check engine ISUZU TF SERIES 2004 Owners Manual
[x] Cancel search | Manufacturer: ISUZU, Model Year: 2004, Model line: TF SERIES, Model: ISUZU TF SERIES 2004Pages: 4264, PDF Size: 72.63 MB
Page 1374 of 4264
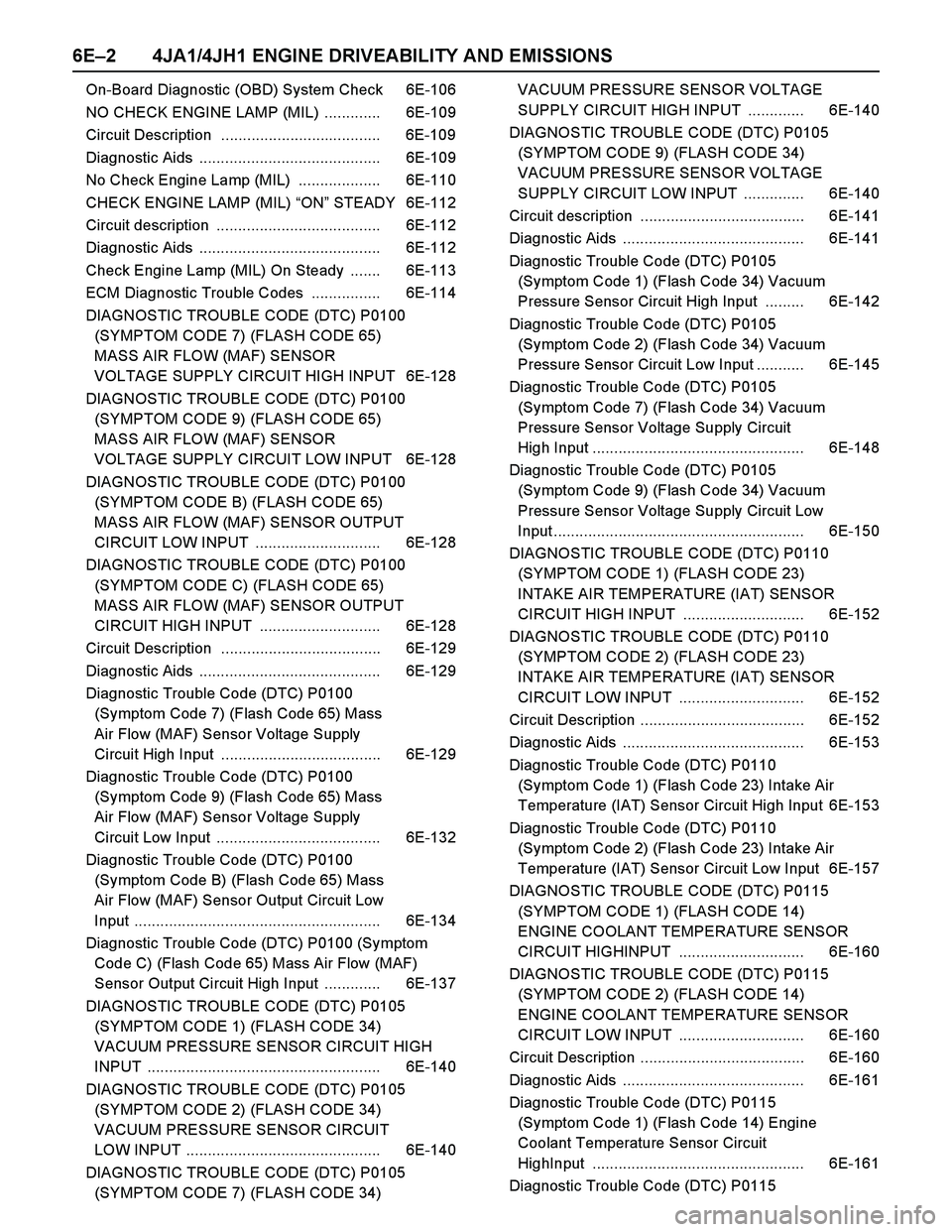
6E–2 4JA1/4JH1 ENGINE DRIVEABILITY AND EMISSIONS
On-Board Diagnostic (OBD) System Check 6E-106
NO CHECK ENGINE LAMP (MIL) ............. 6E-109
Circuit Description ..................................... 6E-109
Diagnostic Aids .......................................... 6E-109
No Check Engine Lamp (MIL) ................... 6E-110
CHECK ENGINE LAMP (MIL) “ON” STEADY 6E-112
Circuit description ...................................... 6E-112
Diagnostic Aids .......................................... 6E-112
Check Engine Lamp (MIL) On Steady ....... 6E-113
ECM Diagnostic Trouble Codes ................ 6E-114
DIAGNOSTIC TROUBLE CODE (DTC) P0100
(SYMPTOM CODE 7) (FLASH CODE 65)
MASS AIR FLOW (MAF) SENSOR
VOLTAGE SUPPLY CIRCUIT HIGH INPUT 6E-128
DIAGNOSTIC TROUBLE CODE (DTC) P0100
(SYMPTOM CODE 9) (FLASH CODE 65)
MASS AIR FLOW (MAF) SENSOR
VOLTAGE SUPPLY CIRCUIT LOW INPUT 6E-128
DIAGNOSTIC TROUBLE CODE (DTC) P0100
(SYMPTOM CODE B) (FLASH CODE 65)
MASS AIR FLOW (MAF) SENSOR OUTPUT
CIRCUIT LOW INPUT ............................. 6E-128
DIAGNOSTIC TROUBLE CODE (DTC) P0100
(SYMPTOM CODE C) (FLASH CODE 65)
MASS AIR FLOW (MAF) SENSOR OUTPUT
CIRCUIT HIGH INPUT ............................ 6E-128
Circuit Description ..................................... 6E-129
Diagnostic Aids .......................................... 6E-129
Diagnostic Trouble Code (DTC) P0100
(Symptom Code 7) (Flash Code 65) Mass
Air Flow (MAF) Sensor Voltage Supply
Circuit High Input ..................................... 6E-129
Diagnostic Trouble Code (DTC) P0100
(Symptom Code 9) (Flash Code 65) Mass
Air Flow (MAF) Sensor Voltage Supply
Circuit Low Input ...................................... 6E-132
Diagnostic Trouble Code (DTC) P0100
(Symptom Code B) (Flash Code 65) Mass
Air Flow (MAF) Sensor Output Circuit Low
Input ......................................................... 6E-134
Diagnostic Trouble Code (DTC) P0100 (Symptom
Code C) (Flash Code 65) Mass Air Flow (MAF)
Sensor Output Circuit High Input ............. 6E-137
DIAGNOSTIC TROUBLE CODE (DTC) P0105
(SYMPTOM CODE 1) (FLASH CODE 34)
VACUUM PRESSURE SENSOR CIRCUIT HIGH
INPUT ...................................................... 6E-140
DIAGNOSTIC TROUBLE CODE (DTC) P0105
(SYMPTOM CODE 2) (FLASH CODE 34)
VACUUM PRESSURE SENSOR CIRCUIT
LOW INPUT ............................................. 6E-140
DIAGNOSTIC TROUBLE CODE (DTC) P0105
(SYMPTOM CODE 7) (FLASH CODE 34) VACUUM PRESSURE SENSOR VOLTAGE
SUPPLY CIRCUIT HIGH INPUT ............. 6E-140
DIAGNOSTIC TROUBLE CODE (DTC) P0105
(SYMPTOM CODE 9) (FLASH CODE 34)
VACUUM PRESSURE SENSOR VOLTAGE
SUPPLY CIRCUIT LOW INPUT .............. 6E-140
Circuit description ...................................... 6E-141
Diagnostic Aids .......................................... 6E-141
Diagnostic Trouble Code (DTC) P0105
(Symptom Code 1) (Flash Code 34) Vacuum
Pressure Sensor Circuit High Input ......... 6E-142
Diagnostic Trouble Code (DTC) P0105
(Symptom Code 2) (Flash Code 34) Vacuum
Pressure Sensor Circuit Low Input ........... 6E-145
Diagnostic Trouble Code (DTC) P0105
(Symptom Code 7) (Flash Code 34) Vacuum
Pressure Sensor Voltage Supply Circuit
High Input ................................................. 6E-148
Diagnostic Trouble Code (DTC) P0105
(Symptom Code 9) (Flash Code 34) Vacuum
Pressure Sensor Voltage Supply Circuit Low
Input .......................................................... 6E-150
DIAGNOSTIC TROUBLE CODE (DTC) P0110
(SYMPTOM CODE 1) (FLASH CODE 23)
INTAKE AIR TEMPERATURE (IAT) SENSOR
CIRCUIT HIGH INPUT ............................ 6E-152
DIAGNOSTIC TROUBLE CODE (DTC) P0110
(SYMPTOM CODE 2) (FLASH CODE 23)
INTAKE AIR TEMPERATURE (IAT) SENSOR
CIRCUIT LOW INPUT ............................. 6E-152
Circuit Description ...................................... 6E-152
Diagnostic Aids .......................................... 6E-153
Diagnostic Trouble Code (DTC) P0110
(Symptom Code 1) (Flash Code 23) Intake Air
Temperature (IAT) Sensor Circuit High Input 6E-153
Diagnostic Trouble Code (DTC) P0110
(Symptom Code 2) (Flash Code 23) Intake Air
Temperature (IAT) Sensor Circuit Low Input 6E-157
DIAGNOSTIC TROUBLE CODE (DTC) P0115
(SYMPTOM CODE 1) (FLASH CODE 14)
ENGINE COOLANT TEMPERATURE SENSOR
CIRCUIT HIGHINPUT ............................. 6E-160
DIAGNOSTIC TROUBLE CODE (DTC) P0115
(SYMPTOM CODE 2) (FLASH CODE 14)
ENGINE COOLANT TEMPERATURE SENSOR
CIRCUIT LOW INPUT ............................. 6E-160
Circuit Description ...................................... 6E-160
Diagnostic Aids .......................................... 6E-161
Diagnostic Trouble Code (DTC) P0115
(Symptom Code 1) (Flash Code 14) Engine
Coolant Temperature Sensor Circuit
HighInput ................................................. 6E-161
Diagnostic Trouble Code (DTC) P0115
Page 1380 of 4264
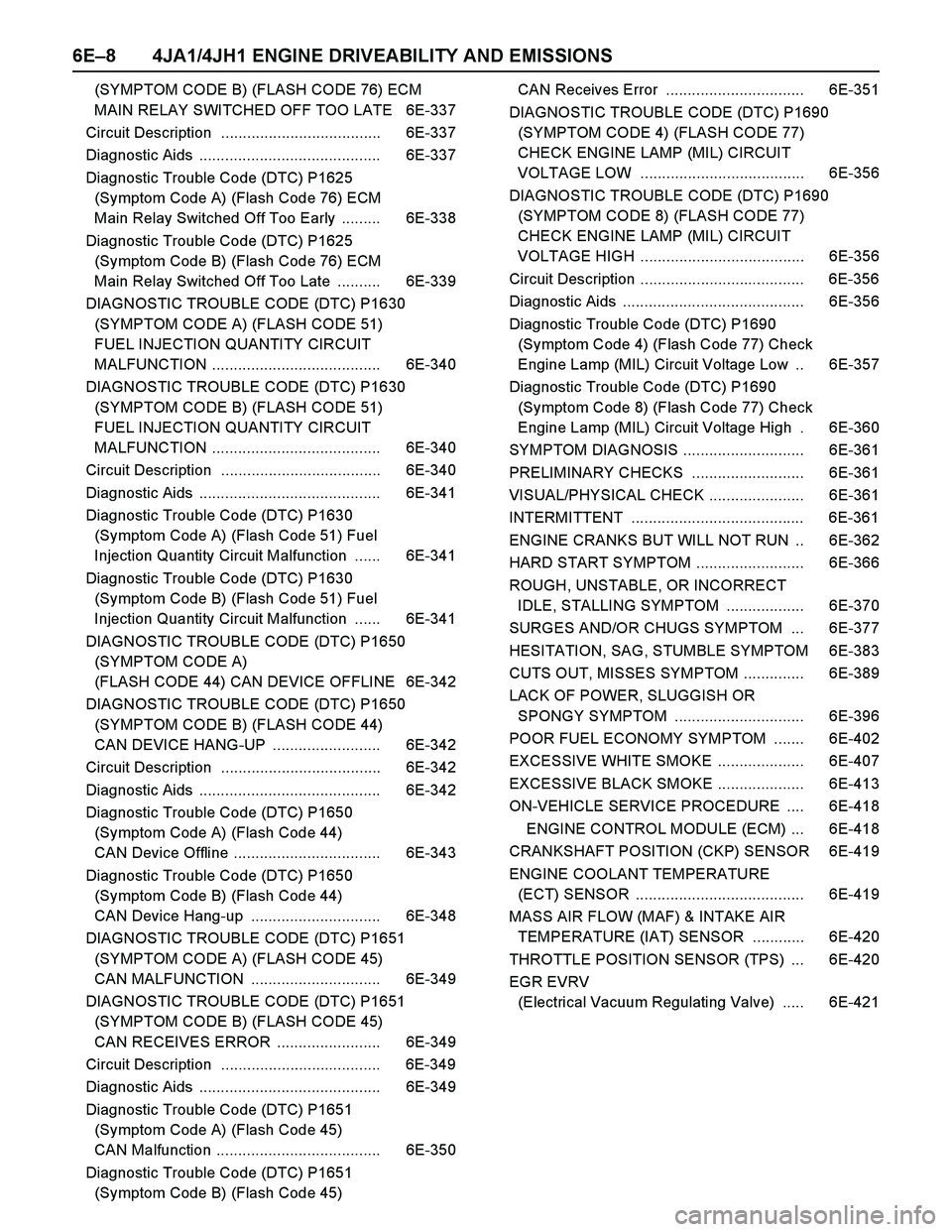
6E–8 4JA1/4JH1 ENGINE DRIVEABILITY AND EMISSIONS
(SYMPTOM CODE B) (FLASH CODE 76) ECM
MAIN RELAY SWITCHED OFF TOO LATE 6E-337
Circuit Description ..................................... 6E-337
Diagnostic Aids .......................................... 6E-337
Diagnostic Trouble Code (DTC) P1625
(Symptom Code A) (Flash Code 76) ECM
Main Relay Switched Off Too Early ......... 6E-338
Diagnostic Trouble Code (DTC) P1625
(Symptom Code B) (Flash Code 76) ECM
Main Relay Switched Off Too Late .......... 6E-339
DIAGNOSTIC TROUBLE CODE (DTC) P1630
(SYMPTOM CODE A) (FLASH CODE 51)
FUEL INJECTION QUANTITY CIRCUIT
MALFUNCTION ....................................... 6E-340
DIAGNOSTIC TROUBLE CODE (DTC) P1630
(SYMPTOM CODE B) (FLASH CODE 51)
FUEL INJECTION QUANTITY CIRCUIT
MALFUNCTION ....................................... 6E-340
Circuit Description ..................................... 6E-340
Diagnostic Aids .......................................... 6E-341
Diagnostic Trouble Code (DTC) P1630
(Symptom Code A) (Flash Code 51) Fuel
Injection Quantity Circuit Malfunction ...... 6E-341
Diagnostic Trouble Code (DTC) P1630
(Symptom Code B) (Flash Code 51) Fuel
Injection Quantity Circuit Malfunction ...... 6E-341
DIAGNOSTIC TROUBLE CODE (DTC) P1650
(SYMPTOM CODE A)
(FLASH CODE 44) CAN DEVICE OFFLINE 6E-342
DIAGNOSTIC TROUBLE CODE (DTC) P1650
(SYMPTOM CODE B) (FLASH CODE 44)
CAN DEVICE HANG-UP ......................... 6E-342
Circuit Description ..................................... 6E-342
Diagnostic Aids .......................................... 6E-342
Diagnostic Trouble Code (DTC) P1650
(Symptom Code A) (Flash Code 44)
CAN Device Offline .................................. 6E-343
Diagnostic Trouble Code (DTC) P1650
(Symptom Code B) (Flash Code 44)
CAN Device Hang-up .............................. 6E-348
DIAGNOSTIC TROUBLE CODE (DTC) P1651
(SYMPTOM CODE A) (FLASH CODE 45)
CAN MALFUNCTION .............................. 6E-349
DIAGNOSTIC TROUBLE CODE (DTC) P1651
(SYMPTOM CODE B) (FLASH CODE 45)
CAN RECEIVES ERROR ........................ 6E-349
Circuit Description ..................................... 6E-349
Diagnostic Aids .......................................... 6E-349
Diagnostic Trouble Code (DTC) P1651
(Symptom Code A) (Flash Code 45)
CAN Malfunction ...................................... 6E-350
Diagnostic Trouble Code (DTC) P1651
(Symptom Code B) (Flash Code 45) CAN Receives Error ................................ 6E-351
DIAGNOSTIC TROUBLE CODE (DTC) P1690
(SYMPTOM CODE 4) (FLASH CODE 77)
CHECK ENGINE LAMP (MIL) CIRCUIT
VOLTAGE LOW ...................................... 6E-356
DIAGNOSTIC TROUBLE CODE (DTC) P1690
(SYMPTOM CODE 8) (FLASH CODE 77)
CHECK ENGINE LAMP (MIL) CIRCUIT
VOLTAGE HIGH ...................................... 6E-356
Circuit Description ...................................... 6E-356
Diagnostic Aids .......................................... 6E-356
Diagnostic Trouble Code (DTC) P1690
(Symptom Code 4) (Flash Code 77) Check
Engine Lamp (MIL) Circuit Voltage Low .. 6E-357
Diagnostic Trouble Code (DTC) P1690
(Symptom Code 8) (Flash Code 77) Check
Engine Lamp (MIL) Circuit Voltage High . 6E-360
SYMPTOM DIAGNOSIS ............................ 6E-361
PRELIMINARY CHECKS .......................... 6E-361
VISUAL/PHYSICAL CHECK ...................... 6E-361
INTERMITTENT ........................................ 6E-361
ENGINE CRANKS BUT WILL NOT RUN .. 6E-362
HARD START SYMPTOM ......................... 6E-366
ROUGH, UNSTABLE, OR INCORRECT
IDLE, STALLING SYMPTOM .................. 6E-370
SURGES AND/OR CHUGS SYMPTOM ... 6E-377
HESITATION, SAG, STUMBLE SYMPTOM 6E-383
CUTS OUT, MISSES SYMPTOM .............. 6E-389
LACK OF POWER, SLUGGISH OR
SPONGY SYMPTOM .............................. 6E-396
POOR FUEL ECONOMY SYMPTOM ....... 6E-402
EXCESSIVE WHITE SMOKE .................... 6E-407
EXCESSIVE BLACK SMOKE .................... 6E-413
ON-VEHICLE SERVICE PROCEDURE .... 6E-418
ENGINE CONTROL MODULE (ECM) ... 6E-418
CRANKSHAFT POSITION (CKP) SENSOR 6E-419
ENGINE COOLANT TEMPERATURE
(ECT) SENSOR ....................................... 6E-419
MASS AIR FLOW (MAF) & INTAKE AIR
TEMPERATURE (IAT) SENSOR ............ 6E-420
THROTTLE POSITION SENSOR (TPS) ... 6E-420
EGR EVRV
(Electrical Vacuum Regulating Valve) ..... 6E-421
Page 1381 of 4264
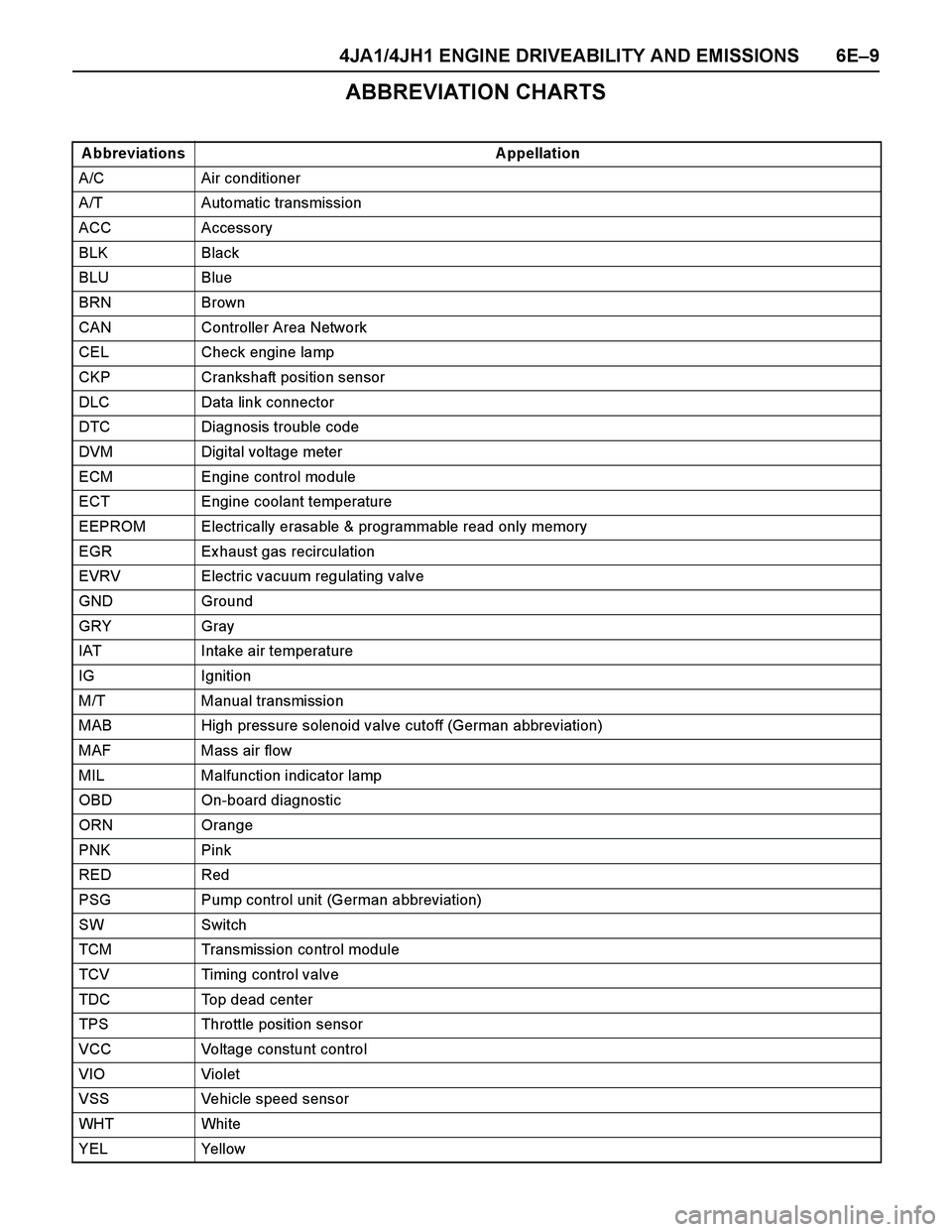
4JA1/4JH1 ENGINE DRIVEABILITY AND EMISSIONS 6E–9
ABBREVIATION CHARTS
A bbreviations A ppellation
A/C Air conditioner
A/T Automatic transmission
ACC Accessory
BLK Black
BLU Blue
BRN Brown
CAN Controller Area Network
CEL Check engine lamp
CKP Crankshaft position sensor
DLC Data link connector
DTC Diagnosis trouble code
DVM Digital voltage meter
ECM Engine control module
ECT Engine coolant temperature
EEPROM Electrically erasable & programmable read only memory
EGR Ex haust gas recirculation
EVRV Electric vacuum regulating valve
GND Ground
GRY Gray
IAT Intake air temperature
IG Ignition
M/T Manual transmission
MAB High pressure solenoid valve cutoff (German abbreviation)
MAF Mass air flow
MIL Malfunction indicator lamp
OBD On-board diagnostic
ORN Orange
PNK Pink
RED Red
PSG Pump control unit (German abbreviation)
SW Switch
TCM Transmission control module
TCV Timing control valve
TDC Top dead center
TPS Throttle position sensor
VCC Voltage constunt control
VIO Violet
VSS Vehicle speed sensor
WHT Whi te
YEL Yellow
Page 1412 of 4264
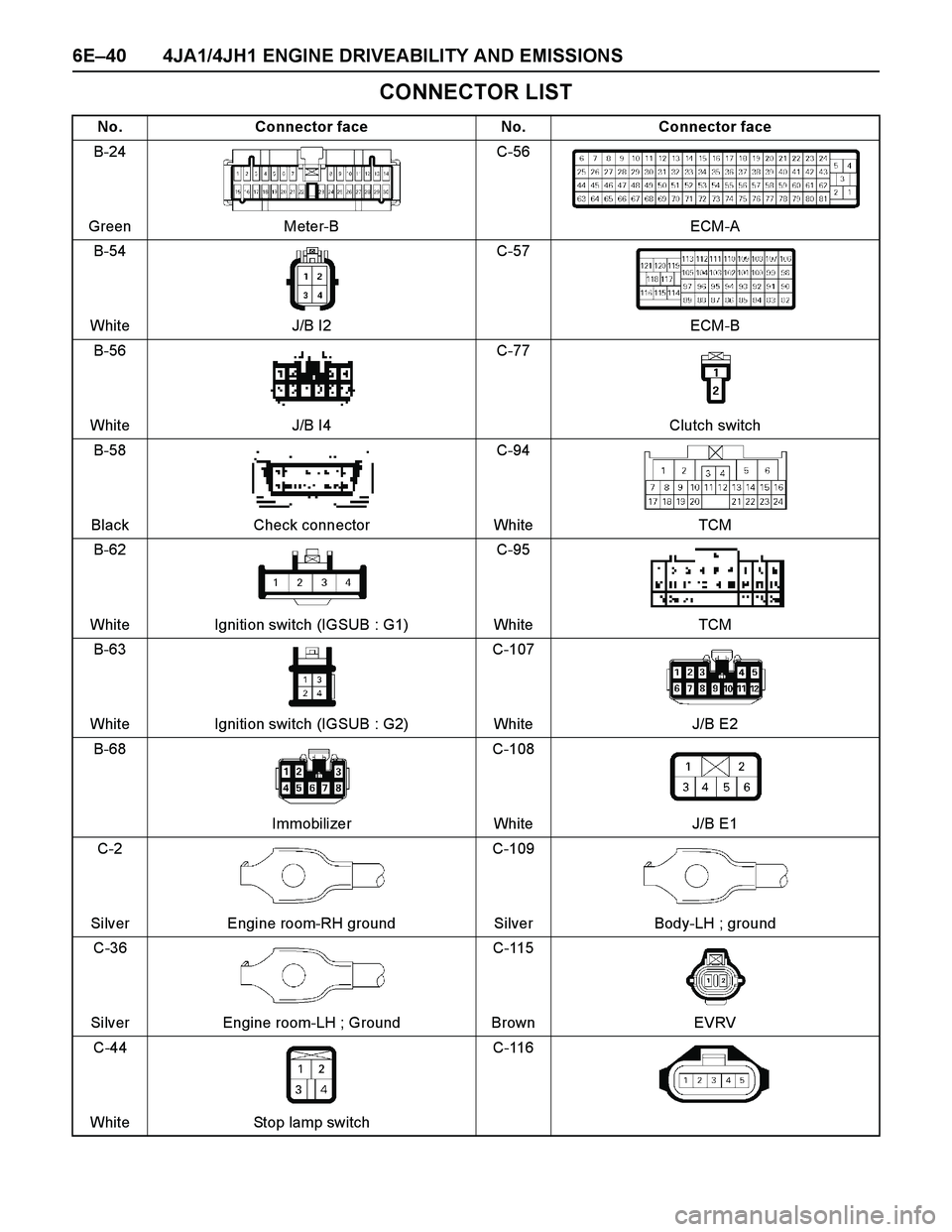
6E–40 4JA1/4JH1 ENGINE DRIVEABILITY AND EMISSIONS
CONNECTOR LIST
No. Connector face No. Connector face
B-24
Green Meter-BC-56
ECM-A
B-54
White J/B I2C-57
ECM-B
B-56
White J/B I4C-77
Clutch switch
B-58
Black Check connectorC-94
White TCM
B-62
White Ignition switch (IGSUB : G1)C-95
White TCM
B-63
White Ignition switch (IGSUB : G2)C-107
White J/B E2
B-68
ImmobilizerC-108
White J/B E1
C-2
Silver Engine room-RH groundC-109
Silver Body-LH ; ground
C-36
Silver Engine room-LH ; GroundC-115
Brown EVRV
C-44
White Stop lamp switchC-116
Page 1431 of 4264
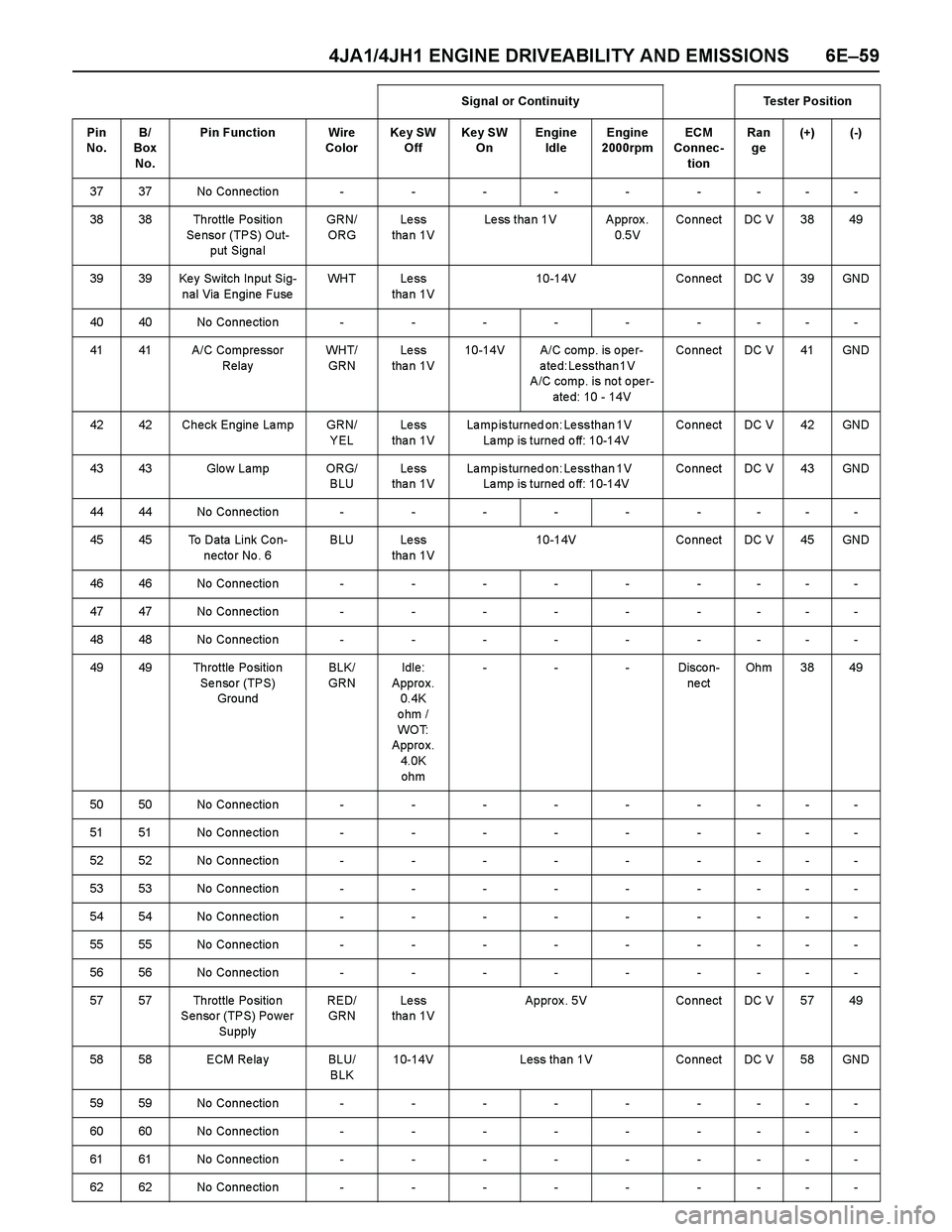
4JA1/4JH1 ENGINE DRIVEABILITY AND EMISSIONS 6E–59
3737No Connection---------
38 38 Throttle Po sitio n
Se nso r (TPS) Out-
put Signa lGRN/
ORGLe ss
tha n 1VLess than 1V Approx.
0.5VCo nnect DC V 38 49
39 39 Ke y Switch Input Sig-
nal Via Engine FuseWH T L e s s
tha n 1V10-14V Co nnect DC V 39 GND
4040No Connection---------
41 41 A/C Compressor
RelayWH T/
GRNLe ss
tha n 1V10-14V A/C comp. is o pe r-
ated: Less than 1V
A/C comp. is no t o pe r-
ate d: 10 - 14VCo nnect DC V 41 GND
42 42 Check Engine La mp GRN/
YELLe ss
tha n 1VLamp is turned on: Less than 1V
Lamp is turned off: 10-14VCo nnect DC V 42 GND
43 43 Glo w Lamp ORG/
BLULe ss
tha n 1VLamp is turned on: Less than 1V
Lamp is turned off: 10-14VCo nnect DC V 43 GND
4444No Connection---------
45 45 To Data Link Co n-
necto r No . 6BLU Less
tha n 1V10-14V Co nnect DC V 45 GND
4646No Connection---------
4747No Connection---------
4848No Connection---------
49 49 Throttle Po sitio n
Se nso r (TPS)
GroundBLK/
GRNIdle:
Appro x.
0.4K
ohm /
WO T:
Appro x.
4.0K
ohm---Discon-
ne ctOh m 3 8 4 9
5050No Connection---------
5151No Connection---------
5252No Connection---------
5353No Connection---------
5454No Connection---------
5555No Connection---------
5656No Connection---------
57 57 Throttle Po sitio n
Senso r (TPS) Po wer
SupplyRED/
GRNLe ss
tha n 1VApprox. 5V Connect DC V 57 49
58 58 ECM Re la y BLU/
BLK10-14V Less than 1V Connect DC V 58 GND
5959No Connection---------
6060No Connection---------
6161No Connection---------
6262No Connection---------Signal or Continuity Tester Position
Pin
No. B/
Box
No.Pin Function Wire
ColorKey SW
OffKey SW
OnEngine
IdleEngine
2000rpmECM
Connec-
tionRan
ge(+) (-)
Page 1449 of 4264
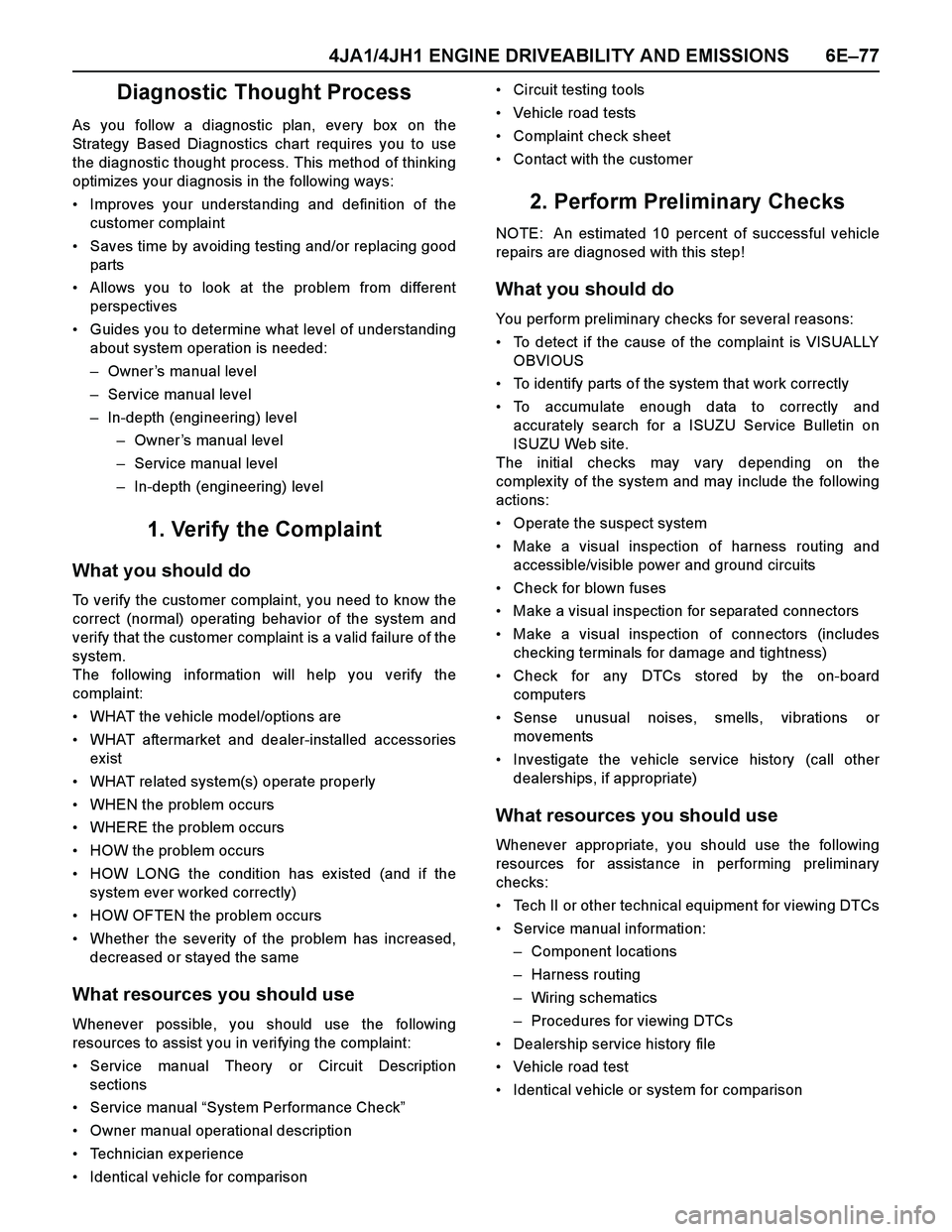
4JA1/4JH1 ENGINE DRIVEABILITY AND EMISSIONS 6E–77
Diagnostic Thought Process
As you follow a diagnostic plan, every box on the
Strategy Based Diagnostics chart requires you to use
the diagnostic thought process. This method of thinking
optimizes your diagnosis in the following ways:
Improves your understanding and definition of the
customer complaint
Saves time by avoiding testing and/or replacing good
parts
Allows you to look at the problem from different
perspectives
Guides you to determine what level of understanding
about system operation is needed:
–Owner’s manual level
–Service manual level
–In-depth (engineering) level
–Owner’s manual level
–Service manual level
–In-depth (engineering) level
1. Verify the Complaint
What you should do
To verify the customer complaint, you need to know the
correct (normal) operating behavior of the system and
verify that the customer complaint is a valid failure of the
system.
The following information will help you verify the
complaint:
WHAT the vehicle model/options are
WHAT aftermarket and dealer-installed accessories
exist
WHAT related system(s) operate properly
WHEN the problem occurs
WHERE the problem occurs
HOW the problem occurs
HOW LONG the condition has ex isted (and if the
system ever worked correctly)
HOW OFTEN the problem occurs
Whether the severity of the problem has increased,
decreased or stayed the same
What resources you should use
Whenever possible, you should use the following
resources to assist you in verifying the complaint:
Service manual Theory or Circuit Description
sections
Service manual “System Performance Check”
Owner manual operational description
Technician ex perience
Identical vehicle for comparisonCircuit testing tools
Vehicle road tests
Complaint check sheet
Contact with the customer
2. Perform Preliminary Checks
NOTE: An estimated 10 percent of successful vehicle
repairs are diagnosed with this step!
What you should do
You perform preliminary checks for several reasons:
To detect if the cause of the complaint is VISUALLY
OBVIOUS
To identify parts of the system that work correctly
To accumulate enough data to correctly and
accurately search for a ISUZU Service Bulletin on
ISUZU Web site.
The initial checks may vary depending on the
complex ity of the system and may include the following
actions:
Operate the suspect system
Make a visual inspection of harness routing and
accessible/visible power and ground circuits
Check for blown fuses
Make a visual inspection for separated connectors
Make a visual inspection of connectors (includes
checking terminals for damage and tightness)
Check for any DTCs stored by the on-board
computers
Sense unusual noises, smells, vibrations or
mov ements
Investigate the vehicle service history (call other
dealerships, if appropriate)
What resources you should use
Whenever appropriate, you should use the following
resources for assistance in performing preliminary
checks:
Tech II or other technical equipment for viewing DTCs
Service manual information:
–Component locations
–Harness routing
–Wiring schematics
–Procedures for viewing DTCs
Dealership service history file
Vehicle road test
Identical vehicle or system for comparison
Page 1450 of 4264
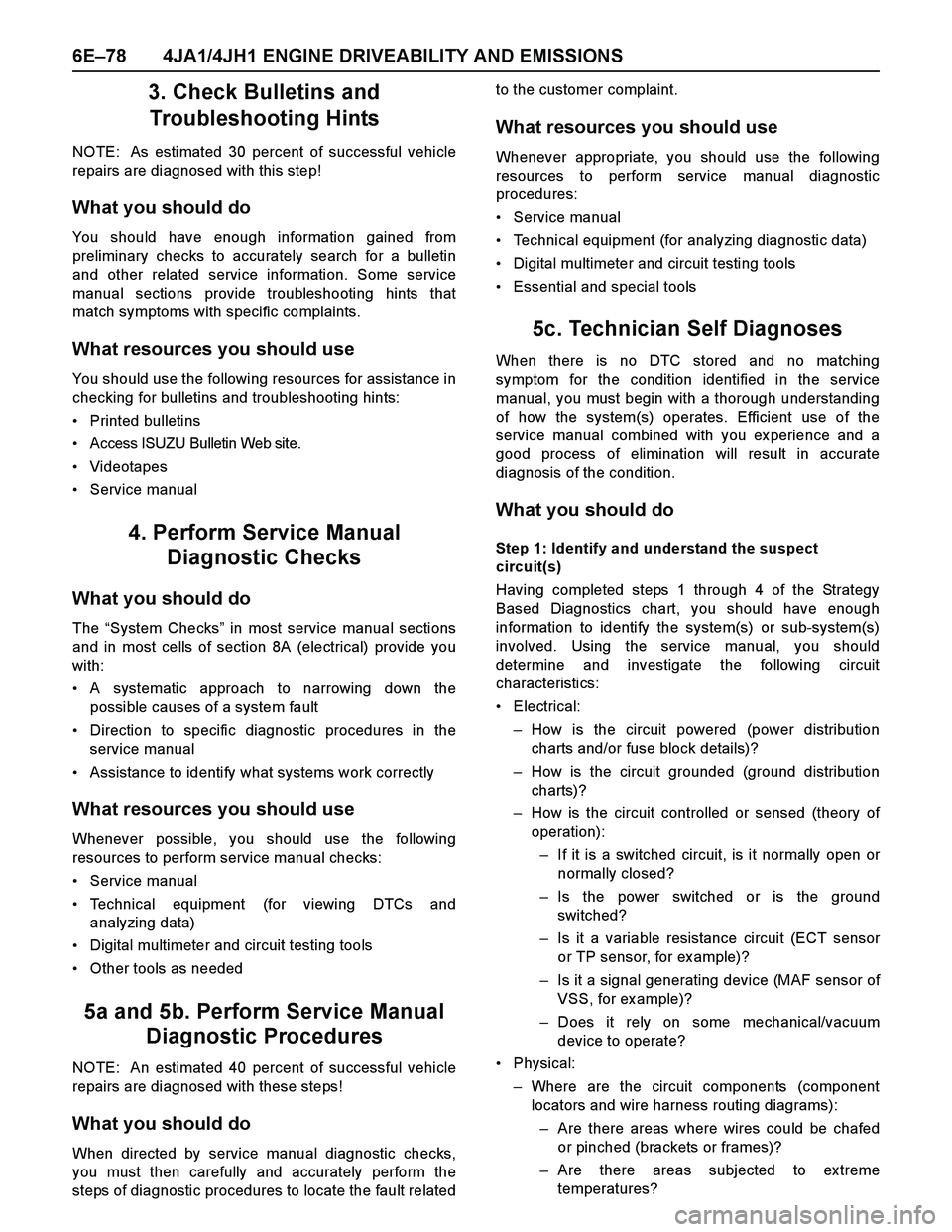
6E–78 4JA1/4JH1 ENGINE DRIVEABILITY AND EMISSIONS
3. Check Bulletins and
Troubleshooting Hints
NOTE: As estimated 30 percent of successful vehicle
repairs are diagnosed with this step!
What you should do
You should have enough information gained from
preliminary checks to accurately search for a bulletin
and other related service information. Some service
manual sections provide troubleshooting hints that
match symptoms with specific complaints.
What resources you should use
You should use the following resources for assistance in
checking for bulletins and troubleshooting hints:
Printed bulletins
Access ISUZU Bulletin Web site.
Videotapes
Service manual
4. Perform Service Manual
Diagnostic Checks
What you should do
The “System Checks” in most service manual sections
and in most cells of section 8A (electrical) provide you
with:
A systematic approach to narrowing down the
possible causes of a system fault
Direction to specific diagnostic procedures in the
service manual
Assistance to identify what systems work correctly
What resources you should use
Whenever possible, you should use the following
resources to perform service manual checks:
Service manual
Technical equipment (for viewing DTCs and
analyzing data)
Digital multimeter and circuit testing tools
Other tools as needed
5a and 5b. Perform Service Manual
Diagnostic Procedures
NOTE: An estimated 40 percent of successful vehicle
repairs are diagnosed with these steps!
What you should do
When directed by service manual diagnostic checks,
you must then carefully and accurately perform the
steps of diagnostic procedures to locate the fault relatedto the customer complaint.
What resources you should use
Whenever appropriate, you should use the following
resources to perform service manual diagnostic
procedures:
Service manual
Technical equipment (for analyzing diagnostic data)
Digital multimeter and circuit testing tools
Essential and special tools
5c. Technician Self Diagnoses
When there is no DTC stored and no matching
symptom for the condition identified in the service
manual, you must begin with a thorough understanding
of how the system(s) operates. Efficient use of the
service manual combined with you ex perience and a
good process of elimination will result in accurate
diagnosis of the condition.
What you should do
Step 1: Identify and understand the suspect
circuit(s)
Having completed steps 1 through 4 of the Strategy
Based Diagnostics chart, you should have enough
information to identify the system(s) or sub-system(s)
involved. Using the service manual, you should
determine and investigate the following circuit
characteristics:
Electrical:
–How is the circuit powered (power distribution
charts and/or fuse block details)?
–How is the circuit grounded (ground distribution
charts)?
–How is the circuit controlled or sensed (theory of
operation):
–If it is a switched circuit, is it normally open or
normally closed?
–Is the power switched or is the ground
switched?
–Is it a variable resistance circuit (ECT sensor
or TP sensor, for ex ample)?
–Is it a signal generating device (MAF sensor of
VSS, for example)?
–Does it rely on some mechanical/vacuum
device to operate?
Physical:
–Where are the circuit components (component
locators and wire harness routing diagrams):
–Are there areas where wires could be chafed
or pinched (brackets or frames)?
–Are there areas subjected to ex treme
temperatures?
Page 1451 of 4264
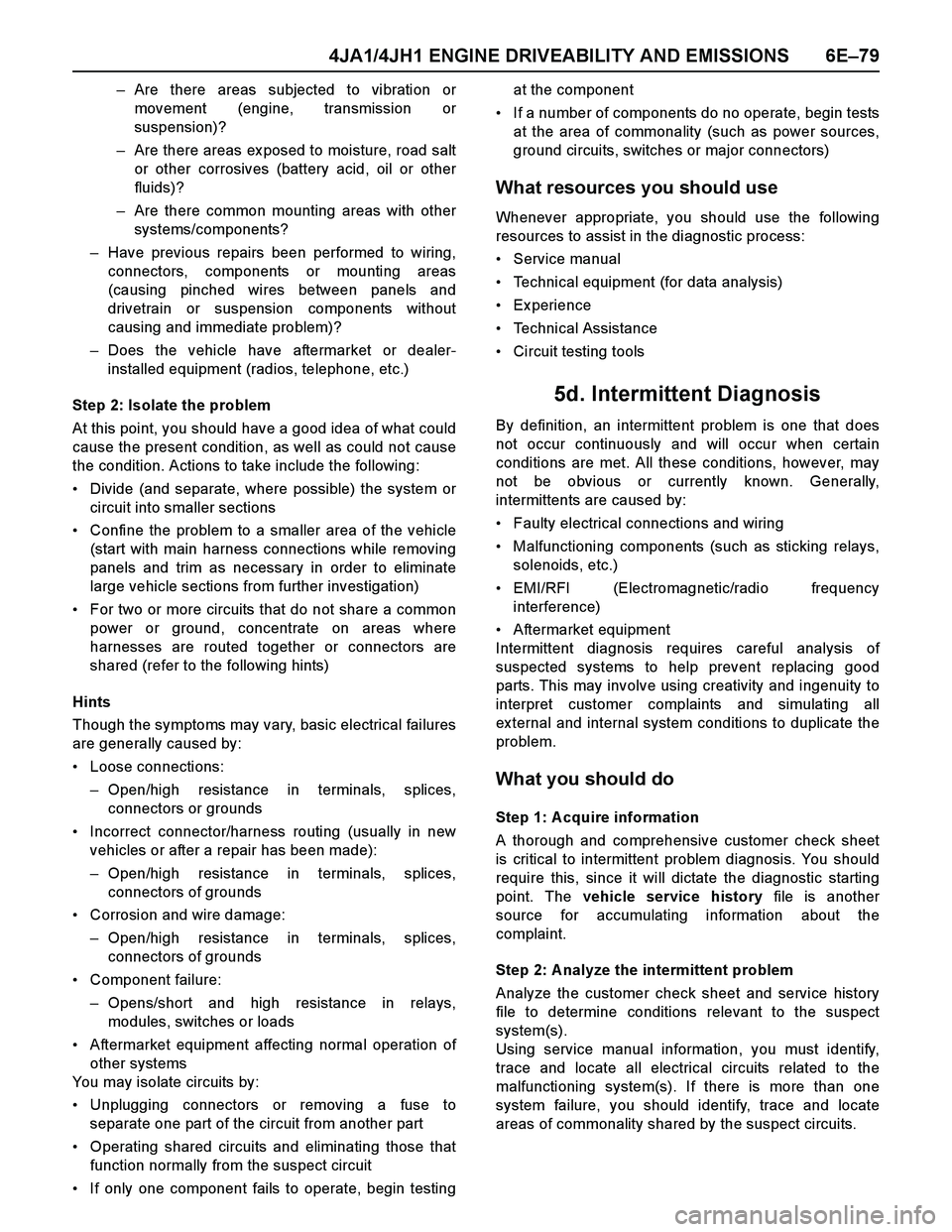
4JA1/4JH1 ENGINE DRIVEABILITY AND EMISSIONS 6E–79
–Are there areas subjected to vibration or
movement (engine, transmission or
suspension)?
–Are there areas ex posed to moisture, road salt
or other corrosives (battery acid, oil or other
fluids)?
–Are there common mounting areas with other
systems/components?
–Have previous repairs been performed to wiring,
connectors, components or mounting areas
(causing pinched wires between panels and
drivetrain or suspension components without
causing and immediate problem)?
–Does the vehicle have aftermarket or dealer-
installed equipment (radios, telephone, etc.)
Step 2: Isolate the problem
At this point, you should have a good idea of what could
cause the present condition, as well as could not cause
the condition. Actions to take include the following:
Divide (and separate, where possible) the system or
circuit into smaller sections
Confine the problem to a smaller area of the vehicle
(start with main harness connections while removing
panels and trim as necessary in order to eliminate
large vehicle sections from further investigation)
For two or more circuits that do not share a common
power or ground, concentrate on areas where
harnesses are routed together or connectors are
shared (refer to the following hints)
Hints
Though the symptoms may vary, basic electrical failures
are generally caused by:
Loose connections:
–Open/high resistance in terminals, splices,
connectors or grounds
Incorrect connector/harness routing (usually in new
vehicles or after a repair has been made):
–Open/high resistance in terminals, splices,
connectors of grounds
Corrosion and wire damage:
–Open/high resistance in terminals, splices,
connectors of grounds
Component failure:
–Opens/short and high resistance in relays,
modules, switches or loads
Aftermarket equipment affecting normal operation of
other systems
You may isolate circuits by:
Unplugging connectors or removing a fuse to
separate one part of the circuit from another part
Operating shared circuits and eliminating those that
function normally from the suspect circuit
If only one component fails to operate, begin testingat the component
If a number of components do no operate, begin tests
at the area of commonality (such as power sources,
ground circuits, switches or major connectors)
What resources you should use
Whenever appropriate, you should use the following
resources to assist in the diagnostic process:
Service manual
Technical equipment (for data analysis)
Ex perience
Technical Assistance
Circuit testing tools
5d. Intermittent Diagnosis
By definition, an intermittent problem is one that does
not occur continuously and will occur when certain
conditions are met. All these conditions, however, may
not be obvious or currently known. Generally,
intermittents are caused by:
Faulty electrical connections and wiring
Malfunctioning components (such as sticking relays,
solenoids, etc.)
EMI/RFI (Electromagnetic/radio frequency
interference)
Aftermarket equipment
Intermittent diagnosis requires careful analysis of
suspected systems to help prevent replacing good
parts. This may involve using creativity and ingenuity to
interpret customer complaints and simulating all
ex ternal and internal system conditions to duplicate the
problem.
What you should do
Step 1: A cquire information
A thorough and comprehensive customer check sheet
is critical to intermittent problem diagnosis. You should
require this, since it will dictate the diagnostic starting
point. The vehicle service history file is another
source for accumulating information about the
complaint.
Step 2: A nalyze the intermittent problem
Analyze the customer check sheet and service history
file to determine conditions relevant to the suspect
system(s).
Using service manual information, you must identify,
trace and locate all electrical circuits related to the
malfunctioning system(s). If there is more than one
system failure, you should identify, trace and locate
areas of commonality shared by the suspect circuits.
Page 1452 of 4264
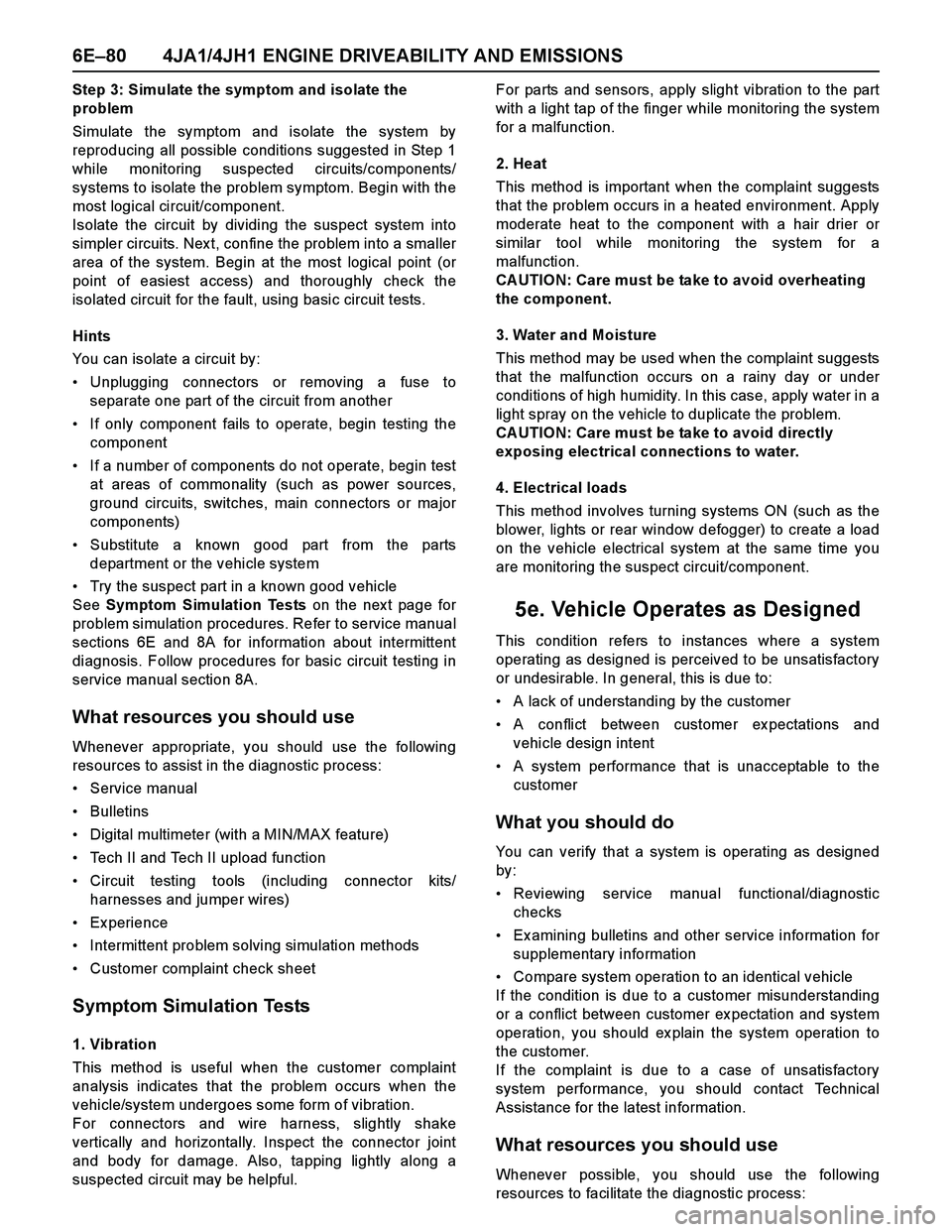
6E–80 4JA1/4JH1 ENGINE DRIVEABILITY AND EMISSIONS
Step 3: Simulate the symptom and isolate the
problem
Simulate the symptom and isolate the system by
reproducing all possible conditions suggested in Step 1
while monitoring suspected circuits/components/
systems to isolate the problem symptom. Begin with the
most logical circuit/component.
Isolate the circuit by dividing the suspect system into
simpler circuits. Nex t, confine the problem into a smaller
area of the system. Begin at the most logical point (or
point of easiest access) and thoroughly check the
isolated circuit for the fault, using basic circuit tests.
Hints
You can isolate a circuit by:
Unplugging connectors or removing a fuse to
separate one part of the circuit from another
If only component fails to operate, begin testing the
component
If a number of components do not operate, begin test
at areas of commonality (such as power sources,
ground circuits, switches, main connectors or major
components)
Substitute a known good part from the parts
department or the vehicle system
Try the suspect part in a known good vehicle
See Symptom Simulation Tests on the nex t page for
problem simulation procedures. Refer to service manual
sections 6E and 8A for information about intermittent
diagnosis. Follow procedures for basic circuit testing in
service manual section 8A.
What resources you should use
Whenever appropriate, you should use the following
resources to assist in the diagnostic process:
Service manual
Bulletins
Digital multimeter (with a MIN/MAX feature)
Tech II and Tech II upload function
Circuit testing tools (including connector kits/
harnesses and jumper wires)
Ex perience
Intermittent problem solving simulation methods
Customer complaint check sheet
Symptom Simulation Tests
1. Vibration
This method is useful when the customer complaint
analysis indicates that the problem occurs when the
vehicle/system undergoes some form of vibration.
For connectors and wire harness, slightly shake
vertically and horizontally. Inspect the connector joint
and body for damage. Also, tapping lightly along a
suspected circuit may be helpful.For parts and sensors, apply slight vibration to the part
with a light tap of the finger while monitoring the system
for a malfunction.
2. Heat
This method is important when the complaint suggests
that the problem occurs in a heated environment. Apply
moderate heat to the component with a hair drier or
similar tool while monitoring the system for a
malfunction.
CA UTION: Care must be take to avoid overheating
the component.
3. Water and Moisture
This method may be used when the complaint suggests
that the malfunction occurs on a rainy day or under
conditions of high humidity. In this case, apply water in a
light spray on the vehicle to duplicate the problem.
CA UTION: Care must be take to avoid directly
exposing electrical connections to water.
4. Electrical loads
This method involves turning systems ON (such as the
blower, lights or rear window defogger) to create a load
on the vehicle electrical system at the same time you
are monitoring the suspect circuit/component.
5e. Vehicle Operates as Designed
This condition refers to instances where a system
operating as designed is perceived to be unsatisfactory
or undesirable. In general, this is due to:
A lack of understanding by the customer
A conflict between customer ex pectations and
vehicle design intent
A system performance that is unacceptable to the
customer
What you should do
You can verify that a system is operating as designed
by:
Reviewing service manual functional/diagnostic
checks
Ex amining bulletins and other service information for
supplementary information
Compare system operation to an identical vehicle
If the condition is due to a customer misunderstanding
or a conflict between customer ex pectation and system
operation, you should ex plain the system operation to
the customer.
If the complaint is due to a case of unsatisfactory
system performance, you should contact Technical
Assistance for the latest information.
What resources you should use
Whenever possible, you should use the following
resources to facilitate the diagnostic process:
Page 1453 of 4264
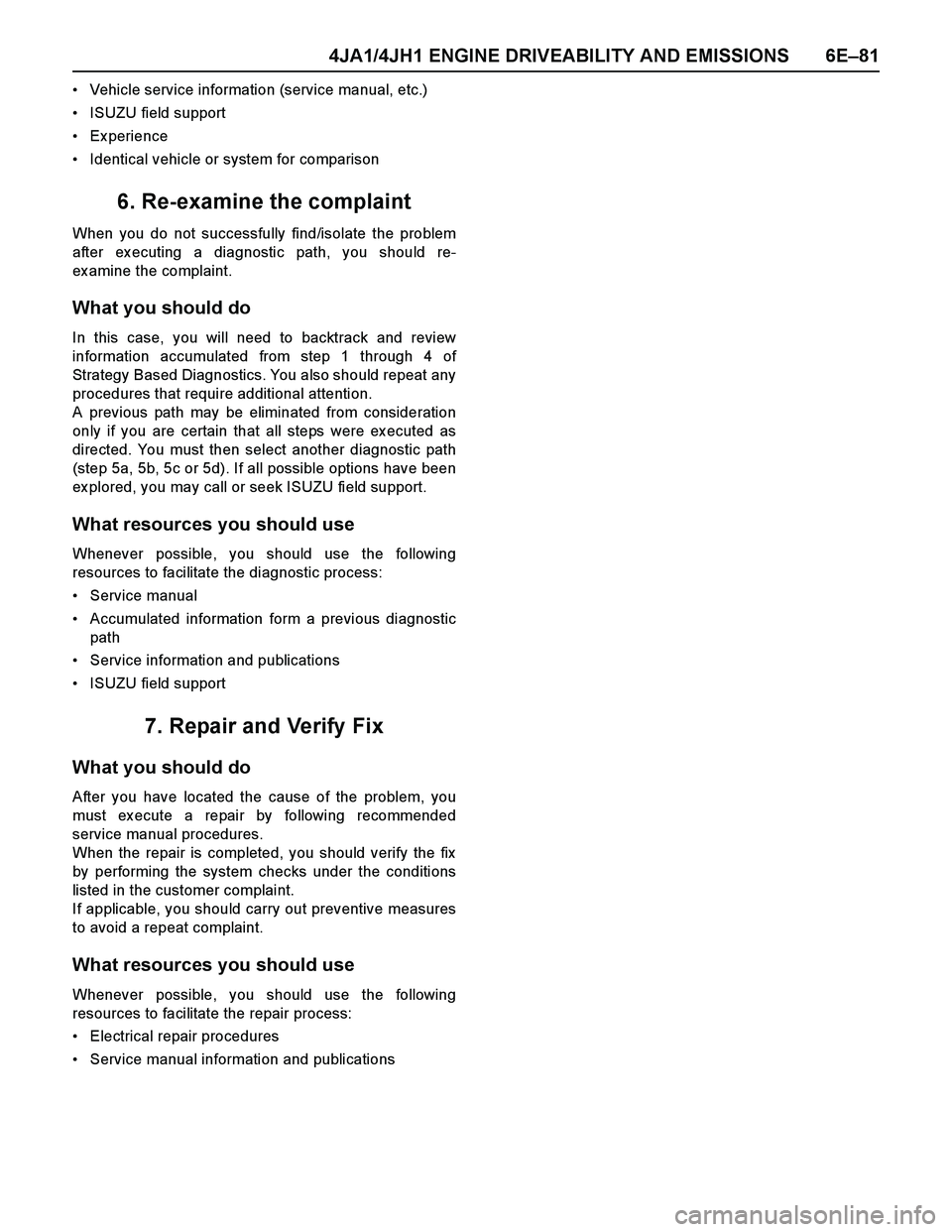
4JA1/4JH1 ENGINE DRIVEABILITY AND EMISSIONS 6E–81
Vehicle service information (service manual, etc.)
ISUZU field support
Ex perience
Identical vehicle or system for comparison
6. Re-examine the complaint
When you do not successfully find/isolate the problem
after ex ecuting a diagnostic path, you should re-
ex amine the complaint.
What you should do
In this case, you will need to backtrack and review
information accumulated from step 1 through 4 of
Strategy Based Diagnostics. You also should repeat any
procedures that require additional attention.
A previous path may be eliminated from consideration
only if you are certain that all steps were ex ecuted as
directed. You must then select another diagnostic path
(step 5a, 5b, 5c or 5d). If all possible options have been
ex plored, you may call or seek ISUZU field support.
What resources you should use
Whenever possible, you should use the following
resources to facilitate the diagnostic process:
Service manual
Accumulated information form a previous diagnostic
path
Service information and publications
ISUZU field support
7. Repair and Verify Fix
What you should do
After you have located the cause of the problem, you
must ex ecute a repair by following recommended
service manual procedures.
When the repair is completed, you should verify the fix
by performing the system checks under the conditions
listed in the customer complaint.
If applicable, you should carry out preventive measures
to avoid a repeat complaint.
What resources you should use
Whenever possible, you should use the following
resources to facilitate the repair process:
Electrical repair procedures
Service manual information and publications