reverse ISUZU TF SERIES 2004 Workshop Manual
[x] Cancel search | Manufacturer: ISUZU, Model Year: 2004, Model line: TF SERIES, Model: ISUZU TF SERIES 2004Pages: 4264, PDF Size: 72.63 MB
Page 3271 of 4264

MANUAL TRANSMISSION 7B1-107
Main Data and Specifications
General Specifications
MUA5G MUA5S
Transmission type Fully synchronized forward and reverse gears
Control method Remote control with the gear shift lever on the floor.
Gear ratio: Transmission 1st 4.008 4.357
2nd 2.301 2.502
3rd 1.427 1.501
4th 1.000 1.000
5th 0.828 0.809
Rev. 3.651 3.970
Transmission oil capacity 2.95 lit. (3.12 US qt)
Type of lubricant Engine oil: Refer to the chart in "SECTION 0"
Page 3275 of 4264
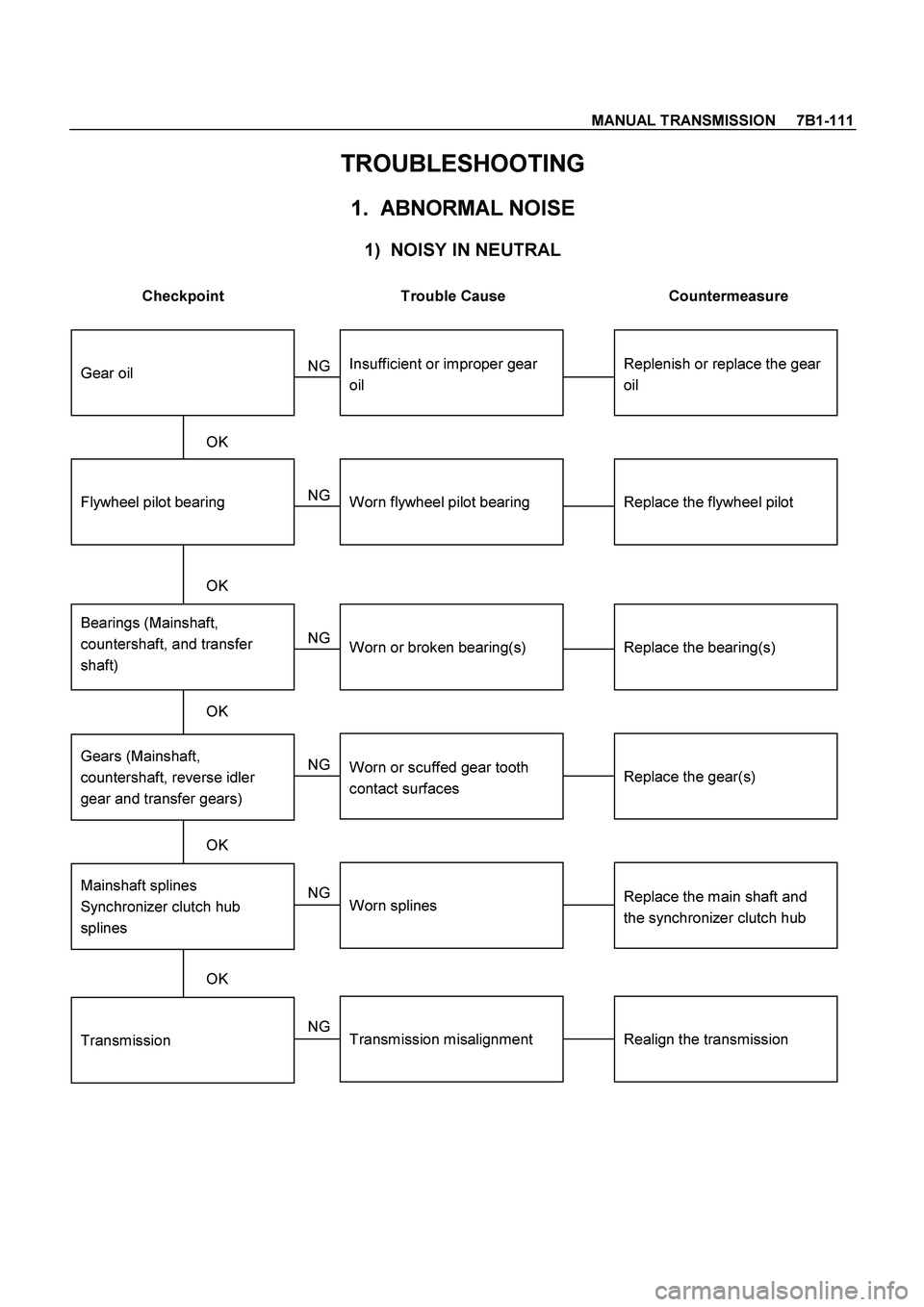
MANUAL TRANSMISSION 7B1-111
TROUBLESHOOTING
1. ABNORMAL NOISE
1) NOISY IN NEUTRAL
Checkpoint Trouble Cause Countermeasure
Replenish or replace the gear
oilInsufficient or improper gear
oil NG
Mainshaft splines
Synchronizer clutch hub
splinesReplace the main shaft and
the synchronizer clutch hub
Replace the gear(s)
Replace the flywheel pilot
Worn splines
Worn or scuffed gear tooth
contact surfaces
Flywheel pilot bearingWorn flywheel pilot bearing
Bearings (Mainshaft,
countershaft, and transfer
shaft)
Gears (Mainshaft,
countershaft, reverse idler
gear and transfer gears)
Replace the bearing(s)Worn or broken bearing(s)
OK
NG NG NG NG OK
OK
OK
Gear oil
TransmissionRealign the transmissionTransmission misalignment OK
NG
Page 3688 of 4264
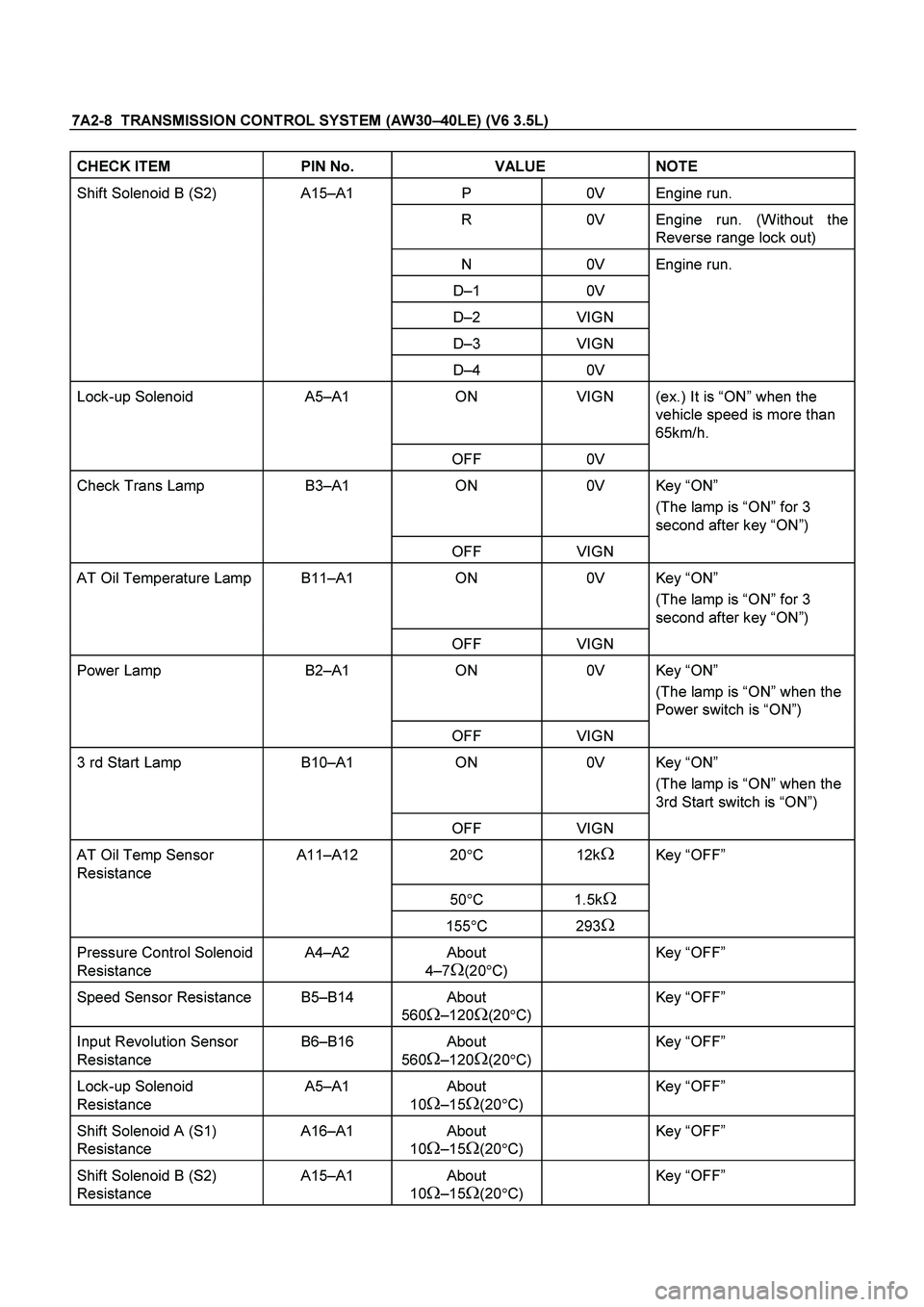
7A2-8 TRANSMISSION CONTROL SYSTEM (AW30 –40LE) (V6 3.5L)
CHECK ITEM PIN No. VALUE NOTE
Shift Solenoid B (S2) A15 –A1 P 0V Engine run.
R 0V Engine run. (Without the
Reverse range lock out)
N 0V Engine run.
D –1 0V
D –2 VIGN
D –3 VIGN
D –4 0V
Lock-up Solenoid A5
–A1 ON VIGN (ex.) It is “ON ” when the
vehicle speed is more than
65km/h.
OFF 0V
Check Trans Lamp B3
–A1 ON 0V Key “ON ”
(The lamp is “ON ” for 3
second after key “ON ”)
OFF VIGN
AT Oil Temperature Lamp B11
–A1 ON 0V Key “ON ”
(The lamp is “ON ” for 3
second after key “ON ”)
OFF VIGN
Power Lamp B2
–A1 ON 0V Key “ON ”
(The lamp is “ON ” when the
Power switch is “ON ”)
OFF VIGN
3 rd Start Lamp B10
–A1 ON 0V Key “ON ”
(The lamp is “ON ” when the
3rd Start switch is “ON ”)
OFF VIGN
AT Oil Temp Sensor
Resistance A11
–A12 20
C
12kKey “OFF ”
50
C 1.5k
155
C 293
Pressure Control Solenoid
Resistance A4
–A2 About
4 –7
(20
C)
Key “OFF ”
Speed Sensor Resistance B5 –B14 About
560
– 120(20
C)
Key “OFF ”
Input Revolution Sensor
Resistance B6
–B16 About
560
– 120(20
C)
Key “OFF ”
Lock-up Solenoid
Resistance A5
–A1 About
10
– 15(20
C)
Key “OFF ”
Shift Solenoid A (S1)
Resistance A16
–A1 About
10
– 15(20 C)
Key “OFF ”
Shift Solenoid B (S2)
Resistance A15
–A1 About
10
– 15(20
C)
Key “OFF ”
Page 3690 of 4264
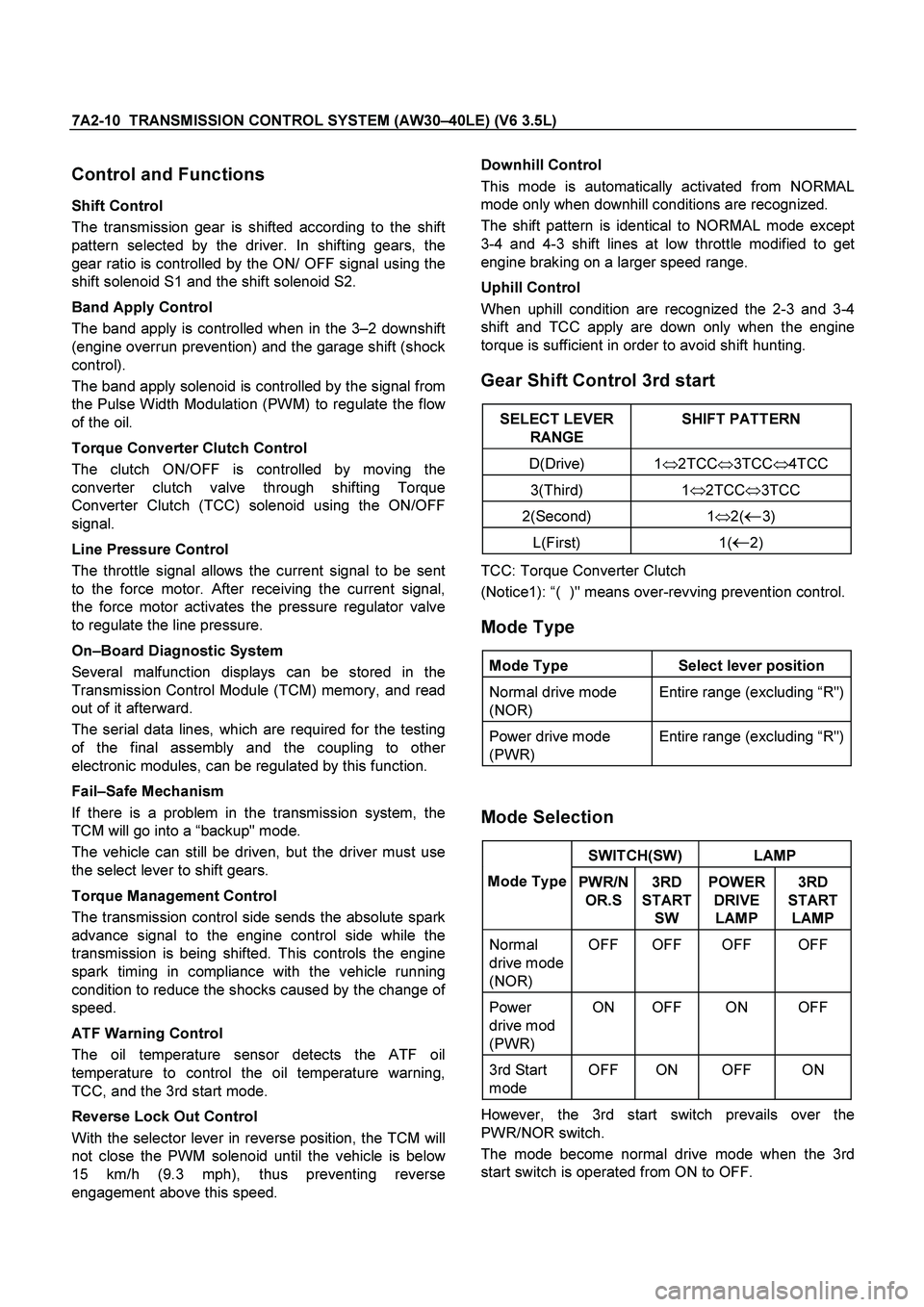
7A2-10 TRANSMISSION CONTROL SYSTEM (AW30 –40LE) (V6 3.5L)
Control and Functions
Shift Control
The transmission gear is shifted according to the shift
pattern selected by the driver. In shifting gears, the
gear ratio is controlled by the ON/ OFF signal using the
shift solenoid S1 and the shift solenoid S2.
Band Apply Control
The band apply is controlled when in the 3 –2 downshift
(engine overrun prevention) and the garage shift (shock
control).
The band apply solenoid is controlled by the signal from
the Pulse Width Modulation (PWM) to regulate the flow
of the oil.
Torque Converter Clutch Control
The clutch ON/OFF is controlled by moving the
converter clutch valve through shifting Torque
Converter Clutch (TCC) solenoid using the ON/OFF
signal.
Line Pressure Control
The throttle signal allows the current signal to be sent
to the force motor. After receiving the current signal,
the force motor activates the pressure regulator valve
to regulate the line pressure.
On –Board Diagnostic System
Several malfunction displays can be stored in the
Transmission Control Module (TCM) memory, and read
out of it afterward.
The serial data lines, which are required for the testing
of the final assembly and the coupling to othe
r
electronic modules, can be regulated by this function.
Fail –Safe Mechanism
If there is a problem in the transmission system, the
TCM will go into a “backup" mode.
The vehicle can still be driven, but the driver must use
the select lever to shift gears.
Torque Management Control
The transmission control side sends the absolute spark
advance signal to the engine control side while the
transmission is being shifted. This controls the engine
spark timing in compliance with the vehicle running
condition to reduce the shocks caused by the change o
f
speed.
ATF Warning Control
The oil temperature sensor detects the ATF oil
temperature to control the oil temperature warning,
TCC, and the 3rd start mode.
Reverse Lock Out Control
With the selector lever in reverse position, the TCM will
not close the PWM solenoid until the vehicle is below
15 km/h (9.3 mph), thus preventing reverse
engagement above this speed.
Downhill Control
This mode is automatically activated from NORMAL
mode only when downhill conditions are recognized.
The shift pattern is identical to NORMAL mode except
3-4 and 4-3 shift lines at low throttle modified to get
engine braking on a larger speed range.
Uphill Control
When uphill condition are recognized the 2-3 and 3-4
shift and TCC apply are down only when the engine
torque is sufficient in order to avoid shift hunting.
Gear Shift Control 3rd start
SELECT LEVER RANGE SHIFT PATTERN
D(Drive) 1
2TCC
3TCC
4TCC
3(Third) 1
2TCC
3TCC
2(Second) 1
2(3)
L(First) 1(2)
TCC: Torque Converter Clutch
(Notice1): “( )" means over-revving prevention control.
Mode Type
Mode Type Select lever position
Normal drive mode
(NOR) Entire range (excluding “R")
Power drive mode
(PWR) Entire range (excluding “R")
Mode Selection
SWITCH(SW) LAMP
Mode Type PWR/N
OR.S 3RD
START SW POWER
DRIVE LAMP 3RD
START LAMP
Normal
drive mode
(NOR) OFF OFF OFF OFF
Power
drive mod
(PWR) ON OFF ON OFF
3rd Start
mode OFF ON OFF ON
However, the 3rd start switch prevails over the
PWR/NOR switch.
The mode become normal drive mode when the 3rd
start switch is operated from ON to OFF.
Page 3691 of 4264
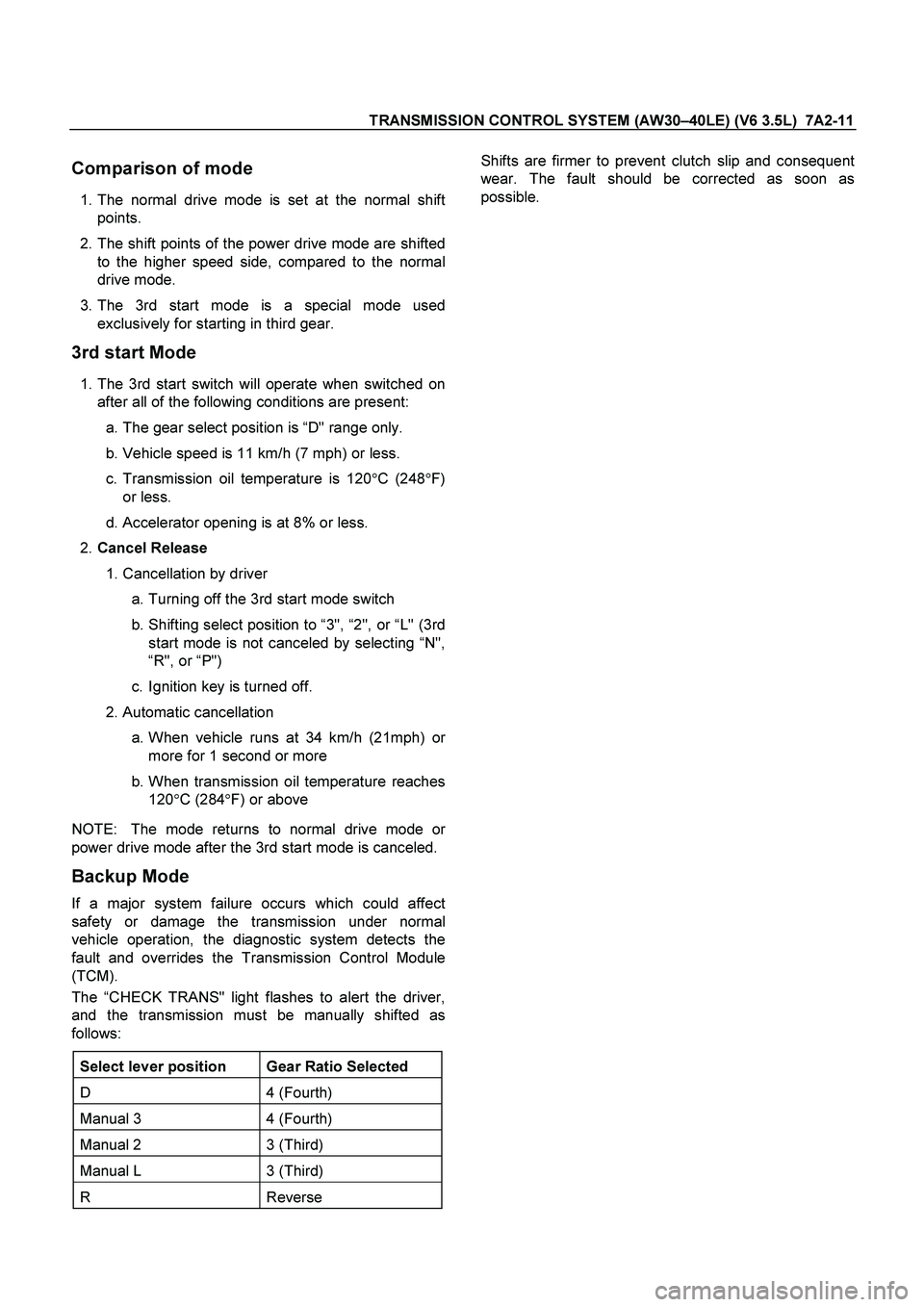
TRANSMISSION CONTROL SYSTEM (AW30 –40LE) (V6 3.5L) 7A2-11
Comparison of mode
1. The normal drive mode is set at the normal shift
points.
2. The shift points of the power drive mode are shifted
to the higher speed side, compared to the normal
drive mode.
3. The 3rd start mode is a special mode used
exclusively for starting in third gear.
3rd start Mode
1. The 3rd start switch will operate when switched on
after all of the following conditions are present:
a. The gear select position is “D" range only.
b. Vehicle speed is 11 km/h (7 mph) or less.
c. Transmission oil temperature is 120
C (248
F)
or less.
d. Accelerator opening is at 8% or less.
2. Cancel Release
1. Cancellation by driver
a. Turning off the 3rd start mode switch
b. Shifting select position to “3", “2", or “L" (3rd
start mode is not canceled by selecting “N",
“ R", or “P")
c. Ignition key is turned off.
2. Automatic cancellation
a. When vehicle runs at 34 km/h (21mph) o
r
more for 1 second or more
b. When transmission oil temperature reaches 120
C (284
F) or above
NOTE: The mode returns to normal drive mode o
r
power drive mode after the 3rd start mode is canceled.
Backup Mode
If a major system failure occurs which could affect
safety or damage the transmission under normal
vehicle operation, the diagnostic system detects the
fault and overrides the Transmission Control Module
(TCM).
The “CHECK TRANS" light flashes to alert the driver,
and the transmission must be manually shifted as
follows:
Select lever position Gear Ratio Selected
D 4 (Fourth)
Manual 3 4 (Fourth)
Manual 2 3 (Third)
Manual L 3 (Third)
R Reverse
Shifts are firmer to prevent clutch slip and consequent
wear. The fault should be corrected as soon as
possible.
Page 3732 of 4264
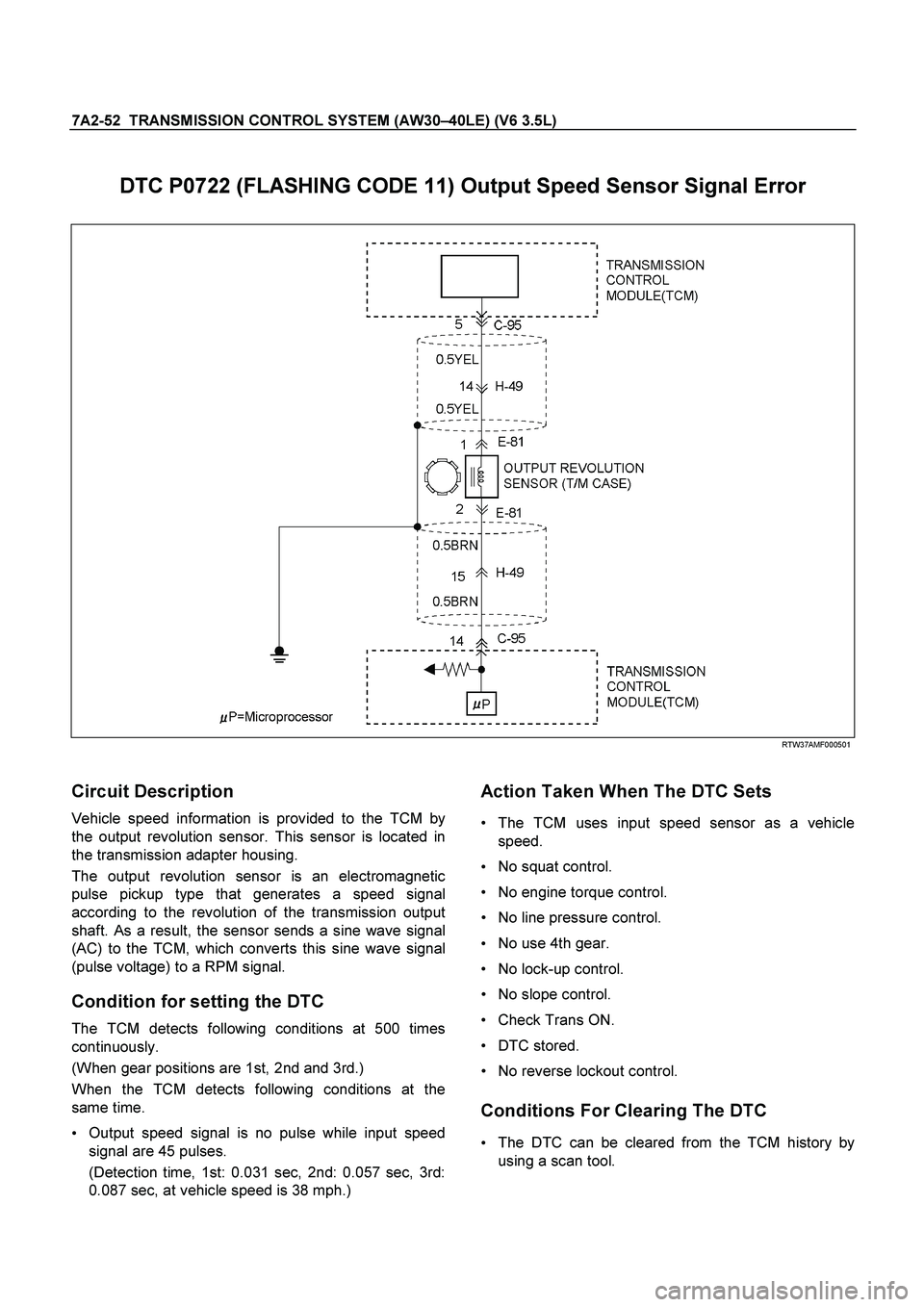
7A2-52 TRANSMISSION CONTROL SYSTEM (AW30–40LE) (V6 3.5L)
DTC P0722 (FLASHING CODE 11) Output Speed Sensor Signal Error
RTW37AMF000501
Circuit Description
Vehicle speed information is provided to the TCM by
the output revolution sensor. This sensor is located in
the transmission adapter housing.
The output revolution sensor is an electromagnetic
pulse pickup type that generates a speed signal
according to the revolution of the transmission output
shaft. As a result, the sensor sends a sine wave signal
(AC) to the TCM, which converts this sine wave signal
(pulse voltage) to a RPM signal.
Condition for setting the DTC
The TCM detects following conditions at 500 times
continuously.
(When gear positions are 1st, 2nd and 3rd.)
When the TCM detects following conditions at the
same time.
Output speed signal is no pulse while input speed
signal are 45 pulses.
(Detection time, 1st: 0.031 sec, 2nd: 0.057 sec, 3rd:
0.087 sec, at vehicle speed is 38 mph.)
Action Taken When The DTC Sets
The TCM uses input speed sensor as a vehicle
speed.
No squat control.
No engine torque control.
No line pressure control.
No use 4th gear.
No lock-up control.
No slope control.
Check Trans ON.
DTC stored.
No reverse lockout control.
Conditions For Clearing The DTC
The DTC can be cleared from the TCM history by
using a scan tool.
Page 3773 of 4264
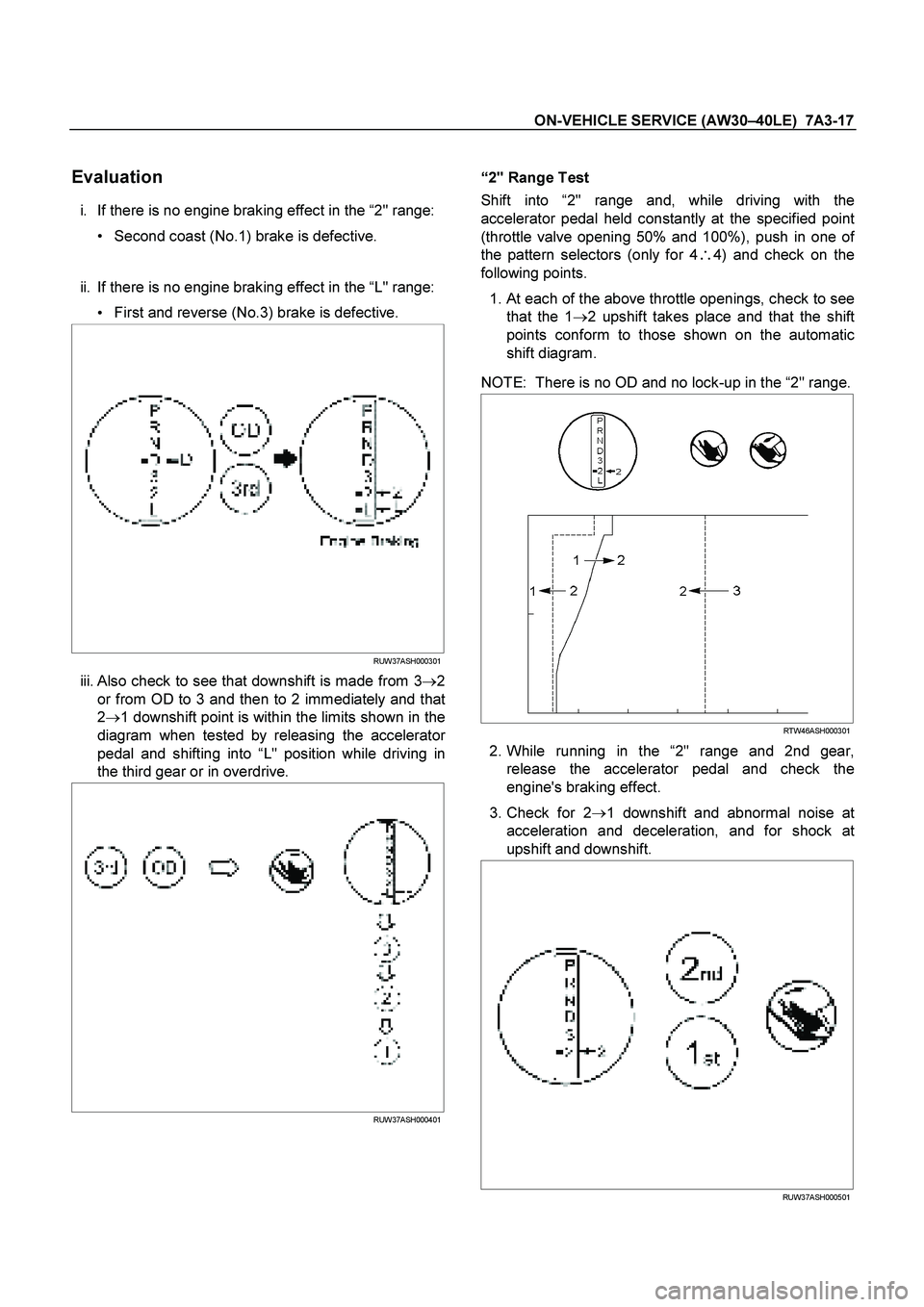
ON-VEHICLE SERVICE (AW30 –40LE) 7A3-17
Evaluation
i. If there is no engine braking effect in the “2" range:
Second coast (No.1) brake is defective.
ii. If there is no engine braking effect in the “L" range:
First and reverse (No.3) brake is defective.
RUW37ASH000301
iii. Also check to see that downshift is made from 3 2
or from OD to 3 and then to 2 immediately and that
2
1 downshift point is within the limits shown in the
diagram when tested by releasing the accelerato
r
pedal and shifting into “L" position while driving in
the third gear or in overdrive.
RUW37ASH000401
“ 2" Range Test
Shift into “2" range and, while driving with the
accelerator pedal held constantly at the specified point
(throttle valve opening 50% and 100%), push in one o
f
the pattern selectors (only for 4
4) and check on the
following points.
1.
At each of the above throttle openings, check to see
that the 1
2 upshift takes place and that the shift
points conform to those shown on the automatic
shift diagram.
NOTE: There is no OD and no lock-up in the “2" range.
RTW46ASH000301
2. While running in the “2" range and 2nd gear,
release the accelerator pedal and check the
engine's braking effect.
3. Check for 2
1 downshift and abnormal noise at
acceleration and deceleration, and for shock at
upshift and downshift.
RUW37ASH000501
Page 3779 of 4264
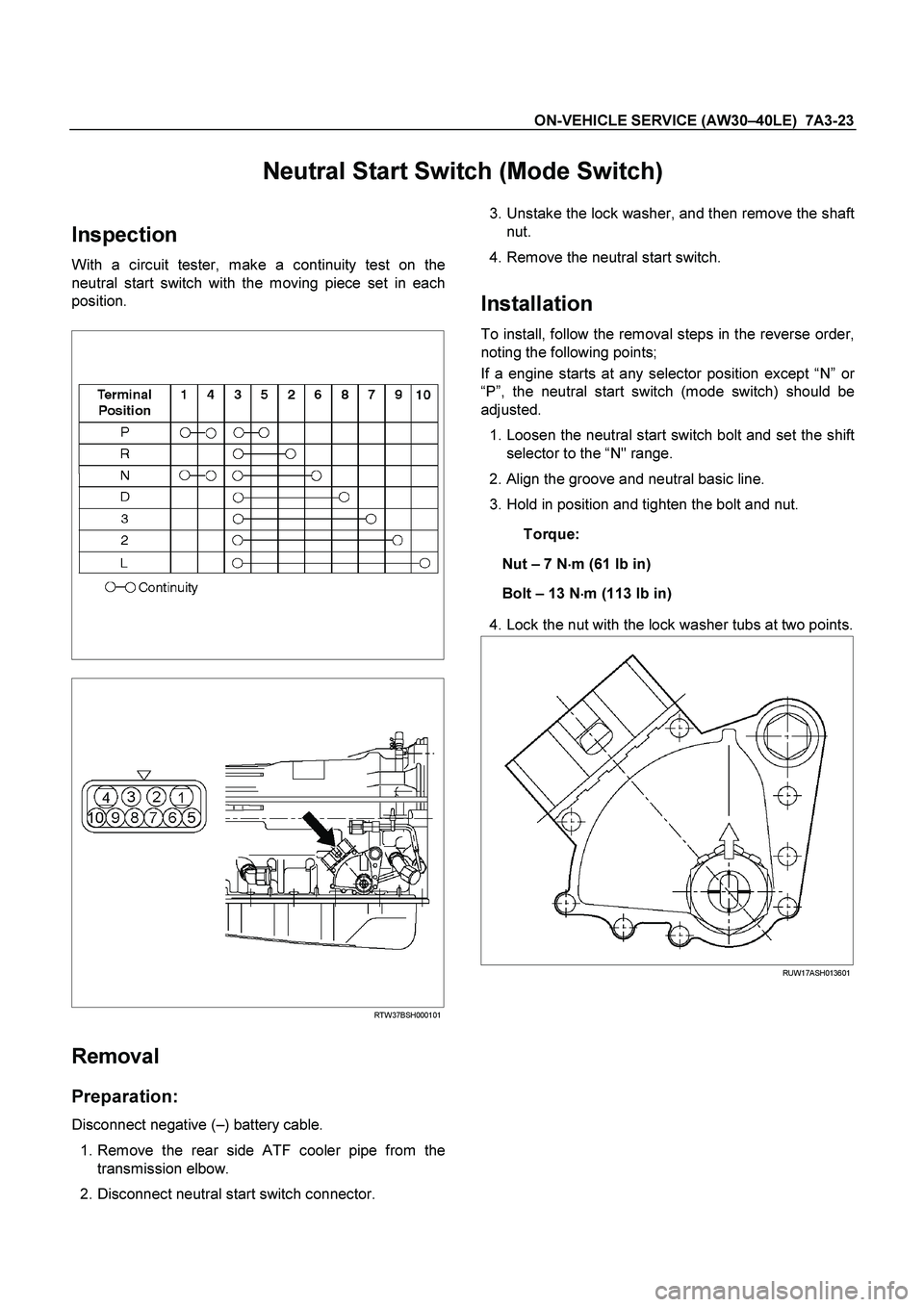
ON-VEHICLE SERVICE (AW30 –40LE) 7A3-23
Neutral Start Switch (Mode Switch)
Inspection
With a circuit tester, make a continuity test on the
neutral start switch with the moving piece set in each
position.
RTW37BSH000101
Removal
Preparation:
Disconnect negative ( –) battery cable.
1. Remove the rear side ATF cooler pipe from the
transmission elbow.
2. Disconnect neutral start switch connector.
3. Unstake the lock washer, and then remove the shaft
nut.
4. Remove the neutral start switch.
Installation
To install, follow the removal steps in the reverse order,
noting the following points;
If a engine starts at any selector position except “N ” o
r
“ P ”, the neutral start switch (mode switch) should be
adjusted.
1. Loosen the neutral start switch bolt and set the shift
selector to the “N" range.
2. Align the groove and neutral basic line.
3. Hold in position and tighten the bolt and nut.
Torque:
Nut – 7 N
m (61 Ib in)
Bolt – 13 N
m (113 Ib in)
4. Lock the nut with the lock washer tubs at two points.
RUW17ASH013601
Page 3790 of 4264
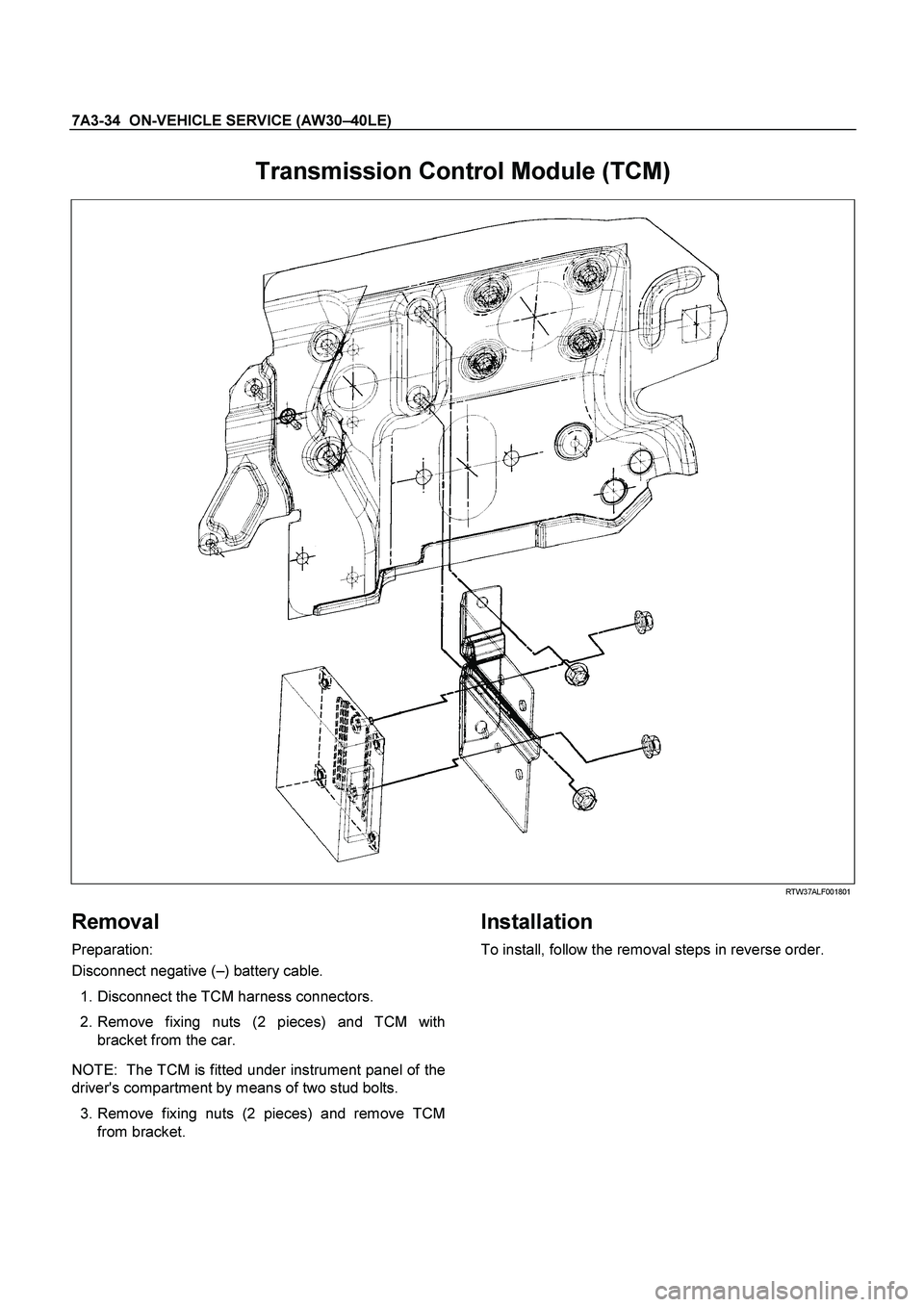
7A3-34 ON-VEHICLE SERVICE (AW30 –40LE)
Transmission Control Module (TCM)
RTW37ALF001801
Removal
Preparation:
Disconnect negative ( –) battery cable.
1. Disconnect the TCM harness connectors.
2. Remove fixing nuts (2 pieces) and TCM with bracket from the car.
NOTE: The TCM is fitted under instrument panel of the
driver's compartment by means of two stud bolts.
3. Remove fixing nuts (2 pieces) and remove TCM
from bracket.
Installation
To install, follow the removal steps in reverse order.
Page 3792 of 4264
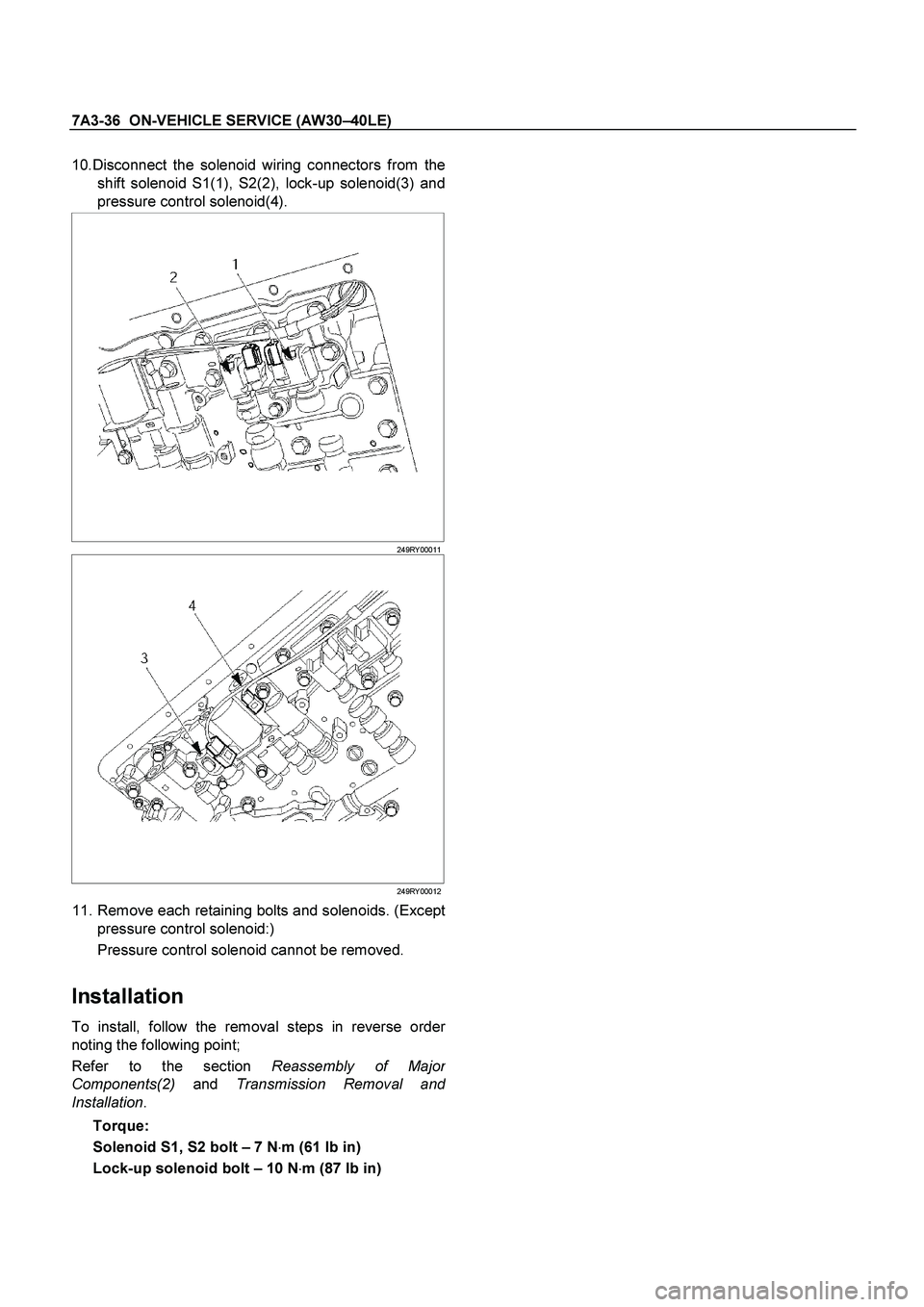
7A3-36 ON-VEHICLE SERVICE (AW30 –40LE)
10.Disconnect the solenoid wiring connectors from the
shift solenoid S1(1), S2(2), lock-up solenoid(3) and
pressure control solenoid(4).
249RY 00011
249RY 00012
11. Remove each retaining bolts and solenoids. (Except
pressure control solenoid:)
Pressure control solenoid cannot be removed.
Installation
To install, follow the removal steps in reverse order
noting the following point;
Refer to the section Reassembly of Majo
r
Components(2) and Transmission Removal an
d
Installation .
Torque:
Solenoid S1, S2 bolt – 7 N m (61 Ib in)
Lock-up solenoid bolt – 10 N m (87 Ib in)