battery ISUZU TF SERIES 2004 Workshop Manual
[x] Cancel search | Manufacturer: ISUZU, Model Year: 2004, Model line: TF SERIES, Model: ISUZU TF SERIES 2004Pages: 4264, PDF Size: 72.63 MB
Page 1718 of 4264
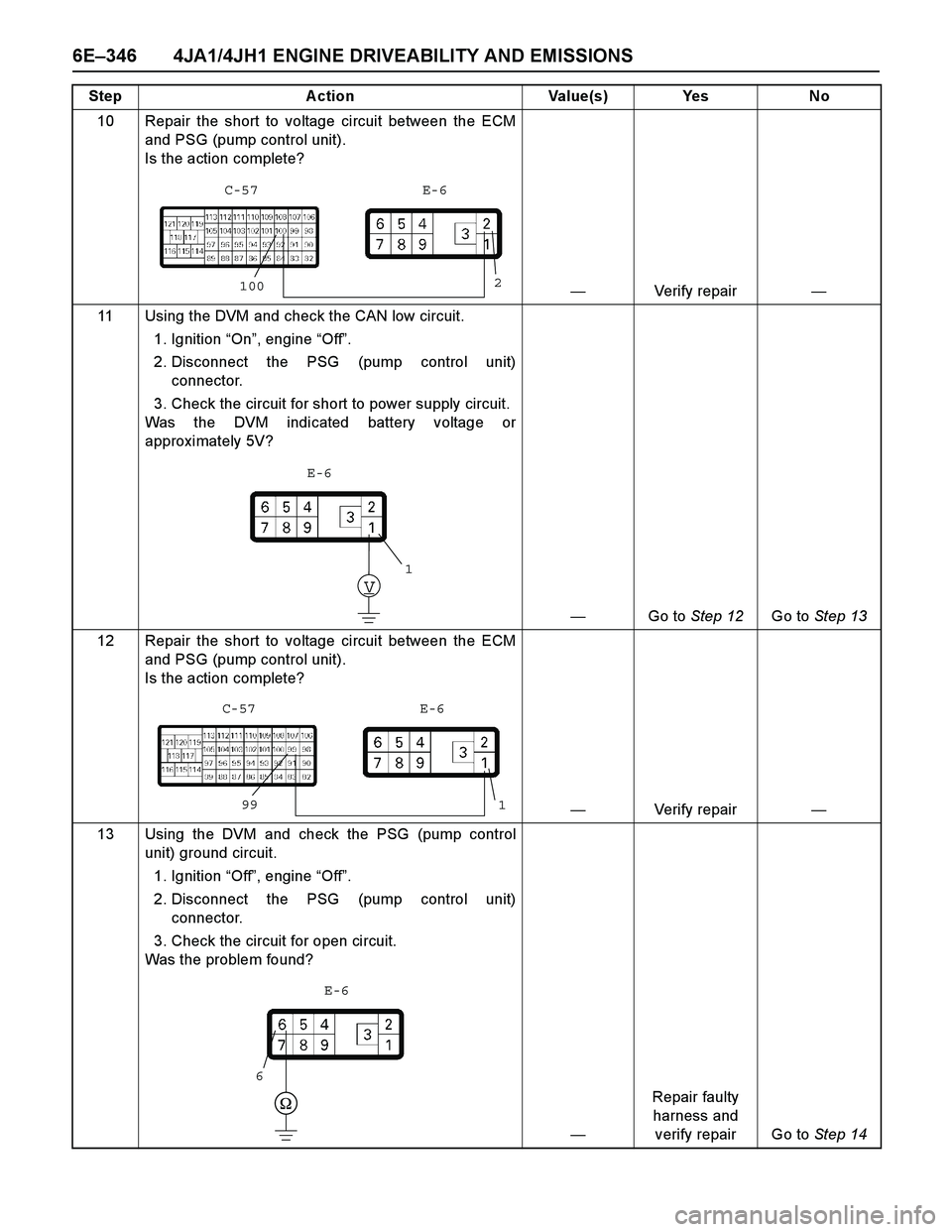
6E–346 4JA1/4JH1 ENGINE DRIVEABILITY AND EMISSIONS
10 Repair the short to voltage circuit between the ECM
and PSG (pump control unit).
Is the action complete?
—Verify repair—
11 Using the DVM and check the CAN low circuit.
1. Ignition “On”, engine “Off”.
2. Disconnect the PSG (pump control unit)
connector.
3. Check the circuit for short to power supply circuit.
Was the DVM indicated battery voltage or
approximately 5V?
—Go to Step 12Go to Step 13
12 Repair the short to voltage circuit between the ECM
and PSG (pump control unit).
Is the action complete?
—Verify repair—
13 Using the DVM and check the PSG (pump control
unit) ground circuit.
1. Ignition “Off”, engine “Off”.
2. Disconnect the PSG (pump control unit)
connector.
3. Check the circuit for open circuit.
Was the problem found?
—Repair faulty
harness and
verify repair Go to Step 14 Step Action Value(s) Yes No
1002 C-57 E-6
1
V
E-6
991 C-57 E-6
6
E-6
Page 1725 of 4264
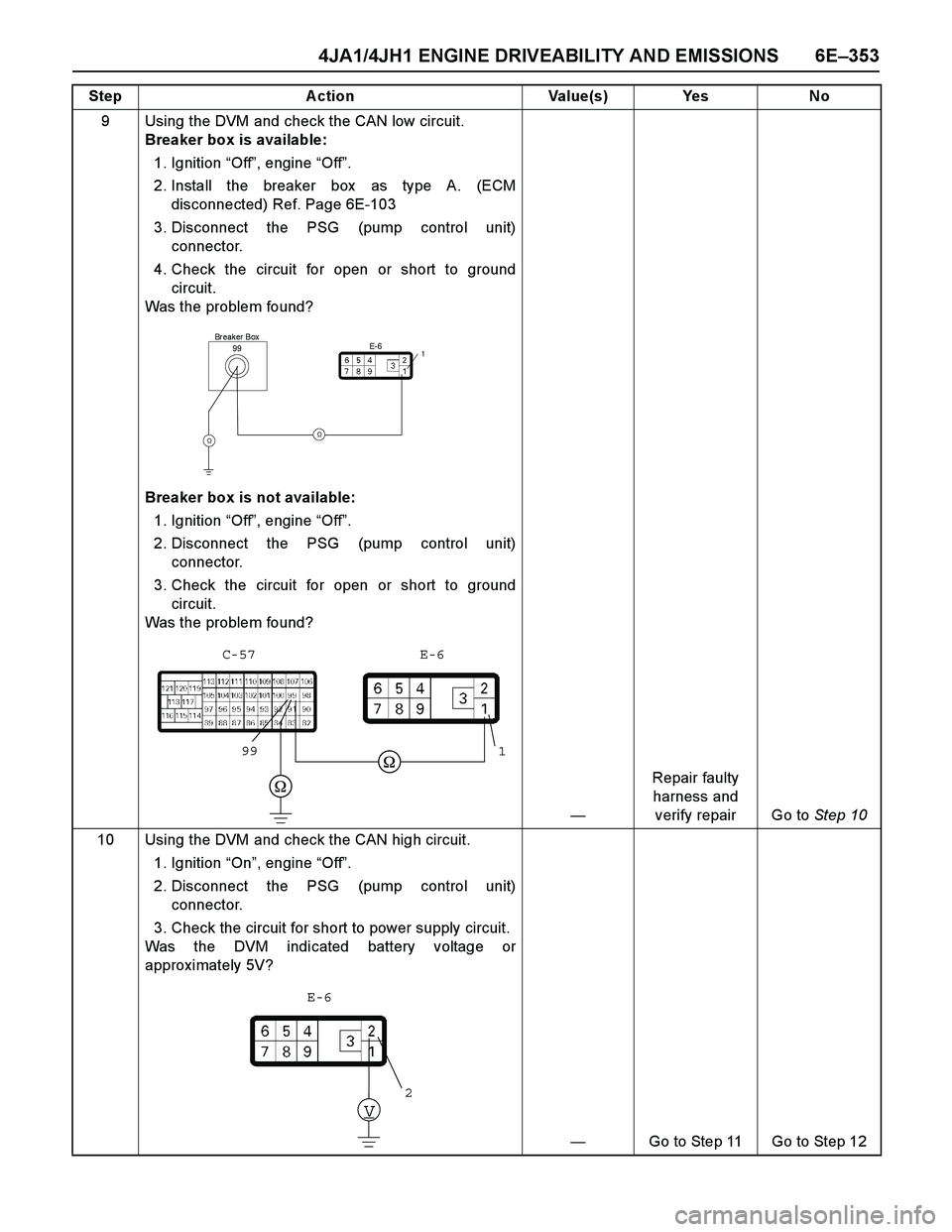
4JA1/4JH1 ENGINE DRIVEABILITY AND EMISSIONS 6E–353
9 Using the DVM and check the CAN low circuit.
Breaker box is available:
1. Ignition “Off”, engine “Off”.
2. Install the breaker box as type A. (ECM
disconnected) Ref. Page 6E-103
3. Disconnect the PSG (pump control unit)
connector.
4. Check the circuit for open or short to ground
circuit.
Was the problem found?
Breaker box is not available:
1. Ignition “Off”, engine “Off”.
2. Disconnect the PSG (pump control unit)
connector.
3. Check the circuit for open or short to ground
circuit.
Was the problem found?
—Repair faulty
harness and
verify repair Go to Step 10
10 Using the DVM and check the CAN high circuit.
1. Ignition “On”, engine “Off”.
2. Disconnect the PSG (pump control unit)
connector.
3. Check the circuit for short to power supply circuit.
Was the DVM indicated battery voltage or
approximately 5V?
—Go to Step 11 Go to Step 12 Step Action Value(s) Yes No
E-699Breaker Box
991 C-57 E-6
2
V
E-6
Page 1726 of 4264
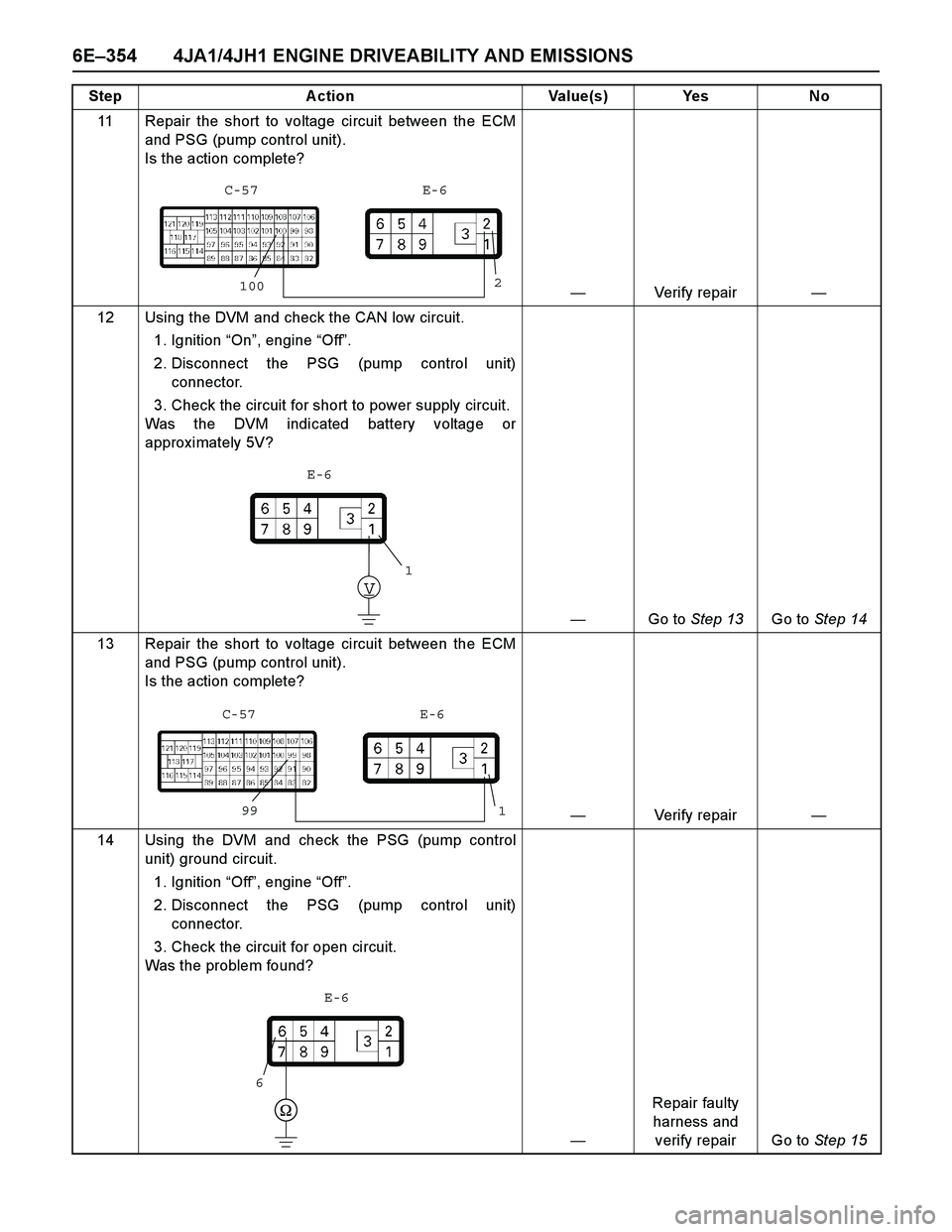
6E–354 4JA1/4JH1 ENGINE DRIVEABILITY AND EMISSIONS
11 Repair the short to voltage circuit between the ECM
and PSG (pump control unit).
Is the action complete?
—Verify repair—
12 Using the DVM and check the CAN low circuit.
1. Ignition “On”, engine “Off”.
2. Disconnect the PSG (pump control unit)
connector.
3. Check the circuit for short to power supply circuit.
Was the DVM indicated battery voltage or
approximately 5V?
—Go to Step 13Go to Step 14
13 Repair the short to voltage circuit between the ECM
and PSG (pump control unit).
Is the action complete?
—Verify repair—
14 Using the DVM and check the PSG (pump control
unit) ground circuit.
1. Ignition “Off”, engine “Off”.
2. Disconnect the PSG (pump control unit)
connector.
3. Check the circuit for open circuit.
Was the problem found?
—Repair faulty
harness and
verify repair Go to Step 15 Step Action Value(s) Yes No
1002 C-57 E-6
1
V
E-6
991 C-57 E-6
6
E-6
Page 1790 of 4264
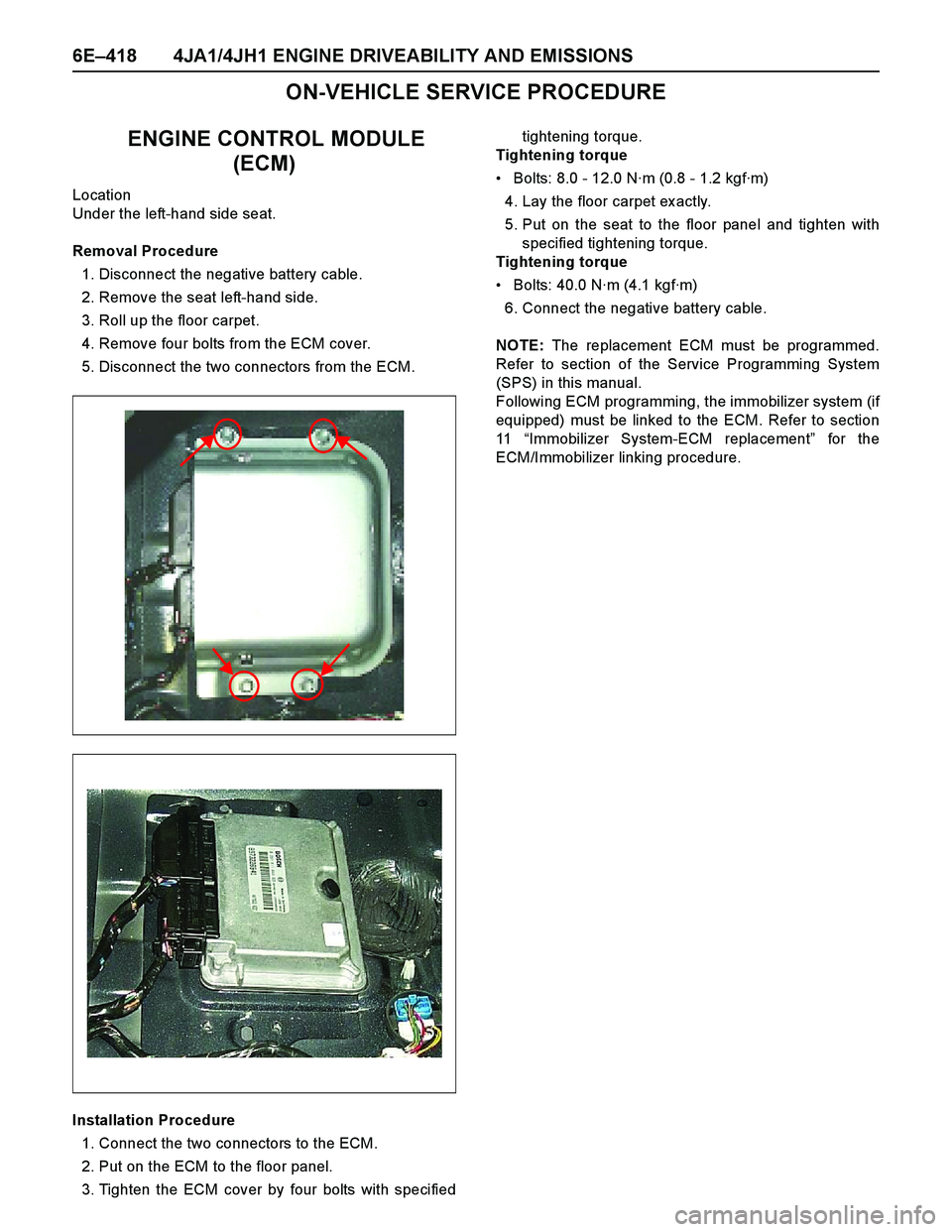
6E–418 4JA1/4JH1 ENGINE DRIVEABILITY AND EMISSIONS
ON-VEHICLE SERVICE PROCEDURE
ENGINE CONTROL MODULE
(ECM)
Location
Under the left-hand side seat.
Removal Procedure
1. Disconnect the negative battery cable.
2. Remove the seat left-hand side.
3. Roll up the floor carpet.
4. Remove four bolts from the ECM cover.
5. Disconnect the two connectors from the ECM.
Installation Procedure
1. Connect the two connectors to the ECM.
2. Put on the ECM to the floor panel.
3. Tighten the ECM cover by four bolts with specifiedtightening torque.
Tightening torque
Bolts: 8.0 - 12.0 N·m (0.8 - 1.2 kgf·m)
4. Lay the floor carpet ex actly.
5. Put on the seat to the floor panel and tighten with
specified tightening torque.
Tightening torque
Bolts: 40.0 N·m (4.1 kgf·m)
6. Connect the negative battery cable.
NOTE: The replacement ECM must be programmed.
Refer to section of the Service Programming System
(SPS) in this manual.
Following ECM programming, the immobilizer system (if
equipped) must be linked to the ECM. Refer to section
11 “Immobilizer System-ECM replacement” for the
ECM/Immobilizer linking procedure.
Page 1791 of 4264
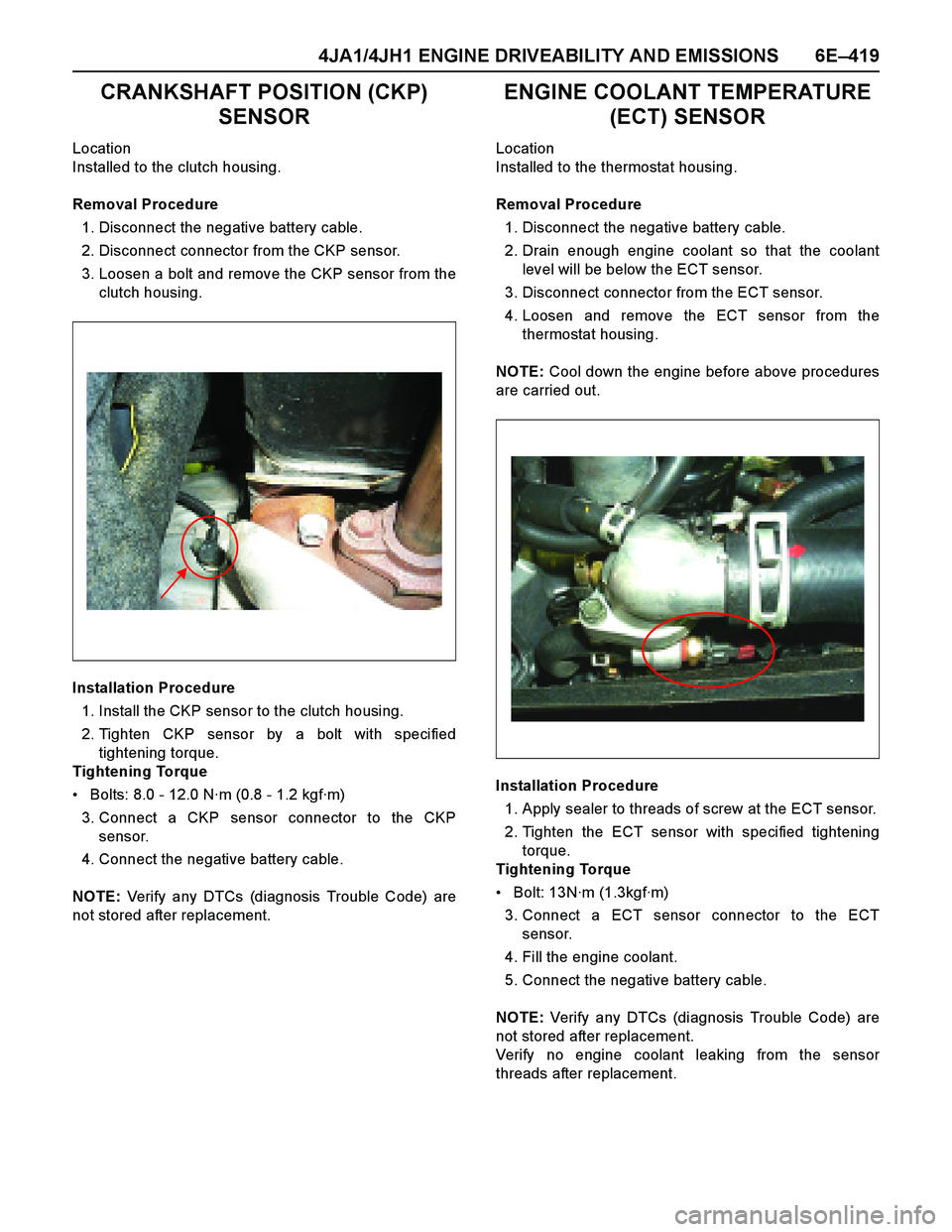
4JA1/4JH1 ENGINE DRIVEABILITY AND EMISSIONS 6E–419
CRANKSHAFT POSITION (CKP)
SENSOR
Location
Installed to the clutch housing.
Removal Procedure
1. Disconnect the negative battery cable.
2. Disconnect connector from the CKP sensor.
3. Loosen a bolt and remove the CKP sensor from the
clutch housing.
Installation Procedure
1. Install the CKP sensor to the clutch housing.
2. Tighten CKP sensor by a bolt with specified
tightening torque.
Tightening Torque
Bolts: 8.0 - 12.0 N·m (0.8 - 1.2 kgf·m)
3. Connect a CKP sensor connector to the CKP
sensor.
4. Connect the negative battery cable.
NOTE: Verify any DTCs (diagnosis Trouble Code) are
not stored after replacement.
ENGINE COOLANT TEMPERATURE
(ECT) SENSOR
Location
Installed to the thermostat housing.
Removal Procedure
1. Disconnect the negative battery cable.
2. Drain enough engine coolant so that the coolant
level will be below the ECT sensor.
3. Disconnect connector from the ECT sensor.
4. Loosen and remove the ECT sensor from the
thermostat housing.
NOTE: Cool down the engine before above procedures
are carried out.
Installation Procedure
1. Apply sealer to threads of screw at the ECT sensor.
2. Tighten the ECT sensor with specified tightening
torque.
Tightening Torque
Bolt: 13N·m (1.3kgf·m)
3. Connect a ECT sensor connector to the ECT
sensor.
4. Fill the engine coolant.
5. Connect the negative battery cable.
NOTE: Verify any DTCs (diagnosis Trouble Code) are
not stored after replacement.
Verify no engine coolant leaking from the sensor
threads after replacement.
Page 1792 of 4264

6E–420 4JA1/4JH1 ENGINE DRIVEABILITY AND EMISSIONS
MASS AIR FLOW (MAF) & INTAKE
AIR TEMPERATURE (IAT) SENSOR
Location
Installed to the intake duct housing.
Removal Procedure
1. Disconnect the negative battery cable.
2. Disconnect a MAF & IAT sensor connector from the
MAF & IAT sensor assembly.
3. Loosen the clips and remove the MAF & IAT sensor
assembly from the intake duct housing.
Installation Procedure
1. Install the MAF & IAT sensor assembly into intake
air duct.
2. Tighten the clips.
3. Connect a MAF & IAT sensor connector to the MAF
& IAT sensor assembly.
4. Connect the negative battery cable.
NOTE: Verify any DTCs (diagnosis Trouble Code) are
not stored after replacement.
THROTTLE POSITION SENSOR
(TPS)
Location
Installed on the throttle body.
Removal Procedure
1. Disconnect the negative battery cable.
2. Disconnect the TPS connector.
3. Loosen two screws and remove TPS from the
throttle body.
Installation Procedure
1. Temporary tighten the TPS by two screws.
2. Connect a TPS connectors to the TPS.
3. Connect the Tech2 to the vehicle.
4. Connect the negative battery cable.
5. Select “Data Display” with the Tech2.
6. Check the throttle position data and adjust the TPS
position.
7. Tighten two screws.
NOTE: Verify any DTCs (diagnosis Trouble Code) are
not stored after replacement.
Page 1793 of 4264
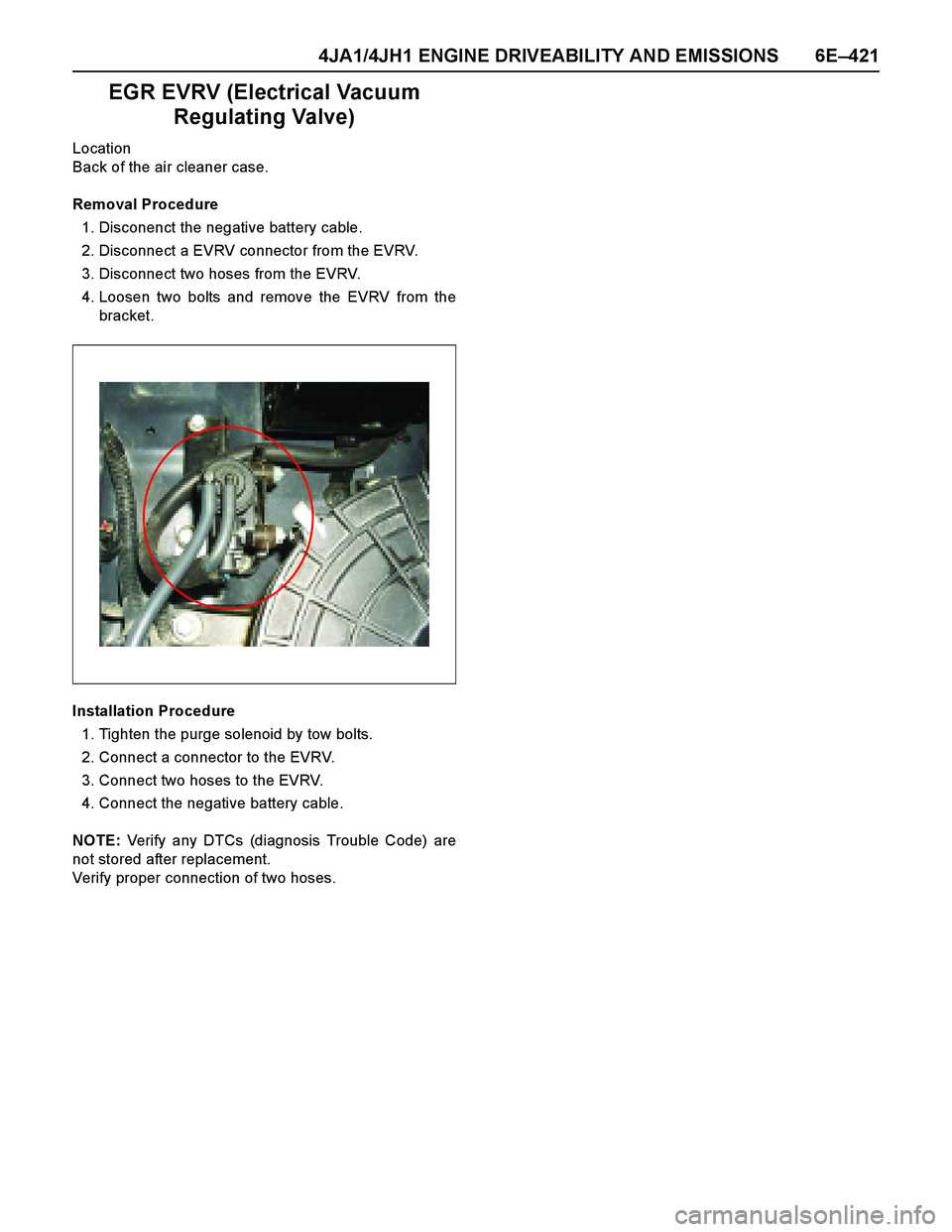
4JA1/4JH1 ENGINE DRIVEABILITY AND EMISSIONS 6E–421
EGR EVRV (Electrical Vacuum
Regulating Valve)
Location
Back of the air cleaner case.
Removal Procedure
1. Disconenct the negative battery cable.
2. Disconnect a EVRV connector from the EVRV.
3. Disconnect two hoses from the EVRV.
4. Loosen two bolts and remove the EVRV from the
bracket.
Installation Procedure
1. Tighten the purge solenoid by tow bolts.
2. Connect a connector to the EVRV.
3. Connect two hoses to the EVRV.
4. Connect the negative battery cable.
NOTE: Verify any DTCs (diagnosis Trouble Code) are
not stored after replacement.
Verify proper connection of two hoses.
Page 1827 of 4264
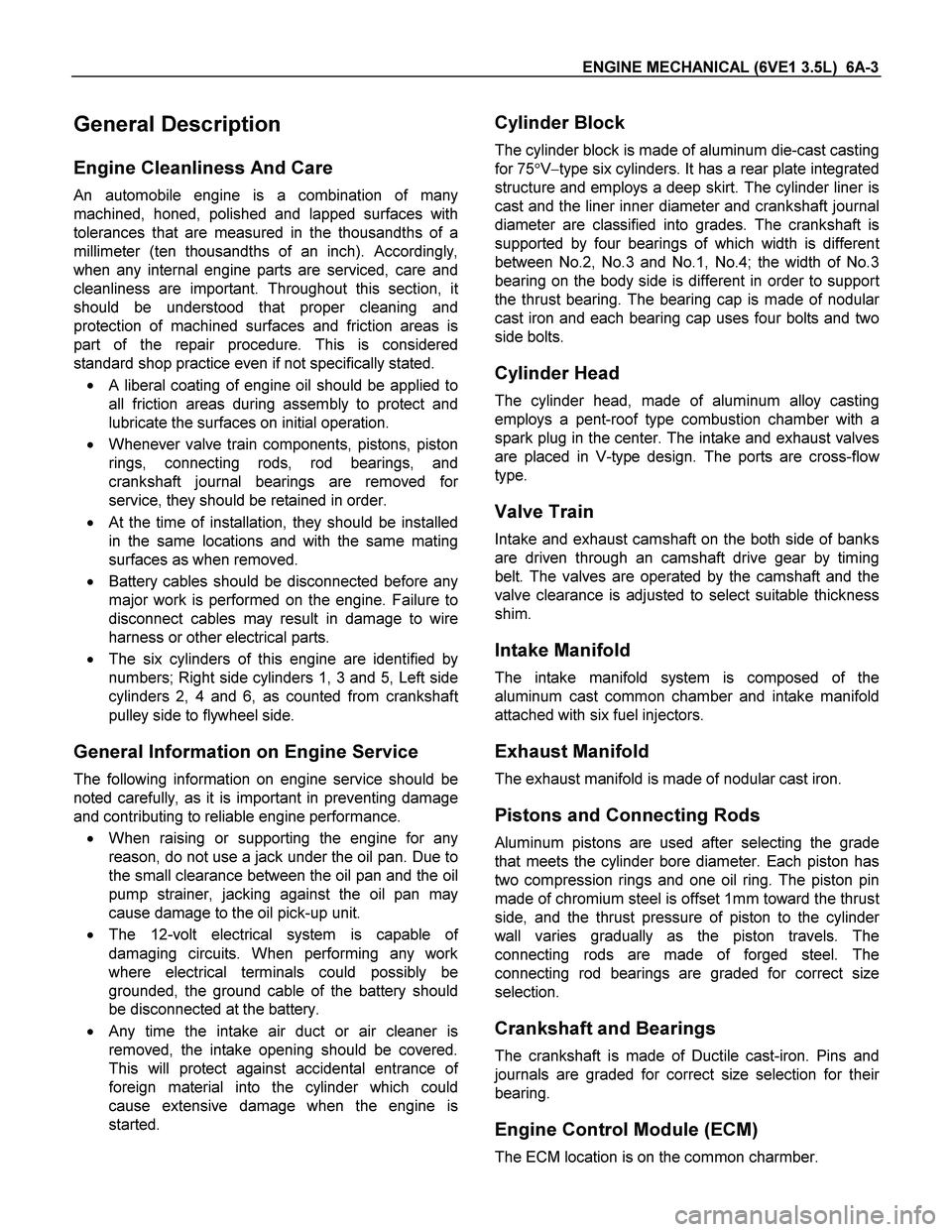
ENGINE MECHANICAL (6VE1 3.5L) 6A-3
General Description
Engine Cleanliness And Care
An automobile engine is a combination of many
machined, honed, polished and lapped surfaces with
tolerances that are measured in the thousandths of a
millimeter (ten thousandths of an inch). Accordingly,
when any internal engine parts are serviced, care and
cleanliness are important. Throughout this section, i
t
should be understood that proper cleaning and
protection of machined surfaces and friction areas is
part of the repair procedure. This is considered
standard shop practice even if not specifically stated.
A liberal coating of engine oil should be applied to
all friction areas during assembly to protect and
lubricate the surfaces on initial operation.
Whenever valve train components, pistons, piston
rings, connecting rods, rod bearings, and
crankshaft journal bearings are removed fo
r
service, they should be retained in order.
At the time of installation, they should be installed
in the same locations and with the same mating
surfaces as when removed.
Battery cables should be disconnected before any
major work is performed on the engine. Failure to
disconnect cables may result in damage to wire
harness or other electrical parts.
The six cylinders of this engine are identified by
numbers; Right side cylinders 1, 3 and 5, Left side
cylinders 2, 4 and 6, as counted from crankshaf
t
pulley side to flywheel side.
General Information on Engine Service
The following information on engine service should be
noted carefully, as it is important in preventing damage
and contributing to reliable engine performance.
When raising or supporting the engine for any
reason, do not use a jack under the oil pan. Due to
the small clearance between the oil pan and the oil
pump strainer, jacking against the oil pan may
cause damage to the oil pick-up unit.
The 12-volt electrical system is capable o
f
damaging circuits. When performing any work
where electrical terminals could possibly be
grounded, the ground cable of the battery should
be disconnected at the battery.
Any time the intake air duct or air cleaner is
removed, the intake opening should be covered.
This will protect against accidental entrance o
f
foreign material into the cylinder which could
cause extensive damage when the engine is
started.
Cylinder Block
The cylinder block is made of aluminum die-cast casting
for 75Vtype six cylinders. It has a rear plate integrated
structure and employs a deep skirt. The cylinder liner is
cast and the liner inner diameter and crankshaft journal
diameter are classified into grades. The crankshaft is
supported by four bearings of which width is differen
t
between No.2, No.3 and No.1, No.4; the width of No.3
bearing on the body side is different in order to suppor
t
the thrust bearing. The bearing cap is made of nodular
cast iron and each bearing cap uses four bolts and two
side bolts.
Cylinder Head
The cylinder head, made of aluminum alloy casting
employs a pent-roof type combustion chamber with a
spark plug in the center. The intake and exhaust valves
are placed in V-type design. The ports are cross-flo
w
type.
Valve Train
Intake and exhaust camshaft on the both side of banks
are driven through an camshaft drive gear by timing
belt. The valves are operated by the camshaft and the
valve clearance is adjusted to select suitable thickness
shim.
Intake Manifold
The intake manifold system is composed of the
aluminum cast common chamber and intake manifold
attached with six fuel injectors.
Exhaust Manifold
The exhaust manifold is made of nodular cast iron.
Pistons and Connecting Rods
Aluminum pistons are used after selecting the grade
that meets the cylinder bore diameter. Each piston has
two compression rings and one oil ring. The piston pin
made of chromium steel is offset 1mm toward the thrus
t
side, and the thrust pressure of piston to the cylinder
wall varies gradually as the piston travels. The
connecting rods are made of forged steel. The
connecting rod bearings are graded for correct size
selection.
Crankshaft and Bearings
The crankshaft is made of Ductile cast-iron. Pins and
journals are graded for correct size selection for thei
r
bearing.
Engine Control Module (ECM)
The ECM location is on the common charmber.
Page 1828 of 4264
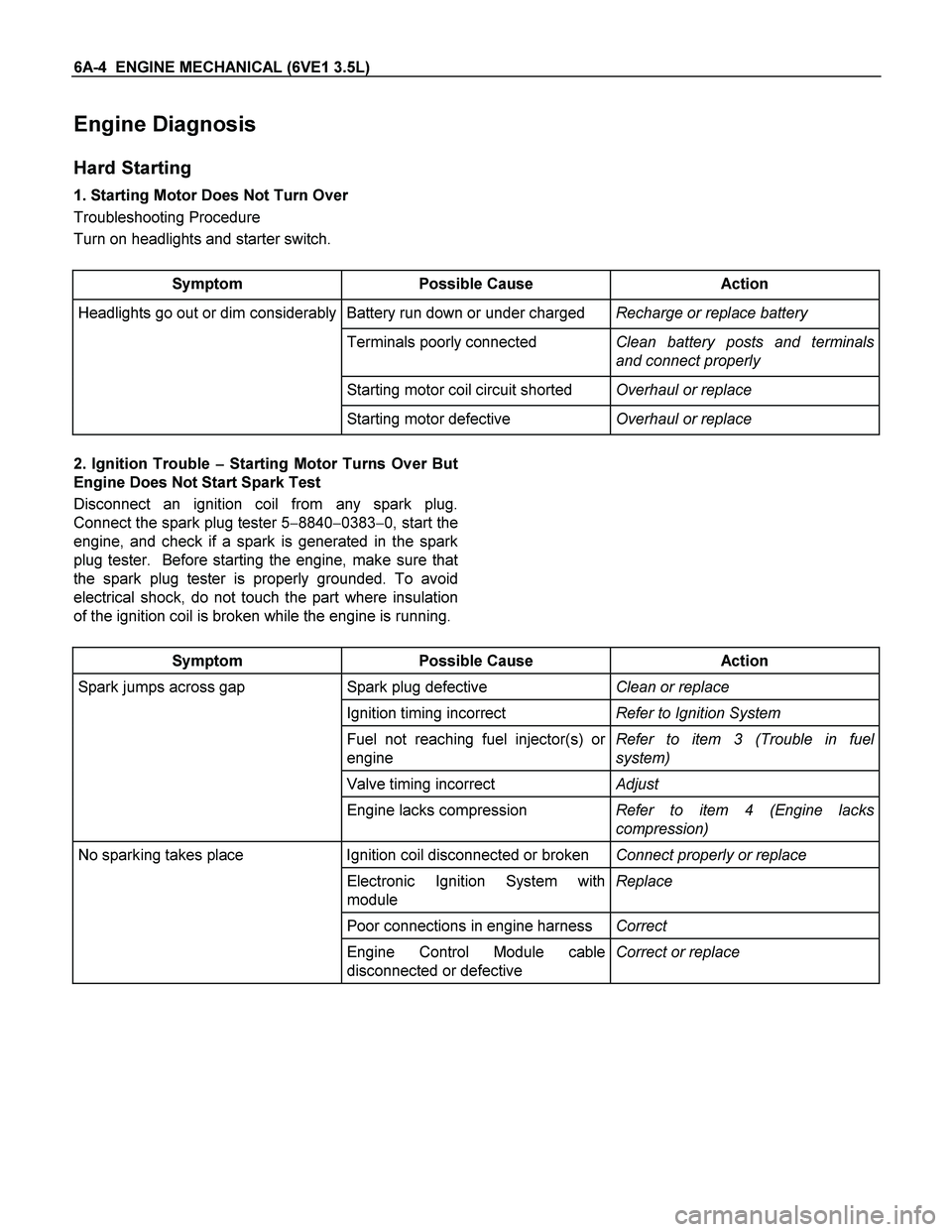
6A-4 ENGINE MECHANICAL (6VE1 3.5L)
Engine Diagnosis
Hard Starting
1. Starting Motor Does Not Turn Over
Troubleshooting Procedure
Turn on headlights and starter switch.
Symptom Possible Cause Action
Headlights go out or dim considerably Battery run down or under charged Recharge or replace battery
Terminals poorly connected Clean battery posts and terminals
and connect properly
Starting motor coil circuit shorted Overhaul or replace
Starting motor defective Overhaul or replace
2. Ignition Trouble
Starting Motor Turns Over But
Engine Does Not Start Spark Test
Disconnect an ignition coil from any spark plug.
Connect the spark plug tester 5884003830, start the
engine, and check if a spark is generated in the spark
plug tester. Before starting the engine, make sure that
the spark plug tester is properly grounded. To avoid
electrical shock, do not touch the part where insulation
of the ignition coil is broken while the engine is running.
Symptom Possible Cause Action
Spark jumps across gap Spark plug defective Clean or replace
Ignition timing incorrect Refer to Ignition System
Fuel not reaching fuel injector(s) or
engine Refer to item 3 (Trouble in fuel
system)
Valve timing incorrect Adjust
Engine lacks compression Refer to item 4 (Engine lacks
compression)
No sparking takes place Ignition coil disconnected or broken Connect properly or replace
Electronic Ignition System with
module Replace
Poor connections in engine harness Correct
Engine Control Module cable
disconnected or defective Correct or replace
Page 1845 of 4264
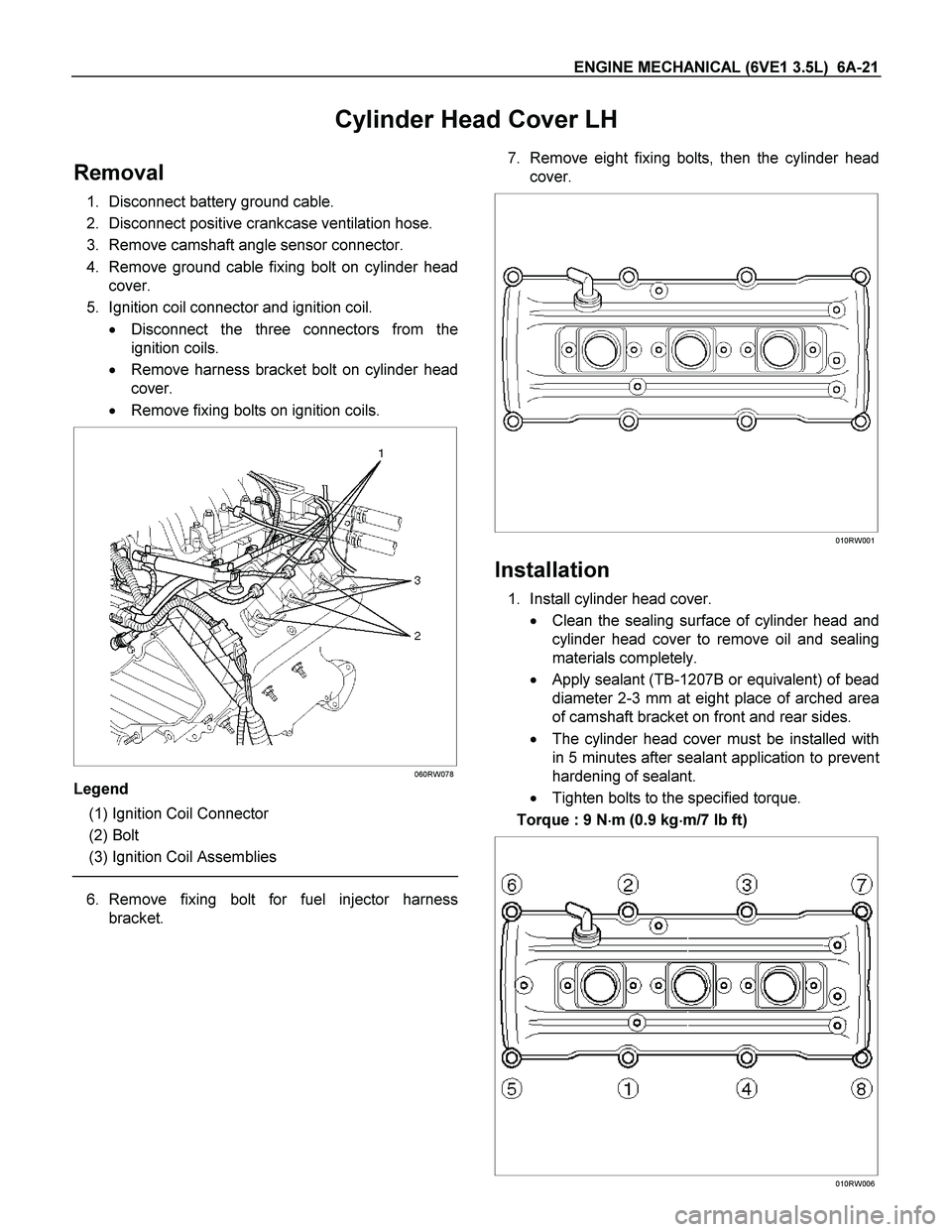
ENGINE MECHANICAL (6VE1 3.5L) 6A-21
Cylinder Head Cover LH
Removal
1. Disconnect battery ground cable.
2. Disconnect positive crankcase ventilation hose.
3. Remove camshaft angle sensor connector.
4. Remove ground cable fixing bolt on cylinder head
cover.
5. Ignition coil connector and ignition coil.
Disconnect the three connectors from the
ignition coils.
Remove harness bracket bolt on cylinder head
cover.
Remove fixing bolts on ignition coils.
060RW078
Legend
(1) Ignition Coil Connector
(2) Bolt
(3) Ignition Coil Assemblies
6. Remove fixing bolt for fuel injector harness
bracket.
7. Remove eight fixing bolts, then the cylinder head
cover.
010RW001
Installation
1. Install cylinder head cover.
Clean the sealing surface of cylinder head and
cylinder head cover to remove oil and sealing
materials completely.
Apply sealant (TB-1207B or equivalent) of bead
diameter 2-3 mm at eight place of arched area
of camshaft bracket on front and rear sides.
The cylinder head cover must be installed with
in 5 minutes after sealant application to preven
t
hardening of sealant.
Tighten bolts to the specified torque.
Torque : 9 N
m (0.9 kg
m/7 lb ft)
010RW006