check engine ISUZU TF SERIES 2004 Workshop Manual
[x] Cancel search | Manufacturer: ISUZU, Model Year: 2004, Model line: TF SERIES, Model: ISUZU TF SERIES 2004Pages: 4264, PDF Size: 72.63 MB
Page 1783 of 4264
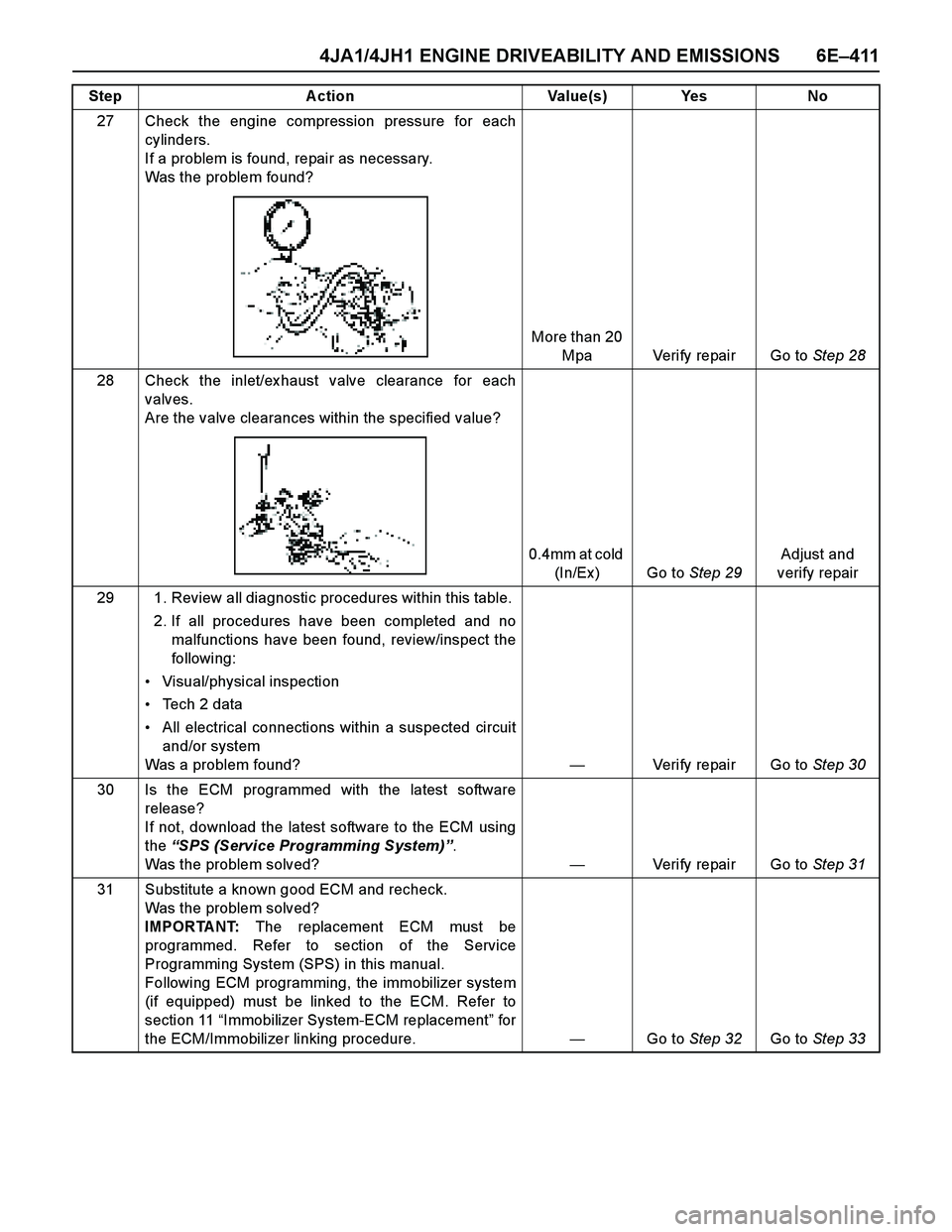
4JA1/4JH1 ENGINE DRIVEABILITY AND EMISSIONS 6E–411
27 Check the engine compression pressure for each
cylinders.
If a problem is found, repair as necessary.
Was the problem found?
More than 20
Mpa Verify repair Go to Step 28
28 Check the inlet/ex haust valve clearance for each
valves.
Are the valve clearances within the specified value?
0.4mm at cold
(In/Ex ) Go to Step 29Adjust and
verify repair
29 1. Review all diagnostic procedures within this table.
2. If all procedures have been completed and no
malfunctions have been found, review/inspect the
followi ng:
Visual/physical inspection
Tech 2 data
All electrical connections within a suspected circuit
and/or system
Was a problem found?—Verify repair Go to Step 30
30 Is the ECM programmed with the latest software
release?
If not, download the latest software to the ECM using
the “SPS (Service Programming System)”.
Was the problem solved?—Verify repair Go to Step 31
31 Substitute a known good ECM and recheck.
Was the problem solved?
IMPORTANT: The replacement ECM must be
programmed. Refer to section of the Service
Programming System (SPS) in this manual.
Following ECM programming, the immobilizer system
(if equipped) must be linked to the ECM. Refer to
section 11 “Immobilizer System-ECM replacement” for
the ECM/Immobilizer linking procedure. —Go to Step 32Go to Step 33 Step Action Value(s) Yes No
Page 1785 of 4264
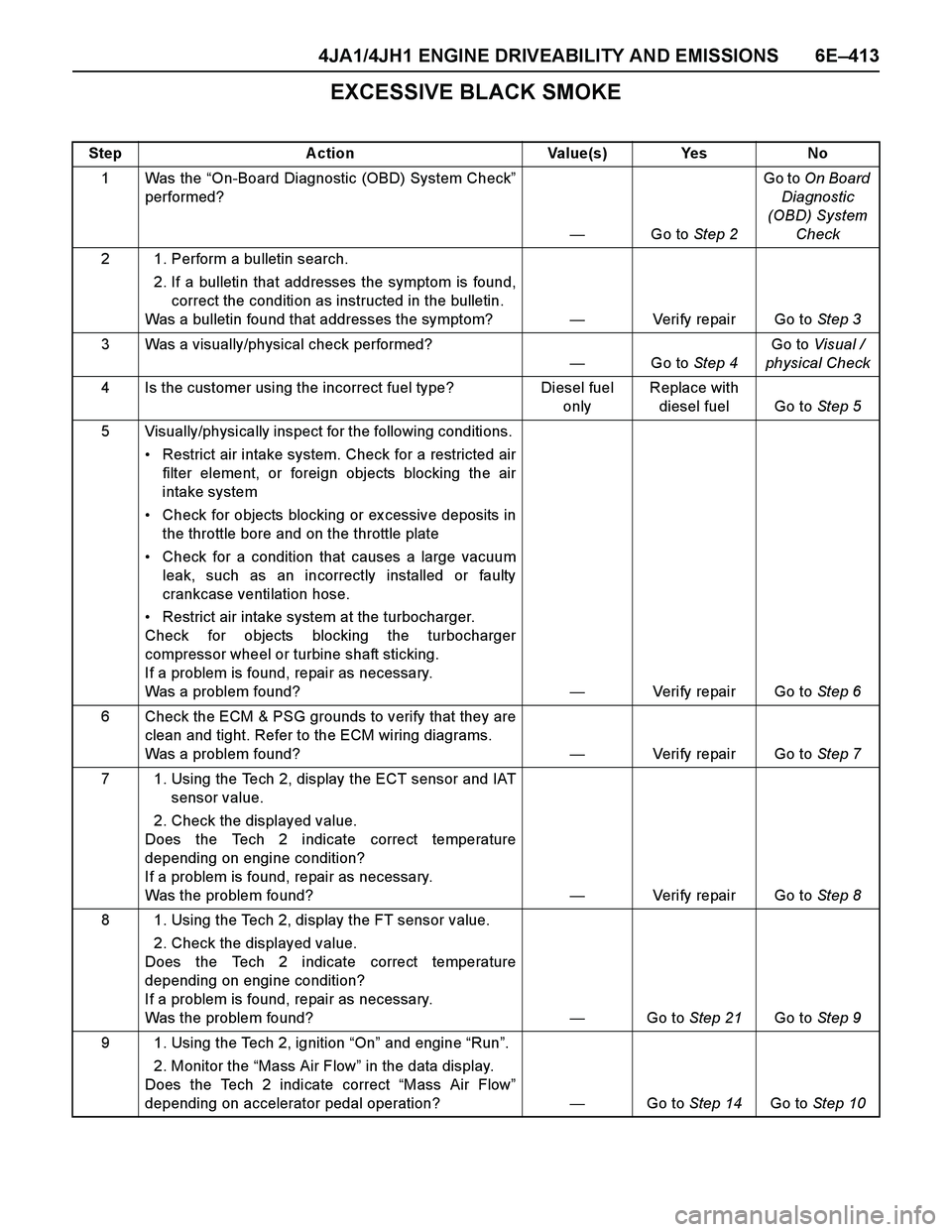
4JA1/4JH1 ENGINE DRIVEABILITY AND EMISSIONS 6E–413
EXCESSIVE BLACK SMOKE
Step Action Value(s) Yes No
1Was the “On-Board Diagnostic (OBD) System Check”
performed?
—Go to Step 2Go to On Board
Diagnostic
(OBD) System
Check
2 1. Perform a bulletin search.
2. If a bulletin that addresses the symptom is found,
correct the condition as instructed in the bulletin.
Was a bulletin found that addresses the symptom?—Verify repair Go to Step 3
3 Was a visually/physical check performed?
—Go to Step 4Go to Visual /
physical Check
4 Is the customer using the incorrect fuel type? Diesel fuel
onlyReplace with
diesel fuel Go to Step 5
5 Visually/physically inspect for the following conditions.
Restrict air intake system. Check for a restricted air
filter element, or foreign objects blocking the air
intake system
Check for objects blocking or ex cessive deposits in
the throttle bore and on the throttle plate
Check for a condition that causes a large vacuum
leak, such as an incorrectly installed or faulty
crankcase ventilation hose.
Restrict air intake system at the turbocharger.
Check for objects blocking the turbocharger
compressor wheel or turbine shaft sticking.
If a problem is found, repair as necessary.
Was a problem found?—Verify repair Go to Step 6
6 Check the ECM & PSG grounds to verify that they are
clean and tight. Refer to the ECM wiring diagrams.
Was a problem found?—Verify repair Go to Step 7
7 1. Using the Tech 2, display the ECT sensor and IAT
sensor value.
2. Check the displayed value.
Does the Tech 2 indicate correct temperature
depending on engine condition?
If a problem is found, repair as necessary.
Was the problem found?—Verify repair Go to Step 8
8 1. Using the Tech 2, display the FT sensor value.
2. Check the displayed value.
Does the Tech 2 indicate correct temperature
depending on engine condition?
If a problem is found, repair as necessary.
Was the problem found?—Go to Step 21Go to Step 9
9 1. Using the Tech 2, ignition “On” and engine “Run”.
2. Monitor the “Mass Air Flow” in the data display.
Does the Tech 2 indicate correct “Mass Air Flow”
depending on accelerator pedal operation? —Go to Step 14Go to Step 10
Page 1786 of 4264
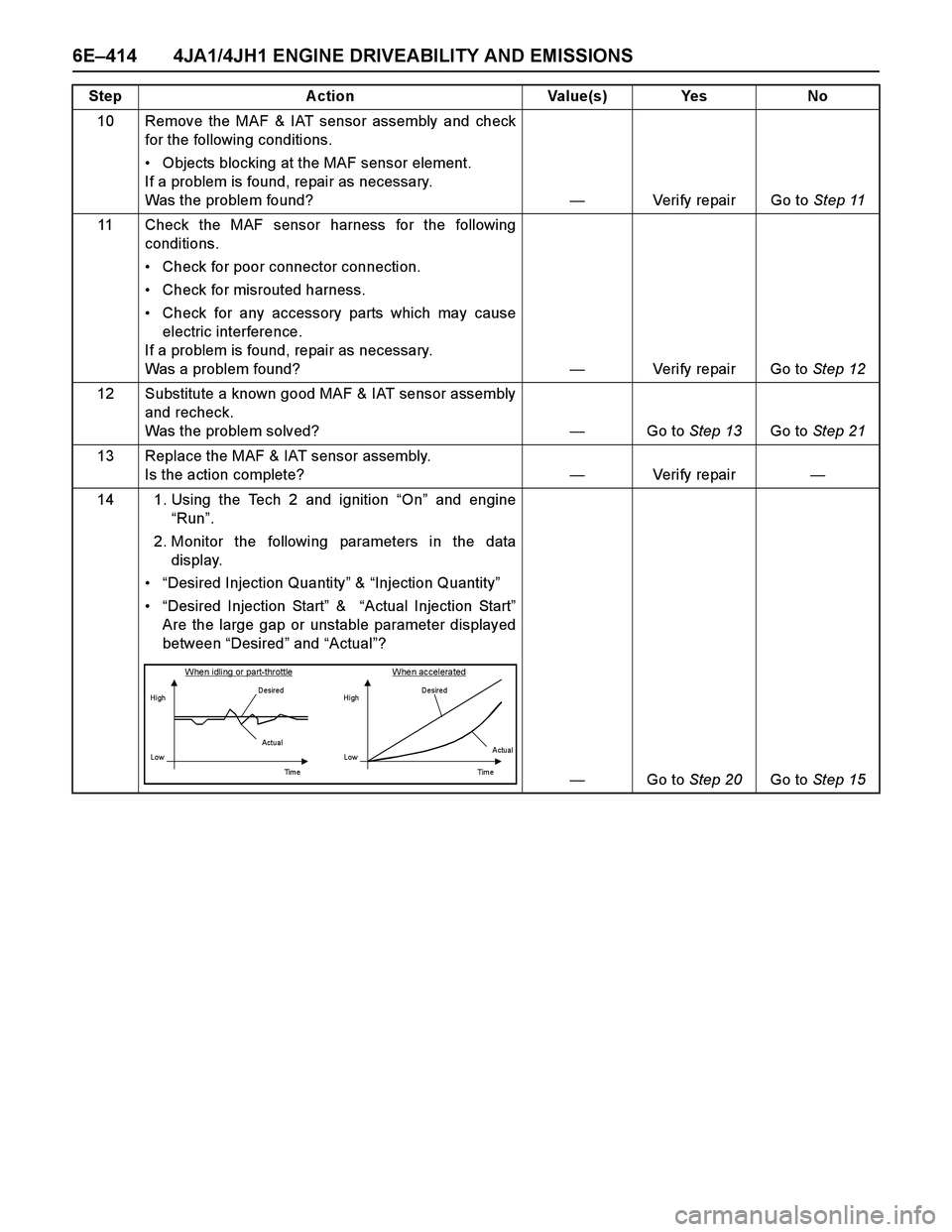
6E–414 4JA1/4JH1 ENGINE DRIVEABILITY AND EMISSIONS
10 Remove the MAF & IAT sensor assembly and check
for the following conditions.
Objects blocking at the MAF sensor element.
If a problem is found, repair as necessary.
Was the problem found?—Verify repair Go to Step 11
11 Check the MAF sensor harness for the following
conditions.
Check for poor connector connection.
Check for misrouted harness.
Check for any accessory parts which may cause
electric interference.
If a problem is found, repair as necessary.
Was a problem found? —Verify repair Go to Step 12
12 Substitute a known good MAF & IAT sensor assembly
and recheck.
Was the problem solved?—Go to Step 13Go to Step 21
13 Replace the MAF & IAT sensor assembly.
Is the action complete?—Veri fy repai r—
14 1. Using the Tech 2 and ignition “On” and engine
“Run”.
2. Monitor the following parameters in the data
display.
“Desired Injection Quantity” & “Injection Quantity”
“Desired Injection Start” & “Actual Injection Start”
Are the large gap or unstable parameter displayed
between “Desired” and “Actual”?
—Go to Step 20Go to Step 15 Step Action Value(s) Yes No
When idling or part-throttle When accelerated
HighD esired
Low
Ti m e Actu al
High
LowD esired
Actual
Tim e
Page 1787 of 4264
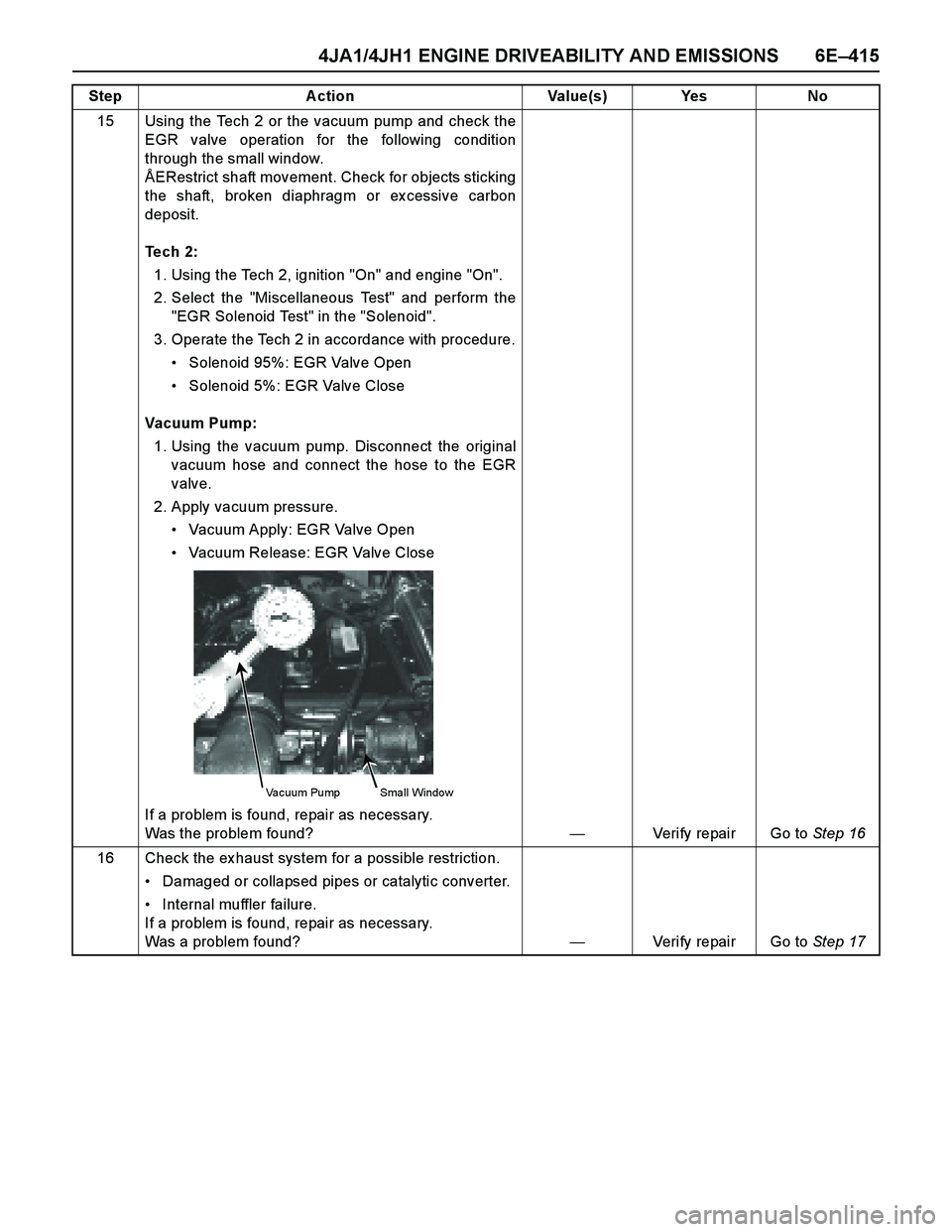
4JA1/4JH1 ENGINE DRIVEABILITY AND EMISSIONS 6E–415
15 Using the Tech 2 or the vacuum pump and check the
EGR valve operation for the following condition
through the small window.
ÅERestrict shaft movement. Check for objects sticking
the shaft, broken diaphragm or ex cessive carbon
deposit.
Tech 2:
1. Using the Tech 2, ignition "On" and engine "On".
2. Select the "Miscellaneous Test" and perform the
"EGR Solenoid Test" in the "Solenoid".
3. Operate the Tech 2 in accordance with procedure.
Solenoid 95%: EGR Valve Open
Solenoid 5%: EGR Valve Close
Vacuum Pump:
1. Using the vacuum pump. Disconnect the original
vacuum hose and connect the hose to the EGR
valve.
2. Apply vacuum pressure.
Vacuum Apply: EGR Valve Open
Vacuum Release: EGR Valve Close
If a problem is found, repair as necessary.
Was the problem found?—Verify repair Go to Step 16
16 Check the ex haust system for a possible restriction.
Damaged or collapsed pipes or catalytic converter.
Internal muffler failure.
If a problem is found, repair as necessary.
Was a problem found?—Verify repair Go to Step 17 Step Action Value(s) Yes No
Vacuum Pump Small Window
Page 1788 of 4264
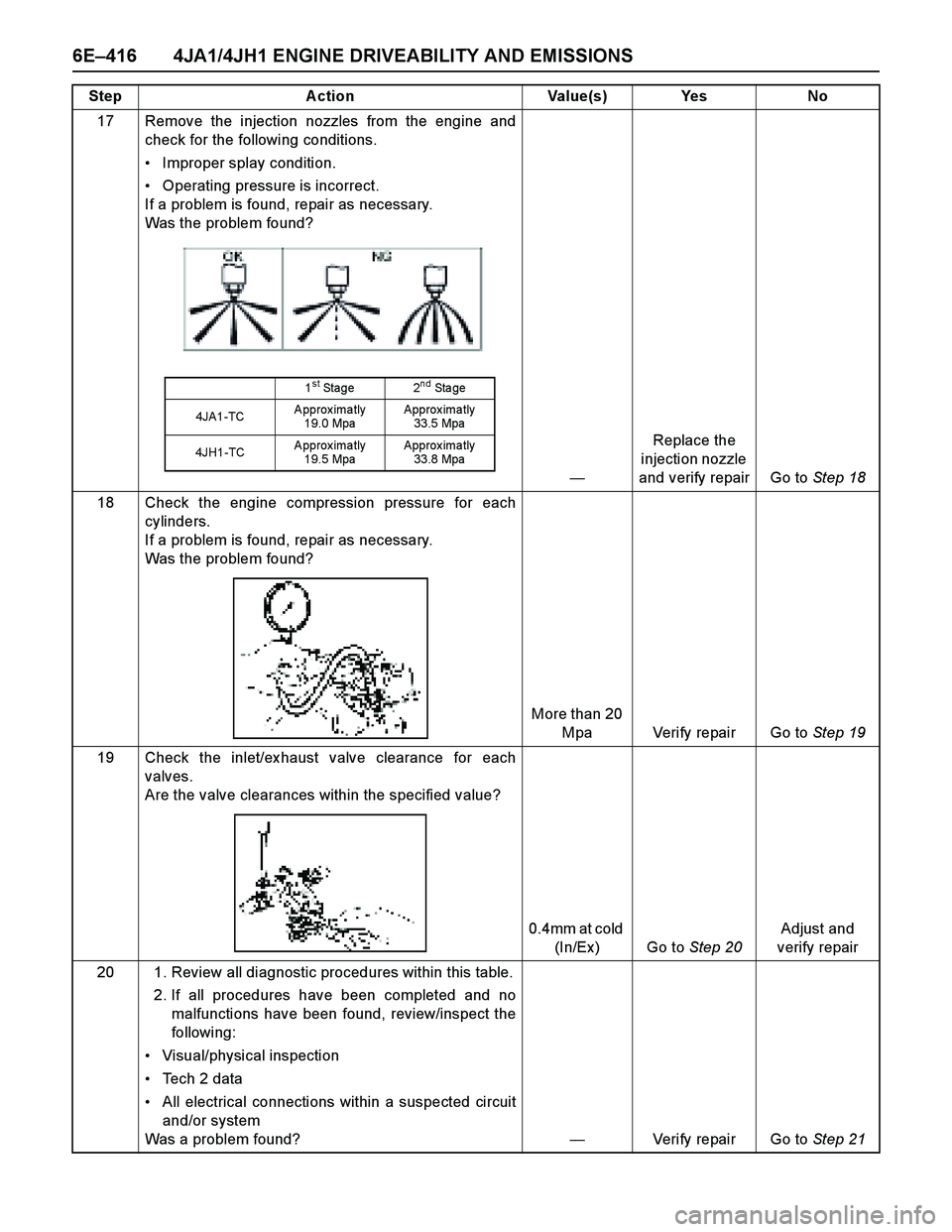
6E–416 4JA1/4JH1 ENGINE DRIVEABILITY AND EMISSIONS
17 Remove the injection nozzles from the engine and
check for the following conditions.
Improper splay condition.
Operating pressure is incorrect.
If a problem is found, repair as necessary.
Was the problem found?
—Replace the
injection nozzle
and verify repair Go to Step 18
18 Check the engine compression pressure for each
cylinders.
If a problem is found, repair as necessary.
Was the problem found?
More than 20
Mpa Verify repair Go to Step 19
19 Check the inlet/ex haust valve clearance for each
valves.
Are the valve clearances within the specified value?
0.4mm at cold
(In/Ex ) Go to Step 20Adjust and
verify repair
20 1. Review all diagnostic procedures within this table.
2. If all procedures have been completed and no
malfunctions have been found, review/inspect the
followi ng:
Visual/physical inspection
Tech 2 data
All electrical connections within a suspected circuit
and/or system
Was a problem found?—Verify repair Go to Step 21 Step Action Value(s) Yes No
1st Stage 2nd Sta ge
4JA1-TCApproximatly
19.0 MpaApprox ima tly
33.5 Mpa
4JH1-TCApproximatly
19.5 MpaApprox ima tly
33.8 Mpa
Page 1789 of 4264
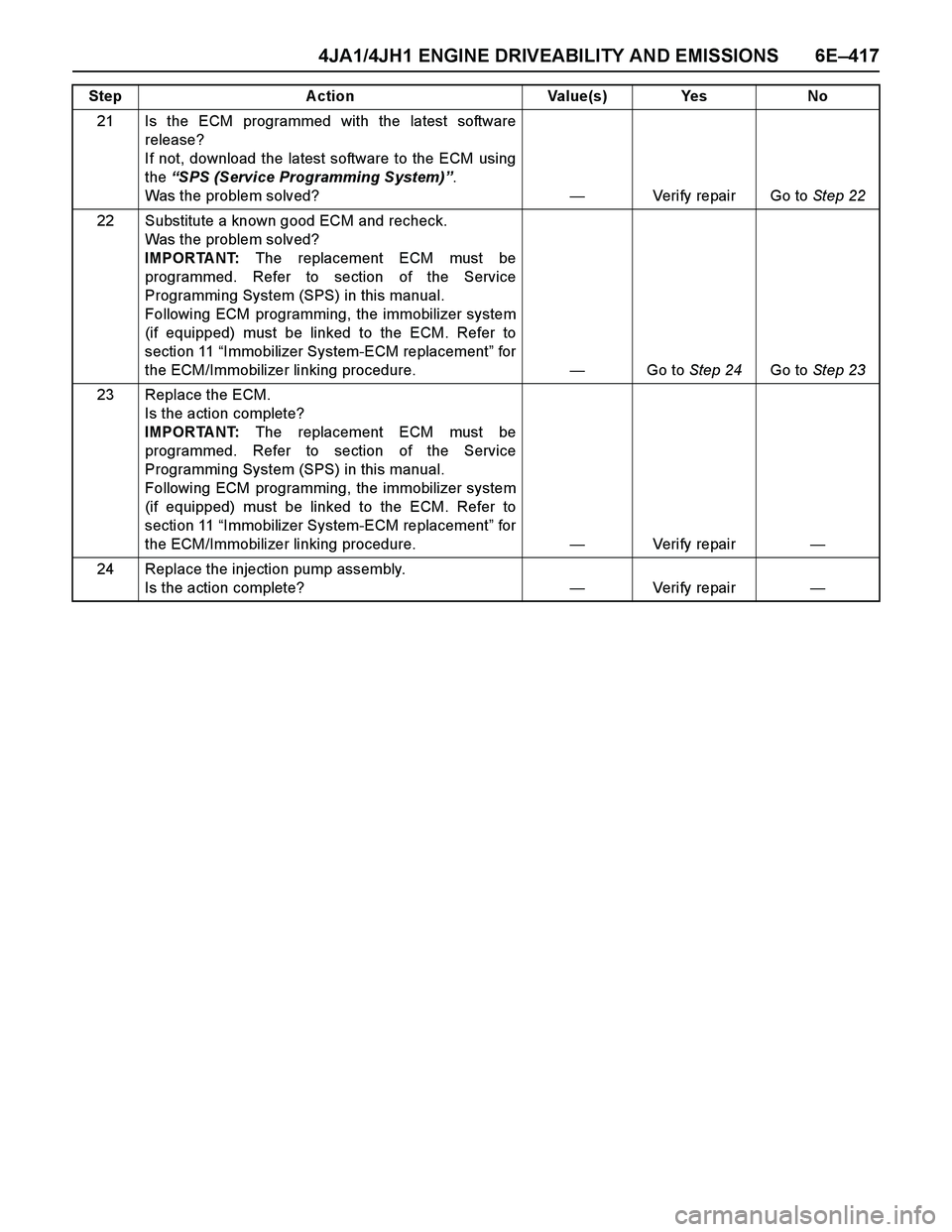
4JA1/4JH1 ENGINE DRIVEABILITY AND EMISSIONS 6E–417
21 Is the ECM programmed with the latest software
release?
If not, download the latest software to the ECM using
the “SPS (Service Programming System)”.
Was the problem solved?—Verify repair Go to Step 22
22 Substitute a known good ECM and recheck.
Was the problem solved?
IMPORTANT: The replacement ECM must be
programmed. Refer to section of the Service
Programming System (SPS) in this manual.
Following ECM programming, the immobilizer system
(if equipped) must be linked to the ECM. Refer to
section 11 “Immobilizer System-ECM replacement” for
the ECM/Immobilizer linking procedure. —Go to Step 24Go to Step 23
23 Replace the ECM.
Is the action complete?
IMPORTANT: The replacement ECM must be
programmed. Refer to section of the Service
Programming System (SPS) in this manual.
Following ECM programming, the immobilizer system
(if equipped) must be linked to the ECM. Refer to
section 11 “Immobilizer System-ECM replacement” for
the ECM/Immobilizer linking procedure.—Veri fy repai r—
24 Replace the injection pump assembly.
Is the action complete?—Veri fy repai r— Step Action Value(s) Yes No
Page 1792 of 4264

6E–420 4JA1/4JH1 ENGINE DRIVEABILITY AND EMISSIONS
MASS AIR FLOW (MAF) & INTAKE
AIR TEMPERATURE (IAT) SENSOR
Location
Installed to the intake duct housing.
Removal Procedure
1. Disconnect the negative battery cable.
2. Disconnect a MAF & IAT sensor connector from the
MAF & IAT sensor assembly.
3. Loosen the clips and remove the MAF & IAT sensor
assembly from the intake duct housing.
Installation Procedure
1. Install the MAF & IAT sensor assembly into intake
air duct.
2. Tighten the clips.
3. Connect a MAF & IAT sensor connector to the MAF
& IAT sensor assembly.
4. Connect the negative battery cable.
NOTE: Verify any DTCs (diagnosis Trouble Code) are
not stored after replacement.
THROTTLE POSITION SENSOR
(TPS)
Location
Installed on the throttle body.
Removal Procedure
1. Disconnect the negative battery cable.
2. Disconnect the TPS connector.
3. Loosen two screws and remove TPS from the
throttle body.
Installation Procedure
1. Temporary tighten the TPS by two screws.
2. Connect a TPS connectors to the TPS.
3. Connect the Tech2 to the vehicle.
4. Connect the negative battery cable.
5. Select “Data Display” with the Tech2.
6. Check the throttle position data and adjust the TPS
position.
7. Tighten two screws.
NOTE: Verify any DTCs (diagnosis Trouble Code) are
not stored after replacement.
Page 1810 of 4264
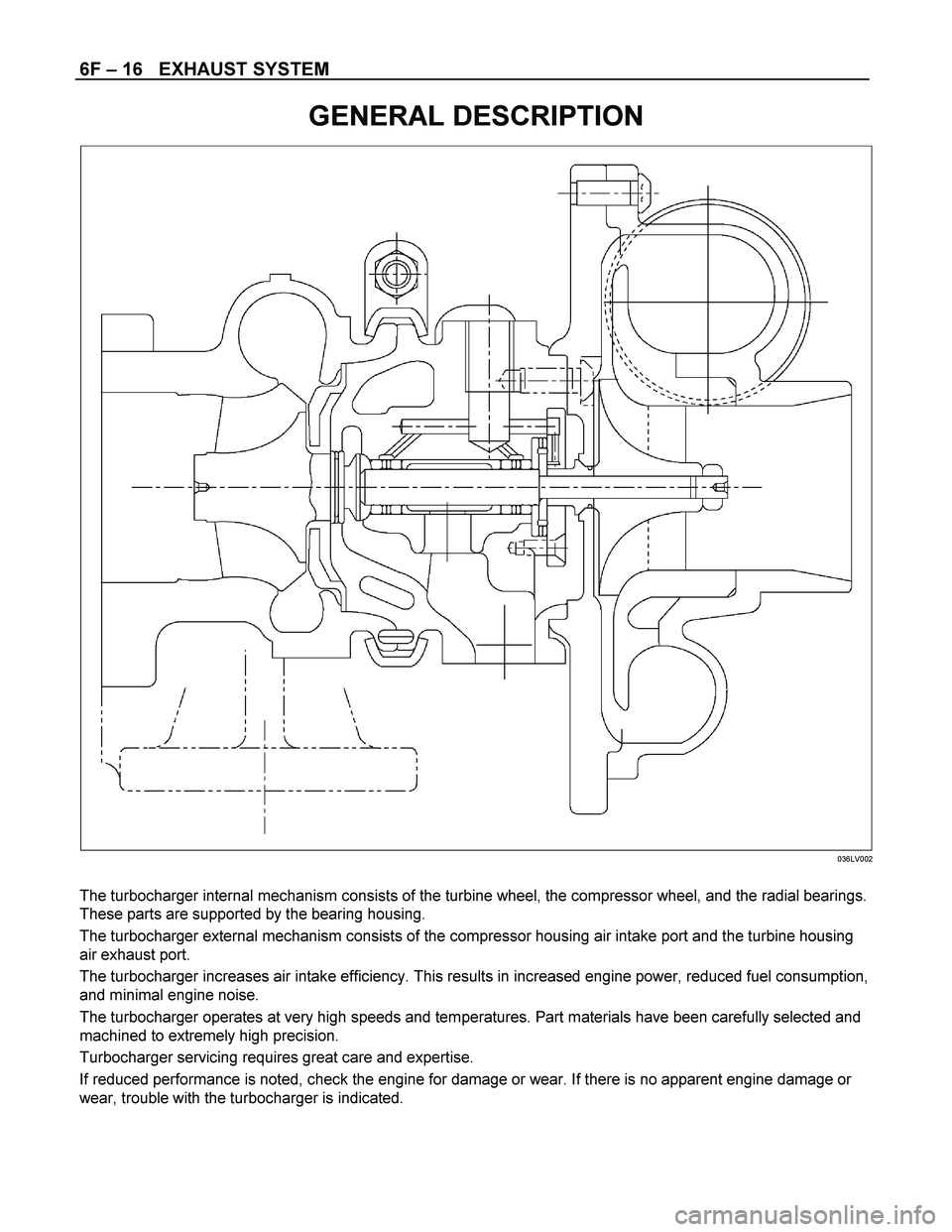
6F – 16 EXHAUST SYSTEM
GENERAL DESCRIPTION
036LV002
The turbocharger internal mechanism consists of the turbine wheel, the compressor wheel, and the radial bearings.
These parts are supported by the bearing housing.
The turbocharger external mechanism consists of the compressor housing air intake port and the turbine housing
air exhaust port.
The turbocharger increases air intake efficiency. This results in increased engine power, reduced fuel consumption,
and minimal engine noise.
The turbocharger operates at very high speeds and temperatures. Part materials have been carefully selected and
machined to extremely high precision.
Turbocharger servicing requires great care and expertise.
If reduced performance is noted, check the engine for damage or wear. If there is no apparent engine damage or
wear, trouble with the turbocharger is indicated.
Page 1811 of 4264
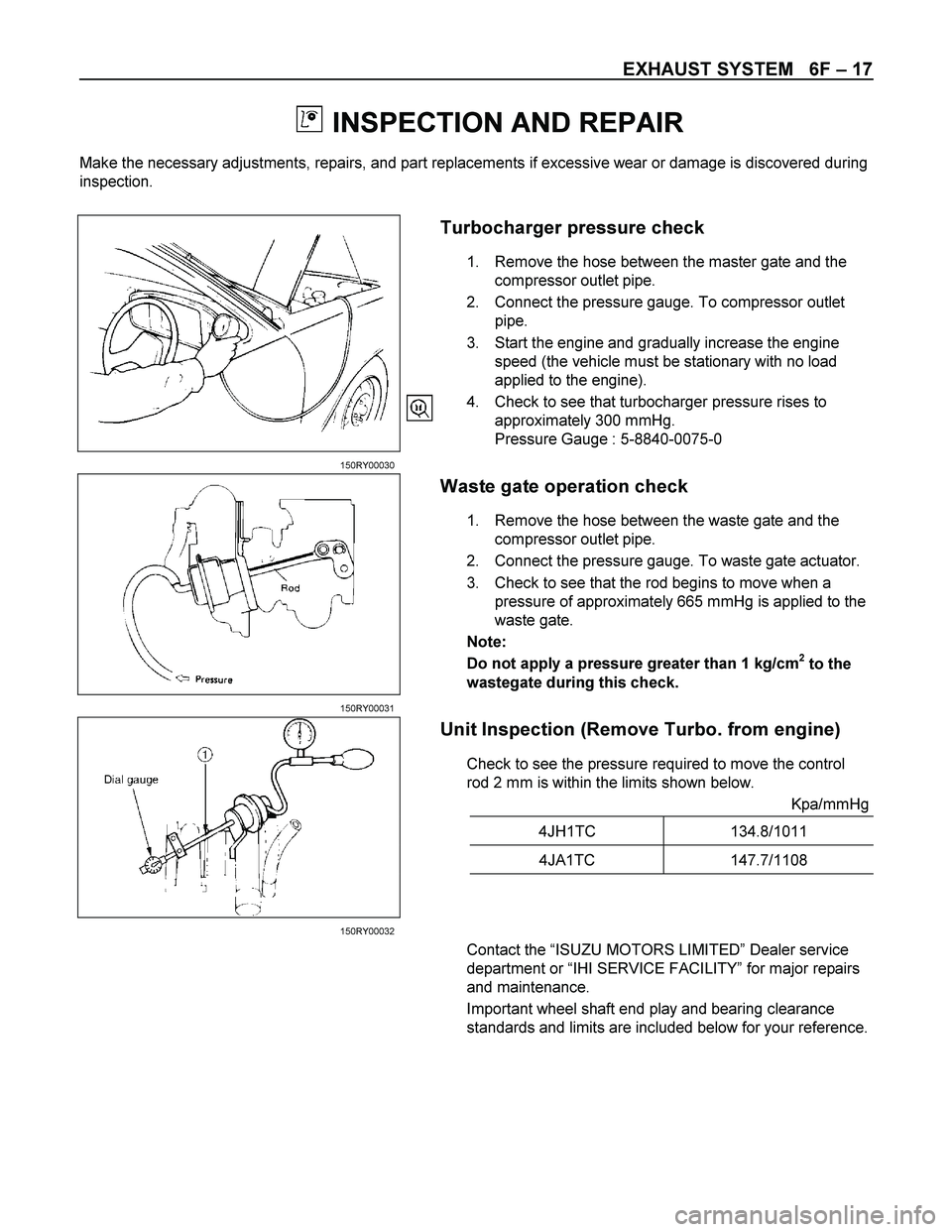
EXHAUST SYSTEM 6F – 17
INSPECTION AND REPAIR
Make the necessary adjustments, repairs, and part replacements if excessive wear or damage is discovered during
inspection.
Turbocharger pressure check
1. Remove the hose between the master gate and the
compressor outlet pipe.
2. Connect the pressure gauge. To compressor outlet
pipe.
3. Start the engine and gradually increase the engine
speed (the vehicle must be stationary with no load
applied to the engine).
4. Check to see that turbocharger pressure rises to
approximately 300 mmHg.
Pressure Gauge : 5-8840-0075-0
150RY00030
Waste gate operation check
1. Remove the hose between the waste gate and the
compressor outlet pipe.
2. Connect the pressure gauge. To waste gate actuator.
3. Check to see that the rod begins to move when a
pressure of approximately 665 mmHg is applied to the
waste gate.
Note:
Do not apply a pressure greater than 1 kg/cm
2 to the
wastegate during this check.
150RY00031
Unit Inspection (Remove Turbo. from engine)
Check to see the pressure required to move the control
rod 2 mm is within the limits shown below.
Kpa/mmHg
4JH1TC 134.8/1011
4JA1TC 147.7/1108
150RY00032
Contact the “ISUZU MOTORS LIMITED” Dealer service
department or “IHI SERVICE FACILITY” for major repairs
and maintenance.
Important wheel shaft end play and bearing clearance
standards and limits are included below for your reference.
Page 1820 of 4264
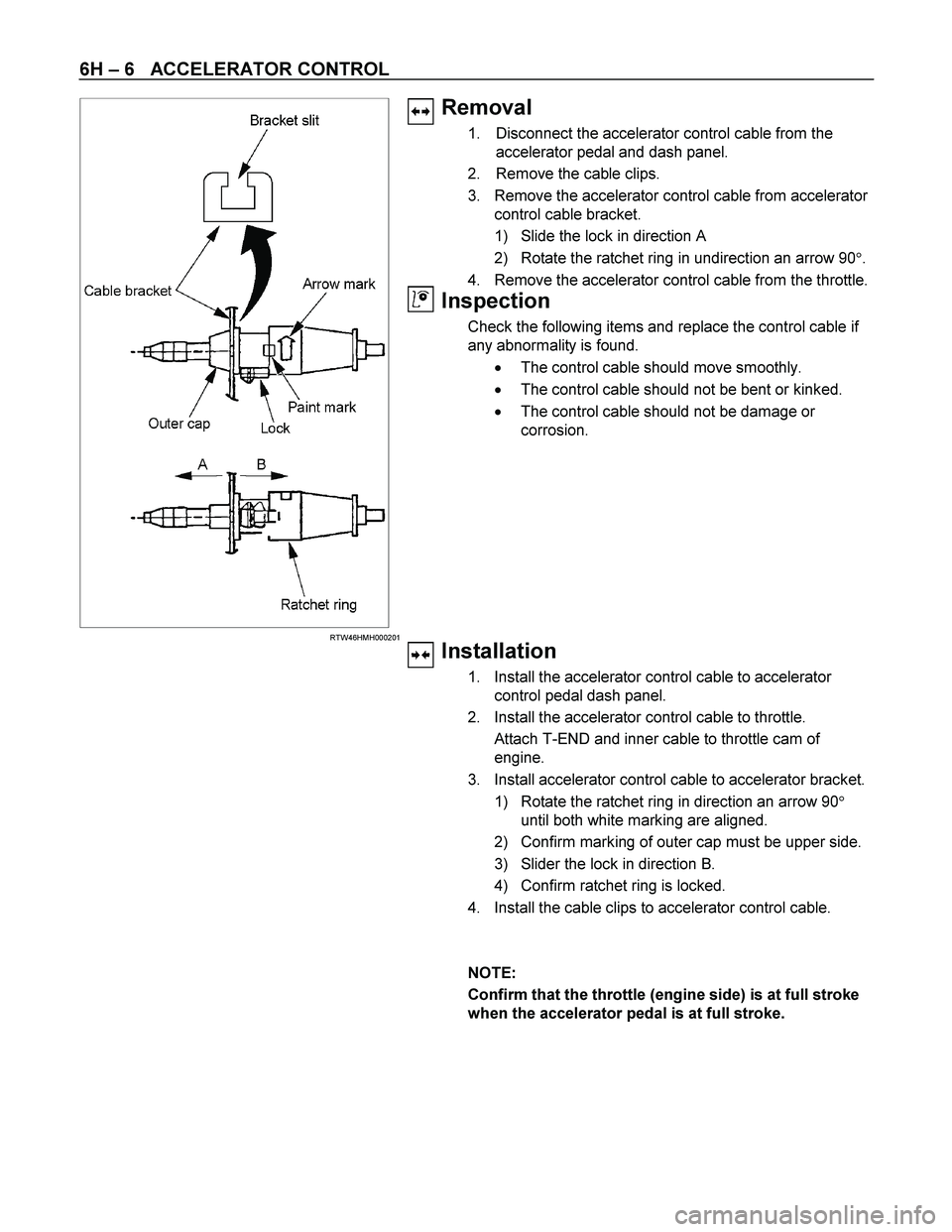
6H – 6 ACCELERATOR CONTROL
RTW46HMH000201
Removal
1. Disconnect the accelerator control cable from the
accelerator pedal and dash panel.
2. Remove the cable clips.
3. Remove the accelerator control cable from accelerator
control cable bracket.
1) Slide the lock in direction A
2) Rotate the ratchet ring in undirection an arrow 90.
4. Remove the accelerator control cable from the throttle.
Inspection
Check the following items and replace the control cable if
any abnormality is found.
The control cable should move smoothly.
The control cable should not be bent or kinked.
The control cable should not be damage or
corrosion.
Installation
1. Install the accelerator control cable to accelerator
control pedal dash panel.
2. Install the accelerator control cable to throttle.
Attach T-END and inner cable to throttle cam of
engine.
3. Install accelerator control cable to accelerator bracket.
1) Rotate the ratchet ring in direction an arrow 90
until both white marking are aligned.
2) Confirm marking of outer cap must be upper side.
3) Slider the lock in direction B.
4) Confirm ratchet ring is locked.
4. Install the cable clips to accelerator control cable.
NOTE:
Confirm that the throttle (engine side) is at full stroke
when the accelerator pedal is at full stroke.