tow INFINITI M35 2006 Factory Service Manual
[x] Cancel search | Manufacturer: INFINITI, Model Year: 2006, Model line: M35, Model: INFINITI M35 2006Pages: 5621, PDF Size: 65.56 MB
Page 87 of 5621
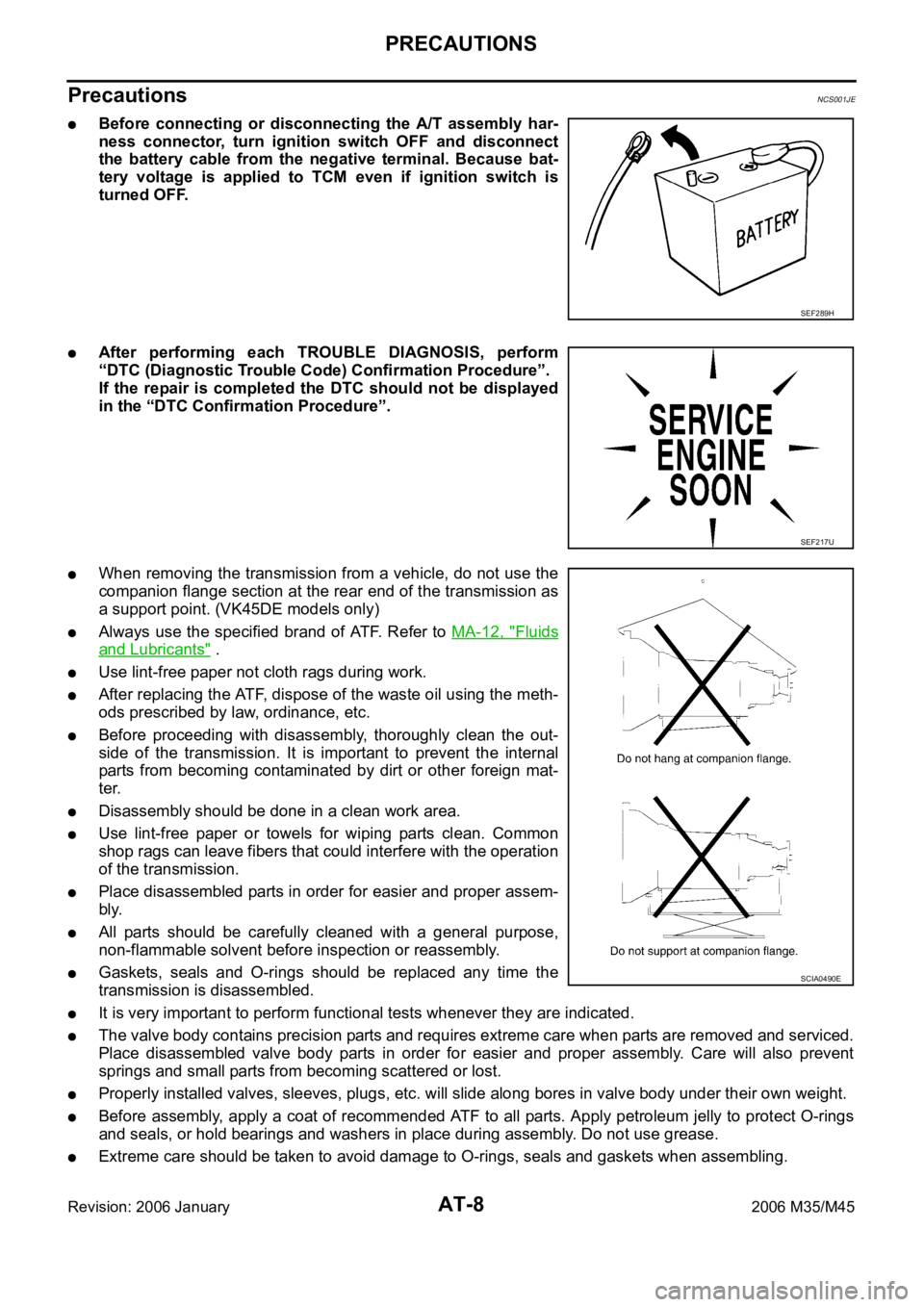
AT-8
PRECAUTIONS
Revision: 2006 January2006 M35/M45
Precautions NCS001JE
Before connecting or disconnecting the A/T assembly har-
ness connector, turn ignition switch OFF and disconnect
the battery cable from the negative terminal. Because bat-
tery voltage is applied to TCM even if ignition switch is
turned OFF.
After performing each TROUBLE DIAGNOSIS, perform
“DTC (Diagnostic Trouble Code) Confirmation Procedure”.
If the repair is completed the DTC should not be displayed
in the “DTC Confirmation Procedure”.
When removing the transmission from a vehicle, do not use the
companion flange section at the rear end of the transmission as
a support point. (VK45DE models only)
Always use the specified brand of ATF. Refer to MA-12, "Fluids
and Lubricants" .
Use lint-free paper not cloth rags during work.
After replacing the ATF, dispose of the waste oil using the meth-
ods prescribed by law, ordinance, etc.
Before proceeding with disassembly, thoroughly clean the out-
side of the transmission. It is important to prevent the internal
parts from becoming contaminated by dirt or other foreign mat-
ter.
Disassembly should be done in a clean work area.
Use lint-free paper or towels for wiping parts clean. Common
shop rags can leave fibers that could interfere with the operation
of the transmission.
Place disassembled parts in order for easier and proper assem-
bly.
All parts should be carefully cleaned with a general purpose,
non-flammable solvent before inspection or reassembly.
Gaskets, seals and O-rings should be replaced any time the
transmission is disassembled.
It is very important to perform functional tests whenever they are indicated.
The valve body contains precision parts and requires extreme care when parts are removed and serviced.
Place disassembled valve body parts in order for easier and proper assembly. Care will also prevent
springs and small parts from becoming scattered or lost.
Properly installed valves, sleeves, plugs, etc. will slide along bores in valve body under their own weight.
Before assembly, apply a coat of recommended ATF to all parts. Apply petroleum jelly to protect O-rings
and seals, or hold bearings and washers in place during assembly. Do not use grease.
Extreme care should be taken to avoid damage to O-rings, seals and gaskets when assembling.
SEF289H
SEF217U
SCIA0490E
Page 94 of 5621
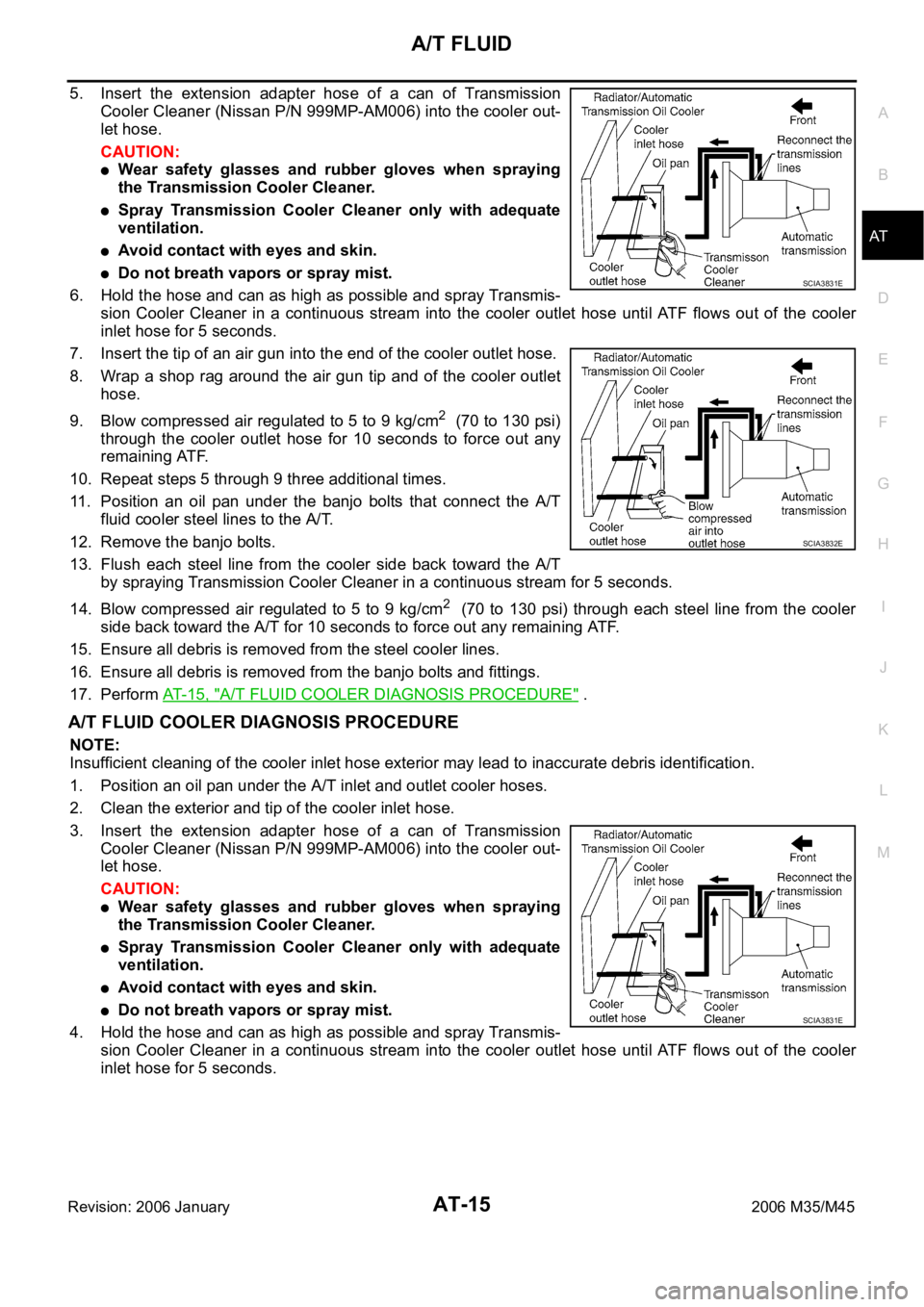
A/T FLUID
AT-15
D
E
F
G
H
I
J
K
L
MA
B
AT
Revision: 2006 January2006 M35/M45
5. Insert the extension adapter hose of a can of Transmission
Cooler Cleaner (Nissan P/N 999MP-AM006) into the cooler out-
let hose.
CAUTION:
Wear safety glasses and rubber gloves when spraying
the Transmission Cooler Cleaner.
Spray Transmission Cooler Cleaner only with adequate
ventilation.
Avoid contact with eyes and skin.
Do not breath vapors or spray mist.
6. Hold the hose and can as high as possible and spray Transmis-
sion Cooler Cleaner in a continuous stream into the cooler outlet hose until ATF flows out of the cooler
inlet hose for 5 seconds.
7. Insert the tip of an air gun into the end of the cooler outlet hose.
8. Wrap a shop rag around the air gun tip and of the cooler outlet
hose.
9. Blow compressed air regulated to 5 to 9 kg/cm
2 (70 to 130 psi)
through the cooler outlet hose for 10 seconds to force out any
remaining ATF.
10. Repeat steps 5 through 9 three additional times.
11. Position an oil pan under the banjo bolts that connect the A/T
fluid cooler steel lines to the A/T.
12. Remove the banjo bolts.
13. Flush each steel line from the cooler side back toward the A/T
by spraying Transmission Cooler Cleaner in a continuous stream for 5 seconds.
14. Blow compressed air regulated to 5 to 9 kg/cm
2 (70 to 130 psi) through each steel line from the cooler
side back toward the A/T for 10 seconds to force out any remaining ATF.
15. Ensure all debris is removed from the steel cooler lines.
16. Ensure all debris is removed from the banjo bolts and fittings.
17. Perform AT- 1 5 , "
A/T FLUID COOLER DIAGNOSIS PROCEDURE" .
A/T FLUID COOLER DIAGNOSIS PROCEDURE
NOTE:
Insufficient cleaning of the cooler inlet hose exterior may lead to inaccurate debris identification.
1. Position an oil pan under the A/T inlet and outlet cooler hoses.
2. Clean the exterior and tip of the cooler inlet hose.
3. Insert the extension adapter hose of a can of Transmission
Cooler Cleaner (Nissan P/N 999MP-AM006) into the cooler out-
let hose.
CAUTION:
Wear safety glasses and rubber gloves when spraying
the Transmission Cooler Cleaner.
Spray Transmission Cooler Cleaner only with adequate
ventilation.
Avoid contact with eyes and skin.
Do not breath vapors or spray mist.
4. Hold the hose and can as high as possible and spray Transmis-
sion Cooler Cleaner in a continuous stream into the cooler outlet hose until ATF flows out of the cooler
inlet hose for 5 seconds.
SCIA3831E
SCIA3832E
SCIA3831E
Page 123 of 5621
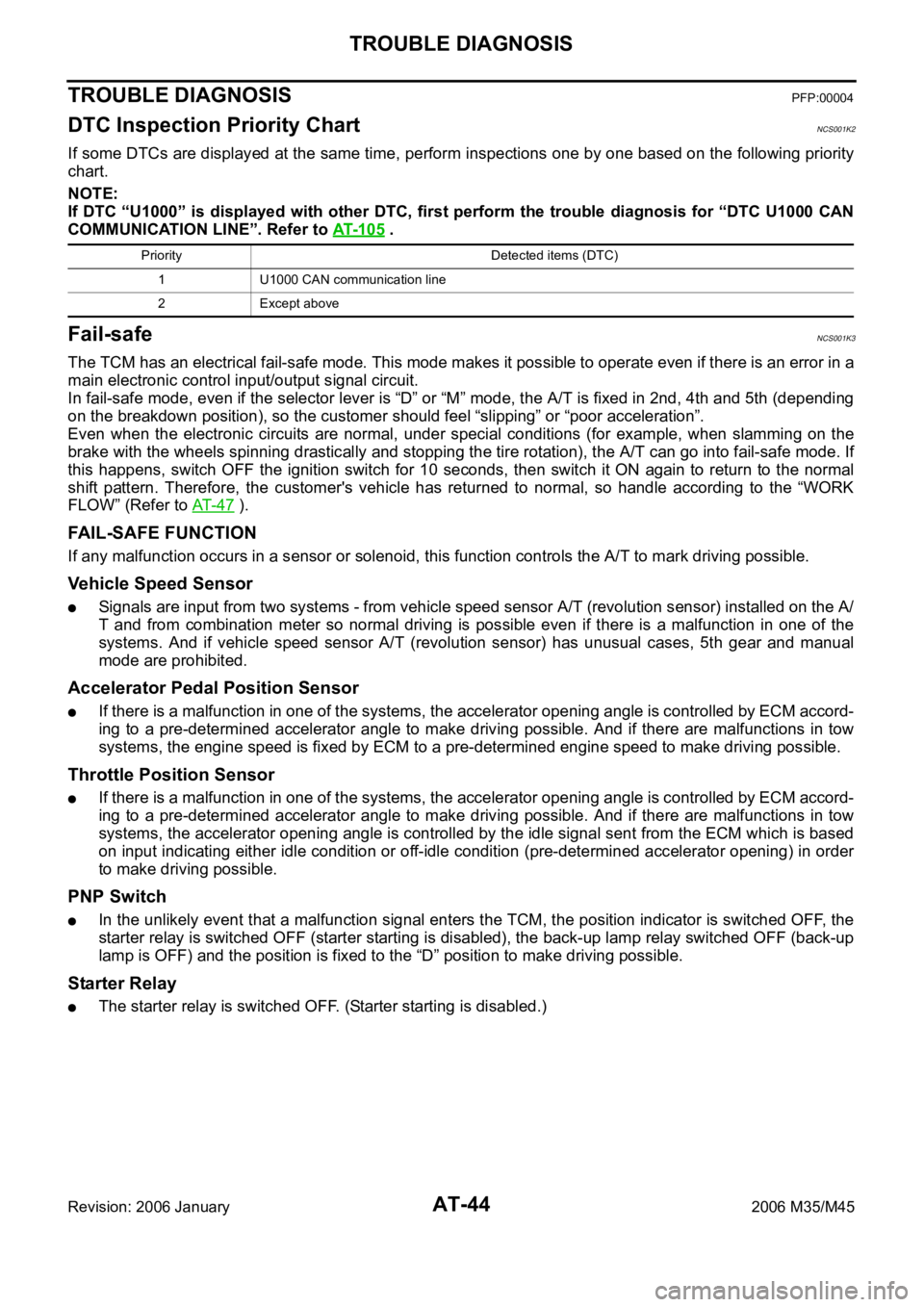
AT-44
TROUBLE DIAGNOSIS
Revision: 2006 January2006 M35/M45
TROUBLE DIAGNOSISPFP:00004
DTC Inspection Priority ChartNCS001K2
If some DTCs are displayed at the same time, perform inspections one by one based on the following priority
chart.
NOTE:
If DTC “U1000” is displayed with other DTC, first perform the trouble diagnosis for “DTC U1000 CAN
COMMUNICATION LINE”. Refer to AT- 1 0 5
.
Fail-safeNCS001K3
The TCM has an electrical fail-safe mode. This mode makes it possible to operate even if there is an error in a
main electronic control input/output signal circuit.
In fail-safe mode, even if the selector lever is “D” or “M” mode, the A/T is fixed in 2nd, 4th and 5th (depending
on the breakdown position), so the customer should feel “slipping” or “poor acceleration”.
Even when the electronic circuits are normal, under special conditions (for example, when slamming on the
brake with the wheels spinning drastically and stopping the tire rotation), the A/T can go into fail-safe mode. If
this happens, switch OFF the ignition switch for 10 seconds, then switch it ON again to return to the normal
shift pattern. Therefore, the customer's vehicle has returned to normal, so handle according to the “WORK
FLOW” (Refer to AT- 4 7
).
FAIL-SAFE FUNCTION
If any malfunction occurs in a sensor or solenoid, this function controls the A/T to mark driving possible.
Vehicle Speed Sensor
Signals are input from two systems - from vehicle speed sensor A/T (revolution sensor) installed on the A/
T and from combination meter so normal driving is possible even if there is a malfunction in one of the
systems. And if vehicle speed sensor A/T (revolution sensor) has unusual cases, 5th gear and manual
mode are prohibited.
Accelerator Pedal Position Sensor
If there is a malfunction in one of the systems, the accelerator opening angle is controlled by ECM accord-
ing to a pre-determined accelerator angle to make driving possible. And if there are malfunctions in tow
systems, the engine speed is fixed by ECM to a pre-determined engine speed to make driving possible.
Throttle Position Sensor
If there is a malfunction in one of the systems, the accelerator opening angle is controlled by ECM accord-
ing to a pre-determined accelerator angle to make driving possible. And if there are malfunctions in tow
systems, the accelerator opening angle is controlled by the idle signal sent from the ECM which is based
on input indicating either idle condition or off-idle condition (pre-determined accelerator opening) in order
to make driving possible.
PNP Switch
In the unlikely event that a malfunction signal enters the TCM, the position indicator is switched OFF, the
starter relay is switched OFF (starter starting is disabled), the back-up lamp relay switched OFF (back-up
lamp is OFF) and the position is fixed to the “D” position to make driving possible.
Starter Relay
The starter relay is switched OFF. (Starter starting is disabled.)
Priority Detected items (DTC)
1 U1000 CAN communication line
2 Except above
Page 306 of 5621
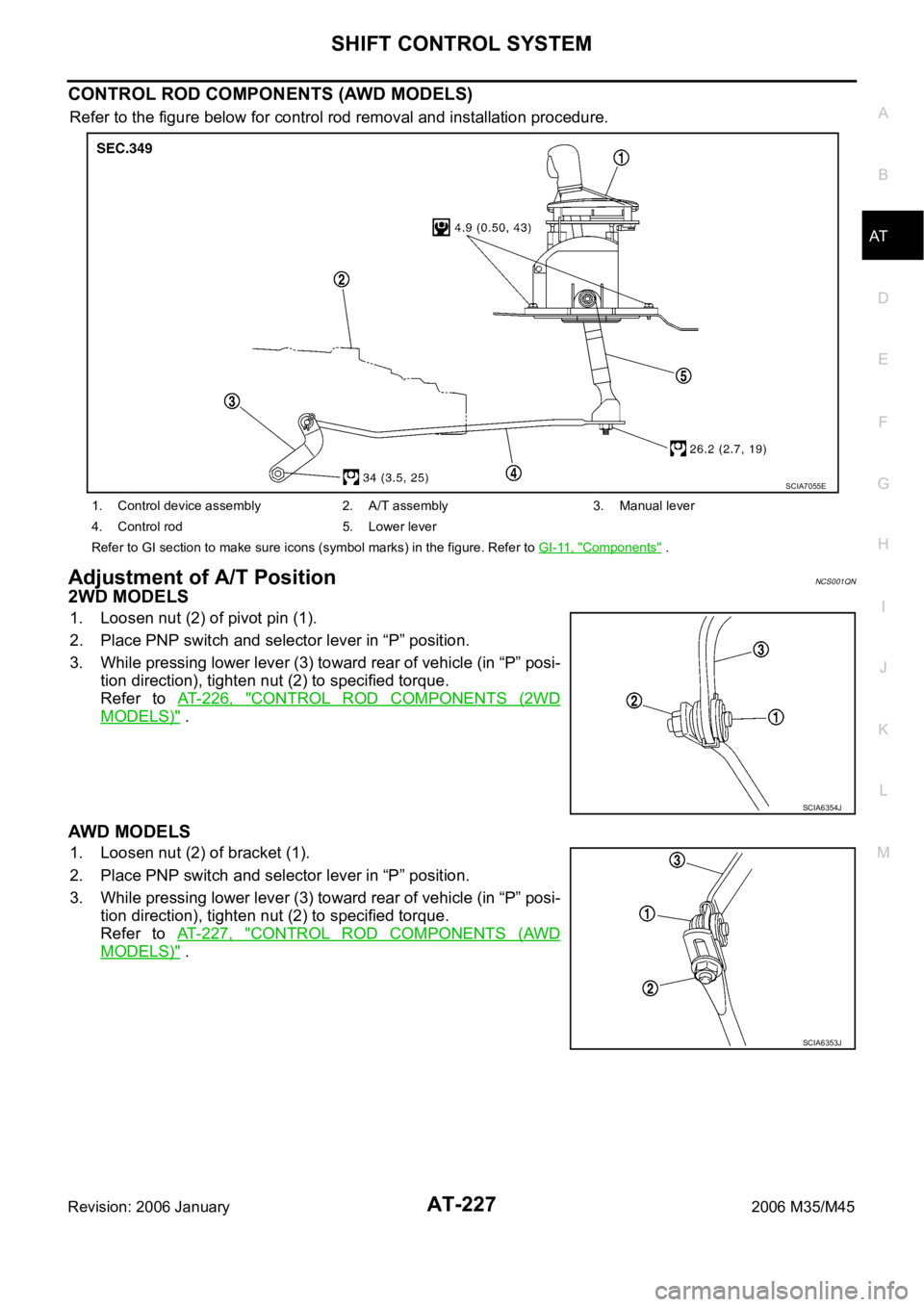
SHIFT CONTROL SYSTEM
AT-227
D
E
F
G
H
I
J
K
L
MA
B
AT
Revision: 2006 January2006 M35/M45
CONTROL ROD COMPONENTS (AWD MODELS)
Refer to the figure below for control rod removal and installation procedure.
Adjustment of A/T PositionNCS001QN
2WD MODELS
1. Loosen nut (2) of pivot pin (1).
2. Place PNP switch and selector lever in “P” position.
3. While pressing lower lever (3) toward rear of vehicle (in “P” posi-
tion direction), tighten nut (2) to specified torque.
Refer to AT- 2 2 6 , "
CONTROL ROD COMPONENTS (2WD
MODELS)" .
AWD MODELS
1. Loosen nut (2) of bracket (1).
2. Place PNP switch and selector lever in “P” position.
3. While pressing lower lever (3) toward rear of vehicle (in “P” posi-
tion direction), tighten nut (2) to specified torque.
Refer to AT-227, "
CONTROL ROD COMPONENTS (AWD
MODELS)" .
1. Control device assembly 2. A/T assembly 3. Manual lever
4. Control rod 5. Lower lever
Refer to GI section to make sure icons (symbol marks) in the figure. Refer to GI-11, "
Components" .
SCIA7055E
SCIA6354J
SCIA6353J
Page 321 of 5621
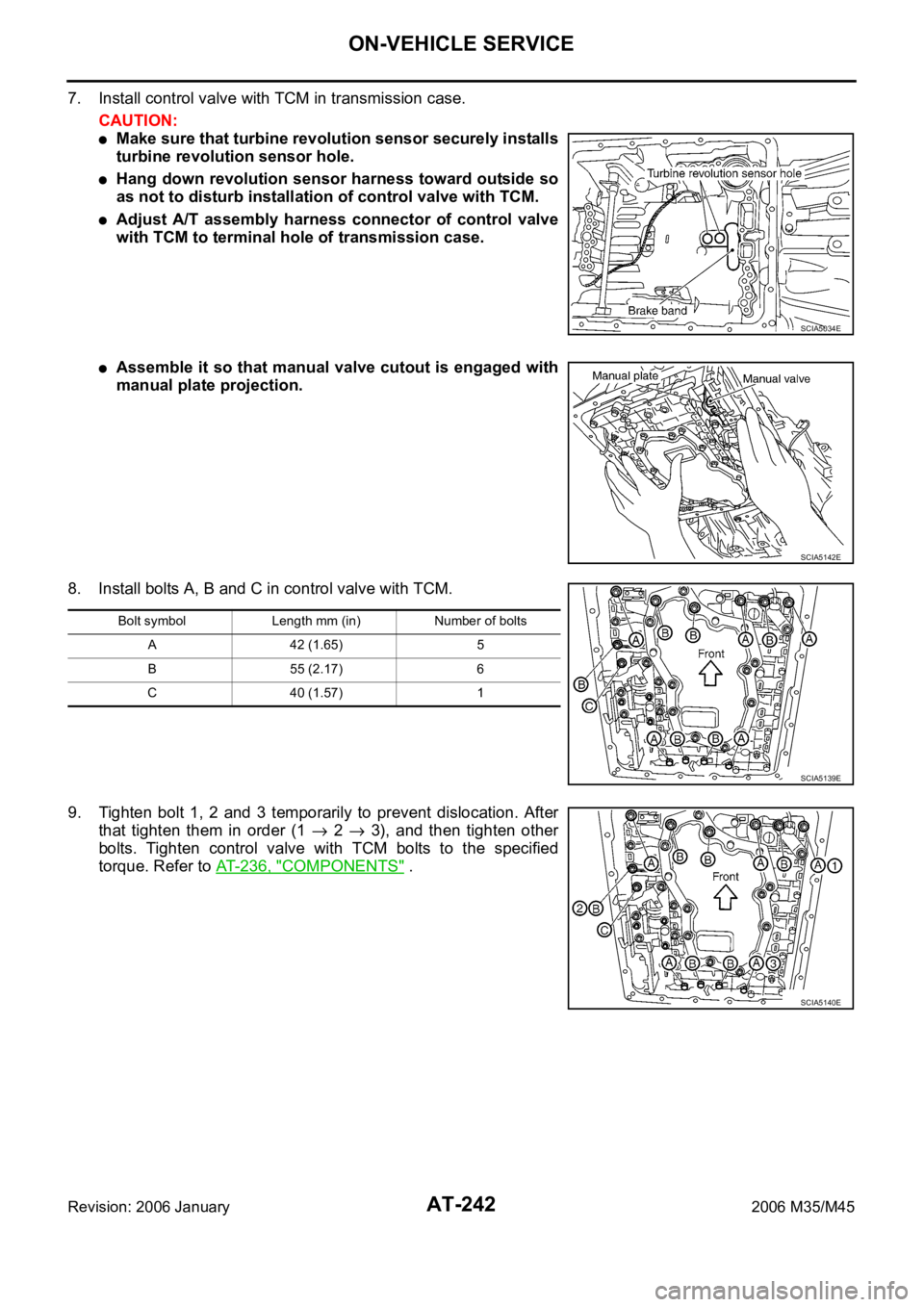
AT-242
ON-VEHICLE SERVICE
Revision: 2006 January2006 M35/M45
7. Install control valve with TCM in transmission case.
CAUTION:
Make sure that turbine revolution sensor securely installs
turbine revolution sensor hole.
Hang down revolution sensor harness toward outside so
as not to disturb installation of control valve with TCM.
Adjust A/T assembly harness connector of control valve
with TCM to terminal hole of transmission case.
Assemble it so that manual valve cutout is engaged with
manual plate projection.
8. Install bolts A, B and C in control valve with TCM.
9. Tighten bolt 1, 2 and 3 temporarily to prevent dislocation. After
that tighten them in order (1
2 3), and then tighten other
bolts. Tighten control valve with TCM bolts to the specified
torque. Refer to AT-236, "
COMPONENTS" .
SCIA5034E
SCIA5142E
Bolt symbol Length mm (in) Number of bolts
A 42 (1.65) 5
B 55 (2.17) 6
C 40 (1.57) 1
SCIA5139E
SCIA5140E
Page 440 of 5621
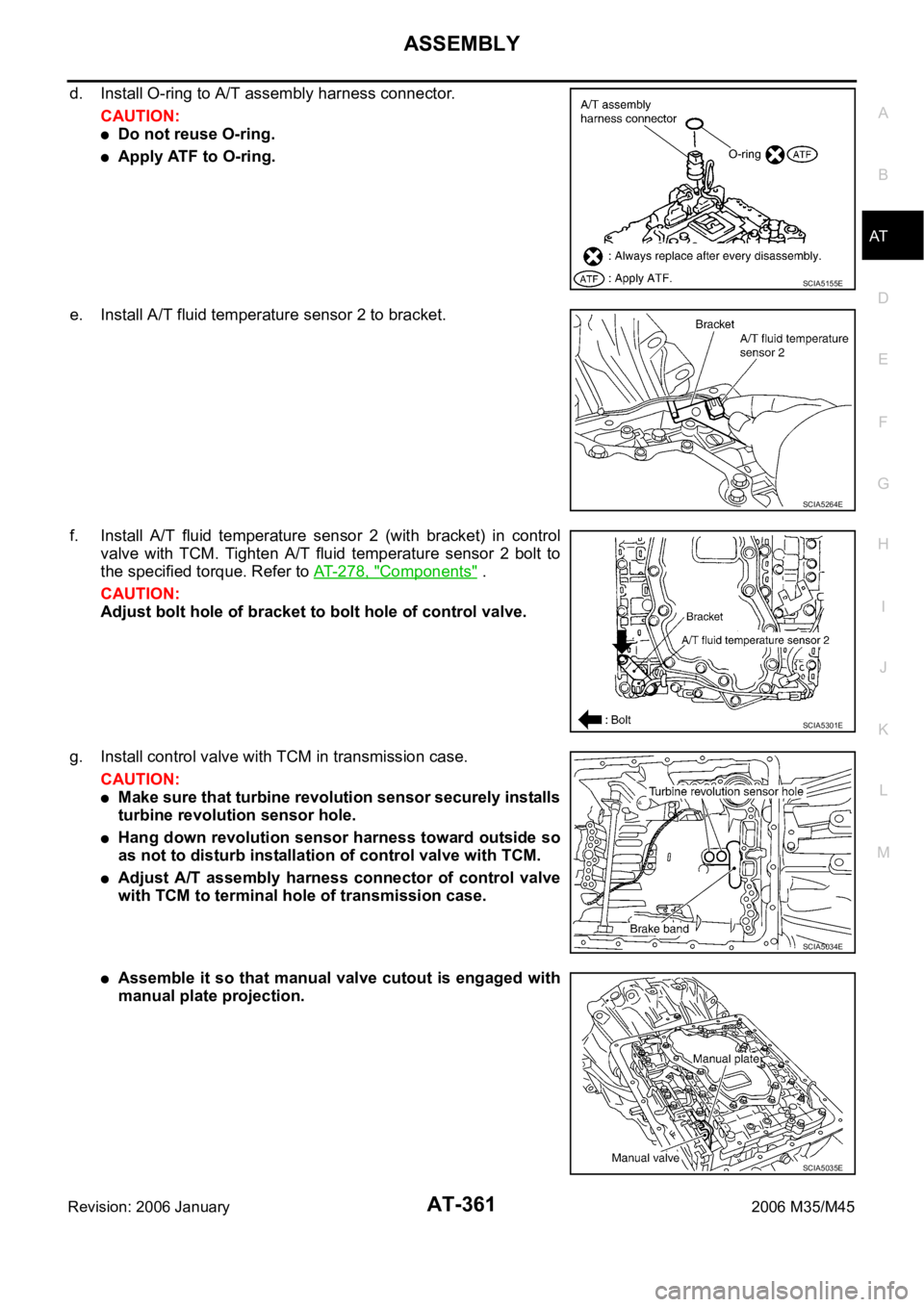
ASSEMBLY
AT-361
D
E
F
G
H
I
J
K
L
MA
B
AT
Revision: 2006 January2006 M35/M45
d. Install O-ring to A/T assembly harness connector.
CAUTION:
Do not reuse O-ring.
Apply ATF to O-ring.
e. Install A/T fluid temperature sensor 2 to bracket.
f. Install A/T fluid temperature sensor 2 (with bracket) in control
valve with TCM. Tighten A/T fluid temperature sensor 2 bolt to
the specified torque. Refer to AT-278, "
Components" .
CAUTION:
Adjust bolt hole of bracket to bolt hole of control valve.
g. Install control valve with TCM in transmission case.
CAUTION:
Make sure that turbine revolution sensor securely installs
turbine revolution sensor hole.
Hang down revolution sensor harness toward outside so
as not to disturb installation of control valve with TCM.
Adjust A/T assembly harness connector of control valve
with TCM to terminal hole of transmission case.
Assemble it so that manual valve cutout is engaged with
manual plate projection.
SCIA5155E
SCIA5264E
SCIA5301E
SCIA5034E
SCIA5035E
Page 582 of 5621
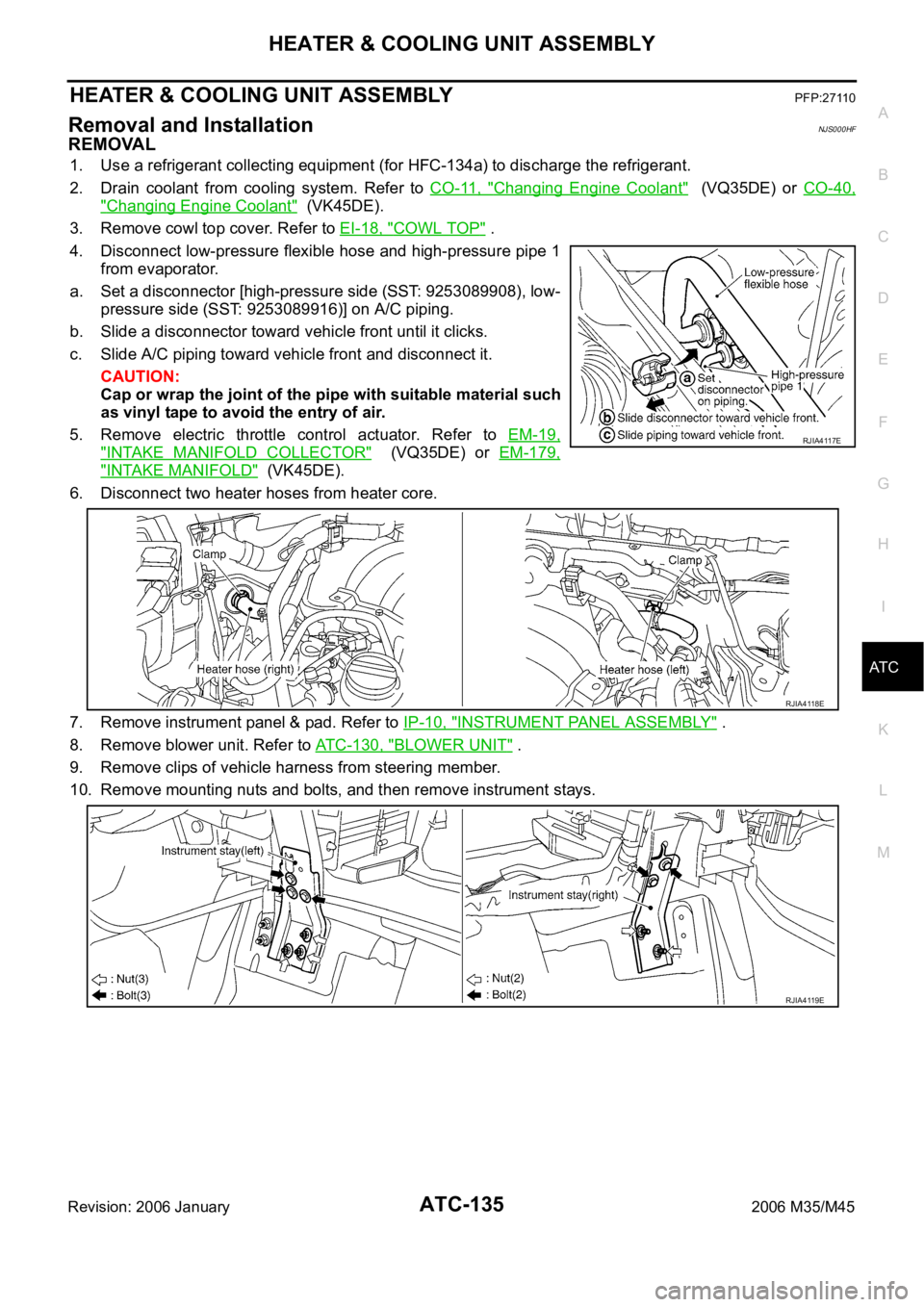
HEATER & COOLING UNIT ASSEMBLY
ATC-135
C
D
E
F
G
H
I
K
L
MA
B
AT C
Revision: 2006 January2006 M35/M45
HEATER & COOLING UNIT ASSEMBLYPFP:27110
Removal and InstallationNJS000HF
REMOVAL
1. Use a refrigerant collecting equipment (for HFC-134a) to discharge the refrigerant.
2. Drain coolant from cooling system. Refer to CO-11, "
Changing Engine Coolant" (VQ35DE) or CO-40,
"Changing Engine Coolant" (VK45DE).
3. Remove cowl top cover. Refer to EI-18, "
COWL TOP" .
4. Disconnect low-pressure flexible hose and high-pressure pipe 1
from evaporator.
a. Set a disconnector [high-pressure side (SST: 9253089908), low-
pressure side (SST: 9253089916)] on A/C piping.
b. Slide a disconnector toward vehicle front until it clicks.
c. Slide A/C piping toward vehicle front and disconnect it.
CAUTION:
Cap or wrap the joint of the pipe with suitable material such
as vinyl tape to avoid the entry of air.
5. Remove electric throttle control actuator. Refer to EM-19,
"INTAKE MANIFOLD COLLECTOR" (VQ35DE) or EM-179,
"INTAKE MANIFOLD" (VK45DE).
6. Disconnect two heater hoses from heater core.
7. Remove instrument panel & pad. Refer to IP-10, "
INSTRUMENT PANEL ASSEMBLY" .
8. Remove blower unit. Refer to ATC-130, "
BLOWER UNIT" .
9. Remove clips of vehicle harness from steering member.
10. Remove mounting nuts and bolts, and then remove instrument stays.
RJIA4117E
RJIA4118E
RJIA4119E
Page 597 of 5621
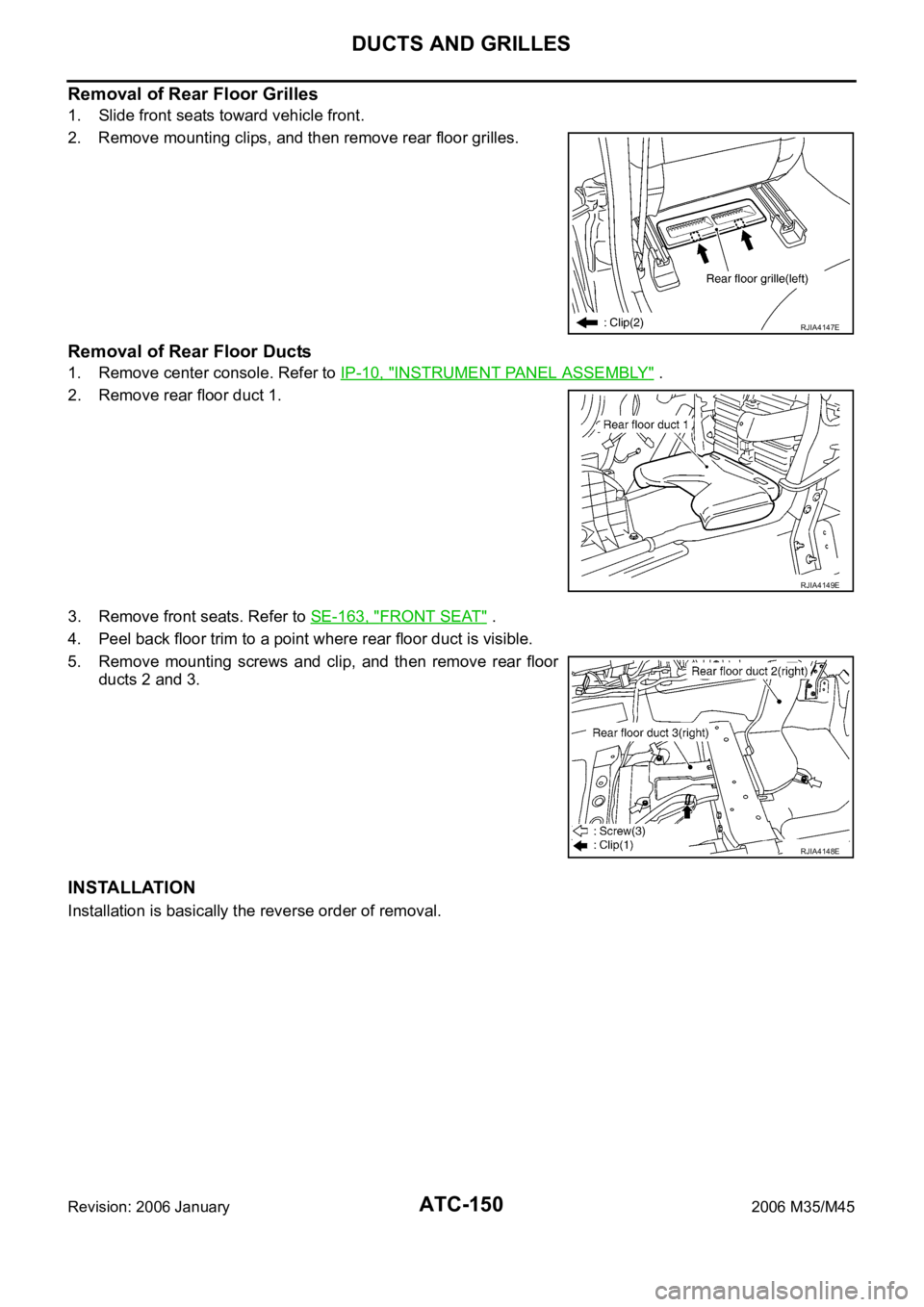
ATC-150
DUCTS AND GRILLES
Revision: 2006 January2006 M35/M45
Removal of Rear Floor Grilles
1. Slide front seats toward vehicle front.
2. Remove mounting clips, and then remove rear floor grilles.
Removal of Rear Floor Ducts
1. Remove center console. Refer to IP-10, "INSTRUMENT PANEL ASSEMBLY" .
2. Remove rear floor duct 1.
3. Remove front seats. Refer to SE-163, "
FRONT SEAT" .
4. Peel back floor trim to a point where rear floor duct is visible.
5. Remove mounting screws and clip, and then remove rear floor
ducts 2 and 3.
INSTALLATION
Installation is basically the reverse order of removal.
RJIA4147E
RJIA4149E
RJIA4148E
Page 605 of 5621
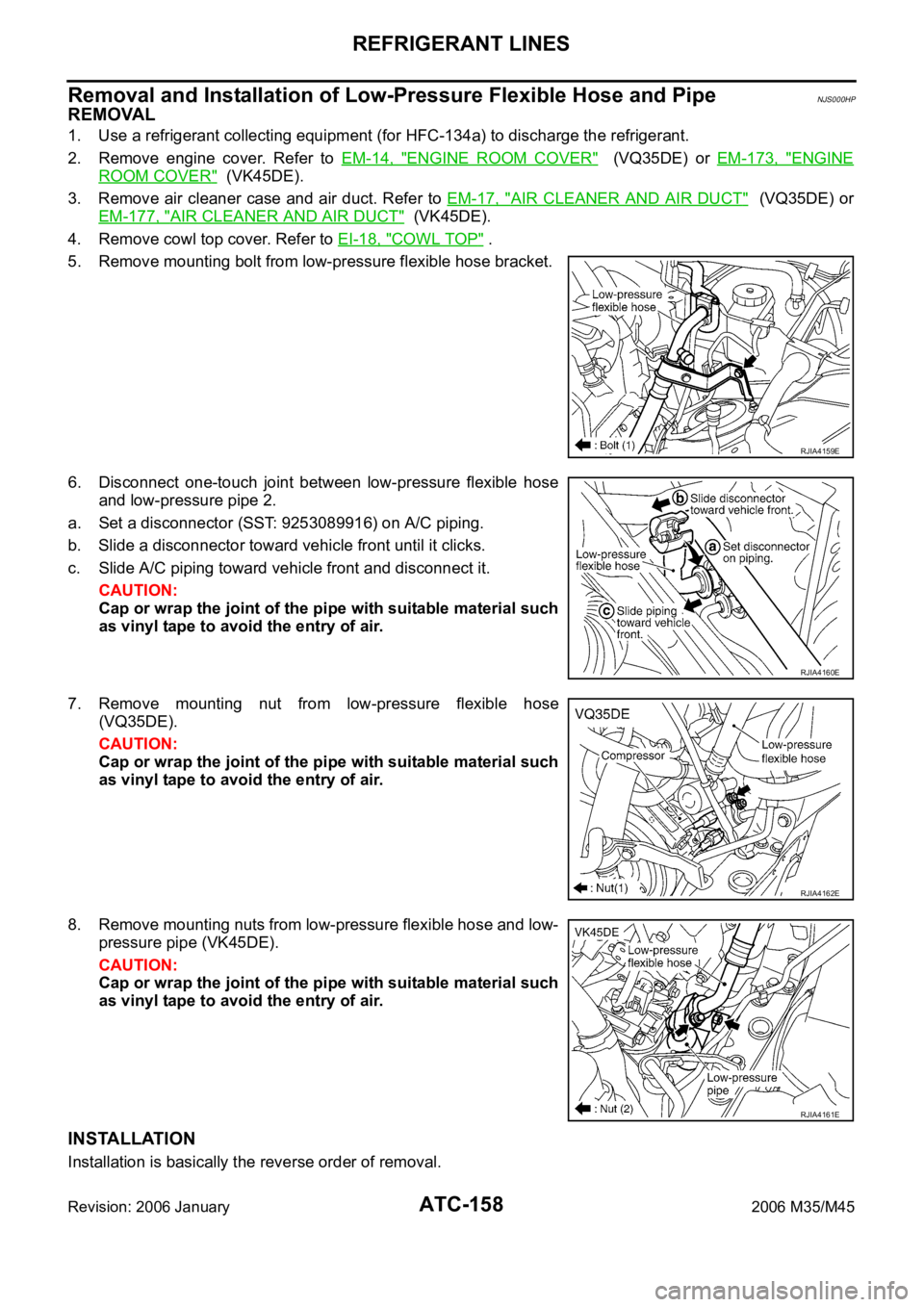
ATC-158
REFRIGERANT LINES
Revision: 2006 January2006 M35/M45
Removal and Installation of Low-Pressure Flexible Hose and PipeNJS000HP
REMOVAL
1. Use a refrigerant collecting equipment (for HFC-134a) to discharge the refrigerant.
2. Remove engine cover. Refer to EM-14, "
ENGINE ROOM COVER" (VQ35DE) or EM-173, "ENGINE
ROOM COVER" (VK45DE).
3. Remove air cleaner case and air duct. Refer to EM-17, "
AIR CLEANER AND AIR DUCT" (VQ35DE) or
EM-177, "
AIR CLEANER AND AIR DUCT" (VK45DE).
4. Remove cowl top cover. Refer to EI-18, "
COWL TOP" .
5. Remove mounting bolt from low-pressure flexible hose bracket.
6. Disconnect one-touch joint between low-pressure flexible hose
and low-pressure pipe 2.
a. Set a disconnector (SST: 9253089916) on A/C piping.
b. Slide a disconnector toward vehicle front until it clicks.
c. Slide A/C piping toward vehicle front and disconnect it.
CAUTION:
Cap or wrap the joint of the pipe with suitable material such
as vinyl tape to avoid the entry of air.
7. Remove mounting nut from low-pressure flexible hose
(VQ35DE).
CAUTION:
Cap or wrap the joint of the pipe with suitable material such
as vinyl tape to avoid the entry of air.
8. Remove mounting nuts from low-pressure flexible hose and low-
pressure pipe (VK45DE).
CAUTION:
Cap or wrap the joint of the pipe with suitable material such
as vinyl tape to avoid the entry of air.
INSTALLATION
Installation is basically the reverse order of removal.
RJIA4159E
RJIA4160E
RJIA4162E
RJIA4161E
Page 608 of 5621
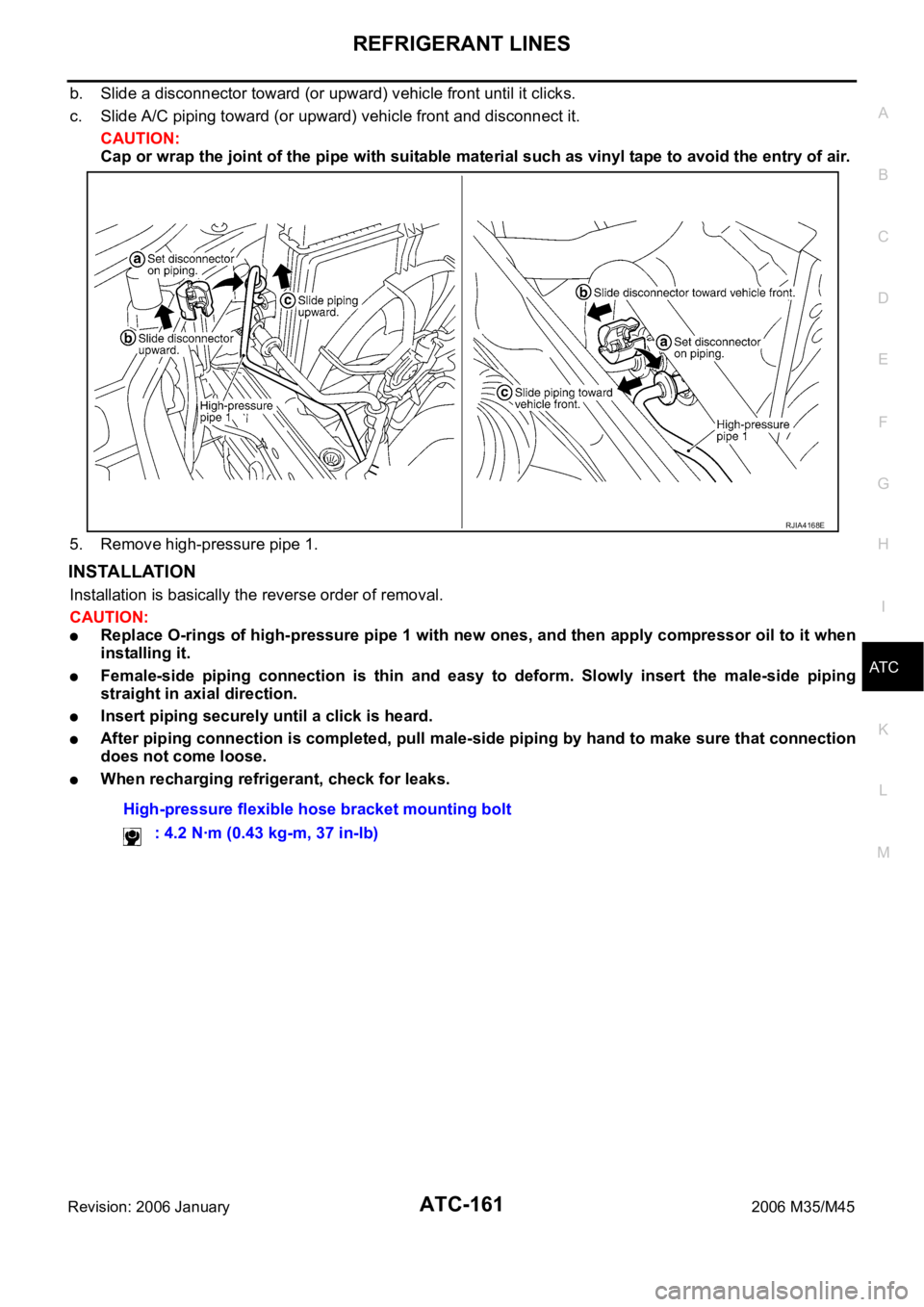
REFRIGERANT LINES
ATC-161
C
D
E
F
G
H
I
K
L
MA
B
AT C
Revision: 2006 January2006 M35/M45
b. Slide a disconnector toward (or upward) vehicle front until it clicks.
c. Slide A/C piping toward (or upward) vehicle front and disconnect it.
CAUTION:
Cap or wrap the joint of the pipe with suitable material such as vinyl tape to avoid the entry of air.
5. Remove high-pressure pipe 1.
INSTALLATION
Installation is basically the reverse order of removal.
CAUTION:
Replace O-rings of high-pressure pipe 1 with new ones, and then apply compressor oil to it when
installing it.
Female-side piping connection is thin and easy to deform. Slowly insert the male-side piping
straight in axial direction.
Insert piping securely until a click is heard.
After piping connection is completed, pull male-side piping by hand to make sure that connection
does not come loose.
When recharging refrigerant, check for leaks.
RJIA4168E
High-pressure flexible hose bracket mounting bolt
: 4.2 Nꞏm (0.43 kg-m, 37 in-lb)