Table of contents JEEP GRAND CHEROKEE 2003 WJ / 2.G Manual PDF
[x] Cancel search | Manufacturer: JEEP, Model Year: 2003, Model line: GRAND CHEROKEE, Model: JEEP GRAND CHEROKEE 2003 WJ / 2.GPages: 2199, PDF Size: 76.01 MB
Page 1954 of 2199
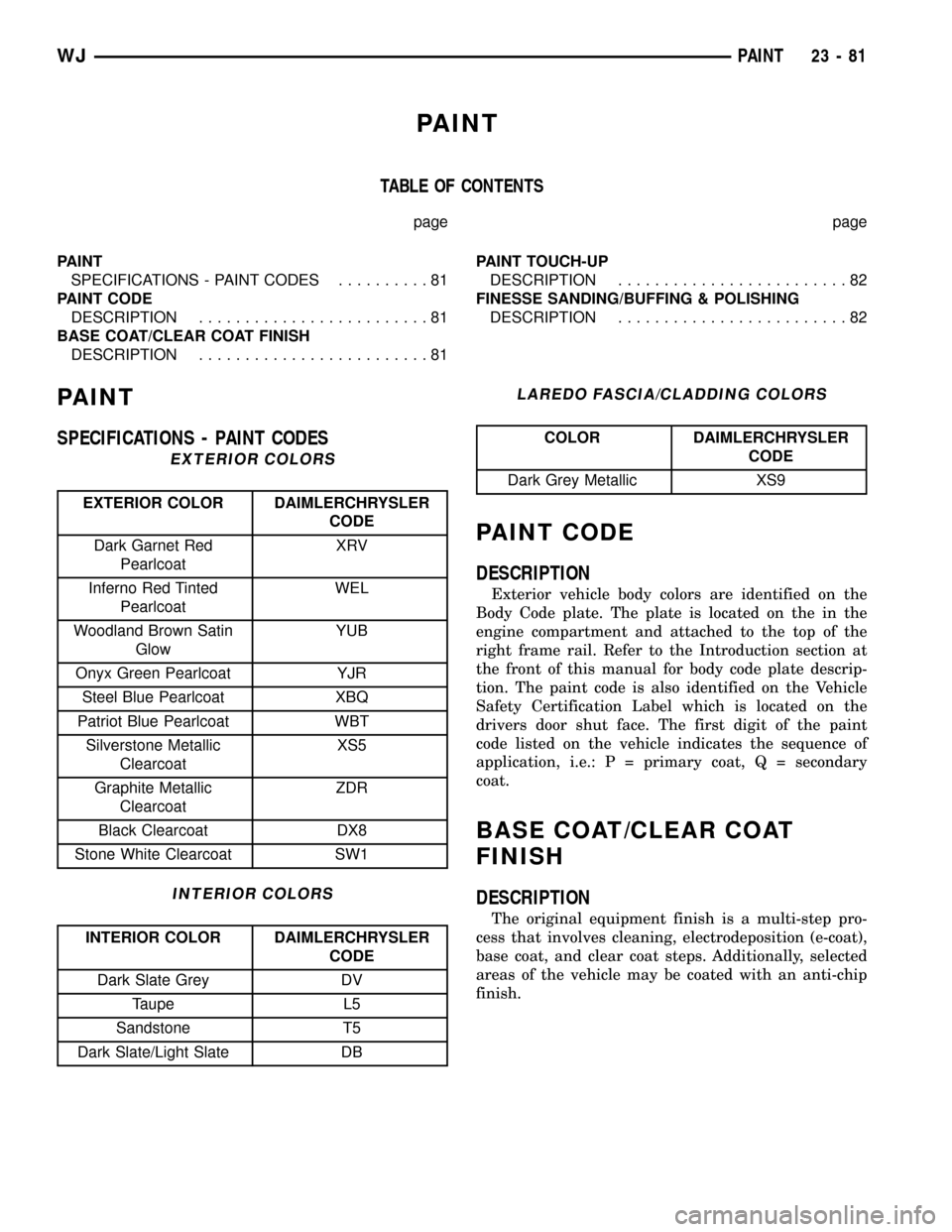
PAINT
TABLE OF CONTENTS
page page
PAINT
SPECIFICATIONS - PAINT CODES..........81
PAINT CODE
DESCRIPTION.........................81
BASE COAT/CLEAR COAT FINISH
DESCRIPTION.........................81PAINT TOUCH-UP
DESCRIPTION.........................82
FINESSE SANDING/BUFFING & POLISHING
DESCRIPTION.........................82
PAINT
SPECIFICATIONS - PAINT CODES
EXTERIOR COLORS
EXTERIOR COLOR DAIMLERCHRYSLER
CODE
Dark Garnet Red
PearlcoatXRV
Inferno Red Tinted
PearlcoatWEL
Woodland Brown Satin
GlowYUB
Onyx Green Pearlcoat YJR
Steel Blue Pearlcoat XBQ
Patriot Blue Pearlcoat WBT
Silverstone Metallic
ClearcoatXS5
Graphite Metallic
ClearcoatZDR
Black Clearcoat DX8
Stone White Clearcoat SW1
INTERIOR COLORS
INTERIOR COLOR DAIMLERCHRYSLER
CODE
Dark Slate Grey DV
Taupe L5
Sandstone T5
Dark Slate/Light Slate DB
LAREDO FASCIA/CLADDING COLORS
COLOR DAIMLERCHRYSLER
CODE
Dark Grey Metallic XS9
PAINT CODE
DESCRIPTION
Exterior vehicle body colors are identified on the
Body Code plate. The plate is located on the in the
engine compartment and attached to the top of the
right frame rail. Refer to the Introduction section at
the front of this manual for body code plate descrip-
tion. The paint code is also identified on the Vehicle
Safety Certification Label which is located on the
drivers door shut face. The first digit of the paint
code listed on the vehicle indicates the sequence of
application, i.e.: P = primary coat, Q = secondary
coat.
BASE COAT/CLEAR COAT
FINISH
DESCRIPTION
The original equipment finish is a multi-step pro-
cess that involves cleaning, electrodeposition (e-coat),
base coat, and clear coat steps. Additionally, selected
areas of the vehicle may be coated with an anti-chip
finish.
WJPAINT 23 - 81
Page 1956 of 2199
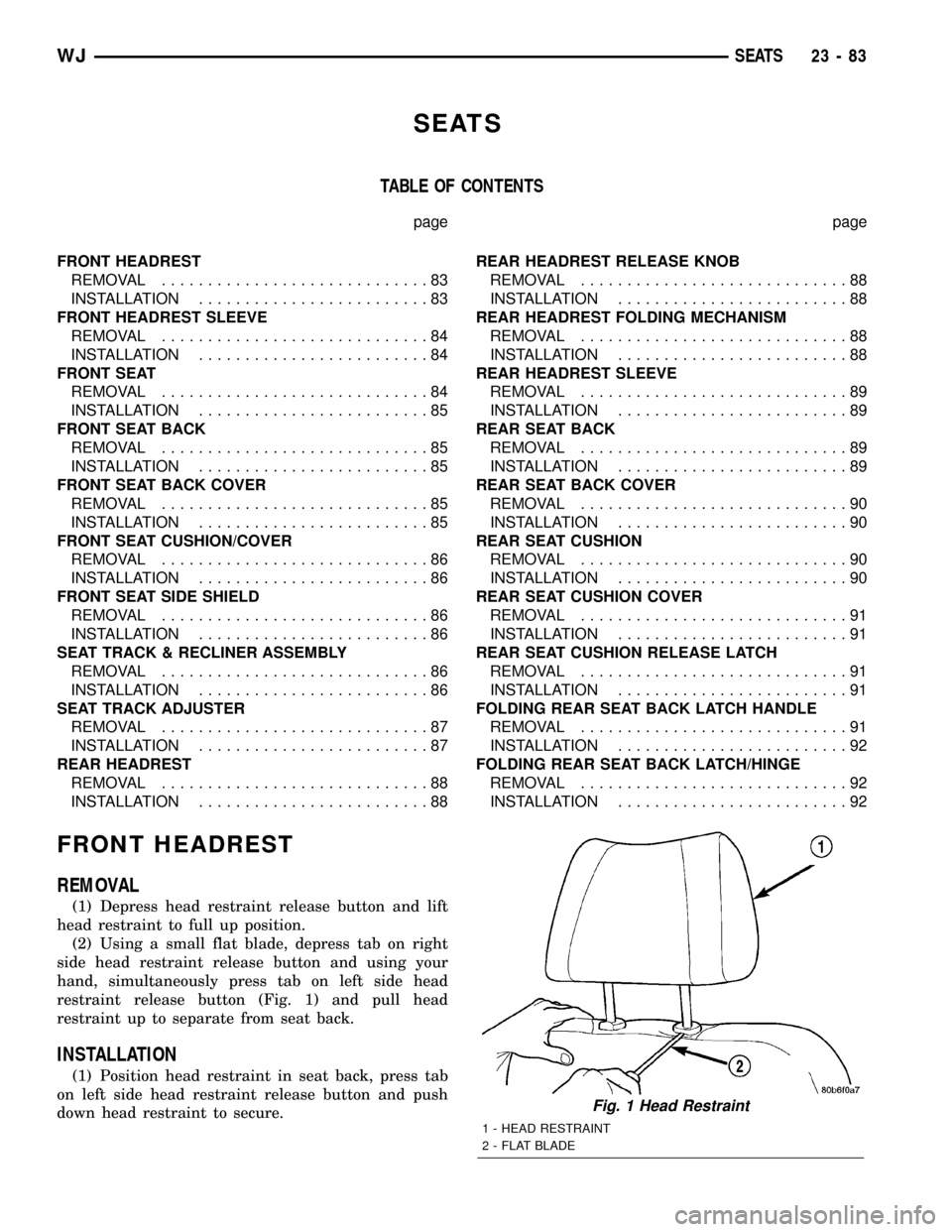
SEATS
TABLE OF CONTENTS
page page
FRONT HEADREST
REMOVAL.............................83
INSTALLATION.........................83
FRONT HEADREST SLEEVE
REMOVAL.............................84
INSTALLATION.........................84
FRONT SEAT
REMOVAL.............................84
INSTALLATION.........................85
FRONT SEAT BACK
REMOVAL.............................85
INSTALLATION.........................85
FRONT SEAT BACK COVER
REMOVAL.............................85
INSTALLATION.........................85
FRONT SEAT CUSHION/COVER
REMOVAL.............................86
INSTALLATION.........................86
FRONT SEAT SIDE SHIELD
REMOVAL.............................86
INSTALLATION.........................86
SEAT TRACK & RECLINER ASSEMBLY
REMOVAL.............................86
INSTALLATION.........................86
SEAT TRACK ADJUSTER
REMOVAL.............................87
INSTALLATION.........................87
REAR HEADREST
REMOVAL.............................88
INSTALLATION.........................88REAR HEADREST RELEASE KNOB
REMOVAL.............................88
INSTALLATION.........................88
REAR HEADREST FOLDING MECHANISM
REMOVAL.............................88
INSTALLATION.........................88
REAR HEADREST SLEEVE
REMOVAL.............................89
INSTALLATION.........................89
REAR SEAT BACK
REMOVAL.............................89
INSTALLATION.........................89
REAR SEAT BACK COVER
REMOVAL.............................90
INSTALLATION.........................90
REAR SEAT CUSHION
REMOVAL.............................90
INSTALLATION.........................90
REAR SEAT CUSHION COVER
REMOVAL.............................91
INSTALLATION.........................91
REAR SEAT CUSHION RELEASE LATCH
REMOVAL.............................91
INSTALLATION.........................91
FOLDING REAR SEAT BACK LATCH HANDLE
REMOVAL.............................91
INSTALLATION.........................92
FOLDING REAR SEAT BACK LATCH/HINGE
REMOVAL.............................92
INSTALLATION.........................92
FRONT HEADREST
REMOVAL
(1) Depress head restraint release button and lift
head restraint to full up position.
(2) Using a small flat blade, depress tab on right
side head restraint release button and using your
hand, simultaneously press tab on left side head
restraint release button (Fig. 1) and pull head
restraint up to separate from seat back.
INSTALLATION
(1) Position head restraint in seat back, press tab
on left side head restraint release button and push
down head restraint to secure.
Fig. 1 Head Restraint
1 - HEAD RESTRAINT
2 - FLAT BLADE
WJSEATS 23 - 83
Page 1966 of 2199
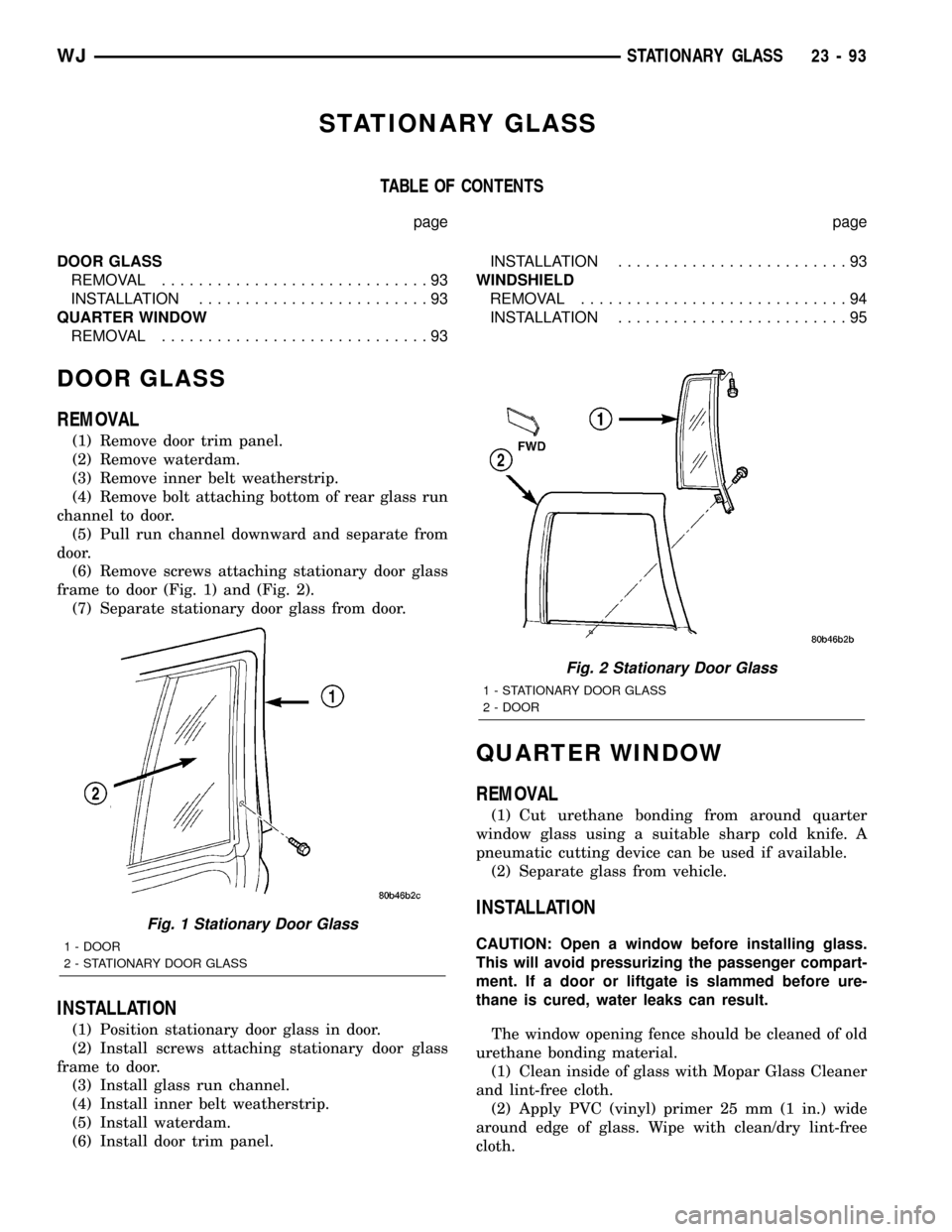
STATIONARY GLASS
TABLE OF CONTENTS
page page
DOOR GLASS
REMOVAL.............................93
INSTALLATION.........................93
QUARTER WINDOW
REMOVAL.............................93INSTALLATION.........................93
WINDSHIELD
REMOVAL.............................94
INSTALLATION.........................95
DOOR GLASS
REMOVAL
(1) Remove door trim panel.
(2) Remove waterdam.
(3) Remove inner belt weatherstrip.
(4) Remove bolt attaching bottom of rear glass run
channel to door.
(5) Pull run channel downward and separate from
door.
(6) Remove screws attaching stationary door glass
frame to door (Fig. 1) and (Fig. 2).
(7) Separate stationary door glass from door.
INSTALLATION
(1) Position stationary door glass in door.
(2) Install screws attaching stationary door glass
frame to door.
(3) Install glass run channel.
(4) Install inner belt weatherstrip.
(5) Install waterdam.
(6) Install door trim panel.
QUARTER WINDOW
REMOVAL
(1) Cut urethane bonding from around quarter
window glass using a suitable sharp cold knife. A
pneumatic cutting device can be used if available.
(2) Separate glass from vehicle.
INSTALLATION
CAUTION: Open a window before installing glass.
This will avoid pressurizing the passenger compart-
ment. If a door or liftgate is slammed before ure-
thane is cured, water leaks can result.
The window opening fence should be cleaned of old
urethane bonding material.
(1) Clean inside of glass with Mopar Glass Cleaner
and lint-free cloth.
(2) Apply PVC (vinyl) primer 25 mm (1 in.) wide
around edge of glass. Wipe with clean/dry lint-free
cloth.
Fig. 1 Stationary Door Glass
1 - DOOR
2 - STATIONARY DOOR GLASS
Fig. 2 Stationary Door Glass
1 - STATIONARY DOOR GLASS
2 - DOOR
WJSTATIONARY GLASS 23 - 93
Page 1969 of 2199
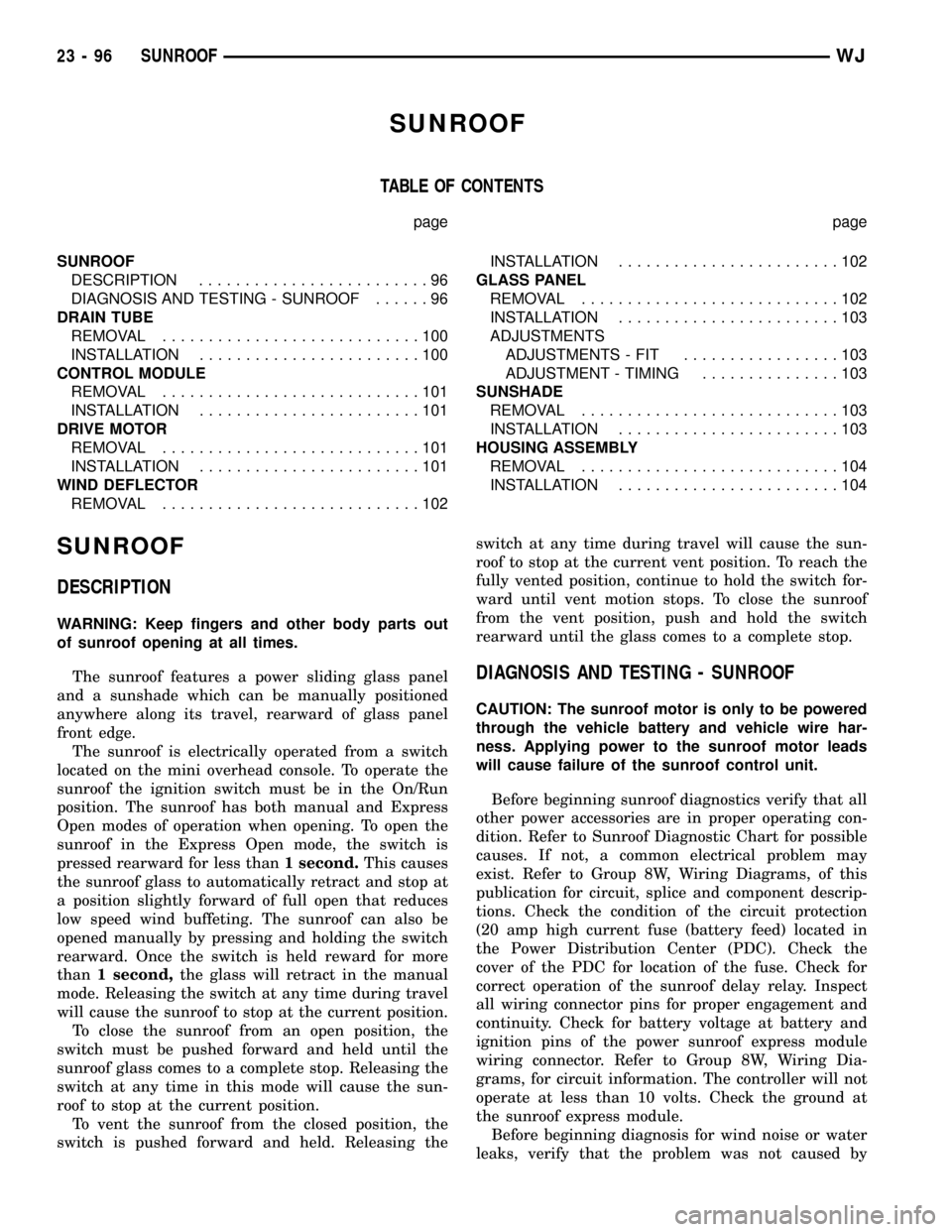
SUNROOF
TABLE OF CONTENTS
page page
SUNROOF
DESCRIPTION.........................96
DIAGNOSIS AND TESTING - SUNROOF......96
DRAIN TUBE
REMOVAL............................100
INSTALLATION........................100
CONTROL MODULE
REMOVAL............................101
INSTALLATION........................101
DRIVE MOTOR
REMOVAL............................101
INSTALLATION........................101
WIND DEFLECTOR
REMOVAL............................102INSTALLATION........................102
GLASS PANEL
REMOVAL............................102
INSTALLATION........................103
ADJUSTMENTS
ADJUSTMENTS - FIT.................103
ADJUSTMENT - TIMING...............103
SUNSHADE
REMOVAL............................103
INSTALLATION........................103
HOUSING ASSEMBLY
REMOVAL............................104
INSTALLATION........................104
SUNROOF
DESCRIPTION
WARNING: Keep fingers and other body parts out
of sunroof opening at all times.
The sunroof features a power sliding glass panel
and a sunshade which can be manually positioned
anywhere along its travel, rearward of glass panel
front edge.
The sunroof is electrically operated from a switch
located on the mini overhead console. To operate the
sunroof the ignition switch must be in the On/Run
position. The sunroof has both manual and Express
Open modes of operation when opening. To open the
sunroof in the Express Open mode, the switch is
pressed rearward for less than1 second.This causes
the sunroof glass to automatically retract and stop at
a position slightly forward of full open that reduces
low speed wind buffeting. The sunroof can also be
opened manually by pressing and holding the switch
rearward. Once the switch is held reward for more
than1 second,the glass will retract in the manual
mode. Releasing the switch at any time during travel
will cause the sunroof to stop at the current position.
To close the sunroof from an open position, the
switch must be pushed forward and held until the
sunroof glass comes to a complete stop. Releasing the
switch at any time in this mode will cause the sun-
roof to stop at the current position.
To vent the sunroof from the closed position, the
switch is pushed forward and held. Releasing theswitch at any time during travel will cause the sun-
roof to stop at the current vent position. To reach the
fully vented position, continue to hold the switch for-
ward until vent motion stops. To close the sunroof
from the vent position, push and hold the switch
rearward until the glass comes to a complete stop.
DIAGNOSIS AND TESTING - SUNROOF
CAUTION: The sunroof motor is only to be powered
through the vehicle battery and vehicle wire har-
ness. Applying power to the sunroof motor leads
will cause failure of the sunroof control unit.
Before beginning sunroof diagnostics verify that all
other power accessories are in proper operating con-
dition. Refer to Sunroof Diagnostic Chart for possible
causes. If not, a common electrical problem may
exist. Refer to Group 8W, Wiring Diagrams, of this
publication for circuit, splice and component descrip-
tions. Check the condition of the circuit protection
(20 amp high current fuse (battery feed) located in
the Power Distribution Center (PDC). Check the
cover of the PDC for location of the fuse. Check for
correct operation of the sunroof delay relay. Inspect
all wiring connector pins for proper engagement and
continuity. Check for battery voltage at battery and
ignition pins of the power sunroof express module
wiring connector. Refer to Group 8W, Wiring Dia-
grams, for circuit information. The controller will not
operate at less than 10 volts. Check the ground at
the sunroof express module.
Before beginning diagnosis for wind noise or water
leaks, verify that the problem was not caused by
23 - 96 SUNROOFWJ
Page 1978 of 2199
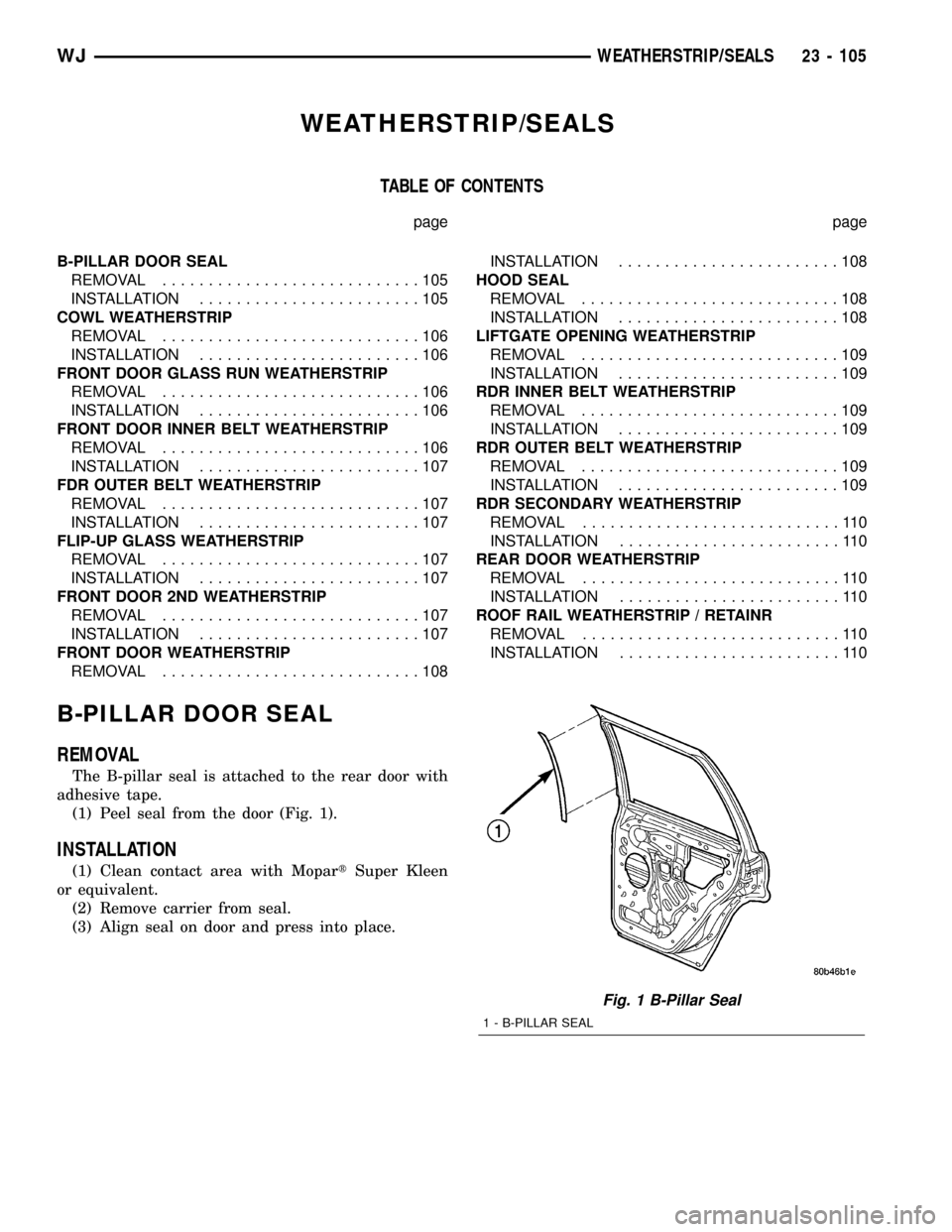
WEATHERSTRIP/SEALS
TABLE OF CONTENTS
page page
B-PILLAR DOOR SEAL
REMOVAL............................105
INSTALLATION........................105
COWL WEATHERSTRIP
REMOVAL............................106
INSTALLATION........................106
FRONT DOOR GLASS RUN WEATHERSTRIP
REMOVAL............................106
INSTALLATION........................106
FRONT DOOR INNER BELT WEATHERSTRIP
REMOVAL............................106
INSTALLATION........................107
FDR OUTER BELT WEATHERSTRIP
REMOVAL............................107
INSTALLATION........................107
FLIP-UP GLASS WEATHERSTRIP
REMOVAL............................107
INSTALLATION........................107
FRONT DOOR 2ND WEATHERSTRIP
REMOVAL............................107
INSTALLATION........................107
FRONT DOOR WEATHERSTRIP
REMOVAL............................108INSTALLATION........................108
HOOD SEAL
REMOVAL............................108
INSTALLATION........................108
LIFTGATE OPENING WEATHERSTRIP
REMOVAL............................109
INSTALLATION........................109
RDR INNER BELT WEATHERSTRIP
REMOVAL............................109
INSTALLATION........................109
RDR OUTER BELT WEATHERSTRIP
REMOVAL............................109
INSTALLATION........................109
RDR SECONDARY WEATHERSTRIP
REMOVAL............................110
INSTALLATION........................110
REAR DOOR WEATHERSTRIP
REMOVAL............................110
INSTALLATION........................110
ROOF RAIL WEATHERSTRIP / RETAINR
REMOVAL............................110
INSTALLATION........................110
B-PILLAR DOOR SEAL
REMOVAL
The B-pillar seal is attached to the rear door with
adhesive tape.
(1) Peel seal from the door (Fig. 1).
INSTALLATION
(1) Clean contact area with MopartSuper Kleen
or equivalent.
(2) Remove carrier from seal.
(3) Align seal on door and press into place.
Fig. 1 B-Pillar Seal
1 - B-PILLAR SEAL
WJWEATHERSTRIP/SEALS 23 - 105
Page 1984 of 2199
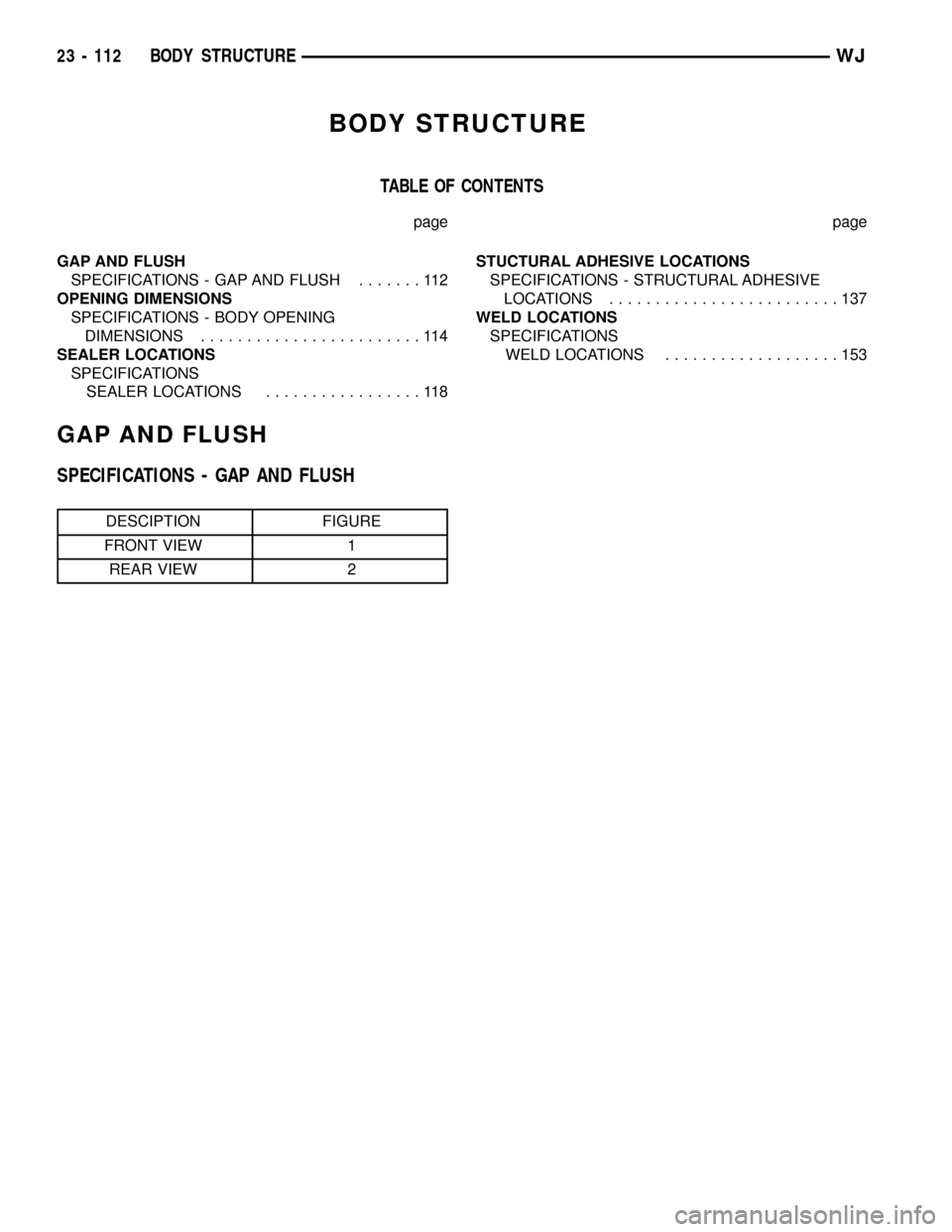
BODY STRUCTURE
TABLE OF CONTENTS
page page
GAP AND FLUSH
SPECIFICATIONS - GAP AND FLUSH.......112
OPENING DIMENSIONS
SPECIFICATIONS - BODY OPENING
DIMENSIONS........................114
SEALER LOCATIONS
SPECIFICATIONS
SEALER LOCATIONS.................118STUCTURAL ADHESIVE LOCATIONS
SPECIFICATIONS - STRUCTURAL ADHESIVE
LOCATIONS.........................137
WELD LOCATIONS
SPECIFICATIONS
WELD LOCATIONS...................153
GAP AND FLUSH
SPECIFICATIONS - GAP AND FLUSH
DESCIPTION FIGURE
FRONT VIEW 1
REAR VIEW 2
23 - 112 BODY STRUCTUREWJ
Page 2078 of 2199
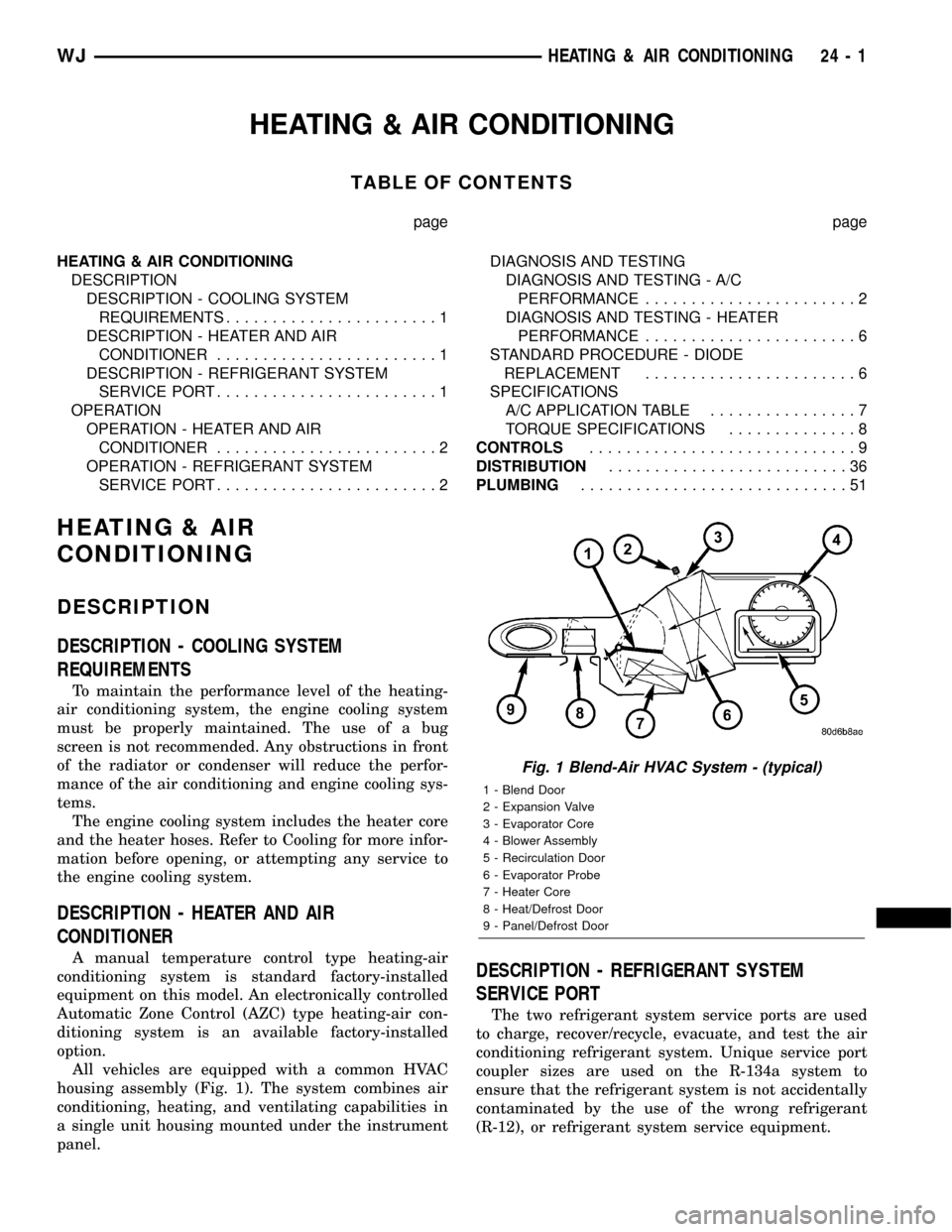
HEATING & AIR CONDITIONING
TABLE OF CONTENTS
page page
HEATING & AIR CONDITIONING
DESCRIPTION
DESCRIPTION - COOLING SYSTEM
REQUIREMENTS.......................1
DESCRIPTION - HEATER AND AIR
CONDITIONER........................1
DESCRIPTION - REFRIGERANT SYSTEM
SERVICE PORT........................1
OPERATION
OPERATION - HEATER AND AIR
CONDITIONER........................2
OPERATION - REFRIGERANT SYSTEM
SERVICE PORT........................2DIAGNOSIS AND TESTING
DIAGNOSIS AND TESTING - A/C
PERFORMANCE.......................2
DIAGNOSIS AND TESTING - HEATER
PERFORMANCE.......................6
STANDARD PROCEDURE - DIODE
REPLACEMENT.......................6
SPECIFICATIONS
A/C APPLICATION TABLE................7
TORQUE SPECIFICATIONS..............8
CONTROLS.............................9
DISTRIBUTION..........................36
PLUMBING.............................51
HEATING & AIR
CONDITIONING
DESCRIPTION
DESCRIPTION - COOLING SYSTEM
REQUIREMENTS
To maintain the performance level of the heating-
air conditioning system, the engine cooling system
must be properly maintained. The use of a bug
screen is not recommended. Any obstructions in front
of the radiator or condenser will reduce the perfor-
mance of the air conditioning and engine cooling sys-
tems.
The engine cooling system includes the heater core
and the heater hoses. Refer to Cooling for more infor-
mation before opening, or attempting any service to
the engine cooling system.
DESCRIPTION - HEATER AND AIR
CONDITIONER
A manual temperature control type heating-air
conditioning system is standard factory-installed
equipment on this model. An electronically controlled
Automatic Zone Control (AZC) type heating-air con-
ditioning system is an available factory-installed
option.
All vehicles are equipped with a common HVAC
housing assembly (Fig. 1). The system combines air
conditioning, heating, and ventilating capabilities in
a single unit housing mounted under the instrument
panel.DESCRIPTION - REFRIGERANT SYSTEM
SERVICE PORT
The two refrigerant system service ports are used
to charge, recover/recycle, evacuate, and test the air
conditioning refrigerant system. Unique service port
coupler sizes are used on the R-134a system to
ensure that the refrigerant system is not accidentally
contaminated by the use of the wrong refrigerant
(R-12), or refrigerant system service equipment.
Fig. 1 Blend-Air HVAC System - (typical)
1 - Blend Door
2 - Expansion Valve
3 - Evaporator Core
4 - Blower Assembly
5 - Recirculation Door
6 - Evaporator Probe
7 - Heater Core
8 - Heat/Defrost Door
9 - Panel/Defrost Door
WJHEATING & AIR CONDITIONING 24 - 1
Page 2086 of 2199
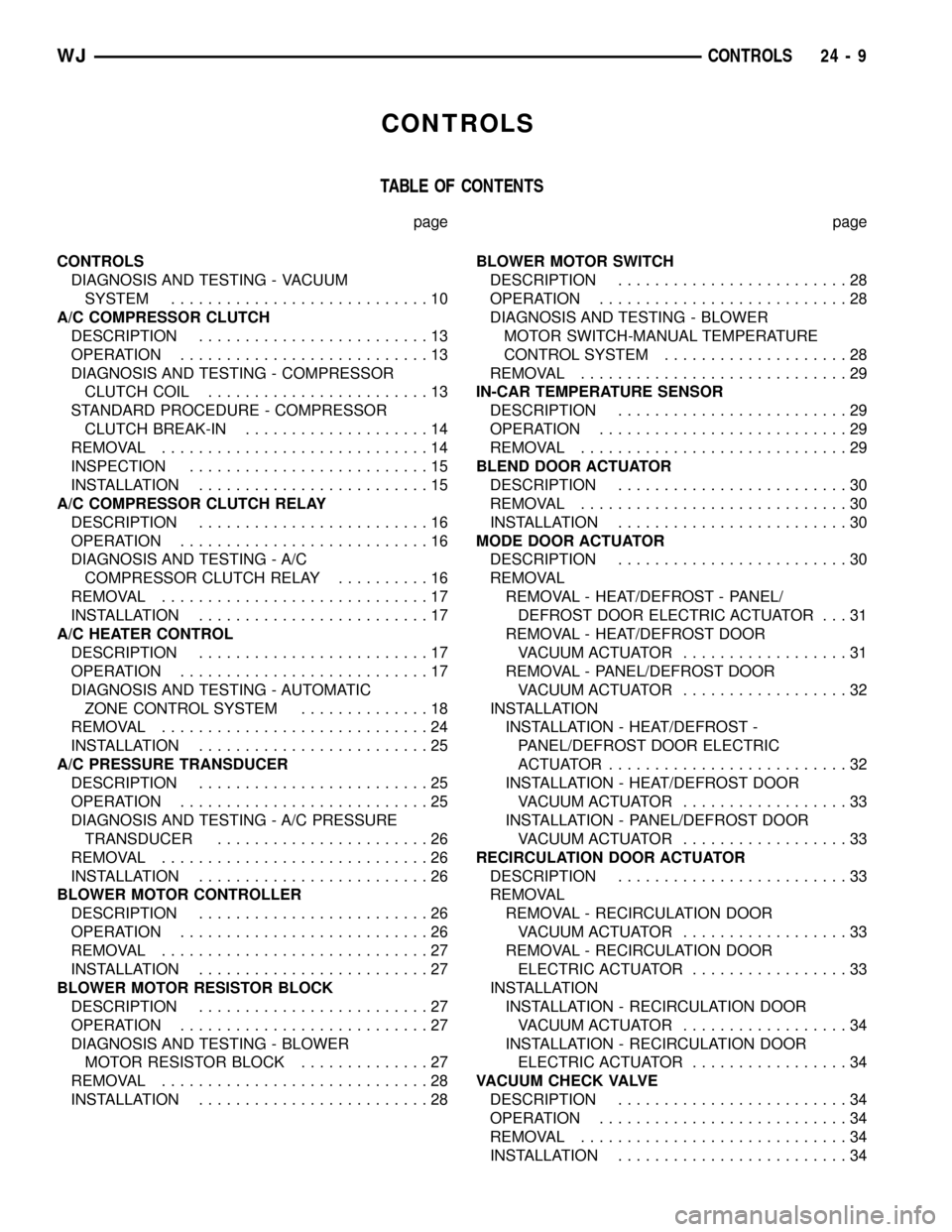
CONTROLS
TABLE OF CONTENTS
page page
CONTROLS
DIAGNOSIS AND TESTING - VACUUM
SYSTEM............................10
A/C COMPRESSOR CLUTCH
DESCRIPTION.........................13
OPERATION...........................13
DIAGNOSIS AND TESTING - COMPRESSOR
CLUTCH COIL........................13
STANDARD PROCEDURE - COMPRESSOR
CLUTCH BREAK-IN....................14
REMOVAL.............................14
INSPECTION..........................15
INSTALLATION.........................15
A/C COMPRESSOR CLUTCH RELAY
DESCRIPTION.........................16
OPERATION...........................16
DIAGNOSIS AND TESTING - A/C
COMPRESSOR CLUTCH RELAY..........16
REMOVAL.............................17
INSTALLATION.........................17
A/C HEATER CONTROL
DESCRIPTION.........................17
OPERATION...........................17
DIAGNOSIS AND TESTING - AUTOMATIC
ZONE CONTROL SYSTEM..............18
REMOVAL.............................24
INSTALLATION.........................25
A/C PRESSURE TRANSDUCER
DESCRIPTION.........................25
OPERATION...........................25
DIAGNOSIS AND TESTING - A/C PRESSURE
TRANSDUCER.......................26
REMOVAL.............................26
INSTALLATION.........................26
BLOWER MOTOR CONTROLLER
DESCRIPTION.........................26
OPERATION...........................26
REMOVAL.............................27
INSTALLATION.........................27
BLOWER MOTOR RESISTOR BLOCK
DESCRIPTION.........................27
OPERATION...........................27
DIAGNOSIS AND TESTING - BLOWER
MOTOR RESISTOR BLOCK..............27
REMOVAL.............................28
INSTALLATION.........................28BLOWER MOTOR SWITCH
DESCRIPTION.........................28
OPERATION...........................28
DIAGNOSIS AND TESTING - BLOWER
MOTOR SWITCH-MANUAL TEMPERATURE
CONTROL SYSTEM....................28
REMOVAL.............................29
IN-CAR TEMPERATURE SENSOR
DESCRIPTION.........................29
OPERATION...........................29
REMOVAL.............................29
BLEND DOOR ACTUATOR
DESCRIPTION.........................30
REMOVAL.............................30
INSTALLATION.........................30
MODE DOOR ACTUATOR
DESCRIPTION.........................30
REMOVAL
REMOVAL - HEAT/DEFROST - PANEL/
DEFROST DOOR ELECTRIC ACTUATOR . . . 31
REMOVAL - HEAT/DEFROST DOOR
VACUUM ACTUATOR..................31
REMOVAL - PANEL/DEFROST DOOR
VACUUM ACTUATOR..................32
INSTALLATION
INSTALLATION - HEAT/DEFROST -
PANEL/DEFROST DOOR ELECTRIC
ACTUATOR..........................32
INSTALLATION - HEAT/DEFROST DOOR
VACUUM ACTUATOR..................33
INSTALLATION - PANEL/DEFROST DOOR
VACUUM ACTUATOR..................33
RECIRCULATION DOOR ACTUATOR
DESCRIPTION.........................33
REMOVAL
REMOVAL - RECIRCULATION DOOR
VACUUM ACTUATOR..................33
REMOVAL - RECIRCULATION DOOR
ELECTRIC ACTUATOR.................33
INSTALLATION
INSTALLATION - RECIRCULATION DOOR
VACUUM ACTUATOR..................34
INSTALLATION - RECIRCULATION DOOR
ELECTRIC ACTUATOR.................34
VACUUM CHECK VALVE
DESCRIPTION.........................34
OPERATION...........................34
REMOVAL.............................34
INSTALLATION.........................34
WJCONTROLS 24 - 9
Page 2113 of 2199

DISTRIBUTION
TABLE OF CONTENTS
page page
AIR OUTLETS
REMOVAL.............................36
INSTALLATION.........................36
BLOWER MOTOR
DESCRIPTION.........................37
OPERATION...........................37
DIAGNOSIS AND TESTING - BLOWER
MOTOR .............................37
REMOVAL.............................37
INSTALLATION.........................38
DEFROSTER DUCTS
REMOVAL.............................38
INSTALLATION.........................39
FLOOR DISTRIBUTION DUCTS
REMOVAL.............................39
INSTALLATION.........................39
INSTRUMENT PANEL DUCTS
REMOVAL.............................39
INSTALLATION.........................39
REAR FLOOR HEAT DUCT
REMOVAL.............................39INSTALLATION.........................39
HVAC HOUSING
REMOVAL.............................41
DISASSEMBLY.........................42
ASSEMBLY............................45
INSTALLATION.........................45
BLEND DOOR
REMOVAL.............................46
INSTALLATION.........................46
MODE DOOR
REMOVAL
REMOVAL - PANEL OUTLET DOOR.......46
REMOVAL - HEAT/DEFROST DOOR.......47
REMOVAL - PANEL/DEFROST DOOR......48
INSTALLATION
INSTALLATION - PANEL OUTLET DOOR....49
INSTALLATION - HEAT/DEFROST DOOR . . . 49
INSTALLATION - PANEL/DEFROST DOOR . . 49
RECIRCULATION DOOR
REMOVAL.............................49
INSTALLATION.........................50
AIR OUTLETS
REMOVAL
The driver side, and passenger side panel outlets
are available for service. The center outlets are only
serviced as part of the instrument cluster center
bezel unit.
(1) Remove the instrument panel top pad from the
instrument panel. Refer to Instrument Panel System
for the procedures.
(2) Remove the two screws that secure each outlet
to the backside of the instrument panel top pad (Fig.
1).
(3) Remove the outlet from the top pad.
INSTALLATION
(1) Fasten the outlet to the top pad. Tighten the
mounting screws to 2.2 N´m (20 in. lbs.).
(2) Install the instrument panel top pad on the
instrument panel. Refer to Instrument Panel System
for the procedures.
Fig. 1 PANEL OUTLETS (PASSENGER SIDE)
1 - MOUNTING SCREWS
2 - MOUNTING SCREWS
3 - PANEL OUTLETS
24 - 36 DISTRIBUTIONWJ
Page 2128 of 2199
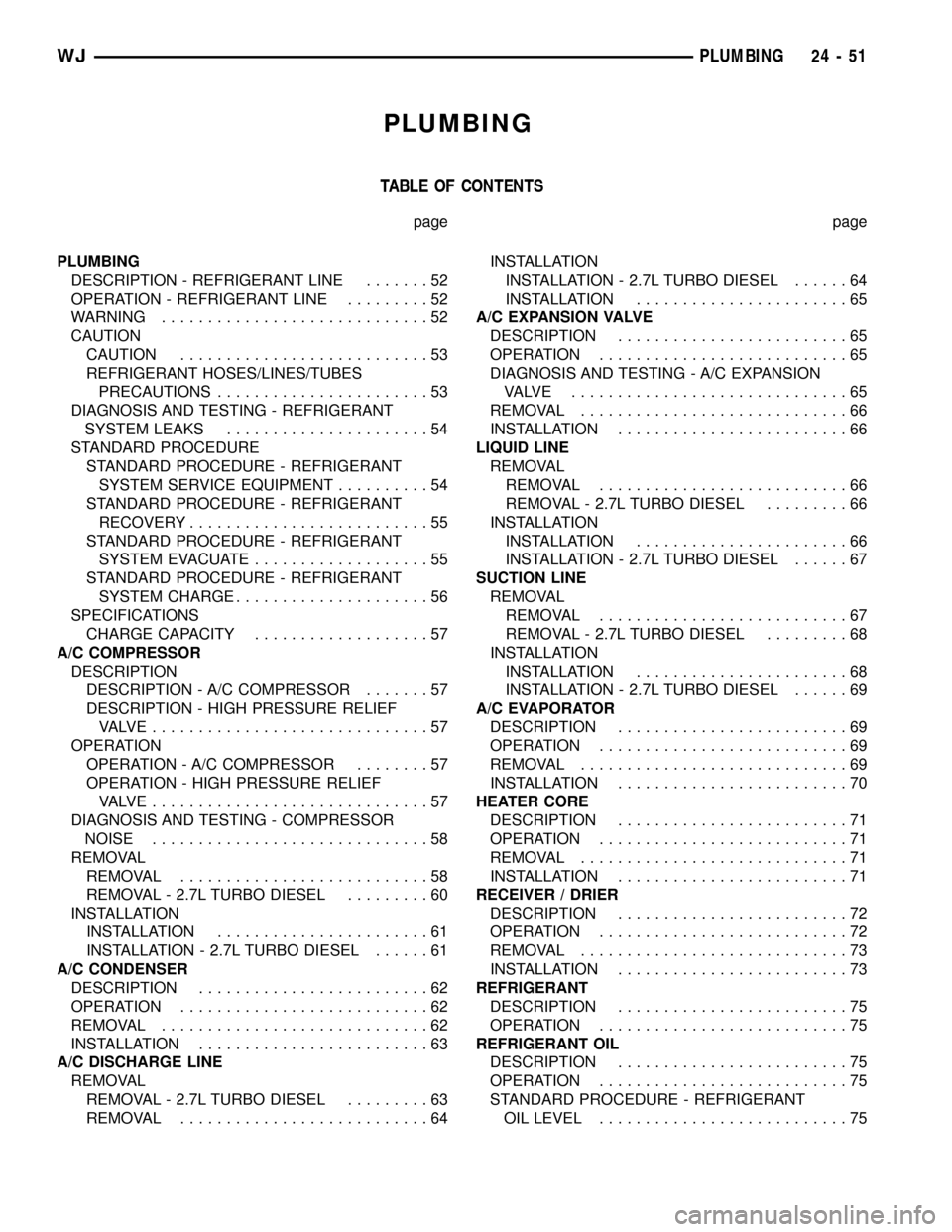
PLUMBING
TABLE OF CONTENTS
page page
PLUMBING
DESCRIPTION - REFRIGERANT LINE.......52
OPERATION - REFRIGERANT LINE.........52
WARNING.............................52
CAUTION
CAUTION...........................53
REFRIGERANT HOSES/LINES/TUBES
PRECAUTIONS.......................53
DIAGNOSIS AND TESTING - REFRIGERANT
SYSTEM LEAKS......................54
STANDARD PROCEDURE
STANDARD PROCEDURE - REFRIGERANT
SYSTEM SERVICE EQUIPMENT..........54
STANDARD PROCEDURE - REFRIGERANT
RECOVERY..........................55
STANDARD PROCEDURE - REFRIGERANT
SYSTEM EVACUATE...................55
STANDARD PROCEDURE - REFRIGERANT
SYSTEM CHARGE.....................56
SPECIFICATIONS
CHARGE CAPACITY...................57
A/C COMPRESSOR
DESCRIPTION
DESCRIPTION - A/C COMPRESSOR.......57
DESCRIPTION - HIGH PRESSURE RELIEF
VALVE..............................57
OPERATION
OPERATION - A/C COMPRESSOR........57
OPERATION - HIGH PRESSURE RELIEF
VALVE..............................57
DIAGNOSIS AND TESTING - COMPRESSOR
NOISE..............................58
REMOVAL
REMOVAL...........................58
REMOVAL - 2.7L TURBO DIESEL.........60
INSTALLATION
INSTALLATION.......................61
INSTALLATION - 2.7L TURBO DIESEL......61
A/C CONDENSER
DESCRIPTION.........................62
OPERATION...........................62
REMOVAL.............................62
INSTALLATION.........................63
A/C DISCHARGE LINE
REMOVAL
REMOVAL - 2.7L TURBO DIESEL.........63
REMOVAL...........................64INSTALLATION
INSTALLATION - 2.7L TURBO DIESEL......64
INSTALLATION.......................65
A/C EXPANSION VALVE
DESCRIPTION.........................65
OPERATION...........................65
DIAGNOSIS AND TESTING - A/C EXPANSION
VALVE ..............................65
REMOVAL.............................66
INSTALLATION.........................66
LIQUID LINE
REMOVAL
REMOVAL...........................66
REMOVAL - 2.7L TURBO DIESEL.........66
INSTALLATION
INSTALLATION.......................66
INSTALLATION - 2.7L TURBO DIESEL......67
SUCTION LINE
REMOVAL
REMOVAL...........................67
REMOVAL - 2.7L TURBO DIESEL.........68
INSTALLATION
INSTALLATION.......................68
INSTALLATION - 2.7L TURBO DIESEL......69
A/C EVAPORATOR
DESCRIPTION.........................69
OPERATION...........................69
REMOVAL.............................69
INSTALLATION.........................70
HEATER CORE
DESCRIPTION.........................71
OPERATION...........................71
REMOVAL.............................71
INSTALLATION.........................71
RECEIVER / DRIER
DESCRIPTION.........................72
OPERATION...........................72
REMOVAL.............................73
INSTALLATION.........................73
REFRIGERANT
DESCRIPTION.........................75
OPERATION...........................75
REFRIGERANT OIL
DESCRIPTION.........................75
OPERATION...........................75
STANDARD PROCEDURE - REFRIGERANT
OIL LEVEL...........................75
WJPLUMBING 24 - 51