service INFINITI M35 2006 Factory Service Manual
[x] Cancel search | Manufacturer: INFINITI, Model Year: 2006, Model line: M35, Model: INFINITI M35 2006Pages: 5621, PDF Size: 65.56 MB
Page 1409 of 5621
![INFINITI M35 2006 Factory Service Manual CO-34
[VK45DE]
PRECAUTIONS
Revision: 2006 January2006 M35/M45
[VK45DE]PRECAUTIONSPFP:00001
Precautions for Supplemental Restraint System (SRS) “AIR BAG” and “SEAT
BELT PRE-TENSIONER”
NBS004R8 INFINITI M35 2006 Factory Service Manual CO-34
[VK45DE]
PRECAUTIONS
Revision: 2006 January2006 M35/M45
[VK45DE]PRECAUTIONSPFP:00001
Precautions for Supplemental Restraint System (SRS) “AIR BAG” and “SEAT
BELT PRE-TENSIONER”
NBS004R8](/img/42/57023/w960_57023-1408.png)
CO-34
[VK45DE]
PRECAUTIONS
Revision: 2006 January2006 M35/M45
[VK45DE]PRECAUTIONSPFP:00001
Precautions for Supplemental Restraint System (SRS) “AIR BAG” and “SEAT
BELT PRE-TENSIONER”
NBS004R8
The Supplemental Restraint System such as “AIR BAG” and “SEAT BELT PRE-TENSIONER”, used along
with a front seat belt, helps to reduce the risk or severity of injury to the driver and front passenger for certain
types of collision. This system includes seat belt switch inputs and dual stage front air bag modules. The SRS
system uses the seat belt switches to determine the front air bag deployment, and may only deploy one front
air bag, depending on the severity of a collision and whether the front occupants are belted or unbelted.
Information necessary to service the system safely is included in the SRS and SB section of this Service Man-
ual.
WAR NING :
To avoid rendering the SRS inoperative, which could increase the risk of personal injury or death
in the event of a collision which would result in air bag inflation, all maintenance must be per-
formed by an authorized NISSAN/INFINITI dealer.
Improper maintenance, including incorrect removal and installation of the SRS, can lead to per-
sonal injury caused by unintentional activation of the system. For removal of Spiral Cable and Air
Bag Module, see the SRS section.
Do not use electrical test equipment on any circuit related to the SRS unless instructed to in this
Service Manual. SRS wiring harnesses can be identified by yellow and/or orange harnesses or
harness connectors.
Page 1410 of 5621
![INFINITI M35 2006 Factory Service Manual PREPARATION
CO-35
[VK45DE]
C
D
E
F
G
H
I
J
K
L
MA
CO
Revision: 2006 January2006 M35/M45
PREPARATIONPFP:00002
Special Service ToolsNBS004R9
The actual shapes of Kent-Moore tools may from those of speci INFINITI M35 2006 Factory Service Manual PREPARATION
CO-35
[VK45DE]
C
D
E
F
G
H
I
J
K
L
MA
CO
Revision: 2006 January2006 M35/M45
PREPARATIONPFP:00002
Special Service ToolsNBS004R9
The actual shapes of Kent-Moore tools may from those of speci](/img/42/57023/w960_57023-1409.png)
PREPARATION
CO-35
[VK45DE]
C
D
E
F
G
H
I
J
K
L
MA
CO
Revision: 2006 January2006 M35/M45
PREPARATIONPFP:00002
Special Service ToolsNBS004R9
The actual shapes of Kent-Moore tools may from those of special service tools illustrated here.
Commercial Service ToolsNBS004RA
Tool number
(Kent-Moore No.)
To o l n a m eDescription
EG17650301
(J33984-A)
Radiator cap tester adapterAdapting radiator cap tester to radiator cap
and thermostat housing filler neck
a: 28 (1.10) dia.
b: 31.4 (1.236) dia.
c: 41.3 (1.626) dia.
Unit: mm (in)
KV99103510
(—)
Radiator plate pliers AInstalling radiator upper and lower tanks
KV99103520
(—)
Radiator plate pliers BRemoving radiator upper and lower tanks
S-NT564
S-NT224
S-NT225
To o l n a m eDescription
Power toolLoosening nuts and bolts
Radiator cap tester Checking radiator and radiator cap
PBIC0190E
PBIC1982E
Page 1415 of 5621
![INFINITI M35 2006 Factory Service Manual CO-40
[VK45DE]
ENGINE COOLANT
Revision: 2006 January2006 M35/M45
ENGINE COOLANTPFP:KQ100
InspectionNBS004RE
LEVEL CHECK
Check if the reservoir tank engine coolant level is within the
“MIN INFINITI M35 2006 Factory Service Manual CO-40
[VK45DE]
ENGINE COOLANT
Revision: 2006 January2006 M35/M45
ENGINE COOLANTPFP:KQ100
InspectionNBS004RE
LEVEL CHECK
Check if the reservoir tank engine coolant level is within the
“MIN](/img/42/57023/w960_57023-1414.png)
CO-40
[VK45DE]
ENGINE COOLANT
Revision: 2006 January2006 M35/M45
ENGINE COOLANTPFP:KQ100
InspectionNBS004RE
LEVEL CHECK
Check if the reservoir tank engine coolant level is within the
“MIN” to “MAX” when engine is cool.
Adjust the engine coolant level as necessary.
LEAK CHECK
To check for leaks, apply pressure to the cooling system with
radiator cap tester (commercial service tool) and radiator cap
tester adapter (SST).
WA R N I N G :
Do not remove radiator cap when engine is hot. Serious
burns could occur from high-pressure engine coolant
escaping from thermostat housing.
CAUTION:
Higher testing pressure than specified may cause radiator
damage.
NOTE:
In a case engine coolant decreases, replenish radiator with engine coolant.
If anything is found, repair or replace damaged parts.
Changing Engine CoolantNBS004RF
WAR NING :
To avoid being scalded, do not change engine coolant when engine is hot.
Wrap a thick cloth around radiator cap and carefully remove radiator cap. First, turn radiator cap a
quarter of a turn to release built-up pressure. Then turn radiator cap all the way.
DRAINING ENGINE COOLANT
1. Remove engine room cover (RH and LH). Refer to EM-173, "ENGINE ROOM COVER" .
2. Remove engine cover with power tool. Refer to EM-179, "
INTAKE MANIFOLD" .
3. Open radiator drain plug at the bottom of radiator, and then remove radiator cap.
When draining all of engine coolant in the system, open water drain plugs on cylinder block. Refer
to EM-250, "
DISASSEMBLY" .
4. Remove reservoir tank as necessary, and drain engine coolant and clean reservoir tank before installing.
SMA412B
Testing pressure : 157 kPa (1.6 kg/cm2 , 23 psi)
PBIC1528E
1 : Radiator drain plug hole
2 : Front engine undercover
: Engine front
PBIC3395E
Page 1420 of 5621
![INFINITI M35 2006 Factory Service Manual RADIATOR
CO-45
[VK45DE]
C
D
E
F
G
H
I
J
K
L
MA
CO
Revision: 2006 January2006 M35/M45
INSTALLATION
Installation is the reverse order of removal.
INSPECTION AFTER INSTALLATION
Check for leaks of eng INFINITI M35 2006 Factory Service Manual RADIATOR
CO-45
[VK45DE]
C
D
E
F
G
H
I
J
K
L
MA
CO
Revision: 2006 January2006 M35/M45
INSTALLATION
Installation is the reverse order of removal.
INSPECTION AFTER INSTALLATION
Check for leaks of eng](/img/42/57023/w960_57023-1419.png)
RADIATOR
CO-45
[VK45DE]
C
D
E
F
G
H
I
J
K
L
MA
CO
Revision: 2006 January2006 M35/M45
INSTALLATION
Installation is the reverse order of removal.
INSPECTION AFTER INSTALLATION
Check for leaks of engine coolant using radiator cap tester adapter [SST: EG17650301 (J33984-A)] and
radiator cap tester (commercial service tool). Refer to CO-40, "
LEAK CHECK" .
Start and warm up engine. Visually Check if there is no leaks of engine coolant and A/T fluid.
Checking Radiator CapNBS004RI
Check valve seat of radiator cap.
–Check if valve seat is swollen to the extent that the edge of the
plunger cannot be seen when watching it vertically from the top.
–Check if valve seat has no soil and damage.
Pull negative-pressure valve to open it, and make sure that it
close completely when released.
–Make sure that there is no dirt or damage on the valve seat of
radiator cap negative-pressure valve.
–Make sure that there are no unusualness in the opening and
closing conditions of negative-pressure valve.
Check radiator cap relief pressure.
–When connecting radiator cap to the radiator cap tester adapter
(SST) and the radiator cap tester (Commercial service tool),
apply engine coolant to the cap seal surface.
Replace radiator cap if there is an unusualness.
CAUTION:
When installing a radiator cap, thoroughly wipe out the radiator filler neck to remove any waxy residue
or foreign material.
Checking RadiatorNBS004RJ
Check radiator for mud or clogging. If necessary, clean radiator as follows:
Be careful not to bend or damage the radiator fins.
When radiator is cleaned without removal, remove all surrounding parts such as cooling fan, radiator
shroud and horns. Then tape the harness and electrical connectors to prevent water from entering.
1. Apply water by hose to the back side of the radiator core vertically downward.
2. Apply water again to all radiator core surface once per minute.
PBIC2816E
SMA967B
Standard : 78 - 98 kPa (0.8 - 1.0 kg/cm2 , 11 - 14 psi)
Limit : 59 kPa (0.6 kg/cm
2 , 9 psi)
SLC755A
Page 1425 of 5621
![INFINITI M35 2006 Factory Service Manual CO-50
[VK45DE]
RADIATOR (ALUMINUM TYPE)
Revision: 2006 January2006 M35/M45
4. Make sure that the rim is completely crimped down.
5. Make sure that there is no leakage. Refer to CO-50, "
INSPECTION INFINITI M35 2006 Factory Service Manual CO-50
[VK45DE]
RADIATOR (ALUMINUM TYPE)
Revision: 2006 January2006 M35/M45
4. Make sure that the rim is completely crimped down.
5. Make sure that there is no leakage. Refer to CO-50, "
INSPECTION](/img/42/57023/w960_57023-1424.png)
CO-50
[VK45DE]
RADIATOR (ALUMINUM TYPE)
Revision: 2006 January2006 M35/M45
4. Make sure that the rim is completely crimped down.
5. Make sure that there is no leakage. Refer to CO-50, "
INSPECTION" .
INSPECTION
1. Apply pressure with radiator cap tester adapter (SST) and radia-
tor cap tester (commercial service tool).
provide used radiator and connect it to tested radiator using
radiator hoses as shown in the figure.
NOTE:
The used radiator should be tested beforehand to confirm it
has no leakage. If used one is not available, it is possible to
use new service part as a radiator testing tool.
WA R N I N G :
To prevent the risk of hose coming undone while under pressure, securely fasten it down with
hose clamp.
CAUTION:
Attach hose to A/T fluid cooler to seal its inlet and outlet.
2. Check for leakage by soaking radiator in water container with
the testing pressure applied.Standard height “H” : 8.0 - 8.4 mm (0.315 - 0.331 in)
SLC554A
Testing pressure
: 157 kPa (1.6 kg/cm
2 , 23 psi)PBIC1658E
PBIC1699E
Page 1428 of 5621
![INFINITI M35 2006 Factory Service Manual WATER PUMP
CO-53
[VK45DE]
C
D
E
F
G
H
I
J
K
L
MA
CO
Revision: 2006 January2006 M35/M45
WAT E R PU M PPFP:21020
ComponentsNBS004RP
Refer to GI-11, "Components" for symbol marks in the figure. INFINITI M35 2006 Factory Service Manual WATER PUMP
CO-53
[VK45DE]
C
D
E
F
G
H
I
J
K
L
MA
CO
Revision: 2006 January2006 M35/M45
WAT E R PU M PPFP:21020
ComponentsNBS004RP
Refer to GI-11, "Components" for symbol marks in the figure.](/img/42/57023/w960_57023-1427.png)
WATER PUMP
CO-53
[VK45DE]
C
D
E
F
G
H
I
J
K
L
MA
CO
Revision: 2006 January2006 M35/M45
WAT E R PU M PPFP:21020
ComponentsNBS004RP
Refer to GI-11, "Components" for symbol marks in the figure.
Removal and InstallationNBS004RQ
CAUTION:
When removing water pump, be careful not to get engine coolant on drive belts.
Water pump can not be disassembled and should be replaced as a unit.
After installing water pump, connect hose and clamp securely, then check for leaks using radiator
cap tester (commercial service tool) and radiator cap tester adapter [SST: EG17650301 (J33984-
A)].
REMOVAL
1. Remove following parts:
Front engine undercover (power tool)
Engine cover: Refer to EM-179, "INTAKE MANIFOLD" .
Engine room cover (RH and LH): Refer to EM-173, "ENGINE ROOM COVER" .
Air duct (inlet): Refer to EM-177, "AIR CLEANER AND AIR DUCT" .
Alternator, water pump and A/C compressor belt: Refer to EM-174, "DRIVE BELTS" .
2. Drain engine coolant from drain plugs on radiator and both side of cylinder block. Refer to CO-40, "
Chang-
ing Engine Coolant" and EM-250, "DISASSEMBLY" .
CAUTION:
Perform this step when engine is cold.
Do not spill engine coolant on drive belts.
3. Remove water pump pulley.
4. Remove water pump.
Engine coolant will leak from cylinder block, so have a receptacle ready under vehicle.
CAUTION:
Handle the water pump vane so that it does not contact any other parts.
Do not disassemble water pump.
1. Water pump 2. Water pump pulley 3. Gasket
PBIC3396E
Page 1429 of 5621
![INFINITI M35 2006 Factory Service Manual CO-54
[VK45DE]
WATER PUMP
Revision: 2006 January2006 M35/M45
INSPECTION AFTER REMOVAL
Visually check that there is no significant dirt or rusting on water
pump body and vane.
Make sure there is no loo INFINITI M35 2006 Factory Service Manual CO-54
[VK45DE]
WATER PUMP
Revision: 2006 January2006 M35/M45
INSPECTION AFTER REMOVAL
Visually check that there is no significant dirt or rusting on water
pump body and vane.
Make sure there is no loo](/img/42/57023/w960_57023-1428.png)
CO-54
[VK45DE]
WATER PUMP
Revision: 2006 January2006 M35/M45
INSPECTION AFTER REMOVAL
Visually check that there is no significant dirt or rusting on water
pump body and vane.
Make sure there is no looseness in vane shaft, and that it turns
smoothly when rotated by hand.
If anything is found, replace water pump.
INSTALLATION
Installation is the reverse order of removal.
INSPECTION AFTER INSTALLATION
Check for leaks of engine coolant using radiator cap tester adapter [SST: EG17650301 (J–33984-A)] and
radiator cap tester (commercial service tool). Refer to CO-40, "
LEAK CHECK" .
Start and warm up engine. Visually check if there is no leaks of engine coolant.
PBIC1539E
Page 1432 of 5621
![INFINITI M35 2006 Factory Service Manual THERMOSTAT AND WATER CONTROL VALVE
CO-57
[VK45DE]
C
D
E
F
G
H
I
J
K
L
MA
CO
Revision: 2006 January2006 M35/M45
Install thermostat with jiggle valve facing upwards. (The position
deviation may be withi INFINITI M35 2006 Factory Service Manual THERMOSTAT AND WATER CONTROL VALVE
CO-57
[VK45DE]
C
D
E
F
G
H
I
J
K
L
MA
CO
Revision: 2006 January2006 M35/M45
Install thermostat with jiggle valve facing upwards. (The position
deviation may be withi](/img/42/57023/w960_57023-1431.png)
THERMOSTAT AND WATER CONTROL VALVE
CO-57
[VK45DE]
C
D
E
F
G
H
I
J
K
L
MA
CO
Revision: 2006 January2006 M35/M45
Install thermostat with jiggle valve facing upwards. (The position
deviation may be within the range of
10 degrees)
Install water control valve with the up-mark facing up and the
frame center part facing upwards. (The position deviation may
be within the range of
10 degrees)
Water Outlet Pipe and Heater Pipe
First apply a neutral detergent to O-rings, then quickly insert the insertion parts of the water outlet pipe and
heater pipe into the installation holes.
INSPECTION AFTER INSTALLATION
Check for leaks of engine coolant using radiator cap tester adapter [SST: EG17650301 (J33984-A)] and
radiator cap tester (commercial service tool). Refer to CO-40, "
LEAK CHECK" .
Start and warm up engine. Visually check if there is no leaks of engine coolant.
PBIC0158E
Page 1433 of 5621
![INFINITI M35 2006 Factory Service Manual CO-58
[VK45DE]
SERVICE DATA AND SPECIFICATIONS (SDS)
Revision: 2006 January2006 M35/M45
SERVICE DATA AND SPECIFICATIONS (SDS)PFP:00030
Standard and LimitNBS004RT
ENGINE COOLANT CAPACITY (APPROXIMATE)
INFINITI M35 2006 Factory Service Manual CO-58
[VK45DE]
SERVICE DATA AND SPECIFICATIONS (SDS)
Revision: 2006 January2006 M35/M45
SERVICE DATA AND SPECIFICATIONS (SDS)PFP:00030
Standard and LimitNBS004RT
ENGINE COOLANT CAPACITY (APPROXIMATE)](/img/42/57023/w960_57023-1432.png)
CO-58
[VK45DE]
SERVICE DATA AND SPECIFICATIONS (SDS)
Revision: 2006 January2006 M35/M45
SERVICE DATA AND SPECIFICATIONS (SDS)PFP:00030
Standard and LimitNBS004RT
ENGINE COOLANT CAPACITY (APPROXIMATE)
Unit: (US qt, Imp qt)
RADIATOR
Unit: kPa (kg/cm2 , psi)
THERMOSTAT
WATER CONTROL VALVE
Engine coolant capacity (With reservoir tank at “MAX” level) 10.4 (11, 9-1/8)
Reservoir tank engine coolant capacity (at “MAX” level) 0.6 (5/8, 1/2)
Radiator cap relief pressureStandard 78 - 98 (0.8 - 1.0, 11 - 14)
Limit 59 (0.6, 9)
Leakage testing pressure 157 (1.6, 23)
ThermostatStandard
Valve opening temperature 80 - 84
C (176 - 183F)
Maximum valve lift More than 10 mm/ 95
C (0.39 in/ 203F)
Valve closing temperature 77
C (171F)
Water control valveStandard
Valve opening temperature 93.5 - 96.5
C (200 - 206F)
Maximum valve lift More than 8 mm/ 108
C (0.315 in/ 226F)
Valve closing temperature 90
C (194F)
Page 1434 of 5621
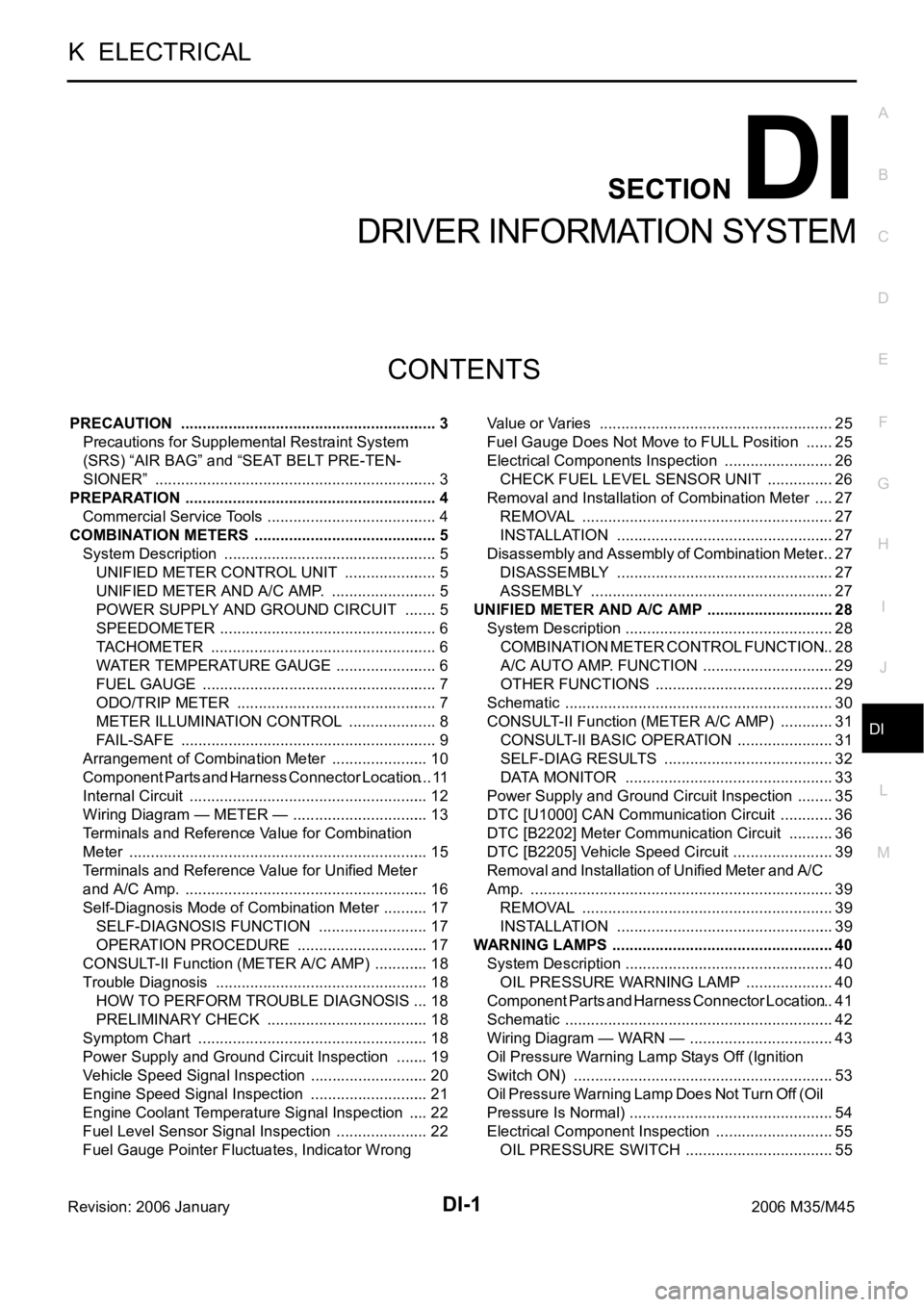
DI-1
DRIVER INFORMATION SYSTEM
K ELECTRICAL
CONTENTS
C
D
E
F
G
H
I
J
L
M
SECTION DI
A
B
DI
Revision: 2006 January2006 M35/M45
DRIVER INFORMATION SYSTEM
PRECAUTION ............................................................ 3
Precautions for Supplemental Restraint System
(SRS) “AIR BAG” and “SEAT BELT PRE-TEN-
SIONER” .................................................................. 3
PREPARATION ........................................................... 4
Commercial Service Tools ........................................ 4
COMBINATION METERS ........................................... 5
System Description .................................................. 5
UNIFIED METER CONTROL UNIT ...................... 5
UNIFIED METER AND A/C AMP. ......................... 5
POWER SUPPLY AND GROUND CIRCUIT ........ 5
SPEEDOMETER ................................................... 6
TACHOMETER ..................................................... 6
WATER TEMPERATURE GAUGE ........................ 6
FUEL GAUGE ....................................................... 7
ODO/TRIP METER ............................................... 7
METER ILLUMINATION CONTROL ..................... 8
FAIL-SAFE ............................................................ 9
Arrangement of Combination Meter ....................... 10
Component Parts and Harness Connector Location .... 11
Internal Circuit ........................................................ 12
Wiring Diagram — METER — ................................ 13
Terminals and Reference Value for Combination
Meter ...................................................................... 15
Terminals and Reference Value for Unified Meter
and A/C Amp. ......................................................... 16
Self-Diagnosis Mode of Combination Meter ........... 17
SELF-DIAGNOSIS FUNCTION .......................... 17
OPERATION PROCEDURE ............................... 17
CONSULT-II Function (METER A/C AMP) ............. 18
Trouble Diagnosis .................................................. 18
HOW TO PERFORM TROUBLE DIAGNOSIS ... 18
PRELIMINARY CHECK ...................................... 18
Symptom Chart ...................................................... 18
Power Supply and Ground Circuit Inspection ........ 19
Vehicle Speed Signal Inspection ............................ 20
Engine Speed Signal Inspection ............................ 21
Engine Coolant Temperature Signal Inspection ..... 22
Fuel Level Sensor Signal Inspection ...................... 22
Fuel Gauge Pointer Fluctuates, Indicator Wrong Value or Varies ....................................................... 25
Fuel Gauge Does Not Move to FULL Position ....... 25
Electrical Components Inspection .......................... 26
CHECK FUEL LEVEL SENSOR UNIT ................ 26
Removal and Installation of Combination Meter ..... 27
REMOVAL ........................................................
... 27
INSTALLATION ................................................... 27
Disassembly and Assembly of Combination Meter ... 27
DISASSEMBLY ................................................... 27
ASSEMBLY ......................................................... 27
UNIFIED METER AND A/C AMP ...........................
... 28
System Description ................................................. 28
COMBINATION METER CONTROL FUNCTION ... 28
A/C AUTO AMP. FUNCTION ............................... 29
OTHER FUNCTIONS .......................................... 29
Schematic ............................................................... 30
CONSULT-II Function (METER A/C AMP) ............. 31
CONSULT-II BASIC OPERATION ....................... 31
SELF-DIAG RESULTS ........................................ 32
DATA MONITOR ................................................. 33
Power Supply and Ground Circuit Inspection ......... 35
DTC [U1000] CAN Communication Circuit ............. 36
DTC [B2202] Meter Communication Circuit ........... 36
DTC [B2205] Vehicle Speed Circuit ........................ 39
Removal and Installation of Unified Meter and A/C
Amp. ....................................................................... 39
REMOVAL ........................................................
... 39
INSTALLATION ................................................... 39
WARNING LAMPS .................................................... 40
System Description ................................................. 40
OIL PRESSURE WARNING LAMP ..................... 40
Component Parts and Harness Connector Location ... 41
Schematic ............................................................... 42
Wiring Diagram — WARN — .................................. 43
Oil Pressure Warning Lamp Stays Off (Ignition
Switch ON) ............................................................. 53
Oil Pressure Warning Lamp Does Not Turn Off (Oil
Pressure Is Normal) ................................................ 54
Electrical Component Inspection ............................ 55
OIL PRESSURE SWITCH ................................... 55