ignition ISUZU TF SERIES 2004 Workshop Manual
[x] Cancel search | Manufacturer: ISUZU, Model Year: 2004, Model line: TF SERIES, Model: ISUZU TF SERIES 2004Pages: 4264, PDF Size: 72.63 MB
Page 2672 of 4264
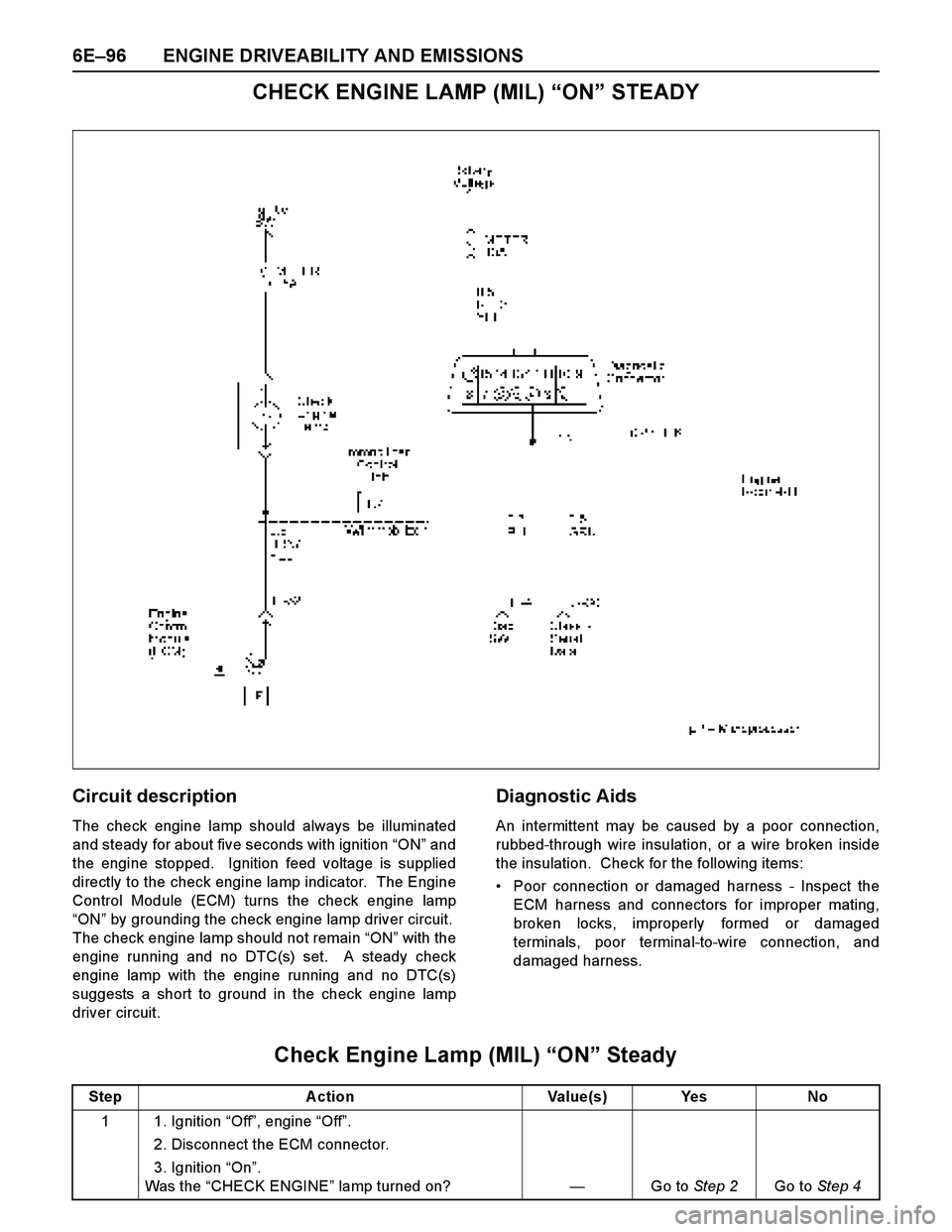
6E–96 ENGINE DRIVEABILITY AND EMISSIONS
CHECK ENGINE LAMP (MIL) “ON” STEADY
Circuit description
The check engine lamp should always be illuminated
and steady for about five seconds with ignition “ON” and
the engine stopped. Ignition feed voltage is supplied
directly to the check engine lamp indicator. The Engine
Control Module (ECM) turns the check engine lamp
“ON” by grounding the check engine lamp driver circuit.
The check engine lamp should not remain “ON” with the
engine running and no DTC(s) set. A steady check
engine lamp with the engine running and no DTC(s)
suggests a short to ground in the check engine lamp
driver circuit.
Diagnostic Aids
An intermittent may be caused by a poor connection,
rubbed-through wire insulation, or a wire broken inside
the insulation. Check for the following items:
Poor connection or damaged harness - Inspect the
ECM harness and connectors for improper mating,
broken locks, improperly formed or damaged
terminals, poor terminal-to-wire connection, and
damaged harness.
Check Engine Lamp (MIL) “ON” Steady
Step Action Value(s) Yes No
1 1. Ignition “Off”, engine “Off”.
2. Disconnect the ECM connector.
3. Ignition “On”.
Was the “CHECK ENGINE” lamp turned on?—Go to Step 2Go to Step 4
Page 2673 of 4264
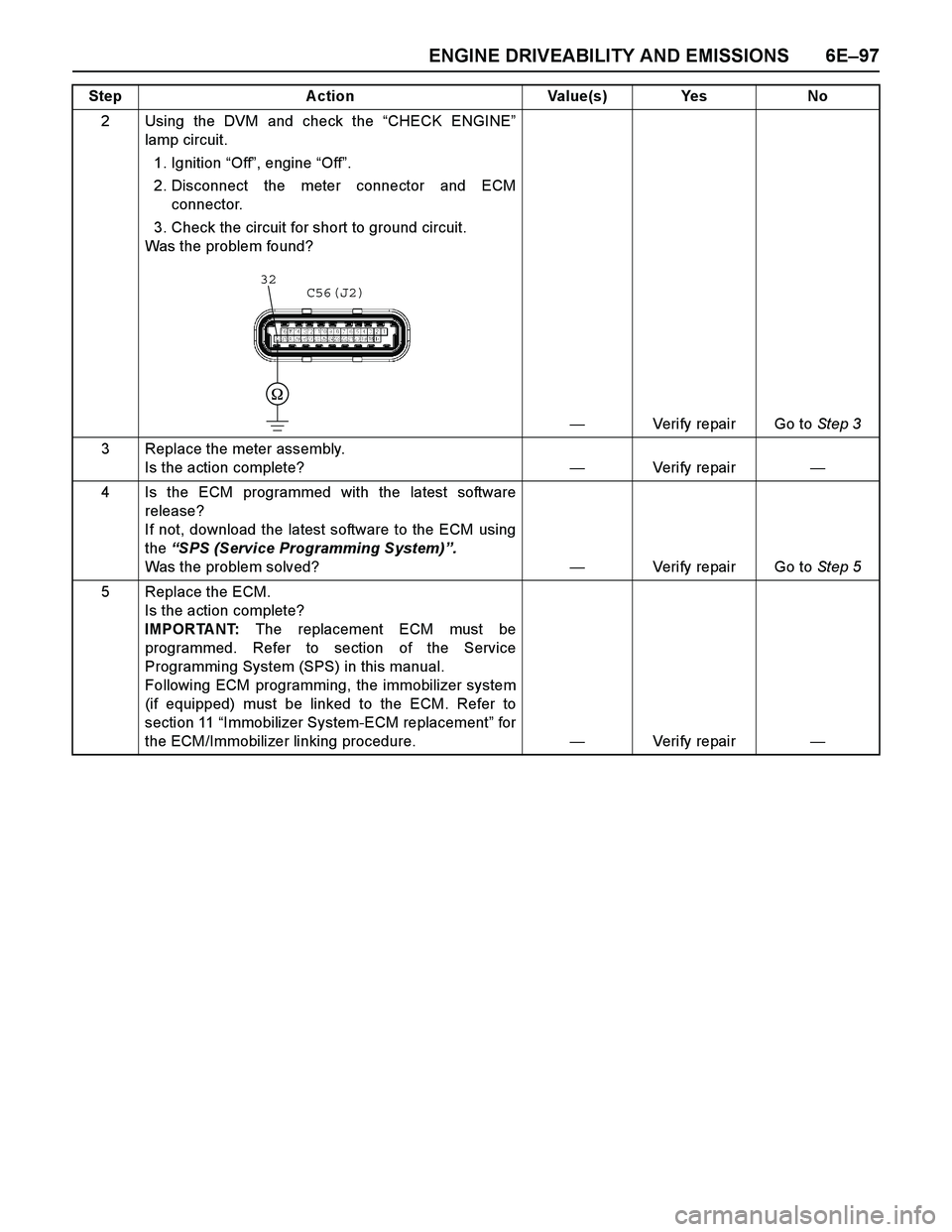
ENGINE DRIVEABILITY AND EMISSIONS 6E–97
2 Using the DVM and check the “CHECK ENGINE”
lamp circuit.
1. Ignition “Off”, engine “Off”.
2. Disconnect the meter connector and ECM
connector.
3. Check the circuit for short to ground circuit.
Was the problem found?
—Verify repair Go to Step 3
3 Replace the meter assembly.
Is the action complete?—Veri fy repai r—
4 Is the ECM programmed with the latest software
release?
If not, download the latest software to the ECM using
the “SPS (Service Programming System)”.
Was the problem solved?—Verify repair Go to Step 5
5 Replace the ECM.
Is the action complete?
IMPORTANT: The replacement ECM must be
programmed. Refer to section of the Service
Programming System (SPS) in this manual.
Following ECM programming, the immobilizer system
(if equipped) must be linked to the ECM. Refer to
section 11 “Immobilizer System-ECM replacement” for
the ECM/Immobilizer linking procedure.—Veri fy repai r— Step Action Value(s) Yes No
32C56(J2)
Page 2674 of 4264
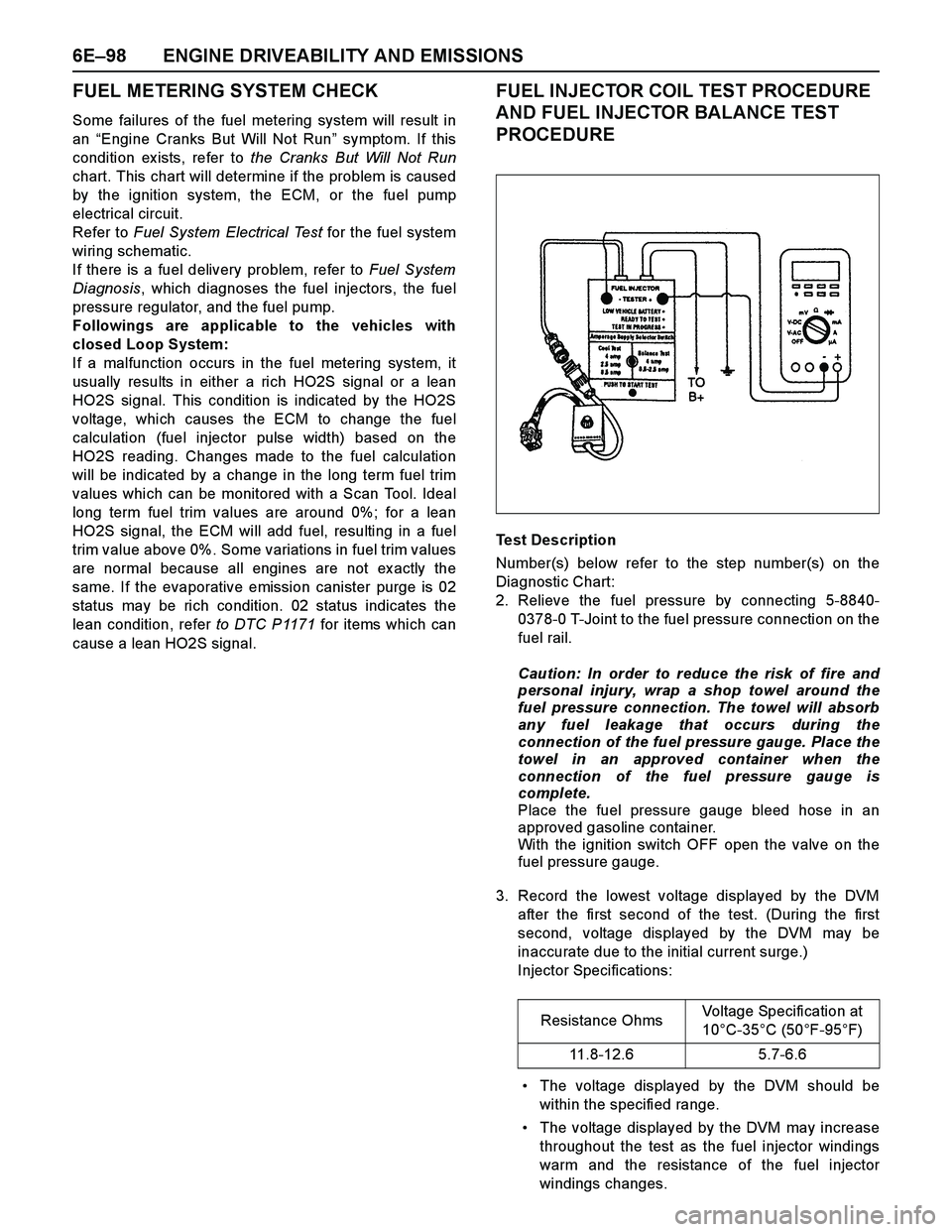
6E–98 ENGINE DRIVEABILITY AND EMISSIONS
FUEL METERING SYSTEM CHECK
Some failures of the fuel metering system will result in
an “Engine Cranks But Will Not Run” symptom. If this
condition ex ists, refer to the Cranks But Will Not Run
chart. This chart will determine if the problem is caused
by the ignition system, the ECM, or the fuel pump
electrical circuit.
Refer to Fuel System Electrical Test for the fuel system
wiring schematic.
If there is a fuel delivery problem, refer to Fuel System
Diagnosis, which diagnoses the fuel injectors, the fuel
pressure regulator, and the fuel pump.
Followings are applicable to the vehicles with
closed Loop System:
If a malfunction occurs in the fuel metering system, it
usually results in either a rich HO2S signal or a lean
HO2S signal. This condition is indicated by the HO2S
voltage, which causes the ECM to change the fuel
calculation (fuel injector pulse width) based on the
HO2S reading. Changes made to the fuel calculation
will be indicated by a change in the long term fuel trim
values which can be monitored with a Scan Tool. Ideal
long term fuel trim values are around 0%; for a lean
HO2S signal, the ECM will add fuel, resulting in a fuel
trim value above 0%. Some variations in fuel trim values
are normal because all engines are not ex actly the
same. If the evaporative emission canister purge is 02
status may be rich condition. 02 status indicates the
lean condition, refer to DTC P1171 for items which can
cause a lean HO2S signal.
FUEL INJECTOR COIL TEST PROCEDURE
AND FUEL INJECTOR BALANCE TEST
PROCEDURE
Test Description
Number(s) below refer to the step number(s) on the
Diagnostic Chart:
2. Relieve the fuel pressure by connecting 5-8840-
0378-0 T-Joint to the fuel pressure connection on the
fuel rail.
Caution: In order to reduce the risk of fire and
personal injury, wrap a shop towel around the
fuel pressure connection. The towel will absorb
any fuel leakage that occurs during the
connection of the fuel pressure gauge. Place the
towel in an approved container when the
connection of the fuel pressure gauge is
complete.
Place the fuel pressure gauge bleed hose in an
approved gasoline container.
With the ignition switch OFF open the valve on the
fuel pressure gauge.
3. Record the lowest voltage displayed by the DVM
after the first second of the test. (During the first
second, voltage displayed by the DVM may be
inaccurate due to the initial current surge.)
Injector Specifications:
The voltage displayed by the DVM should be
within the specified range.
The voltage displayed by the DVM may increase
throughout the test as the fuel injector windings
warm and the resistance of the fuel injector
windings changes.Resistance OhmsVoltage Specification at
10°C-35°C (50°F-95°F)
11.8-12.6 5.7-6.6
Page 2679 of 4264
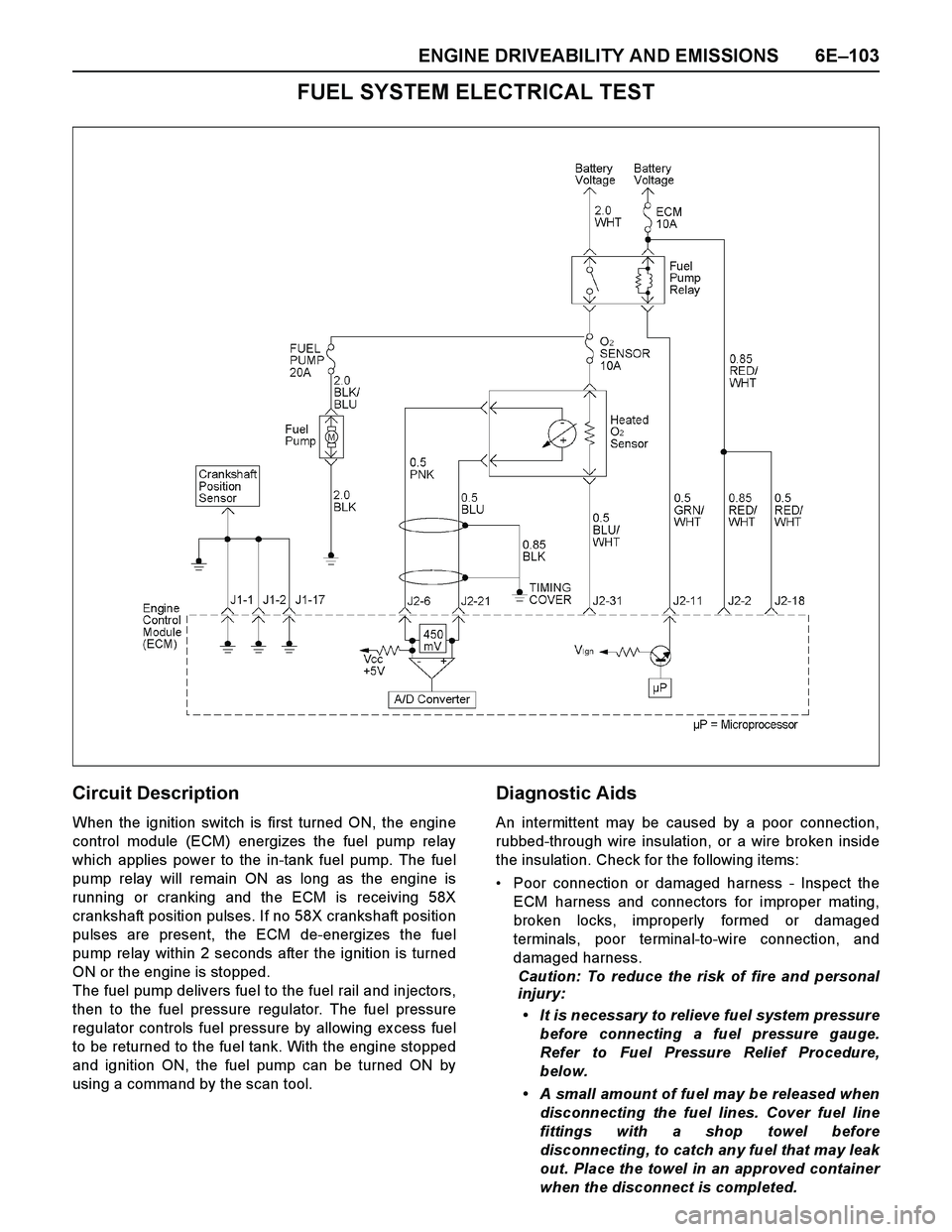
ENGINE DRIVEABILITY AND EMISSIONS 6E–103
FUEL SYSTEM ELECTRICAL TEST
Circuit Description
When the ignition switch is first turned ON, the engine
control module (ECM) energizes the fuel pump relay
which applies power to the in-tank fuel pump. The fuel
pump relay will remain ON as long as the engine is
running or cranking and the ECM is receiving 58X
crankshaft position pulses. If no 58X crankshaft position
pulses are present, the ECM de-energizes the fuel
pump relay within 2 seconds after the ignition is turned
ON or the engine is stopped.
The fuel pump delivers fuel to the fuel rail and injectors,
then to the fuel pressure regulator. The fuel pressure
regulator controls fuel pressure by allowing ex cess fuel
to be returned to the fuel tank. With the engine stopped
and ignition ON, the fuel pump can be turned ON by
using a command by the scan tool.
Diagnostic Aids
An intermittent may be caused by a poor connection,
rubbed-through wire insulation, or a wire broken inside
the insulation. Check for the following items:
Poor connection or damaged harness - Inspect the
ECM harness and connectors for improper mating,
broken locks, improperly formed or damaged
terminals, poor terminal-to-wire connection, and
damaged harness.
Caution: To reduce the risk of fire and personal
injury:
It is necessary to relieve fuel system pressure
before connecting a fuel pressure gauge.
Refer to Fuel Pressure Relief Procedure,
below.
A small amount of fuel may be released when
disconnecting the fuel lines. Cover fuel line
fittings with a shop towel before
disconnecting, to catch any fuel that may leak
out. Place the towel in an approved container
when the disconnect is completed.
Page 2680 of 4264
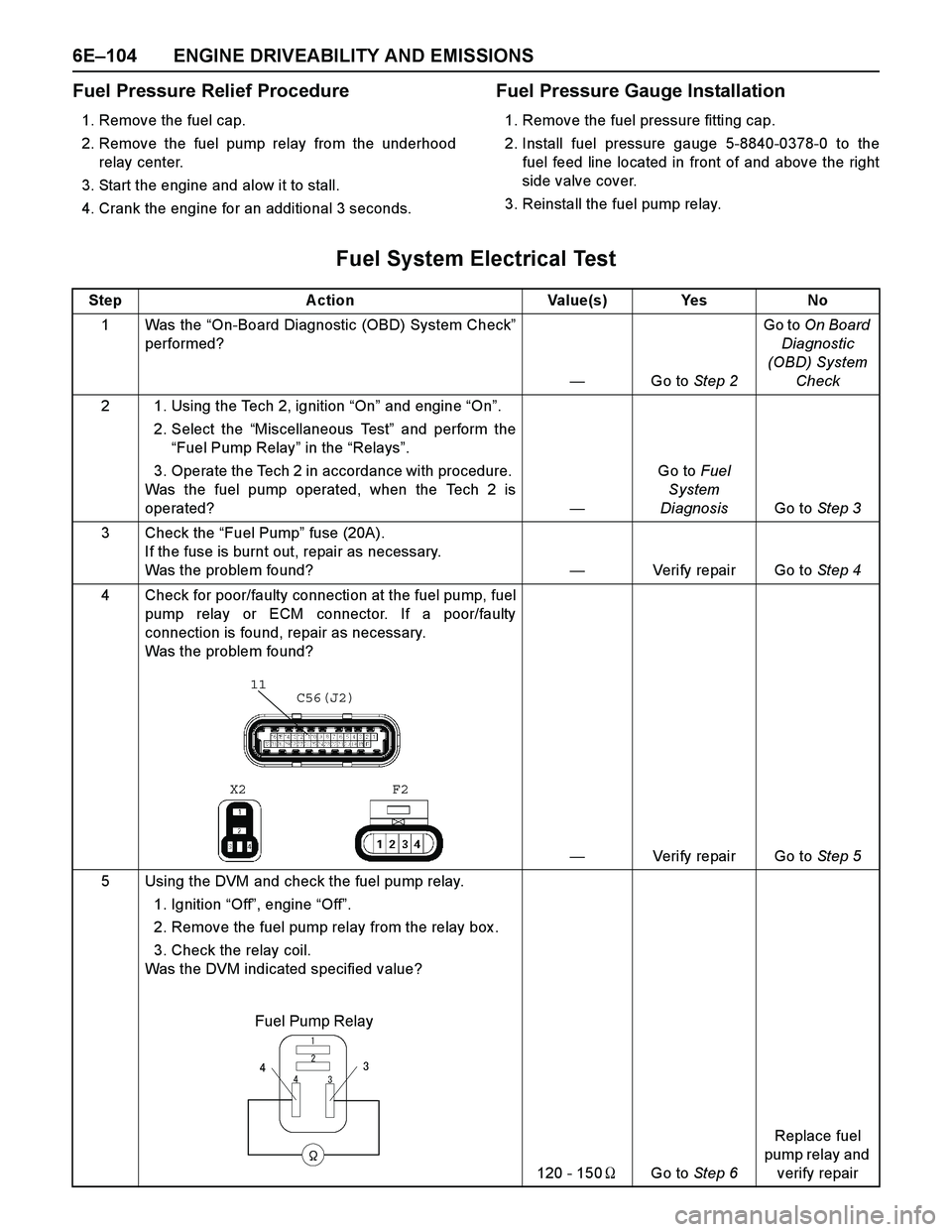
6E–104 ENGINE DRIVEABILITY AND EMISSIONS
Fuel Pressure Relief Procedure
1. Remove the fuel cap.
2. Remove the fuel pump relay from the underhood
relay center.
3. Start the engine and alow it to stall.
4. Crank the engine for an additional 3 seconds.
Fuel Pressure Gauge Installation
1. Remove the fuel pressure fitting cap.
2. Install fuel pressure gauge 5-8840-0378-0 to the
fuel feed line located in front of and above the right
side valve cover.
3. Reinstall the fuel pump relay.
Fuel System Electrical Test
Step Action Value(s) Yes No
1Was the “On-Board Diagnostic (OBD) System Check”
performed?
—Go to Step 2Go to On Board
Diagnostic
(OBD) System
Check
2 1. Using the Tech 2, ignition “On” and engine “On”.
2. Select the “Miscellaneous Test” and perform the
“Fuel Pump Relay” in the “Relays”.
3. Operate the Tech 2 in accordance with procedure.
Was the fuel pump operated, when the Tech 2 is
operated?—Go to Fuel
System
DiagnosisGo to Step 3
3 Check the “Fuel Pump” fuse (20A).
If the fuse is burnt out, repair as necessary.
Was the problem found?—Verify repair Go to Step 4
4 Check for poor/faulty connection at the fuel pump, fuel
pump relay or ECM connector. If a poor/faulty
connection is found, repair as necessary.
Was the problem found?
—Verify repair Go to Step 5
5 Using the DVM and check the fuel pump relay.
1. Ignition “Off”, engine “Off”.
2. Remove the fuel pump relay from the relay box .
3. Check the relay coil.
Was the DVM indicated specified value?
120 - 150Go to Step 6Replace fuel
pump relay and
verify repair
11C56(J2)
F2 X2
Fuel Pump Relay
Page 2681 of 4264
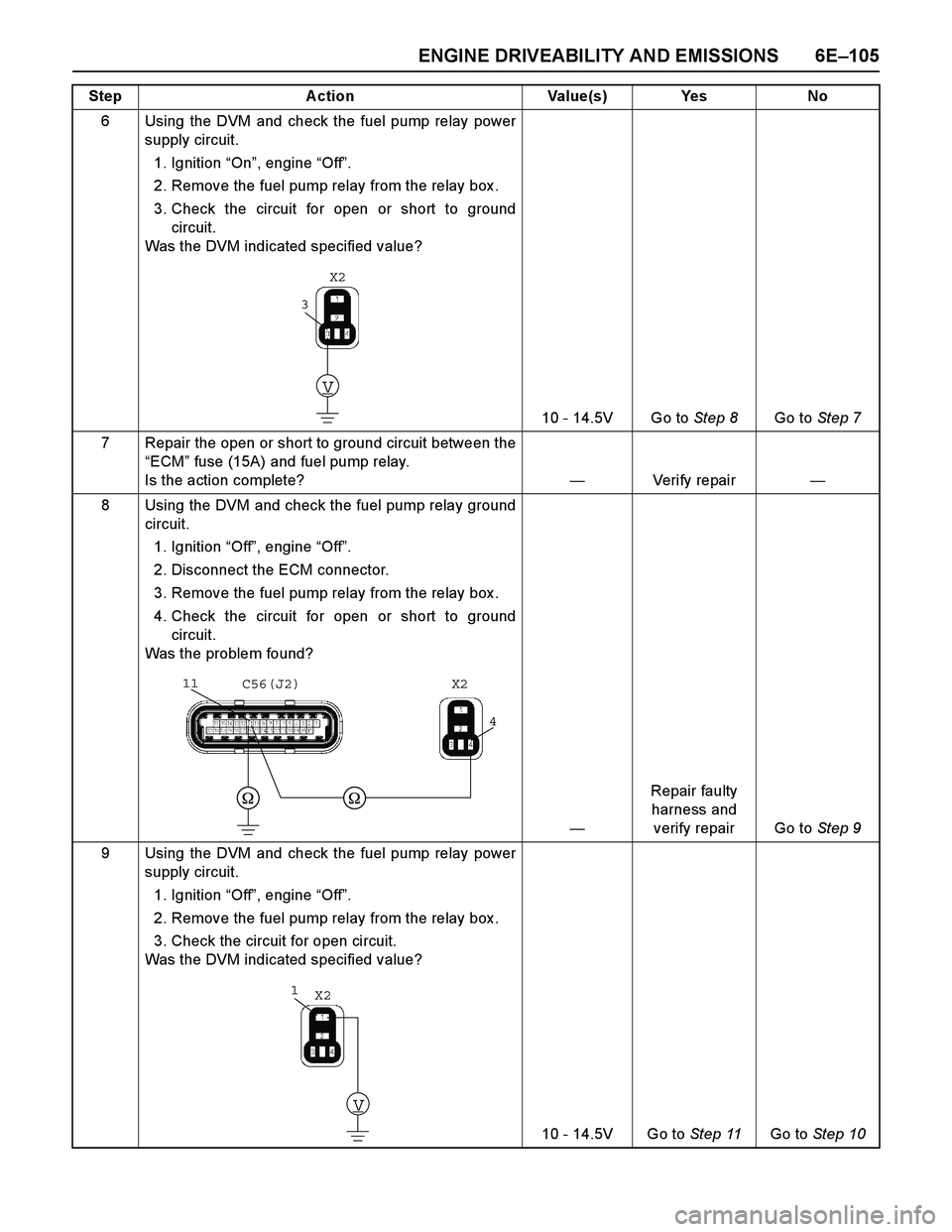
ENGINE DRIVEABILITY AND EMISSIONS 6E–105
6 Using the DVM and check the fuel pump relay power
supply circuit.
1. Ignition “On”, engine “Off”.
2. Remove the fuel pump relay from the relay box .
3. Check the circuit for open or short to ground
circuit.
Was the DVM indicated specified value?
10 - 14.5V Go to Step 8Go to Step 7
7 Repair the open or short to ground circuit between the
“ECM” fuse (15A) and fuel pump relay.
Is the action complete?—Veri fy repai r—
8 Using the DVM and check the fuel pump relay ground
circuit.
1. Ignition “Off”, engine “Off”.
2. Disconnect the ECM connector.
3. Remove the fuel pump relay from the relay box .
4. Check the circuit for open or short to ground
circuit.
Was the problem found?
—Repair faulty
harness and
verify repair Go to Step 9
9 Using the DVM and check the fuel pump relay power
supply circuit.
1. Ignition “Off”, engine “Off”.
2. Remove the fuel pump relay from the relay box .
3. Check the circuit for open circuit.
Was the DVM indicated specified value?
10 - 14.5V Go to Step 11Go to Step 10 Step Action Value(s) Yes No
V
3
X2
4
11C56(J2) X2
V
1X2
Page 2682 of 4264
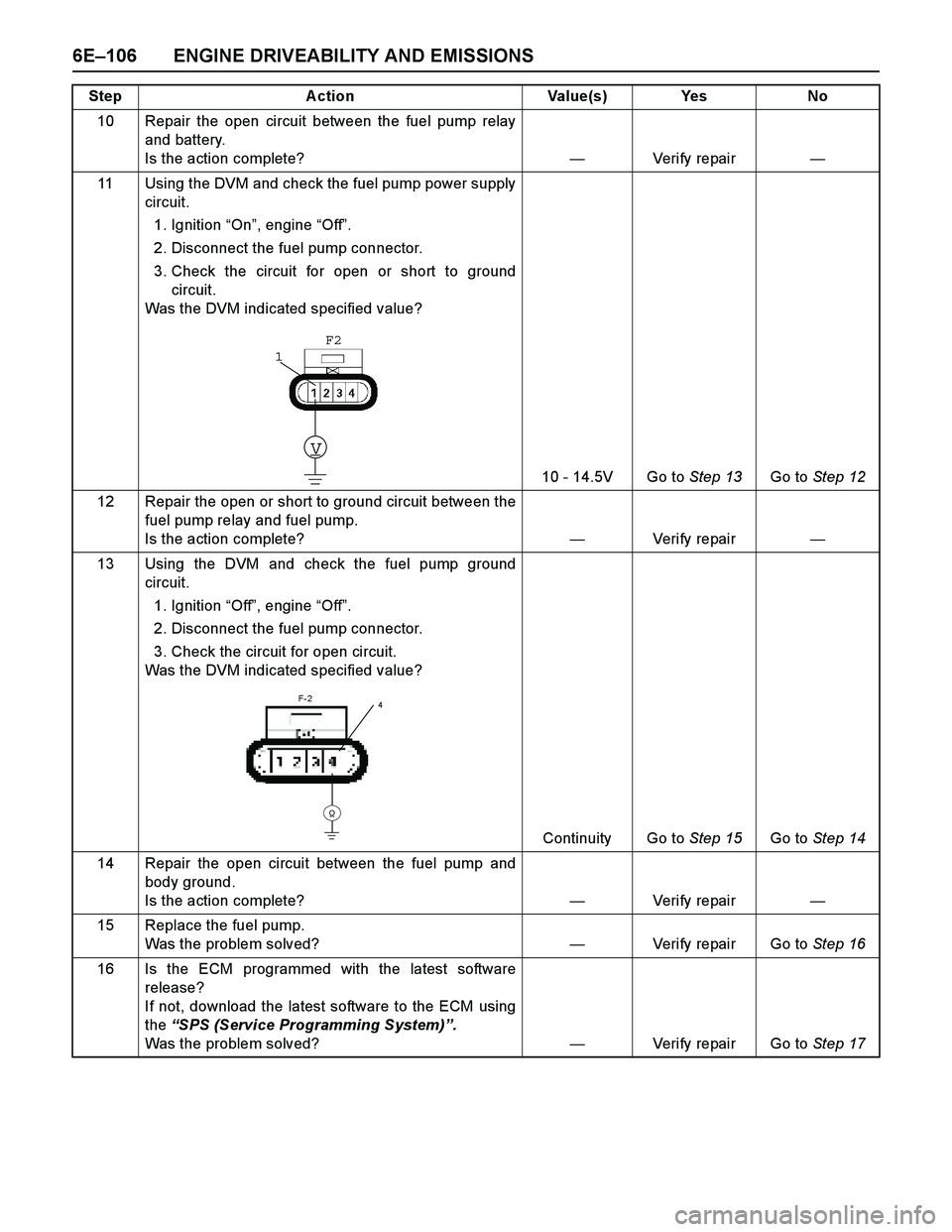
6E–106 ENGINE DRIVEABILITY AND EMISSIONS
10 Repair the open circuit between the fuel pump relay
and battery.
Is the action complete?—Veri fy repai r—
11 Using the DVM and check the fuel pump power supply
circuit.
1. Ignition “On”, engine “Off”.
2. Disconnect the fuel pump connector.
3. Check the circuit for open or short to ground
circuit.
Was the DVM indicated specified value?
10 - 14.5V Go to Step 13Go to Step 12
12 Repair the open or short to ground circuit between the
fuel pump relay and fuel pump.
Is the action complete?—Veri fy repai r—
13 Using the DVM and check the fuel pump ground
circuit.
1. Ignition “Off”, engine “Off”.
2. Disconnect the fuel pump connector.
3. Check the circuit for open circuit.
Was the DVM indicated specified value?
Continuity Go to Step 15Go to Step 14
14 Repair the open circuit between the fuel pump and
body ground.
Is the action complete?—Veri fy repai r—
15 Replace the fuel pump.
Was the problem solved?—Verify repair Go to Step 16
16 Is the ECM programmed with the latest software
release?
If not, download the latest software to the ECM using
the “SPS (Service Programming System)”.
Was the problem solved?—Verify repair Go to Step 17 Step Action Value(s) Yes No
V
1
F2
F-2
Page 2684 of 4264
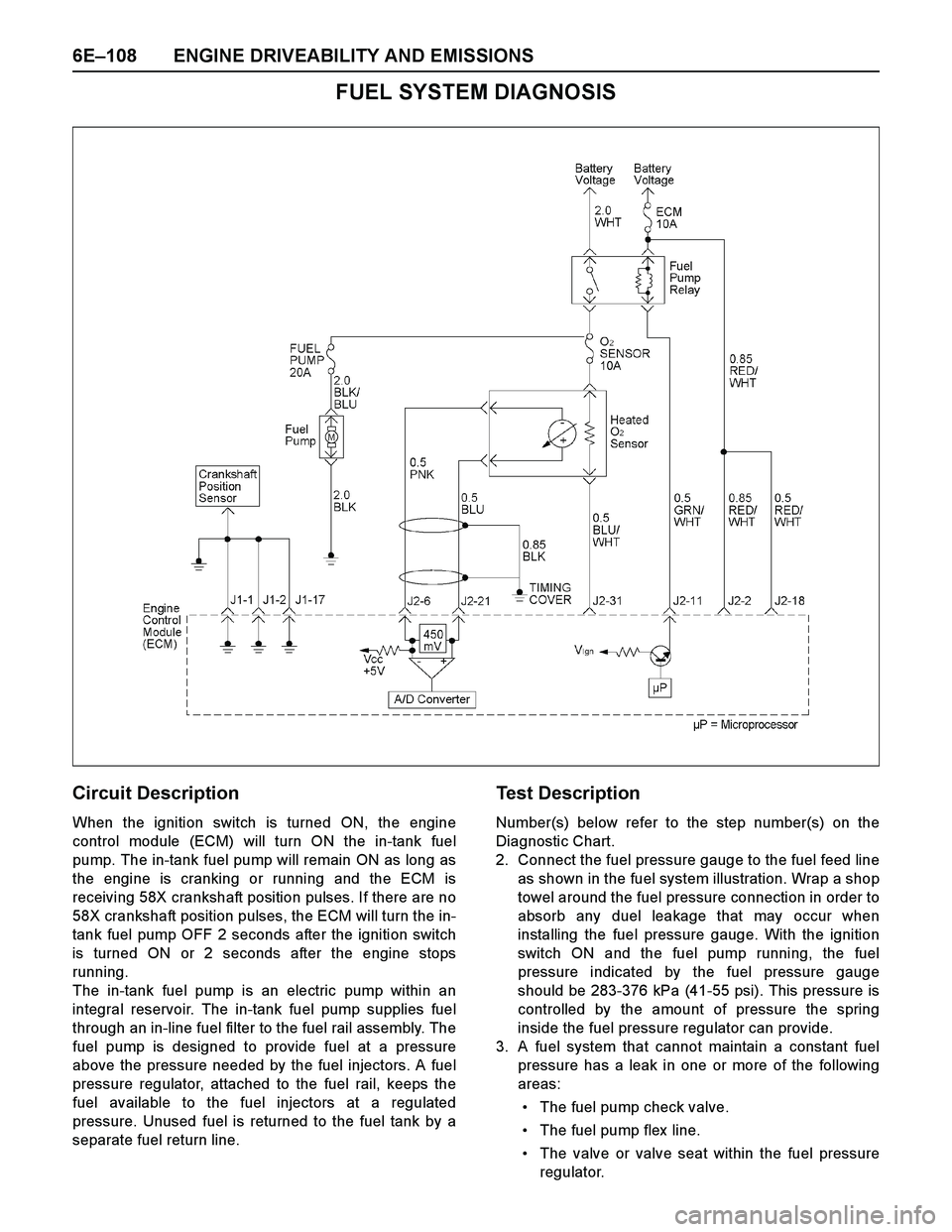
6E–108 ENGINE DRIVEABILITY AND EMISSIONS
FUEL SYSTEM DIAGNOSIS
Circuit Description
When the ignition switch is turned ON, the engine
control module (ECM) will turn ON the in-tank fuel
pump. The in-tank fuel pump will remain ON as long as
the engine is cranking or running and the ECM is
receiving 58X crankshaft position pulses. If there are no
58X crankshaft position pulses, the ECM will turn the in-
tank fuel pump OFF 2 seconds after the ignition switch
is turned ON or 2 seconds after the engine stops
running.
The in-tank fuel pump is an electric pump within an
integral reservoir. The in-tank fuel pump supplies fuel
through an in-line fuel filter to the fuel rail assembly. The
fuel pump is designed to provide fuel at a pressure
above the pressure needed by the fuel injectors. A fuel
pressure regulator, attached to the fuel rail, keeps the
fuel available to the fuel injectors at a regulated
pressure. Unused fuel is returned to the fuel tank by a
separate fuel return line.
Test Description
Number(s) below refer to the step number(s) on the
Diagnostic Chart.
2. Connect the fuel pressure gauge to the fuel feed line
as shown in the fuel system illustration. Wrap a shop
towel around the fuel pressure connection in order to
absorb any duel leakage that may occur when
installing the fuel pressure gauge. With the ignition
switch ON and the fuel pump running, the fuel
pressure indicated by the fuel pressure gauge
should be 283-376 kPa (41-55 psi). This pressure is
controlled by the amount of pressure the spring
inside the fuel pressure regulator can provide.
3. A fuel system that cannot maintain a constant fuel
pressure has a leak in one or more of the following
areas:
The fuel pump check valve.
The fuel pump flex line.
The valve or valve seat within the fuel pressure
regulator.
Page 2686 of 4264
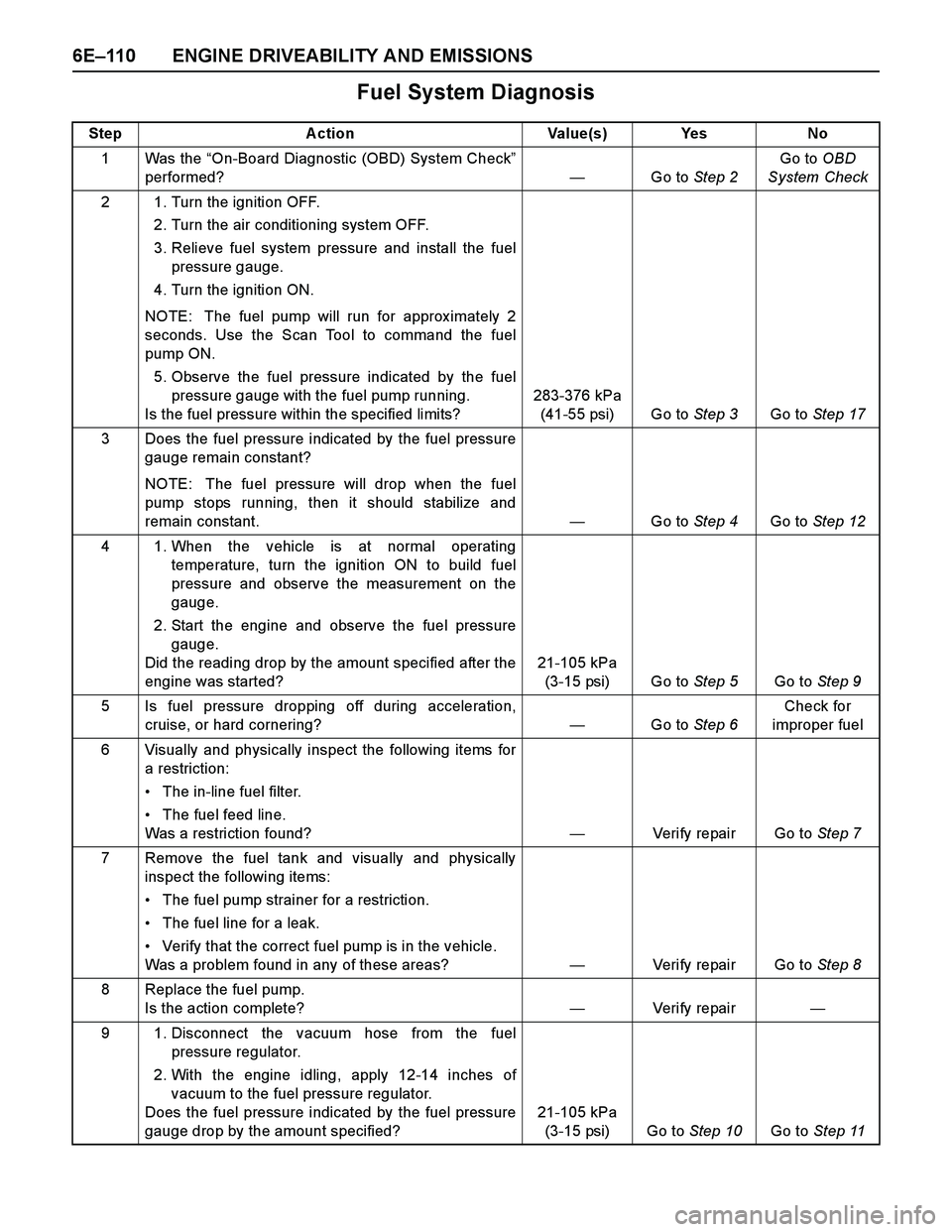
6E–110 ENGINE DRIVEABILITY AND EMISSIONS
Fuel System Diagnosis
Step Action Value(s) Yes No
1Was the “On-Board Diagnostic (OBD) System Check”
performed?—Go to Step 2Go to OBD
System Check
2 1. Turn the ignition OFF.
2. Turn the air conditioning system OFF.
3. Relieve fuel system pressure and install the fuel
pressure gauge.
4. Turn the ignition ON.
NOTE: The fuel pump will run for approx imately 2
seconds. Use the Scan Tool to command the fuel
pump ON.
5. Observe the fuel pressure indicated by the fuel
pressure gauge with the fuel pump running.
Is the fuel pressure within the specified limits?283-376 kPa
(41-55 psi) Go to Step 3Go to Step 17
3 Does the fuel pressure indicated by the fuel pressure
gauge remain constant?
NOTE: The fuel pressure will drop when the fuel
pump stops running, then it should stabilize and
remain constant.—Go to Step 4Go to Step 12
4 1. When the vehicle is at normal operating
temperature, turn the ignition ON to build fuel
pressure and observe the measurement on the
gauge.
2. Start the engine and observe the fuel pressure
gauge.
Did the reading drop by the amount specified after the
engine was started?21-105 kPa
(3-15 psi) Go to Step 5Go to Step 9
5 Is fuel pressure dropping off during acceleration,
cruise, or hard cornering?—Go to Step 6Check for
improper fuel
6 Visually and physically inspect the following items for
a restriction:
The in-line fuel filter.
The fuel feed line.
Was a restriction found?—Verify repair Go to Step 7
7 Remove the fuel tank and visually and physically
inspect the following items:
The fuel pump strainer for a restriction.
The fuel line for a leak.
Verify that the correct fuel pump is in the vehicle.
Was a problem found in any of these areas?—Verify repair Go to Step 8
8 Replace the fuel pump.
Is the action complete?—Veri fy repai r—
9 1. Disconnect the vacuum hose from the fuel
pressure regulator.
2. With the engine idling, apply 12-14 inches of
vacuum to the fuel pressure regulator.
Does the fuel pressure indicated by the fuel pressure
gauge drop by the amount specified?21-105 kPa
(3-15 psi) Go to Step 10Go to Step 11
Page 2691 of 4264
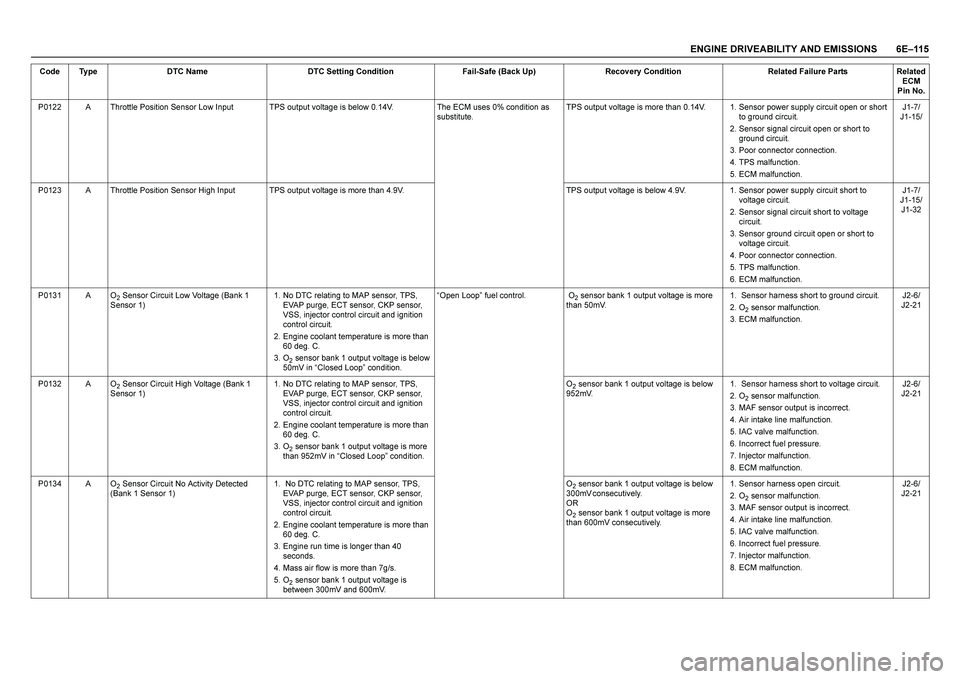
ENGINE DRIVEABILITY AND EMISSIONS 6E–115
P0122 A Throttle Position Sensor Low Input TPS output voltage is below 0.14V. The ECM uses 0% condition as
substitute.TPS output voltage is more than 0.14V. 1. Sensor power supply circuit open or short
to ground circuit.
2. Sensor signal circuit open or short to
ground circuit.
3. Poor connector connection.
4. TPS malfunction.
5. ECM malfunction.J1-7/
J1-15/
P0123 A Throttle Position Sensor High Input TPS output voltage is more than 4.9V. TPS output voltage is below 4.9V. 1. Sensor power supply circuit short to
voltage circuit.
2. Sensor signal circuit short to voltage
circuit.
3. Sensor ground circuit open or short to
voltage circuit.
4. Poor connector connection.
5. TPS malfunction.
6. ECM malfunction.J1-7/
J1-15/
J1-32
P0131 A O
2 Sensor Circuit Low Voltage (Bank 1
Sensor 1)1. No DTC relating to MAP sensor, TPS,
EVAP purge, ECT sensor, CKP sensor,
VSS, injector control circuit and ignition
control circuit.
2. Engine coolant temperature is more than
60 deg. C.
3. O
2 sensor bank 1 output voltage is below
50mV in “Closed Loop” condition. “Open Loop” fuel control. O
2 sensor bank 1 output voltage is more
than 50mV.1. Sensor harness short to ground circuit.
2. O
2 sensor malfunction.
3. ECM malfunction.J2-6/
J2-21
P0132 A O
2 Sensor Circuit High Voltage (Bank 1
Sensor 1)1. No DTC relating to MAP sensor, TPS,
EVAP purge, ECT sensor, CKP sensor,
VSS, injector control circuit and ignition
control circuit.
2. Engine coolant temperature is more than
60 deg. C.
3. O
2 sensor bank 1 output voltage is more
than 952mV in “Closed Loop” condition. O
2 sensor bank 1 output voltage is below
952mV.1. Sensor harness short to voltage circuit.
2. O
2 sensor malfunction.
3. MAF sensor output is incorrect.
4. Air intake line malfunction.
5. IAC valve malfunction.
6. Incorrect fuel pressure.
7. Injector malfunction.
8. ECM malfunction.J2-6/
J2-21
P0134 A O
2 Sensor Circuit No Activity Detected
(Bank 1 Sensor 1)1. No DTC relating to MAP sensor, TPS,
EVAP purge, ECT sensor, CKP sensor,
VSS, injector control circuit and ignition
control circuit.
2. Engine coolant temperature is more than
60 deg. C.
3. Engine run time is longer than 40
seconds.
4. Mass air flow is more than 7g/s.
5. O
2 sensor bank 1 output voltage is
between 300mV and 600mV.O
2 sensor bank 1 output voltage is below
3 0 0 m V c o n s e c u t i v e l y .
O R
O2 sensor bank 1 output voltage is more
than 600mV consecutively.1. Sensor harness open circuit.
2. O
2 sensor malfunction.
3. MAF sensor output is incorrect.
4. Air intake line malfunction.
5. IAC valve malfunction.
6. Incorrect fuel pressure.
7. Injector malfunction.
8. ECM malfunction.J2-6/
J2-21 Code Type DTC Name DTC Setting Condition Fail-Safe (Back Up) Recovery Condition Related Failure Parts Related
ECM
Pin No.