fuel pressure ISUZU TF SERIES 2004 Workshop Manual
[x] Cancel search | Manufacturer: ISUZU, Model Year: 2004, Model line: TF SERIES, Model: ISUZU TF SERIES 2004Pages: 4264, PDF Size: 72.63 MB
Page 2531 of 4264
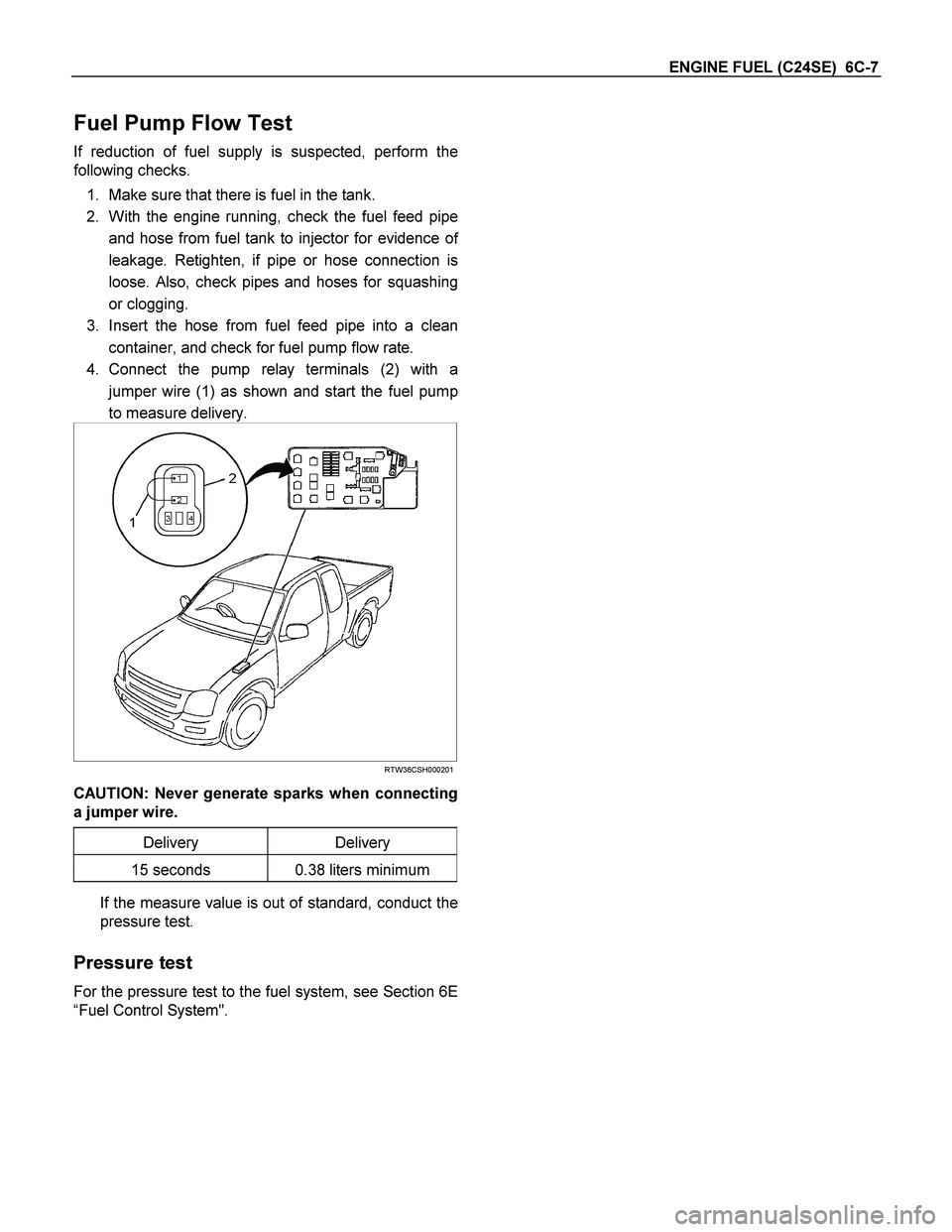
ENGINE FUEL (C24SE) 6C-7
Fuel Pump Flow Test
If reduction of fuel supply is suspected, perform the
following checks.
1. Make sure that there is fuel in the tank.
2. With the engine running, check the fuel feed pipe
and hose from fuel tank to injector for evidence o
f
leakage. Retighten, if pipe or hose connection is
loose. Also, check pipes and hoses for squashing
or clogging.
3. Insert the hose from fuel feed pipe into a clean
container, and check for fuel pump flow rate.
4. Connect the pump relay terminals (2) with a
jumper wire (1) as shown and start the fuel pump
to measure delivery.
RTW36CSH000201
CAUTION: Never generate sparks when connecting
a jumper wire.
Delivery Delivery
15 seconds 0.38 liters minimum
If the measure value is out of standard, conduct the
pressure test.
Pressure test
For the pressure test to the fuel system, see Section 6E
“Fuel Control System".
Page 2533 of 4264
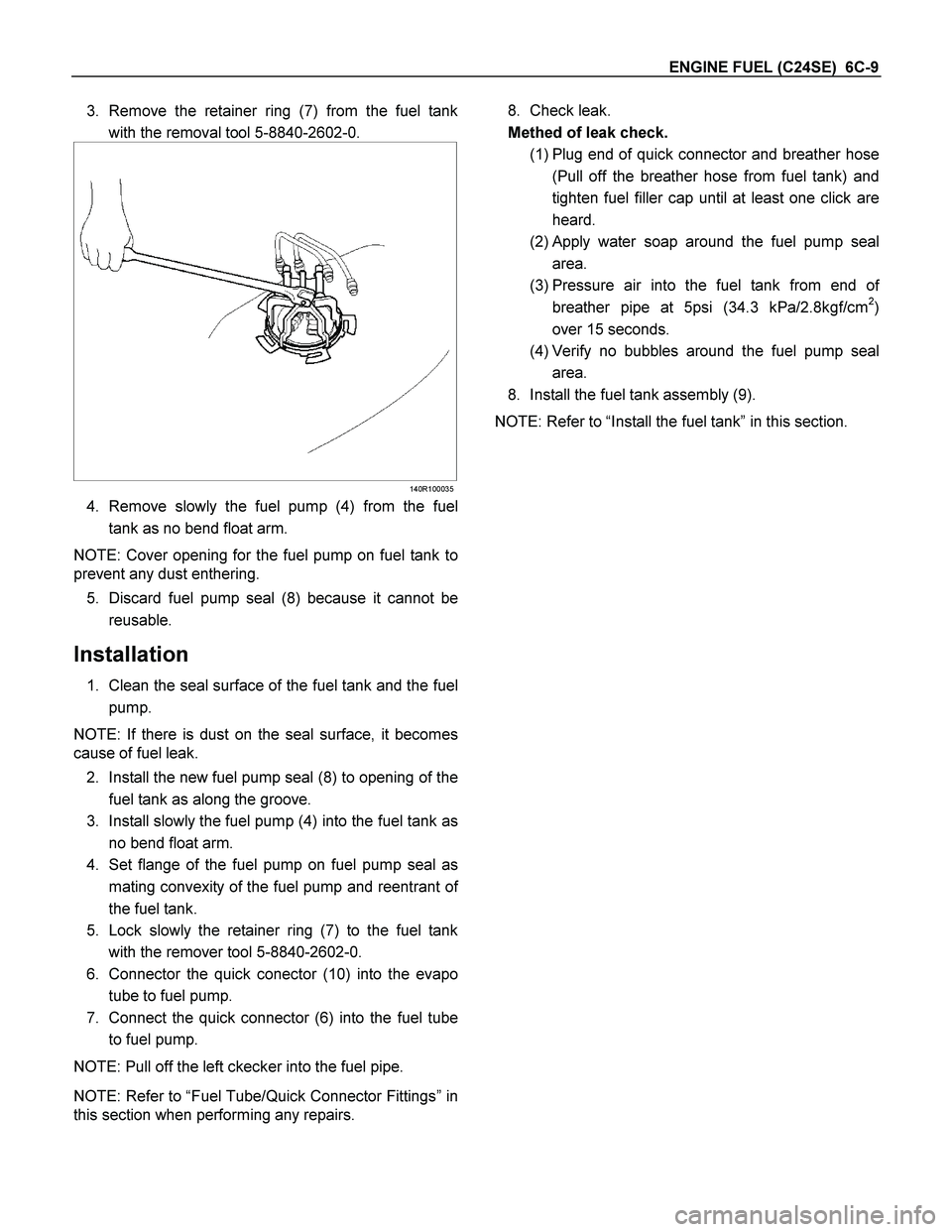
ENGINE FUEL (C24SE) 6C-9
3. Remove the retainer ring (7) from the fuel tank
with the removal tool 5-8840-2602-0.
140R100035
4. Remove slowly the fuel pump (4) from the fuel
tank as no bend float arm.
NOTE: Cover opening for the fuel pump on fuel tank to
prevent any dust enthering.
5. Discard fuel pump seal (8) because it cannot be
reusable.
Installation
1. Clean the seal surface of the fuel tank and the fuel
pump.
NOTE: If there is dust on the seal surface, it becomes
cause of fuel leak.
2. Install the new fuel pump seal (8) to opening of the
fuel tank as along the groove.
3. Install slowly the fuel pump (4) into the fuel tank as
no bend float arm.
4. Set flange of the fuel pump on fuel pump seal as
mating convexity of the fuel pump and reentrant o
f
the fuel tank.
5. Lock slowly the retainer ring (7) to the fuel tank
with the remover tool 5-8840-2602-0.
6. Connector the quick conector (10) into the evapo
tube to fuel pump.
7. Connect the quick connector (6) into the fuel tube
to fuel pump.
NOTE: Pull off the left ckecker into the fuel pipe.
NOTE: Refer to “Fuel Tube/Quick Connector Fittings” in
this section when performing any repairs.
8. Check leak.
Methed of leak check.
(1) Plug end of quick connector and breather hose
(Pull off the breather hose from fuel tank) and
tighten fuel filler cap until at least one click are
heard.
(2) Apply water soap around the fuel pump seal
area.
(3) Pressure air into the fuel tank from end o
f
breather pipe at 5psi (34.3 kPa/2.8kgf/cm2)
over 15 seconds.
(4) Verify no bubbles around the fuel pump seal
area.
8. Install the fuel tank assembly (9).
NOTE: Refer to “Install the fuel tank” in this section.
Page 2534 of 4264
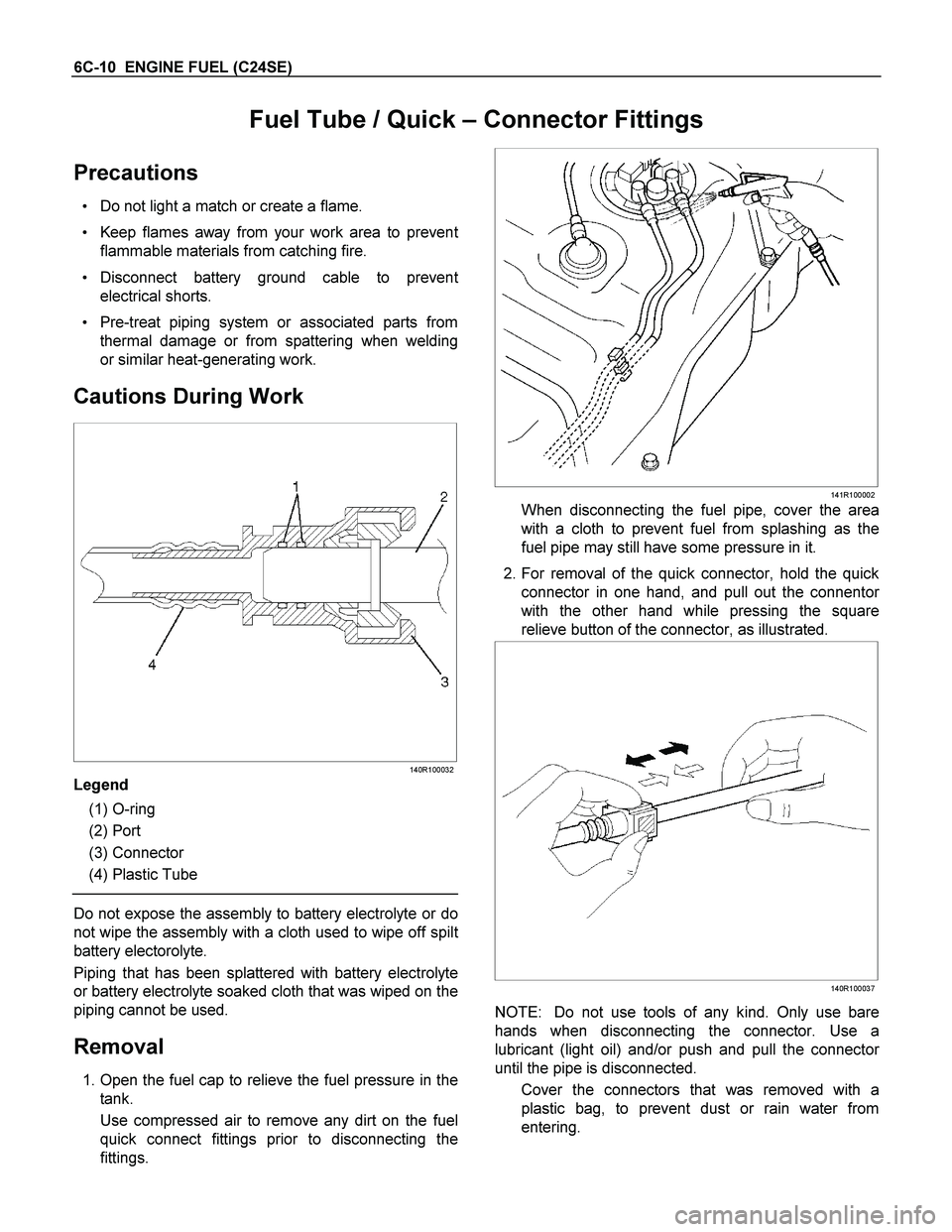
6C-10 ENGINE FUEL (C24SE)
Fuel Tube / Quick – Connector Fittings
Precautions
Do not light a match or create a flame.
Keep flames away from your work area to preven
t
flammable materials from catching fire.
Disconnect battery ground cable to preven
t
electrical shorts.
Pre-treat piping system or associated parts from
thermal damage or from spattering when welding
or similar heat-generating work.
Cautions During Work
140R100032
Legend
(1) O-ring
(2) Port
(3) Connector
(4) Plastic Tube
Do not expose the assembly to battery electrolyte or do
not wipe the assembly with a cloth used to wipe off spil
t
battery electorolyte.
Piping that has been splattered with battery electrolyte
or battery electrolyte soaked cloth that was wiped on the
piping cannot be used.
Removal
1. Open the fuel cap to relieve the fuel pressure in the
tank.
Use compressed air to remove any dirt on the fuel
quick connect fittings prior to disconnecting the
fittings.
141R100002
When disconnecting the fuel pipe, cover the area
with a cloth to prevent fuel from splashing as the
fuel pipe may still have some pressure in it.
2. For removal of the quick connector, hold the quick
connector in one hand, and pull out the connento
r
with the other hand while pressing the square
relieve button of the connector, as illustrated.
140R100037
NOTE: Do not use tools of any kind. Only use bare
hands when disconnecting the connector. Use a
lubricant (light oil) and/or push and pull the connecto
r
until the pipe is disconnected.
Cover the connectors that was removed with a
plastic bag, to prevent dust or rain water from
entering.
Page 2535 of 4264
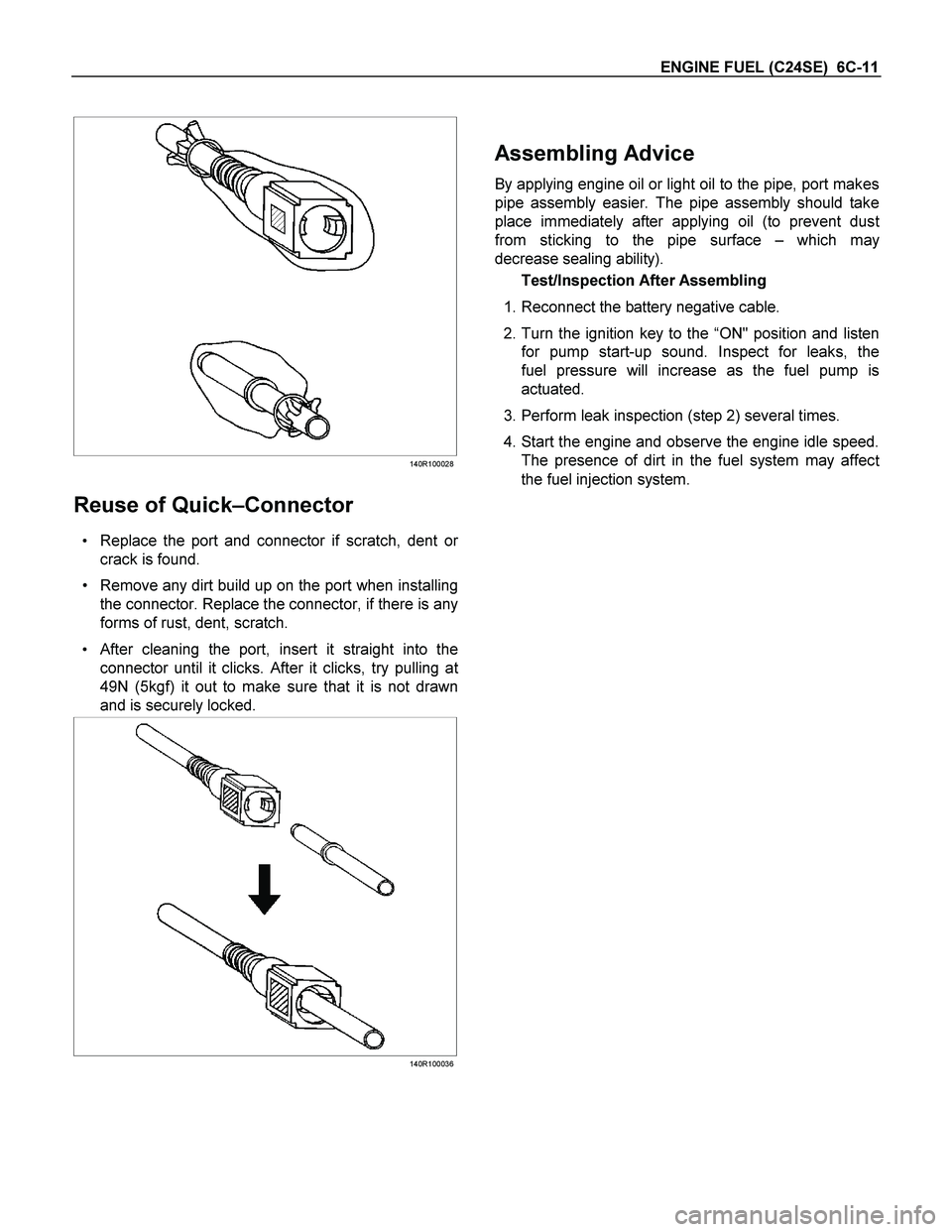
ENGINE FUEL (C24SE) 6C-11
140R100028
Reuse of Quick–Connector
Replace the port and connector if scratch, dent or
crack is found.
Remove any dirt build up on the port when installing
the connector. Replace the connector, if there is any
forms of rust, dent, scratch.
After cleaning the port, insert it straight into the
connector until it clicks. After it clicks, try pulling a
t
49N (5kgf) it out to make sure that it is not drawn
and is securely locked.
140R100036
Assembling Advice
By applying engine oil or light oil to the pipe, port makes
pipe assembly easier. The pipe assembly should take
place immediately after applying oil (to prevent dus
t
from sticking to the pipe surface –which may
decrease sealing ability).
Test/Inspection After Assembling
1. Reconnect the battery negative cable.
2. Turn the ignition key to the “ON" position and listen
for pump start-up sound. Inspect for leaks, the
fuel pressure will increase as the fuel pump is
actuated.
3. Perform leak inspection (step 2) several times.
4. Start the engine and observe the engine idle speed.
The presence of dirt in the fuel system may affec
t
the fuel injection system.
Page 2538 of 4264
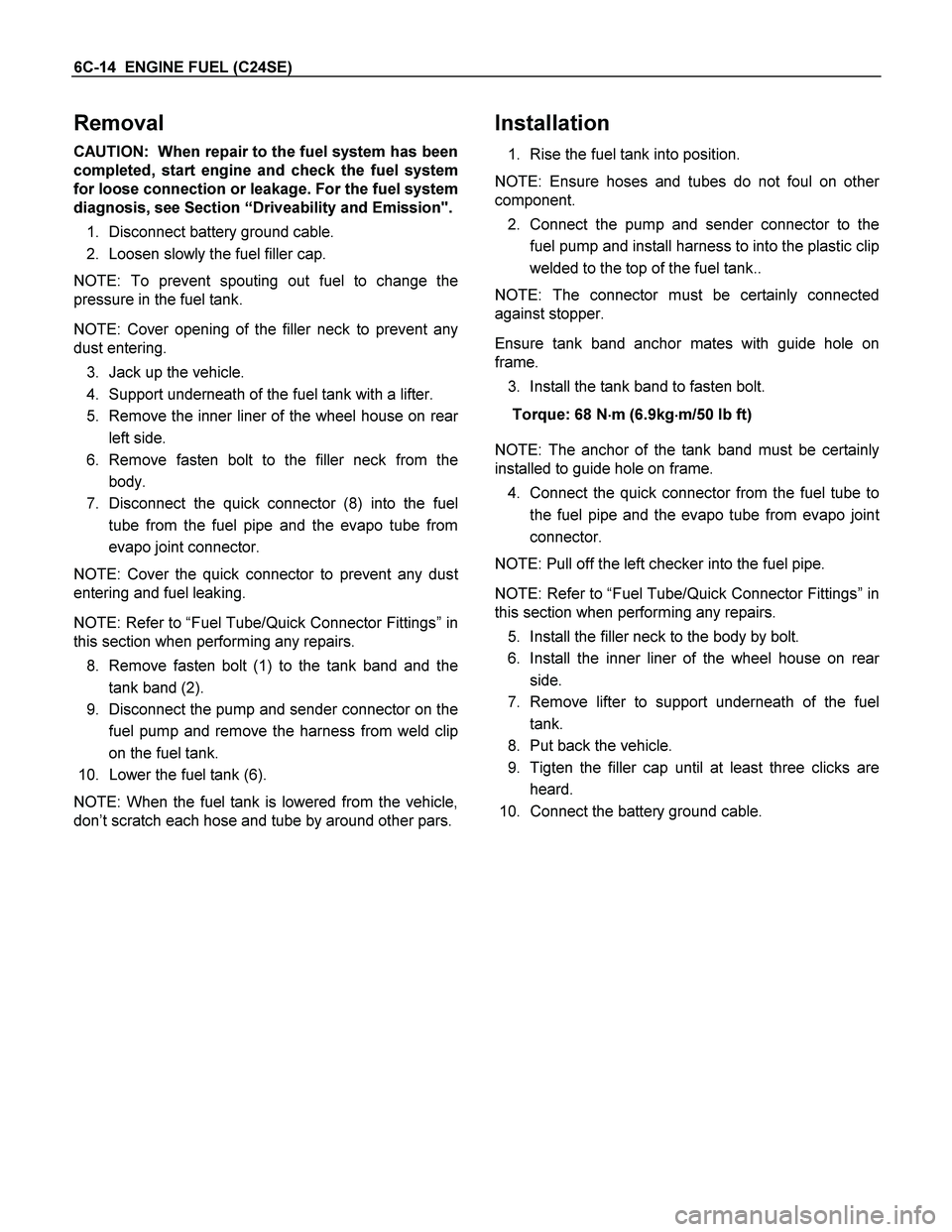
6C-14 ENGINE FUEL (C24SE)
Removal
CAUTION: When repair to the fuel system has been
completed, start engine and check the fuel system
for loose connection or leakage. For the fuel system
diagnosis, see Section “Driveability and Emission".
1. Disconnect battery ground cable.
2. Loosen slowly the fuel filler cap.
NOTE: To prevent spouting out fuel to change the
pressure in the fuel tank.
NOTE: Cover opening of the filler neck to prevent any
dust entering.
3. Jack up the vehicle.
4. Support underneath of the fuel tank with a lifter.
5. Remove the inner liner of the wheel house on rea
r
left side.
6. Remove fasten bolt to the filler neck from the
body.
7. Disconnect the quick connector (8) into the fuel
tube from the fuel pipe and the evapo tube from
evapo joint connector.
NOTE: Cover the quick connector to prevent any dus
t
entering and fuel leaking.
NOTE: Refer to “Fuel Tube/Quick Connector Fittings” in
this section when performing any repairs.
8. Remove fasten bolt (1) to the tank band and the
tank band (2).
9. Disconnect the pump and sender connector on the
fuel pump and remove the harness from weld clip
on the fuel tank.
10. Lower the fuel tank (6).
NOTE: When the fuel tank is lowered from the vehicle,
don’t scratch each hose and tube by around other pars.
Installation
1. Rise the fuel tank into position.
NOTE: Ensure hoses and tubes do not foul on othe
r
component.
2. Connect the pump and sender connector to the
fuel pump and install harness to into the plastic clip
welded to the top of the fuel tank..
NOTE: The connector must be certainly connected
against stopper.
Ensure tank band anchor mates with guide hole on
frame.
3. Install the tank band to fasten bolt.
Torque: 68 N
m (6.9kg
m/50 lb ft)
NOTE: The anchor of the tank band must be certainly
installed to guide hole on frame.
4. Connect the quick connector from the fuel tube to
the fuel pipe and the evapo tube from evapo join
t
connector.
NOTE: Pull off the left checker into the fuel pipe.
NOTE: Refer to “Fuel Tube/Quick Connector Fittings” in
this section when performing any repairs.
5. Install the filler neck to the body by bolt.
6. Install the inner liner of the wheel house on rea
r
side.
7. Remove lifter to support underneath of the fuel
tank.
8. Put back the vehicle.
9. Tigten the filler cap until at least three clicks are
heard.
10. Connect the battery ground cable.
Page 2540 of 4264
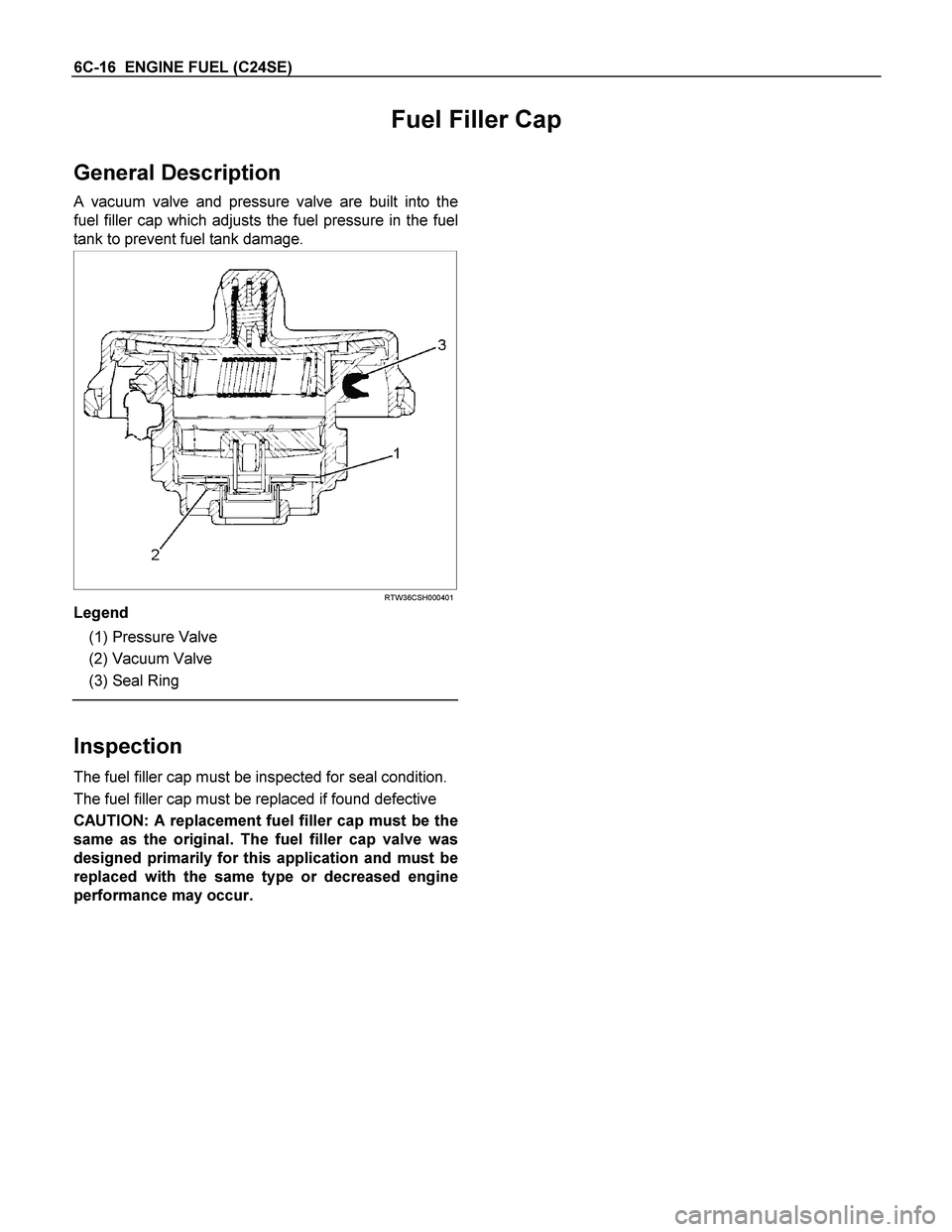
6C-16 ENGINE FUEL (C24SE)
Fuel Filler Cap
General Description
A vacuum valve and pressure valve are built into the
fuel filler cap which adjusts the fuel pressure in the fuel
tank to prevent fuel tank damage.
RTW36CSH000401
Legend
(1) Pressure Valve
(2) Vacuum Valve
(3) Seal Ring
Inspection
The fuel filler cap must be inspected for seal condition.
The fuel filler cap must be replaced if found defective
CAUTION: A replacement fuel filler cap must be the
same as the original. The fuel filler cap valve was
designed primarily for this application and must be
replaced with the same type or decreased engine
performance may occur.
Page 2577 of 4264
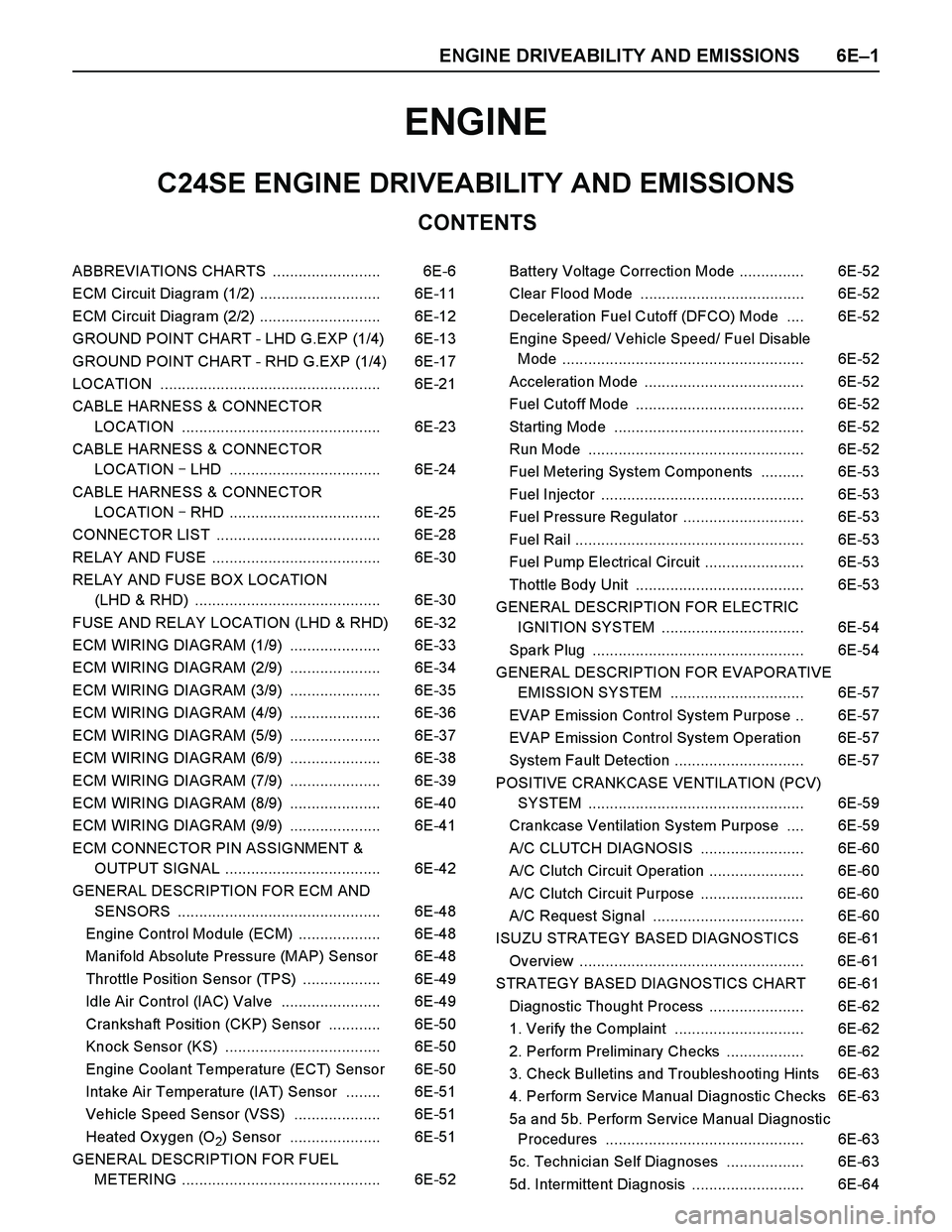
ENGINE DRIVEABILITY AND EMISSIONS 6E–1
ENGINE
CONTENTS
C24SE ENGINE DRIVEABILITY AND EMISSIONS
ABBREVIATIONS CHARTS ......................... 6E-6
ECM Circuit Diagram (1/2) ............................ 6E-11
ECM Circuit Diagram (2/2) ............................ 6E-12
GROUND POINT CHART - LHD G.EXP (1/4) 6E-13
GROUND POINT CHART - RHD G.EXP (1/4) 6E-17
LOCATION ................................................... 6E-21
CABLE HARNESS & CONNECTOR
LOCATION .............................................. 6E-23
CABLE HARNESS & CONNECTOR
LOCATION LHD ................................... 6E-24
CABLE HARNESS & CONNECTOR
LOCATION RHD ................................... 6E-25
CONNECTOR LIST ...................................... 6E-28
RELAY AND FUSE ....................................... 6E-30
RELAY AND FUSE BOX LOCATION
(LHD & RHD) ........................................... 6E-30
FUSE AND RELAY LOCATION (LHD & RHD) 6E-32
ECM WIRING DIAGRAM (1/9) ..................... 6E-33
ECM WIRING DIAGRAM (2/9) ..................... 6E-34
ECM WIRING DIAGRAM (3/9) ..................... 6E-35
ECM WIRING DIAGRAM (4/9) ..................... 6E-36
ECM WIRING DIAGRAM (5/9) ..................... 6E-37
ECM WIRING DIAGRAM (6/9) ..................... 6E-38
ECM WIRING DIAGRAM (7/9) ..................... 6E-39
ECM WIRING DIAGRAM (8/9) ..................... 6E-40
ECM WIRING DIAGRAM (9/9) ..................... 6E-41
ECM CONNECTOR PIN ASSIGNMENT &
OUTPUT SIGNAL .................................... 6E-42
GENERAL DESCRIPTION FOR ECM AND
SENSORS ............................................... 6E-48
Engine Control Module (ECM) ................... 6E-48
Manifold Absolute Pressure (MAP) Sensor 6E-48
Throttle Position Sensor (TPS) .................. 6E-49
Idle Air Control (IAC) Valve ....................... 6E-49
Crankshaft Position (CKP) Sensor ............ 6E-50
Knock Sensor (KS) .................................... 6E-50
Engine Coolant Temperature (ECT) Sensor 6E-50
Intake Air Temperature (IAT) Sensor ........ 6E-51
Vehicle Speed Sensor (VSS) .................... 6E-51
Heated Ox ygen (O
2) Sensor ..................... 6E-51
GENERAL DESCRIPTION FOR FUEL
METERING .............................................. 6E-52Battery Voltage Correction Mode ............... 6E-52
Clear Flood Mode ...................................... 6E-52
Deceleration Fuel Cutoff (DFCO) Mode .... 6E-52
Engine Speed/ Vehicle Speed/ Fuel Disable
Mode ........................................................ 6E-52
Acceleration Mode ..................................... 6E-52
Fuel Cutoff Mode ....................................... 6E-52
Starting Mode ............................................ 6E-52
Run Mode .................................................. 6E-52
Fuel Metering System Components .......... 6E-53
Fuel Injector ............................................... 6E-53
Fuel Pressure Regulator ............................ 6E-53
Fuel Rail ..................................................... 6E-53
Fuel Pump Electrical Circuit ....................... 6E-53
Thottle Body Unit ....................................... 6E-53
GENERAL DESCRIPTION FOR ELECTRIC
IGNITION SYSTEM ................................. 6E-54
Spark Plug ................................................. 6E-54
GENERAL DESCRIPTION FOR EVAPORATIVE
EMISSION SYSTEM ............................... 6E-57
EVAP Emission Control System Purpose .. 6E-57
EVAP Emission Control System Operation 6E-57
System Fault Detection .............................. 6E-57
POSITIVE CRANKCASE VENTILATION (PCV)
SYSTEM .................................................. 6E-59
Crankcase Ventilation System Purpose .... 6E-59
A/C CLUTCH DIAGNOSIS ........................ 6E-60
A/C Clutch Circuit Operation ...................... 6E-60
A/C Clutch Circuit Purpose ........................ 6E-60
A/C Request Signal ................................... 6E-60
ISUZU STRATEGY BASED DIAGNOSTICS 6E-61
Overview .................................................... 6E-61
STRATEGY BASED DIAGNOSTICS CHART 6E-61
Diagnostic Thought Process ...................... 6E-62
1. Verify the Complaint .............................. 6E-62
2. Perform Preliminary Checks .................. 6E-62
3. Check Bulletins and Troubleshooting Hints 6E-63
4. Perform Service Manual Diagnostic Checks 6E-63
5a and 5b. Perform Service Manual Diagnostic
Procedures .............................................. 6E-63
5c. Technician Self Diagnoses .................. 6E-63
5d. Intermittent Diagnosis .......................... 6E-64
Page 2578 of 4264
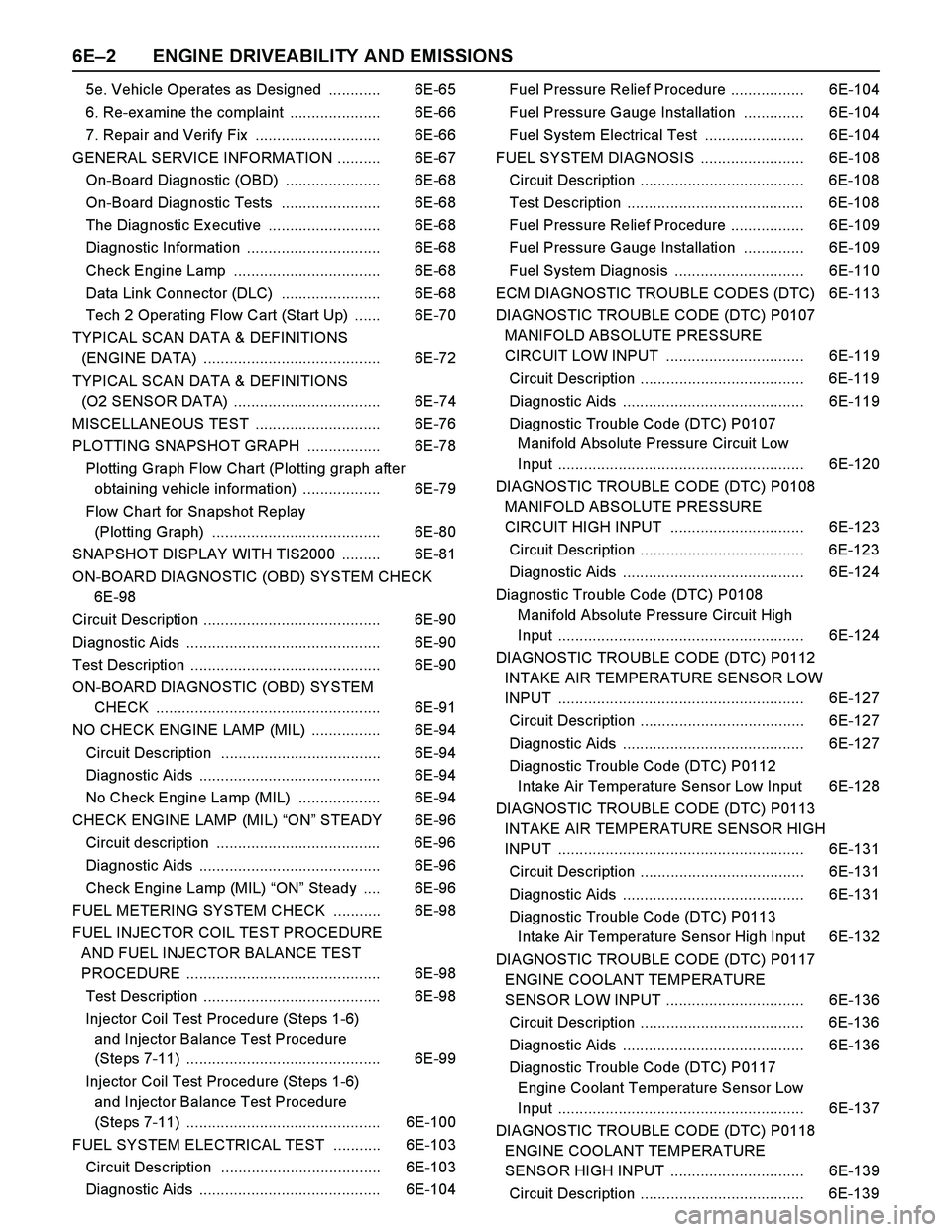
6E–2 ENGINE DRIVEABILITY AND EMISSIONS
5e. Vehicle Operates as Designed ............ 6E-65
6. Re-examine the complaint ..................... 6E-66
7. Repair and Verify Fix ............................. 6E-66
GENERAL SERVICE INFORMATION .......... 6E-67
On-Board Diagnostic (OBD) ...................... 6E-68
On-Board Diagnostic Tests ....................... 6E-68
The Diagnostic Executive .......................... 6E-68
Diagnostic Information ............................... 6E-68
Check Engine Lamp .................................. 6E-68
Data Link Connector (DLC) ....................... 6E-68
Tech 2 Operating Flow Cart (Start Up) ...... 6E-70
TYPICAL SCAN DATA & DEFINITIONS
(ENGINE DATA) ......................................... 6E-72
TYPICAL SCAN DATA & DEFINITIONS
(O2 SENSOR DATA) .................................. 6E-74
MISCELLANEOUS TEST ............................. 6E-76
PLOTTING SNAPSHOT GRAPH ................. 6E-78
Plotting Graph Flow Chart (Plotting graph after
obtaining vehicle information) .................. 6E-79
Flow Chart for Snapshot Replay
(Plotting Graph) ....................................... 6E-80
SNAPSHOT DISPLAY WITH TIS2000 ......... 6E-81
ON-BOARD DIAGNOSTIC (OBD) SYSTEM CHECK
6E-98
Circuit Description ......................................... 6E-90
Diagnostic Aids ............................................. 6E-90
Test Description ............................................ 6E-90
ON-BOARD DIAGNOSTIC (OBD) SYSTEM
CHECK .................................................... 6E-91
NO CHECK ENGINE LAMP (MIL) ................ 6E-94
Circuit Description ..................................... 6E-94
Diagnostic Aids .......................................... 6E-94
No Check Engine Lamp (MIL) ................... 6E-94
CHECK ENGINE LAMP (MIL) “ON” STEADY 6E-96
Circuit description ...................................... 6E-96
Diagnostic Aids .......................................... 6E-96
Check Engine Lamp (MIL) “ON” Steady .... 6E-96
FUEL METERING SYSTEM CHECK ........... 6E-98
FUEL INJECTOR COIL TEST PROCEDURE
AND FUEL INJECTOR BALANCE TEST
PROCEDURE ............................................. 6E-98
Test Description ......................................... 6E-98
Injector Coil Test Procedure (Steps 1-6)
and Injector Balance Test Procedure
(Steps 7-11) ............................................. 6E-99
Injector Coil Test Procedure (Steps 1-6)
and Injector Balance Test Procedure
(Steps 7-11) ............................................. 6E-100
FUEL SYSTEM ELECTRICAL TEST ........... 6E-103
Circuit Description ..................................... 6E-103
Diagnostic Aids .......................................... 6E-104Fuel Pressure Relief Procedure ................. 6E-104
Fuel Pressure Gauge Installation .............. 6E-104
Fuel System Electrical Test ....................... 6E-104
FUEL SYSTEM DIAGNOSIS ........................ 6E-108
Circuit Description ...................................... 6E-108
Test Description ......................................... 6E-108
Fuel Pressure Relief Procedure ................. 6E-109
Fuel Pressure Gauge Installation .............. 6E-109
Fuel System Diagnosis .............................. 6E-110
ECM DIAGNOSTIC TROUBLE CODES (DTC) 6E-113
DIAGNOSTIC TROUBLE CODE (DTC) P0107
MANIFOLD ABSOLUTE PRESSURE
CIRCUIT LOW INPUT ................................ 6E-119
Circuit Description ...................................... 6E-119
Diagnostic Aids .......................................... 6E-119
Diagnostic Trouble Code (DTC) P0107
Manifold Absolute Pressure Circuit Low
Input ......................................................... 6E-120
DIAGNOSTIC TROUBLE CODE (DTC) P0108
MANIFOLD ABSOLUTE PRESSURE
CIRCUIT HIGH INPUT ............................... 6E-123
Circuit Description ...................................... 6E-123
Diagnostic Aids .......................................... 6E-124
Diagnostic Trouble Code (DTC) P0108
Manifold Absolute Pressure Circuit High
Input ......................................................... 6E-124
DIAGNOSTIC TROUBLE CODE (DTC) P0112
INTAKE AIR TEMPERATURE SENSOR LOW
INPUT ......................................................... 6E-127
Circuit Description ...................................... 6E-127
Diagnostic Aids .......................................... 6E-127
Diagnostic Trouble Code (DTC) P0112
Intake Air Temperature Sensor Low Input 6E-128
DIAGNOSTIC TROUBLE CODE (DTC) P0113
INTAKE AIR TEMPERATURE SENSOR HIGH
INPUT ......................................................... 6E-131
Circuit Description ...................................... 6E-131
Diagnostic Aids .......................................... 6E-131
Diagnostic Trouble Code (DTC) P0113
Intake Air Temperature Sensor High Input 6E-132
DIAGNOSTIC TROUBLE CODE (DTC) P0117
ENGINE COOLANT TEMPERATURE
SENSOR LOW INPUT ................................ 6E-136
Circuit Description ...................................... 6E-136
Diagnostic Aids .......................................... 6E-136
Diagnostic Trouble Code (DTC) P0117
Engine Coolant Temperature Sensor Low
Input ......................................................... 6E-137
DIAGNOSTIC TROUBLE CODE (DTC) P0118
ENGINE COOLANT TEMPERATURE
SENSOR HIGH INPUT ............................... 6E-139
Circuit Description ...................................... 6E-139
Page 2581 of 4264
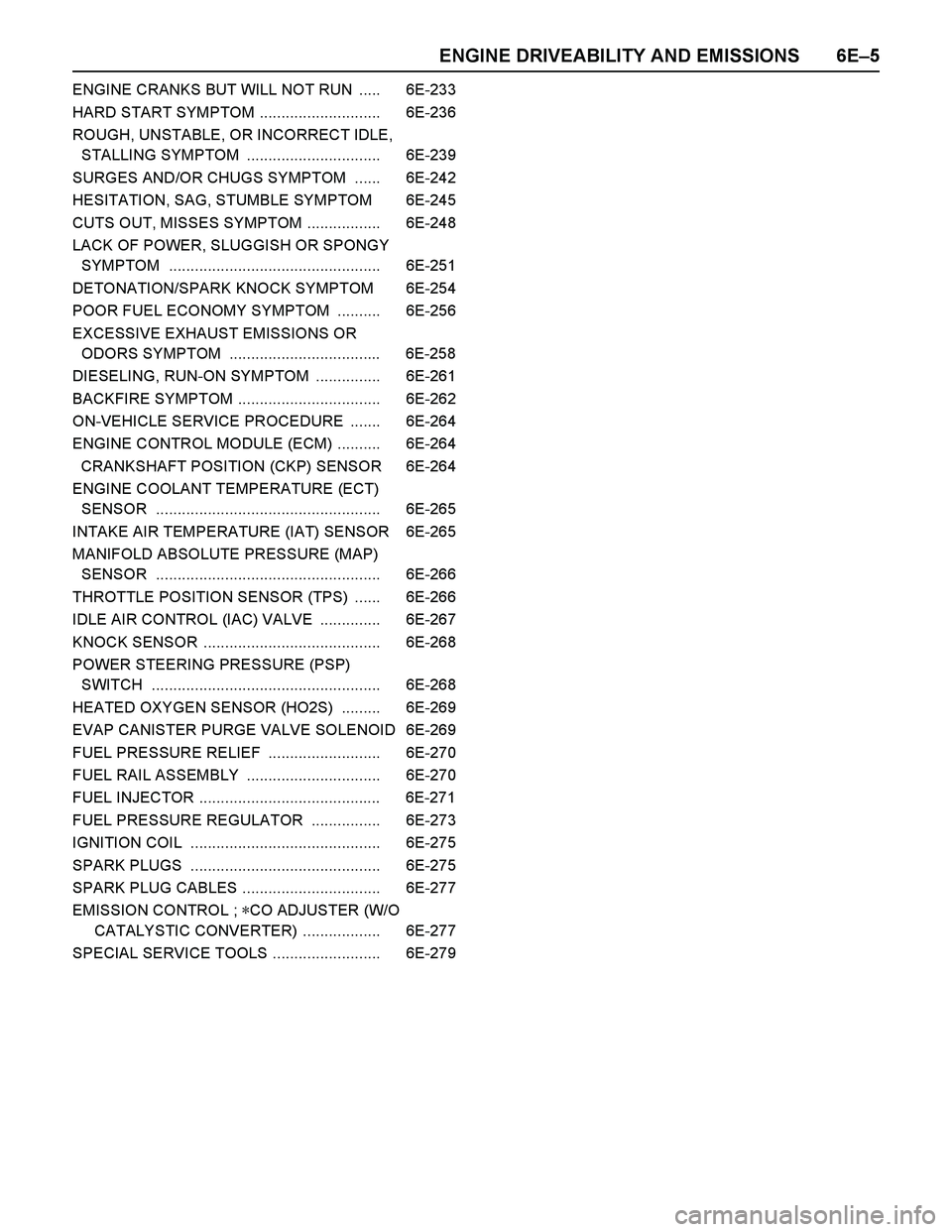
ENGINE DRIVEABILITY AND EMISSIONS 6E–5
ENGINE CRANKS BUT WILL NOT RUN ..... 6E-233
HARD START SYMPTOM ............................ 6E-236
ROUGH, UNSTABLE, OR INCORRECT IDLE,
STALLING SYMPTOM ............................... 6E-239
SURGES AND/OR CHUGS SYMPTOM ...... 6E-242
HESITATION, SAG, STUMBLE SYMPTOM 6E-245
CUTS OUT, MISSES SYMPTOM ................. 6E-248
LACK OF POWER, SLUGGISH OR SPONGY
SYMPTOM ................................................. 6E-251
DETONATION/SPARK KNOCK SYMPTOM 6E-254
POOR FUEL ECONOMY SYMPTOM .......... 6E-256
EXCESSIVE EXHAUST EMISSIONS OR
ODORS SYMPTOM ................................... 6E-258
DIESELING, RUN-ON SYMPTOM ............... 6E-261
BACKFIRE SYMPTOM ................................. 6E-262
ON-VEHICLE SERVICE PROCEDURE ....... 6E-264
ENGINE CONTROL MODULE (ECM) .......... 6E-264
CRANKSHAFT POSITION (CKP) SENSOR 6E-264
ENGINE COOLANT TEMPERATURE (ECT)
SENSOR .................................................... 6E-265
INTAKE AIR TEMPERATURE (IAT) SENSOR 6E-265
MANIFOLD ABSOLUTE PRESSURE (MAP)
SENSOR .................................................... 6E-266
THROTTLE POSITION SENSOR (TPS) ...... 6E-266
IDLE AIR CONTROL (IAC) VALVE .............. 6E-267
KNOCK SENSOR ......................................... 6E-268
POWER STEERING PRESSURE (PSP)
SWITCH ..................................................... 6E-268
HEATED OXYGEN SENSOR (HO2S) ......... 6E-269
EVAP CANISTER PURGE VALVE SOLENOID 6E-269
FUEL PRESSURE RELIEF .......................... 6E-270
FUEL RAIL ASSEMBLY ............................... 6E-270
FUEL INJECTOR .......................................... 6E-271
FUEL PRESSURE REGULATOR ................ 6E-273
IGNITION COIL ............................................ 6E-275
SPARK PLUGS ............................................ 6E-275
SPARK PLUG CABLES ................................ 6E-277
EMISSION CONTROL ; CO ADJUSTER (W/O
CATALYSTIC CONVERTER) .................. 6E-277
SPECIAL SERVICE TOOLS ......................... 6E-279
Page 2582 of 4264
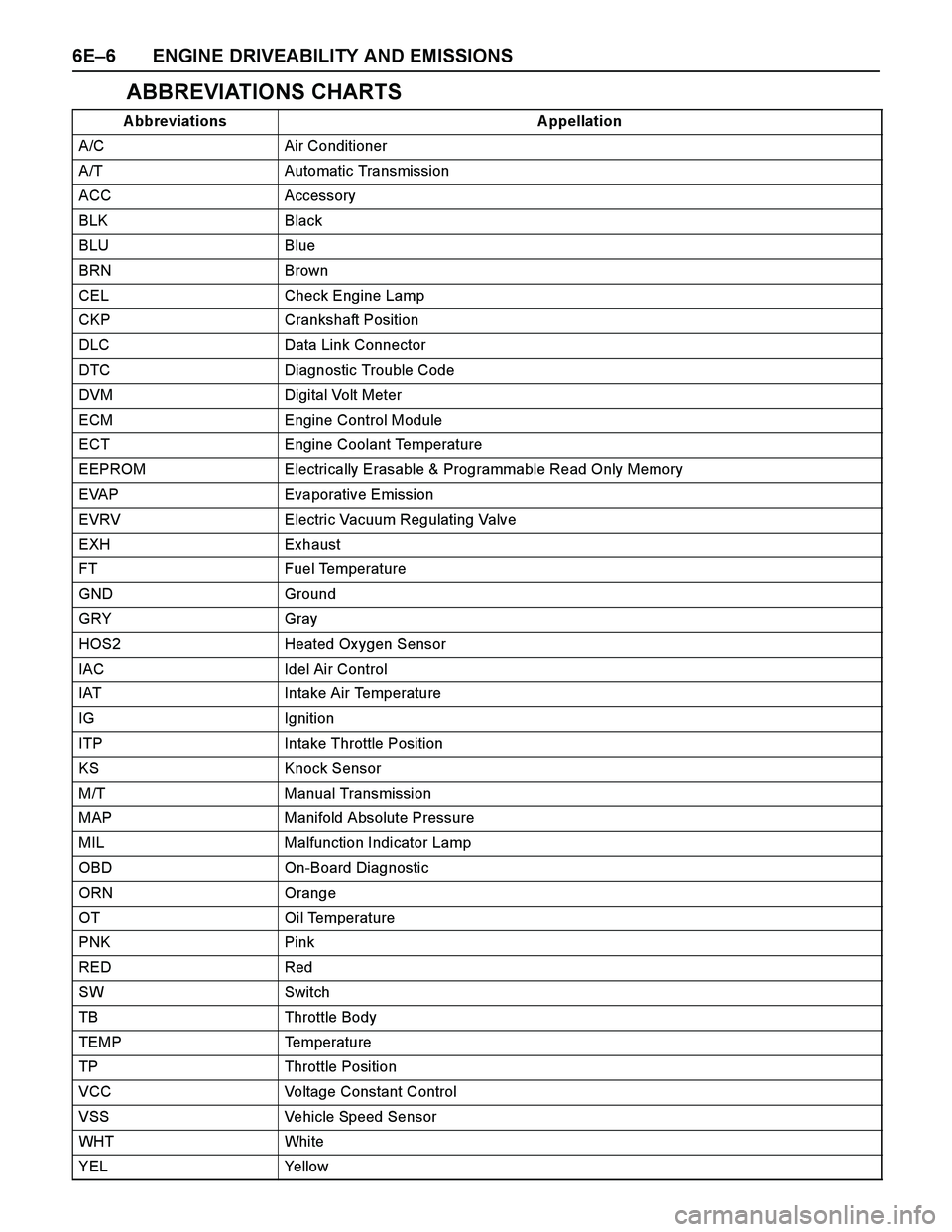
6E–6 ENGINE DRIVEABILITY AND EMISSIONS
ABBREVIATIONS CHARTS
A bbreviations A ppellation
A/C Air Conditioner
A/T Automatic Transmission
ACC Accessory
BLK Black
BLU Blue
BRN Brown
CEL Check Engine Lamp
CKP Crankshaft Position
DLC Data Link Connector
DTC Diagnostic Trouble Code
DVM Digital Volt Meter
ECM Engine Control Module
ECT Engine Coolant Temperature
EEPROM Electrically Erasable & Programmable Read Only Memory
EVAP Evaporative Emission
EVRV Electric Vacuum Regulating Valve
EXH Exhaust
FT Fuel Temperature
GND Ground
GRY Gray
HOS2 Heated Ox ygen Sensor
IAC Idel Air Control
IAT Intake Air Temperature
IG Ignition
ITP Intake Throttle Position
KS Knock Sensor
M/T Manual Transmission
MAP Manifold Absolute Pressure
MIL Malfunction Indicator Lamp
OBD On-Board Diagnostic
ORN Orange
OT Oil Temperature
PNK Pink
RED Red
SW Switch
TB Throttle Body
TEMP Temperature
TP Throttle Posi tion
VCC Voltage Constant Control
VSS Vehicle Speed Sensor
WHT Whi te
Y EL Yellow