Intake JAGUAR XFR 2010 1.G Manual Online
[x] Cancel search | Manufacturer: JAGUAR, Model Year: 2010, Model line: XFR, Model: JAGUAR XFR 2010 1.GPages: 3039, PDF Size: 58.49 MB
Page 1364 of 3039
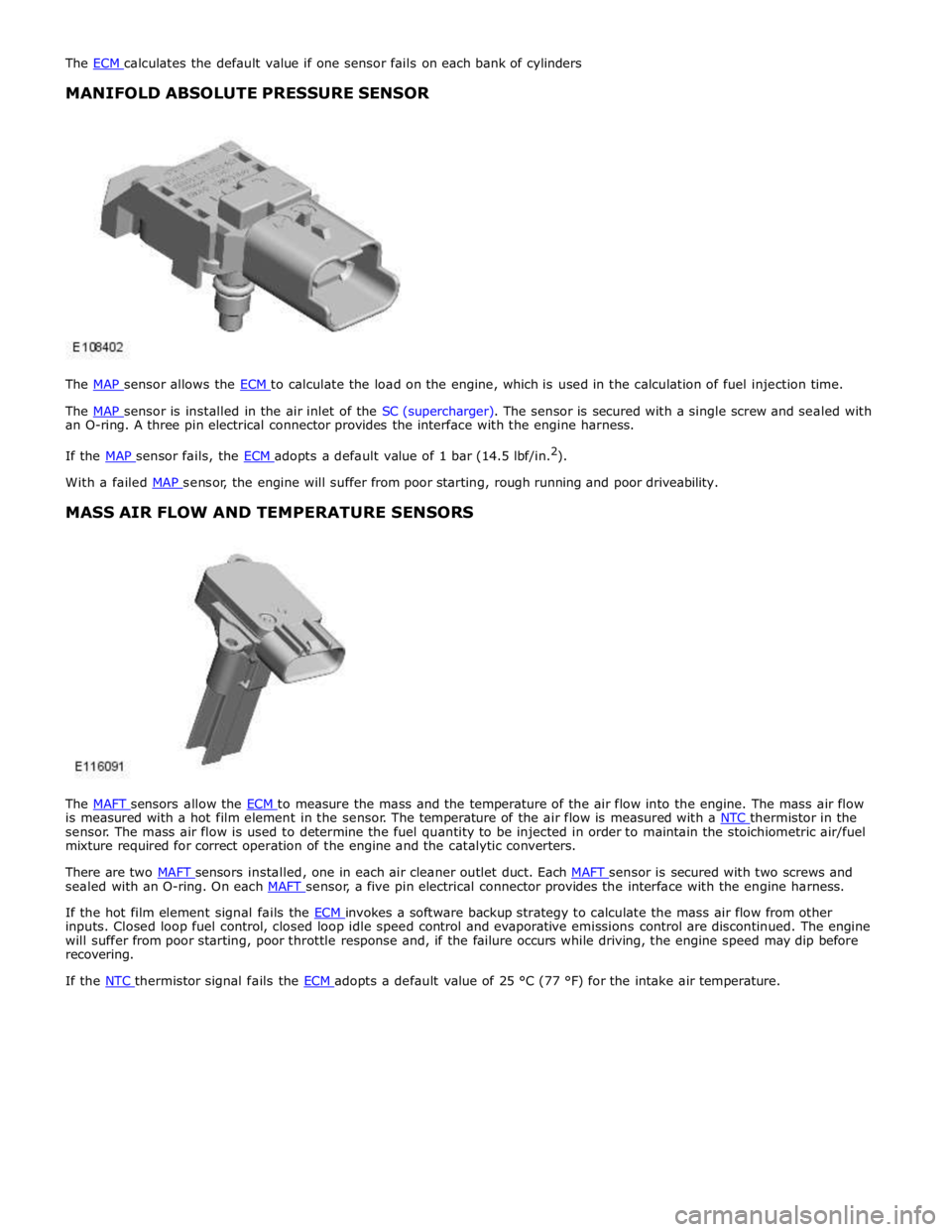
MANIFOLD ABSOLUTE PRESSURE SENSOR
The MAP sensor allows the ECM to calculate the load on the engine, which is used in the calculation of fuel injection time.
The MAP sensor is installed in the air inlet of the SC (supercharger). The sensor is secured with a single screw and sealed with an O-ring. A three pin electrical connector provides the interface with the engine harness.
If the MAP sensor fails, the ECM adopts a default value of 1 bar (14.5 lbf/in.2
). With a failed MAP sensor, the engine will suffer from poor starting, rough running and poor driveability.
MASS AIR FLOW AND TEMPERATURE SENSORS
The MAFT sensors allow the ECM to measure the mass and the temperature of the air flow into the engine. The mass air flow is measured with a hot film element in the sensor. The temperature of the air flow is measured with a NTC thermistor in the sensor. The mass air flow is used to determine the fuel quantity to be injected in order to maintain the stoichiometric air/fuel
mixture required for correct operation of the engine and the catalytic converters.
There are two MAFT sensors installed, one in each air cleaner outlet duct. Each MAFT sensor is secured with two screws and sealed with an O-ring. On each MAFT sensor, a five pin electrical connector provides the interface with the engine harness.
If the hot film element signal fails the ECM invokes a software backup strategy to calculate the mass air flow from other inputs. Closed loop fuel control, closed loop idle speed control and evaporative emissions control are discontinued. The engine
will suffer from poor starting, poor throttle response and, if the failure occurs while driving, the engine speed may dip before
recovering.
If the NTC thermistor signal fails the ECM adopts a default value of 25 °C (77 °F) for the intake air temperature.
Page 1365 of 3039
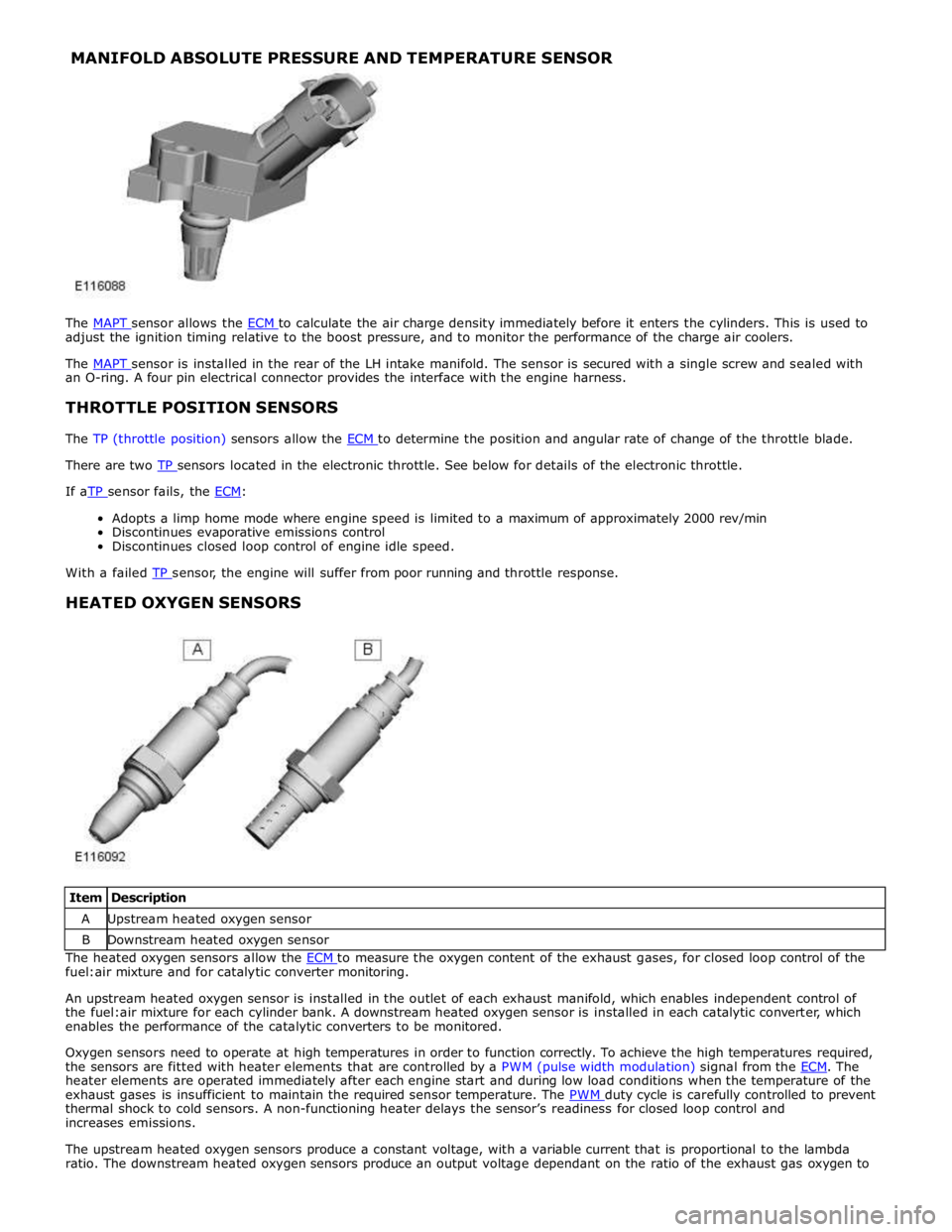
MANIFOLD ABSOLUTE PRESSURE AND TEMPERATURE SENSOR
The MAPT sensor allows the ECM to calculate the air charge density immediately before it enters the cylinders. This is used to adjust the ignition timing relative to the boost pressure, and to monitor the performance of the charge air coolers.
The MAPT sensor is installed in the rear of the LH intake manifold. The sensor is secured with a single screw and sealed with an O-ring. A four pin electrical connector provides the interface with the engine harness.
THROTTLE POSITION SENSORS
The TP (throttle position) sensors allow the ECM to determine the position and angular rate of change of the throttle blade. There are two TP sensors located in the electronic throttle. See below for details of the electronic throttle. If aTP sensor fails, the ECM:
Adopts a limp home mode where engine speed is limited to a maximum of approximately 2000 rev/min
Discontinues evaporative emissions control
Discontinues closed loop control of engine idle speed.
With a failed TP sensor, the engine will suffer from poor running and throttle response.
HEATED OXYGEN SENSORS
Item Description A Upstream heated oxygen sensor B Downstream heated oxygen sensor The heated oxygen sensors allow the ECM to measure the oxygen content of the exhaust gases, for closed loop control of the fuel:air mixture and for catalytic converter monitoring.
An upstream heated oxygen sensor is installed in the outlet of each exhaust manifold, which enables independent control of
the fuel:air mixture for each cylinder bank. A downstream heated oxygen sensor is installed in each catalytic converter, which
enables the performance of the catalytic converters to be monitored.
Oxygen sensors need to operate at high temperatures in order to function correctly. To achieve the high temperatures required,
the sensors are fitted with heater elements that are controlled by a PWM (pulse width modulation) signal from the ECM. The heater elements are operated immediately after each engine start and during low load conditions when the temperature of the
exhaust gases is insufficient to maintain the required sensor temperature. The PWM duty cycle is carefully controlled to prevent thermal shock to cold sensors. A non-functioning heater delays the sensor’s readiness for closed loop control and
increases emissions.
The upstream heated oxygen sensors produce a constant voltage, with a variable current that is proportional to the lambda
ratio. The downstream heated oxygen sensors produce an output voltage dependant on the ratio of the exhaust gas oxygen to
Page 1367 of 3039
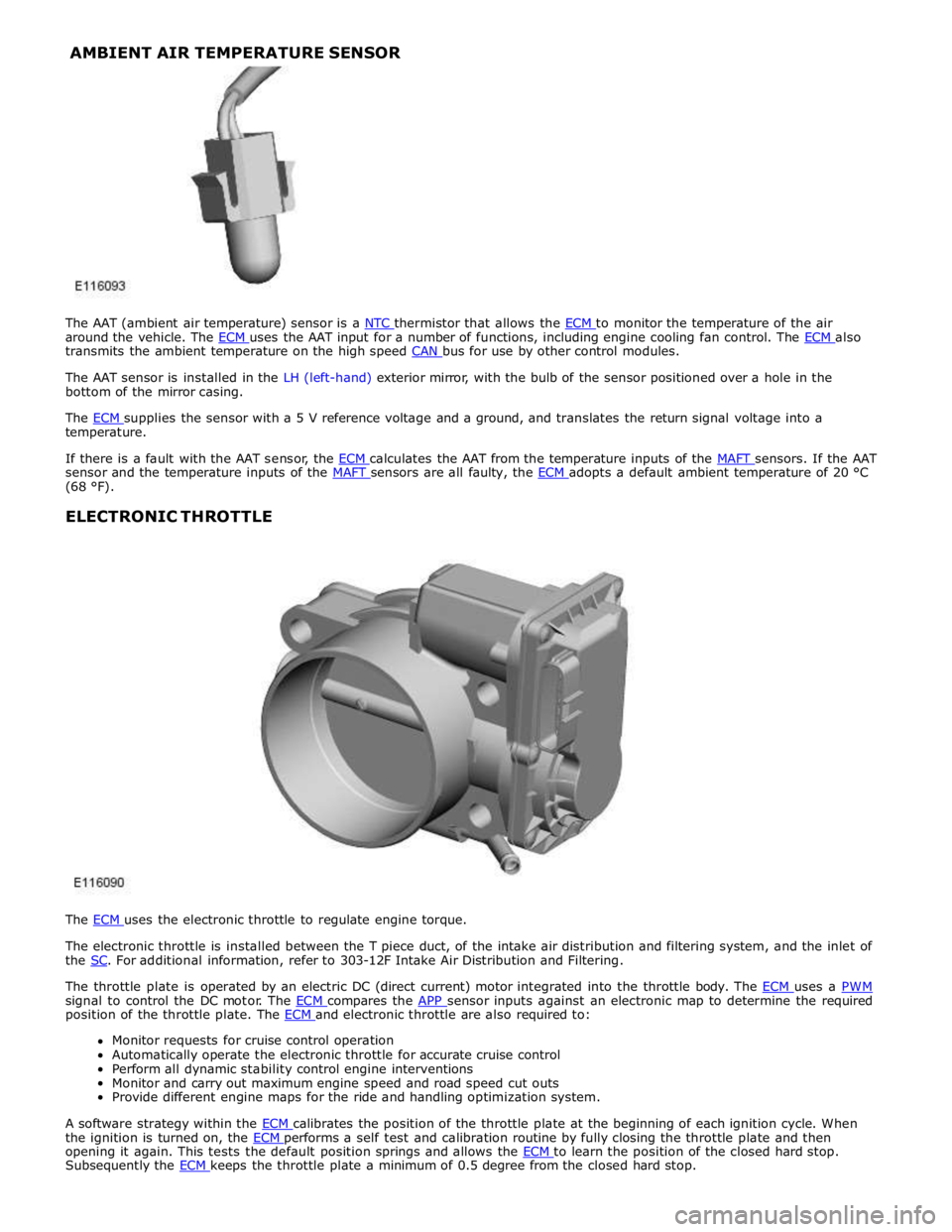
around the vehicle. The ECM uses the AAT input for a number of functions, including engine cooling fan control. The ECM also transmits the ambient temperature on the high speed CAN bus for use by other control modules.
The AAT sensor is installed in the LH (left-hand) exterior mirror, with the bulb of the sensor positioned over a hole in the
bottom of the mirror casing.
The ECM supplies the sensor with a 5 V reference voltage and a ground, and translates the return signal voltage into a temperature.
If there is a fault with the AAT sensor, the ECM calculates the AAT from the temperature inputs of the MAFT sensors. If the AAT sensor and the temperature inputs of the MAFT sensors are all faulty, the ECM adopts a default ambient temperature of 20 °C (68 °F).
ELECTRONIC THROTTLE
The ECM uses the electronic throttle to regulate engine torque.
The electronic throttle is installed between the T piece duct, of the intake air distribution and filtering system, and the inlet of
the SC. For additional information, refer to 303-12F Intake Air Distribution and Filtering.
The throttle plate is operated by an electric DC (direct current) motor integrated into the throttle body. The ECM uses a PWM signal to control the DC motor. The ECM compares the APP sensor inputs against an electronic map to determine the required position of the throttle plate. The ECM and electronic throttle are also required to: Monitor requests for cruise control operation
Automatically operate the electronic throttle for accurate cruise control
Perform all dynamic stability control engine interventions
Monitor and carry out maximum engine speed and road speed cut outs
Provide different engine maps for the ride and handling optimization system.
A software strategy within the ECM calibrates the position of the throttle plate at the beginning of each ignition cycle. When the ignition is turned on, the ECM performs a self test and calibration routine by fully closing the throttle plate and then opening it again. This tests the default position springs and allows the ECM to learn the position of the closed hard stop. Subsequently the ECM keeps the throttle plate a minimum of 0.5 degree from the closed hard stop. AMBIENT AIR TEMPERATURE SENSOR
Page 1370 of 3039
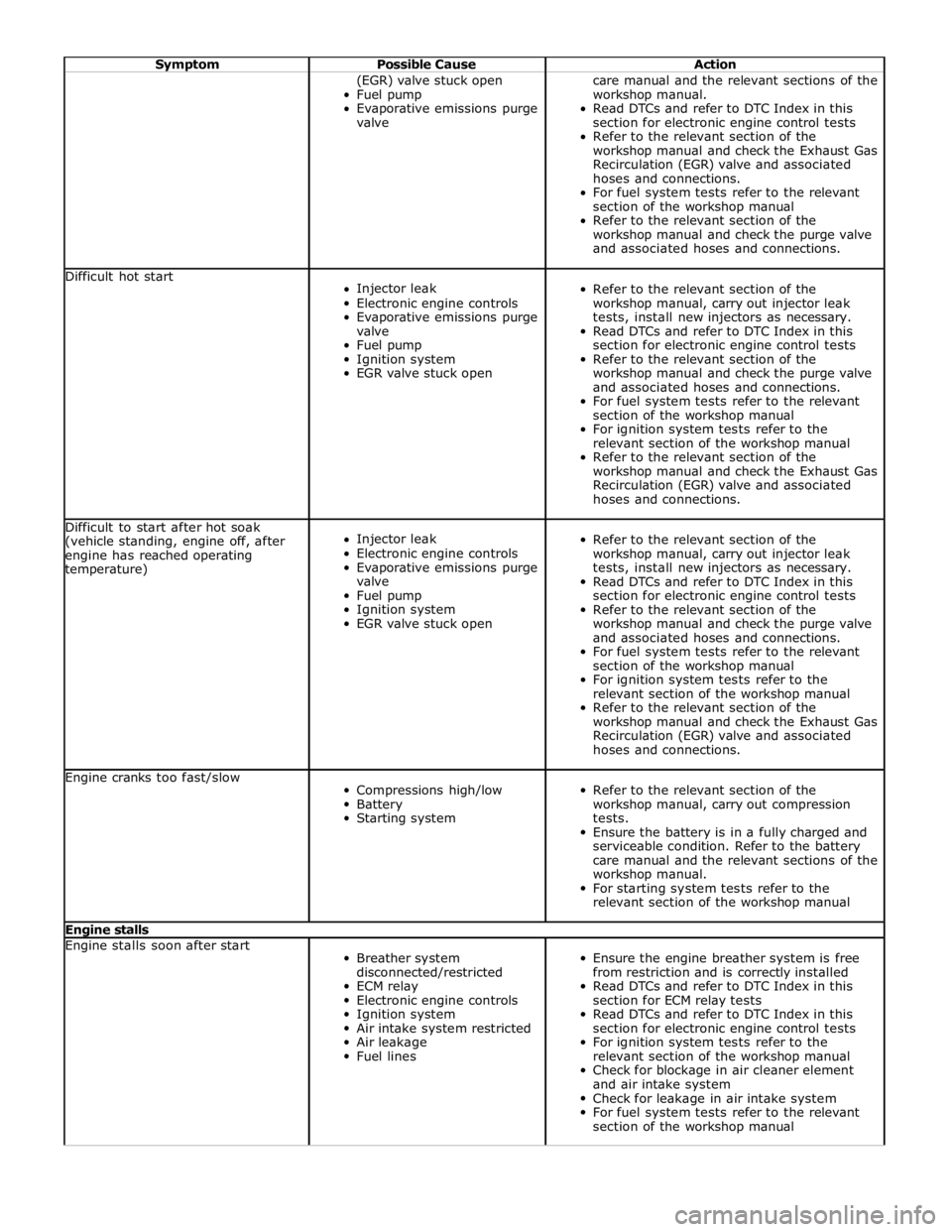
Symptom Possible Cause Action (EGR) valve stuck open
Fuel pump
Evaporative emissions purge
valve care manual and the relevant sections of the
workshop manual.
Read DTCs and refer to DTC Index in this
section for electronic engine control tests
Refer to the relevant section of the
workshop manual and check the Exhaust Gas
Recirculation (EGR) valve and associated
hoses and connections.
For fuel system tests refer to the relevant
section of the workshop manual
Refer to the relevant section of the
workshop manual and check the purge valve
and associated hoses and connections. Difficult hot start
Injector leak
Electronic engine controls
Evaporative emissions purge
valve
Fuel pump
Ignition system
EGR valve stuck open
Refer to the relevant section of the
workshop manual, carry out injector leak
tests, install new injectors as necessary.
Read DTCs and refer to DTC Index in this
section for electronic engine control tests
Refer to the relevant section of the
workshop manual and check the purge valve
and associated hoses and connections.
For fuel system tests refer to the relevant
section of the workshop manual
For ignition system tests refer to the
relevant section of the workshop manual
Refer to the relevant section of the
workshop manual and check the Exhaust Gas
Recirculation (EGR) valve and associated
hoses and connections. Difficult to start after hot soak
(vehicle standing, engine off, after
engine has reached operating
temperature)
Injector leak
Electronic engine controls
Evaporative emissions purge
valve
Fuel pump
Ignition system
EGR valve stuck open
Refer to the relevant section of the
workshop manual, carry out injector leak
tests, install new injectors as necessary.
Read DTCs and refer to DTC Index in this
section for electronic engine control tests
Refer to the relevant section of the
workshop manual and check the purge valve
and associated hoses and connections.
For fuel system tests refer to the relevant
section of the workshop manual
For ignition system tests refer to the
relevant section of the workshop manual
Refer to the relevant section of the
workshop manual and check the Exhaust Gas
Recirculation (EGR) valve and associated
hoses and connections. Engine cranks too fast/slow
Compressions high/low
Battery
Starting system
Refer to the relevant section of the
workshop manual, carry out compression
tests.
Ensure the battery is in a fully charged and
serviceable condition. Refer to the battery
care manual and the relevant sections of the
workshop manual.
For starting system tests refer to the
relevant section of the workshop manual Engine stalls Engine stalls soon after start
Breather system
disconnected/restricted
ECM relay
Electronic engine controls
Ignition system
Air intake system restricted
Air leakage
Fuel lines
Ensure the engine breather system is free
from restriction and is correctly installed
Read DTCs and refer to DTC Index in this
section for ECM relay tests
Read DTCs and refer to DTC Index in this
section for electronic engine control tests
For ignition system tests refer to the
relevant section of the workshop manual
Check for blockage in air cleaner element
and air intake system
Check for leakage in air intake system
For fuel system tests refer to the relevant
section of the workshop manual
Page 1371 of 3039
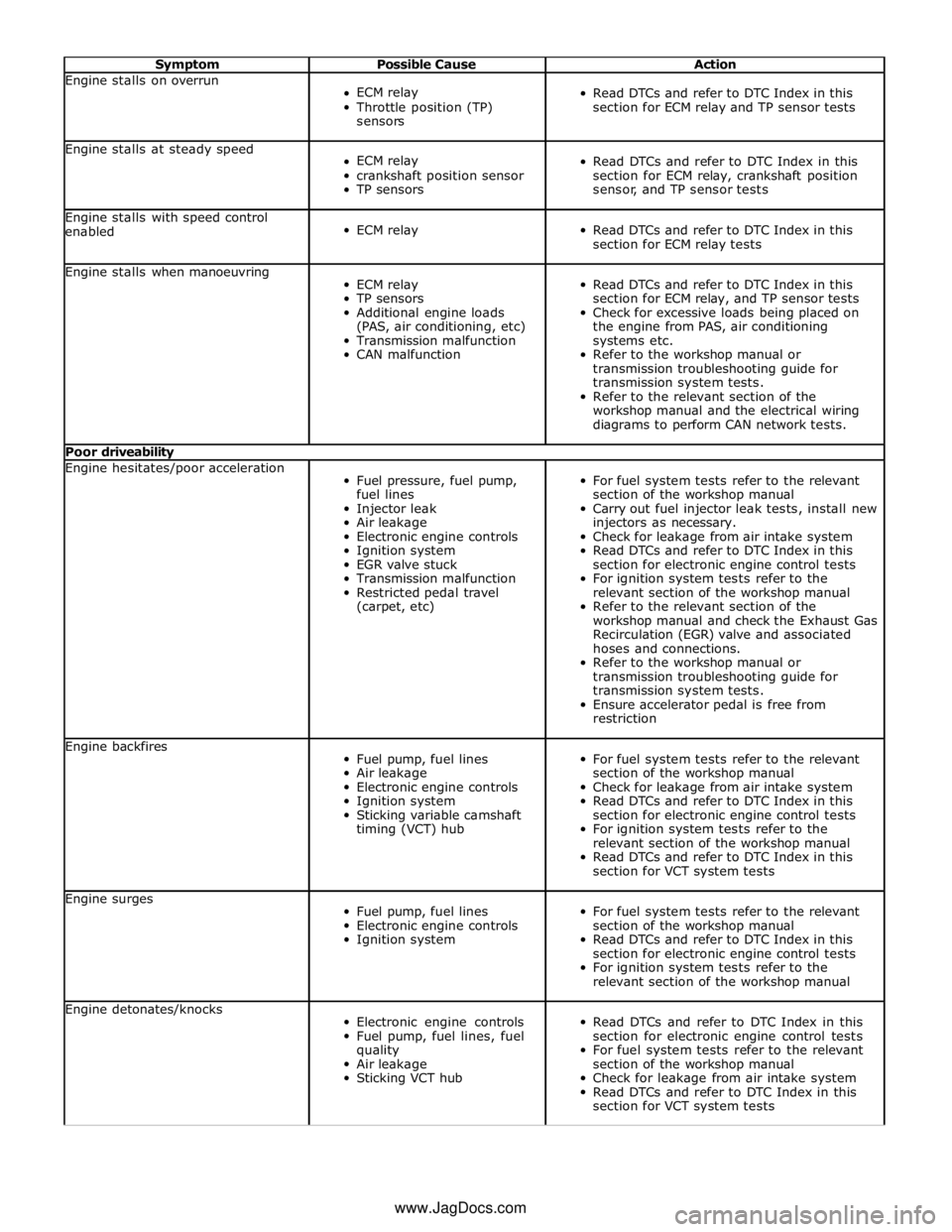
Symptom Possible Cause Action Engine stalls on overrun
ECM relay
Throttle position (TP)
sensors
Read DTCs and refer to DTC Index in this
section for ECM relay and TP sensor tests Engine stalls at steady speed
ECM relay
crankshaft position sensor
TP sensors
Read DTCs and refer to DTC Index in this
section for ECM relay, crankshaft position
sensor, and TP sensor tests Engine stalls with speed control
enabled
ECM relay
Read DTCs and refer to DTC Index in this
section for ECM relay tests Engine stalls when manoeuvring
ECM relay
TP sensors
Additional engine loads
(PAS, air conditioning, etc)
Transmission malfunction
CAN malfunction
Read DTCs and refer to DTC Index in this
section for ECM relay, and TP sensor tests
Check for excessive loads being placed on
the engine from PAS, air conditioning
systems etc.
Refer to the workshop manual or
transmission troubleshooting guide for
transmission system tests.
Refer to the relevant section of the
workshop manual and the electrical wiring
diagrams to perform CAN network tests. Poor driveability Engine hesitates/poor acceleration
Fuel pressure, fuel pump,
fuel lines
Injector leak
Air leakage
Electronic engine controls
Ignition system
EGR valve stuck
Transmission malfunction
Restricted pedal travel
(carpet, etc)
For fuel system tests refer to the relevant
section of the workshop manual
Carry out fuel injector leak tests, install new
injectors as necessary.
Check for leakage from air intake system
Read DTCs and refer to DTC Index in this
section for electronic engine control tests
For ignition system tests refer to the
relevant section of the workshop manual
Refer to the relevant section of the
workshop manual and check the Exhaust Gas
Recirculation (EGR) valve and associated
hoses and connections.
Refer to the workshop manual or
transmission troubleshooting guide for
transmission system tests.
Ensure accelerator pedal is free from
restriction Engine backfires
Fuel pump, fuel lines
Air leakage
Electronic engine controls
Ignition system
Sticking variable camshaft
timing (VCT) hub
For fuel system tests refer to the relevant
section of the workshop manual
Check for leakage from air intake system
Read DTCs and refer to DTC Index in this
section for electronic engine control tests
For ignition system tests refer to the
relevant section of the workshop manual
Read DTCs and refer to DTC Index in this
section for VCT system tests Engine surges
Fuel pump, fuel lines
Electronic engine controls
Ignition system
For fuel system tests refer to the relevant
section of the workshop manual
Read DTCs and refer to DTC Index in this
section for electronic engine control tests
For ignition system tests refer to the
relevant section of the workshop manual Engine detonates/knocks
Electronic engine controls
Fuel pump, fuel lines, fuel
quality
Air leakage
Sticking VCT hub
Read DTCs and refer to DTC Index in this
section for electronic engine control tests
For fuel system tests refer to the relevant
section of the workshop manual
Check for leakage from air intake system
Read DTCs and refer to DTC Index in this
section for VCT system tests www.JagDocs.com
Page 1372 of 3039
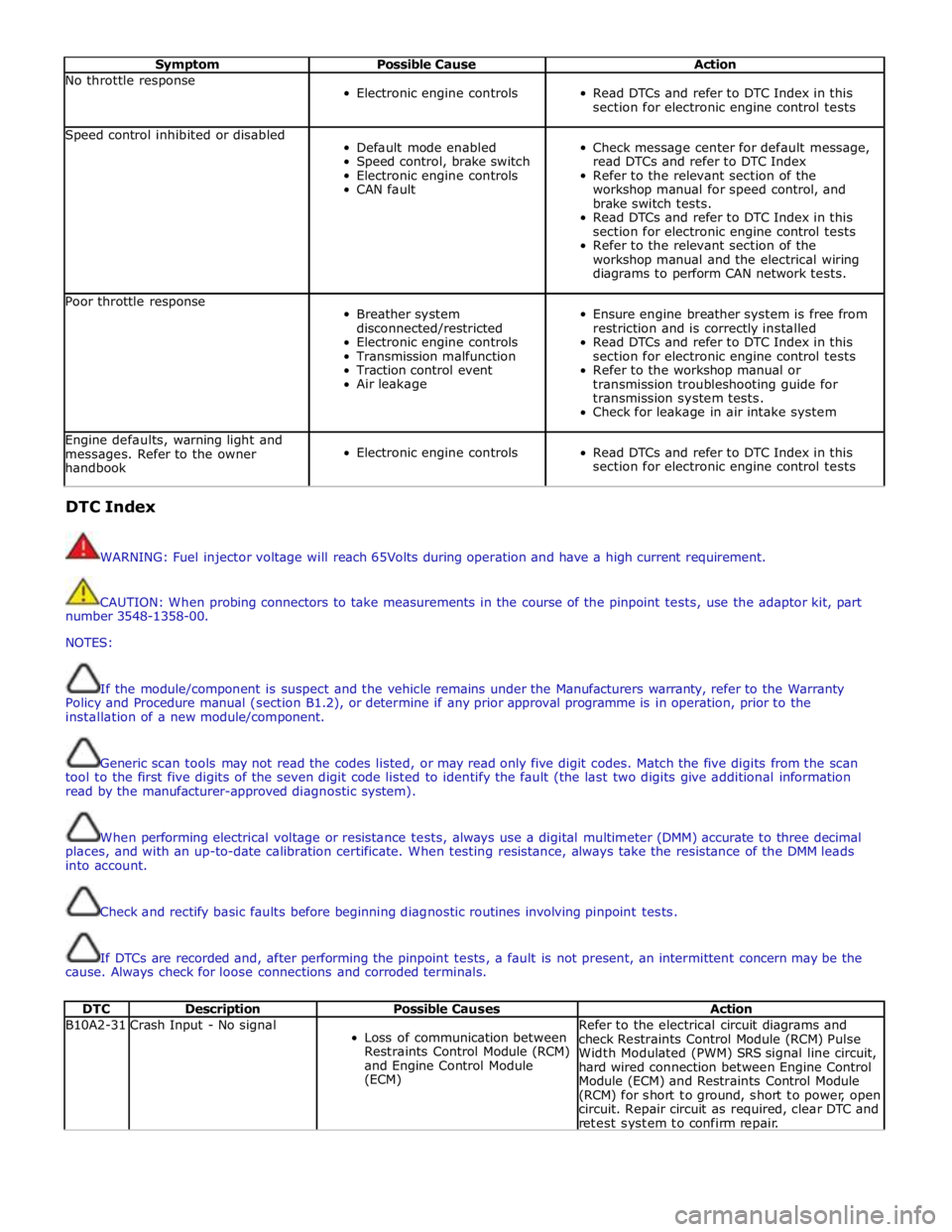
Symptom Possible Cause Action No throttle response
Electronic engine controls
Read DTCs and refer to DTC Index in this
section for electronic engine control tests Speed control inhibited or disabled
Default mode enabled
Speed control, brake switch
Electronic engine controls
CAN fault
Check message center for default message,
read DTCs and refer to DTC Index
Refer to the relevant section of the
workshop manual for speed control, and
brake switch tests.
Read DTCs and refer to DTC Index in this
section for electronic engine control tests
Refer to the relevant section of the
workshop manual and the electrical wiring
diagrams to perform CAN network tests. Poor throttle response
Breather system
disconnected/restricted
Electronic engine controls
Transmission malfunction
Traction control event
Air leakage
Ensure engine breather system is free from
restriction and is correctly installed
Read DTCs and refer to DTC Index in this
section for electronic engine control tests
Refer to the workshop manual or
transmission troubleshooting guide for
transmission system tests.
Check for leakage in air intake system Engine defaults, warning light and
messages. Refer to the owner
handbook
Electronic engine controls
Read DTCs and refer to DTC Index in this
section for electronic engine control tests DTC Index
WARNING: Fuel injector voltage will reach 65Volts during operation and have a high current requirement.
CAUTION: When probing connectors to take measurements in the course of the pinpoint tests, use the adaptor kit, part
number 3548-1358-00.
NOTES:
If the module/component is suspect and the vehicle remains under the Manufacturers warranty, refer to the Warranty
Policy and Procedure manual (section B1.2), or determine if any prior approval programme is in operation, prior to the
installation of a new module/component.
Generic scan tools may not read the codes listed, or may read only five digit codes. Match the five digits from the scan
tool to the first five digits of the seven digit code listed to identify the fault (the last two digits give additional information
read by the manufacturer-approved diagnostic system).
When performing electrical voltage or resistance tests, always use a digital multimeter (DMM) accurate to three decimal
places, and with an up-to-date calibration certificate. When testing resistance, always take the resistance of the DMM leads
into account.
Check and rectify basic faults before beginning diagnostic routines involving pinpoint tests.
If DTCs are recorded and, after performing the pinpoint tests, a fault is not present, an intermittent concern may be the
cause. Always check for loose connections and corroded terminals.
DTC Description Possible Causes Action B10A2-31 Crash Input - No signal
Loss of communication between
Restraints Control Module (RCM)
and Engine Control Module
(ECM) Refer to the electrical circuit diagrams and
check Restraints Control Module (RCM) Pulse
Width Modulated (PWM) SRS signal line circuit,
hard wired connection between Engine Control
Module (ECM) and Restraints Control Module
(RCM) for short to ground, short to power, open
circuit. Repair circuit as required, clear DTC and
retest system to confirm repair.
Page 1390 of 3039
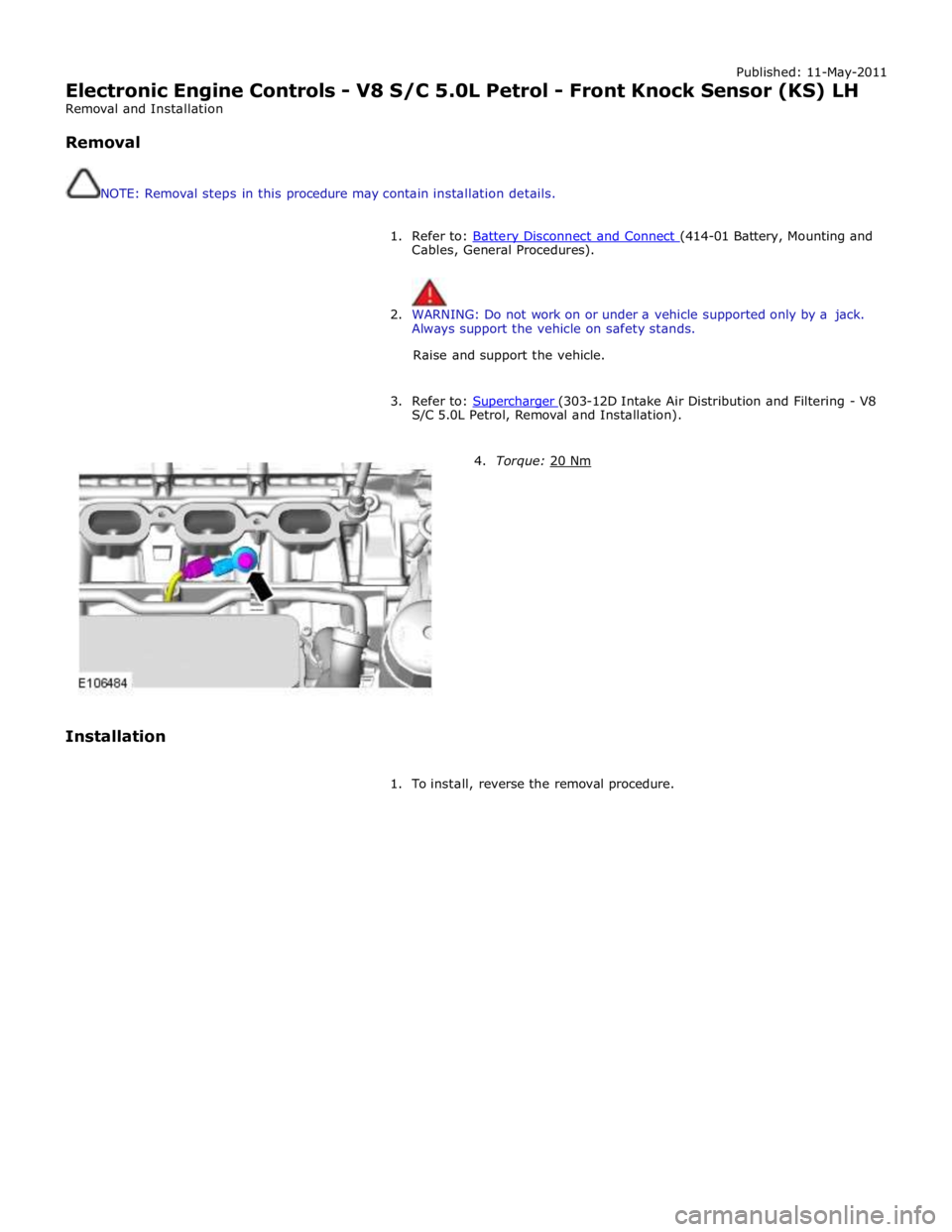
Published: 11-May-2011
Electronic Engine Controls - V8 S/C 5.0L Petrol - Front Knock Sensor (KS) LH
Removal and Installation
Removal
NOTE: Removal steps in this procedure may contain installation details.
1. Refer to: Battery Disconnect and Connect (414-01 Battery, Mounting and Cables, General Procedures).
2. WARNING: Do not work on or under a vehicle supported only by a jack.
Always support the vehicle on safety stands.
Raise and support the vehicle.
3. Refer to: Supercharger (303-12D Intake Air Distribution and Filtering - V8 S/C 5.0L Petrol, Removal and Installation).
Installation
4. Torque: 20 Nm
1. To install, reverse the removal procedure.
Page 1391 of 3039
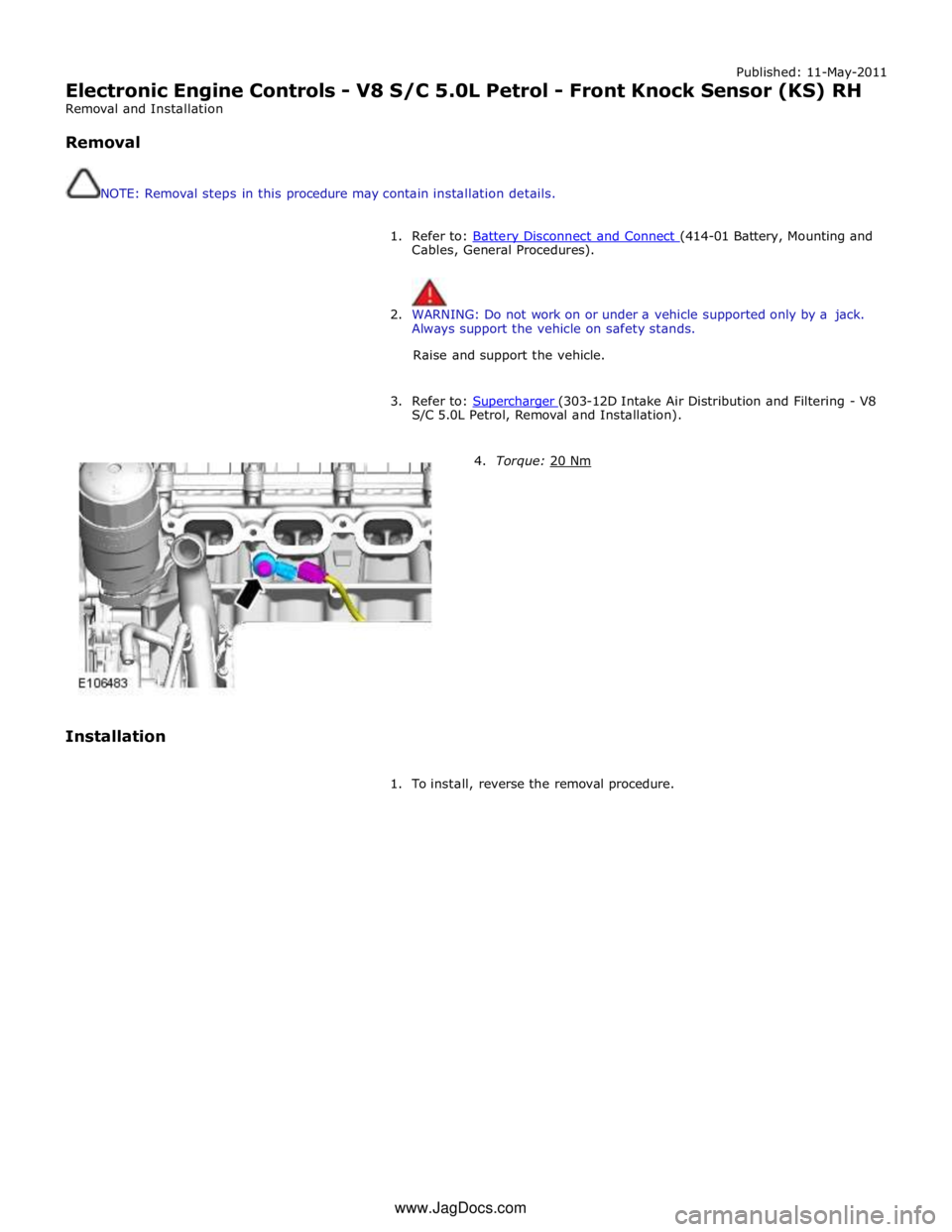
Published: 11-May-2011
Electronic Engine Controls - V8 S/C 5.0L Petrol - Front Knock Sensor (KS) RH
Removal and Installation
Removal
NOTE: Removal steps in this procedure may contain installation details.
1. Refer to: Battery Disconnect and Connect (414-01 Battery, Mounting and Cables, General Procedures).
2. WARNING: Do not work on or under a vehicle supported only by a jack.
Always support the vehicle on safety stands.
Raise and support the vehicle.
3. Refer to: Supercharger (303-12D Intake Air Distribution and Filtering - V8 S/C 5.0L Petrol, Removal and Installation).
Installation
4. Torque: 20 Nm
1. To install, reverse the removal procedure. www.JagDocs.com
Page 1402 of 3039
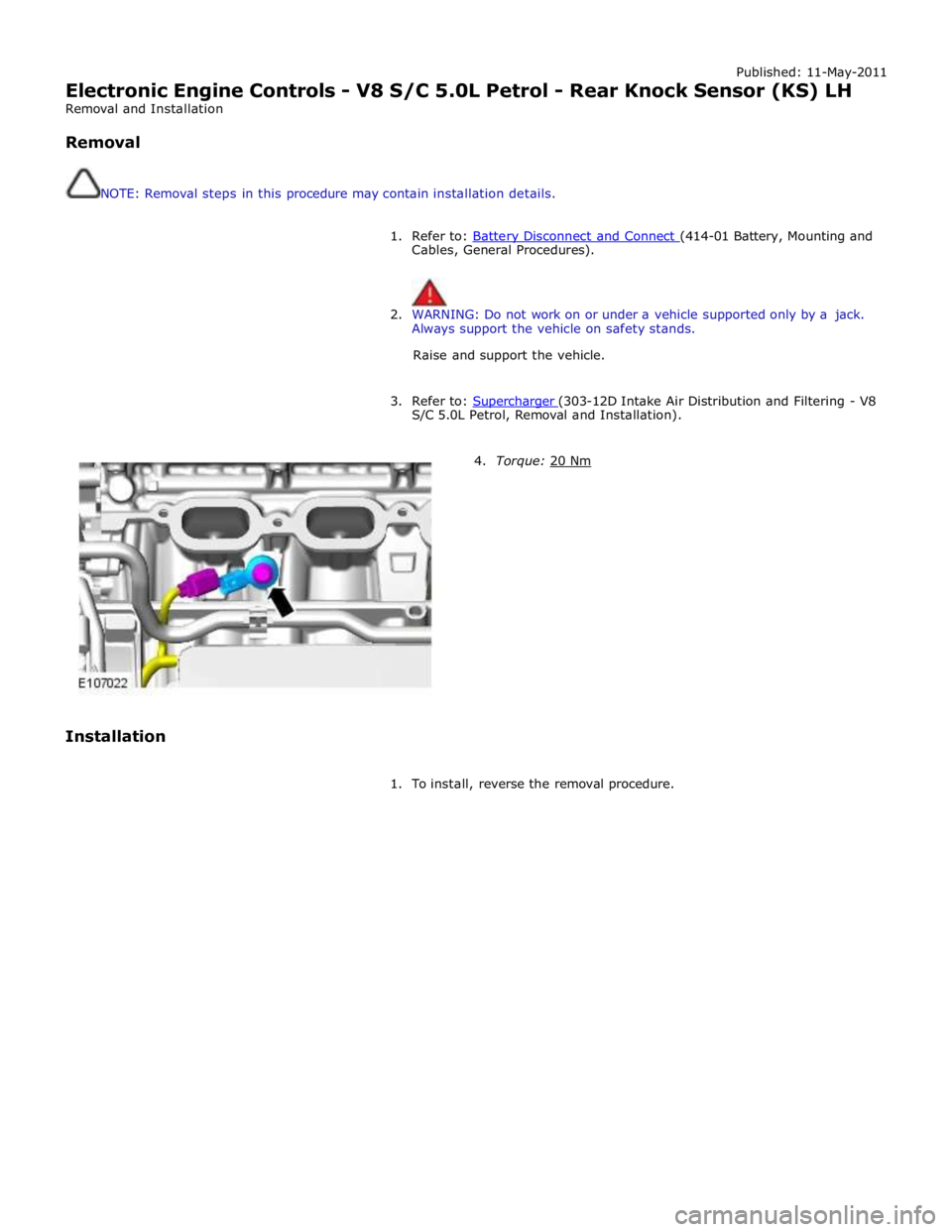
Published: 11-May-2011
Electronic Engine Controls - V8 S/C 5.0L Petrol - Rear Knock Sensor (KS) LH
Removal and Installation
Removal
NOTE: Removal steps in this procedure may contain installation details.
1. Refer to: Battery Disconnect and Connect (414-01 Battery, Mounting and Cables, General Procedures).
2. WARNING: Do not work on or under a vehicle supported only by a jack.
Always support the vehicle on safety stands.
Raise and support the vehicle.
3. Refer to: Supercharger (303-12D Intake Air Distribution and Filtering - V8 S/C 5.0L Petrol, Removal and Installation).
Installation
4. Torque: 20 Nm
1. To install, reverse the removal procedure.
Page 1403 of 3039
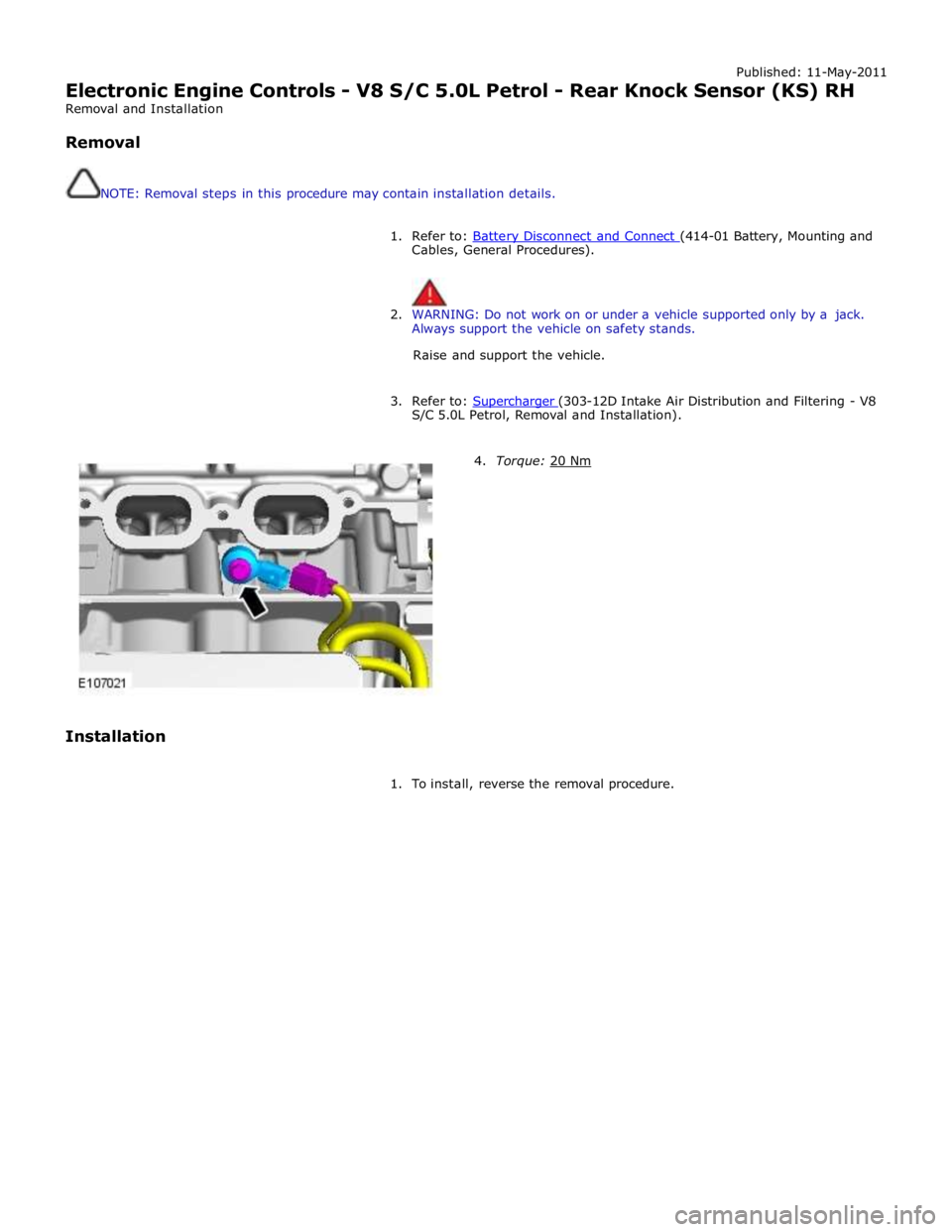
Published: 11-May-2011
Electronic Engine Controls - V8 S/C 5.0L Petrol - Rear Knock Sensor (KS) RH
Removal and Installation
Removal
NOTE: Removal steps in this procedure may contain installation details.
1. Refer to: Battery Disconnect and Connect (414-01 Battery, Mounting and Cables, General Procedures).
2. WARNING: Do not work on or under a vehicle supported only by a jack.
Always support the vehicle on safety stands.
Raise and support the vehicle.
3. Refer to: Supercharger (303-12D Intake Air Distribution and Filtering - V8 S/C 5.0L Petrol, Removal and Installation).
Installation
4. Torque: 20 Nm
1. To install, reverse the removal procedure.