ISUZU AXIOM 2002 Service Repair Manual
Manufacturer: ISUZU, Model Year: 2002, Model line: AXIOM, Model: ISUZU AXIOM 2002Pages: 2100, PDF Size: 19.35 MB
Page 711 of 2100
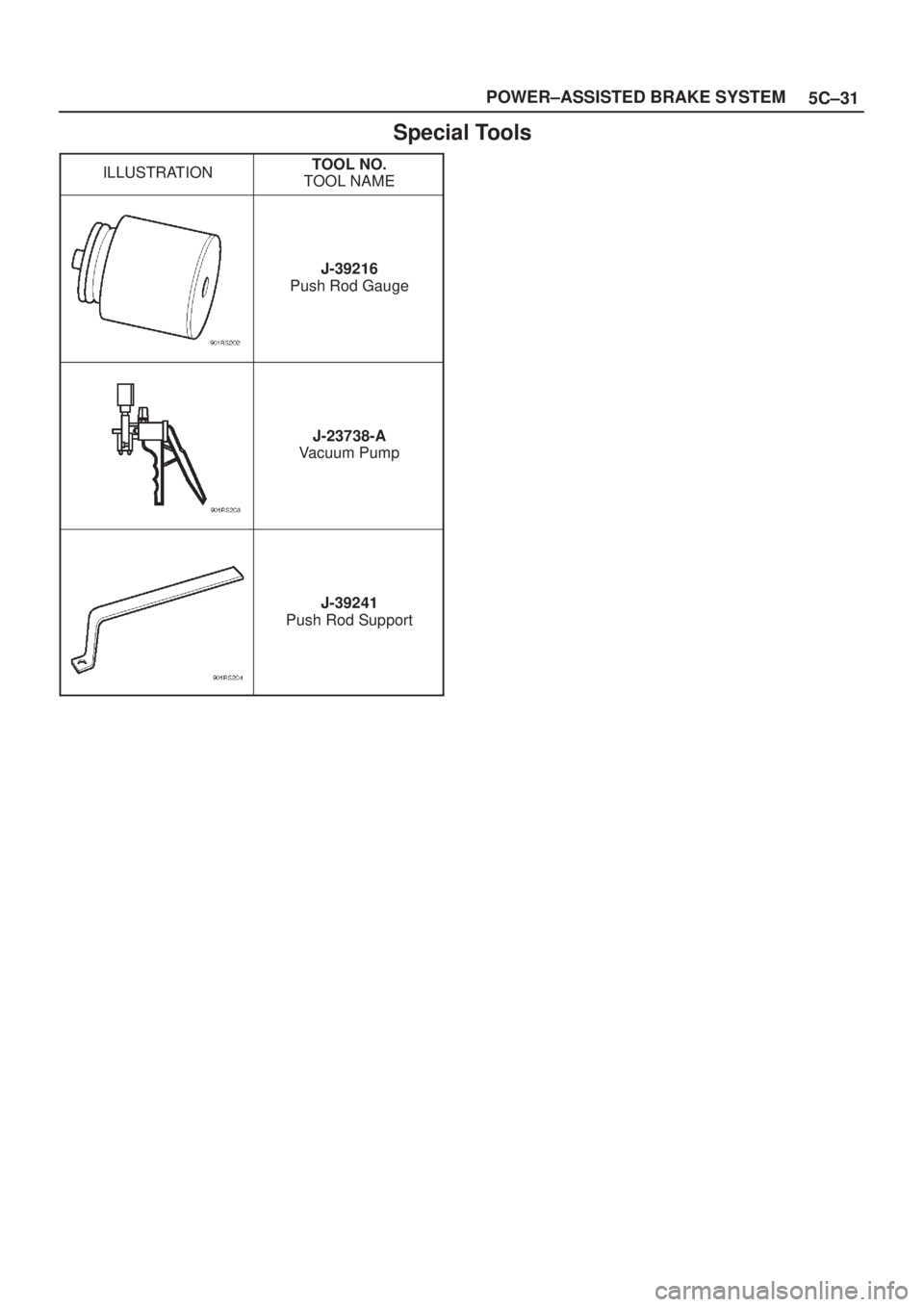
5C±31 POWER±ASSISTED BRAKE SYSTEM
Special Tools
ILLUSTRATIONTOOL NO.
TOOL NAME
J-39216
Push Rod Gauge
J-23738-A
Vacuum Pump
J-39241
Push Rod Support
Page 712 of 2100
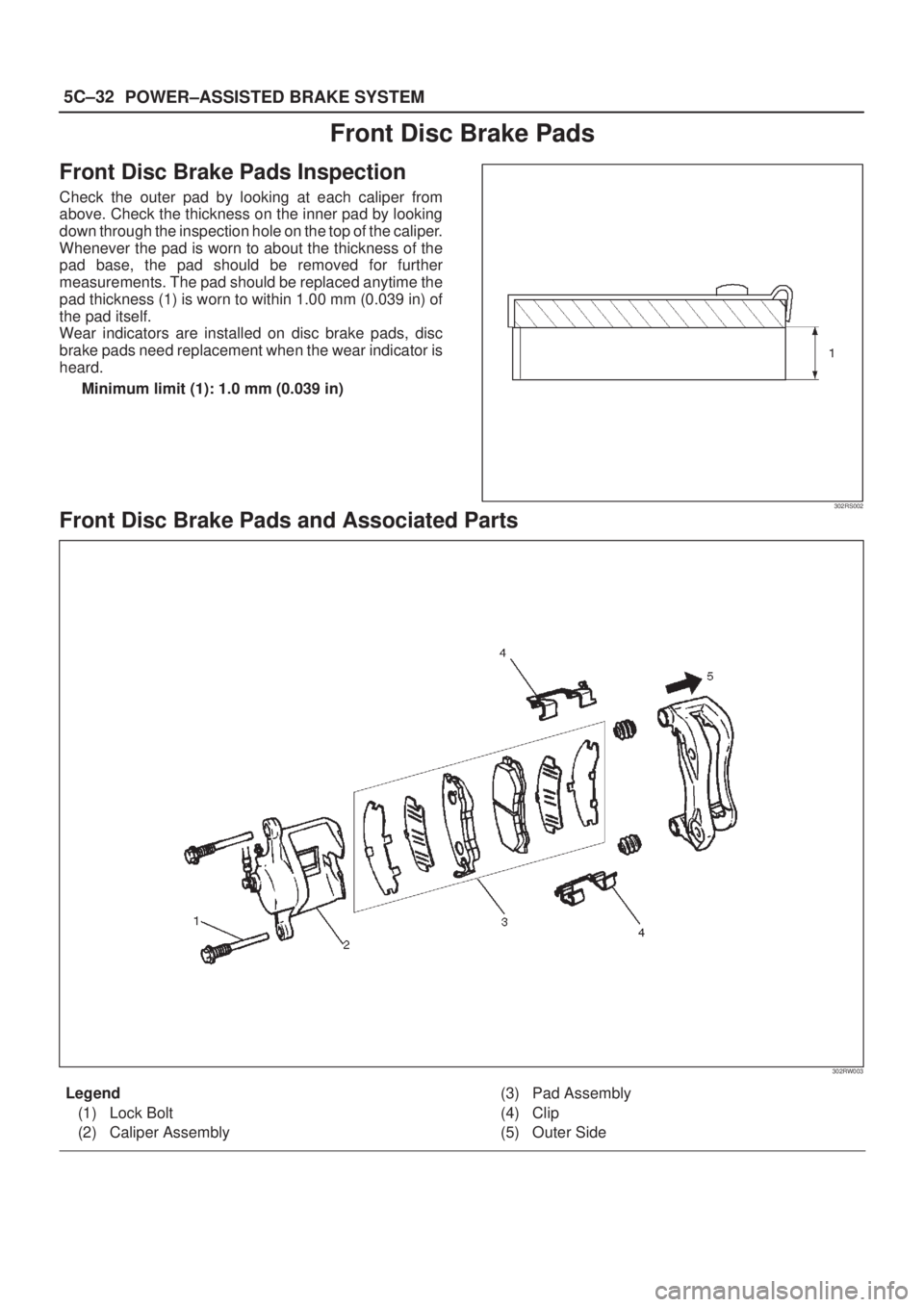
5C±32
POWER±ASSISTED BRAKE SYSTEM
Front Disc Brake Pads
Front Disc Brake Pads Inspection
Check the outer pad by looking at each caliper from
above. Check the thickness on the inner pad by looking
down through the inspection hole on the top of the caliper.
Whenever the pad is worn to about the thickness of the
pad base, the pad should be removed for further
measurements. The pad should be replaced anytime the
pad thickness (1) is worn to within 1.00 mm (0.039 in) of
the pad itself.
Wear indicators are installed on disc brake pads, disc
brake pads need replacement when the wear indicator is
heard.
Minimum limit (1): 1.0 mm (0.039 in)
302RS002
Front Disc Brake Pads and Associated Parts
302RW003
Legend
(1) Lock Bolt
(2) Caliper Assembly(3) Pad Assembly
(4) Clip
(5) Outer Side
Page 713 of 2100
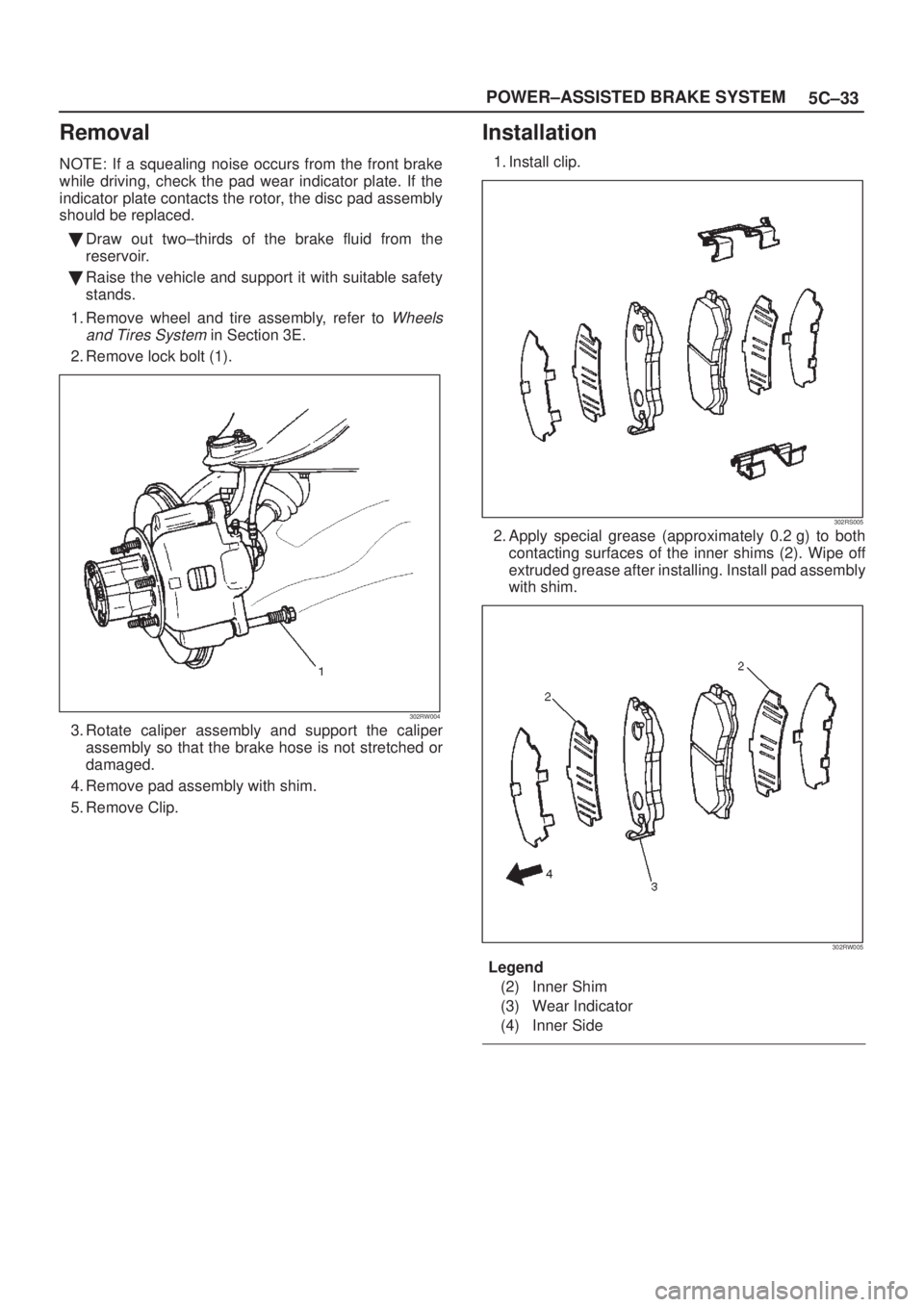
5C±33 POWER±ASSISTED BRAKE SYSTEM
Removal
NOTE: If a squealing noise occurs from the front brake
while driving, check the pad wear indicator plate. If the
indicator plate contacts the rotor, the disc pad assembly
should be replaced.
Draw out two±thirds of the brake fluid from the
reservoir.
Raise the vehicle and support it with suitable safety
stands.
1. Remove wheel and tire assembly, refer to
Wheels
and Tires System
in Section 3E.
2. Remove lock bolt (1).
302RW004
3. Rotate caliper assembly and support the caliper
assembly so that the brake hose is not stretched or
damaged.
4. Remove pad assembly with shim.
5. Remove Clip.
Installation
1. Install clip.
302RS005
2. Apply special grease (approximately 0.2 g) to both
contacting surfaces of the inner shims (2). Wipe off
extruded grease after installing. Install pad assembly
with shim.
302RW005
Legend
(2) Inner Shim
(3) Wear Indicator
(4) Inner Side
Page 714 of 2100
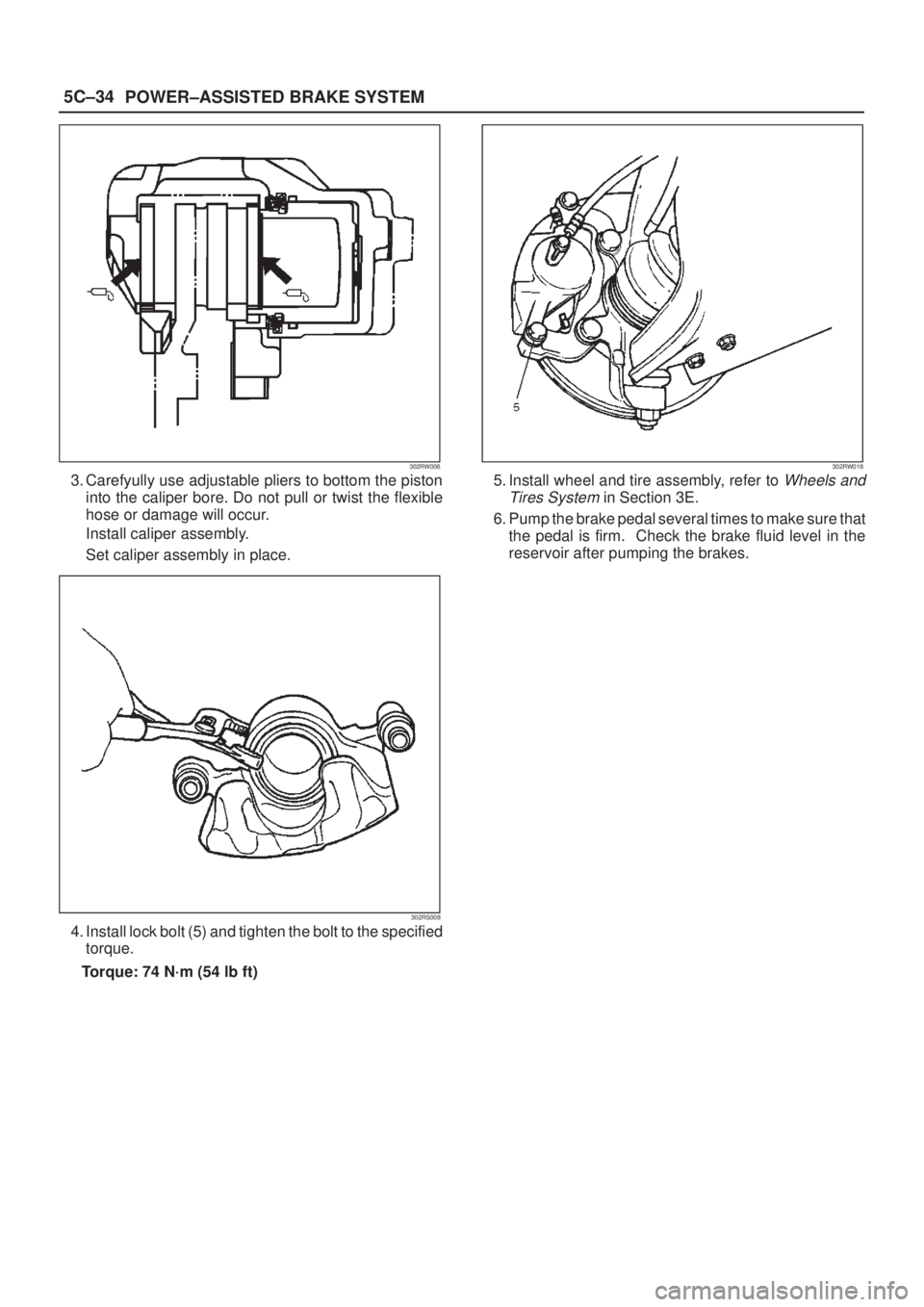
5C±34
POWER±ASSISTED BRAKE SYSTEM
302RW006
3. Carefyully use adjustable pliers to bottom the piston
into the caliper bore. Do not pull or twist the flexible
hose or damage will occur.
Install caliper assembly.
Set caliper assembly in place.
302RS008
4. Install lock bolt (5) and tighten the bolt to the specified
torque.
Torque: 74 N´m (54 lb ft)
302RW018
5. Install wheel and tire assembly, refer to Wheels and
Tires System
in Section 3E.
6. Pump the brake pedal several times to make sure that
the pedal is firm. Check the brake fluid level in the
reservoir after pumping the brakes.
Page 715 of 2100
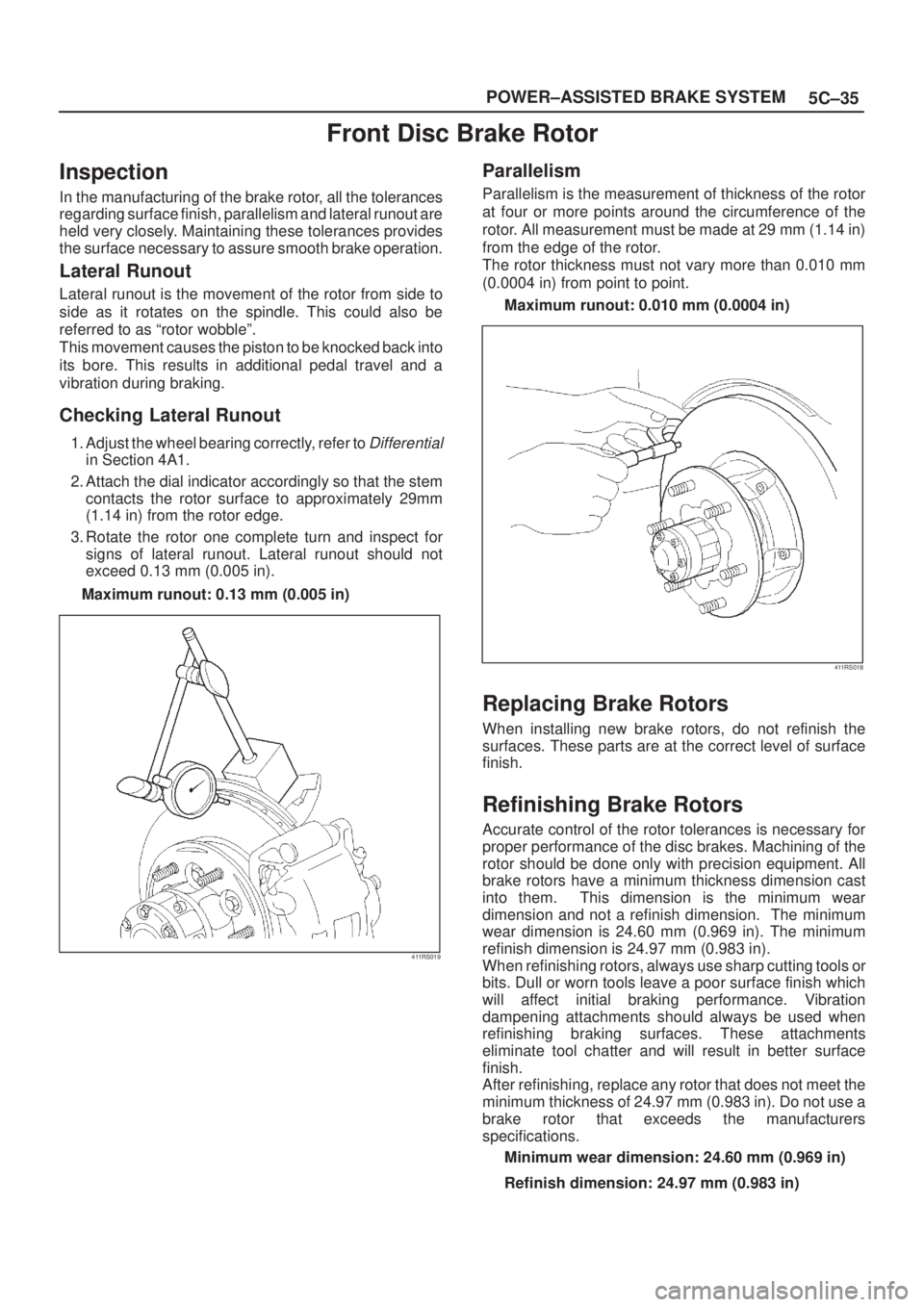
5C±35 POWER±ASSISTED BRAKE SYSTEM
Front Disc Brake Rotor
Inspection
In the manufacturing of the brake rotor, all the tolerances
regarding surface finish, parallelism and lateral runout are
held very closely. Maintaining these tolerances provides
the surface necessary to assure smooth brake operation.
Lateral Runout
Lateral runout is the movement of the rotor from side to
side as it rotates on the spindle. This could also be
referred to as ªrotor wobbleº.
This movement causes the piston to be knocked back into
its bore. This results in additional pedal travel and a
vibration during braking.
Checking Lateral Runout
1. Adjust the wheel bearing correctly, refer to Differential
in Section 4A1.
2. Attach the dial indicator accordingly so that the stem
contacts the rotor surface to approximately 29mm
(1.14 in) from the rotor edge.
3. Rotate the rotor one complete turn and inspect for
signs of lateral runout. Lateral runout should not
exceed 0.13 mm (0.005 in).
Maximum runout: 0.13 mm (0.005 in)
411RS019
Parallelism
Parallelism is the measurement of thickness of the rotor
at four or more points around the circumference of the
rotor. All measurement must be made at 29 mm (1.14 in)
from the edge of the rotor.
The rotor thickness must not vary more than 0.010 mm
(0.0004 in) from point to point.
Maximum runout: 0.010 mm (0.0004 in)
411RS018
Replacing Brake Rotors
When installing new brake rotors, do not refinish the
surfaces. These parts are at the correct level of surface
finish.
Refinishing Brake Rotors
Accurate control of the rotor tolerances is necessary for
proper performance of the disc brakes. Machining of the
rotor should be done only with precision equipment. All
brake rotors have a minimum thickness dimension cast
into them. This dimension is the minimum wear
dimension and not a refinish dimension. The minimum
wear dimension is 24.60 mm (0.969 in). The minimum
refinish dimension is 24.97 mm (0.983 in).
When refinishing rotors, always use sharp cutting tools or
bits. Dull or worn tools leave a poor surface finish which
will affect initial braking performance. Vibration
dampening attachments should always be used when
refinishing braking surfaces. These attachments
eliminate tool chatter and will result in better surface
finish.
After refinishing, replace any rotor that does not meet the
minimum thickness of 24.97 mm (0.983 in). Do not use a
brake rotor that exceeds the manufacturers
specifications.
Minimum wear dimension: 24.60 mm (0.969 in)
Refinish dimension: 24.97 mm (0.983 in)
Page 716 of 2100
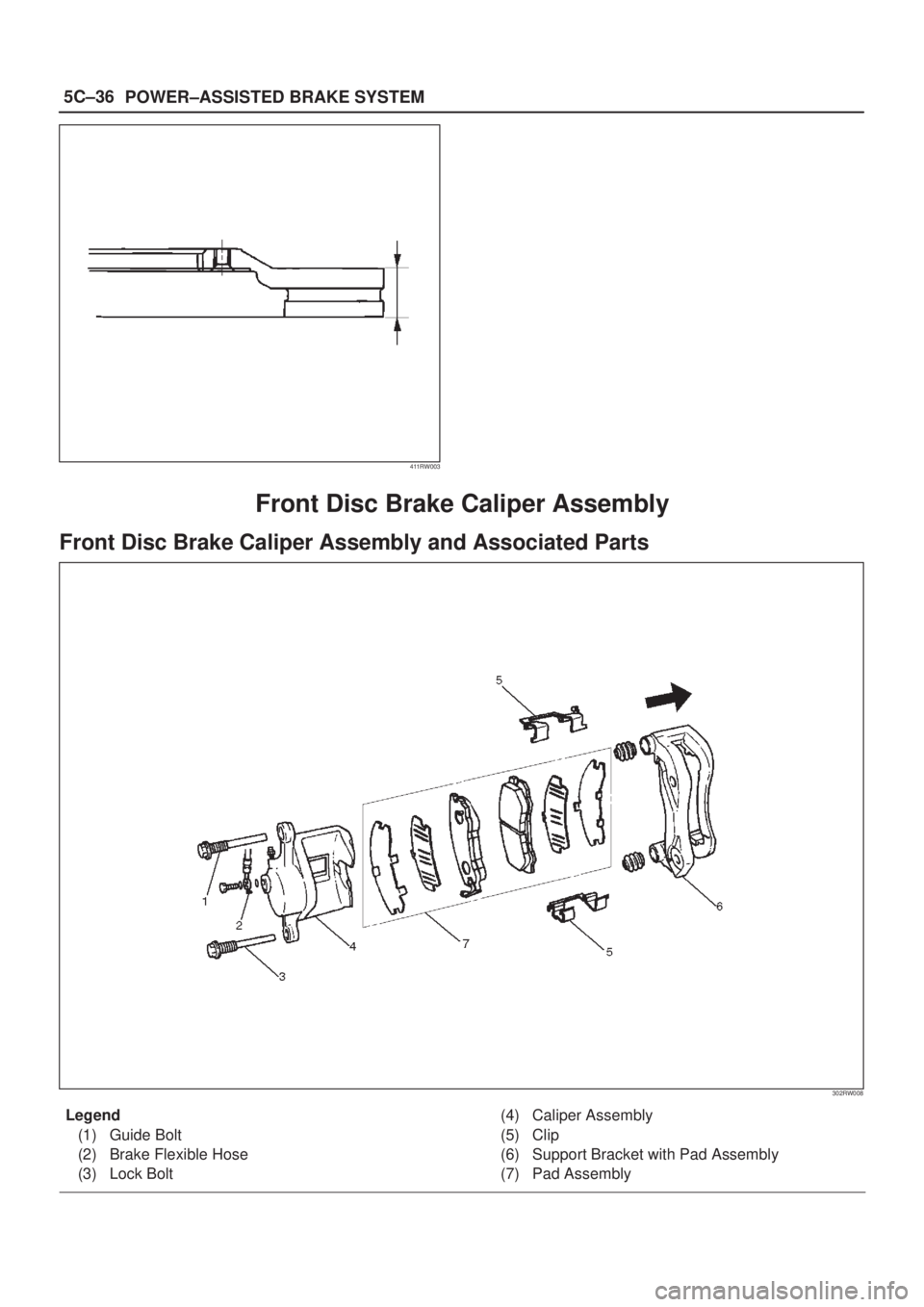
5C±36
POWER±ASSISTED BRAKE SYSTEM
411RW003
Front Disc Brake Caliper Assembly
Front Disc Brake Caliper Assembly and Associated Parts
302RW008
Legend
(1) Guide Bolt
(2) Brake Flexible Hose
(3) Lock Bolt(4) Caliper Assembly
(5) Clip
(6) Support Bracket with Pad Assembly
(7) Pad Assembly
Page 717 of 2100
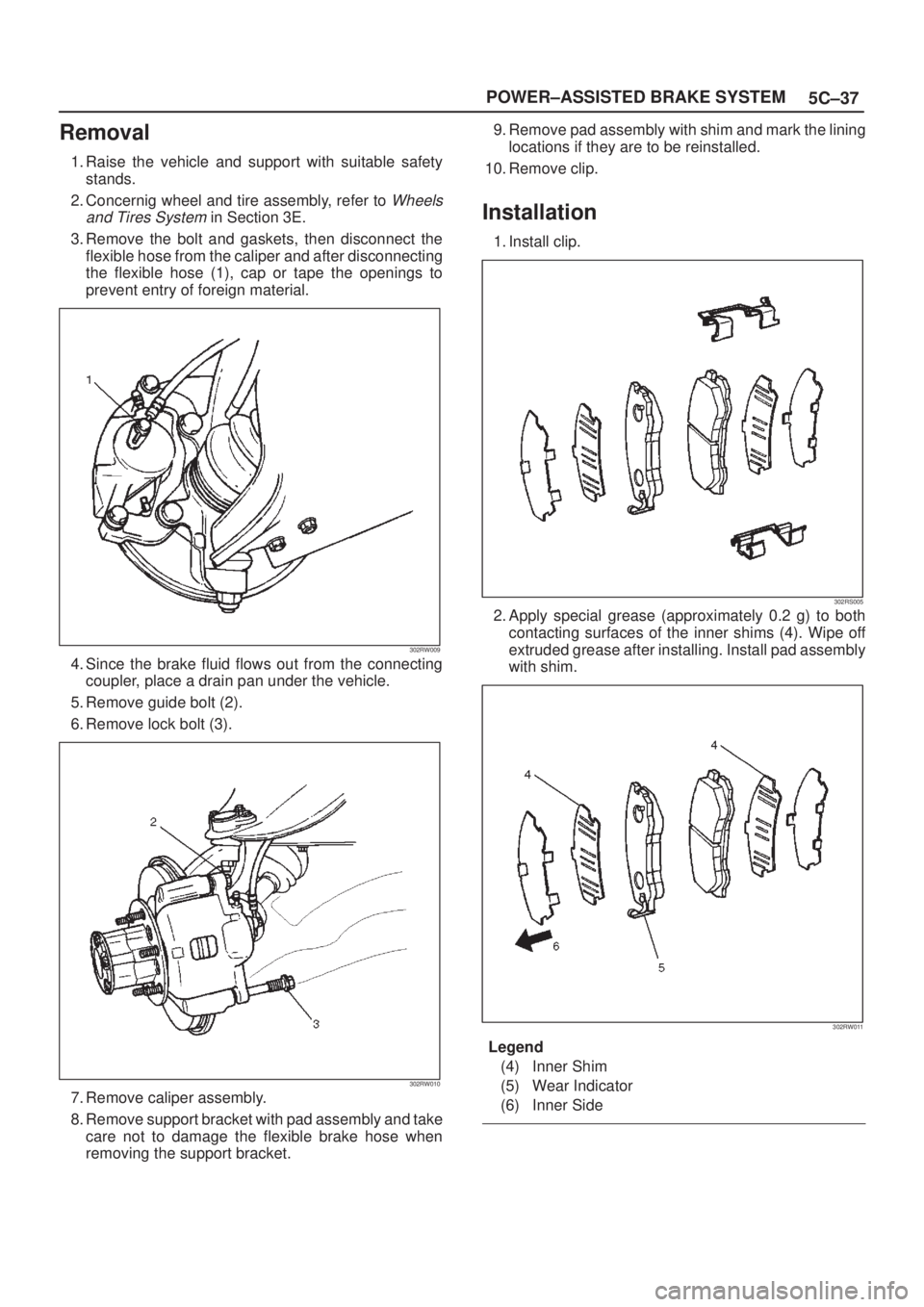
5C±37 POWER±ASSISTED BRAKE SYSTEM
Removal
1. Raise the vehicle and support with suitable safety
stands.
2. Concernig wheel and tire assembly, refer to
Wheels
and Tires System
in Section 3E.
3. Remove the bolt and gaskets, then disconnect the
flexible hose from the caliper and after disconnecting
the flexible hose (1), cap or tape the openings to
prevent entry of foreign material.
302RW009
4. Since the brake fluid flows out from the connecting
coupler, place a drain pan under the vehicle.
5. Remove guide bolt (2).
6. Remove lock bolt (3).
302RW010
7. Remove caliper assembly.
8. Remove support bracket with pad assembly and take
care not to damage the flexible brake hose when
removing the support bracket.9. Remove pad assembly with shim and mark the lining
locations if they are to be reinstalled.
10. Remove clip.
Installation
1. Install clip.
302RS005
2. Apply special grease (approximately 0.2 g) to both
contacting surfaces of the inner shims (4). Wipe off
extruded grease after installing. Install pad assembly
with shim.
302RW011
Legend
(4) Inner Shim
(5) Wear Indicator
(6) Inner Side
Page 718 of 2100
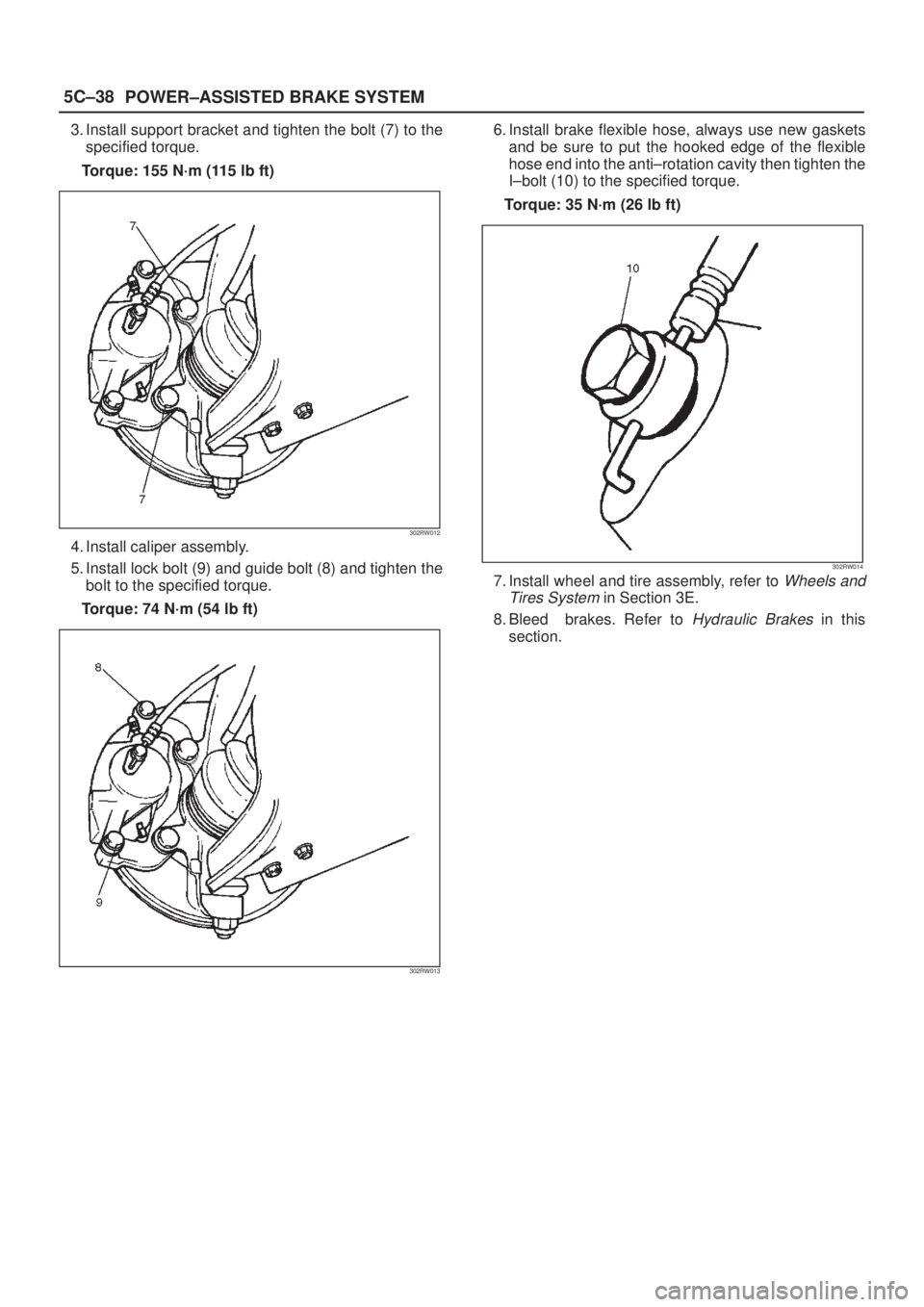
5C±38
POWER±ASSISTED BRAKE SYSTEM
3. Install support bracket and tighten the bolt (7) to the
specified torque.
Torque: 155 N´m (115 lb ft)
302RW012
4. Install caliper assembly.
5. Install lock bolt (9) and guide bolt (8) and tighten the
bolt to the specified torque.
Torque: 74 N´m (54 lb ft)
302RW013
6. Install brake flexible hose, always use new gaskets
and be sure to put the hooked edge of the flexible
hose end into the anti±rotation cavity then tighten the
I±bolt (10) to the specified torque.
Torque: 35 N´m (26 lb ft)
302RW014
7. Install wheel and tire assembly, refer to Wheels and
Tires System
in Section 3E.
8. Bleed brakes. Refer to
Hydraulic Brakes in this
section.
Page 719 of 2100
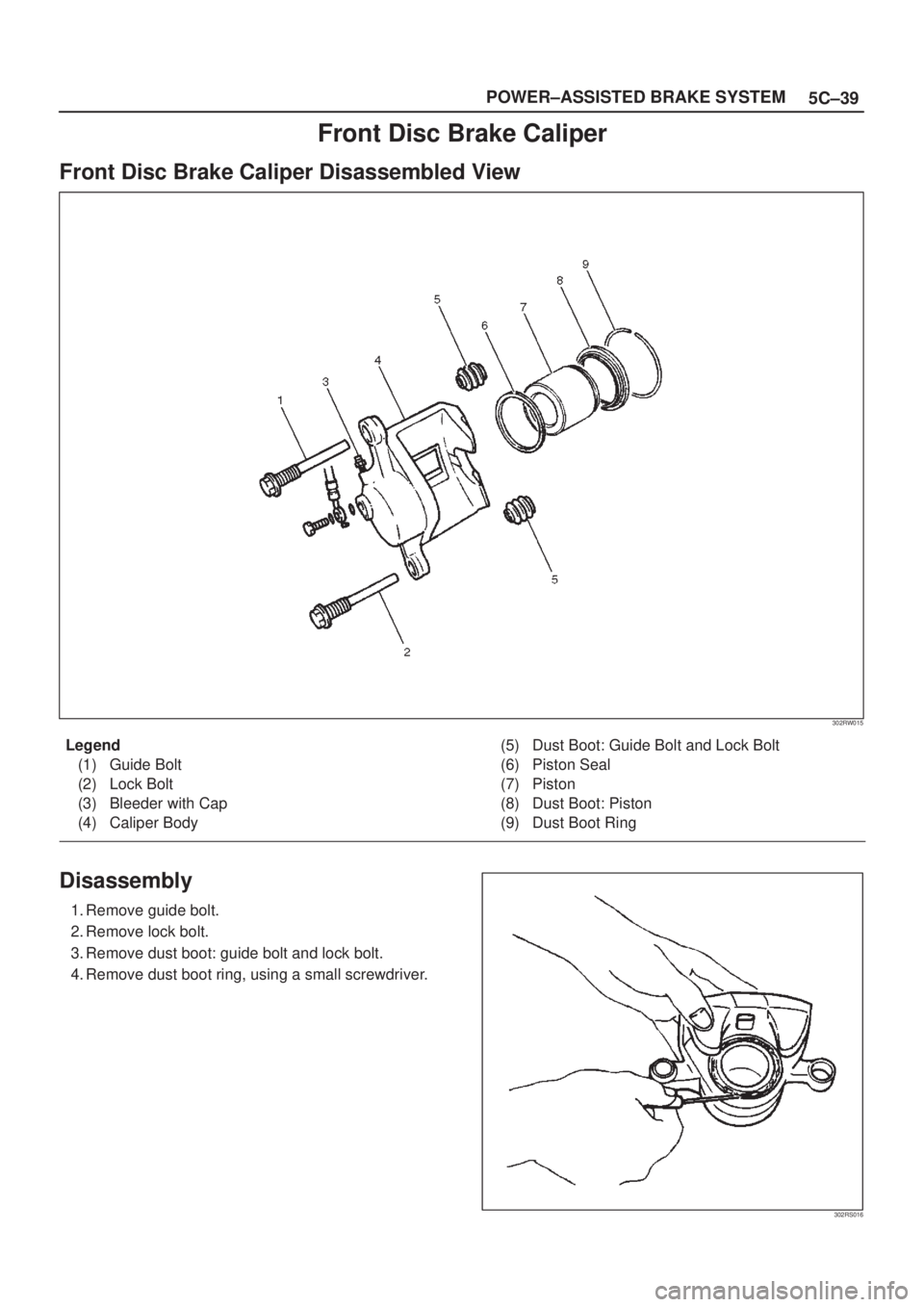
5C±39 POWER±ASSISTED BRAKE SYSTEM
Front Disc Brake Caliper
Front Disc Brake Caliper Disassembled View
302RW015
Legend
(1) Guide Bolt
(2) Lock Bolt
(3) Bleeder with Cap
(4) Caliper Body(5) Dust Boot: Guide Bolt and Lock Bolt
(6) Piston Seal
(7) Piston
(8) Dust Boot: Piston
(9) Dust Boot Ring
Disassembly
1. Remove guide bolt.
2. Remove lock bolt.
3. Remove dust boot: guide bolt and lock bolt.
4. Remove dust boot ring, using a small screwdriver.
302RS016
Page 720 of 2100
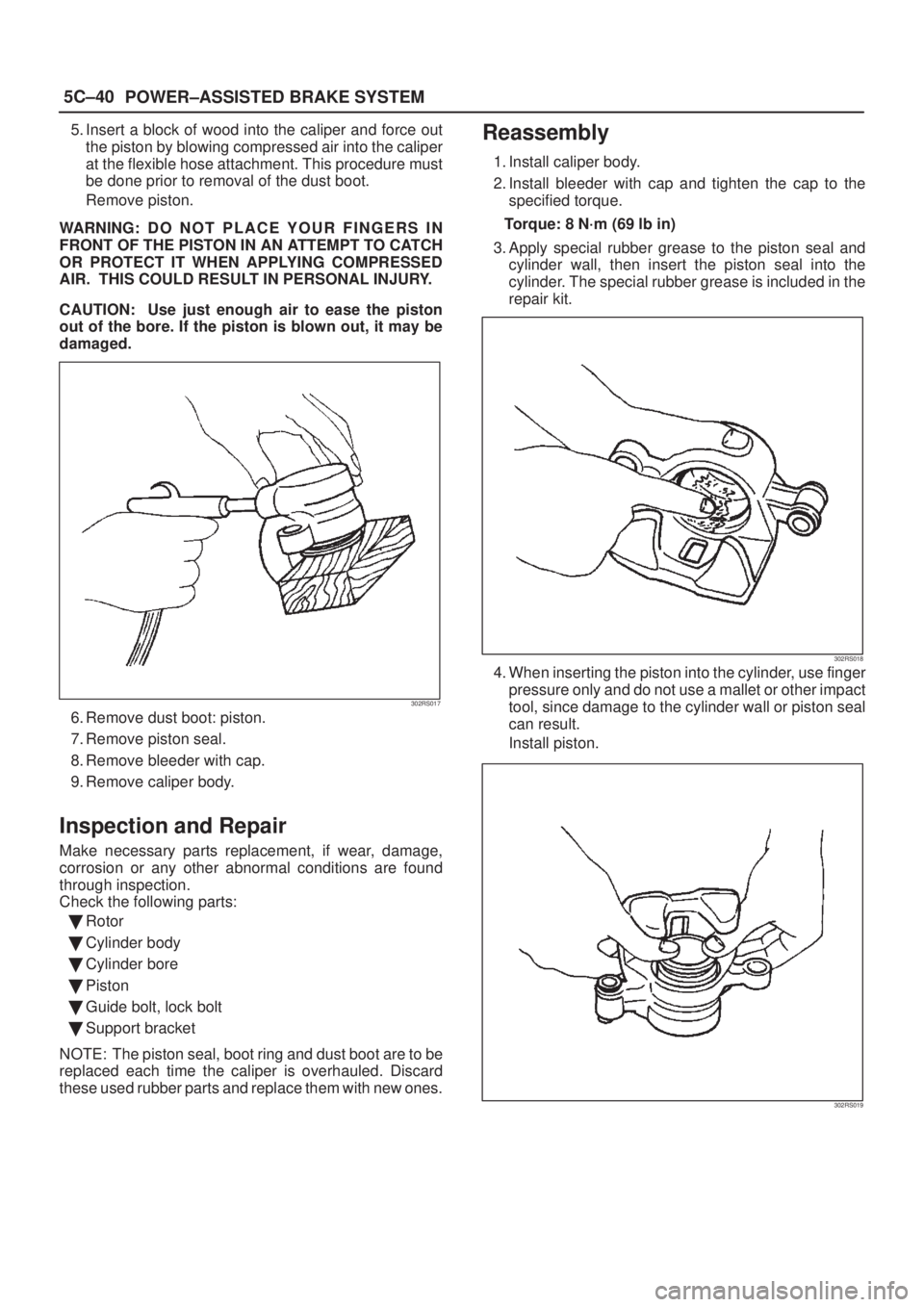
5C±40
POWER±ASSISTED BRAKE SYSTEM
5. Insert a block of wood into the caliper and force out
the piston by blowing compressed air into the caliper
at the flexible hose attachment. This procedure must
be done prior to removal of the dust boot.
Remove piston.
WARNING: D O N O T P L A C E Y O U R F I N G E R S I N
FRONT OF THE PISTON IN AN ATTEMPT TO CATCH
OR PROTECT IT WHEN APPLYING COMPRESSED
AIR. THIS COULD RESULT IN PERSONAL INJURY.
CAUTION: Use just enough air to ease the piston
out of the bore. If the piston is blown out, it may be
damaged.
302RS017
6. Remove dust boot: piston.
7. Remove piston seal.
8. Remove bleeder with cap.
9. Remove caliper body.
Inspection and Repair
Make necessary parts replacement, if wear, damage,
corrosion or any other abnormal conditions are found
through inspection.
Check the following parts:
Rotor
Cylinder body
Cylinder bore
Piston
Guide bolt, lock bolt
Support bracket
NOTE: The piston seal, boot ring and dust boot are to be
replaced each time the caliper is overhauled. Discard
these used rubber parts and replace them with new ones.
Reassembly
1. Install caliper body.
2. Install bleeder with cap and tighten the cap to the
specified torque.
Torque: 8 N´m (69 lb in)
3. Apply special rubber grease to the piston seal and
cylinder wall, then insert the piston seal into the
cylinder. The special rubber grease is included in the
repair kit.
302RS018
4. When inserting the piston into the cylinder, use finger
pressure only and do not use a mallet or other impact
tool, since damage to the cylinder wall or piston seal
can result.
Install piston.
302RS019