transmission INFINITI M35 2006 Factory Service Manual
[x] Cancel search | Manufacturer: INFINITI, Model Year: 2006, Model line: M35, Model: INFINITI M35 2006Pages: 5621, PDF Size: 65.56 MB
Page 1 of 5621
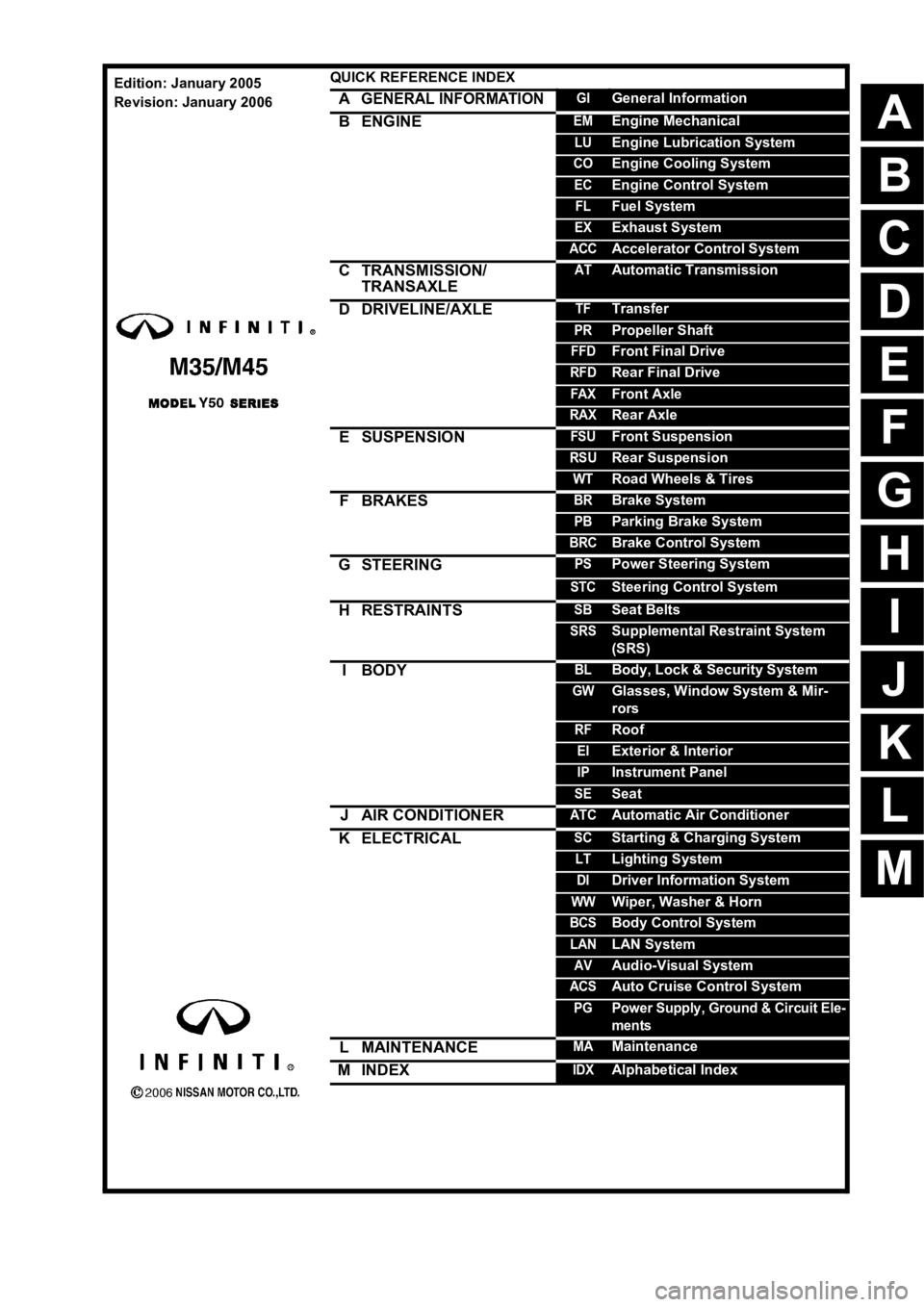
A
B
C
D
E
F
G
H
I
J
K
M
L
QUICK REFERENCE INDEX
AGENERAL INFORMATIONGIGeneral Information
BENGINEEMEngine Mechanical
LUEngine Lubrication System
COEngine Cooling System
ECEngine Control System
FLFuel System
EXExhaust System
ACCAccelerator Control System
CTRANSMISSION/
TRANSAXLEATAutomatic Transmission
DDRIVELINE/AXLETFTransfer
PRPropeller Shaft
FFDFront Final Drive
RFDRear Final Drive
FAXFront Axle
RAXRear Axle
ESUSPENSIONFSUFront Suspension
RSURear Suspension
WTRoad Wheels & Tires
FBRAKESBRBrake System
PBParking Brake System
BRCBrake Control System
GSTEERINGPSPower Steering System
STCSteering Control System
HRESTRAINTSSBSeat Belts
SRSSupplemental Restraint System
(SRS)
IBODYBLBody, Lock & Security System
GWGlasses, Window System & Mir-
rors
RFRoof
EIExterior & Interior
IPInstrument Panel
SESeat
JAIR CONDITIONERATCAutomatic Air Conditioner
KELECTRICALSCStarting & Charging System
LTLighting System
DIDriver Information System
WWWiper, Washer & Horn
BCSBody Control System
LANLAN System
AVAudio-Visual System
ACSAuto Cruise Control System
PGPower Supply, Ground & Circuit Ele-
ments
LMAINTENANCEMAMaintenance
MINDEXIDXAlphabetical Index
Edition: January 2005
Revision: January 2006
Page 5 of 5621
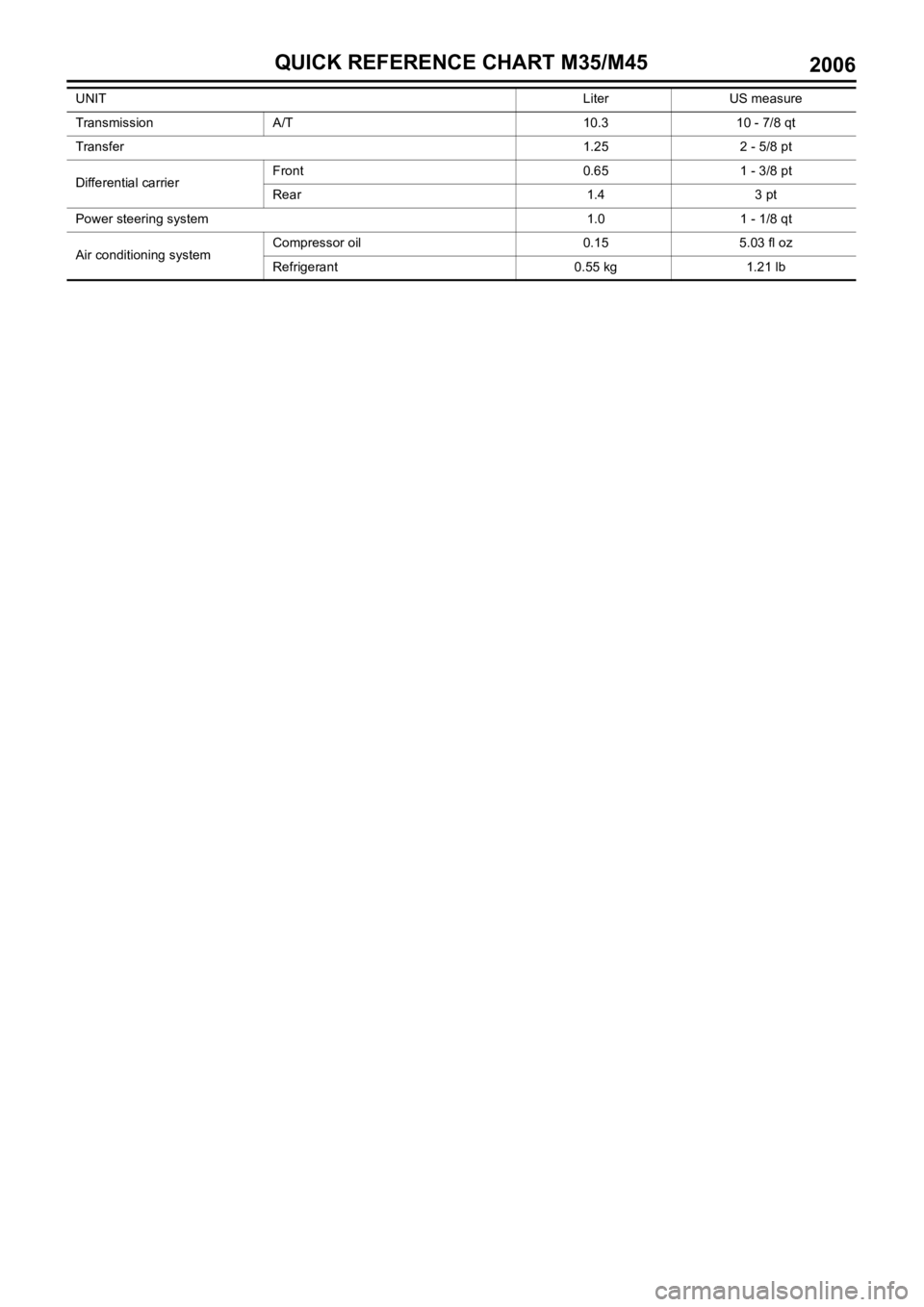
QUICK REFERENCE CHART M35/M45
Transmission A/T 10.3 10 - 7/8 qt
Transfer1.25 2 - 5/8 pt
Differential carrierFront 0.65 1 - 3/8 pt
Rear 1.4 3 pt
Power steering system 1.0 1 - 1/8 qt
Air conditioning systemCompressor oil 0.15 5.03 fl oz
Refrigerant 0.55 kg 1.21 lb UNITLiter US measure
2006
Page 16 of 5621
![INFINITI M35 2006 Factory Service Manual DESCRIPTION
ACS-7
[ICC]
C
D
E
F
G
H
I
J
L
MA
B
ACS
Revision: 2006 January2006 M35/M45
Components DescriptionNKS004CH
CAN CommunicationNKS004CI
CAN (Controller Area Network) is a serial communication l INFINITI M35 2006 Factory Service Manual DESCRIPTION
ACS-7
[ICC]
C
D
E
F
G
H
I
J
L
MA
B
ACS
Revision: 2006 January2006 M35/M45
Components DescriptionNKS004CH
CAN CommunicationNKS004CI
CAN (Controller Area Network) is a serial communication l](/img/42/57023/w960_57023-15.png)
DESCRIPTION
ACS-7
[ICC]
C
D
E
F
G
H
I
J
L
MA
B
ACS
Revision: 2006 January2006 M35/M45
Components DescriptionNKS004CH
CAN CommunicationNKS004CI
CAN (Controller Area Network) is a serial communication line for real time application. It is an on-vehicle mul-
tiplex communication line with high data communication speed and excellent error detection ability. Many elec-
tric control units are equipped onto a vehicle, and each control unit shares information and links with other
control units during operation (not independent). In CAN communication, control units are connected with 2
communication lines (CAN H line, CAN L line) allowing a high rate of information transmission with less wiring.
Each control unit transmits/receives data but selectively reads required data only.
CAN COMMUNICATION UNIT
Refer to LAN-34, "CAN Communication Unit" .
ComponentVehicle-to-
vehicle
distance
control modeConventional
(fixed speed)
cruise
control modeBrake assist
(with pre-
view func-
tion)Description
ICC sensor integrated unit
Controls vehicle distance by operating electric throttle
control actuator based on that sensor signals and
CAN communication data.
Controls vehicle distance by transmitting deceleration
degree commandment value signal to ABS actuator
and electric unit (control unit) when deceleration with
brake is needed.
Irradiates laser beam, and receives reflected laser
beam to measure distance from preceding vehicle.
ECM
Transmits accelerator pedal position signal, ICC brake
switch signal, stop lamp switch signal and ICC steering
switch signal to ICC sensor integrated unit through CAN
communication.
ABS actuator and electric
unit (control unit)
Transmits vehicle speed signal (wheel speed) and
stop lamp switch signal to ICC sensor integrated unit
through CAN communication.
Receives Deceleration degree commandment value
signal from ICC sensor integrated unit, and controls
brake fluid pressure with the ABS motor.
BCM
Transmits front wiper request signal to ICC sensor inte-
grated unit through CAN communication.
TCM
Transmits gear position signal and output shaft revolu-
tion signal to ICC sensor integrated unit through CAN
communication.
Unified meter and A/C amp.
Receives meter display signal, ICC warning lamp signal
and buzzer output signal from ICC sensor integrated
unit through CAN communication.
ICC brake switch
Transmits operating signal to ECM when depressing
brake pedal. ICC sensor integrated unit cancels cruise
system at driver's brake operation.
Stop lamp switch
Transmits operating signal to ECM and ABS actuator
and electric unit (control unit) when depressing brake
pedal. ICC sensor integrated unit cancels cruise system
at driver's brake operation.
Page 80 of 5621
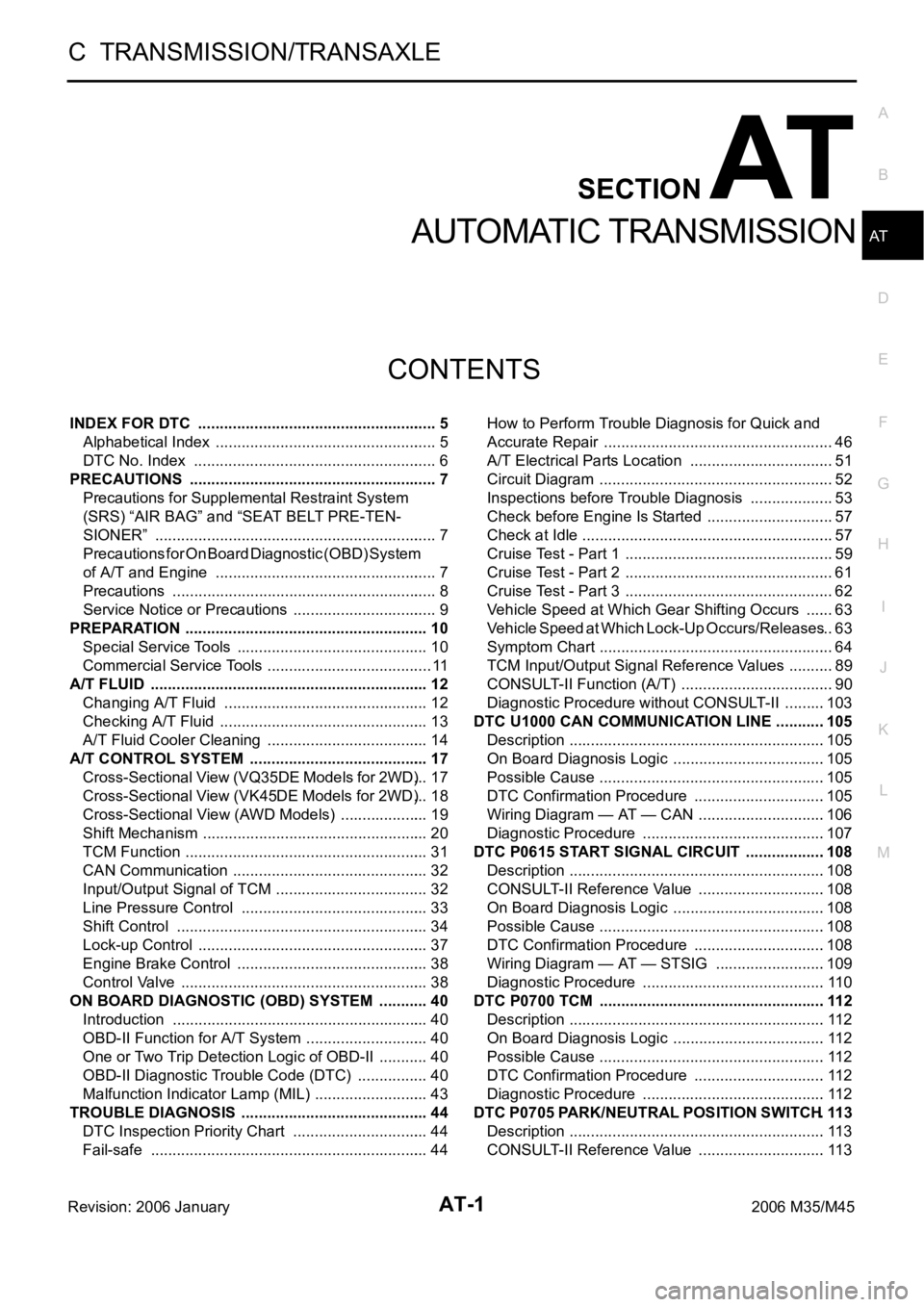
AT-1
AUTOMATIC TRANSMISSION
C TRANSMISSION/TRANSAXLE
CONTENTS
D
E
F
G
H
I
J
K
L
M
SECTION AT
A
B
AT
Revision: 2006 January2006 M35/M45
AUTOMATIC TRANSMISSION
INDEX FOR DTC ........................................................ 5
Alphabetical Index .................................................... 5
DTC No. Index ......................................................... 6
PRECAUTIONS .......................................................... 7
Precautions for Supplemental Restraint System
(SRS) “AIR BAG” and “SEAT BELT PRE-TEN-
SIONER” .................................................................. 7
Precautions for On Board Diagnostic (OBD) System
of A/T and Engine .................................................... 7
Precautions .............................................................. 8
Service Notice or Precautions .................................. 9
PREPARATION ......................................................... 10
Special Service Tools ............................................. 10
Commercial Service Tools ....................................... 11
A/T FLUID ................................................................. 12
Changing A/T Fluid .............................................
... 12
Checking A/T Fluid ................................................. 13
A/T Fluid Cooler Cleaning ...................................... 14
A/T CONTROL SYSTEM .......................................... 17
Cross-Sectional View (VQ35DE Models for 2WD) ... 17
Cross-Sectional View (VK45DE Models for 2WD) ... 18
Cross-Sectional View (AWD Models) ..................... 19
Shift Mechanism ..................................................... 20
TCM Function ......................................................... 31
CAN Communication .............................................. 32
Input/Output Signal of TCM .................................... 32
Line Pressure Control ............................................ 33
Shift Control ........................................................... 34
Lock-up Control ...................................................... 37
Engine Brake Control ............................................. 38
Control Valve .......................................................... 38
ON BOARD DIAGNOSTIC (OBD) SYSTEM ............ 40
Introduction ............................................................ 40
OBD-II Function for A/T System ............................. 40
One or Two Trip Detection Logic of OBD-II ............ 40
OBD-II Diagnostic Trouble Code (DTC) ................. 40
Malfunction Indicator Lamp (MIL) ........................... 43
TROUBLE DIAGNOSIS ............................................ 44
DTC Inspection Priority Chart ................................ 44
Fail-safe ................................................................. 44How to Perform Trouble Diagnosis for Quick and
Accurate Repair ...................................................... 46
A/T Electrical Parts Location .................................. 51
Circuit Diagram ....................................................... 52
Inspections before Trouble Diagnosis .................... 53
Check before Engine Is Started .............................. 57
Check at Idle ........................................................... 57
Cruise Test - Part 1 ................................................. 59
Cruise Test - Part 2 ................................................. 61
Cruise Test - Part 3 ................................................. 62
Vehicle Speed at Which Gear Shifting Occurs ....... 63
Vehicle Speed at Which Lock-Up Occurs/Releases ... 63
Symptom Chart ....................................................... 64
TCM Input/Output Signal Reference Values ........... 89
CONSULT-II Function (A/T) .................................... 90
Diagnostic Procedure without CONSULT-II ..........103
DTC U1000 CAN COMMUNICATION LINE ............105
Description ............................................................105
On Board Diagnosis Logic ....................................105
Possible Cause .....................................................105
DTC Confirmation Procedure ...............................105
Wiring Diagram — AT — CAN ..............................106
Diagnostic Procedure ...........................................107
DTC P0615 START SIGNAL CIRCUIT ...................108
Description ............................................................108
CONSULT-II Reference Value ..............................108
On Board Diagnosis Logic ....................................108
Possible Cause .....................................................108
DTC Confirmation Procedure ...............................108
Wiring Diagram — AT — STSIG ..........................109
Diagnostic Procedure ...........................................110
DTC P0700 TCM .....................................................112
Description ............................................................112
On Board Diagnosis Logic ....................................112
Possible Cause .....................................................112
DTC Confirmation Procedure ...............................112
Diagnostic Procedure ...........................................112
DTC P0705 PARK/NEUTRAL POSITION SWITCH .113
Description ............................................................113
CONSULT-II Reference Value ..............................113
Page 83 of 5621
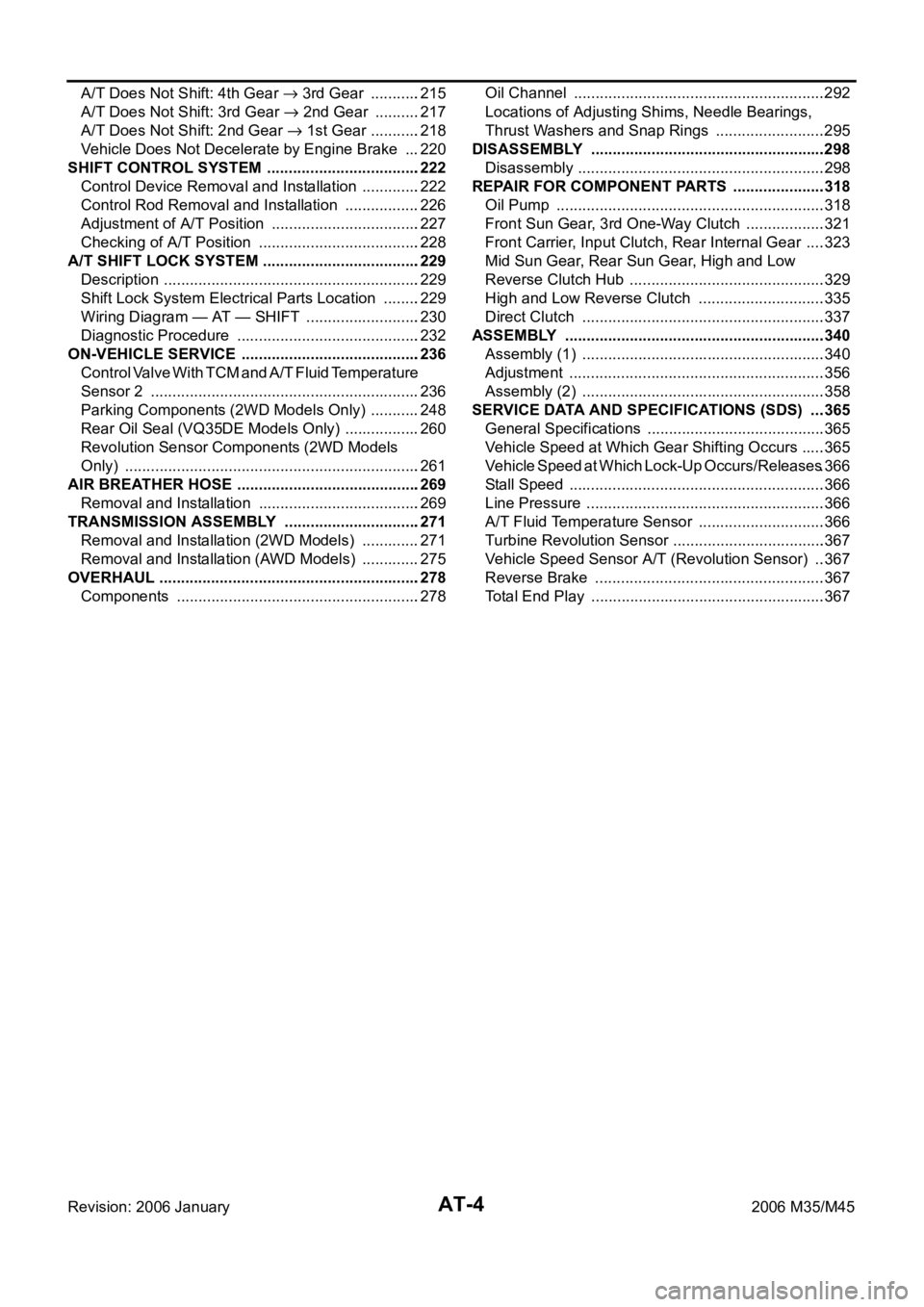
AT-4Revision: 2006 January2006 M35/M45 A/T Does Not Shift: 4th Gear
3rd Gear ............215
A/T Does Not Shift: 3rd Gear
2nd Gear ...........217
A/T Does Not Shift: 2nd Gear
1st Gear ............218
Vehicle Does Not Decelerate by Engine Brake ....220
SHIFT CONTROL SYSTEM ....................................222
Control Device Removal and Installation ..............222
Control Rod Removal and Installation ..................226
Adjustment of A/T Position ...................................227
Checking of A/T Position ......................................228
A/T SHIFT LOCK SYSTEM .....................................229
Description ............................................................229
Shift Lock System Electrical Parts Location .........229
Wiring Diagram — AT — SHIFT ...........................230
Diagnostic Procedure ...........................................232
ON-VEHICLE SERVICE ..........................................236
C o n t r o l V a l v e W i t h T C M a n d A / T F l u i d Te m p e r a t u r e
Sensor 2 ...............................................................236
Parking Components (2WD Models Only) ............248
Rear Oil Seal (VQ35DE Models Only) ..................260
Revolution Sensor Components (2WD Models
Only) .....................................................................261
AIR BREATHER HOSE ...........................................269
Removal and Installation ......................................269
TRANSMISSION ASSEMBLY ................................271
Removal and Installation (2WD Models) ..............271
Removal and Installation (AWD Models) ..............275
OVERHAUL .............................................................278
Components .........................................................278Oil Channel ...........................................................292
Locations of Adjusting Shims, Needle Bearings,
Thrust Washers and Snap Rings ..........................295
DISASSEMBLY .......................................................298
Disassembly ..........................................................298
REPAIR FOR COMPONENT PARTS ......................318
Oil Pump ...............................................................318
Front Sun Gear, 3rd One-Way Clutch ...................321
Front Carrier, Input Clutch, Rear Internal Gear .....323
Mid Sun Gear, Rear Sun Gear, High and Low
Reverse Clutch Hub ..............................................329
High and Low Reverse Clutch ..............................335
Direct Clutch .........................................................337
ASSEMBLY .............................................................340
Assembly (1) .........................................................340
Adjustment ............................................................356
Assembly (2) .........................................................358
SERVICE DATA AND SPECIFICATIONS (SDS) ....365
General Specifications ......................................... .365
Vehicle Speed at Which Gear Shifting Occurs ......365
Vehicle Speed at Which Lock-Up Occurs/Releases .366
Stall Speed ............................................................366
Line Pressure ........................................................366
A/T Fluid Temperature Sensor ..............................366
Turbine Revolution Sensor ....................................367
Vehicle Speed Sensor A/T (Revolution Sensor) ...367
Reverse Brake ......................................................367
Total End Play .......................................................367
Page 87 of 5621
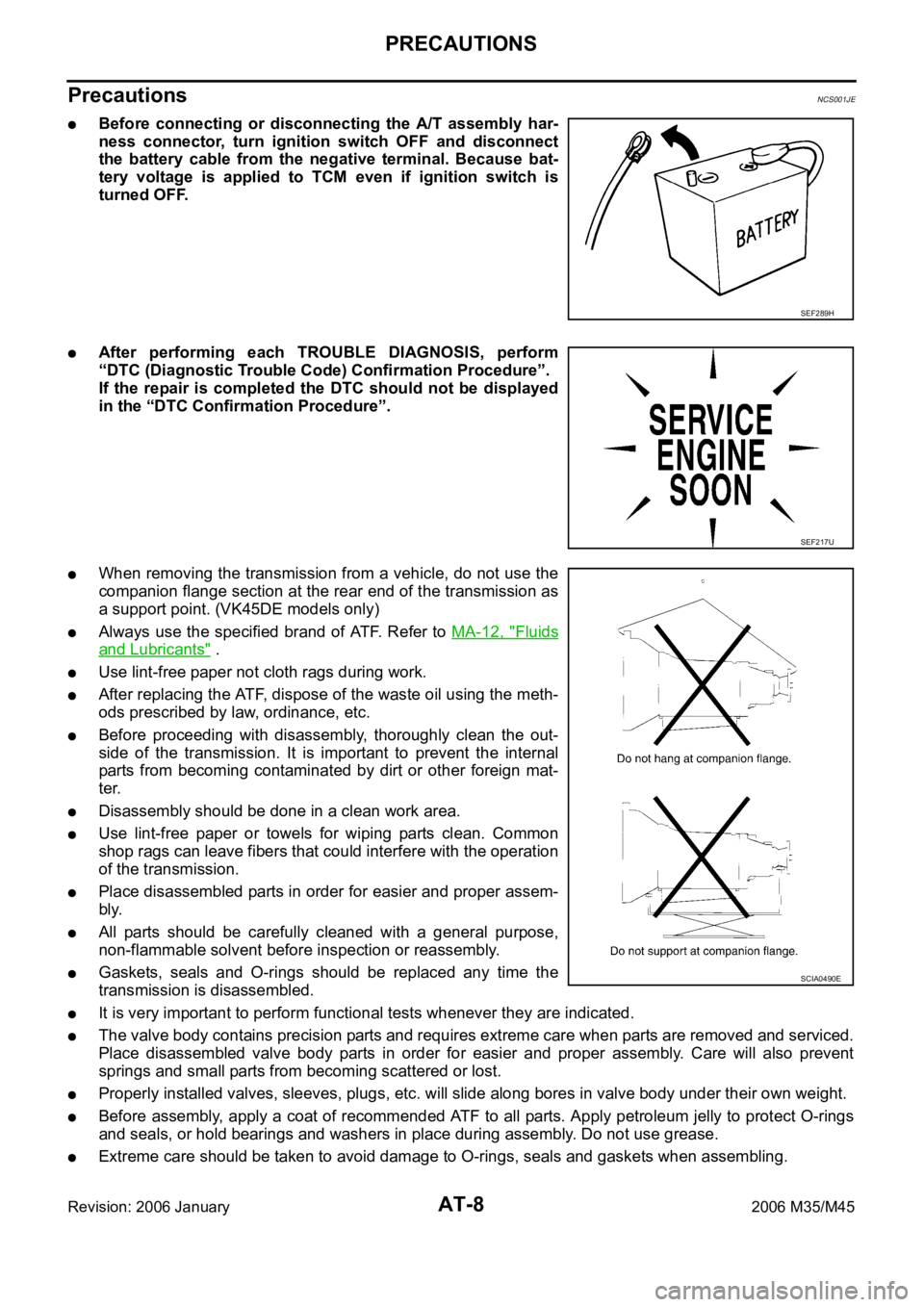
AT-8
PRECAUTIONS
Revision: 2006 January2006 M35/M45
Precautions NCS001JE
Before connecting or disconnecting the A/T assembly har-
ness connector, turn ignition switch OFF and disconnect
the battery cable from the negative terminal. Because bat-
tery voltage is applied to TCM even if ignition switch is
turned OFF.
After performing each TROUBLE DIAGNOSIS, perform
“DTC (Diagnostic Trouble Code) Confirmation Procedure”.
If the repair is completed the DTC should not be displayed
in the “DTC Confirmation Procedure”.
When removing the transmission from a vehicle, do not use the
companion flange section at the rear end of the transmission as
a support point. (VK45DE models only)
Always use the specified brand of ATF. Refer to MA-12, "Fluids
and Lubricants" .
Use lint-free paper not cloth rags during work.
After replacing the ATF, dispose of the waste oil using the meth-
ods prescribed by law, ordinance, etc.
Before proceeding with disassembly, thoroughly clean the out-
side of the transmission. It is important to prevent the internal
parts from becoming contaminated by dirt or other foreign mat-
ter.
Disassembly should be done in a clean work area.
Use lint-free paper or towels for wiping parts clean. Common
shop rags can leave fibers that could interfere with the operation
of the transmission.
Place disassembled parts in order for easier and proper assem-
bly.
All parts should be carefully cleaned with a general purpose,
non-flammable solvent before inspection or reassembly.
Gaskets, seals and O-rings should be replaced any time the
transmission is disassembled.
It is very important to perform functional tests whenever they are indicated.
The valve body contains precision parts and requires extreme care when parts are removed and serviced.
Place disassembled valve body parts in order for easier and proper assembly. Care will also prevent
springs and small parts from becoming scattered or lost.
Properly installed valves, sleeves, plugs, etc. will slide along bores in valve body under their own weight.
Before assembly, apply a coat of recommended ATF to all parts. Apply petroleum jelly to protect O-rings
and seals, or hold bearings and washers in place during assembly. Do not use grease.
Extreme care should be taken to avoid damage to O-rings, seals and gaskets when assembling.
SEF289H
SEF217U
SCIA0490E
Page 88 of 5621
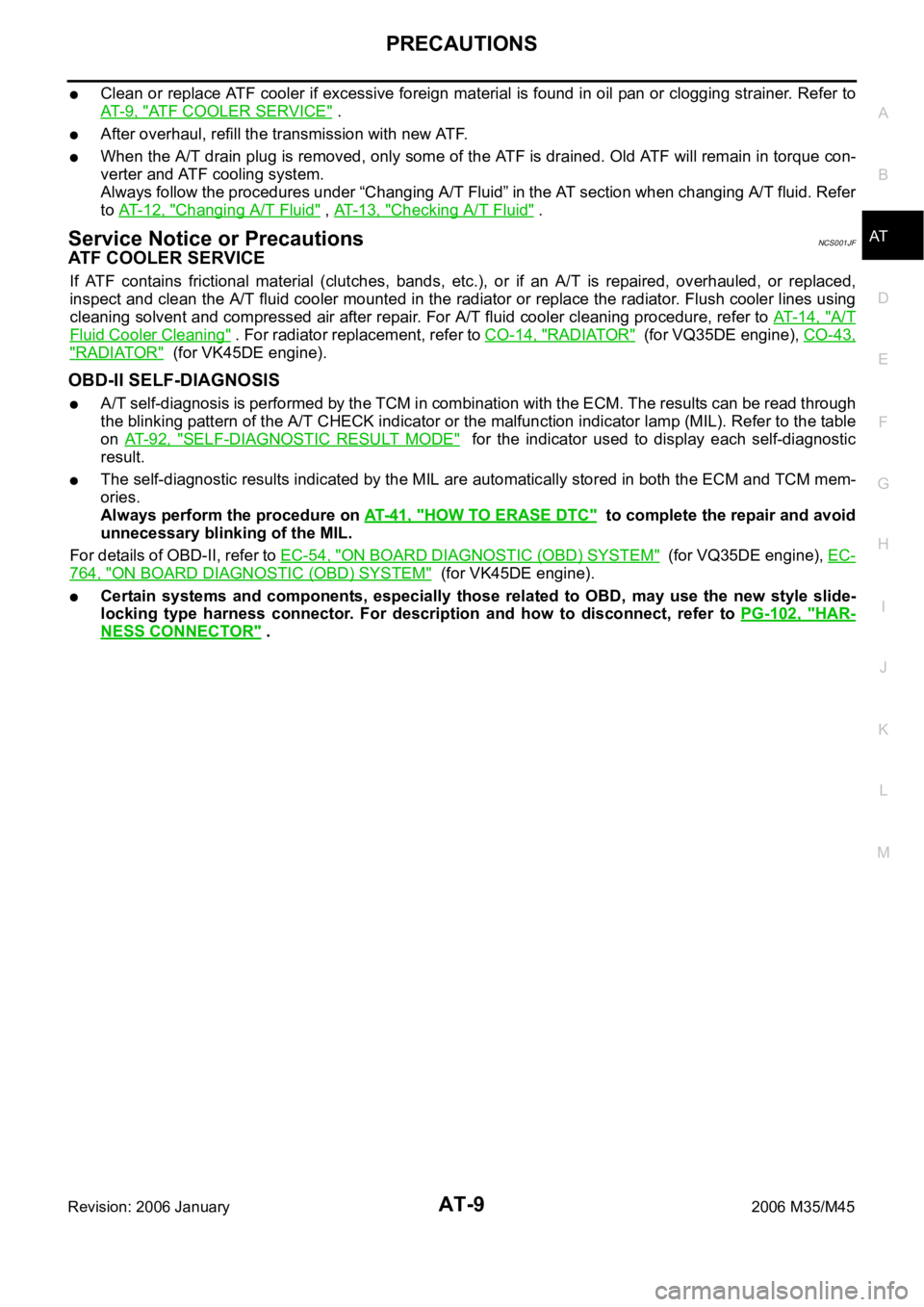
PRECAUTIONS
AT-9
D
E
F
G
H
I
J
K
L
MA
B
AT
Revision: 2006 January2006 M35/M45
Clean or replace ATF cooler if excessive foreign material is found in oil pan or clogging strainer. Refer to
AT- 9 , "
ATF COOLER SERVICE" .
After overhaul, refill the transmission with new ATF.
When the A/T drain plug is removed, only some of the ATF is drained. Old ATF will remain in torque con-
verter and ATF cooling system.
Always follow the procedures under “Changing A/T Fluid” in the AT section when changing A/T fluid. Refer
to AT- 1 2 , "
Changing A/T Fluid" , AT- 1 3 , "Checking A/T Fluid" .
Service Notice or PrecautionsNCS001JF
ATF COOLER SERVICE
If ATF contains frictional material (clutches, bands, etc.), or if an A/T is repaired, overhauled, or replaced,
inspect and clean the A/T fluid cooler mounted in the radiator or replace the radiator. Flush cooler lines using
cleaning solvent and compressed air after repair. For A/T fluid cooler cleaning procedure, refer to AT- 1 4 , "
A/T
Fluid Cooler Cleaning" . For radiator replacement, refer to CO-14, "RADIATOR" (for VQ35DE engine), CO-43,
"RADIATOR" (for VK45DE engine).
OBD-II SELF-DIAGNOSIS
A/T self-diagnosis is performed by the TCM in combination with the ECM. The results can be read through
the blinking pattern of the A/T CHECK indicator or the malfunction indicator lamp (MIL). Refer to the table
on AT- 9 2 , "
SELF-DIAGNOSTIC RESULT MODE" for the indicator used to display each self-diagnostic
result.
The self-diagnostic results indicated by the MIL are automatically stored in both the ECM and TCM mem-
ories.
Always perform the procedure on AT- 4 1 , "
HOW TO ERASE DTC" to complete the repair and avoid
unnecessary blinking of the MIL.
For details of OBD-II, refer to EC-54, "
ON BOARD DIAGNOSTIC (OBD) SYSTEM" (for VQ35DE engine), EC-
764, "ON BOARD DIAGNOSTIC (OBD) SYSTEM" (for VK45DE engine).
Certain systems and components, especially those related to OBD, may use the new style slide-
locking type harness connector. For description and how to disconnect, refer to PG-102, "
HAR-
NESS CONNECTOR" .
Page 94 of 5621
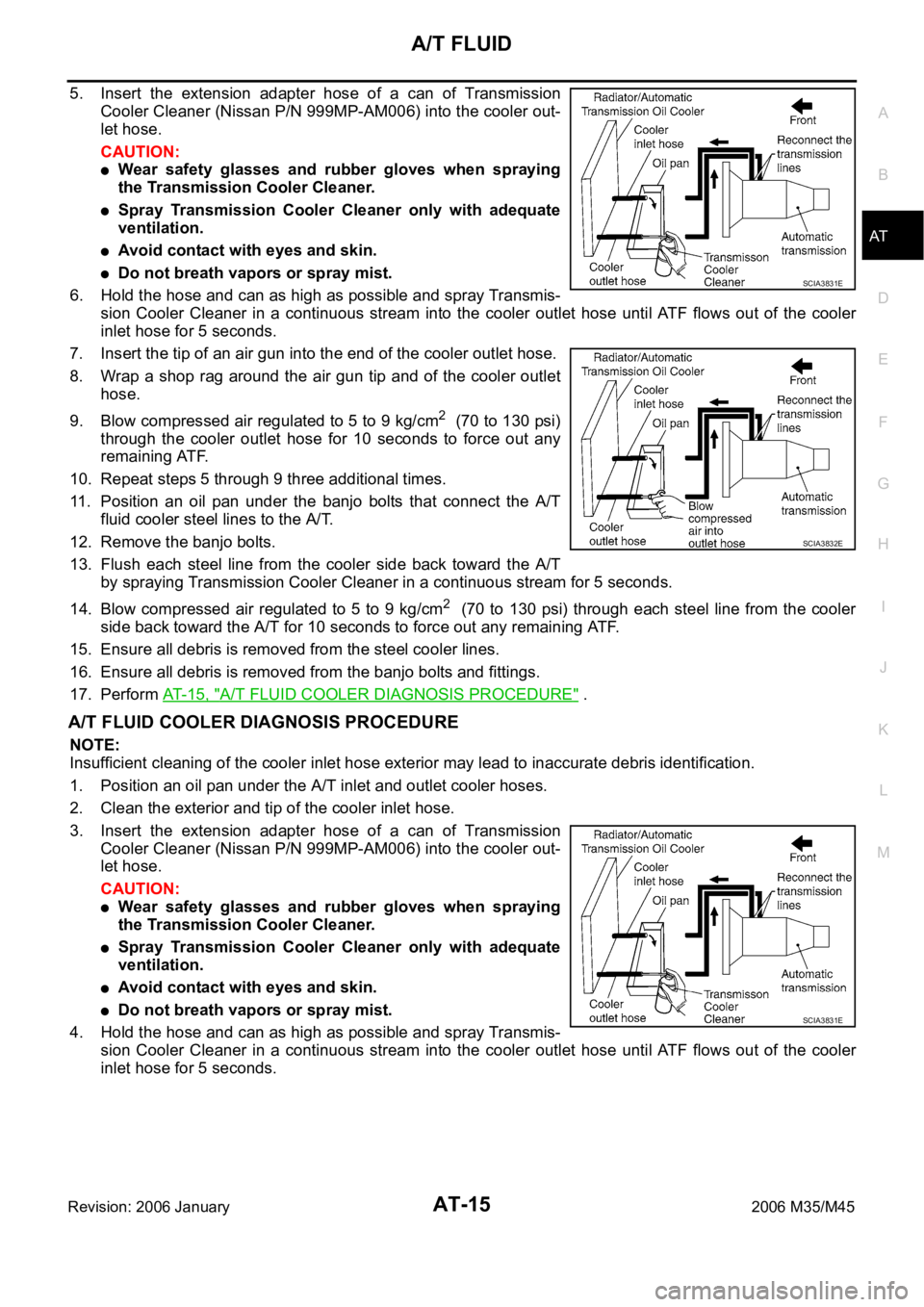
A/T FLUID
AT-15
D
E
F
G
H
I
J
K
L
MA
B
AT
Revision: 2006 January2006 M35/M45
5. Insert the extension adapter hose of a can of Transmission
Cooler Cleaner (Nissan P/N 999MP-AM006) into the cooler out-
let hose.
CAUTION:
Wear safety glasses and rubber gloves when spraying
the Transmission Cooler Cleaner.
Spray Transmission Cooler Cleaner only with adequate
ventilation.
Avoid contact with eyes and skin.
Do not breath vapors or spray mist.
6. Hold the hose and can as high as possible and spray Transmis-
sion Cooler Cleaner in a continuous stream into the cooler outlet hose until ATF flows out of the cooler
inlet hose for 5 seconds.
7. Insert the tip of an air gun into the end of the cooler outlet hose.
8. Wrap a shop rag around the air gun tip and of the cooler outlet
hose.
9. Blow compressed air regulated to 5 to 9 kg/cm
2 (70 to 130 psi)
through the cooler outlet hose for 10 seconds to force out any
remaining ATF.
10. Repeat steps 5 through 9 three additional times.
11. Position an oil pan under the banjo bolts that connect the A/T
fluid cooler steel lines to the A/T.
12. Remove the banjo bolts.
13. Flush each steel line from the cooler side back toward the A/T
by spraying Transmission Cooler Cleaner in a continuous stream for 5 seconds.
14. Blow compressed air regulated to 5 to 9 kg/cm
2 (70 to 130 psi) through each steel line from the cooler
side back toward the A/T for 10 seconds to force out any remaining ATF.
15. Ensure all debris is removed from the steel cooler lines.
16. Ensure all debris is removed from the banjo bolts and fittings.
17. Perform AT- 1 5 , "
A/T FLUID COOLER DIAGNOSIS PROCEDURE" .
A/T FLUID COOLER DIAGNOSIS PROCEDURE
NOTE:
Insufficient cleaning of the cooler inlet hose exterior may lead to inaccurate debris identification.
1. Position an oil pan under the A/T inlet and outlet cooler hoses.
2. Clean the exterior and tip of the cooler inlet hose.
3. Insert the extension adapter hose of a can of Transmission
Cooler Cleaner (Nissan P/N 999MP-AM006) into the cooler out-
let hose.
CAUTION:
Wear safety glasses and rubber gloves when spraying
the Transmission Cooler Cleaner.
Spray Transmission Cooler Cleaner only with adequate
ventilation.
Avoid contact with eyes and skin.
Do not breath vapors or spray mist.
4. Hold the hose and can as high as possible and spray Transmis-
sion Cooler Cleaner in a continuous stream into the cooler outlet hose until ATF flows out of the cooler
inlet hose for 5 seconds.
SCIA3831E
SCIA3832E
SCIA3831E
Page 99 of 5621
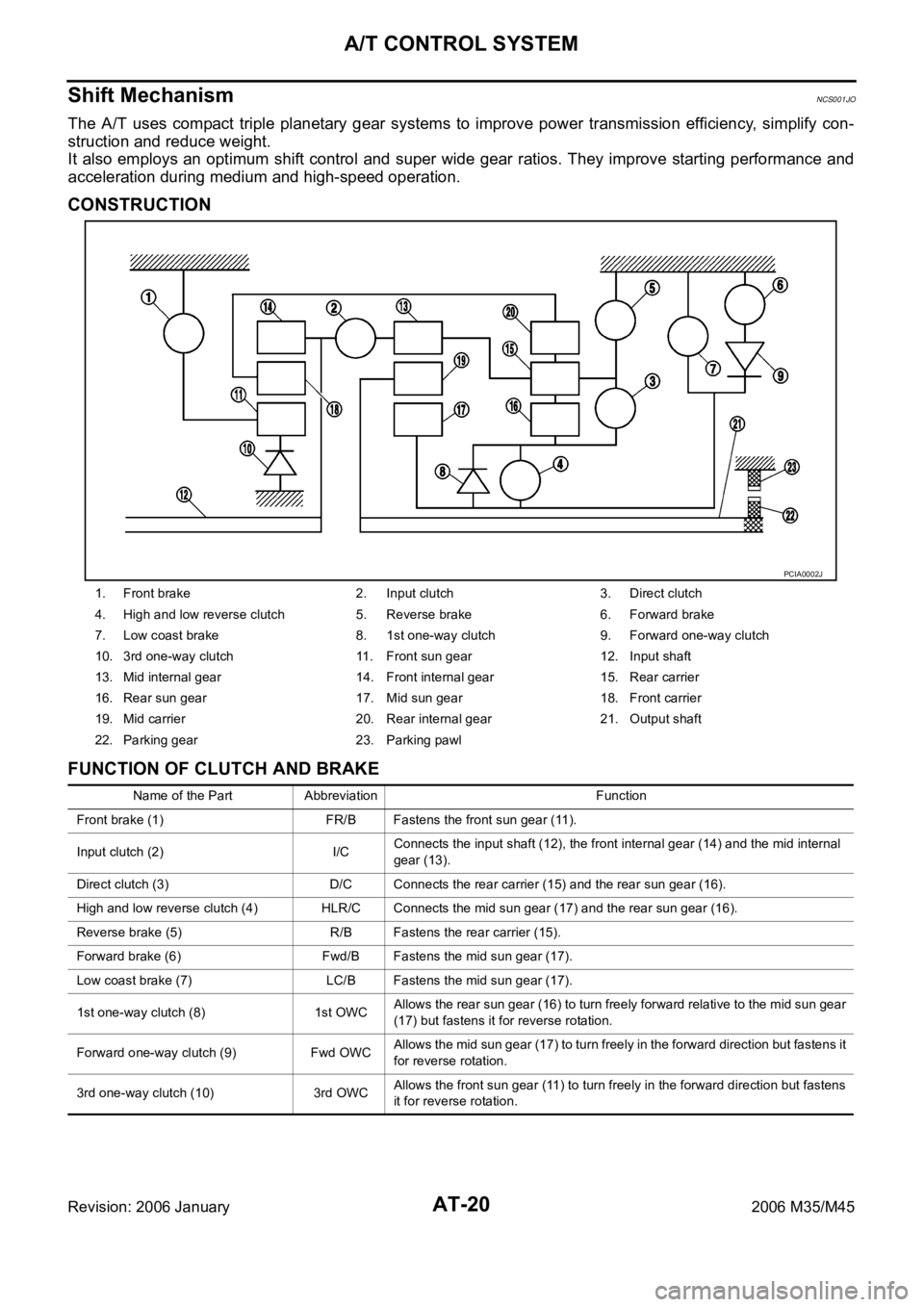
AT-20
A/T CONTROL SYSTEM
Revision: 2006 January2006 M35/M45
Shift MechanismNCS001JO
The A/T uses compact triple planetary gear systems to improve power transmission efficiency, simplify con-
struction and reduce weight.
It also employs an optimum shift control and super wide gear ratios. They improve starting performance and
acceleration during medium and high-speed operation.
CONSTRUCTION
FUNCTION OF CLUTCH AND BRAKE
1. Front brake 2. Input clutch 3. Direct clutch
4. High and low reverse clutch 5. Reverse brake 6. Forward brake
7. Low coast brake 8. 1st one-way clutch 9. Forward one-way clutch
10. 3rd one-way clutch 11. Front sun gear 12. Input shaft
13. Mid internal gear 14. Front internal gear 15. Rear carrier
16. Rear sun gear 17. Mid sun gear 18. Front carrier
19. Mid carrier 20. Rear internal gear 21. Output shaft
22. Parking gear 23. Parking pawl
PCIA0002J
Name of the Part Abbreviation Function
Front brake (1) FR/B Fastens the front sun gear (11).
Input clutch (2) I/CConnects the input shaft (12), the front internal gear (14) and the mid internal
gear (13).
Direct clutch (3) D/C Connects the rear carrier (15) and the rear sun gear (16).
High and low reverse clutch (4) HLR/C Connects the mid sun gear (17) and the rear sun gear (16).
Reverse brake (5) R/B Fastens the rear carrier (15).
Forward brake (6) Fwd/B Fastens the mid sun gear (17).
Low coast brake (7) LC/B Fastens the mid sun gear (17).
1st one-way clutch (8) 1st OWCAllows the rear sun gear (16) to turn freely forward relative to the mid sun gear
(17) but fastens it for reverse rotation.
Forward one-way clutch (9) Fwd OWCAllows the mid sun gear (17) to turn freely in the forward direction but fastens it
for reverse rotation.
3rd one-way clutch (10) 3rd OWCAllows the front sun gear (11) to turn freely in the forward direction but fastens
it for reverse rotation.
Page 101 of 5621
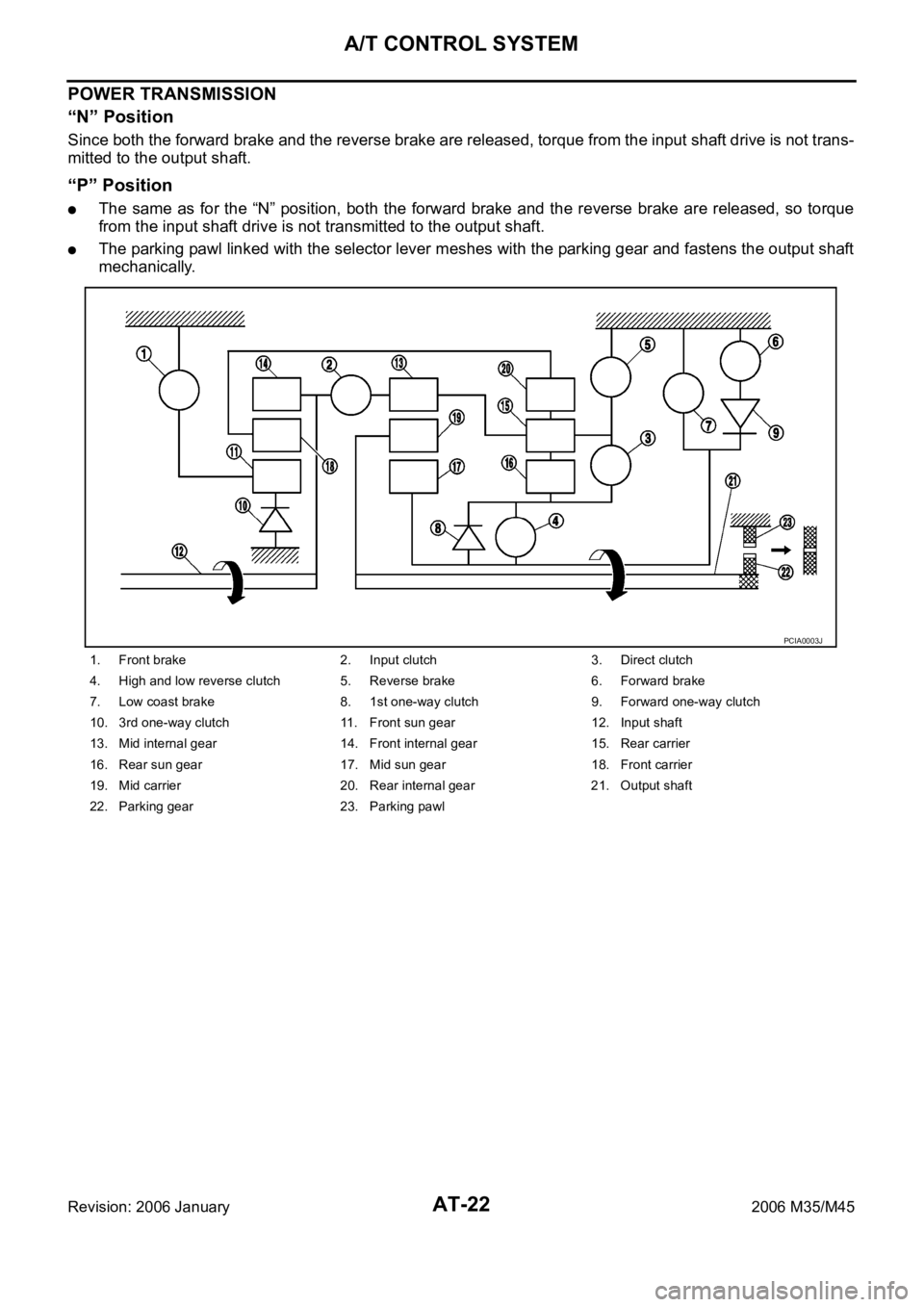
AT-22
A/T CONTROL SYSTEM
Revision: 2006 January2006 M35/M45
POWER TRANSMISSION
“N” Position
Since both the forward brake and the reverse brake are released, torque from the input shaft drive is not trans-
mitted to the output shaft.
“P” Position
The same as for the “N” position, both the forward brake and the reverse brake are released, so torque
from the input shaft drive is not transmitted to the output shaft.
The parking pawl linked with the selector lever meshes with the parking gear and fastens the output shaft
mechanically.
1. Front brake 2. Input clutch 3. Direct clutch
4. High and low reverse clutch 5. Reverse brake 6. Forward brake
7. Low coast brake 8. 1st one-way clutch 9. Forward one-way clutch
10. 3rd one-way clutch 11. Front sun gear 12. Input shaft
13. Mid internal gear 14. Front internal gear 15. Rear carrier
16. Rear sun gear 17. Mid sun gear 18. Front carrier
19. Mid carrier 20. Rear internal gear 21. Output shaft
22. Parking gear 23. Parking pawl
PCIA0003J