Panel INFINITI M35 2006 Factory Service Manual
[x] Cancel search | Manufacturer: INFINITI, Model Year: 2006, Model line: M35, Model: INFINITI M35 2006Pages: 5621, PDF Size: 65.56 MB
Page 5187 of 5621
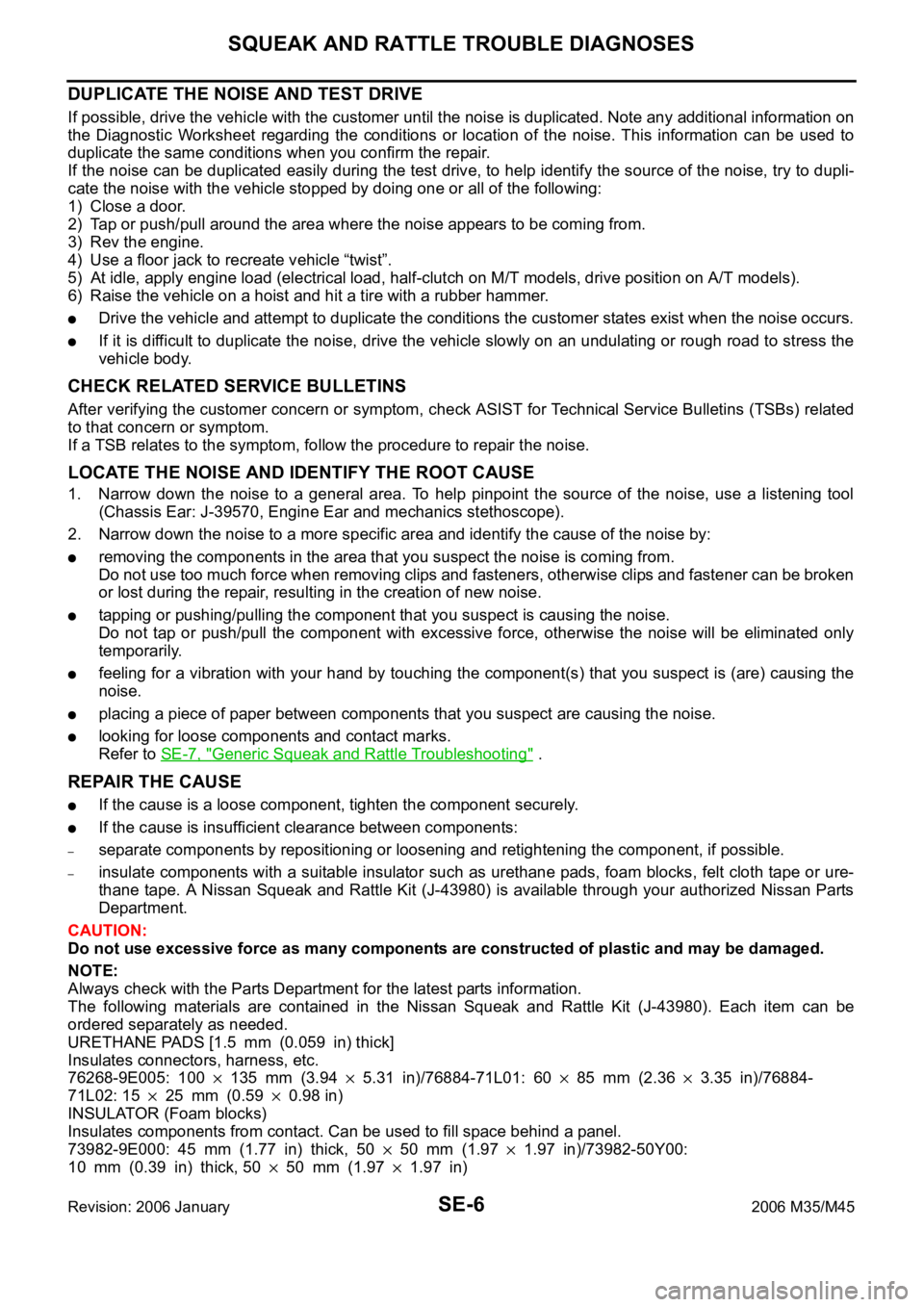
SE-6
SQUEAK AND RATTLE TROUBLE DIAGNOSES
Revision: 2006 January2006 M35/M45
DUPLICATE THE NOISE AND TEST DRIVE
If possible, drive the vehicle with the customer until the noise is duplicated. Note any additional information on
the Diagnostic Worksheet regarding the conditions or location of the noise. This information can be used to
duplicate the same conditions when you confirm the repair.
If the noise can be duplicated easily during the test drive, to help identify the source of the noise, try to dupli-
cate the noise with the vehicle stopped by doing one or all of the following:
1) Close a door.
2) Tap or push/pull around the area where the noise appears to be coming from.
3) Rev the engine.
4) Use a floor jack to recreate vehicle “twist”.
5) At idle, apply engine load (electrical load, half-clutch on M/T models, drive position on A/T models).
6) Raise the vehicle on a hoist and hit a tire with a rubber hammer.
Drive the vehicle and attempt to duplicate the conditions the customer states exist when the noise occurs.
If it is difficult to duplicate the noise, drive the vehicle slowly on an undulating or rough road to stress the
vehicle body.
CHECK RELATED SERVICE BULLETINS
After verifying the customer concern or symptom, check ASIST for Technical Service Bulletins (TSBs) related
to that concern or symptom.
If a TSB relates to the symptom, follow the procedure to repair the noise.
LOCATE THE NOISE AND IDENTIFY THE ROOT CAUSE
1. Narrow down the noise to a general area. To help pinpoint the source of the noise, use a listening tool
(Chassis Ear: J-39570, Engine Ear and mechanics stethoscope).
2. Narrow down the noise to a more specific area and identify the cause of the noise by:
removing the components in the area that you suspect the noise is coming from.
Do not use too much force when removing clips and fasteners, otherwise clips and fastener can be broken
or lost during the repair, resulting in the creation of new noise.
tapping or pushing/pulling the component that you suspect is causing the noise.
Do not tap or push/pull the component with excessive force, otherwise the noise will be eliminated only
temporarily.
feeling for a vibration with your hand by touching the component(s) that you suspect is (are) causing the
noise.
placing a piece of paper between components that you suspect are causing the noise.
looking for loose components and contact marks.
Refer to SE-7, "
Generic Squeak and Rattle Troubleshooting" .
REPAIR THE CAUSE
If the cause is a loose component, tighten the component securely.
If the cause is insufficient clearance between components:
–separate components by repositioning or loosening and retightening the component, if possible.
–insulate components with a suitable insulator such as urethane pads, foam blocks, felt cloth tape or ure-
thane tape. A Nissan Squeak and Rattle Kit (J-43980) is available through your authorized Nissan Parts
Department.
CAUTION:
Do not use excessive force as many components are constructed of plastic and may be damaged.
NOTE:
Always check with the Parts Department for the latest parts information.
The following materials are contained in the Nissan Squeak and Rattle Kit (J-43980). Each item can be
ordered separately as needed.
URETHANE PADS [1.5 mm (0.059 in) thick]
Insulates connectors, harness, etc.
76268-9E005: 100
135 mm (3.945.31 in)/76884-71L01: 6085 mm (2.363.35 in)/76884-
71L02: 15
25 mm (0.590.98 in)
INSULATOR (Foam blocks)
Insulates components from contact. Can be used to fill space behind a panel.
73982-9E000: 45 mm (1.77 in) thick, 50
50 mm (1.971.97 in)/73982-50Y00:
10 mm (0.39 in) thick, 50
50 mm (1.971.97 in)
Page 5188 of 5621
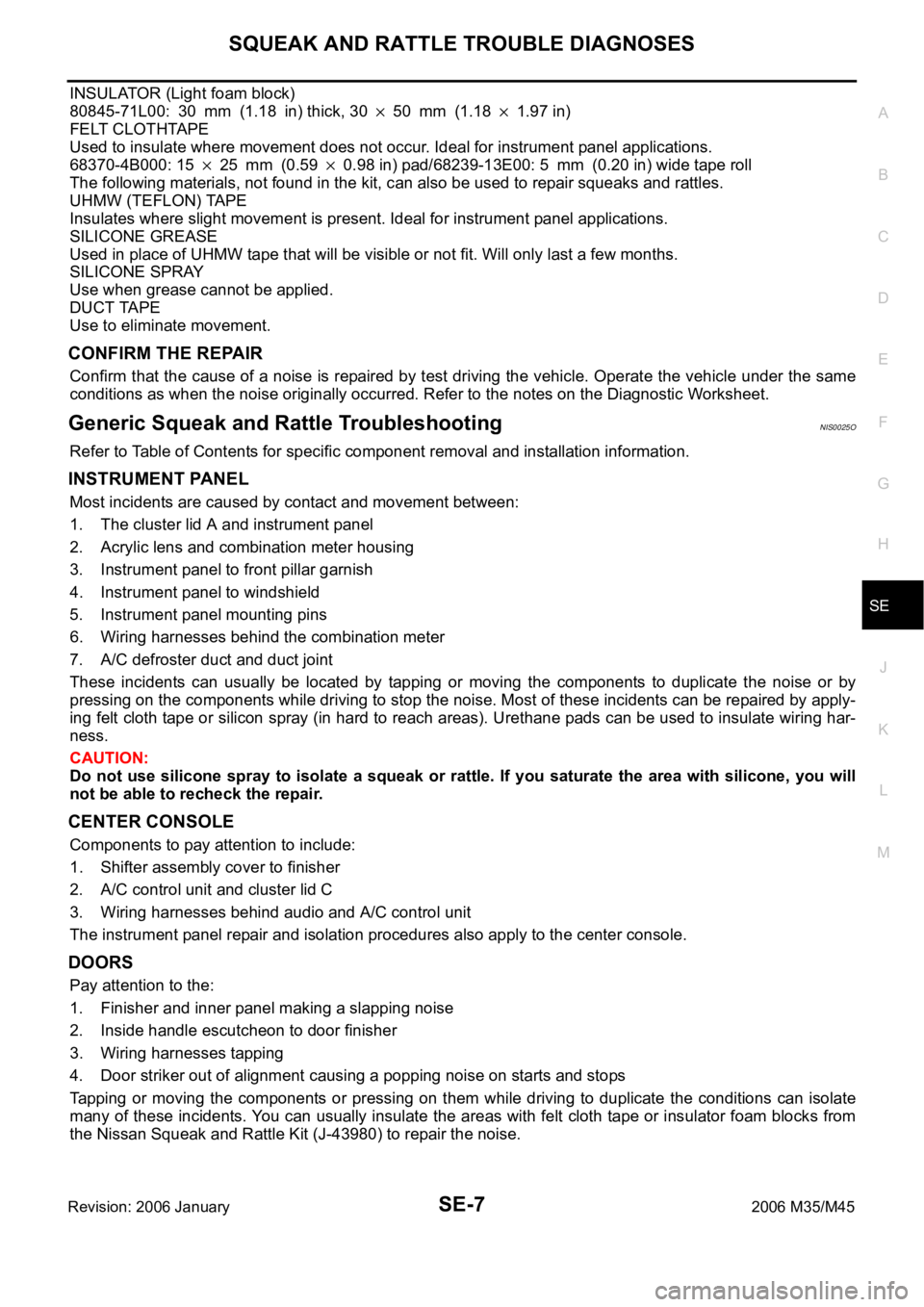
SQUEAK AND RATTLE TROUBLE DIAGNOSES
SE-7
C
D
E
F
G
H
J
K
L
MA
B
SE
Revision: 2006 January2006 M35/M45
INSULATOR (Light foam block)
80845-71L00: 30 mm (1.18 in) thick, 30
50 mm (1.181.97 in)
FELT CLOTHTAPE
Used to insulate where movement does not occur. Ideal for instrument panel applications.
68370-4B000: 15
25 mm (0.590.98 in) pad/68239-13E00: 5 mm (0.20 in) wide tape roll
The following materials, not found in the kit, can also be used to repair squeaks and rattles.
UHMW (TEFLON) TAPE
Insulates where slight movement is present. Ideal for instrument panel applications.
SILICONE GREASE
Used in place of UHMW tape that will be visible or not fit. Will only last a few months.
SILICONE SPRAY
Use when grease cannot be applied.
DUCT TAPE
Use to eliminate movement.
CONFIRM THE REPAIR
Confirm that the cause of a noise is repaired by test driving the vehicle. Operate the vehicle under the same
conditions as when the noise originally occurred. Refer to the notes on the Diagnostic Worksheet.
Generic Squeak and Rattle TroubleshootingNIS0025O
Refer to Table of Contents for specific component removal and installation information.
INSTRUMENT PANEL
Most incidents are caused by contact and movement between:
1. The cluster lid A and instrument panel
2. Acrylic lens and combination meter housing
3. Instrument panel to front pillar garnish
4. Instrument panel to windshield
5. Instrument panel mounting pins
6. Wiring harnesses behind the combination meter
7. A/C defroster duct and duct joint
These incidents can usually be located by tapping or moving the components to duplicate the noise or by
pressing on the components while driving to stop the noise. Most of these incidents can be repaired by apply-
ing felt cloth tape or silicon spray (in hard to reach areas). Urethane pads can be used to insulate wiring har-
ness.
CAUTION:
Do not use silicone spray to isolate a squeak or rattle. If you saturate the area with silicone, you will
not be able to recheck the repair.
CENTER CONSOLE
Components to pay attention to include:
1. Shifter assembly cover to finisher
2. A/C control unit and cluster lid C
3. Wiring harnesses behind audio and A/C control unit
The instrument panel repair and isolation procedures also apply to the center console.
DOORS
Pay attention to the:
1. Finisher and inner panel making a slapping noise
2. Inside handle escutcheon to door finisher
3. Wiring harnesses tapping
4. Door striker out of alignment causing a popping noise on starts and stops
Tapping or moving the components or pressing on them while driving to duplicate the conditions can isolate
many of these incidents. You can usually insulate the areas with felt cloth tape or insulator foam blocks from
the Nissan Squeak and Rattle Kit (J-43980) to repair the noise.
Page 5192 of 5621
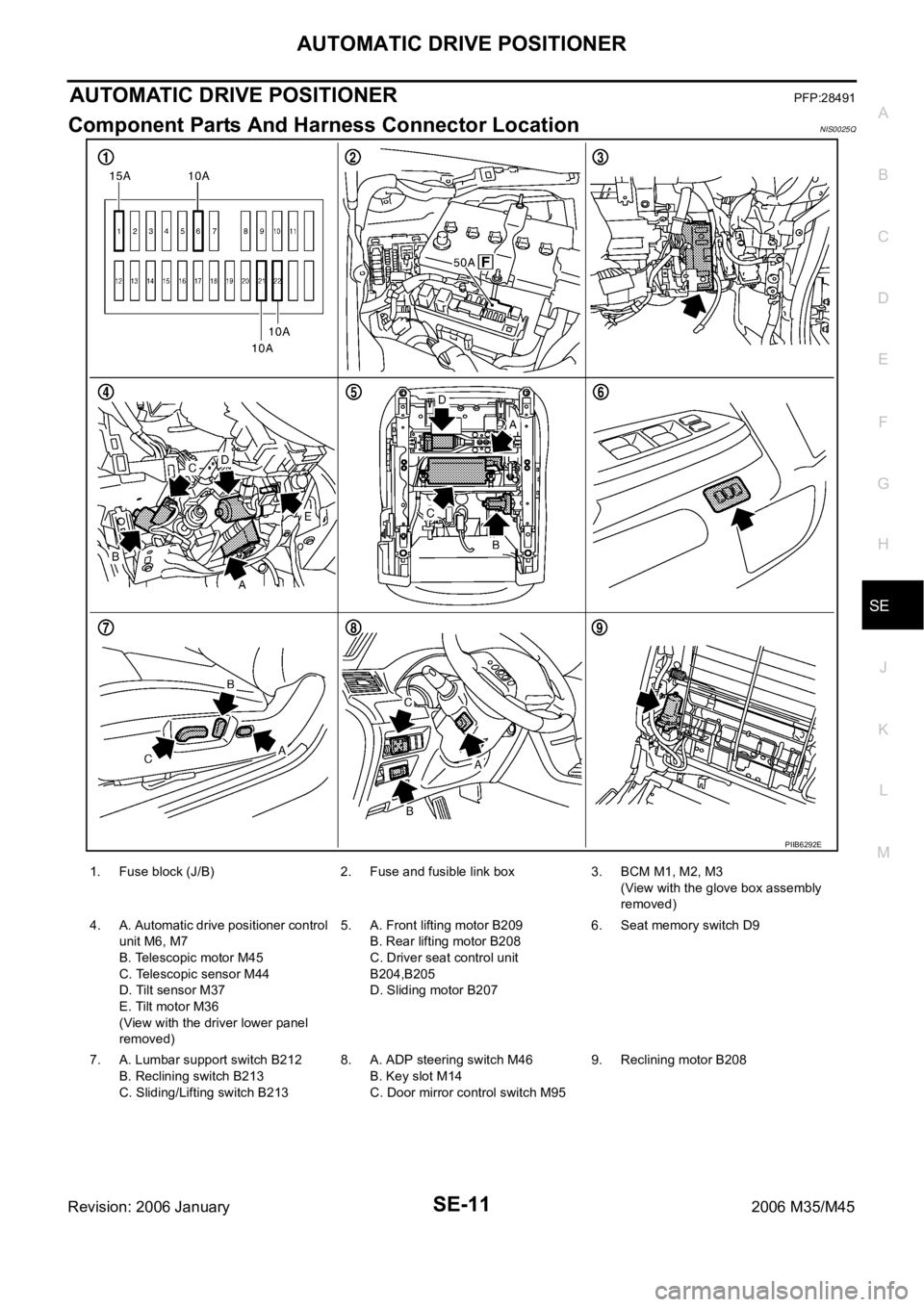
AUTOMATIC DRIVE POSITIONER
SE-11
C
D
E
F
G
H
J
K
L
MA
B
SE
Revision: 2006 January2006 M35/M45
AUTOMATIC DRIVE POSITIONERPFP:28491
Component Parts And Harness Connector LocationNIS0025Q
PIIB6292E
1. Fuse block (J/B) 2. Fuse and fusible link box 3. BCM M1, M2, M3
(View with the glove box assembly
removed)
4. A. Automatic drive positioner control
unit M6, M7
B. Telescopic motor M45
C. Telescopic sensor M44
D. Tilt sensor M37
E. Tilt motor M36
(View with the driver lower panel
removed)5. A. Front lifting motor B209
B. Rear lifting motor B208
C. Driver seat control unit
B204,B205
D. Sliding motor B2076. Seat memory switch D9
7. A. Lumbar support switch B212
B. Reclining switch B213
C. Sliding/Lifting switch B2138. A. ADP steering switch M46
B. Key slot M14
C. Door mirror control switch M959. Reclining motor B208
Page 5195 of 5621
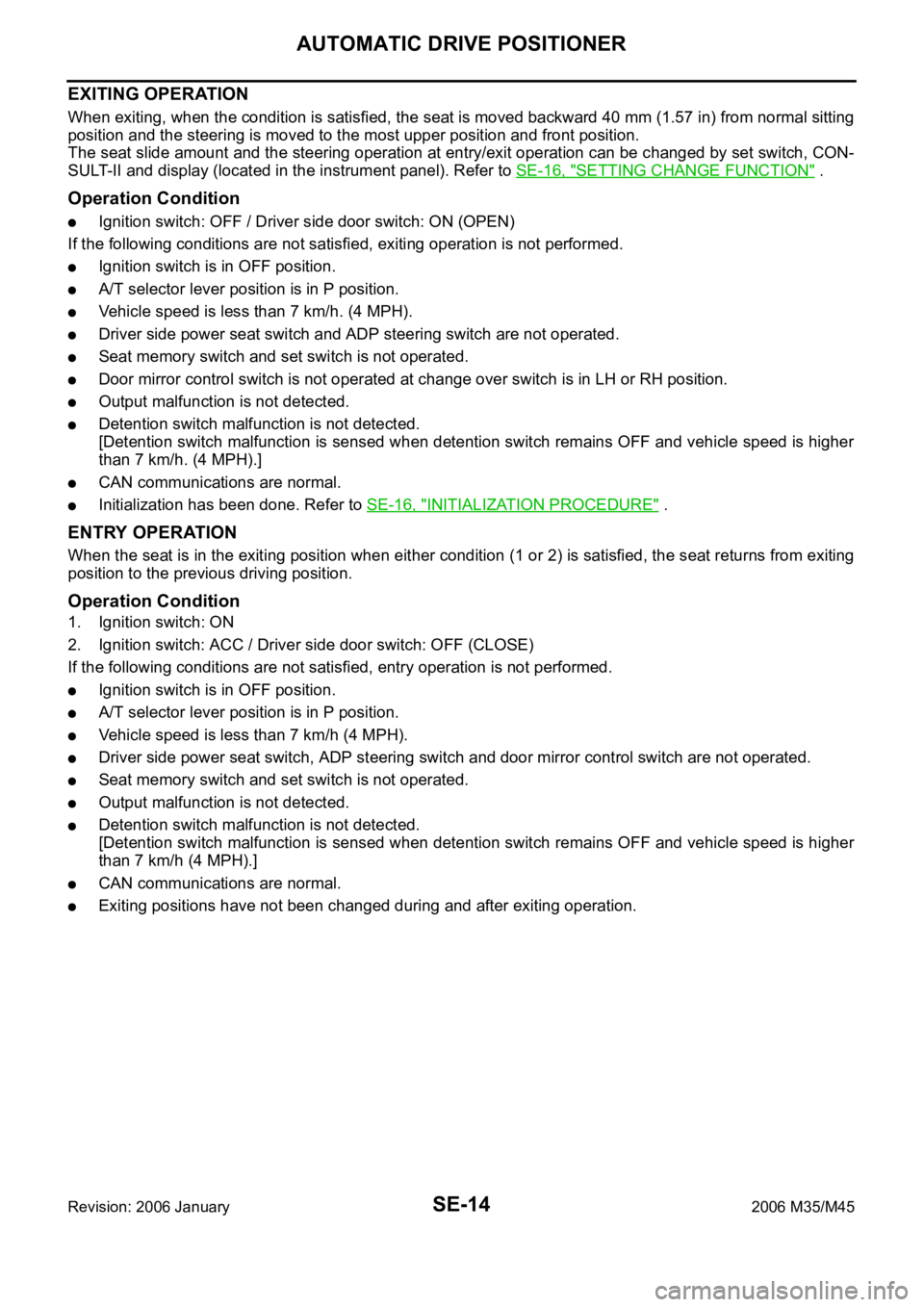
SE-14
AUTOMATIC DRIVE POSITIONER
Revision: 2006 January2006 M35/M45
EXITING OPERATION
When exiting, when the condition is satisfied, the seat is moved backward 40 mm (1.57 in) from normal sitting
position and the steering is moved to the most upper position and front position.
The seat slide amount and the steering operation at entry/exit operation can be changed by set switch, CON-
SULT-II and display (located in the instrument panel). Refer to SE-16, "
SETTING CHANGE FUNCTION" .
Operation Condition
Ignition switch: OFF / Driver side door switch: ON (OPEN)
If the following conditions are not satisfied, exiting operation is not performed.
Ignition switch is in OFF position.
A/T selector lever position is in P position.
Vehicle speed is less than 7 km/h. (4 MPH).
Driver side power seat switch and ADP steering switch are not operated.
Seat memory switch and set switch is not operated.
Door mirror control switch is not operated at change over switch is in LH or RH position.
Output malfunction is not detected.
Detention switch malfunction is not detected.
[Detention switch malfunction is sensed when detention switch remains OFF and vehicle speed is higher
than 7 km/h. (4 MPH).]
CAN communications are normal.
Initialization has been done. Refer to SE-16, "INITIALIZATION PROCEDURE" .
ENTRY OPERATION
When the seat is in the exiting position when either condition (1 or 2) is satisfied, the seat returns from exiting
position to the previous driving position.
Operation Condition
1. Ignition switch: ON
2. Ignition switch: ACC / Driver side door switch: OFF (CLOSE)
If the following conditions are not satisfied, entry operation is not performed.
Ignition switch is in OFF position.
A/T selector lever position is in P position.
Vehicle speed is less than 7 km/h (4 MPH).
Driver side power seat switch, ADP steering switch and door mirror control switch are not operated.
Seat memory switch and set switch is not operated.
Output malfunction is not detected.
Detention switch malfunction is not detected.
[Detention switch malfunction is sensed when detention switch remains OFF and vehicle speed is higher
than 7 km/h (4 MPH).]
CAN communications are normal.
Exiting positions have not been changed during and after exiting operation.
Page 5197 of 5621
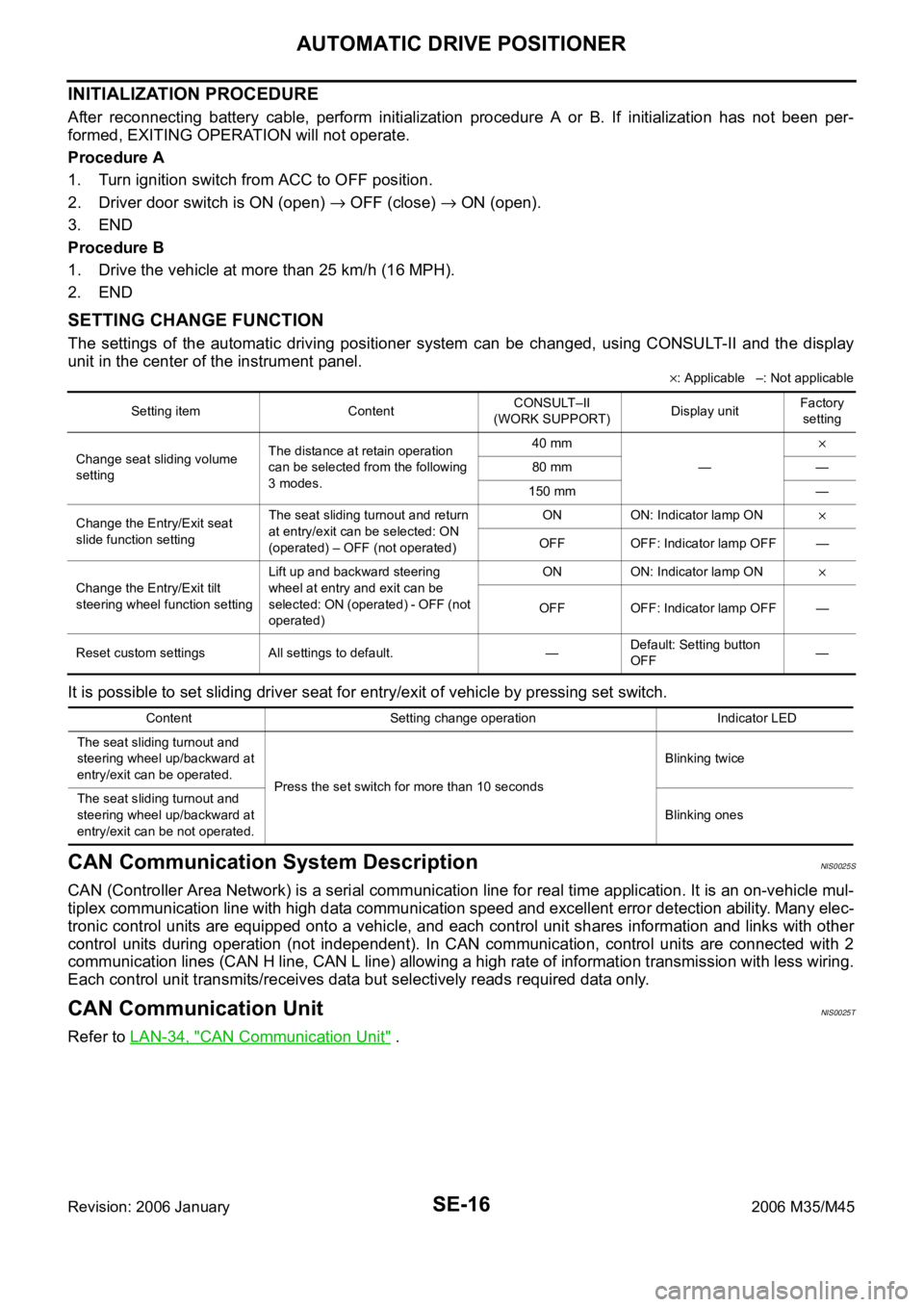
SE-16
AUTOMATIC DRIVE POSITIONER
Revision: 2006 January2006 M35/M45
INITIALIZATION PROCEDURE
After reconnecting battery cable, perform initialization procedure A or B. If initialization has not been per-
formed, EXITING OPERATION will not operate.
Procedure A
1. Turn ignition switch from ACC to OFF position.
2. Driver door switch is ON (open)
OFF (close) ON (open).
3. END
Procedure B
1. Drive the vehicle at more than 25 km/h (16 MPH).
2. END
SETTING CHANGE FUNCTION
The settings of the automatic driving positioner system can be changed, using CONSULT-II and the display
unit in the center of the instrument panel.
: Applicable –: Not applicable
It is possible to set sliding driver seat for entry/exit of vehicle by pressing set switch.
CAN Communication System DescriptionNIS0025S
CAN (Controller Area Network) is a serial communication line for real time application. It is an on-vehicle mul-
tiplex communication line with high data communication speed and excellent error detection ability. Many elec-
tronic control units are equipped onto a vehicle, and each control unit shares information and links with other
control units during operation (not independent). In CAN communication, control units are connected with 2
communication lines (CAN H line, CAN L line) allowing a high rate of information transmission with less wiring.
Each control unit transmits/receives data but selectively reads required data only.
CAN Communication UnitNIS0025T
Refer to LAN-34, "CAN Communication Unit" .
Setting item ContentCONSULT–II
(WORK SUPPORT)Display unitFactory
setting
Change seat sliding volume
settingThe distance at retain operation
can be selected from the following
3 modes.40 mm
—
80 mm —
150 mm —
Change the Entry/Exit seat
slide function settingThe seat sliding turnout and return
at entry/exit can be selected: ON
(operated) – OFF (not operated)ON ON: Indicator lamp ON
OFF OFF: Indicator lamp OFF —
Change the Entry/Exit tilt
steering wheel function settingLift up and backward steering
wheel at entry and exit can be
selected: ON (operated) - OFF (not
operated)ON ON: Indicator lamp ON
OFF OFF: Indicator lamp OFF —
Reset custom settings All settings to default. —Default: Setting button
OFF—
Content Setting change operation Indicator LED
The seat sliding turnout and
steering wheel up/backward at
entry/exit can be operated.
Press the set switch for more than 10 secondsBlinking twice
The seat sliding turnout and
steering wheel up/backward at
entry/exit can be not operated.Blinking ones
Page 5364 of 5621
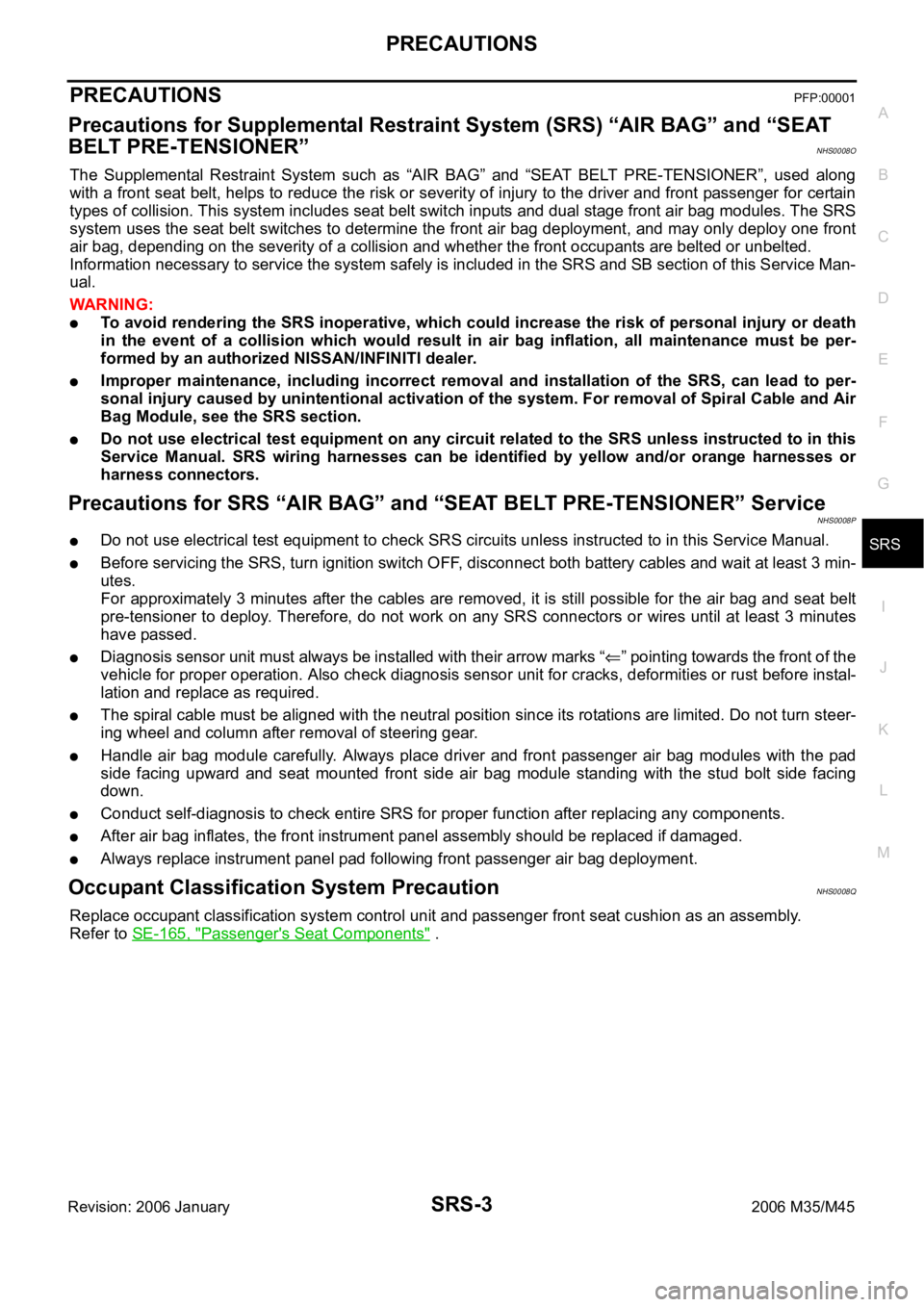
PRECAUTIONS
SRS-3
C
D
E
F
G
I
J
K
L
MA
B
SRS
Revision: 2006 January2006 M35/M45
PRECAUTIONSPFP:00001
Precautions for Supplemental Restraint System (SRS) “AIR BAG” and “SEAT
BELT PRE-TENSIONER”
NHS0008O
The Supplemental Restraint System such as “AIR BAG” and “SEAT BELT PRE-TENSIONER”, used along
with a front seat belt, helps to reduce the risk or severity of injury to the driver and front passenger for certain
types of collision. This system includes seat belt switch inputs and dual stage front air bag modules. The SRS
system uses the seat belt switches to determine the front air bag deployment, and may only deploy one front
air bag, depending on the severity of a collision and whether the front occupants are belted or unbelted.
Information necessary to service the system safely is included in the SRS and SB section of this Service Man-
ual.
WAR NING :
To avoid rendering the SRS inoperative, which could increase the risk of personal injury or death
in the event of a collision which would result in air bag inflation, all maintenance must be per-
formed by an authorized NISSAN/INFINITI dealer.
Improper maintenance, including incorrect removal and installation of the SRS, can lead to per-
sonal injury caused by unintentional activation of the system. For removal of Spiral Cable and Air
Bag Module, see the SRS section.
Do not use electrical test equipment on any circuit related to the SRS unless instructed to in this
Service Manual. SRS wiring harnesses can be identified by yellow and/or orange harnesses or
harness connectors.
Precautions for SRS “AIR BAG” and “SEAT BELT PRE-TENSIONER” ServiceNHS0008P
Do not use electrical test equipment to check SRS circuits unless instructed to in this Service Manual.
Before servicing the SRS, turn ignition switch OFF, disconnect both battery cables and wait at least 3 min-
utes.
For approximately 3 minutes after the cables are removed, it is still possible for the air bag and seat belt
pre-tensioner to deploy. Therefore, do not work on any SRS connectors or wires until at least 3 minutes
have passed.
Diagnosis sensor unit must always be installed with their arrow marks “” pointing towards the front of the
vehicle for proper operation. Also check diagnosis sensor unit for cracks, deformities or rust before instal-
lation and replace as required.
The spiral cable must be aligned with the neutral position since its rotations are limited. Do not turn steer-
ing wheel and column after removal of steering gear.
Handle air bag module carefully. Always place driver and front passenger air bag modules with the pad
side facing upward and seat mounted front side air bag module standing with the stud bolt side facing
down.
Conduct self-diagnosis to check entire SRS for proper function after replacing any components.
After air bag inflates, the front instrument panel assembly should be replaced if damaged.
Always replace instrument panel pad following front passenger air bag deployment.
Occupant Classification System PrecautionNHS0008Q
Replace occupant classification system control unit and passenger front seat cushion as an assembly.
Refer to SE-165, "
Passenger's Seat Components" .
Page 5403 of 5621
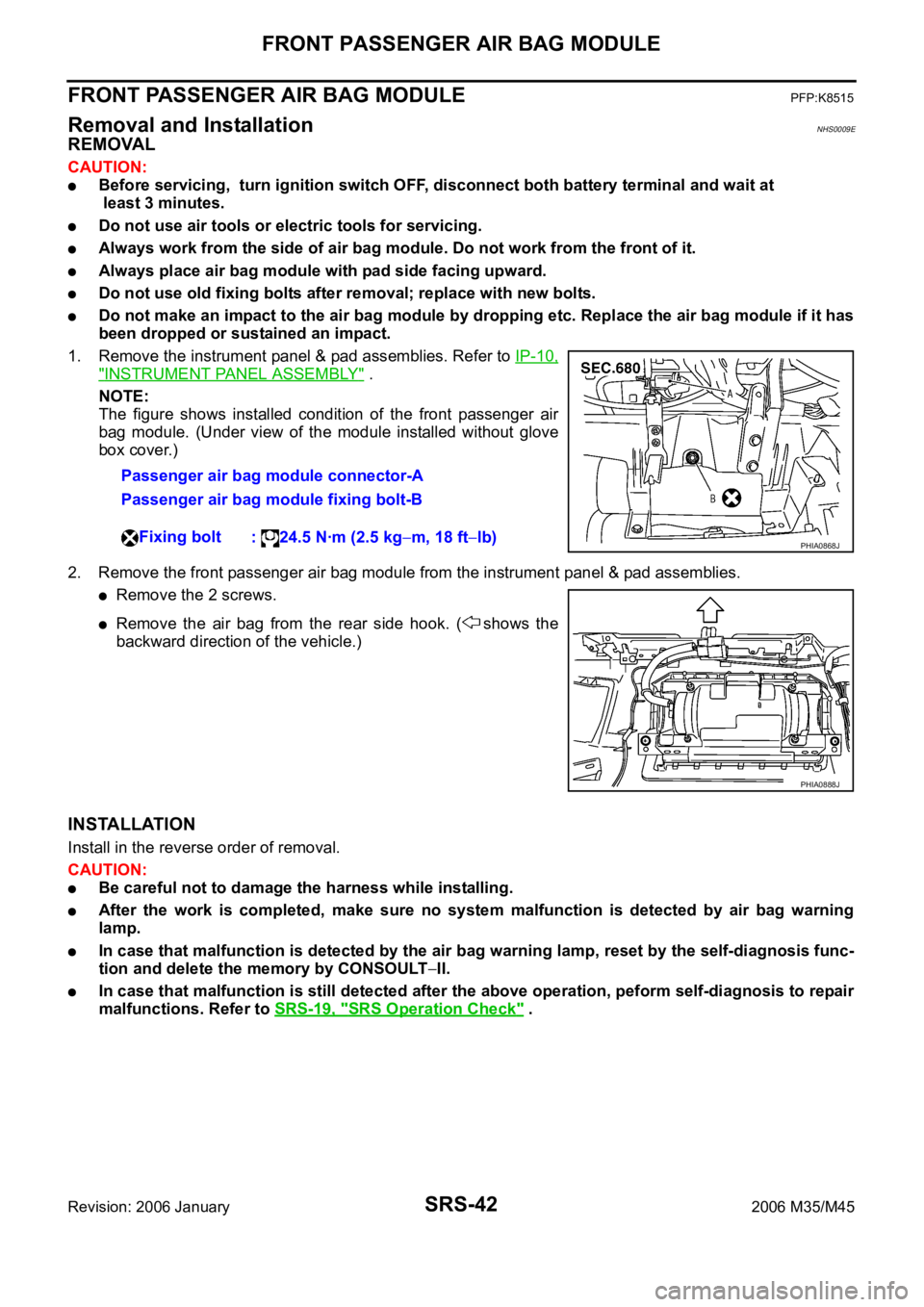
SRS-42
FRONT PASSENGER AIR BAG MODULE
Revision: 2006 January2006 M35/M45
FRONT PASSENGER AIR BAG MODULEPFP:K8515
Removal and InstallationNHS0009E
REMOVAL
CAUTION:
Before servicing, turn ignition switch OFF, disconnect both battery terminal and wait at
least 3 minutes.
Do not use air tools or electric tools for servicing.
Always work from the side of air bag module. Do not work from the front of it.
Always place air bag module with pad side facing upward.
Do not use old fixing bolts after removal; replace with new bolts.
Do not make an impact to the air bag module by dropping etc. Replace the air bag module if it has
been dropped or sustained an impact.
1. Remove the instrument panel & pad assemblies. Refer to IP-10,
"INSTRUMENT PANEL ASSEMBLY" .
NOTE:
The figure shows installed condition of the front passenger air
bag module. (Under view of the module installed without glove
box cover.)
2. Remove the front passenger air bag module from the instrument panel & pad assemblies.
Remove the 2 screws.
Remove the air bag from the rear side hook. ( shows the
backward direction of the vehicle.)
INSTALLATION
Install in the reverse order of removal.
CAUTION:
Be careful not to damage the harness while installing.
After the work is completed, make sure no system malfunction is detected by air bag warning
lamp.
In case that malfunction is detected by the air bag warning lamp, reset by the self-diagnosis func-
tion and delete the memory by CONSOULT
II.
In case that malfunction is still detected after the above operation, peform self-diagnosis to repair
malfunctions. Refer to SRS-19, "
SRS Operation Check" . Passenger air bag module connector-A
Passenger air bag module fixing bolt-B
Fixing bolt
: 24.5 Nꞏm (2.5 kg
m, 18 ftlb)PHIA0868J
PHIA0888J
Page 5409 of 5621
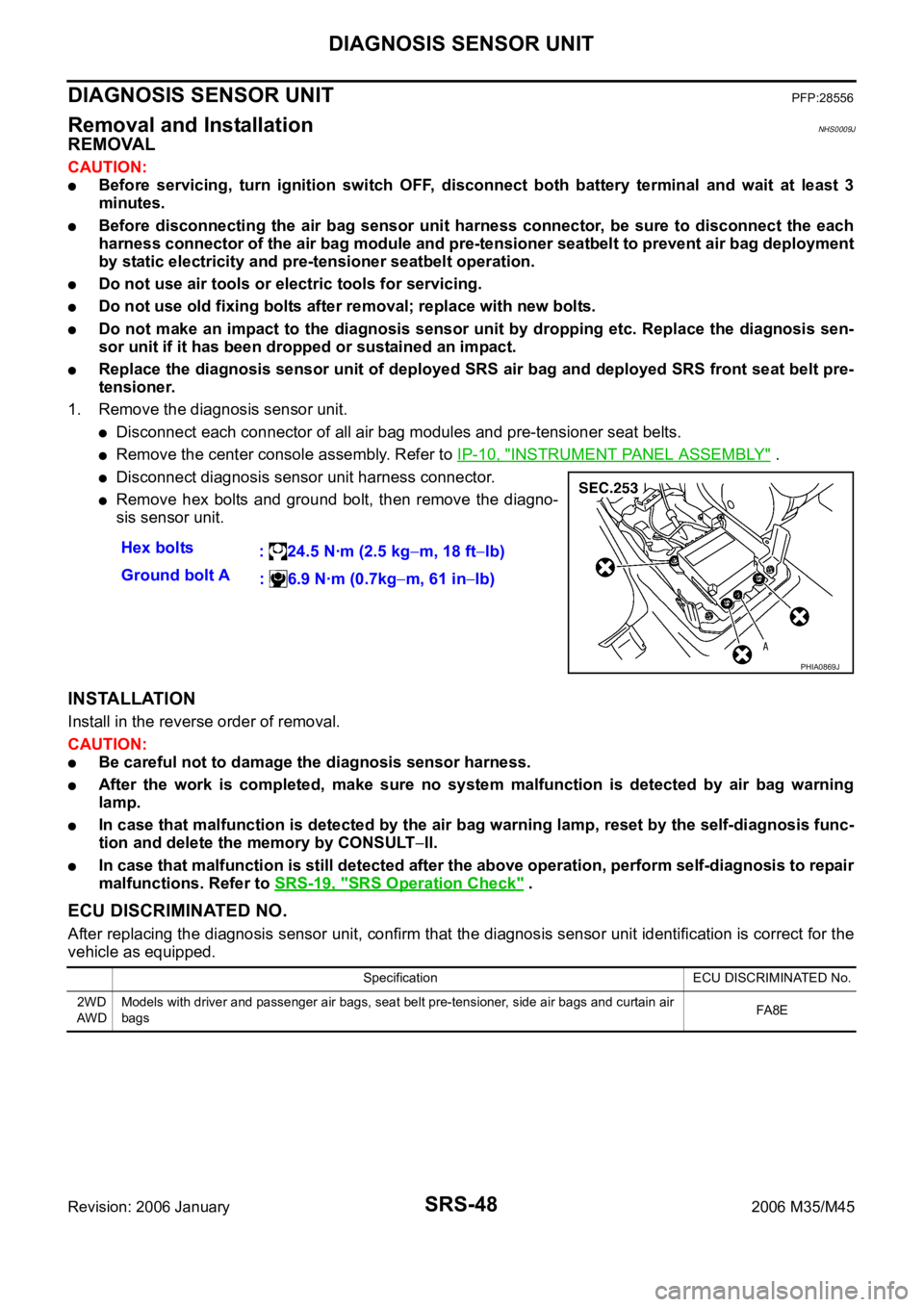
SRS-48
DIAGNOSIS SENSOR UNIT
Revision: 2006 January2006 M35/M45
DIAGNOSIS SENSOR UNITPFP:28556
Removal and InstallationNHS0009J
REMOVAL
CAUTION:
Before servicing, turn ignition switch OFF, disconnect both battery terminal and wait at least 3
minutes.
Before disconnecting the air bag sensor unit harness connector, be sure to disconnect the each
harness connector of the air bag module and pre-tensioner seatbelt to prevent air bag deployment
by static electricity and pre-tensioner seatbelt operation.
Do not use air tools or electric tools for servicing.
Do not use old fixing bolts after removal; replace with new bolts.
Do not make an impact to the diagnosis sensor unit by dropping etc. Replace the diagnosis sen-
sor unit if it has been dropped or sustained an impact.
Replace the diagnosis sensor unit of deployed SRS air bag and deployed SRS front seat belt pre-
tensioner.
1. Remove the diagnosis sensor unit.
Disconnect each connector of all air bag modules and pre-tensioner seat belts.
Remove the center console assembly. Refer to IP-10, "INSTRUMENT PANEL ASSEMBLY" .
Disconnect diagnosis sensor unit harness connector.
Remove hex bolts and ground bolt, then remove the diagno-
sis sensor unit.
INSTALLATION
Install in the reverse order of removal.
CAUTION:
Be careful not to damage the diagnosis sensor harness.
After the work is completed, make sure no system malfunction is detected by air bag warning
lamp.
In case that malfunction is detected by the air bag warning lamp, reset by the self-diagnosis func-
tion and delete the memory by CONSULT
ll.
In case that malfunction is still detected after the above operation, perform self-diagnosis to repair
malfunctions. Refer to SRS-19, "
SRS Operation Check" .
ECU DISCRIMINATED NO.
After replacing the diagnosis sensor unit, confirm that the diagnosis sensor unit identification is correct for the
vehicle as equipped.Hex bolts
: 24.5 Nꞏm (2.5 kg
m, 18 ftlb)
Ground bolt A
: 6.9 Nꞏm (0.7kg
m, 61 inlb)
PHIA0869J
Specification ECU DISCRIMINATED No.
2WD
AW DModels with driver and passenger air bags, seat belt pre-tensioner, side air bags and curtain air
bagsFA 8 E
Page 5412 of 5621
![INFINITI M35 2006 Factory Service Manual COLLISION DIAGNOSIS
SRS-51
C
D
E
F
G
I
J
K
L
MA
B
SRS
Revision: 2006 January2006 M35/M45
Steering wheel [same text as in current manual]
Spiral cab INFINITI M35 2006 Factory Service Manual COLLISION DIAGNOSIS
SRS-51
C
D
E
F
G
I
J
K
L
MA
B
SRS
Revision: 2006 January2006 M35/M45
Steering wheel [same text as in current manual]
Spiral cab](/img/42/57023/w960_57023-5411.png)
COLLISION DIAGNOSIS
SRS-51
C
D
E
F
G
I
J
K
L
MA
B
SRS
Revision: 2006 January2006 M35/M45
Steering wheel [same text as in current manual]
Spiral cable If the Driver airbag has deployed:
REPLACE the spiral cable.If the Driver airbag has not deployed:
[same text as in current manual]
Harness and con-
nectors1. Check connectors for poor connection, damage, and terminals for deformities.
2. Check harness for binding, chafing, cuts, or deformities.
3. If no damage is found, reinstall the harness and connectors.
4. If damaged—REPLACE damaged section of harness. Do not repair, splice or modify any SRS harness.
Instrument panel 1. Visually check instrument panel for damage.
2. If no damage is found, reinstall the instrument panel.
3. If damaged—REPLACE the instrument panel with bolts. Part SRS is activatedSRS is NOT activated
Page 5565 of 5621
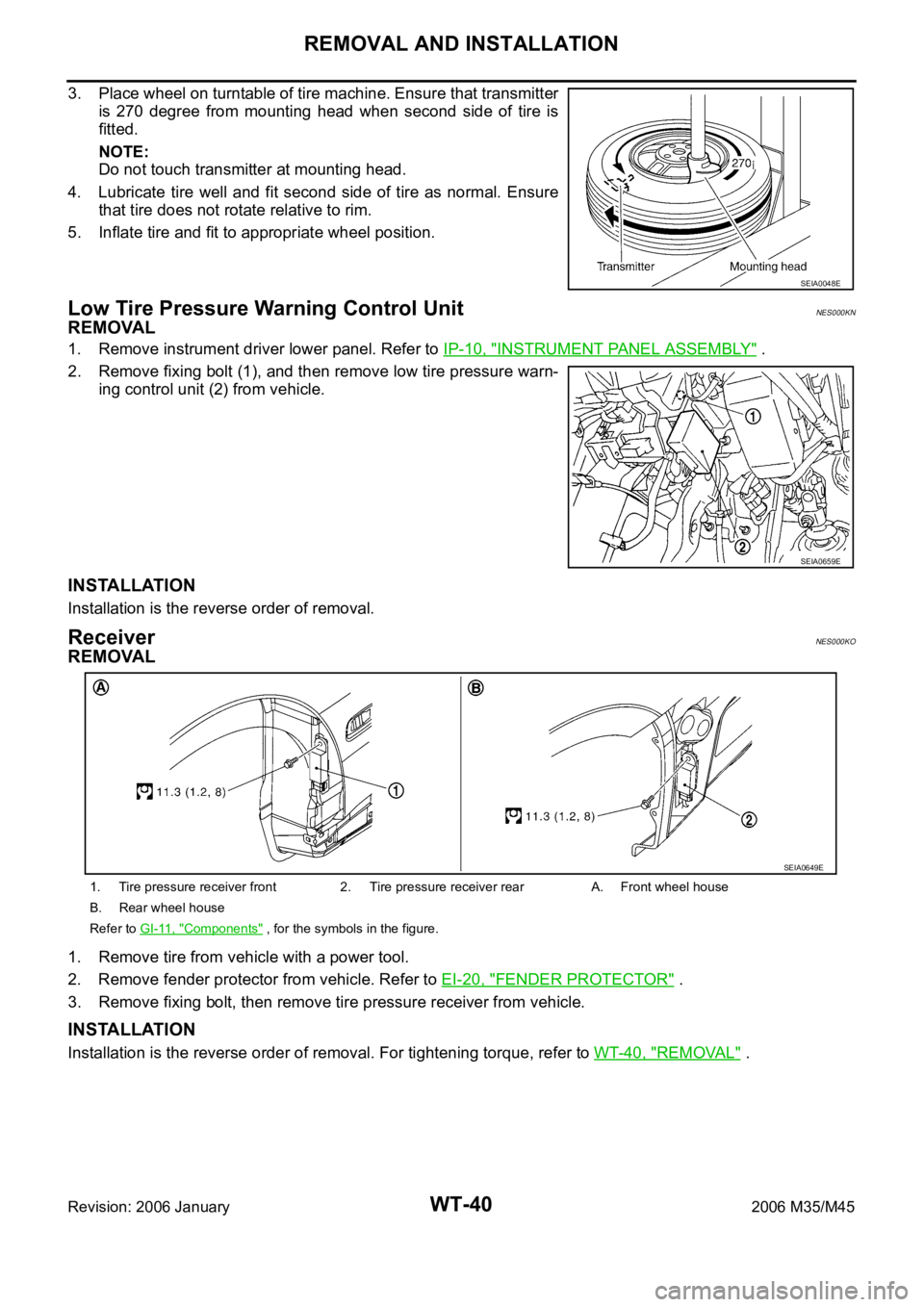
WT-40
REMOVAL AND INSTALLATION
Revision: 2006 January2006 M35/M45
3. Place wheel on turntable of tire machine. Ensure that transmitter
is 270 degree from mounting head when second side of tire is
fitted.
NOTE:
Do not touch transmitter at mounting head.
4. Lubricate tire well and fit second side of tire as normal. Ensure
that tire does not rotate relative to rim.
5. Inflate tire and fit to appropriate wheel position.
Low Tire Pressure Warning Control UnitNES000KN
REMOVAL
1. Remove instrument driver lower panel. Refer to IP-10, "INSTRUMENT PANEL ASSEMBLY" .
2. Remove fixing bolt (1), and then remove low tire pressure warn-
ing control unit (2) from vehicle.
INSTALLATION
Installation is the reverse order of removal.
ReceiverNES000KO
REMOVAL
1. Remove tire from vehicle with a power tool.
2. Remove fender protector from vehicle. Refer to EI-20, "
FENDER PROTECTOR" .
3. Remove fixing bolt, then remove tire pressure receiver from vehicle.
INSTALLATION
Installation is the reverse order of removal. For tightening torque, refer to WT-40, "REMOVAL" .
SEIA0048E
SEIA0659E
1. Tire pressure receiver front 2. Tire pressure receiver rear A. Front wheel house
B. Rear wheel house
Refer to GI-11, "
Components" , for the symbols in the figure.
SEIA0649E