ................................................ ... 26
INSPECTION AFTER INSTALLATION ............. ... 27
Changing Spark Plugs (Platinum-Tipped Type) ... ... 27
REMOVAL ........................................................ ... 27
INSPECTION AFTER REMOVAL .................... ... 27
INSTALLATION ................................................ ... 28
Checking EVAP Vapor Lines ............................... ... 28
CHASSIS AND BODY MAINTENANCE ................ ... 29
Checking Exhaust System ................................... ... 29
Checking A/T Fluid .............................................. ... 29
Changing A/T Fluid .............................................. ... 31
Checking Transfer Fluid ...................................... ... 31
Changing Transfer Fluid ...................................... ... 32
Checking Propeller Shaft ..................................... ... 32
Checking Differential Gear Oil ............................. ... 32
Changing Differential Gear Oil ............................. ... 33
Balancing Wheels (Bonding Weight Type) .......... ... 33
REMOVAL ........................................................ ... 33
WHEEL BALANCE ADJUSTMENT .................. ... 33
Tire Rotation ........................................................ ... 35
Checking Brake Fluid Level and Leaks ............... ... 35
Checking Brake Lines and Cables ...................... ... 35
Changing Brake Fluid .......................................... ... 35
Checking Disc Brake ........................................... ... 36
Page 4136 of 4731
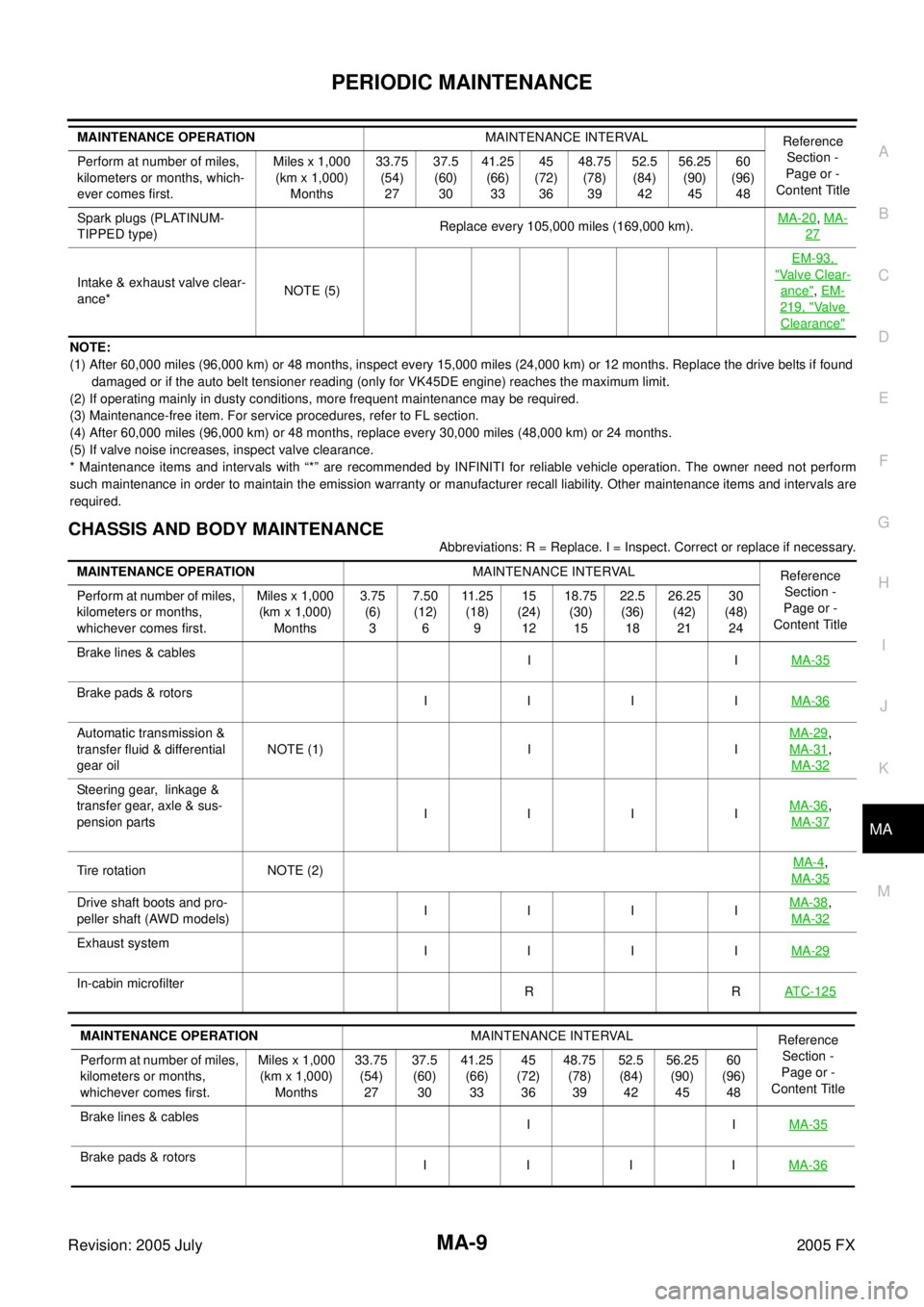
PERIODIC MAINTENANCE MA-9
C
D E
F
G H
I
J
K
M A
B
MA
Revision: 2005 July 2005 FX
NOTE:
(1) After 60,000 miles (96,000 km) or 48 months, inspect every 15,000 miles (24,000 km) or 12 months. Replace the drive belts i f found
damaged or if the auto belt tensioner reading (only for VK45DE engine) reaches the maximum limit.
(2) If operating mainly in dusty conditions, more frequent maintenance may be required.
(3) Maintenance-free item. For service procedures, refer to FL section.
(4) After 60,000 miles (96,000 km) or 48 months, replace every 30,000 miles (48,000 km) or 24 months.
(5) If valve noise increases, inspect valve clearance.
* Maintenance items and intervals with “*” are recommended by INFINITI for reliable vehicle operation. The owner need not perfo rm
such maintenance in order to maintain the emission warranty or manufacturer recall liability. Other maintenance items and inter vals are
required.
CHASSIS AND BODY MAINTENANCE
Abbreviations: R = Replace. I = Inspect. Correct or replace if necessary.
Spark plugs (PLATINUM-
TIPPED type) Replace every 105,000 miles (169,000 km). MA-20
,
MA-
27
Intake & exhaust valve clear-
ance* NOTE (5) EM-93, "Valve Clear-
ance",
EM-
219, "Va l v e
Clearance"
MAINTENANCE OPERATION MAINTENANCE INTERVAL
Reference
Section -
Page or -
Content Title
Perform at number of miles,
kilometers or months, which-
ever comes first. Miles x 1,000
(km x 1,000) Months 33.75
(54) 27 37.5
(60) 30 41.25
(66) 33 45
(72) 36 48.75
(78) 39 52.5
(84) 42 56.25
(90) 45 60
(96) 48
MAINTENANCE OPERATION MAINTENANCE INTERVAL
Reference
Section -
Page or -
Content Title
Perform at number of miles,
kilometers or months,
whichever comes first. Miles x 1,000
(km x 1,000)
Months 3.75
(6)
3 7.50
(12)
6 11 . 2 5
(18)
9 15
(24)
12 18.75
(30)
15 22.5
(36)
18 26.25
(42)
21 30
(48)
24
Brake lines & cables II MA-35
Brake pads & rotors
IIII MA-36
Automatic transmission &
transfer fluid & differential
gear oil NOTE (1) I I MA-29,
MA-31
,
MA-32
Steering gear, linkage &
transfer gear, axle & sus-
pension parts IIII MA-36
,
MA-37
Tire rotation NOTE (2) MA-4,
MA-35
Drive shaft boots and pro-
peller shaft (AWD models) IIII MA-38,
MA-32
Exhaust system IIII MA-29
In-cabin microfilter
RR AT C - 1 2 5
MAINTENANCE OPERATION MAINTENANCE INTERVAL
Reference
Section -
Page or -
Content Title
Perform at number of miles,
kilometers or months,
whichever comes first. Miles x 1,000
(km x 1,000)
Months 33.75
(54)
27 37.5
(60)
30 41.25
(66)
33 45
(72)
36 48.75
(78)
39 52.5
(84)
42 56.25
(90)
45 60
(96)
48
Brake lines & cables II MA-35
Brake pads & rotors
I III MA-36
Page 4137 of 4731
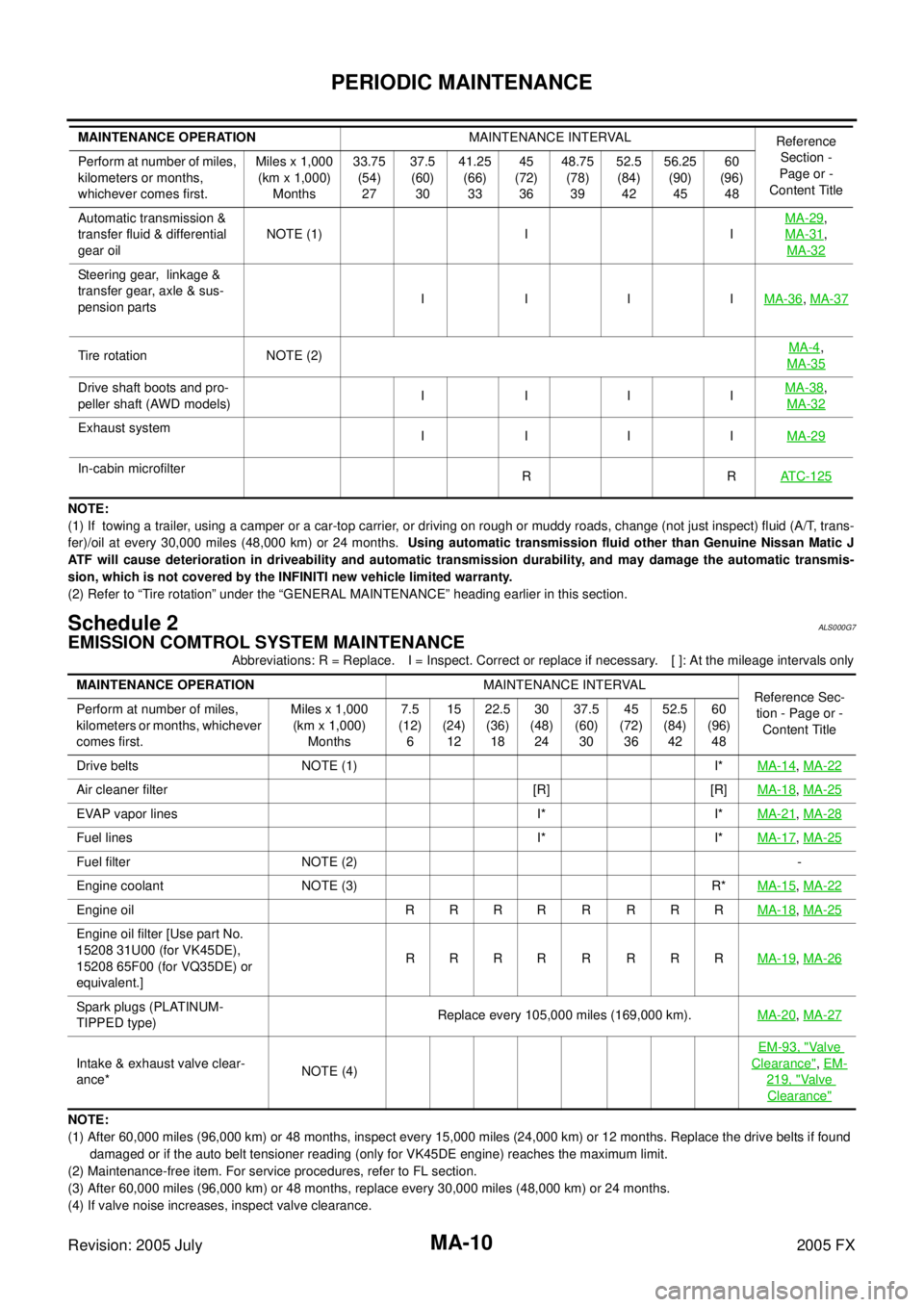
MA-10
PERIODIC MAINTENANCE
Revision: 2005 July 2005 FX
NOTE:
(1) If towing a trailer, using a camper or a car-top carrier, or driving on rough or muddy roads, change (not just inspect) fl uid (A/T, trans-
fer)/oil at every 30,000 miles (48,000 km) or 24 months. Using automatic transmission fluid other than Genuine Nissan Matic J
ATF will cause deterioration in driveability and automatic transmission durability, and may damage the automatic transmis-
sion, which is not covered by the INFINITI new vehicle limited warranty.
(2) Refer to “Tire rotation” under the “GENERAL MAINTENANCE” heading earlier in this section.
Schedule 2ALS000G7
EMISSION COMTROL SYSTEM MAINTENANCE
Abbreviations: R = Replace. I = Inspect. Correct or replace if necessary. [ ]: At the mileage intervals only
NOTE:
(1) After 60,000 miles (96,000 km) or 48 months, inspect every 15,000 miles (24,000 km) or 12 months. Replace the drive belts i f found
damaged or if the auto belt tensioner reading (only for VK45DE engine) reaches the maximum limit.
(2) Maintenance-free item. For service procedures, refer to FL section.
(3) After 60,000 miles (96,000 km) or 48 months, replace every 30,000 miles (48,000 km) or 24 months.
(4) If valve noise increases, inspect valve clearance. Automatic transmission &
transfer fluid & differential
gear oil NOTE (1) I I
MA-29
,
MA-31
,
MA-32
Steering gear, linkage &
transfer gear, axle & sus-
pension parts I III
MA-36
, MA-37
Tire rotation NOTE (2) MA-4,
MA-35
Drive shaft boots and pro-
peller shaft (AWD models) I III MA-38,
MA-32
Exhaust system I III MA-29
In-cabin microfilter
RR ATC-125
MAINTENANCE OPERATION MAINTENANCE INTERVAL
Reference
Section -
Page or -
Content Title
Perform at number of miles,
kilometers or months,
whichever comes first. Miles x 1,000
(km x 1,000) Months 33.75
(54) 27 37.5
(60) 30 41.25
(66) 33 45
(72) 36 48.75
(78) 39 52.5
(84) 42 56.25
(90) 45 60
(96) 48
MAINTENANCE OPERATION MAINTENANCE INTERVAL
Reference Sec-
tion - Page or - Content Title
Perform at number of miles,
kilometers or months, whichever
comes first. Miles x 1,000
(km x 1,000) Months 7.5
(12) 6 15
(24) 12 22.5
(36) 18 30
(48) 24 37.5
(60) 30 45
(72) 36 52.5
(84) 42 60
(96) 48
Drive belts NOTE (1) I* MA-14
, MA-22
Air cleaner filter [R] [R] MA-18, MA-25
EVAP vapor lines I* I* MA-21, MA-28
Fuel lines I* I* MA-17, MA-25
Fuel filter NOTE (2) -
Engine coolant NOTE (3) R* MA-15
, MA-22
Engine oil R R R R R R R R MA-18, MA-25
Engine oil filter [Use part No.
15208 31U00 (for VK45DE),
15208 65F00 (for VQ35DE) or
equivalent.] RRRR R RRR
MA-19
, MA-26
Spark plugs (PLATINUM-
TIPPED type) Replace every 105,000 miles (169,000 km).
MA-20, MA-27
Intake & exhaust valve clear-
ance* NOTE (4) EM-93, "
Va l v e
Clearance",
EM-
219, "Va l v e
Clearance"