JEEP GRAND CHEROKEE 2003 WJ / 2.G Workshop Manual
Manufacturer: JEEP, Model Year: 2003, Model line: GRAND CHEROKEE, Model: JEEP GRAND CHEROKEE 2003 WJ / 2.GPages: 2199, PDF Size: 76.01 MB
Page 1821 of 2199
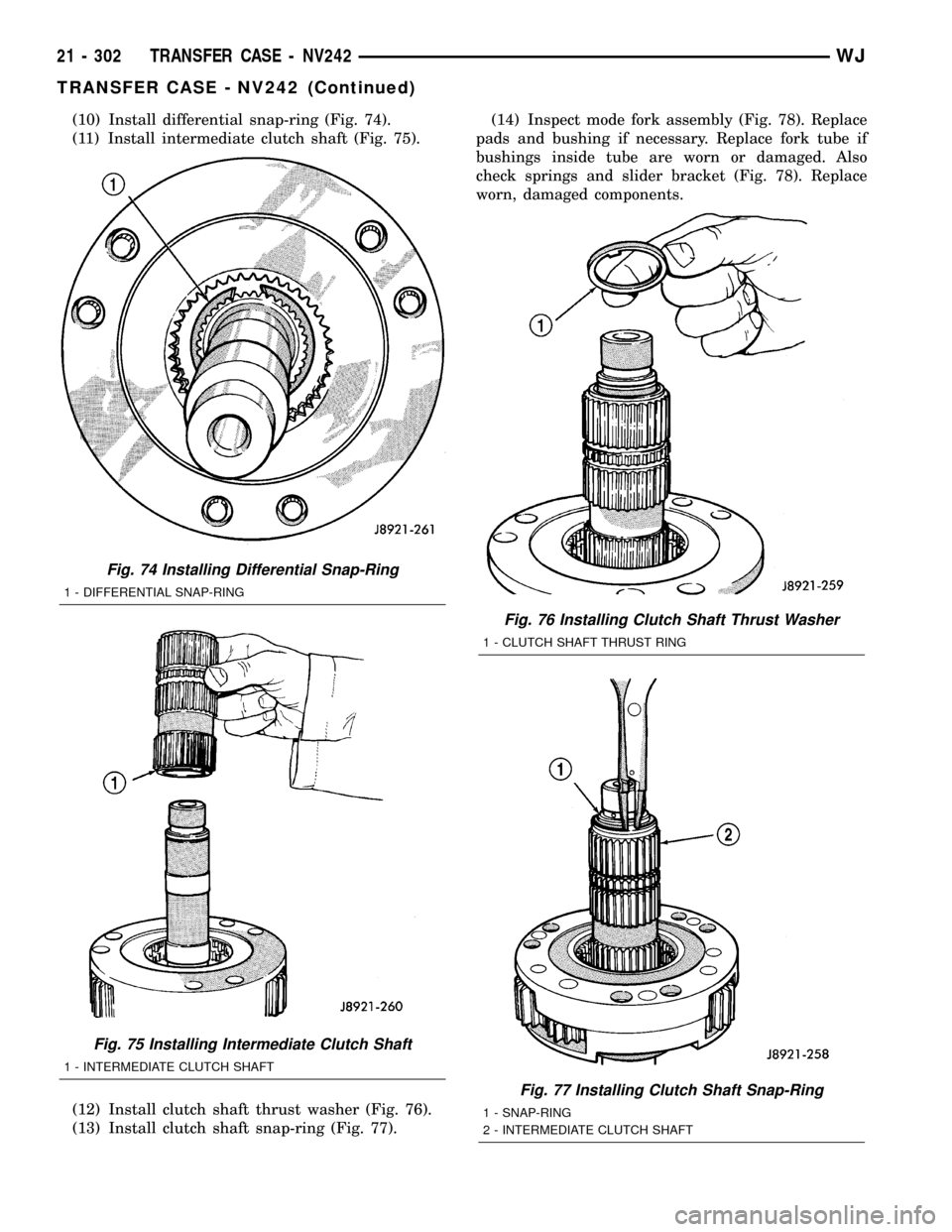
(10) Install differential snap-ring (Fig. 74).
(11) Install intermediate clutch shaft (Fig. 75).
(12) Install clutch shaft thrust washer (Fig. 76).
(13) Install clutch shaft snap-ring (Fig. 77).(14) Inspect mode fork assembly (Fig. 78). Replace
pads and bushing if necessary. Replace fork tube if
bushings inside tube are worn or damaged. Also
check springs and slider bracket (Fig. 78). Replace
worn, damaged components.
Fig. 74 Installing Differential Snap-Ring
1 - DIFFERENTIAL SNAP-RING
Fig. 75 Installing Intermediate Clutch Shaft
1 - INTERMEDIATE CLUTCH SHAFT
Fig. 76 Installing Clutch Shaft Thrust Washer
1 - CLUTCH SHAFT THRUST RING
Fig. 77 Installing Clutch Shaft Snap-Ring
1 - SNAP-RING
2 - INTERMEDIATE CLUTCH SHAFT
21 - 302 TRANSFER CASE - NV242WJ
TRANSFER CASE - NV242 (Continued)
Page 1822 of 2199
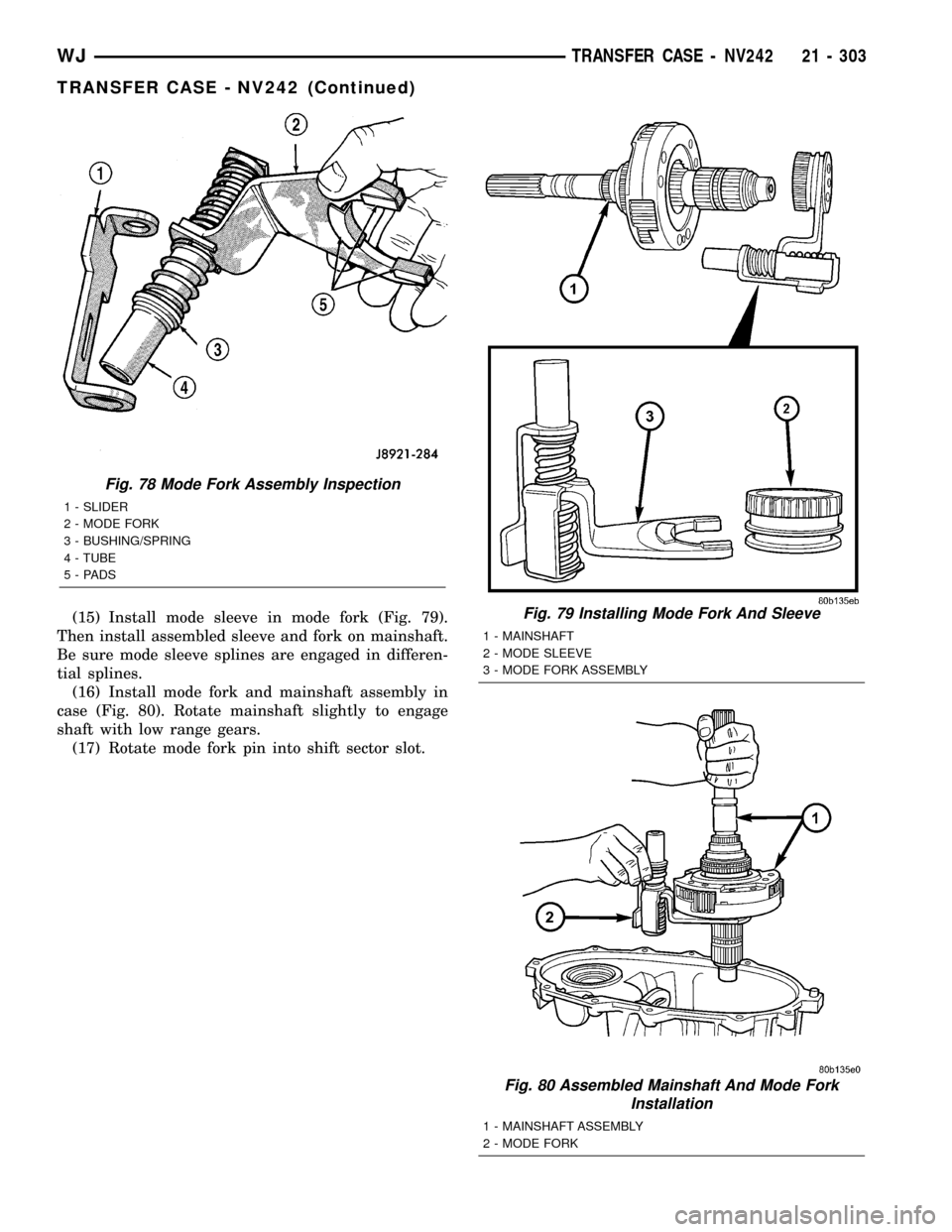
(15) Install mode sleeve in mode fork (Fig. 79).
Then install assembled sleeve and fork on mainshaft.
Be sure mode sleeve splines are engaged in differen-
tial splines.
(16) Install mode fork and mainshaft assembly in
case (Fig. 80). Rotate mainshaft slightly to engage
shaft with low range gears.
(17) Rotate mode fork pin into shift sector slot.Fig. 79 Installing Mode Fork And Sleeve
1 - MAINSHAFT
2 - MODE SLEEVE
3 - MODE FORK ASSEMBLY
Fig. 80 Assembled Mainshaft And Mode Fork
Installation
1 - MAINSHAFT ASSEMBLY
2 - MODE FORK
Fig. 78 Mode Fork Assembly Inspection
1 - SLIDER
2 - MODE FORK
3 - BUSHING/SPRING
4 - TUBE
5-PADS
WJTRANSFER CASE - NV242 21 - 303
TRANSFER CASE - NV242 (Continued)
Page 1823 of 2199
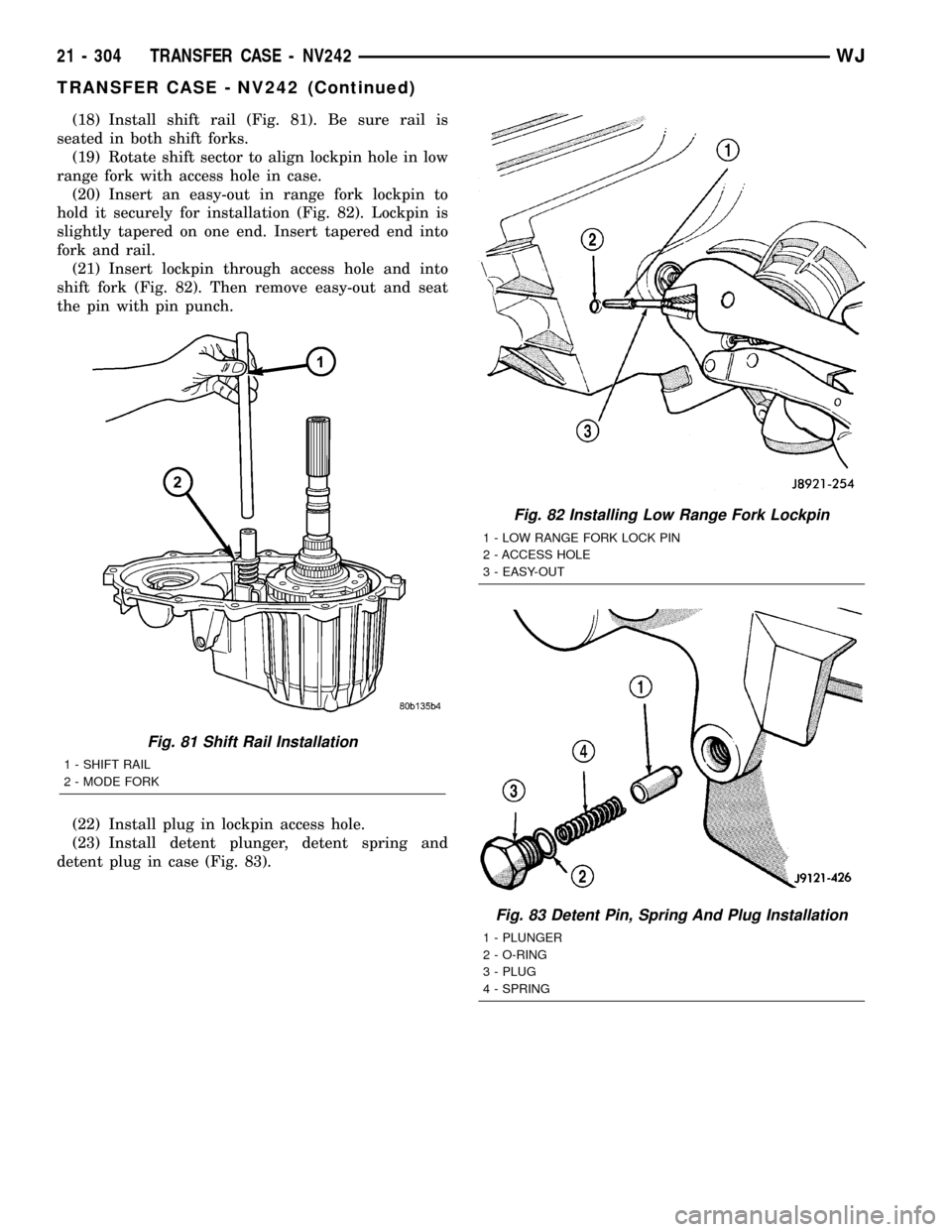
(18) Install shift rail (Fig. 81). Be sure rail is
seated in both shift forks.
(19) Rotate shift sector to align lockpin hole in low
range fork with access hole in case.
(20) Insert an easy-out in range fork lockpin to
hold it securely for installation (Fig. 82). Lockpin is
slightly tapered on one end. Insert tapered end into
fork and rail.
(21) Insert lockpin through access hole and into
shift fork (Fig. 82). Then remove easy-out and seat
the pin with pin punch.
(22) Install plug in lockpin access hole.
(23) Install detent plunger, detent spring and
detent plug in case (Fig. 83).
Fig. 81 Shift Rail Installation
1 - SHIFT RAIL
2 - MODE FORK
Fig. 82 Installing Low Range Fork Lockpin
1 - LOW RANGE FORK LOCK PIN
2 - ACCESS HOLE
3 - EASY-OUT
Fig. 83 Detent Pin, Spring And Plug Installation
1 - PLUNGER
2 - O-RING
3 - PLUG
4 - SPRING
21 - 304 TRANSFER CASE - NV242WJ
TRANSFER CASE - NV242 (Continued)
Page 1824 of 2199
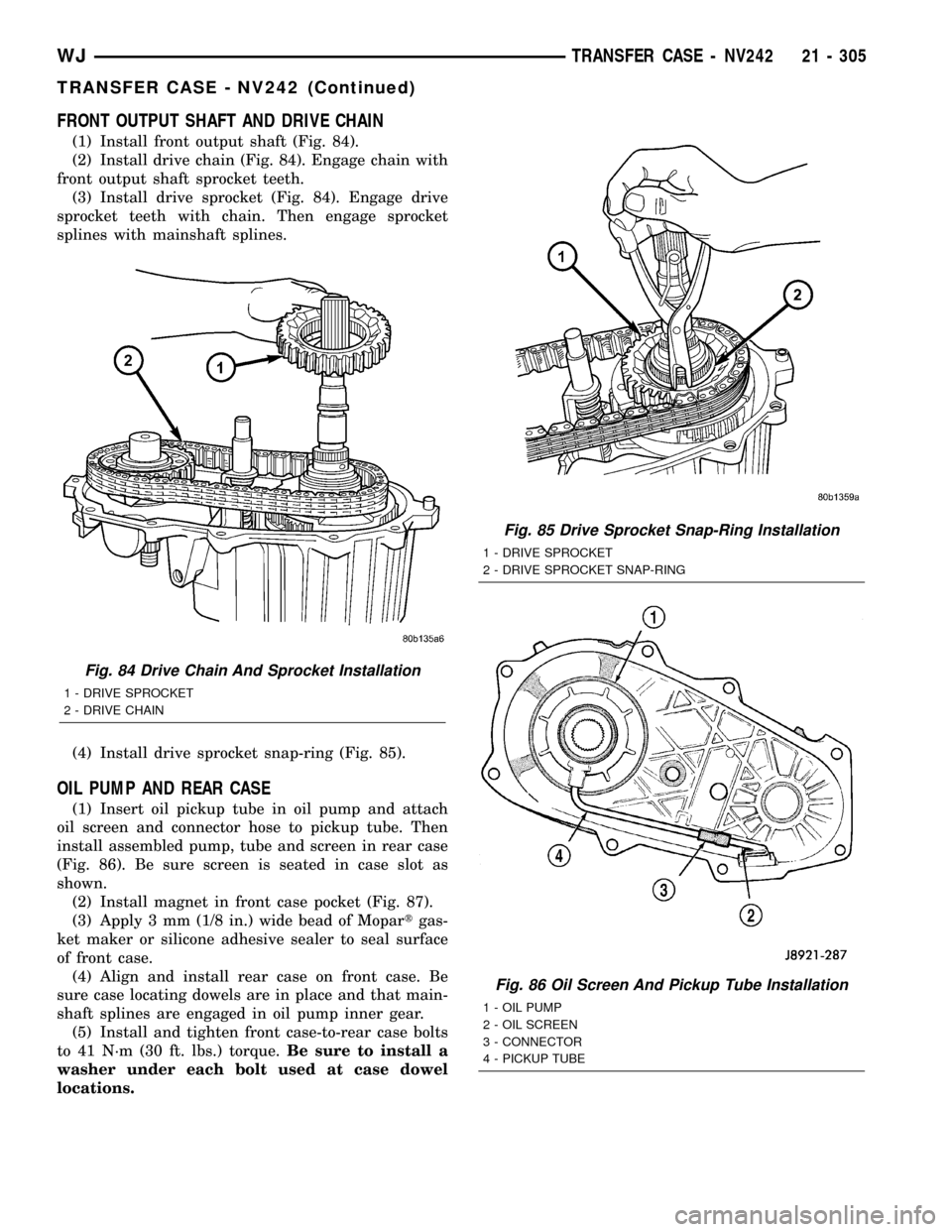
FRONT OUTPUT SHAFT AND DRIVE CHAIN
(1) Install front output shaft (Fig. 84).
(2) Install drive chain (Fig. 84). Engage chain with
front output shaft sprocket teeth.
(3) Install drive sprocket (Fig. 84). Engage drive
sprocket teeth with chain. Then engage sprocket
splines with mainshaft splines.
(4) Install drive sprocket snap-ring (Fig. 85).
OIL PUMP AND REAR CASE
(1) Insert oil pickup tube in oil pump and attach
oil screen and connector hose to pickup tube. Then
install assembled pump, tube and screen in rear case
(Fig. 86). Be sure screen is seated in case slot as
shown.
(2) Install magnet in front case pocket (Fig. 87).
(3) Apply 3 mm (1/8 in.) wide bead of Mopartgas-
ket maker or silicone adhesive sealer to seal surface
of front case.
(4) Align and install rear case on front case. Be
sure case locating dowels are in place and that main-
shaft splines are engaged in oil pump inner gear.
(5) Install and tighten front case-to-rear case bolts
to 41 N´m (30 ft. lbs.) torque.Be sure to install a
washer under each bolt used at case dowel
locations.
Fig. 84 Drive Chain And Sprocket Installation
1 - DRIVE SPROCKET
2 - DRIVE CHAIN
Fig. 85 Drive Sprocket Snap-Ring Installation
1 - DRIVE SPROCKET
2 - DRIVE SPROCKET SNAP-RING
Fig. 86 Oil Screen And Pickup Tube Installation
1 - OIL PUMP
2 - OIL SCREEN
3 - CONNECTOR
4 - PICKUP TUBE
WJTRANSFER CASE - NV242 21 - 305
TRANSFER CASE - NV242 (Continued)
Page 1825 of 2199
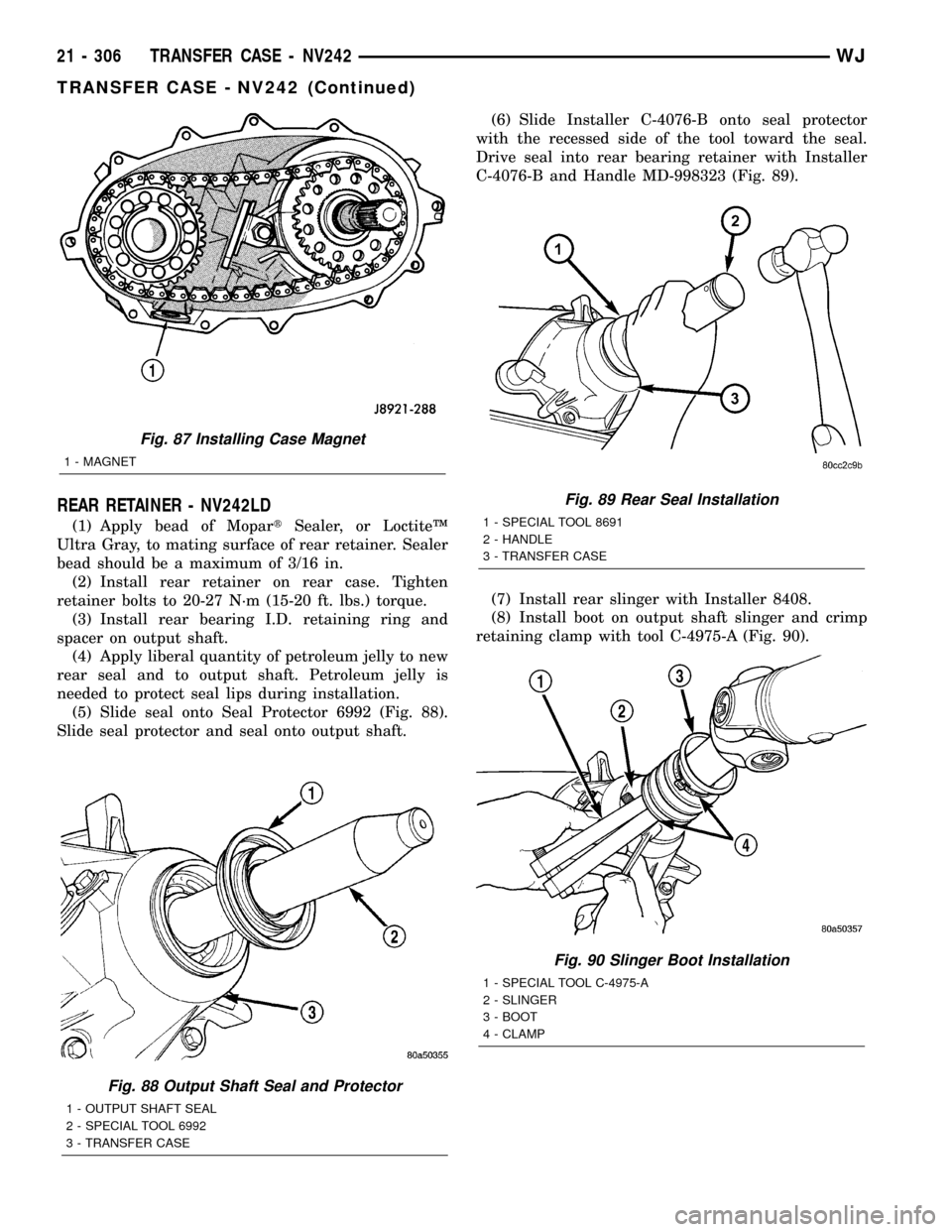
REAR RETAINER - NV242LD
(1) Apply bead of MopartSealer, or LoctiteŸ
Ultra Gray, to mating surface of rear retainer. Sealer
bead should be a maximum of 3/16 in.
(2) Install rear retainer on rear case. Tighten
retainer bolts to 20-27 N´m (15-20 ft. lbs.) torque.
(3) Install rear bearing I.D. retaining ring and
spacer on output shaft.
(4) Apply liberal quantity of petroleum jelly to new
rear seal and to output shaft. Petroleum jelly is
needed to protect seal lips during installation.
(5) Slide seal onto Seal Protector 6992 (Fig. 88).
Slide seal protector and seal onto output shaft.(6) Slide Installer C-4076-B onto seal protector
with the recessed side of the tool toward the seal.
Drive seal into rear bearing retainer with Installer
C-4076-B and Handle MD-998323 (Fig. 89).
(7) Install rear slinger with Installer 8408.
(8) Install boot on output shaft slinger and crimp
retaining clamp with tool C-4975-A (Fig. 90).
Fig. 88 Output Shaft Seal and Protector
1 - OUTPUT SHAFT SEAL
2 - SPECIAL TOOL 6992
3 - TRANSFER CASE
Fig. 87 Installing Case Magnet
1 - MAGNET
Fig. 89 Rear Seal Installation
1 - SPECIAL TOOL 8691
2 - HANDLE
3 - TRANSFER CASE
Fig. 90 Slinger Boot Installation
1 - SPECIAL TOOL C-4975-A
2 - SLINGER
3 - BOOT
4 - CLAMP
21 - 306 TRANSFER CASE - NV242WJ
TRANSFER CASE - NV242 (Continued)
Page 1826 of 2199
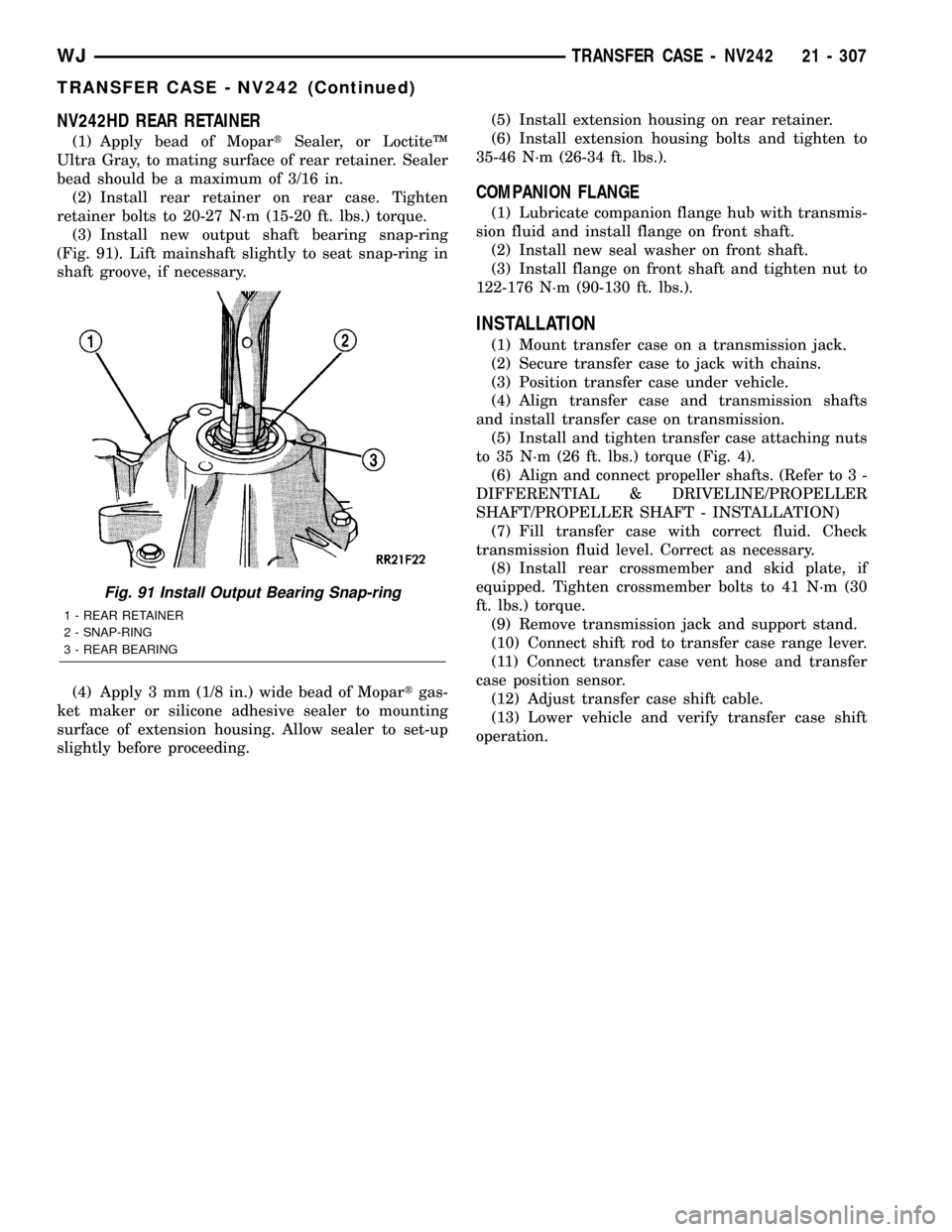
NV242HD REAR RETAINER
(1) Apply bead of MopartSealer, or LoctiteŸ
Ultra Gray, to mating surface of rear retainer. Sealer
bead should be a maximum of 3/16 in.
(2) Install rear retainer on rear case. Tighten
retainer bolts to 20-27 N´m (15-20 ft. lbs.) torque.
(3) Install new output shaft bearing snap-ring
(Fig. 91). Lift mainshaft slightly to seat snap-ring in
shaft groove, if necessary.
(4) Apply 3 mm (1/8 in.) wide bead of Mopartgas-
ket maker or silicone adhesive sealer to mounting
surface of extension housing. Allow sealer to set-up
slightly before proceeding.(5) Install extension housing on rear retainer.
(6) Install extension housing bolts and tighten to
35-46 N´m (26-34 ft. lbs.).
COMPANION FLANGE
(1) Lubricate companion flange hub with transmis-
sion fluid and install flange on front shaft.
(2) Install new seal washer on front shaft.
(3) Install flange on front shaft and tighten nut to
122-176 N´m (90-130 ft. lbs.).
INSTALLATION
(1) Mount transfer case on a transmission jack.
(2) Secure transfer case to jack with chains.
(3) Position transfer case under vehicle.
(4) Align transfer case and transmission shafts
and install transfer case on transmission.
(5) Install and tighten transfer case attaching nuts
to 35 N´m (26 ft. lbs.) torque (Fig. 4).
(6) Align and connect propeller shafts. (Refer to 3 -
DIFFERENTIAL & DRIVELINE/PROPELLER
SHAFT/PROPELLER SHAFT - INSTALLATION)
(7) Fill transfer case with correct fluid. Check
transmission fluid level. Correct as necessary.
(8) Install rear crossmember and skid plate, if
equipped. Tighten crossmember bolts to 41 N´m (30
ft. lbs.) torque.
(9) Remove transmission jack and support stand.
(10) Connect shift rod to transfer case range lever.
(11) Connect transfer case vent hose and transfer
case position sensor.
(12) Adjust transfer case shift cable.
(13) Lower vehicle and verify transfer case shift
operation.
Fig. 91 Install Output Bearing Snap-ring
1 - REAR RETAINER
2 - SNAP-RING
3 - REAR BEARING
WJTRANSFER CASE - NV242 21 - 307
TRANSFER CASE - NV242 (Continued)
Page 1827 of 2199
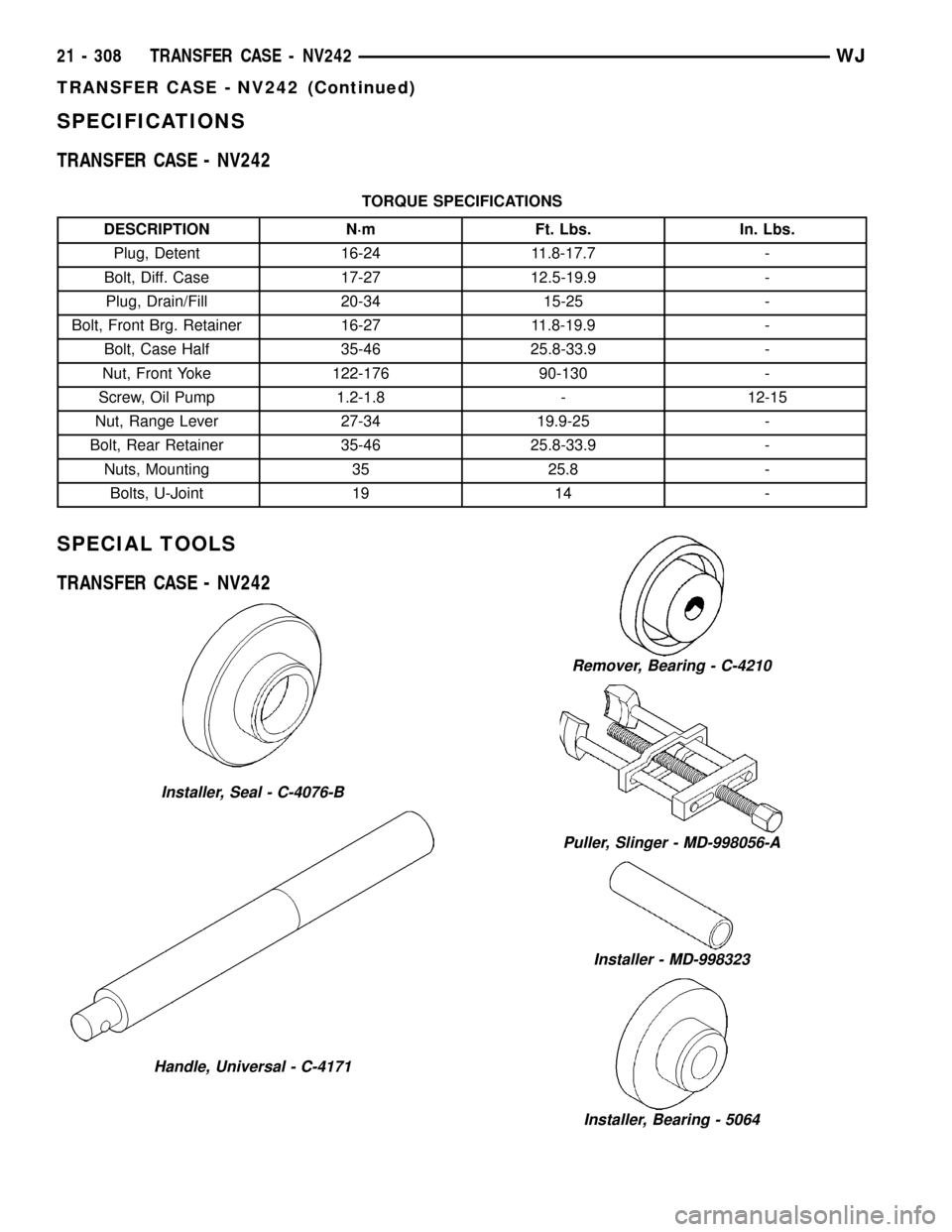
SPECIFICATIONS
TRANSFER CASE - NV242
TORQUE SPECIFICATIONS
DESCRIPTION N´m Ft. Lbs. In. Lbs.
Plug, Detent 16-24 11.8-17.7 -
Bolt, Diff. Case 17-27 12.5-19.9 -
Plug, Drain/Fill 20-34 15-25 -
Bolt, Front Brg. Retainer 16-27 11.8-19.9 -
Bolt, Case Half 35-46 25.8-33.9 -
Nut, Front Yoke 122-176 90-130 -
Screw, Oil Pump 1.2-1.8 - 12-15
Nut, Range Lever 27-34 19.9-25 -
Bolt, Rear Retainer 35-46 25.8-33.9 -
Nuts, Mounting 35 25.8 -
Bolts, U-Joint 19 14 -
SPECIAL TOOLS
TRANSFER CASE - NV242
Installer, Seal - C-4076-B
Handle, Universal - C-4171
Remover, Bearing - C-4210
Puller, Slinger - MD-998056-A
Installer - MD-998323
Installer, Bearing - 5064
21 - 308 TRANSFER CASE - NV242WJ
TRANSFER CASE - NV242 (Continued)
Page 1828 of 2199
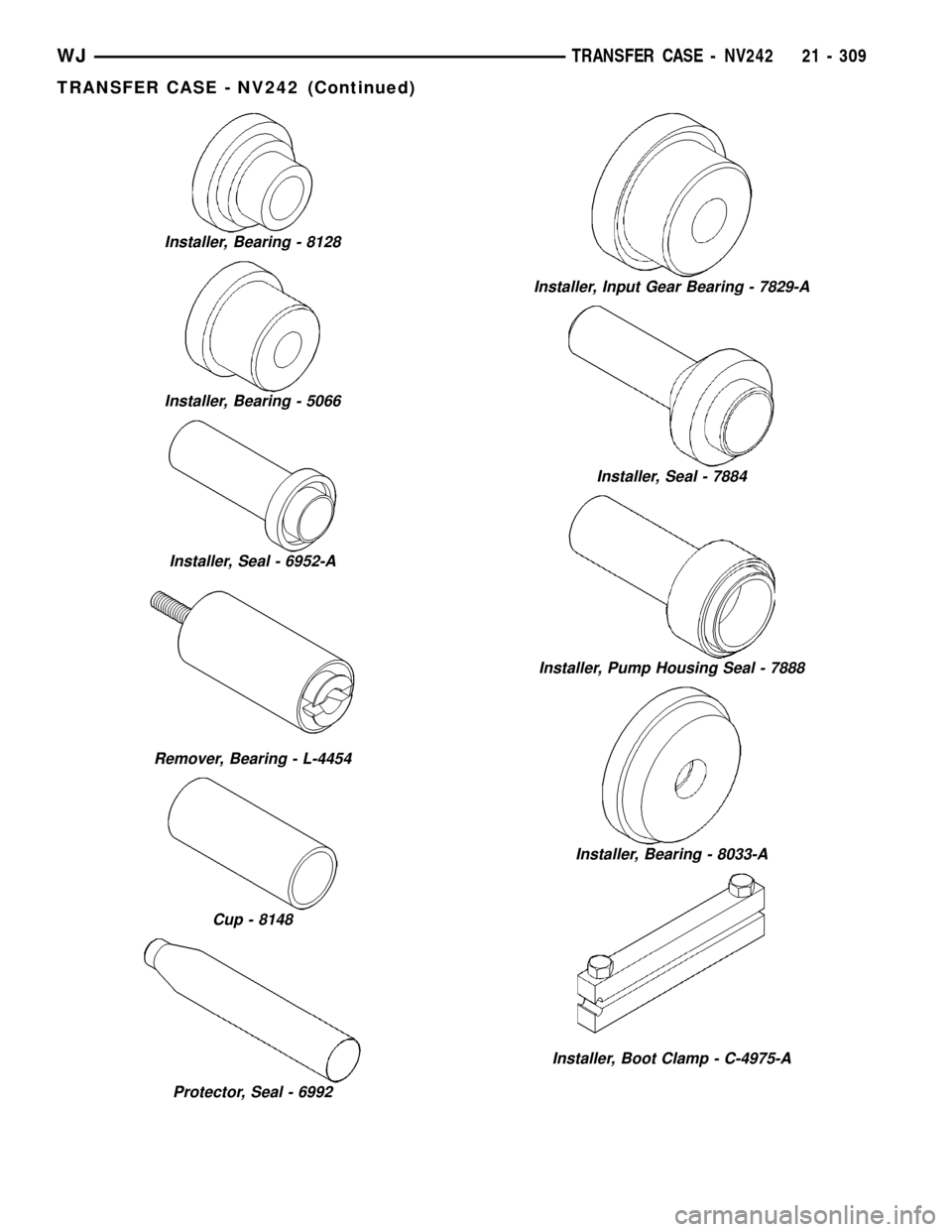
Installer, Bearing - 8128
Installer, Bearing - 5066
Installer, Seal - 6952-A
Remover, Bearing - L-4454
Cup - 8148
Protector, Seal - 6992
Installer, Input Gear Bearing - 7829-A
Installer, Seal - 7884
Installer, Pump Housing Seal - 7888
Installer, Bearing - 8033-A
Installer, Boot Clamp - C-4975-A
WJTRANSFER CASE - NV242 21 - 309
TRANSFER CASE - NV242 (Continued)
Page 1829 of 2199
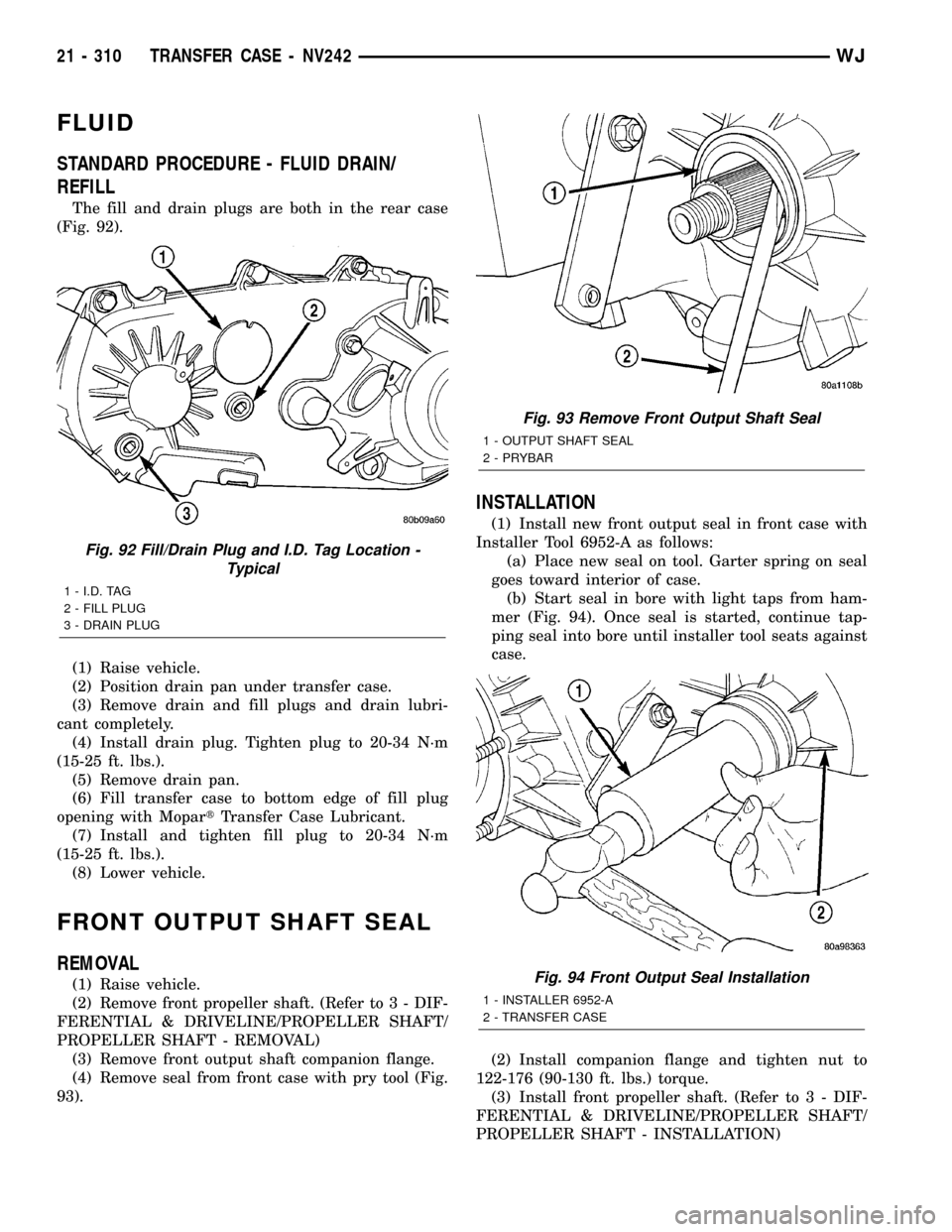
FLUID
STANDARD PROCEDURE - FLUID DRAIN/
REFILL
The fill and drain plugs are both in the rear case
(Fig. 92).
(1) Raise vehicle.
(2) Position drain pan under transfer case.
(3) Remove drain and fill plugs and drain lubri-
cant completely.
(4) Install drain plug. Tighten plug to 20-34 N´m
(15-25 ft. lbs.).
(5) Remove drain pan.
(6) Fill transfer case to bottom edge of fill plug
opening with MopartTransfer Case Lubricant.
(7) Install and tighten fill plug to 20-34 N´m
(15-25 ft. lbs.).
(8) Lower vehicle.
FRONT OUTPUT SHAFT SEAL
REMOVAL
(1) Raise vehicle.
(2) Remove front propeller shaft. (Refer to 3 - DIF-
FERENTIAL & DRIVELINE/PROPELLER SHAFT/
PROPELLER SHAFT - REMOVAL)
(3) Remove front output shaft companion flange.
(4) Remove seal from front case with pry tool (Fig.
93).
INSTALLATION
(1) Install new front output seal in front case with
Installer Tool 6952-A as follows:
(a) Place new seal on tool. Garter spring on seal
goes toward interior of case.
(b) Start seal in bore with light taps from ham-
mer (Fig. 94). Once seal is started, continue tap-
ping seal into bore until installer tool seats against
case.
(2) Install companion flange and tighten nut to
122-176 (90-130 ft. lbs.) torque.
(3) Install front propeller shaft. (Refer to 3 - DIF-
FERENTIAL & DRIVELINE/PROPELLER SHAFT/
PROPELLER SHAFT - INSTALLATION)
Fig. 92 Fill/Drain Plug and I.D. Tag Location -
Typical
1 - I.D. TAG
2 - FILL PLUG
3 - DRAIN PLUG
Fig. 93 Remove Front Output Shaft Seal
1 - OUTPUT SHAFT SEAL
2 - PRYBAR
Fig. 94 Front Output Seal Installation
1 - INSTALLER 6952-A
2 - TRANSFER CASE
21 - 310 TRANSFER CASE - NV242WJ
Page 1830 of 2199
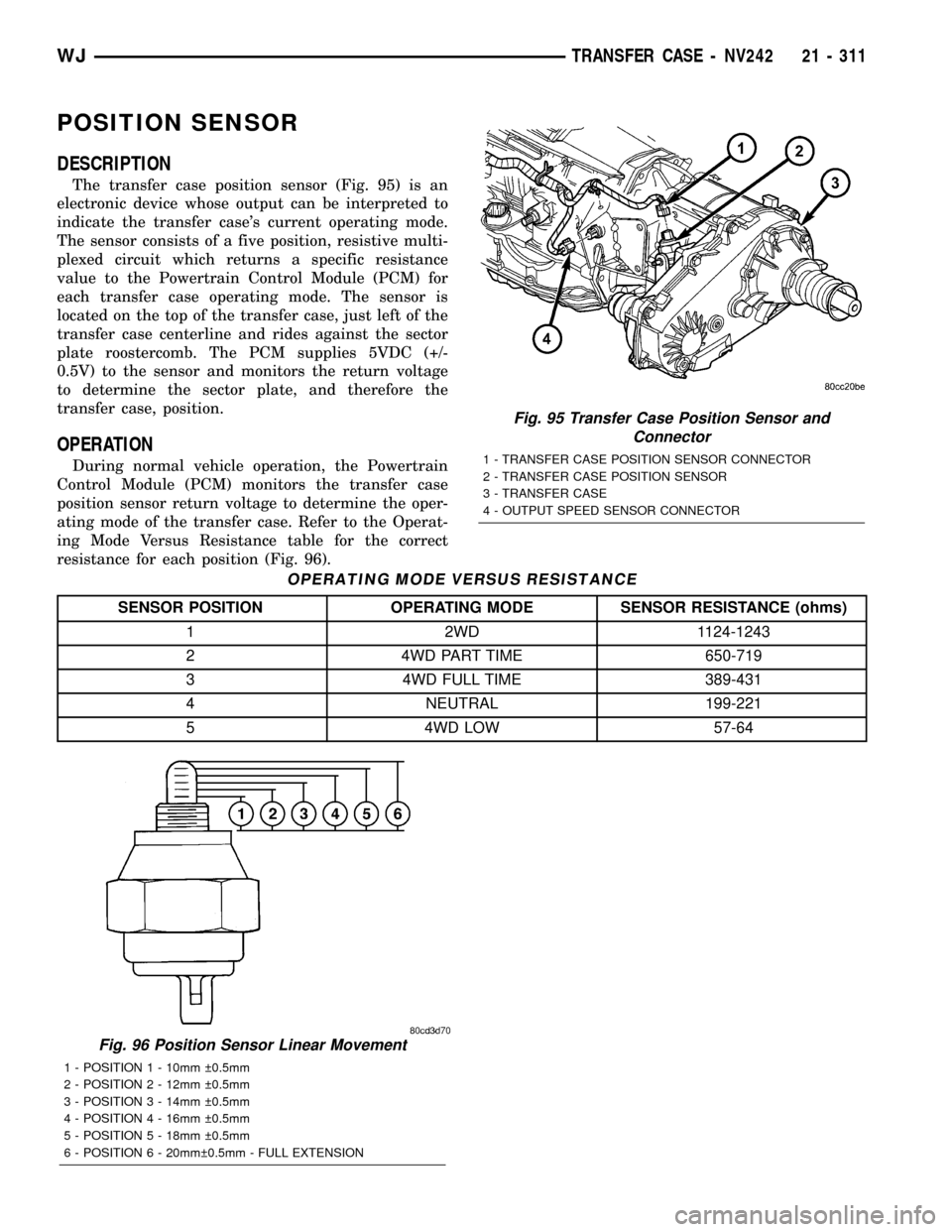
POSITION SENSOR
DESCRIPTION
The transfer case position sensor (Fig. 95) is an
electronic device whose output can be interpreted to
indicate the transfer case's current operating mode.
The sensor consists of a five position, resistive multi-
plexed circuit which returns a specific resistance
value to the Powertrain Control Module (PCM) for
each transfer case operating mode. The sensor is
located on the top of the transfer case, just left of the
transfer case centerline and rides against the sector
plate roostercomb. The PCM supplies 5VDC (+/-
0.5V) to the sensor and monitors the return voltage
to determine the sector plate, and therefore the
transfer case, position.
OPERATION
During normal vehicle operation, the Powertrain
Control Module (PCM) monitors the transfer case
position sensor return voltage to determine the oper-
ating mode of the transfer case. Refer to the Operat-
ing Mode Versus Resistance table for the correct
resistance for each position (Fig. 96).
OPERATING MODE VERSUS RESISTANCE
SENSOR POSITION OPERATING MODE SENSOR RESISTANCE (ohms)
1 2WD 1124-1243
2 4WD PART TIME 650-719
3 4WD FULL TIME 389-431
4 NEUTRAL 199-221
5 4WD LOW 57-64
Fig. 96 Position Sensor Linear Movement
1 - POSITION 1 - 10mm 0.5mm
2 - POSITION 2 - 12mm 0.5mm
3 - POSITION 3 - 14mm 0.5mm
4 - POSITION 4 - 16mm 0.5mm
5 - POSITION 5 - 18mm 0.5mm
6 - POSITION 6 - 20mm 0.5mm - FULL EXTENSION
Fig. 95 Transfer Case Position Sensor and
Connector
1 - TRANSFER CASE POSITION SENSOR CONNECTOR
2 - TRANSFER CASE POSITION SENSOR
3 - TRANSFER CASE
4 - OUTPUT SPEED SENSOR CONNECTOR
WJTRANSFER CASE - NV242 21 - 311