Linkage JEEP GRAND CHEROKEE 2002 WJ / 2.G Service Manual
[x] Cancel search | Manufacturer: JEEP, Model Year: 2002, Model line: GRAND CHEROKEE, Model: JEEP GRAND CHEROKEE 2002 WJ / 2.GPages: 2199, PDF Size: 76.01 MB
Page 1875 of 2199
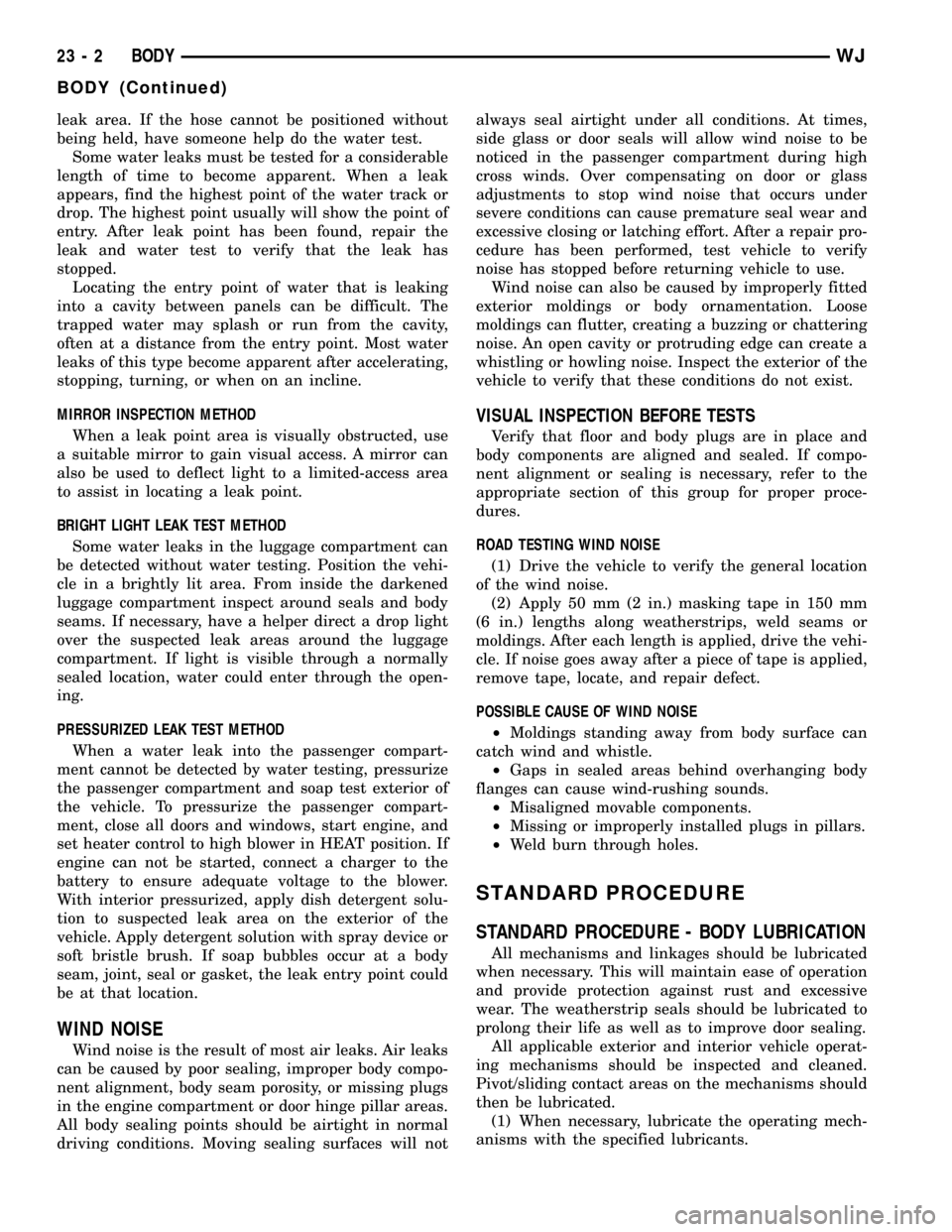
leak area. If the hose cannot be positioned without
being held, have someone help do the water test.
Some water leaks must be tested for a considerable
length of time to become apparent. When a leak
appears, find the highest point of the water track or
drop. The highest point usually will show the point of
entry. After leak point has been found, repair the
leak and water test to verify that the leak has
stopped.
Locating the entry point of water that is leaking
into a cavity between panels can be difficult. The
trapped water may splash or run from the cavity,
often at a distance from the entry point. Most water
leaks of this type become apparent after accelerating,
stopping, turning, or when on an incline.
MIRROR INSPECTION METHOD
When a leak point area is visually obstructed, use
a suitable mirror to gain visual access. A mirror can
also be used to deflect light to a limited-access area
to assist in locating a leak point.
BRIGHT LIGHT LEAK TEST METHOD
Some water leaks in the luggage compartment can
be detected without water testing. Position the vehi-
cle in a brightly lit area. From inside the darkened
luggage compartment inspect around seals and body
seams. If necessary, have a helper direct a drop light
over the suspected leak areas around the luggage
compartment. If light is visible through a normally
sealed location, water could enter through the open-
ing.
PRESSURIZED LEAK TEST METHOD
When a water leak into the passenger compart-
ment cannot be detected by water testing, pressurize
the passenger compartment and soap test exterior of
the vehicle. To pressurize the passenger compart-
ment, close all doors and windows, start engine, and
set heater control to high blower in HEAT position. If
engine can not be started, connect a charger to the
battery to ensure adequate voltage to the blower.
With interior pressurized, apply dish detergent solu-
tion to suspected leak area on the exterior of the
vehicle. Apply detergent solution with spray device or
soft bristle brush. If soap bubbles occur at a body
seam, joint, seal or gasket, the leak entry point could
be at that location.
WIND NOISE
Wind noise is the result of most air leaks. Air leaks
can be caused by poor sealing, improper body compo-
nent alignment, body seam porosity, or missing plugs
in the engine compartment or door hinge pillar areas.
All body sealing points should be airtight in normal
driving conditions. Moving sealing surfaces will notalways seal airtight under all conditions. At times,
side glass or door seals will allow wind noise to be
noticed in the passenger compartment during high
cross winds. Over compensating on door or glass
adjustments to stop wind noise that occurs under
severe conditions can cause premature seal wear and
excessive closing or latching effort. After a repair pro-
cedure has been performed, test vehicle to verify
noise has stopped before returning vehicle to use.
Wind noise can also be caused by improperly fitted
exterior moldings or body ornamentation. Loose
moldings can flutter, creating a buzzing or chattering
noise. An open cavity or protruding edge can create a
whistling or howling noise. Inspect the exterior of the
vehicle to verify that these conditions do not exist.
VISUAL INSPECTION BEFORE TESTS
Verify that floor and body plugs are in place and
body components are aligned and sealed. If compo-
nent alignment or sealing is necessary, refer to the
appropriate section of this group for proper proce-
dures.
ROAD TESTING WIND NOISE
(1) Drive the vehicle to verify the general location
of the wind noise.
(2) Apply 50 mm (2 in.) masking tape in 150 mm
(6 in.) lengths along weatherstrips, weld seams or
moldings. After each length is applied, drive the vehi-
cle. If noise goes away after a piece of tape is applied,
remove tape, locate, and repair defect.
POSSIBLE CAUSE OF WIND NOISE
²Moldings standing away from body surface can
catch wind and whistle.
²Gaps in sealed areas behind overhanging body
flanges can cause wind-rushing sounds.
²Misaligned movable components.
²Missing or improperly installed plugs in pillars.
²Weld burn through holes.
STANDARD PROCEDURE
STANDARD PROCEDURE - BODY LUBRICATION
All mechanisms and linkages should be lubricated
when necessary. This will maintain ease of operation
and provide protection against rust and excessive
wear. The weatherstrip seals should be lubricated to
prolong their life as well as to improve door sealing.
All applicable exterior and interior vehicle operat-
ing mechanisms should be inspected and cleaned.
Pivot/sliding contact areas on the mechanisms should
then be lubricated.
(1) When necessary, lubricate the operating mech-
anisms with the specified lubricants.
23 - 2 BODYWJ
BODY (Continued)
Page 1878 of 2199
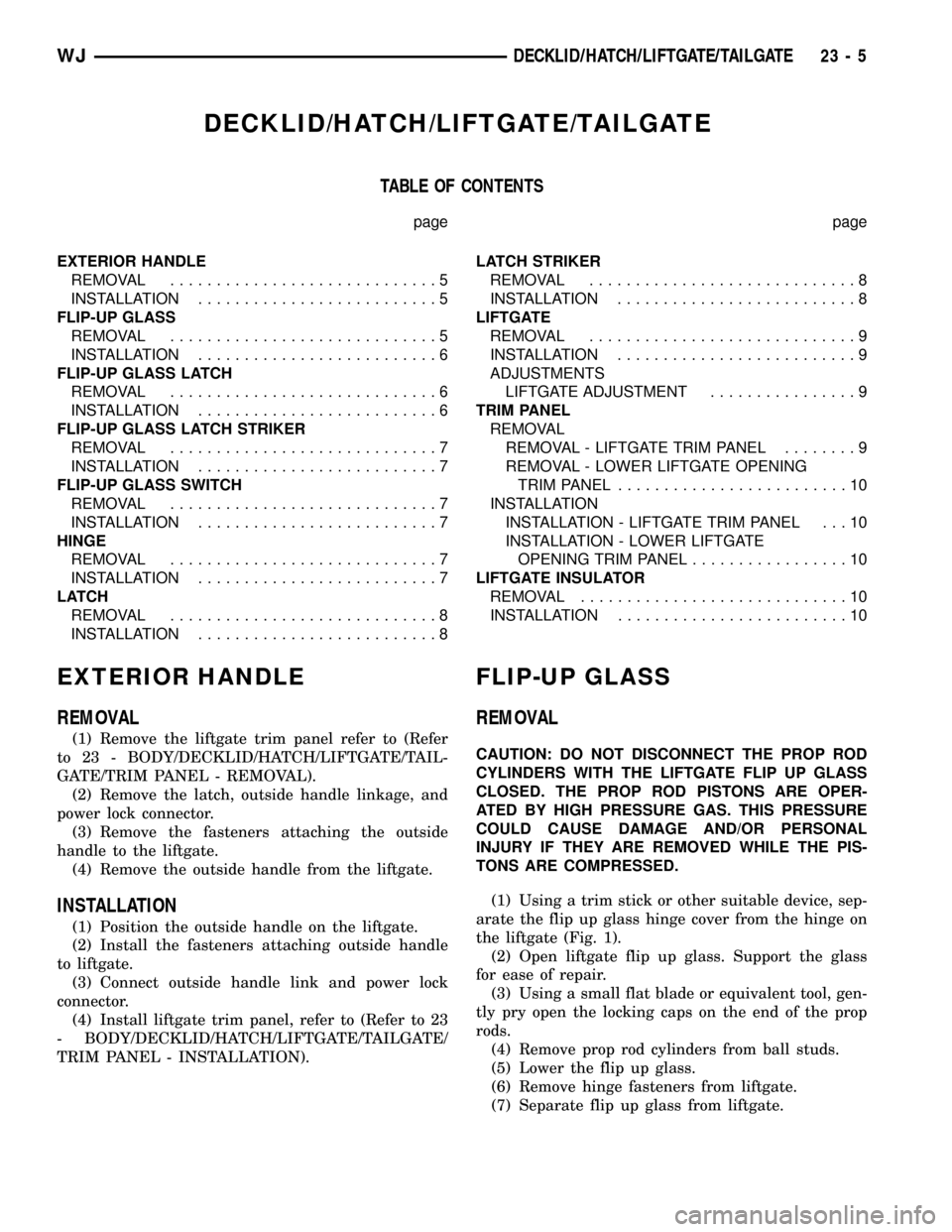
DECKLID/HATCH/LIFTGATE/TAILGATE
TABLE OF CONTENTS
page page
EXTERIOR HANDLE
REMOVAL.............................5
INSTALLATION..........................5
FLIP-UP GLASS
REMOVAL.............................5
INSTALLATION..........................6
FLIP-UP GLASS LATCH
REMOVAL.............................6
INSTALLATION..........................6
FLIP-UP GLASS LATCH STRIKER
REMOVAL.............................7
INSTALLATION..........................7
FLIP-UP GLASS SWITCH
REMOVAL.............................7
INSTALLATION..........................7
HINGE
REMOVAL.............................7
INSTALLATION..........................7
LATCH
REMOVAL.............................8
INSTALLATION..........................8LATCH STRIKER
REMOVAL.............................8
INSTALLATION..........................8
LIFTGATE
REMOVAL.............................9
INSTALLATION..........................9
ADJUSTMENTS
LIFTGATE ADJUSTMENT................9
TRIM PANEL
REMOVAL
REMOVAL - LIFTGATE TRIM PANEL........9
REMOVAL - LOWER LIFTGATE OPENING
TRIM PANEL.........................10
INSTALLATION
INSTALLATION - LIFTGATE TRIM PANEL . . . 10
INSTALLATION - LOWER LIFTGATE
OPENING TRIM PANEL.................10
LIFTGATE INSULATOR
REMOVAL.............................10
INSTALLATION.........................10
EXTERIOR HANDLE
REMOVAL
(1) Remove the liftgate trim panel refer to (Refer
to 23 - BODY/DECKLID/HATCH/LIFTGATE/TAIL-
GATE/TRIM PANEL - REMOVAL).
(2) Remove the latch, outside handle linkage, and
power lock connector.
(3) Remove the fasteners attaching the outside
handle to the liftgate.
(4) Remove the outside handle from the liftgate.
INSTALLATION
(1) Position the outside handle on the liftgate.
(2) Install the fasteners attaching outside handle
to liftgate.
(3) Connect outside handle link and power lock
connector.
(4) Install liftgate trim panel, refer to (Refer to 23
- BODY/DECKLID/HATCH/LIFTGATE/TAILGATE/
TRIM PANEL - INSTALLATION).
FLIP-UP GLASS
REMOVAL
CAUTION: DO NOT DISCONNECT THE PROP ROD
CYLINDERS WITH THE LIFTGATE FLIP UP GLASS
CLOSED. THE PROP ROD PISTONS ARE OPER-
ATED BY HIGH PRESSURE GAS. THIS PRESSURE
COULD CAUSE DAMAGE AND/OR PERSONAL
INJURY IF THEY ARE REMOVED WHILE THE PIS-
TONS ARE COMPRESSED.
(1) Using a trim stick or other suitable device, sep-
arate the flip up glass hinge cover from the hinge on
the liftgate (Fig. 1).
(2) Open liftgate flip up glass. Support the glass
for ease of repair.
(3) Using a small flat blade or equivalent tool, gen-
tly pry open the locking caps on the end of the prop
rods.
(4) Remove prop rod cylinders from ball studs.
(5) Lower the flip up glass.
(6) Remove hinge fasteners from liftgate.
(7) Separate flip up glass from liftgate.
WJDECKLID/HATCH/LIFTGATE/TAILGATE 23 - 5
Page 1890 of 2199
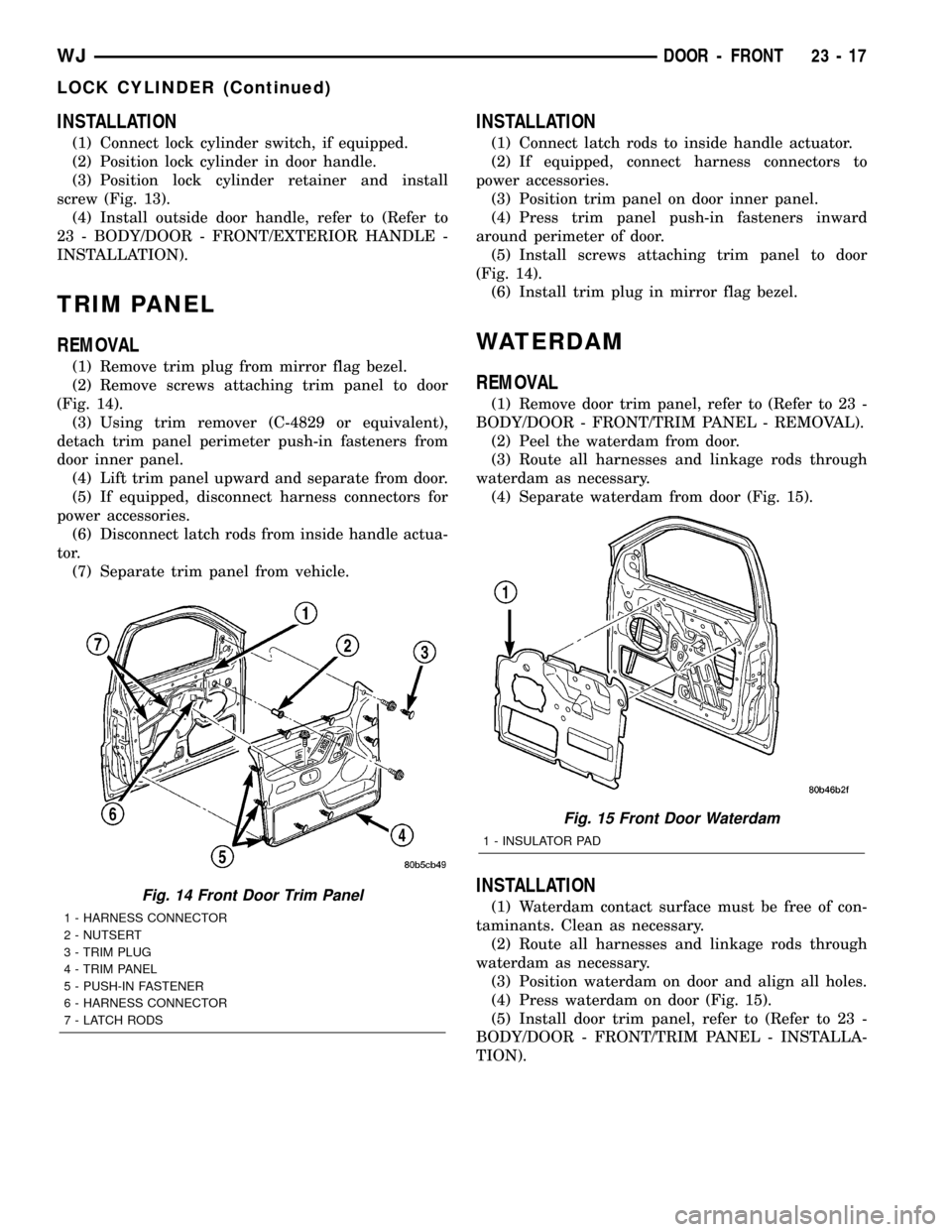
INSTALLATION
(1) Connect lock cylinder switch, if equipped.
(2) Position lock cylinder in door handle.
(3) Position lock cylinder retainer and install
screw (Fig. 13).
(4) Install outside door handle, refer to (Refer to
23 - BODY/DOOR - FRONT/EXTERIOR HANDLE -
INSTALLATION).
TRIM PANEL
REMOVAL
(1) Remove trim plug from mirror flag bezel.
(2) Remove screws attaching trim panel to door
(Fig. 14).
(3) Using trim remover (C-4829 or equivalent),
detach trim panel perimeter push-in fasteners from
door inner panel.
(4) Lift trim panel upward and separate from door.
(5) If equipped, disconnect harness connectors for
power accessories.
(6) Disconnect latch rods from inside handle actua-
tor.
(7) Separate trim panel from vehicle.
INSTALLATION
(1) Connect latch rods to inside handle actuator.
(2) If equipped, connect harness connectors to
power accessories.
(3) Position trim panel on door inner panel.
(4) Press trim panel push-in fasteners inward
around perimeter of door.
(5) Install screws attaching trim panel to door
(Fig. 14).
(6) Install trim plug in mirror flag bezel.
WATERDAM
REMOVAL
(1) Remove door trim panel, refer to (Refer to 23 -
BODY/DOOR - FRONT/TRIM PANEL - REMOVAL).
(2) Peel the waterdam from door.
(3) Route all harnesses and linkage rods through
waterdam as necessary.
(4) Separate waterdam from door (Fig. 15).
INSTALLATION
(1) Waterdam contact surface must be free of con-
taminants. Clean as necessary.
(2) Route all harnesses and linkage rods through
waterdam as necessary.
(3) Position waterdam on door and align all holes.
(4) Press waterdam on door (Fig. 15).
(5) Install door trim panel, refer to (Refer to 23 -
BODY/DOOR - FRONT/TRIM PANEL - INSTALLA-
TION).Fig. 14 Front Door Trim Panel
1 - HARNESS CONNECTOR
2 - NUTSERT
3 - TRIM PLUG
4 - TRIM PANEL
5 - PUSH-IN FASTENER
6 - HARNESS CONNECTOR
7 - LATCH RODS
Fig. 15 Front Door Waterdam
1 - INSULATOR PAD
WJDOOR - FRONT 23 - 17
LOCK CYLINDER (Continued)
Page 1896 of 2199
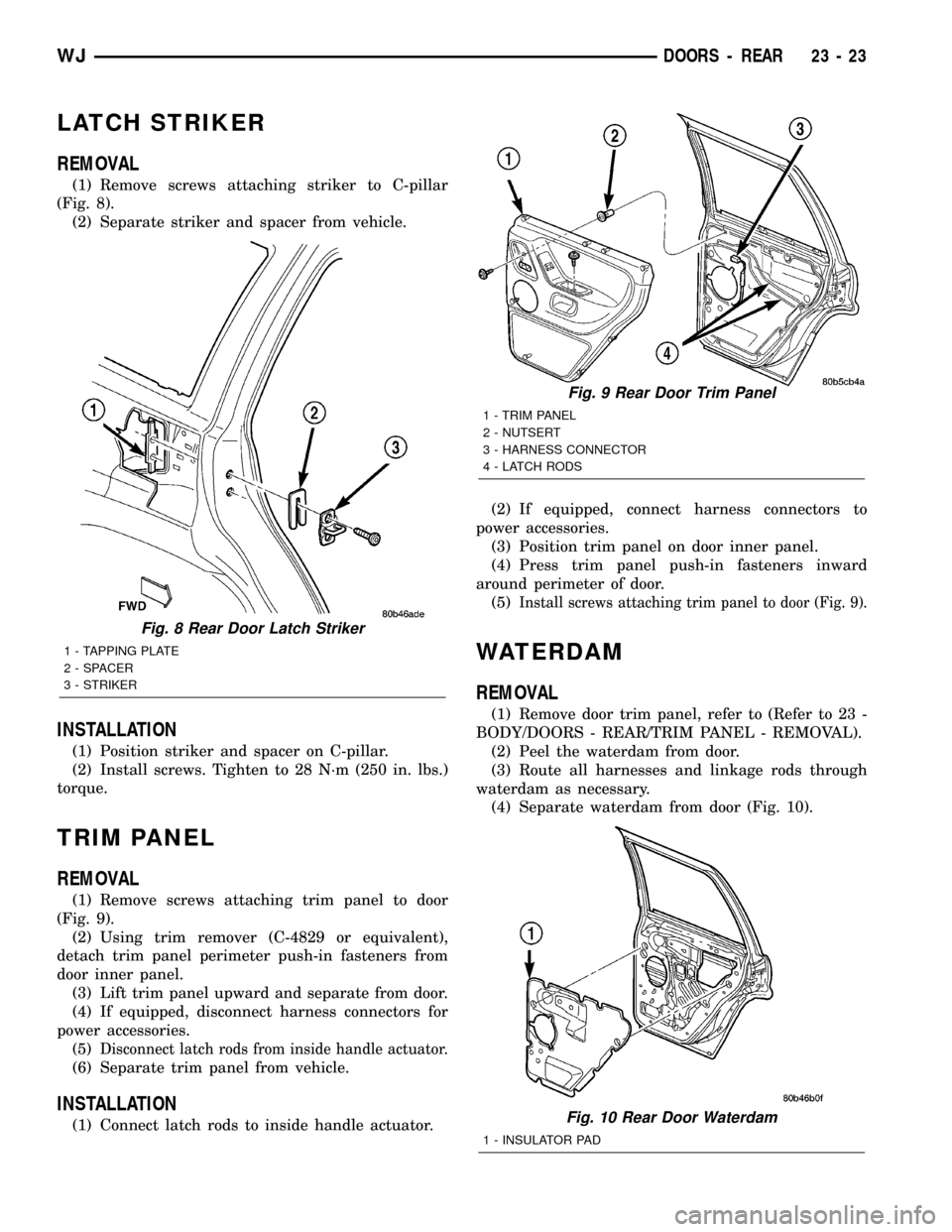
LATCH STRIKER
REMOVAL
(1) Remove screws attaching striker to C-pillar
(Fig. 8).
(2) Separate striker and spacer from vehicle.
INSTALLATION
(1) Position striker and spacer on C-pillar.
(2) Install screws. Tighten to 28 N´m (250 in. lbs.)
torque.
TRIM PANEL
REMOVAL
(1) Remove screws attaching trim panel to door
(Fig. 9).
(2) Using trim remover (C-4829 or equivalent),
detach trim panel perimeter push-in fasteners from
door inner panel.
(3) Lift trim panel upward and separate from door.
(4) If equipped, disconnect harness connectors for
power accessories.
(5)
Disconnect latch rods from inside handle actuator.
(6) Separate trim panel from vehicle.
INSTALLATION
(1) Connect latch rods to inside handle actuator.(2) If equipped, connect harness connectors to
power accessories.
(3) Position trim panel on door inner panel.
(4) Press trim panel push-in fasteners inward
around perimeter of door.
(5)
Install screws attaching trim panel to door (Fig. 9).
WATERDAM
REMOVAL
(1) Remove door trim panel, refer to (Refer to 23 -
BODY/DOORS - REAR/TRIM PANEL - REMOVAL).
(2) Peel the waterdam from door.
(3) Route all harnesses and linkage rods through
waterdam as necessary.
(4) Separate waterdam from door (Fig. 10).
Fig. 8 Rear Door Latch Striker
1 - TAPPING PLATE
2 - SPACER
3 - STRIKER
Fig. 9 Rear Door Trim Panel
1 - TRIM PANEL
2 - NUTSERT
3 - HARNESS CONNECTOR
4 - LATCH RODS
Fig. 10 Rear Door Waterdam
1 - INSULATOR PAD
WJDOORS - REAR 23 - 23
Page 1897 of 2199
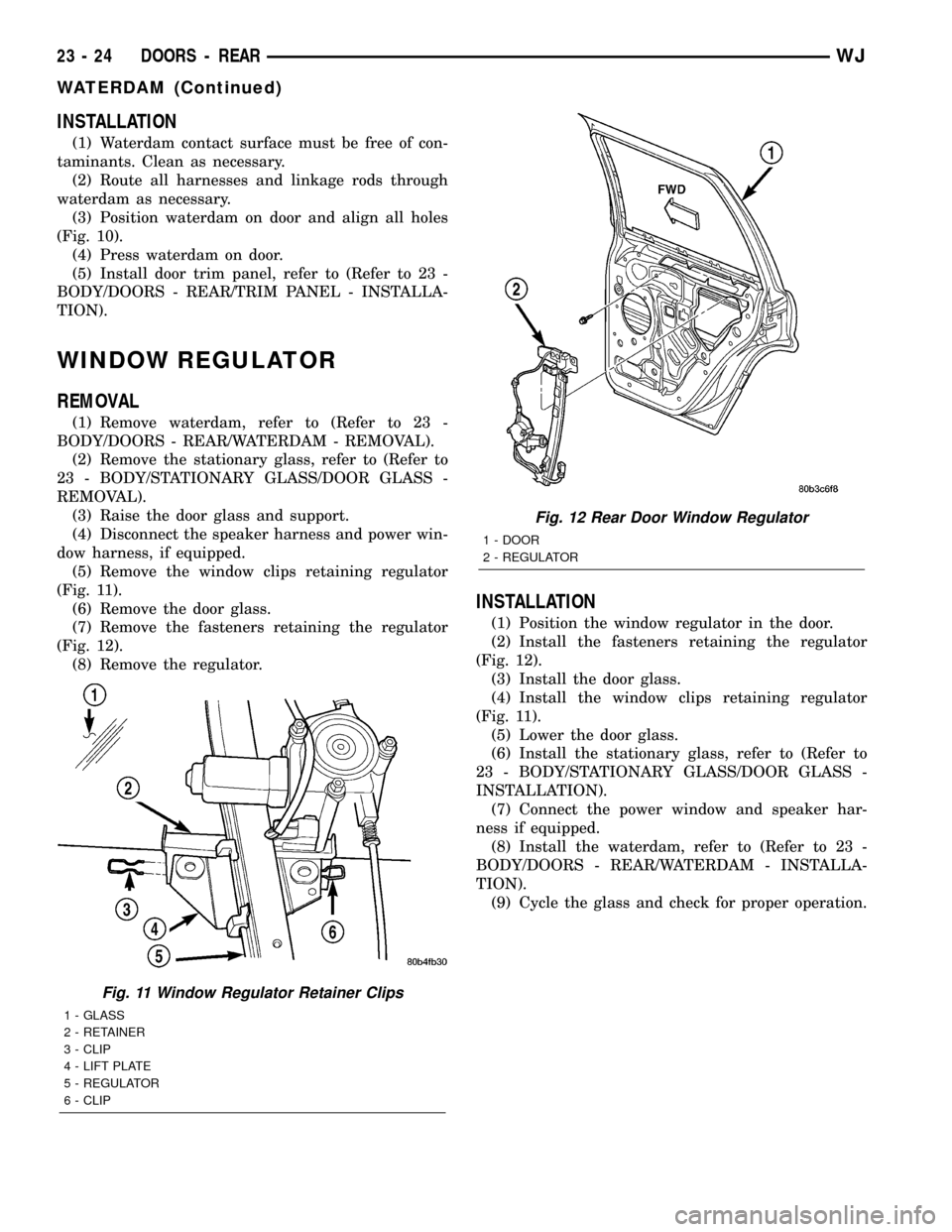
INSTALLATION
(1) Waterdam contact surface must be free of con-
taminants. Clean as necessary.
(2) Route all harnesses and linkage rods through
waterdam as necessary.
(3) Position waterdam on door and align all holes
(Fig. 10).
(4) Press waterdam on door.
(5) Install door trim panel, refer to (Refer to 23 -
BODY/DOORS - REAR/TRIM PANEL - INSTALLA-
TION).
WINDOW REGULATOR
REMOVAL
(1) Remove waterdam, refer to (Refer to 23 -
BODY/DOORS - REAR/WATERDAM - REMOVAL).
(2) Remove the stationary glass, refer to (Refer to
23 - BODY/STATIONARY GLASS/DOOR GLASS -
REMOVAL).
(3) Raise the door glass and support.
(4) Disconnect the speaker harness and power win-
dow harness, if equipped.
(5) Remove the window clips retaining regulator
(Fig. 11).
(6) Remove the door glass.
(7) Remove the fasteners retaining the regulator
(Fig. 12).
(8) Remove the regulator.
INSTALLATION
(1) Position the window regulator in the door.
(2) Install the fasteners retaining the regulator
(Fig. 12).
(3) Install the door glass.
(4) Install the window clips retaining regulator
(Fig. 11).
(5) Lower the door glass.
(6) Install the stationary glass, refer to (Refer to
23 - BODY/STATIONARY GLASS/DOOR GLASS -
INSTALLATION).
(7) Connect the power window and speaker har-
ness if equipped.
(8) Install the waterdam, refer to (Refer to 23 -
BODY/DOORS - REAR/WATERDAM - INSTALLA-
TION).
(9) Cycle the glass and check for proper operation.
Fig. 11 Window Regulator Retainer Clips
1 - GLASS
2 - RETAINER
3 - CLIP
4 - LIFT PLATE
5 - REGULATOR
6 - CLIP
Fig. 12 Rear Door Window Regulator
1 - DOOR
2 - REGULATOR
23 - 24 DOORS - REARWJ
WATERDAM (Continued)
Page 1949 of 2199
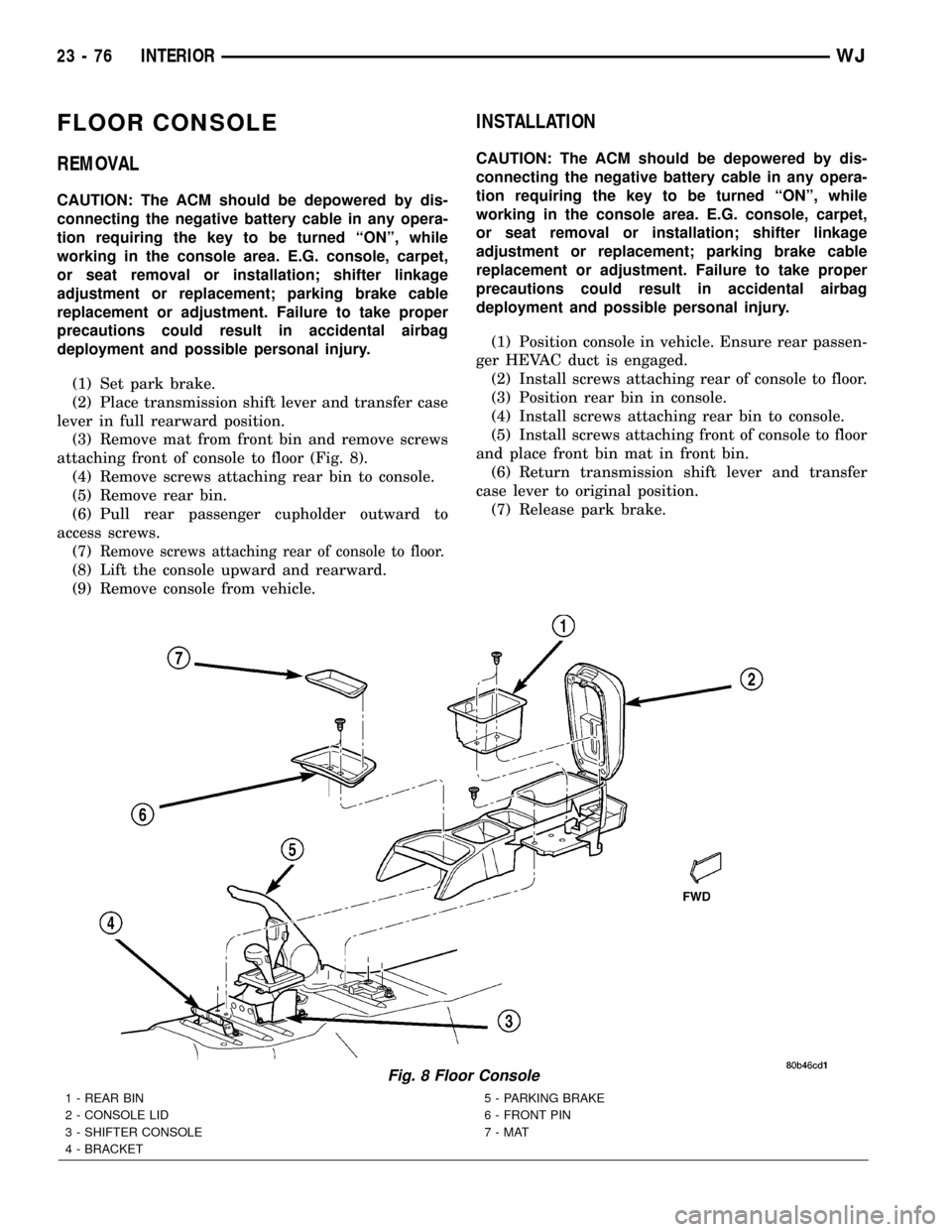
FLOOR CONSOLE
REMOVAL
CAUTION: The ACM should be depowered by dis-
connecting the negative battery cable in any opera-
tion requiring the key to be turned ªONº, while
working in the console area. E.G. console, carpet,
or seat removal or installation; shifter linkage
adjustment or replacement; parking brake cable
replacement or adjustment. Failure to take proper
precautions could result in accidental airbag
deployment and possible personal injury.
(1) Set park brake.
(2) Place transmission shift lever and transfer case
lever in full rearward position.
(3) Remove mat from front bin and remove screws
attaching front of console to floor (Fig. 8).
(4) Remove screws attaching rear bin to console.
(5) Remove rear bin.
(6) Pull rear passenger cupholder outward to
access screws.
(7)
Remove screws attaching rear of console to floor.
(8) Lift the console upward and rearward.
(9) Remove console from vehicle.
INSTALLATION
CAUTION: The ACM should be depowered by dis-
connecting the negative battery cable in any opera-
tion requiring the key to be turned ªONº, while
working in the console area. E.G. console, carpet,
or seat removal or installation; shifter linkage
adjustment or replacement; parking brake cable
replacement or adjustment. Failure to take proper
precautions could result in accidental airbag
deployment and possible personal injury.
(1) Position console in vehicle. Ensure rear passen-
ger HEVAC duct is engaged.
(2) Install screws attaching rear of console to floor.
(3) Position rear bin in console.
(4) Install screws attaching rear bin to console.
(5) Install screws attaching front of console to floor
and place front bin mat in front bin.
(6) Return transmission shift lever and transfer
case lever to original position.
(7) Release park brake.
Fig. 8 Floor Console
1 - REAR BIN
2 - CONSOLE LID
3 - SHIFTER CONSOLE
4 - BRACKET5 - PARKING BRAKE
6 - FRONT PIN
7-MAT
23 - 76 INTERIORWJ
Page 2108 of 2199
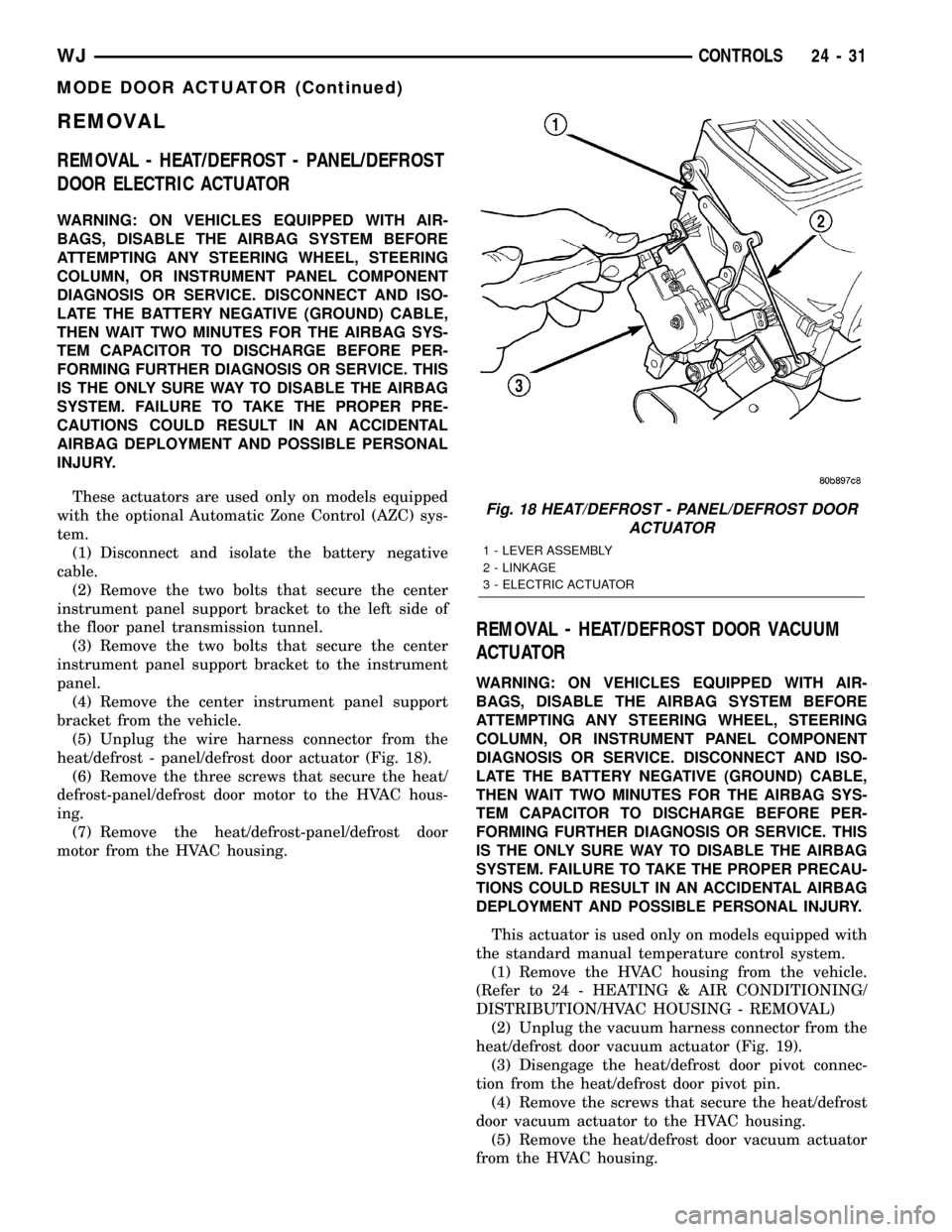
REMOVAL
REMOVAL - HEAT/DEFROST - PANEL/DEFROST
DOOR ELECTRIC ACTUATOR
WARNING: ON VEHICLES EQUIPPED WITH AIR-
BAGS, DISABLE THE AIRBAG SYSTEM BEFORE
ATTEMPTING ANY STEERING WHEEL, STEERING
COLUMN, OR INSTRUMENT PANEL COMPONENT
DIAGNOSIS OR SERVICE. DISCONNECT AND ISO-
LATE THE BATTERY NEGATIVE (GROUND) CABLE,
THEN WAIT TWO MINUTES FOR THE AIRBAG SYS-
TEM CAPACITOR TO DISCHARGE BEFORE PER-
FORMING FURTHER DIAGNOSIS OR SERVICE. THIS
IS THE ONLY SURE WAY TO DISABLE THE AIRBAG
SYSTEM. FAILURE TO TAKE THE PROPER PRE-
CAUTIONS COULD RESULT IN AN ACCIDENTAL
AIRBAG DEPLOYMENT AND POSSIBLE PERSONAL
INJURY.
These actuators are used only on models equipped
with the optional Automatic Zone Control (AZC) sys-
tem.
(1) Disconnect and isolate the battery negative
cable.
(2) Remove the two bolts that secure the center
instrument panel support bracket to the left side of
the floor panel transmission tunnel.
(3) Remove the two bolts that secure the center
instrument panel support bracket to the instrument
panel.
(4) Remove the center instrument panel support
bracket from the vehicle.
(5) Unplug the wire harness connector from the
heat/defrost - panel/defrost door actuator (Fig. 18).
(6) Remove the three screws that secure the heat/
defrost-panel/defrost door motor to the HVAC hous-
ing.
(7) Remove the heat/defrost-panel/defrost door
motor from the HVAC housing.
REMOVAL - HEAT/DEFROST DOOR VACUUM
ACTUATOR
WARNING: ON VEHICLES EQUIPPED WITH AIR-
BAGS, DISABLE THE AIRBAG SYSTEM BEFORE
ATTEMPTING ANY STEERING WHEEL, STEERING
COLUMN, OR INSTRUMENT PANEL COMPONENT
DIAGNOSIS OR SERVICE. DISCONNECT AND ISO-
LATE THE BATTERY NEGATIVE (GROUND) CABLE,
THEN WAIT TWO MINUTES FOR THE AIRBAG SYS-
TEM CAPACITOR TO DISCHARGE BEFORE PER-
FORMING FURTHER DIAGNOSIS OR SERVICE. THIS
IS THE ONLY SURE WAY TO DISABLE THE AIRBAG
SYSTEM. FAILURE TO TAKE THE PROPER PRECAU-
TIONS COULD RESULT IN AN ACCIDENTAL AIRBAG
DEPLOYMENT AND POSSIBLE PERSONAL INJURY.
This actuator is used only on models equipped with
the standard manual temperature control system.
(1) Remove the HVAC housing from the vehicle.
(Refer to 24 - HEATING & AIR CONDITIONING/
DISTRIBUTION/HVAC HOUSING - REMOVAL)
(2) Unplug the vacuum harness connector from the
heat/defrost door vacuum actuator (Fig. 19).
(3) Disengage the heat/defrost door pivot connec-
tion from the heat/defrost door pivot pin.
(4) Remove the screws that secure the heat/defrost
door vacuum actuator to the HVAC housing.
(5) Remove the heat/defrost door vacuum actuator
from the HVAC housing.
Fig. 18 HEAT/DEFROST - PANEL/DEFROST DOOR
ACTUATOR
1 - LEVER ASSEMBLY
2 - LINKAGE
3 - ELECTRIC ACTUATOR
WJCONTROLS 24 - 31
MODE DOOR ACTUATOR (Continued)
Page 2109 of 2199
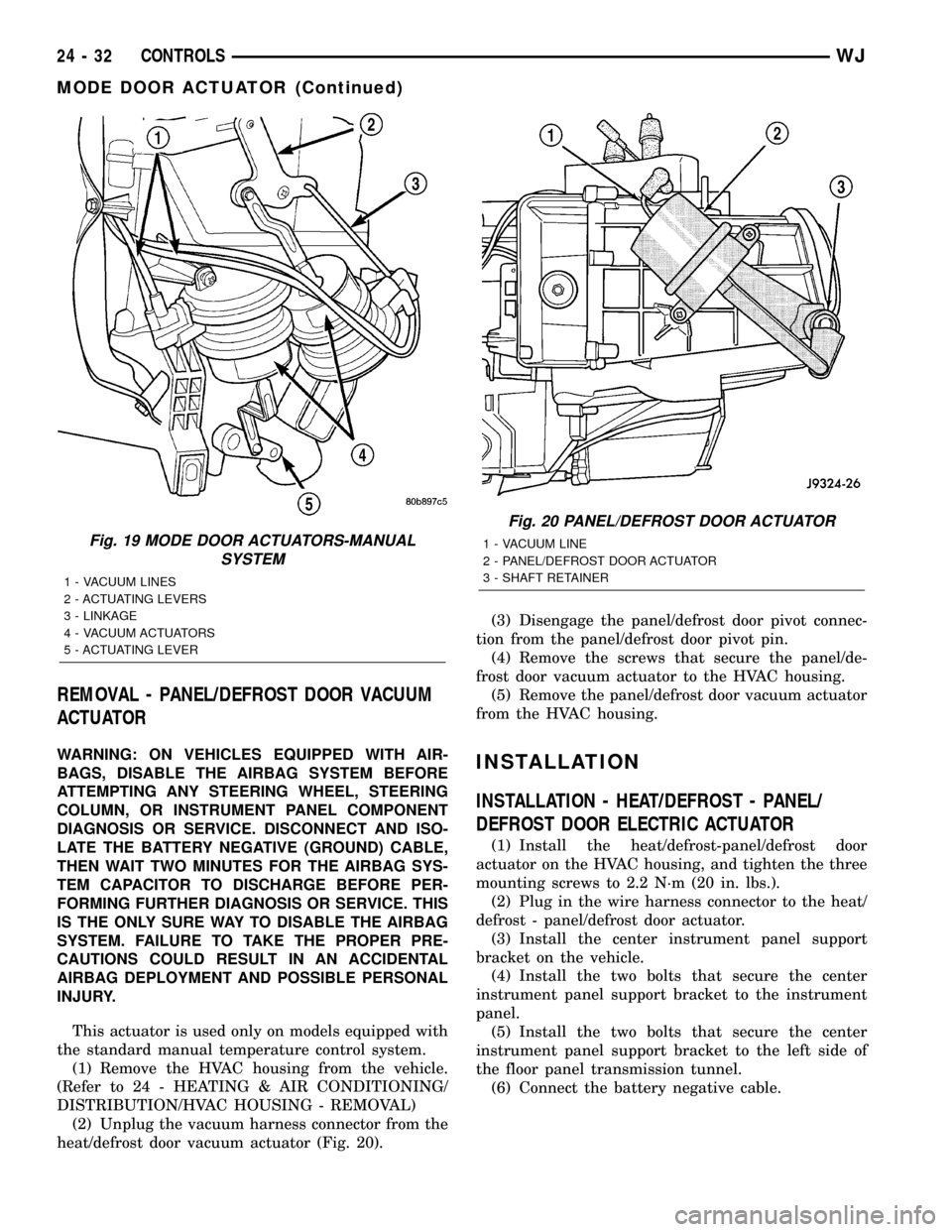
REMOVAL - PANEL/DEFROST DOOR VACUUM
ACTUATOR
WARNING: ON VEHICLES EQUIPPED WITH AIR-
BAGS, DISABLE THE AIRBAG SYSTEM BEFORE
ATTEMPTING ANY STEERING WHEEL, STEERING
COLUMN, OR INSTRUMENT PANEL COMPONENT
DIAGNOSIS OR SERVICE. DISCONNECT AND ISO-
LATE THE BATTERY NEGATIVE (GROUND) CABLE,
THEN WAIT TWO MINUTES FOR THE AIRBAG SYS-
TEM CAPACITOR TO DISCHARGE BEFORE PER-
FORMING FURTHER DIAGNOSIS OR SERVICE. THIS
IS THE ONLY SURE WAY TO DISABLE THE AIRBAG
SYSTEM. FAILURE TO TAKE THE PROPER PRE-
CAUTIONS COULD RESULT IN AN ACCIDENTAL
AIRBAG DEPLOYMENT AND POSSIBLE PERSONAL
INJURY.
This actuator is used only on models equipped with
the standard manual temperature control system.
(1) Remove the HVAC housing from the vehicle.
(Refer to 24 - HEATING & AIR CONDITIONING/
DISTRIBUTION/HVAC HOUSING - REMOVAL)
(2) Unplug the vacuum harness connector from the
heat/defrost door vacuum actuator (Fig. 20).(3) Disengage the panel/defrost door pivot connec-
tion from the panel/defrost door pivot pin.
(4) Remove the screws that secure the panel/de-
frost door vacuum actuator to the HVAC housing.
(5) Remove the panel/defrost door vacuum actuator
from the HVAC housing.INSTALLATION
INSTALLATION - HEAT/DEFROST - PANEL/
DEFROST DOOR ELECTRIC ACTUATOR
(1) Install the heat/defrost-panel/defrost door
actuator on the HVAC housing, and tighten the three
mounting screws to 2.2 N´m (20 in. lbs.).
(2) Plug in the wire harness connector to the heat/
defrost - panel/defrost door actuator.
(3) Install the center instrument panel support
bracket on the vehicle.
(4) Install the two bolts that secure the center
instrument panel support bracket to the instrument
panel.
(5) Install the two bolts that secure the center
instrument panel support bracket to the left side of
the floor panel transmission tunnel.
(6) Connect the battery negative cable.
Fig. 19 MODE DOOR ACTUATORS-MANUAL
SYSTEM
1 - VACUUM LINES
2 - ACTUATING LEVERS
3 - LINKAGE
4 - VACUUM ACTUATORS
5 - ACTUATING LEVER
Fig. 20 PANEL/DEFROST DOOR ACTUATOR
1 - VACUUM LINE
2 - PANEL/DEFROST DOOR ACTUATOR
3 - SHAFT RETAINER
24 - 32 CONTROLSWJ
MODE DOOR ACTUATOR (Continued)
Page 2116 of 2199
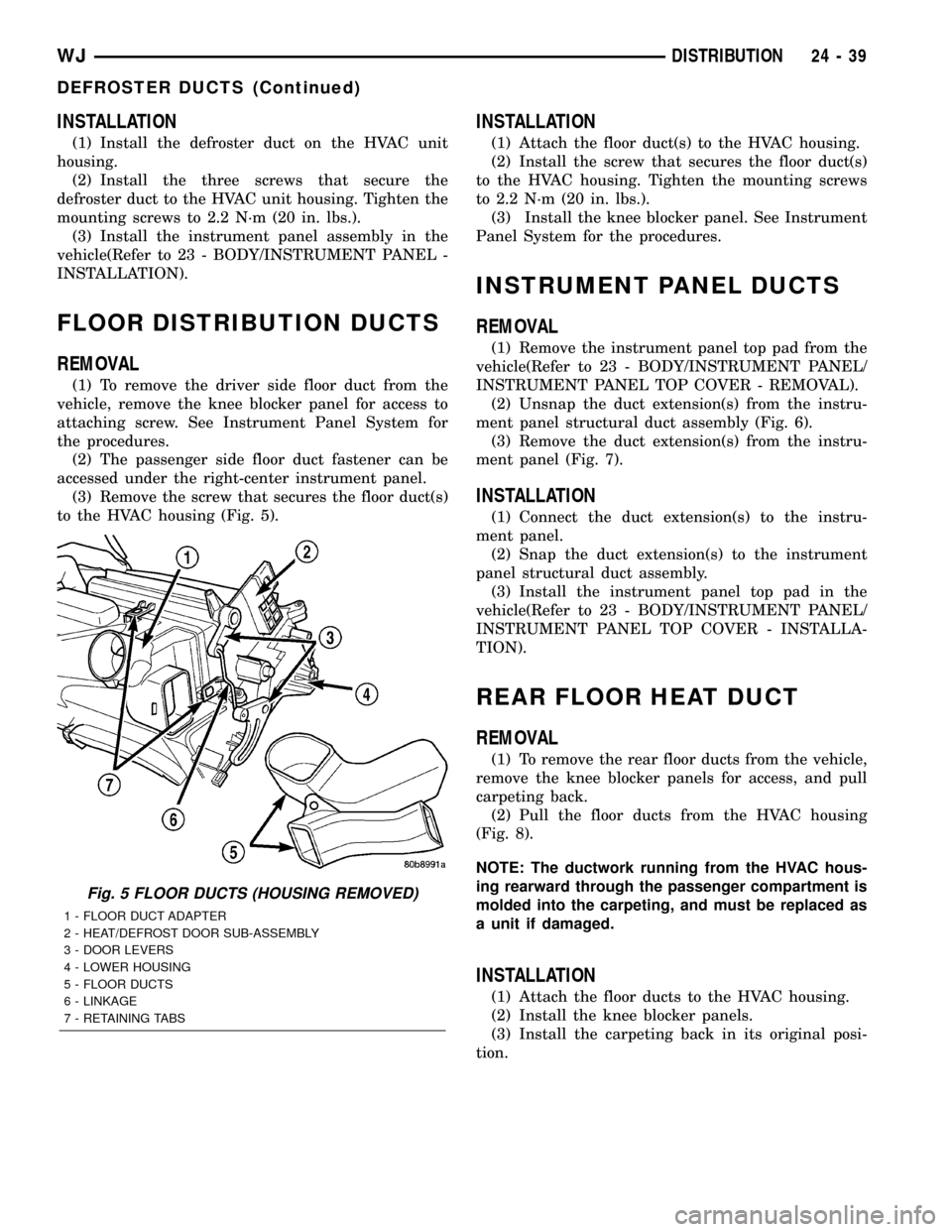
INSTALLATION
(1) Install the defroster duct on the HVAC unit
housing.
(2) Install the three screws that secure the
defroster duct to the HVAC unit housing. Tighten the
mounting screws to 2.2 N´m (20 in. lbs.).
(3) Install the instrument panel assembly in the
vehicle(Refer to 23 - BODY/INSTRUMENT PANEL -
INSTALLATION).
FLOOR DISTRIBUTION DUCTS
REMOVAL
(1) To remove the driver side floor duct from the
vehicle, remove the knee blocker panel for access to
attaching screw. See Instrument Panel System for
the procedures.
(2) The passenger side floor duct fastener can be
accessed under the right-center instrument panel.
(3) Remove the screw that secures the floor duct(s)
to the HVAC housing (Fig. 5).
INSTALLATION
(1) Attach the floor duct(s) to the HVAC housing.
(2) Install the screw that secures the floor duct(s)
to the HVAC housing. Tighten the mounting screws
to 2.2 N´m (20 in. lbs.).
(3) Install the knee blocker panel. See Instrument
Panel System for the procedures.
INSTRUMENT PANEL DUCTS
REMOVAL
(1) Remove the instrument panel top pad from the
vehicle(Refer to 23 - BODY/INSTRUMENT PANEL/
INSTRUMENT PANEL TOP COVER - REMOVAL).
(2) Unsnap the duct extension(s) from the instru-
ment panel structural duct assembly (Fig. 6).
(3) Remove the duct extension(s) from the instru-
ment panel (Fig. 7).
INSTALLATION
(1) Connect the duct extension(s) to the instru-
ment panel.
(2) Snap the duct extension(s) to the instrument
panel structural duct assembly.
(3) Install the instrument panel top pad in the
vehicle(Refer to 23 - BODY/INSTRUMENT PANEL/
INSTRUMENT PANEL TOP COVER - INSTALLA-
TION).
REAR FLOOR HEAT DUCT
REMOVAL
(1) To remove the rear floor ducts from the vehicle,
remove the knee blocker panels for access, and pull
carpeting back.
(2) Pull the floor ducts from the HVAC housing
(Fig. 8).
NOTE: The ductwork running from the HVAC hous-
ing rearward through the passenger compartment is
molded into the carpeting, and must be replaced as
a unit if damaged.
INSTALLATION
(1) Attach the floor ducts to the HVAC housing.
(2) Install the knee blocker panels.
(3) Install the carpeting back in its original posi-
tion.
Fig. 5 FLOOR DUCTS (HOUSING REMOVED)
1 - FLOOR DUCT ADAPTER
2 - HEAT/DEFROST DOOR SUB-ASSEMBLY
3 - DOOR LEVERS
4 - LOWER HOUSING
5 - FLOOR DUCTS
6 - LINKAGE
7 - RETAINING TABS
WJDISTRIBUTION 24 - 39
DEFROSTER DUCTS (Continued)
Page 2120 of 2199
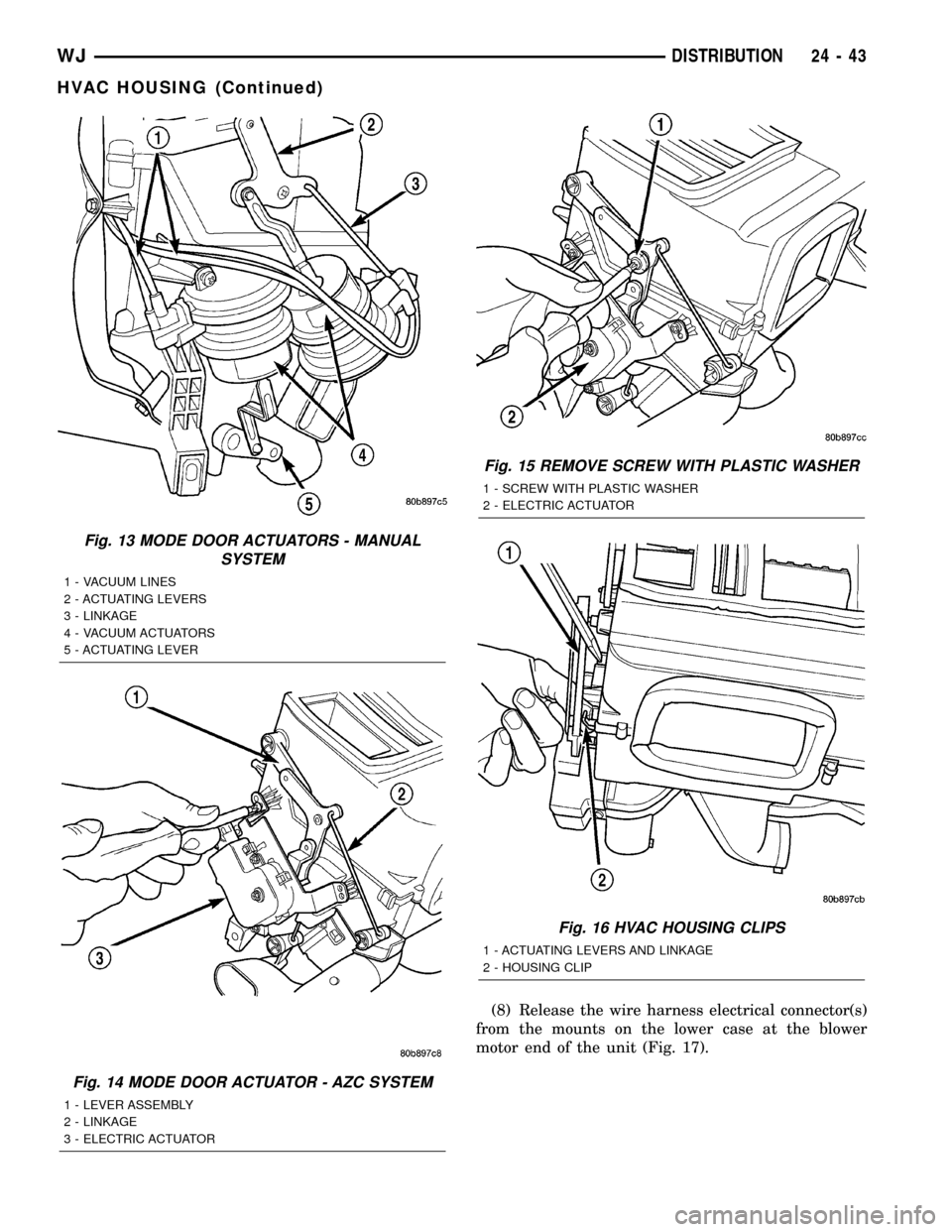
(8) Release the wire harness electrical connector(s)
from the mounts on the lower case at the blower
motor end of the unit (Fig. 17).
Fig. 13 MODE DOOR ACTUATORS - MANUAL
SYSTEM
1 - VACUUM LINES
2 - ACTUATING LEVERS
3 - LINKAGE
4 - VACUUM ACTUATORS
5 - ACTUATING LEVER
Fig. 14 MODE DOOR ACTUATOR - AZC SYSTEM
1 - LEVER ASSEMBLY
2 - LINKAGE
3 - ELECTRIC ACTUATOR
Fig. 15 REMOVE SCREW WITH PLASTIC WASHER
1 - SCREW WITH PLASTIC WASHER
2 - ELECTRIC ACTUATOR
Fig. 16 HVAC HOUSING CLIPS
1 - ACTUATING LEVERS AND LINKAGE
2 - HOUSING CLIP
WJDISTRIBUTION 24 - 43
HVAC HOUSING (Continued)