check oil ISUZU TF SERIES 2004 Manual PDF
[x] Cancel search | Manufacturer: ISUZU, Model Year: 2004, Model line: TF SERIES, Model: ISUZU TF SERIES 2004Pages: 4264, PDF Size: 72.63 MB
Page 1169 of 4264
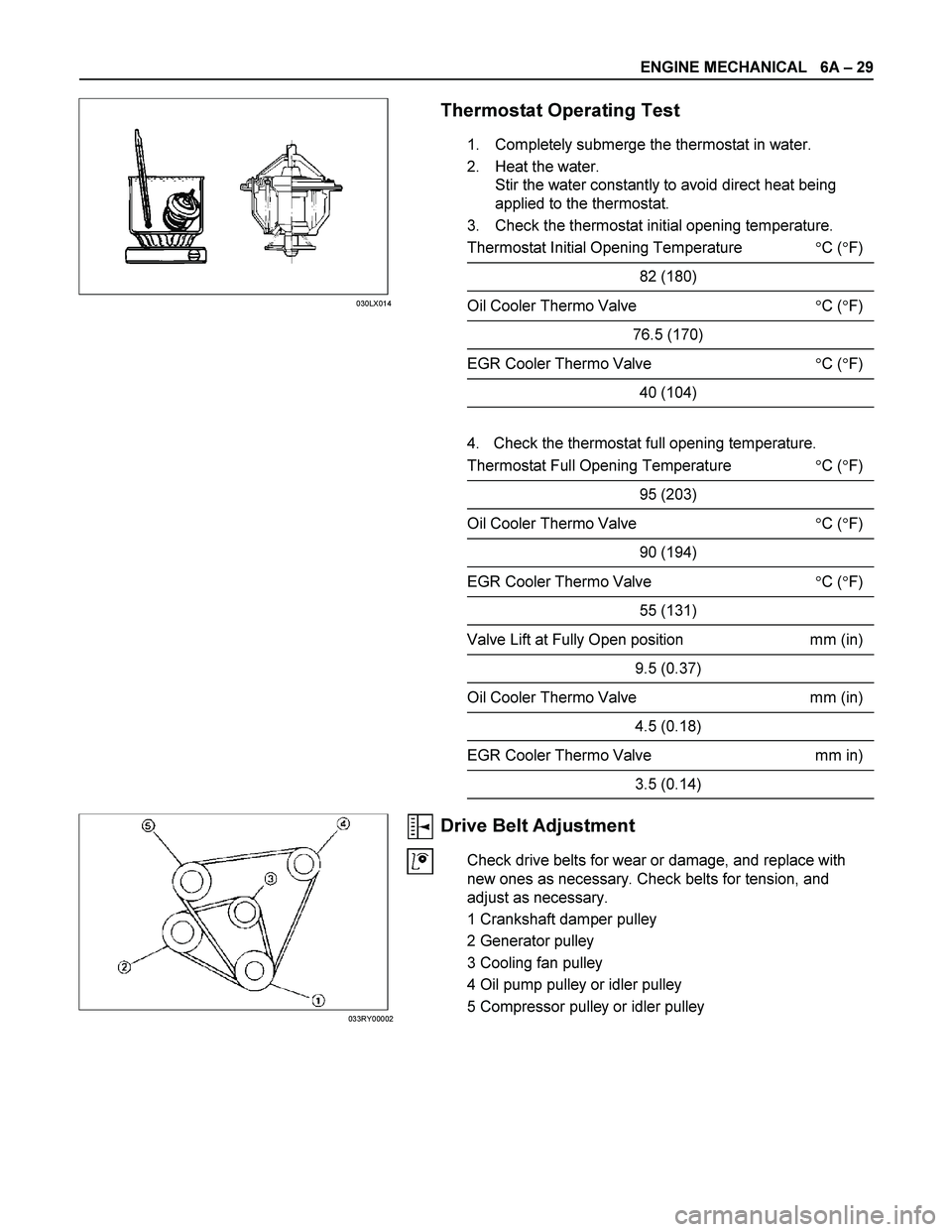
ENGINE MECHANICAL 6A – 29
Thermostat Operating Test
1. Completely submerge the thermostat in water.
2. Heat the water.
Stir the water constantly to avoid direct heat being
applied to the thermostat.
3. Check the thermostat initial opening temperature.
Thermostat Initial Opening Temperature C (F)
82 (180)
Oil Cooler Thermo Valve C (F)
76.5 (170)
EGR Cooler Thermo Valve C (F)
40 (104)
4. Check the thermostat full opening temperature.
Thermostat Full Opening Temperature C (F)
95 (203)
Oil Cooler Thermo Valve C (F)
90 (194)
EGR Cooler Thermo Valve C (F)
55 (131)
Valve Lift at Fully Open position mm (in)
9.5 (0.37)
Oil Cooler Thermo Valve mm (in)
4.5 (0.18)
EGR Cooler Thermo Valve mm in)
3.5 (0.14)
Drive Belt Adjustment
Check drive belts for wear or damage, and replace with
new ones as necessary. Check belts for tension, and
adjust as necessary.
1 Crankshaft damper pulley
2 Generator pulley
3 Cooling fan pulley
4 Oil pump pulley or idler pulley
5 Compressor pulley or idler pulley
030LX014
033RY00002
Page 1181 of 4264
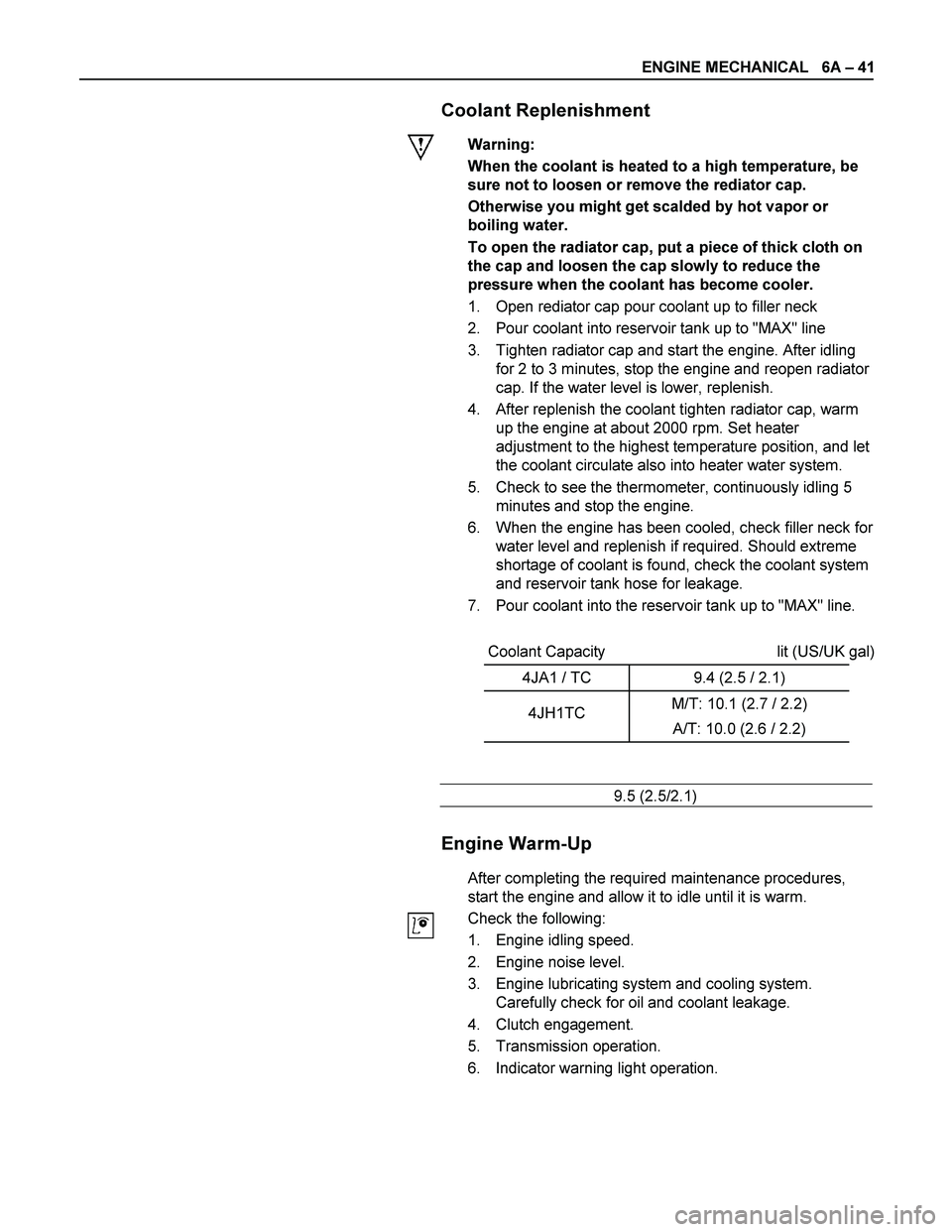
ENGINE MECHANICAL 6A – 41
Coolant Replenishment
Warning:
When the coolant is heated to a high temperature, be
sure not to loosen or remove the rediator cap.
Otherwise you might get scalded by hot vapor or
boiling water.
To open the radiator cap, put a piece of thick cloth on
the cap and loosen the cap slowly to reduce the
pressure when the coolant has become cooler.
1. Open rediator cap pour coolant up to filler neck
2. Pour coolant into reservoir tank up to "MAX" line
3. Tighten radiator cap and start the engine. After idling
for 2 to 3 minutes, stop the engine and reopen radiator
cap. If the water level is lower, replenish.
4. After replenish the coolant tighten radiator cap, warm
up the engine at about 2000 rpm. Set heater
adjustment to the highest temperature position, and let
the coolant circulate also into heater water system.
5. Check to see the thermometer, continuously idling 5
minutes and stop the engine.
6. When the engine has been cooled, check filler neck for
water level and replenish if required. Should extreme
shortage of coolant is found, check the coolant system
and reservoir tank hose for leakage.
7. Pour coolant into the reservoir tank up to "MAX" line.
Coolant Capacity lit (US/UK gal)
4JA1 / TC 9.4 (2.5 / 2.1)
4JH1TC M/T: 10.1 (2.7 / 2.2)
A/T: 10.0 (2.6 / 2.2)
9.5 (2.5/2.1)
Engine Warm-Up
After completing the required maintenance procedures,
start the engine and allow it to idle until it is warm.
Check the following:
1. Engine idling speed.
2. Engine noise level.
3. Engine lubricating system and cooling system.
Carefully check for oil and coolant leakage.
4. Clutch engagement.
5. Transmission operation.
6. Indicator warning light operation.
Page 1209 of 4264
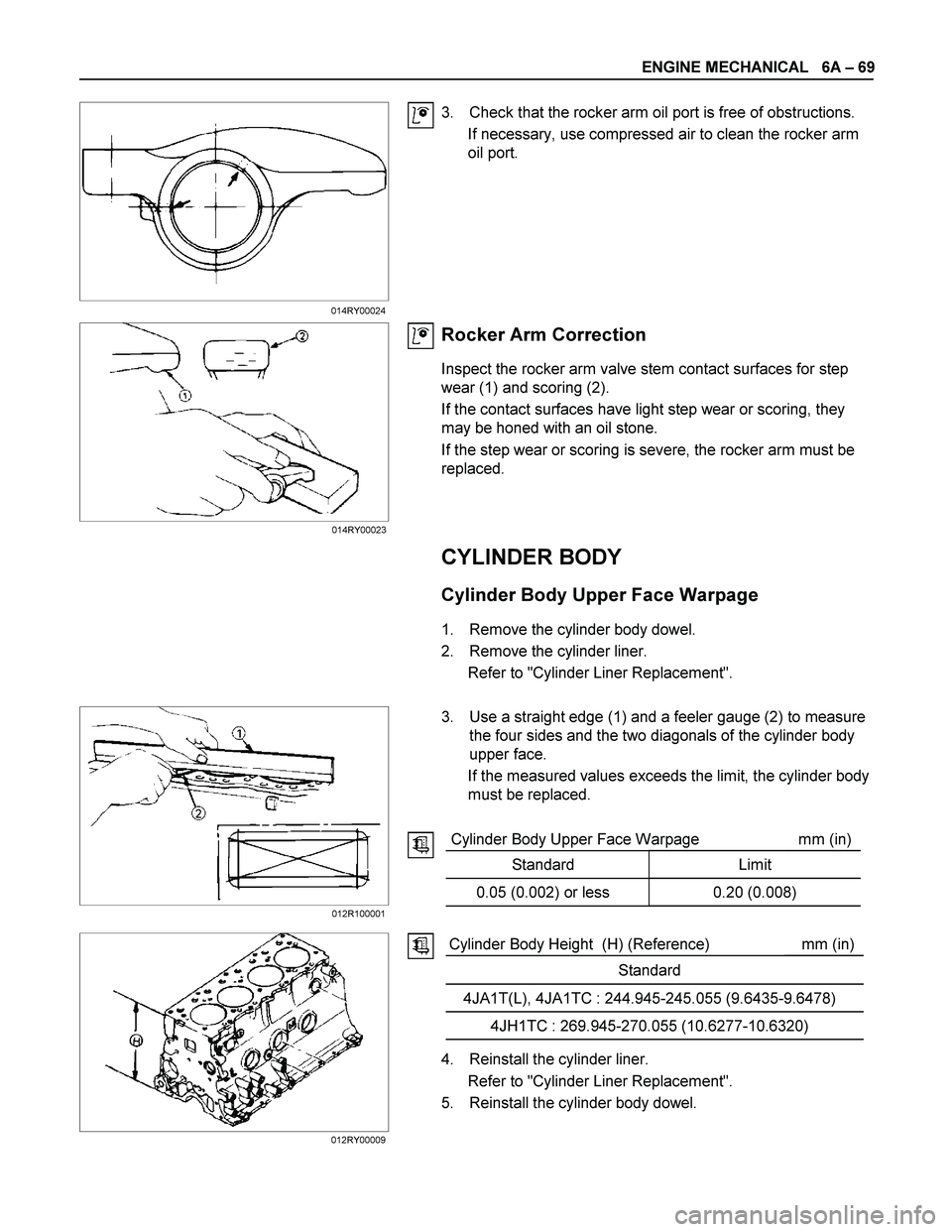
ENGINE MECHANICAL 6A – 69
3. Check that the rocker arm oil port is free of obstructions.
If necessary, use compressed air to clean the rocker arm
oil port.
Rocker Arm Correction
Inspect the rocker arm valve stem contact surfaces for step
wear (1) and scoring (2).
If the contact surfaces have light step wear or scoring, they
may be honed with an oil stone.
If the step wear or scoring is severe, the rocker arm must be
replaced.
CYLINDER BODY
Cylinder Body Upper Face Warpage
1. Remove the cylinder body dowel.
2. Remove the cylinder liner.
Refer to "Cylinder Liner Replacement".
3. Use a straight edge (1) and a feeler gauge (2) to measure
the four sides and the two diagonals of the cylinder body
upper face.
If the measured values exceeds the limit, the cylinder body
must be replaced.
Cylinder Body Upper Face Warpage mm (in)
Standard Limit
0.05 (0.002) or less 0.20 (0.008)
Cylinder Body Height (H) (Reference) mm (in)
Standard
4JA1T(L), 4JA1TC : 244.945-245.055 (9.6435-9.6478)
4JH1TC : 269.945-270.055 (10.6277-10.6320)
4. Reinstall the cylinder liner.
Refer to "Cylinder Liner Replacement".
5. Reinstall the cylinder body dowel.
014RY00024
012R100001
012RY00009014RY00023
Page 1213 of 4264
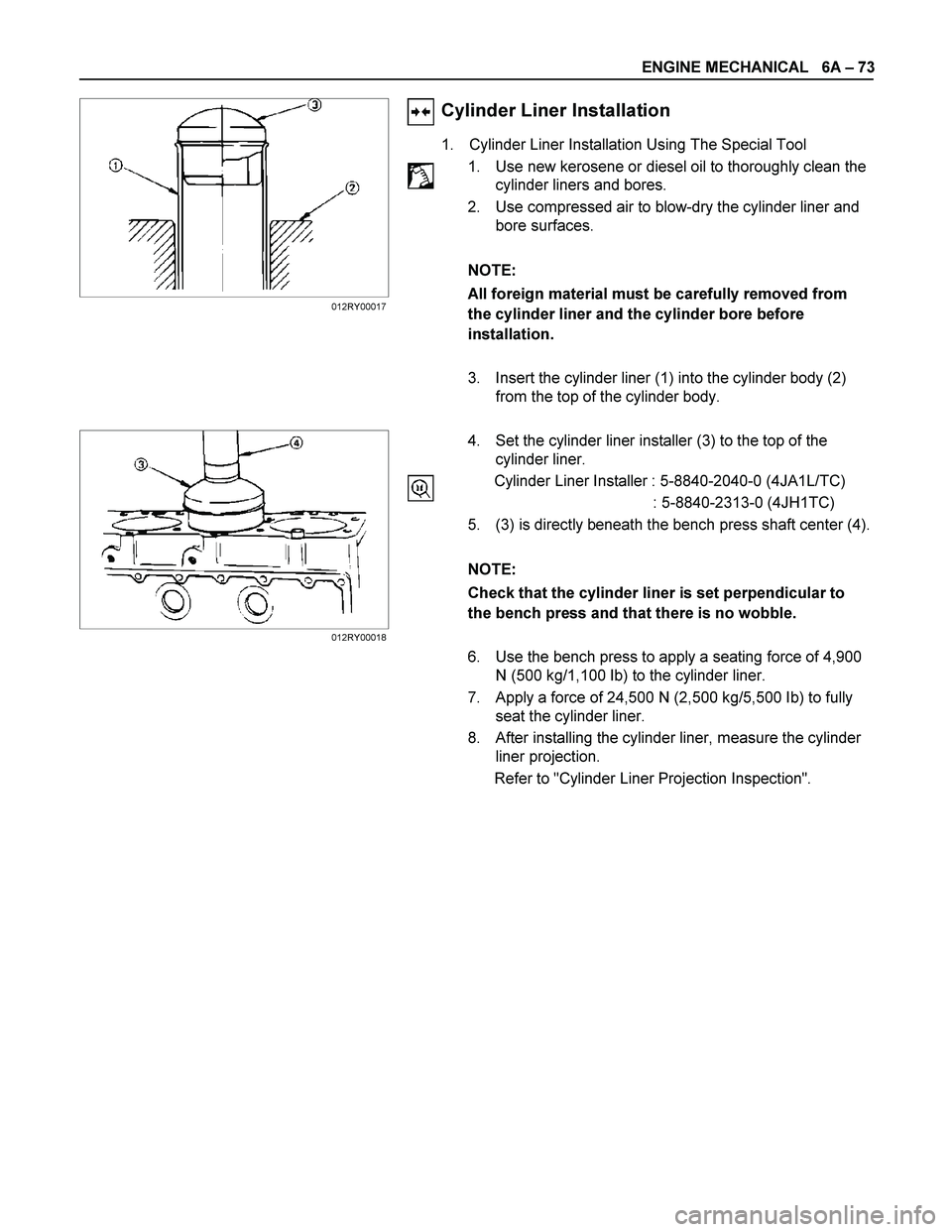
ENGINE MECHANICAL 6A – 73
Cylinder Liner Installation
1. Cylinder Liner Installation Using The Special Tool
1. Use new kerosene or diesel oil to thoroughly clean the
cylinder liners and bores.
2. Use compressed air to blow-dry the cylinder liner and
bore surfaces.
NOTE:
All foreign material must be carefully removed from
the cylinder liner and the cylinder bore before
installation.
3. Insert the cylinder liner (1) into the cylinder body (2)
from the top of the cylinder body.
4. Set the cylinder liner installer (3) to the top of the
cylinder liner.
Cylinder Liner Installer : 5-8840-2040-0 (4JA1L/TC)
: 5-8840-2313-0 (4JH1TC)
5. (3) is directly beneath the bench press shaft center (4).
NOTE:
Check that the cylinder liner is set perpendicular to
the bench press and that there is no wobble.
6. Use the bench press to apply a seating force of 4,900
N (500 kg/1,100 Ib) to the cylinder liner.
7. Apply a force of 24,500 N (2,500 kg/5,500 Ib) to fully
seat the cylinder liner.
8. After installing the cylinder liner, measure the cylinder
liner projection.
Refer to "Cylinder Liner Projection Inspection".
012RY00017
012RY00018
Page 1232 of 4264
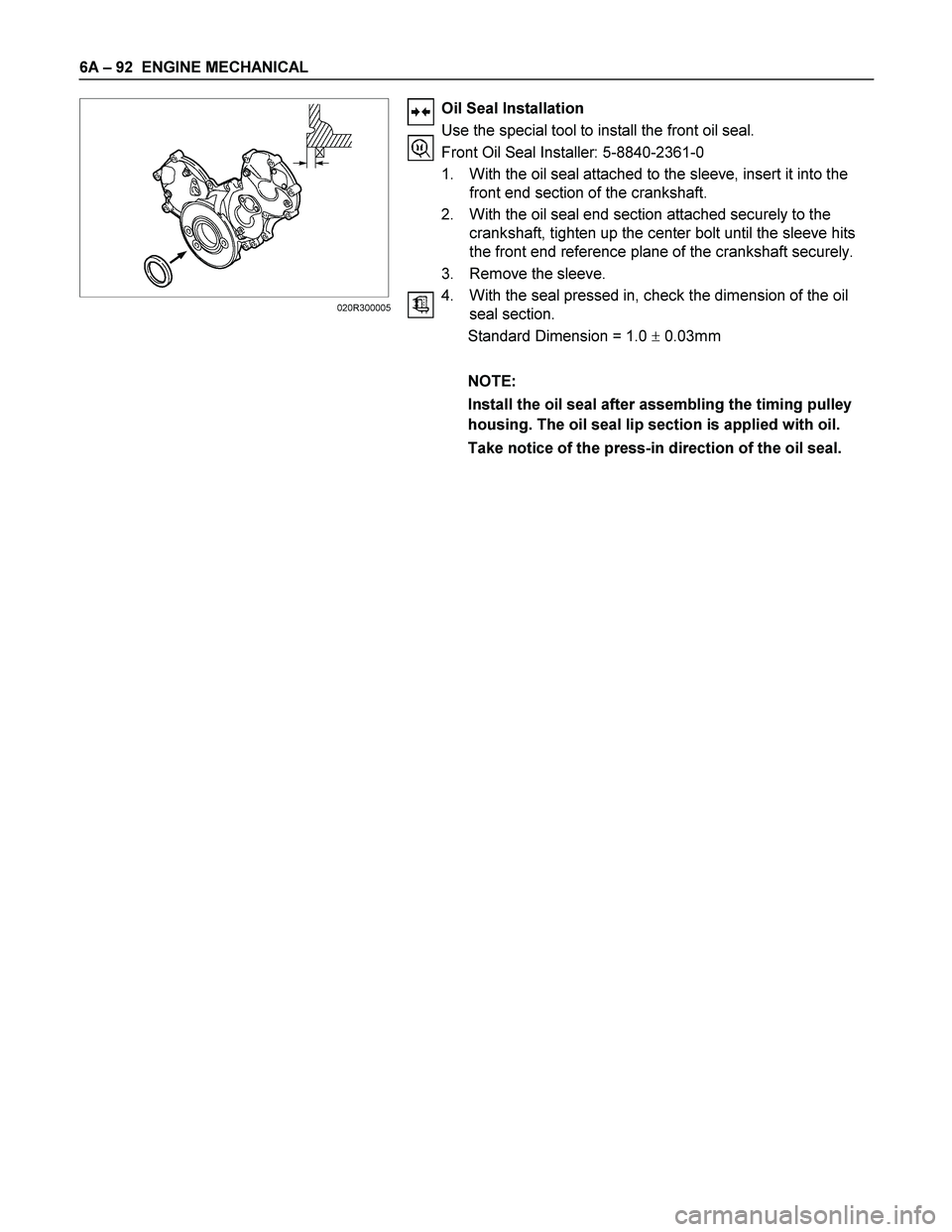
6A – 92 ENGINE MECHANICAL
Oil Seal Installation
Use the special tool to install the front oil seal.
Front Oil Seal Installer: 5-8840-2361-0
1. With the oil seal attached to the sleeve, insert it into the
front end section of the crankshaft.
2. With the oil seal end section attached securely to the
crankshaft, tighten up the center bolt until the sleeve hits
the front end reference plane of the crankshaft securely.
3. Remove the sleeve.
4. With the seal pressed in, check the dimension of the oil
seal section.
Standard Dimension = 1.0 0.03mm
NOTE:
Install the oil seal after assembling the timing pulley
housing. The oil seal lip section is applied with oil.
Take notice of the press-in direction of the oil seal.
020R300005
Page 1237 of 4264
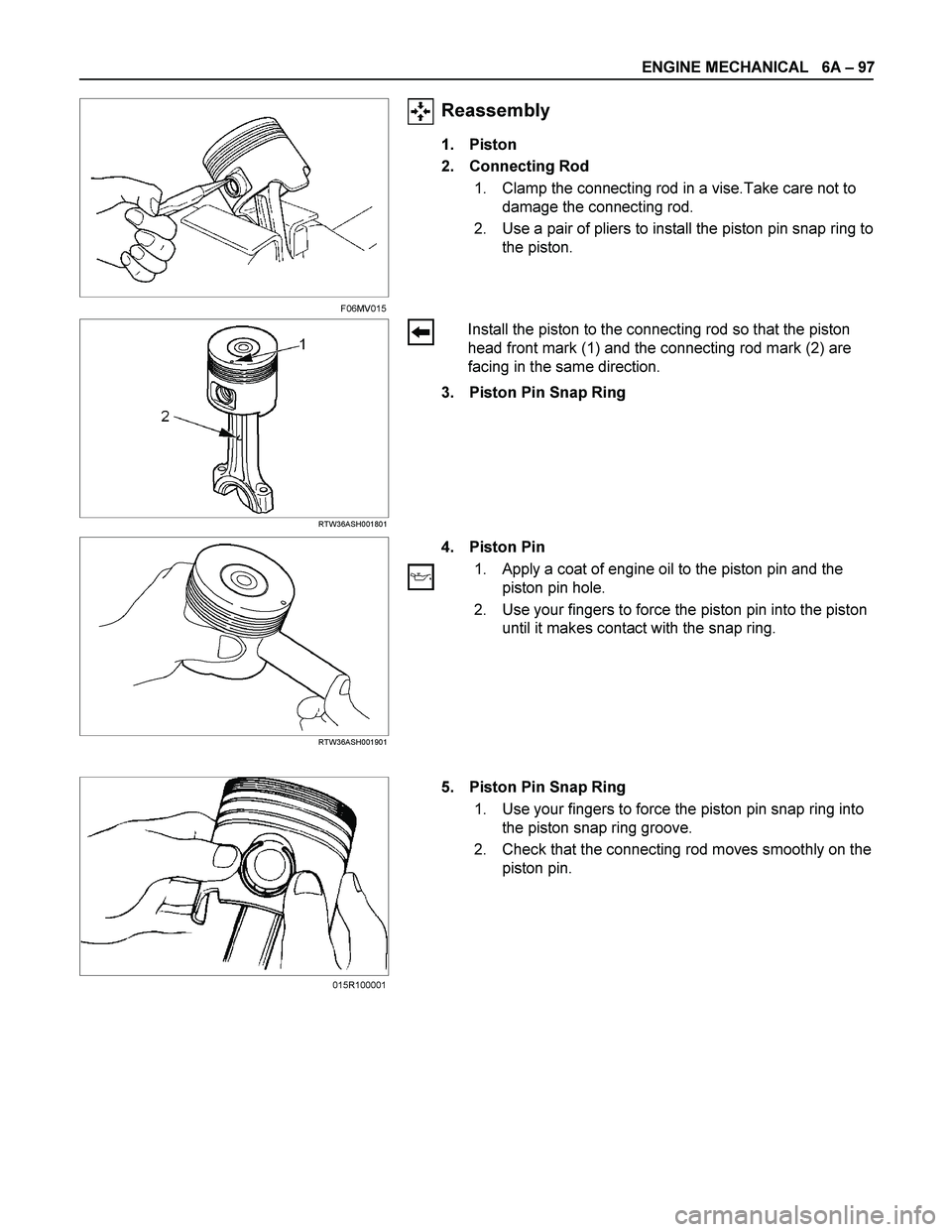
ENGINE MECHANICAL 6A – 97
Reassembly
1. Piston
2. Connecting Rod
1. Clamp the connecting rod in a vise.Take care not to
damage the connecting rod.
2. Use a pair of pliers to install the piston pin snap ring to
the piston.
RTW36ASH001801
Install the piston to the connecting rod so that the piston
head front mark (1) and the connecting rod mark (2) are
facing in the same direction.
3. Piston Pin Snap Ring
RTW36ASH001901
4. Piston Pin
1. Apply a coat of engine oil to the piston pin and the
piston pin hole.
2. Use your fingers to force the piston pin into the piston
until it makes contact with the snap ring.
5. Piston Pin Snap Ring
1. Use your fingers to force the piston pin snap ring into
the piston snap ring groove.
2. Check that the connecting rod moves smoothly on the
piston pin.
F06MV015
015R100001
Page 1238 of 4264
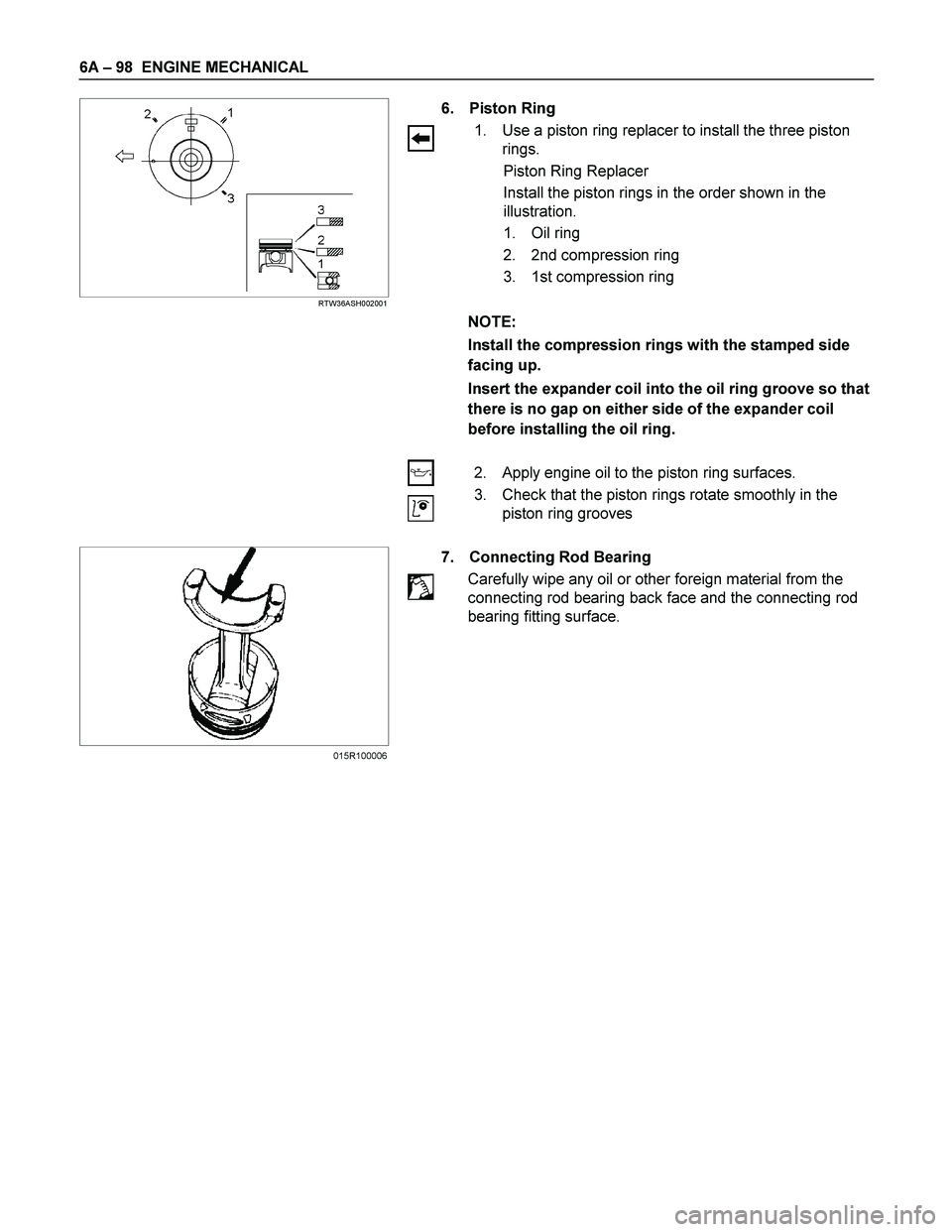
6A – 98 ENGINE MECHANICAL
RTW36ASH002001
6. Piston Ring
1. Use a piston ring replacer to install the three piston
rings.
Piston Ring Replacer
Install the piston rings in the order shown in the
illustration.
1. Oil ring
2. 2nd compression ring
3. 1st compression ring
NOTE:
Install the compression rings with the stamped side
facing up.
Insert the expander coil into the oil ring groove so that
there is no gap on either side of the expander coil
before installing the oil ring.
2. Apply engine oil to the piston ring surfaces.
3. Check that the piston rings rotate smoothly in the
piston ring grooves
7. Connecting Rod Bearing
Carefully wipe any oil or other foreign material from the
connecting rod bearing back face and the connecting rod
bearing fitting surface.
015R100006
Page 1245 of 4264
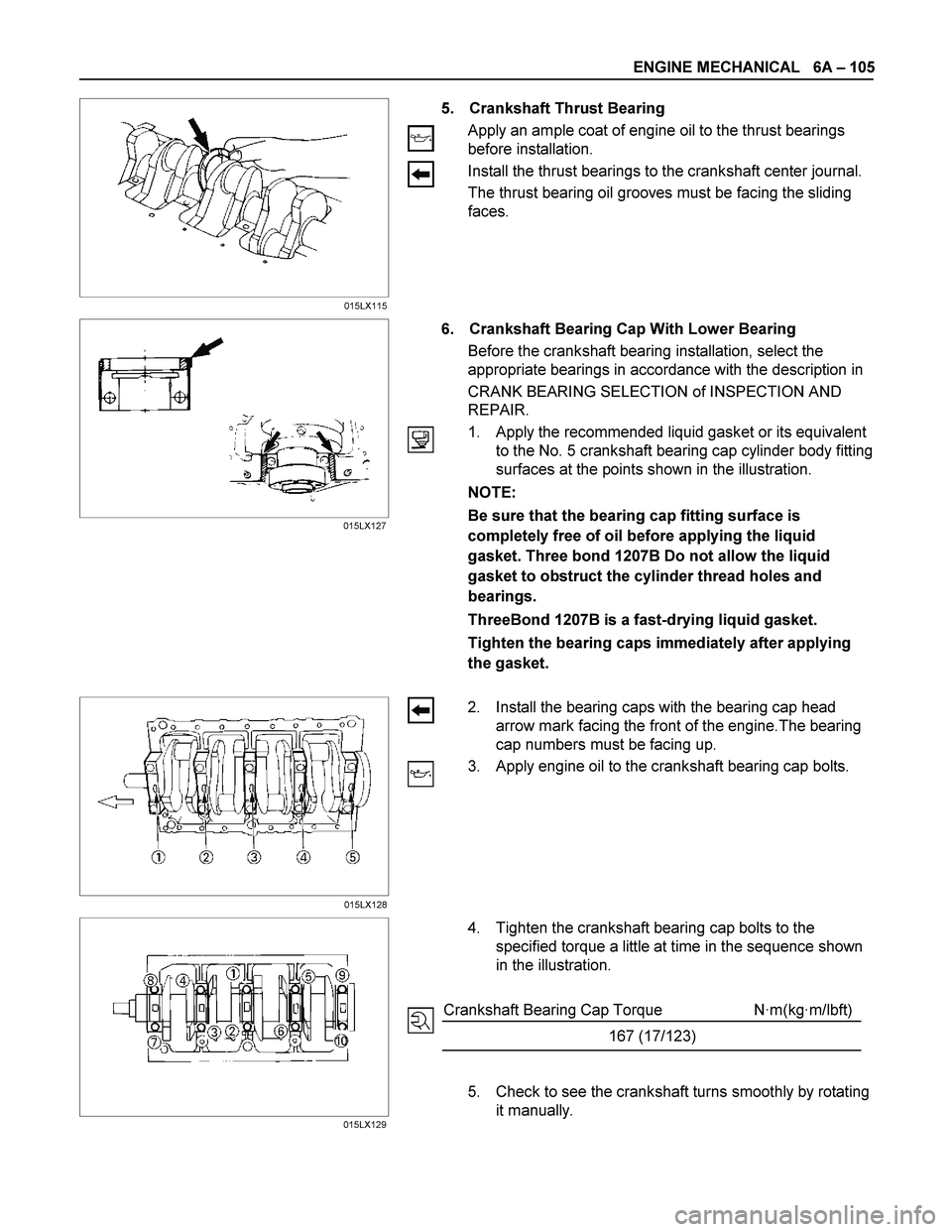
ENGINE MECHANICAL 6A – 105
5. Crankshaft Thrust Bearing
Apply an ample coat of engine oil to the thrust bearings
before installation.
Install the thrust bearings to the crankshaft center journal.
The thrust bearing oil grooves must be facing the sliding
faces.
6. Crankshaft Bearing Cap With Lower Bearing
Before the crankshaft bearing installation, select the
appropriate bearings in accordance with the description in
CRANK BEARING SELECTION of INSPECTION AND
REPAIR.
1. Apply the recommended liquid gasket or its equivalent
to the No. 5 crankshaft bearing cap cylinder body fitting
surfaces at the points shown in the illustration.
NOTE:
Be sure that the bearing cap fitting surface is
completely free of oil before applying the liquid
gasket. Three bond 1207B Do not allow the liquid
gasket to obstruct the cylinder thread holes and
bearings.
ThreeBond 1207B is a fast-drying liquid gasket.
Tighten the bearing caps immediately after applying
the gasket.
2. Install the bearing caps with the bearing cap head
arrow mark facing the front of the engine.The bearing
cap numbers must be facing up.
3. Apply engine oil to the crankshaft bearing cap bolts.
4. Tighten the crankshaft bearing cap bolts to the
specified torque a little at time in the sequence shown
in the illustration.
Crankshaft Bearing Cap Torque N·m(kg·m/lbft)
167 (17/123)
5. Check to see the crankshaft turns smoothly by rotating
it manually.
015LX115
015LX127
015LX128
015LX129
Page 1248 of 4264
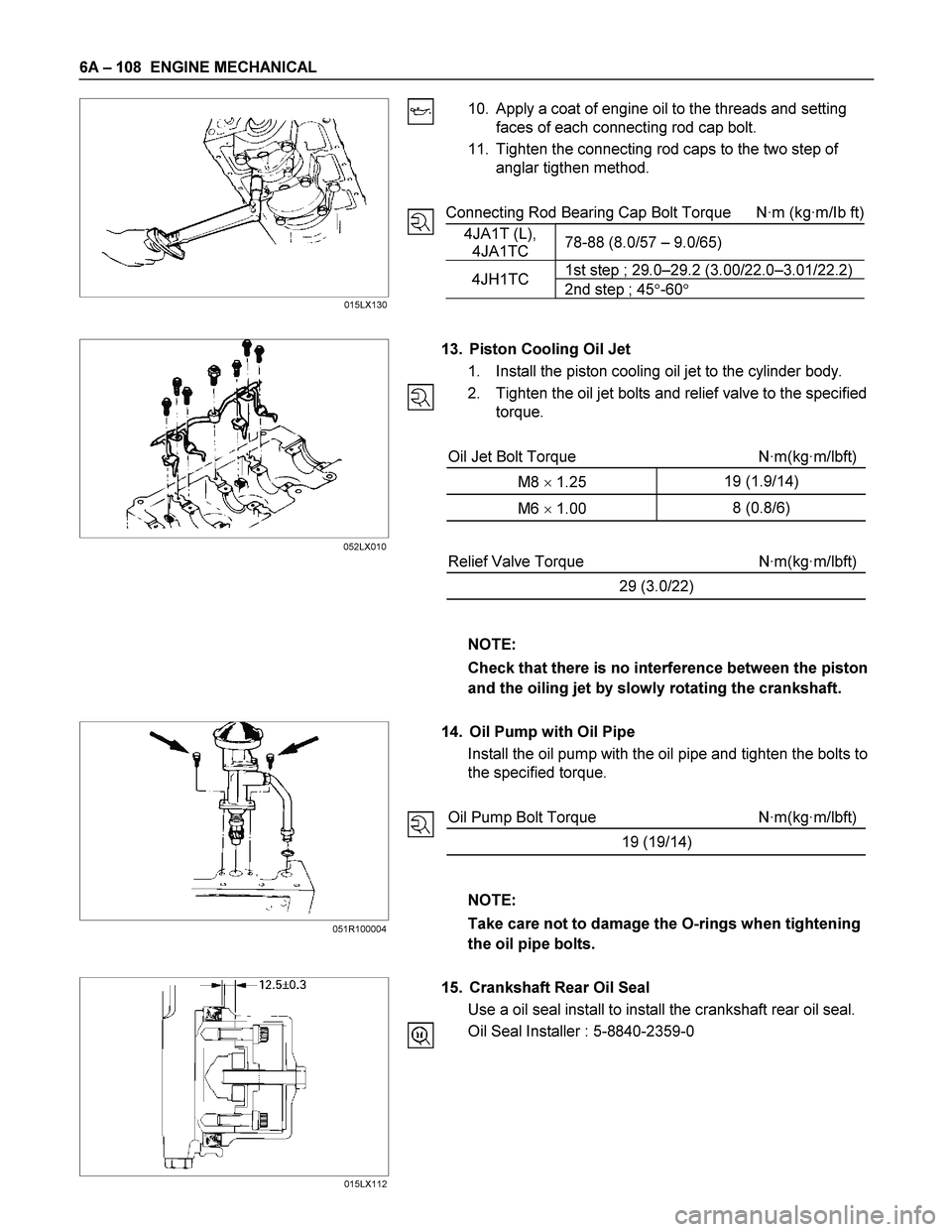
6A – 108 ENGINE MECHANICAL
10. Apply a coat of engine oil to the threads and setting
faces of each connecting rod cap bolt.
11. Tighten the connecting rod caps to the two step of
anglar tigthen method.
Connecting Rod Bearing Cap Bolt Torque N·m (kg·m/Ib ft)
4JA1T (L),
4JA1TC 78-88 (8.0/57 – 9.0/65)
1st step ; 29.0–29.2 (3.00/22.0–3.01/22.2)4JH1TC
2nd step ; 45-60
13. Piston Cooling Oil Jet
1. Install the piston cooling oil jet to the cylinder body.
2. Tighten the oil jet bolts and relief valve to the specified
torque.
Oil Jet Bolt Torque N·m(kg·m/lbft)
M8 1.25 19 (1.9/14)
M6 1.00 8 (0.8/6)
Relief Valve Torque N·m(kg·m/lbft)
29 (3.0/22)
NOTE:
Check that there is no interference between the piston
and the oiling jet by slowly rotating the crankshaft.
14. Oil Pump with Oil Pipe
Install the oil pump with the oil pipe and tighten the bolts to
the specified torque.
Oil Pump Bolt Torque N·m(kg·m/lbft)
19 (19/14)
NOTE:
Take care not to damage the O-rings when tightening
the oil pipe bolts.
15. Crankshaft Rear Oil Seal
Use a oil seal install to install the crankshaft rear oil seal.
Oil Seal Installer : 5-8840-2359-0
015LX130
015LX112 052LX010
051R100004
Page 1257 of 4264
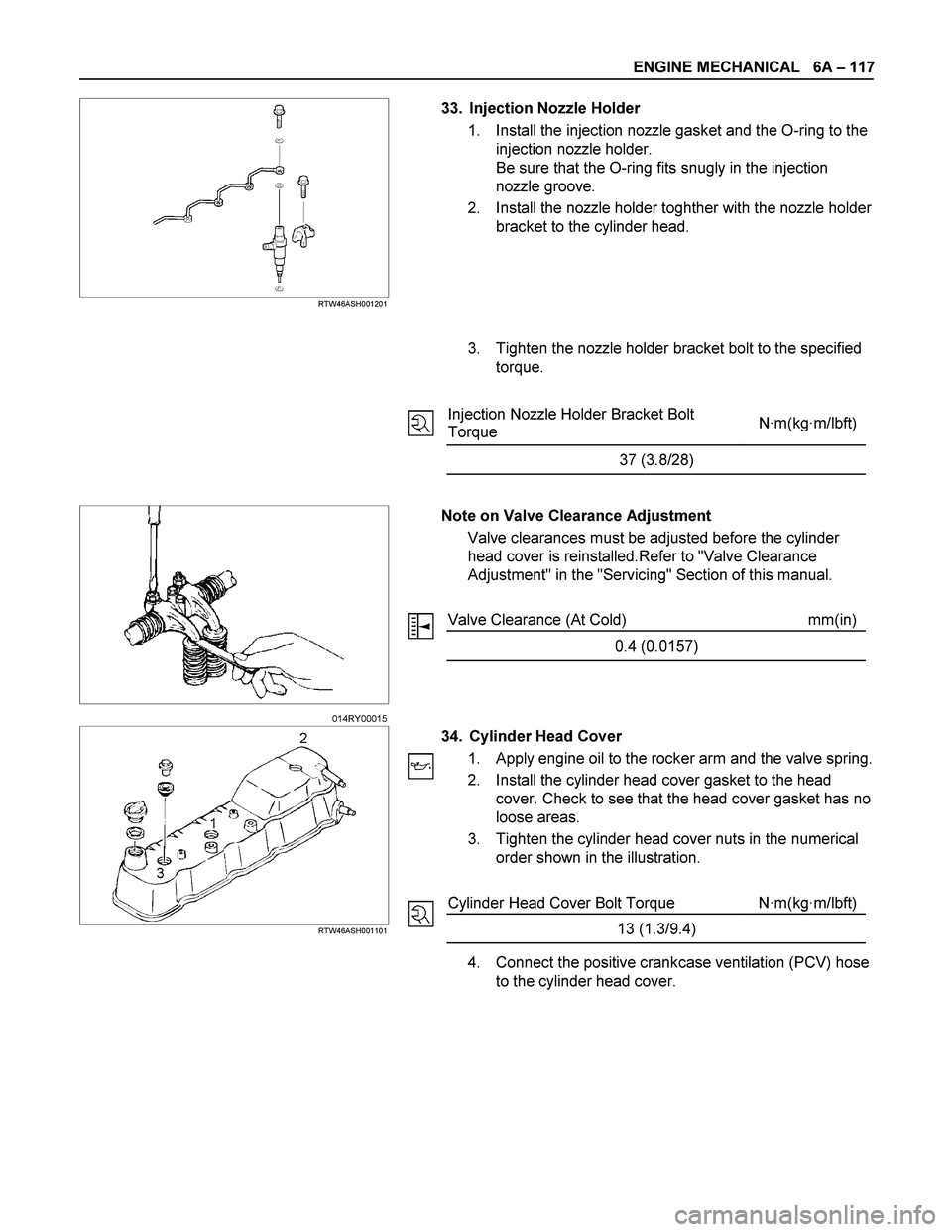
ENGINE MECHANICAL 6A – 117
RTW46ASH001201
33. Injection Nozzle Holder
1. Install the injection nozzle gasket and the O-ring to the
injection nozzle holder.
Be sure that the O-ring fits snugly in the injection
nozzle groove.
2. Install the nozzle holder toghther with the nozzle holder
bracket to the cylinder head.
3. Tighten the nozzle holder bracket bolt to the specified
torque.
Injection Nozzle Holder Bracket Bolt
Torque N·m(kg·m/lbft)
37 (3.8/28)
Note on Valve Clearance Adjustment
Valve clearances must be adjusted before the cylinder
head cover is reinstalled.Refer to "Valve Clearance
Adjustment" in the "Servicing" Section of this manual.
Valve Clearance (At Cold) mm(in)
0.4 (0.0157)
RTW46ASH001101
34. Cylinder Head Cover
1. Apply engine oil to the rocker arm and the valve spring.
2. Install the cylinder head cover gasket to the head
cover. Check to see that the head cover gasket has no
loose areas.
3. Tighten the cylinder head cover nuts in the numerical
order shown in the illustration.
Cylinder Head Cover Bolt Torque N·m(kg·m/lbft)
13 (1.3/9.4)
4. Connect the positive crankcase ventilation (PCV) hose
to the cylinder head cover.
014RY00015