Cable JEEP GRAND CHEROKEE 2002 WJ / 2.G Workshop Manual
[x] Cancel search | Manufacturer: JEEP, Model Year: 2002, Model line: GRAND CHEROKEE, Model: JEEP GRAND CHEROKEE 2002 WJ / 2.GPages: 2199, PDF Size: 76.01 MB
Page 488 of 2199
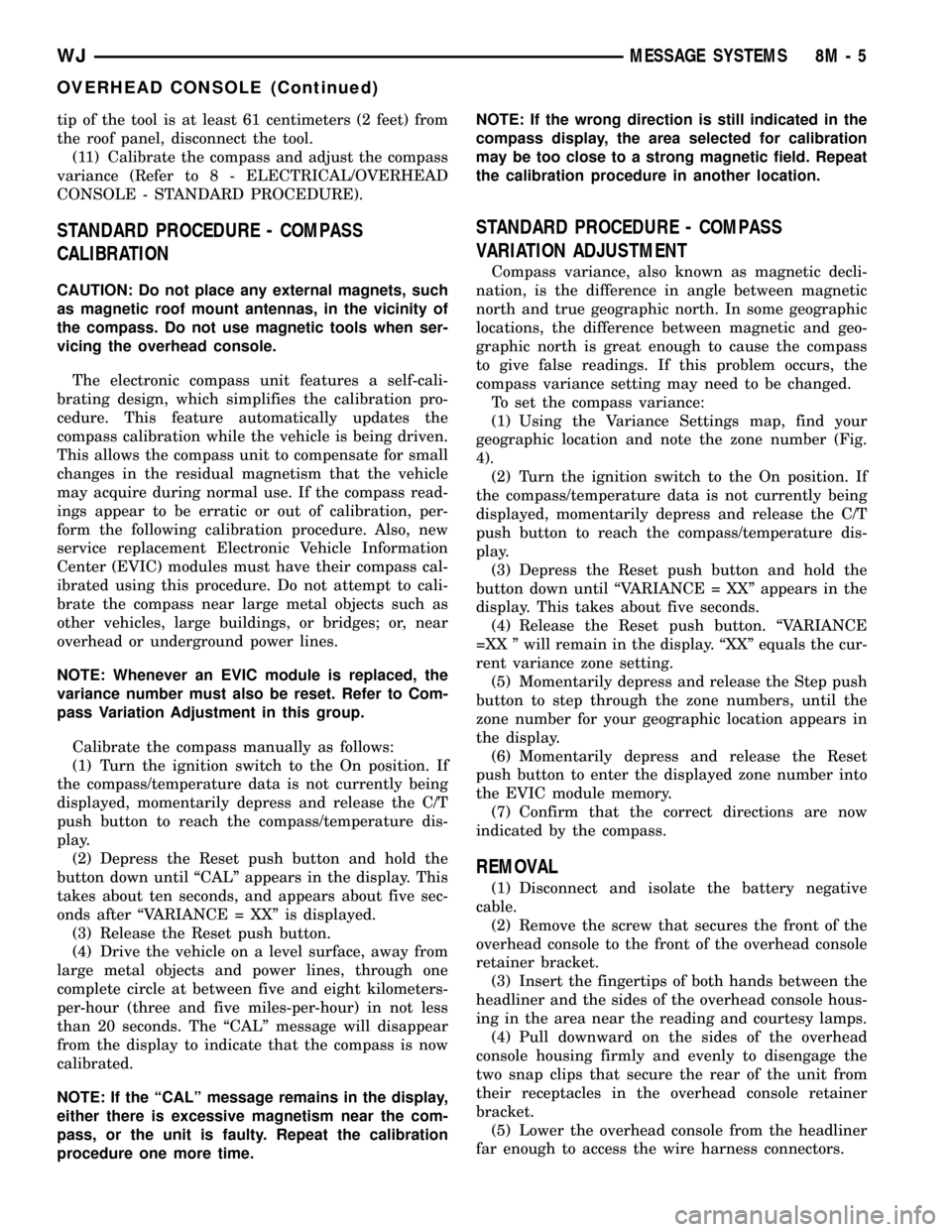
tip of the tool is at least 61 centimeters (2 feet) from
the roof panel, disconnect the tool.
(11) Calibrate the compass and adjust the compass
variance (Refer to 8 - ELECTRICAL/OVERHEAD
CONSOLE - STANDARD PROCEDURE).
STANDARD PROCEDURE - COMPASS
CALIBRATION
CAUTION: Do not place any external magnets, such
as magnetic roof mount antennas, in the vicinity of
the compass. Do not use magnetic tools when ser-
vicing the overhead console.
The electronic compass unit features a self-cali-
brating design, which simplifies the calibration pro-
cedure. This feature automatically updates the
compass calibration while the vehicle is being driven.
This allows the compass unit to compensate for small
changes in the residual magnetism that the vehicle
may acquire during normal use. If the compass read-
ings appear to be erratic or out of calibration, per-
form the following calibration procedure. Also, new
service replacement Electronic Vehicle Information
Center (EVIC) modules must have their compass cal-
ibrated using this procedure. Do not attempt to cali-
brate the compass near large metal objects such as
other vehicles, large buildings, or bridges; or, near
overhead or underground power lines.
NOTE: Whenever an EVIC module is replaced, the
variance number must also be reset. Refer to Com-
pass Variation Adjustment in this group.
Calibrate the compass manually as follows:
(1) Turn the ignition switch to the On position. If
the compass/temperature data is not currently being
displayed, momentarily depress and release the C/T
push button to reach the compass/temperature dis-
play.
(2) Depress the Reset push button and hold the
button down until ªCALº appears in the display. This
takes about ten seconds, and appears about five sec-
onds after ªVARIANCE = XXº is displayed.
(3) Release the Reset push button.
(4) Drive the vehicle on a level surface, away from
large metal objects and power lines, through one
complete circle at between five and eight kilometers-
per-hour (three and five miles-per-hour) in not less
than 20 seconds. The ªCALº message will disappear
from the display to indicate that the compass is now
calibrated.
NOTE: If the ªCALº message remains in the display,
either there is excessive magnetism near the com-
pass, or the unit is faulty. Repeat the calibration
procedure one more time.NOTE: If the wrong direction is still indicated in the
compass display, the area selected for calibration
may be too close to a strong magnetic field. Repeat
the calibration procedure in another location.
STANDARD PROCEDURE - COMPASS
VARIATION ADJUSTMENT
Compass variance, also known as magnetic decli-
nation, is the difference in angle between magnetic
north and true geographic north. In some geographic
locations, the difference between magnetic and geo-
graphic north is great enough to cause the compass
to give false readings. If this problem occurs, the
compass variance setting may need to be changed.
To set the compass variance:
(1) Using the Variance Settings map, find your
geographic location and note the zone number (Fig.
4).
(2) Turn the ignition switch to the On position. If
the compass/temperature data is not currently being
displayed, momentarily depress and release the C/T
push button to reach the compass/temperature dis-
play.
(3) Depress the Reset push button and hold the
button down until ªVARIANCE = XXº appears in the
display. This takes about five seconds.
(4) Release the Reset push button. ªVARIANCE
=XX º will remain in the display. ªXXº equals the cur-
rent variance zone setting.
(5) Momentarily depress and release the Step push
button to step through the zone numbers, until the
zone number for your geographic location appears in
the display.
(6) Momentarily depress and release the Reset
push button to enter the displayed zone number into
the EVIC module memory.
(7) Confirm that the correct directions are now
indicated by the compass.
REMOVAL
(1) Disconnect and isolate the battery negative
cable.
(2) Remove the screw that secures the front of the
overhead console to the front of the overhead console
retainer bracket.
(3) Insert the fingertips of both hands between the
headliner and the sides of the overhead console hous-
ing in the area near the reading and courtesy lamps.
(4) Pull downward on the sides of the overhead
console housing firmly and evenly to disengage the
two snap clips that secure the rear of the unit from
their receptacles in the overhead console retainer
bracket.
(5) Lower the overhead console from the headliner
far enough to access the wire harness connectors.
WJMESSAGE SYSTEMS 8M - 5
OVERHEAD CONSOLE (Continued)
Page 489 of 2199
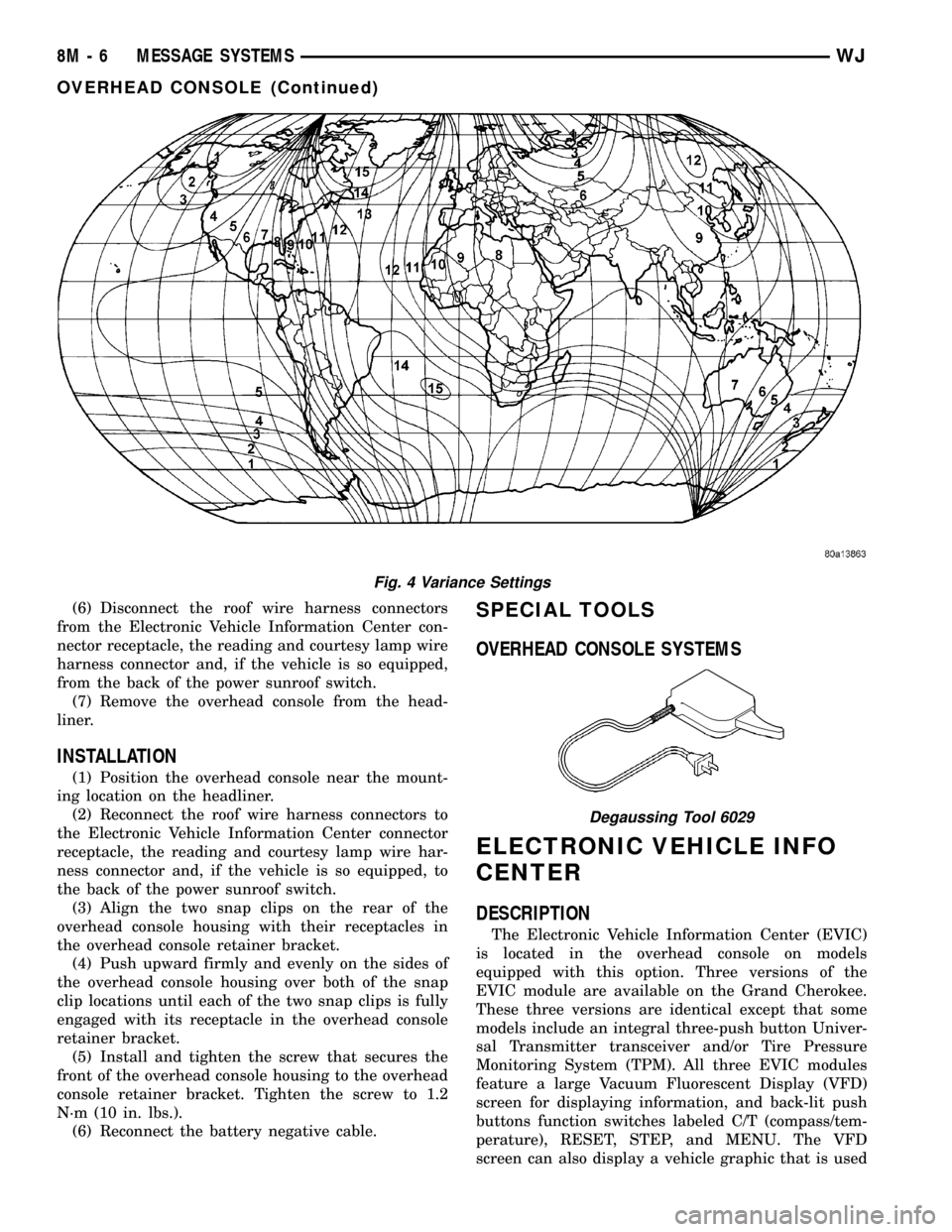
(6) Disconnect the roof wire harness connectors
from the Electronic Vehicle Information Center con-
nector receptacle, the reading and courtesy lamp wire
harness connector and, if the vehicle is so equipped,
from the back of the power sunroof switch.
(7) Remove the overhead console from the head-
liner.
INSTALLATION
(1) Position the overhead console near the mount-
ing location on the headliner.
(2) Reconnect the roof wire harness connectors to
the Electronic Vehicle Information Center connector
receptacle, the reading and courtesy lamp wire har-
ness connector and, if the vehicle is so equipped, to
the back of the power sunroof switch.
(3) Align the two snap clips on the rear of the
overhead console housing with their receptacles in
the overhead console retainer bracket.
(4) Push upward firmly and evenly on the sides of
the overhead console housing over both of the snap
clip locations until each of the two snap clips is fully
engaged with its receptacle in the overhead console
retainer bracket.
(5) Install and tighten the screw that secures the
front of the overhead console housing to the overhead
console retainer bracket. Tighten the screw to 1.2
N´m (10 in. lbs.).
(6) Reconnect the battery negative cable.
SPECIAL TOOLS
OVERHEAD CONSOLE SYSTEMS
ELECTRONIC VEHICLE INFO
CENTER
DESCRIPTION
The Electronic Vehicle Information Center (EVIC)
is located in the overhead console on models
equipped with this option. Three versions of the
EVIC module are available on the Grand Cherokee.
These three versions are identical except that some
models include an integral three-push button Univer-
sal Transmitter transceiver and/or Tire Pressure
Monitoring System (TPM). All three EVIC modules
feature a large Vacuum Fluorescent Display (VFD)
screen for displaying information, and back-lit push
buttons function switches labeled C/T (compass/tem-
perature), RESET, STEP, and MENU. The VFD
screen can also display a vehicle graphic that is used
Fig. 4 Variance Settings
Degaussing Tool 6029
8M - 6 MESSAGE SYSTEMSWJ
OVERHEAD CONSOLE (Continued)
Page 492 of 2199
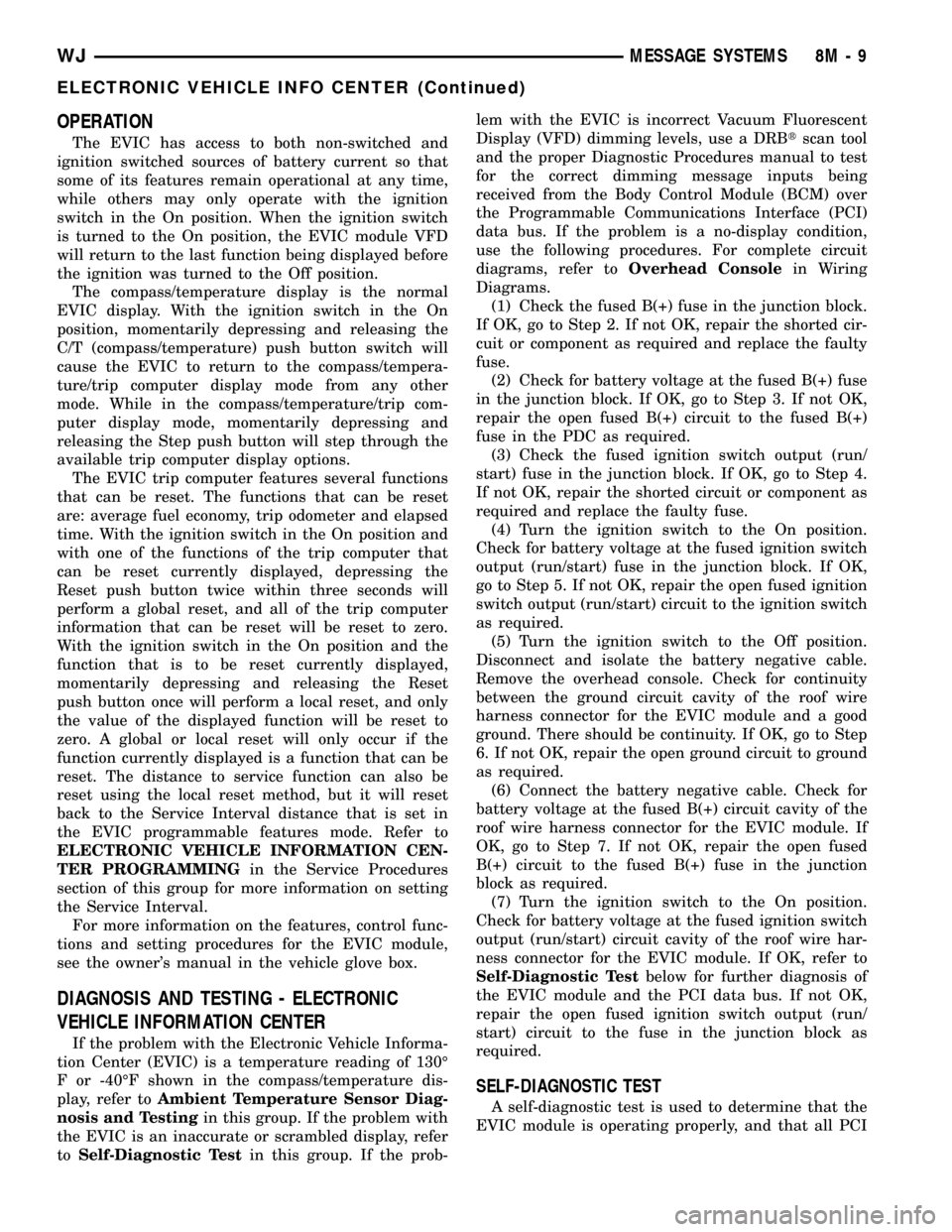
OPERATION
The EVIC has access to both non-switched and
ignition switched sources of battery current so that
some of its features remain operational at any time,
while others may only operate with the ignition
switch in the On position. When the ignition switch
is turned to the On position, the EVIC module VFD
will return to the last function being displayed before
the ignition was turned to the Off position.
The compass/temperature display is the normal
EVIC display. With the ignition switch in the On
position, momentarily depressing and releasing the
C/T (compass/temperature) push button switch will
cause the EVIC to return to the compass/tempera-
ture/trip computer display mode from any other
mode. While in the compass/temperature/trip com-
puter display mode, momentarily depressing and
releasing the Step push button will step through the
available trip computer display options.
The EVIC trip computer features several functions
that can be reset. The functions that can be reset
are: average fuel economy, trip odometer and elapsed
time. With the ignition switch in the On position and
with one of the functions of the trip computer that
can be reset currently displayed, depressing the
Reset push button twice within three seconds will
perform a global reset, and all of the trip computer
information that can be reset will be reset to zero.
With the ignition switch in the On position and the
function that is to be reset currently displayed,
momentarily depressing and releasing the Reset
push button once will perform a local reset, and only
the value of the displayed function will be reset to
zero. A global or local reset will only occur if the
function currently displayed is a function that can be
reset. The distance to service function can also be
reset using the local reset method, but it will reset
back to the Service Interval distance that is set in
the EVIC programmable features mode. Refer to
ELECTRONIC VEHICLE INFORMATION CEN-
TER PROGRAMMINGin the Service Procedures
section of this group for more information on setting
the Service Interval.
For more information on the features, control func-
tions and setting procedures for the EVIC module,
see the owner's manual in the vehicle glove box.
DIAGNOSIS AND TESTING - ELECTRONIC
VEHICLE INFORMATION CENTER
If the problem with the Electronic Vehicle Informa-
tion Center (EVIC) is a temperature reading of 130É
F or -40ÉF shown in the compass/temperature dis-
play, refer toAmbient Temperature Sensor Diag-
nosis and Testingin this group. If the problem with
the EVIC is an inaccurate or scrambled display, refer
toSelf-Diagnostic Testin this group. If the prob-lem with the EVIC is incorrect Vacuum Fluorescent
Display (VFD) dimming levels, use a DRBtscan tool
and the proper Diagnostic Procedures manual to test
for the correct dimming message inputs being
received from the Body Control Module (BCM) over
the Programmable Communications Interface (PCI)
data bus. If the problem is a no-display condition,
use the following procedures. For complete circuit
diagrams, refer toOverhead Consolein Wiring
Diagrams.
(1) Check the fused B(+) fuse in the junction block.
If OK, go to Step 2. If not OK, repair the shorted cir-
cuit or component as required and replace the faulty
fuse.
(2) Check for battery voltage at the fused B(+) fuse
in the junction block. If OK, go to Step 3. If not OK,
repair the open fused B(+) circuit to the fused B(+)
fuse in the PDC as required.
(3) Check the fused ignition switch output (run/
start) fuse in the junction block. If OK, go to Step 4.
If not OK, repair the shorted circuit or component as
required and replace the faulty fuse.
(4) Turn the ignition switch to the On position.
Check for battery voltage at the fused ignition switch
output (run/start) fuse in the junction block. If OK,
go to Step 5. If not OK, repair the open fused ignition
switch output (run/start) circuit to the ignition switch
as required.
(5) Turn the ignition switch to the Off position.
Disconnect and isolate the battery negative cable.
Remove the overhead console. Check for continuity
between the ground circuit cavity of the roof wire
harness connector for the EVIC module and a good
ground. There should be continuity. If OK, go to Step
6. If not OK, repair the open ground circuit to ground
as required.
(6) Connect the battery negative cable. Check for
battery voltage at the fused B(+) circuit cavity of the
roof wire harness connector for the EVIC module. If
OK, go to Step 7. If not OK, repair the open fused
B(+) circuit to the fused B(+) fuse in the junction
block as required.
(7) Turn the ignition switch to the On position.
Check for battery voltage at the fused ignition switch
output (run/start) circuit cavity of the roof wire har-
ness connector for the EVIC module. If OK, refer to
Self-Diagnostic Testbelow for further diagnosis of
the EVIC module and the PCI data bus. If not OK,
repair the open fused ignition switch output (run/
start) circuit to the fuse in the junction block as
required.
SELF-DIAGNOSTIC TEST
A self-diagnostic test is used to determine that the
EVIC module is operating properly, and that all PCI
WJMESSAGE SYSTEMS 8M - 9
ELECTRONIC VEHICLE INFO CENTER (Continued)
Page 493 of 2199
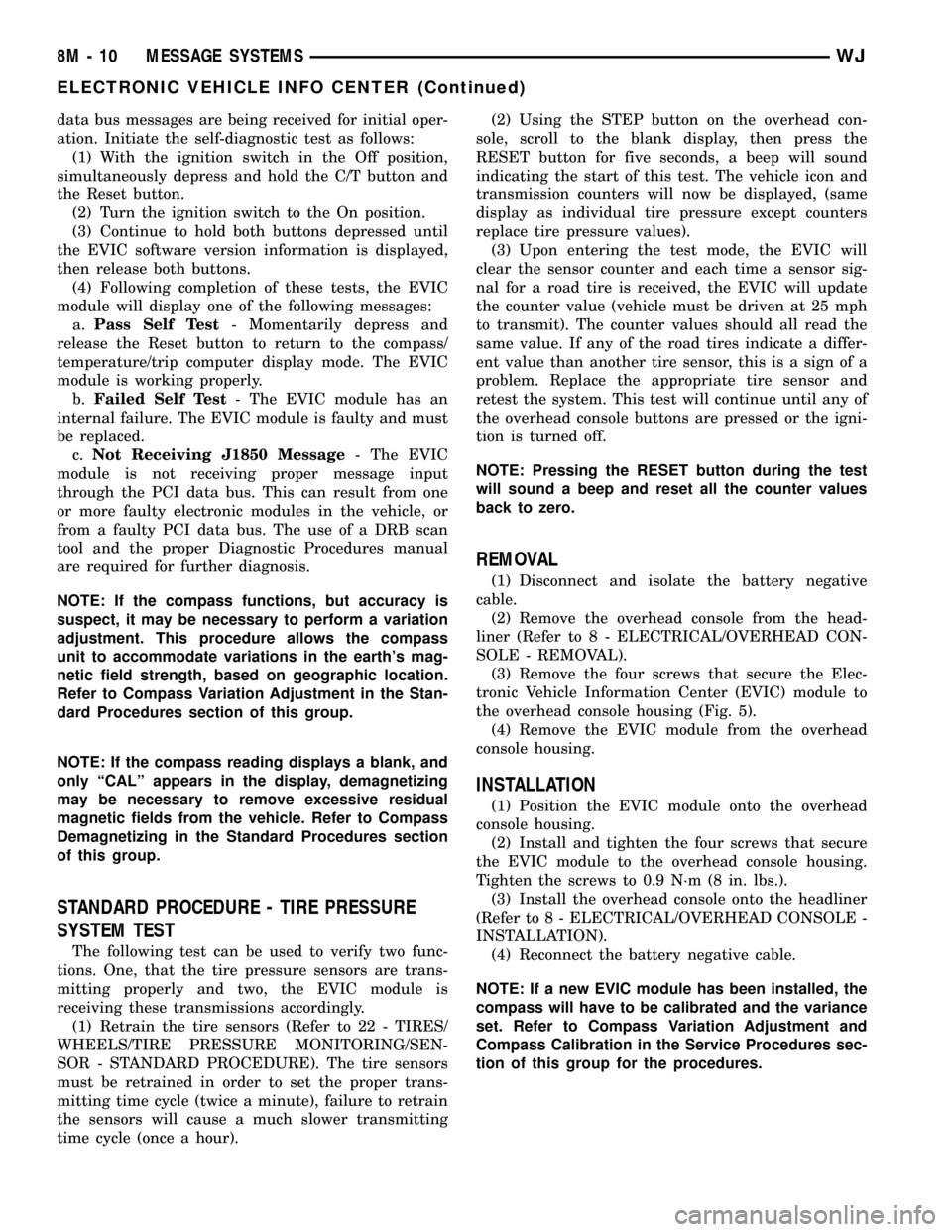
data bus messages are being received for initial oper-
ation. Initiate the self-diagnostic test as follows:
(1) With the ignition switch in the Off position,
simultaneously depress and hold the C/T button and
the Reset button.
(2) Turn the ignition switch to the On position.
(3) Continue to hold both buttons depressed until
the EVIC software version information is displayed,
then release both buttons.
(4) Following completion of these tests, the EVIC
module will display one of the following messages:
a.Pass Self Test- Momentarily depress and
release the Reset button to return to the compass/
temperature/trip computer display mode. The EVIC
module is working properly.
b.Failed Self Test- The EVIC module has an
internal failure. The EVIC module is faulty and must
be replaced.
c.Not Receiving J1850 Message- The EVIC
module is not receiving proper message input
through the PCI data bus. This can result from one
or more faulty electronic modules in the vehicle, or
from a faulty PCI data bus. The use of a DRB scan
tool and the proper Diagnostic Procedures manual
are required for further diagnosis.
NOTE: If the compass functions, but accuracy is
suspect, it may be necessary to perform a variation
adjustment. This procedure allows the compass
unit to accommodate variations in the earth's mag-
netic field strength, based on geographic location.
Refer to Compass Variation Adjustment in the Stan-
dard Procedures section of this group.
NOTE: If the compass reading displays a blank, and
only ªCALº appears in the display, demagnetizing
may be necessary to remove excessive residual
magnetic fields from the vehicle. Refer to Compass
Demagnetizing in the Standard Procedures section
of this group.
STANDARD PROCEDURE - TIRE PRESSURE
SYSTEM TEST
The following test can be used to verify two func-
tions. One, that the tire pressure sensors are trans-
mitting properly and two, the EVIC module is
receiving these transmissions accordingly.
(1) Retrain the tire sensors (Refer to 22 - TIRES/
WHEELS/TIRE PRESSURE MONITORING/SEN-
SOR - STANDARD PROCEDURE). The tire sensors
must be retrained in order to set the proper trans-
mitting time cycle (twice a minute), failure to retrain
the sensors will cause a much slower transmitting
time cycle (once a hour).(2) Using the STEP button on the overhead con-
sole, scroll to the blank display, then press the
RESET button for five seconds, a beep will sound
indicating the start of this test. The vehicle icon and
transmission counters will now be displayed, (same
display as individual tire pressure except counters
replace tire pressure values).
(3) Upon entering the test mode, the EVIC will
clear the sensor counter and each time a sensor sig-
nal for a road tire is received, the EVIC will update
the counter value (vehicle must be driven at 25 mph
to transmit). The counter values should all read the
same value. If any of the road tires indicate a differ-
ent value than another tire sensor, this is a sign of a
problem. Replace the appropriate tire sensor and
retest the system. This test will continue until any of
the overhead console buttons are pressed or the igni-
tion is turned off.
NOTE: Pressing the RESET button during the test
will sound a beep and reset all the counter values
back to zero.
REMOVAL
(1) Disconnect and isolate the battery negative
cable.
(2) Remove the overhead console from the head-
liner (Refer to 8 - ELECTRICAL/OVERHEAD CON-
SOLE - REMOVAL).
(3) Remove the four screws that secure the Elec-
tronic Vehicle Information Center (EVIC) module to
the overhead console housing (Fig. 5).
(4) Remove the EVIC module from the overhead
console housing.
INSTALLATION
(1) Position the EVIC module onto the overhead
console housing.
(2) Install and tighten the four screws that secure
the EVIC module to the overhead console housing.
Tighten the screws to 0.9 N´m (8 in. lbs.).
(3) Install the overhead console onto the headliner
(Refer to 8 - ELECTRICAL/OVERHEAD CONSOLE -
INSTALLATION).
(4) Reconnect the battery negative cable.
NOTE: If a new EVIC module has been installed, the
compass will have to be calibrated and the variance
set. Refer to Compass Variation Adjustment and
Compass Calibration in the Service Procedures sec-
tion of this group for the procedures.
8M - 10 MESSAGE SYSTEMSWJ
ELECTRONIC VEHICLE INFO CENTER (Continued)
Page 495 of 2199
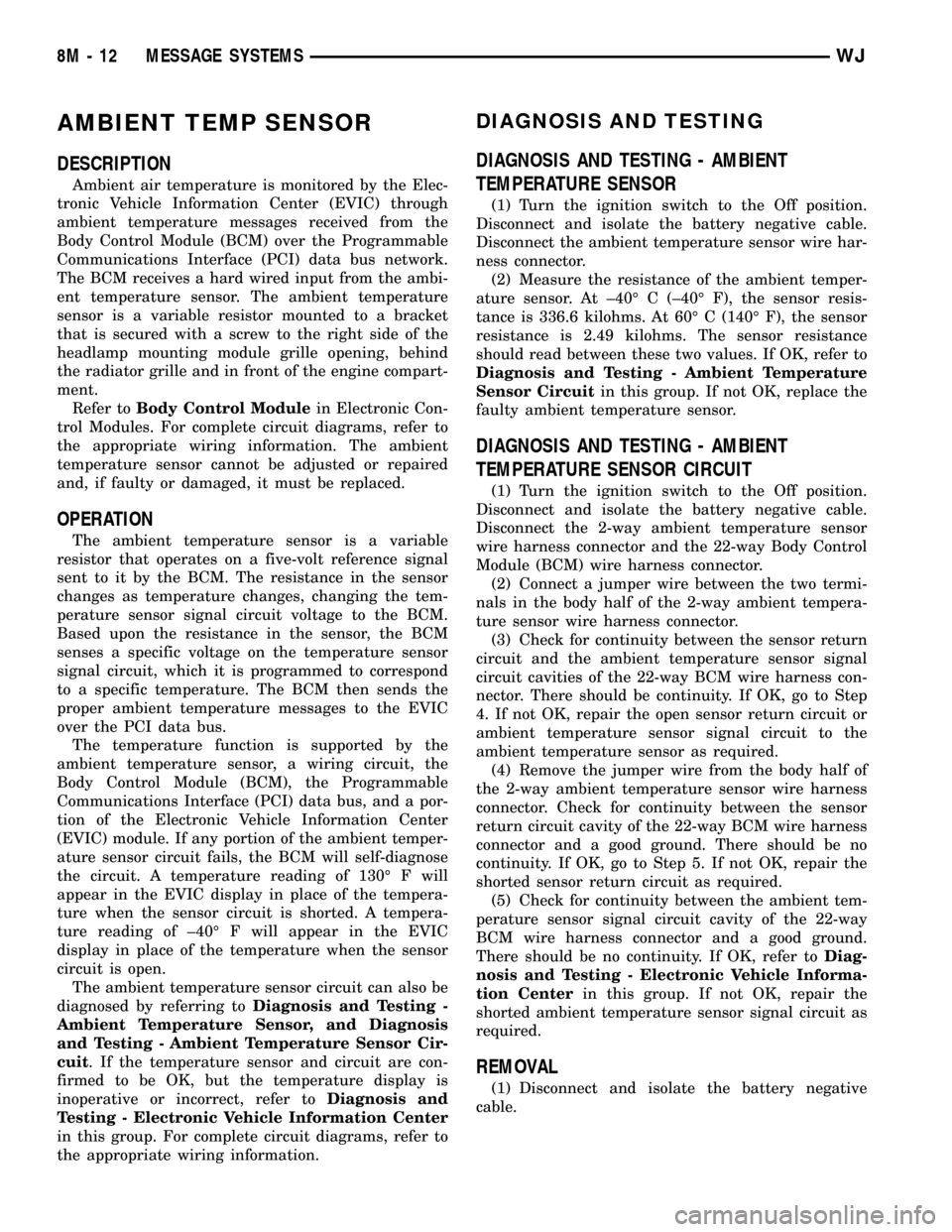
AMBIENT TEMP SENSOR
DESCRIPTION
Ambient air temperature is monitored by the Elec-
tronic Vehicle Information Center (EVIC) through
ambient temperature messages received from the
Body Control Module (BCM) over the Programmable
Communications Interface (PCI) data bus network.
The BCM receives a hard wired input from the ambi-
ent temperature sensor. The ambient temperature
sensor is a variable resistor mounted to a bracket
that is secured with a screw to the right side of the
headlamp mounting module grille opening, behind
the radiator grille and in front of the engine compart-
ment.
Refer toBody Control Modulein Electronic Con-
trol Modules. For complete circuit diagrams, refer to
the appropriate wiring information. The ambient
temperature sensor cannot be adjusted or repaired
and, if faulty or damaged, it must be replaced.
OPERATION
The ambient temperature sensor is a variable
resistor that operates on a five-volt reference signal
sent to it by the BCM. The resistance in the sensor
changes as temperature changes, changing the tem-
perature sensor signal circuit voltage to the BCM.
Based upon the resistance in the sensor, the BCM
senses a specific voltage on the temperature sensor
signal circuit, which it is programmed to correspond
to a specific temperature. The BCM then sends the
proper ambient temperature messages to the EVIC
over the PCI data bus.
The temperature function is supported by the
ambient temperature sensor, a wiring circuit, the
Body Control Module (BCM), the Programmable
Communications Interface (PCI) data bus, and a por-
tion of the Electronic Vehicle Information Center
(EVIC) module. If any portion of the ambient temper-
ature sensor circuit fails, the BCM will self-diagnose
the circuit. A temperature reading of 130É F will
appear in the EVIC display in place of the tempera-
ture when the sensor circuit is shorted. A tempera-
ture reading of ±40É F will appear in the EVIC
display in place of the temperature when the sensor
circuit is open.
The ambient temperature sensor circuit can also be
diagnosed by referring toDiagnosis and Testing -
Ambient Temperature Sensor, and Diagnosis
and Testing - Ambient Temperature Sensor Cir-
cuit. If the temperature sensor and circuit are con-
firmed to be OK, but the temperature display is
inoperative or incorrect, refer toDiagnosis and
Testing - Electronic Vehicle Information Center
in this group. For complete circuit diagrams, refer to
the appropriate wiring information.
DIAGNOSIS AND TESTING
DIAGNOSIS AND TESTING - AMBIENT
TEMPERATURE SENSOR
(1) Turn the ignition switch to the Off position.
Disconnect and isolate the battery negative cable.
Disconnect the ambient temperature sensor wire har-
ness connector.
(2) Measure the resistance of the ambient temper-
ature sensor. At ±40É C (±40É F), the sensor resis-
tance is 336.6 kilohms. At 60É C (140É F), the sensor
resistance is 2.49 kilohms. The sensor resistance
should read between these two values. If OK, refer to
Diagnosis and Testing - Ambient Temperature
Sensor Circuitin this group. If not OK, replace the
faulty ambient temperature sensor.
DIAGNOSIS AND TESTING - AMBIENT
TEMPERATURE SENSOR CIRCUIT
(1) Turn the ignition switch to the Off position.
Disconnect and isolate the battery negative cable.
Disconnect the 2-way ambient temperature sensor
wire harness connector and the 22-way Body Control
Module (BCM) wire harness connector.
(2) Connect a jumper wire between the two termi-
nals in the body half of the 2-way ambient tempera-
ture sensor wire harness connector.
(3) Check for continuity between the sensor return
circuit and the ambient temperature sensor signal
circuit cavities of the 22-way BCM wire harness con-
nector. There should be continuity. If OK, go to Step
4. If not OK, repair the open sensor return circuit or
ambient temperature sensor signal circuit to the
ambient temperature sensor as required.
(4) Remove the jumper wire from the body half of
the 2-way ambient temperature sensor wire harness
connector. Check for continuity between the sensor
return circuit cavity of the 22-way BCM wire harness
connector and a good ground. There should be no
continuity. If OK, go to Step 5. If not OK, repair the
shorted sensor return circuit as required.
(5) Check for continuity between the ambient tem-
perature sensor signal circuit cavity of the 22-way
BCM wire harness connector and a good ground.
There should be no continuity. If OK, refer toDiag-
nosis and Testing - Electronic Vehicle Informa-
tion Centerin this group. If not OK, repair the
shorted ambient temperature sensor signal circuit as
required.
REMOVAL
(1) Disconnect and isolate the battery negative
cable.
8M - 12 MESSAGE SYSTEMSWJ
Page 496 of 2199
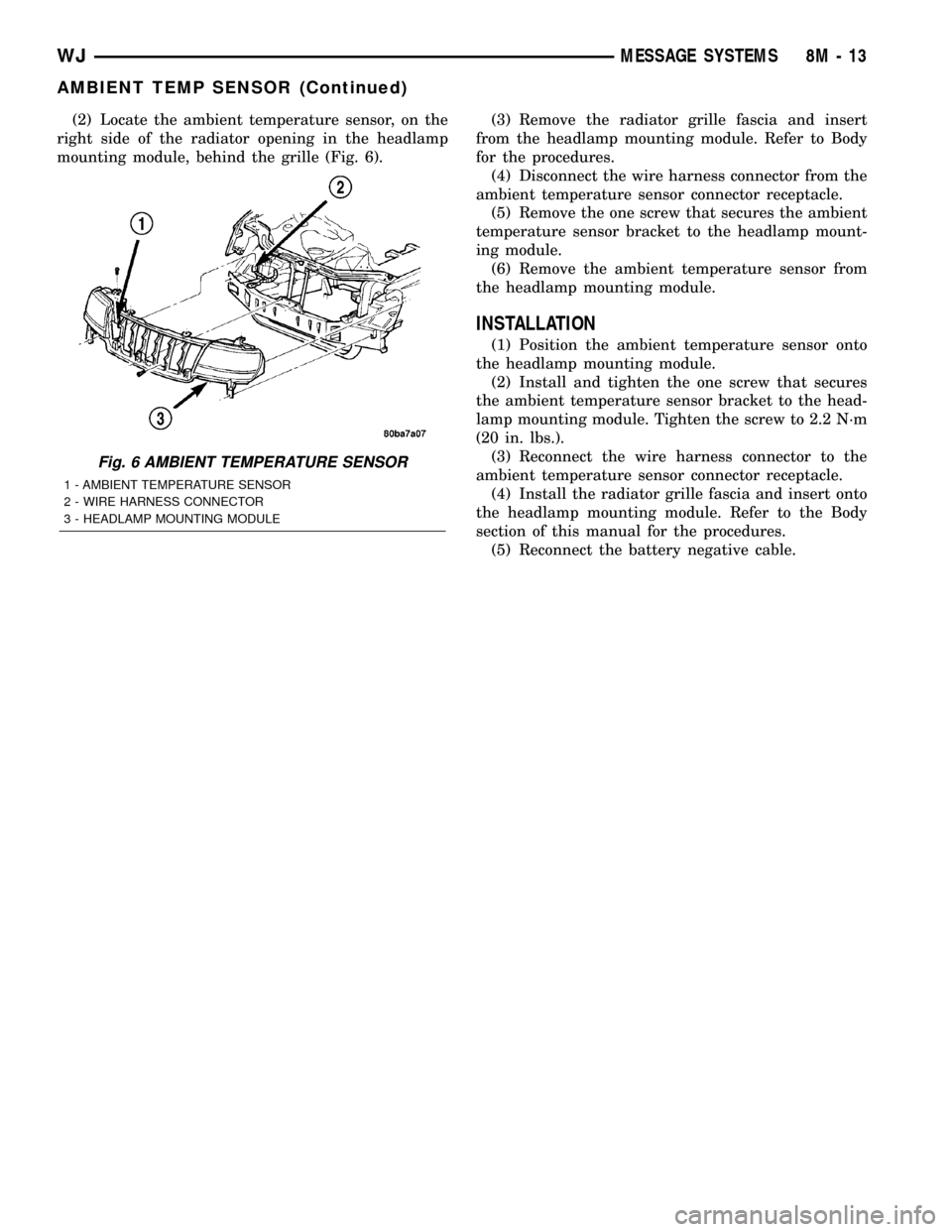
(2) Locate the ambient temperature sensor, on the
right side of the radiator opening in the headlamp
mounting module, behind the grille (Fig. 6).(3) Remove the radiator grille fascia and insert
from the headlamp mounting module. Refer to Body
for the procedures.
(4) Disconnect the wire harness connector from the
ambient temperature sensor connector receptacle.
(5) Remove the one screw that secures the ambient
temperature sensor bracket to the headlamp mount-
ing module.
(6) Remove the ambient temperature sensor from
the headlamp mounting module.
INSTALLATION
(1) Position the ambient temperature sensor onto
the headlamp mounting module.
(2) Install and tighten the one screw that secures
the ambient temperature sensor bracket to the head-
lamp mounting module. Tighten the screw to 2.2 N´m
(20 in. lbs.).
(3) Reconnect the wire harness connector to the
ambient temperature sensor connector receptacle.
(4) Install the radiator grille fascia and insert onto
the headlamp mounting module. Refer to the Body
section of this manual for the procedures.
(5) Reconnect the battery negative cable.
Fig. 6 AMBIENT TEMPERATURE SENSOR
1 - AMBIENT TEMPERATURE SENSOR
2 - WIRE HARNESS CONNECTOR
3 - HEADLAMP MOUNTING MODULE
WJMESSAGE SYSTEMS 8M - 13
AMBIENT TEMP SENSOR (Continued)
Page 513 of 2199
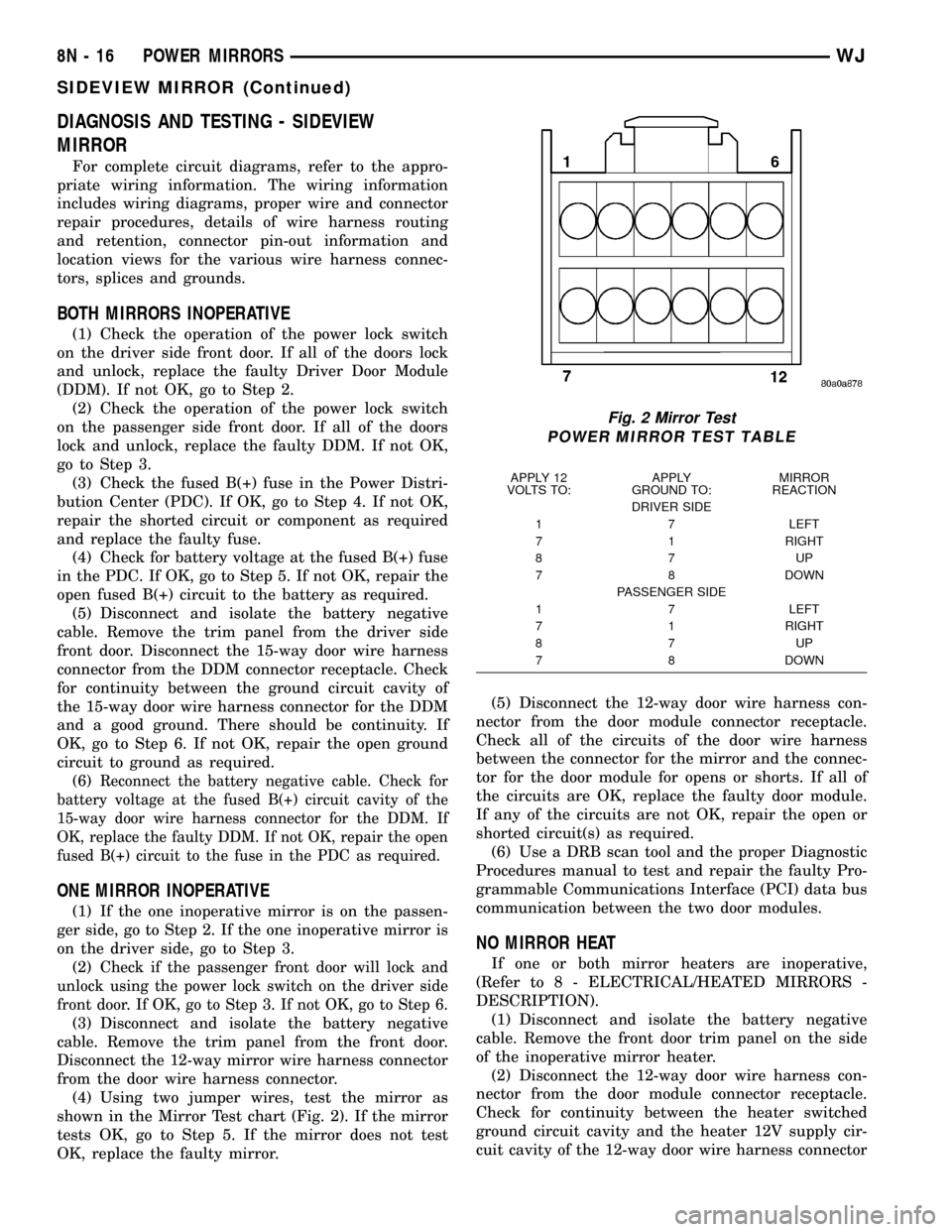
DIAGNOSIS AND TESTING - SIDEVIEW
MIRROR
For complete circuit diagrams, refer to the appro-
priate wiring information. The wiring information
includes wiring diagrams, proper wire and connector
repair procedures, details of wire harness routing
and retention, connector pin-out information and
location views for the various wire harness connec-
tors, splices and grounds.
BOTH MIRRORS INOPERATIVE
(1) Check the operation of the power lock switch
on the driver side front door. If all of the doors lock
and unlock, replace the faulty Driver Door Module
(DDM). If not OK, go to Step 2.
(2) Check the operation of the power lock switch
on the passenger side front door. If all of the doors
lock and unlock, replace the faulty DDM. If not OK,
go to Step 3.
(3) Check the fused B(+) fuse in the Power Distri-
bution Center (PDC). If OK, go to Step 4. If not OK,
repair the shorted circuit or component as required
and replace the faulty fuse.
(4) Check for battery voltage at the fused B(+) fuse
in the PDC. If OK, go to Step 5. If not OK, repair the
open fused B(+) circuit to the battery as required.
(5) Disconnect and isolate the battery negative
cable. Remove the trim panel from the driver side
front door. Disconnect the 15-way door wire harness
connector from the DDM connector receptacle. Check
for continuity between the ground circuit cavity of
the 15-way door wire harness connector for the DDM
and a good ground. There should be continuity. If
OK, go to Step 6. If not OK, repair the open ground
circuit to ground as required.
(6)
Reconnect the battery negative cable. Check for
battery voltage at the fused B(+) circuit cavity of the
15-way door wire harness connector for the DDM. If
OK, replace the faulty DDM. If not OK, repair the open
fused B(+) circuit to the fuse in the PDC as required.
ONE MIRROR INOPERATIVE
(1) If the one inoperative mirror is on the passen-
ger side, go to Step 2. If the one inoperative mirror is
on the driver side, go to Step 3.
(2)
Check if the passenger front door will lock and
unlock using the power lock switch on the driver side
front door. If OK, go to Step 3. If not OK, go to Step 6.
(3) Disconnect and isolate the battery negative
cable. Remove the trim panel from the front door.
Disconnect the 12-way mirror wire harness connector
from the door wire harness connector.
(4) Using two jumper wires, test the mirror as
shown in the Mirror Test chart (Fig. 2). If the mirror
tests OK, go to Step 5. If the mirror does not test
OK, replace the faulty mirror.(5) Disconnect the 12-way door wire harness con-
nector from the door module connector receptacle.
Check all of the circuits of the door wire harness
between the connector for the mirror and the connec-
tor for the door module for opens or shorts. If all of
the circuits are OK, replace the faulty door module.
If any of the circuits are not OK, repair the open or
shorted circuit(s) as required.
(6) Use a DRB scan tool and the proper Diagnostic
Procedures manual to test and repair the faulty Pro-
grammable Communications Interface (PCI) data bus
communication between the two door modules.
NO MIRROR HEAT
If one or both mirror heaters are inoperative,
(Refer to 8 - ELECTRICAL/HEATED MIRRORS -
DESCRIPTION).
(1) Disconnect and isolate the battery negative
cable. Remove the front door trim panel on the side
of the inoperative mirror heater.
(2) Disconnect the 12-way door wire harness con-
nector from the door module connector receptacle.
Check for continuity between the heater switched
ground circuit cavity and the heater 12V supply cir-
cuit cavity of the 12-way door wire harness connector
Fig. 2 Mirror Test
POWER MIRROR TEST TABLE
APPLY 12
VOLTS TO:APPLY
GROUND TO:MIRROR
REACTION
DRIVER SIDE
1 7 LEFT
7 1 RIGHT
87UP
7 8 DOWN
PASSENGER SIDE
1 7 LEFT
7 1 RIGHT
87UP
7 8 DOWN
8N - 16 POWER MIRRORSWJ
SIDEVIEW MIRROR (Continued)
Page 514 of 2199
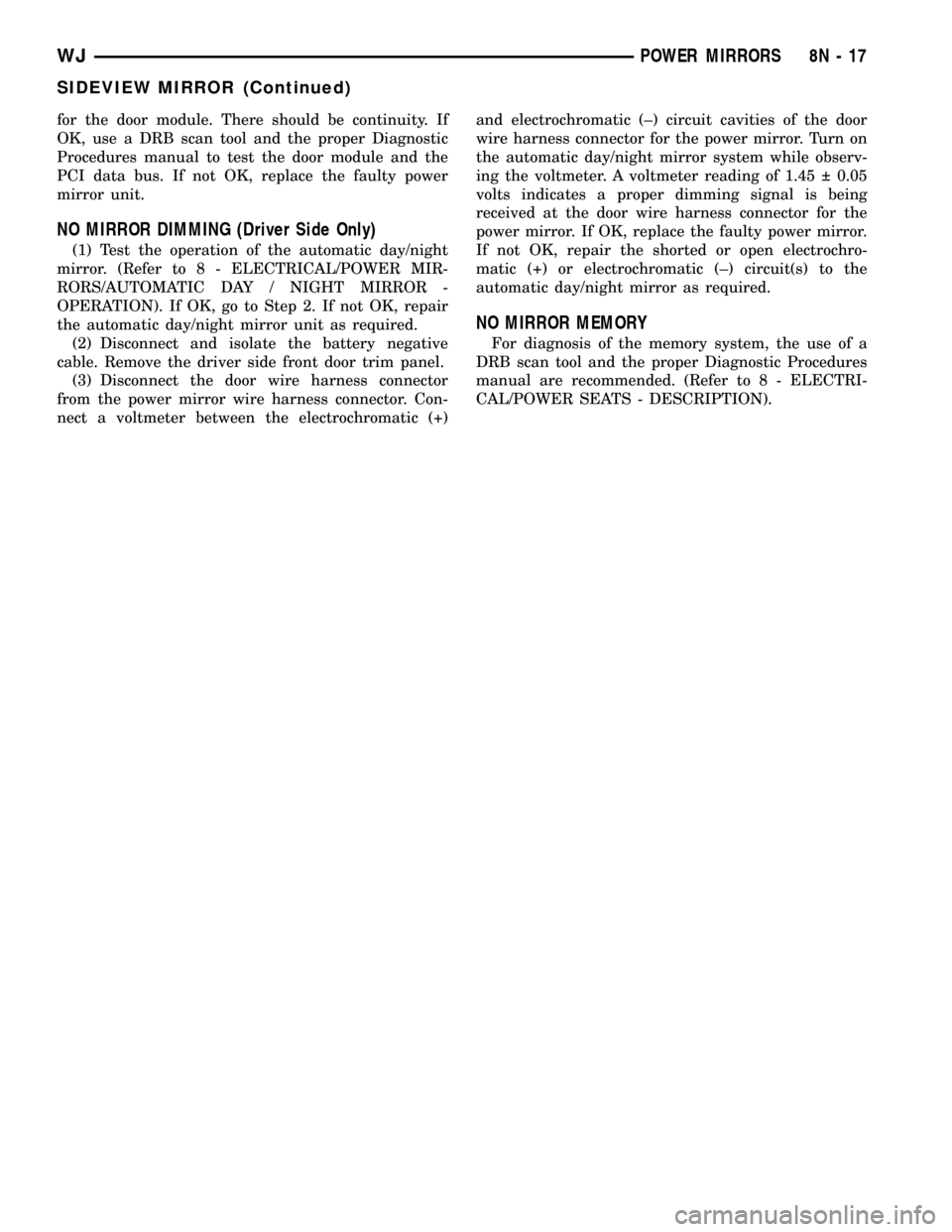
for the door module. There should be continuity. If
OK, use a DRB scan tool and the proper Diagnostic
Procedures manual to test the door module and the
PCI data bus. If not OK, replace the faulty power
mirror unit.
NO MIRROR DIMMING (Driver Side Only)
(1) Test the operation of the automatic day/night
mirror. (Refer to 8 - ELECTRICAL/POWER MIR-
RORS/AUTOMATIC DAY / NIGHT MIRROR -
OPERATION). If OK, go to Step 2. If not OK, repair
the automatic day/night mirror unit as required.
(2) Disconnect and isolate the battery negative
cable. Remove the driver side front door trim panel.
(3) Disconnect the door wire harness connector
from the power mirror wire harness connector. Con-
nect a voltmeter between the electrochromatic (+)and electrochromatic (±) circuit cavities of the door
wire harness connector for the power mirror. Turn on
the automatic day/night mirror system while observ-
ing the voltmeter. A voltmeter reading of 1.45 0.05
volts indicates a proper dimming signal is being
received at the door wire harness connector for the
power mirror. If OK, replace the faulty power mirror.
If not OK, repair the shorted or open electrochro-
matic (+) or electrochromatic (±) circuit(s) to the
automatic day/night mirror as required.
NO MIRROR MEMORY
For diagnosis of the memory system, the use of a
DRB scan tool and the proper Diagnostic Procedures
manual are recommended. (Refer to 8 - ELECTRI-
CAL/POWER SEATS - DESCRIPTION).
WJPOWER MIRRORS 8N - 17
SIDEVIEW MIRROR (Continued)
Page 519 of 2199
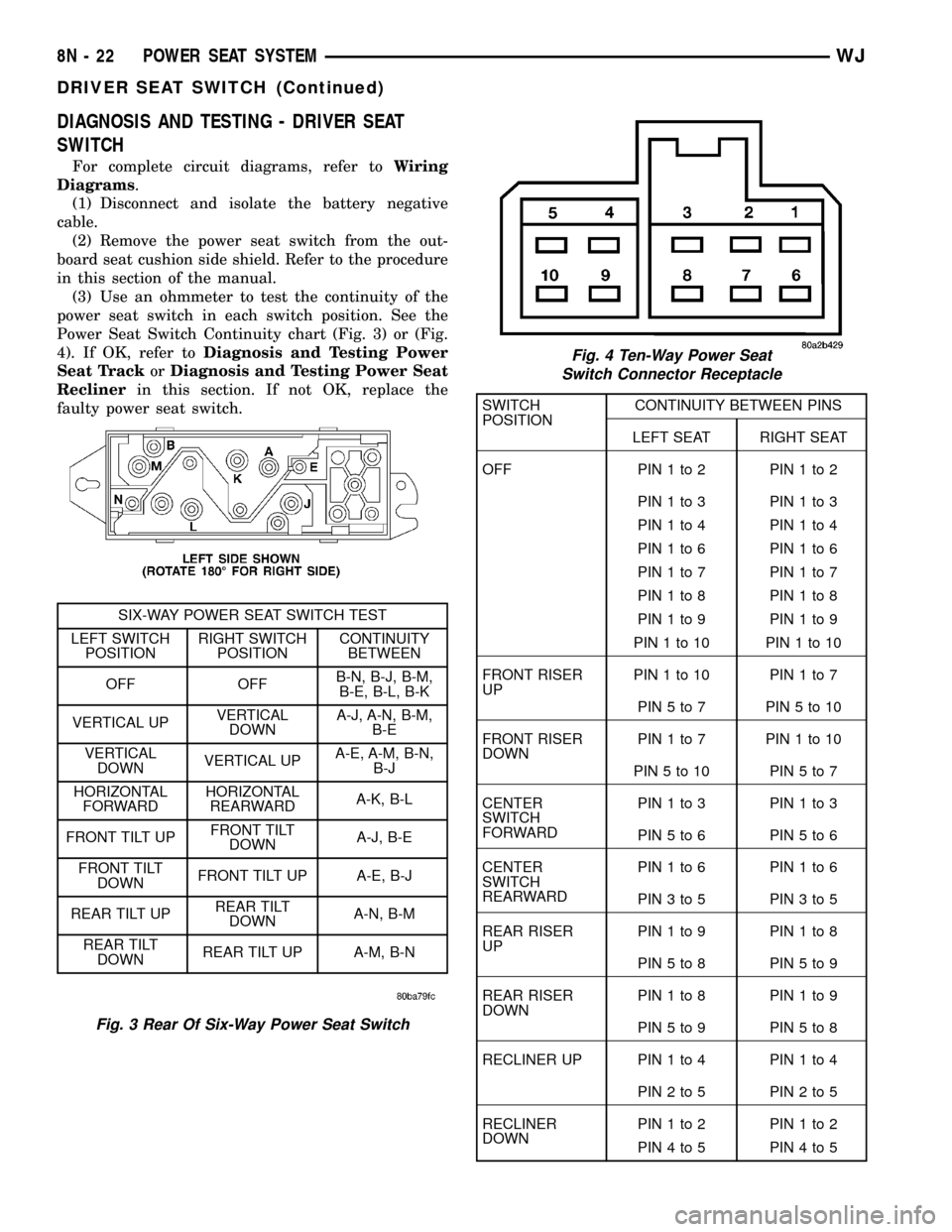
DIAGNOSIS AND TESTING - DRIVER SEAT
SWITCH
For complete circuit diagrams, refer toWiring
Diagrams.
(1) Disconnect and isolate the battery negative
cable.
(2) Remove the power seat switch from the out-
board seat cushion side shield. Refer to the procedure
in this section of the manual.
(3) Use an ohmmeter to test the continuity of the
power seat switch in each switch position. See the
Power Seat Switch Continuity chart (Fig. 3) or (Fig.
4). If OK, refer toDiagnosis and Testing Power
Seat TrackorDiagnosis and Testing Power Seat
Reclinerin this section. If not OK, replace the
faulty power seat switch.
SWITCH
POSITIONCONTINUITY BETWEEN PINS
LEFT SEAT RIGHT SEAT
OFF PIN1to2 PIN1to2
PIN1to3 PIN1to3
PIN1to4 PIN1to4
PIN1to6 PIN1to6
PIN1to7 PIN1to7
PIN1to8 PIN1to8
PIN1to9 PIN1to9
PIN1to10 PIN1to10
FRONT RISER
UPPIN1to10 PIN1to7
PIN5to7 PIN5to10
FRONT RISER
DOWNPIN1to7 PIN1to10
PIN5to10 PIN5to7
CENTER
SWITCH
FORWARDPIN1to3 PIN1to3
PIN5to6 PIN5to6
CENTER
SWITCH
REARWARDPIN1to6 PIN1to6
PIN3to5 PIN3to5
REAR RISER
UPPIN1to9 PIN1to8
PIN5to8 PIN5to9
REAR RISER
DOWNPIN1to8 PIN1to9
PIN5to9 PIN5to8
RECLINER UP PIN 1 to 4 PIN 1 to 4
PIN2to5 PIN2to5
RECLINER
DOWNPIN1to2 PIN1to2
PIN4to5 PIN4to5
Fig. 3 Rear Of Six-Way Power Seat Switch
SIX-WAY POWER SEAT SWITCH TEST
LEFT SWITCH
POSITIONRIGHT SWITCH
POSITIONCONTINUITY
BETWEEN
OFF OFFB-N, B-J, B-M,
B-E, B-L, B-K
VERTICAL UPVERTICAL
DOWNA-J, A-N, B-M,
B-E
VERTICAL
DOWNVERTICAL UPA-E, A-M, B-N,
B-J
HORIZONTAL
FORWARDHORIZONTAL
REARWARDA-K, B-L
FRONT TILT UPFRONT TILT
DOWNA-J, B-E
FRONT TILT
DOWNFRONT TILT UP A-E, B-J
REAR TILT UPREAR TILT
DOWNA-N, B-M
REAR TILT
DOWNREAR TILT UP A-M, B-N
Fig. 4 Ten-Way Power Seat
Switch Connector Receptacle
8N - 22 POWER SEAT SYSTEMWJ
DRIVER SEAT SWITCH (Continued)
Page 520 of 2199
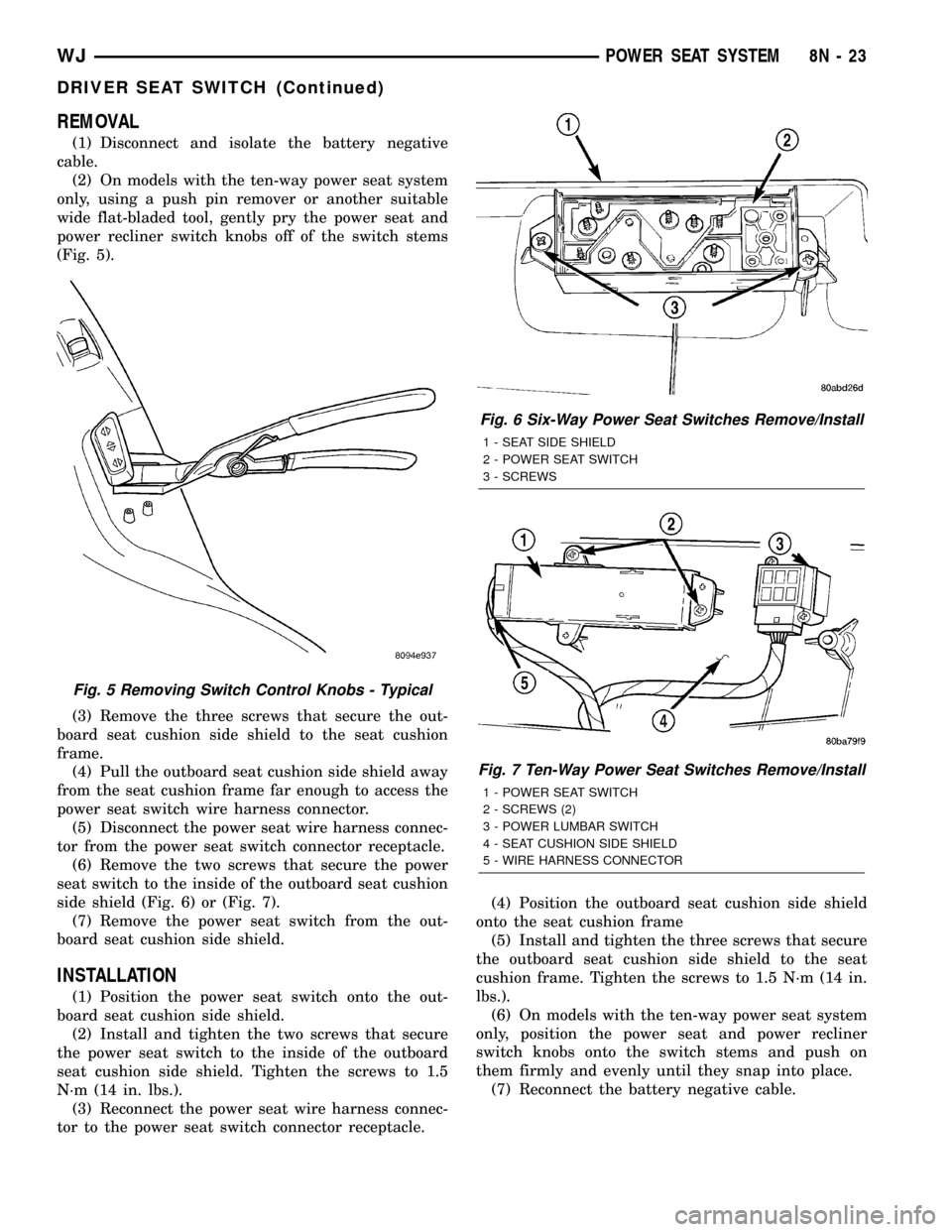
REMOVAL
(1) Disconnect and isolate the battery negative
cable.
(2) On models with the ten-way power seat system
only, using a push pin remover or another suitable
wide flat-bladed tool, gently pry the power seat and
power recliner switch knobs off of the switch stems
(Fig. 5).
(3) Remove the three screws that secure the out-
board seat cushion side shield to the seat cushion
frame.
(4) Pull the outboard seat cushion side shield away
from the seat cushion frame far enough to access the
power seat switch wire harness connector.
(5) Disconnect the power seat wire harness connec-
tor from the power seat switch connector receptacle.
(6) Remove the two screws that secure the power
seat switch to the inside of the outboard seat cushion
side shield (Fig. 6) or (Fig. 7).
(7) Remove the power seat switch from the out-
board seat cushion side shield.
INSTALLATION
(1) Position the power seat switch onto the out-
board seat cushion side shield.
(2) Install and tighten the two screws that secure
the power seat switch to the inside of the outboard
seat cushion side shield. Tighten the screws to 1.5
N´m (14 in. lbs.).
(3) Reconnect the power seat wire harness connec-
tor to the power seat switch connector receptacle.(4) Position the outboard seat cushion side shield
onto the seat cushion frame
(5) Install and tighten the three screws that secure
the outboard seat cushion side shield to the seat
cushion frame. Tighten the screws to 1.5 N´m (14 in.
lbs.).
(6) On models with the ten-way power seat system
only, position the power seat and power recliner
switch knobs onto the switch stems and push on
them firmly and evenly until they snap into place.
(7) Reconnect the battery negative cable.
Fig. 5 Removing Switch Control Knobs - Typical
Fig. 6 Six-Way Power Seat Switches Remove/Install
1 - SEAT SIDE SHIELD
2 - POWER SEAT SWITCH
3 - SCREWS
Fig. 7 Ten-Way Power Seat Switches Remove/Install
1 - POWER SEAT SWITCH
2 - SCREWS (2)
3 - POWER LUMBAR SWITCH
4 - SEAT CUSHION SIDE SHIELD
5 - WIRE HARNESS CONNECTOR
WJPOWER SEAT SYSTEM 8N - 23
DRIVER SEAT SWITCH (Continued)