power steering fluid INFINITI M35 2006 Factory Service Manual
[x] Cancel search | Manufacturer: INFINITI, Model Year: 2006, Model line: M35, Model: INFINITI M35 2006Pages: 5621, PDF Size: 65.56 MB
Page 1300 of 5621
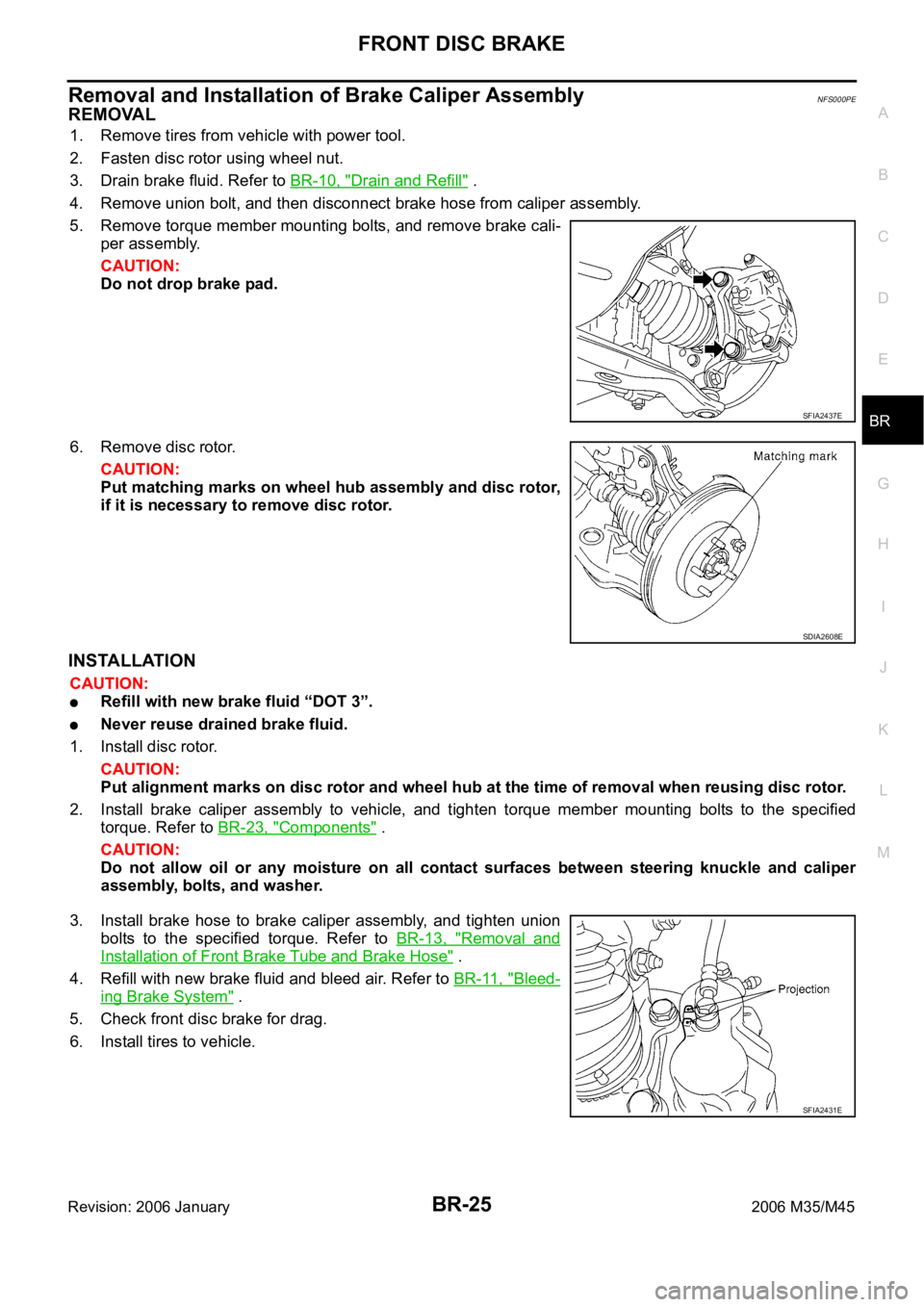
FRONT DISC BRAKE
BR-25
C
D
E
G
H
I
J
K
L
MA
B
BR
Revision: 2006 January2006 M35/M45
Removal and Installation of Brake Caliper AssemblyNFS000PE
REMOVAL
1. Remove tires from vehicle with power tool.
2. Fasten disc rotor using wheel nut.
3. Drain brake fluid. Refer to BR-10, "
Drain and Refill" .
4. Remove union bolt, and then disconnect brake hose from caliper assembly.
5. Remove torque member mounting bolts, and remove brake cali-
per assembly.
CAUTION:
Do not drop brake pad.
6. Remove disc rotor.
CAUTION:
Put matching marks on wheel hub assembly and disc rotor,
if it is necessary to remove disc rotor.
INSTALLATION
CAUTION:
Refill with new brake fluid “DOT 3”.
Never reuse drained brake fluid.
1. Install disc rotor.
CAUTION:
Put alignment marks on disc rotor and wheel hub at the time of removal when reusing disc rotor.
2. Install brake caliper assembly to vehicle, and tighten torque member mounting bolts to the specified
torque. Refer to BR-23, "
Components" .
CAUTION:
Do not allow oil or any moisture on all contact surfaces between steering knuckle and caliper
assembly, bolts, and washer.
3. Install brake hose to brake caliper assembly, and tighten union
bolts to the specified torque. Refer to BR-13, "
Removal and
Installation of Front Brake Tube and Brake Hose" .
4. Refill with new brake fluid and bleed air. Refer to BR-11, "
Bleed-
ing Brake System" .
5. Check front disc brake for drag.
6. Install tires to vehicle.
SFIA2437E
SDIA2608E
SFIA2431E
Page 1312 of 5621
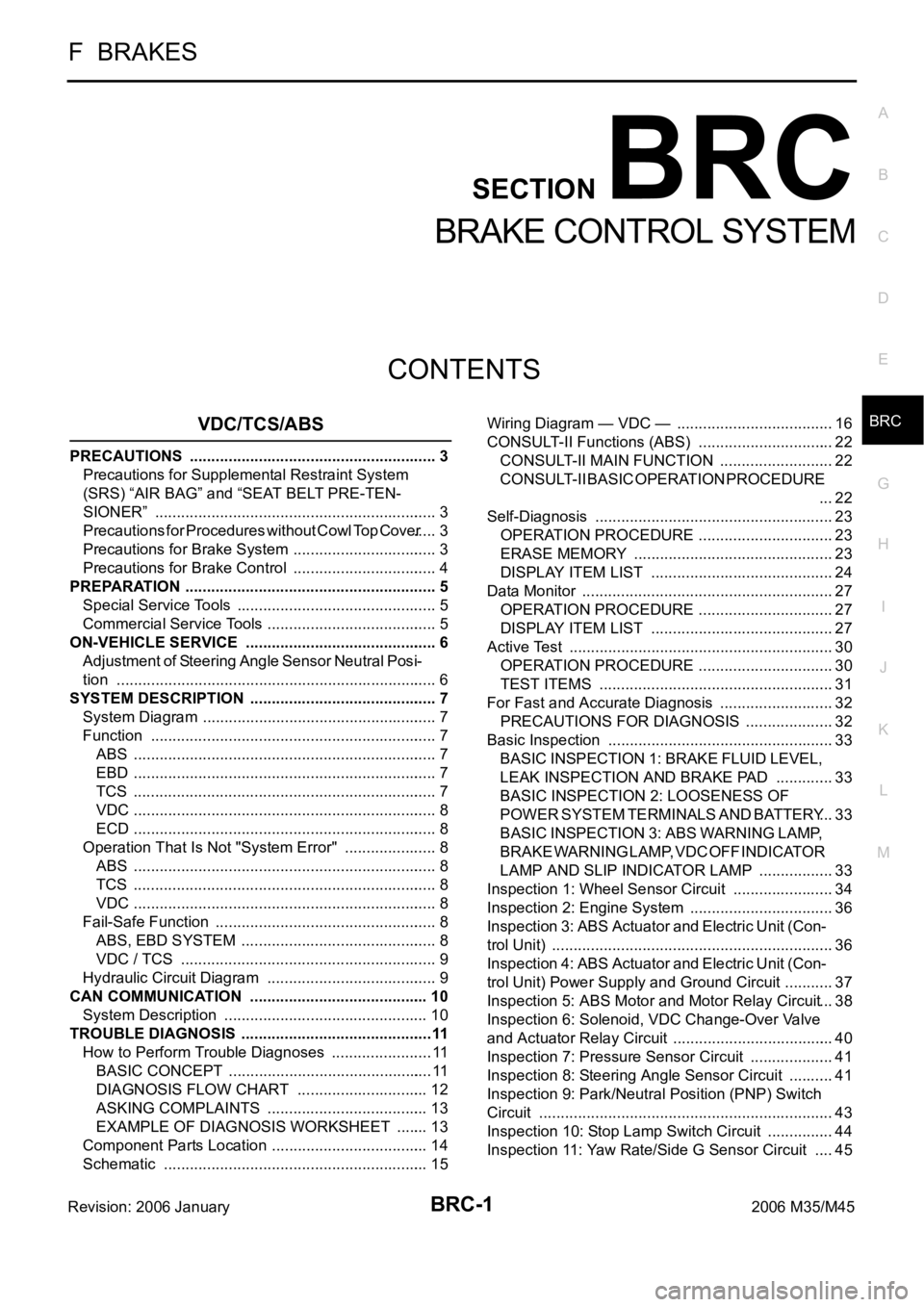
BRC-1
BRAKE CONTROL SYSTEM
F BRAKES
CONTENTS
C
D
E
G
H
I
J
K
L
M
SECTION BRC
A
B
BRC
Revision: 2006 January2006 M35/M45
BRAKE CONTROL SYSTEM
VDC/TCS/ABS
PRECAUTIONS .......................................................... 3
Precautions for Supplemental Restraint System
(SRS) “AIR BAG” and “SEAT BELT PRE-TEN-
SIONER” .................................................................. 3
Precautions for Procedures without Cowl Top Cover ..... 3
Precautions for Brake System .................................. 3
Precautions for Brake Control .................................. 4
PREPARATION ........................................................... 5
Special Service Tools ............................................... 5
Commercial Service Tools ........................................ 5
ON-VEHICLE SERVICE ............................................. 6
Adjustment of Steering Angle Sensor Neutral Posi-
tion ........................................................................... 6
SYSTEM DESCRIPTION ............................................ 7
System Diagram ....................................................... 7
Function ................................................................... 7
ABS ....................................................................... 7
EBD ....................................................................... 7
TCS ....................................................................... 7
VDC ....................................................................... 8
ECD ....................................................................... 8
Operation That Is Not "System Error" ...................... 8
ABS ....................................................................... 8
TCS ....................................................................... 8
VDC ....................................................................... 8
Fail-Safe Function .................................................... 8
ABS, EBD SYSTEM .............................................. 8
VDC / TCS ............................................................ 9
Hydraulic Circuit Diagram ........................................ 9
CAN COMMUNICATION .......................................... 10
System Description ................................................ 10
TROUBLE DIAGNOSIS .............................................11
How to Perform Trouble Diagnoses ........................ 11
BASIC CONCEPT ................................................ 11
DIAGNOSIS FLOW CHART ............................... 12
ASKING COMPLAINTS ...................................... 13
EXAMPLE OF DIAGNOSIS WORKSHEET ........ 13
Component Parts Location ..................................... 14
Schematic .............................................................. 15Wiring Diagram — VDC — ..................................... 16
CONSULT-II Functions (ABS) ................................ 22
CONSULT-II MAIN FUNCTION ........................... 22
CONSULT-II BASIC OPERATION PROCEDURE
... 22
Self-Diagnosis .....................................................
... 23
OPERATION PROCEDURE ................................ 23
ERASE MEMORY ............................................... 23
DISPLAY ITEM LIST ........................................... 24
Data Monitor ........................................................... 27
OPERATION PROCEDURE ................................ 27
DISPLAY ITEM LIST ........................................... 27
Active Test .............................................................. 30
OPERATION PROCEDURE ................................ 30
TEST ITEMS ....................................................... 31
For Fast and Accurate Diagnosis ........................... 32
PRECAUTIONS FOR DIAGNOSIS ..................... 32
Basic Inspection ..................................................... 33
BASIC INSPECTION 1: BRAKE FLUID LEVEL,
LEAK INSPECTION AND BRAKE PAD .............. 33
BASIC INSPECTION 2: LOOSENESS OF
POWER SYSTEM TERMINALS AND BATTERY ... 33
BASIC INSPECTION 3: ABS WARNING LAMP,
BRAKE WARNING LAMP, VDC OFF INDICATOR
LAMP AND SLIP INDICATOR LAMP .................. 33
Inspection 1: Wheel Sensor Circuit ........................ 34
Inspection 2: Engine System .................................. 36
Inspection 3: ABS Actuator and Electric Unit (Con-
trol Unit) .................................................................. 36
Inspection 4: ABS Actuator and Electric Unit (Con-
trol Unit) Power Supply and Ground Circuit ............ 37
Inspection 5: ABS Motor and Motor Relay Circuit ... 38
Inspection 6: Solenoid, VDC Change-Over Valve
and Actuator Relay Circuit ...................................... 40
Inspection 7: Pressure Sensor Circuit .................... 41
Inspection 8: Steering Angle Sensor Circuit ........... 41
Inspection 9: Park/Neutral Position (PNP) Switch
Circuit ..................................................................... 43
Inspection 10: Stop Lamp Switch Circuit ................ 44
Inspection 11: Yaw Rate/Side G Sensor Circuit ..... 45
Page 1337 of 5621
![INFINITI M35 2006 Factory Service Manual BRC-26
[VDC/TCS/ABS]
TROUBLE DIAGNOSIS
Revision: 2006 January2006 M35/M45
Note 1: After completing repairs of shorted sensor circuit, when ignition switch is turned ON, ABS warning lamp turns on. Make INFINITI M35 2006 Factory Service Manual BRC-26
[VDC/TCS/ABS]
TROUBLE DIAGNOSIS
Revision: 2006 January2006 M35/M45
Note 1: After completing repairs of shorted sensor circuit, when ignition switch is turned ON, ABS warning lamp turns on. Make](/img/42/57023/w960_57023-1336.png)
BRC-26
[VDC/TCS/ABS]
TROUBLE DIAGNOSIS
Revision: 2006 January2006 M35/M45
Note 1: After completing repairs of shorted sensor circuit, when ignition switch is turned ON, ABS warning lamp turns on. Make sure that
ABS warning lamp turns off while driving vehicle at 30 km/h (19 MPH) or more for approximately 1 minute according to self-diagnosis
procedure. In addition, if wheel sensor 2 is displayed for wheels, check wheel sensor circuit and also check control unit power voltage.
Note 2: When malfunctions are detected in several systems, including CAN communication circuit [U1000], troubleshoot CAN communi-
cation circuit. Refer to BRC-51, "
Inspection 16: CAN Communication Circuit" . C1147 USV LINE [FL-RR]VDC switch-over solenoid valve (USV1) on the primary side is
open circuit or shorted, or the control line is open or shorted to
the power supply or the ground.
BRC-40,
"Inspection 6:
Solenoid, VDC
Change-Over
Valve and Actua-
tor Relay Circuit"
C1148 USV LINE [FR-RL]VDC switch-over solenoid valve (USV2) on the secondary side is
open circuit or shorted, or the control line is open or shorted to
the power supply or the ground.
C1149 HSV LINE [FL-RR]VDC switch-over solenoid valve (HSV1) on the primary side is
open circuit or shorted, or the control line is open or shorted to
the power supply or the ground.
C1150 HSV LINE [FR-RL]VDC switch-over solenoid valve (HSV2) on the secondary side is
open circuit or shorted, or the control line is open or shorted to
the power supply or the ground.
C1153 EMERGENCY BRAKEWhen ABS actuator and electric unit (control unit) is malfunction-
ing. (pressure increase is too much or too little)BRC-36,
"Inspection 3:
ABS Actuator
and Electric Unit
(Control Unit)"
C1154 PNP POS SIGTCM or ABS actuator and electric unit (control unit) internal mal-
function.BRC-43,
"Inspection 9:
Park/Neutral
Position (PNP)
Switch Circuit"
C1155 BR FLUID LEVEL LOWBrake fluid level is low or communication line between the ABS
actuator and electric unit (control unit) and brake fluid level switch
is open or shorted. BRC-48,
"Inspection 12:
Brake Fluid
Level Switch Cir-
cuit"
C1156 ST ANG SEN COM CIRCAN communication circuit or steering angle sensor is malfunc-
tioning.BRC-51, "Inspection 16:
CAN Communi-
cation Circuit"
C1170 VARIANT CODING In a case where VARIANT CODING is different.BRC-36,
"Inspection 3:
ABS Actuator
and Electric Unit
(Control Unit)"
C1185 ACC CONT ICC sensor integrated unit internal malfunction.BRC-50,
"Inspection 14:
ICC Sensor Inte-
grated Unit Cir-
cuit (With ICC)"
U1000 CAN COMM CIRCUIT When there is a malfunction in the CAN communication circuit.BRC-51,
"Inspection 16:
CAN Communi-
cation Circuit"
(Note 2)
U1100 ACC COMM CIRCUITWhen there is a malfunction in the CAN communication circuit or
ICC sensor integrated unit.BRC-51,
"Inspection 16:
CAN Communi-
cation Circuit"
Code Display item Malfunction detecting condition Check item
Page 3077 of 5621
![INFINITI M35 2006 Factory Service Manual EM-14
[VQ35DE]
ENGINE ROOM COVER
Revision: 2006 January2006 M35/M45
ENGINE ROOM COVERPFP:14049
ComponentsNBS004MS
Removal and InstallationNBS004MT
REMOVAL
CAUTION:
Do not damage or scratch cover when INFINITI M35 2006 Factory Service Manual EM-14
[VQ35DE]
ENGINE ROOM COVER
Revision: 2006 January2006 M35/M45
ENGINE ROOM COVERPFP:14049
ComponentsNBS004MS
Removal and InstallationNBS004MT
REMOVAL
CAUTION:
Do not damage or scratch cover when](/img/42/57023/w960_57023-3076.png)
EM-14
[VQ35DE]
ENGINE ROOM COVER
Revision: 2006 January2006 M35/M45
ENGINE ROOM COVERPFP:14049
ComponentsNBS004MS
Removal and InstallationNBS004MT
REMOVAL
CAUTION:
Do not damage or scratch cover when installing or removing.
Refer to EM-19, "INTAKE MANIFOLD COLLECTOR" for removal and installation of engine cover.
Refer to EM-17, "AIR CLEANER AND AIR DUCT" for removal and installation of air duct (inlet).
Remove the washer tank cap before removing the engine room cover (RH).
Remove the engine room covers (RH and LH) by lifting the clipped point using a clip driver.
Major parts and inspection points under each cover are as follows; (numbered as in figure)
1. Upper side of engine assembly
2. Battery, relay box
3. Power steering fluid reservoir tank, engine coolant reservoir tank, relay box
4. Engine assembly front side, drive belts, cooling fan
5. Mass air flow sensor, air cleaner case
6. Brake master cylinder, brake booster
INSTALLATION
Installation is the reverse order of removal.
1. Engine cover 2. Battery cover 3. Engine room cover (RH)
4. Air duct (inlet) 5. Engine room cover (LH) 6. Brake master cylinder cover
A. Clip (secure at back surface)
PBIC3824E
Page 3078 of 5621
![INFINITI M35 2006 Factory Service Manual DRIVE BELTS
EM-15
[VQ35DE]
C
D
E
F
G
H
I
J
K
L
MA
EM
Revision: 2006 January2006 M35/M45
DRIVE BELTSPFP:02117
Checking Drive BeltsNBS004MU
WAR NING :
Be sure to perform when engine is stopped.
1. Inspe INFINITI M35 2006 Factory Service Manual DRIVE BELTS
EM-15
[VQ35DE]
C
D
E
F
G
H
I
J
K
L
MA
EM
Revision: 2006 January2006 M35/M45
DRIVE BELTSPFP:02117
Checking Drive BeltsNBS004MU
WAR NING :
Be sure to perform when engine is stopped.
1. Inspe](/img/42/57023/w960_57023-3077.png)
DRIVE BELTS
EM-15
[VQ35DE]
C
D
E
F
G
H
I
J
K
L
MA
EM
Revision: 2006 January2006 M35/M45
DRIVE BELTSPFP:02117
Checking Drive BeltsNBS004MU
WAR NING :
Be sure to perform when engine is stopped.
1. Inspect belts for cracks, fraying, wear and oil. If necessary, replace.
2. Inspect drive belt deflection or tension at a point on belt midway
between pulleys.
Inspection should be done only when engine is cold, or over
30 minutes after engine is stopped.
Measure the belt tension with belt tension gauge (Commercial
service tool: BT3373-F or equivalent) at points marked
shown in the figure.
When measuring the deflection, apply 98 N (10 kg, 22 lb) at
the marked point.
Adjust if the belt deflection exceeds the limit or if the belt ten-
sion is not within specifications.
CAUTION:
When checking the belt deflection or the tension immediately after installation, first adjust it to
the specified value. Then, after turning crankshaft two turns or more, re-adjust to the specified
value to avoid variation in deflection between pulleys.
Tighten idler pulley lock nut by hand and measure the deflection or the tension without loose-
ness.
Belt Deflection and Tension
*: If belt tension gauge cannot be installed at check points shown, check drive belt tension at different location on belt.
Tension AdjustmentNBS004MV
CAUTION:
When belt is replaced with a new one, adjust it to value for “New belt” to accommodate for insuffi-
cient adaptability with pulley grooves.
When deflection or tension of belt being used exceeds “Limit”, adjust it to value for “After adjust-
ment”.
When checking belt deflection or tension immediately after installation, first adjust it to the speci-
fied value. Then, after turning crankshaft two turns or more, re-adjust to the specified value to
avoid variation in deflection between pulleys.
When installing belt, make sure that it is correctly engaged with pulley grooves.
Keep engine oil, working fluid and engine coolant away from belt and pulley grooves.
Do not twist or bend belt excessively.
KBIA1731J
ItemsDeflection adjustment Unit: mm (in) Tension adjustment* Unit: N (kg, lb)
Used belt
New beltUsed belt
New belt
Limit After adjustment Limit After adjustment
Alternator and
power steering
oil pump belt7 (0.28)4 - 5
(0.16 - 0.20)3.5 - 4.5
(0.138 - 0.177)294 (30, 66)730 - 818
(74.5 - 83.5,
164 - 184)838 - 926
(85.5 - 94.5,
188 - 208)
A/C compressor
belt12 (0.47)9 - 10
(0.35 - 0.39)8 - 9
(0.31 - 0.35)196 (20, 44)348 - 436
(35.5 - 44.5,
78 - 98)470 - 559
(48 - 57,
106 - 126)
Applied pushing
force98 N (10 kg, 22 lb) —
PortionBelt tightening method for adjustment
Alternator and power steering oil pump belt Adjusting bolt on idler pulley
A/C compressor belt Adjusting bolt on idler pulley
Page 3117 of 5621
![INFINITI M35 2006 Factory Service Manual EM-54
[VQ35DE]
FRONT TIMING CHAIN CASE
Revision: 2006 January2006 M35/M45
FRONT TIMING CHAIN CASEPFP:13599
Removal and InstallationNBS004NI
NOTE:
This section describes removal/installation procedure INFINITI M35 2006 Factory Service Manual EM-54
[VQ35DE]
FRONT TIMING CHAIN CASE
Revision: 2006 January2006 M35/M45
FRONT TIMING CHAIN CASEPFP:13599
Removal and InstallationNBS004NI
NOTE:
This section describes removal/installation procedure](/img/42/57023/w960_57023-3116.png)
EM-54
[VQ35DE]
FRONT TIMING CHAIN CASE
Revision: 2006 January2006 M35/M45
FRONT TIMING CHAIN CASEPFP:13599
Removal and InstallationNBS004NI
NOTE:
This section describes removal/installation procedure of front timing chain case and timing chain related
parts without removing oil pan (upper) on the vehicle.
When oil pan (upper) needs to be removed or installed, or when rear timing chain case is removed or
installed, remove oil pans (upper and lower) first. Then remove front timing chain case, timing chain
related parts, and rear timing chain case in this order, and install in reverse order of removal. Refer to EM-
64, "TIMING CHAIN" .
Refer to EM-64, "TIMING CHAIN" for component parts location.
REMOVAL
1. Remove engine room cover (RH and LH). Refer to EM-14, "ENGINE ROOM COVER" .
2. Disconnect the battery cable from the negative terminal. Refer to SC-4, "
BATTERY" .
3. Remove engine cover with power tool. Refer to EM-19, "
INTAKE MANIFOLD COLLECTOR" .
4. Remove air duct (inlet) and air cleaner case assembly. Refer to EM-17, "
AIR CLEANER AND AIR DUCT"
.
5. Remove front and rear engine undercover with power tool.
6. Release the fuel pressure. Refer to EC-98, "
FUEL PRESSURE RELEASE" .
7. Drain engine oil. Refer to LU-9, "
Changing Engine Oil" .
CAUTION:
Perform this step when the engine is cold.
Do not spill engine oil on drive belts.
8. Drain engine coolant from radiator. Refer to CO-11, "
Changing Engine Coolant" .
CAUTION:
Perform this step when the engine is cold.
Do not spill engine coolant on drive belts.
9. Remove radiator hose (upper and lower) and A/T fluid cooler hose. Refer to CO-14, "
RADIATOR" .
10. Separate engine harnesses removing their brackets from front timing chain case.
11. Remove drive belts. Refer to EM-15, "
DRIVE BELTS" .
12. Remove intake manifold collectors (upper and lower). Refer to EM-19, "
INTAKE MANIFOLD COLLEC-
TOR" .
13. Remove power steering oil pump from bracket with piping connected, and temporarily secure it aside.
Refer to PS-29, "
POWER STEERING OIL PUMP" .
14. Remove power steering oil pump bracket. Refer to PS-29, "
POWER STEERING OIL PUMP" .
15. Remove alternator. Refer to SC-23, "
CHARGING SYSTEM" .
16. Remove water bypass hose, water hose clamp and idler pulley bracket from front timing chain case.
17. Remove intake valve timing control covers.
Loosen mounting bolts in reverse order as shown in the fig-
ure.
U s e t h e s e a l c u t t e r [ S S T: K V 1 0 1111 0 0 ( J 3 7 2 2 8 ) ] t o c u t l i q u i d
gasket for removal.
CAUTION:
Shaft is internally jointed with camshaft sprocket (INT) cen-
ter hole. When removing, keep it horizontal until it is com-
pletely disconnected.
SEM728G
Page 3126 of 5621
![INFINITI M35 2006 Factory Service Manual FRONT TIMING CHAIN CASE
EM-63
[VQ35DE]
C
D
E
F
G
H
I
J
K
L
MA
EM
Revision: 2006 January2006 M35/M45
10. Rotate crankshaft pulley in normal direction (clockwise when viewed from front) to c INFINITI M35 2006 Factory Service Manual FRONT TIMING CHAIN CASE
EM-63
[VQ35DE]
C
D
E
F
G
H
I
J
K
L
MA
EM
Revision: 2006 January2006 M35/M45
10. Rotate crankshaft pulley in normal direction (clockwise when viewed from front) to c](/img/42/57023/w960_57023-3125.png)
FRONT TIMING CHAIN CASE
EM-63
[VQ35DE]
C
D
E
F
G
H
I
J
K
L
MA
EM
Revision: 2006 January2006 M35/M45
10. Rotate crankshaft pulley in normal direction (clockwise when viewed from front) to confirm it turns
smoothly.
11. For the following operations, perform steps in the reverse order of removal.
INSPECTION AFTER INSTALLATION
Inspection for Leaks
The following are procedures for checking fluids leak, lubricates leak.
Before starting engine, check oil/fluid levels including engine coolant and engine oil. If less than required
quantity, fill to the specified level. Refer to MA-12, "
RECOMMENDED FLUIDS AND LUBRICANTS" .
Use procedure below to check for fuel leakage.
–Turn ignition switch “ON” (with engine stopped). With fuel pressure applied to fuel piping, check for fuel
leakage at connection points.
–Start engine. With engine speed increased, check again for fuel leakage at connection points.
Run engine to check for unusual noise and vibration.
NOTE:
If hydraulic pressure inside chain tensioner drops after removal/installation, slack in guide may generate a
pounding noise during and just after the engine start. However, this does not indicate an unusualness.
Noise will stop after hydraulic pressure rises.
Warm up engine thoroughly to make sure there is no leakage of fuel, or any oil/fluids including engine oil
and engine coolant.
Bleed air from lines and hoses of applicable lines, such as in cooling system.
After cooling down engine, again check oil/fluid levels including engine oil and engine coolant. Refill to the
specified level, if necessary.
Summary of the inspection items:
* Transmission/transaxle/CVT fluid, power steering fluid, brake fluid, etc. Item Before starting engine Engine running After engine stopped
Engine coolant Level Leakage Level
Engine oil Level Leakage Level
Other oils and fluid* Level Leakage Level
Fuel Leakage Leakage Leakage
Page 3128 of 5621
![INFINITI M35 2006 Factory Service Manual TIMING CHAIN
EM-65
[VQ35DE]
C
D
E
F
G
H
I
J
K
L
MA
EM
Revision: 2006 January2006 M35/M45
Removal and InstallationNBS004NK
NOTE:
This section describes procedures for removing/installing front timing c INFINITI M35 2006 Factory Service Manual TIMING CHAIN
EM-65
[VQ35DE]
C
D
E
F
G
H
I
J
K
L
MA
EM
Revision: 2006 January2006 M35/M45
Removal and InstallationNBS004NK
NOTE:
This section describes procedures for removing/installing front timing c](/img/42/57023/w960_57023-3127.png)
TIMING CHAIN
EM-65
[VQ35DE]
C
D
E
F
G
H
I
J
K
L
MA
EM
Revision: 2006 January2006 M35/M45
Removal and InstallationNBS004NK
NOTE:
This section describes procedures for removing/installing front timing chain case and timing chain related
parts, and rear timing chain case, when oil pan (upper) needs to be removed/installed for engine overhaul,
etc.
To remove/install front timing chain case, timing chain, and its related parts without removing oil pan
(upper), refer to EM-54, "
FRONT TIMING CHAIN CASE" .
REMOVAL
1. Remove engine room cover (RH and LH) Refer to EM-14, "ENGINE ROOM COVER" .
2. Remove front tire.
3. Disconnect the battery cable from the negative terminal.
4. Remove engine cover with power tool. Refer to EM-19, "
INTAKE MANIFOLD COLLECTOR" .
5. Remove air duct (inlet) and air cleaner case assembly. Refer to EM-17, "
AIR CLEANER AND AIR DUCT"
.
6. Remove front and rear engine undercover with power tool.
7. Release the fuel pressure. Refer to EC-98, "
FUEL PRESSURE RELEASE" .
8. Drain engine coolant from radiator. Refer to CO-11, "
Changing Engine Coolant" .
CAUTION:
Perform this step when the engine is cold.
Do not spill engine coolant on drive belts.
9. Remove radiator hose (upper and lower) and A/T fluid cooler hose. Refer to CO-14, "
RADIATOR" .
10. Drain engine oil. Refer to LU-9, "
Changing Engine Oil" .
CAUTION:
Perform this step when the engine is cold.
Do not spill engine oil on drive belts.
11. Separate engine harnesses removing their brackets from front timing chain case.
12. Remove intake manifold collectors (upper and lower). Refer to EM-19, "
INTAKE MANIFOLD COLLEC-
TOR" .
13. Remove radiator cooling fan assembly. Refer to CO-22, "
COOLING FAN" .
14. Remove drive belts. Refer to EM-15, "
DRIVE BELTS" .
15. Remove A/C compressor from bracket with piping connected, and temporarily secure it aside. Refer to
ATC-155, "
Removal and Installation of Compressor" .
16. Remove power steering oil pump from bracket with piping connected, and temporarily secure it aside.
Refer to PS-29, "
POWER STEERING OIL PUMP" .
17. Remove power steering oil pump bracket. Refer to PS-29, "
POWER STEERING OIL PUMP" .
18. Remove alternator. Refer to SC-23, "
CHARGING SYSTEM" .
19. Remove water bypass hose, water hose clamp and idler pulley bracket from front timing chain case.
20. Remove intake valve timing control covers.
1. Timing chain tensioner (secondary) 2. Internal chain guide 3. Timing chain tensioner (secondary)
4. Camshaft sprocket (EXH) 5. Timing chain (secondary) 6. Timing chain (primary)
7. Camshaft sprocket (INT) 8. Camshaft sprocket (EXH) 9. Timing chain (secondary)
10. Camshaft sprocket (INT) 11. Slack guide 12. Crankshaft sprocket
13. Timing chain tensioner (primary) 14. Intake valve timing control cover 15. Collared O-ring
16. O-ring 17. Chain tensioner cover 18. Intake valve timing control cover
19. Water hose clamp 20. Idler pulley bracket 21. Idler pulley
22. Crankshaft pulley 23. Front oil seal 24. Idler pulley
25. A/C compressor bracket 26. Water pump cover 27. Bracket
28. Front timing chain case 29. Bracket 30. Rear timing chain case
31. O-ring 32. Tension guide 33. Water drain plug (front side)
Page 3146 of 5621
![INFINITI M35 2006 Factory Service Manual TIMING CHAIN
EM-83
[VQ35DE]
C
D
E
F
G
H
I
J
K
L
MA
EM
Revision: 2006 January2006 M35/M45
Summary of the inspection items:
* Transmission/transaxle/CVT fluid, power steering fluid, brake fluid, etc. It INFINITI M35 2006 Factory Service Manual TIMING CHAIN
EM-83
[VQ35DE]
C
D
E
F
G
H
I
J
K
L
MA
EM
Revision: 2006 January2006 M35/M45
Summary of the inspection items:
* Transmission/transaxle/CVT fluid, power steering fluid, brake fluid, etc. It](/img/42/57023/w960_57023-3145.png)
TIMING CHAIN
EM-83
[VQ35DE]
C
D
E
F
G
H
I
J
K
L
MA
EM
Revision: 2006 January2006 M35/M45
Summary of the inspection items:
* Transmission/transaxle/CVT fluid, power steering fluid, brake fluid, etc. Item Before starting engine Engine running After engine stopped
Engine coolant Level Leakage Level
Engine oil Level Leakage Level
Other oils and fluid* Level Leakage Level
Fuel Leakage Leakage Leakage
Page 3156 of 5621
![INFINITI M35 2006 Factory Service Manual CAMSHAFT
EM-93
[VQ35DE]
C
D
E
F
G
H
I
J
K
L
MA
EM
Revision: 2006 January2006 M35/M45
Summary of the inspection items:
* Transmission/transaxle/CVT fluid, power steering fluid, brake fluid, etc.
Va l v INFINITI M35 2006 Factory Service Manual CAMSHAFT
EM-93
[VQ35DE]
C
D
E
F
G
H
I
J
K
L
MA
EM
Revision: 2006 January2006 M35/M45
Summary of the inspection items:
* Transmission/transaxle/CVT fluid, power steering fluid, brake fluid, etc.
Va l v](/img/42/57023/w960_57023-3155.png)
CAMSHAFT
EM-93
[VQ35DE]
C
D
E
F
G
H
I
J
K
L
MA
EM
Revision: 2006 January2006 M35/M45
Summary of the inspection items:
* Transmission/transaxle/CVT fluid, power steering fluid, brake fluid, etc.
Va l v e C l e a r a n c eNBS004NN
INSPECTION
Perform inspection as follows after removal, installation or replacement of camshaft or valve-related parts, or if
there is unusual engine conditions regarding valve clearance.
In cases of removing/installing or replacing camshaft and valve-
related parts, or of unusual engine conditions due to changes in
valve clearance (found malfunctions during stating, idling or causing
noise), perform inspection as follows:
1. Remove rocker covers (right and left bank). Refer to EM-51, "
ROCKER COVER" .
2. Measure the valve clearance as follows:
a. Set No. 1 cylinder at TDC of its compression stroke.
Rotate crankshaft pulley clockwise to align timing mark
(grooved line without color) with timing indicator.
Make sure that intake and exhaust cam nose on No. 1 cylin-
der (engine front side of right bank) are located as shown in
the figure.
If not, turn crankshaft one revolution (360 degrees) and align
as shown in the figure.
Item Before starting engine Engine running After engine stopped
Engine coolant Level Leakage Level
Engine oil Level Leakage Level
Other oils and fluid* Level Leakage Level
Fuel Leakage Leakage Leakage
SEM713A
KBIA1717J
SEM418G