oil ISUZU TF SERIES 2004 Workshop Manual
[x] Cancel search | Manufacturer: ISUZU, Model Year: 2004, Model line: TF SERIES, Model: ISUZU TF SERIES 2004Pages: 4264, PDF Size: 72.63 MB
Page 2848 of 4264
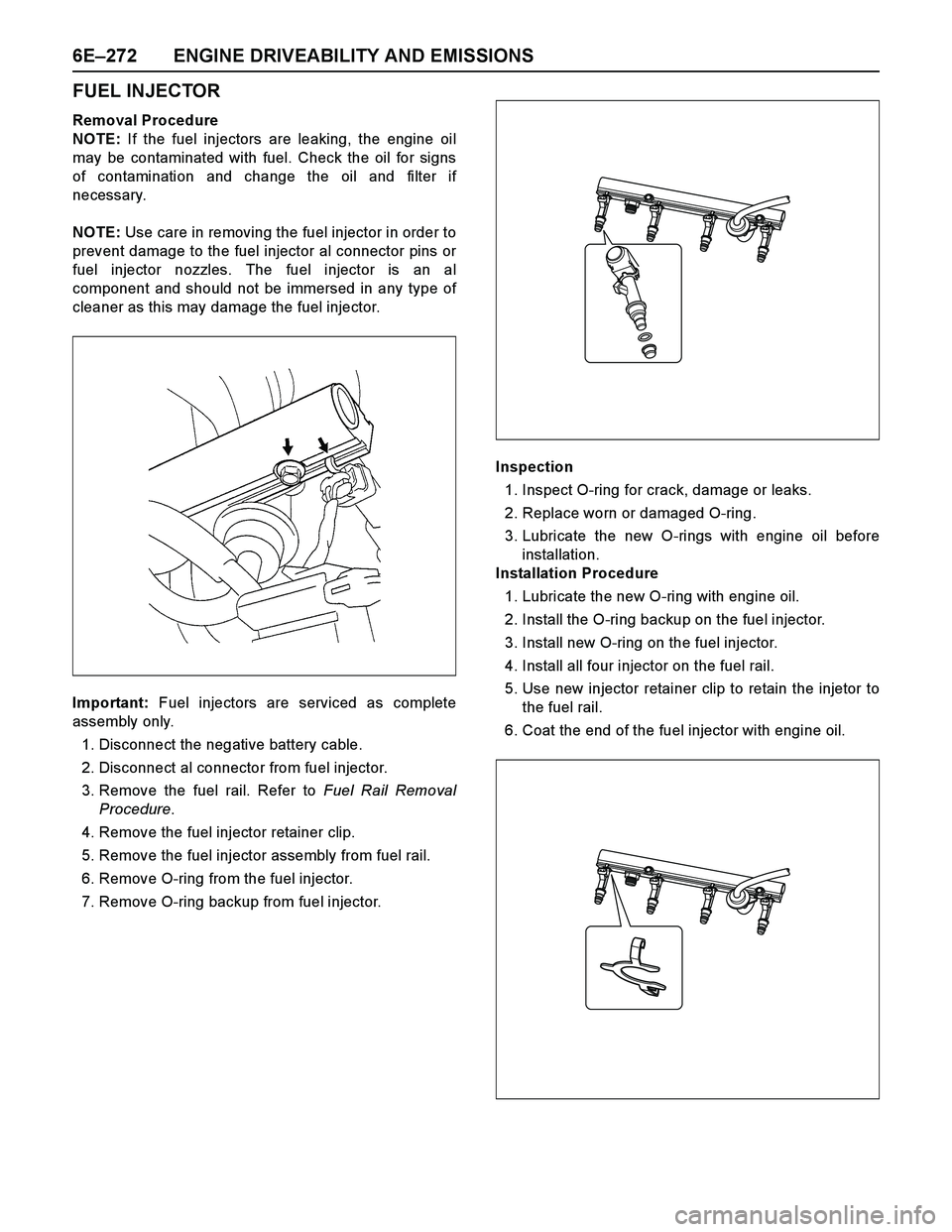
6E–272 ENGINE DRIVEABILITY AND EMISSIONS
FUEL INJECTOR
Removal Procedure
NOTE: If the fuel injectors are leaking, the engine oil
may be contaminated with fuel. Check the oil for signs
of contamination and change the oil and filter if
necessary.
NOTE: Use care in removing the fuel injector in order to
prevent damage to the fuel injector al connector pins or
fuel injector nozzles. The fuel injector is an al
component and should not be immersed in any type of
cleaner as this may damage the fuel injector.
Important: Fuel injectors are serviced as complete
assembly only.
1. Disconnect the negative battery cable.
2. Disconnect al connector from fuel injector.
3. Remove the fuel rail. Refer to Fuel Rail Removal
Procedure.
4. Remove the fuel injector retainer clip.
5. Remove the fuel injector assembly from fuel rail.
6. Remove O-ring from the fuel injector.
7. Remove O-ring backup from fuel injector.Inspection
1. Inspect O-ring for crack, damage or leaks.
2. Replace worn or damaged O-ring.
3. Lubricate the new O-rings with engine oil before
installation.
Installation Procedure
1. Lubricate the new O-ring with engine oil.
2. Install the O-ring backup on the fuel injector.
3. Install new O-ring on the fuel injector.
4. Install all four injector on the fuel rail.
5. Use new injector retainer clip to retain the injetor to
the fuel rail.
6. Coat the end of the fuel injector with engine oil.
Page 2851 of 4264
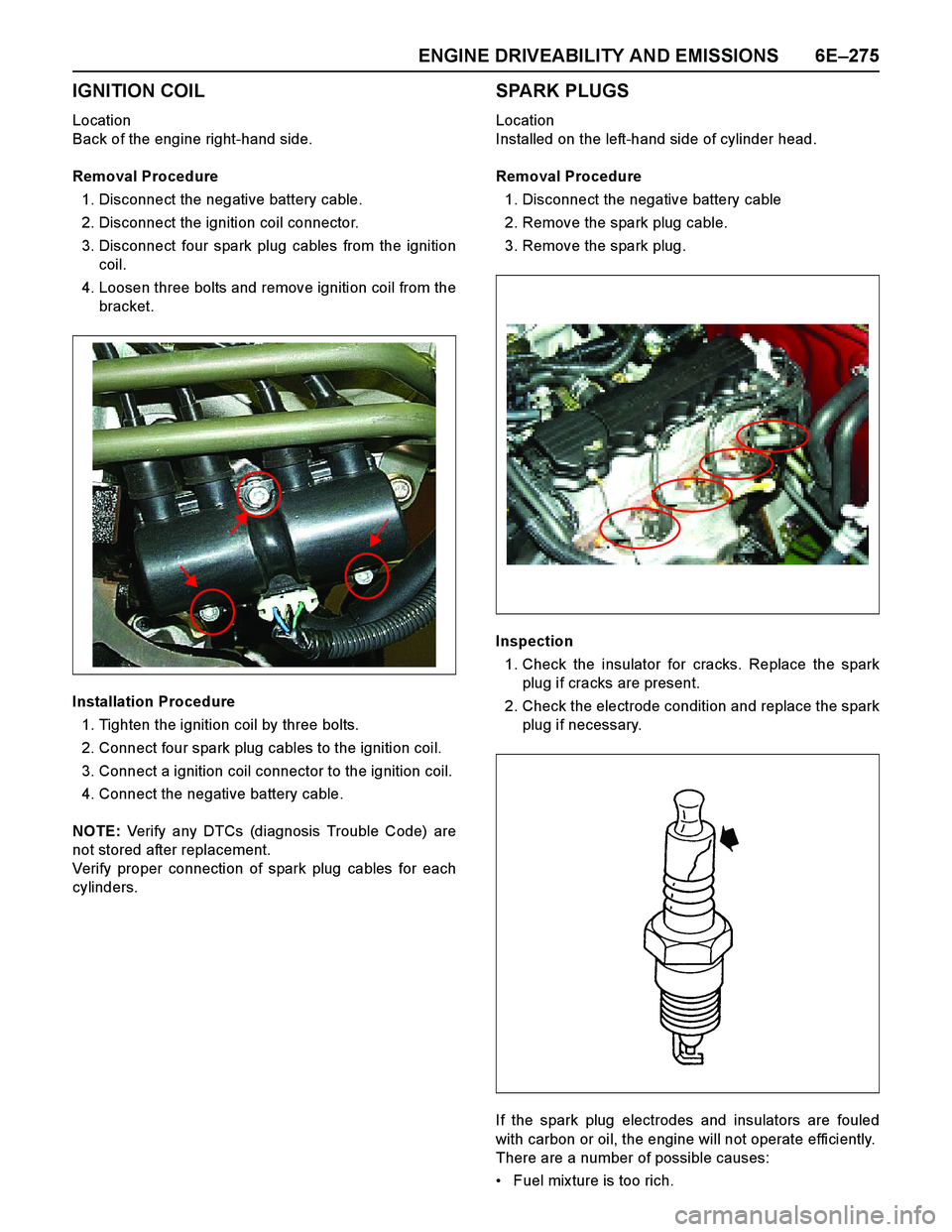
ENGINE DRIVEABILITY AND EMISSIONS 6E–275
IGNITION COIL
Location
Back of the engine right-hand side.
Removal Procedure
1. Disconnect the negative battery cable.
2. Disconnect the ignition coil connector.
3. Disconnect four spark plug cables from the ignition
coil.
4. Loosen three bolts and remove ignition coil from the
bracket.
Installation Procedure
1. Tighten the ignition coil by three bolts.
2. Connect four spark plug cables to the ignition coil.
3. Connect a ignition coil connector to the ignition coil.
4. Connect the negative battery cable.
NOTE: Verify any DTCs (diagnosis Trouble Code) are
not stored after replacement.
Verify proper connection of spark plug cables for each
cylinders.
SPARK PLUGS
Location
Installed on the left-hand side of cylinder head.
Removal Procedure
1. Disconnect the negative battery cable
2. Remove the spark plug cable.
3. Remove the spark plug.
Inspection
1. Check the insulator for cracks. Replace the spark
plug if cracks are present.
2. Check the electrode condition and replace the spark
plug if necessary.
If the spark plug electrodes and insulators are fouled
with carbon or oil, the engine will not operate efficiently.
There are a number of possible causes:
Fuel mix ture is too rich.
Page 2852 of 4264
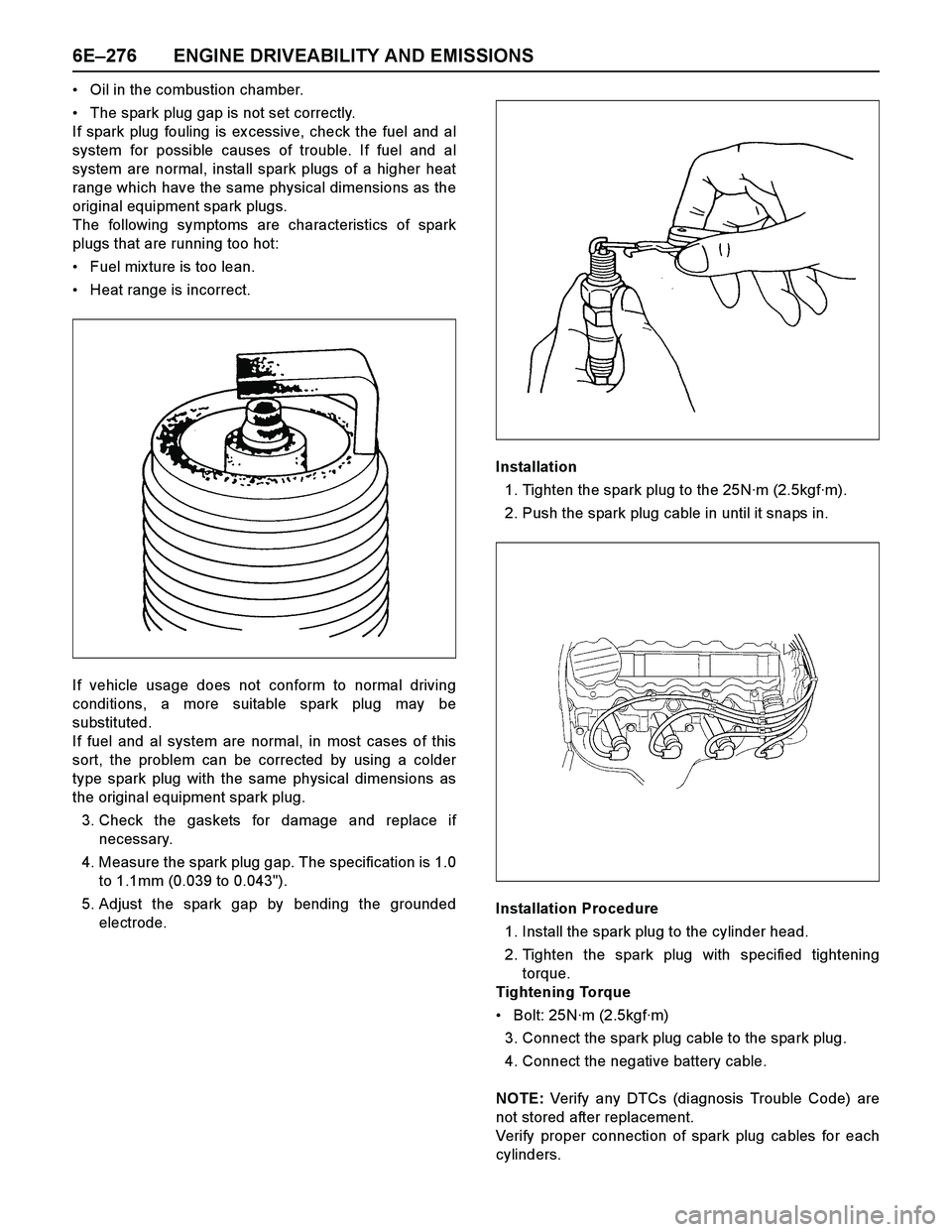
6E–276 ENGINE DRIVEABILITY AND EMISSIONS
Oil in the combustion chamber.
The spark plug gap is not set correctly.
If spark plug fouling is ex cessive, check the fuel and al
system for possible causes of trouble. If fuel and al
system are normal, install spark plugs of a higher heat
range which have the same physical dimensions as the
original equipment spark plugs.
The following symptoms are characteristics of spark
plugs that are running too hot:
Fuel mixture is too lean.
Heat range is incorrect.
If vehicle usage does not conform to normal driving
conditions, a more suitable spark plug may be
substituted.
If fuel and al system are normal, in most cases of this
sort, the problem can be corrected by using a colder
type spark plug with the same physical dimensions as
the original equipment spark plug.
3. Check the gaskets for damage and replace if
necessary.
4. Measure the spark plug gap. The specification is 1.0
to 1.1mm (0.039 to 0.043").
5. Adjust the spark gap by bending the grounded
electrode.Installation
1. Tighten the spark plug to the 25N·m (2.5kgf·m).
2. Push the spark plug cable in until it snaps in.
Installation Procedure
1. Install the spark plug to the cylinder head.
2. Tighten the spark plug with specified tightening
torque.
Tightening Torque
Bolt: 25N·m (2.5kgf·m)
3. Connect the spark plug cable to the spark plug.
4. Connect the negative battery cable.
NOTE: Verify any DTCs (diagnosis Trouble Code) are
not stored after replacement.
Verify proper connection of spark plug cables for each
cylinders.
Page 2853 of 4264
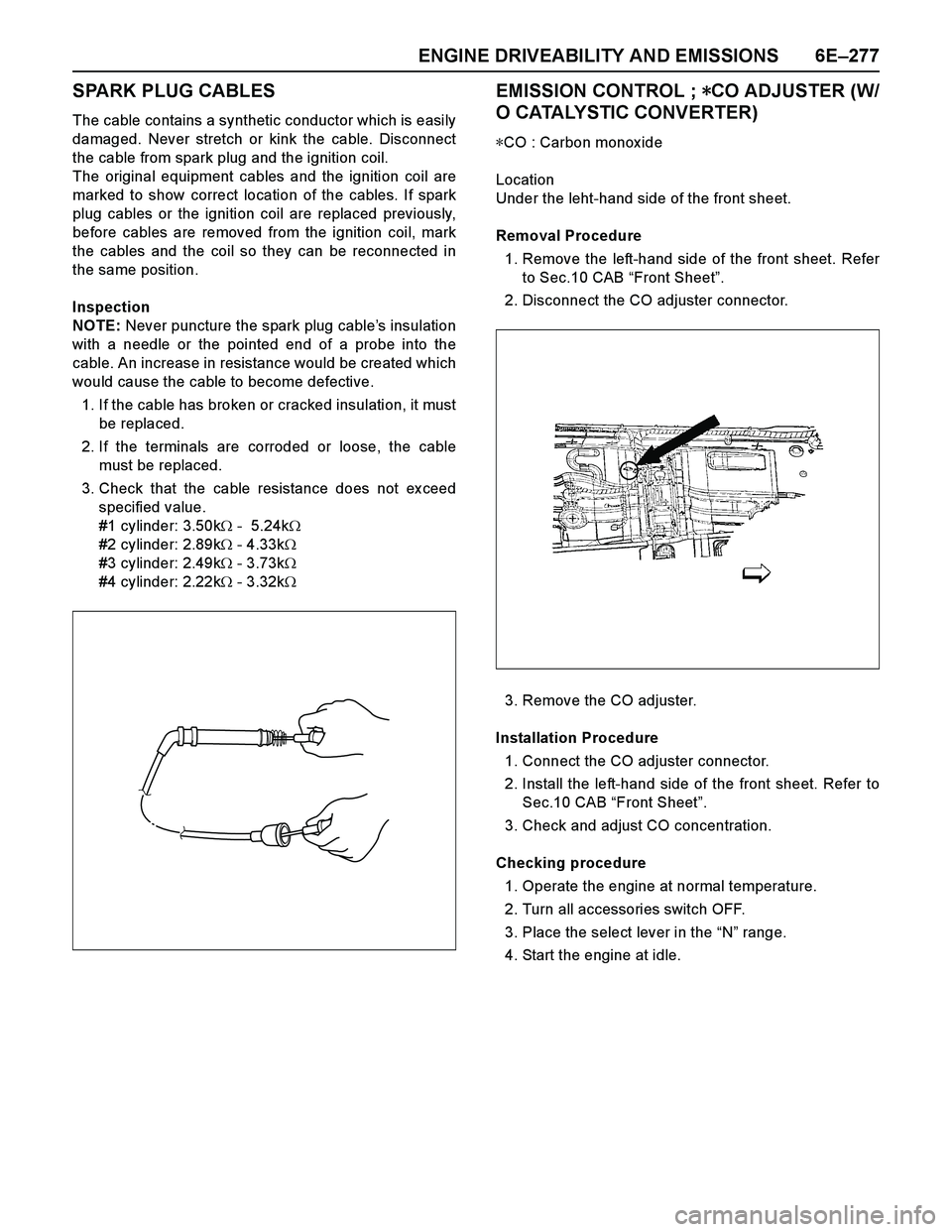
ENGINE DRIVEABILITY AND EMISSIONS 6E–277
SPARK PLUG CABLES
The cable contains a synthetic conductor which is easily
damaged. Never stretch or kink the cable. Disconnect
the cable from spark plug and the ignition coil.
The original equipment cables and the ignition coil are
marked to show correct location of the cables. If spark
plug cables or the ignition coil are replaced previously,
before cables are removed from the ignition coil, mark
the cables and the coil so they can be reconnected in
the same position.
Inspection
NOTE: Never puncture the spark plug cable’s insulation
with a needle or the pointed end of a probe into the
cable. An increase in resistance would be created which
would cause the cable to become defective.
1. If the cable has broken or cracked insulation, it must
be replaced.
2. If the terminals are corroded or loose, the cable
must be replaced.
3. Check that the cable resistance does not ex ceed
specified value.
#1 cylinder: 3.50k - 5.24k
#2 cylinder: 2.89k - 4.33k
#3 cylinder: 2.49k - 3.73k
#4 cylinder: 2.22k - 3.32k
EMISSION CONTROL ;
CO ADJUSTER (W/
O CATALYSTIC CONVERTER)
CO : Carbon monox ide
Location
Under the leht-hand side of the front sheet.
Removal Procedure
1. Remove the left-hand side of the front sheet. Refer
to Sec.10 CAB “Front Sheet”.
2. Disconnect the CO adjuster connector.
3. Remove the CO adjuster.
Installation Procedure
1. Connect the CO adjuster connector.
2. Install the left-hand side of the front sheet. Refer to
Sec.10 CAB “Front Sheet”.
3. Check and adjust CO concentration.
Checking procedure
1. Operate the engine at normal temperature.
2. Turn all accessories switch OFF.
3. Place the select lever in the “N” range.
4. Start the engine at idle.
Page 2873 of 4264
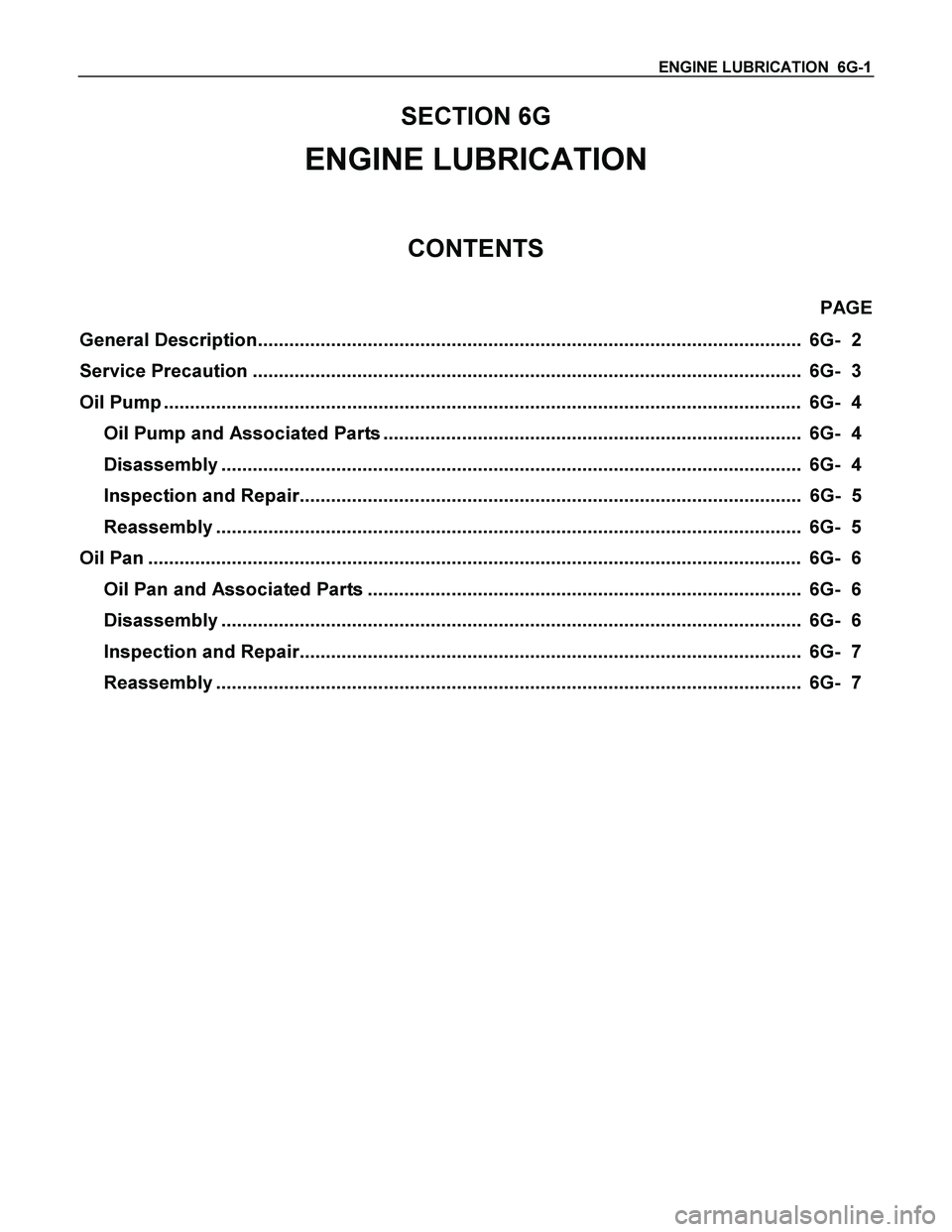
ENGINE LUBRICATION 6G-1
SECTION 6G
ENGINE LUBRICATION
CONTENTS
PAGE
General Description........................................................................................................ 6G- 2
Service Precaution ......................................................................................................... 6G- 3
Oil Pump .......................................................................................................................... 6G- 4
Oil Pump and Associated Parts ................................................................................ 6G- 4
Disassembly ............................................................................................................... 6G- 4
Inspection and Repair................................................................................................ 6G- 5
Reassembly ................................................................................................................ 6G- 5
Oil Pan ............................................................................................................................. 6G- 6
Oil Pan and Associated Parts ................................................................................... 6G- 6
Disassembly ............................................................................................................... 6G- 6
Inspection and Repair................................................................................................ 6G- 7
Reassembly ................................................................................................................ 6G- 7
Page 2874 of 4264
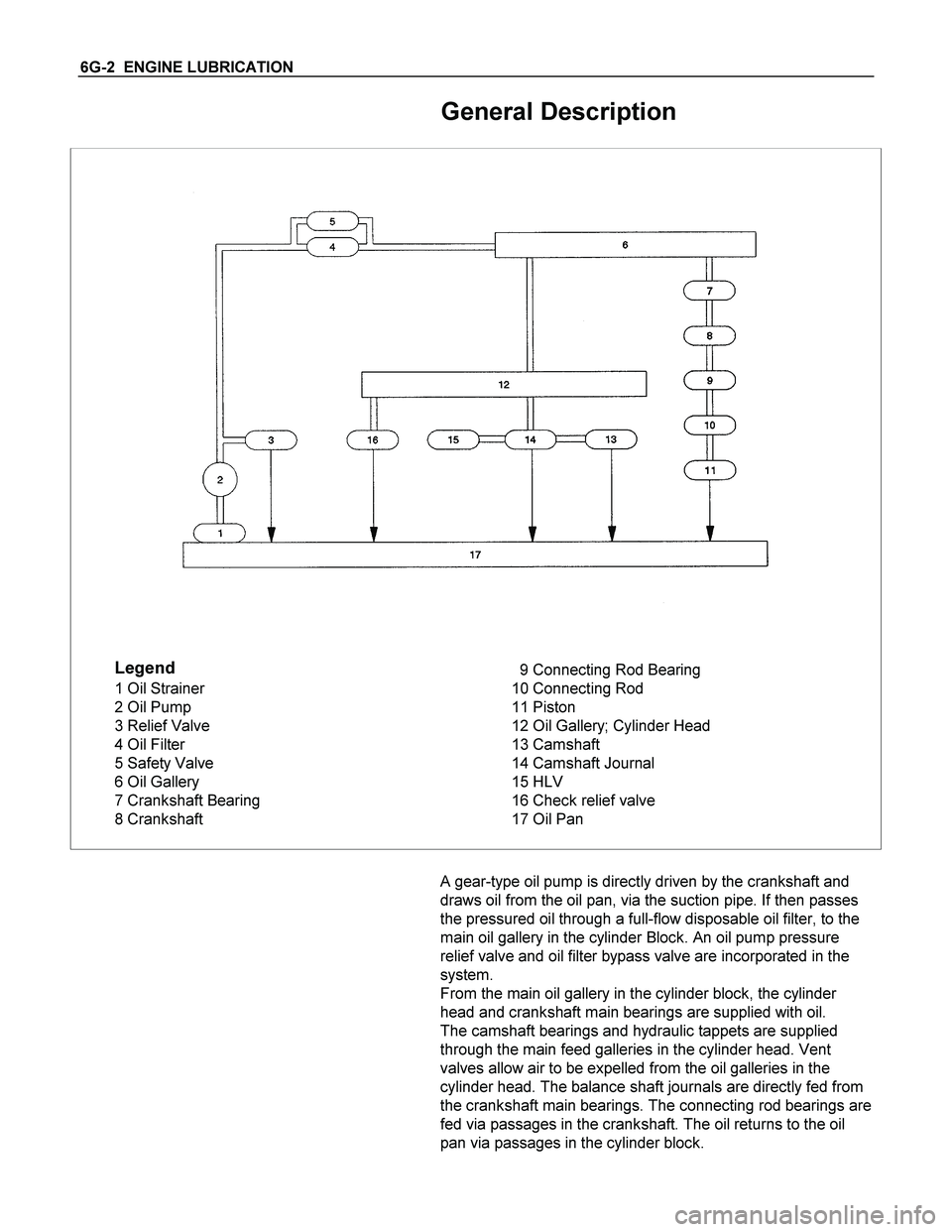
6G-2 ENGINE LUBRICATION
General Description
Legend
1 Oil Strainer
2 Oil Pump
3 Relief Valve
4 Oil Filter
5 Safety Valve
6 Oil Gallery
7 Crankshaft Bearing
8 Crankshaft9 Connecting Rod Bearing
10 Connecting Rod
11 Piston
12 Oil Gallery; Cylinder Head
13 Camshaft
14 Camshaft Journal
15 HLV
16 Check relief valve
17 Oil Pan
A gear-type oil pump is directly driven by the crankshaft and
draws oil from the oil pan, via the suction pipe. If then passes
the pressured oil through a full-flow disposable oil filter, to the
main oil gallery in the cylinder Block. An oil pump pressure
relief valve and oil filter bypass valve are incorporated in the
system.
From the main oil gallery in the cylinder block, the cylinder
head and crankshaft main bearings are supplied with oil.
The camshaft bearings and hydraulic tappets are supplied
through the main feed galleries in the cylinder head. Vent
valves allow air to be expelled from the oil galleries in the
cylinder head. The balance shaft journals are directly fed from
the crankshaft main bearings. The connecting rod bearings are
fed via passages in the crankshaft. The oil returns to the oil
pan via passages in the cylinder block.
Page 2876 of 4264
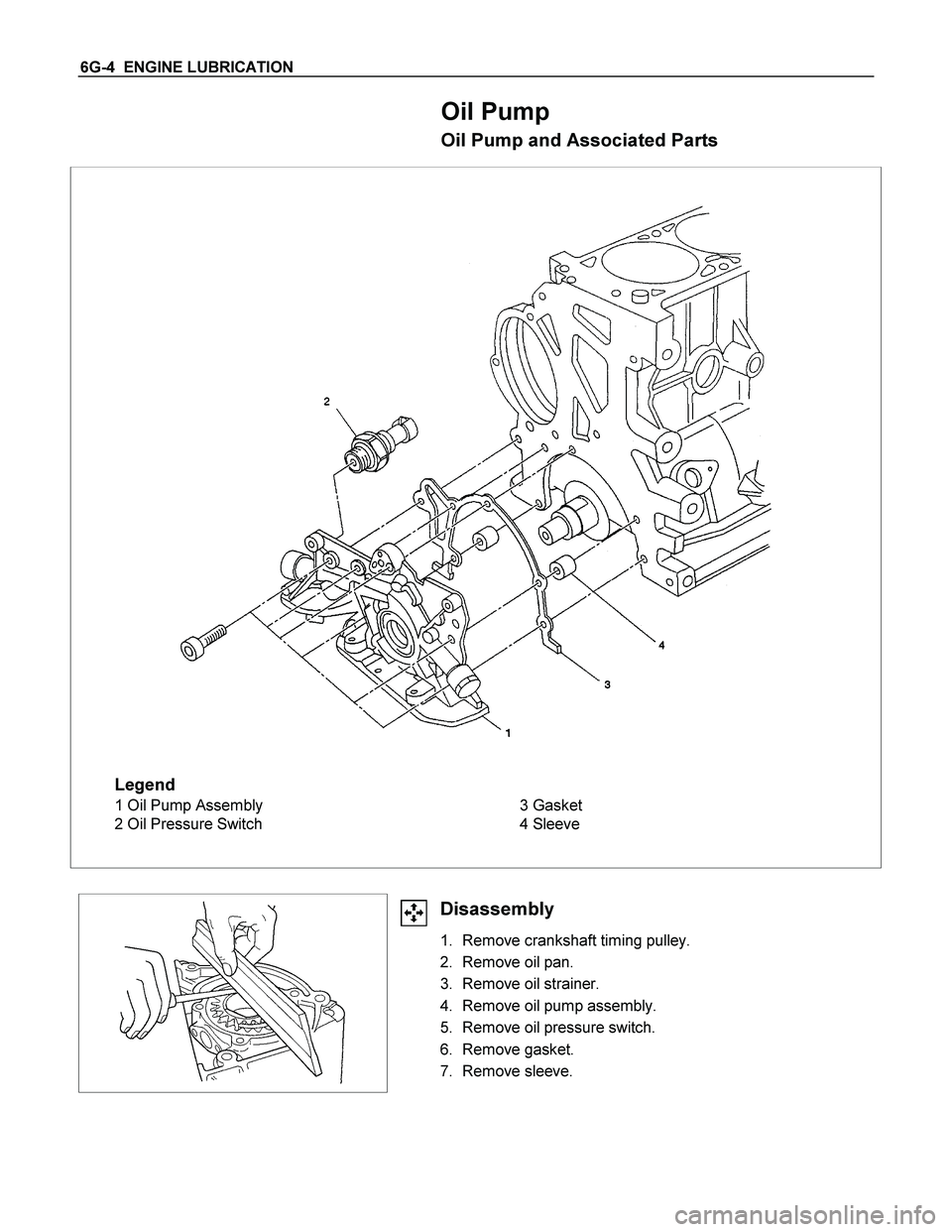
6G-4 ENGINE LUBRICATION
Oil Pump
Oil Pump and Associated Parts
Legend
1 Oil Pump Assembly
2 Oil Pressure Switch3 Gasket
4 Sleeve
Disassembly
1. Remove crankshaft timing pulley.
2. Remove oil pan.
3. Remove oil strainer.
4. Remove oil pump assembly.
5. Remove oil pressure switch.
6. Remove gasket.
7. Remove sleeve.
Page 2877 of 4264
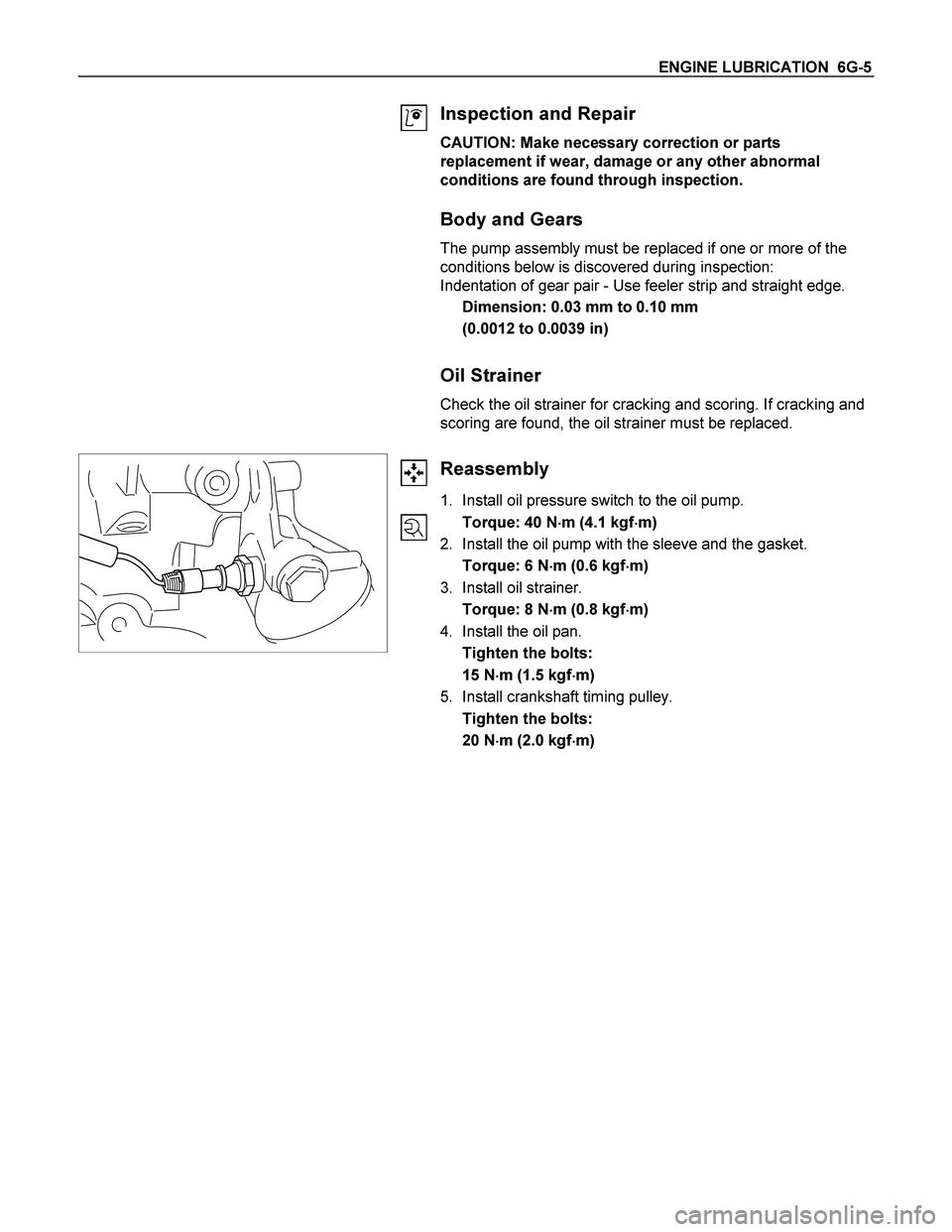
ENGINE LUBRICATION 6G-5
Inspection and Repair
CAUTION: Make necessary correction or parts
replacement if wear, damage or any other abnormal
conditions are found through inspection.
Body and Gears
The pump assembly must be replaced if one or more of the
conditions below is discovered during inspection:
Indentation of gear pair - Use feeler strip and straight edge.
Dimension: 0.03 mm to 0.10 mm
(0.0012 to 0.0039 in)
Oil Strainer
Check the oil strainer for cracking and scoring. If cracking and
scoring are found, the oil strainer must be replaced.
Reassembly
1. Install oil pressure switch to the oil pump.
Torque: 40 N
m (4.1 kgf
m)
2. Install the oil pump with the sleeve and the gasket.
Torque: 6 N
m (0.6 kgf
m)
3. Install oil strainer.
Torque: 8 N
m (0.8 kgf
m)
4. Install the oil pan.
Tighten the bolts:
15 N
m (1.5 kgf
m)
5. Install crankshaft timing pulley.
Tighten the bolts:
20 N
m (2.0 kgf
m)
Page 2878 of 4264
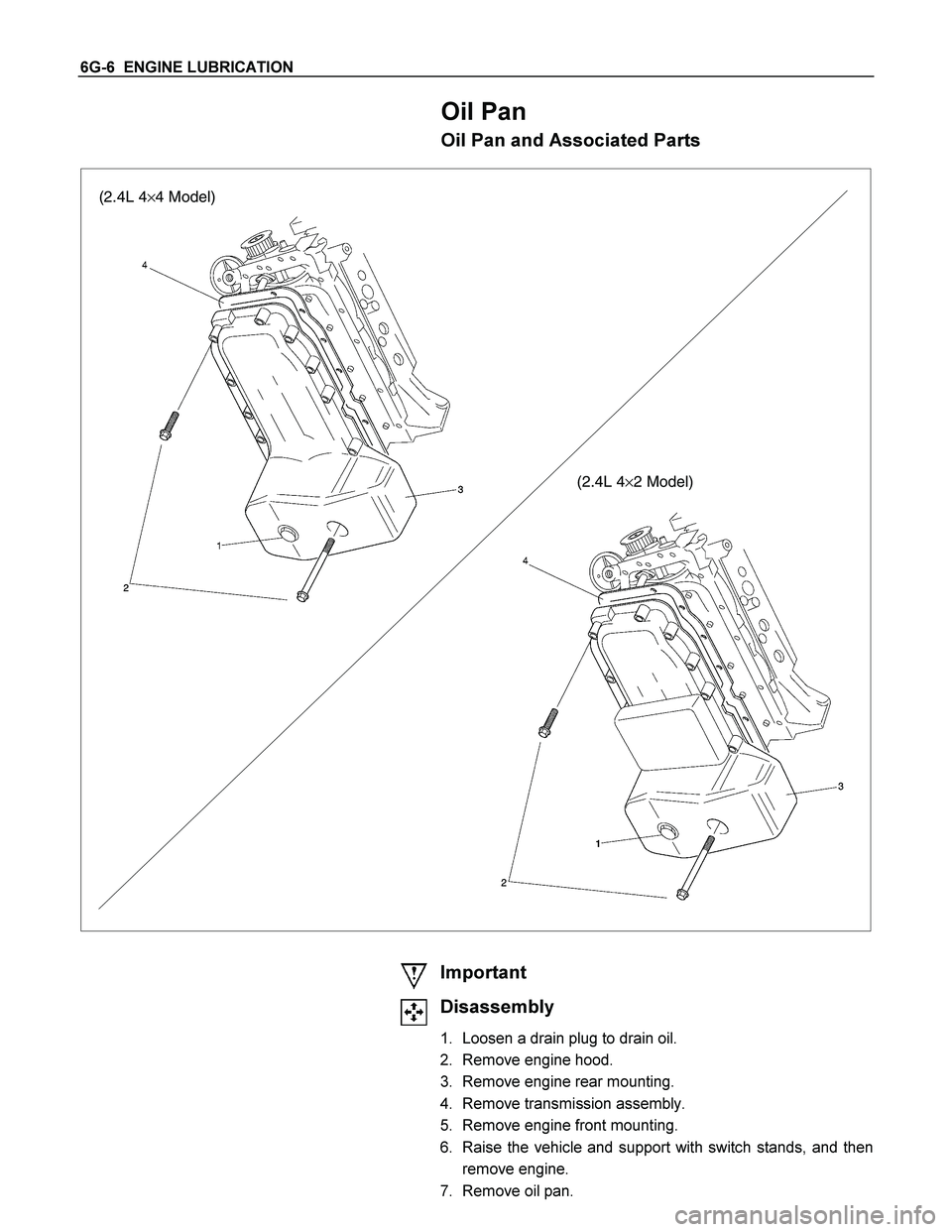
6G-6 ENGINE LUBRICATION
Oil Pan
Oil Pan and Associated Parts
(2.4L 4 ×4 Model)
(2.4L 4 ×2 Model)
Important
Disassembly
1. Loosen a drain plug to drain oil.
2. Remove engine hood.
3. Remove engine rear mounting.
4. Remove transmission assembly.
5. Remove engine front mounting.
6. Raise the vehicle and support with switch stands, and then remove engine.
7. Remove oil pan.
Page 2879 of 4264

ENGINE LUBRICATION 6G-7
Inspection and Repair
CAUTION: Make necessary correction or parts replacement if wear, damage or any other
abnormal conditions are found through
inspection.
Reassembly
To install, follows the disassembly steps in the reverse order.
Important
Sealer - Apply silicon into groove in oil pan lugs prior to fitment of oil pan to block, remove excess sealer after oil pan
is bolted to block.
(2.4L 4 ×4 Model)
4
3
1
2
(2.4L 4 ×2 Model)
4
3
1
2
Torque
Bolts - Tighten bolts to the specified torque.
Torque : 20 N m (2.0 kgf m)
Engine oil - Refill engine oil to the oil pan. (Lit)
Replacement Oil Fill Volume 2.4L
Without filter change 4.00
With filter change 4.25