fuel cap release INFINITI QX4 2005 Factory Service Manual
[x] Cancel search | Manufacturer: INFINITI, Model Year: 2005, Model line: QX4, Model: INFINITI QX4 2005Pages: 3419, PDF Size: 80.18 MB
Page 1226 of 3419
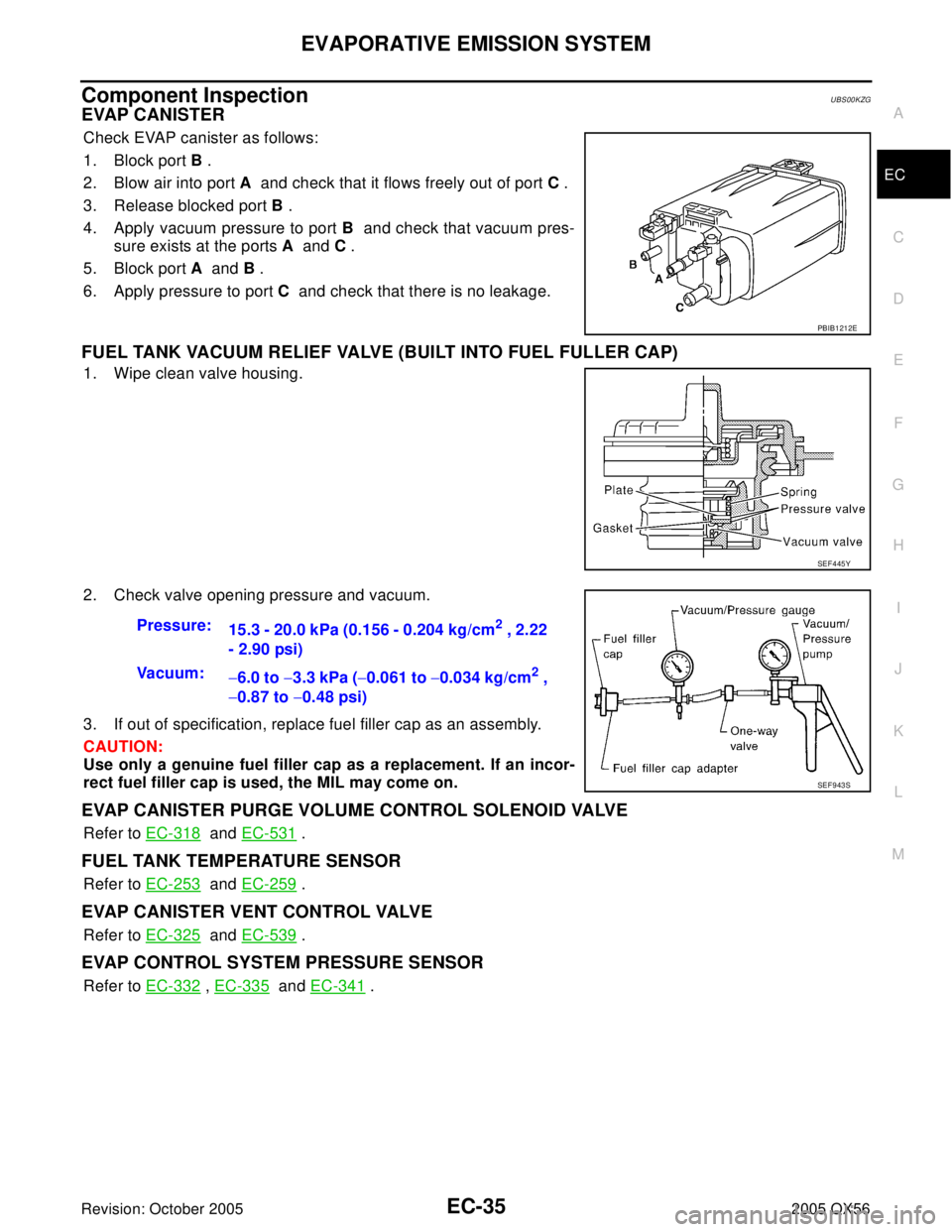
EVAPORATIVE EMISSION SYSTEM
EC-35
C
D
E
F
G
H
I
J
K
L
MA
EC
Revision: October 20052005 QX56
Component InspectionUBS00KZG
EVAP CANISTER
Check EVAP canister as follows:
1. Block port B .
2. Blow air into port A and check that it flows freely out of port C .
3. Release blocked port B .
4. Apply vacuum pressure to port B and check that vacuum pres-
sure exists at the ports A and C .
5. Block port A and B .
6. Apply pressure to port C and check that there is no leakage.
FUEL TANK VACUUM RELIEF VALVE (BUILT INTO FUEL FULLER CAP)
1. Wipe clean valve housing.
2. Check valve opening pressure and vacuum.
3. If out of specification, replace fuel filler cap as an assembly.
CAUTION:
Use only a genuine fuel filler cap as a replacement. If an incor-
rect fuel filler cap is used, the MIL may come on.
EVAP CANISTER PURGE VOLUME CONTROL SOLENOID VALVE
Refer to EC-318 and EC-531 .
FUEL TANK TEMPERATURE SENSOR
Refer to EC-253 and EC-259 .
EVAP CANISTER VENT CONTROL VALVE
Refer to EC-325 and EC-539 .
EVAP CONTROL SYSTEM PRESSURE SENSOR
Refer to EC-332 , EC-335 and EC-341 .
PBIB1212E
SEF 4 45 Y
Pressure:
15.3 - 20.0 kPa (0.156 - 0.204 kg/cm2 , 2.22
- 2.90 psi)
Va c u u m :
−6.0 to −3.3 kPa (−0.061 to −0.034 kg/cm
2 ,
−0.87 to −0.48 psi)
SEF 9 43 S
Page 1906 of 3419
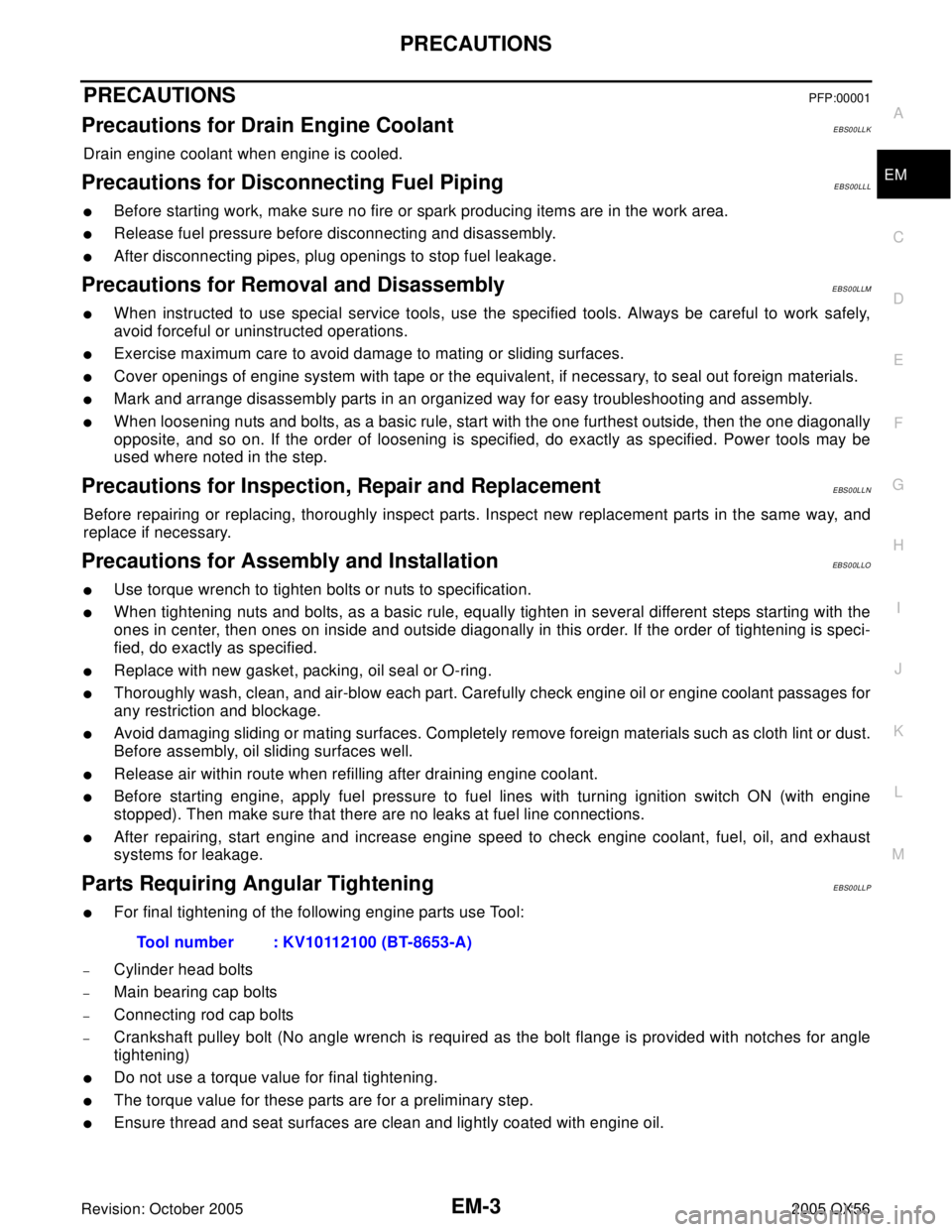
PRECAUTIONS
EM-3
C
D
E
F
G
H
I
J
K
L
MA
EM
Revision: October 20052005 QX56
PRECAUTIONSPFP:00001
Precautions for Drain Engine CoolantEBS00LLK
Drain engine coolant when engine is cooled.
Precautions for Disconnecting Fuel PipingEBS00LLL
Before starting work, make sure no fire or spark producing items are in the work area.
Release fuel pressure before disconnecting and disassembly.
After disconnecting pipes, plug openings to stop fuel leakage.
Precautions for Removal and DisassemblyEBS00LLM
When instructed to use special service tools, use the specified tools. Always be careful to work safely,
avoid forceful or uninstructed operations.
Exercise maximum care to avoid damage to mating or sliding surfaces.
Cover openings of engine system with tape or the equivalent, if necessary, to seal out foreign materials.
Mark and arrange disassembly parts in an organized way for easy troubleshooting and assembly.
When loosening nuts and bolts, as a basic rule, start with the one furthest outside, then the one diagonally
opposite, and so on. If the order of loosening is specified, do exactly as specified. Power tools may be
used where noted in the step.
Precautions for Inspection, Repair and ReplacementEBS00LLN
Before repairing or replacing, thoroughly inspect parts. Inspect new replacement parts in the same way, and
replace if necessary.
Precautions for Assembly and InstallationEBS00LLO
Use torque wrench to tighten bolts or nuts to specification.
When tightening nuts and bolts, as a basic rule, equally tighten in several different steps starting with the
ones in center, then ones on inside and outside diagonally in this order. If the order of tightening is speci-
fied, do exactly as specified.
Replace with new gasket, packing, oil seal or O-ring.
Thoroughly wash, clean, and air-blow each part. Carefully check engine oil or engine coolant passages for
any restriction and blockage.
Avoid damaging sliding or mating surfaces. Completely remove foreign materials such as cloth lint or dust.
Before assembly, oil sliding surfaces well.
Release air within route when refilling after draining engine coolant.
Before starting engine, apply fuel pressure to fuel lines with turning ignition switch ON (with engine
stopped). Then make sure that there are no leaks at fuel line connections.
After repairing, start engine and increase engine speed to check engine coolant, fuel, oil, and exhaust
systems for leakage.
Parts Requiring Angular TighteningEBS00LLP
For final tightening of the following engine parts use Tool:
–Cylinder head bolts
–Main bearing cap bolts
–Connecting rod cap bolts
–Crankshaft pulley bolt (No angle wrench is required as the bolt flange is provided with notches for angle
tightening)
Do not use a torque value for final tightening.
The torque value for these parts are for a preliminary step.
Ensure thread and seat surfaces are clean and lightly coated with engine oil. Tool number : KV10112100 (BT-8653-A)
Page 1932 of 3419
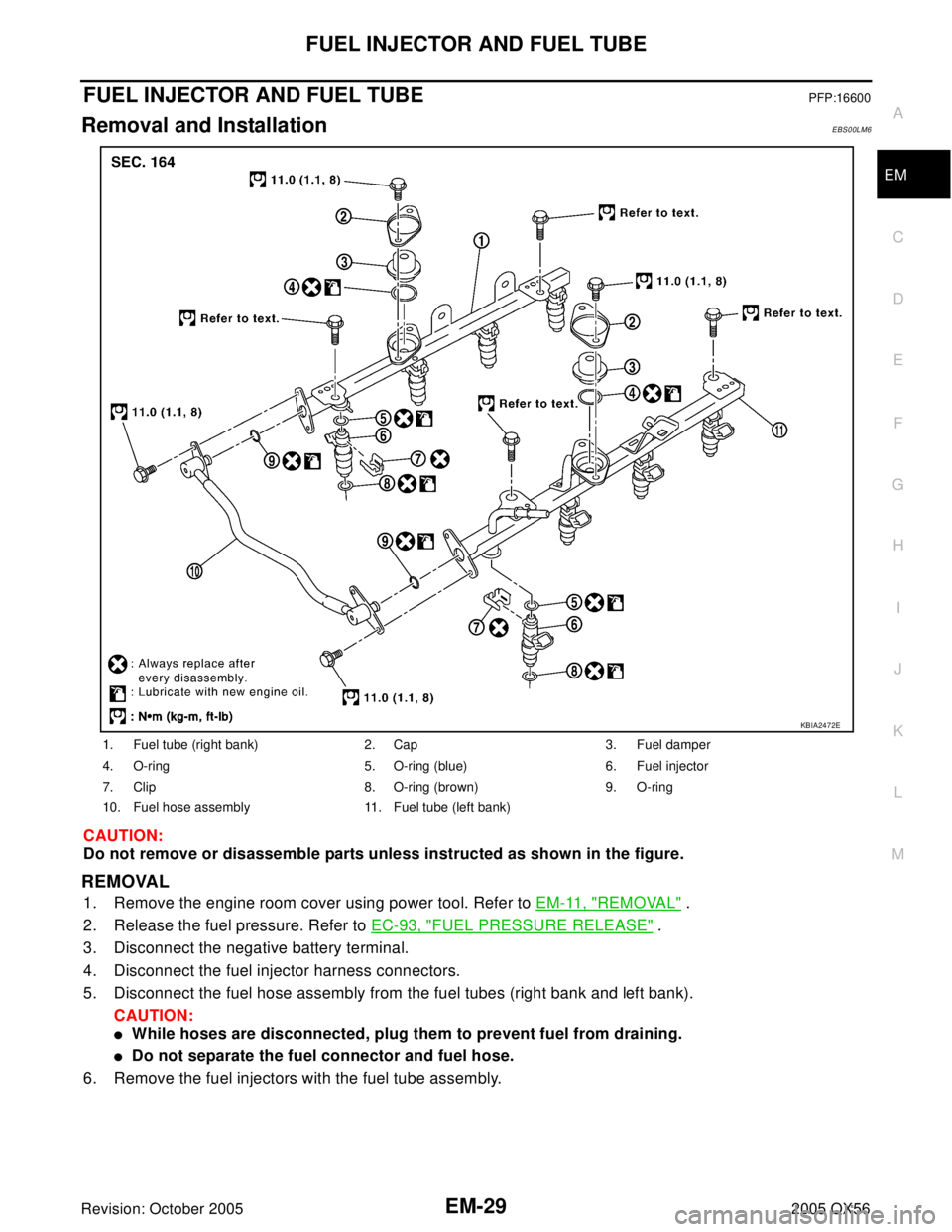
FUEL INJECTOR AND FUEL TUBE
EM-29
C
D
E
F
G
H
I
J
K
L
MA
EM
Revision: October 20052005 QX56
FUEL INJECTOR AND FUEL TUBEPFP:16600
Removal and InstallationEBS00LM6
CAUTION:
Do not remove or disassemble parts unless instructed as shown in the figure.
REMOVAL
1. Remove the engine room cover using power tool. Refer to EM-11, "REMOVAL" .
2. Release the fuel pressure. Refer to EC-93, "
FUEL PRESSURE RELEASE" .
3. Disconnect the negative battery terminal.
4. Disconnect the fuel injector harness connectors.
5. Disconnect the fuel hose assembly from the fuel tubes (right bank and left bank).
CAUTION:
While hoses are disconnected, plug them to prevent fuel from draining.
Do not separate the fuel connector and fuel hose.
6. Remove the fuel injectors with the fuel tube assembly.
1. Fuel tube (right bank) 2. Cap 3. Fuel damper
4. O-ring 5. O-ring (blue) 6. Fuel injector
7. Clip 8. O-ring (brown) 9. O-ring
10. Fuel hose assembly 11. Fuel tube (left bank)
KBIA2472E
Page 2068 of 3419
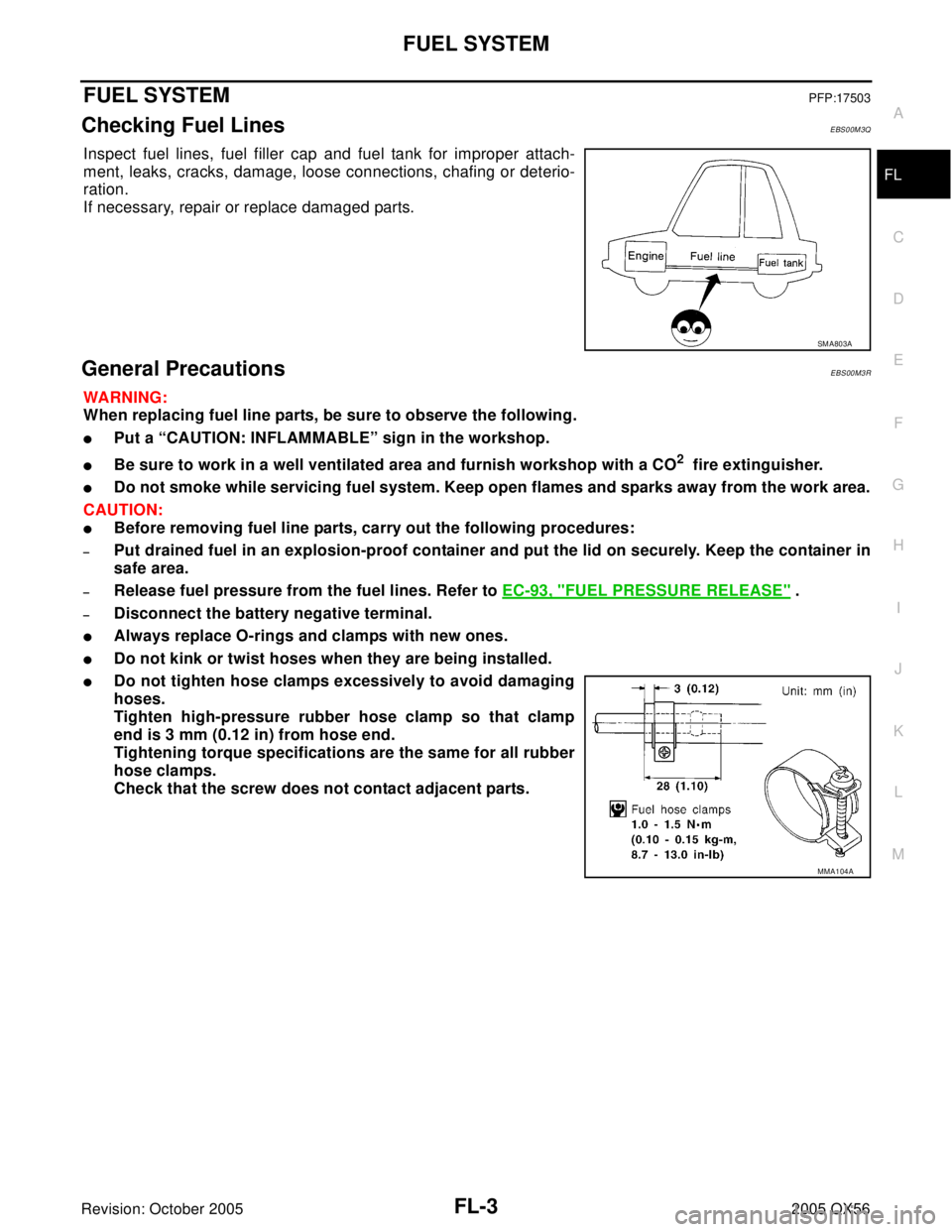
FUEL SYSTEM
FL-3
C
D
E
F
G
H
I
J
K
L
MA
FL
Revision: October 20052005 QX56
FUEL SYSTEMPFP:17503
Checking Fuel LinesEBS00M3Q
Inspect fuel lines, fuel filler cap and fuel tank for improper attach-
ment, leaks, cracks, damage, loose connections, chafing or deterio-
ration.
If necessary, repair or replace damaged parts.
General PrecautionsEBS00M3R
WA RN ING:
When replacing fuel line parts, be sure to observe the following.
Put a “CAUTION: INFLAMMABLE” sign in the workshop.
Be sure to work in a well ventilated area and furnish workshop with a CO2 fire extinguisher.
Do not smoke while servicing fuel system. Keep open flames and sparks away from the work area.
CAUTION:
Before removing fuel line parts, carry out the following procedures:
–Put drained fuel in an explosion-proof container and put the lid on securely. Keep the container in
safe area.
–Release fuel pressure from the fuel lines. Refer to EC-93, "FUEL PRESSURE RELEASE" .
–Disconnect the battery negative terminal.
Always replace O-rings and clamps with new ones.
Do not kink or twist hoses when they are being installed.
Do not tighten hose clamps excessively to avoid damaging
hoses.
Tighten high-pressure rubber hose clamp so that clamp
end is 3 mm (0.12 in) from hose end.
Tightening torque specifications are the same for all rubber
hose clamps.
Check that the screw does not contact adjacent parts.
SM A80 3A
MMA104A
Page 2070 of 3419
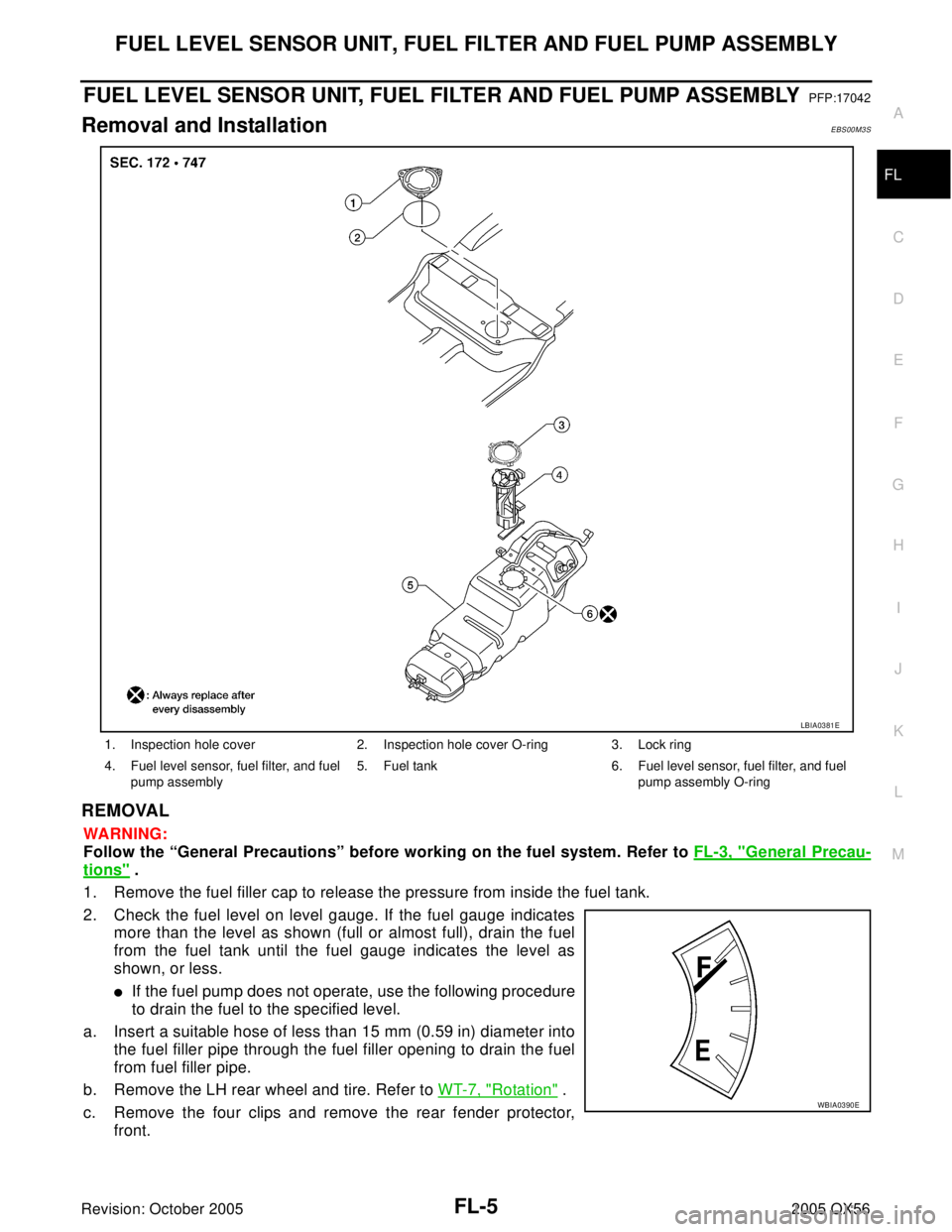
FUEL LEVEL SENSOR UNIT, FUEL FILTER AND FUEL PUMP ASSEMBLY
FL-5
C
D
E
F
G
H
I
J
K
L
MA
FL
Revision: October 20052005 QX56
FUEL LEVEL SENSOR UNIT, FUEL FILTER AND FUEL PUMP ASSEMBLYPFP:17042
Removal and InstallationEBS00M3S
REMOVAL
WA RN ING:
Follow the “General Precautions” before working on the fuel system. Refer to FL-3, "
General Precau-
tions" .
1. Remove the fuel filler cap to release the pressure from inside the fuel tank.
2. Check the fuel level on level gauge. If the fuel gauge indicates
more than the level as shown (full or almost full), drain the fuel
from the fuel tank until the fuel gauge indicates the level as
shown, or less.
If the fuel pump does not operate, use the following procedure
to drain the fuel to the specified level.
a. Insert a suitable hose of less than 15 mm (0.59 in) diameter into
the fuel filler pipe through the fuel filler opening to drain the fuel
from fuel filler pipe.
b. Remove the LH rear wheel and tire. Refer to WT-7, "
Rotation" .
c. Remove the four clips and remove the rear fender protector,
front.
1. Inspection hole cover 2. Inspection hole cover O-ring 3. Lock ring
4. Fuel level sensor, fuel filter, and fuel
pump assembly5. Fuel tank 6. Fuel level sensor, fuel filter, and fuel
pump assembly O-ring
LBIA0381E
WBIA0390E
Page 2075 of 3419
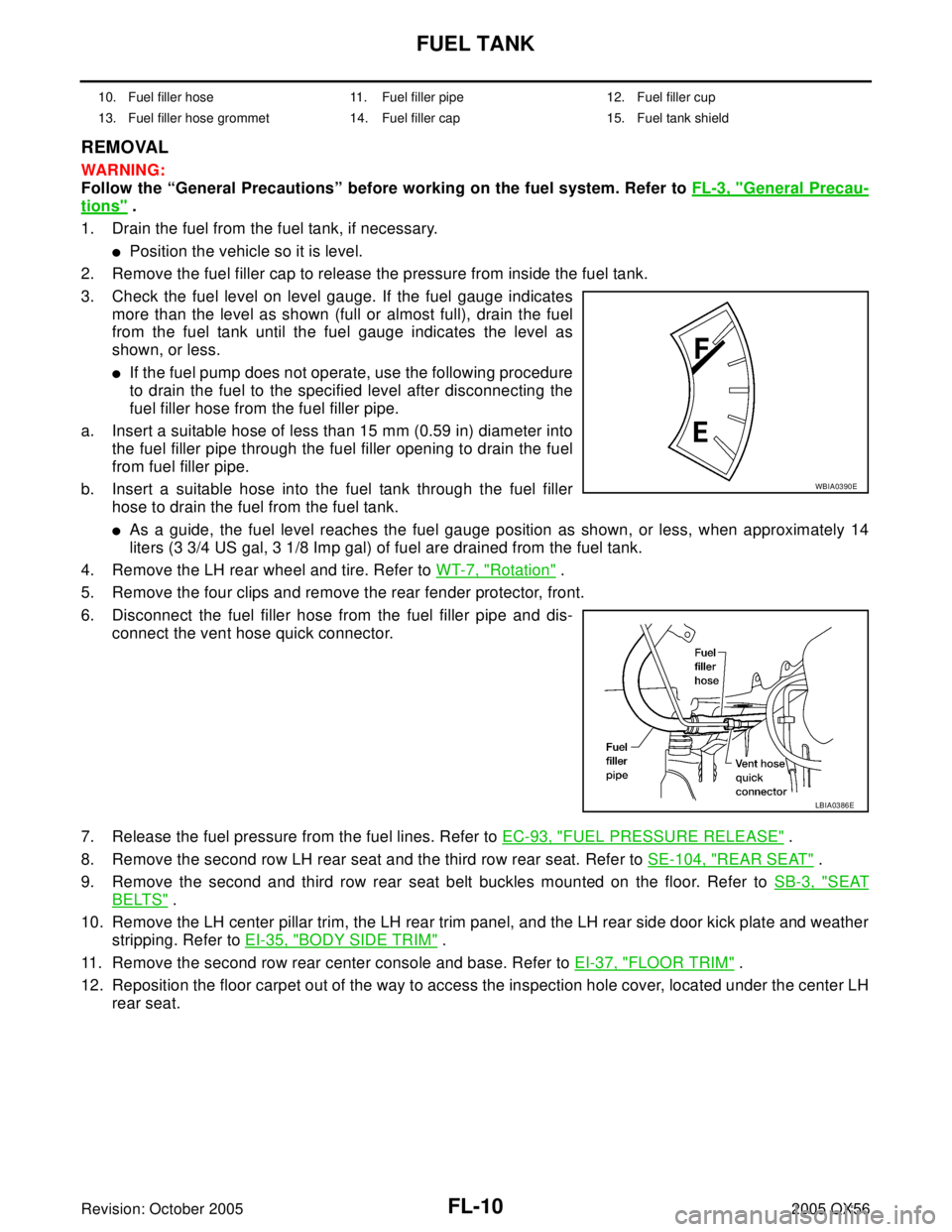
FL-10Revision: October 2005
FUEL TANK
2005 QX56
REMOVAL
WAR NIN G:
Follow the “General Precautions” before working on the fuel system. Refer to FL-3, "
General Precau-
tions" .
1. Drain the fuel from the fuel tank, if necessary.
Position the vehicle so it is level.
2. Remove the fuel filler cap to release the pressure from inside the fuel tank.
3. Check the fuel level on level gauge. If the fuel gauge indicates
more than the level as shown (full or almost full), drain the fuel
from the fuel tank until the fuel gauge indicates the level as
shown, or less.
If the fuel pump does not operate, use the following procedure
to drain the fuel to the specified level after disconnecting the
fuel filler hose from the fuel filler pipe.
a. Insert a suitable hose of less than 15 mm (0.59 in) diameter into
the fuel filler pipe through the fuel filler opening to drain the fuel
from fuel filler pipe.
b. Insert a suitable hose into the fuel tank through the fuel filler
hose to drain the fuel from the fuel tank.
As a guide, the fuel level reaches the fuel gauge position as shown, or less, when approximately 14
liters (3 3/4 US gal, 3 1/8 Imp gal) of fuel are drained from the fuel tank.
4. Remove the LH rear wheel and tire. Refer to WT-7, "
Rotation" .
5. Remove the four clips and remove the rear fender protector, front.
6. Disconnect the fuel filler hose from the fuel filler pipe and dis-
connect the vent hose quick connector.
7. Release the fuel pressure from the fuel lines. Refer to EC-93, "
FUEL PRESSURE RELEASE" .
8. Remove the second row LH rear seat and the third row rear seat. Refer to SE-104, "
REAR SEAT" .
9. Remove the second and third row rear seat belt buckles mounted on the floor. Refer to SB-3, "
SEAT
BELTS" .
10. Remove the LH center pillar trim, the LH rear trim panel, and the LH rear side door kick plate and weather
stripping. Refer to EI-35, "
BODY SIDE TRIM" .
11. Remove the second row rear center console and base. Refer to EI-37, "
FLOOR TRIM" .
12. Reposition the floor carpet out of the way to access the inspection hole cover, located under the center LH
rear seat.
10. Fuel filler hose 11. Fuel filler pipe 12. Fuel filler cup
13. Fuel filler hose grommet 14. Fuel filler cap 15. Fuel tank shield
WBIA0390E
LBIA0386E
Page 2902 of 3419
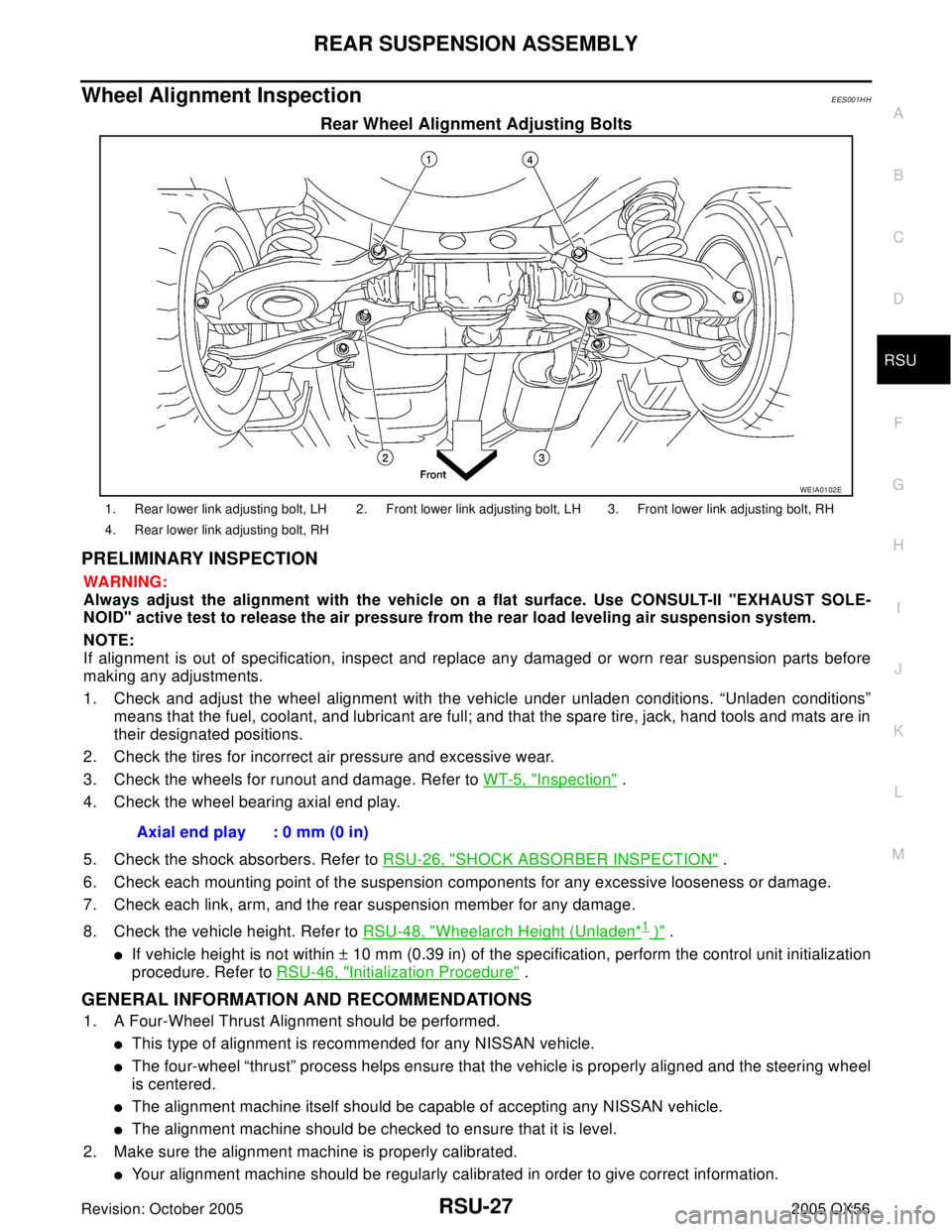
REAR SUSPENSION ASSEMBLY
RSU-27
C
D
F
G
H
I
J
K
L
MA
B
RSU
Revision: October 20052005 QX56
Wheel Alignment InspectionEES001HH
Rear Wheel Alignment Adjusting Bolts
PRELIMINARY INSPECTION
WA RN ING:
Always adjust the alignment with the vehicle on a flat surface. Use CONSULT-II "EXHAUST SOLE-
NOID" active test to release the air pressure from the rear load leveling air suspension system.
NOTE:
If alignment is out of specification, inspect and replace any damaged or worn rear suspension parts before
making any adjustments.
1. Check and adjust the wheel alignment with the vehicle under unladen conditions. “Unladen conditions”
means that the fuel, coolant, and lubricant are full; and that the spare tire, jack, hand tools and mats are in
their designated positions.
2. Check the tires for incorrect air pressure and excessive wear.
3. Check the wheels for runout and damage. Refer to WT-5, "
Inspection" .
4. Check the wheel bearing axial end play.
5. Check the shock absorbers. Refer to RSU-26, "
SHOCK ABSORBER INSPECTION" .
6. Check each mounting point of the suspension components for any excessive looseness or damage.
7. Check each link, arm, and the rear suspension member for any damage.
8. Check the vehicle height. Refer to RSU-48, "
Wheelarch Height (Unladen*1 )" .
If vehicle height is not within ± 10 mm (0.39 in) of the specification, perform the control unit initialization
procedure. Refer to RSU-46, "
Initialization Procedure" .
GENERAL INFORMATION AND RECOMMENDATIONS
1. A Four-Wheel Thrust Alignment should be performed.
This type of alignment is recommended for any NISSAN vehicle.
The four-wheel “thrust” process helps ensure that the vehicle is properly aligned and the steering wheel
is centered.
The alignment machine itself should be capable of accepting any NISSAN vehicle.
The alignment machine should be checked to ensure that it is level.
2. Make sure the alignment machine is properly calibrated.
Your alignment machine should be regularly calibrated in order to give correct information.
WEIA0102E
1. Rear lower link adjusting bolt, LH 2. Front lower link adjusting bolt, LH 3. Front lower link adjusting bolt, RH
4. Rear lower link adjusting bolt, RH
Axial end play : 0 mm (0 in)