Oil sensor JEEP GRAND CHEROKEE 2002 WJ / 2.G Owner's Manual
[x] Cancel search | Manufacturer: JEEP, Model Year: 2002, Model line: GRAND CHEROKEE, Model: JEEP GRAND CHEROKEE 2002 WJ / 2.GPages: 2199, PDF Size: 76.01 MB
Page 402 of 2199
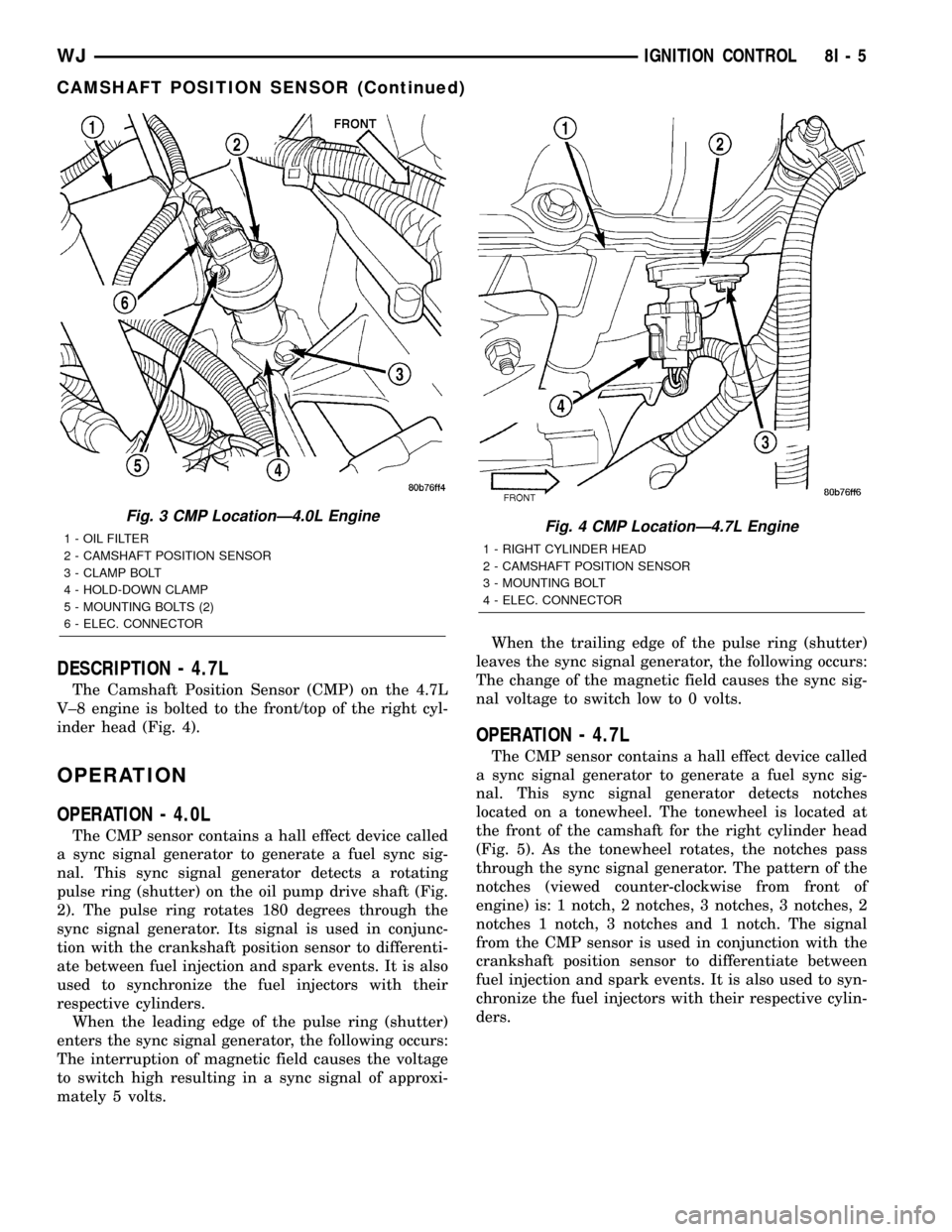
DESCRIPTION - 4.7L
The Camshaft Position Sensor (CMP) on the 4.7L
V±8 engine is bolted to the front/top of the right cyl-
inder head (Fig. 4).
OPERATION
OPERATION - 4.0L
The CMP sensor contains a hall effect device called
a sync signal generator to generate a fuel sync sig-
nal. This sync signal generator detects a rotating
pulse ring (shutter) on the oil pump drive shaft (Fig.
2). The pulse ring rotates 180 degrees through the
sync signal generator. Its signal is used in conjunc-
tion with the crankshaft position sensor to differenti-
ate between fuel injection and spark events. It is also
used to synchronize the fuel injectors with their
respective cylinders.
When the leading edge of the pulse ring (shutter)
enters the sync signal generator, the following occurs:
The interruption of magnetic field causes the voltage
to switch high resulting in a sync signal of approxi-
mately 5 volts.When the trailing edge of the pulse ring (shutter)
leaves the sync signal generator, the following occurs:
The change of the magnetic field causes the sync sig-
nal voltage to switch low to 0 volts.
OPERATION - 4.7L
The CMP sensor contains a hall effect device called
a sync signal generator to generate a fuel sync sig-
nal. This sync signal generator detects notches
located on a tonewheel. The tonewheel is located at
the front of the camshaft for the right cylinder head
(Fig. 5). As the tonewheel rotates, the notches pass
through the sync signal generator. The pattern of the
notches (viewed counter-clockwise from front of
engine) is: 1 notch, 2 notches, 3 notches, 3 notches, 2
notches 1 notch, 3 notches and 1 notch. The signal
from the CMP sensor is used in conjunction with the
crankshaft position sensor to differentiate between
fuel injection and spark events. It is also used to syn-
chronize the fuel injectors with their respective cylin-
ders.
Fig. 3 CMP LocationÐ4.0L Engine
1 - OIL FILTER
2 - CAMSHAFT POSITION SENSOR
3 - CLAMP BOLT
4 - HOLD-DOWN CLAMP
5 - MOUNTING BOLTS (2)
6 - ELEC. CONNECTORFig. 4 CMP LocationÐ4.7L Engine
1 - RIGHT CYLINDER HEAD
2 - CAMSHAFT POSITION SENSOR
3 - MOUNTING BOLT
4 - ELEC. CONNECTOR
WJIGNITION CONTROL 8I - 5
CAMSHAFT POSITION SENSOR (Continued)
Page 403 of 2199
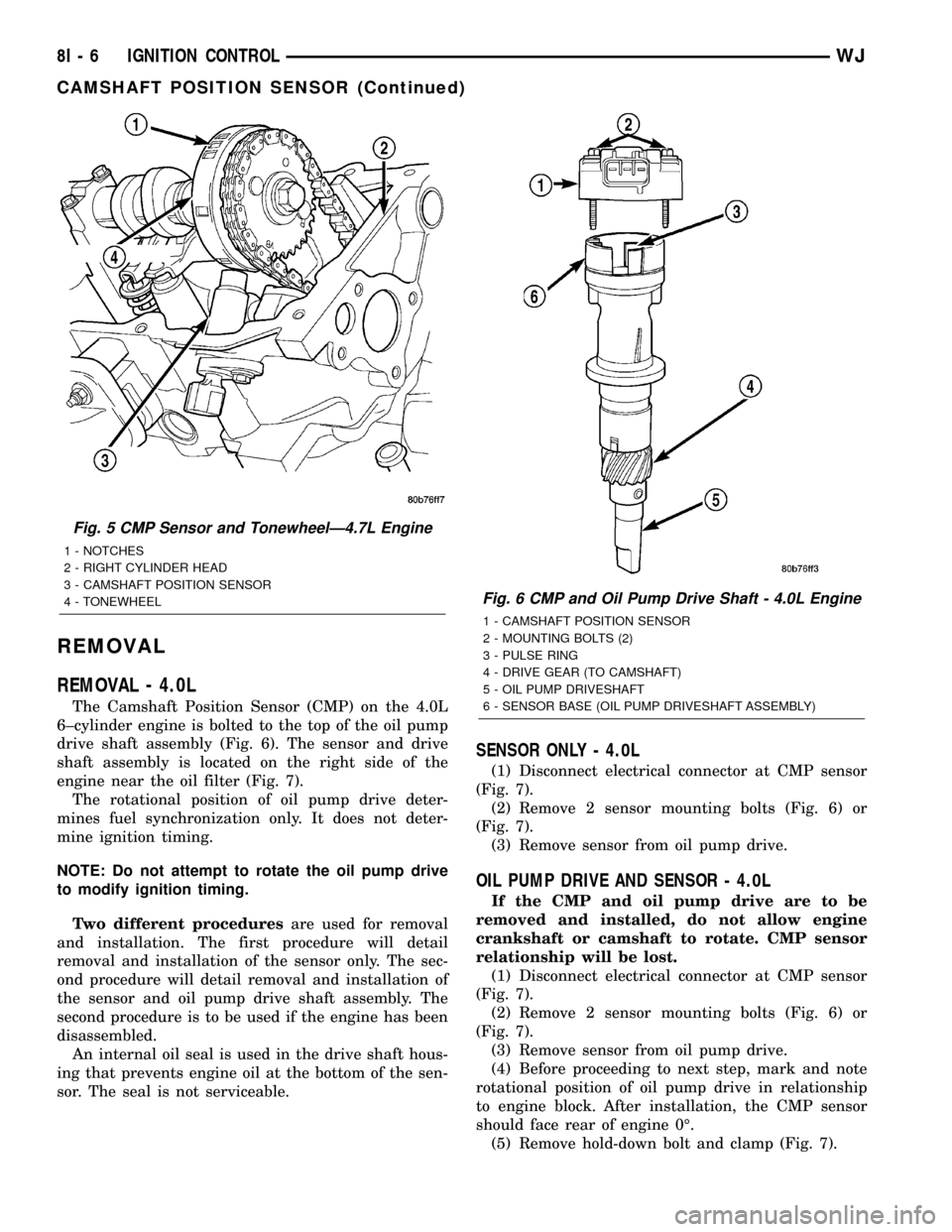
REMOVAL
REMOVAL - 4.0L
The Camshaft Position Sensor (CMP) on the 4.0L
6±cylinder engine is bolted to the top of the oil pump
drive shaft assembly (Fig. 6). The sensor and drive
shaft assembly is located on the right side of the
engine near the oil filter (Fig. 7).
The rotational position of oil pump drive deter-
mines fuel synchronization only. It does not deter-
mine ignition timing.
NOTE: Do not attempt to rotate the oil pump drive
to modify ignition timing.
Two different proceduresare used for removal
and installation. The first procedure will detail
removal and installation of the sensor only. The sec-
ond procedure will detail removal and installation of
the sensor and oil pump drive shaft assembly. The
second procedure is to be used if the engine has been
disassembled.
An internal oil seal is used in the drive shaft hous-
ing that prevents engine oil at the bottom of the sen-
sor. The seal is not serviceable.
SENSOR ONLY - 4.0L
(1) Disconnect electrical connector at CMP sensor
(Fig. 7).
(2) Remove 2 sensor mounting bolts (Fig. 6) or
(Fig. 7).
(3) Remove sensor from oil pump drive.
OIL PUMP DRIVE AND SENSOR - 4.0L
If the CMP and oil pump drive are to be
removed and installed, do not allow engine
crankshaft or camshaft to rotate. CMP sensor
relationship will be lost.
(1) Disconnect electrical connector at CMP sensor
(Fig. 7).
(2) Remove 2 sensor mounting bolts (Fig. 6) or
(Fig. 7).
(3) Remove sensor from oil pump drive.
(4) Before proceeding to next step, mark and note
rotational position of oil pump drive in relationship
to engine block. After installation, the CMP sensor
should face rear of engine 0É.
(5) Remove hold-down bolt and clamp (Fig. 7).
Fig. 5 CMP Sensor and TonewheelÐ4.7L Engine
1 - NOTCHES
2 - RIGHT CYLINDER HEAD
3 - CAMSHAFT POSITION SENSOR
4 - TONEWHEEL
Fig. 6 CMP and Oil Pump Drive Shaft - 4.0L Engine
1 - CAMSHAFT POSITION SENSOR
2 - MOUNTING BOLTS (2)
3 - PULSE RING
4 - DRIVE GEAR (TO CAMSHAFT)
5 - OIL PUMP DRIVESHAFT
6 - SENSOR BASE (OIL PUMP DRIVESHAFT ASSEMBLY)
8I - 6 IGNITION CONTROLWJ
CAMSHAFT POSITION SENSOR (Continued)
Page 404 of 2199
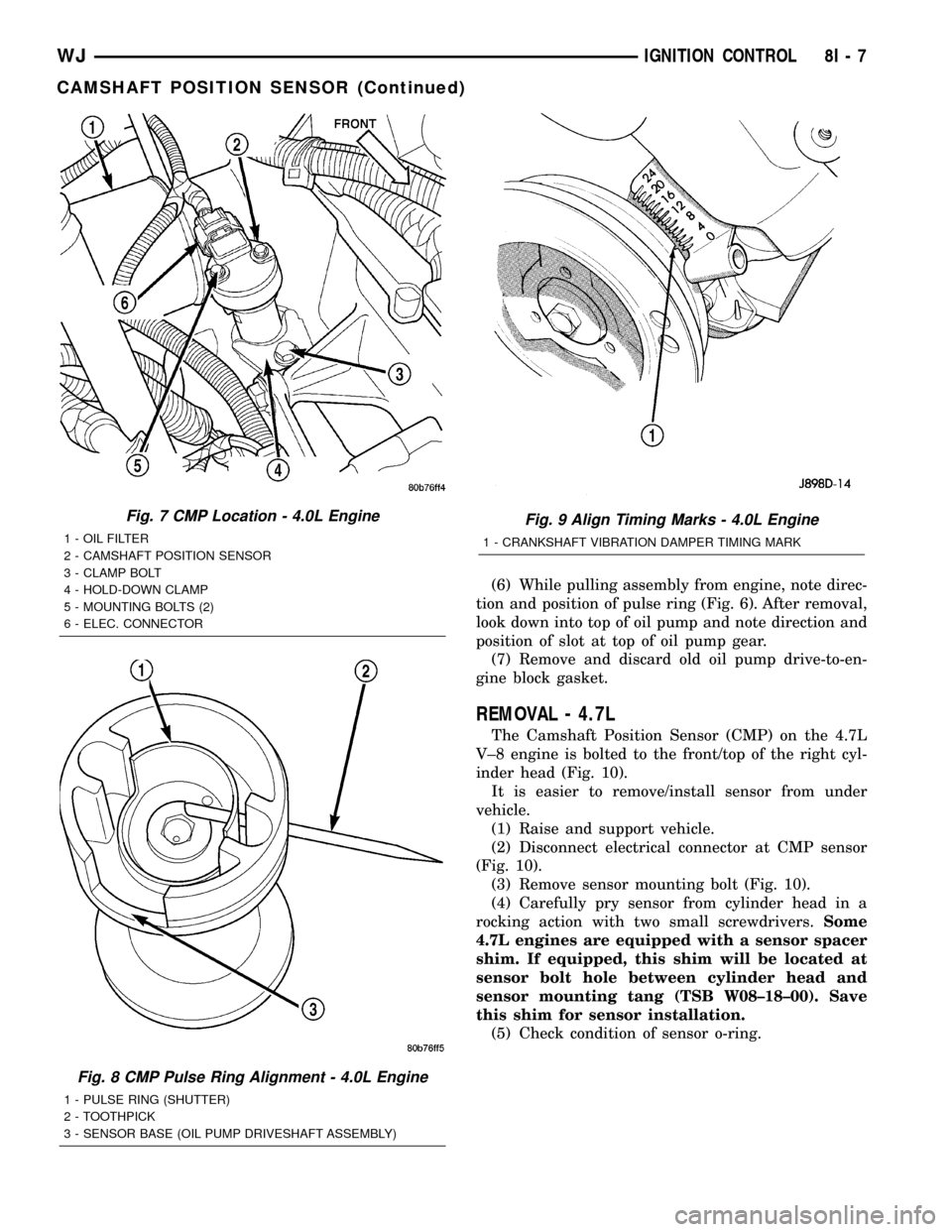
(6) While pulling assembly from engine, note direc-
tion and position of pulse ring (Fig. 6). After removal,
look down into top of oil pump and note direction and
position of slot at top of oil pump gear.
(7) Remove and discard old oil pump drive-to-en-
gine block gasket.
REMOVAL - 4.7L
The Camshaft Position Sensor (CMP) on the 4.7L
V±8 engine is bolted to the front/top of the right cyl-
inder head (Fig. 10).
It is easier to remove/install sensor from under
vehicle.
(1) Raise and support vehicle.
(2) Disconnect electrical connector at CMP sensor
(Fig. 10).
(3) Remove sensor mounting bolt (Fig. 10).
(4) Carefully pry sensor from cylinder head in a
rocking action with two small screwdrivers.Some
4.7L engines are equipped with a sensor spacer
shim. If equipped, this shim will be located at
sensor bolt hole between cylinder head and
sensor mounting tang (TSB W08±18±00). Save
this shim for sensor installation.
(5) Check condition of sensor o-ring.
Fig. 7 CMP Location - 4.0L Engine
1 - OIL FILTER
2 - CAMSHAFT POSITION SENSOR
3 - CLAMP BOLT
4 - HOLD-DOWN CLAMP
5 - MOUNTING BOLTS (2)
6 - ELEC. CONNECTOR
Fig. 8 CMP Pulse Ring Alignment - 4.0L Engine
1 - PULSE RING (SHUTTER)
2 - TOOTHPICK
3 - SENSOR BASE (OIL PUMP DRIVESHAFT ASSEMBLY)
Fig. 9 Align Timing Marks - 4.0L Engine
1 - CRANKSHAFT VIBRATION DAMPER TIMING MARK
WJIGNITION CONTROL 8I - 7
CAMSHAFT POSITION SENSOR (Continued)
Page 405 of 2199
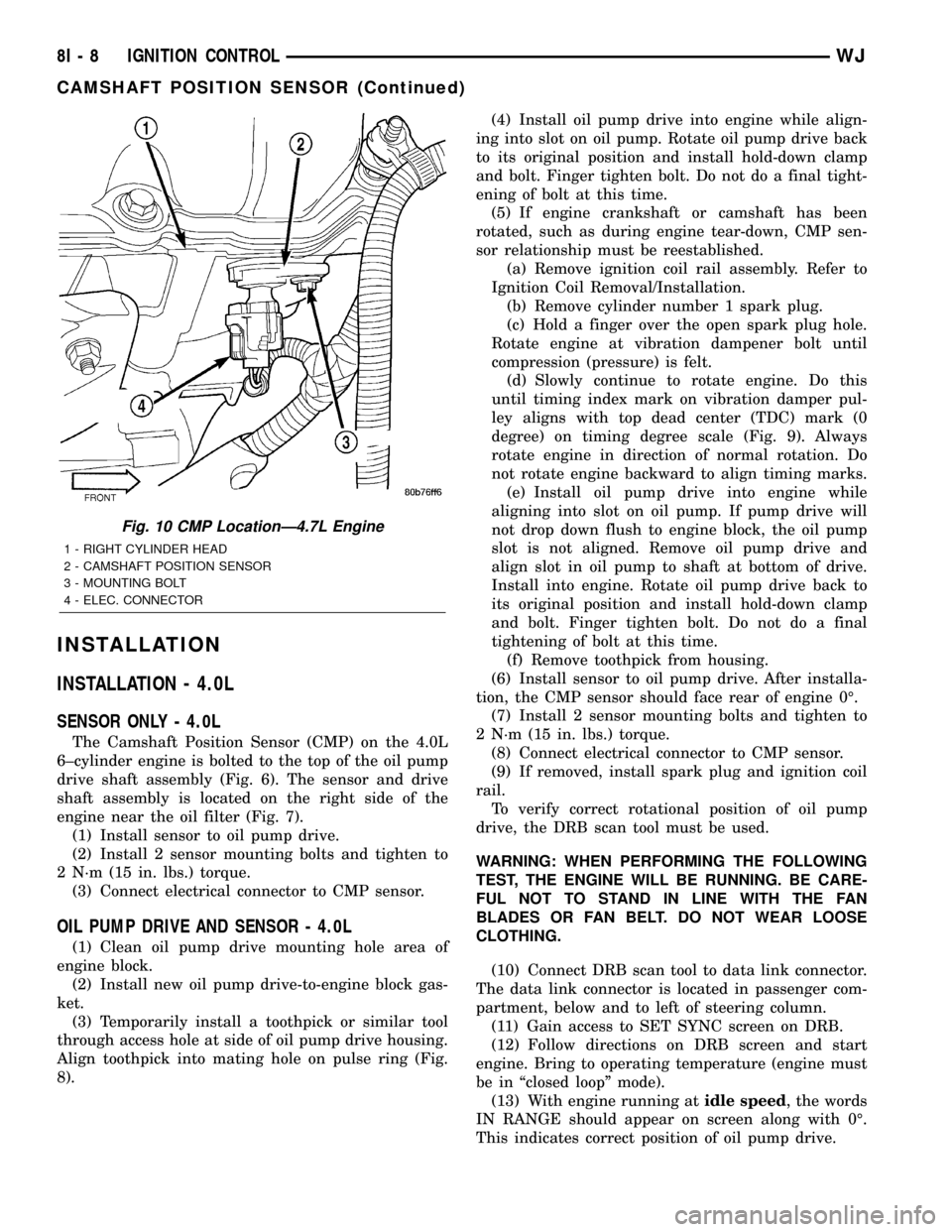
INSTALLATION
INSTALLATION - 4.0L
SENSOR ONLY - 4.0L
The Camshaft Position Sensor (CMP) on the 4.0L
6±cylinder engine is bolted to the top of the oil pump
drive shaft assembly (Fig. 6). The sensor and drive
shaft assembly is located on the right side of the
engine near the oil filter (Fig. 7).
(1) Install sensor to oil pump drive.
(2) Install 2 sensor mounting bolts and tighten to
2 N´m (15 in. lbs.) torque.
(3) Connect electrical connector to CMP sensor.
OIL PUMP DRIVE AND SENSOR - 4.0L
(1) Clean oil pump drive mounting hole area of
engine block.
(2) Install new oil pump drive-to-engine block gas-
ket.
(3) Temporarily install a toothpick or similar tool
through access hole at side of oil pump drive housing.
Align toothpick into mating hole on pulse ring (Fig.
8).(4) Install oil pump drive into engine while align-
ing into slot on oil pump. Rotate oil pump drive back
to its original position and install hold-down clamp
and bolt. Finger tighten bolt. Do not do a final tight-
ening of bolt at this time.
(5) If engine crankshaft or camshaft has been
rotated, such as during engine tear-down, CMP sen-
sor relationship must be reestablished.
(a) Remove ignition coil rail assembly. Refer to
Ignition Coil Removal/Installation.
(b) Remove cylinder number 1 spark plug.
(c) Hold a finger over the open spark plug hole.
Rotate engine at vibration dampener bolt until
compression (pressure) is felt.
(d) Slowly continue to rotate engine. Do this
until timing index mark on vibration damper pul-
ley aligns with top dead center (TDC) mark (0
degree) on timing degree scale (Fig. 9). Always
rotate engine in direction of normal rotation. Do
not rotate engine backward to align timing marks.
(e) Install oil pump drive into engine while
aligning into slot on oil pump. If pump drive will
not drop down flush to engine block, the oil pump
slot is not aligned. Remove oil pump drive and
align slot in oil pump to shaft at bottom of drive.
Install into engine. Rotate oil pump drive back to
its original position and install hold-down clamp
and bolt. Finger tighten bolt. Do not do a final
tightening of bolt at this time.
(f) Remove toothpick from housing.
(6) Install sensor to oil pump drive. After installa-
tion, the CMP sensor should face rear of engine 0É.
(7) Install 2 sensor mounting bolts and tighten to
2 N´m (15 in. lbs.) torque.
(8) Connect electrical connector to CMP sensor.
(9) If removed, install spark plug and ignition coil
rail.
To verify correct rotational position of oil pump
drive, the DRB scan tool must be used.
WARNING: WHEN PERFORMING THE FOLLOWING
TEST, THE ENGINE WILL BE RUNNING. BE CARE-
FUL NOT TO STAND IN LINE WITH THE FAN
BLADES OR FAN BELT. DO NOT WEAR LOOSE
CLOTHING.
(10) Connect DRB scan tool to data link connector.
The data link connector is located in passenger com-
partment, below and to left of steering column.
(11) Gain access to SET SYNC screen on DRB.
(12) Follow directions on DRB screen and start
engine. Bring to operating temperature (engine must
be in ªclosed loopº mode).
(13) With engine running atidle speed, the words
IN RANGE should appear on screen along with 0É.
This indicates correct position of oil pump drive.
Fig. 10 CMP LocationÐ4.7L Engine
1 - RIGHT CYLINDER HEAD
2 - CAMSHAFT POSITION SENSOR
3 - MOUNTING BOLT
4 - ELEC. CONNECTOR
8I - 8 IGNITION CONTROLWJ
CAMSHAFT POSITION SENSOR (Continued)
Page 406 of 2199
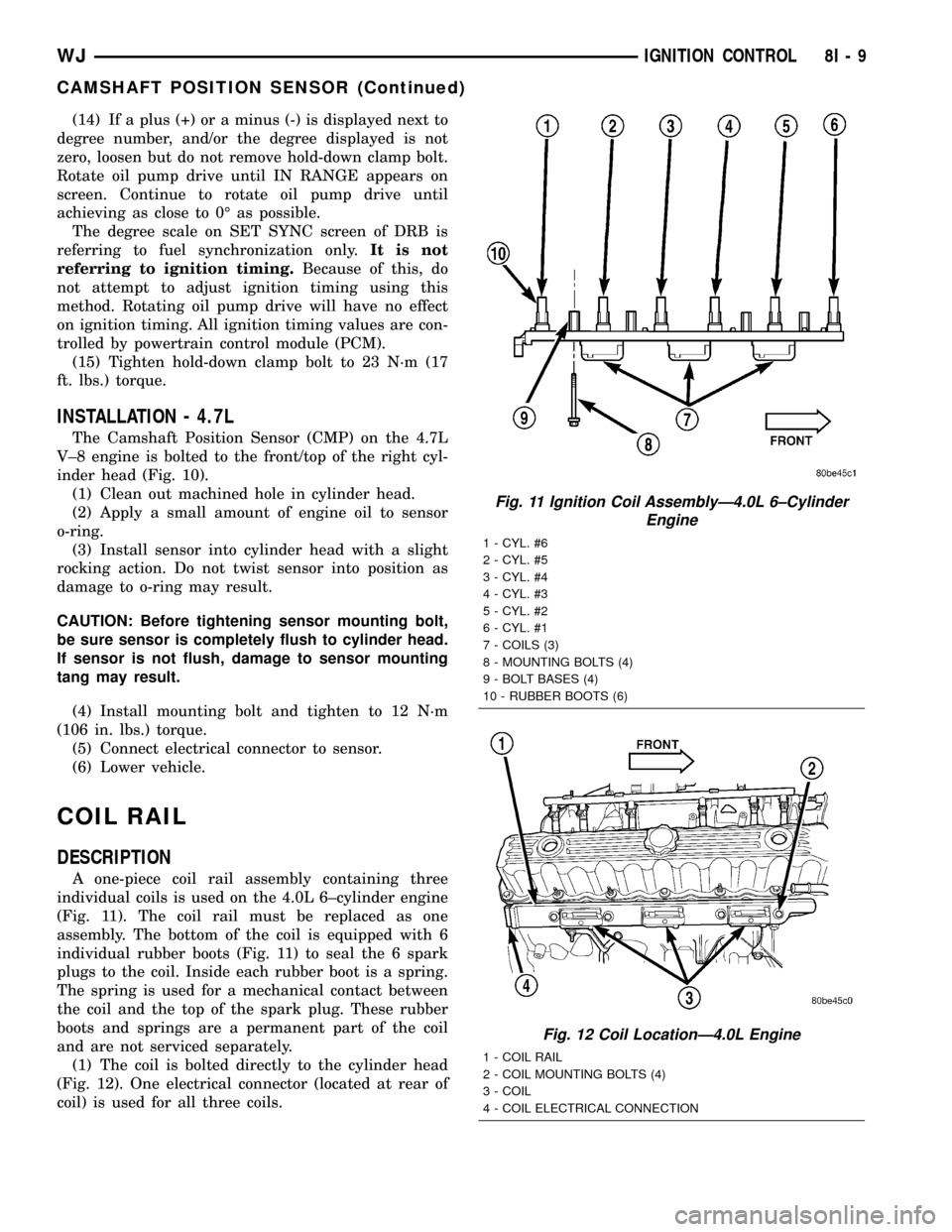
(14) If a plus (+) or a minus (-) is displayed next to
degree number, and/or the degree displayed is not
zero, loosen but do not remove hold-down clamp bolt.
Rotate oil pump drive until IN RANGE appears on
screen. Continue to rotate oil pump drive until
achieving as close to 0É as possible.
The degree scale on SET SYNC screen of DRB is
referring to fuel synchronization only.It is not
referring to ignition timing.Because of this, do
not attempt to adjust ignition timing using this
method. Rotating oil pump drive will have no effect
on ignition timing. All ignition timing values are con-
trolled by powertrain control module (PCM).
(15) Tighten hold-down clamp bolt to 23 N´m (17
ft. lbs.) torque.
INSTALLATION - 4.7L
The Camshaft Position Sensor (CMP) on the 4.7L
V±8 engine is bolted to the front/top of the right cyl-
inder head (Fig. 10).
(1) Clean out machined hole in cylinder head.
(2) Apply a small amount of engine oil to sensor
o-ring.
(3) Install sensor into cylinder head with a slight
rocking action. Do not twist sensor into position as
damage to o-ring may result.
CAUTION: Before tightening sensor mounting bolt,
be sure sensor is completely flush to cylinder head.
If sensor is not flush, damage to sensor mounting
tang may result.
(4) Install mounting bolt and tighten to 12 N´m
(106 in. lbs.) torque.
(5) Connect electrical connector to sensor.
(6) Lower vehicle.
COIL RAIL
DESCRIPTION
A one-piece coil rail assembly containing three
individual coils is used on the 4.0L 6±cylinder engine
(Fig. 11). The coil rail must be replaced as one
assembly. The bottom of the coil is equipped with 6
individual rubber boots (Fig. 11) to seal the 6 spark
plugs to the coil. Inside each rubber boot is a spring.
The spring is used for a mechanical contact between
the coil and the top of the spark plug. These rubber
boots and springs are a permanent part of the coil
and are not serviced separately.
(1) The coil is bolted directly to the cylinder head
(Fig. 12). One electrical connector (located at rear of
coil) is used for all three coils.
Fig. 11 Ignition Coil AssemblyÐ4.0L 6±Cylinder
Engine
1 - CYL. #6
2 - CYL. #5
3 - CYL. #4
4 - CYL. #3
5 - CYL. #2
6 - CYL. #1
7 - COILS (3)
8 - MOUNTING BOLTS (4)
9 - BOLT BASES (4)
10 - RUBBER BOOTS (6)
Fig. 12 Coil LocationÐ4.0L Engine
1 - COIL RAIL
2 - COIL MOUNTING BOLTS (4)
3 - COIL
4 - COIL ELECTRICAL CONNECTION
WJIGNITION CONTROL 8I - 9
CAMSHAFT POSITION SENSOR (Continued)
Page 410 of 2199
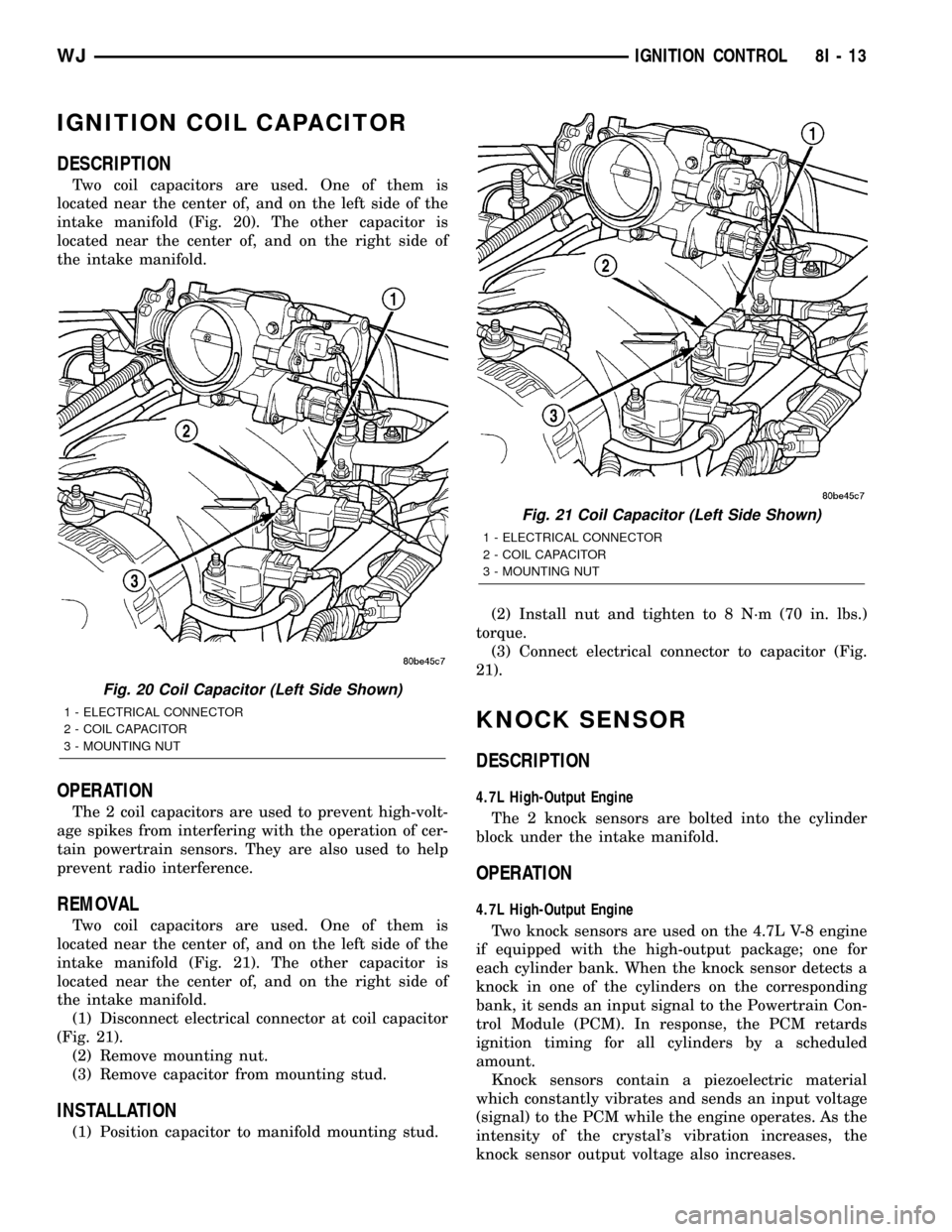
IGNITION COIL CAPACITOR
DESCRIPTION
Two coil capacitors are used. One of them is
located near the center of, and on the left side of the
intake manifold (Fig. 20). The other capacitor is
located near the center of, and on the right side of
the intake manifold.
OPERATION
The 2 coil capacitors are used to prevent high-volt-
age spikes from interfering with the operation of cer-
tain powertrain sensors. They are also used to help
prevent radio interference.
REMOVAL
Two coil capacitors are used. One of them is
located near the center of, and on the left side of the
intake manifold (Fig. 21). The other capacitor is
located near the center of, and on the right side of
the intake manifold.
(1) Disconnect electrical connector at coil capacitor
(Fig. 21).
(2) Remove mounting nut.
(3) Remove capacitor from mounting stud.
INSTALLATION
(1) Position capacitor to manifold mounting stud.(2) Install nut and tighten to 8 N´m (70 in. lbs.)
torque.
(3) Connect electrical connector to capacitor (Fig.
21).
KNOCK SENSOR
DESCRIPTION
4.7L High-Output Engine
The 2 knock sensors are bolted into the cylinder
block under the intake manifold.
OPERATION
4.7L High-Output Engine
Two knock sensors are used on the 4.7L V-8 engine
if equipped with the high-output package; one for
each cylinder bank. When the knock sensor detects a
knock in one of the cylinders on the corresponding
bank, it sends an input signal to the Powertrain Con-
trol Module (PCM). In response, the PCM retards
ignition timing for all cylinders by a scheduled
amount.
Knock sensors contain a piezoelectric material
which constantly vibrates and sends an input voltage
(signal) to the PCM while the engine operates. As the
intensity of the crystal's vibration increases, the
knock sensor output voltage also increases.
Fig. 20 Coil Capacitor (Left Side Shown)
1 - ELECTRICAL CONNECTOR
2 - COIL CAPACITOR
3 - MOUNTING NUT
Fig. 21 Coil Capacitor (Left Side Shown)
1 - ELECTRICAL CONNECTOR
2 - COIL CAPACITOR
3 - MOUNTING NUT
WJIGNITION CONTROL 8I - 13
Page 412 of 2199
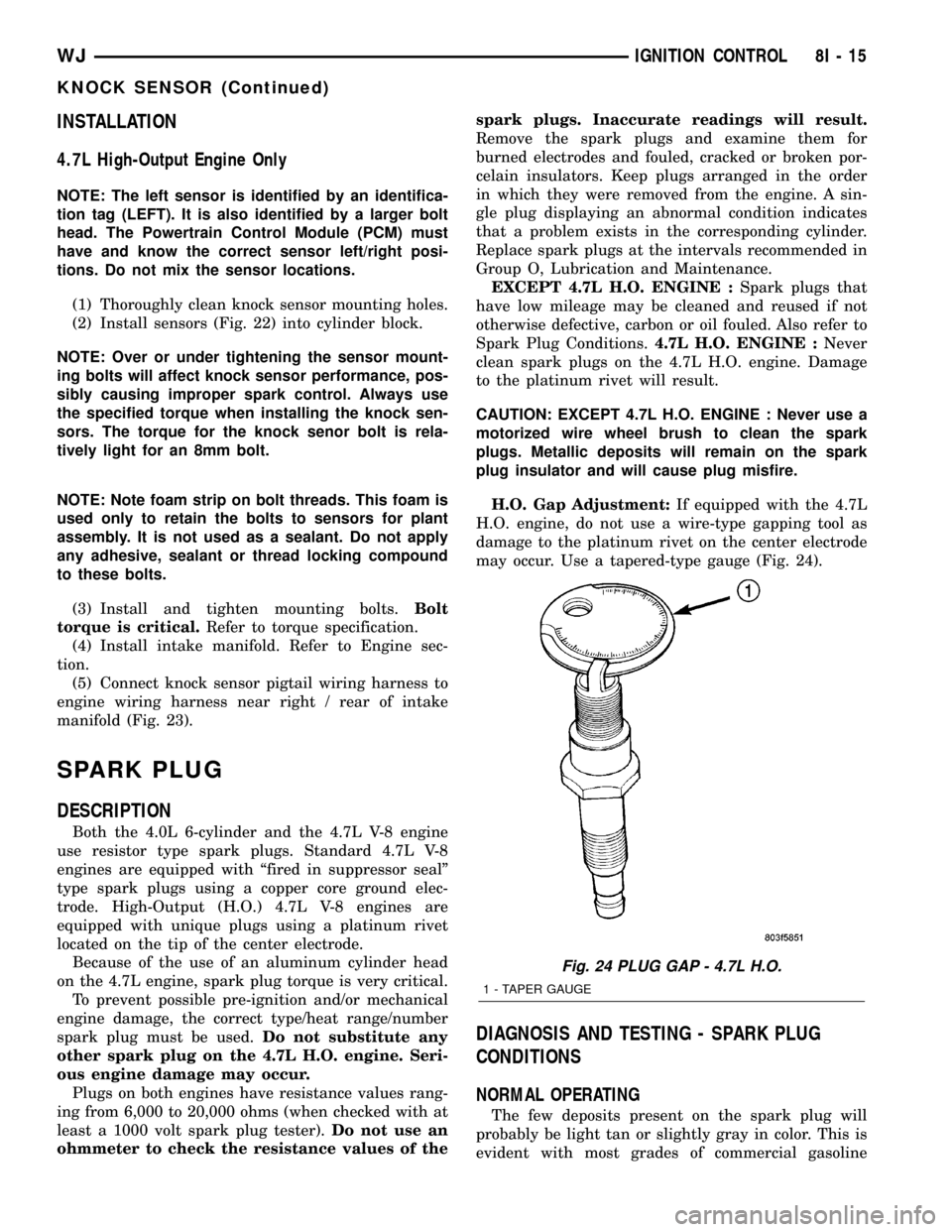
INSTALLATION
4.7L High-Output Engine Only
NOTE: The left sensor is identified by an identifica-
tion tag (LEFT). It is also identified by a larger bolt
head. The Powertrain Control Module (PCM) must
have and know the correct sensor left/right posi-
tions. Do not mix the sensor locations.
(1) Thoroughly clean knock sensor mounting holes.
(2) Install sensors (Fig. 22) into cylinder block.
NOTE: Over or under tightening the sensor mount-
ing bolts will affect knock sensor performance, pos-
sibly causing improper spark control. Always use
the specified torque when installing the knock sen-
sors. The torque for the knock senor bolt is rela-
tively light for an 8mm bolt.
NOTE: Note foam strip on bolt threads. This foam is
used only to retain the bolts to sensors for plant
assembly. It is not used as a sealant. Do not apply
any adhesive, sealant or thread locking compound
to these bolts.
(3) Install and tighten mounting bolts.Bolt
torque is critical.Refer to torque specification.
(4) Install intake manifold. Refer to Engine sec-
tion.
(5) Connect knock sensor pigtail wiring harness to
engine wiring harness near right / rear of intake
manifold (Fig. 23).
SPARK PLUG
DESCRIPTION
Both the 4.0L 6-cylinder and the 4.7L V-8 engine
use resistor type spark plugs. Standard 4.7L V-8
engines are equipped with ªfired in suppressor sealº
type spark plugs using a copper core ground elec-
trode. High-Output (H.O.) 4.7L V-8 engines are
equipped with unique plugs using a platinum rivet
located on the tip of the center electrode.
Because of the use of an aluminum cylinder head
on the 4.7L engine, spark plug torque is very critical.
To prevent possible pre-ignition and/or mechanical
engine damage, the correct type/heat range/number
spark plug must be used.Do not substitute any
other spark plug on the 4.7L H.O. engine. Seri-
ous engine damage may occur.
Plugs on both engines have resistance values rang-
ing from 6,000 to 20,000 ohms (when checked with at
least a 1000 volt spark plug tester).Do not use an
ohmmeter to check the resistance values of thespark plugs. Inaccurate readings will result.
Remove the spark plugs and examine them for
burned electrodes and fouled, cracked or broken por-
celain insulators. Keep plugs arranged in the order
in which they were removed from the engine. A sin-
gle plug displaying an abnormal condition indicates
that a problem exists in the corresponding cylinder.
Replace spark plugs at the intervals recommended in
Group O, Lubrication and Maintenance.
EXCEPT 4.7L H.O. ENGINE :Spark plugs that
have low mileage may be cleaned and reused if not
otherwise defective, carbon or oil fouled. Also refer to
Spark Plug Conditions.4.7L H.O. ENGINE :Never
clean spark plugs on the 4.7L H.O. engine. Damage
to the platinum rivet will result.
CAUTION: EXCEPT 4.7L H.O. ENGINE : Never use a
motorized wire wheel brush to clean the spark
plugs. Metallic deposits will remain on the spark
plug insulator and will cause plug misfire.
H.O. Gap Adjustment:If equipped with the 4.7L
H.O. engine, do not use a wire-type gapping tool as
damage to the platinum rivet on the center electrode
may occur. Use a tapered-type gauge (Fig. 24).
DIAGNOSIS AND TESTING - SPARK PLUG
CONDITIONS
NORMAL OPERATING
The few deposits present on the spark plug will
probably be light tan or slightly gray in color. This is
evident with most grades of commercial gasoline
Fig. 24 PLUG GAP - 4.7L H.O.
1 - TAPER GAUGE
WJIGNITION CONTROL 8I - 15
KNOCK SENSOR (Continued)
Page 440 of 2199
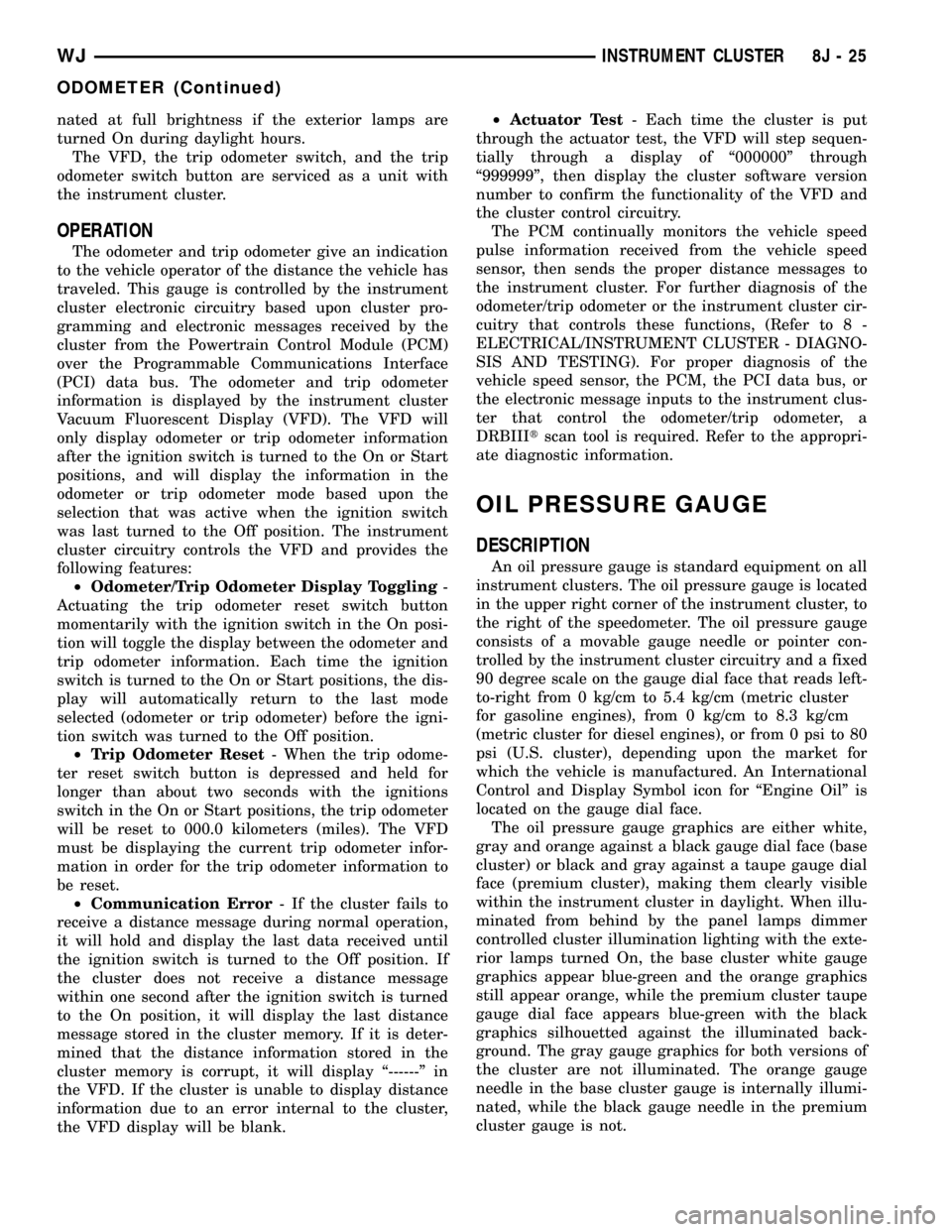
nated at full brightness if the exterior lamps are
turned On during daylight hours.
The VFD, the trip odometer switch, and the trip
odometer switch button are serviced as a unit with
the instrument cluster.
OPERATION
The odometer and trip odometer give an indication
to the vehicle operator of the distance the vehicle has
traveled. This gauge is controlled by the instrument
cluster electronic circuitry based upon cluster pro-
gramming and electronic messages received by the
cluster from the Powertrain Control Module (PCM)
over the Programmable Communications Interface
(PCI) data bus. The odometer and trip odometer
information is displayed by the instrument cluster
Vacuum Fluorescent Display (VFD). The VFD will
only display odometer or trip odometer information
after the ignition switch is turned to the On or Start
positions, and will display the information in the
odometer or trip odometer mode based upon the
selection that was active when the ignition switch
was last turned to the Off position. The instrument
cluster circuitry controls the VFD and provides the
following features:
²Odometer/Trip Odometer Display Toggling-
Actuating the trip odometer reset switch button
momentarily with the ignition switch in the On posi-
tion will toggle the display between the odometer and
trip odometer information. Each time the ignition
switch is turned to the On or Start positions, the dis-
play will automatically return to the last mode
selected (odometer or trip odometer) before the igni-
tion switch was turned to the Off position.
²Trip Odometer Reset- When the trip odome-
ter reset switch button is depressed and held for
longer than about two seconds with the ignitions
switch in the On or Start positions, the trip odometer
will be reset to 000.0 kilometers (miles). The VFD
must be displaying the current trip odometer infor-
mation in order for the trip odometer information to
be reset.
²Communication Error- If the cluster fails to
receive a distance message during normal operation,
it will hold and display the last data received until
the ignition switch is turned to the Off position. If
the cluster does not receive a distance message
within one second after the ignition switch is turned
to the On position, it will display the last distance
message stored in the cluster memory. If it is deter-
mined that the distance information stored in the
cluster memory is corrupt, it will display ª------º in
the VFD. If the cluster is unable to display distance
information due to an error internal to the cluster,
the VFD display will be blank.²Actuator Test- Each time the cluster is put
through the actuator test, the VFD will step sequen-
tially through a display of ª000000º through
ª999999º, then display the cluster software version
number to confirm the functionality of the VFD and
the cluster control circuitry.
The PCM continually monitors the vehicle speed
pulse information received from the vehicle speed
sensor, then sends the proper distance messages to
the instrument cluster. For further diagnosis of the
odometer/trip odometer or the instrument cluster cir-
cuitry that controls these functions, (Refer to 8 -
ELECTRICAL/INSTRUMENT CLUSTER - DIAGNO-
SIS AND TESTING). For proper diagnosis of the
vehicle speed sensor, the PCM, the PCI data bus, or
the electronic message inputs to the instrument clus-
ter that control the odometer/trip odometer, a
DRBIIItscan tool is required. Refer to the appropri-
ate diagnostic information.
OIL PRESSURE GAUGE
DESCRIPTION
An oil pressure gauge is standard equipment on all
instrument clusters. The oil pressure gauge is located
in the upper right corner of the instrument cluster, to
the right of the speedometer. The oil pressure gauge
consists of a movable gauge needle or pointer con-
trolled by the instrument cluster circuitry and a fixed
90 degree scale on the gauge dial face that reads left-
to-right from 0 kg/cm to 5.4 kg/cm (metric cluster
for gasoline engines), from 0 kg/cm to 8.3 kg/cm
(metric cluster for diesel engines), or from 0 psi to 80
psi (U.S. cluster), depending upon the market for
which the vehicle is manufactured. An International
Control and Display Symbol icon for ªEngine Oilº is
located on the gauge dial face.
The oil pressure gauge graphics are either white,
gray and orange against a black gauge dial face (base
cluster) or black and gray against a taupe gauge dial
face (premium cluster), making them clearly visible
within the instrument cluster in daylight. When illu-
minated from behind by the panel lamps dimmer
controlled cluster illumination lighting with the exte-
rior lamps turned On, the base cluster white gauge
graphics appear blue-green and the orange graphics
still appear orange, while the premium cluster taupe
gauge dial face appears blue-green with the black
graphics silhouetted against the illuminated back-
ground. The gray gauge graphics for both versions of
the cluster are not illuminated. The orange gauge
needle in the base cluster gauge is internally illumi-
nated, while the black gauge needle in the premium
cluster gauge is not.
WJINSTRUMENT CLUSTER 8J - 25
ODOMETER (Continued)
Page 441 of 2199
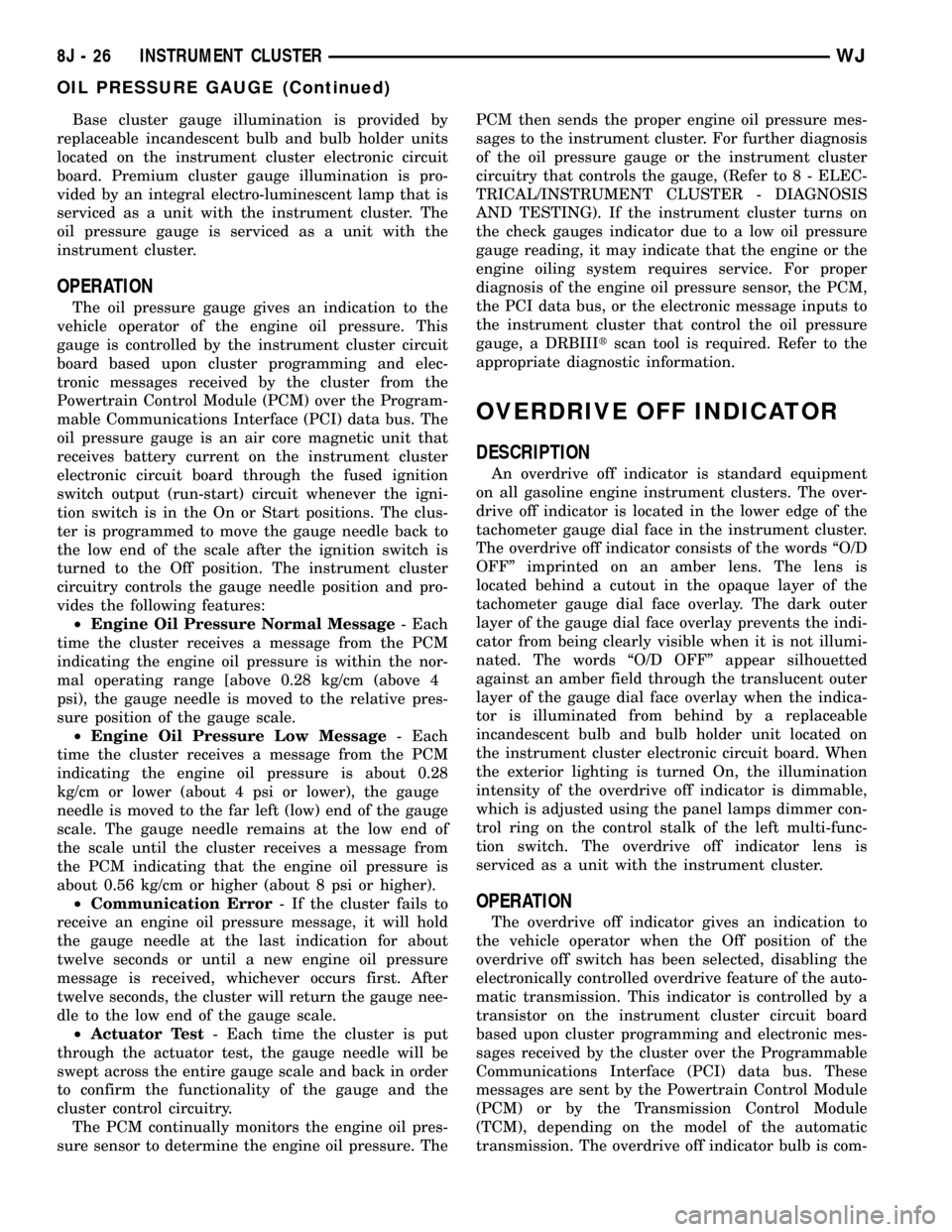
Base cluster gauge illumination is provided by
replaceable incandescent bulb and bulb holder units
located on the instrument cluster electronic circuit
board. Premium cluster gauge illumination is pro-
vided by an integral electro-luminescent lamp that is
serviced as a unit with the instrument cluster. The
oil pressure gauge is serviced as a unit with the
instrument cluster.
OPERATION
The oil pressure gauge gives an indication to the
vehicle operator of the engine oil pressure. This
gauge is controlled by the instrument cluster circuit
board based upon cluster programming and elec-
tronic messages received by the cluster from the
Powertrain Control Module (PCM) over the Program-
mable Communications Interface (PCI) data bus. The
oil pressure gauge is an air core magnetic unit that
receives battery current on the instrument cluster
electronic circuit board through the fused ignition
switch output (run-start) circuit whenever the igni-
tion switch is in the On or Start positions. The clus-
ter is programmed to move the gauge needle back to
the low end of the scale after the ignition switch is
turned to the Off position. The instrument cluster
circuitry controls the gauge needle position and pro-
vides the following features:
²Engine Oil Pressure Normal Message- Each
time the cluster receives a message from the PCM
indicating the engine oil pressure is within the nor-
mal operating range [above 0.28 kg/cm (above 4
psi), the gauge needle is moved to the relative pres-
sure position of the gauge scale.
²Engine Oil Pressure Low Message- Each
time the cluster receives a message from the PCM
indicating the engine oil pressure is about 0.28
kg/cm or lower (about 4 psi or lower), the gauge
needle is moved to the far left (low) end of the gauge
scale. The gauge needle remains at the low end of
the scale until the cluster receives a message from
the PCM indicating that the engine oil pressure is
about 0.56 kg/cm or higher (about 8 psi or higher).
²Communication Error- If the cluster fails to
receive an engine oil pressure message, it will hold
the gauge needle at the last indication for about
twelve seconds or until a new engine oil pressure
message is received, whichever occurs first. After
twelve seconds, the cluster will return the gauge nee-
dle to the low end of the gauge scale.
²Actuator Test- Each time the cluster is put
through the actuator test, the gauge needle will be
swept across the entire gauge scale and back in order
to confirm the functionality of the gauge and the
cluster control circuitry.
The PCM continually monitors the engine oil pres-
sure sensor to determine the engine oil pressure. ThePCM then sends the proper engine oil pressure mes-
sages to the instrument cluster. For further diagnosis
of the oil pressure gauge or the instrument cluster
circuitry that controls the gauge, (Refer to 8 - ELEC-
TRICAL/INSTRUMENT CLUSTER - DIAGNOSIS
AND TESTING). If the instrument cluster turns on
the check gauges indicator due to a low oil pressure
gauge reading, it may indicate that the engine or the
engine oiling system requires service. For proper
diagnosis of the engine oil pressure sensor, the PCM,
the PCI data bus, or the electronic message inputs to
the instrument cluster that control the oil pressure
gauge, a DRBIIItscan tool is required. Refer to the
appropriate diagnostic information.
OVERDRIVE OFF INDICATOR
DESCRIPTION
An overdrive off indicator is standard equipment
on all gasoline engine instrument clusters. The over-
drive off indicator is located in the lower edge of the
tachometer gauge dial face in the instrument cluster.
The overdrive off indicator consists of the words ªO/D
OFFº imprinted on an amber lens. The lens is
located behind a cutout in the opaque layer of the
tachometer gauge dial face overlay. The dark outer
layer of the gauge dial face overlay prevents the indi-
cator from being clearly visible when it is not illumi-
nated. The words ªO/D OFFº appear silhouetted
against an amber field through the translucent outer
layer of the gauge dial face overlay when the indica-
tor is illuminated from behind by a replaceable
incandescent bulb and bulb holder unit located on
the instrument cluster electronic circuit board. When
the exterior lighting is turned On, the illumination
intensity of the overdrive off indicator is dimmable,
which is adjusted using the panel lamps dimmer con-
trol ring on the control stalk of the left multi-func-
tion switch. The overdrive off indicator lens is
serviced as a unit with the instrument cluster.
OPERATION
The overdrive off indicator gives an indication to
the vehicle operator when the Off position of the
overdrive off switch has been selected, disabling the
electronically controlled overdrive feature of the auto-
matic transmission. This indicator is controlled by a
transistor on the instrument cluster circuit board
based upon cluster programming and electronic mes-
sages received by the cluster over the Programmable
Communications Interface (PCI) data bus. These
messages are sent by the Powertrain Control Module
(PCM) or by the Transmission Control Module
(TCM), depending on the model of the automatic
transmission. The overdrive off indicator bulb is com-
8J - 26 INSTRUMENT CLUSTERWJ
OIL PRESSURE GAUGE (Continued)
Page 448 of 2199
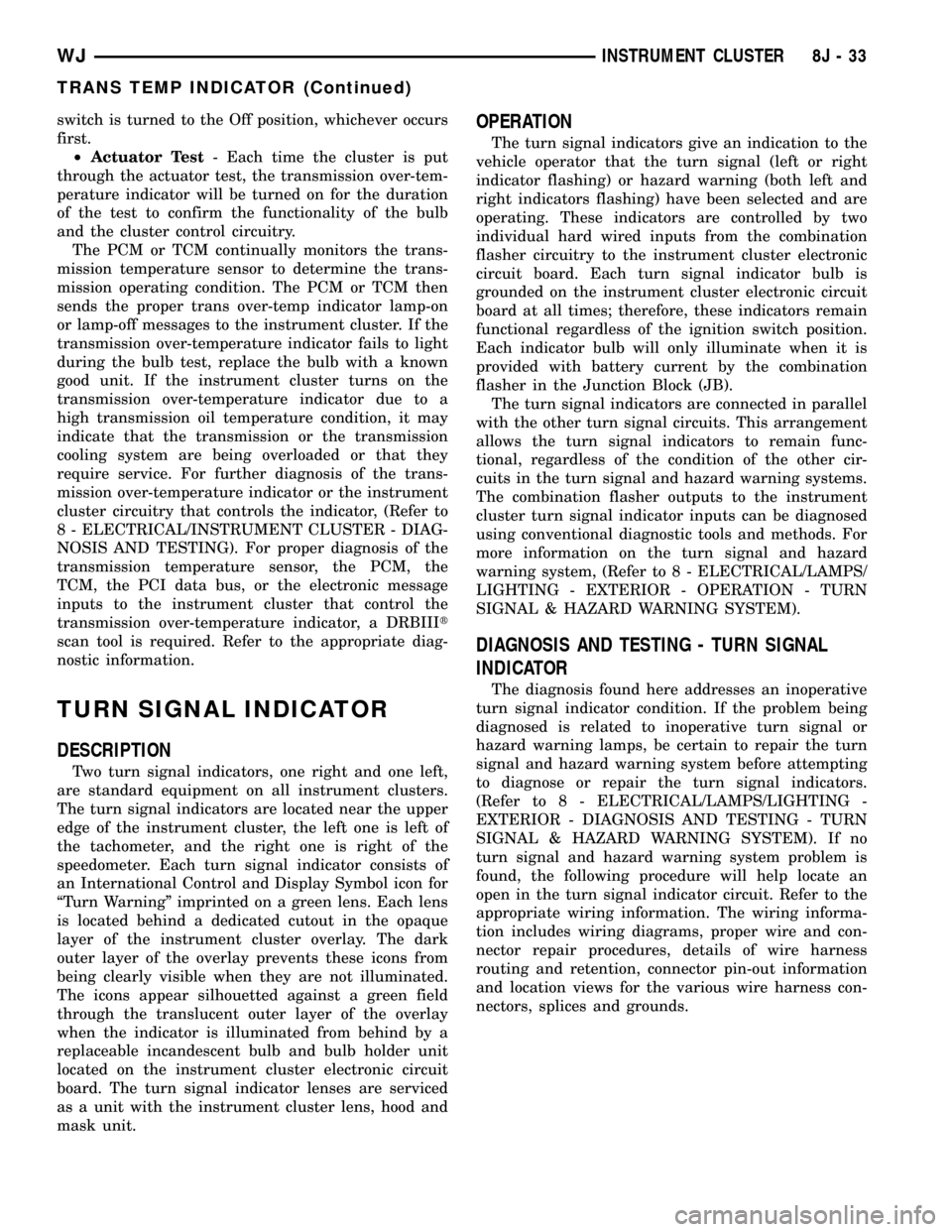
switch is turned to the Off position, whichever occurs
first.
²Actuator Test- Each time the cluster is put
through the actuator test, the transmission over-tem-
perature indicator will be turned on for the duration
of the test to confirm the functionality of the bulb
and the cluster control circuitry.
The PCM or TCM continually monitors the trans-
mission temperature sensor to determine the trans-
mission operating condition. The PCM or TCM then
sends the proper trans over-temp indicator lamp-on
or lamp-off messages to the instrument cluster. If the
transmission over-temperature indicator fails to light
during the bulb test, replace the bulb with a known
good unit. If the instrument cluster turns on the
transmission over-temperature indicator due to a
high transmission oil temperature condition, it may
indicate that the transmission or the transmission
cooling system are being overloaded or that they
require service. For further diagnosis of the trans-
mission over-temperature indicator or the instrument
cluster circuitry that controls the indicator, (Refer to
8 - ELECTRICAL/INSTRUMENT CLUSTER - DIAG-
NOSIS AND TESTING). For proper diagnosis of the
transmission temperature sensor, the PCM, the
TCM, the PCI data bus, or the electronic message
inputs to the instrument cluster that control the
transmission over-temperature indicator, a DRBIIIt
scan tool is required. Refer to the appropriate diag-
nostic information.
TURN SIGNAL INDICATOR
DESCRIPTION
Two turn signal indicators, one right and one left,
are standard equipment on all instrument clusters.
The turn signal indicators are located near the upper
edge of the instrument cluster, the left one is left of
the tachometer, and the right one is right of the
speedometer. Each turn signal indicator consists of
an International Control and Display Symbol icon for
ªTurn Warningº imprinted on a green lens. Each lens
is located behind a dedicated cutout in the opaque
layer of the instrument cluster overlay. The dark
outer layer of the overlay prevents these icons from
being clearly visible when they are not illuminated.
The icons appear silhouetted against a green field
through the translucent outer layer of the overlay
when the indicator is illuminated from behind by a
replaceable incandescent bulb and bulb holder unit
located on the instrument cluster electronic circuit
board. The turn signal indicator lenses are serviced
as a unit with the instrument cluster lens, hood and
mask unit.
OPERATION
The turn signal indicators give an indication to the
vehicle operator that the turn signal (left or right
indicator flashing) or hazard warning (both left and
right indicators flashing) have been selected and are
operating. These indicators are controlled by two
individual hard wired inputs from the combination
flasher circuitry to the instrument cluster electronic
circuit board. Each turn signal indicator bulb is
grounded on the instrument cluster electronic circuit
board at all times; therefore, these indicators remain
functional regardless of the ignition switch position.
Each indicator bulb will only illuminate when it is
provided with battery current by the combination
flasher in the Junction Block (JB).
The turn signal indicators are connected in parallel
with the other turn signal circuits. This arrangement
allows the turn signal indicators to remain func-
tional, regardless of the condition of the other cir-
cuits in the turn signal and hazard warning systems.
The combination flasher outputs to the instrument
cluster turn signal indicator inputs can be diagnosed
using conventional diagnostic tools and methods. For
more information on the turn signal and hazard
warning system, (Refer to 8 - ELECTRICAL/LAMPS/
LIGHTING - EXTERIOR - OPERATION - TURN
SIGNAL & HAZARD WARNING SYSTEM).
DIAGNOSIS AND TESTING - TURN SIGNAL
INDICATOR
The diagnosis found here addresses an inoperative
turn signal indicator condition. If the problem being
diagnosed is related to inoperative turn signal or
hazard warning lamps, be certain to repair the turn
signal and hazard warning system before attempting
to diagnose or repair the turn signal indicators.
(Refer to 8 - ELECTRICAL/LAMPS/LIGHTING -
EXTERIOR - DIAGNOSIS AND TESTING - TURN
SIGNAL & HAZARD WARNING SYSTEM). If no
turn signal and hazard warning system problem is
found, the following procedure will help locate an
open in the turn signal indicator circuit. Refer to the
appropriate wiring information. The wiring informa-
tion includes wiring diagrams, proper wire and con-
nector repair procedures, details of wire harness
routing and retention, connector pin-out information
and location views for the various wire harness con-
nectors, splices and grounds.
WJINSTRUMENT CLUSTER 8J - 33
TRANS TEMP INDICATOR (Continued)