torque INFINITI QX56 2008 Factory Manual PDF
[x] Cancel search | Manufacturer: INFINITI, Model Year: 2008, Model line: QX56, Model: INFINITI QX56 2008Pages: 4083, PDF Size: 81.73 MB
Page 1297 of 4083
![INFINITI QX56 2008 Factory Manual PDF REAR FINAL DRIVEDLN-267
< DISASSEMBLY AND ASSEMBLY > [REAR FINAL DRIVE: R230]
C
EF
G H
I
J
K L
M A
B
DLN
N
O P
17. Apply a 3.2mm (0.126 in) bead of sealant to the mating surface of the carrier cover.
INFINITI QX56 2008 Factory Manual PDF REAR FINAL DRIVEDLN-267
< DISASSEMBLY AND ASSEMBLY > [REAR FINAL DRIVE: R230]
C
EF
G H
I
J
K L
M A
B
DLN
N
O P
17. Apply a 3.2mm (0.126 in) bead of sealant to the mating surface of the carrier cover.](/img/42/57030/w960_57030-1296.png)
REAR FINAL DRIVEDLN-267
< DISASSEMBLY AND ASSEMBLY > [REAR FINAL DRIVE: R230]
C
EF
G H
I
J
K L
M A
B
DLN
N
O P
17. Apply a 3.2mm (0.126 in) bead of sealant to the mating surface of the carrier cover.
• Use Genuine Silicone RTV or equivalent. Refer to GI-15,
"Recommended Chemical Products and Sealants".
CAUTION:
Remove any old sealant adheri ng to the mating surfaces.
Also remove any moisture, oil, or foreign material adhering
to the application and mating surfaces.
18. Install the carrier cover to the gear carrier. Tighten the bolts to the specified torque. Refer to "COMPONENTS".
19. Install the side flange. Refer to "Side Flange".
Side Flange
1. Apply multi-purpose grease to the lips of the new side oil seal. Then drive the new side oil seal in evenly until it becomes flush
with the gear carrier using Tool.
CAUTION:
• Do not reuse side oil seal.
• Do not incline the new side oil seal when installing.
• Apply multi-purpose grease to the lips of the new side oil seal.
2. Install the side flange using Tool.
a. Install the Tool to the side oil seal as shown.
b. Insert the side flange until the serrated part of the side flange has engaged the serrated part of the side gear and remove the
Tool.
c. Drive in the side flange using suitable tool. NOTE:
Installation is completed when the driving sound of the side
flange turns into a sound which seems to affect the whole rear
final drive assembly.
WDIA0282E
Tool number : ST35271000 ( — )
SPD560
Tool number : KV38107900 (J-39352)
SDIA0822E
Revision: March 2010 2008 QX56
Page 1298 of 4083
![INFINITI QX56 2008 Factory Manual PDF DLN-268
< SERVICE DATA AND SPECIFICATIONS (SDS) [REAR FINAL DRIVE: R230]
SERVICE DATA AND SPECIFICATIONS (SDS)
SERVICE DATA AND SPECIFICATIONS (SDS)
SERVICE DATA AND SPECIFICATIONS (SDS)
General Speci INFINITI QX56 2008 Factory Manual PDF DLN-268
< SERVICE DATA AND SPECIFICATIONS (SDS) [REAR FINAL DRIVE: R230]
SERVICE DATA AND SPECIFICATIONS (SDS)
SERVICE DATA AND SPECIFICATIONS (SDS)
SERVICE DATA AND SPECIFICATIONS (SDS)
General Speci](/img/42/57030/w960_57030-1297.png)
DLN-268
< SERVICE DATA AND SPECIFICATIONS (SDS) [REAR FINAL DRIVE: R230]
SERVICE DATA AND SPECIFICATIONS (SDS)
SERVICE DATA AND SPECIFICATIONS (SDS)
SERVICE DATA AND SPECIFICATIONS (SDS)
General SpecificationINFOID:0000000001604464
Inspection and AdjustmentINFOID:0000000001604465
DRIVE GEAR RUNOUT
Unit: mm (in)
SIDE GEAR CLEARANCE
Unit: mm (in)
PRELOAD TORQUE
Unit: N·m (kg-m, in-lb)
BACKLASH
Unit: mm (in)
COMPANION FLANGE RUNOUT
Unit: mm (in)
SELECTIVE PARTS
Applied model 4WD
VK56DE A/T
SE LE, SE*
Final drive model R230
Gear ratio 2.9373.357
Number of teeth (Drive gear/Drive pinion) 47 / 1647/14
Oil capacity (Approx.) 1.75 (3 3/4 US pt, 3 1/8 Imp pt)
Number of pinion gears 2
Drive pinion adjustment spacer type Collapsible
ItemRunout limit
Drive gear back face 0.05 (0.0020) or less
ItemSpecification
Side gear back clearance
(Clearance limit between side gear and differential case for adjusting
side gear backlash) 0.20 (0.0079) or less
(Each gear should rotate smoothly without excessive resis- tance during differential motion.)
Item Specification
Drive pinion bearing preload torque 1.77 − 2.64 N·m (0.18 − 0.26 kg−m, 16 − 23 in-lb)
Side bearing preload torque (reference value determined by drive
gear bolt pulling force) 0.20
− 0.52 N·m (0.02 − 0.05 kg −m, 2 − 4 in-lb)
Drive gear bolt pulling force (by spring gauge) 34.2 − 39.2 N (3.5 − 4.0 kg, 7.7 − 8.8 lb)
Total preload torque
(Total preload torque = drive pinion bearing preload torque + Side
bearing preload torque) 2.05
− 4.11 N·m (0.21 − 0.42 kg−m, 19 − 36 in-lb)
Item Specification
Drive gear to drive pinion gear 0.13 − 0.18 (0.0051 − 0.0070)
Item Runout limit
Outer side of the companion flange 0.08 (0.0031) or less
Revision: March 2010 2008 QX56
Page 1339 of 4083
![INFINITI QX56 2008 Factory Manual PDF EC-40
< FUNCTION DIAGNOSIS >[VK56DE]
INTAKE VALVE TIMING CONTROL
INTAKE VALVE TIMING CONTROL
DescriptionINFOID:0000000001351376
SYSTEM DESCRIPTION
*: This signal is sent to the ECM through CAN communi INFINITI QX56 2008 Factory Manual PDF EC-40
< FUNCTION DIAGNOSIS >[VK56DE]
INTAKE VALVE TIMING CONTROL
INTAKE VALVE TIMING CONTROL
DescriptionINFOID:0000000001351376
SYSTEM DESCRIPTION
*: This signal is sent to the ECM through CAN communi](/img/42/57030/w960_57030-1338.png)
EC-40
< FUNCTION DIAGNOSIS >[VK56DE]
INTAKE VALVE TIMING CONTROL
INTAKE VALVE TIMING CONTROL
DescriptionINFOID:0000000001351376
SYSTEM DESCRIPTION
*: This signal is sent to the ECM through CAN communication line
This mechanism hydraulically controls cam phases c
ontinuously with the fixed operating angle of the intake
valve.
The ECM receives signals such as crankshaft posit ion, camshaft position, engine speed, and engine coolant
temperature. Then, the ECM sends ON/OFF pulse duty si gnals to the intake valve timing (IVT) control sole-
noid valve depending on driving status. This makes it po ssible to control the shut/open timing of the intake
valve to increase engine torque in low/mid speed range and output in high-speed range.
Sensor Input signal to ECM function ECMActuator
Crankshaft position sensor (POS)
Camshaft position sensor (PHASE) Engine speed
Intake valve
timing controlIntake valve timing control
solenoid valve
Intake valve timing control position sensor Intake valve timing signal
Engine coolant temperature sensor
Engine coolant temperature
Wheel sensor Vehicle speed*
PBIB3276E
Revision: March 2010 2008 QX56
Page 1454 of 4083
![INFINITI QX56 2008 Factory Manual PDF P0133, P0153 A/F SENSOR 1EC-155
< COMPONENT DIAGNOSIS > [VK56DE]
C
D
E
F
G H
I
J
K L
M A
EC
NP
O
Refer to
EC-86, "Ground Inspection".
OK or NG
OK >> GO TO 2.
NG >> Repair or replace ground connection INFINITI QX56 2008 Factory Manual PDF P0133, P0153 A/F SENSOR 1EC-155
< COMPONENT DIAGNOSIS > [VK56DE]
C
D
E
F
G H
I
J
K L
M A
EC
NP
O
Refer to
EC-86, "Ground Inspection".
OK or NG
OK >> GO TO 2.
NG >> Repair or replace ground connection](/img/42/57030/w960_57030-1453.png)
P0133, P0153 A/F SENSOR 1EC-155
< COMPONENT DIAGNOSIS > [VK56DE]
C
D
E
F
G H
I
J
K L
M A
EC
NP
O
Refer to
EC-86, "Ground Inspection".
OK or NG
OK >> GO TO 2.
NG >> Repair or replace ground connections.
2.RETIGHTEN A/F SENSOR 1
Loosen and retighten the A/F sensor 1.
>> GO TO 3.
3.CHECK EXHAUST GAS LEAK
1. Start engine and run it at idle.
2. Listen for an exhaust gas leak before three way catalyst (manifold).
OK or NG
OK >> GO TO 4.
NG >> Repair or replace.
4.CHECK FOR INTAKE AIR LEAK
Listen for an intake air leak after the mass air flow sensor.
OK or NG
OK >> GO TO 5.
NG >> Repair or replace.
5.CLEAR THE SELF-LEARNING DATA
With CONSULT-III
1. Start engine and warm it up to normal operating temperature.
BBIA0354E
Tightening torque: 50 N-m (5.1 kg-m, 37 ft-lb)
BBIA0375E
PBIB1216E
Revision: March 2010 2008 QX56
Page 1685 of 4083
![INFINITI QX56 2008 Factory Manual PDF EC-386
< COMPONENT DIAGNOSIS >[VK56DE]
P2A00, P2A03 A/F SENSOR 1
8. Keep engine speed between 2,500 and 3,000 rpm for 20 minutes.
9. Check 1st trip DTC.
10. If 1st trip DTC is detected, go to
EC-386, INFINITI QX56 2008 Factory Manual PDF EC-386
< COMPONENT DIAGNOSIS >[VK56DE]
P2A00, P2A03 A/F SENSOR 1
8. Keep engine speed between 2,500 and 3,000 rpm for 20 minutes.
9. Check 1st trip DTC.
10. If 1st trip DTC is detected, go to
EC-386,](/img/42/57030/w960_57030-1684.png)
EC-386
< COMPONENT DIAGNOSIS >[VK56DE]
P2A00, P2A03 A/F SENSOR 1
8. Keep engine speed between 2,500 and 3,000 rpm for 20 minutes.
9. Check 1st trip DTC.
10. If 1st trip DTC is detected, go to
EC-386, "
Diagnosis Procedure".
WITH GST
1. Start engine and warm it up to normal operating temperature.
2. Turn ignition switch OFF and wait at least 10 seconds.
3. Disconnect mass air flow sensor harness connector.
4. Start engine and let it idle for at least 5 seconds.
5. Stop engine and reconnect mass air flow sensor harness con-
nector.
6. Select Service $03 with GST and make sure that DTC P0102 is detected.
7. Select Service $04 with GST and erase the DTC P0102.
8. Start engine and keep the engine speed between 3,500 and 4,000 rpm for 1 minute under no load.
9. Let engine idle for 1 minute.
10. Keep engine speed between 2,500 and 3,000 rpm for 20 min- utes.
11. Select Service $07 with GST. If 1st trip DTC is detected, go to EC-386, "
Diagnosis Procedure".
Diagnosis ProcedureINFOID:0000000001365861
1.CHECK GROUND CONNECTIONS
1. Turn ignition switch OFF.
2. Loosen and retighten two ground screws on the body. Refer to EC-86, "
Ground Inspection".
OK or NG
OK >> GO TO 2.
NG >> Repair or replace ground connections.
2.RETIGHTEN A/F SENSOR 1
1. Loosen and retighten the A/F sensor 1.
BBIA0368E
BBIA0354E
Tightening torque: 50 N-m (5.1 kg-m, 37 ft-lb)
BBIA0375E
Revision: March 2010 2008 QX56
Page 1764 of 4083
![INFINITI QX56 2008 Factory Manual PDF ECM
EC-465
< ECU DIAGNOSIS > [VK56DE]
C
D
E
F
G H
I
J
K L
M A
EC
NP
OOUTPUT SPEED SENSOR*6P0720
0720—2×TM-48
1GR INCORRECT RATIO P07310731—2×TM-53
2GR INCORRECT RATIO P07320732—2×TM-55
3GR IN INFINITI QX56 2008 Factory Manual PDF ECM
EC-465
< ECU DIAGNOSIS > [VK56DE]
C
D
E
F
G H
I
J
K L
M A
EC
NP
OOUTPUT SPEED SENSOR*6P0720
0720—2×TM-48
1GR INCORRECT RATIO P07310731—2×TM-53
2GR INCORRECT RATIO P07320732—2×TM-55
3GR IN](/img/42/57030/w960_57030-1763.png)
ECM
EC-465
< ECU DIAGNOSIS > [VK56DE]
C
D
E
F
G H
I
J
K L
M A
EC
NP
OOUTPUT SPEED SENSOR*6P0720
0720—2×TM-48
1GR INCORRECT RATIO P07310731—2×TM-53
2GR INCORRECT RATIO P07320732—2×TM-55
3GR INCORRECT RATIO P07330733—2×TM-57
4GR INCORRECT RATIO P07340734—2×TM-59
5GR INCORRECT RATIO P07350735—2×TM-61
TORQUE CONVERTER P07400740—2×TM-63
TORQUE CONVERTER P07440744—2×TM-65
PC SOLENOID A P07450745—2×TM-67
P-N POS SW/CIRCUIT P08500850—2×EC-296
INTK TIM S/CIRC-B1 P11401140—2×EC-299
INTK TIM S/CIRC-B2 P11451145—2×EC-299
CLOSED LOOP-B1 P11481148—1×EC-303
CLOSED LOOP-B2 P11681168—1×EC-303
TCS C/U FUNCTN P12111211—2—EC-304
TCS/CIRC P12121212—2—EC-305
ENG OVER TEMP P12171217—1×EC-36
CTP LEARNING-B1 P12251225—2—EC-310
CTP LEARNING-B1 P12261226—2—EC-312
COLD START CONTROL P14211421—2×EC-314
BAT CURRENT SENSOR P15501550—2—EC-316
BAT CURRENT SENSOR P15511551—2—EC-320
BAT CURRENT SENSOR P15521552—2—EC-320
BAT CURRENT SENSOR P15531553—2—EC-324
BAT CURRENT SENSOR P15541554—2—EC-328
ASCD SW P15641564—1—EC-332
(Models
with ICC) EC-336
(Models
with ASCD)
ICC COMMAND VALUE*
9P1568 1568—1—EC-340
ASCD BRAKE SW P15721572—1—EC-341
(Models
with ICC) EC-347
(Models
with ASCD)
ASCD VHL SPD SEN*
8P1574 1574—1—EC-352
(Models
with ICC)
EC-354
(Models
with ASCD)
ID DISCARD IMM-ECM P16111611—2—SEC-39
CHAIN OF ECM-IMMU P16121612—2—SEC-35
CHAIN OF IMMU-KEY P16141614—2—SEC-29
Items
(CONSULT-IIl screen terms) DTC*
1
SRT code Trip
MILReference
page
CONSULT-IIl
GST*
2ECM*3
Revision: March 2010 2008 QX56
Page 1788 of 4083
![INFINITI QX56 2008 Factory Manual PDF PRECAUTIONSEC-489
< PRECAUTION > [VK56DE]
C
D
E
F
G H
I
J
K L
M A
EC
NP
O
•
When measuring ECM signals with a circuit tester, never allow
the two tester probes to contact.
Accidental contact of prob INFINITI QX56 2008 Factory Manual PDF PRECAUTIONSEC-489
< PRECAUTION > [VK56DE]
C
D
E
F
G H
I
J
K L
M A
EC
NP
O
•
When measuring ECM signals with a circuit tester, never allow
the two tester probes to contact.
Accidental contact of prob](/img/42/57030/w960_57030-1787.png)
PRECAUTIONSEC-489
< PRECAUTION > [VK56DE]
C
D
E
F
G H
I
J
K L
M A
EC
NP
O
•
When measuring ECM signals with a circuit tester, never allow
the two tester probes to contact.
Accidental contact of probes will cause a short circuit and
damage the ECM power transistor.
• Do not use ECM ground termina ls when measuring input/out-
put voltage. Doing so may result in damage to the ECM's tran-
sistor. Use a ground other than ECM terminals, such as the
ground.
• B1 indicates the bank 1, B2 indicates the bank 2 as shown in
the figure.
• Do not operate fuel pump when there is no fuel in lines.
• Tighten fuel hose clamps to the specified torque.
SEF348N
PBIB1144E
BBIA0402E
Revision: March 2010 2008 QX56
Page 1807 of 4083
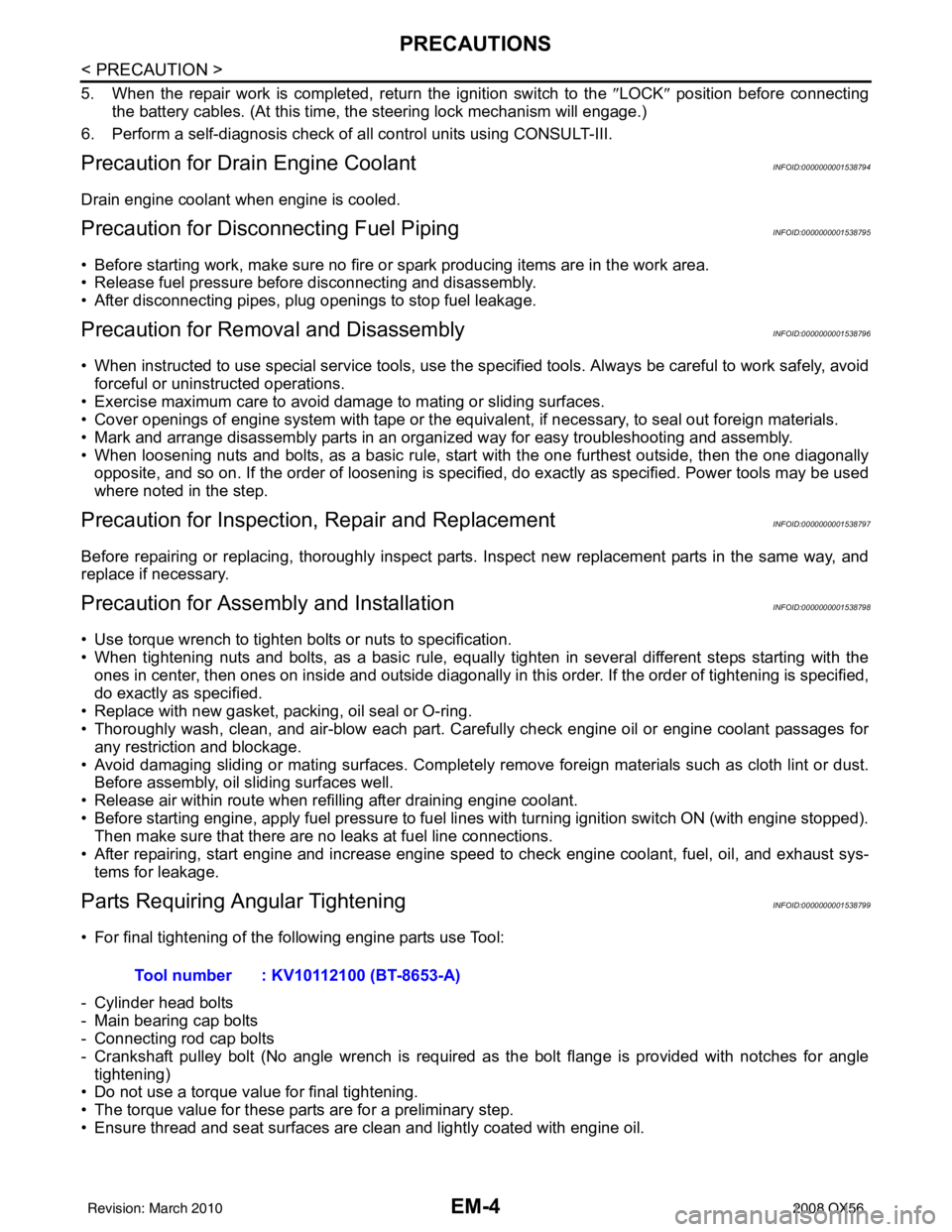
EM-4
< PRECAUTION >
PRECAUTIONS
5. When the repair work is completed, return the ignition switch to the ″LOCK ″ position before connecting
the battery cables. (At this time, the steering lock mechanism will engage.)
6. Perform a self-diagnosis check of a ll control units using CONSULT-III.
Precaution for Drain Engine CoolantINFOID:0000000001538794
Drain engine coolant when engine is cooled.
Precaution for Disconnecting Fuel PipingINFOID:0000000001538795
• Before starting work, make sure no fire or spark producing items are in the work area.
• Release fuel pressure before disconnecting and disassembly.
• After disconnecting pipes, plug openings to stop fuel leakage.
Precaution for Removal and DisassemblyINFOID:0000000001538796
• When instructed to use special service tools, use the s pecified tools. Always be careful to work safely, avoid
forceful or uninstructed operations.
• Exercise maximum care to avoid damage to mating or sliding surfaces.
• Cover openings of engine system with tape or the equivalent, if necessary, to seal out foreign materials.
• Mark and arrange disassembly parts in an organi zed way for easy troubleshooting and assembly.
• When loosening nuts and bolts, as a basic rule, start with the one furthest outside, then the one diagonally opposite, and so on. If the order of loosening is specified, do exactly as specified. Power tools may be used
where noted in the step.
Precaution for Inspection, Repair and ReplacementINFOID:0000000001538797
Before repairing or replacing, thoroughly inspect parts. Inspect new replacement parts in the same way, and
replace if necessary.
Precaution for Assembly and InstallationINFOID:0000000001538798
• Use torque wrench to tighten bolts or nuts to specification.
• When tightening nuts and bolts, as a basic rule, equally tighten in several different steps starting with theones in center, then ones on inside and outside diagonally in this order. If the order of tightening is specified,
do exactly as specified.
• Replace with new gasket, packing, oil seal or O-ring.
• Thoroughly wash, clean, and air-blow each part. Carefully check engine oil or engine coolant passages for any restriction and blockage.
• Avoid damaging sliding or mating surfaces. Completely remove foreign materials such as cloth lint or dust. Before assembly, oil sliding surfaces well.
• Release air within route when refilling after draining engine coolant.
• Before starting engine, apply fuel pressure to fuel lines with turning ignition switch ON (with engine stopped). Then make sure that there are no leaks at fuel line connections.
• After repairing, start engine and increase engine s peed to check engine coolant, fuel, oil, and exhaust sys-
tems for leakage.
Parts Requiring Angular TighteningINFOID:0000000001538799
• For final tightening of the following engine parts use Tool:
- Cylinder head bolts
- Main bearing cap bolts
- Connecting rod cap bolts
- Crankshaft pulley bolt (No angle wrench is required as the bolt flange is provided with notches for angle tightening)
• Do not use a torque value for final tightening.
• The torque value for these parts are for a preliminary step.
• Ensure thread and seat surfaces are clean and lightly coated with engine oil. Tool number : KV10112100 (BT-8653-A)
Revision: March 2010
2008 QX56
Page 1835 of 4083
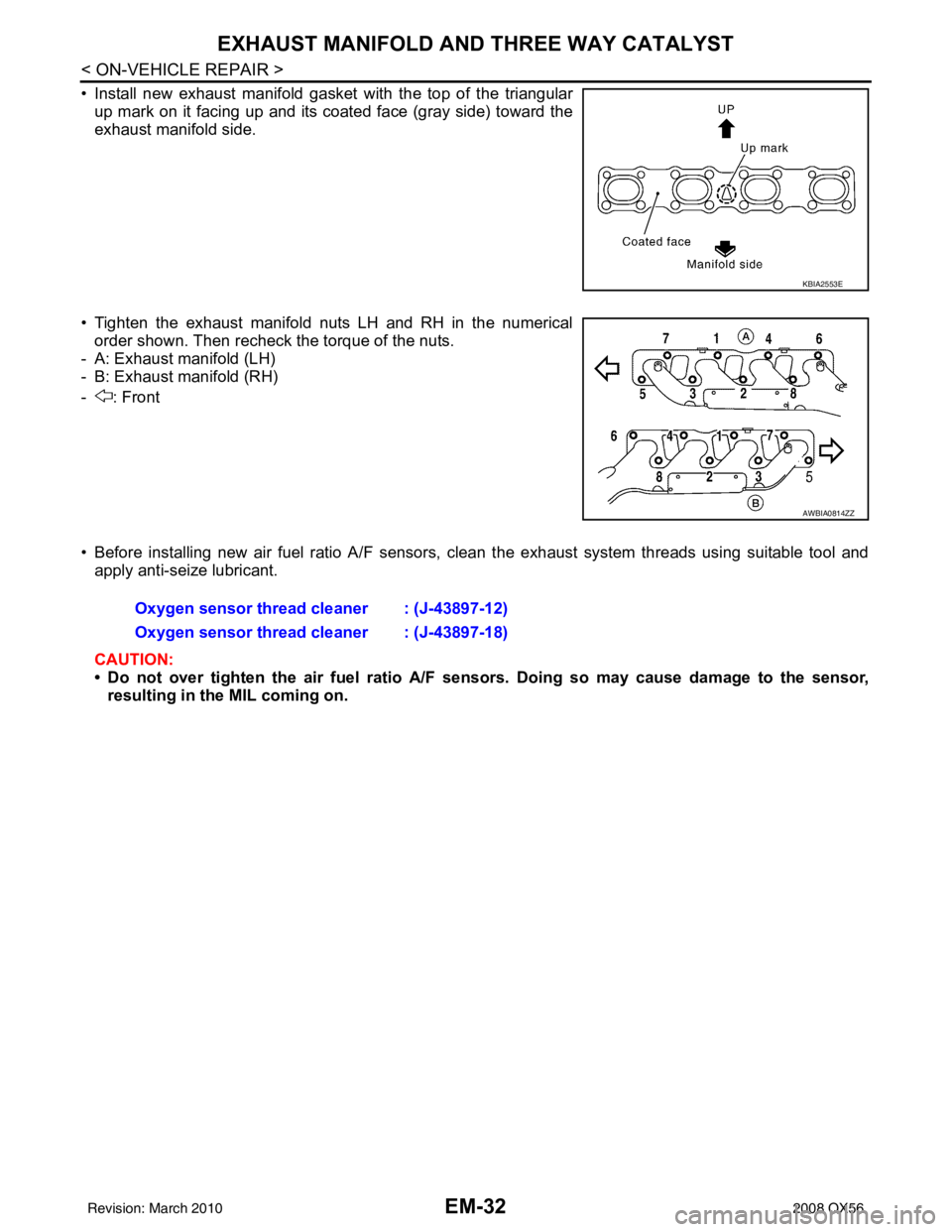
EM-32
< ON-VEHICLE REPAIR >
EXHAUST MANIFOLD AND THREE WAY CATALYST
• Install new exhaust manifold gasket with the top of the triangularup mark on it facing up and its coated face (gray side) toward the
exhaust manifold side.
• Tighten the exhaust manifold nuts LH and RH in the numerical order shown. Then recheck the torque of the nuts.
- A: Exhaust manifold (LH)
- B: Exhaust manifold (RH)
- : Front
• Before installing new air fuel ratio A/F sensors, clean the exhaust system threads using suitable tool and
apply anti-seize lubricant.
CAUTION:
• Do not over tighten the air fuel ratio A/F se nsors. Doing so may cause damage to the sensor,
resulting in the MIL coming on.
KBIA2553E
AWBIA0814ZZ
Oxygen sensor thread cleaner : (J-43897-12)
Oxygen sensor thread cleaner : (J-43897-18)
Revision: March 2010 2008 QX56
Page 1854 of 4083
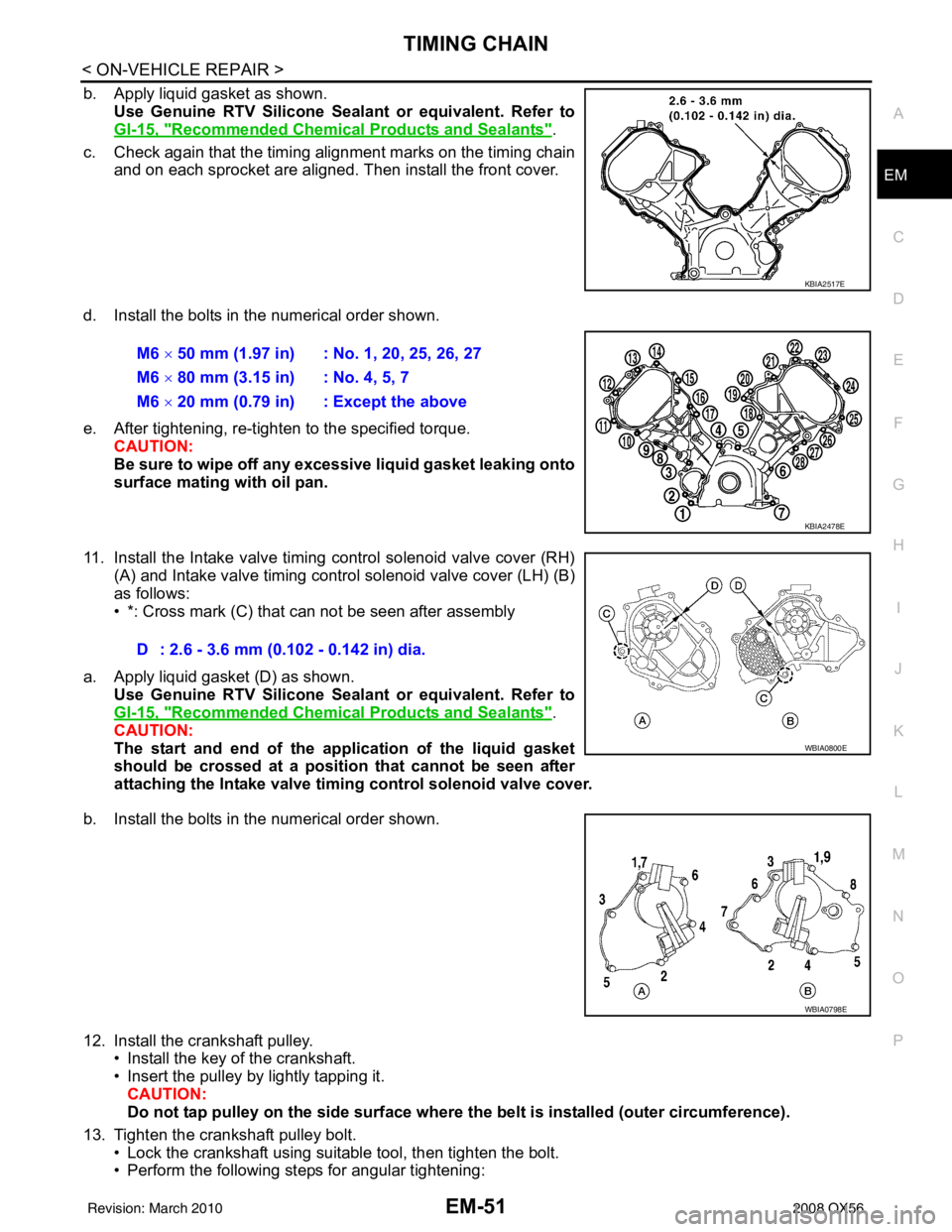
TIMING CHAINEM-51
< ON-VEHICLE REPAIR >
C
DE
F
G H
I
J
K L
M A
EM
NP
O
b. Apply liquid gasket as shown.
Use Genuine RTV Silicone Seal ant or equivalent. Refer to
GI-15, "
Recommended Chemical Products and Sealants".
c. Check again that the timing alignment marks on the timing chain and on each sprocket are aligned. Then install the front cover.
d. Install the bolts in the numerical order shown.
e. After tightening, re-tighten to the specified torque. CAUTION:
Be sure to wipe off any excessive liquid gasket leaking onto
surface mating with oil pan.
11. Install the Intake valve timing control solenoid valve cover (RH) (A) and Intake valve timing control solenoid valve cover (LH) (B)
as follows:
• *: Cross mark (C) that can not be seen after assembly
a. Apply liquid gasket (D) as shown. Use Genuine RTV Silicone Seal ant or equivalent. Refer to
GI-15, "
Recommended Chemical Products and Sealants".
CAUTION:
The start and end of the appl ication of the liquid gasket
should be crossed at a positi on that cannot be seen after
attaching the Intake valve timing control solenoid valve cover.
b. Install the bolts in the numerical order shown.
12. Install the crankshaft pulley. • Install the key of the crankshaft.
• Insert the pulley by lightly tapping it.
CAUTION:
Do not tap pulley on the side surface where th e belt is installed (outer circumference).
13. Tighten the crankshaft pulley bolt. • Lock the crankshaft using suitable tool, then tighten the bolt.
• Perform the following steps for angular tightening:
KBIA2517E
M6 × 50 mm (1.97 in) : No. 1, 20, 25, 26, 27
M6 × 80 mm (3.15 in) : No. 4, 5, 7
M6 × 20 mm (0.79 in) : Except the above
KBIA2478E
D : 2.6 - 3.6 mm (0.102 - 0.142 in) dia.
WBIA0800E
WBIA0798E
Revision: March 2010 2008 QX56