sensor INFINITI FX35 2008 Service Manual
[x] Cancel search | Manufacturer: INFINITI, Model Year: 2008, Model line: FX35, Model: INFINITI FX35 2008Pages: 3924, PDF Size: 81.37 MB
Page 3088 of 3924
![INFINITI FX35 2008 Service Manual
LAN-68
< SERVICE INFORMATION >[CAN]
TROUBLE DIAGNOSIS
Component Parts Location
INFOID:0000000001328647
Harness LayoutINFOID:0000000001328648
Refer to PG-40, "Harness Layout".
Malfunction Area ChartI INFINITI FX35 2008 Service Manual
LAN-68
< SERVICE INFORMATION >[CAN]
TROUBLE DIAGNOSIS
Component Parts Location
INFOID:0000000001328647
Harness LayoutINFOID:0000000001328648
Refer to PG-40, "Harness Layout".
Malfunction Area ChartI](/img/42/57017/w960_57017-3087.png)
LAN-68
< SERVICE INFORMATION >[CAN]
TROUBLE DIAGNOSIS
Component Parts Location
INFOID:0000000001328647
Harness LayoutINFOID:0000000001328648
Refer to PG-40, "Harness Layout".
Malfunction Area ChartINFOID:0000000001328649
MAIN LINE
BRANCH LINE
1. AWD control unit M92 2. ICC unit M88 3. ECM M90
4. IPDM E/R E9 5. ICC sensor E39 6. Display control unit M76
7. Unified meter and A/C amp. M55 8. Steering angle sensor M14 9. Intelligent Key unit M34
10. ABS actuator and el ectric unit (con-
trol unit) E56 11. BCM M3 12. Data link connector M5
13. LDW camera unit R9 14. Driver seat control unit B152 15. A/T assembly F44
16. Air bag diagnosis sensor unit M72
PKID0616E
Malfunction Area Reference
Main line between TCM and data link connector LAN-69, "
Main Line Between TCM and Data Link Connector"
Main line between data link connector and unified meter and A/C
amp.LAN-69, "Main Line Between Data Link Connector and Unified
Meter and A/C Amp."
Main line betwee
n unified meter and A/C amp. and ABS actuator
and electric unit (control unit) LAN-70, "Main Line Between Unified Meter and A/C Amp. and
ABS Actuator and Electric Unit (Control Unit)"
Main line between ABS actuator and electric unit (control unit)
and driver seat control unitLAN-71, "Main Line Between ABS Actuator and Electric Unit
(Control Unit) and Driver Seat Control Unit"
Malfunction Area Reference
ECM branch line circuit LAN-72, "
ECM Branch Line Circuit"
AWD control unit branch line circuit LAN-72, "AWD Control Unit Branch Line Circuit"
Display control unit branch line circuit LAN-73, "Display Control Unit Branch Line Circuit"
ICC unit branch line circuitLAN-74, "ICC Unit Branch Line Circuit"
TCM branch line circuit LAN-74, "TCM Branch Line Circuit"
BCM branch line circuit LAN-75, "BCM Branch Line Circuit"
3AA93ABC3ACD3AC03ACA3AC03AC63AC53A913A773A893A873A873A8E3A773A983AC73AC93AC03AC3
3A893A873A873A8F3A773A9D3AAF3A8A3A8C3A863A9D3AAF3A8B3A8C
Page 3089 of 3924
![INFINITI FX35 2008 Service Manual
TROUBLE DIAGNOSISLAN-69
< SERVICE INFORMATION > [CAN]
C
D
E
F
G H
I
J
L
M A
B
LAN
N
O P
SHORT CIRCUIT
Main Line Between TCM an d Data Link ConnectorINFOID:0000000001328650
INSPECTION PROCEDURE
1.CHEC INFINITI FX35 2008 Service Manual
TROUBLE DIAGNOSISLAN-69
< SERVICE INFORMATION > [CAN]
C
D
E
F
G H
I
J
L
M A
B
LAN
N
O P
SHORT CIRCUIT
Main Line Between TCM an d Data Link ConnectorINFOID:0000000001328650
INSPECTION PROCEDURE
1.CHEC](/img/42/57017/w960_57017-3088.png)
TROUBLE DIAGNOSISLAN-69
< SERVICE INFORMATION > [CAN]
C
D
E
F
G H
I
J
L
M A
B
LAN
N
O P
SHORT CIRCUIT
Main Line Between TCM an d Data Link ConnectorINFOID:0000000001328650
INSPECTION PROCEDURE
1.CHECK HARNESS CONTINUITY (OPEN CIRCUIT)
1. Turn the ignition switch OFF.
2. Disconnect the battery cabl e from the negative terminal.
3. Disconnect the following harness connectors.
-ECM
- Harness connectors M82 and F102
4. Check the continuity between the har ness connector and the data link connector.
OK or NG
OK >> Present error: Check the following items again. - Decision of CAN system type.
- Not received CONSULT-III data [SELF-DIAG RESULTS, CAN DIAG SUPPORT MNTR (“ECU
list” included)].
- Not copied from on-board diagnosis.
- Procedure for detecting root cause.
Past error: Error was detected in the main line between the TCM and the data link connector.
NG >> Repair the main line between the harness connector M82 and the data link connector.
Main Line Between Data Link Conne ctor and Unified Meter and A/C Amp.INFOID:0000000001328651
INSPECTION PROCEDURE
1.CHECK HARNESS CONTI NUITY (OPEN CIRCUIT)
1. Turn the ignition switch OFF.
2. Disconnect the battery cabl e from the negative terminal.
3. Disconnect the following harness connectors.
-ECM
- Unified meter and A/C amp.
4. Check the continuity between the data link c onnector and the unified meter and A/C amp. harness con-
nector.
Data link connector branch line circuit LAN-75, "Data Link Connector Branch Line Circuit"
Intelligent Key unit branch line circuitLAN-76, "Intelligent Key Unit Branch Line Circuit"
LDW camera unit branch line circuitLAN-76, "LDW Camera Unit Branch Line Circuit"
Steering angle sensor branch line circuit LAN-77, "Steering Angle Sensor Branch Line Circuit"
Unified meter and A/C amp. branch line circuit LAN-78, "Unified Meter and A/C Amp. Branch Line Circuit"
ABS actuator and electric unit (control unit) branch line circuit LAN-78, "ABS Actuator and Electric Unit (Control Unit) Branch
Line Circuit"
ICC sensor branch line circuit
LAN-79, "ICC Sensor Branch Line Circuit"
Driver seat control unit branch line circuitLAN-79, "Driver Seat Control Unit Branch Line Circuit"
IPDM E/R branch line circuit LAN-80, "IPDM E/R Branch Line Circuit"
Malfunction Area Reference
Malfunction Area Reference
CAN communication circuit LAN-81, "
CAN Communication Circuit"
Harness connector Data link connector
Continuity
Connector No. Terminal No. Connector No. Terminal No.
M82 14H
M5 6Yes
15H 14 Yes
3AA93ABC3ACD3AC03ACA3AC03AC63AC53A913A773A893A873A873A8E3A773A983AC73AC93AC03AC3
3A893A873A873A8F3A773A9D3AAF3A8A3A8C3A863A9D3AAF3A8B3A8C
Page 3095 of 3924
![INFINITI FX35 2008 Service Manual
TROUBLE DIAGNOSISLAN-75
< SERVICE INFORMATION > [CAN]
C
D
E
F
G H
I
J
L
M A
B
LAN
N
O P
OK >> GO TO 3.
NG >> Repair the TCM branch line.
3.CHECK POWER SUPPLY AND GROUND CIRCUIT
Check the power supply INFINITI FX35 2008 Service Manual
TROUBLE DIAGNOSISLAN-75
< SERVICE INFORMATION > [CAN]
C
D
E
F
G H
I
J
L
M A
B
LAN
N
O P
OK >> GO TO 3.
NG >> Repair the TCM branch line.
3.CHECK POWER SUPPLY AND GROUND CIRCUIT
Check the power supply](/img/42/57017/w960_57017-3094.png)
TROUBLE DIAGNOSISLAN-75
< SERVICE INFORMATION > [CAN]
C
D
E
F
G H
I
J
L
M A
B
LAN
N
O P
OK >> GO TO 3.
NG >> Repair the TCM branch line.
3.CHECK POWER SUPPLY AND GROUND CIRCUIT
Check the power supply and the ground circuit of the TCM. Refer to AT-161, "
Diagnosis Procedure".
OK or NG
OK >> Present error: Replace the control valve with TCM. Refer to AT-215, "Control Valve with TCM
and A/T Fluid Temperature Sensor 2".
Past error: Error was detected in the TCM branch line.
NG >> Repair the power supply and the ground circuit.
BCM Branch Line CircuitINFOID:0000000001328659
INSPECTION PROCEDURE
1.CHECK CONNECTOR
1. Turn the ignition switch OFF.
2. Disconnect the battery cabl e from the negative terminal.
3. Check the terminals and connectors of the BC M for damage, bend and loose connection (unit side and
connector side).
OK or NG
OK >> GO TO 2.
NG >> Repair the terminal and connector.
2.CHECK HARNESS FOR OPEN CIRCUIT
1. Disconnect the connector of BCM.
2. Check the resistance between the BCM harness connector terminals.
OK or NG
OK >> GO TO 3.
NG >> Repair the BCM branch line.
3.CHECK POWER SUPPLY AND GROUND CIRCUIT
Check the power supply and the ground circuit of the BCM. Refer to BCS-10, "
Schematic".
OK or NG
OK >> Present error: Replace the BCM. Refer to BCS-13, "Removal and Installation of BCM".
Past error: Error was detected in the BCM branch line.
NG >> Repair the power supply and the ground circuit.
Data Link Connector Branch Line CircuitINFOID:0000000001328660
INSPECTION PROCEDURE
1.CHECK CONNECTOR
1. Turn the ignition switch OFF.
2. Disconnect the battery cabl e from the negative terminal.
3. Check the terminals and connectors of the data link connector for damage, bend and loose connection (connector side and harness side).
OK or NG
OK >> GO TO 2.
NG >> Repair the terminal and connector.
2.CHECK HARNESS FOR OPEN CIRCUIT
Check the resistance between the data link connector terminals.
BCM harness connector Resistance (Ω)
Connector No. Terminal No.
M3 39 40 Approx. 54 – 66
3AA93ABC3ACD3AC03ACA3AC03AC63AC53A913A773A893A873A873A8E3A773A983AC73AC93AC03AC3
3A893A873A873A8F3A773A9D3AAF3A8A3A8C3A863A9D3AAF3A8B3A8C
Page 3097 of 3924
![INFINITI FX35 2008 Service Manual
TROUBLE DIAGNOSISLAN-77
< SERVICE INFORMATION > [CAN]
C
D
E
F
G H
I
J
L
M A
B
LAN
N
O P
- Harness connector R1
- Harness connector M31
OK or NG
OK >> GO TO 2.
NG >> Repair the terminal and connector. INFINITI FX35 2008 Service Manual
TROUBLE DIAGNOSISLAN-77
< SERVICE INFORMATION > [CAN]
C
D
E
F
G H
I
J
L
M A
B
LAN
N
O P
- Harness connector R1
- Harness connector M31
OK or NG
OK >> GO TO 2.
NG >> Repair the terminal and connector.](/img/42/57017/w960_57017-3096.png)
TROUBLE DIAGNOSISLAN-77
< SERVICE INFORMATION > [CAN]
C
D
E
F
G H
I
J
L
M A
B
LAN
N
O P
- Harness connector R1
- Harness connector M31
OK or NG
OK >> GO TO 2.
NG >> Repair the terminal and connector.
2.CHECK HARNESS FOR OPEN CIRCUIT
1. Disconnect the connector of LDW camera unit.
2. Check the resistance between the LDW camera unit harness connector terminals.
OK or NG
OK >> GO TO 3.
NG >> Repair the LDW camera unit branch line. (Replac e the room lamp harness if error is detected on
the shield line.)
3.CHECK POWER SUPPLY AND GROUND CIRCUIT
Check the power supply and the ground circuit of the LDW camera unit. Re\
fer to DI-84, "
Power Supply and
Ground Circuit Inspection".
OK or NG
OK >> Present error: Replace the LDW camera unit. Refer to DI-91, "Removal and Installation for LDW
Camera Unit".
Past error: Error was detected in the LDW camera unit branch line.
NG >> Repair the power supply and the ground circuit.
Steering Angle Sensor Branch Line CircuitINFOID:0000000001328663
INSPECTION PROCEDURE
1.CHECK CONNECTOR
1. Turn the ignition switch OFF.
2. Disconnect the battery cabl e from the negative terminal.
3. Check the terminals and connectors of the steer ing angle sensor for damage, bend and loose connection
(unit side and connector side).
OK or NG
OK >> GO TO 2.
NG >> Repair the terminal and connector.
2.CHECK HARNESS FOR OPEN CIRCUIT
1. Disconnect the connector of steering angle sensor.
2. Check the resistance between the steering angle sensor harness connector terminals.
OK or NG
OK >> GO TO 3.
NG >> Repair the steering angle sensor branch line.
3.CHECK POWER SUPPLY AND GROUND CIRCUIT
Check the power supply and the ground circuit of the steering angle sensor. Refer to BRC-17, "
Schematic".
OK or NG
OK >> Present error: Replace the steering angle sensor. Refer to BRC-56, "Removal and Installation".
Past error: Error was detected in the steering angle sensor branch line.
LDW camera unit harness connector
Resistance (Ω)
Connector No. Terminal No.
R9 10 5 Approx. 54 – 66
Steering angle sensor harness connector Resistance (Ω)
Connector No. Terminal No.
M14 4 5 Approx. 54 – 66
3AA93ABC3ACD3AC03ACA3AC03AC63AC53A913A773A893A873A873A8E3A773A983AC73AC93AC03AC3
3A893A873A873A8F3A773A9D3AAF3A8A3A8C3A863A9D3AAF3A8B3A8C
Page 3099 of 3924
![INFINITI FX35 2008 Service Manual
TROUBLE DIAGNOSISLAN-79
< SERVICE INFORMATION > [CAN]
C
D
E
F
G H
I
J
L
M A
B
LAN
N
O P
OK >> GO TO 3.
NG >> Repair the ABS actuator and electric unit (control unit) branch line.
3.CHECK POWER SUPPLY INFINITI FX35 2008 Service Manual
TROUBLE DIAGNOSISLAN-79
< SERVICE INFORMATION > [CAN]
C
D
E
F
G H
I
J
L
M A
B
LAN
N
O P
OK >> GO TO 3.
NG >> Repair the ABS actuator and electric unit (control unit) branch line.
3.CHECK POWER SUPPLY](/img/42/57017/w960_57017-3098.png)
TROUBLE DIAGNOSISLAN-79
< SERVICE INFORMATION > [CAN]
C
D
E
F
G H
I
J
L
M A
B
LAN
N
O P
OK >> GO TO 3.
NG >> Repair the ABS actuator and electric unit (control unit) branch line.
3.CHECK POWER SUPPLY AND GROUND CIRCUIT
Check the power supply and the ground circuit of the A BS actuator and electric unit (control unit). Refer to
BRC-17, "
Schematic".
OK or NG
OK >> Present error: Replace the ABS actuator and electric unit (control unit). Refer to BRC-54,
"Removal and Installation".
Past error: Error was detected in the ABS act uator and electric unit (control unit) branch line.
NG >> Repair the power supply and the ground circuit.
ICC Sensor Branch Line CircuitINFOID:0000000001328666
INSPECTION PROCEDURE
1.CHECK CONNECTOR
1. Turn the ignition switch OFF.
2. Disconnect the battery cabl e from the negative terminal.
3. Check the terminals and connectors of the ICC s ensor for damage, bend and loose connection (unit side
and connector side).
OK or NG
OK >> GO TO 2.
NG >> Repair the terminal and connector.
2.CHECK HARNESS FOR OPEN CIRCUIT
1. Disconnect the connector of ICC sensor.
2. Check the resistance between the I CC sensor harness connector terminals.
OK or NG
OK >> GO TO 3.
NG >> Repair the ICC sensor branch line.
3.CHECK POWER SUPPLY AND GROUND CIRCUIT
Check the power supply and the ground circuit of the ICC sensor. Refer to ACS-19, "
Schematic".
OK or NG
OK >> Present error: Replace the ICC sensor. Refer to ACS-65, "ICC Sensor".
Past error: Error was detected in the ICC sensor branch line.
NG >> Repair the power supply and the ground circuit.
Driver Seat Control Un it Branch Line CircuitINFOID:0000000001328667
INSPECTION PROCEDURE
1.CHECK CONNECTOR
1. Turn the ignition switch OFF.
2. Disconnect the battery cabl e from the negative terminal.
3. Check the following terminals and connectors for damage, bend and loose connection (unit side and con-
nector side).
- Driver seat control unit
- Harness connector B151
- Harness connector B8
OK or NG
OK >> GO TO 2.
NG >> Repair the terminal and connector.
ICC sensor harness connector Resistance (Ω)
Connector No. Terminal No.
E39 3 6 Approx. 54 – 66
3AA93ABC3ACD3AC03ACA3AC03AC63AC53A913A773A893A873A873A8E3A773A983AC73AC93AC03AC3
3A893A873A873A8F3A773A9D3AAF3A8A3A8C3A863A9D3AAF3A8B3A8C
Page 3103 of 3924
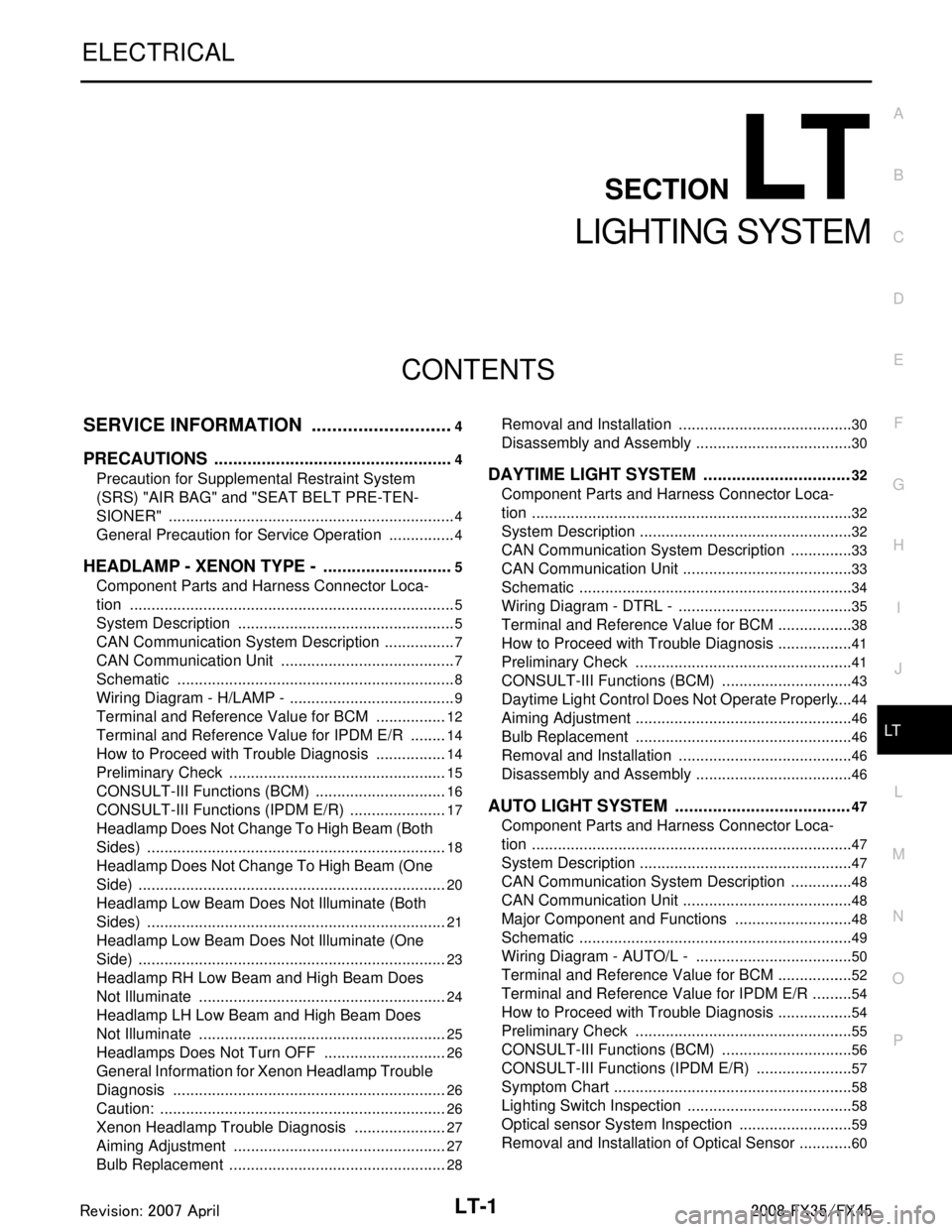
LT-1
ELECTRICAL
C
DE
F
G H
I
J
L
M
SECTION LT
A
B
LT
N
O P
CONTENTS
LIGHTING SYSTEM
SERVICE INFORMATION .. ..........................4
PRECAUTIONS .............................................. .....4
Precaution for Supplemental Restraint System
(SRS) "AIR BAG" and "SEAT BELT PRE-TEN-
SIONER" ............................................................. ......
4
General Precaution for Service Operation ................4
HEADLAMP - XENON TYPE - ............................5
Component Parts and Harness Connector Loca-
tion ...................................................................... ......
5
System Description ...................................................5
CAN Communication System Description .................7
CAN Communication Unit .........................................7
Schematic .................................................................8
Wiring Diagram - H/LAMP - .......................................9
Terminal and Reference Value for BCM .................12
Terminal and Reference Value for IPDM E/R .........14
How to Proceed with Trouble Diagnosis .................14
Preliminary Check ...................................................15
CONSULT-III Functions (BCM) ...............................16
CONSULT-III Functions (IPDM E/R) .......................17
Headlamp Does Not Change To High Beam (Both
Sides) ......................................................................
18
Headlamp Does Not Change To High Beam (One
Side) ........................................................................
20
Headlamp Low Beam Does Not Illuminate (Both
Sides) .................................................................. ....
21
Headlamp Low Beam Does Not Illuminate (One
Side) .................................................................... ....
23
Headlamp RH Low Beam and High Beam Does
Not Illuminate ..........................................................
24
Headlamp LH Low Beam and High Beam Does
Not Illuminate ..........................................................
25
Headlamps Does Not Turn OFF .............................26
General Information for Xenon Headlamp Trouble
Diagnosis ................................................................
26
Caution: ...................................................................26
Xenon Headlamp Trouble Diagnosis ......................27
Aiming Adjustment ..................................................27
Bulb Replacement ...................................................28
Removal and Installation ..................................... ....30
Disassembly and Assembly .....................................30
DAYTIME LIGHT SYSTEM ...............................32
Component Parts and Harness Connector Loca-
tion ....................................................................... ....
32
System Description ..................................................32
CAN Communication System Description ...............33
CAN Communication Unit ........................................33
Schematic ................................................................34
Wiring Diagram - DTRL - .........................................35
Terminal and Reference Value for BCM ..................38
How to Proceed with Trouble Diagnosis ..................41
Preliminary Check ...................................................41
CONSULT-III Functions (BCM) ...............................43
Daytime Light Control Does Not Operate Properly ....44
Aiming Adjustment ...................................................46
Bulb Replacement ...................................................46
Removal and Installation .........................................46
Disassembly and Assembly .....................................46
AUTO LIGHT SYSTEM .....................................47
Component Parts and Harness Connector Loca-
tion ...........................................................................
47
System Description ..................................................47
CAN Communication System Description ...............48
CAN Communication Unit ........................................48
Major Component and Functions ............................48
Schematic ................................................................49
Wiring Diagram - AUTO/L - .....................................50
Terminal and Reference Value for BCM ..................52
Terminal and Reference Value for IPDM E/R ..........54
How to Proceed with Trouble Diagnosis ..................54
Preliminary Check ...................................................55
CONSULT-III Functions (BCM) ...............................56
CONSULT-III Functions (IPDM E/R) .......................57
Symptom Chart ........................................................58
Lighting Switch Inspection .......................................58
Optical sensor System Inspection ...........................59
Removal and Installation of Optical Sensor .............60
3AA93ABC3ACD3AC03ACA3AC03AC63AC53A913A773A893A873A873A8E3A773A983AC73AC93AC03AC3
3A893A873A873A8F3A773A9D3AAF3A8A3A8C3A863A9D3AAF3A8B3A8C
Page 3119 of 3924
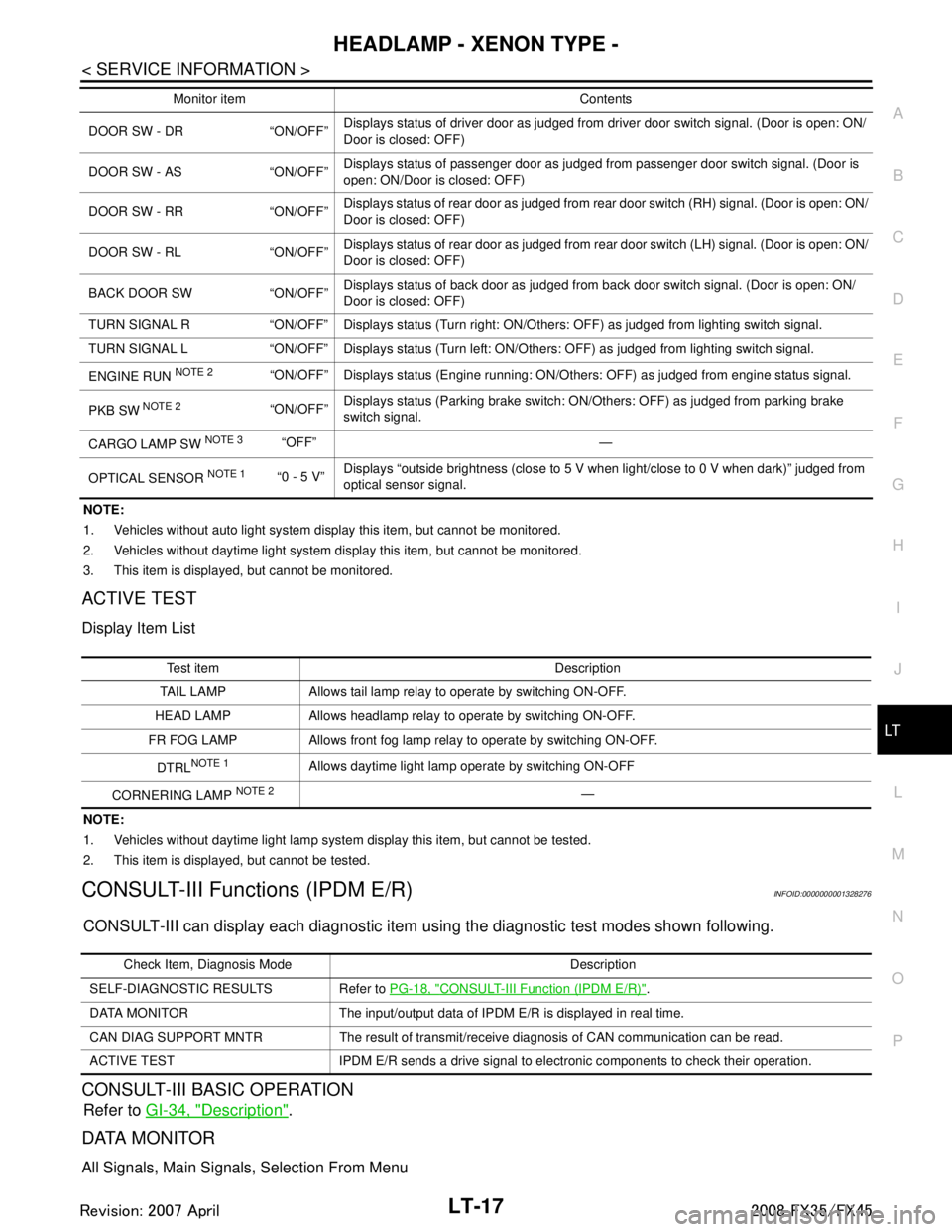
HEADLAMP - XENON TYPE -LT-17
< SERVICE INFORMATION >
C
DE
F
G H
I
J
L
M A
B
LT
N
O P
NOTE:
1. Vehicles without auto light system display this item, but cannot be monitored.
2. Vehicles without daytime light system display this item, but cannot be monitored.
3. This item is displayed, but cannot be monitored.
ACTIVE TEST
Display Item List
NOTE:
1. Vehicles without daytime light lamp system display this item, but cannot be tested.
2. This item is displayed, but cannot be tested.
CONSULT-III Functions (IPDM E/R)INFOID:0000000001328276
CONSULT-III can display each diagnostic item us ing the diagnostic test modes shown following.
CONSULT-III BASIC OPERATION
Refer to GI-34, "Description".
DATA MONITOR
All Signals, Main Signals, Selection From Menu
DOOR SW - DR “ON/OFF” Displays status of driver door as judged from driver door switch signal. (Door is open: ON/
Door is closed: OFF)
DOOR SW - AS “ON/OFF” Displays status of passenger door as judged from passenger door switch signal. (Door is
open: ON/Door is closed: OFF)
DOOR SW - RR “ON/OFF” Displays status of rear door as judged from rear door switch (RH) signal. (Door is open: ON/
Door is closed: OFF)
DOOR SW - RL “ON/OFF” Displays status of rear door as judged from rear door switch (LH) signal. (Door is open: ON/
Door is closed: OFF)
BACK DOOR SW “ON/OFF” Displays status of back door as judged from back door switch signal. (Door is open: ON/
Door is closed: OFF)
TURN SIGNAL R “ON/OFF” Display s status (Turn right: ON/Others: OFF) as judged from lighting switch signal.
TURN SIGNAL L “ON/OFF” Display s status (Turn left: ON/Others: OFF) as judged from lighting switch signal.
ENGINE RUN
NOTE 2“ON/OFF” Displays status (Engine running: ON/Others: OFF) as judged from engine status signal.
PKB SW
NOTE 2“ON/OFF” Displays status (Parking brake switch: ON/Others: OFF) as judged from parking brake
switch signal.
CARGO LAMP SW
NOTE 3 “OFF” —
OPTICAL SENSOR
NOTE 1 “0 - 5 V” Displays “outside brightness (close to 5 V when light/close to 0 V when dark)” judged from
optical sensor signal.
Monitor item Contents
Te s t i t e m D e s c r i p t i o n
TAIL LAMP Allows tail lamp relay to operate by switching ON-OFF.
HEAD LAMP Allows headlamp relay to operate by switching ON-OFF.
FR FOG LAMP Allows front fog lamp relay to operate by switching ON-OFF.
DTRL
NOTE 1Allows daytime light lamp operate by switching ON-OFF
CORNERING LAMP
NOTE 2—
Check Item, Diagnosis Mode Description
SELF-DIAGNOSTIC RESULTS Refer to PG-18, "
CONSULT-III Function (IPDM E/R)".
DATA MONITOR The input/output data of IPDM E/R is displayed in real time.
CAN DIAG SUPPORT MNTR The result of transmit/receive diagnosis of CAN communication can be read.
ACTIVE TEST IPDM E/R sends a drive signal to electronic components to check their operation.
3AA93ABC3ACD3AC03ACA3AC03AC63AC53A913A773A893A873A873A8E3A773A983AC73AC93AC03AC3
3A893A873A873A8F3A773A9D3AAF3A8A3A8C3A863A9D3AAF3A8B3A8C
Page 3146 of 3924
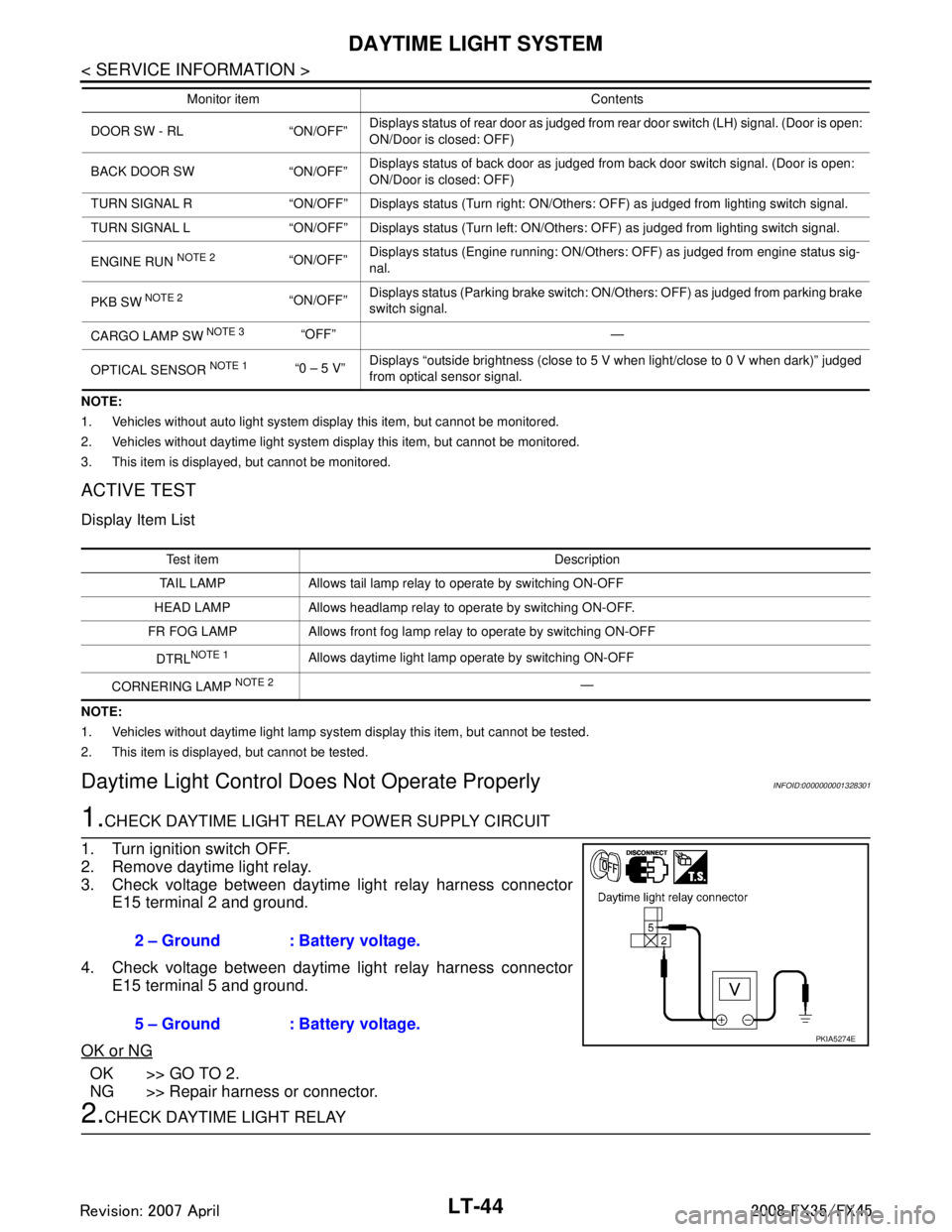
LT-44
< SERVICE INFORMATION >
DAYTIME LIGHT SYSTEM
NOTE:
1. Vehicles without auto light system display this item, but cannot be monitored.
2. Vehicles without daytime light system display this item, but cannot be monitored.
3. This item is displayed, but cannot be monitored.
ACTIVE TEST
Display Item List
NOTE:
1. Vehicles without daytime light lamp system display this item, but cannot be tested.
2. This item is displayed, but cannot be tested.
Daytime Light Control Does Not Operate ProperlyINFOID:0000000001328301
1.CHECK DAYTIME LIGHT RELAY POWER SUPPLY CIRCUIT
1. Turn ignition switch OFF.
2. Remove daytime light relay.
3. Check voltage between daytime light relay harness connector E15 terminal 2 and ground.
4. Check voltage between daytime light relay harness connector E15 terminal 5 and ground.
OK or NG
OK >> GO TO 2.
NG >> Repair harness or connector.
2.CHECK DAYTIME LIGHT RELAY
DOOR SW - RL “ON/OFF” Displays status of rear door as judged from rear door switch (LH) signal. (Door is open:
ON/Door is closed: OFF)
BACK DOOR SW “ON/OFF” Displays status of back door as judged from back door switch signal. (Door is open:
ON/Door is closed: OFF)
TURN SIGNAL R “ON/OFF” Displays status (Turn right: ON/Others: OFF) as judged from lighting switch signal.
TURN SIGNAL L “ON/OFF” Displays status (Turn left: ON/Others: OFF) as judged from lighting switch signal.
ENGINE RUN
NOTE 2“ON/OFF” Displays status (Engine running: ON/Others: OFF) as judged from engine status sig-
nal.
PKB SW
NOTE 2“ON/OFF” Displays status (Parking brake switch: ON/Others: OFF) as judged from parking brake
switch signal.
CARGO LAMP SW
NOTE 3 “OFF” —
OPTICAL SENSOR
NOTE 1 “0 – 5 V” Displays “outside brightness (close to 5 V when light/close to 0 V when dark)” judged
from optical sensor signal.
Monitor item Contents
Test item Description
TAIL LAMP Allows tail lamp relay to operate by switching ON-OFF
HEAD LAMP Allows headlamp relay to operate by switching ON-OFF.
FR FOG LAMP Allows front fog lamp relay to operate by switching ON-OFF
DTRL
NOTE 1Allows daytime light lamp operate by switching ON-OFF
CORNERING LAMP
NOTE 2—
2 – Ground : Battery voltage.
5 – Ground : Battery voltage.
PKIA5274E
3AA93ABC3ACD3AC03ACA3AC03AC63AC53A913A773A893A873A873A8E3A773A983AC73AC93AC03AC3
3A893A873A873A8F3A773A9D3AAF3A8A3A8C3A863A9D3AAF3A8B3A8C
Page 3149 of 3924
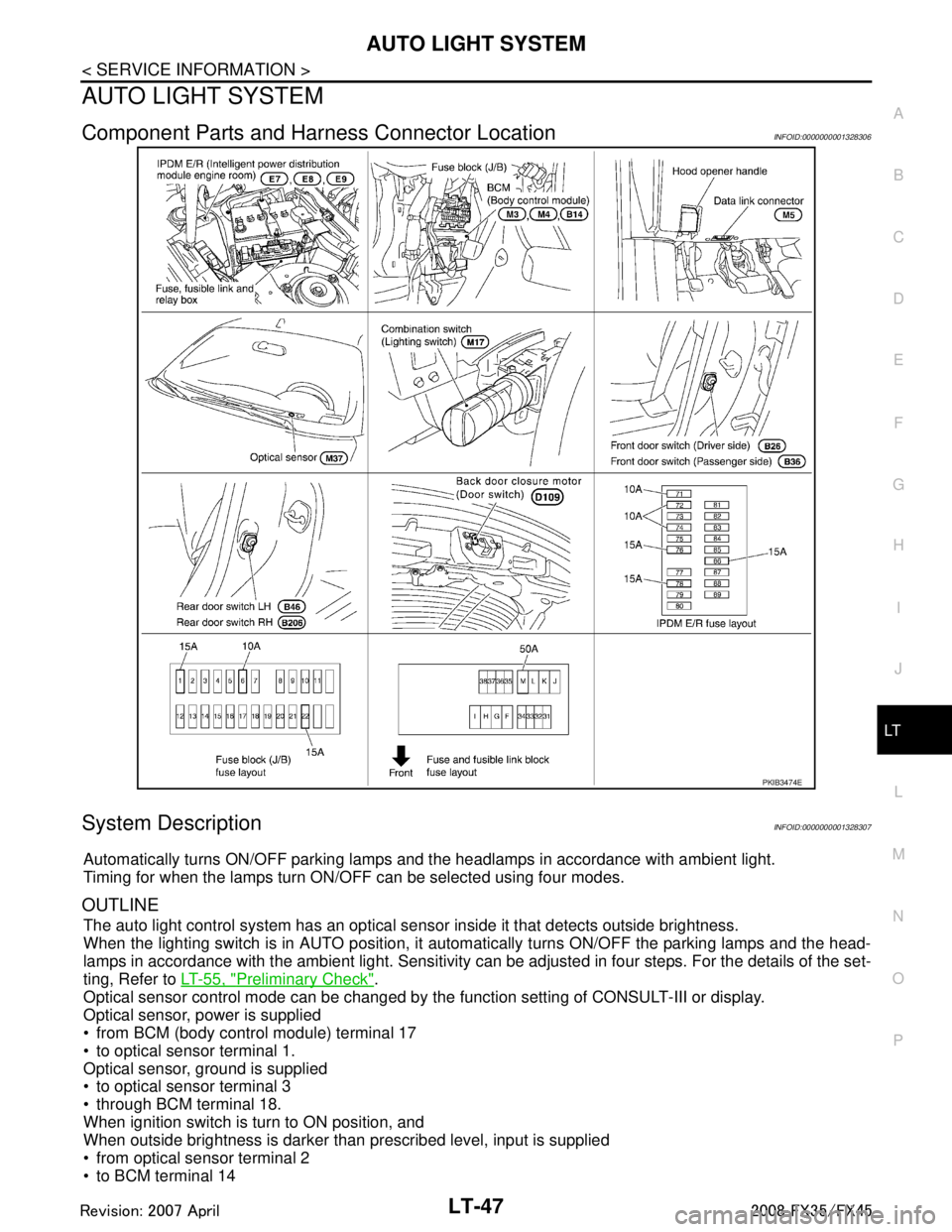
AUTO LIGHT SYSTEMLT-47
< SERVICE INFORMATION >
C
DE
F
G H
I
J
L
M A
B
LT
N
O P
AUTO LIGHT SYSTEM
Component Parts and Har ness Connector LocationINFOID:0000000001328306
System DescriptionINFOID:0000000001328307
Automatically turns ON/OFF parking lamps and the headlamps in accordance with ambient light.
Timing for when the lamps turn ON/OFF can be selected using four modes.
OUTLINE
The auto light control system has an optical s ensor inside it that detects outside brightness.
When the lighting switch is in AUTO position, it automatically turns ON/OFF the parking lamps and the head-
lamps in accordance with the ambient li ght. Sensitivity can be adjusted in four steps. For the details of the set-
ting, Refer to LT-55, "
Preliminary Check".
Optical sensor control mode can be changed by the function setting of CONSULT-III or display.
Optical sensor, power is supplied
from BCM (body control module) terminal 17
to optical sensor terminal 1.
Optical sensor, ground is supplied
to optical sensor terminal 3
through BCM terminal 18.
When ignition switch is turn to ON position, and
When outside brightness is darker than prescribed level, input is supplied
from optical sensor terminal 2
to BCM terminal 14
PKIB3474E
3AA93ABC3ACD3AC03ACA3AC03AC63AC53A913A773A893A873A873A8E3A773A983AC73AC93AC03AC3
3A893A873A873A8F3A773A9D3AAF3A8A3A8C3A863A9D3AAF3A8B3A8C
Page 3150 of 3924
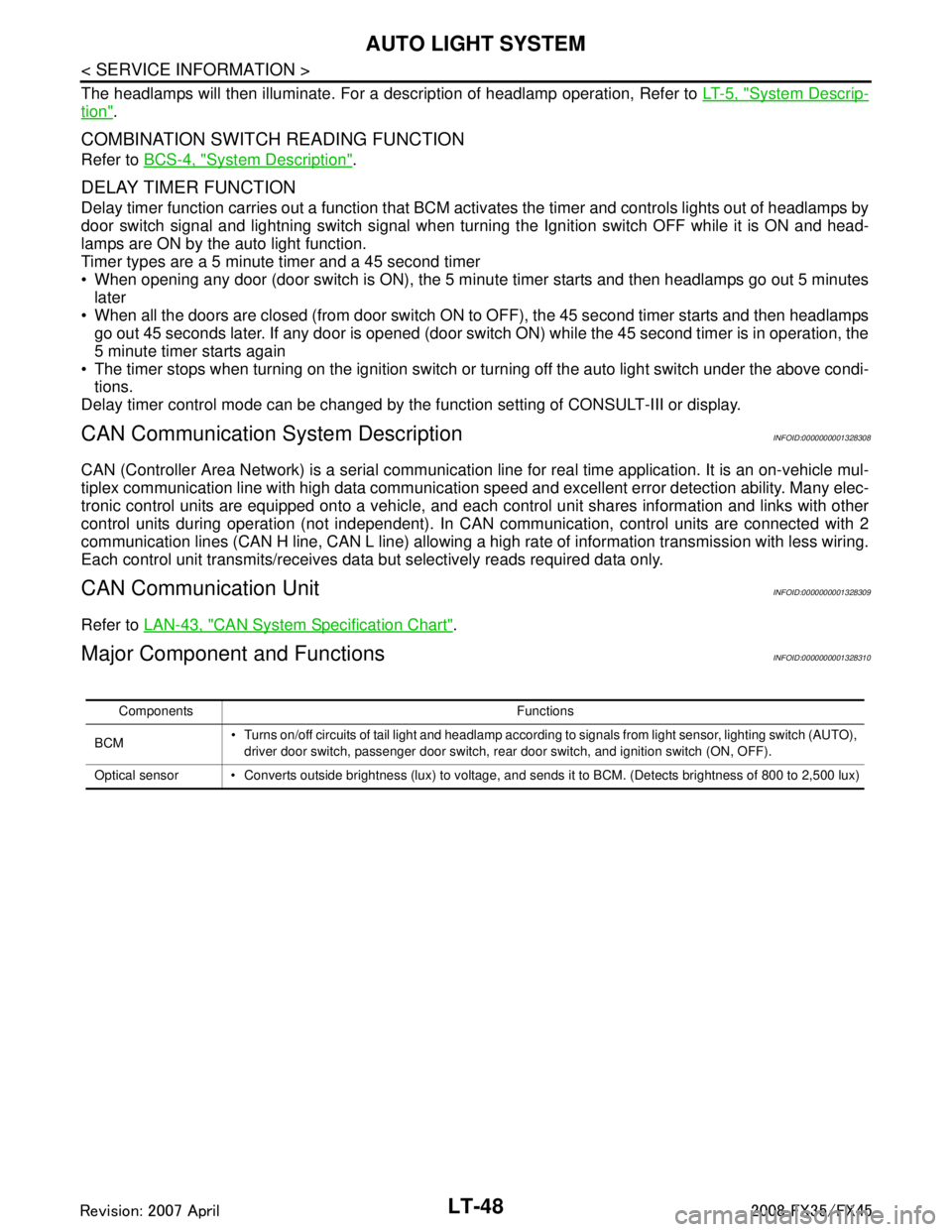
LT-48
< SERVICE INFORMATION >
AUTO LIGHT SYSTEM
The headlamps will then illuminate. For a description of headlamp operation, Refer to LT- 5 , "System Descrip-
tion".
COMBINATION SWITCH READING FUNCTION
Refer to BCS-4, "System Description".
DELAY TIMER FUNCTION
Delay timer function carries out a function that BCM ac tivates the timer and controls lights out of headlamps by
door switch signal and lightning switch signal when turn ing the Ignition switch OFF while it is ON and head-
lamps are ON by the auto light function.
Timer types are a 5 minute timer and a 45 second timer
When opening any door (door switch is ON), the 5 mi nute timer starts and then headlamps go out 5 minutes
later
When all the doors are closed (from door switch ON to OFF), the 45 second timer starts and then headlamps go out 45 seconds later. If any door is opened (door switch ON) while the 45 second timer is in operation, the
5 minute timer starts again
The timer stops when turning on the ignition switch or turning off the auto light switch under the above condi-
tions.
Delay timer control mode can be changed by the f unction setting of CONSULT-III or display.
CAN Communication System DescriptionINFOID:0000000001328308
CAN (Controller Area Network) is a serial communication line for real time application. It is an on-vehicle mul-
tiplex communication line with high data communication s peed and excellent error detection ability. Many elec-
tronic control units are equipped onto a vehicle, and each control unit shares information and links with other
control units during operation (not independent). In CA N communication, control units are connected with 2
communication lines (CAN H line, CAN L line) allowing a high rate of information transmission with less wiring.
Each control unit transmits/receives data but selectively reads required data only.
CAN Communication UnitINFOID:0000000001328309
Refer to LAN-43, "CAN System Specification Chart".
Major Component and FunctionsINFOID:0000000001328310
Components Functions
BCM Turns on/off circuits of tail light and headlamp according to signals from light sensor, lighting switch (AUTO),
driver door switch, passenger door switch, rear door switch, and ignition switch (ON, OFF).
Optical sensor Converts outside brightness (lux) to voltage, and sends it to BCM. (Detects brightness of 800 to 2,500 lux)
3AA93ABC3ACD3AC03ACA3AC03AC63AC53A913A773A893A873A873A8E3A773A983AC73AC93AC03AC3
3A893A873A873A8F3A773A9D3AAF3A8A3A8C3A863A9D3AAF3A8B3A8C