wiring diagram INFINITI QX56 2010 Factory Service Manual
[x] Cancel search | Manufacturer: INFINITI, Model Year: 2010, Model line: QX56, Model: INFINITI QX56 2010Pages: 4210, PDF Size: 81.91 MB
Page 697 of 4210
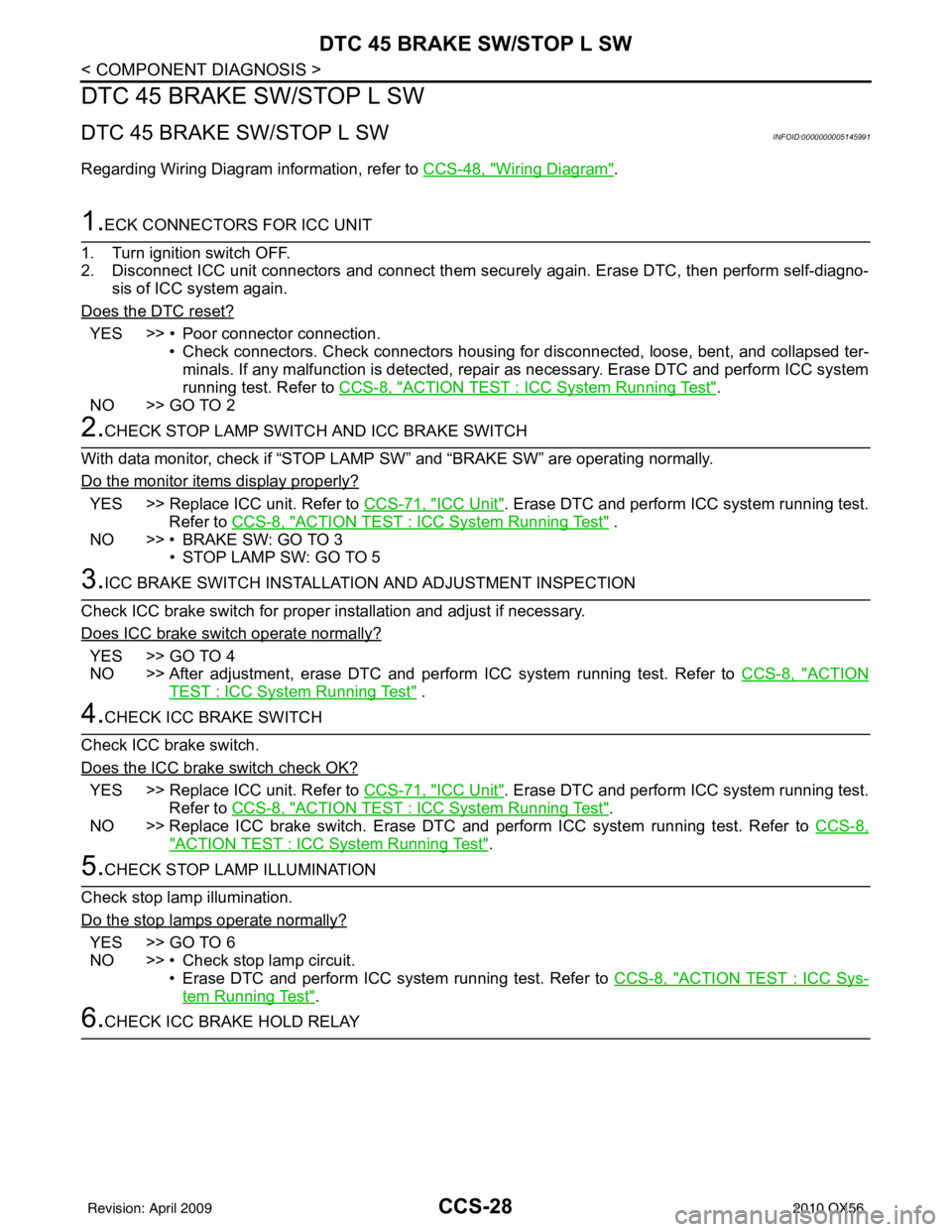
CCS-28
< COMPONENT DIAGNOSIS >
DTC 45 BRAKE SW/STOP L SW
DTC 45 BRAKE SW/STOP L SW
DTC 45 BRAKE SW/STOP L SWINFOID:0000000005145991
Regarding Wiring Diagram information, refer to CCS-48, "Wiring Diagram".
1.ECK CONNECTORS FOR ICC UNIT
1. Turn ignition switch OFF.
2. Disconnect ICC unit connectors and connect them secu rely again. Erase DTC, then perform self-diagno-
sis of ICC system again.
Does the DTC reset?
YES >> • Poor connector connection. • Check connectors. Check connectors housing for disconnected, loose, bent, and collapsed ter-
minals. If any malfunction is detected, repair as necessary. Erase DTC and perform ICC system
running test. Refer to CCS-8, "
ACTION TEST : ICC System Running Test".
NO >> GO TO 2
2.CHECK STOP LAMP SWITCH AND ICC BRAKE SWITCH
With data monitor, check if “STOP LAMP SW” and “BRAKE SW” are operating normally.
Do the monitor items display properly?
YES >> Replace ICC unit. Refer to CCS-71, "ICC Unit". Erase DTC and perform ICC system running test.
Refer to CCS-8, "
ACTION TEST : ICC System Running Test" .
NO >> • BRAKE SW: GO TO 3
• STOP LAMP SW: GO TO 5
3.ICC BRAKE SWITCH INSTALLATION AND ADJUSTMENT INSPECTION
Check ICC brake switch for proper installation and adjust if necessary.
Does ICC brake switch operate normally?
YES >> GO TO 4
NO >> After adjustment, erase DTC and perform ICC system running test. Refer to \
CCS-8, "
ACTION
TEST : ICC System Running Test" .
4.CHECK ICC BRAKE SWITCH
Check ICC brake switch.
Does the ICC brake switch check OK?
YES >> Replace ICC unit. Refer to CCS-71, "ICC Unit". Erase DTC and perform ICC system running test.
Refer to CCS-8, "
ACTION TEST : ICC System Running Test".
NO >> Replace ICC brake switch. Erase DTC and perform ICC system running test. Refer to CCS-8,
"ACTION TEST : ICC System Running Test".
5.CHECK STOP LAMP ILLUMINATION
Check stop lamp illumination.
Do the stop lamps operate normally?
YES >> GO TO 6
NO >> • Check stop lamp circuit. • Erase DTC and perform ICC system running test. Refer to CCS-8, "
ACTION TEST : ICC Sys-
tem Running Test".
6.CHECK ICC BRAKE HOLD RELAY
Revision: April 20092010 QX56
Page 699 of 4210
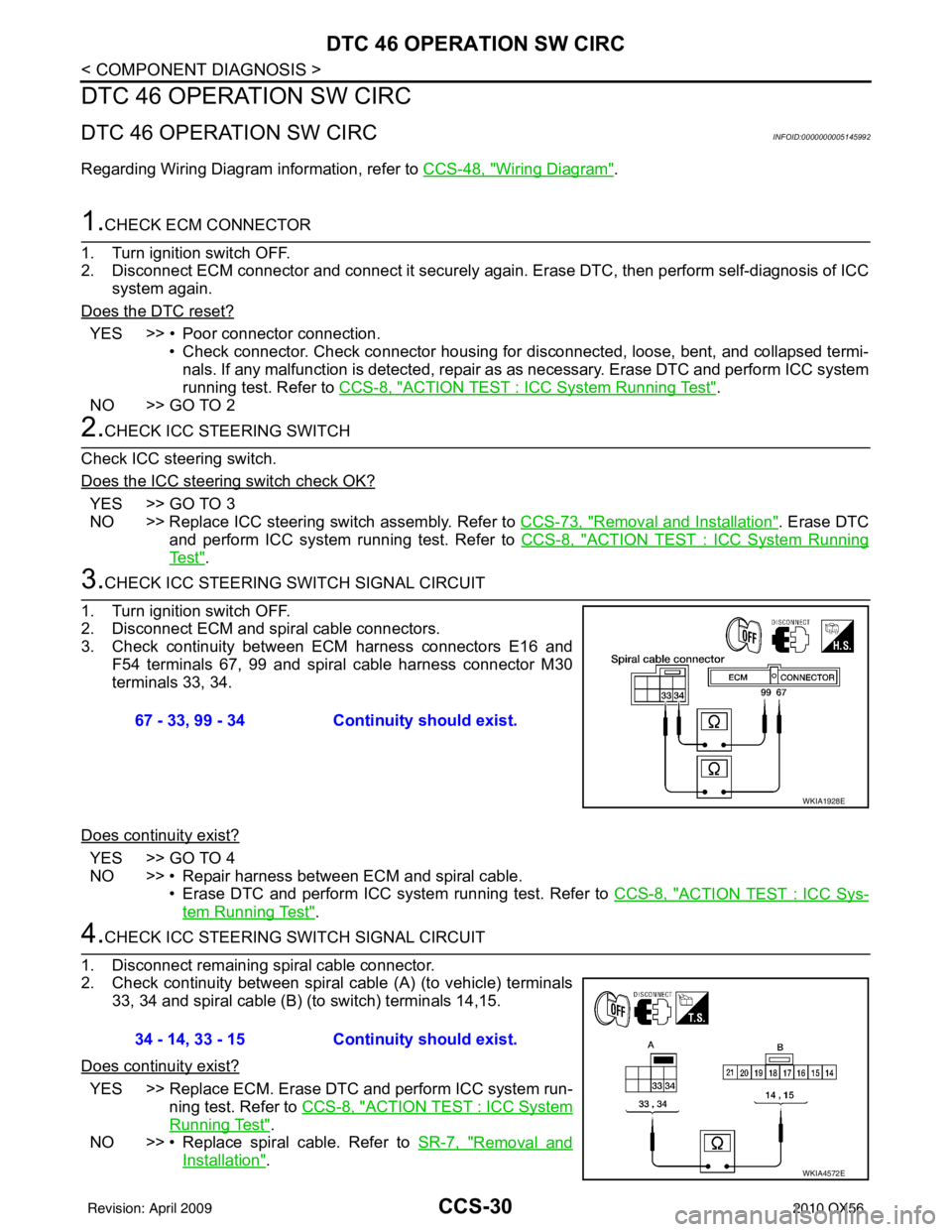
CCS-30
< COMPONENT DIAGNOSIS >
DTC 46 OPERATION SW CIRC
DTC 46 OPERATION SW CIRC
DTC 46 OPERATION SW CIRCINFOID:0000000005145992
Regarding Wiring Diagram information, refer to CCS-48, "Wiring Diagram".
1.CHECK ECM CONNECTOR
1. Turn ignition switch OFF.
2. Disconnect ECM connector and connect it securely again. Erase DTC, then perform self-diagnosis of ICC
system again.
Does the DTC reset?
YES >> • Poor connector connection. • Check connector. Check connector housing for disconnected, loose, bent, and collapsed termi-
nals. If any malfunction is detected, repair as as necessary. Erase DTC and perform ICC system
running test. Refer to CCS-8, "
ACTION TEST : ICC System Running Test".
NO >> GO TO 2
2.CHECK ICC STEERING SWITCH
Check ICC steering switch.
Does the ICC steeri ng switch check OK?
YES >> GO TO 3
NO >> Replace ICC steering switch assembly. Refer to CCS-73, "
Removal and Installation". Erase DTC
and perform ICC system running test. Refer to CCS-8, "
ACTION TEST : ICC System Running
Te s t".
3.CHECK ICC STEERING SWITCH SIGNAL CIRCUIT
1. Turn ignition switch OFF.
2. Disconnect ECM and spiral cable connectors.
3. Check continuity between ECM harness connectors E16 and F54 terminals 67, 99 and spiral cable harness connector M30
terminals 33, 34.
Does continuity exist?
YES >> GO TO 4
NO >> • Repair harness between ECM and spiral cable. • Erase DTC and perform ICC system running test. Refer to CCS-8, "
ACTION TEST : ICC Sys-
tem Running Test".
4.CHECK ICC STEERING SWITCH SIGNAL CIRCUIT
1. Disconnect remaining spiral cable connector.
2. Check continuity between spiral cable (A) (to vehicle) terminals 33, 34 and spiral cable (B) (to switch) terminals 14,15.
Does continuity exist?
YES >> Replace ECM. Erase DTC and perform ICC system run- ning test. Refer to CCS-8, "
ACTION TEST : ICC System
Running Test".
NO >> • Replace spiral cable. Refer to SR-7, "
Removal and
Installation".
67 - 33, 99 - 34
Continuity should exist.
WKIA1928E
34 - 14, 33 - 15Continuity should exist.
WKIA4572E
Revision: April 20092010 QX56
Page 702 of 4210
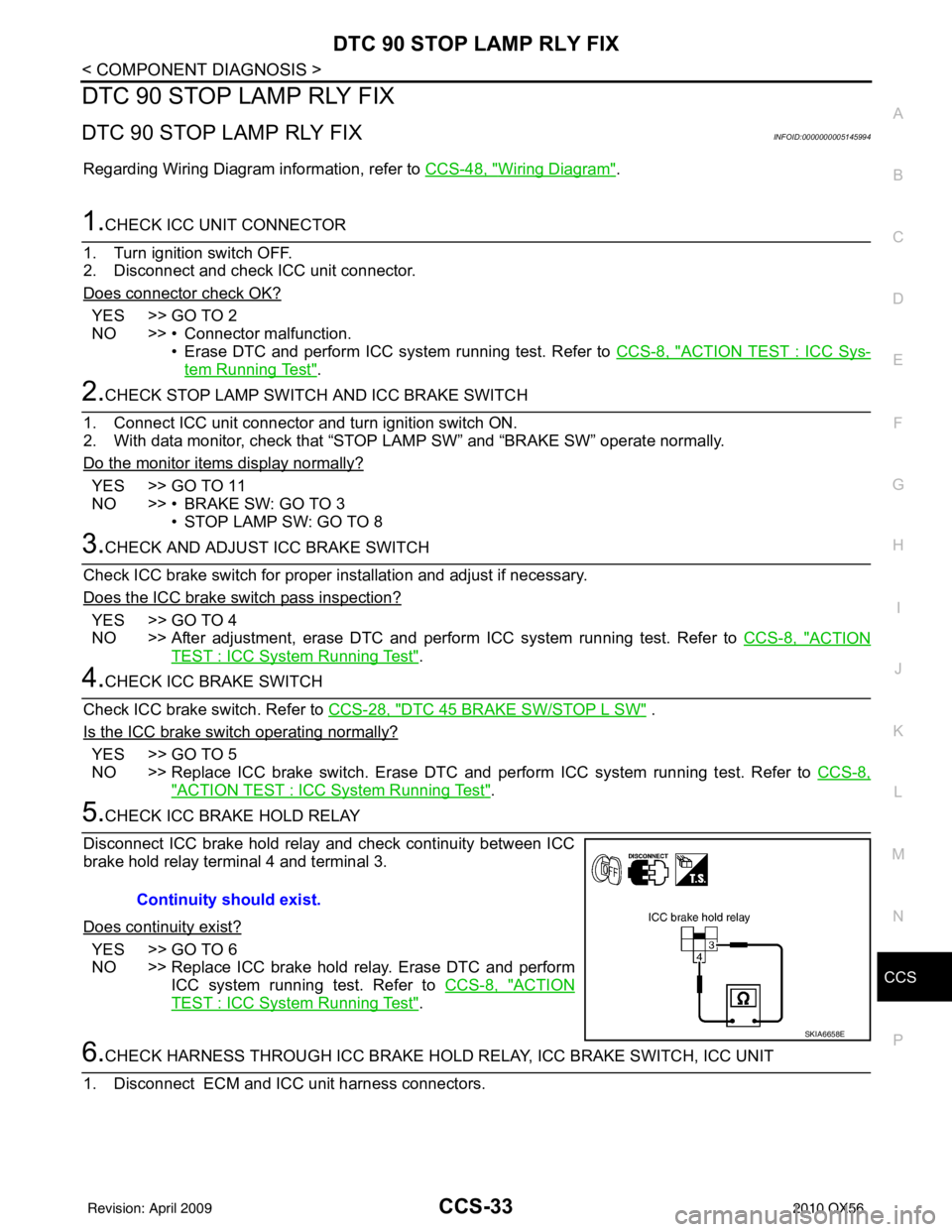
CCS
DTC 90 STOP LAMP RLY FIXCCS-33
< COMPONENT DIAGNOSIS >
C
DE
F
G H
I
J
K L
M B
N P A
DTC 90 STOP LAMP RLY FIX
DTC 90 STOP LAMP RLY FIXINFOID:0000000005145994
Regarding Wiring Diagram information, refer to CCS-48, "Wiring Diagram".
1.CHECK ICC UNIT CONNECTOR
1. Turn ignition switch OFF.
2. Disconnect and check ICC unit connector.
Does connector check OK?
YES >> GO TO 2
NO >> • Connector malfunction. • Erase DTC and perform ICC system running test. Refer to CCS-8, "
ACTION TEST : ICC Sys-
tem Running Test".
2.CHECK STOP LAMP SWITCH AND ICC BRAKE SWITCH
1. Connect ICC unit connector and turn ignition switch ON.
2. With data monitor, check that “STOP LAMP SW” and “BRAKE SW” operate normally.
Do the monitor items display normally?
YES >> GO TO 11
NO >> • BRAKE SW: GO TO 3 • STOP LAMP SW: GO TO 8
3.CHECK AND ADJUST ICC BRAKE SWITCH
Check ICC brake switch for proper installation and adjust if necessary.
Does the ICC brake switch pass inspection?
YES >> GO TO 4
NO >> After adjustment, erase DTC and perfo rm ICC system running test. Refer to CCS-8, "
ACTION
TEST : ICC System Running Test".
4.CHECK ICC BRAKE SWITCH
Check ICC brake switch. Refer to CCS-28, "
DTC 45 BRAKE SW/STOP L SW" .
Is the ICC brake switch operating normally?
YES >> GO TO 5
NO >> Replace ICC brake switch. Erase DTC and perform ICC system running test. Refer to CCS-8,
"ACTION TEST : ICC System Running Test".
5.CHECK ICC BRAKE HOLD RELAY
Disconnect ICC brake hold relay and check continuity between ICC
brake hold relay terminal 4 and terminal 3.
Does continuity exist?
YES >> GO TO 6
NO >> Replace ICC brake hold relay. Erase DTC and perform ICC system running test. Refer to CCS-8, "
ACTION
TEST : ICC System Running Test".
6.CHECK HARNESS THROUGH ICC BRAKE HOLD RELAY, ICC BRAKE SWITCH, ICC UNIT
1. Disconnect ECM and ICC unit harness connectors. Continuity should exist.
SKIA6658E
Revision: April 20092010 QX56
Page 708 of 4210
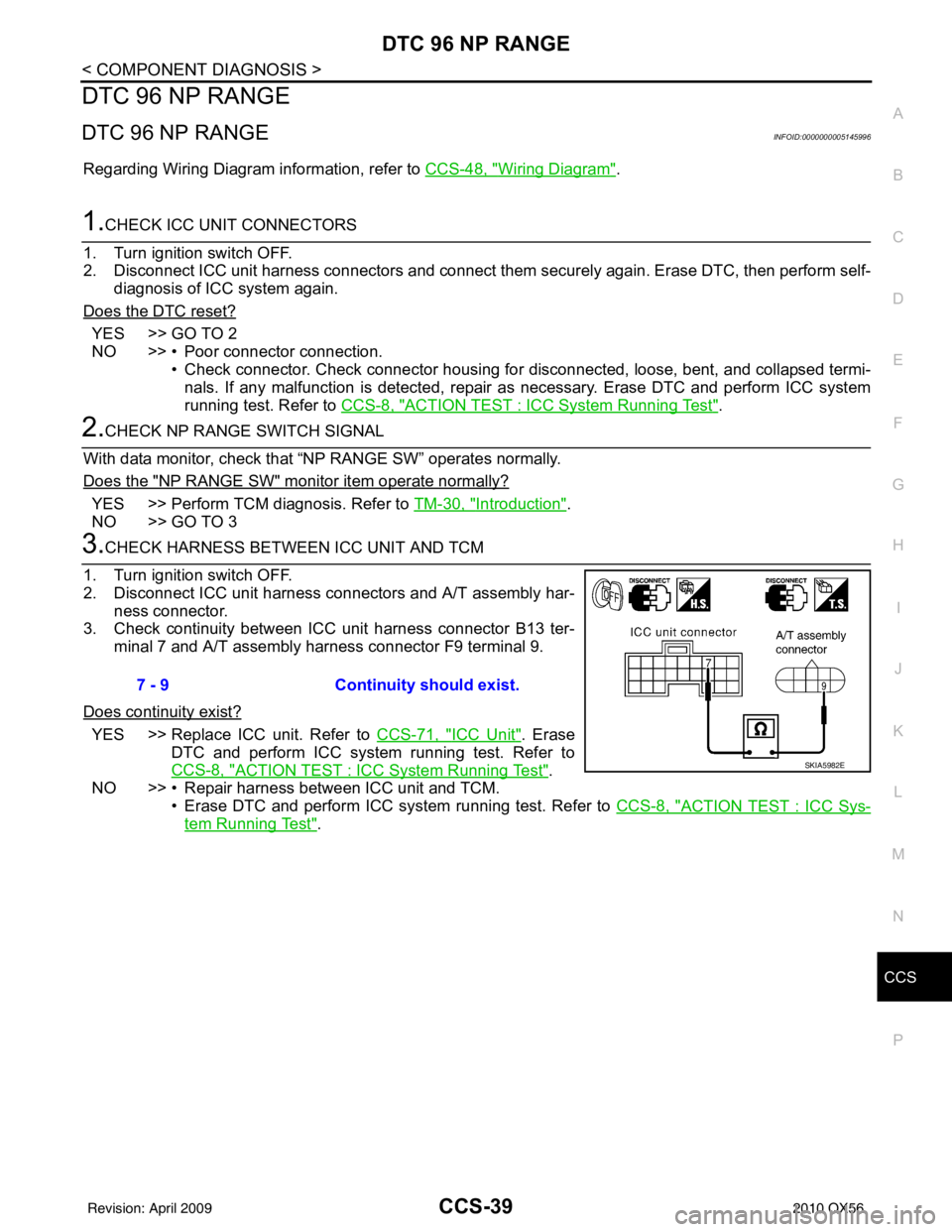
CCS
DTC 96 NP RANGECCS-39
< COMPONENT DIAGNOSIS >
C
DE
F
G H
I
J
K L
M B
N P A
DTC 96 NP RANGE
DTC 96 NP RANGEINFOID:0000000005145996
Regarding Wiring Diagram information, refer to CCS-48, "Wiring Diagram".
1.CHECK ICC UNIT CONNECTORS
1. Turn ignition switch OFF.
2. Disconnect ICC unit harness connectors and connect them securely again. Erase DTC, then perform self- diagnosis of ICC system again.
Does the DTC reset?
YES >> GO TO 2
NO >> • Poor connector connection. • Check connector. Check connector housing for disconnected, loose, bent, and collapsed termi-nals. If any malfunction is detected, repair as necessary. Erase DTC and perform ICC system
running test. Refer to CCS-8, "
ACTION TEST : ICC System Running Test".
2.CHECK NP RANGE SWITCH SIGNAL
With data monitor, check that “NP RANGE SW” operates normally.
Does the "NP RANGE SW" monitor item operate normally?
YES >> Perform TCM diagnosis. Refer to TM-30, "Introduction".
NO >> GO TO 3
3.CHECK HARNESS BETWEEN ICC UNIT AND TCM
1. Turn ignition switch OFF.
2. Disconnect ICC unit harness connectors and A/T assembly har- ness connector.
3. Check continuity between ICC unit harness connector B13 ter- minal 7 and A/T assembly harness connector F9 terminal 9.
Does continuity exist?
YES >> Replace ICC unit. Refer to CCS-71, "ICC Unit". Erase
DTC and perform ICC system running test. Refer to
CCS-8, "
ACTION TEST : ICC System Running Test".
NO >> • Repair harness between ICC unit and TCM. • Erase DTC and perform ICC system running test. Refer to CCS-8, "
ACTION TEST : ICC Sys-
tem Running Test".
7 - 9 Continuity
should exist.
SKIA5982E
Revision: April 20092010 QX56
Page 717 of 4210
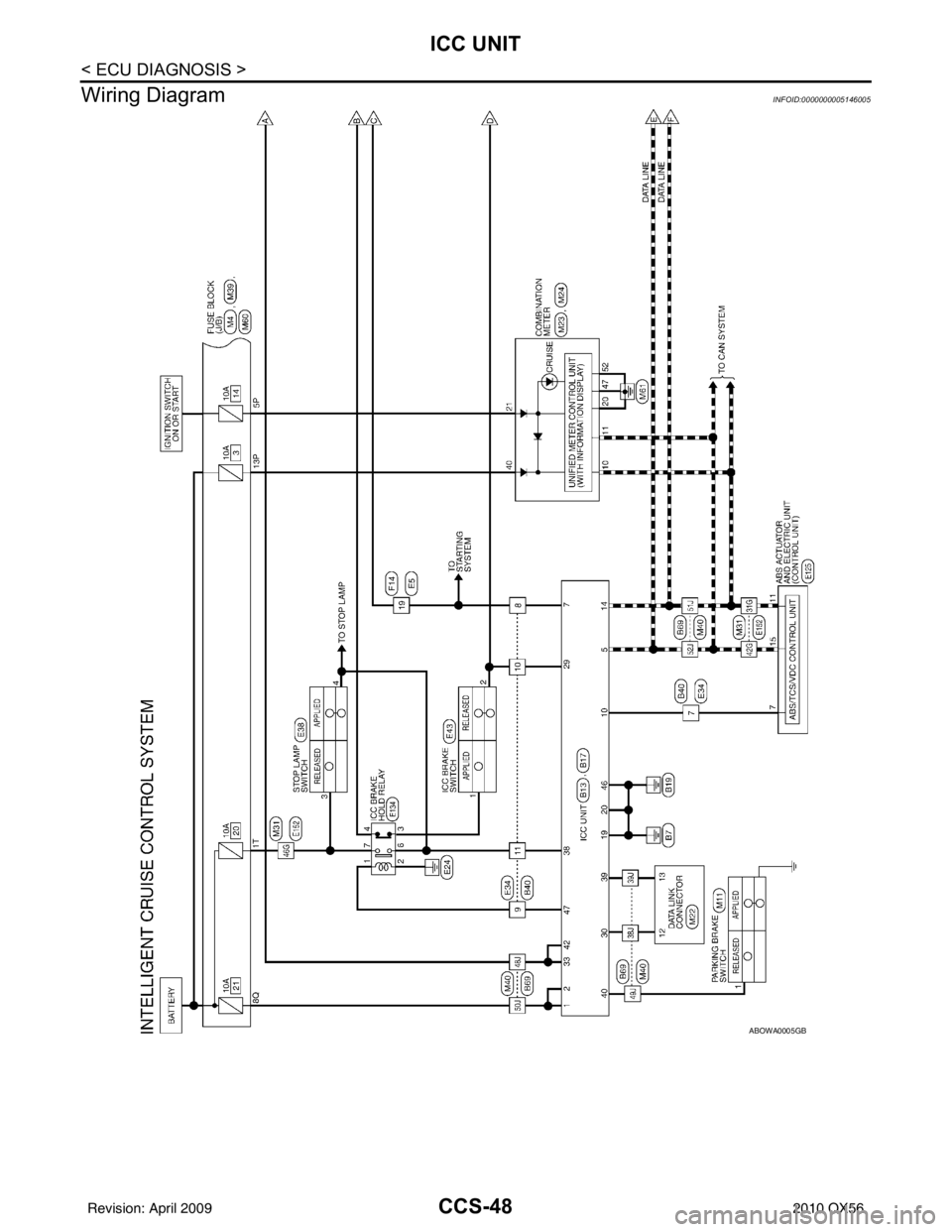
CCS-48
< ECU DIAGNOSIS >
ICC UNIT
Wiring Diagram
INFOID:0000000005146005
ABOWA0005GB
Revision: April 20092010 QX56
Page 743 of 4210
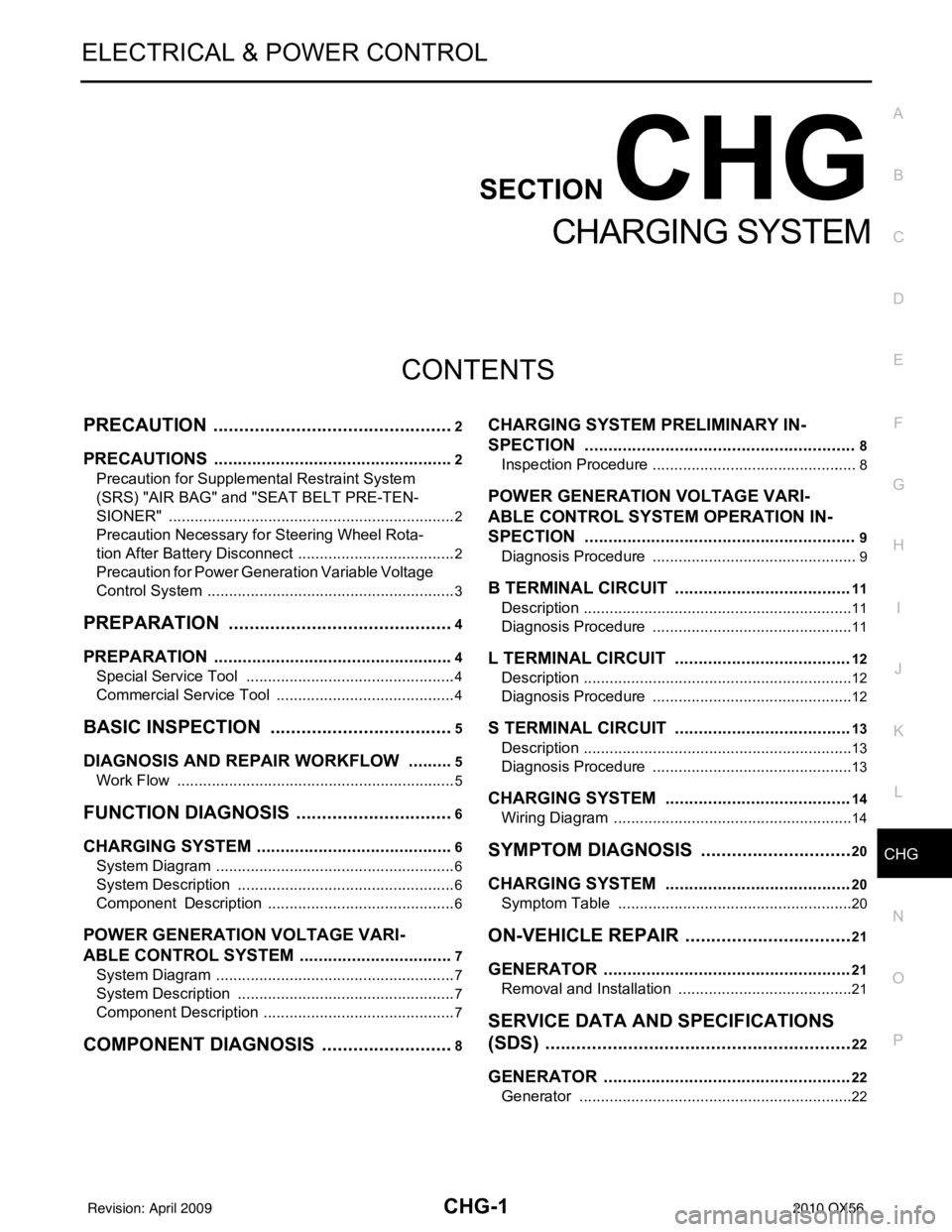
CHG
CHG-1
ELECTRICAL & POWER CONTROL
C
DE
F
G H
I
J
K L
B
SECTION CHG
A
O P
N
CONTENTS
CHARGING SYSTEM
PRECAUTION .......
........................................2
PRECAUTIONS .............................................. .....2
Precaution for Supplemental Restraint System
(SRS) "AIR BAG" and "SEAT BELT PRE-TEN-
SIONER" ............................................................. ......
2
Precaution Necessary for Steering Wheel Rota-
tion After Battery Disconnect ............................... ......
2
Precaution for Power Generation Variable Voltage
Control System ..........................................................
3
PREPARATION ............................................4
PREPARATION .............................................. .....4
Special Service Tool ........................................... ......4
Commercial Service Tool ..........................................4
BASIC INSPECTION ....................................5
DIAGNOSIS AND REPAIR WORKFLOW ..... .....5
Work Flow ........................................................... ......5
FUNCTION DIAGNOSIS ...............................6
CHARGING SYSTEM ..................................... .....6
System Diagram .................................................. ......6
System Description ...................................................6
Component Description ............................................6
POWER GENERATION VOLTAGE VARI-
ABLE CONTROL SYSTEM .................................
7
System Diagram .................................................. ......7
System Description ...................................................7
Component Description .............................................7
COMPONENT DIAGNOSIS ..........................8
CHARGING SYSTEM PRELIMINARY IN-
SPECTION ....... ..................................................
8
Inspection Procedure ........................................... .....8
POWER GENERATION VOLTAGE VARI-
ABLE CONTROL SYSTEM OPERATION IN-
SPECTION .........................................................
9
Diagnosis Procedure ........................................... .....9
B TERMINAL CIRCUIT .....................................11
Description ...............................................................11
Diagnosis Procedure ...............................................11
L TERMINAL CIRCUIT .....................................12
Description ...............................................................12
Diagnosis Procedure ...............................................12
S TERMINAL CIRCUIT .....................................13
Description ...............................................................13
Diagnosis Procedure ...............................................13
CHARGING SYSTEM .......................................14
Wiring Diagram ........................................................14
SYMPTOM DIAGNOSIS ..............................20
CHARGING SYSTEM .......................................20
Symptom Table ................................................... ....20
ON-VEHICLE REPAIR .................................21
GENERATOR ....................................................21
Removal and Installation ..................................... ....21
SERVICE DATA AND SPECIFICATIONS
(SDS) ............... .......................................... ...
22
GENERATOR ....................................................22
Generator ............................................................ ....22
Revision: April 20092010 QX56
Page 751 of 4210
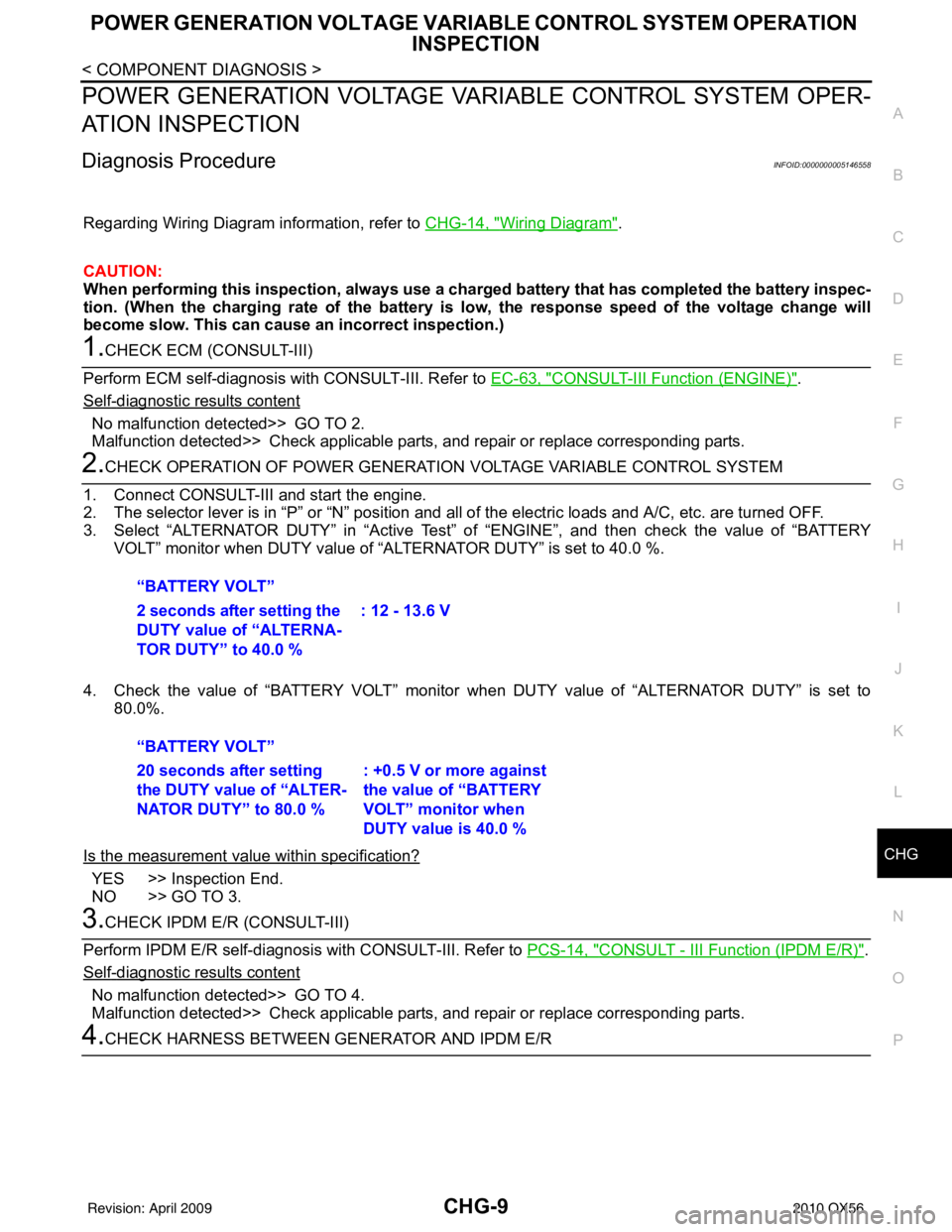
CHG
POWER GENERATION VOLTAGE VARIABLE CONTROL SYSTEM OPERATION
INSPECTION
CHG-9
< COMPONENT DIAGNOSIS >
C
DE
F
G H
I
J
K L
B A
O P
N
POWER GENERATION VOLTAGE VARI
ABLE CONTROL SYSTEM OPER-
ATION INSPECTION
Diagnosis ProcedureINFOID:0000000005146558
Regarding Wiring Diagram information, refer to CHG-14, "Wiring Diagram".
CAUTION:
When performing this inspection, always use a charged battery that has completed the battery inspec-
tion. (When the charging rate of the battery is low, the response speed of the voltage change will
become slow. This can cause an incorrect inspection.)
1.CHECK ECM (CONSULT-III)
Perform ECM self-diagnosis with CONSULT-III. Refer to EC-63, "
CONSULT-III Function (ENGINE)".
Self
-diagnostic results content
No malfunction detected>> GO TO 2.
Malfunction detected>> Check applicable parts, and repair or replace corresponding parts.
2.CHECK OPERATION OF POWER GENERATION VOLTAGE VARIABLE CONTROL SYSTEM
1. Connect CONSULT-III and start the engine.
2. The selector lever is in “P” or “N” position and a ll of the electric loads and A/C, etc. are turned OFF.
3. Select “ALTERNATOR DUTY” in “Active Test” of “ENGINE”, and then check the value of “BATTERY
VOLT” monitor when DUTY value of “ALTERNATOR DUTY” is set to 40.0 %.
4. Check the value of “BATTERY VOLT” monitor when DUTY value of “ALTERNATOR DUTY” is set to 80.0%.
Is the measurement val ue within specification?
YES >> Inspection End.
NO >> GO TO 3.
3.CHECK IPDM E/R (CONSULT-III)
Perform IPDM E/R self-diagnosis with CONSULT-III. Refer to PCS-14, "
CONSULT - III Function (IPDM E/R)".
Self
-diagnostic results content
No malfunction detected>> GO TO 4.
Malfunction detected>> Check applicable parts, and repair or replace corresponding parts.
4.CHECK HARNESS BETWEEN GE NERATOR AND IPDM E/R
“BATTERY VOLT”
2 seconds after setting the
DUTY value of “ALTERNA-
TOR DUTY” to 40.0 %
: 12 - 13.6 V
“BATTERY VOLT”
20 seconds after setting
the DUTY value of “ALTER-
NATOR DUTY” to 80.0 % : +0.5 V or more against
the value of “BATTERY
VOLT” monitor when
DUTY value is 40.0 %
Revision: April 20092010 QX56
Page 753 of 4210
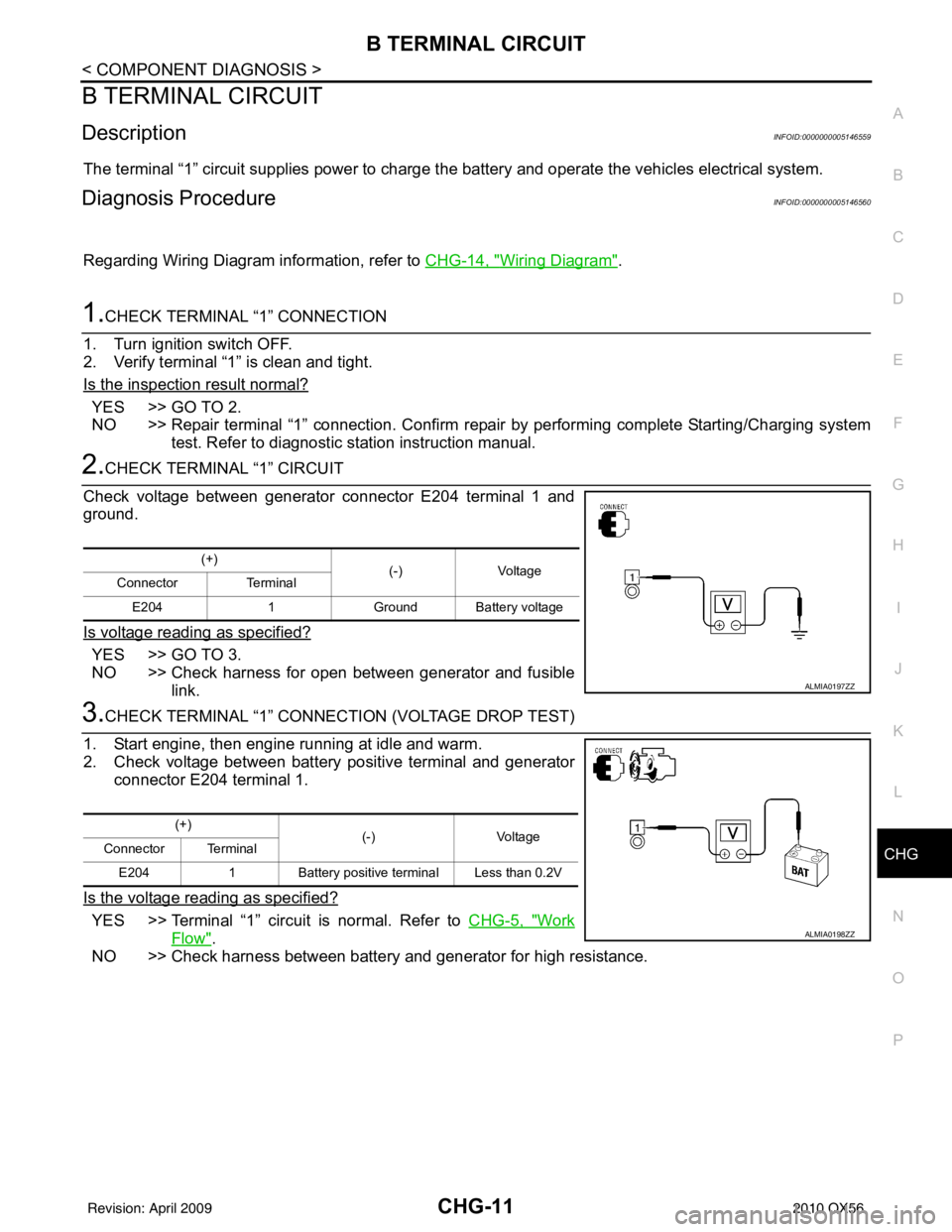
CHG
B TERMINAL CIRCUITCHG-11
< COMPONENT DIAGNOSIS >
C
DE
F
G H
I
J
K L
B A
O P
N
B TERMINAL CIRCUIT
DescriptionINFOID:0000000005146559
The terminal “1” circuit supplies power to charge the battery and operate the vehicles electrical system.
Diagnosis ProcedureINFOID:0000000005146560
Regarding Wiring Diagram information, refer to
CHG-14, "Wiring Diagram".
1.CHECK TERMINAL “1” CONNECTION
1. Turn ignition switch OFF.
2. Verify terminal “1” is clean and tight.
Is the inspection result normal?
YES >> GO TO 2.
NO >> Repair terminal “1” connection. Confirm repa ir by performing complete Starting/Charging system
test. Refer to diagnostic station instruction manual.
2.CHECK TERMINAL “1” CIRCUIT
Check voltage between generator connector E204 terminal 1 and
ground.
Is voltage reading as specified?
YES >> GO TO 3.
NO >> Check harness for open between generator and fusible link.
3.CHECK TERMINAL “1” CONNECTION (VOLTAGE DROP TEST)
1. Start engine, then engine running at idle and warm.
2. Check voltage between battery positive terminal and generator connector E204 terminal 1.
Is the voltage reading as specified?
YES >> Terminal “1” circuit is normal. Refer to CHG-5, "Work
Flow".
NO >> Check harness between battery and generator for high resistance.
(+) (-) Voltage
Connector Terminal
E204 1Ground Battery voltage
ALMIA0197ZZ
(+)
(-)Voltage
Connector Terminal
E204 1 Battery positive terminal Less than 0.2V
ALMIA0198ZZ
Revision: April 20092010 QX56
Page 754 of 4210
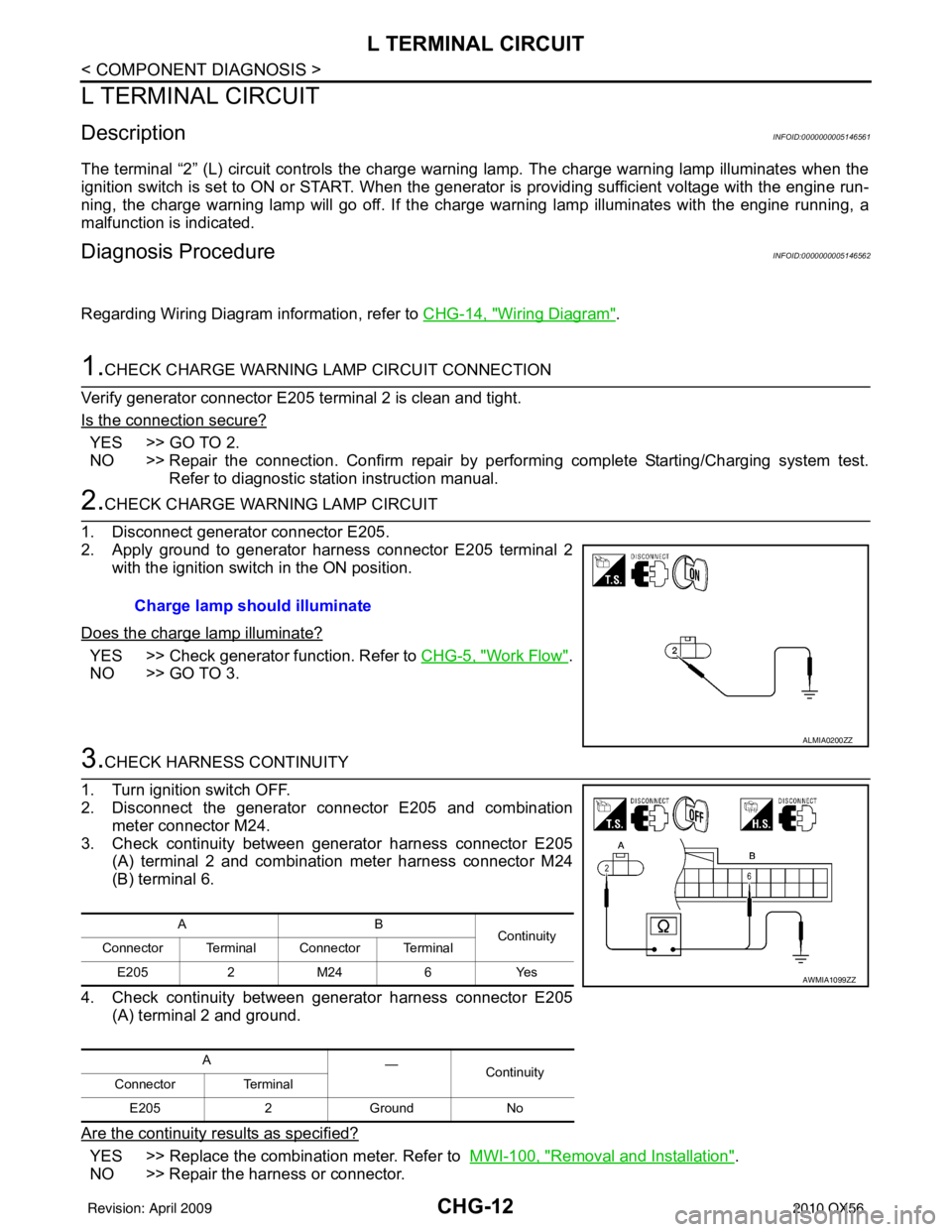
CHG-12
< COMPONENT DIAGNOSIS >
L TERMINAL CIRCUIT
L TERMINAL CIRCUIT
DescriptionINFOID:0000000005146561
The terminal “2” (L) circuit controls the charge warning lamp. The charge warning lamp illuminates when the
ignition switch is set to ON or START. When the generator is providing sufficient voltage with the engine run-
ning, the charge warning lamp will go off. If the c harge warning lamp illuminates with the engine running, a
malfunction is indicated.
Diagnosis ProcedureINFOID:0000000005146562
Regarding Wiring Diagram information, refer to CHG-14, "Wiring Diagram".
1.CHECK CHARGE WARNING LAMP CIRCUIT CONNECTION
Verify generator connector E205 terminal 2 is clean and tight.
Is the connection secure?
YES >> GO TO 2.
NO >> Repair the connection. Confirm repair by per forming complete Starting/Charging system test.
Refer to diagnostic station instruction manual.
2.CHECK CHARGE WARNING LAMP CIRCUIT
1. Disconnect generator connector E205.
2. Apply ground to generator harness connector E205 terminal 2 with the ignition switch in the ON position.
Does the charge lamp illuminate?
YES >> Check generator function. Refer to CHG-5, "Work Flow".
NO >> GO TO 3.
3.CHECK HARNESS CONTINUITY
1. Turn ignition switch OFF.
2. Disconnect the generator connector E205 and combination meter connector M24.
3. Check continuity between generator harness connector E205 (A) terminal 2 and combination meter harness connector M24
(B) terminal 6.
4. Check continuity between generator harness connector E205 (A) terminal 2 and ground.
Are the continuity results as specified?
YES >> Replace the combination meter. Refer to MWI-100, "Removal and Installation".
NO >> Repair the harness or connector. Charge lamp should illuminate
ALMIA0200ZZ
AB
Continuity
Connector Terminal Connector Terminal
E205 2M24 6Yes
A —
Continuity
Connector Terminal
E205 2Ground No
AWMIA1099ZZ
Revision: April 20092010 QX56
Page 755 of 4210
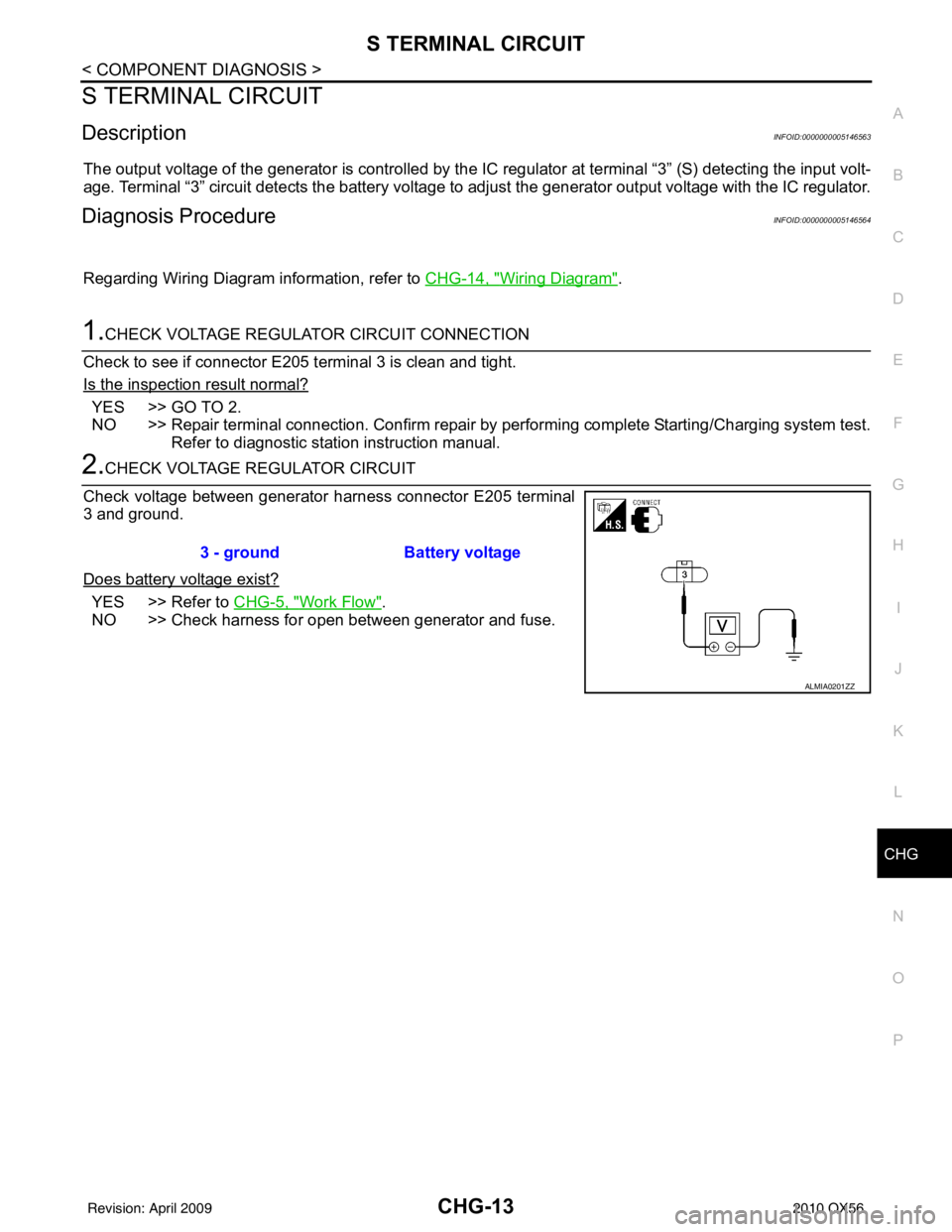
CHG
S TERMINAL CIRCUITCHG-13
< COMPONENT DIAGNOSIS >
C
DE
F
G H
I
J
K L
B A
O P
N
S TERMINAL CIRCUIT
DescriptionINFOID:0000000005146563
The output voltage of the generator is controlled by the IC
regulator at terminal “3” (S) detecting the input volt-
age. Terminal “3” circuit detects the battery voltage to adjust the generator output voltage with the IC regulator.
Diagnosis ProcedureINFOID:0000000005146564
Regarding Wiring Diagram information, refer to CHG-14, "Wiring Diagram".
1.CHECK VOLTAGE REGULATOR CIRCUIT CONNECTION
Check to see if connector E205 terminal 3 is clean and tight.
Is the inspection result normal?
YES >> GO TO 2.
NO >> Repair terminal connection. Confirm repair by performing complete Starting/Charging system test.
Refer to diagnostic station instruction manual.
2.CHECK VOLTAGE REGULATOR CIRCUIT
Check voltage between generator harness connector E205 terminal
3 and ground.
Does battery voltage exist?
YES >> Refer to CHG-5, "Work Flow".
NO >> Check harness for open between generator and fuse. 3 - ground
Battery voltage
ALMIA0201ZZ
Revision: April 20092010 QX56