ISUZU AXIOM 2002 Service Repair Manual
Manufacturer: ISUZU, Model Year: 2002, Model line: AXIOM, Model: ISUZU AXIOM 2002Pages: 2100, PDF Size: 19.35 MB
Page 2021 of 2100
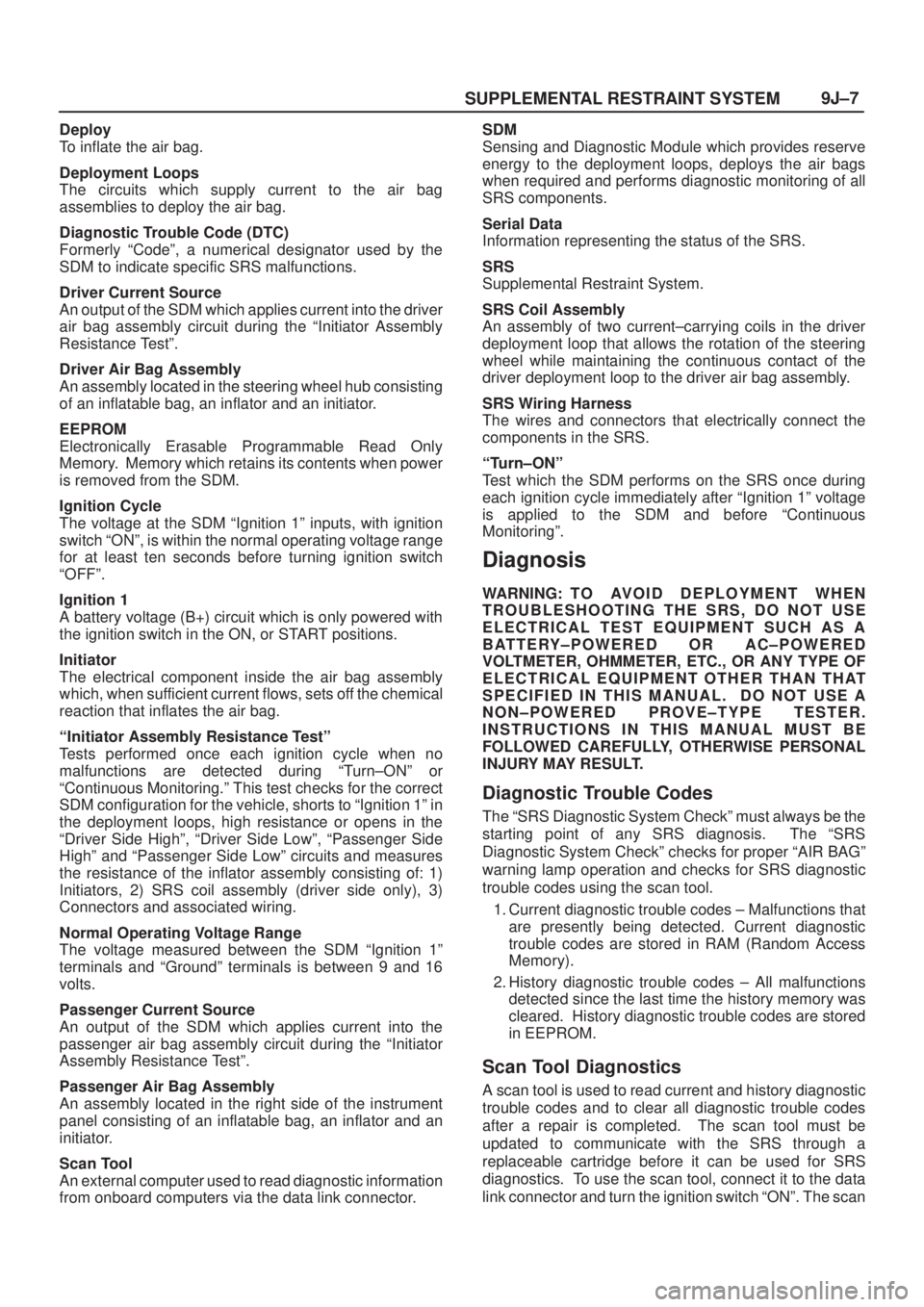
SUPPLEMENTAL RESTRAINT SYSTEM9J±7
Deploy
To inflate the air bag.
Deployment Loops
The circuits which supply current to the air bag
assemblies to deploy the air bag.
Diagnostic Trouble Code (DTC)
Formerly ªCodeº, a numerical designator used by the
SDM to indicate specific SRS malfunctions.
Driver Current Source
An output of the SDM which applies current into the driver
air bag assembly circuit during the ªInitiator Assembly
Resistance Testº.
Driver Air Bag Assembly
An assembly located in the steering wheel hub consisting
of an inflatable bag, an inflator and an initiator.
EEPROM
Electronically Erasable Programmable Read Only
Memory. Memory which retains its contents when power
is removed from the SDM.
Ignition Cycle
The voltage at the SDM ªIgnition 1º inputs, with ignition
switch ªONº, is within the normal operating voltage range
for at least ten seconds before turning ignition switch
ªOFFº.
Ignition 1
A battery voltage (B+) circuit which is only powered with
the ignition switch in the ON, or START positions.
Initiator
The electrical component inside the air bag assembly
which, when sufficient current flows, sets off the chemical
reaction that inflates the air bag.
ªInitiator Assembly Resistance Testº
Tests performed once each ignition cycle when no
malfunctions are detected during ªTurn±ONº or
ªContinuous Monitoring.º This test checks for the correct
SDM configuration for the vehicle, shorts to ªIgnition 1º in
the deployment loops, high resistance or opens in the
ªDriver Side Highº, ªDriver Side Lowº, ªPassenger Side
Highº and ªPassenger Side Lowº circuits and measures
the resistance of the inflator assembly consisting of: 1)
Initiators, 2) SRS coil assembly (driver side only), 3)
Connectors and associated wiring.
Normal Operating Voltage Range
The voltage measured between the SDM ªIgnition 1º
terminals and ªGroundº terminals is between 9 and 16
volts.
Passenger Current Source
An output of the SDM which applies current into the
passenger air bag assembly circuit during the ªInitiator
Assembly Resistance Testº.
Passenger Air Bag Assembly
An assembly located in the right side of the instrument
panel consisting of an inflatable bag, an inflator and an
initiator.
Scan Tool
An external computer used to read diagnostic information
from onboard computers via the data link connector.SDM
Sensing and Diagnostic Module which provides reserve
energy to the deployment loops, deploys the air bags
when required and performs diagnostic monitoring of all
SRS components.
Serial Data
Information representing the status of the SRS.
SRS
Supplemental Restraint System.
SRS Coil Assembly
An assembly of two current±carrying coils in the driver
deployment loop that allows the rotation of the steering
wheel while maintaining the continuous contact of the
driver deployment loop to the driver air bag assembly.
SRS Wiring Harness
The wires and connectors that electrically connect the
components in the SRS.
ªTurn±ONº
Test which the SDM performs on the SRS once during
each ignition cycle immediately after ªIgnition 1º voltage
is applied to the SDM and before ªContinuous
Monitoringº.
Diagnosis
WARNING: T O AV O I D D E P L O Y M E N T W H E N
TROUBLESHOOTING THE SRS, DO NOT USE
ELECTRICAL TEST EQUIPMENT SUCH AS A
BATTERY±POWERED OR AC±POWERED
VOLTMETER, OHMMETER, ETC., OR ANY TYPE OF
ELECTRICAL EQUIPMENT OTHER THAN THAT
SPECIFIED IN THIS MANUAL. DO NOT USE A
NON±POWERED PROVE±TYPE TESTER.
INSTRUCTIONS IN THIS MANUAL MUST BE
FOLLOWED CAREFULLY, OTHERWISE PERSONAL
INJURY MAY RESULT.
Diagnostic Trouble Codes
The ªSRS Diagnostic System Checkº must always be the
starting point of any SRS diagnosis. The ªSRS
Diagnostic System Checkº checks for proper ªAIR BAGº
warning lamp operation and checks for SRS diagnostic
trouble codes using the scan tool.
1. Current diagnostic trouble codes ± Malfunctions that
are presently being detected. Current diagnostic
trouble codes are stored in RAM (Random Access
Memory).
2. History diagnostic trouble codes ± All malfunctions
detected since the last time the history memory was
cleared. History diagnostic trouble codes are stored
in EEPROM.
Scan Tool Diagnostics
A scan tool is used to read current and history diagnostic
trouble codes and to clear all diagnostic trouble codes
after a repair is completed. The scan tool must be
updated to communicate with the SRS through a
replaceable cartridge before it can be used for SRS
diagnostics. To use the scan tool, connect it to the data
link connector and turn the ignition switch ªONº. The scan
Page 2022 of 2100

SUPPLEMENTAL RESTRAINT SYSTEM 9J±8
tool reads serial data from the SDM ªSerial Dataº line
terminal ª24º to the data link connector terminal ª9º.
Use of Special Tools
WARNING: T O AV O I D D E P L O Y M E N T W H E N
TROUBLESHOOTING THE SRS, DO NOT USE
ELECTRICAL TEST EQUIPMENT SUCH AS A
BATTERY±POWERED OR AC±POWERED
VOLTMETER, OHMMETER, ETC, OR ANY TYPE OF
ELECTRICAL EQUIPMENT OTHER THAN THAT
SPECIFIED IN THIS MANUAL. DO NOT USE A NON
POWERED PROVE±TYPE TESTER. INSTRUCTIONSIN THIS MANUAL MUST BE FOLLOWED
CAREFULLY, OTHERWISE PERSONAL INJURY MAY
RESULT. YOU SHOULD BE FAMILIAR WITH THE
TOOLS LISTED IN THIS SECTION UNDER THE
HANDLING SRS SPECIAL TOOLS.
You should be able to measure voltage and resistance.
You should be familiar with proper use of a scan tool such
as the Tech 2 Diagnostic Computer, SRS
Driver/Passenger Load Tool J±41433, Connector Test
Adapter Kit J±35616±A, and the DVM (Digital Multimeter)
J±39200.
SRS Connector Body Face Views
D09RW003
Legend
(1) SDM
(2) Driver Air Bag Assembly
(3) Passenger Air Bag Assembly(4) ªAir Bagº Warning Lamp
(5) SRS Coil Assembly
(6) DLC
Repairs and Inspections Required
After an Accident
NOTE: If any SRS components are damaged, they must
be replaced. If SRS component mounting points are
damaged, they must be replaced.
Never use SRS parts from another vehicle. This does
not include remanufactured parts purchased from an
authorized dealer; they may be used for SRS repairs.Do not attempt to service the SDM, the SRS coil
assembly, or the air bag assembly. Service of these
items is by replacement only.
Verify the part number of replacement air bag
assembly.
CAUTION: Never use the air bag assembly from
another vehicle and difference model year air bag
assembly.
The air bag assembly has identification colors on the
bar code label as follows.
Page 2023 of 2100
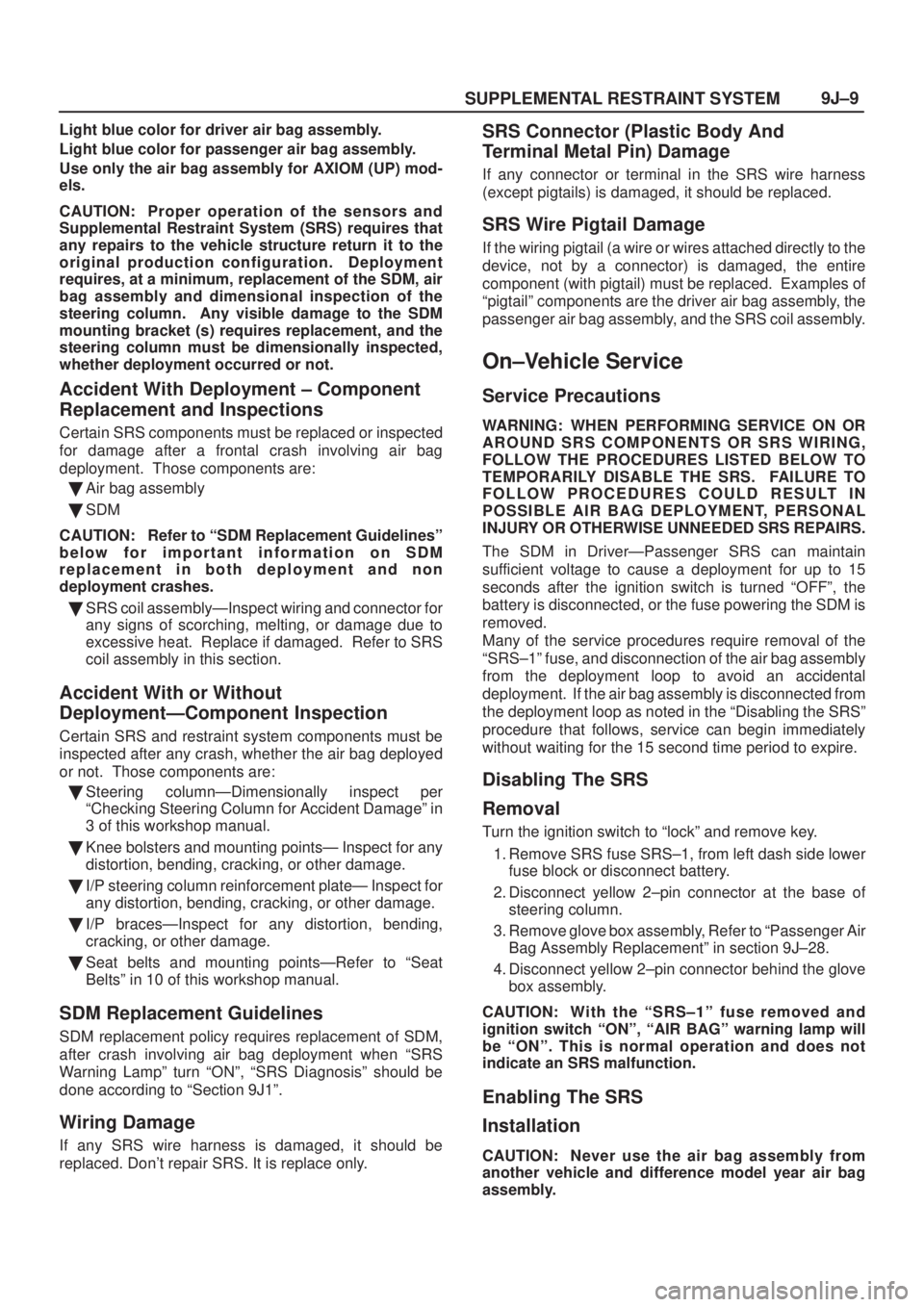
SUPPLEMENTAL RESTRAINT SYSTEM9J±9
Light blue color for driver air bag assembly.
Light blue color for passenger air bag assembly.
Use only the air bag assembly for AXIOM (UP) mod-
els.
CAUTION: Proper operation of the sensors and
Supplemental Restraint System (SRS) requires that
any repairs to the vehicle structure return it to the
original production configuration. Deployment
requires, at a minimum, replacement of the SDM, air
bag assembly and dimensional inspection of the
steering column. Any visible damage to the SDM
mounting bracket (s) requires replacement, and the
steering column must be dimensionally inspected,
whether deployment occurred or not.
Accident With Deployment ± Component
Replacement and Inspections
Certain SRS components must be replaced or inspected
for damage after a frontal crash involving air bag
deployment. Those components are:
Air bag assembly
SDM
CAUTION: Refer to ªSDM Replacement Guidelinesº
below for important information on SDM
replacement in both deployment and non
deployment crashes.
SRS coil assemblyÐInspect wiring and connector for
any signs of scorching, melting, or damage due to
excessive heat. Replace if damaged. Refer to SRS
coil assembly in this section.
Accident With or Without
DeploymentÐComponent Inspection
Certain SRS and restraint system components must be
inspected after any crash, whether the air bag deployed
or not. Those components are:
Steering columnÐDimensionally inspect per
ªChecking Steering Column for Accident Damageº in
3 of this workshop manual.
Knee bolsters and mounting pointsÐ Inspect for any
distortion, bending, cracking, or other damage.
I/P steering column reinforcement plateÐ Inspect for
any distortion, bending, cracking, or other damage.
I/P bracesÐInspect for any distortion, bending,
cracking, or other damage.
Seat belts and mounting pointsÐRefer to ªSeat
Beltsº in 10 of this workshop manual.
SDM Replacement Guidelines
SDM replacement policy requires replacement of SDM,
after crash involving air bag deployment when ªSRS
Warning Lampº turn ªONº, ªSRS Diagnosisº should be
done according to ªSection 9J1º.
Wiring Damage
If any SRS wire harness is damaged, it should be
replaced. Don't repair SRS. It is replace only.
SRS Connector (Plastic Body And
Terminal Metal Pin) Damage
If any connector or terminal in the SRS wire harness
(except pigtails) is damaged, it should be replaced.
SRS Wire Pigtail Damage
If the wiring pigtail (a wire or wires attached directly to the
device, not by a connector) is damaged, the entire
component (with pigtail) must be replaced. Examples of
ªpigtailº components are the driver air bag assembly, the
passenger air bag assembly, and the SRS coil assembly.
On±Vehicle Service
Service Precautions
WARNING: WHEN PERFORMING SERVICE ON OR
AROUND SRS COMPONENTS OR SRS WIRING,
FOLLOW THE PROCEDURES LISTED BELOW TO
TEMPORARILY DISABLE THE SRS. FAILURE TO
FOLLOW PROCEDURES COULD RESULT IN
POSSIBLE AIR BAG DEPLOYMENT, PERSONAL
INJURY OR OTHERWISE UNNEEDED SRS REPAIRS.
The SDM in DriverÐPassenger SRS can maintain
sufficient voltage to cause a deployment for up to 15
seconds after the ignition switch is turned ªOFFº, the
battery is disconnected, or the fuse powering the SDM is
removed.
Many of the service procedures require removal of the
ªSRS±1º fuse, and disconnection of the air bag assembly
from the deployment loop to avoid an accidental
deployment. If the air bag assembly is disconnected from
the deployment loop as noted in the ªDisabling the SRSº
procedure that follows, service can begin immediately
without waiting for the 15 second time period to expire.
Disabling The SRS
Removal
Turn the ignition switch to ªlockº and remove key.
1. Remove SRS fuse SRS±1, from left dash side lower
fuse block or disconnect battery.
2. Disconnect yellow 2±pin connector at the base of
steering column.
3. Remove glove box assembly, Refer to ªPassenger Air
Bag Assembly Replacementº in section 9J±28.
4. Disconnect yellow 2±pin connector behind the glove
box assembly.
CAUTION: With the ªSRS±1º fuse removed and
ignition switch ªONº, ªAIR BAGº warning lamp will
be ªONº. This is normal operation and does not
indicate an SRS malfunction.
Enabling The SRS
Installation
CAUTION: Never use the air bag assembly from
another vehicle and difference model year air bag
assembly.
Page 2024 of 2100
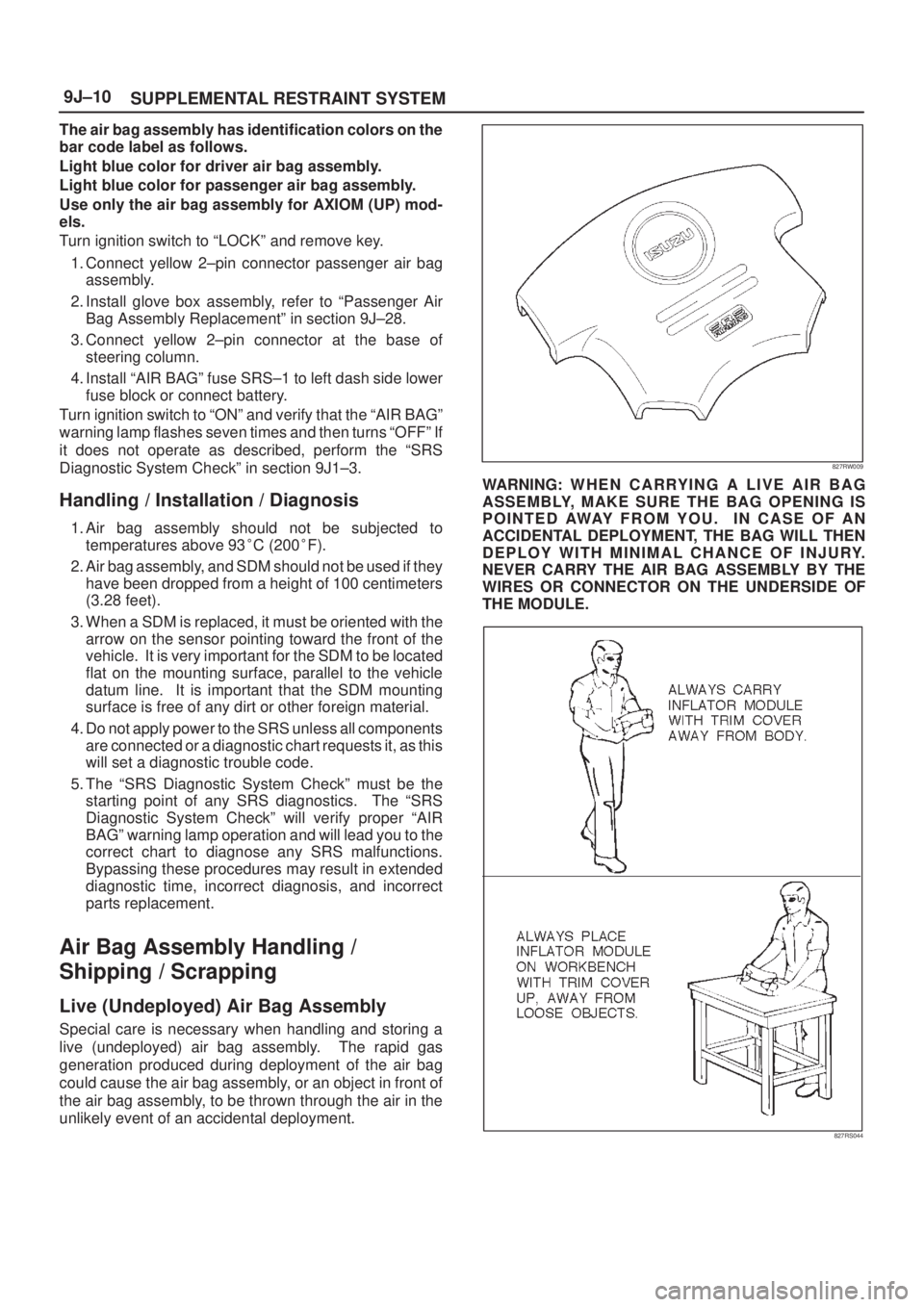
SUPPLEMENTAL RESTRAINT SYSTEM 9J±10
The air bag assembly has identification colors on the
bar code label as follows.
Light blue color for driver air bag assembly.
Light blue color for passenger air bag assembly.
Use only the air bag assembly for AXIOM (UP) mod-
els.
Turn ignition switch to ªLOCKº and remove key.
1. Connect yellow 2±pin connector passenger air bag
assembly.
2. Install glove box assembly, refer to ªPassenger Air
Bag Assembly Replacementº in section 9J±28.
3. Connect yellow 2±pin connector at the base of
steering column.
4. Install ªAIR BAGº fuse SRS±1 to left dash side lower
fuse block or connect battery.
Turn ignition switch to ªONº and verify that the ªAIR BAGº
warning lamp flashes seven times and then turns ªOFFº If
it does not operate as described, perform the ªSRS
Diagnostic System Checkº in section 9J1±3.
Handling / Installation / Diagnosis
1. Air bag assembly should not be subjected to
temperatures above 93C (200F).
2. Air bag assembly, and SDM should not be used if they
have been dropped from a height of 100 centimeters
(3.28 feet).
3. When a SDM is replaced, it must be oriented with the
arrow on the sensor pointing toward the front of the
vehicle. It is very important for the SDM to be located
flat on the mounting surface, parallel to the vehicle
datum line. It is important that the SDM mounting
surface is free of any dirt or other foreign material.
4. Do not apply power to the SRS unless all components
are connected or a diagnostic chart requests it, as this
will set a diagnostic trouble code.
5. The ªSRS Diagnostic System Checkº must be the
starting point of any SRS diagnostics. The ªSRS
Diagnostic System Checkº will verify proper ªAIR
BAGº warning lamp operation and will lead you to the
correct chart to diagnose any SRS malfunctions.
Bypassing these procedures may result in extended
diagnostic time, incorrect diagnosis, and incorrect
parts replacement.
Air Bag Assembly Handling /
Shipping / Scrapping
Live (Undeployed) Air Bag Assembly
Special care is necessary when handling and storing a
live (undeployed) air bag assembly. The rapid gas
generation produced during deployment of the air bag
could cause the air bag assembly, or an object in front of
the air bag assembly, to be thrown through the air in the
unlikely event of an accidental deployment.
827RW009
WARNING: W H E N C A R RY I N G A L I V E A I R B A G
ASSEMBLY, MAKE SURE THE BAG OPENING IS
POINTED AWAY FROM YOU. IN CASE OF AN
ACCIDENTAL DEPLOYMENT, THE BAG WILL THEN
DEPLOY WITH MINIMAL CHANCE OF INJURY.
NEVER CARRY THE AIR BAG ASSEMBLY BY THE
WIRES OR CONNECTOR ON THE UNDERSIDE OF
THE MODULE.
827RS044
Page 2025 of 2100
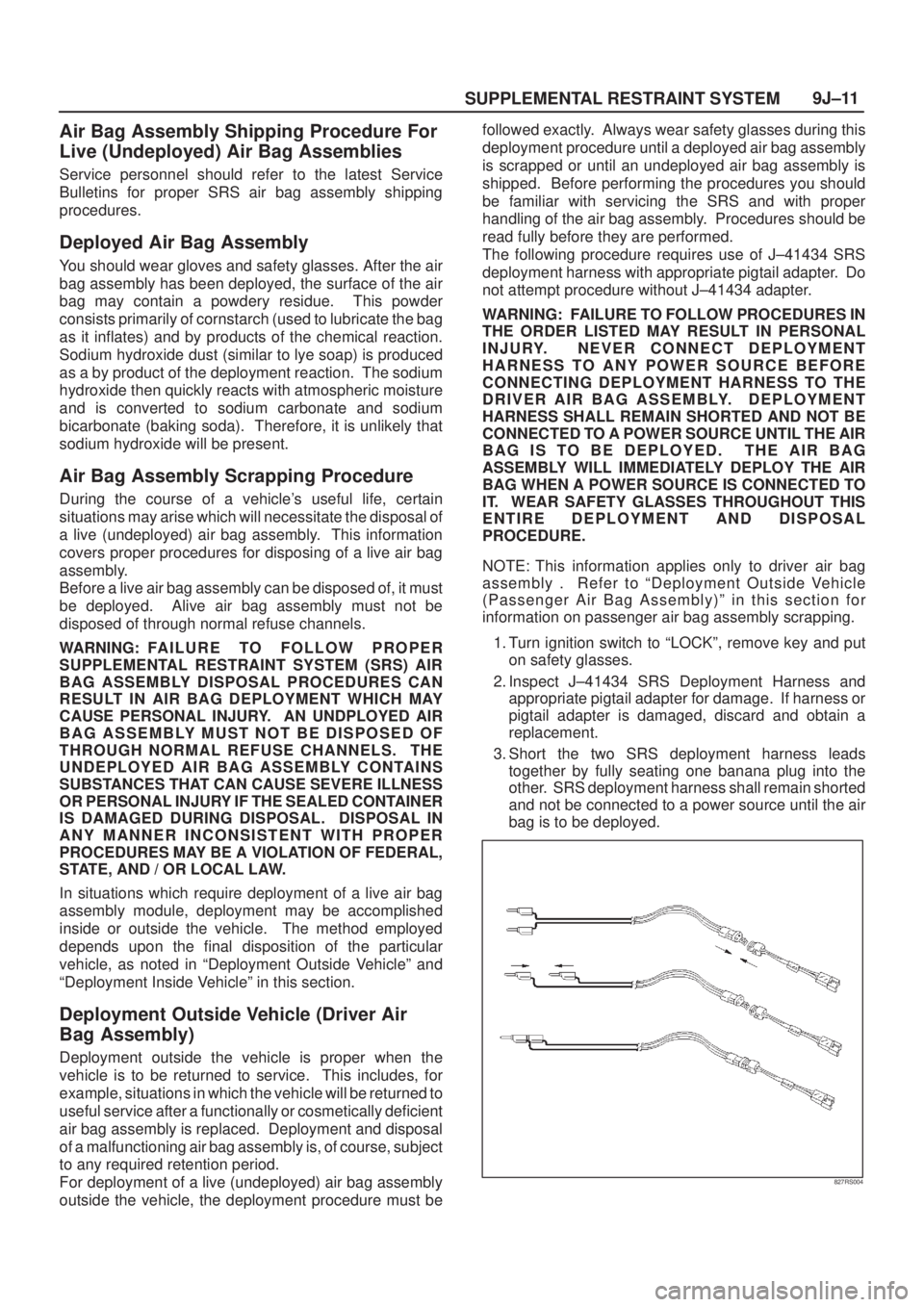
SUPPLEMENTAL RESTRAINT SYSTEM9J±11
Air Bag Assembly Shipping Procedure For
Live (Undeployed) Air Bag Assemblies
Service personnel should refer to the latest Service
Bulletins for proper SRS air bag assembly shipping
procedures.
Deployed Air Bag Assembly
You should wear gloves and safety glasses. After the air
bag assembly has been deployed, the surface of the air
bag may contain a powdery residue. This powder
consists primarily of cornstarch (used to lubricate the bag
as it inflates) and by products of the chemical reaction.
Sodium hydroxide dust (similar to lye soap) is produced
as a by product of the deployment reaction. The sodium
hydroxide then quickly reacts with atmospheric moisture
and is converted to sodium carbonate and sodium
bicarbonate (baking soda). Therefore, it is unlikely that
sodium hydroxide will be present.
Air Bag Assembly Scrapping Procedure
During the course of a vehicle's useful life, certain
situations may arise which will necessitate the disposal of
a live (undeployed) air bag assembly. This information
covers proper procedures for disposing of a live air bag
assembly.
Before a live air bag assembly can be disposed of, it must
be deployed. Alive air bag assembly must not be
disposed of through normal refuse channels.
WARNING: FA I L U R E T O F O L L O W P R O P E R
SUPPLEMENTAL RESTRAINT SYSTEM (SRS) AIR
BAG ASSEMBLY DISPOSAL PROCEDURES CAN
RESULT IN AIR BAG DEPLOYMENT WHICH MAY
CAUSE PERSONAL INJURY. AN UNDPLOYED AIR
BAG ASSEMBLY MUST NOT BE DISPOSED OF
THROUGH NORMAL REFUSE CHANNELS. THE
UNDEPLOYED AIR BAG ASSEMBLY CONTAINS
SUBSTANCES THAT CAN CAUSE SEVERE ILLNESS
OR PERSONAL INJURY IF THE SEALED CONTAINER
IS DAMAGED DURING DISPOSAL. DISPOSAL IN
ANY MANNER INCONSISTENT WITH PROPER
PROCEDURES MAY BE A VIOLATION OF FEDERAL,
STATE, AND / OR LOCAL LAW.
In situations which require deployment of a live air bag
assembly module, deployment may be accomplished
inside or outside the vehicle. The method employed
depends upon the final disposition of the particular
vehicle, as noted in ªDeployment Outside Vehicleº and
ªDeployment Inside Vehicleº in this section.
Deployment Outside Vehicle (Driver Air
Bag Assembly)
Deployment outside the vehicle is proper when the
vehicle is to be returned to service. This includes, for
example, situations in which the vehicle will be returned to
useful service after a functionally or cosmetically deficient
air bag assembly is replaced. Deployment and disposal
of a malfunctioning air bag assembly is, of course, subject
to any required retention period.
For deployment of a live (undeployed) air bag assembly
outside the vehicle, the deployment procedure must befollowed exactly. Always wear safety glasses during this
deployment procedure until a deployed air bag assembly
is scrapped or until an undeployed air bag assembly is
shipped. Before performing the procedures you should
be familiar with servicing the SRS and with proper
handling of the air bag assembly. Procedures should be
read fully before they are performed.
The following procedure requires use of J±41434 SRS
deployment harness with appropriate pigtail adapter. Do
not attempt procedure without J±41434 adapter.
WARNING: FAILURE TO FOLLOW PROCEDURES IN
THE ORDER LISTED MAY RESULT IN PERSONAL
INJURY. NEVER CONNECT DEPLOYMENT
HARNESS TO ANY POWER SOURCE BEFORE
CONNECTING DEPLOYMENT HARNESS TO THE
DRIVER AIR BAG ASSEMBLY. DEPLOYMENT
HARNESS SHALL REMAIN SHORTED AND NOT BE
CONNECTED TO A POWER SOURCE UNTIL THE AIR
BAG IS TO BE DEPLOYED. THE AIR BAG
ASSEMBLY WILL IMMEDIATELY DEPLOY THE AIR
BAG WHEN A POWER SOURCE IS CONNECTED TO
IT. WEAR SAFETY GLASSES THROUGHOUT THIS
ENTIRE DEPLOYMENT AND DISPOSAL
PROCEDURE.
NOTE: This information applies only to driver air bag
assembly . Refer to ªDeployment Outside Vehicle
(Passenger Air Bag Assembly)º in this section for
information on passenger air bag assembly scrapping.
1. Turn ignition switch to ªLOCKº, remove key and put
on safety glasses.
2. Inspect J±41434 SRS Deployment Harness and
appropriate pigtail adapter for damage. If harness or
pigtail adapter is damaged, discard and obtain a
replacement.
3. Short the two SRS deployment harness leads
together by fully seating one banana plug into the
other. SRS deployment harness shall remain shorted
and not be connected to a power source until the air
bag is to be deployed.
827RS004
Page 2026 of 2100
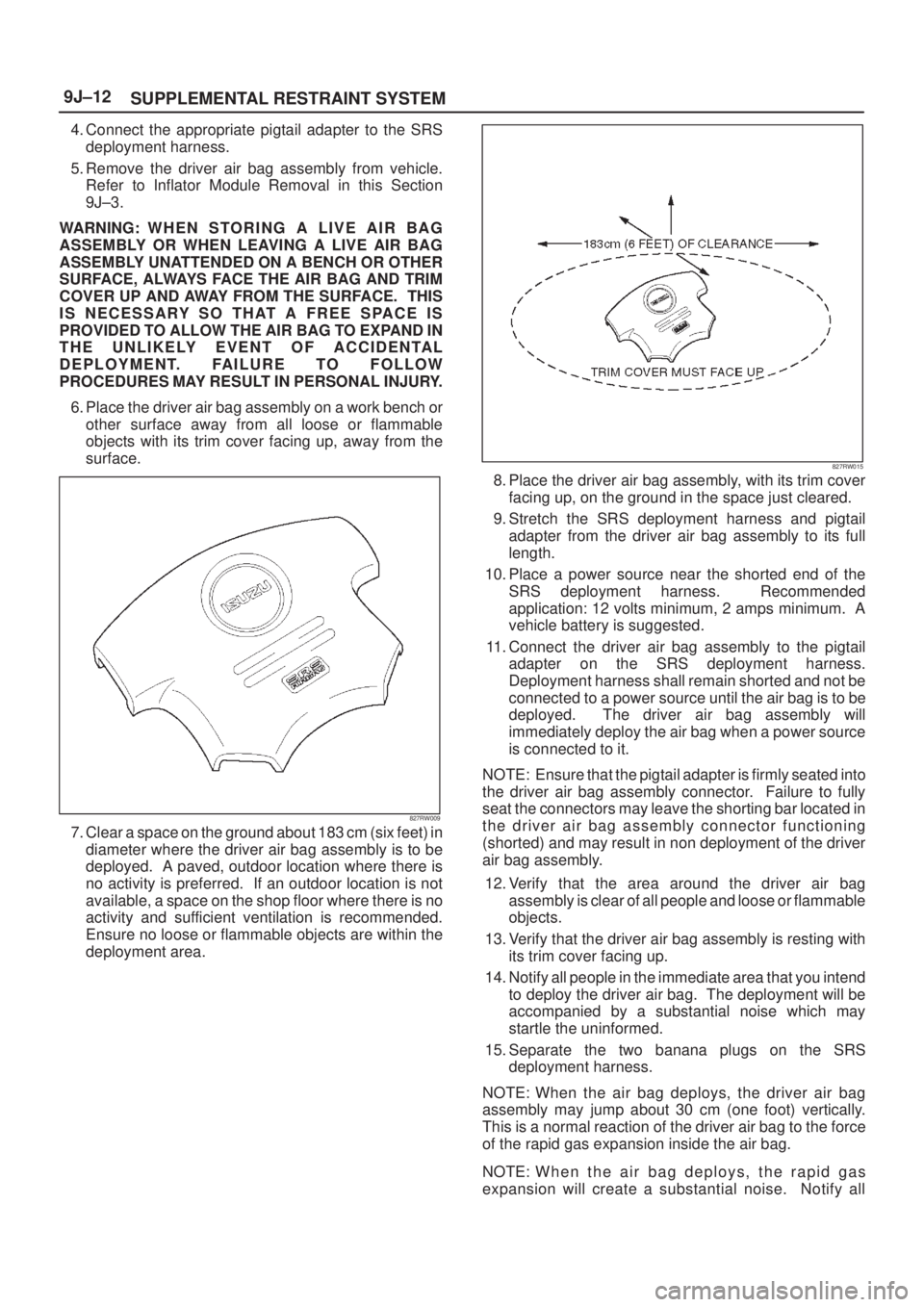
SUPPLEMENTAL RESTRAINT SYSTEM 9J±12
4. Connect the appropriate pigtail adapter to the SRS
deployment harness.
5. Remove the driver air bag assembly from vehicle.
Refer to Inflator Module Removal in this Section
9J±3.
WARNING: W H E N S T O R I N G A L I V E A I R B A G
ASSEMBLY OR WHEN LEAVING A LIVE AIR BAG
ASSEMBLY UNATTENDED ON A BENCH OR OTHER
SURFACE, ALWAYS FACE THE AIR BAG AND TRIM
COVER UP AND AWAY FROM THE SURFACE. THIS
IS NECESSARY SO THAT A FREE SPACE IS
PROVIDED TO ALLOW THE AIR BAG TO EXPAND IN
THE UNLIKELY EVENT OF ACCIDENTAL
DEPLOYMENT. FAILURE TO FOLLOW
PROCEDURES MAY RESULT IN PERSONAL INJURY.
6. Place the driver air bag assembly on a work bench or
other surface away from all loose or flammable
objects with its trim cover facing up, away from the
surface.
827RW009
7. Clear a space on the ground about 183 cm (six feet) in
diameter where the driver air bag assembly is to be
deployed. A paved, outdoor location where there is
no activity is preferred. If an outdoor location is not
available, a space on the shop floor where there is no
activity and sufficient ventilation is recommended.
Ensure no loose or flammable objects are within the
deployment area.
827RW015
8. Place the driver air bag assembly, with its trim cover
facing up, on the ground in the space just cleared.
9. Stretch the SRS deployment harness and pigtail
adapter from the driver air bag assembly to its full
length.
10. Place a power source near the shorted end of the
SRS deployment harness. Recommended
application: 12 volts minimum, 2 amps minimum. A
vehicle battery is suggested.
11. Connect the driver air bag assembly to the pigtail
adapter on the SRS deployment harness.
Deployment harness shall remain shorted and not be
connected to a power source until the air bag is to be
deployed. The driver air bag assembly will
immediately deploy the air bag when a power source
is connected to it.
NOTE: Ensure that the pigtail adapter is firmly seated into
the driver air bag assembly connector. Failure to fully
seat the connectors may leave the shorting bar located in
the driver air bag assembly connector functioning
(shorted) and may result in non deployment of the driver
air bag assembly.
12. Verify that the area around the driver air bag
assembly is clear of all people and loose or flammable
objects.
13. Verify that the driver air bag assembly is resting with
its trim cover facing up.
14. Notify all people in the immediate area that you intend
to deploy the driver air bag. The deployment will be
accompanied by a substantial noise which may
startle the uninformed.
15. Separate the two banana plugs on the SRS
deployment harness.
NOTE: When the air bag deploys, the driver air bag
assembly may jump about 30 cm (one foot) vertically.
This is a normal reaction of the driver air bag to the force
of the rapid gas expansion inside the air bag.
NOTE: W h e n t h e a i r b a g deploys, the rapid gas
expansion will create a substantial noise. Notify all
Page 2027 of 2100
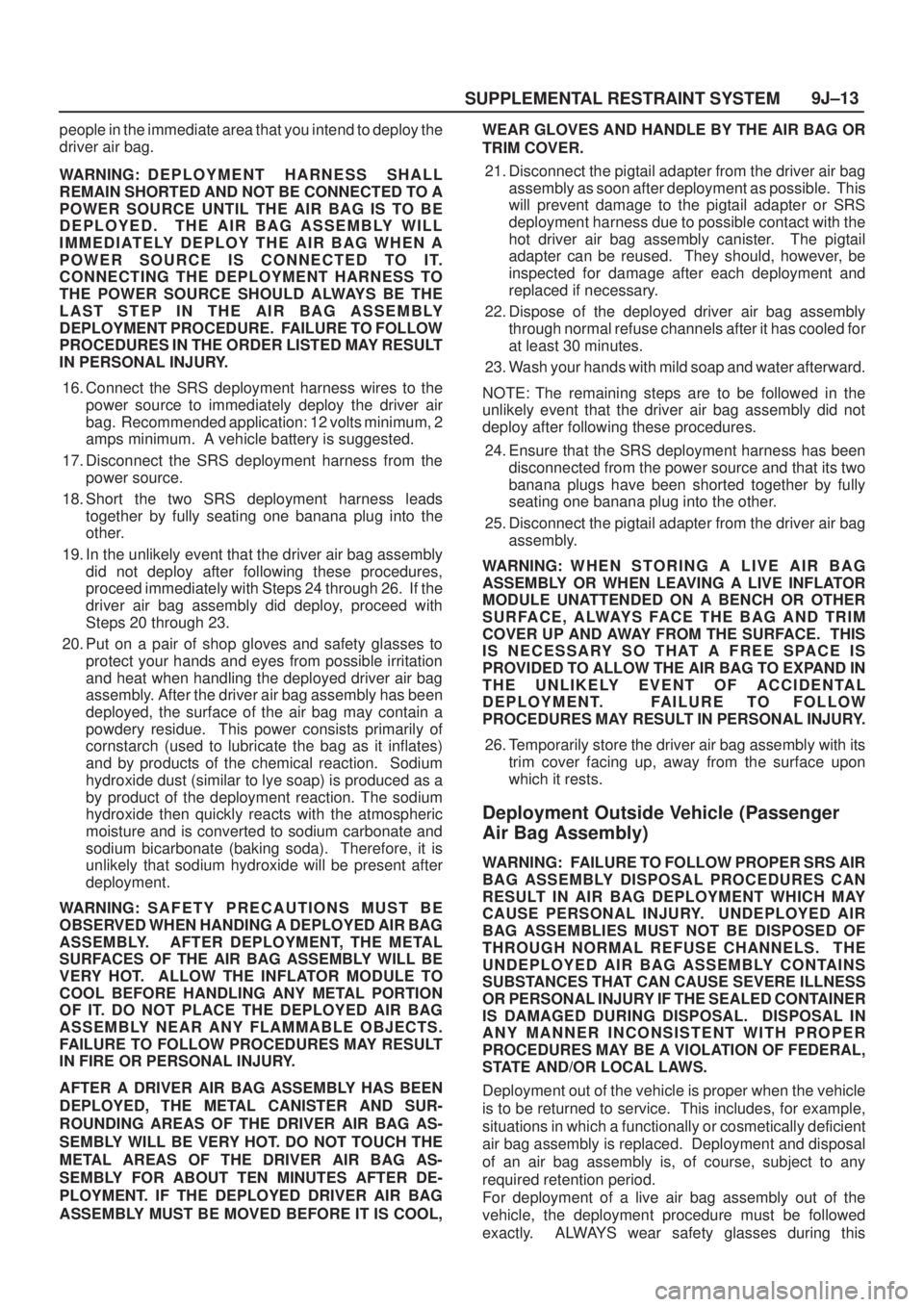
SUPPLEMENTAL RESTRAINT SYSTEM9J±13
people in the immediate area that you intend to deploy the
driver air bag.
WARNING: D E P L O Y M E N T HARNESS SHALL
REMAIN SHORTED AND NOT BE CONNECTED TO A
POWER SOURCE UNTIL THE AIR BAG IS TO BE
DEPLOYED. THE AIR BAG ASSEMBLY WILL
IMMEDIATELY DEPLOY THE AIR BAG WHEN A
POWER SOURCE IS CONNECTED TO IT.
CONNECTING THE DEPLOYMENT HARNESS TO
THE POWER SOURCE SHOULD ALWAYS BE THE
LAST STEP IN THE AIR BAG ASSEMBLY
DEPLOYMENT PROCEDURE. FAILURE TO FOLLOW
PROCEDURES IN THE ORDER LISTED MAY RESULT
IN PERSONAL INJURY.
16. Connect the SRS deployment harness wires to the
power source to immediately deploy the driver air
bag. Recommended application: 12 volts minimum, 2
amps minimum. A vehicle battery is suggested.
17. Disconnect the SRS deployment harness from the
power source.
18. Short the two SRS deployment harness leads
together by fully seating one banana plug into the
other.
19. In the unlikely event that the driver air bag assembly
did not deploy after following these procedures,
proceed immediately with Steps 24 through 26. If the
driver air bag assembly did deploy, proceed with
Steps 20 through 23.
20. Put on a pair of shop gloves and safety glasses to
protect your hands and eyes from possible irritation
and heat when handling the deployed driver air bag
assembly. After the driver air bag assembly has been
deployed, the surface of the air bag may contain a
powdery residue. This power consists primarily of
cornstarch (used to lubricate the bag as it inflates)
and by products of the chemical reaction. Sodium
hydroxide dust (similar to lye soap) is produced as a
by product of the deployment reaction. The sodium
hydroxide then quickly reacts with the atmospheric
moisture and is converted to sodium carbonate and
sodium bicarbonate (baking soda). Therefore, it is
unlikely that sodium hydroxide will be present after
deployment.
WARNING: S A F E T Y P R ECAUTIONS MUST BE
OBSERVED WHEN HANDING A DEPLOYED AIR BAG
ASSEMBLY. AFTER DEPLOYMENT, THE METAL
SURFACES OF THE AIR BAG ASSEMBLY WILL BE
VERY HOT. ALLOW THE INFLATOR MODULE TO
COOL BEFORE HANDLING ANY METAL PORTION
OF IT. DO NOT PLACE THE DEPLOYED AIR BAG
ASSEMBLY NEAR ANY FLAMMABLE OBJECTS.
FAILURE TO FOLLOW PROCEDURES MAY RESULT
IN FIRE OR PERSONAL INJURY.
AFTER A DRIVER AIR BAG ASSEMBLY HAS BEEN
DEPLOYED, THE METAL CANISTER AND SUR-
ROUNDING AREAS OF THE DRIVER AIR BAG AS-
SEMBLY WILL BE VERY HOT. DO NOT TOUCH THE
METAL AREAS OF THE DRIVER AIR BAG AS-
SEMBLY FOR ABOUT TEN MINUTES AFTER DE-
PLOYMENT. IF THE DEPLOYED DRIVER AIR BAG
ASSEMBLY MUST BE MOVED BEFORE IT IS COOL,WEAR GLOVES AND HANDLE BY THE AIR BAG OR
TRIM COVER.
21. Disconnect the pigtail adapter from the driver air bag
assembly as soon after deployment as possible. This
will prevent damage to the pigtail adapter or SRS
deployment harness due to possible contact with the
hot driver air bag assembly canister. The pigtail
adapter can be reused. They should, however, be
inspected for damage after each deployment and
replaced if necessary.
22. Dispose of the deployed driver air bag assembly
through normal refuse channels after it has cooled for
at least 30 minutes.
23. Wash your hands with mild soap and water afterward.
NOTE: The remaining steps are to be followed in the
unlikely event that the driver air bag assembly did not
deploy after following these procedures.
24. Ensure that the SRS deployment harness has been
disconnected from the power source and that its two
banana plugs have been shorted together by fully
seating one banana plug into the other.
25. Disconnect the pigtail adapter from the driver air bag
assembly.
WARNING: W H E N S T O R I N G A L I V E A I R B A G
ASSEMBLY OR WHEN LEAVING A LIVE INFLATOR
MODULE UNATTENDED ON A BENCH OR OTHER
S U R FA C E , A LWAY S FA C E T H E B A G A N D T R I M
COVER UP AND AWAY FROM THE SURFACE. THIS
IS NECESSARY SO THAT A FREE SPACE IS
PROVIDED TO ALLOW THE AIR BAG TO EXPAND IN
THE UNLIKELY EVENT OF ACCIDENTAL
DEPLOYMENT. FAILURE TO FOLLOW
PROCEDURES MAY RESULT IN PERSONAL INJURY.
26. Temporarily store the driver air bag assembly with its
trim cover facing up, away from the surface upon
which it rests.
Deployment Outside Vehicle (Passenger
Air Bag Assembly)
WARNING: FAILURE TO FOLLOW PROPER SRS AIR
BAG ASSEMBLY DISPOSAL PROCEDURES CAN
RESULT IN AIR BAG DEPLOYMENT WHICH MAY
CAUSE PERSONAL INJURY. UNDEPLOYED AIR
BAG ASSEMBLIES MUST NOT BE DISPOSED OF
THROUGH NORMAL REFUSE CHANNELS. THE
UNDEPLOYED AIR BAG ASSEMBLY CONTAINS
SUBSTANCES THAT CAN CAUSE SEVERE ILLNESS
OR PERSONAL INJURY IF THE SEALED CONTAINER
IS DAMAGED DURING DISPOSAL. DISPOSAL IN
ANY MANNER INCONSISTENT WITH PROPER
PROCEDURES MAY BE A VIOLATION OF FEDERAL,
STATE AND/OR LOCAL LAWS.
Deployment out of the vehicle is proper when the vehicle
is to be returned to service. This includes, for example,
situations in which a functionally or cosmetically deficient
air bag assembly is replaced. Deployment and disposal
of an air bag assembly is, of course, subject to any
required retention period.
For deployment of a live air bag assembly out of the
vehicle, the deployment procedure must be followed
exactly. ALWAYS wear safety glasses during this
Page 2028 of 2100
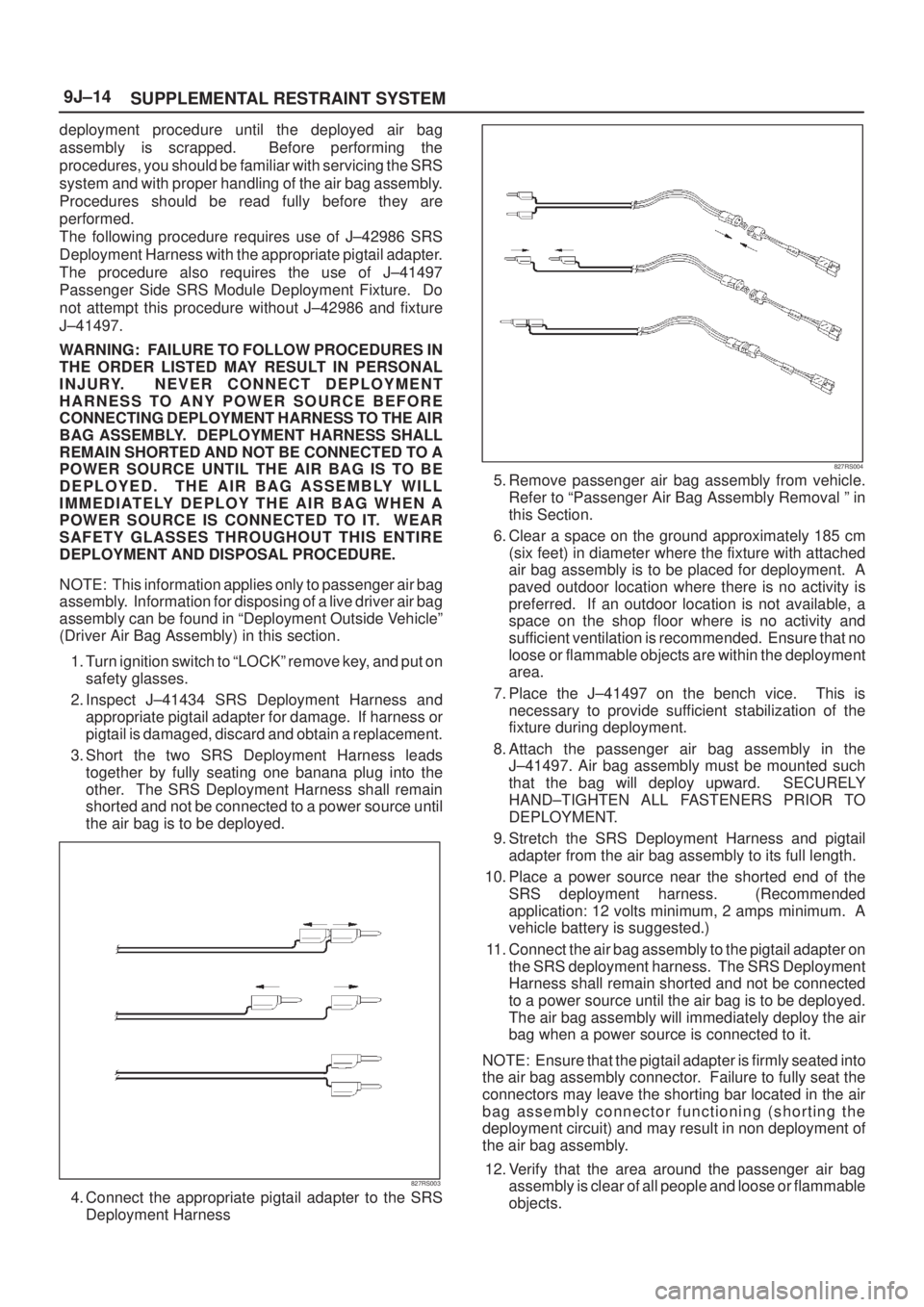
SUPPLEMENTAL RESTRAINT SYSTEM 9J±14
deployment procedure until the deployed air bag
assembly is scrapped. Before performing the
procedures, you should be familiar with servicing the SRS
system and with proper handling of the air bag assembly.
Procedures should be read fully before they are
performed.
The following procedure requires use of J±42986 SRS
Deployment Harness with the appropriate pigtail adapter.
The procedure also requires the use of J±41497
Passenger Side SRS Module Deployment Fixture. Do
not attempt this procedure without J±42986 and fixture
J±41497.
WARNING: FAILURE TO FOLLOW PROCEDURES IN
THE ORDER LISTED MAY RESULT IN PERSONAL
INJURY. NEVER CONNECT DEPLOYMENT
HARNESS TO ANY POWER SOURCE BEFORE
CONNECTING DEPLOYMENT HARNESS TO THE AIR
BAG ASSEMBLY. DEPLOYMENT HARNESS SHALL
REMAIN SHORTED AND NOT BE CONNECTED TO A
POWER SOURCE UNTIL THE AIR BAG IS TO BE
DEPLOYED. THE AIR BAG ASSEMBLY WILL
IMMEDIATELY DEPLOY THE AIR BAG WHEN A
POWER SOURCE IS CONNECTED TO IT. WEAR
SAFETY GLASSES THROUGHOUT THIS ENTIRE
DEPLOYMENT AND DISPOSAL PROCEDURE.
NOTE: This information applies only to passenger air bag
assembly. Information for disposing of a live driver air bag
assembly can be found in ªDeployment Outside Vehicleº
(Driver Air Bag Assembly) in this section.
1. Turn ignition switch to ªLOCKº remove key, and put on
safety glasses.
2. Inspect J±41434 SRS Deployment Harness and
appropriate pigtail adapter for damage. If harness or
pigtail is damaged, discard and obtain a replacement.
3. Short the two SRS Deployment Harness leads
together by fully seating one banana plug into the
other. The SRS Deployment Harness shall remain
shorted and not be connected to a power source until
the air bag is to be deployed.
827RS003
4. Connect the appropriate pigtail adapter to the SRS
Deployment Harness
827RS004
5. Remove passenger air bag assembly from vehicle.
Refer to ªPassenger Air Bag Assembly Removal º in
this Section.
6. Clear a space on the ground approximately 185 cm
(six feet) in diameter where the fixture with attached
air bag assembly is to be placed for deployment. A
paved outdoor location where there is no activity is
preferred. If an outdoor location is not available, a
space on the shop floor where is no activity and
sufficient ventilation is recommended. Ensure that no
loose or flammable objects are within the deployment
area.
7. Place the J±41497 on the bench vice. This is
necessary to provide sufficient stabilization of the
fixture during deployment.
8. Attach the passenger air bag assembly in the
J±41497. Air bag assembly must be mounted such
that the bag will deploy upward. SECURELY
HAND±TIGHTEN ALL FASTENERS PRIOR TO
DEPLOYMENT.
9. Stretch the SRS Deployment Harness and pigtail
adapter from the air bag assembly to its full length.
10. Place a power source near the shorted end of the
SRS deployment harness. (Recommended
application: 12 volts minimum, 2 amps minimum. A
vehicle battery is suggested.)
11. Connect the air bag assembly to the pigtail adapter on
the SRS deployment harness. The SRS Deployment
Harness shall remain shorted and not be connected
to a power source until the air bag is to be deployed.
The air bag assembly will immediately deploy the air
bag when a power source is connected to it.
NOTE: Ensure that the pigtail adapter is firmly seated into
the air bag assembly connector. Failure to fully seat the
connectors may leave the shorting bar located in the air
bag assembly connector functioning (shorting the
deployment circuit) and may result in non deployment of
the air bag assembly.
12. Verify that the area around the passenger air bag
assembly is clear of all people and loose or flammable
objects.
Page 2029 of 2100
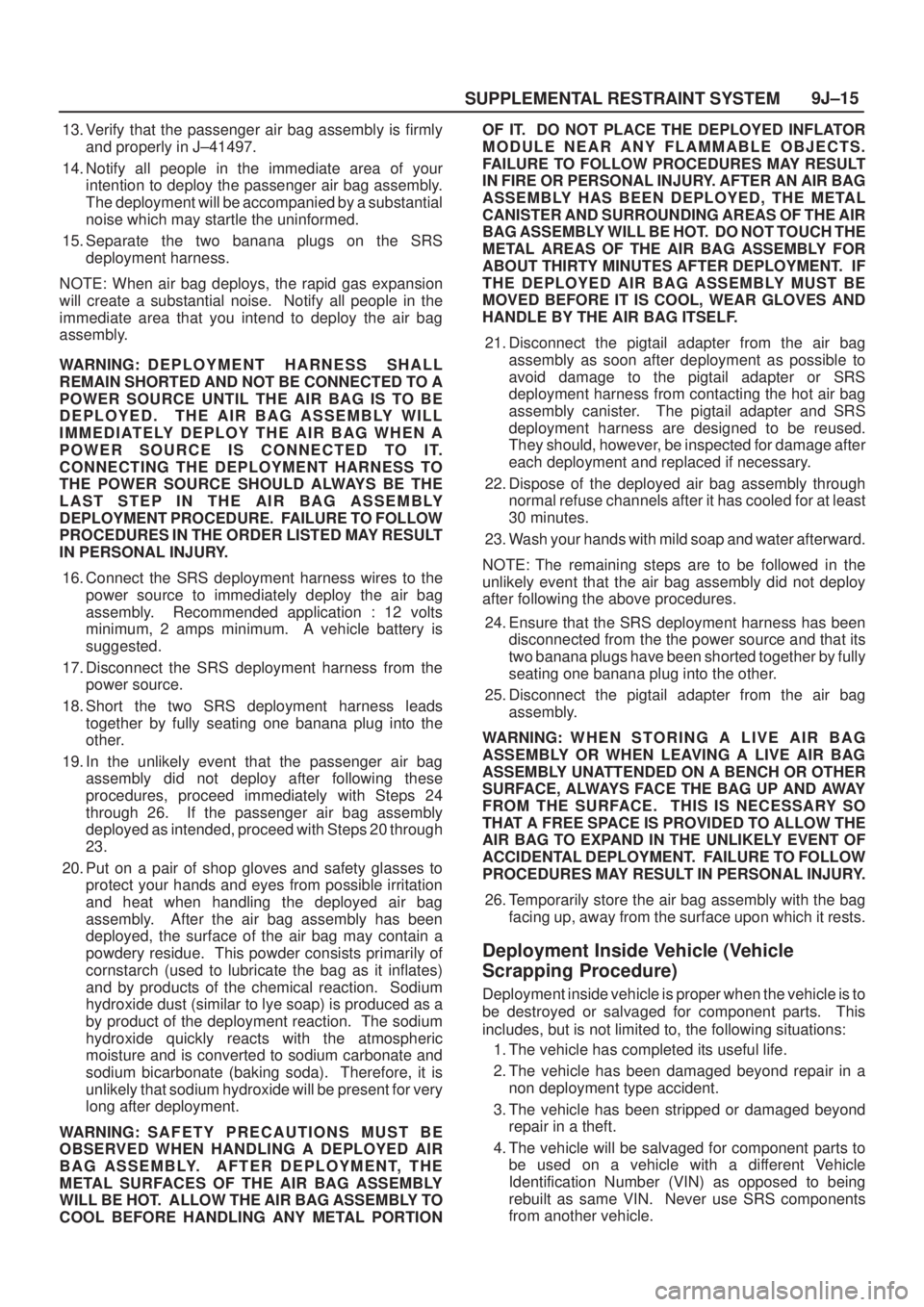
SUPPLEMENTAL RESTRAINT SYSTEM9J±15
13. Verify that the passenger air bag assembly is firmly
and properly in J±41497.
14. Notify all people in the immediate area of your
intention to deploy the passenger air bag assembly.
The deployment will be accompanied by a substantial
noise which may startle the uninformed.
15. Separate the two banana plugs on the SRS
deployment harness.
NOTE: When air bag deploys, the rapid gas expansion
will create a substantial noise. Notify all people in the
immediate area that you intend to deploy the air bag
assembly.
WARNING: D E P L O Y M E N T HARNESS SHALL
REMAIN SHORTED AND NOT BE CONNECTED TO A
POWER SOURCE UNTIL THE AIR BAG IS TO BE
DEPLOYED. THE AIR BAG ASSEMBLY WILL
IMMEDIATELY DEPLOY THE AIR BAG WHEN A
POWER SOURCE IS CONNECTED TO IT.
CONNECTING THE DEPLOYMENT HARNESS TO
THE POWER SOURCE SHOULD ALWAYS BE THE
LAST STEP IN THE AIR BAG ASSEMBLY
DEPLOYMENT PROCEDURE. FAILURE TO FOLLOW
PROCEDURES IN THE ORDER LISTED MAY RESULT
IN PERSONAL INJURY.
16. Connect the SRS deployment harness wires to the
power source to immediately deploy the air bag
assembly. Recommended application : 12 volts
minimum, 2 amps minimum. A vehicle battery is
suggested.
17. Disconnect the SRS deployment harness from the
power source.
18. Short the two SRS deployment harness leads
together by fully seating one banana plug into the
other.
19. In the unlikely event that the passenger air bag
assembly did not deploy after following these
procedures, proceed immediately with Steps 24
through 26. If the passenger air bag assembly
deployed as intended, proceed with Steps 20 through
23.
20. Put on a pair of shop gloves and safety glasses to
protect your hands and eyes from possible irritation
and heat when handling the deployed air bag
assembly. After the air bag assembly has been
deployed, the surface of the air bag may contain a
powdery residue. This powder consists primarily of
cornstarch (used to lubricate the bag as it inflates)
and by products of the chemical reaction. Sodium
hydroxide dust (similar to lye soap) is produced as a
by product of the deployment reaction. The sodium
hydroxide quickly reacts with the atmospheric
moisture and is converted to sodium carbonate and
sodium bicarbonate (baking soda). Therefore, it is
unlikely that sodium hydroxide will be present for very
long after deployment.
WARNING: S A F E T Y P R ECAUTIONS MUST BE
OBSERVED WHEN HANDLING A DEPLOYED AIR
BAG ASSEMBLY. AFTER DEPLOYMENT, THE
METAL SURFACES OF THE AIR BAG ASSEMBLY
WILL BE HOT. ALLOW THE AIR BAG ASSEMBLY TO
COOL BEFORE HANDLING ANY METAL PORTIONOF IT. DO NOT PLACE THE DEPLOYED INFLATOR
MODULE NEAR ANY FLAMMABLE OBJECTS.
FAILURE TO FOLLOW PROCEDURES MAY RESULT
IN FIRE OR PERSONAL INJURY. AFTER AN AIR BAG
ASSEMBLY HAS BEEN DEPLOYED, THE METAL
CANISTER AND SURROUNDING AREAS OF THE AIR
BAG ASSEMBLY WILL BE HOT. DO NOT TOUCH THE
METAL AREAS OF THE AIR BAG ASSEMBLY FOR
ABOUT THIRTY MINUTES AFTER DEPLOYMENT. IF
THE DEPLOYED AIR BAG ASSEMBLY MUST BE
MOVED BEFORE IT IS COOL, WEAR GLOVES AND
HANDLE BY THE AIR BAG ITSELF.
21. Disconnect the pigtail adapter from the air bag
assembly as soon after deployment as possible to
avoid damage to the pigtail adapter or SRS
deployment harness from contacting the hot air bag
assembly canister. The pigtail adapter and SRS
deployment harness are designed to be reused.
They should, however, be inspected for damage after
each deployment and replaced if necessary.
22. Dispose of the deployed air bag assembly through
normal refuse channels after it has cooled for at least
30 minutes.
23. Wash your hands with mild soap and water afterward.
NOTE: The remaining steps are to be followed in the
unlikely event that the air bag assembly did not deploy
after following the above procedures.
24. Ensure that the SRS deployment harness has been
disconnected from the the power source and that its
two banana plugs have been shorted together by fully
seating one banana plug into the other.
25. Disconnect the pigtail adapter from the air bag
assembly.
WARNING: W H E N S T O R I N G A L I V E A I R B A G
ASSEMBLY OR WHEN LEAVING A LIVE AIR BAG
ASSEMBLY UNATTENDED ON A BENCH OR OTHER
SURFACE, ALWAYS FACE THE BAG UP AND AWAY
FROM THE SURFACE. THIS IS NECESSARY SO
THAT A FREE SPACE IS PROVIDED TO ALLOW THE
AIR BAG TO EXPAND IN THE UNLIKELY EVENT OF
ACCIDENTAL DEPLOYMENT. FAILURE TO FOLLOW
PROCEDURES MAY RESULT IN PERSONAL INJURY.
26. Temporarily store the air bag assembly with the bag
facing up, away from the surface upon which it rests.
Deployment Inside Vehicle (Vehicle
Scrapping Procedure)
Deployment inside vehicle is proper when the vehicle is to
be destroyed or salvaged for component parts. This
includes, but is not limited to, the following situations:
1. The vehicle has completed its useful life.
2. The vehicle has been damaged beyond repair in a
non deployment type accident.
3. The vehicle has been stripped or damaged beyond
repair in a theft.
4. The vehicle will be salvaged for component parts to
be used on a vehicle with a different Vehicle
Identification Number (VIN) as opposed to being
rebuilt as same VIN. Never use SRS components
from another vehicle.
Page 2030 of 2100
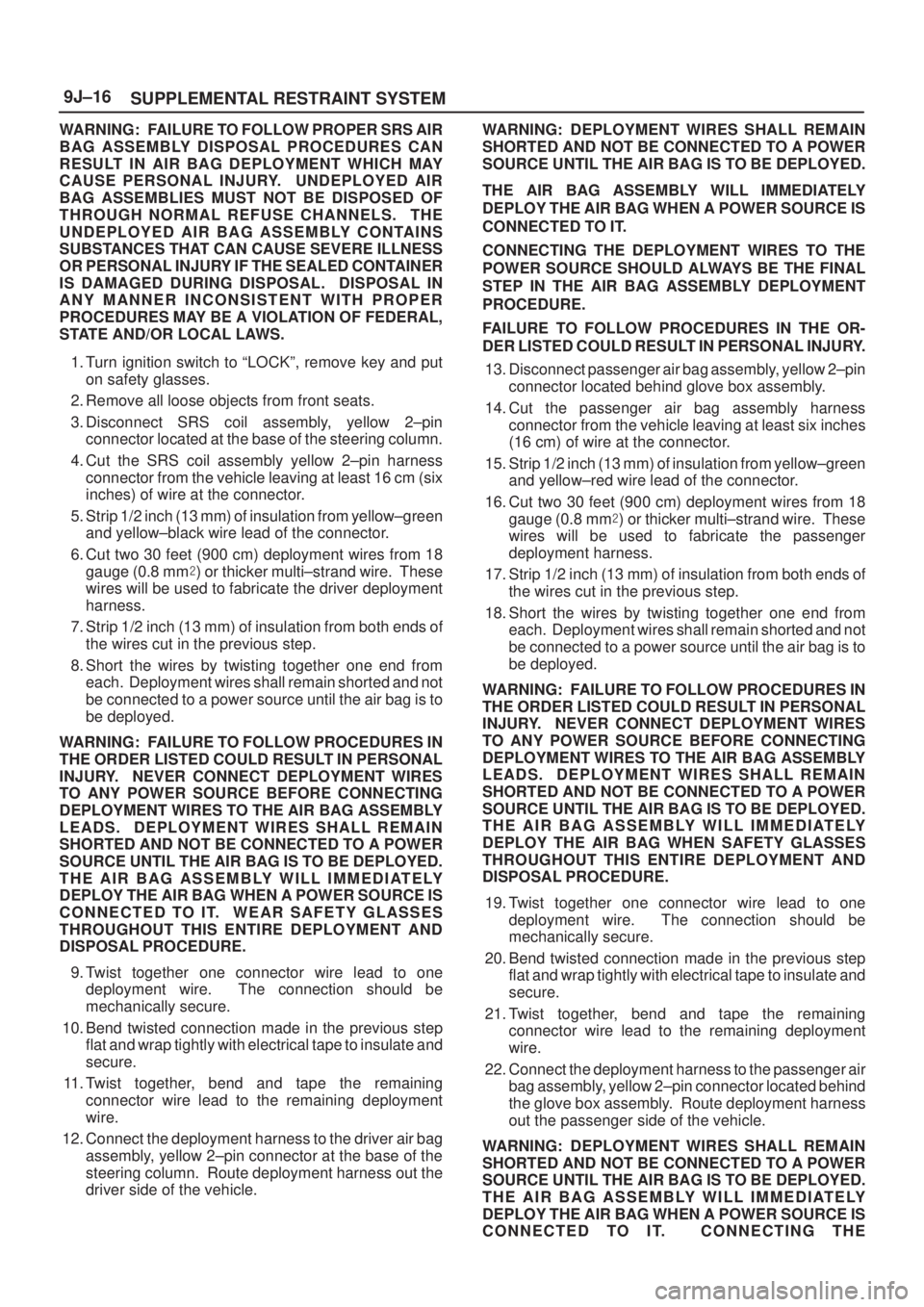
SUPPLEMENTAL RESTRAINT SYSTEM 9J±16
WARNING: FAILURE TO FOLLOW PROPER SRS AIR
BAG ASSEMBLY DISPOSAL PROCEDURES CAN
RESULT IN AIR BAG DEPLOYMENT WHICH MAY
CAUSE PERSONAL INJURY. UNDEPLOYED AIR
BAG ASSEMBLIES MUST NOT BE DISPOSED OF
THROUGH NORMAL REFUSE CHANNELS. THE
UNDEPLOYED AIR BAG ASSEMBLY CONTAINS
SUBSTANCES THAT CAN CAUSE SEVERE ILLNESS
OR PERSONAL INJURY IF THE SEALED CONTAINER
IS DAMAGED DURING DISPOSAL. DISPOSAL IN
ANY MANNER INCONSISTENT WITH PROPER
PROCEDURES MAY BE A VIOLATION OF FEDERAL,
STATE AND/OR LOCAL LAWS.
1. Turn ignition switch to ªLOCKº, remove key and put
on safety glasses.
2. Remove all loose objects from front seats.
3. Disconnect SRS coil assembly, yellow 2±pin
connector located at the base of the steering column.
4. Cut the SRS coil assembly yellow 2±pin harness
connector from the vehicle leaving at least 16 cm (six
inches) of wire at the connector.
5. Strip 1/2 inch (13 mm) of insulation from yellow±green
and yellow±black wire lead of the connector.
6. Cut two 30 feet (900 cm) deployment wires from 18
gauge (0.8 mm) or thicker multi±strand wire. These
wires will be used to fabricate the driver deployment
harness.
7. Strip 1/2 inch (13 mm) of insulation from both ends of
the wires cut in the previous step.
8. Short the wires by twisting together one end from
each. Deployment wires shall remain shorted and not
be connected to a power source until the air bag is to
be deployed.
WARNING: FAILURE TO FOLLOW PROCEDURES IN
THE ORDER LISTED COULD RESULT IN PERSONAL
INJURY. NEVER CONNECT DEPLOYMENT WIRES
TO ANY POWER SOURCE BEFORE CONNECTING
DEPLOYMENT WIRES TO THE AIR BAG ASSEMBLY
LEADS. DEPLOYMENT WIRES SHALL REMAIN
SHORTED AND NOT BE CONNECTED TO A POWER
SOURCE UNTIL THE AIR BAG IS TO BE DEPLOYED.
THE AIR BAG ASSEMBLY WILL IMMEDIATELY
DEPLOY THE AIR BAG WHEN A POWER SOURCE IS
CONNECTED TO IT. WEAR SAFETY GLASSES
THROUGHOUT THIS ENTIRE DEPLOYMENT AND
DISPOSAL PROCEDURE.
9. Twist together one connector wire lead to one
deployment wire. The connection should be
mechanically secure.
10. Bend twisted connection made in the previous step
flat and wrap tightly with electrical tape to insulate and
secure.
11. Twist together, bend and tape the remaining
connector wire lead to the remaining deployment
wire.
12. Connect the deployment harness to the driver air bag
assembly, yellow 2±pin connector at the base of the
steering column. Route deployment harness out the
driver side of the vehicle.WARNING: DEPLOYMENT WIRES SHALL REMAIN
SHORTED AND NOT BE CONNECTED TO A POWER
SOURCE UNTIL THE AIR BAG IS TO BE DEPLOYED.
THE AIR BAG ASSEMBLY WILL IMMEDIATELY
DEPLOY THE AIR BAG WHEN A POWER SOURCE IS
CONNECTED TO IT.
CONNECTING THE DEPLOYMENT WIRES TO THE
POWER SOURCE SHOULD ALWAYS BE THE FINAL
STEP IN THE AIR BAG ASSEMBLY DEPLOYMENT
PROCEDURE.
FAILURE TO FOLLOW PROCEDURES IN THE OR-
DER LISTED COULD RESULT IN PERSONAL INJURY.
13. Disconnect passenger air bag assembly, yellow 2±pin
connector located behind glove box assembly.
14. Cut the passenger air bag assembly harness
connector from the vehicle leaving at least six inches
(16 cm) of wire at the connector.
15. Strip 1/2 inch (13 mm) of insulation from yellow±green
and yellow±red wire lead of the connector.
16. Cut two 30 feet (900 cm) deployment wires from 18
gauge (0.8 mm) or thicker multi±strand wire. These
wires will be used to fabricate the passenger
deployment harness.
17. Strip 1/2 inch (13 mm) of insulation from both ends of
the wires cut in the previous step.
18. Short the wires by twisting together one end from
each. Deployment wires shall remain shorted and not
be connected to a power source until the air bag is to
be deployed.
WARNING: FAILURE TO FOLLOW PROCEDURES IN
THE ORDER LISTED COULD RESULT IN PERSONAL
INJURY. NEVER CONNECT DEPLOYMENT WIRES
TO ANY POWER SOURCE BEFORE CONNECTING
DEPLOYMENT WIRES TO THE AIR BAG ASSEMBLY
LEADS. DEPLOYMENT WIRES SHALL REMAIN
SHORTED AND NOT BE CONNECTED TO A POWER
SOURCE UNTIL THE AIR BAG IS TO BE DEPLOYED.
THE AIR BAG ASSEMBLY WILL IMMEDIATELY
DEPLOY THE AIR BAG WHEN SAFETY GLASSES
THROUGHOUT THIS ENTIRE DEPLOYMENT AND
DISPOSAL PROCEDURE.
19. Twist together one connector wire lead to one
deployment wire. The connection should be
mechanically secure.
20. Bend twisted connection made in the previous step
flat and wrap tightly with electrical tape to insulate and
secure.
21. Twist together, bend and tape the remaining
connector wire lead to the remaining deployment
wire.
22. Connect the deployment harness to the passenger air
bag assembly, yellow 2±pin connector located behind
the glove box assembly. Route deployment harness
out the passenger side of the vehicle.
WARNING: DEPLOYMENT WIRES SHALL REMAIN
SHORTED AND NOT BE CONNECTED TO A POWER
SOURCE UNTIL THE AIR BAG IS TO BE DEPLOYED.
THE AIR BAG ASSEMBLY WILL IMMEDIATELY
DEPLOY THE AIR BAG WHEN A POWER SOURCE IS
CONNECTED TO IT. CONNECTING THE