battery ISUZU TF SERIES 2004 Workshop Manual
[x] Cancel search | Manufacturer: ISUZU, Model Year: 2004, Model line: TF SERIES, Model: ISUZU TF SERIES 2004Pages: 4264, PDF Size: 72.63 MB
Page 1345 of 4264
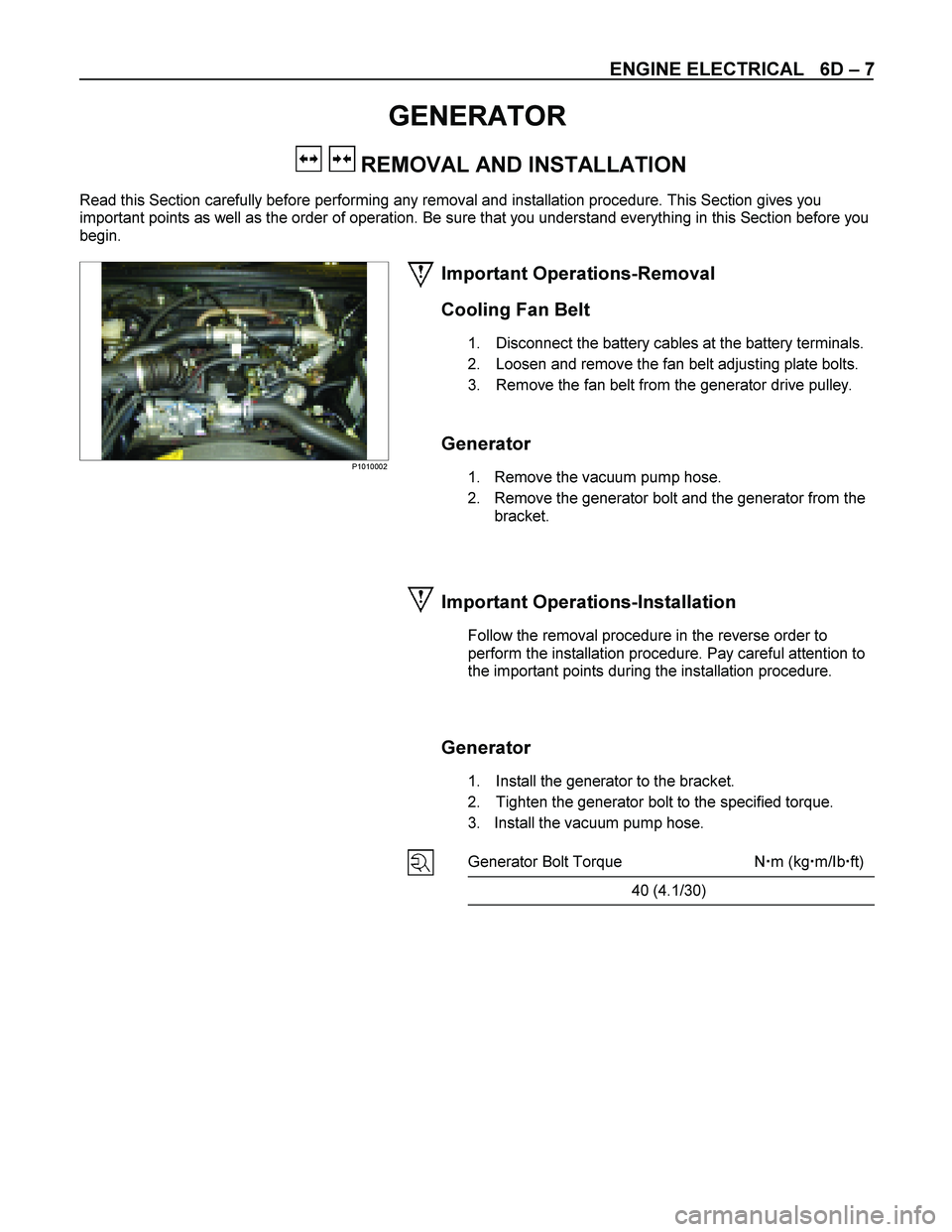
ENGINE ELECTRICAL 6D – 7
GENERATOR
REMOVAL AND INSTALLATION
Read this Section carefully before performing any removal and installation procedure. This Section gives you
important points as well as the order of operation. Be sure that you understand everything in this Section before you
begin.
P1010002
Important Operations-Removal
Cooling Fan Belt
1. Disconnect the battery cables at the battery terminals.
2. Loosen and remove the fan belt adjusting plate bolts.
3. Remove the fan belt from the generator drive pulley.
Generator
1. Remove the vacuum pump hose.
2. Remove the generator bolt and the generator from the bracket.
Important Operations-Installation
Follow the removal procedure in the reverse order to
perform the installation procedure. Pay careful attention to
the important points during the installation procedure.
Generator
1. Install the generator to the bracket.
2. Tighten the generator bolt to the specified torque.
3. Install the vacuum pump hose.
Generator Bolt Torque N m (kg m/Ib ft)
40 (4.1/30)
Page 1346 of 4264
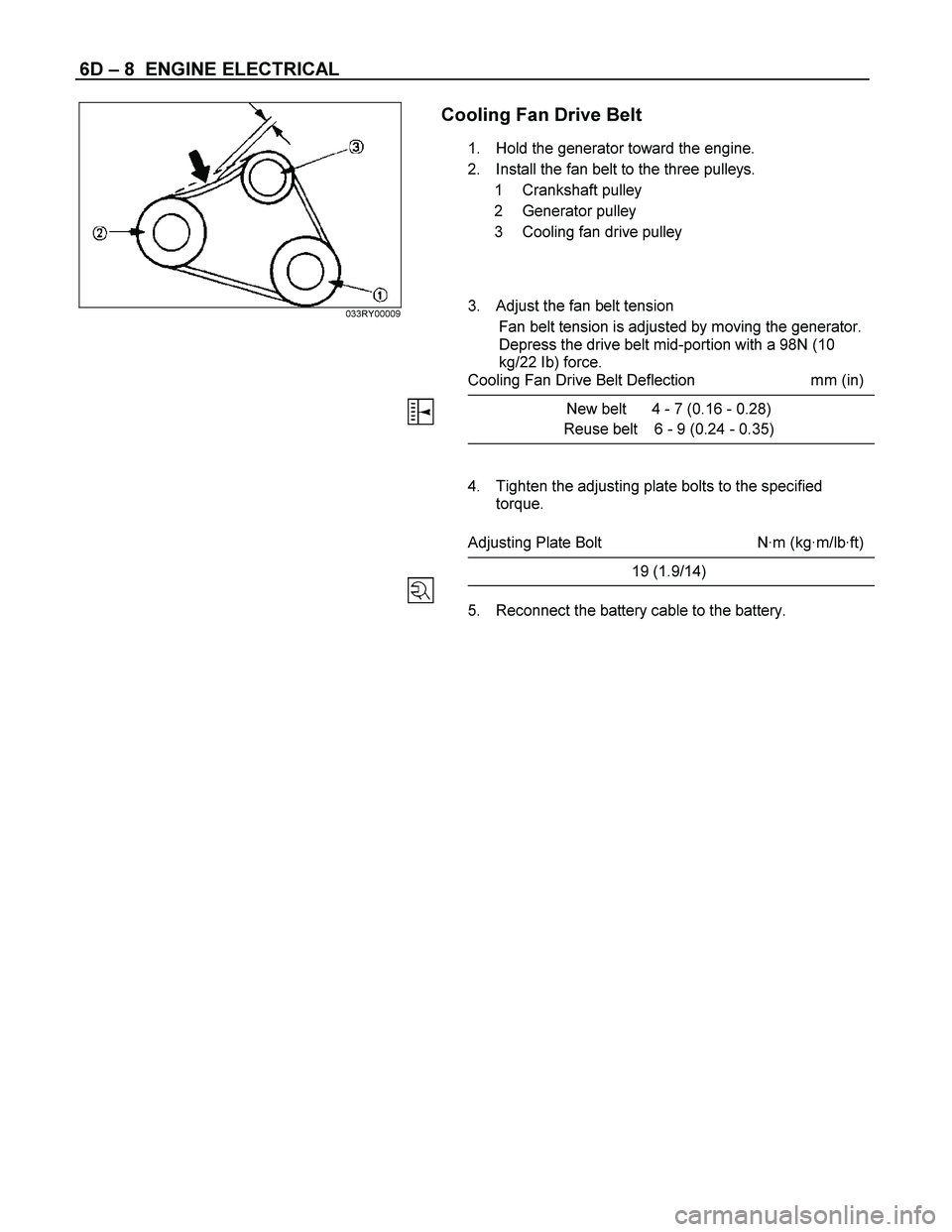
6D – 8 ENGINE ELECTRICAL
033RY00009
Cooling Fan Drive Belt
1. Hold the generator toward the engine.
2. Install the fan belt to the three pulleys.
1 Crankshaft pulley
2 Generator pulley
3 Cooling fan drive pulley
3. Adjust the fan belt tension
Fan belt tension is adjusted by moving the generator.
Depress the drive belt mid-portion with a 98N (10
kg/22 Ib) force.
Cooling Fan Drive Belt Deflection mm (in)
New belt 4 - 7 (0.16 - 0.28)
Reuse belt 6 - 9 (0.24 - 0.35)
4. Tighten the adjusting plate bolts to the specified
torque.
Adjusting Plate Bolt N·m (kg·m/lb·ft)
19 (1.9/14)
5. Reconnect the battery cable to the battery.
Page 1360 of 4264
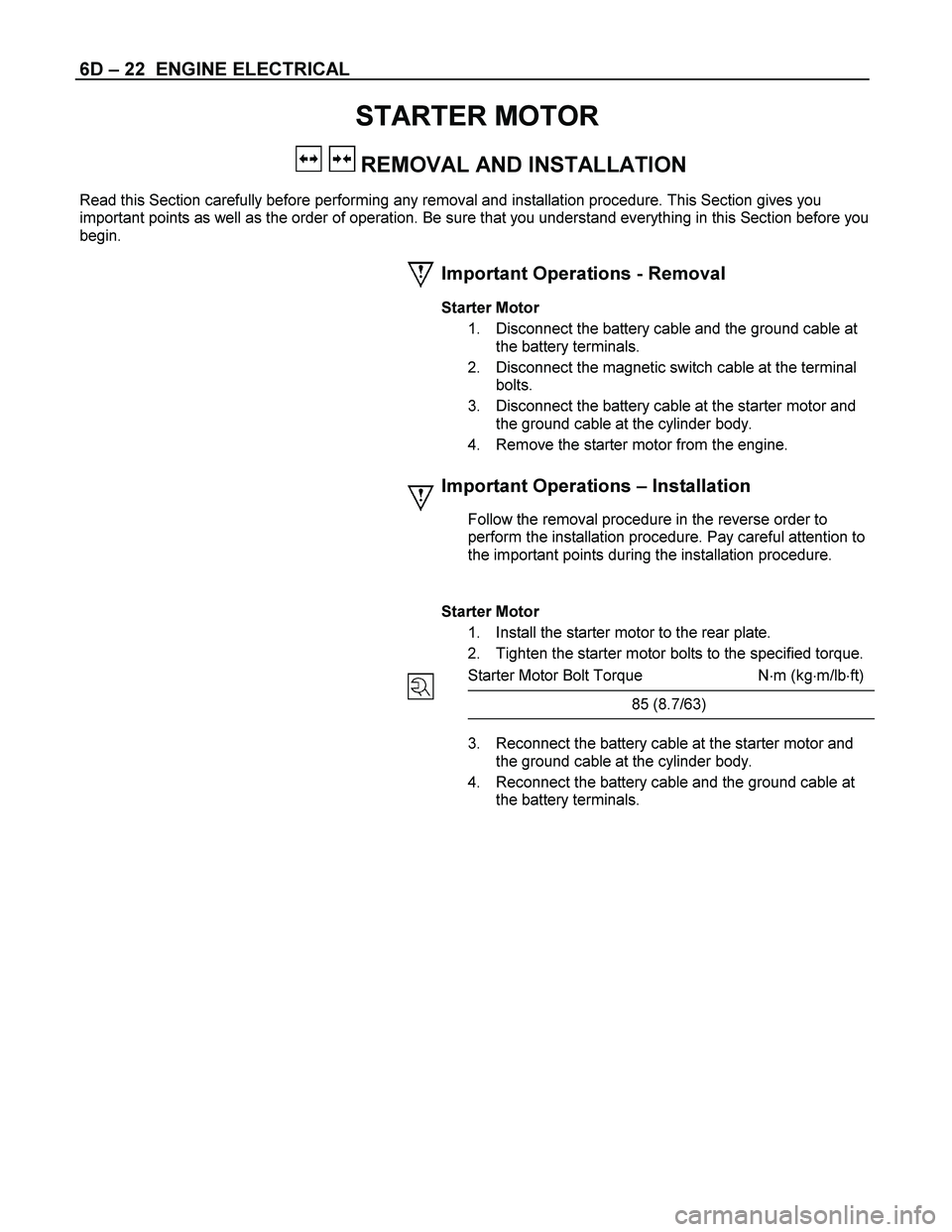
6D – 22 ENGINE ELECTRICAL
STARTER MOTOR
REMOVAL AND INSTALLATION
Read this Section carefully before performing any removal and installation procedure. This Section gives you
important points as well as the order of operation. Be sure that you understand everything in this Section before you
begin.
Important Operations - Removal
Starter Motor
1. Disconnect the battery cable and the ground cable at the battery terminals.
2. Disconnect the magnetic switch cable at the terminal bolts.
3. Disconnect the battery cable at the starter motor and the ground cable at the cylinder body.
4. Remove the starter motor from the engine.
Important Operations – Installation
Follow the removal procedure in the reverse order to
perform the installation procedure. Pay careful attention to
the important points during the installation procedure.
Starter Motor
1. Install the starter motor to the rear plate.
2. Tighten the starter motor bolts to the specified torque.
Starter Motor Bolt Torque N m (kg m/lb ft)
85 (8.7/63)
3. Reconnect the battery cable at the starter motor and
the ground cable at the cylinder body.
4. Reconnect the battery cable and the ground cable at the battery terminals.
Page 1370 of 4264
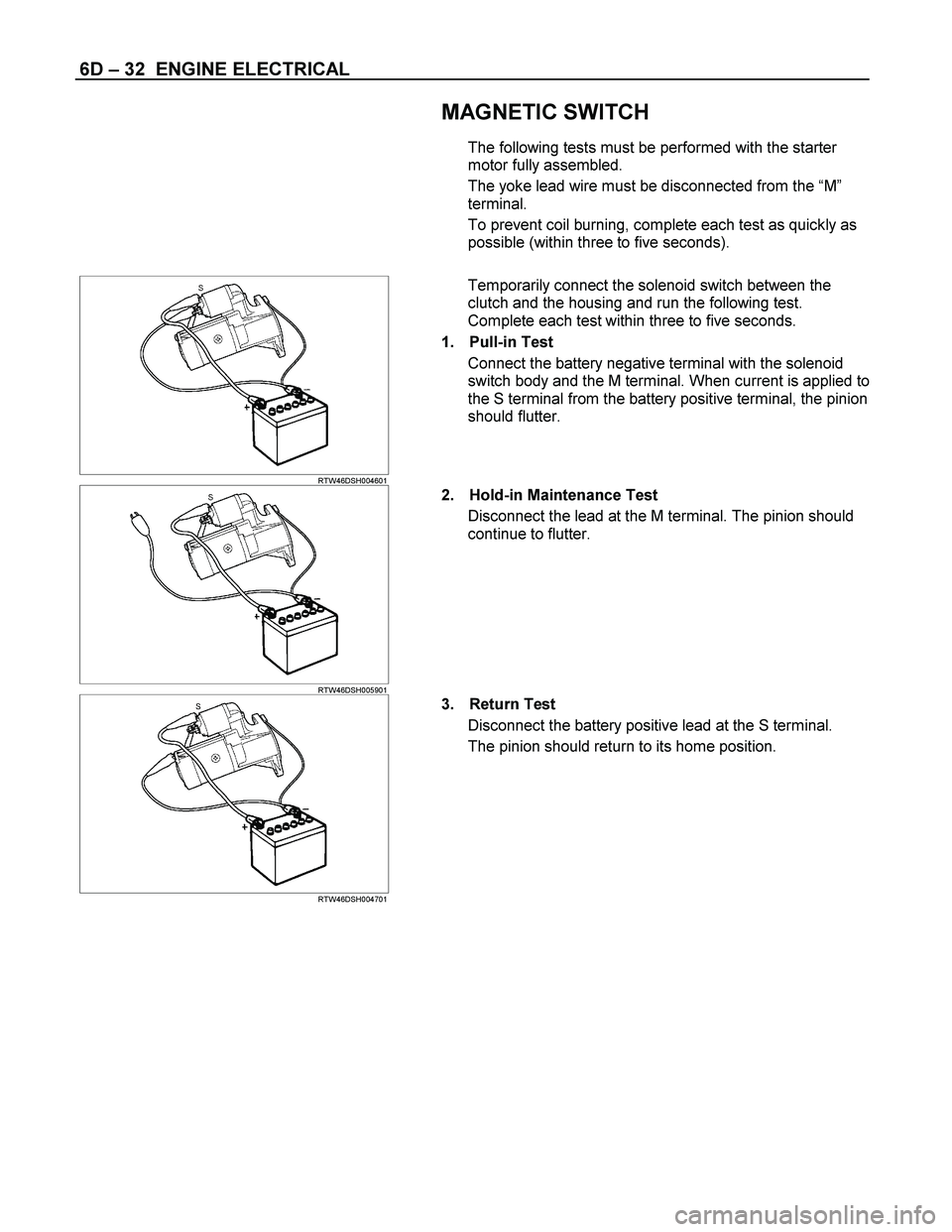
6D – 32 ENGINE ELECTRICAL
MAGNETIC SWITCH
The following tests must be performed with the starter
motor fully assembled.
The yoke lead wire must be disconnected from the “M”
terminal.
To prevent coil burning, complete each test as quickly as
possible (within three to five seconds).
RTW46DSH004601
Temporarily connect the solenoid switch between the
clutch and the housing and run the following test.
Complete each test within three to five seconds.
1. Pull-in Test
Connect the battery negative terminal with the solenoid
switch body and the M terminal. When current is applied to
the S terminal from the battery positive terminal, the pinion
should flutter.
RTW46DSH005901
2. Hold-in Maintenance Test
Disconnect the lead at the M terminal. The pinion should
continue to flutter.
RTW46DSH004701
3. Return Test
Disconnect the battery positive lead at the S terminal.
The pinion should return to its home position.
Page 1377 of 4264
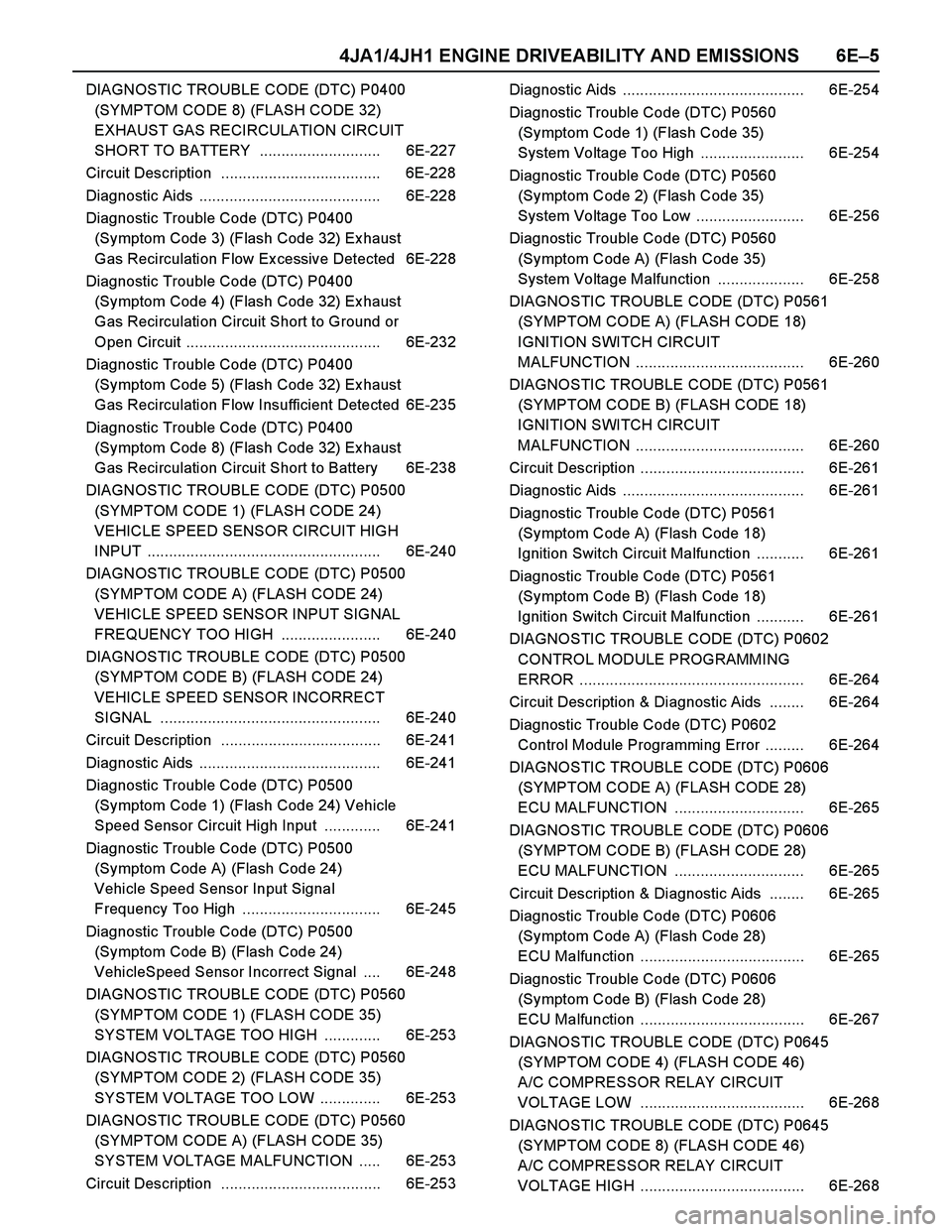
4JA1/4JH1 ENGINE DRIVEABILITY AND EMISSIONS 6E–5
DIAGNOSTIC TROUBLE CODE (DTC) P0400
(SYMPTOM CODE 8) (FLASH CODE 32)
EXHAUST GAS RECIRCULATION CIRCUIT
SHORT TO BATTERY ............................ 6E-227
Circuit Description ..................................... 6E-228
Diagnostic Aids .......................................... 6E-228
Diagnostic Trouble Code (DTC) P0400
(Symptom Code 3) (Flash Code 32) Ex haust
Gas Recirculation Flow Ex cessive Detected 6E-228
Diagnostic Trouble Code (DTC) P0400
(Symptom Code 4) (Flash Code 32) Ex haust
Gas Recirculation Circuit Short to Ground or
Open Circuit ............................................. 6E-232
Diagnostic Trouble Code (DTC) P0400
(Symptom Code 5) (Flash Code 32) Ex haust
Gas Recirculation Flow Insufficient Detected 6E-235
Diagnostic Trouble Code (DTC) P0400
(Symptom Code 8) (Flash Code 32) Ex haust
Gas Recirculation Circuit Short to Battery 6E-238
DIAGNOSTIC TROUBLE CODE (DTC) P0500
(SYMPTOM CODE 1) (FLASH CODE 24)
VEHICLE SPEED SENSOR CIRCUIT HIGH
INPUT ...................................................... 6E-240
DIAGNOSTIC TROUBLE CODE (DTC) P0500
(SYMPTOM CODE A) (FLASH CODE 24)
VEHICLE SPEED SENSOR INPUT SIGNAL
FREQUENCY TOO HIGH ....................... 6E-240
DIAGNOSTIC TROUBLE CODE (DTC) P0500
(SYMPTOM CODE B) (FLASH CODE 24)
VEHICLE SPEED SENSOR INCORRECT
SIGNAL ................................................... 6E-240
Circuit Description ..................................... 6E-241
Diagnostic Aids .......................................... 6E-241
Diagnostic Trouble Code (DTC) P0500
(Symptom Code 1) (Flash Code 24) Vehicle
Speed Sensor Circuit High Input ............. 6E-241
Diagnostic Trouble Code (DTC) P0500
(Symptom Code A) (Flash Code 24)
Vehicle Speed Sensor Input Signal
Frequency Too High ................................ 6E-245
Diagnostic Trouble Code (DTC) P0500
(Symptom Code B) (Flash Code 24)
VehicleSpeed Sensor Incorrect Signal .... 6E-248
DIAGNOSTIC TROUBLE CODE (DTC) P0560
(SYMPTOM CODE 1) (FLASH CODE 35)
SYSTEM VOLTAGE TOO HIGH ............. 6E-253
DIAGNOSTIC TROUBLE CODE (DTC) P0560
(SYMPTOM CODE 2) (FLASH CODE 35)
SYSTEM VOLTAGE TOO LOW .............. 6E-253
DIAGNOSTIC TROUBLE CODE (DTC) P0560
(SYMPTOM CODE A) (FLASH CODE 35)
SYSTEM VOLTAGE MALFUNCTION ..... 6E-253
Circuit Description ..................................... 6E-253Diagnostic Aids .......................................... 6E-254
Diagnostic Trouble Code (DTC) P0560
(Symptom Code 1) (Flash Code 35)
System Voltage Too High ........................ 6E-254
Diagnostic Trouble Code (DTC) P0560
(Symptom Code 2) (Flash Code 35)
System Voltage Too Low ......................... 6E-256
Diagnostic Trouble Code (DTC) P0560
(Symptom Code A) (Flash Code 35)
System Voltage Malfunction .................... 6E-258
DIAGNOSTIC TROUBLE CODE (DTC) P0561
(SYMPTOM CODE A) (FLASH CODE 18)
IGNITION SWITCH CIRCUIT
MALFUNCTION ....................................... 6E-260
DIAGNOSTIC TROUBLE CODE (DTC) P0561
(SYMPTOM CODE B) (FLASH CODE 18)
IGNITION SWITCH CIRCUIT
MALFUNCTION ....................................... 6E-260
Circuit Description ...................................... 6E-261
Diagnostic Aids .......................................... 6E-261
Diagnostic Trouble Code (DTC) P0561
(Symptom Code A) (Flash Code 18)
Ignition Switch Circuit Malfunction ........... 6E-261
Diagnostic Trouble Code (DTC) P0561
(Symptom Code B) (Flash Code 18)
Ignition Switch Circuit Malfunction ........... 6E-261
DIAGNOSTIC TROUBLE CODE (DTC) P0602
CONTROL MODULE PROGRAMMING
ERROR .................................................... 6E-264
Circuit Description & Diagnostic Aids ........ 6E-264
Diagnostic Trouble Code (DTC) P0602
Control Module Programming Error ......... 6E-264
DIAGNOSTIC TROUBLE CODE (DTC) P0606
(SYMPTOM CODE A) (FLASH CODE 28)
ECU MALFUNCTION .............................. 6E-265
DIAGNOSTIC TROUBLE CODE (DTC) P0606
(SYMPTOM CODE B) (FLASH CODE 28)
ECU MALFUNCTION .............................. 6E-265
Circuit Description & Diagnostic Aids ........ 6E-265
Diagnostic Trouble Code (DTC) P0606
(Symptom Code A) (Flash Code 28)
ECU Malfunction ...................................... 6E-265
Diagnostic Trouble Code (DTC) P0606
(Symptom Code B) (Flash Code 28)
ECU Malfunction ...................................... 6E-267
DIAGNOSTIC TROUBLE CODE (DTC) P0645
(SYMPTOM CODE 4) (FLASH CODE 46)
A/C COMPRESSOR RELAY CIRCUIT
VOLTAGE LOW ...................................... 6E-268
DIAGNOSTIC TROUBLE CODE (DTC) P0645
(SYMPTOM CODE 8) (FLASH CODE 46)
A/C COMPRESSOR RELAY CIRCUIT
VOLTAGE HIGH ...................................... 6E-268
Page 1382 of 4264
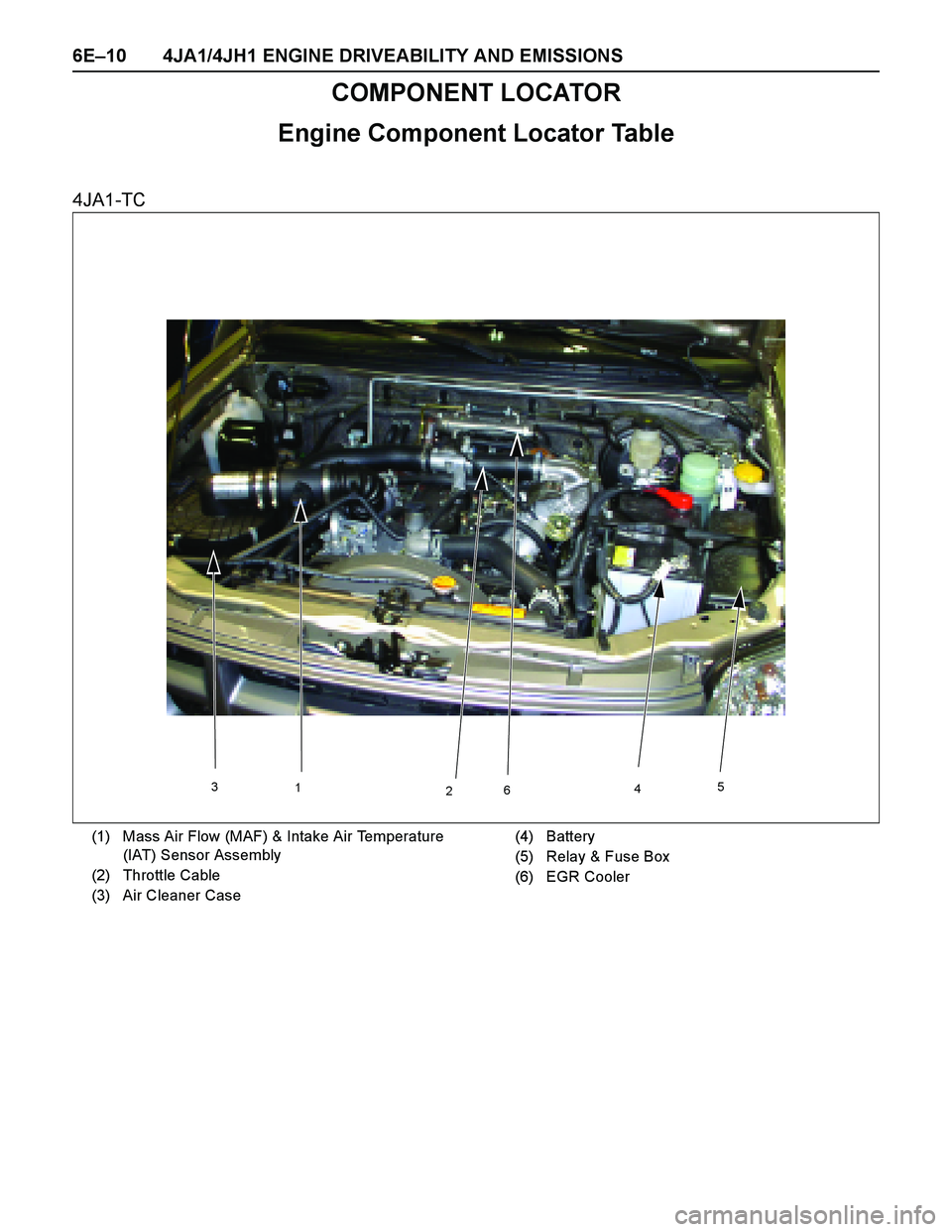
6E–10 4JA1/4JH1 ENGINE DRIVEABILITY AND EMISSIONS
COMPONENT LOCATOR
Engine Component Locator Table
4JA1-TC
3
1
2645
(1) Mass Air Flow (MAF) & Intake Air Temperature
(IAT) Sensor Assembly
(2) Throttle Cable
(3) Air Cleaner Case(4) Battery
(5) Relay & Fuse Box
(6) EGR Cooler
Page 1383 of 4264
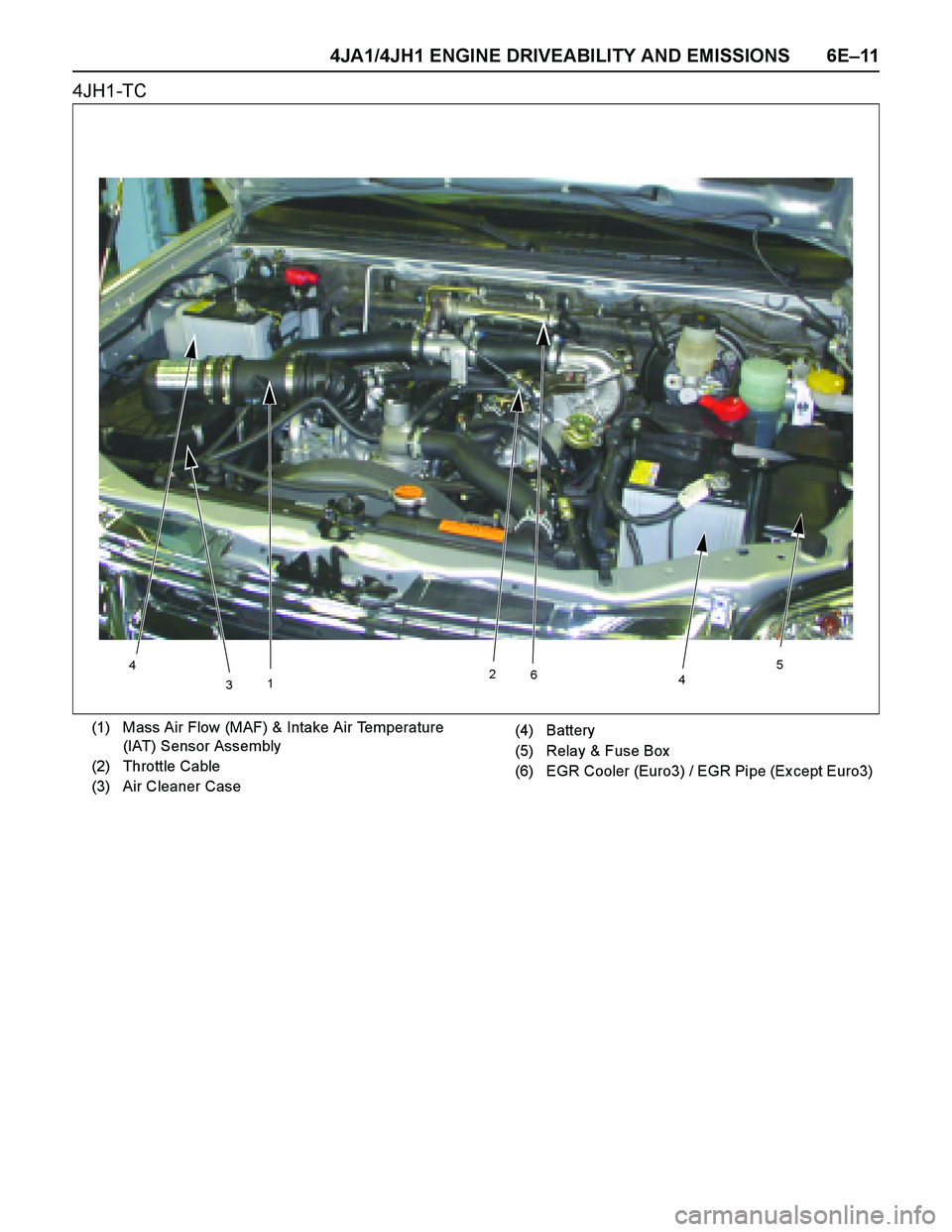
4JA1/4JH1 ENGINE DRIVEABILITY AND EMISSIONS 6E–11
4JH1-TC
312
6
45
4
(1) Mass Air Flow (MAF) & Intake Air Temperature
(IAT) Sensor Assembly
(2) Throttle Cable
(3) Air Cleaner Case(4) Battery
(5) Relay & Fuse Box
(6) EGR Cooler (Euro3) / EGR Pipe (Ex cept Euro3)
Page 1414 of 4264
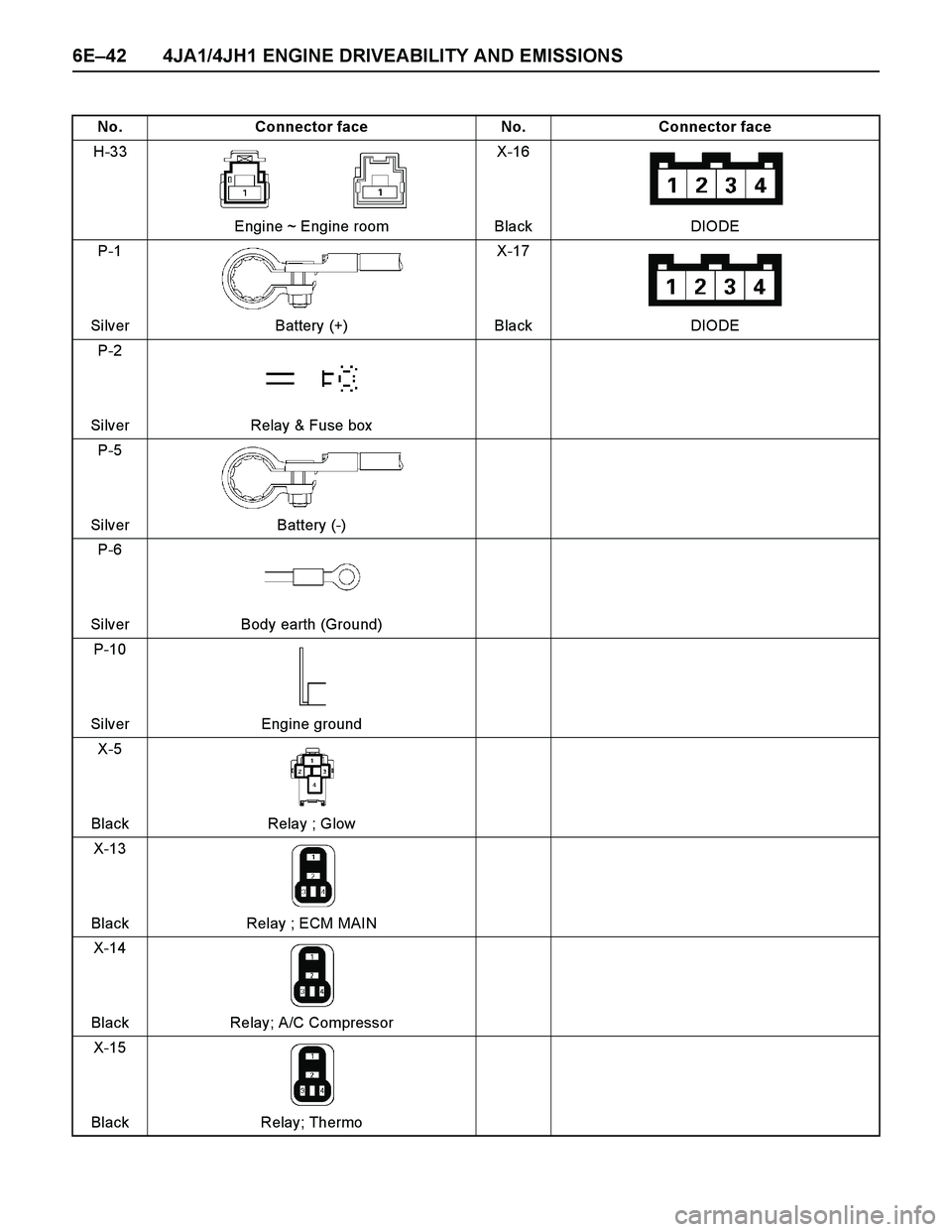
6E–42 4JA1/4JH1 ENGINE DRIVEABILITY AND EMISSIONS
No. Connector face No. Connector face
H-33
Engine ~ Engine roomX-16
Black DIODE
P-1
Silver Battery (+)X-17
Black DIODE
P-2
Silver Relay & Fuse box
P-5
Silver Battery (-)
P-6
Silver Body earth (Ground)
P-10
Silver Engine ground
X-5
Black Relay ; Glow
X-13
Black Relay ; ECM MAIN
X-14
Black Relay; A/C Compressor
X-15
Black Relay; Thermo
Page 1451 of 4264
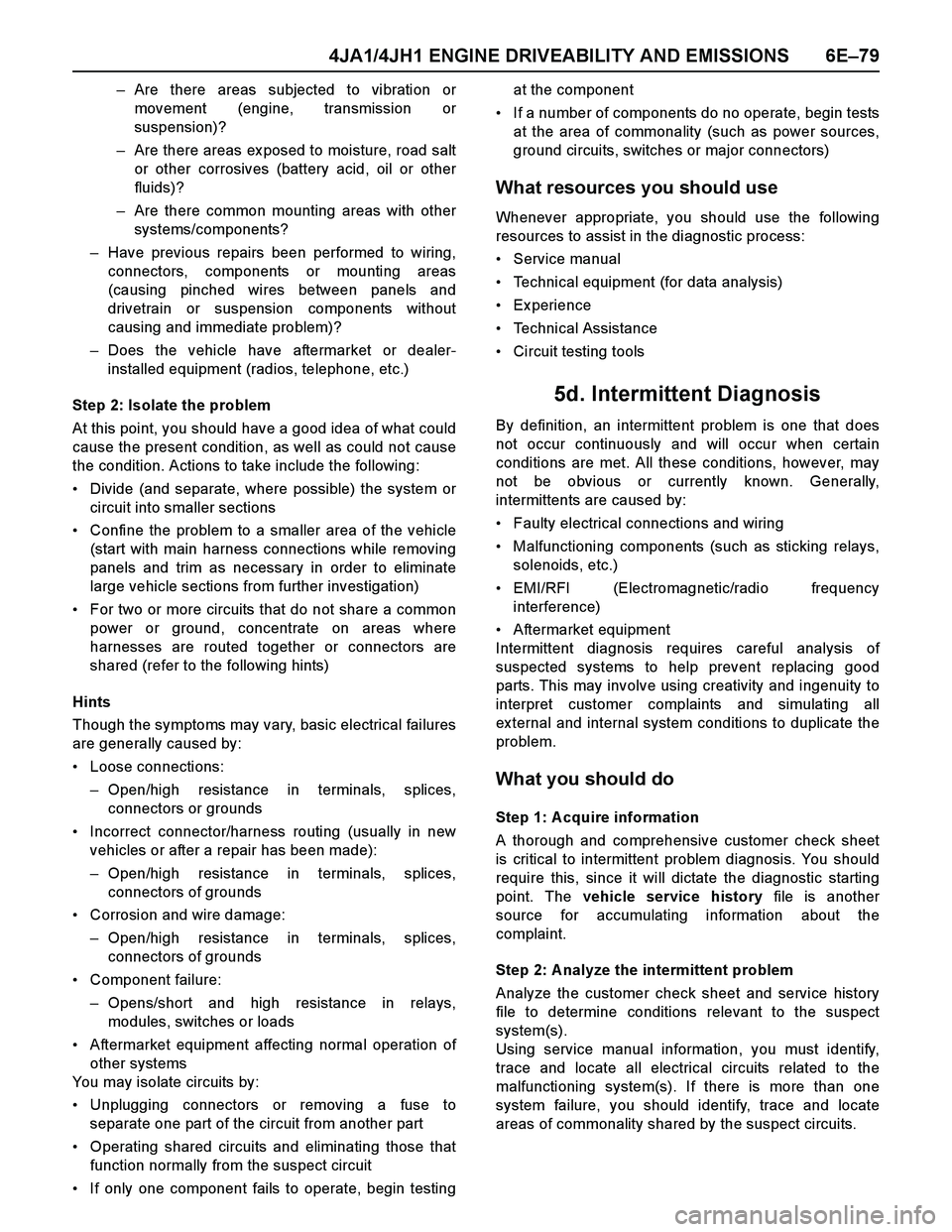
4JA1/4JH1 ENGINE DRIVEABILITY AND EMISSIONS 6E–79
–Are there areas subjected to vibration or
movement (engine, transmission or
suspension)?
–Are there areas ex posed to moisture, road salt
or other corrosives (battery acid, oil or other
fluids)?
–Are there common mounting areas with other
systems/components?
–Have previous repairs been performed to wiring,
connectors, components or mounting areas
(causing pinched wires between panels and
drivetrain or suspension components without
causing and immediate problem)?
–Does the vehicle have aftermarket or dealer-
installed equipment (radios, telephone, etc.)
Step 2: Isolate the problem
At this point, you should have a good idea of what could
cause the present condition, as well as could not cause
the condition. Actions to take include the following:
Divide (and separate, where possible) the system or
circuit into smaller sections
Confine the problem to a smaller area of the vehicle
(start with main harness connections while removing
panels and trim as necessary in order to eliminate
large vehicle sections from further investigation)
For two or more circuits that do not share a common
power or ground, concentrate on areas where
harnesses are routed together or connectors are
shared (refer to the following hints)
Hints
Though the symptoms may vary, basic electrical failures
are generally caused by:
Loose connections:
–Open/high resistance in terminals, splices,
connectors or grounds
Incorrect connector/harness routing (usually in new
vehicles or after a repair has been made):
–Open/high resistance in terminals, splices,
connectors of grounds
Corrosion and wire damage:
–Open/high resistance in terminals, splices,
connectors of grounds
Component failure:
–Opens/short and high resistance in relays,
modules, switches or loads
Aftermarket equipment affecting normal operation of
other systems
You may isolate circuits by:
Unplugging connectors or removing a fuse to
separate one part of the circuit from another part
Operating shared circuits and eliminating those that
function normally from the suspect circuit
If only one component fails to operate, begin testingat the component
If a number of components do no operate, begin tests
at the area of commonality (such as power sources,
ground circuits, switches or major connectors)
What resources you should use
Whenever appropriate, you should use the following
resources to assist in the diagnostic process:
Service manual
Technical equipment (for data analysis)
Ex perience
Technical Assistance
Circuit testing tools
5d. Intermittent Diagnosis
By definition, an intermittent problem is one that does
not occur continuously and will occur when certain
conditions are met. All these conditions, however, may
not be obvious or currently known. Generally,
intermittents are caused by:
Faulty electrical connections and wiring
Malfunctioning components (such as sticking relays,
solenoids, etc.)
EMI/RFI (Electromagnetic/radio frequency
interference)
Aftermarket equipment
Intermittent diagnosis requires careful analysis of
suspected systems to help prevent replacing good
parts. This may involve using creativity and ingenuity to
interpret customer complaints and simulating all
ex ternal and internal system conditions to duplicate the
problem.
What you should do
Step 1: A cquire information
A thorough and comprehensive customer check sheet
is critical to intermittent problem diagnosis. You should
require this, since it will dictate the diagnostic starting
point. The vehicle service history file is another
source for accumulating information about the
complaint.
Step 2: A nalyze the intermittent problem
Analyze the customer check sheet and service history
file to determine conditions relevant to the suspect
system(s).
Using service manual information, you must identify,
trace and locate all electrical circuits related to the
malfunctioning system(s). If there is more than one
system failure, you should identify, trace and locate
areas of commonality shared by the suspect circuits.
Page 1471 of 4264
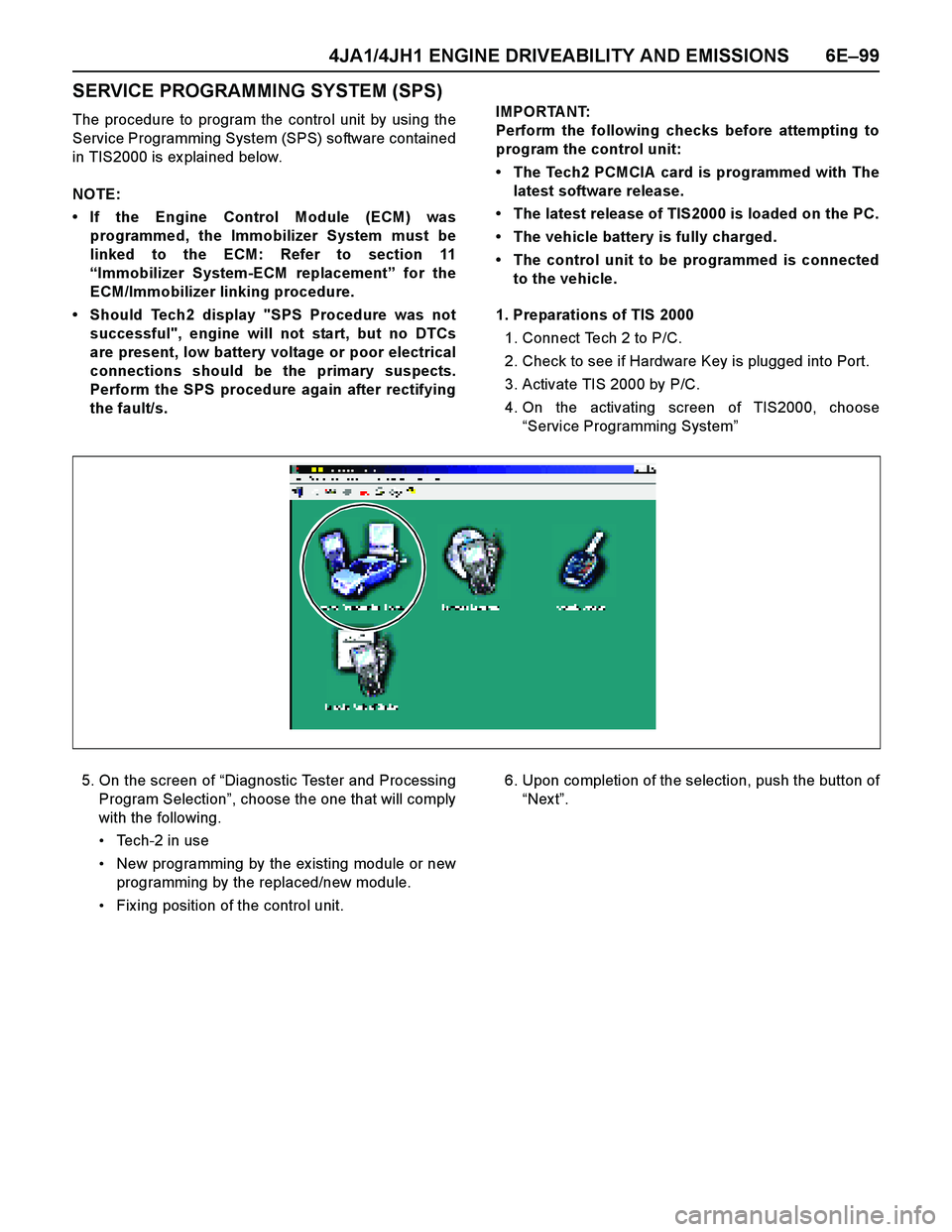
4JA1/4JH1 ENGINE DRIVEABILITY AND EMISSIONS 6E–99
SERVICE PROGRAMMING SYSTEM (SPS)
The procedure to program the control unit by using the
Service Programming System (SPS) software contained
in TIS2000 is ex plained below.
NOTE:
If the Engine Control Module (ECM) was
programmed, the Immobilizer System must be
linked to the ECM: Refer to section 11
“Immobilizer System-ECM replacement” for the
ECM/Immobilizer linking procedure.
Should Tech2 display "SPS Procedure was not
successful", engine will not start, but no DTCs
are present, low battery voltage or poor electrical
connections should be the primary suspects.
Perform the SPS procedure again after rectifying
the fault/s.IMPORTANT:
Perform the following checks before attempting to
program the control unit:
The Tech2 PCMCIA card is programmed with The
latest software release.
The latest release of TIS2000 is loaded on the PC.
The vehicle battery is fully charged.
The control unit to be programmed is connected
to the vehicle.
1. Preparations of TIS 2000
1. Connect Tech 2 to P/C.
2. Check to see if Hardware Key is plugged into Port.
3. Activate TIS 2000 by P/C.
4. On the activating screen of TIS2000, choose
“Service Programming System”
5. On the screen of “Diagnostic Tester and Processing
Program Selection”, choose the one that will comply
with the following.
Tech-2 in use
New programming by the ex isting module or new
programming by the replaced/new module.
Fix ing position of the control unit.6. Upon completion of the selection, push the button of
“Nex t”.