clock JAGUAR XJ6 1997 2.G User Guide
[x] Cancel search | Manufacturer: JAGUAR, Model Year: 1997, Model line: XJ6, Model: JAGUAR XJ6 1997 2.GPages: 227, PDF Size: 7.2 MB
Page 172 of 227
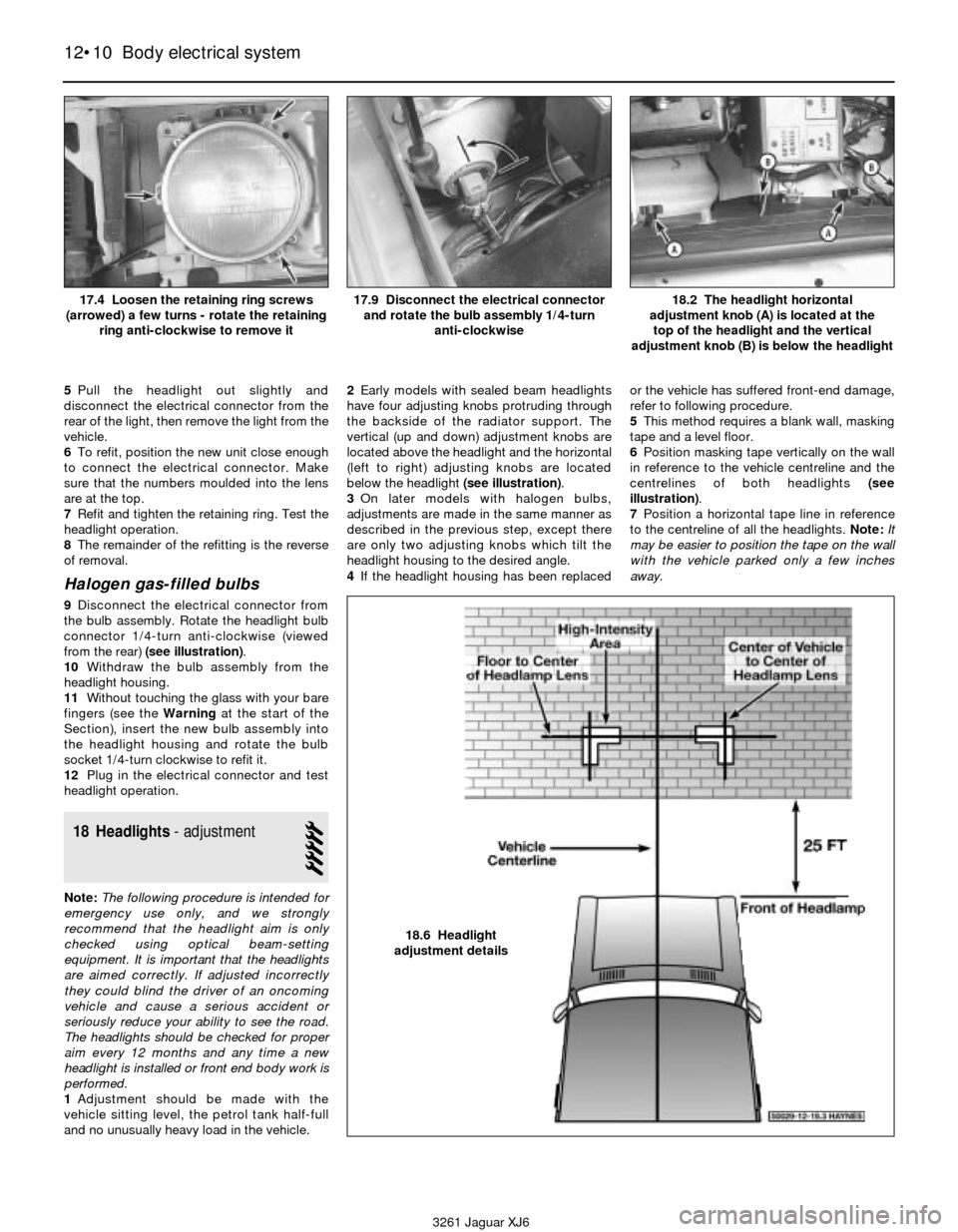
5Pull the headlight out slightly and
disconnect the electrical connector from the
rear of the light, then remove the light from the
vehicle.
6To refit, position the new unit close enough
to connect the electrical connector. Make
sure that the numbers moulded into the lens
are at the top.
7Refit and tighten the retaining ring. Test the
headlight operation.
8The remainder of the refitting is the reverse
of removal.
Halogen gas-filled bulbs
9Disconnect the electrical connector from
the bulb assembly. Rotate the headlight bulb
connector 1/4-turn anti-clockwise (viewed
from the rear) (see illustration).
10Withdraw the bulb assembly from the
headlight housing.
11Without touching the glass with your bare
fingers (see the Warningat the start of the
Section), insert the new bulb assembly into
the headlight housing and rotate the bulb
socket 1/4-turn clockwise to refit it.
12Plug in the electrical connector and test
headlight operation.
18 Headlights- adjustment
5
Note:The following procedure is intended for
emergency use only, and we strongly
recommend that the headlight aim is only
checked using optical beam-setting
equipment. It is important that the headlights
are aimed correctly. If adjusted incorrectly
they could blind the driver of an oncoming
vehicle and cause a serious accident or
seriously reduce your ability to see the road.
The headlights should be checked for proper
aim every 12 months and any time a new
headlight is installed or front end body work is
performed.
1Adjustment should be made with the
vehicle sitting level, the petrol tank half-full
and no unusually heavy load in the vehicle.2Early models with sealed beam headlights
have four adjusting knobs protruding through
the backside of the radiator support. The
vertical (up and down) adjustment knobs are
located above the headlight and the horizontal
(left to right) adjusting knobs are located
below the headlight (see illustration).
3On later models with halogen bulbs,
adjustments are made in the same manner as
described in the previous step, except there
are only two adjusting knobs which tilt the
headlight housing to the desired angle.
4If the headlight housing has been replacedor the vehicle has suffered front-end damage,
refer to following procedure.
5This method requires a blank wall, masking
tape and a level floor.
6Position masking tape vertically on the wall
in reference to the vehicle centreline and the
centrelines of both headlights (see
illustration).
7Position a horizontal tape line in reference
to the centreline of all the headlights. Note:It
may be easier to position the tape on the wall
with the vehicle parked only a few inches
away.
12•10 Body electrical system
3261 Jaguar XJ618.2 The headlight horizontal
adjustment knob (A) is located at the
top of the headlight and the vertical
adjustment knob (B) is below the headlight
17.4 Loosen the retaining ring screws
(arrowed) a few turns - rotate the retaining
ring anti-clockwise to remove it17.9 Disconnect the electrical connector
and rotate the bulb assembly 1/4-turn
anti-clockwise
18.6 Headlight
adjustment details
Page 173 of 227
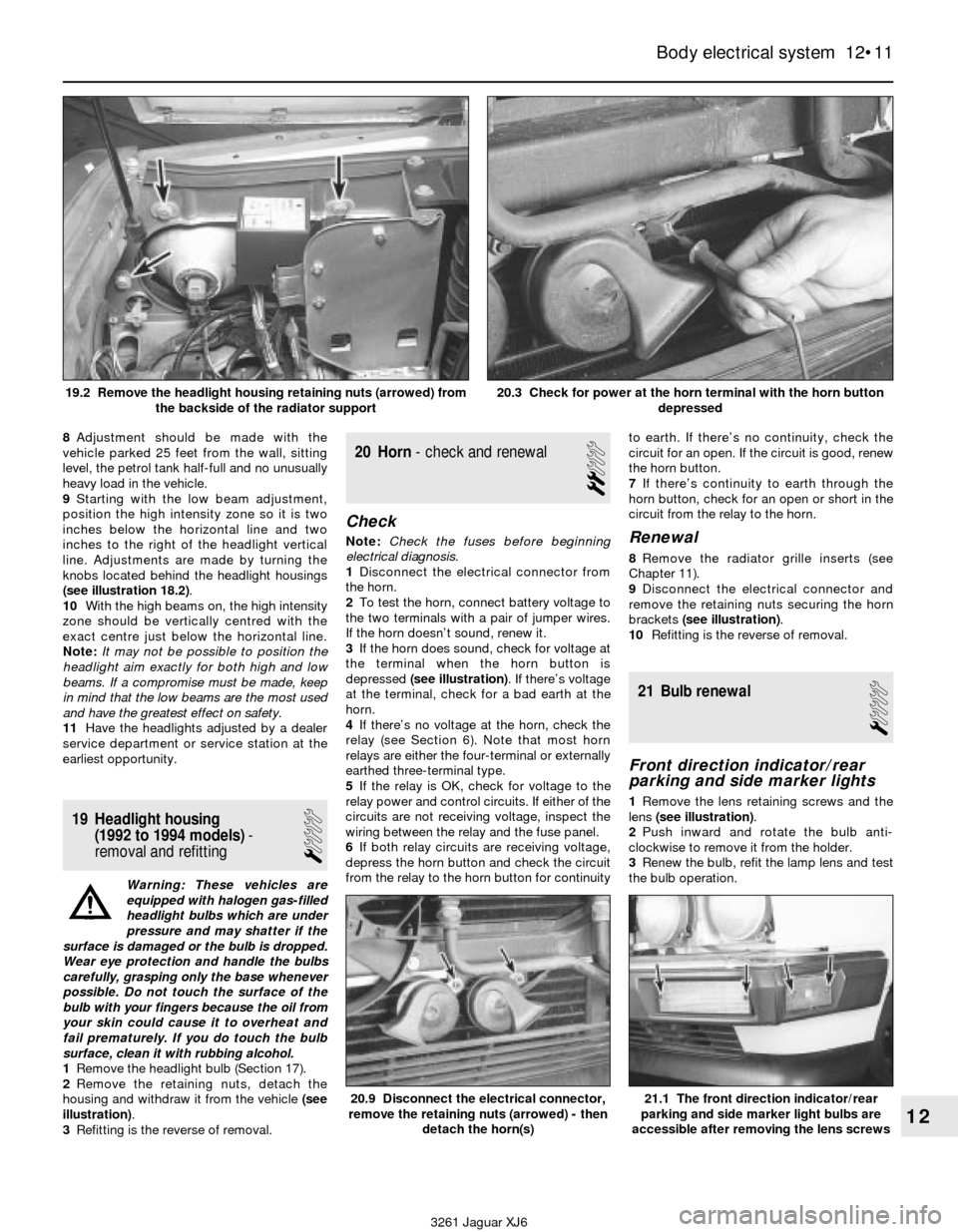
8Adjustment should be made with the
vehicle parked 25 feet from the wall, sitting
level, the petrol tank half-full and no unusually
heavy load in the vehicle.
9Starting with the low beam adjustment,
position the high intensity zone so it is two
inches below the horizontal line and two
inches to the right of the headlight vertical
line. Adjustments are made by turning the
knobs located behind the headlight housings
(see illustration 18.2).
10With the high beams on, the high intensity
zone should be vertically centred with the
exact centre just below the horizontal line.
Note:It may not be possible to position the
headlight aim exactly for both high and low
beams. If a compromise must be made, keep
in mind that the low beams are the most used
and have the greatest effect on safety.
11Have the headlights adjusted by a dealer
service department or service station at the
earliest opportunity.
19 Headlight housing
(1992 to 1994 models)-
removal and refitting
1
Warning: These vehicles are
equipped with halogen gas-filled
headlight bulbs which are under
pressure and may shatter if the
surface is damaged or the bulb is dropped.
Wear eye protection and handle the bulbs
carefully, grasping only the base whenever
possible. Do not touch the surface of the
bulb with your fingers because the oil from
your skin could cause it to overheat and
fail prematurely. If you do touch the bulb
surface, clean it with rubbing alcohol.
1Remove the headlight bulb (Section 17).
2Remove the retaining nuts, detach the
housing and withdraw it from the vehicle (see
illustration).
3Refitting is the reverse of removal.
20 Horn- check and renewal
2
Check
Note:Check the fuses before beginning
electrical diagnosis.
1Disconnect the electrical connector from
the horn.
2To test the horn, connect battery voltage to
the two terminals with a pair of jumper wires.
If the horn doesn’t sound, renew it.
3If the horn does sound, check for voltage at
the terminal when the horn button is
depressed (see illustration). If there’s voltage
at the terminal, check for a bad earth at the
horn.
4If there’s no voltage at the horn, check the
relay (see Section 6). Note that most horn
relays are either the four-terminal or externally
earthed three-terminal type.
5If the relay is OK, check for voltage to the
relay power and control circuits. If either of the
circuits are not receiving voltage, inspect the
wiring between the relay and the fuse panel.
6If both relay circuits are receiving voltage,
depress the horn button and check the circuit
from the relay to the horn button for continuityto earth. If there’s no continuity, check the
circuit for an open. If the circuit is good, renew
the horn button.
7If there’s continuity to earth through the
horn button, check for an open or short in the
circuit from the relay to the horn.Renewal
8Remove the radiator grille inserts (see
Chapter 11).
9Disconnect the electrical connector and
remove the retaining nuts securing the horn
brackets (see illustration).
10Refitting is the reverse of removal.
21 Bulb renewal
1
Front direction indicator/rear
parking and side marker lights
1Remove the lens retaining screws and the
lens (see illustration).
2Push inward and rotate the bulb anti-
clockwise to remove it from the holder.
3Renew the bulb, refit the lamp lens and test
the bulb operation.
Body electrical system 12•11
12
20.9 Disconnect the electrical connector,
remove the retaining nuts (arrowed) - then
detach the horn(s)21.1 The front direction indicator/rear
parking and side marker light bulbs are
accessible after removing the lens screws
3261 Jaguar XJ6 19.2 Remove the headlight housing retaining nuts (arrowed) from
the backside of the radiator support
20.3 Check for power at the horn terminal with the horn button
depressed
Page 174 of 227
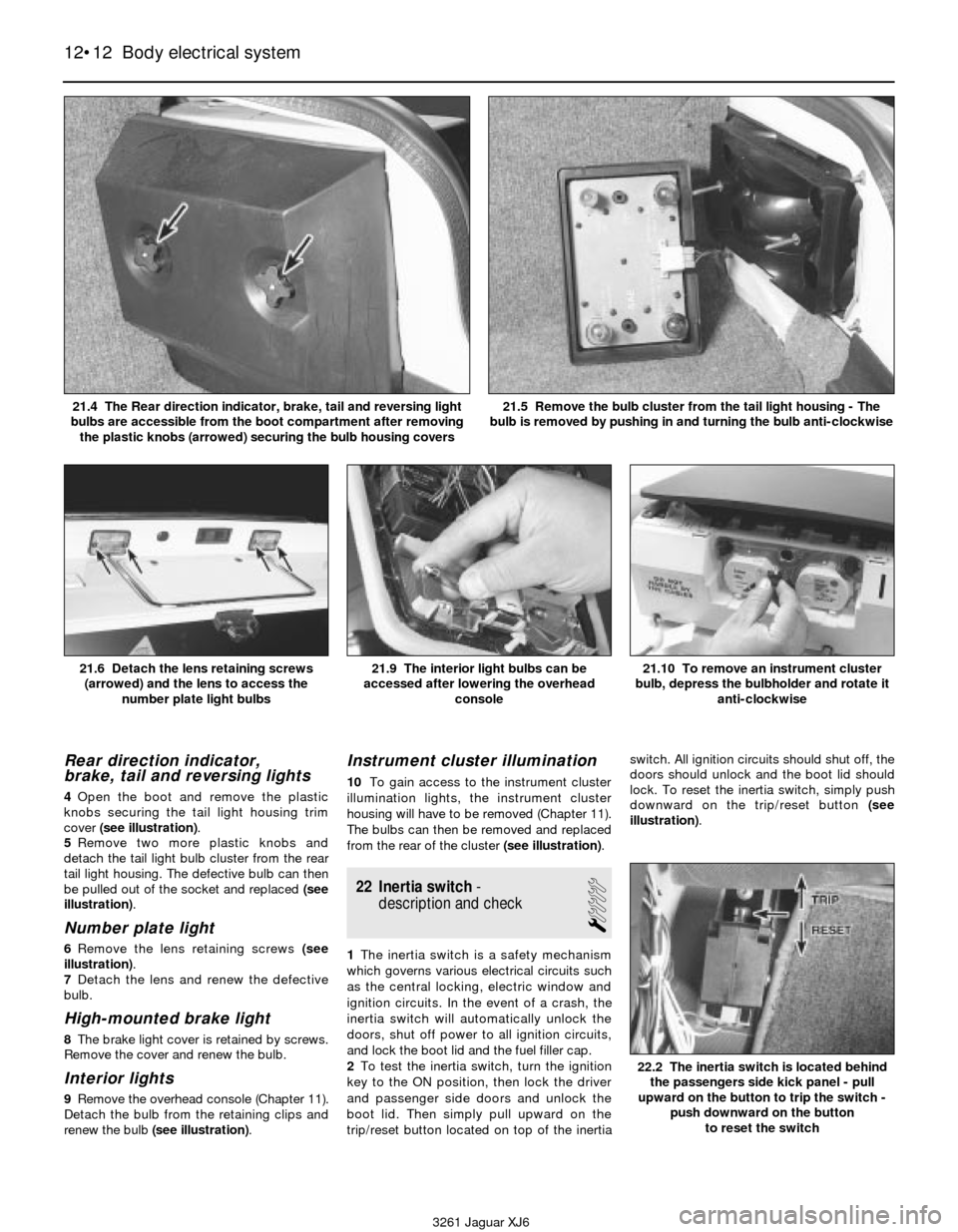
Rear direction indicator,
brake, tail and reversing lights
4Open the boot and remove the plastic
knobs securing the tail light housing trim
cover (see illustration).
5Remove two more plastic knobs and
detach the tail light bulb cluster from the rear
tail light housing. The defective bulb can then
be pulled out of the socket and replaced (see
illustration).
Number plate light
6Remove the lens retaining screws (see
illustration).
7Detach the lens and renew the defective
bulb.
High-mounted brake light
8The brake light cover is retained by screws.
Remove the cover and renew the bulb.
Interior lights
9Remove the overhead console (Chapter 11).
Detach the bulb from the retaining clips and
renew the bulb (see illustration).
Instrument cluster illumination
10To gain access to the instrument cluster
illumination lights, the instrument cluster
housing will have to be removed (Chapter 11).
The bulbs can then be removed and replaced
from the rear of the cluster (see illustration).
22 Inertia switch-
description and check
1
1The inertia switch is a safety mechanism
which governs various electrical circuits such
as the central locking, electric window and
ignition circuits. In the event of a crash, the
inertia switch will automatically unlock the
doors, shut off power to all ignition circuits,
and lock the boot lid and the fuel filler cap.
2To test the inertia switch, turn the ignition
key to the ON position, then lock the driver
and passenger side doors and unlock the
boot lid. Then simply pull upward on the
trip/reset button located on top of the inertiaswitch. All ignition circuits should shut off, the
doors should unlock and the boot lid should
lock. To reset the inertia switch, simply push
downward on the trip/reset button (see
illustration).
12•12 Body electrical system
21.6 Detach the lens retaining screws
(arrowed) and the lens to access the
number plate light bulbs21.9 The interior light bulbs can be
accessed after lowering the overhead
console21.10 To remove an instrument cluster
bulb, depress the bulbholder and rotate it
anti-clockwise
3261 Jaguar XJ6 21.4 The Rear direction indicator, brake, tail and reversing light
bulbs are accessible from the boot compartment after removing
the plastic knobs (arrowed) securing the bulb housing covers
21.5 Remove the bulb cluster from the tail light housing - The
bulb is removed by pushing in and turning the bulb anti-clockwise
22.2 The inertia switch is located behind
the passengers side kick panel - pull
upward on the button to trip the switch -
push downward on the button
to reset the switch
Page 176 of 227
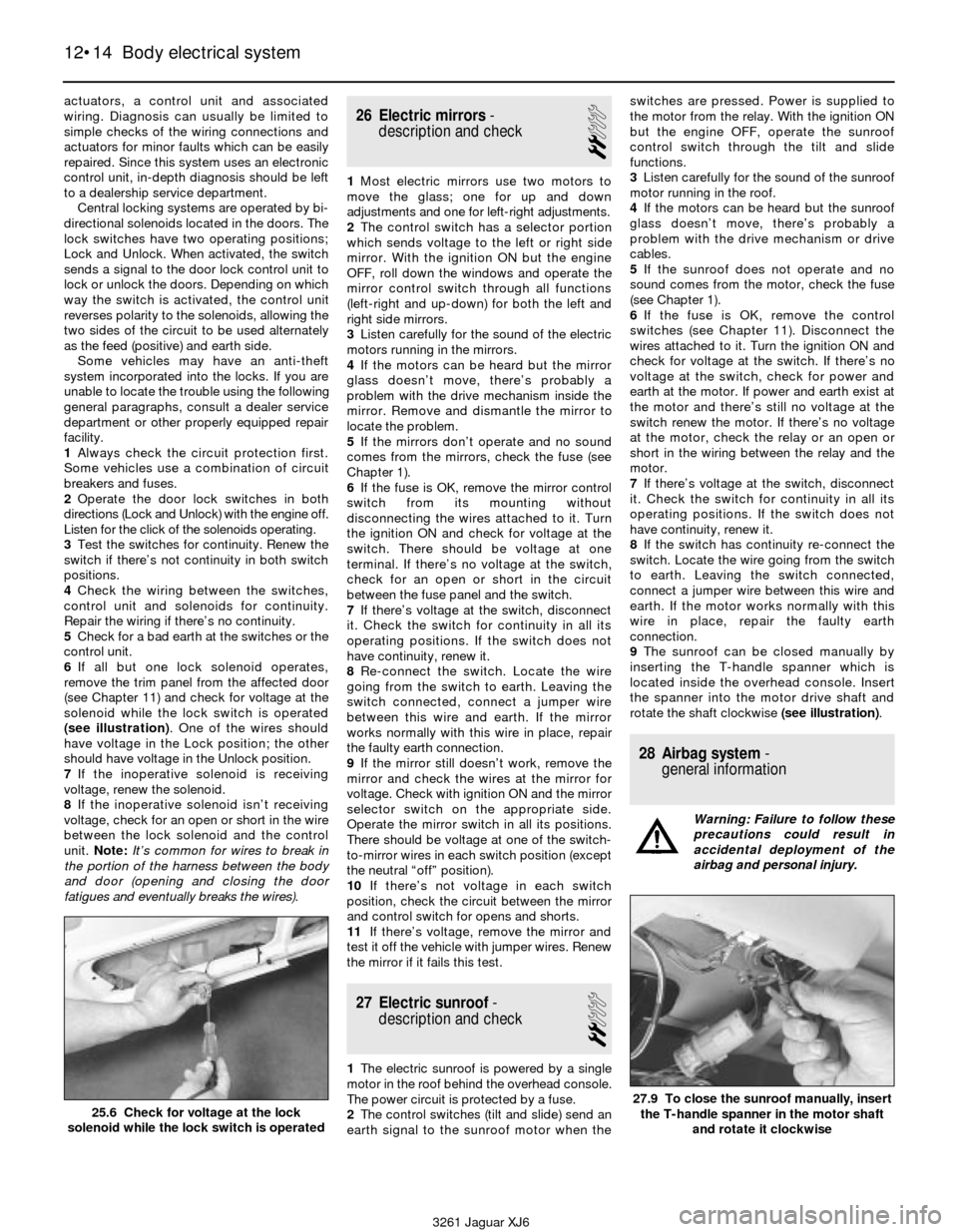
actuators, a control unit and associated
wiring. Diagnosis can usually be limited to
simple checks of the wiring connections and
actuators for minor faults which can be easily
repaired. Since this system uses an electronic
control unit, in-depth diagnosis should be left
to a dealership service department.
Central locking systems are operated by bi-
directional solenoids located in the doors. The
lock switches have two operating positions;
Lock and Unlock. When activated, the switch
sends a signal to the door lock control unit to
lock or unlock the doors. Depending on which
way the switch is activated, the control unit
reverses polarity to the solenoids, allowing the
two sides of the circuit to be used alternately
as the feed (positive) and earth side.
Some vehicles may have an anti-theft
system incorporated into the locks. If you are
unable to locate the trouble using the following
general paragraphs, consult a dealer service
department or other properly equipped repair
facility.
1Always check the circuit protection first.
Some vehicles use a combination of circuit
breakers and fuses.
2Operate the door lock switches in both
directions (Lock and Unlock) with the engine off.
Listen for the click of the solenoids operating.
3Test the switches for continuity. Renew the
switch if there’s not continuity in both switch
positions.
4Check the wiring between the switches,
control unit and solenoids for continuity.
Repair the wiring if there’s no continuity.
5Check for a bad earth at the switches or the
control unit.
6If all but one lock solenoid operates,
remove the trim panel from the affected door
(see Chapter 11) and check for voltage at the
solenoid while the lock switch is operated
(see illustration). One of the wires should
have voltage in the Lock position; the other
should have voltage in the Unlock position.
7If the inoperative solenoid is receiving
voltage, renew the solenoid.
8If the inoperative solenoid isn’t receiving
voltage, check for an open or short in the wire
between the lock solenoid and the control
unit. Note:It’s common for wires to break in
the portion of the harness between the body
and door (opening and closing the door
fatigues and eventually breaks the wires).26 Electric mirrors-
description and check
2
1Most electric mirrors use two motors to
move the glass; one for up and down
adjustments and one for left-right adjustments.
2The control switch has a selector portion
which sends voltage to the left or right side
mirror. With the ignition ON but the engine
OFF, roll down the windows and operate the
mirror control switch through all functions
(left-right and up-down) for both the left and
right side mirrors.
3Listen carefully for the sound of the electric
motors running in the mirrors.
4If the motors can be heard but the mirror
glass doesn’t move, there’s probably a
problem with the drive mechanism inside the
mirror. Remove and dismantle the mirror to
locate the problem.
5If the mirrors don’t operate and no sound
comes from the mirrors, check the fuse (see
Chapter 1).
6If the fuse is OK, remove the mirror control
switch from its mounting without
disconnecting the wires attached to it. Turn
the ignition ON and check for voltage at the
switch. There should be voltage at one
terminal. If there’s no voltage at the switch,
check for an open or short in the circuit
between the fuse panel and the switch.
7If there’s voltage at the switch, disconnect
it. Check the switch for continuity in all its
operating positions. If the switch does not
have continuity, renew it.
8Re-connect the switch. Locate the wire
going from the switch to earth. Leaving the
switch connected, connect a jumper wire
between this wire and earth. If the mirror
works normally with this wire in place, repair
the faulty earth connection.
9If the mirror still doesn’t work, remove the
mirror and check the wires at the mirror for
voltage. Check with ignition ON and the mirror
selector switch on the appropriate side.
Operate the mirror switch in all its positions.
There should be voltage at one of the switch-
to-mirror wires in each switch position (except
the neutral “off” position).
10If there’s not voltage in each switch
position, check the circuit between the mirror
and control switch for opens and shorts.
11If there’s voltage, remove the mirror and
test it off the vehicle with jumper wires. Renew
the mirror if it fails this test.
27 Electric sunroof-
description and check
2
1The electric sunroof is powered by a single
motor in the roof behind the overhead console.
The power circuit is protected by a fuse.
2The control switches (tilt and slide) send an
earth signal to the sunroof motor when theswitches are pressed. Power is supplied to
the motor from the relay. With the ignition ON
but the engine OFF, operate the sunroof
control switch through the tilt and slide
functions.
3Listen carefully for the sound of the sunroof
motor running in the roof.
4If the motors can be heard but the sunroof
glass doesn’t move, there’s probably a
problem with the drive mechanism or drive
cables.
5If the sunroof does not operate and no
sound comes from the motor, check the fuse
(see Chapter 1).
6If the fuse is OK, remove the control
switches (see Chapter 11). Disconnect the
wires attached to it. Turn the ignition ON and
check for voltage at the switch. If there’s no
voltage at the switch, check for power and
earth at the motor. If power and earth exist at
the motor and there’s still no voltage at the
switch renew the motor. If there’s no voltage
at the motor, check the relay or an open or
short in the wiring between the relay and the
motor.
7If there’s voltage at the switch, disconnect
it. Check the switch for continuity in all its
operating positions. If the switch does not
have continuity, renew it.
8If the switch has continuity re-connect the
switch. Locate the wire going from the switch
to earth. Leaving the switch connected,
connect a jumper wire between this wire and
earth. If the motor works normally with this
wire in place, repair the faulty earth
connection.
9The sunroof can be closed manually by
inserting the T-handle spanner which is
located inside the overhead console. Insert
the spanner into the motor drive shaft and
rotate the shaft clockwise (see illustration).
28 Airbag system-
general information
Warning: Failure to follow these
precautions could result in
accidental deployment of the
airbag and personal injury.
12•14 Body electrical system
25.6 Check for voltage at the lock
solenoid while the lock switch is operated27.9 To close the sunroof manually, insert
the T-handle spanner in the motor shaft
and rotate it clockwise
3261 Jaguar XJ6
Page 204 of 227
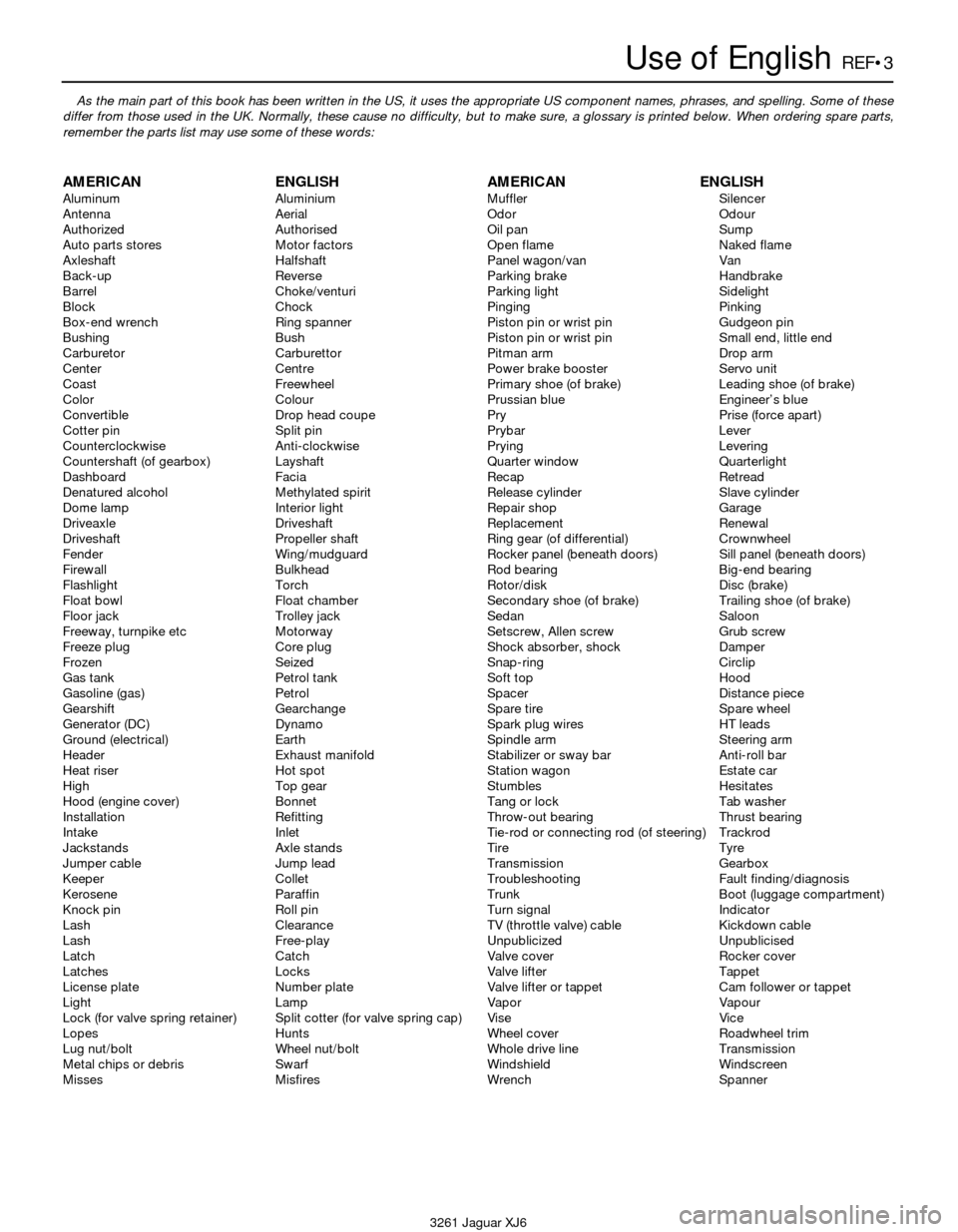
3261 Jaguar XJ6
Use of EnglishREF•3
As the main part of this book has been written in the US, it uses the appropriate US component names, phrases, and spelling. Some of these
differ from those used in the UK. Normally, these cause no difficulty, but to make sure, a glossary is printed below. When ordering spare parts,
remember the parts list may use some of these words:
AMERICAN ENGLISH
Aluminum Aluminium
Antenna Aerial
Authorized Authorised
Auto parts stores Motor factors
Axleshaft Halfshaft
Back-up Reverse
Barrel Choke/venturi
Block Chock
Box-end wrench Ring spanner
Bushing Bush
Carburetor Carburettor
Center Centre
Coast Freewheel
Color Colour
Convertible Drop head coupe
Cotter pin Split pin
Counterclockwise Anti-clockwise
Countershaft (of gearbox) Layshaft
Dashboard Facia
Denatured alcohol Methylated spirit
Dome lamp Interior light
Driveaxle Driveshaft
Driveshaft Propeller shaft
Fender Wing/mudguard
Firewall Bulkhead
Flashlight Torch
Float bowl Float chamber
Floor jack Trolley jack
Freeway, turnpike etc Motorway
Freeze plug Core plug
Frozen Seized
Gas tank Petrol tank
Gasoline (gas) Petrol
Gearshift Gearchange
Generator (DC) Dynamo
Ground (electrical) Earth
Header Exhaust manifold
Heat riser Hot spot
High Top gear
Hood (engine cover) Bonnet
Installation Refitting
Intake Inlet
Jackstands Axle stands
Jumper cable Jump lead
Keeper Collet
Kerosene Paraffin
Knock pin Roll pin
Lash Clearance
Lash Free-play
Latch Catch
Latches Locks
License plate Number plate
Light Lamp
Lock (for valve spring retainer) Split cotter (for valve spring cap)
Lopes Hunts
Lug nut/bolt Wheel nut/bolt
Metal chips or debris Swarf
Misses Misfires
AMERICAN ENGLISH
Muffler Silencer
Odor Odour
Oil pan Sump
Open flame Naked flame
Panel wagon/van Van
Parking brake Handbrake
Parking light Sidelight
Pinging Pinking
Piston pin or wrist pin Gudgeon pin
Piston pin or wrist pin Small end, little end
Pitman arm Drop arm
Power brake booster Servo unit
Primary shoe (of brake) Leading shoe (of brake)
Prussian blue Engineer’s blue
Pry Prise (force apart)
Prybar Lever
Prying Levering
Quarter window Quarterlight
Recap Retread
Release cylinder Slave cylinder
Repair shop Garage
Replacement Renewal
Ring gear (of differential) Crownwheel
Rocker panel (beneath doors) Sill panel (beneath doors)
Rod bearing Big-end bearing
Rotor/disk Disc (brake)
Secondary shoe (of brake) Trailing shoe (of brake)
Sedan Saloon
Setscrew, Allen screw Grub screw
Shock absorber, shock Damper
Snap-ring Circlip
Soft top Hood
Spacer Distance piece
Spare tire Spare wheel
Spark plug wires HT leads
Spindle arm Steering arm
Stabilizer or sway bar Anti-roll bar
Station wagon Estate car
Stumbles Hesitates
Tang or lock Tab washer
Throw-out bearing Thrust bearing
Tie-rod or connecting rod (of steering) Trackrod
Tire Tyre
Transmission Gearbox
Troubleshooting Fault finding/diagnosis
Trunk Boot (luggage compartment)
Turn signal Indicator
TV (throttle valve) cable Kickdown cable
Unpublicized Unpublicised
Valve cover Rocker cover
Valve lifter Tappet
Valve lifter or tappet Cam follower or tappet
Vapor Vapour
Vise Vice
Wheel cover Roadwheel trim
Whole drive line Transmission
Windshield Windscreen
Wrench Spanner
Page 211 of 227
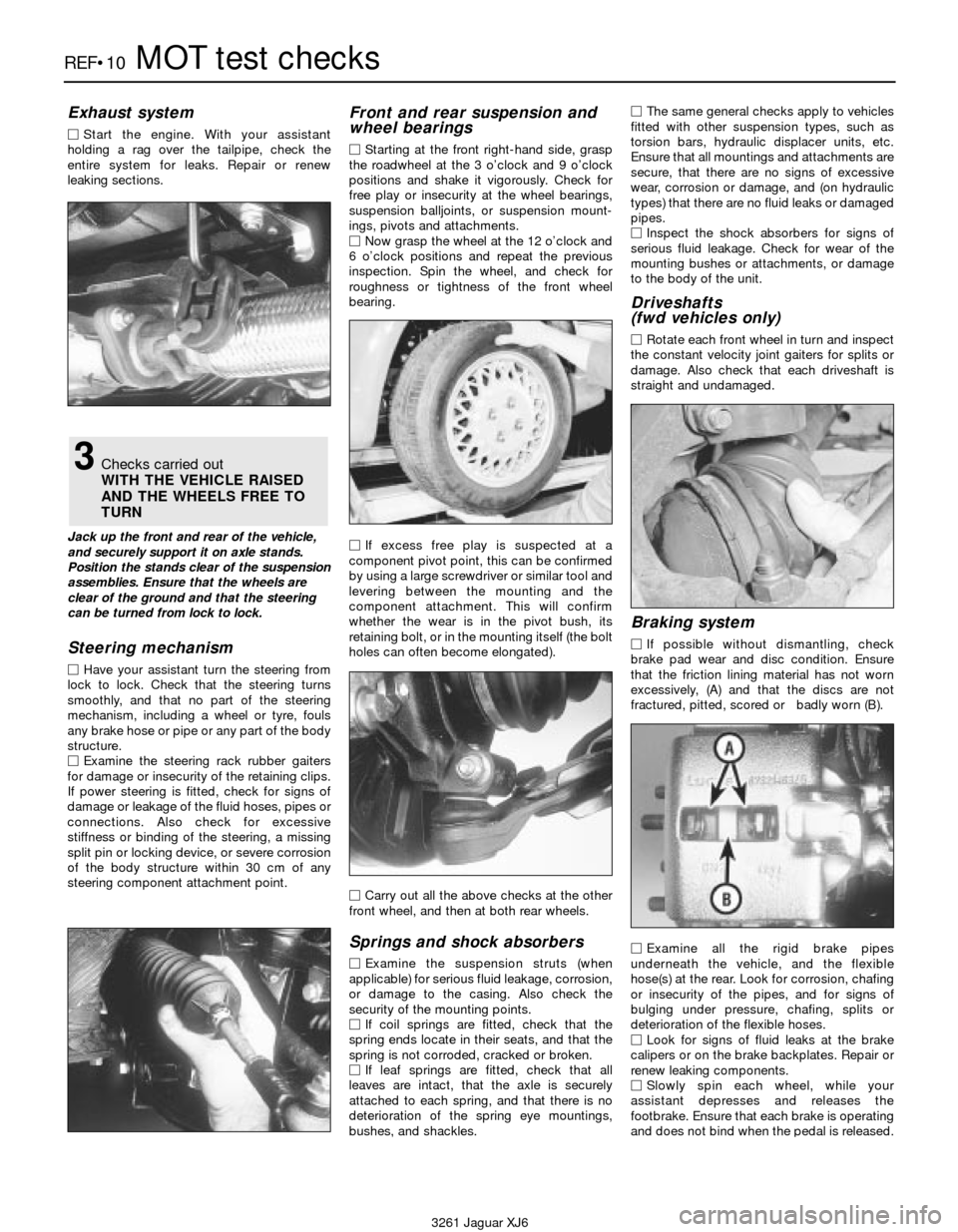
3261 Jaguar XJ6
REF•10MOT test checks
Exhaust system
MStart the engine. With your assistant
holding a rag over the tailpipe, check the
entire system for leaks. Repair or renew
leaking sections.
Jack up the front and rear of the vehicle,
and securely support it on axle stands.
Position the stands clear of the suspension
assemblies. Ensure that the wheels are
clear of the ground and that the steering
can be turned from lock to lock.
Steering mechanism
MHave your assistant turn the steering from
lock to lock. Check that the steering turns
smoothly, and that no part of the steering
mechanism, including a wheel or tyre, fouls
any brake hose or pipe or any part of the body
structure.
MExamine the steering rack rubber gaiters
for damage or insecurity of the retaining clips.
If power steering is fitted, check for signs of
damage or leakage of the fluid hoses, pipes or
connections. Also check for excessive
stiffness or binding of the steering, a missing
split pin or locking device, or severe corrosion
of the body structure within 30 cm of any
steering component attachment point.
Front and rear suspension and
wheel bearings
MStarting at the front right-hand side, grasp
the roadwheel at the 3 o’clock and 9 o’clock
positions and shake it vigorously. Check for
free play or insecurity at the wheel bearings,
suspension balljoints, or suspension mount-
ings, pivots and attachments.
MNow grasp the wheel at the 12 o’clock and
6 o’clock positions and repeat the previous
inspection. Spin the wheel, and check for
roughness or tightness of the front wheel
bearing.
MIf excess free play is suspected at a
component pivot point, this can be confirmed
by using a large screwdriver or similar tool and
levering between the mounting and the
component attachment. This will confirm
whether the wear is in the pivot bush, its
retaining bolt, or in the mounting itself (the bolt
holes can often become elongated).
MCarry out all the above checks at the other
front wheel, and then at both rear wheels.
Springs and shock absorbers
MExamine the suspension struts (when
applicable) for serious fluid leakage, corrosion,
or damage to the casing. Also check the
security of the mounting points.
MIf coil springs are fitted, check that the
spring ends locate in their seats, and that the
spring is not corroded, cracked or broken.
MIf leaf springs are fitted, check that all
leaves are intact, that the axle is securely
attached to each spring, and that there is no
deterioration of the spring eye mountings,
bushes, and shackles.MThe same general checks apply to vehicles
fitted with other suspension types, such as
torsion bars, hydraulic displacer units, etc.
Ensure that all mountings and attachments are
secure, that there are no signs of excessive
wear, corrosion or damage, and (on hydraulic
types) that there are no fluid leaks or damaged
pipes.
MInspect the shock absorbers for signs of
serious fluid leakage. Check for wear of the
mounting bushes or attachments, or damage
to the body of the unit.
Driveshafts
(fwd vehicles only)
MRotate each front wheel in turn and inspect
the constant velocity joint gaiters for splits or
damage. Also check that each driveshaft is
straight and undamaged.
Braking system
MIf possible without dismantling, check
brake pad wear and disc condition. Ensure
that the friction lining material has not worn
excessively, (A) and that the discs are not
fractured, pitted, scored or badly worn (B).
MExamine all the rigid brake pipes
underneath the vehicle, and the flexible
hose(s) at the rear. Look for corrosion, chafing
or insecurity of the pipes, and for signs of
bulging under pressure, chafing, splits or
deterioration of the flexible hoses.
MLook for signs of fluid leaks at the brake
calipers or on the brake backplates. Repair or
renew leaking components.
MSlowly spin each wheel, while your
assistant depresses and releases the
footbrake. Ensure that each brake is operating
and does not bind when the pedal is released.
3Checks carried out
WITH THE VEHICLE RAISED
AND THE WHEELS FREE TO
TURN