fuse panel fuse 23 JEEP GRAND CHEROKEE 2002 WJ / 2.G Owner's Manual
[x] Cancel search | Manufacturer: JEEP, Model Year: 2002, Model line: GRAND CHEROKEE, Model: JEEP GRAND CHEROKEE 2002 WJ / 2.GPages: 2199, PDF Size: 76.01 MB
Page 420 of 2199
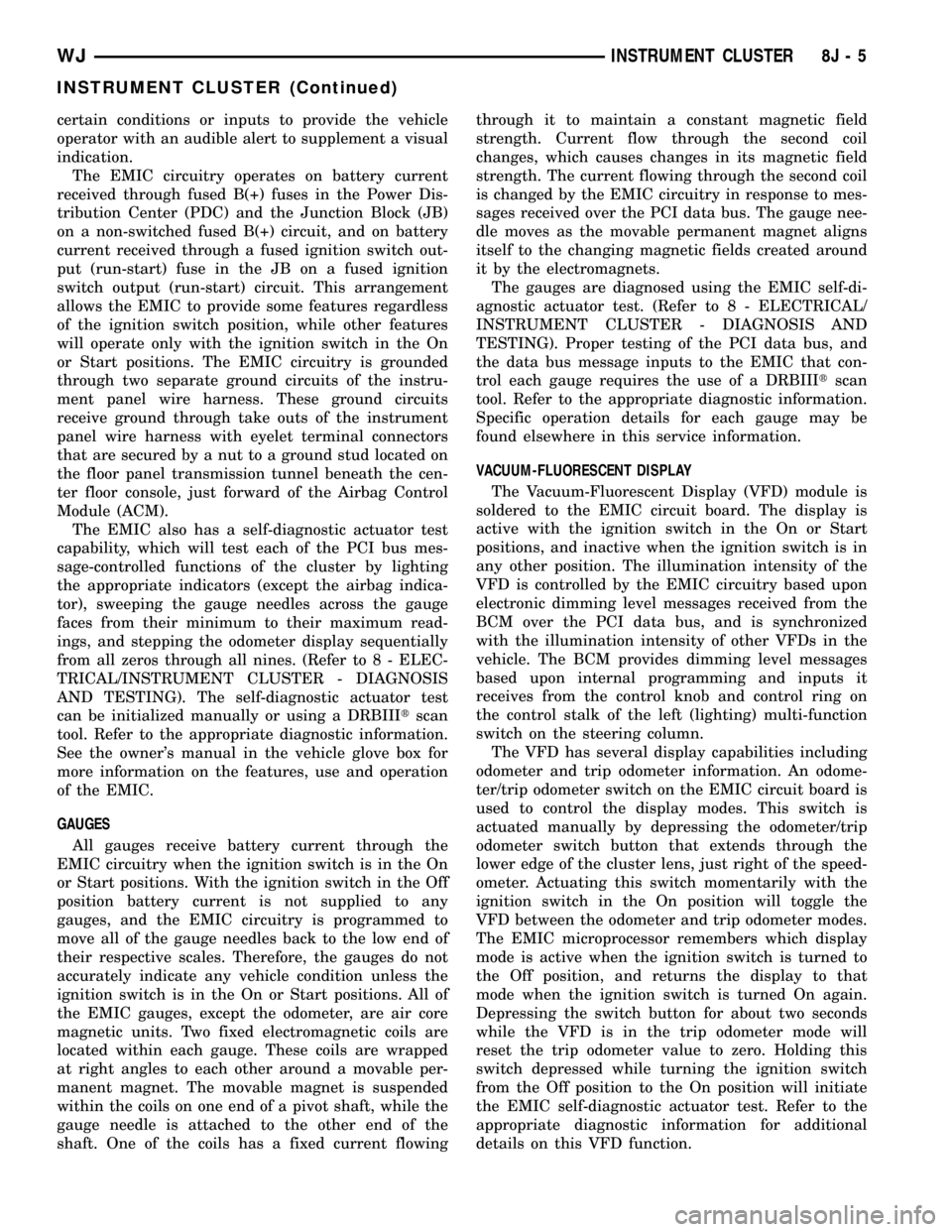
certain conditions or inputs to provide the vehicle
operator with an audible alert to supplement a visual
indication.
The EMIC circuitry operates on battery current
received through fused B(+) fuses in the Power Dis-
tribution Center (PDC) and the Junction Block (JB)
on a non-switched fused B(+) circuit, and on battery
current received through a fused ignition switch out-
put (run-start) fuse in the JB on a fused ignition
switch output (run-start) circuit. This arrangement
allows the EMIC to provide some features regardless
of the ignition switch position, while other features
will operate only with the ignition switch in the On
or Start positions. The EMIC circuitry is grounded
through two separate ground circuits of the instru-
ment panel wire harness. These ground circuits
receive ground through take outs of the instrument
panel wire harness with eyelet terminal connectors
that are secured by a nut to a ground stud located on
the floor panel transmission tunnel beneath the cen-
ter floor console, just forward of the Airbag Control
Module (ACM).
The EMIC also has a self-diagnostic actuator test
capability, which will test each of the PCI bus mes-
sage-controlled functions of the cluster by lighting
the appropriate indicators (except the airbag indica-
tor), sweeping the gauge needles across the gauge
faces from their minimum to their maximum read-
ings, and stepping the odometer display sequentially
from all zeros through all nines. (Refer to 8 - ELEC-
TRICAL/INSTRUMENT CLUSTER - DIAGNOSIS
AND TESTING). The self-diagnostic actuator test
can be initialized manually or using a DRBIIItscan
tool. Refer to the appropriate diagnostic information.
See the owner's manual in the vehicle glove box for
more information on the features, use and operation
of the EMIC.
GAUGES
All gauges receive battery current through the
EMIC circuitry when the ignition switch is in the On
or Start positions. With the ignition switch in the Off
position battery current is not supplied to any
gauges, and the EMIC circuitry is programmed to
move all of the gauge needles back to the low end of
their respective scales. Therefore, the gauges do not
accurately indicate any vehicle condition unless the
ignition switch is in the On or Start positions. All of
the EMIC gauges, except the odometer, are air core
magnetic units. Two fixed electromagnetic coils are
located within each gauge. These coils are wrapped
at right angles to each other around a movable per-
manent magnet. The movable magnet is suspended
within the coils on one end of a pivot shaft, while the
gauge needle is attached to the other end of the
shaft. One of the coils has a fixed current flowingthrough it to maintain a constant magnetic field
strength. Current flow through the second coil
changes, which causes changes in its magnetic field
strength. The current flowing through the second coil
is changed by the EMIC circuitry in response to mes-
sages received over the PCI data bus. The gauge nee-
dle moves as the movable permanent magnet aligns
itself to the changing magnetic fields created around
it by the electromagnets.
The gauges are diagnosed using the EMIC self-di-
agnostic actuator test. (Refer to 8 - ELECTRICAL/
INSTRUMENT CLUSTER - DIAGNOSIS AND
TESTING). Proper testing of the PCI data bus, and
the data bus message inputs to the EMIC that con-
trol each gauge requires the use of a DRBIIItscan
tool. Refer to the appropriate diagnostic information.
Specific operation details for each gauge may be
found elsewhere in this service information.
VACUUM-FLUORESCENT DISPLAY
The Vacuum-Fluorescent Display (VFD) module is
soldered to the EMIC circuit board. The display is
active with the ignition switch in the On or Start
positions, and inactive when the ignition switch is in
any other position. The illumination intensity of the
VFD is controlled by the EMIC circuitry based upon
electronic dimming level messages received from the
BCM over the PCI data bus, and is synchronized
with the illumination intensity of other VFDs in the
vehicle. The BCM provides dimming level messages
based upon internal programming and inputs it
receives from the control knob and control ring on
the control stalk of the left (lighting) multi-function
switch on the steering column.
The VFD has several display capabilities including
odometer and trip odometer information. An odome-
ter/trip odometer switch on the EMIC circuit board is
used to control the display modes. This switch is
actuated manually by depressing the odometer/trip
odometer switch button that extends through the
lower edge of the cluster lens, just right of the speed-
ometer. Actuating this switch momentarily with the
ignition switch in the On position will toggle the
VFD between the odometer and trip odometer modes.
The EMIC microprocessor remembers which display
mode is active when the ignition switch is turned to
the Off position, and returns the display to that
mode when the ignition switch is turned On again.
Depressing the switch button for about two seconds
while the VFD is in the trip odometer mode will
reset the trip odometer value to zero. Holding this
switch depressed while turning the ignition switch
from the Off position to the On position will initiate
the EMIC self-diagnostic actuator test. Refer to the
appropriate diagnostic information for additional
details on this VFD function.
WJINSTRUMENT CLUSTER 8J - 5
INSTRUMENT CLUSTER (Continued)
Page 421 of 2199
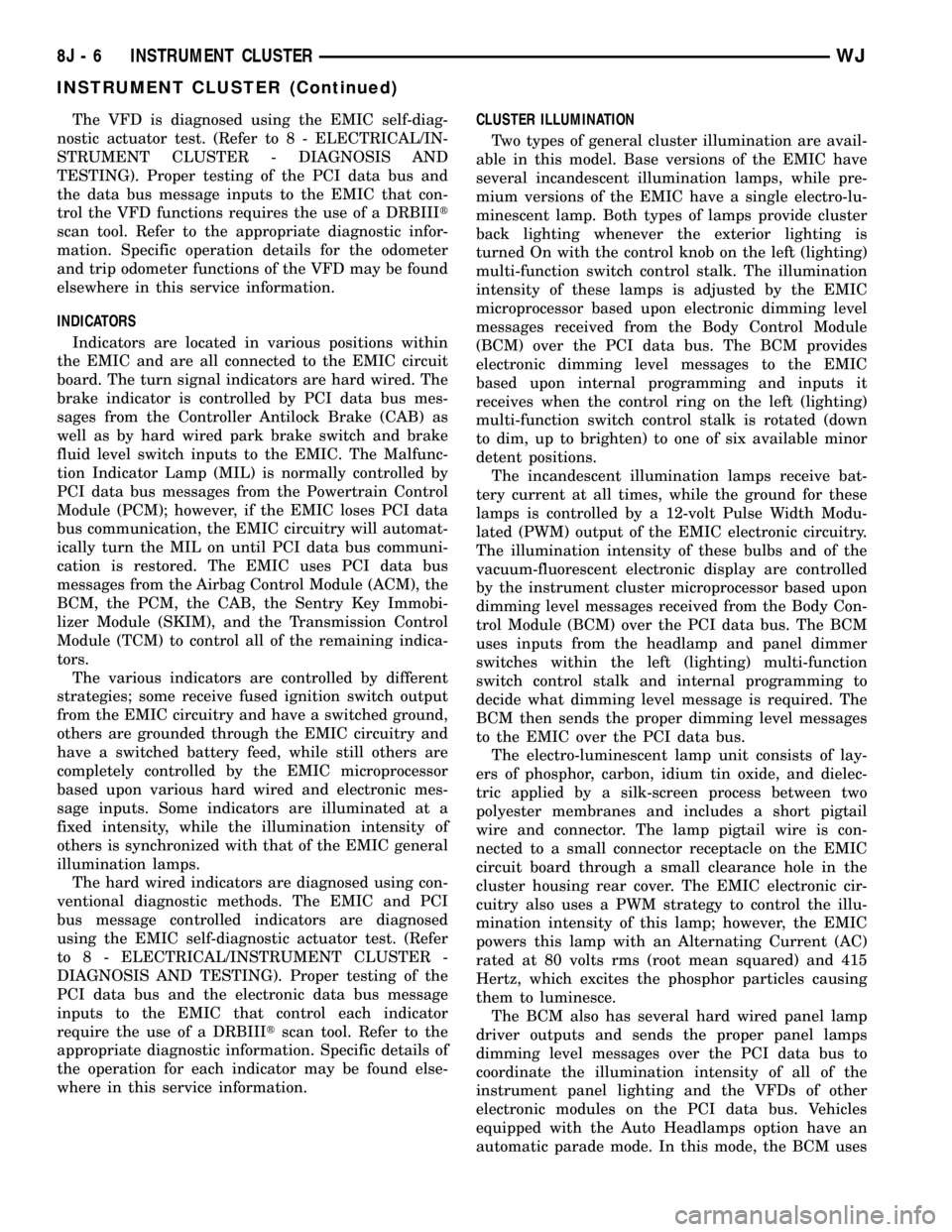
The VFD is diagnosed using the EMIC self-diag-
nostic actuator test. (Refer to 8 - ELECTRICAL/IN-
STRUMENT CLUSTER - DIAGNOSIS AND
TESTING). Proper testing of the PCI data bus and
the data bus message inputs to the EMIC that con-
trol the VFD functions requires the use of a DRBIIIt
scan tool. Refer to the appropriate diagnostic infor-
mation. Specific operation details for the odometer
and trip odometer functions of the VFD may be found
elsewhere in this service information.
INDICATORS
Indicators are located in various positions within
the EMIC and are all connected to the EMIC circuit
board. The turn signal indicators are hard wired. The
brake indicator is controlled by PCI data bus mes-
sages from the Controller Antilock Brake (CAB) as
well as by hard wired park brake switch and brake
fluid level switch inputs to the EMIC. The Malfunc-
tion Indicator Lamp (MIL) is normally controlled by
PCI data bus messages from the Powertrain Control
Module (PCM); however, if the EMIC loses PCI data
bus communication, the EMIC circuitry will automat-
ically turn the MIL on until PCI data bus communi-
cation is restored. The EMIC uses PCI data bus
messages from the Airbag Control Module (ACM), the
BCM, the PCM, the CAB, the Sentry Key Immobi-
lizer Module (SKIM), and the Transmission Control
Module (TCM) to control all of the remaining indica-
tors.
The various indicators are controlled by different
strategies; some receive fused ignition switch output
from the EMIC circuitry and have a switched ground,
others are grounded through the EMIC circuitry and
have a switched battery feed, while still others are
completely controlled by the EMIC microprocessor
based upon various hard wired and electronic mes-
sage inputs. Some indicators are illuminated at a
fixed intensity, while the illumination intensity of
others is synchronized with that of the EMIC general
illumination lamps.
The hard wired indicators are diagnosed using con-
ventional diagnostic methods. The EMIC and PCI
bus message controlled indicators are diagnosed
using the EMIC self-diagnostic actuator test. (Refer
to 8 - ELECTRICAL/INSTRUMENT CLUSTER -
DIAGNOSIS AND TESTING). Proper testing of the
PCI data bus and the electronic data bus message
inputs to the EMIC that control each indicator
require the use of a DRBIIItscan tool. Refer to the
appropriate diagnostic information. Specific details of
the operation for each indicator may be found else-
where in this service information.CLUSTER ILLUMINATION
Two types of general cluster illumination are avail-
able in this model. Base versions of the EMIC have
several incandescent illumination lamps, while pre-
mium versions of the EMIC have a single electro-lu-
minescent lamp. Both types of lamps provide cluster
back lighting whenever the exterior lighting is
turned On with the control knob on the left (lighting)
multi-function switch control stalk. The illumination
intensity of these lamps is adjusted by the EMIC
microprocessor based upon electronic dimming level
messages received from the Body Control Module
(BCM) over the PCI data bus. The BCM provides
electronic dimming level messages to the EMIC
based upon internal programming and inputs it
receives when the control ring on the left (lighting)
multi-function switch control stalk is rotated (down
to dim, up to brighten) to one of six available minor
detent positions.
The incandescent illumination lamps receive bat-
tery current at all times, while the ground for these
lamps is controlled by a 12-volt Pulse Width Modu-
lated (PWM) output of the EMIC electronic circuitry.
The illumination intensity of these bulbs and of the
vacuum-fluorescent electronic display are controlled
by the instrument cluster microprocessor based upon
dimming level messages received from the Body Con-
trol Module (BCM) over the PCI data bus. The BCM
uses inputs from the headlamp and panel dimmer
switches within the left (lighting) multi-function
switch control stalk and internal programming to
decide what dimming level message is required. The
BCM then sends the proper dimming level messages
to the EMIC over the PCI data bus.
The electro-luminescent lamp unit consists of lay-
ers of phosphor, carbon, idium tin oxide, and dielec-
tric applied by a silk-screen process between two
polyester membranes and includes a short pigtail
wire and connector. The lamp pigtail wire is con-
nected to a small connector receptacle on the EMIC
circuit board through a small clearance hole in the
cluster housing rear cover. The EMIC electronic cir-
cuitry also uses a PWM strategy to control the illu-
mination intensity of this lamp; however, the EMIC
powers this lamp with an Alternating Current (AC)
rated at 80 volts rms (root mean squared) and 415
Hertz, which excites the phosphor particles causing
them to luminesce.
The BCM also has several hard wired panel lamp
driver outputs and sends the proper panel lamps
dimming level messages over the PCI data bus to
coordinate the illumination intensity of all of the
instrument panel lighting and the VFDs of other
electronic modules on the PCI data bus. Vehicles
equipped with the Auto Headlamps option have an
automatic parade mode. In this mode, the BCM uses
8J - 6 INSTRUMENT CLUSTERWJ
INSTRUMENT CLUSTER (Continued)
Page 422 of 2199
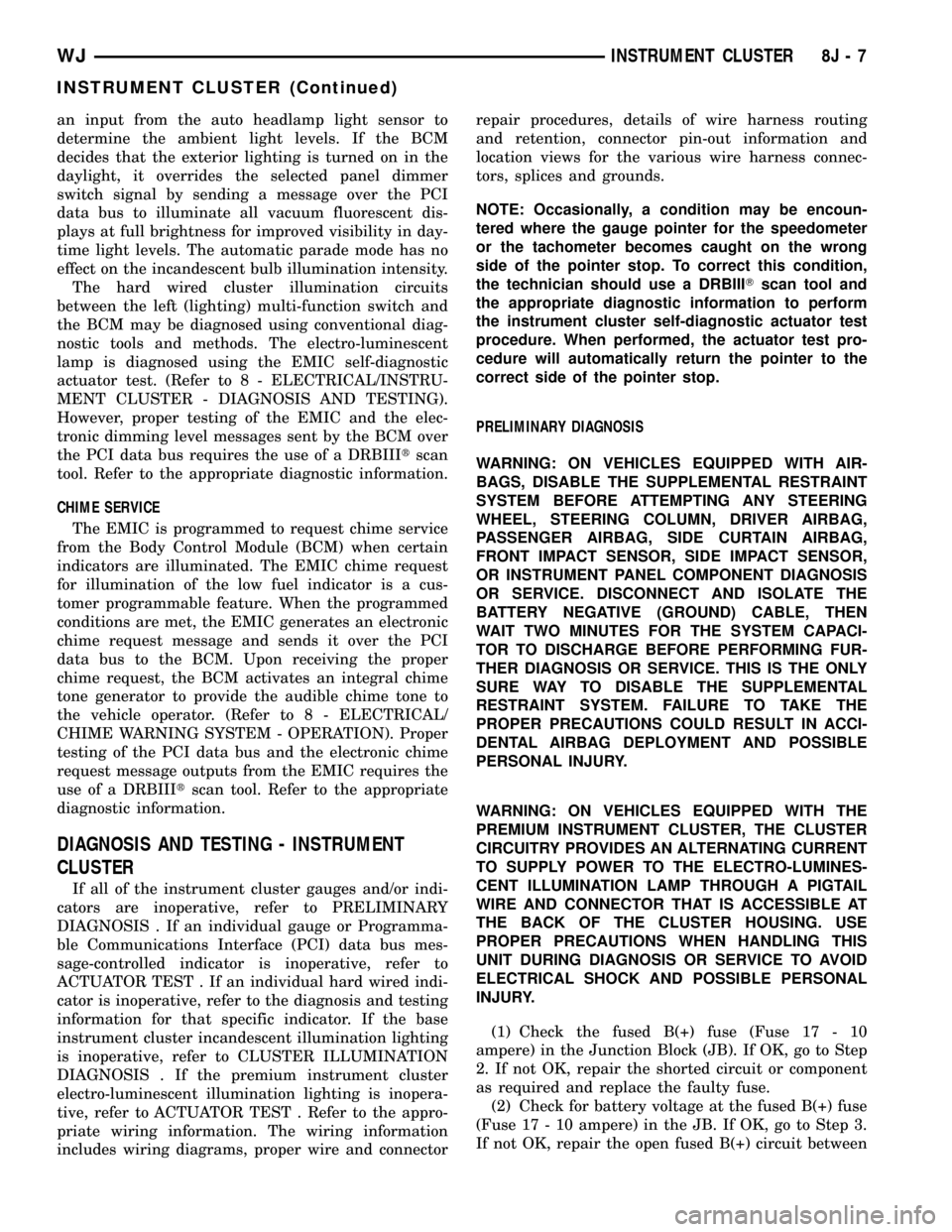
an input from the auto headlamp light sensor to
determine the ambient light levels. If the BCM
decides that the exterior lighting is turned on in the
daylight, it overrides the selected panel dimmer
switch signal by sending a message over the PCI
data bus to illuminate all vacuum fluorescent dis-
plays at full brightness for improved visibility in day-
time light levels. The automatic parade mode has no
effect on the incandescent bulb illumination intensity.
The hard wired cluster illumination circuits
between the left (lighting) multi-function switch and
the BCM may be diagnosed using conventional diag-
nostic tools and methods. The electro-luminescent
lamp is diagnosed using the EMIC self-diagnostic
actuator test. (Refer to 8 - ELECTRICAL/INSTRU-
MENT CLUSTER - DIAGNOSIS AND TESTING).
However, proper testing of the EMIC and the elec-
tronic dimming level messages sent by the BCM over
the PCI data bus requires the use of a DRBIIItscan
tool. Refer to the appropriate diagnostic information.
CHIME SERVICE
The EMIC is programmed to request chime service
from the Body Control Module (BCM) when certain
indicators are illuminated. The EMIC chime request
for illumination of the low fuel indicator is a cus-
tomer programmable feature. When the programmed
conditions are met, the EMIC generates an electronic
chime request message and sends it over the PCI
data bus to the BCM. Upon receiving the proper
chime request, the BCM activates an integral chime
tone generator to provide the audible chime tone to
the vehicle operator. (Refer to 8 - ELECTRICAL/
CHIME WARNING SYSTEM - OPERATION). Proper
testing of the PCI data bus and the electronic chime
request message outputs from the EMIC requires the
use of a DRBIIItscan tool. Refer to the appropriate
diagnostic information.
DIAGNOSIS AND TESTING - INSTRUMENT
CLUSTER
If all of the instrument cluster gauges and/or indi-
cators are inoperative, refer to PRELIMINARY
DIAGNOSIS . If an individual gauge or Programma-
ble Communications Interface (PCI) data bus mes-
sage-controlled indicator is inoperative, refer to
ACTUATOR TEST . If an individual hard wired indi-
cator is inoperative, refer to the diagnosis and testing
information for that specific indicator. If the base
instrument cluster incandescent illumination lighting
is inoperative, refer to CLUSTER ILLUMINATION
DIAGNOSIS . If the premium instrument cluster
electro-luminescent illumination lighting is inopera-
tive, refer to ACTUATOR TEST . Refer to the appro-
priate wiring information. The wiring information
includes wiring diagrams, proper wire and connectorrepair procedures, details of wire harness routing
and retention, connector pin-out information and
location views for the various wire harness connec-
tors, splices and grounds.
NOTE: Occasionally, a condition may be encoun-
tered where the gauge pointer for the speedometer
or the tachometer becomes caught on the wrong
side of the pointer stop. To correct this condition,
the technician should use a DRBIIITscan tool and
the appropriate diagnostic information to perform
the instrument cluster self-diagnostic actuator test
procedure. When performed, the actuator test pro-
cedure will automatically return the pointer to the
correct side of the pointer stop.
PRELIMINARY DIAGNOSIS
WARNING: ON VEHICLES EQUIPPED WITH AIR-
BAGS, DISABLE THE SUPPLEMENTAL RESTRAINT
SYSTEM BEFORE ATTEMPTING ANY STEERING
WHEEL, STEERING COLUMN, DRIVER AIRBAG,
PASSENGER AIRBAG, SIDE CURTAIN AIRBAG,
FRONT IMPACT SENSOR, SIDE IMPACT SENSOR,
OR INSTRUMENT PANEL COMPONENT DIAGNOSIS
OR SERVICE. DISCONNECT AND ISOLATE THE
BATTERY NEGATIVE (GROUND) CABLE, THEN
WAIT TWO MINUTES FOR THE SYSTEM CAPACI-
TOR TO DISCHARGE BEFORE PERFORMING FUR-
THER DIAGNOSIS OR SERVICE. THIS IS THE ONLY
SURE WAY TO DISABLE THE SUPPLEMENTAL
RESTRAINT SYSTEM. FAILURE TO TAKE THE
PROPER PRECAUTIONS COULD RESULT IN ACCI-
DENTAL AIRBAG DEPLOYMENT AND POSSIBLE
PERSONAL INJURY.
WARNING: ON VEHICLES EQUIPPED WITH THE
PREMIUM INSTRUMENT CLUSTER, THE CLUSTER
CIRCUITRY PROVIDES AN ALTERNATING CURRENT
TO SUPPLY POWER TO THE ELECTRO-LUMINES-
CENT ILLUMINATION LAMP THROUGH A PIGTAIL
WIRE AND CONNECTOR THAT IS ACCESSIBLE AT
THE BACK OF THE CLUSTER HOUSING. USE
PROPER PRECAUTIONS WHEN HANDLING THIS
UNIT DURING DIAGNOSIS OR SERVICE TO AVOID
ELECTRICAL SHOCK AND POSSIBLE PERSONAL
INJURY.
(1) Check the fused B(+) fuse (Fuse 17 - 10
ampere) in the Junction Block (JB). If OK, go to Step
2. If not OK, repair the shorted circuit or component
as required and replace the faulty fuse.
(2) Check for battery voltage at the fused B(+) fuse
(Fuse 17 - 10 ampere) in the JB. If OK, go to Step 3.
If not OK, repair the open fused B(+) circuit between
WJINSTRUMENT CLUSTER 8J - 7
INSTRUMENT CLUSTER (Continued)
Page 423 of 2199
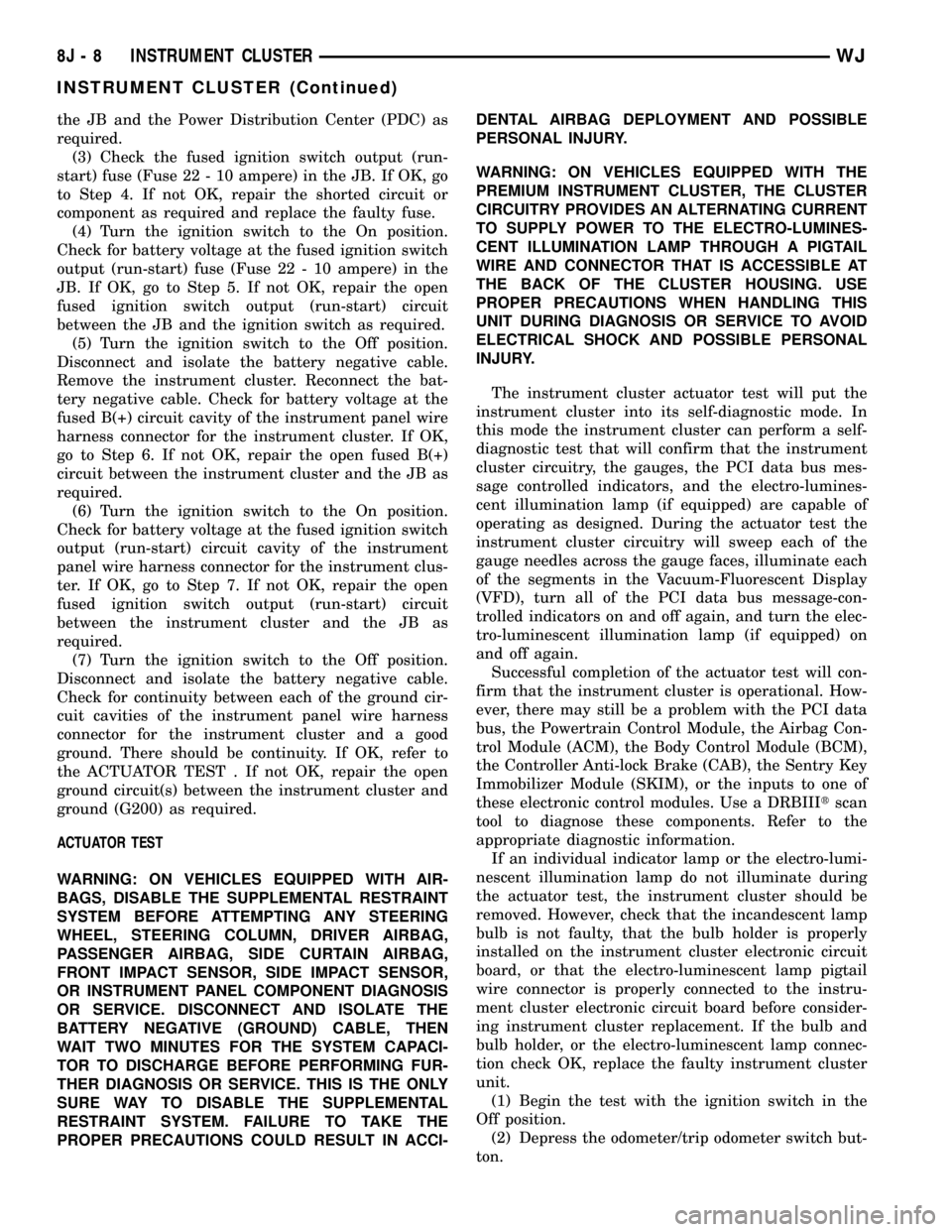
the JB and the Power Distribution Center (PDC) as
required.
(3) Check the fused ignition switch output (run-
start) fuse (Fuse 22 - 10 ampere) in the JB. If OK, go
to Step 4. If not OK, repair the shorted circuit or
component as required and replace the faulty fuse.
(4) Turn the ignition switch to the On position.
Check for battery voltage at the fused ignition switch
output (run-start) fuse (Fuse 22 - 10 ampere) in the
JB. If OK, go to Step 5. If not OK, repair the open
fused ignition switch output (run-start) circuit
between the JB and the ignition switch as required.
(5) Turn the ignition switch to the Off position.
Disconnect and isolate the battery negative cable.
Remove the instrument cluster. Reconnect the bat-
tery negative cable. Check for battery voltage at the
fused B(+) circuit cavity of the instrument panel wire
harness connector for the instrument cluster. If OK,
go to Step 6. If not OK, repair the open fused B(+)
circuit between the instrument cluster and the JB as
required.
(6) Turn the ignition switch to the On position.
Check for battery voltage at the fused ignition switch
output (run-start) circuit cavity of the instrument
panel wire harness connector for the instrument clus-
ter. If OK, go to Step 7. If not OK, repair the open
fused ignition switch output (run-start) circuit
between the instrument cluster and the JB as
required.
(7) Turn the ignition switch to the Off position.
Disconnect and isolate the battery negative cable.
Check for continuity between each of the ground cir-
cuit cavities of the instrument panel wire harness
connector for the instrument cluster and a good
ground. There should be continuity. If OK, refer to
the ACTUATOR TEST . If not OK, repair the open
ground circuit(s) between the instrument cluster and
ground (G200) as required.
ACTUATOR TEST
WARNING: ON VEHICLES EQUIPPED WITH AIR-
BAGS, DISABLE THE SUPPLEMENTAL RESTRAINT
SYSTEM BEFORE ATTEMPTING ANY STEERING
WHEEL, STEERING COLUMN, DRIVER AIRBAG,
PASSENGER AIRBAG, SIDE CURTAIN AIRBAG,
FRONT IMPACT SENSOR, SIDE IMPACT SENSOR,
OR INSTRUMENT PANEL COMPONENT DIAGNOSIS
OR SERVICE. DISCONNECT AND ISOLATE THE
BATTERY NEGATIVE (GROUND) CABLE, THEN
WAIT TWO MINUTES FOR THE SYSTEM CAPACI-
TOR TO DISCHARGE BEFORE PERFORMING FUR-
THER DIAGNOSIS OR SERVICE. THIS IS THE ONLY
SURE WAY TO DISABLE THE SUPPLEMENTAL
RESTRAINT SYSTEM. FAILURE TO TAKE THE
PROPER PRECAUTIONS COULD RESULT IN ACCI-DENTAL AIRBAG DEPLOYMENT AND POSSIBLE
PERSONAL INJURY.
WARNING: ON VEHICLES EQUIPPED WITH THE
PREMIUM INSTRUMENT CLUSTER, THE CLUSTER
CIRCUITRY PROVIDES AN ALTERNATING CURRENT
TO SUPPLY POWER TO THE ELECTRO-LUMINES-
CENT ILLUMINATION LAMP THROUGH A PIGTAIL
WIRE AND CONNECTOR THAT IS ACCESSIBLE AT
THE BACK OF THE CLUSTER HOUSING. USE
PROPER PRECAUTIONS WHEN HANDLING THIS
UNIT DURING DIAGNOSIS OR SERVICE TO AVOID
ELECTRICAL SHOCK AND POSSIBLE PERSONAL
INJURY.
The instrument cluster actuator test will put the
instrument cluster into its self-diagnostic mode. In
this mode the instrument cluster can perform a self-
diagnostic test that will confirm that the instrument
cluster circuitry, the gauges, the PCI data bus mes-
sage controlled indicators, and the electro-lumines-
cent illumination lamp (if equipped) are capable of
operating as designed. During the actuator test the
instrument cluster circuitry will sweep each of the
gauge needles across the gauge faces, illuminate each
of the segments in the Vacuum-Fluorescent Display
(VFD), turn all of the PCI data bus message-con-
trolled indicators on and off again, and turn the elec-
tro-luminescent illumination lamp (if equipped) on
and off again.
Successful completion of the actuator test will con-
firm that the instrument cluster is operational. How-
ever, there may still be a problem with the PCI data
bus, the Powertrain Control Module, the Airbag Con-
trol Module (ACM), the Body Control Module (BCM),
the Controller Anti-lock Brake (CAB), the Sentry Key
Immobilizer Module (SKIM), or the inputs to one of
these electronic control modules. Use a DRBIIItscan
tool to diagnose these components. Refer to the
appropriate diagnostic information.
If an individual indicator lamp or the electro-lumi-
nescent illumination lamp do not illuminate during
the actuator test, the instrument cluster should be
removed. However, check that the incandescent lamp
bulb is not faulty, that the bulb holder is properly
installed on the instrument cluster electronic circuit
board, or that the electro-luminescent lamp pigtail
wire connector is properly connected to the instru-
ment cluster electronic circuit board before consider-
ing instrument cluster replacement. If the bulb and
bulb holder, or the electro-luminescent lamp connec-
tion check OK, replace the faulty instrument cluster
unit.
(1) Begin the test with the ignition switch in the
Off position.
(2) Depress the odometer/trip odometer switch but-
ton.
8J - 8 INSTRUMENT CLUSTERWJ
INSTRUMENT CLUSTER (Continued)
Page 428 of 2199
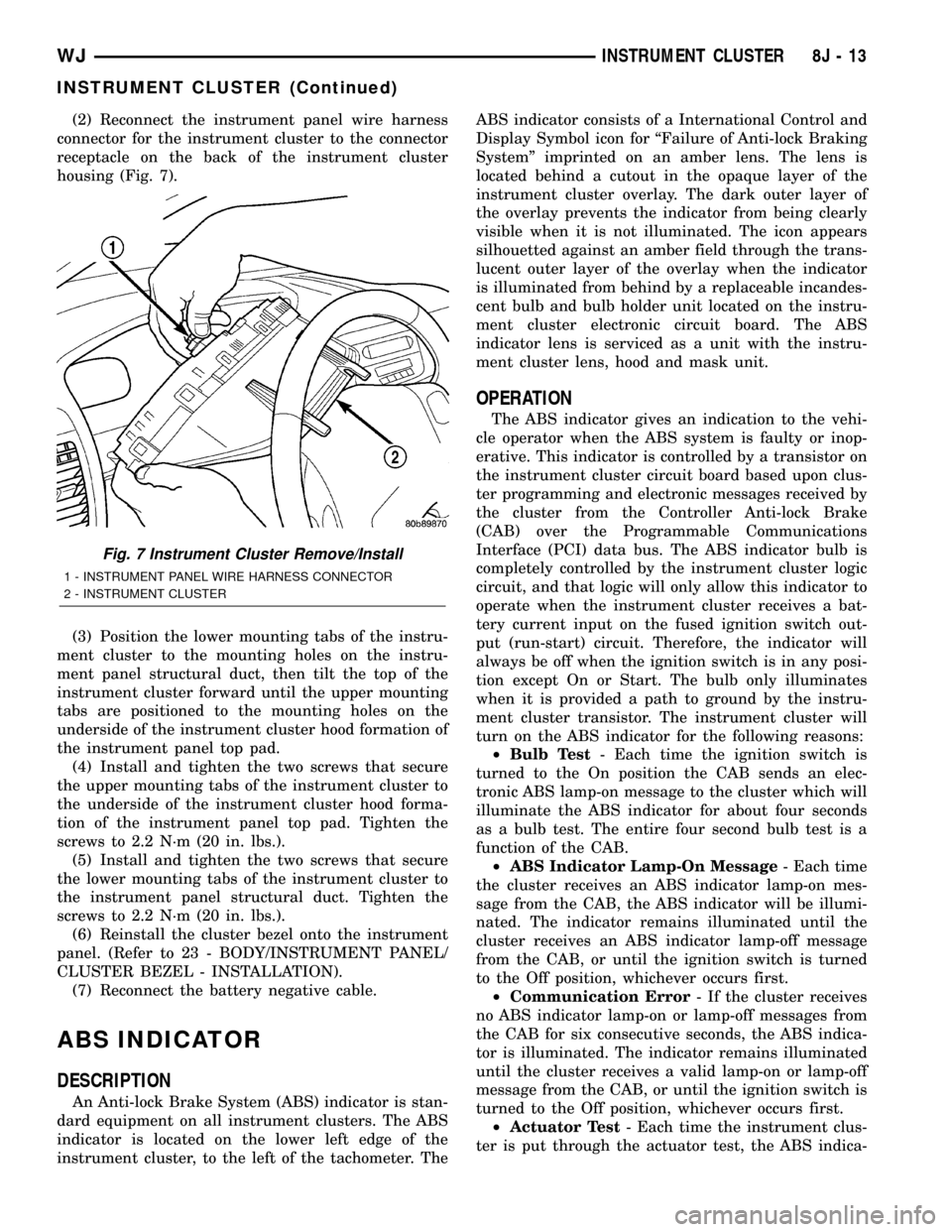
(2) Reconnect the instrument panel wire harness
connector for the instrument cluster to the connector
receptacle on the back of the instrument cluster
housing (Fig. 7).
(3) Position the lower mounting tabs of the instru-
ment cluster to the mounting holes on the instru-
ment panel structural duct, then tilt the top of the
instrument cluster forward until the upper mounting
tabs are positioned to the mounting holes on the
underside of the instrument cluster hood formation of
the instrument panel top pad.
(4) Install and tighten the two screws that secure
the upper mounting tabs of the instrument cluster to
the underside of the instrument cluster hood forma-
tion of the instrument panel top pad. Tighten the
screws to 2.2 N´m (20 in. lbs.).
(5) Install and tighten the two screws that secure
the lower mounting tabs of the instrument cluster to
the instrument panel structural duct. Tighten the
screws to 2.2 N´m (20 in. lbs.).
(6) Reinstall the cluster bezel onto the instrument
panel. (Refer to 23 - BODY/INSTRUMENT PANEL/
CLUSTER BEZEL - INSTALLATION).
(7) Reconnect the battery negative cable.
ABS INDICATOR
DESCRIPTION
An Anti-lock Brake System (ABS) indicator is stan-
dard equipment on all instrument clusters. The ABS
indicator is located on the lower left edge of the
instrument cluster, to the left of the tachometer. TheABS indicator consists of a International Control and
Display Symbol icon for ªFailure of Anti-lock Braking
Systemº imprinted on an amber lens. The lens is
located behind a cutout in the opaque layer of the
instrument cluster overlay. The dark outer layer of
the overlay prevents the indicator from being clearly
visible when it is not illuminated. The icon appears
silhouetted against an amber field through the trans-
lucent outer layer of the overlay when the indicator
is illuminated from behind by a replaceable incandes-
cent bulb and bulb holder unit located on the instru-
ment cluster electronic circuit board. The ABS
indicator lens is serviced as a unit with the instru-
ment cluster lens, hood and mask unit.
OPERATION
The ABS indicator gives an indication to the vehi-
cle operator when the ABS system is faulty or inop-
erative. This indicator is controlled by a transistor on
the instrument cluster circuit board based upon clus-
ter programming and electronic messages received by
the cluster from the Controller Anti-lock Brake
(CAB) over the Programmable Communications
Interface (PCI) data bus. The ABS indicator bulb is
completely controlled by the instrument cluster logic
circuit, and that logic will only allow this indicator to
operate when the instrument cluster receives a bat-
tery current input on the fused ignition switch out-
put (run-start) circuit. Therefore, the indicator will
always be off when the ignition switch is in any posi-
tion except On or Start. The bulb only illuminates
when it is provided a path to ground by the instru-
ment cluster transistor. The instrument cluster will
turn on the ABS indicator for the following reasons:
²Bulb Test- Each time the ignition switch is
turned to the On position the CAB sends an elec-
tronic ABS lamp-on message to the cluster which will
illuminate the ABS indicator for about four seconds
as a bulb test. The entire four second bulb test is a
function of the CAB.
²ABS Indicator Lamp-On Message- Each time
the cluster receives an ABS indicator lamp-on mes-
sage from the CAB, the ABS indicator will be illumi-
nated. The indicator remains illuminated until the
cluster receives an ABS indicator lamp-off message
from the CAB, or until the ignition switch is turned
to the Off position, whichever occurs first.
²Communication Error- If the cluster receives
no ABS indicator lamp-on or lamp-off messages from
the CAB for six consecutive seconds, the ABS indica-
tor is illuminated. The indicator remains illuminated
until the cluster receives a valid lamp-on or lamp-off
message from the CAB, or until the ignition switch is
turned to the Off position, whichever occurs first.
²Actuator Test- Each time the instrument clus-
ter is put through the actuator test, the ABS indica-
Fig. 7 Instrument Cluster Remove/Install
1 - INSTRUMENT PANEL WIRE HARNESS CONNECTOR
2 - INSTRUMENT CLUSTER
WJINSTRUMENT CLUSTER 8J - 13
INSTRUMENT CLUSTER (Continued)
Page 433 of 2199
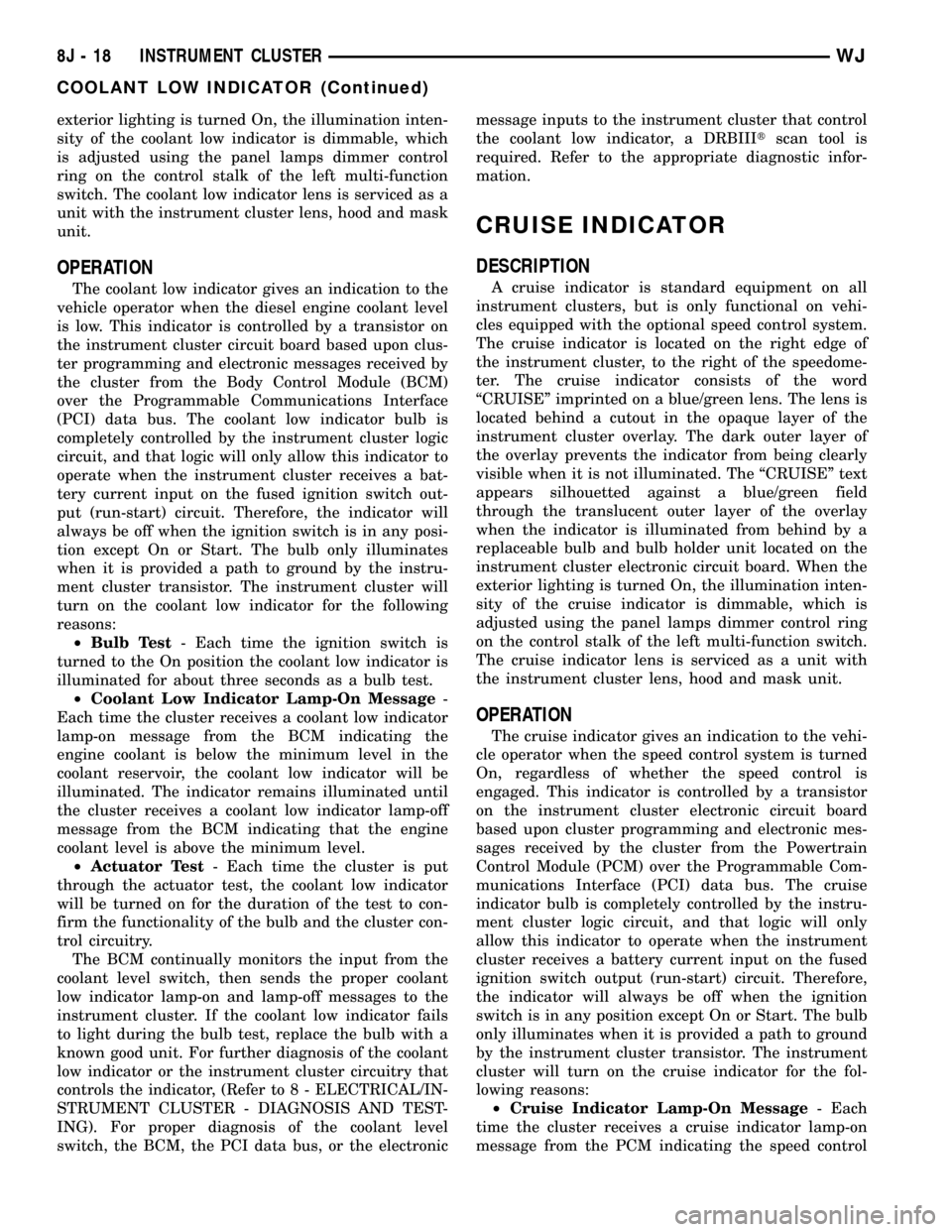
exterior lighting is turned On, the illumination inten-
sity of the coolant low indicator is dimmable, which
is adjusted using the panel lamps dimmer control
ring on the control stalk of the left multi-function
switch. The coolant low indicator lens is serviced as a
unit with the instrument cluster lens, hood and mask
unit.
OPERATION
The coolant low indicator gives an indication to the
vehicle operator when the diesel engine coolant level
is low. This indicator is controlled by a transistor on
the instrument cluster circuit board based upon clus-
ter programming and electronic messages received by
the cluster from the Body Control Module (BCM)
over the Programmable Communications Interface
(PCI) data bus. The coolant low indicator bulb is
completely controlled by the instrument cluster logic
circuit, and that logic will only allow this indicator to
operate when the instrument cluster receives a bat-
tery current input on the fused ignition switch out-
put (run-start) circuit. Therefore, the indicator will
always be off when the ignition switch is in any posi-
tion except On or Start. The bulb only illuminates
when it is provided a path to ground by the instru-
ment cluster transistor. The instrument cluster will
turn on the coolant low indicator for the following
reasons:
²Bulb Test- Each time the ignition switch is
turned to the On position the coolant low indicator is
illuminated for about three seconds as a bulb test.
²Coolant Low Indicator Lamp-On Message-
Each time the cluster receives a coolant low indicator
lamp-on message from the BCM indicating the
engine coolant is below the minimum level in the
coolant reservoir, the coolant low indicator will be
illuminated. The indicator remains illuminated until
the cluster receives a coolant low indicator lamp-off
message from the BCM indicating that the engine
coolant level is above the minimum level.
²Actuator Test- Each time the cluster is put
through the actuator test, the coolant low indicator
will be turned on for the duration of the test to con-
firm the functionality of the bulb and the cluster con-
trol circuitry.
The BCM continually monitors the input from the
coolant level switch, then sends the proper coolant
low indicator lamp-on and lamp-off messages to the
instrument cluster. If the coolant low indicator fails
to light during the bulb test, replace the bulb with a
known good unit. For further diagnosis of the coolant
low indicator or the instrument cluster circuitry that
controls the indicator, (Refer to 8 - ELECTRICAL/IN-
STRUMENT CLUSTER - DIAGNOSIS AND TEST-
ING). For proper diagnosis of the coolant level
switch, the BCM, the PCI data bus, or the electronicmessage inputs to the instrument cluster that control
the coolant low indicator, a DRBIIItscan tool is
required. Refer to the appropriate diagnostic infor-
mation.
CRUISE INDICATOR
DESCRIPTION
A cruise indicator is standard equipment on all
instrument clusters, but is only functional on vehi-
cles equipped with the optional speed control system.
The cruise indicator is located on the right edge of
the instrument cluster, to the right of the speedome-
ter. The cruise indicator consists of the word
ªCRUISEº imprinted on a blue/green lens. The lens is
located behind a cutout in the opaque layer of the
instrument cluster overlay. The dark outer layer of
the overlay prevents the indicator from being clearly
visible when it is not illuminated. The ªCRUISEº text
appears silhouetted against a blue/green field
through the translucent outer layer of the overlay
when the indicator is illuminated from behind by a
replaceable bulb and bulb holder unit located on the
instrument cluster electronic circuit board. When the
exterior lighting is turned On, the illumination inten-
sity of the cruise indicator is dimmable, which is
adjusted using the panel lamps dimmer control ring
on the control stalk of the left multi-function switch.
The cruise indicator lens is serviced as a unit with
the instrument cluster lens, hood and mask unit.
OPERATION
The cruise indicator gives an indication to the vehi-
cle operator when the speed control system is turned
On, regardless of whether the speed control is
engaged. This indicator is controlled by a transistor
on the instrument cluster electronic circuit board
based upon cluster programming and electronic mes-
sages received by the cluster from the Powertrain
Control Module (PCM) over the Programmable Com-
munications Interface (PCI) data bus. The cruise
indicator bulb is completely controlled by the instru-
ment cluster logic circuit, and that logic will only
allow this indicator to operate when the instrument
cluster receives a battery current input on the fused
ignition switch output (run-start) circuit. Therefore,
the indicator will always be off when the ignition
switch is in any position except On or Start. The bulb
only illuminates when it is provided a path to ground
by the instrument cluster transistor. The instrument
cluster will turn on the cruise indicator for the fol-
lowing reasons:
²Cruise Indicator Lamp-On Message- Each
time the cluster receives a cruise indicator lamp-on
message from the PCM indicating the speed control
8J - 18 INSTRUMENT CLUSTERWJ
COOLANT LOW INDICATOR (Continued)
Page 435 of 2199
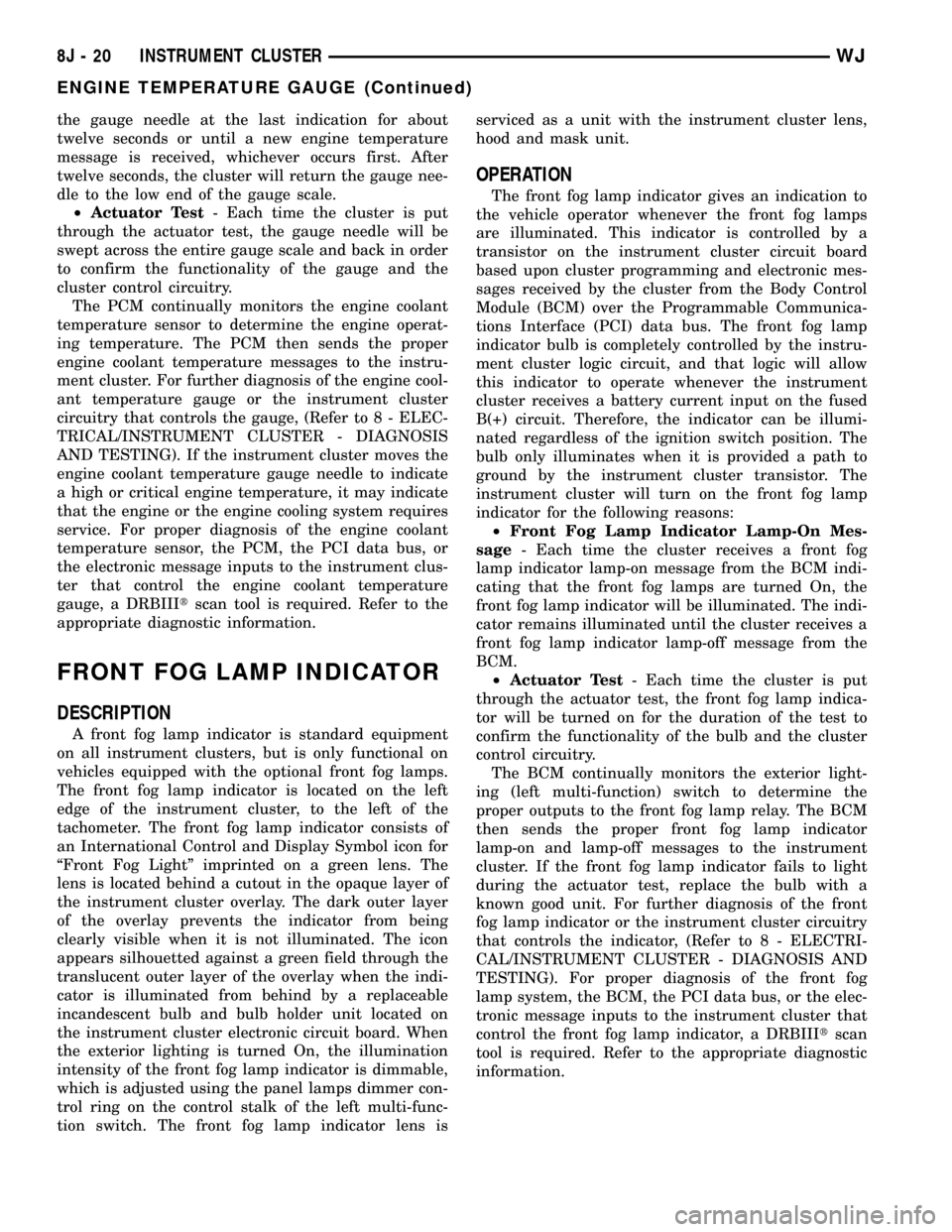
the gauge needle at the last indication for about
twelve seconds or until a new engine temperature
message is received, whichever occurs first. After
twelve seconds, the cluster will return the gauge nee-
dle to the low end of the gauge scale.
²Actuator Test- Each time the cluster is put
through the actuator test, the gauge needle will be
swept across the entire gauge scale and back in order
to confirm the functionality of the gauge and the
cluster control circuitry.
The PCM continually monitors the engine coolant
temperature sensor to determine the engine operat-
ing temperature. The PCM then sends the proper
engine coolant temperature messages to the instru-
ment cluster. For further diagnosis of the engine cool-
ant temperature gauge or the instrument cluster
circuitry that controls the gauge, (Refer to 8 - ELEC-
TRICAL/INSTRUMENT CLUSTER - DIAGNOSIS
AND TESTING). If the instrument cluster moves the
engine coolant temperature gauge needle to indicate
a high or critical engine temperature, it may indicate
that the engine or the engine cooling system requires
service. For proper diagnosis of the engine coolant
temperature sensor, the PCM, the PCI data bus, or
the electronic message inputs to the instrument clus-
ter that control the engine coolant temperature
gauge, a DRBIIItscan tool is required. Refer to the
appropriate diagnostic information.
FRONT FOG LAMP INDICATOR
DESCRIPTION
A front fog lamp indicator is standard equipment
on all instrument clusters, but is only functional on
vehicles equipped with the optional front fog lamps.
The front fog lamp indicator is located on the left
edge of the instrument cluster, to the left of the
tachometer. The front fog lamp indicator consists of
an International Control and Display Symbol icon for
ªFront Fog Lightº imprinted on a green lens. The
lens is located behind a cutout in the opaque layer of
the instrument cluster overlay. The dark outer layer
of the overlay prevents the indicator from being
clearly visible when it is not illuminated. The icon
appears silhouetted against a green field through the
translucent outer layer of the overlay when the indi-
cator is illuminated from behind by a replaceable
incandescent bulb and bulb holder unit located on
the instrument cluster electronic circuit board. When
the exterior lighting is turned On, the illumination
intensity of the front fog lamp indicator is dimmable,
which is adjusted using the panel lamps dimmer con-
trol ring on the control stalk of the left multi-func-
tion switch. The front fog lamp indicator lens isserviced as a unit with the instrument cluster lens,
hood and mask unit.
OPERATION
The front fog lamp indicator gives an indication to
the vehicle operator whenever the front fog lamps
are illuminated. This indicator is controlled by a
transistor on the instrument cluster circuit board
based upon cluster programming and electronic mes-
sages received by the cluster from the Body Control
Module (BCM) over the Programmable Communica-
tions Interface (PCI) data bus. The front fog lamp
indicator bulb is completely controlled by the instru-
ment cluster logic circuit, and that logic will allow
this indicator to operate whenever the instrument
cluster receives a battery current input on the fused
B(+) circuit. Therefore, the indicator can be illumi-
nated regardless of the ignition switch position. The
bulb only illuminates when it is provided a path to
ground by the instrument cluster transistor. The
instrument cluster will turn on the front fog lamp
indicator for the following reasons:
²Front Fog Lamp Indicator Lamp-On Mes-
sage- Each time the cluster receives a front fog
lamp indicator lamp-on message from the BCM indi-
cating that the front fog lamps are turned On, the
front fog lamp indicator will be illuminated. The indi-
cator remains illuminated until the cluster receives a
front fog lamp indicator lamp-off message from the
BCM.
²Actuator Test- Each time the cluster is put
through the actuator test, the front fog lamp indica-
tor will be turned on for the duration of the test to
confirm the functionality of the bulb and the cluster
control circuitry.
The BCM continually monitors the exterior light-
ing (left multi-function) switch to determine the
proper outputs to the front fog lamp relay. The BCM
then sends the proper front fog lamp indicator
lamp-on and lamp-off messages to the instrument
cluster. If the front fog lamp indicator fails to light
during the actuator test, replace the bulb with a
known good unit. For further diagnosis of the front
fog lamp indicator or the instrument cluster circuitry
that controls the indicator, (Refer to 8 - ELECTRI-
CAL/INSTRUMENT CLUSTER - DIAGNOSIS AND
TESTING). For proper diagnosis of the front fog
lamp system, the BCM, the PCI data bus, or the elec-
tronic message inputs to the instrument cluster that
control the front fog lamp indicator, a DRBIIItscan
tool is required. Refer to the appropriate diagnostic
information.
8J - 20 INSTRUMENT CLUSTERWJ
ENGINE TEMPERATURE GAUGE (Continued)
Page 436 of 2199
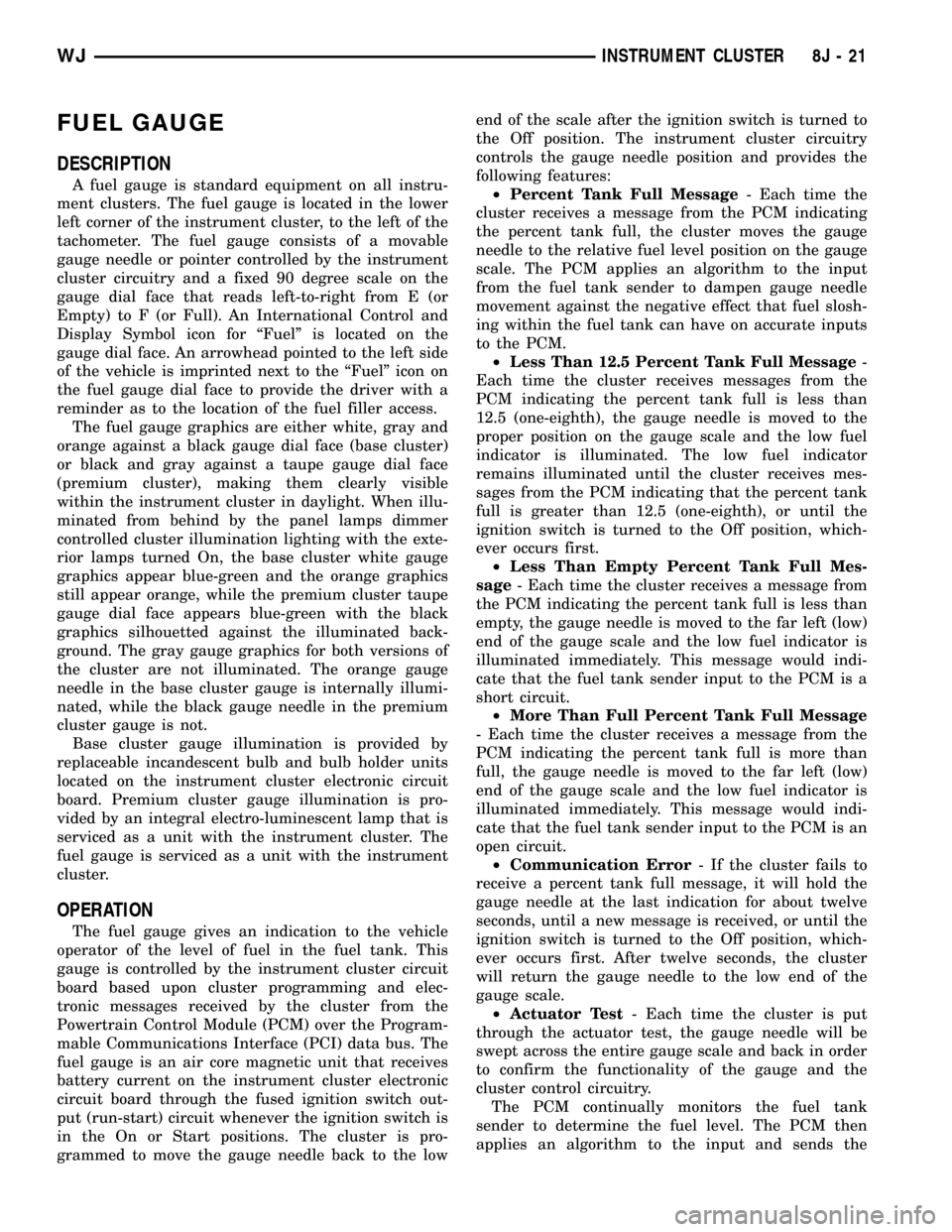
FUEL GAUGE
DESCRIPTION
A fuel gauge is standard equipment on all instru-
ment clusters. The fuel gauge is located in the lower
left corner of the instrument cluster, to the left of the
tachometer. The fuel gauge consists of a movable
gauge needle or pointer controlled by the instrument
cluster circuitry and a fixed 90 degree scale on the
gauge dial face that reads left-to-right from E (or
Empty) to F (or Full). An International Control and
Display Symbol icon for ªFuelº is located on the
gauge dial face. An arrowhead pointed to the left side
of the vehicle is imprinted next to the ªFuelº icon on
the fuel gauge dial face to provide the driver with a
reminder as to the location of the fuel filler access.
The fuel gauge graphics are either white, gray and
orange against a black gauge dial face (base cluster)
or black and gray against a taupe gauge dial face
(premium cluster), making them clearly visible
within the instrument cluster in daylight. When illu-
minated from behind by the panel lamps dimmer
controlled cluster illumination lighting with the exte-
rior lamps turned On, the base cluster white gauge
graphics appear blue-green and the orange graphics
still appear orange, while the premium cluster taupe
gauge dial face appears blue-green with the black
graphics silhouetted against the illuminated back-
ground. The gray gauge graphics for both versions of
the cluster are not illuminated. The orange gauge
needle in the base cluster gauge is internally illumi-
nated, while the black gauge needle in the premium
cluster gauge is not.
Base cluster gauge illumination is provided by
replaceable incandescent bulb and bulb holder units
located on the instrument cluster electronic circuit
board. Premium cluster gauge illumination is pro-
vided by an integral electro-luminescent lamp that is
serviced as a unit with the instrument cluster. The
fuel gauge is serviced as a unit with the instrument
cluster.
OPERATION
The fuel gauge gives an indication to the vehicle
operator of the level of fuel in the fuel tank. This
gauge is controlled by the instrument cluster circuit
board based upon cluster programming and elec-
tronic messages received by the cluster from the
Powertrain Control Module (PCM) over the Program-
mable Communications Interface (PCI) data bus. The
fuel gauge is an air core magnetic unit that receives
battery current on the instrument cluster electronic
circuit board through the fused ignition switch out-
put (run-start) circuit whenever the ignition switch is
in the On or Start positions. The cluster is pro-
grammed to move the gauge needle back to the lowend of the scale after the ignition switch is turned to
the Off position. The instrument cluster circuitry
controls the gauge needle position and provides the
following features:
²Percent Tank Full Message- Each time the
cluster receives a message from the PCM indicating
the percent tank full, the cluster moves the gauge
needle to the relative fuel level position on the gauge
scale. The PCM applies an algorithm to the input
from the fuel tank sender to dampen gauge needle
movement against the negative effect that fuel slosh-
ing within the fuel tank can have on accurate inputs
to the PCM.
²Less Than 12.5 Percent Tank Full Message-
Each time the cluster receives messages from the
PCM indicating the percent tank full is less than
12.5 (one-eighth), the gauge needle is moved to the
proper position on the gauge scale and the low fuel
indicator is illuminated. The low fuel indicator
remains illuminated until the cluster receives mes-
sages from the PCM indicating that the percent tank
full is greater than 12.5 (one-eighth), or until the
ignition switch is turned to the Off position, which-
ever occurs first.
²Less Than Empty Percent Tank Full Mes-
sage- Each time the cluster receives a message from
the PCM indicating the percent tank full is less than
empty, the gauge needle is moved to the far left (low)
end of the gauge scale and the low fuel indicator is
illuminated immediately. This message would indi-
cate that the fuel tank sender input to the PCM is a
short circuit.
²More Than Full Percent Tank Full Message
- Each time the cluster receives a message from the
PCM indicating the percent tank full is more than
full, the gauge needle is moved to the far left (low)
end of the gauge scale and the low fuel indicator is
illuminated immediately. This message would indi-
cate that the fuel tank sender input to the PCM is an
open circuit.
²Communication Error- If the cluster fails to
receive a percent tank full message, it will hold the
gauge needle at the last indication for about twelve
seconds, until a new message is received, or until the
ignition switch is turned to the Off position, which-
ever occurs first. After twelve seconds, the cluster
will return the gauge needle to the low end of the
gauge scale.
²Actuator Test- Each time the cluster is put
through the actuator test, the gauge needle will be
swept across the entire gauge scale and back in order
to confirm the functionality of the gauge and the
cluster control circuitry.
The PCM continually monitors the fuel tank
sender to determine the fuel level. The PCM then
applies an algorithm to the input and sends the
WJINSTRUMENT CLUSTER 8J - 21
Page 437 of 2199
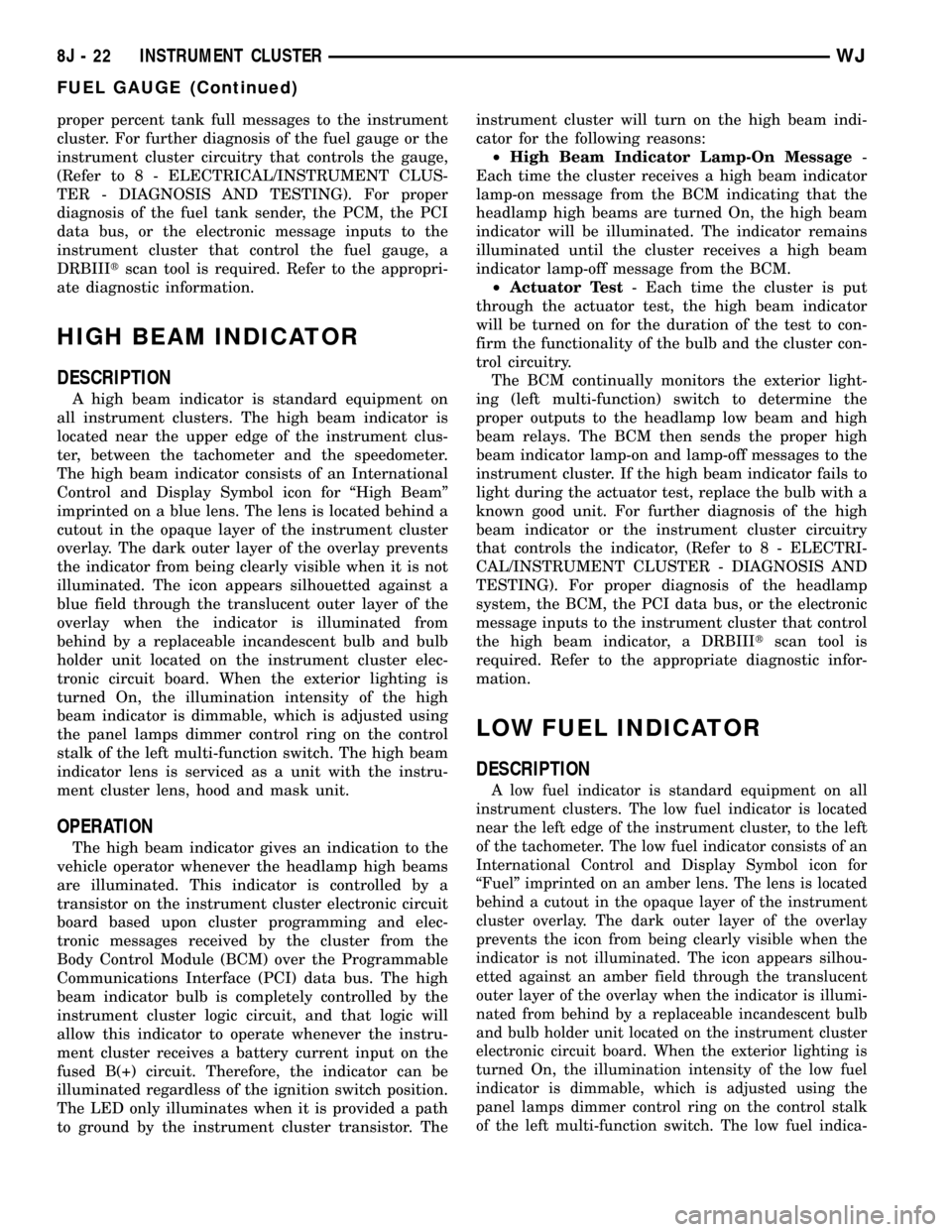
proper percent tank full messages to the instrument
cluster. For further diagnosis of the fuel gauge or the
instrument cluster circuitry that controls the gauge,
(Refer to 8 - ELECTRICAL/INSTRUMENT CLUS-
TER - DIAGNOSIS AND TESTING). For proper
diagnosis of the fuel tank sender, the PCM, the PCI
data bus, or the electronic message inputs to the
instrument cluster that control the fuel gauge, a
DRBIIItscan tool is required. Refer to the appropri-
ate diagnostic information.
HIGH BEAM INDICATOR
DESCRIPTION
A high beam indicator is standard equipment on
all instrument clusters. The high beam indicator is
located near the upper edge of the instrument clus-
ter, between the tachometer and the speedometer.
The high beam indicator consists of an International
Control and Display Symbol icon for ªHigh Beamº
imprinted on a blue lens. The lens is located behind a
cutout in the opaque layer of the instrument cluster
overlay. The dark outer layer of the overlay prevents
the indicator from being clearly visible when it is not
illuminated. The icon appears silhouetted against a
blue field through the translucent outer layer of the
overlay when the indicator is illuminated from
behind by a replaceable incandescent bulb and bulb
holder unit located on the instrument cluster elec-
tronic circuit board. When the exterior lighting is
turned On, the illumination intensity of the high
beam indicator is dimmable, which is adjusted using
the panel lamps dimmer control ring on the control
stalk of the left multi-function switch. The high beam
indicator lens is serviced as a unit with the instru-
ment cluster lens, hood and mask unit.
OPERATION
The high beam indicator gives an indication to the
vehicle operator whenever the headlamp high beams
are illuminated. This indicator is controlled by a
transistor on the instrument cluster electronic circuit
board based upon cluster programming and elec-
tronic messages received by the cluster from the
Body Control Module (BCM) over the Programmable
Communications Interface (PCI) data bus. The high
beam indicator bulb is completely controlled by the
instrument cluster logic circuit, and that logic will
allow this indicator to operate whenever the instru-
ment cluster receives a battery current input on the
fused B(+) circuit. Therefore, the indicator can be
illuminated regardless of the ignition switch position.
The LED only illuminates when it is provided a path
to ground by the instrument cluster transistor. Theinstrument cluster will turn on the high beam indi-
cator for the following reasons:
²High Beam Indicator Lamp-On Message-
Each time the cluster receives a high beam indicator
lamp-on message from the BCM indicating that the
headlamp high beams are turned On, the high beam
indicator will be illuminated. The indicator remains
illuminated until the cluster receives a high beam
indicator lamp-off message from the BCM.
²Actuator Test- Each time the cluster is put
through the actuator test, the high beam indicator
will be turned on for the duration of the test to con-
firm the functionality of the bulb and the cluster con-
trol circuitry.
The BCM continually monitors the exterior light-
ing (left multi-function) switch to determine the
proper outputs to the headlamp low beam and high
beam relays. The BCM then sends the proper high
beam indicator lamp-on and lamp-off messages to the
instrument cluster. If the high beam indicator fails to
light during the actuator test, replace the bulb with a
known good unit. For further diagnosis of the high
beam indicator or the instrument cluster circuitry
that controls the indicator, (Refer to 8 - ELECTRI-
CAL/INSTRUMENT CLUSTER - DIAGNOSIS AND
TESTING). For proper diagnosis of the headlamp
system, the BCM, the PCI data bus, or the electronic
message inputs to the instrument cluster that control
the high beam indicator, a DRBIIItscan tool is
required. Refer to the appropriate diagnostic infor-
mation.
LOW FUEL INDICATOR
DESCRIPTION
A low fuel indicator is standard equipment on all
instrument clusters. The low fuel indicator is located
near the left edge of the instrument cluster, to the left
of the tachometer. The low fuel indicator consists of an
International Control and Display Symbol icon for
ªFuelº imprinted on an amber lens. The lens is located
behind a cutout in the opaque layer of the instrument
cluster overlay. The dark outer layer of the overlay
prevents the icon from being clearly visible when the
indicator is not illuminated. The icon appears silhou-
etted against an amber field through the translucent
outer layer of the overlay when the indicator is illumi-
nated from behind by a replaceable incandescent bulb
and bulb holder unit located on the instrument cluster
electronic circuit board. When the exterior lighting is
turned On, the illumination intensity of the low fuel
indicator is dimmable, which is adjusted using the
panel lamps dimmer control ring on the control stalk
of the left multi-function switch. The low fuel indica-
8J - 22 INSTRUMENT CLUSTERWJ
FUEL GAUGE (Continued)
Page 439 of 2199
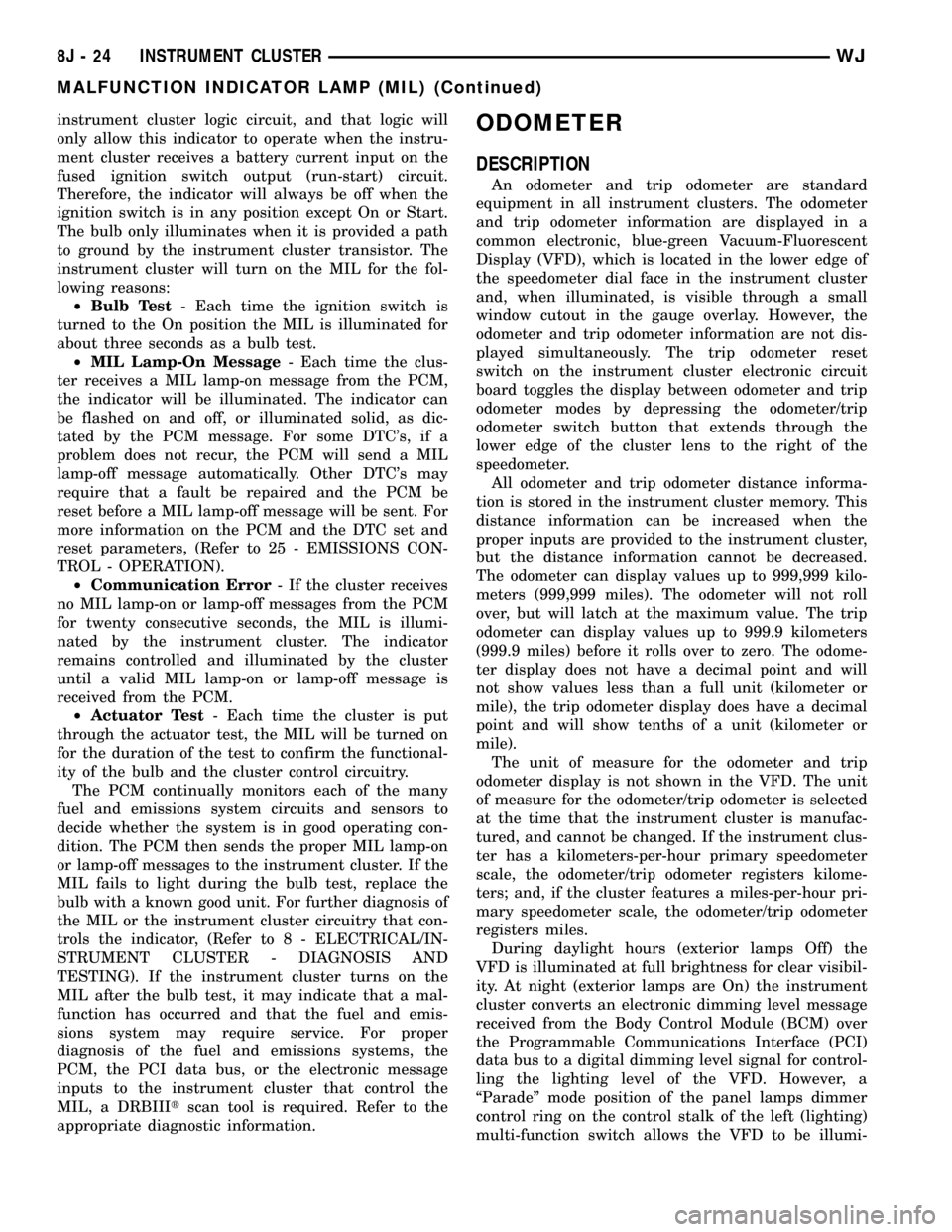
instrument cluster logic circuit, and that logic will
only allow this indicator to operate when the instru-
ment cluster receives a battery current input on the
fused ignition switch output (run-start) circuit.
Therefore, the indicator will always be off when the
ignition switch is in any position except On or Start.
The bulb only illuminates when it is provided a path
to ground by the instrument cluster transistor. The
instrument cluster will turn on the MIL for the fol-
lowing reasons:
²Bulb Test- Each time the ignition switch is
turned to the On position the MIL is illuminated for
about three seconds as a bulb test.
²MIL Lamp-On Message- Each time the clus-
ter receives a MIL lamp-on message from the PCM,
the indicator will be illuminated. The indicator can
be flashed on and off, or illuminated solid, as dic-
tated by the PCM message. For some DTC's, if a
problem does not recur, the PCM will send a MIL
lamp-off message automatically. Other DTC's may
require that a fault be repaired and the PCM be
reset before a MIL lamp-off message will be sent. For
more information on the PCM and the DTC set and
reset parameters, (Refer to 25 - EMISSIONS CON-
TROL - OPERATION).
²Communication Error- If the cluster receives
no MIL lamp-on or lamp-off messages from the PCM
for twenty consecutive seconds, the MIL is illumi-
nated by the instrument cluster. The indicator
remains controlled and illuminated by the cluster
until a valid MIL lamp-on or lamp-off message is
received from the PCM.
²Actuator Test- Each time the cluster is put
through the actuator test, the MIL will be turned on
for the duration of the test to confirm the functional-
ity of the bulb and the cluster control circuitry.
The PCM continually monitors each of the many
fuel and emissions system circuits and sensors to
decide whether the system is in good operating con-
dition. The PCM then sends the proper MIL lamp-on
or lamp-off messages to the instrument cluster. If the
MIL fails to light during the bulb test, replace the
bulb with a known good unit. For further diagnosis of
the MIL or the instrument cluster circuitry that con-
trols the indicator, (Refer to 8 - ELECTRICAL/IN-
STRUMENT CLUSTER - DIAGNOSIS AND
TESTING). If the instrument cluster turns on the
MIL after the bulb test, it may indicate that a mal-
function has occurred and that the fuel and emis-
sions system may require service. For proper
diagnosis of the fuel and emissions systems, the
PCM, the PCI data bus, or the electronic message
inputs to the instrument cluster that control the
MIL, a DRBIIItscan tool is required. Refer to the
appropriate diagnostic information.ODOMETER
DESCRIPTION
An odometer and trip odometer are standard
equipment in all instrument clusters. The odometer
and trip odometer information are displayed in a
common electronic, blue-green Vacuum-Fluorescent
Display (VFD), which is located in the lower edge of
the speedometer dial face in the instrument cluster
and, when illuminated, is visible through a small
window cutout in the gauge overlay. However, the
odometer and trip odometer information are not dis-
played simultaneously. The trip odometer reset
switch on the instrument cluster electronic circuit
board toggles the display between odometer and trip
odometer modes by depressing the odometer/trip
odometer switch button that extends through the
lower edge of the cluster lens to the right of the
speedometer.
All odometer and trip odometer distance informa-
tion is stored in the instrument cluster memory. This
distance information can be increased when the
proper inputs are provided to the instrument cluster,
but the distance information cannot be decreased.
The odometer can display values up to 999,999 kilo-
meters (999,999 miles). The odometer will not roll
over, but will latch at the maximum value. The trip
odometer can display values up to 999.9 kilometers
(999.9 miles) before it rolls over to zero. The odome-
ter display does not have a decimal point and will
not show values less than a full unit (kilometer or
mile), the trip odometer display does have a decimal
point and will show tenths of a unit (kilometer or
mile).
The unit of measure for the odometer and trip
odometer display is not shown in the VFD. The unit
of measure for the odometer/trip odometer is selected
at the time that the instrument cluster is manufac-
tured, and cannot be changed. If the instrument clus-
ter has a kilometers-per-hour primary speedometer
scale, the odometer/trip odometer registers kilome-
ters; and, if the cluster features a miles-per-hour pri-
mary speedometer scale, the odometer/trip odometer
registers miles.
During daylight hours (exterior lamps Off) the
VFD is illuminated at full brightness for clear visibil-
ity. At night (exterior lamps are On) the instrument
cluster converts an electronic dimming level message
received from the Body Control Module (BCM) over
the Programmable Communications Interface (PCI)
data bus to a digital dimming level signal for control-
ling the lighting level of the VFD. However, a
ªParadeº mode position of the panel lamps dimmer
control ring on the control stalk of the left (lighting)
multi-function switch allows the VFD to be illumi-
8J - 24 INSTRUMENT CLUSTERWJ
MALFUNCTION INDICATOR LAMP (MIL) (Continued)