radiator INFINITI M35 2006 Factory Manual Online
[x] Cancel search | Manufacturer: INFINITI, Model Year: 2006, Model line: M35, Model: INFINITI M35 2006Pages: 5621, PDF Size: 65.56 MB
Page 3177 of 5621
![INFINITI M35 2006 Factory Manual Online EM-114
[VQ35DE]
ENGINE ASSEMBLY
Revision: 2006 January2006 M35/M45
REMOVAL
Outline
At first, remove the engine and the transmission assembly with front suspension member from vehicle down-
ward. Then INFINITI M35 2006 Factory Manual Online EM-114
[VQ35DE]
ENGINE ASSEMBLY
Revision: 2006 January2006 M35/M45
REMOVAL
Outline
At first, remove the engine and the transmission assembly with front suspension member from vehicle down-
ward. Then](/img/42/57023/w960_57023-3176.png)
EM-114
[VQ35DE]
ENGINE ASSEMBLY
Revision: 2006 January2006 M35/M45
REMOVAL
Outline
At first, remove the engine and the transmission assembly with front suspension member from vehicle down-
ward. Then separate the engine from transmission.
Preparation
1. Release fuel pressure. Refer to EC-98, "FUEL PRESSURE RELEASE" .
2. Drain engine coolant from radiator. Refer to CO-11, "
Changing Engine Coolant" .
CAUTION:
Perform this step when engine is cold.
Do not spill engine coolant on drive belts.
3. Disconnect both battery cables. Refer to SC-4, "
BATTERY" .
4. Remove the following parts:
Engine room cover (RH and LH); Refer toEM-14, "ENGINE ROOM COVER" .
Engine cover; Refer to EM-19, "INTAKE MANIFOLD COLLECTOR" .
Front road wheel and tires (power tool)
Front and rear engine undercover (power tool)
Cowl top cover (RH); Refer to EI-18, "COWL TOP" .
Air duct and air cleaner case assembly; EM-17, "AIR CLEANER AND AIR DUCT" .
5. Discharge refrigerant from A/C circuit. Refer to ATC-151, "
REFRIGERANT LINES" .
6. Remove radiator hoses (upper and lower). Refer to CO-14, "
RADIATOR" .
Engine Room LH
1. Disconnect heater hose from vehicle-side, and fit a plug onto hose end to prevent engine coolant leak.
2. Disconnect wire bonding (between vehicle to left bank cylinder head).
3. Disconnect A/C piping from A/C compressor, and temporarily fasten it on vehicle with a rope. Refer to
AT C - 1 5 1 , "
REFRIGERANT LINES" .
4. Disconnect brake booster vacuum hose.
Engine Room RH
1. Disconnect battery positive cable at vehicle side and temporarily fasten it on engine.
2. Disconnect grounding cable.
3. Disconnect fuel feed hose (with damper) and EVAP hose. Refer to EM-45, "
FUEL INJECTOR AND FUEL
TUBE" .
CAUTION:
Fit plugs onto disconnected hoses to prevent fuel leak.
4. Remove reservoir tank of power steering oil pump and piping from vehicle, and temporarily secure them
on engine. Refer to PS-29, "
POWER STEERING OIL PUMP" .
CAUTION:
When temporarily securing, keep the reservoir tank upright to avoid a fluid leak.
Vehicle inside
Follow procedure below to disconnect engine room harness connectors at passenger room side, and tempo-
rarily secure them on engine.
1. Remove passenger-side kicking plate, dash side finisher, and glove box. Refer to EI-37, "
BODY SIDE
TRIM" and IP-10, "INSTRUMENT PANEL ASSEMBLY" .
2. Disconnect engine room harness connectors at unit sides TCM, ECM and other.
3. Disengage intermediate fixing point. Pull out engine room harnesses to engine room side, and temporarily
secure them on engine.
CAUTION:
When pulling out harnesses, take care not to damage harnesses and connectors.
After temporarily securing, cover connectors with vinyl or similar material to protect against for-
eign material adhesion.
Page 3182 of 5621
![INFINITI M35 2006 Factory Manual Online ENGINE ASSEMBLY
EM-119
[VQ35DE]
C
D
E
F
G
H
I
J
K
L
MA
EM
Revision: 2006 January2006 M35/M45
If items or work required are not covered by the engine section, refer to the applicable sections.
Always u INFINITI M35 2006 Factory Manual Online ENGINE ASSEMBLY
EM-119
[VQ35DE]
C
D
E
F
G
H
I
J
K
L
MA
EM
Revision: 2006 January2006 M35/M45
If items or work required are not covered by the engine section, refer to the applicable sections.
Always u](/img/42/57023/w960_57023-3181.png)
ENGINE ASSEMBLY
EM-119
[VQ35DE]
C
D
E
F
G
H
I
J
K
L
MA
EM
Revision: 2006 January2006 M35/M45
If items or work required are not covered by the engine section, refer to the applicable sections.
Always use the support point specified for lifting.
Use either 2-pole lift type or separate type lift as best you can. If board-on type is used for
unavoidable reasons, support at rear axle jacking point with transmission jack or similar tool
before starting work, in preparation for the backward shift of center of gravity.
For supporting points for lifting and jacking point at rear axle, refer to GI-42, "Garage Jack and
Safety Stand and 2-Pole Lift" .
REMOVAL
Outline
At first, remove the engine, the transmission assembly, the transfer assembly and the front final drive assem-
bly with front suspension member from vehicle downward. Then separate the engine, the transmission assem-
bly, the transfer and the front final drive assembly.
Preparation
1. Release fuel pressure. Refer to EC-98, "FUEL PRESSURE RELEASE" .
2. Drain engine coolant from radiator. Refer to CO-11, "
Changing Engine Coolant" .
CAUTION:
Perform this step when engine is cold.
Do not spill engine coolant on drive belts.
3. Disconnect both battery terminals. Refer to SC-4, "
BATTERY" .
4. Remove the following parts:
Engine room cover (RH and LH); Refer to EM-14, "ENGINE ROOM COVER" .
Engine cover; Refer to EM-19, "INTAKE MANIFOLD COLLECTOR" .
Front road wheel and tires (power tool)
Front and rear engine undercover (power tool)
Front cross bar; Refer to FSU-23, "FRONT SUSPENSION ASSEMBLY" .
Cowl top cover (RH); Refer to EI-18, "COWL TOP" .
Air duct and air cleaner case assembly; EM-17, "AIR CLEANER AND AIR DUCT" .
5. Discharge refrigerant from A/C circuit. Refer to ATC-151, "
REFRIGERANT LINES" .
6. Remove radiator hoses (upper and lower). Refer to CO-14, "
RADIATOR" .
Engine Room LH
1. Disconnect heater hose from vehicle-side, and fit a plug onto hose end to prevent engine coolant leak.
2. Disconnect wire bonding (between vehicle to left bank cylinder head).
3. Disconnect A/C piping from A/C compressor, and temporarily fasten it on vehicle with a rope. Refer to
AT C - 1 5 1 , "
REFRIGERANT LINES" .
4. Disconnect brake booster vacuum hose.
Engine Room RH
1. Disconnect battery positive cable vehicle side and temporarily fasten it on engine.
2. Disconnect grounding cables.
3. Disconnect fuel feed hose (with damper) and EVAP hose. Refer to EM-45, "
FUEL INJECTOR AND FUEL
TUBE" .
CAUTION:
Fit plugs onto disconnected hoses to prevent fuel leak.
4. Remove reservoir tank of power steering oil pump and piping from vehicle, and temporarily secure them
on engine. Refer to PS-29, "
POWER STEERING OIL PUMP" .
CAUTION:
When temporarily securing, keep the reservoir tank upright to avoid a fluid leak.
Vehicle inSide
Follow procedure below to disconnect engine room harness connectors at passenger room side, and tempo-
rarily secure them on engine.
Page 3243 of 5621
![INFINITI M35 2006 Factory Manual Online EM-180
[VK45DE]
INTAKE MANIFOLD
Revision: 2006 January2006 M35/M45
Refer to GI-11, "Components" for symbol marks in the figure.
Removal and InstallationNBS004OU
REMOVAL
WAR NING :
To avoid th INFINITI M35 2006 Factory Manual Online EM-180
[VK45DE]
INTAKE MANIFOLD
Revision: 2006 January2006 M35/M45
Refer to GI-11, "Components" for symbol marks in the figure.
Removal and InstallationNBS004OU
REMOVAL
WAR NING :
To avoid th](/img/42/57023/w960_57023-3242.png)
EM-180
[VK45DE]
INTAKE MANIFOLD
Revision: 2006 January2006 M35/M45
Refer to GI-11, "Components" for symbol marks in the figure.
Removal and InstallationNBS004OU
REMOVAL
WAR NING :
To avoid the danger of being scalded, never drain the engine coolant when the engine is hot.
1. Remove engine room cover (RH and LH). Refer to EM-173, "
ENGINE ROOM COVER" .
2. Remove engine cover with power tool.
3. Release fuel pressure. Refer to EC-809, "
FUEL PRESSURE RELEASE" .
4. Remove air duct (inlet), air cleaner case and air duct and resonator assembly. Refer to EM-177, "
AIR
CLEANER AND AIR DUCT" .
5. Drain engine coolant from radiator. Refer to CO-40, "
DRAINING ENGINE COOLANT" .
CAUTION:
Perform this step when the engine is cold.
Do not spill engine coolant on drive belts.
1. PCV tube 2. PCV hose 3. PCV hose
4. Engine cover bracket (RH) 5.EVAP canister purge control sole-
noid valve6. EVAP hose
7. EVAP service port 8. EVAP tube 9. Vacuum hose
10. PCV hose 11. PCV tube 12. PCV hose
13. PCV hose 14. Vacuum hose 15. Vacuum hose
16. Vacuum tank 17. EVAP hose 18. Water hose
19. Intake manifold adapter 20. Gasket 21. Electric throttle control actuator
22. Gasket 23. Intake manifold (lower) 24. Gasket
25. Water hose 26. Engine cover bracket (LH) 27. Vacuum hose
28. Vacuum hose 29. Vacuum hose 30. Water hose
31. VIAS control solenoid valve 32. Vacuum hose 33. Intake manifold (upper)
34. Gasket
A. To centralized under-floor piping B. To rocker cover (right bank) C. To rocker cover (left bank)
D. To thermostat housing E. To air duct and resonator assembly F. To heater pipe
PBIC3365E
Page 3247 of 5621
![INFINITI M35 2006 Factory Manual Online EM-184
[VK45DE]
EXHAUST MANIFOLD AND THREE WAY CATALYST
Revision: 2006 January2006 M35/M45
5. Drain engine coolant from radiator. Refer to CO-40, "Changing Engine Coolant" .
CAUTION:
Perform t INFINITI M35 2006 Factory Manual Online EM-184
[VK45DE]
EXHAUST MANIFOLD AND THREE WAY CATALYST
Revision: 2006 January2006 M35/M45
5. Drain engine coolant from radiator. Refer to CO-40, "Changing Engine Coolant" .
CAUTION:
Perform t](/img/42/57023/w960_57023-3246.png)
EM-184
[VK45DE]
EXHAUST MANIFOLD AND THREE WAY CATALYST
Revision: 2006 January2006 M35/M45
5. Drain engine coolant from radiator. Refer to CO-40, "Changing Engine Coolant" .
CAUTION:
Perform this step when engine is cold.
Do not spill engine coolant on drive belts.
6. Remove radiator. Refer to CO-43, "
RADIATOR" .
7. Remove drive belts. Refer to EM-174, "
DRIVE BELTS" .
8. Remove exhaust front tube with power tool. Refer to EX-3, "
EXHAUST SYSTEM" .
9. Remove air fuel ratio sensor 1 as follows:
a. Disconnect harness connector of each air fuel ratio sensor 1.
b. Remove air fuel ratio sensor 1 on both bank with heated oxygen
sensor wrench (SST).
CAUTION:
Be careful not to damage air fuel ratio sensor 1.
Discard any air fuel ratio sensor 1 which has been
dropped onto a hard surface such as a concrete floor;
replace with a new one.
10. Remove exhaust manifold and three way catalyst (left bank) as follows:
a. Disconnect A/C piping from A/C compressor, then remove A/C compressor with power tool. Refer to AT C -
151, "REFRIGERANT LINES" .
b. Remove steering lower joint to enable steering shaft to move freely. Refer to PS-13, "
STEERING COL-
UMN" .
c. Remove starter motor. Refer to SC-10, "
STARTING SYSTEM" .
d. Remove nuts on bottom of engine mounting insulator (LH), and lift up left side of engine approximately 3
cm (1.18 in) with transmission jack. Refer to EM-244, "
ENGINE ASSEMBLY" .
e. Remove exhaust manifold cover (left bank).
f. Loosen nuts in the reverse order of figure to remove exhaust
manifold and three way catalyst (left bank) with power tool.
NOTE:
Disregard No. 9 to No. 12 when loosening.
11. Remove exhaust manifold and three way catalyst (right bank) as follows:
a. Remove alternator and bracket. Refer to SC-23, "
CHARGING SYSTEM" .
PBIC2333E
A : Left bank
B : Right bank
: Engine front
PBIC3300E
Page 3293 of 5621
![INFINITI M35 2006 Factory Manual Online EM-230
[VK45DE]
OIL SEAL
Revision: 2006 January2006 M35/M45
Removal and Installation of Front Oil SealNBS004PD
REMOVAL
1. Remove the following parts:
Front engine undercover (power tool)
Radiator; Ref INFINITI M35 2006 Factory Manual Online EM-230
[VK45DE]
OIL SEAL
Revision: 2006 January2006 M35/M45
Removal and Installation of Front Oil SealNBS004PD
REMOVAL
1. Remove the following parts:
Front engine undercover (power tool)
Radiator; Ref](/img/42/57023/w960_57023-3292.png)
EM-230
[VK45DE]
OIL SEAL
Revision: 2006 January2006 M35/M45
Removal and Installation of Front Oil SealNBS004PD
REMOVAL
1. Remove the following parts:
Front engine undercover (power tool)
Radiator; Refer to CO-43, "RADIATOR" .
Drive belt; Refer to EM-174, "DRIVE BELTS" .
Rear plate cover; Refer to EM-187, "OIL PAN AND OIL STRAINER" .
2. Remove crankshaft pulley as follows:
a. Set ring gear stopper (SST).
b. Loosen crankshaft pulley bolt, and then pull crankshaft pulley
with both hands to remove it.
CAUTION:
Do not remove crankshaft pulley bolt. Keep loosened
crankshaft pulley bolt in place to protect removed crank-
shaft pulley from dropping.
Do not remove balance weight (inner hexagon bolt) at the
front of crankshaft pulley.
3. Remove front oil seal using suitable tool.
CAUTION:
Be careful not to damage front cover and oil pump drive
spacer.
INSTALLATION
1. Apply new engine oil to both oil seal lip and dust seal lip of new front oil seal.
2. Install front oil seal.
PBIC1656E
SBIA0358E
SBIA0359E
Page 3308 of 5621
![INFINITI M35 2006 Factory Manual Online ENGINE ASSEMBLY
EM-245
[VK45DE]
C
D
E
F
G
H
I
J
K
L
MA
EM
Revision: 2006 January2006 M35/M45
Always use the support point specified for lifting.
Use either 2-pole lift type or separate type li INFINITI M35 2006 Factory Manual Online ENGINE ASSEMBLY
EM-245
[VK45DE]
C
D
E
F
G
H
I
J
K
L
MA
EM
Revision: 2006 January2006 M35/M45
Always use the support point specified for lifting.
Use either 2-pole lift type or separate type li](/img/42/57023/w960_57023-3307.png)
ENGINE ASSEMBLY
EM-245
[VK45DE]
C
D
E
F
G
H
I
J
K
L
MA
EM
Revision: 2006 January2006 M35/M45
Always use the support point specified for lifting.
Use either 2-pole lift type or separate type lift as best you can. If board-on type is used for
unavoidable reasons, support at the rear axle jacking point with transmission jack or similar tool
before starting work, in preparation for the backward shift of center of gravity.
For supporting points for lifting and jacking point at rear axle, refer to GI-42, "Garage Jack and
Safety Stand and 2-Pole Lift" .
REMOVAL
Outline
At first, remove engine, transmission assembly with front suspension member from vehicle downward. Then
separate engine from transmission.
Preparation
1. Release fuel pressure. Refer to EC-809, "FUEL PRESSURE RELEASE" .
2. Drain engine coolant from radiator. Refer to CO-40, "
Changing Engine Coolant" .
CAUTION:
Perform this step when engine is cold.
Do not spill engine coolant on drive belts.
3. Disconnect both battery cables. Refer to SC-4, "
BATTERY" .
4. Remove crankshaft position sensor (POS) from transmission.
CAUTION:
Handle carefully to avoid dropping and shocks.
Do not disassemble.
Do not allow metal powder to adhere to magnetic part at sensor tip.
Do not place sensors in a location where they are exposed to magnetism.
5. Remove the following parts:
Front and rear engine undercover (power tool)
Air duct (inlet), air duct and air cleaner case assembly; Refer to EM-177, "AIR CLEANER AND AIR
DUCT" .
Front road wheels and tires (power tool)
Engine Room LH
1. Disconnect heater hoses, and install plugs to avoid leakage of engine coolant.
2. Disconnect wire bonding from exhaust manifold cover to vehicle.
3. Disconnect vacuum hose between vehicle and engine and set it aside.
4. Discharge refrigerant from A/C circuit. Refer to ATC-151, "
REFRIGERANT LINES" .
5. Remove A/C piping from A/C compressor, and temporarily fasten it on vehicle with a rope. Refer to AT C -
151, "REFRIGERANT LINES" .
Engine Room RH
1. Disconnect fuel feed hose and EVAP hose. Refer to EM-193, "FUEL INJECTOR AND FUEL TUBE" .
CAUTION:
Fit plugs onto disconnected hose to prevent fuel leak.
2. Disconnect ground cable (between vehicle and right bank cylinder head).
3. Disconnect vacuum hose between vehicle and engine and set it aside.
4. Disconnect reservoir tank of power steering oil pump from engine, and move it aside for easier work.
CAUTION:
When temporarily securing, keep reservoir tank upright to avoid a fluid leak.
Ve h i c le i n s i d e
Follow procedure below to disconnect engine room harness connectors at passenger room side, and tempo-
rarily secure them on engine.
1. Remove passenger-side kicking plate, dash side finisher, and glove box. Refer to EI-37, "
BODY SIDE
TRIM" and IP-10, "INSTRUMENT PANEL ASSEMBLY" .
2. Disconnect engine room harness connectors at unit sides TCM, ECM and other.
Page 3468 of 5621
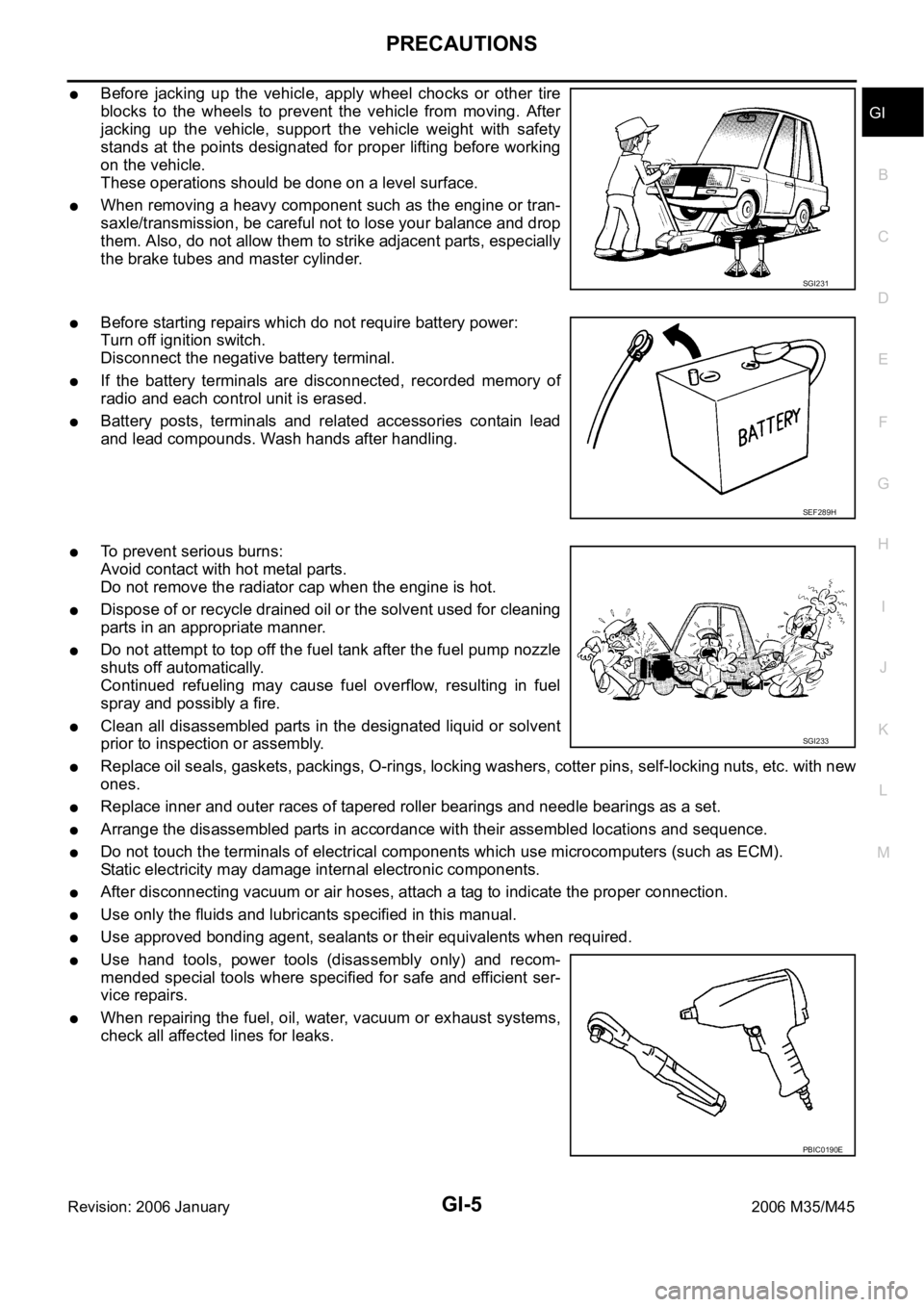
PRECAUTIONS
GI-5
C
D
E
F
G
H
I
J
K
L
MB
GI
Revision: 2006 January2006 M35/M45
Before jacking up the vehicle, apply wheel chocks or other tire
blocks to the wheels to prevent the vehicle from moving. After
jacking up the vehicle, support the vehicle weight with safety
stands at the points designated for proper lifting before working
on the vehicle.
These operations should be done on a level surface.
When removing a heavy component such as the engine or tran-
saxle/transmission, be careful not to lose your balance and drop
them. Also, do not allow them to strike adjacent parts, especially
the brake tubes and master cylinder.
Before starting repairs which do not require battery power:
Turn off ignition switch.
Disconnect the negative battery terminal.
If the battery terminals are disconnected, recorded memory of
radio and each control unit is erased.
Battery posts, terminals and related accessories contain lead
and lead compounds. Wash hands after handling.
To prevent serious burns:
Avoid contact with hot metal parts.
Do not remove the radiator cap when the engine is hot.
Dispose of or recycle drained oil or the solvent used for cleaning
parts in an appropriate manner.
Do not attempt to top off the fuel tank after the fuel pump nozzle
shuts off automatically.
Continued refueling may cause fuel overflow, resulting in fuel
spray and possibly a fire.
Clean all disassembled parts in the designated liquid or solvent
prior to inspection or assembly.
Replace oil seals, gaskets, packings, O-rings, locking washers, cotter pins, self-locking nuts, etc. with new
ones.
Replace inner and outer races of tapered roller bearings and needle bearings as a set.
Arrange the disassembled parts in accordance with their assembled locations and sequence.
Do not touch the terminals of electrical components which use microcomputers (such as ECM).
Static electricity may damage internal electronic components.
After disconnecting vacuum or air hoses, attach a tag to indicate the proper connection.
Use only the fluids and lubricants specified in this manual.
Use approved bonding agent, sealants or their equivalents when required.
Use hand tools, power tools (disassembly only) and recom-
mended special tools where specified for safe and efficient ser-
vice repairs.
When repairing the fuel, oil, water, vacuum or exhaust systems,
check all affected lines for leaks.
SGI231
SEF289H
SGI233
PBIC0190E
Page 3527 of 5621
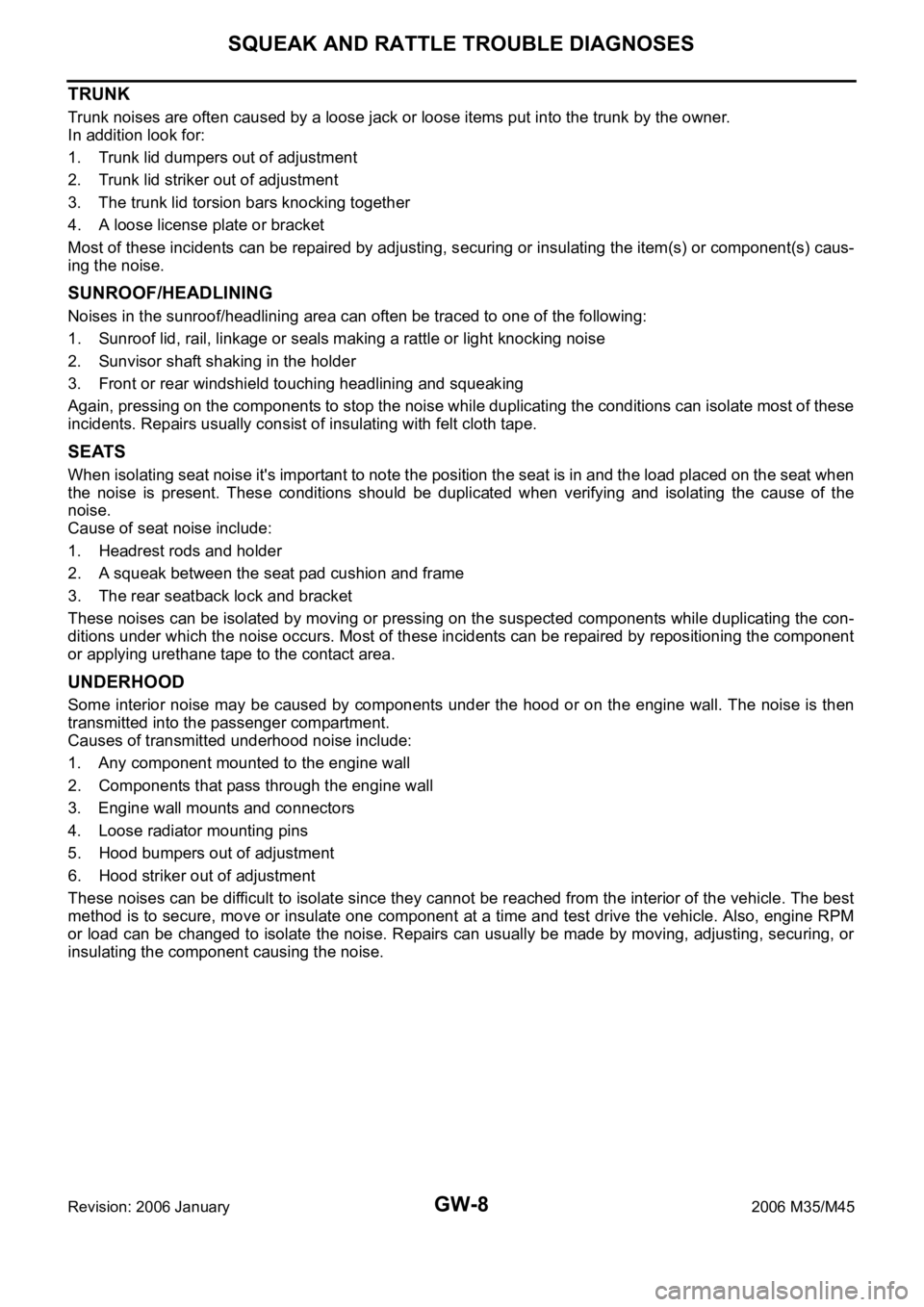
GW-8
SQUEAK AND RATTLE TROUBLE DIAGNOSES
Revision: 2006 January2006 M35/M45
TRUNK
Trunk noises are often caused by a loose jack or loose items put into the trunk by the owner.
In addition look for:
1. Trunk lid dumpers out of adjustment
2. Trunk lid striker out of adjustment
3. The trunk lid torsion bars knocking together
4. A loose license plate or bracket
Most of these incidents can be repaired by adjusting, securing or insulating the item(s) or component(s) caus-
ing the noise.
SUNROOF/HEADLINING
Noises in the sunroof/headlining area can often be traced to one of the following:
1. Sunroof lid, rail, linkage or seals making a rattle or light knocking noise
2. Sunvisor shaft shaking in the holder
3. Front or rear windshield touching headlining and squeaking
Again, pressing on the components to stop the noise while duplicating the conditions can isolate most of these
incidents. Repairs usually consist of insulating with felt cloth tape.
SEATS
When isolating seat noise it's important to note the position the seat is in and the load placed on the seat when
the noise is present. These conditions should be duplicated when verifying and isolating the cause of the
noise.
Cause of seat noise include:
1. Headrest rods and holder
2. A squeak between the seat pad cushion and frame
3. The rear seatback lock and bracket
These noises can be isolated by moving or pressing on the suspected components while duplicating the con-
ditions under which the noise occurs. Most of these incidents can be repaired by repositioning the component
or applying urethane tape to the contact area.
UNDERHOOD
Some interior noise may be caused by components under the hood or on the engine wall. The noise is then
transmitted into the passenger compartment.
Causes of transmitted underhood noise include:
1. Any component mounted to the engine wall
2. Components that pass through the engine wall
3. Engine wall mounts and connectors
4. Loose radiator mounting pins
5. Hood bumpers out of adjustment
6. Hood striker out of adjustment
These noises can be difficult to isolate since they cannot be reached from the interior of the vehicle. The best
method is to secure, move or insulate one component at a time and test drive the vehicle. Also, engine RPM
or load can be changed to isolate the noise. Repairs can usually be made by moving, adjusting, securing, or
insulating the component causing the noise.
Page 3647 of 5621
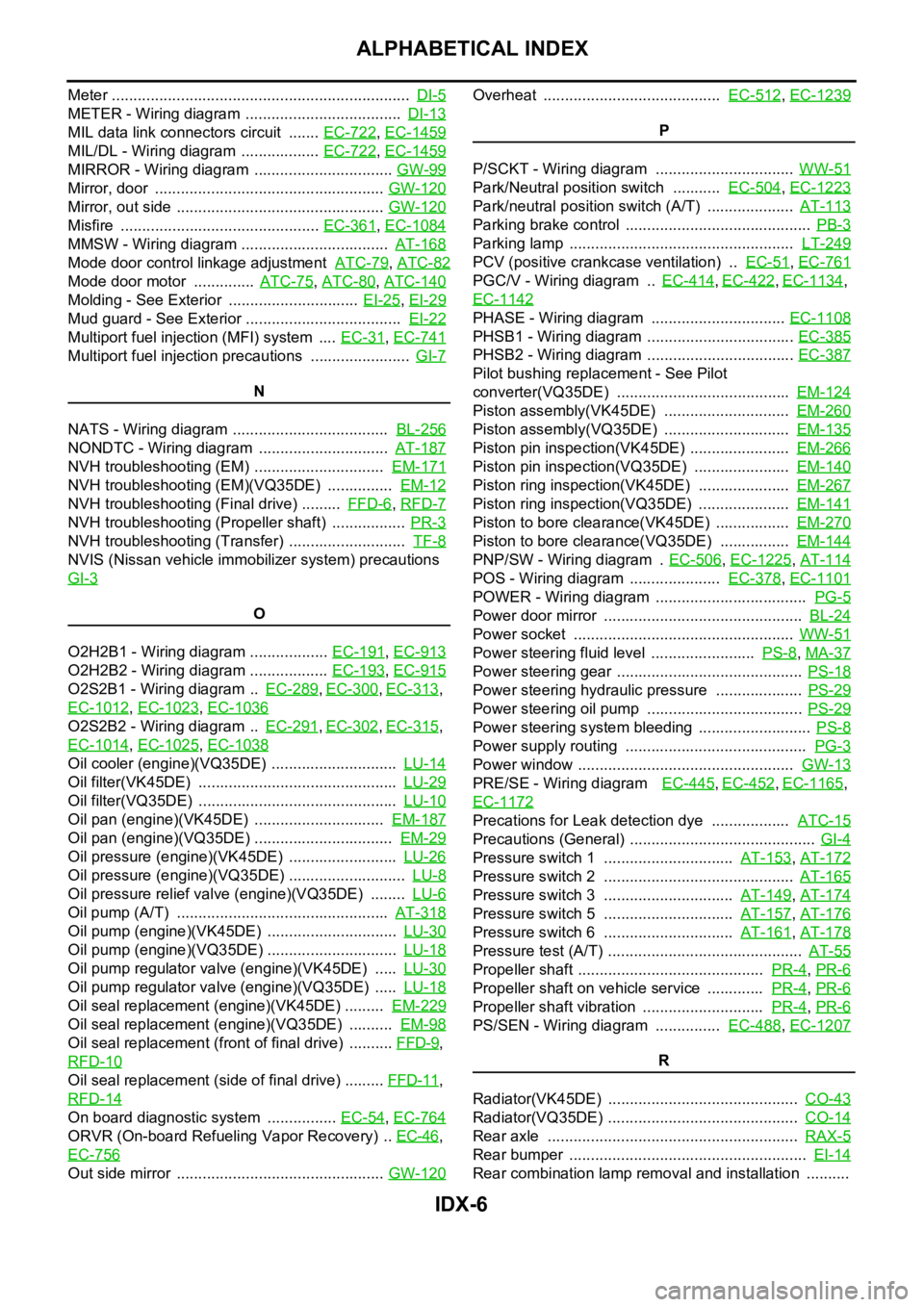
IDX-6
ALPHABETICAL INDEX
Meter ..................................................................... DI-5
METER - Wiring diagram .................................... DI-13
MIL data link connectors circuit ....... EC-722, EC-1459
MIL/DL - Wiring diagram .................. EC-722, EC-1459
MIRROR - Wiring diagram ................................ GW-99
Mirror, door ..................................................... GW-120
Mirror, out side ................................................ GW-120
Misfire .............................................. EC-361, EC-1084
MMSW - Wiring diagram .................................. AT-168
Mode door control linkage adjustment ATC-79, ATC-82
Mode door motor .............. ATC-75, ATC-80, ATC-140
Molding - See Exterior .............................. EI-25, EI-29
Mud guard - See Exterior .................................... EI-22
Multiport fuel injection (MFI) system .... EC-31, EC-741
Multiport fuel injection precautions ....................... GI-7
N
NATS - Wiring diagram .................................... BL-256
NONDTC - Wiring diagram .............................. AT-187
NVH troubleshooting (EM) .............................. EM-171
NVH troubleshooting (EM)(VQ35DE) ............... EM-12
NVH troubleshooting (Final drive) ......... FFD-6, RFD-7
NVH troubleshooting (Propeller shaft) ................. PR-3
NVH troubleshooting (Transfer) ........................... TF-8
NVIS (Nissan vehicle immobilizer system) precautions
GI-3
O
O2H2B1 - Wiring diagram .................. EC-191
, EC-913
O2H2B2 - Wiring diagram .................. EC-193, EC-915
O2S2B1 - Wiring diagram .. EC-289, EC-300, EC-313,
EC-1012
, EC-1023, EC-1036
O2S2B2 - Wiring diagram .. EC-291, EC-302, EC-315,
EC-1014
, EC-1025, EC-1038
Oil cooler (engine)(VQ35DE) ............................. LU-14
Oil filter(VK45DE) .............................................. LU-29
Oil filter(VQ35DE) .............................................. LU-10
Oil pan (engine)(VK45DE) .............................. EM-187
Oil pan (engine)(VQ35DE) ................................ EM-29
Oil pressure (engine)(VK45DE) ......................... LU-26
Oil pressure (engine)(VQ35DE) ........................... LU-8
Oil pressure relief valve (engine)(VQ35DE) ........ LU-6
Oil pump (A/T) ................................................. AT-318
Oil pump (engine)(VK45DE) .............................. LU-30
Oil pump (engine)(VQ35DE) .............................. LU-18
Oil pump regulator valve (engine)(VK45DE) ..... LU-30
Oil pump regulator valve (engine)(VQ35DE) ..... LU-18
Oil seal replacement (engine)(VK45DE) ......... EM-229
Oil seal replacement (engine)(VQ35DE) .......... EM-98
Oil seal replacement (front of final drive) .......... FFD-9,
RFD-10
Oil seal replacement (side of final drive) ......... FFD-11,
RFD-14
On board diagnostic system ................ EC-54, EC-764
ORVR (On-board Refueling Vapor Recovery) .. EC-46,
EC-756
Out side mirror ................................................ GW-120
Overheat ......................................... EC-512, EC-1239
P
P/SCKT - Wiring diagram ................................ WW-51
Park/Neutral position switch ........... EC-504, EC-1223
Park/neutral position switch (A/T) .................... AT-113
Parking brake control ........................................... PB-3
Parking lamp .................................................... LT-249
PCV (positive crankcase ventilation) .. EC-51, EC-761
PGC/V - Wiring diagram .. EC-414, EC-422, EC-1134,
EC-1142
PHASE - Wiring diagram ............................... EC-1108
PHSB1 - Wiring diagram .................................. EC-385
PHSB2 - Wiring diagram .................................. EC-387
Pilot bushing replacement - See Pilot
converter(VQ35DE) ........................................ EM-124
Piston assembly(VK45DE) ............................. EM-260
Piston assembly(VQ35DE) ............................. EM-135
Piston pin inspection(VK45DE) ....................... EM-266
Piston pin inspection(VQ35DE) ...................... EM-140
Piston ring inspection(VK45DE) ..................... EM-267
Piston ring inspection(VQ35DE) ..................... EM-141
Piston to bore clearance(VK45DE) ................. EM-270
Piston to bore clearance(VQ35DE) ................ EM-144
PNP/SW - Wiring diagram . EC-506, EC-1225, AT-114
POS - Wiring diagram ..................... EC-378, EC-1101
POWER - Wiring diagram ................................... PG-5
Power door mirror .............................................. BL-24
Power socket ................................................... WW-51
Power steering fluid level ........................ PS-8, MA-37
Power steering gear ........................................... PS-18
Power steering hydraulic pressure .................... PS-29
Power steering oil pump .................................... PS-29
Power steering system bleeding .......................... PS-8
Power supply routing .......................................... PG-3
Power window .................................................. GW-13
PRE/SE - Wiring diagram EC-445, EC-452, EC-1165,
EC-1172
Precations for Leak detection dye .................. ATC-15
Precautions (General) ........................................... GI-4
Pressure switch 1 .............................. AT-153, AT-172
Pressure switch 2 ............................................ AT-165
Pressure switch 3 .............................. AT-149, AT-174
Pressure switch 5 .............................. AT-157, AT-176
Pressure switch 6 .............................. AT-161, AT-178
Pressure test (A/T) ............................................. AT-55
Propeller shaft ........................................... PR-4, PR-6
Propeller shaft on vehicle service ............. PR-4, PR-6
Propeller shaft vibration ............................ PR-4, PR-6
PS/SEN - Wiring diagram ............... EC-488, EC-1207
R
Radiator(VK45DE) ............................................ CO-43
Radiator(VQ35DE) ............................................ CO-14
Rear axle .......................................................... RAX-5
Rear bumper ....................................................... EI-14
Rear combination lamp removal and installation ..........
Page 3656 of 5621
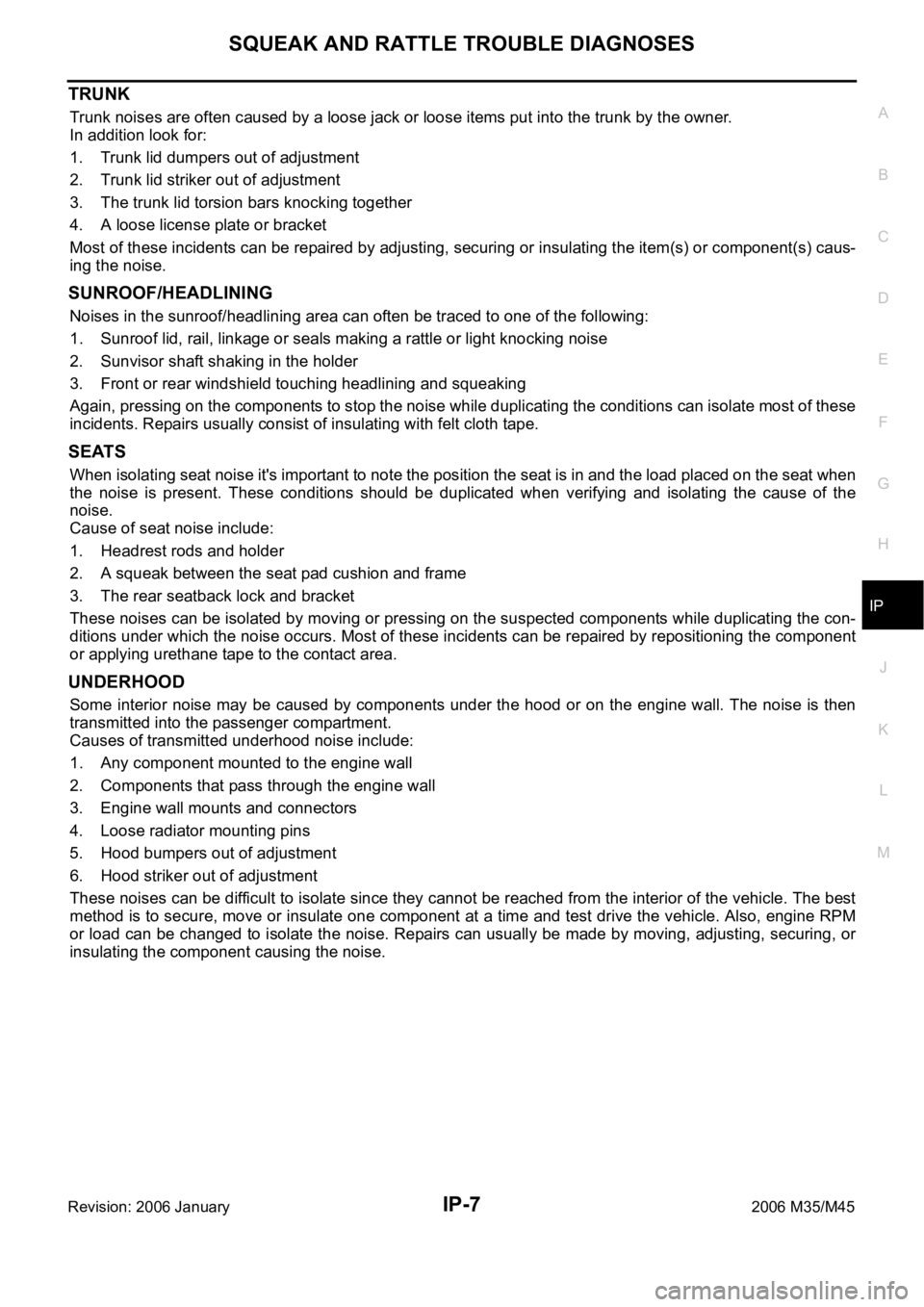
SQUEAK AND RATTLE TROUBLE DIAGNOSES
IP-7
C
D
E
F
G
H
J
K
L
MA
B
IP
Revision: 2006 January2006 M35/M45
TRUNK
Trunk noises are often caused by a loose jack or loose items put into the trunk by the owner.
In addition look for:
1. Trunk lid dumpers out of adjustment
2. Trunk lid striker out of adjustment
3. The trunk lid torsion bars knocking together
4. A loose license plate or bracket
Most of these incidents can be repaired by adjusting, securing or insulating the item(s) or component(s) caus-
ing the noise.
SUNROOF/HEADLINING
Noises in the sunroof/headlining area can often be traced to one of the following:
1. Sunroof lid, rail, linkage or seals making a rattle or light knocking noise
2. Sunvisor shaft shaking in the holder
3. Front or rear windshield touching headlining and squeaking
Again, pressing on the components to stop the noise while duplicating the conditions can isolate most of these
incidents. Repairs usually consist of insulating with felt cloth tape.
SEATS
When isolating seat noise it's important to note the position the seat is in and the load placed on the seat when
the noise is present. These conditions should be duplicated when verifying and isolating the cause of the
noise.
Cause of seat noise include:
1. Headrest rods and holder
2. A squeak between the seat pad cushion and frame
3. The rear seatback lock and bracket
These noises can be isolated by moving or pressing on the suspected components while duplicating the con-
ditions under which the noise occurs. Most of these incidents can be repaired by repositioning the component
or applying urethane tape to the contact area.
UNDERHOOD
Some interior noise may be caused by components under the hood or on the engine wall. The noise is then
transmitted into the passenger compartment.
Causes of transmitted underhood noise include:
1. Any component mounted to the engine wall
2. Components that pass through the engine wall
3. Engine wall mounts and connectors
4. Loose radiator mounting pins
5. Hood bumpers out of adjustment
6. Hood striker out of adjustment
These noises can be difficult to isolate since they cannot be reached from the interior of the vehicle. The best
method is to secure, move or insulate one component at a time and test drive the vehicle. Also, engine RPM
or load can be changed to isolate the noise. Repairs can usually be made by moving, adjusting, securing, or
insulating the component causing the noise.