transmission INFINITI M35 2006 Factory Service Manual
[x] Cancel search | Manufacturer: INFINITI, Model Year: 2006, Model line: M35, Model: INFINITI M35 2006Pages: 5621, PDF Size: 65.56 MB
Page 5446 of 5621
![INFINITI M35 2006 Factory Service Manual TROUBLE DIAGNOSIS
STC-31
[RAS]
C
D
E
F
H
I
J
K
L
MA
B
STC
Revision: 2006 January2006 M35/M45
Diagnosis Procedure with Self-Diagnosis Function (Without CONSULT- I I )NGS000EL
DESCRIPTION
If a malfunc INFINITI M35 2006 Factory Service Manual TROUBLE DIAGNOSIS
STC-31
[RAS]
C
D
E
F
H
I
J
K
L
MA
B
STC
Revision: 2006 January2006 M35/M45
Diagnosis Procedure with Self-Diagnosis Function (Without CONSULT- I I )NGS000EL
DESCRIPTION
If a malfunc](/img/42/57023/w960_57023-5445.png)
TROUBLE DIAGNOSIS
STC-31
[RAS]
C
D
E
F
H
I
J
K
L
MA
B
STC
Revision: 2006 January2006 M35/M45
Diagnosis Procedure with Self-Diagnosis Function (Without CONSULT- I I )NGS000EL
DESCRIPTION
If a malfunction is detected in the system, the RAS warning lamp turns on and indicates the malfunction. At
that time, fail-safe activates, and then stops the function.
SELF-DIAGNOSIS PROCEDURE
1. Start engine.
2. Turn steering wheel left and right at 20
or more and 5 times or more within 10 seconds. And then depress
the service brake 5 times or more.
3. RAS warning lamp blinks (displays normal/malfunction).
SELF-DIAGNOSIS DISPLAY
RAS warning lamp blinks and displays the self-diagnostic results.
Only DTCs are displayed as the pattern shown in the figure, and
then repeat the display.
If all items are normal, RAS warning lamp blinks at 4 Hz cycle.
SELF-DIAGNOSIS DISPLAY ITEMS
HOW TO ERASE SELF-DIAGNOSIS
If there is the history data for when the fail-safe has activated in the past, erase the memory with CONSULT-II.
Refer to STC-29, "
How to Erase Self-Diagnostic Results" .
CAN CommunicationNGS000EM
SYSTEM DESCRIPTION
CAN (Controller Area Network) is a serial communication line for real time application. It is an on-vehicle mul-
tiplex communication line with high data communication speed and excellent error detection ability. Many elec-
tronic control units are equipped onto a vehicle, and each control unit shares information and links with other
control units during operation (not independent). In CAN communication, control units are connected with 2
communication lines (CAN H line, CAN L line) allowing a high rate of information transmission with less wiring.
Each control unit transmits/receives data but selectively reads required data only. Refer to LAN-34, "
CAN
Communication Unit" .
SGIA1243E
DTC (warning lamp blinks) Diagnosis item Inspection item
11 RAS control unitSTC-35, "
Inspection 1: RAS Control Unit Malfunction"
12 Motor power supplySTC-35, "Inspection 2: Motor Power Supply System"
13 Motor outputSTC-37, "Inspection 3: RAS Motor Output Malfunction"
21 Vehicle speed signalSTC-38, "Inspection 4: Vehicle Speed Signal"
22 Steering angle signalSTC-38, "Inspection 5: Steering Angle Signal Malfunction"
24 Rear wheel steering angle (main)STC-40, "Inspection 6: Rear Main Signal and Rear Sub Signal
Malfunction"
25 Rear wheel steering angle (sub)STC-40, "Inspection 6: Rear Main Signal and Rear Sub Signal
Malfunction"
26 VDCSTC-42, "Inspection 7: VDC Malfunction"
33 Engine speed signalSTC-43, "Inspection 8: Engine Speed Signal Malfunction"
Page 5476 of 5621
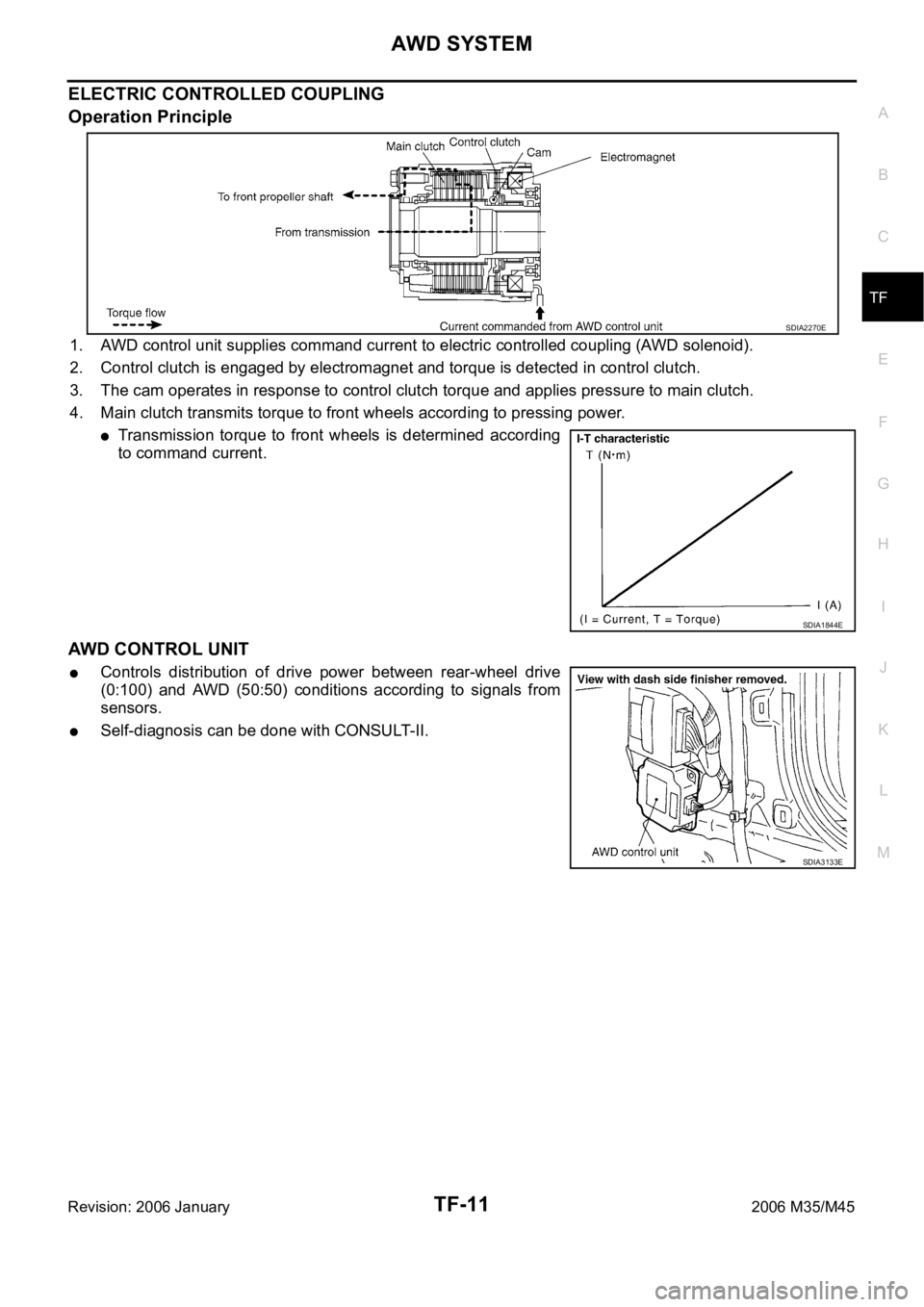
AWD SYSTEM
TF-11
C
E
F
G
H
I
J
K
L
MA
B
TF
Revision: 2006 January2006 M35/M45
ELECTRIC CONTROLLED COUPLING
Operation Principle
1. AWD control unit supplies command current to electric controlled coupling (AWD solenoid).
2. Control clutch is engaged by electromagnet and torque is detected in control clutch.
3. The cam operates in response to control clutch torque and applies pressure to main clutch.
4. Main clutch transmits torque to front wheels according to pressing power.
Transmission torque to front wheels is determined according
to command current.
AWD CONTROL UNIT
Controls distribution of drive power between rear-wheel drive
(0:100) and AWD (50:50) conditions according to signals from
sensors.
Self-diagnosis can be done with CONSULT-II.
SDIA2270E
SDIA1844E
SDIA3133E
Page 5478 of 5621
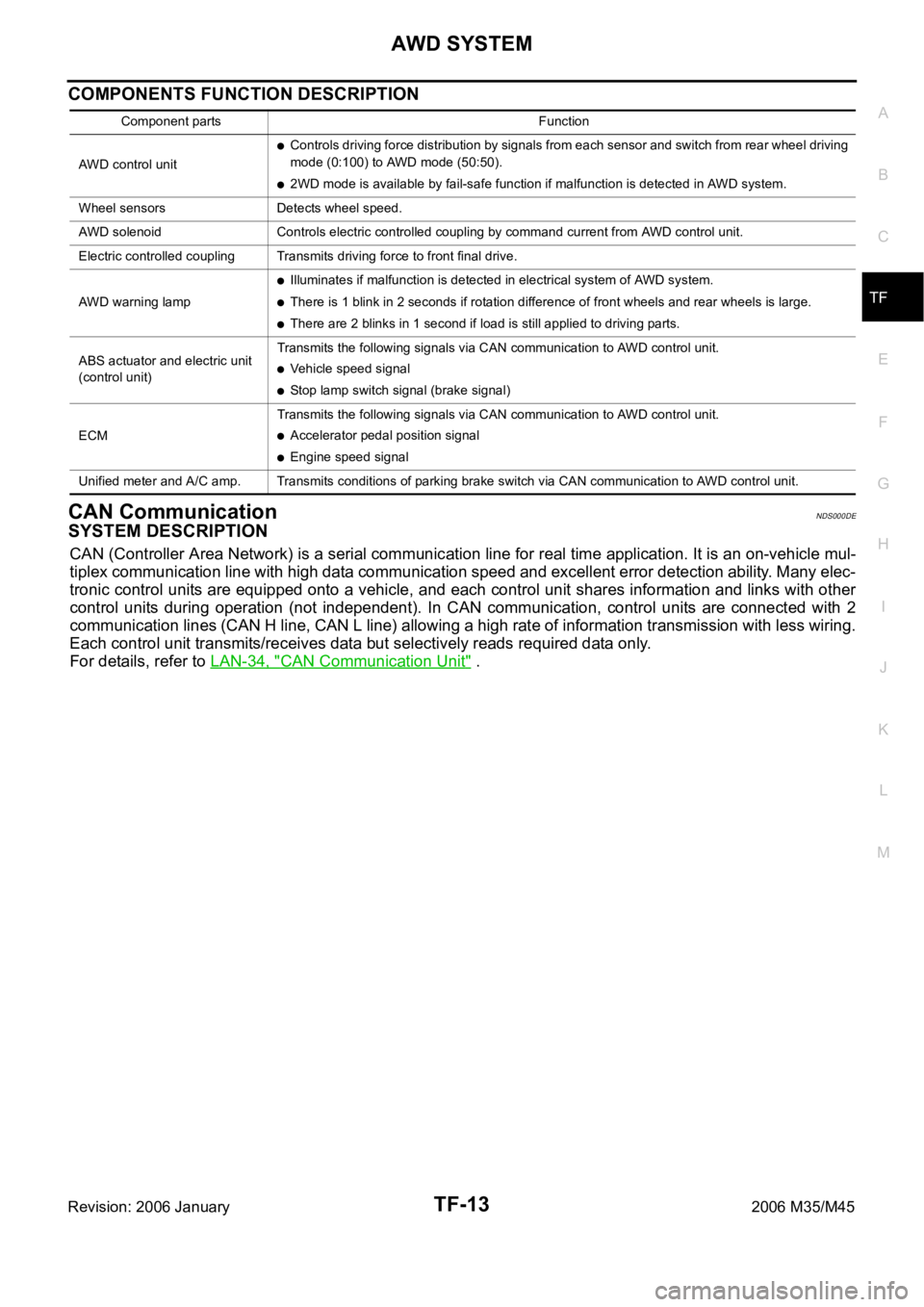
AWD SYSTEM
TF-13
C
E
F
G
H
I
J
K
L
MA
B
TF
Revision: 2006 January2006 M35/M45
COMPONENTS FUNCTION DESCRIPTION
CAN CommunicationNDS000DE
SYSTEM DESCRIPTION
CAN (Controller Area Network) is a serial communication line for real time application. It is an on-vehicle mul-
tiplex communication line with high data communication speed and excellent error detection ability. Many elec-
tronic control units are equipped onto a vehicle, and each control unit shares information and links with other
control units during operation (not independent). In CAN communication, control units are connected with 2
communication lines (CAN H line, CAN L line) allowing a high rate of information transmission with less wiring.
Each control unit transmits/receives data but selectively reads required data only.
For details, refer to LAN-34, "
CAN Communication Unit" .
Component parts Function
AWD control unit
Controls driving force distribution by signals from each sensor and switch from rear wheel driving
mode (0:100) to AWD mode (50:50).
2WD mode is available by fail-safe function if malfunction is detected in AWD system.
Wheel sensors Detects wheel speed.
AWD solenoid Controls electric controlled coupling by command current from AWD control unit.
Electric controlled coupling Transmits driving force to front final drive.
AWD warning lamp
Illuminates if malfunction is detected in electrical system of AWD system.
There is 1 blink in 2 seconds if rotation difference of front wheels and rear wheels is large.
There are 2 blinks in 1 second if load is still applied to driving parts.
ABS actuator and electric unit
(control unit)Transmits the following signals via CAN communication to AWD control unit.
Vehicle speed signal
Stop lamp switch signal (brake signal)
ECMTransmits the following signals via CAN communication to AWD control unit.
Accelerator pedal position signal
Engine speed signal
Unified meter and A/C amp. Transmits conditions of parking brake switch via CAN communication to AWD control unit.
Page 5509 of 5621
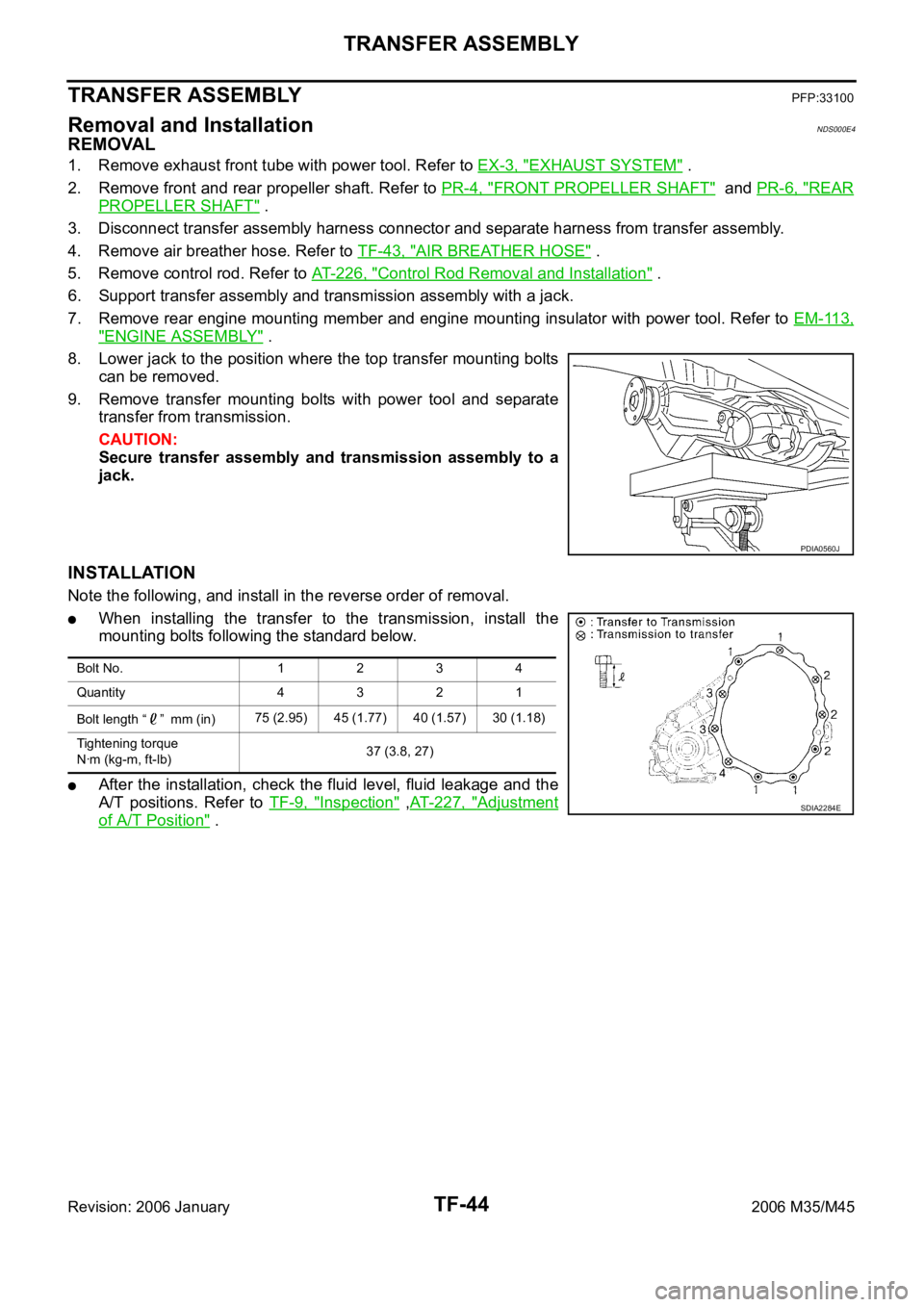
TF-44
TRANSFER ASSEMBLY
Revision: 2006 January2006 M35/M45
TRANSFER ASSEMBLYPFP:33100
Removal and InstallationNDS000E4
REMOVAL
1. Remove exhaust front tube with power tool. Refer to EX-3, "EXHAUST SYSTEM" .
2. Remove front and rear propeller shaft. Refer to PR-4, "
FRONT PROPELLER SHAFT" and PR-6, "REAR
PROPELLER SHAFT" .
3. Disconnect transfer assembly harness connector and separate harness from transfer assembly.
4. Remove air breather hose. Refer to TF-43, "
AIR BREATHER HOSE" .
5. Remove control rod. Refer to AT-226, "
Control Rod Removal and Installation" .
6. Support transfer assembly and transmission assembly with a jack.
7. Remove rear engine mounting member and engine mounting insulator with power tool. Refer to EM-113,
"ENGINE ASSEMBLY" .
8. Lower jack to the position where the top transfer mounting bolts
can be removed.
9. Remove transfer mounting bolts with power tool and separate
transfer from transmission.
CAUTION:
Secure transfer assembly and transmission assembly to a
jack.
INSTALLATION
Note the following, and install in the reverse order of removal.
When installing the transfer to the transmission, install the
mounting bolts following the standard below.
After the installation, check the fluid level, fluid leakage and the
A/T positions. Refer to TF-9, "
Inspection" ,AT- 2 2 7 , "Adjustment
of A/T Position" .
PDIA0560J
Bolt No. 1234
Quantity 4321
Bolt length “ ” mm (in)75 (2.95) 45 (1.77) 40 (1.57) 30 (1.18)
Tightening torque
Nꞏm (kg-m, ft-lb)37 (3.8, 27)
SDIA2284E
Page 5521 of 5621
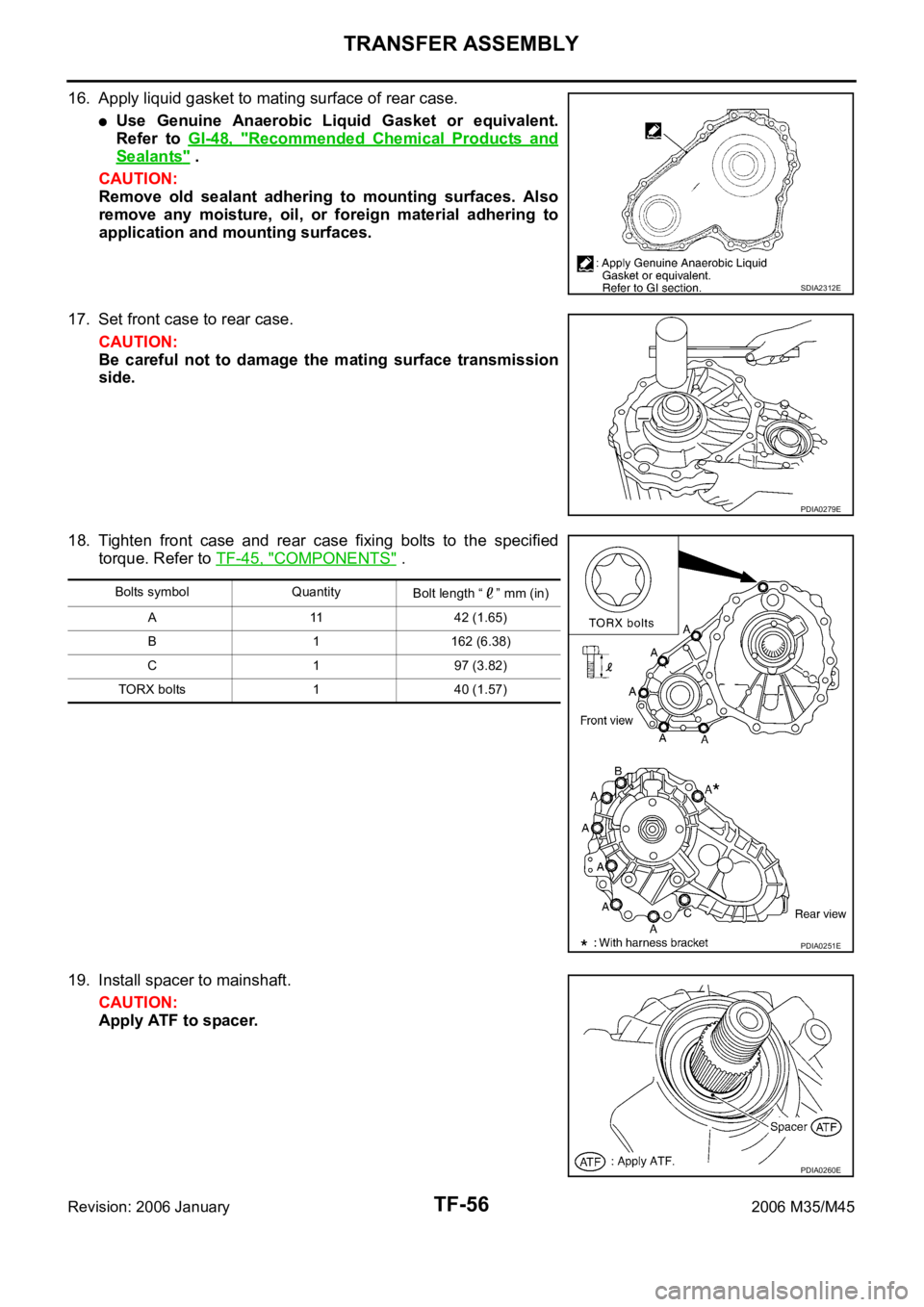
TF-56
TRANSFER ASSEMBLY
Revision: 2006 January2006 M35/M45
16. Apply liquid gasket to mating surface of rear case.
Use Genuine Anaerobic Liquid Gasket or equivalent.
Refer to GI-48, "
Recommended Chemical Products and
Sealants" .
CAUTION:
Remove old sealant adhering to mounting surfaces. Also
remove any moisture, oil, or foreign material adhering to
application and mounting surfaces.
17. Set front case to rear case.
CAUTION:
Be careful not to damage the mating surface transmission
side.
18. Tighten front case and rear case fixing bolts to the specified
torque. Refer to TF-45, "
COMPONENTS" .
19. Install spacer to mainshaft.
CAUTION:
Apply ATF to spacer.
SDIA2312E
PDIA0279E
Bolts symbol Quantity
Bolt length “ ” mm (in)
A 11 42 (1.65)
B 1 162 (6.38)
C 1 97 (3.82)
TORX bolts 1 40 (1.57)
PDIA0251E
PDIA0260E
Page 5537 of 5621
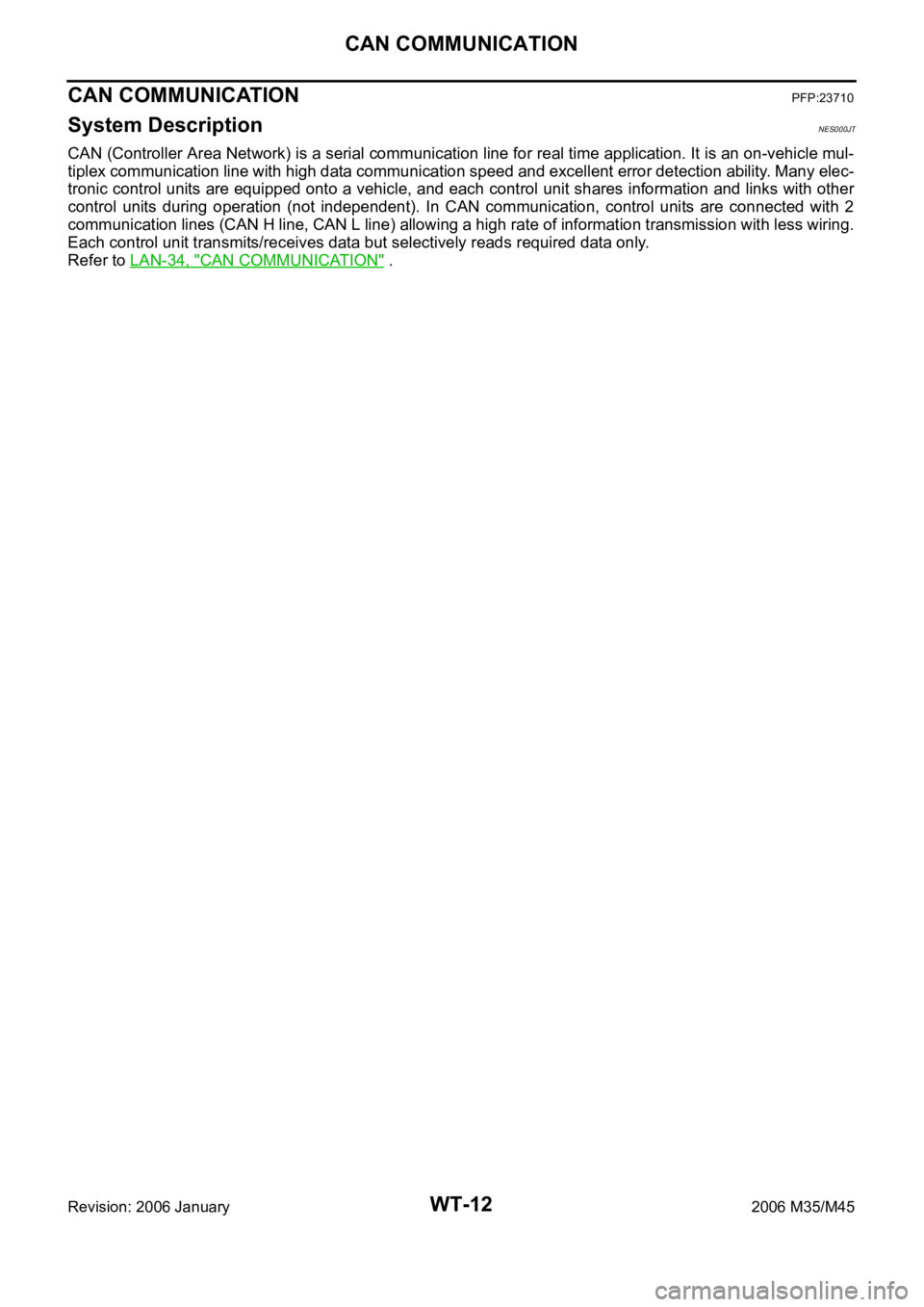
WT-12
CAN COMMUNICATION
Revision: 2006 January2006 M35/M45
CAN COMMUNICATIONPFP:23710
System DescriptionNES000JT
CAN (Controller Area Network) is a serial communication line for real time application. It is an on-vehicle mul-
tiplex communication line with high data communication speed and excellent error detection ability. Many elec-
tronic control units are equipped onto a vehicle, and each control unit shares information and links with other
control units during operation (not independent). In CAN communication, control units are connected with 2
communication lines (CAN H line, CAN L line) allowing a high rate of information transmission with less wiring.
Each control unit transmits/receives data but selectively reads required data only.
Refer to LAN-34, "
CAN COMMUNICATION" .
Page 5578 of 5621
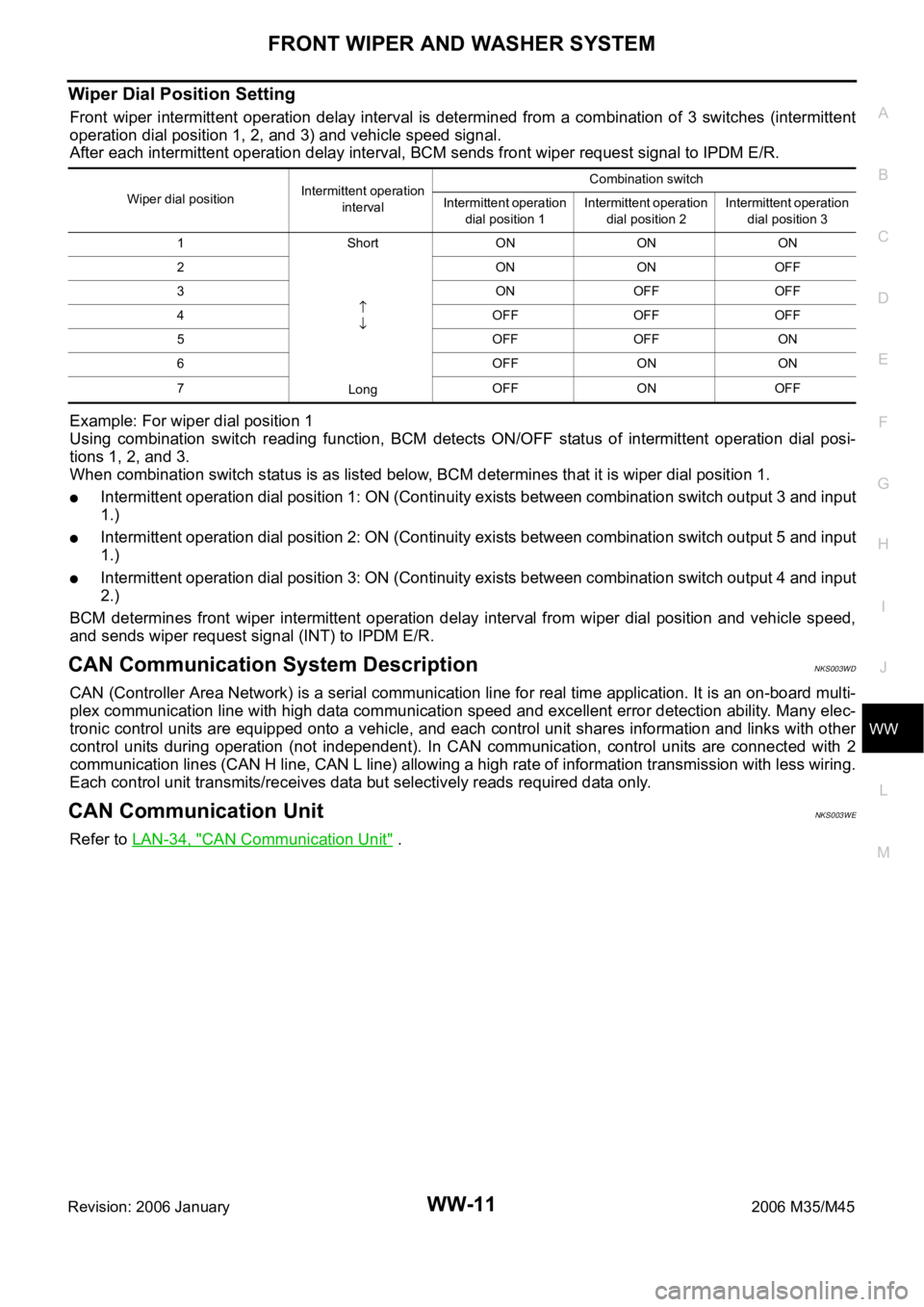
FRONT WIPER AND WASHER SYSTEM
WW-11
C
D
E
F
G
H
I
J
L
MA
B
WW
Revision: 2006 January2006 M35/M45
Wiper Dial Position Setting
Front wiper intermittent operation delay interval is determined from a combination of 3 switches (intermittent
operation dial position 1, 2, and 3) and vehicle speed signal.
After each intermittent operation delay interval, BCM sends front wiper request signal to IPDM E/R.
Example: For wiper dial position 1
Using combination switch reading function, BCM detects ON/OFF status of intermittent operation dial posi-
tions 1, 2, and 3.
When combination switch status is as listed below, BCM determines that it is wiper dial position 1.
Intermittent operation dial position 1: ON (Continuity exists between combination switch output 3 and input
1.)
Intermittent operation dial position 2: ON (Continuity exists between combination switch output 5 and input
1.)
Intermittent operation dial position 3: ON (Continuity exists between combination switch output 4 and input
2.)
BCM determines front wiper intermittent operation delay interval from wiper dial position and vehicle speed,
and sends wiper request signal (INT) to IPDM E/R.
CAN Communication System DescriptionNKS003WD
CAN (Controller Area Network) is a serial communication line for real time application. It is an on-board multi-
plex communication line with high data communication speed and excellent error detection ability. Many elec-
tronic control units are equipped onto a vehicle, and each control unit shares information and links with other
control units during operation (not independent). In CAN communication, control units are connected with 2
communication lines (CAN H line, CAN L line) allowing a high rate of information transmission with less wiring.
Each control unit transmits/receives data but selectively reads required data only.
CAN Communication UnitNKS003WE
Refer to LAN-34, "CAN Communication Unit" .
Wiper dial positionIntermittent operation
intervalCombination switch
Intermittent operation
dial position 1Intermittent operation
dial position 2Intermittent operation
dial position 3
1Short
LongON ON ON
2ONONOFF
3ONOFFOFF
4 OFF OFF OFF
5OFFOFFON
6 OFF ON ON
7 OFF ON OFF