jacking JAGUAR XJ6 1997 2.G Workshop Manual
[x] Cancel search | Manufacturer: JAGUAR, Model Year: 1997, Model line: XJ6, Model: JAGUAR XJ6 1997 2.GPages: 227, PDF Size: 7.2 MB
Page 3 of 227
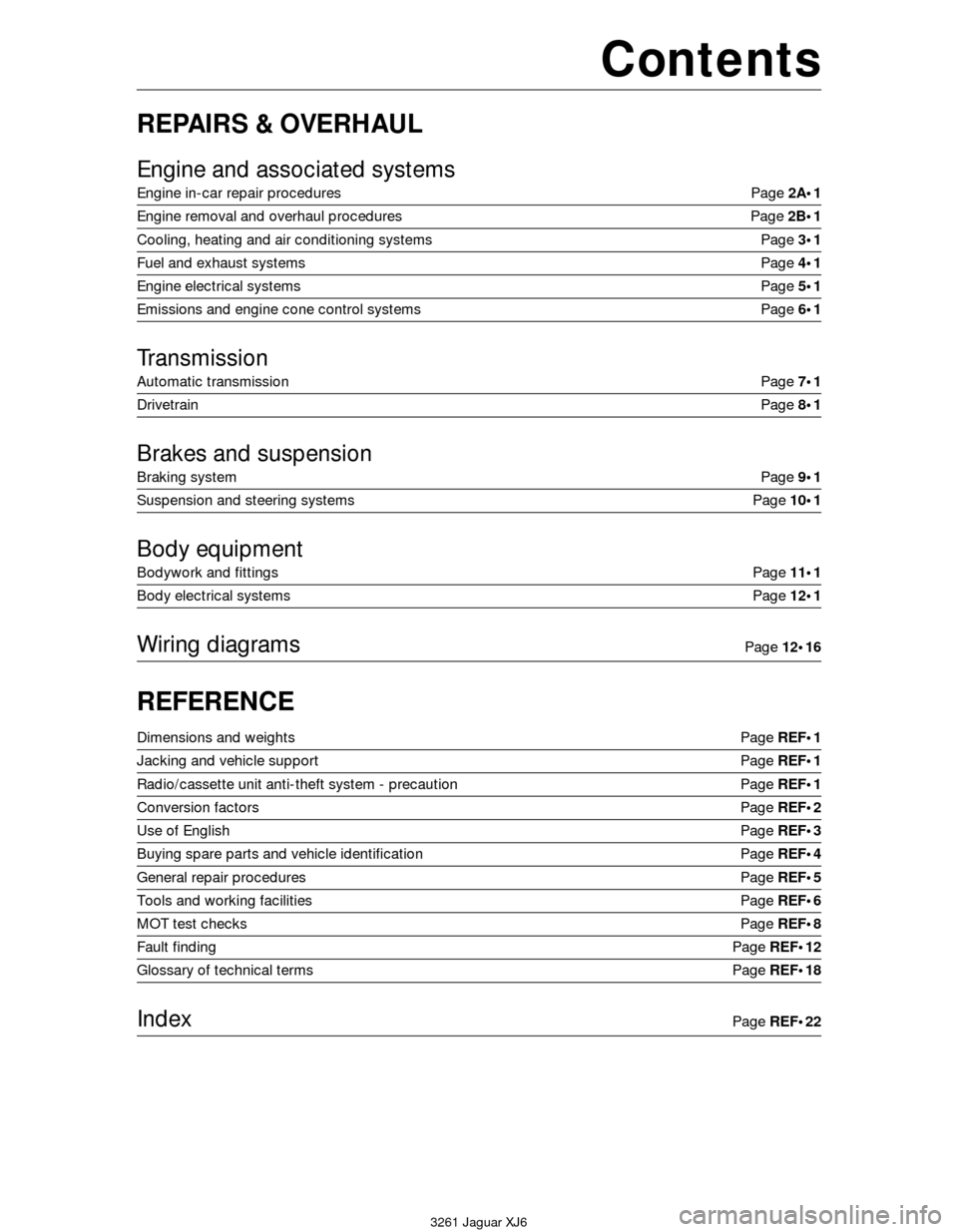
3261 Jaguar XJ6
REPAIRS & OVERHAUL
Engine and associated systems
Engine in-car repair procedures Page 2A•1
Engine removal and overhaul procedures Page 2B•1
Cooling, heating and air conditioning systems Page 3•1
Fuel and exhaust systems Page 4•1
Engine electrical systems Page 5•1
Emissions and engine cone control systems Page 6•1
Transmission
Automatic transmissionPage 7•1
DrivetrainPage 8•1
Brakes and suspension
Braking systemPage 9•1
Suspension and steering systems Page 10•1
Body equipment
Bodywork and fittingsPage 11•1
Body electrical systems Page 12•1
Wiring diagramsPage 12•16
REFERENCE
Dimensions and weights Page REF•1
Jacking and vehicle support Page REF•1
Radio/cassette unit anti-theft system - precaution Page REF•1
Conversion factorsPage REF•2
Use of EnglishPage REF•3
Buying spare parts and vehicle identification Page REF•4
General repair procedures Page REF•5
Tools and working facilities Page REF•6
MOT test checksPage REF•8
Fault findingPage REF•12
Glossary of technical terms Page REF•18
IndexPage REF•22
Contents
Page 5 of 227
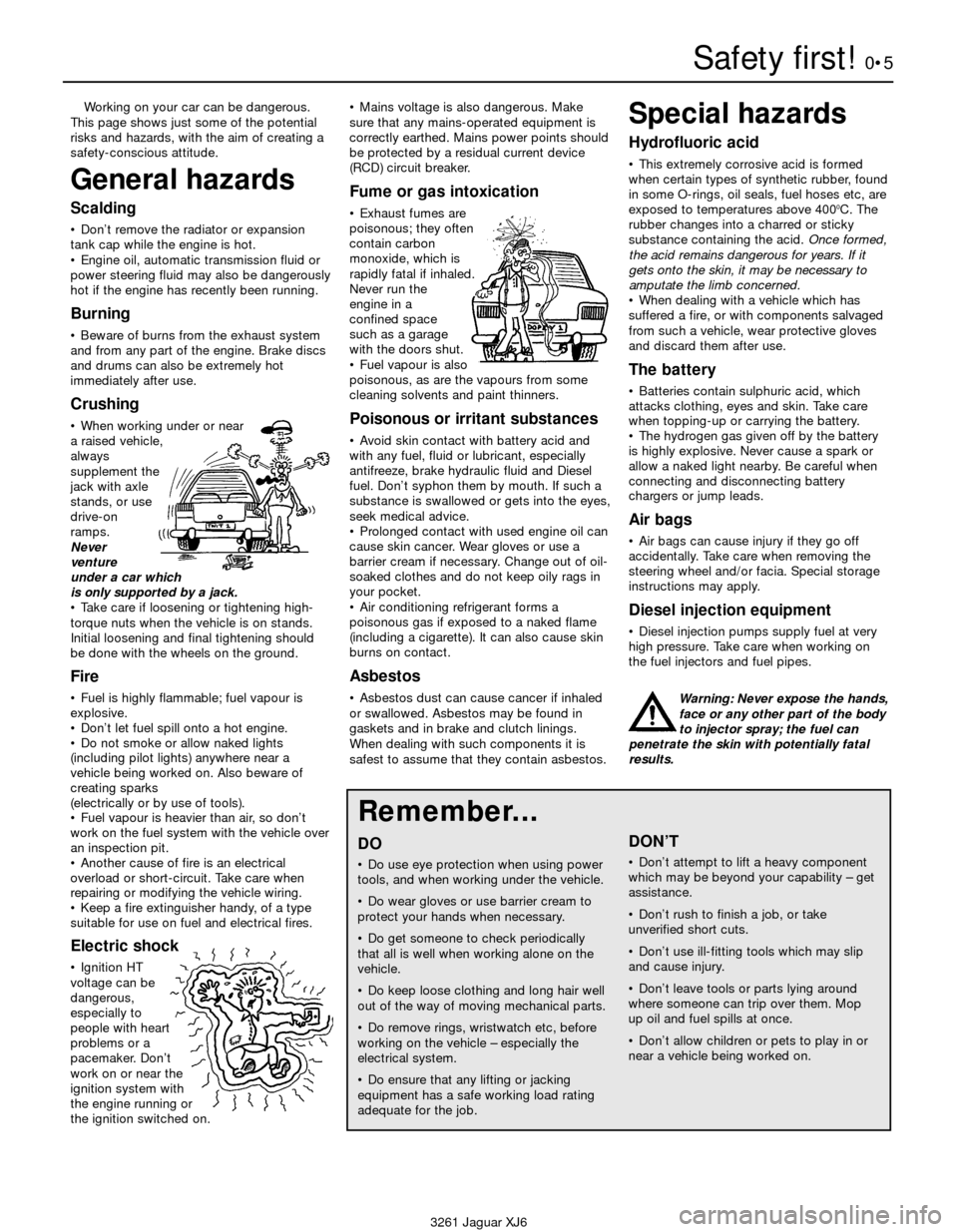
3261 Jaguar XJ6
Safety first!0•5
Working on your car can be dangerous.
This page shows just some of the potential
risks and hazards, with the aim of creating a
safety-conscious attitude.
General hazards
Scalding
• Don’t remove the radiator or expansion
tank cap while the engine is hot.
• Engine oil, automatic transmission fluid or
power steering fluid may also be dangerously
hot if the engine has recently been running.
Burning
• Beware of burns from the exhaust system
and from any part of the engine. Brake discs
and drums can also be extremely hot
immediately after use.
Crushing
• When working under or near
a raised vehicle,
always
supplement the
jack with axle
stands, or use
drive-on
ramps.
Never
venture
under a car which
is only supported by a jack.
• Take care if loosening or tightening high-
torque nuts when the vehicle is on stands.
Initial loosening and final tightening should
be done with the wheels on the ground.
Fire
• Fuel is highly flammable; fuel vapour is
explosive.
• Don’t let fuel spill onto a hot engine.
• Do not smoke or allow naked lights
(including pilot lights) anywhere near a
vehicle being worked on. Also beware of
creating sparks
(electrically or by use of tools).
• Fuel vapour is heavier than air, so don’t
work on the fuel system with the vehicle over
an inspection pit.
• Another cause of fire is an electrical
overload or short-circuit. Take care when
repairing or modifying the vehicle wiring.
• Keep a fire extinguisher handy, of a type
suitable for use on fuel and electrical fires.
Electric shock
• Ignition HT
voltage can be
dangerous,
especially to
people with heart
problems or a
pacemaker. Don’t
work on or near the
ignition system with
the engine running or
the ignition switched on.• Mains voltage is also dangerous. Make
sure that any mains-operated equipment is
correctly earthed. Mains power points should
be protected by a residual current device
(RCD) circuit breaker.
Fume or gas intoxication
• Exhaust fumes are
poisonous; they often
contain carbon
monoxide, which is
rapidly fatal if inhaled.
Never run the
engine in a
confined space
such as a garage
with the doors shut.
• Fuel vapour is also
poisonous, as are the vapours from some
cleaning solvents and paint thinners.
Poisonous or irritant substances
• Avoid skin contact with battery acid and
with any fuel, fluid or lubricant, especially
antifreeze, brake hydraulic fluid and Diesel
fuel. Don’t syphon them by mouth. If such a
substance is swallowed or gets into the eyes,
seek medical advice.
• Prolonged contact with used engine oil can
cause skin cancer. Wear gloves or use a
barrier cream if necessary. Change out of oil-
soaked clothes and do not keep oily rags in
your pocket.
• Air conditioning refrigerant forms a
poisonous gas if exposed to a naked flame
(including a cigarette). It can also cause skin
burns on contact.
Asbestos
• Asbestos dust can cause cancer if inhaled
or swallowed. Asbestos may be found in
gaskets and in brake and clutch linings.
When dealing with such components it is
safest to assume that they contain asbestos.
Special hazards
Hydrofluoric acid
• This extremely corrosive acid is formed
when certain types of synthetic rubber, found
in some O-rings, oil seals, fuel hoses etc, are
exposed to temperatures above 400
0C. The
rubber changes into a charred or sticky
substance containing the acid. Once formed,
the acid remains dangerous for years. If it
gets onto the skin, it may be necessary to
amputate the limb concerned.
• When dealing with a vehicle which has
suffered a fire, or with components salvaged
from such a vehicle, wear protective gloves
and discard them after use.
The battery
• Batteries contain sulphuric acid, which
attacks clothing, eyes and skin. Take care
when topping-up or carrying the battery.
• The hydrogen gas given off by the battery
is highly explosive. Never cause a spark or
allow a naked light nearby. Be careful when
connecting and disconnecting battery
chargers or jump leads.
Air bags
• Air bags can cause injury if they go off
accidentally. Take care when removing the
steering wheel and/or facia. Special storage
instructions may apply.
Diesel injection equipment
• Diesel injection pumps supply fuel at very
high pressure. Take care when working on
the fuel injectors and fuel pipes.
Warning: Never expose the hands,
face or any other part of the body
to injector spray; the fuel can
penetrate the skin with potentially fatal
results.
Remember...
DO
• Do use eye protection when using power
tools, and when working under the vehicle.
• Do wear gloves or use barrier cream to
protect your hands when necessary.
• Do get someone to check periodically
that all is well when working alone on the
vehicle.
• Do keep loose clothing and long hair well
out of the way of moving mechanical parts.
• Do remove rings, wristwatch etc, before
working on the vehicle – especially the
electrical system.
• Do ensure that any lifting or jacking
equipment has a safe working load rating
adequate for the job.
A few tips
DON’T
• Don’t attempt to lift a heavy component
which may be beyond your capability – get
assistance.
• Don’t rush to finish a job, or take
unverified short cuts.
• Don’t use ill-fitting tools which may slip
and cause injury.
• Don’t leave tools or parts lying around
where someone can trip over them. Mop
up oil and fuel spills at once.
• Don’t allow children or pets to play in or
near a vehicle being worked on.
Page 29 of 227
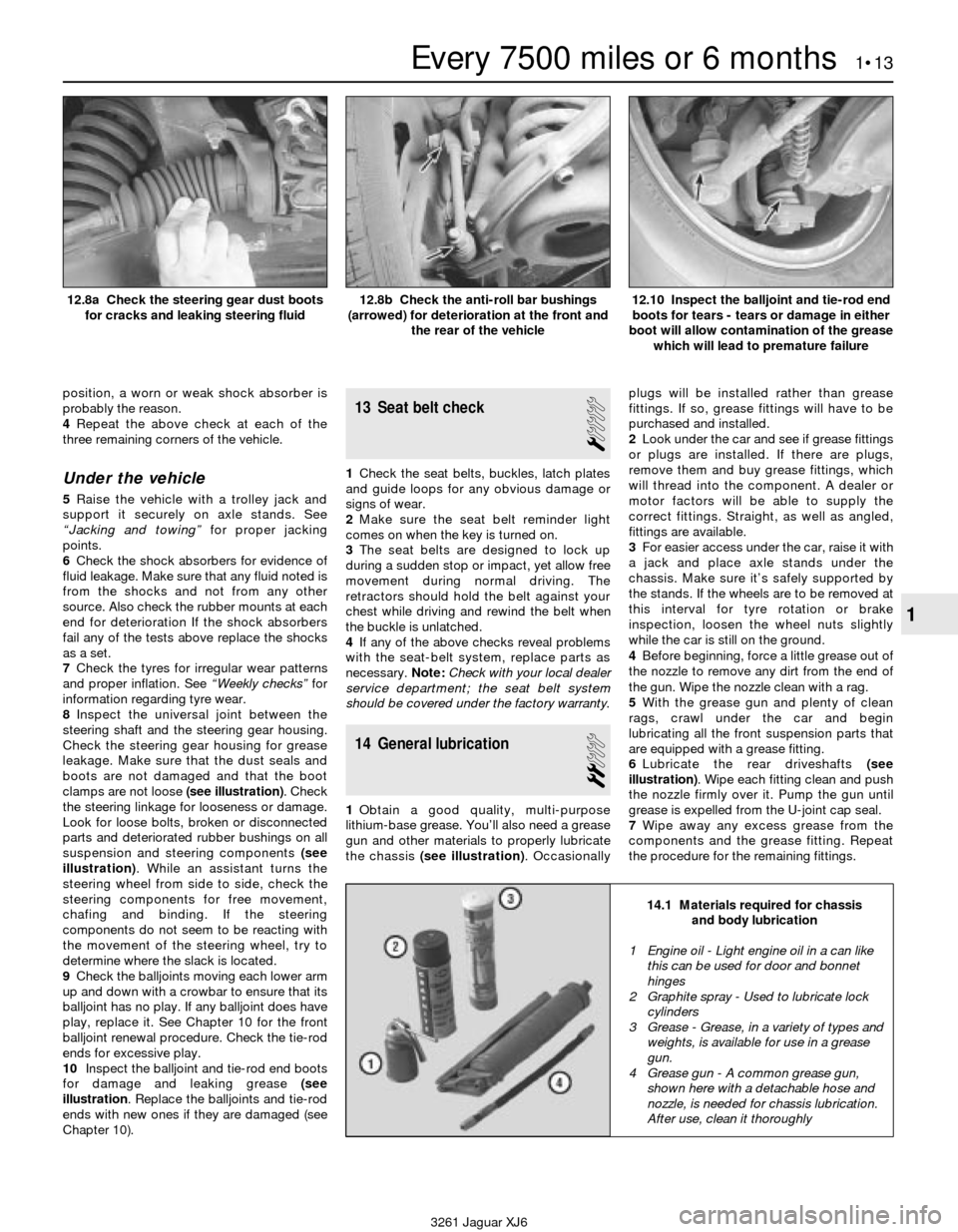
position, a worn or weak shock absorber is
probably the reason.
4Repeat the above check at each of the
three remaining corners of the vehicle.
Under the vehicle
5Raise the vehicle with a trolley jack and
support it securely on axle stands. See
“Jacking and towing”for proper jacking
points.
6Check the shock absorbers for evidence of
fluid leakage. Make sure that any fluid noted is
from the shocks and not from any other
source. Also check the rubber mounts at each
end for deterioration If the shock absorbers
fail any of the tests above replace the shocks
as a set.
7Check the tyres for irregular wear patterns
and proper inflation. See “Weekly checks”for
information regarding tyre wear.
8Inspect the universal joint between the
steering shaft and the steering gear housing.
Check the steering gear housing for grease
leakage. Make sure that the dust seals and
boots are not damaged and that the boot
clamps are not loose (see illustration). Check
the steering linkage for looseness or damage.
Look for loose bolts, broken or disconnected
parts and deteriorated rubber bushings on all
suspension and steering components (see
illustration). While an assistant turns the
steering wheel from side to side, check the
steering components for free movement,
chafing and binding. If the steering
components do not seem to be reacting with
the movement of the steering wheel, try to
determine where the slack is located.
9Check the balljoints moving each lower arm
up and down with a crowbar to ensure that its
balljoint has no play. If any balljoint does have
play, replace it. See Chapter 10 for the front
balljoint renewal procedure. Check the tie-rod
ends for excessive play.
10Inspect the balljoint and tie-rod end boots
for damage and leaking grease (see
illustration. Replace the balljoints and tie-rod
ends with new ones if they are damaged (see
Chapter 10).
13 Seat belt check
1
1Check the seat belts, buckles, latch plates
and guide loops for any obvious damage or
signs of wear.
2Make sure the seat belt reminder light
comes on when the key is turned on.
3The seat belts are designed to lock up
during a sudden stop or impact, yet allow free
movement during normal driving. The
retractors should hold the belt against your
chest while driving and rewind the belt when
the buckle is unlatched.
4If any of the above checks reveal problems
with the seat-belt system, replace parts as
necessary.Note:Check with your local dealer
service department; the seat belt system
should be covered under the factory warranty.
14 General lubrication
2
1Obtain a good quality, multi-purpose
lithium-base grease. You’ll also need a grease
gun and other materials to properly lubricate
the chassis (see illustration). Occasionallyplugs will be installed rather than grease
fittings. If so, grease fittings will have to be
purchased and installed.
2Look under the car and see if grease fittings
or plugs are installed. If there are plugs,
remove them and buy grease fittings, which
will thread into the component. A dealer or
motor factors will be able to supply the
correct fittings. Straight, as well as angled,
fittings are available.
3For easier access under the car, raise it with
a jack and place axle stands under the
chassis. Make sure it’s safely supported by
the stands. If the wheels are to be removed at
this interval for tyre rotation or brake
inspection, loosen the wheel nuts slightly
while the car is still on the ground.
4Before beginning, force a little grease out of
the nozzle to remove any dirt from the end of
the gun. Wipe the nozzle clean with a rag.
5With the grease gun and plenty of clean
rags, crawl under the car and begin
lubricating all the front suspension parts that
are equipped with a grease fitting.
6Lubricate the rear driveshafts (see
illustration). Wipe each fitting clean and push
the nozzle firmly over it. Pump the gun until
grease is expelled from the U-joint cap seal.
7Wipe away any excess grease from the
components and the grease fitting. Repeat
the procedure for the remaining fittings.
Every 7500 miles or 6 months 1•13
1
14.1 Materials required for chassis
and body lubrication
3261 Jaguar XJ6 12.8a Check the steering gear dust boots
for cracks and leaking steering fluid
12.8b Check the anti-roll bar bushings
(arrowed) for deterioration at the front and
the rear of the vehicle12.10 Inspect the balljoint and tie-rod end
boots for tears - tears or damage in either
boot will allow contamination of the grease
which will lead to premature failure
1 Engine oil - Light engine oil in a can like
this can be used for door and bonnet
hinges
2 Graphite spray - Used to lubricate lock
cylinders
3 Grease - Grease, in a variety of types and
weights, is available for use in a grease
gun.
4 Grease gun - A common grease gun,
shown here with a detachable hose and
nozzle, is needed for chassis lubrication.
After use, clean it thoroughly
Page 202 of 227
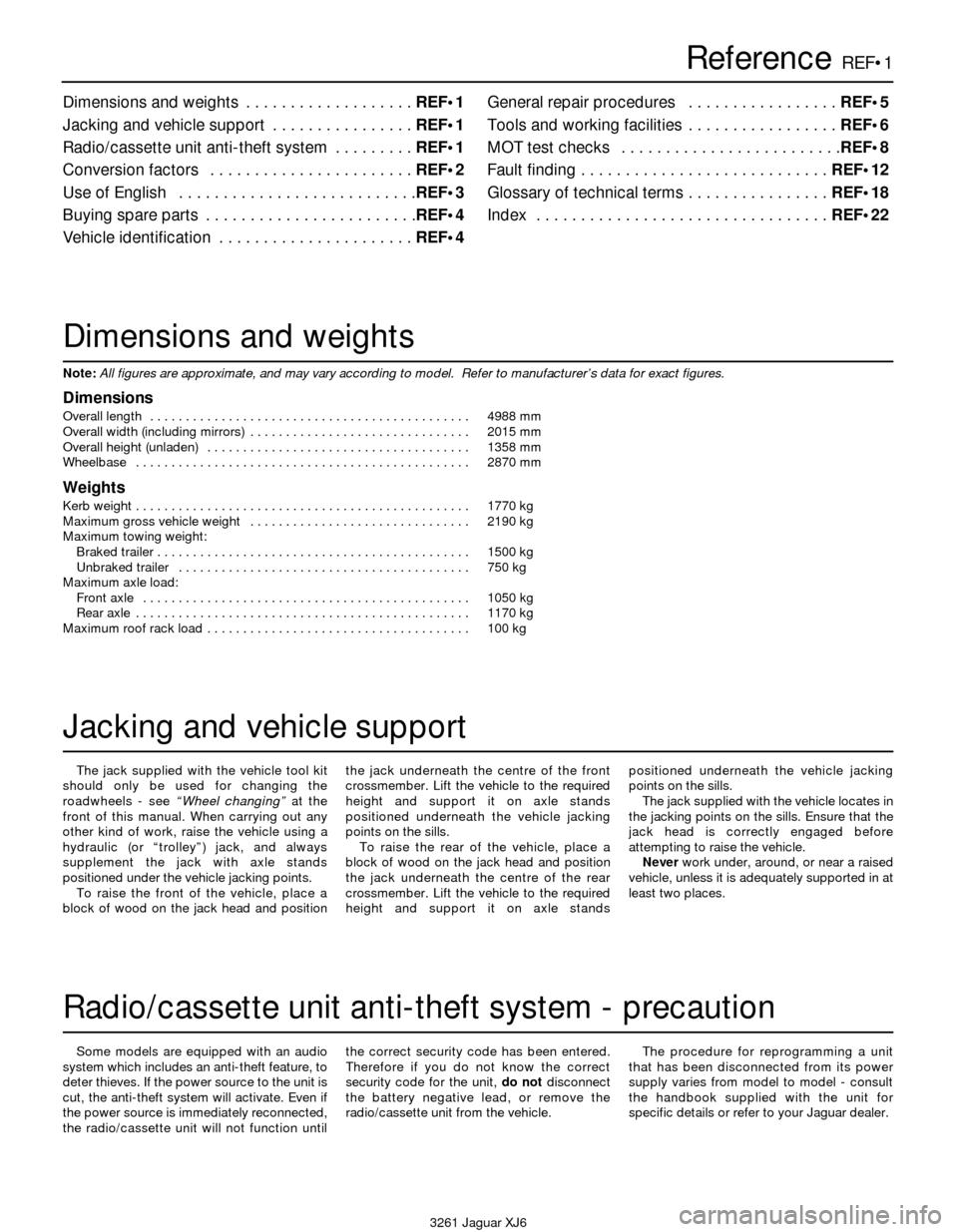
3261 Jaguar XJ6
Dimensions and weights . . . . . . . . . . . . . . . . . . .REF•1
Jacking and vehicle support . . . . . . . . . . . . . . . .REF•1
Radio/cassette unit anti-theft system . . . . . . . . .REF•1
Conversion factors . . . . . . . . . . . . . . . . . . . . . . .REF•2
Use of English . . . . . . . . . . . . . . . . . . . . . . . . . . .REF•3
Buying spare parts . . . . . . . . . . . . . . . . . . . . . . . .REF•4
Vehicle identification . . . . . . . . . . . . . . . . . . . . . .REF•4General repair procedures . . . . . . . . . . . . . . . . .REF•5
Tools and working facilities . . . . . . . . . . . . . . . . .REF•6
MOT test checks . . . . . . . . . . . . . . . . . . . . . . . . .REF•8
Fault finding . . . . . . . . . . . . . . . . . . . . . . . . . . . .REF•12
Glossary of technical terms . . . . . . . . . . . . . . . .REF•18
Index . . . . . . . . . . . . . . . . . . . . . . . . . . . . . . . . .REF•22
Dimensions and weights
Note:All figures are approximate, and may vary according to model. Refer to manufacturer’s data for exact figures.
Dimensions
Overall length . . . . . . . . . . . . . . . . . . . . . . . . . . . . . . . . . . . . . . . . . . . . . 4988 mm
Overall width (including mirrors) . . . . . . . . . . . . . . . . . . . . . . . . . . . . . . . 2015 mm
Overall height (unladen) . . . . . . . . . . . . . . . . . . . . . . . . . . . . . . . . . . . . . 1358 mm
Wheelbase . . . . . . . . . . . . . . . . . . . . . . . . . . . . . . . . . . . . . . . . . . . . . . . 2870 mm
Weights
Kerb weight . . . . . . . . . . . . . . . . . . . . . . . . . . . . . . . . . . . . . . . . . . . . . . . 1770 kg
Maximum gross vehicle weight . . . . . . . . . . . . . . . . . . . . . . . . . . . . . . . 2190 kg
Maximum towing weight:
Braked trailer . . . . . . . . . . . . . . . . . . . . . . . . . . . . . . . . . . . . . . . . . . . . 1500 kg
Unbraked trailer . . . . . . . . . . . . . . . . . . . . . . . . . . . . . . . . . . . . . . . . . 750 kg
Maximum axle load:
Front axle . . . . . . . . . . . . . . . . . . . . . . . . . . . . . . . . . . . . . . . . . . . . . . 1050 kg
Rear axle . . . . . . . . . . . . . . . . . . . . . . . . . . . . . . . . . . . . . . . . . . . . . . . 1170 kg
Maximum roof rack load . . . . . . . . . . . . . . . . . . . . . . . . . . . . . . . . . . . . . 100 kg
ReferenceREF•1
Radio/cassette unit anti-theft system - precaution
Some models are equipped with an audio
system which includes an anti-theft feature, to
deter thieves. If the power source to the unit is
cut, the anti-theft system will activate. Even if
the power source is immediately reconnected,
the radio/cassette unit will not function untilthe correct security code has been entered.
Therefore if you do not know the correct
security code for the unit, do notdisconnect
the battery negative lead, or remove the
radio/cassette unit from the vehicle.The procedure for reprogramming a unit
that has been disconnected from its power
supply varies from model to model - consult
the handbook supplied with the unit for
specific details or refer to your Jaguar dealer. The jack supplied with the vehicle tool kit
should only be used for changing the
roadwheels - see “Wheel changing”at the
front of this manual. When carrying out any
other kind of work, raise the vehicle using a
hydraulic (or “trolley”) jack, and always
supplement the jack with axle stands
positioned under the vehicle jacking points.
To raise the front of the vehicle, place a
block of wood on the jack head and positionthe jack underneath the centre of the front
crossmember. Lift the vehicle to the required
height and support it on axle stands
positioned underneath the vehicle jacking
points on the sills.
To raise the rear of the vehicle, place a
block of wood on the jack head and position
the jack underneath the centre of the rear
crossmember. Lift the vehicle to the required
height and support it on axle standspositioned underneath the vehicle jacking
points on the sills.
The jack supplied with the vehicle locates in
the jacking points on the sills. Ensure that the
jack head is correctly engaged before
attempting to raise the vehicle.
Neverwork under, around, or near a raised
vehicle, unless it is adequately supported in at
least two places.
Jacking and vehicle support
Page 224 of 227
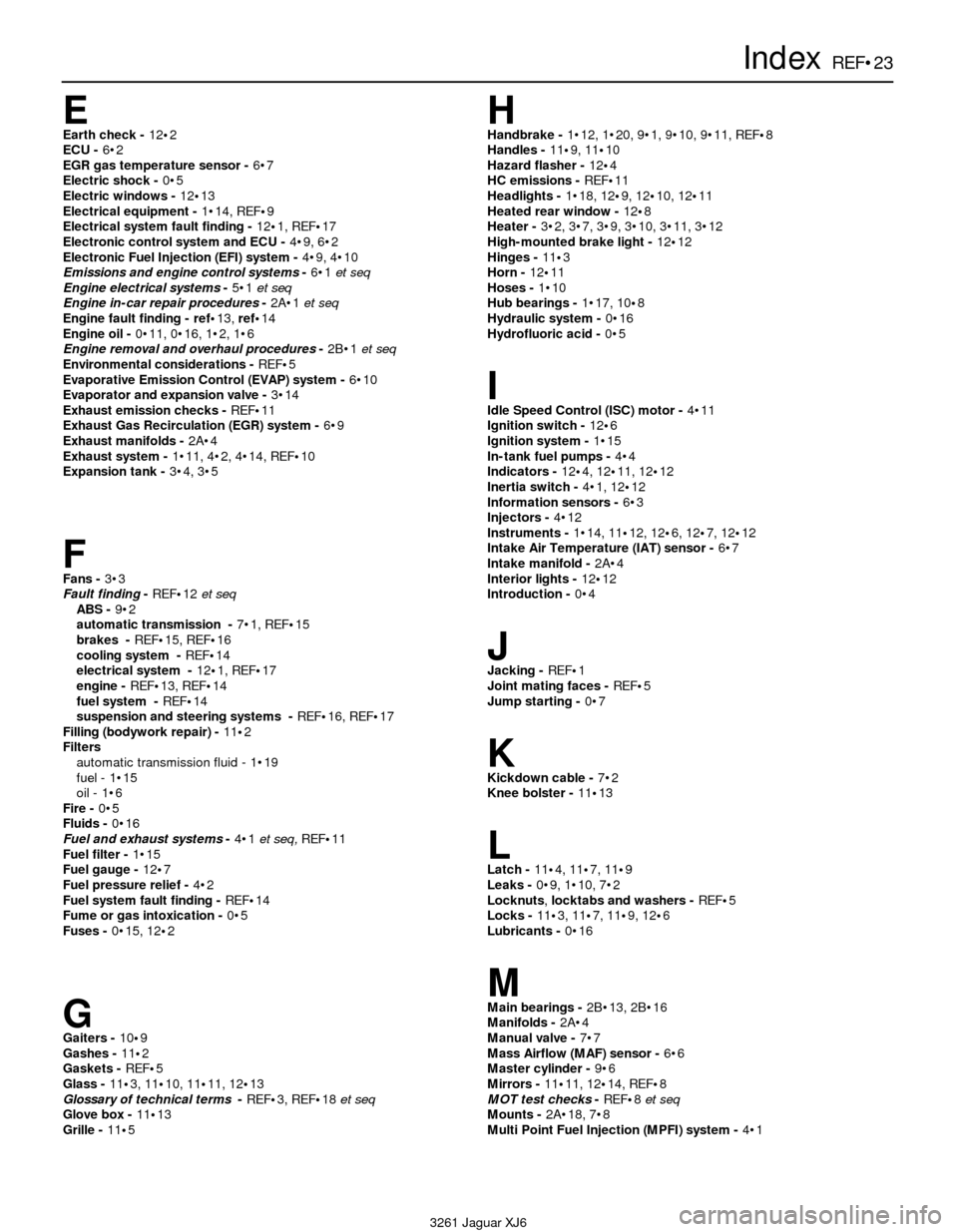
3261 Jaguar XJ6
IndexREF•23
EEarth check - 12•2
ECU -6•2
EGR gas temperature sensor -6•7
Electric shock -0•5
Electric windows - 12•13
Electrical equipment -1•14, REF•9
Electrical system fault finding - 12•1, REF•17
Electronic control system and ECU -4•9, 6•2
Electronic Fuel Injection (EFI) system -4•9, 4•10
Emissions and engine control systems-6•1et seq
Engine electrical systems-5•1et seq
Engine in-car repair procedures-2A•1et seq
Engine fault finding - ref•13,ref•14
Engine oil -0•11, 0•16, 1•2, 1•6
Engine removal and overhaul procedures-2B•1et seq
Environmental considerations - REF•5
Evaporative Emission Control (EVAP) system -6•10
Evaporator and expansion valve -3•14
Exhaust emission checks - REF•11
Exhaust Gas Recirculation (EGR) system -6•9
Exhaust manifolds -2A•4
Exhaust system -1•11, 4•2, 4•14, REF•10
Expansion tank -3•4, 3•5
FFans -3•3
Fault finding- REF•12et seq
ABS -9•2
automatic transmission - 7•1, REF•15
brakes - REF•15, REF•16
cooling system - REF•14
electrical system - 12•1, REF•17
engine - REF•13, REF•14
fuel system - REF•14
suspension and steering systems - REF•16, REF•17
Filling (bodywork repair) - 11•2
Filters
automatic transmission fluid - 1•19
fuel - 1•15
oil - 1•6
Fire -0•5
Fluids -0•16
Fuel and exhaust systems-4•1et seq, REF•11
Fuel filter -1•15
Fuel gauge - 12•7
Fuel pressure relief -4•2
Fuel system fault finding - REF•14
Fume or gas intoxication -0•5
Fuses -0•15, 12•2
GGaiters - 10•9
Gashes - 11•2
Gaskets - REF•5
Glass - 11•3, 11•10, 11•11, 12•13
Glossary of technical terms- REF•3, REF•18et seq
Glove box - 11•13
Grille - 11•5
HHandbrake -1•12, 1•20, 9•1, 9•10, 9•11, REF•8
Handles - 11•9, 11•10
Hazard flasher - 12•4
HC emissions - REF•11
Headlights -1•18, 12•9, 12•10, 12•11
Heated rear window - 12•8
Heater -3•2, 3•7, 3•9, 3•10, 3•11, 3•12
High-mounted brake light - 12•12
Hinges - 11•3
Horn - 12•11
Hoses -1•10
Hub bearings - 1•17, 10•8
Hydraulic system -0•16
Hydrofluoric acid -0•5
IIdle Speed Control (ISC) motor -4•11
Ignition switch - 12•6
Ignition system -1•15
In-tank fuel pumps -4•4
Indicators - 12•4, 12•11, 12•12
Inertia switch -4•1, 12•12
Information sensors -6•3
Injectors -4•12
Instruments - 1•14, 11•12, 12•6, 12•7, 12•12
Intake Air Temperature (IAT) sensor -6•7
Intake manifold -2A•4
Interior lights - 12•12
Introduction -0•4
JJacking - REF•1
Joint mating faces - REF•5
Jump starting -0•7
KKickdown cable -7•2
Knee bolster - 11•13
LLatch - 11•4, 11•7, 11•9
Leaks -0•9, 1•10, 7•2
Locknuts,locktabs and washers - REF•5
Locks - 11•3, 11•7, 11•9, 12•6
Lubricants -0•16
MMain bearings -2B•13, 2B•16
Manifolds -2A•4
Manual valve -7•7
Mass Airflow (MAF) sensor -6•6
Master cylinder -9•6
Mirrors - 11•11, 12•14, REF•8
MOT test checks- REF•8et seq
Mounts -2A•18, 7•8
Multi Point Fuel Injection (MPFI) system -4•1