technical data JAGUAR XF 2009 1.G AJ133 5.0L Engine Manual
[x] Cancel search | Manufacturer: JAGUAR, Model Year: 2009, Model line: XF, Model: JAGUAR XF 2009 1.GPages: 36, PDF Size: 0.38 MB
Page 17 of 36
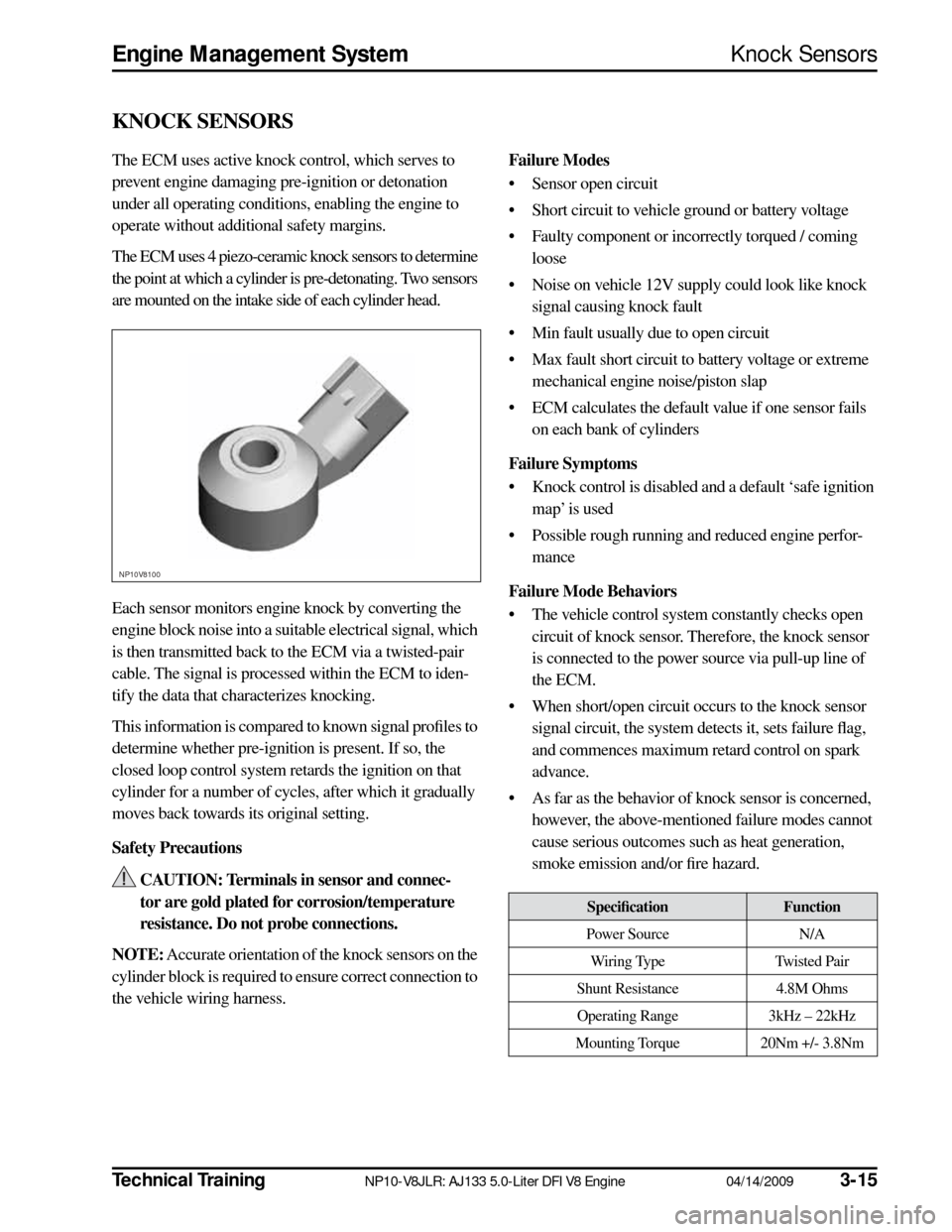
Technical Training
NP10-V8JLR: AJ133 5.0-Liter DFI V8 Engine 04/14/2009
3-15
Engine Management System
Knock Sensors
KNOCK SENSORS
The ECM uses active knock control, which serves to
prevent engine damaging pre-ignition or detonation
under all operating conditions, enabling the engine to
operate without additional safety margins.
The ECM uses 4 piezo-ceramic knock sensors to determine
the point at which a cylinder is pre-detonating. Two sensors
are mounted on the intake side of each cylinder head.
Each sensor monitors engine knock by converting the
engine block noise into a suitable electrical signal, which
is then transmitted back to the ECM via a twisted-pair
cable. The signal is processed within the ECM to iden-
tify the data that characterizes knocking.
This information is compared to known signal profiles to
determine whether pre-ignition is present. If so, the
closed loop control system retards the ignition on that
cylinder for a number of cycles, after which it gradually
moves back towards its original setting.
Safety Precautions CAUTION: Terminals in sensor and connec-
tor are gold plated for corrosion/temperature
resistance. Do not probe connections.
NOTE:
Accurate orientation of the knock sensors on the
cylinder block is required to ensure correct connection to
the vehicle wiring harness.
Failure Modes
• Sensor open circuit
• Short circuit to vehicle ground or battery voltage
• Faulty component or incorrectly torqued / coming loose
• Noise on vehicle 12V supply could look like knock signal causing knock fault
• Min fault usually due to open circuit
• Max fault short circuit to battery voltage or extreme mechanical engine noise/piston slap
• ECM calculates the default value if one sensor fails on each bank of cylinders
Failure Symptoms
• Knock control is disabled and a default ‘safe ignition map’ is used
• Possible rough running and reduced engine perfor- mance
Failure Mode Behaviors
• The vehicle control system constantly checks open circuit of knock sensor. Therefore, the knock sensor
is connected to the power source via pull-up line of
the ECM.
• When short/open circuit occurs to the knock sensor signal circuit, the system detects it, sets failure flag,
and commences maximum retard control on spark
advance.
• As far as the behavior of knock sensor is concerned, however, the above-mentioned failure modes cannot
cause serious outcomes such as heat generation,
smoke emission and/or fire hazard.
NP10V8100
Specification
Function
Power Source N/A
Wiring Type Twisted Pair
Shunt Resistance 4.8M Ohms
Operating Range 3kHz – 22kHz
Mounting Torque 20Nm +/- 3.8Nm
Page 32 of 36
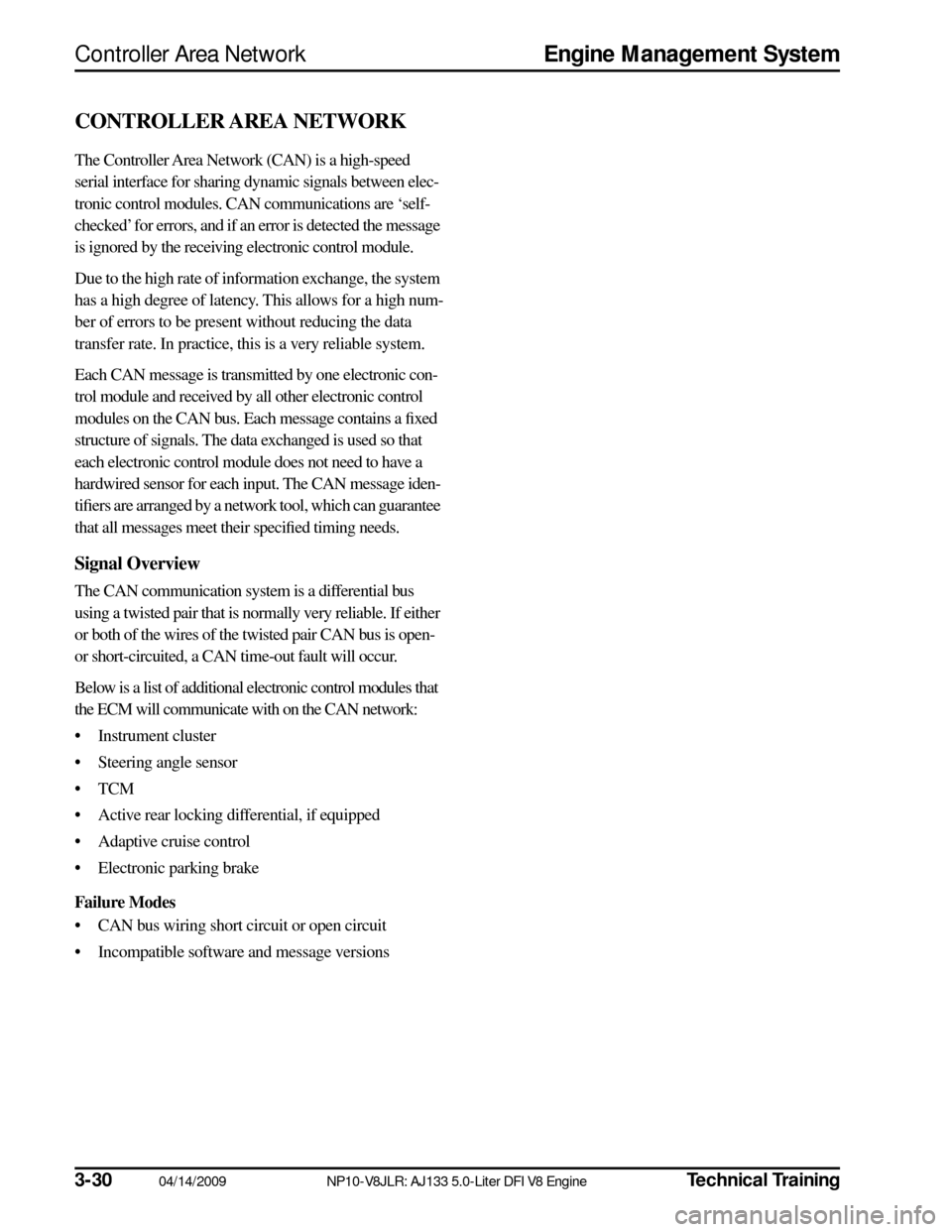
3-3004/14/2009NP10-V8JLR: AJ133 5.0-Liter DFI V8 EngineTechnical Training
Controller Area Network Engine Management System
CONTROLLER AREA NETWORK
The Controller Area Network (CAN) is a high-speed
serial interface for sharing dynamic signals between elec-
tronic control modules. CAN communications are ‘self-
checked’ for errors, and if an error is detected the message
is ignored by the receiving electronic control module.
Due to the high rate of information exchange, the system
has a high degree of latency. This allows for a high num-
ber of errors to be present without reducing the data
transfer rate. In practice, this is a very reliable system.
Each CAN message is transmitted by one electronic con-
trol module and received by all other electronic control
modules on the CAN bus. Each message contains a fixed
structure of signals. The data exchanged is used so that
each electronic control module does not need to have a
hardwired sensor for each input. The CAN message iden-
tifiers are arranged by a network tool, which can guarantee
that all messages meet their specified timing needs.
Signal Overview
The CAN communication system is a differential bus
using a twisted pair that is normally very reliable. If either
or both of the wires of the twisted pair CAN bus is open-
or short-circuited, a CAN time-out fault will occur.
Below is a list of additional electronic control modules that
the ECM will communicate with on the CAN network:
• Instrument cluster
• Steering angle sensor
•TCM
• Active rear locking differential, if equipped
• Adaptive cruise control
• Electronic parking brake
Failure Modes
• CAN bus wiring short circuit or open circuit
• Incompatible software and message versions