troubleshoot JEEP GRAND CHEROKEE 2003 WJ / 2.G Workshop Manual
[x] Cancel search | Manufacturer: JEEP, Model Year: 2003, Model line: GRAND CHEROKEE, Model: JEEP GRAND CHEROKEE 2003 WJ / 2.GPages: 2199, PDF Size: 76.01 MB
Page 251 of 2199
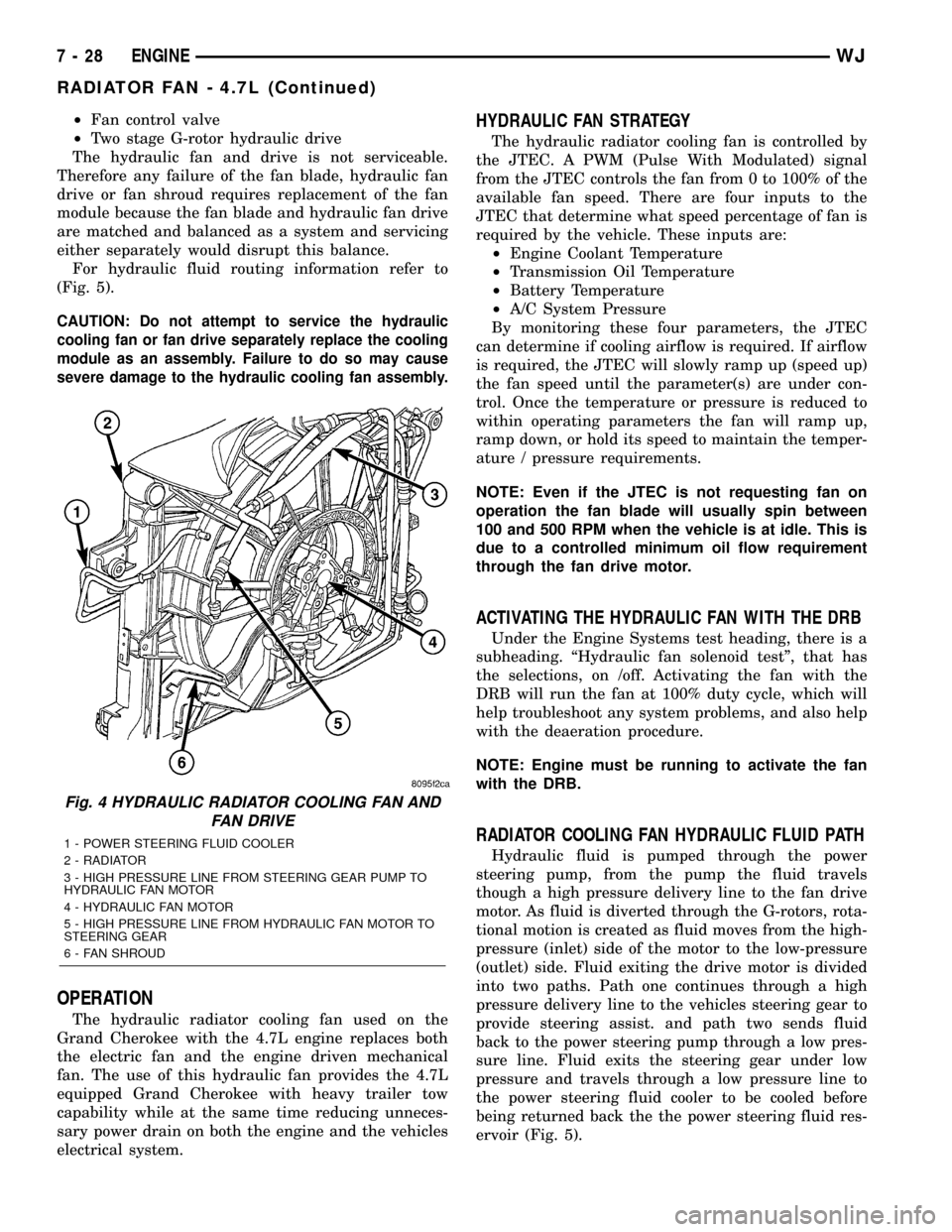
²Fan control valve
²Two stage G-rotor hydraulic drive
The hydraulic fan and drive is not serviceable.
Therefore any failure of the fan blade, hydraulic fan
drive or fan shroud requires replacement of the fan
module because the fan blade and hydraulic fan drive
are matched and balanced as a system and servicing
either separately would disrupt this balance.
For hydraulic fluid routing information refer to
(Fig. 5).
CAUTION: Do not attempt to service the hydraulic
cooling fan or fan drive separately replace the cooling
module as an assembly. Failure to do so may cause
severe damage to the hydraulic cooling fan assembly.
OPERATION
The hydraulic radiator cooling fan used on the
Grand Cherokee with the 4.7L engine replaces both
the electric fan and the engine driven mechanical
fan. The use of this hydraulic fan provides the 4.7L
equipped Grand Cherokee with heavy trailer tow
capability while at the same time reducing unneces-
sary power drain on both the engine and the vehicles
electrical system.
HYDRAULIC FAN STRATEGY
The hydraulic radiator cooling fan is controlled by
the JTEC. A PWM (Pulse With Modulated) signal
from the JTEC controls the fan from 0 to 100% of the
available fan speed. There are four inputs to the
JTEC that determine what speed percentage of fan is
required by the vehicle. These inputs are:
²Engine Coolant Temperature
²Transmission Oil Temperature
²Battery Temperature
²A/C System Pressure
By monitoring these four parameters, the JTEC
can determine if cooling airflow is required. If airflow
is required, the JTEC will slowly ramp up (speed up)
the fan speed until the parameter(s) are under con-
trol. Once the temperature or pressure is reduced to
within operating parameters the fan will ramp up,
ramp down, or hold its speed to maintain the temper-
ature / pressure requirements.
NOTE: Even if the JTEC is not requesting fan on
operation the fan blade will usually spin between
100 and 500 RPM when the vehicle is at idle. This is
due to a controlled minimum oil flow requirement
through the fan drive motor.
ACTIVATING THE HYDRAULIC FAN WITH THE DRB
Under the Engine Systems test heading, there is a
subheading. ªHydraulic fan solenoid testº, that has
the selections, on /off. Activating the fan with the
DRB will run the fan at 100% duty cycle, which will
help troubleshoot any system problems, and also help
with the deaeration procedure.
NOTE: Engine must be running to activate the fan
with the DRB.
RADIATOR COOLING FAN HYDRAULIC FLUID PATH
Hydraulic fluid is pumped through the power
steering pump, from the pump the fluid travels
though a high pressure delivery line to the fan drive
motor. As fluid is diverted through the G-rotors, rota-
tional motion is created as fluid moves from the high-
pressure (inlet) side of the motor to the low-pressure
(outlet) side. Fluid exiting the drive motor is divided
into two paths. Path one continues through a high
pressure delivery line to the vehicles steering gear to
provide steering assist. and path two sends fluid
back to the power steering pump through a low pres-
sure line. Fluid exits the steering gear under low
pressure and travels through a low pressure line to
the power steering fluid cooler to be cooled before
being returned back the the power steering fluid res-
ervoir (Fig. 5).
Fig. 4 HYDRAULIC RADIATOR COOLING FAN AND
FAN DRIVE
1 - POWER STEERING FLUID COOLER
2 - RADIATOR
3 - HIGH PRESSURE LINE FROM STEERING GEAR PUMP TO
HYDRAULIC FAN MOTOR
4 - HYDRAULIC FAN MOTOR
5 - HIGH PRESSURE LINE FROM HYDRAULIC FAN MOTOR TO
STEERING GEAR
6 - FAN SHROUD
7 - 28 ENGINEWJ
RADIATOR FAN - 4.7L (Continued)
Page 597 of 2199
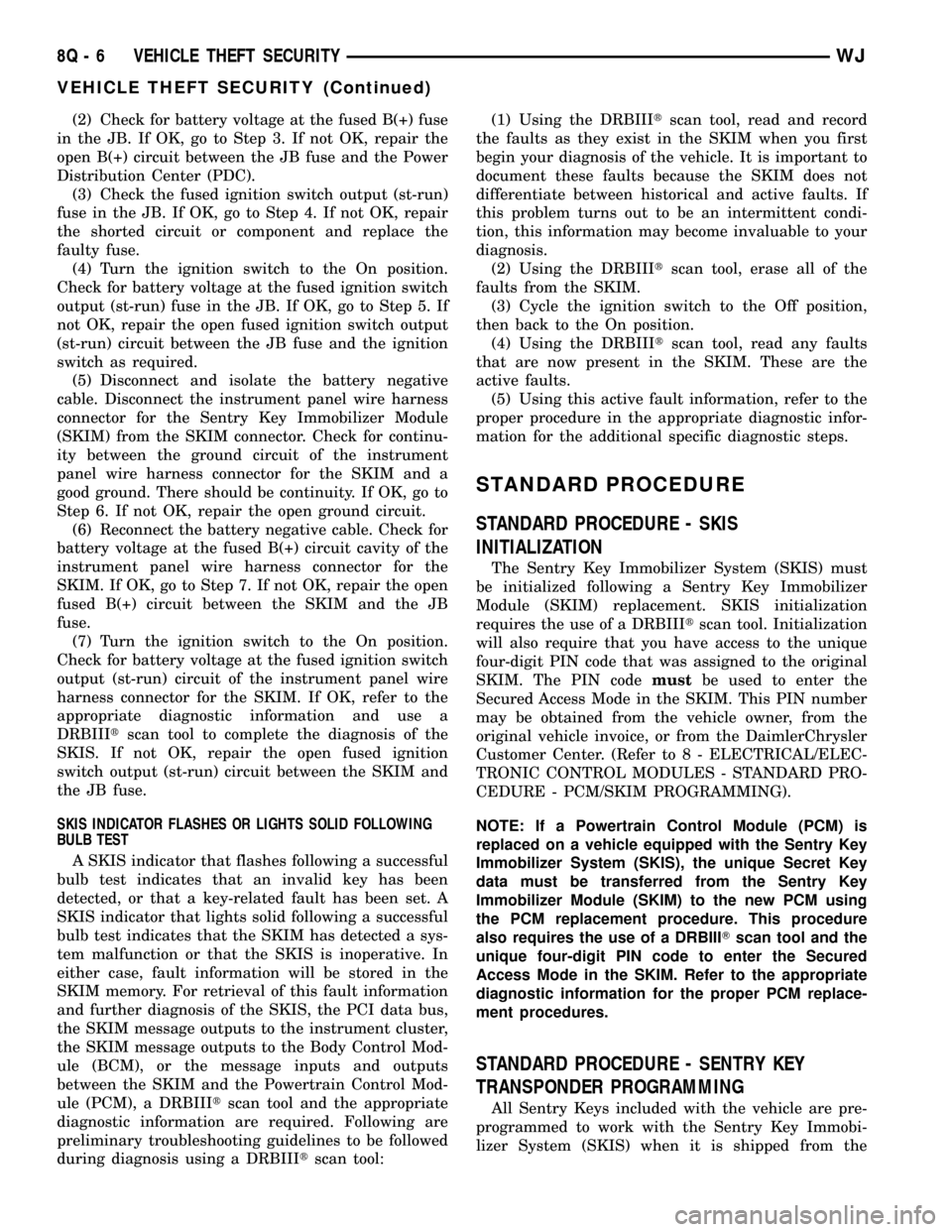
(2) Check for battery voltage at the fused B(+) fuse
in the JB. If OK, go to Step 3. If not OK, repair the
open B(+) circuit between the JB fuse and the Power
Distribution Center (PDC).
(3) Check the fused ignition switch output (st-run)
fuse in the JB. If OK, go to Step 4. If not OK, repair
the shorted circuit or component and replace the
faulty fuse.
(4) Turn the ignition switch to the On position.
Check for battery voltage at the fused ignition switch
output (st-run) fuse in the JB. If OK, go to Step 5. If
not OK, repair the open fused ignition switch output
(st-run) circuit between the JB fuse and the ignition
switch as required.
(5) Disconnect and isolate the battery negative
cable. Disconnect the instrument panel wire harness
connector for the Sentry Key Immobilizer Module
(SKIM) from the SKIM connector. Check for continu-
ity between the ground circuit of the instrument
panel wire harness connector for the SKIM and a
good ground. There should be continuity. If OK, go to
Step 6. If not OK, repair the open ground circuit.
(6) Reconnect the battery negative cable. Check for
battery voltage at the fused B(+) circuit cavity of the
instrument panel wire harness connector for the
SKIM. If OK, go to Step 7. If not OK, repair the open
fused B(+) circuit between the SKIM and the JB
fuse.
(7) Turn the ignition switch to the On position.
Check for battery voltage at the fused ignition switch
output (st-run) circuit of the instrument panel wire
harness connector for the SKIM. If OK, refer to the
appropriate diagnostic information and use a
DRBIIItscan tool to complete the diagnosis of the
SKIS. If not OK, repair the open fused ignition
switch output (st-run) circuit between the SKIM and
the JB fuse.
SKIS INDICATOR FLASHES OR LIGHTS SOLID FOLLOWING
BULB TEST
A SKIS indicator that flashes following a successful
bulb test indicates that an invalid key has been
detected, or that a key-related fault has been set. A
SKIS indicator that lights solid following a successful
bulb test indicates that the SKIM has detected a sys-
tem malfunction or that the SKIS is inoperative. In
either case, fault information will be stored in the
SKIM memory. For retrieval of this fault information
and further diagnosis of the SKIS, the PCI data bus,
the SKIM message outputs to the instrument cluster,
the SKIM message outputs to the Body Control Mod-
ule (BCM), or the message inputs and outputs
between the SKIM and the Powertrain Control Mod-
ule (PCM), a DRBIIItscan tool and the appropriate
diagnostic information are required. Following are
preliminary troubleshooting guidelines to be followed
during diagnosis using a DRBIIItscan tool:(1) Using the DRBIIItscan tool, read and record
the faults as they exist in the SKIM when you first
begin your diagnosis of the vehicle. It is important to
document these faults because the SKIM does not
differentiate between historical and active faults. If
this problem turns out to be an intermittent condi-
tion, this information may become invaluable to your
diagnosis.
(2) Using the DRBIIItscan tool, erase all of the
faults from the SKIM.
(3) Cycle the ignition switch to the Off position,
then back to the On position.
(4) Using the DRBIIItscan tool, read any faults
that are now present in the SKIM. These are the
active faults.
(5) Using this active fault information, refer to the
proper procedure in the appropriate diagnostic infor-
mation for the additional specific diagnostic steps.
STANDARD PROCEDURE
STANDARD PROCEDURE - SKIS
INITIALIZATION
The Sentry Key Immobilizer System (SKIS) must
be initialized following a Sentry Key Immobilizer
Module (SKIM) replacement. SKIS initialization
requires the use of a DRBIIItscan tool. Initialization
will also require that you have access to the unique
four-digit PIN code that was assigned to the original
SKIM. The PIN codemustbe used to enter the
Secured Access Mode in the SKIM. This PIN number
may be obtained from the vehicle owner, from the
original vehicle invoice, or from the DaimlerChrysler
Customer Center. (Refer to 8 - ELECTRICAL/ELEC-
TRONIC CONTROL MODULES - STANDARD PRO-
CEDURE - PCM/SKIM PROGRAMMING).
NOTE: If a Powertrain Control Module (PCM) is
replaced on a vehicle equipped with the Sentry Key
Immobilizer System (SKIS), the unique Secret Key
data must be transferred from the Sentry Key
Immobilizer Module (SKIM) to the new PCM using
the PCM replacement procedure. This procedure
also requires the use of a DRBIIITscan tool and the
unique four-digit PIN code to enter the Secured
Access Mode in the SKIM. Refer to the appropriate
diagnostic information for the proper PCM replace-
ment procedures.
STANDARD PROCEDURE - SENTRY KEY
TRANSPONDER PROGRAMMING
All Sentry Keys included with the vehicle are pre-
programmed to work with the Sentry Key Immobi-
lizer System (SKIS) when it is shipped from the
8Q - 6 VEHICLE THEFT SECURITYWJ
VEHICLE THEFT SECURITY (Continued)
Page 662 of 2199
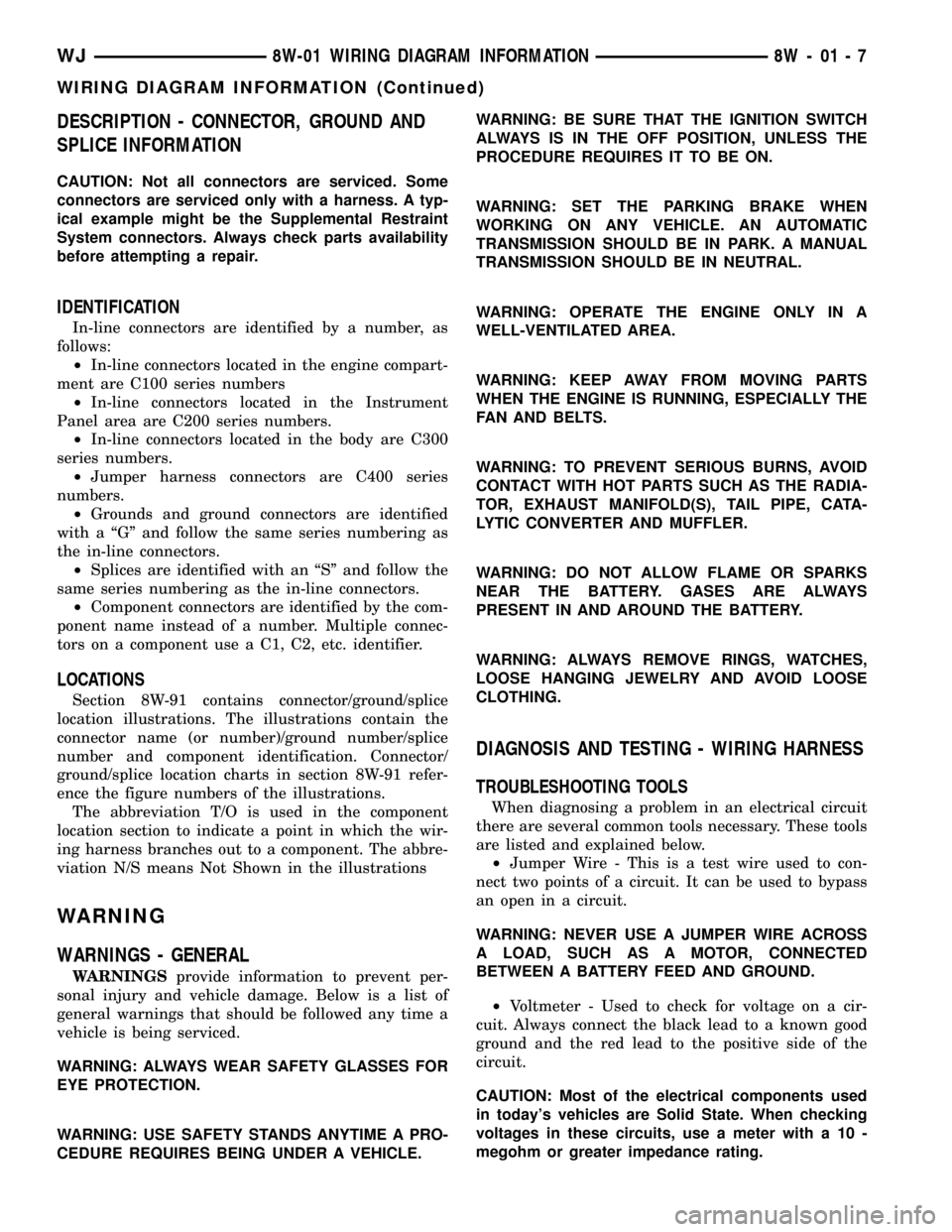
DESCRIPTION - CONNECTOR, GROUND AND
SPLICE INFORMATION
CAUTION: Not all connectors are serviced. Some
connectors are serviced only with a harness. A typ-
ical example might be the Supplemental Restraint
System connectors. Always check parts availability
before attempting a repair.
IDENTIFICATION
In-line connectors are identified by a number, as
follows:
²In-line connectors located in the engine compart-
ment are C100 series numbers
²In-line connectors located in the Instrument
Panel area are C200 series numbers.
²In-line connectors located in the body are C300
series numbers.
²Jumper harness connectors are C400 series
numbers.
²Grounds and ground connectors are identified
with a ªGº and follow the same series numbering as
the in-line connectors.
²Splices are identified with an ªSº and follow the
same series numbering as the in-line connectors.
²Component connectors are identified by the com-
ponent name instead of a number. Multiple connec-
tors on a component use a C1, C2, etc. identifier.
LOCATIONS
Section 8W-91 contains connector/ground/splice
location illustrations. The illustrations contain the
connector name (or number)/ground number/splice
number and component identification. Connector/
ground/splice location charts in section 8W-91 refer-
ence the figure numbers of the illustrations.
The abbreviation T/O is used in the component
location section to indicate a point in which the wir-
ing harness branches out to a component. The abbre-
viation N/S means Not Shown in the illustrations
WARNING
WARNINGS - GENERAL
WARNINGSprovide information to prevent per-
sonal injury and vehicle damage. Below is a list of
general warnings that should be followed any time a
vehicle is being serviced.
WARNING: ALWAYS WEAR SAFETY GLASSES FOR
EYE PROTECTION.
WARNING: USE SAFETY STANDS ANYTIME A PRO-
CEDURE REQUIRES BEING UNDER A VEHICLE.WARNING: BE SURE THAT THE IGNITION SWITCH
ALWAYS IS IN THE OFF POSITION, UNLESS THE
PROCEDURE REQUIRES IT TO BE ON.
WARNING: SET THE PARKING BRAKE WHEN
WORKING ON ANY VEHICLE. AN AUTOMATIC
TRANSMISSION SHOULD BE IN PARK. A MANUAL
TRANSMISSION SHOULD BE IN NEUTRAL.
WARNING: OPERATE THE ENGINE ONLY IN A
WELL-VENTILATED AREA.
WARNING: KEEP AWAY FROM MOVING PARTS
WHEN THE ENGINE IS RUNNING, ESPECIALLY THE
FAN AND BELTS.
WARNING: TO PREVENT SERIOUS BURNS, AVOID
CONTACT WITH HOT PARTS SUCH AS THE RADIA-
TOR, EXHAUST MANIFOLD(S), TAIL PIPE, CATA-
LYTIC CONVERTER AND MUFFLER.
WARNING: DO NOT ALLOW FLAME OR SPARKS
NEAR THE BATTERY. GASES ARE ALWAYS
PRESENT IN AND AROUND THE BATTERY.
WARNING: ALWAYS REMOVE RINGS, WATCHES,
LOOSE HANGING JEWELRY AND AVOID LOOSE
CLOTHING.
DIAGNOSIS AND TESTING - WIRING HARNESS
TROUBLESHOOTING TOOLS
When diagnosing a problem in an electrical circuit
there are several common tools necessary. These tools
are listed and explained below.
²Jumper Wire - This is a test wire used to con-
nect two points of a circuit. It can be used to bypass
an open in a circuit.
WARNING: NEVER USE A JUMPER WIRE ACROSS
A LOAD, SUCH AS A MOTOR, CONNECTED
BETWEEN A BATTERY FEED AND GROUND.
²Voltmeter - Used to check for voltage on a cir-
cuit. Always connect the black lead to a known good
ground and the red lead to the positive side of the
circuit.
CAUTION: Most of the electrical components used
in today's vehicles are Solid State. When checking
voltages in these circuits, use a meter with a 10 -
megohm or greater impedance rating.
WJ8W-01 WIRING DIAGRAM INFORMATION 8W - 01 - 7
WIRING DIAGRAM INFORMATION (Continued)
Page 663 of 2199
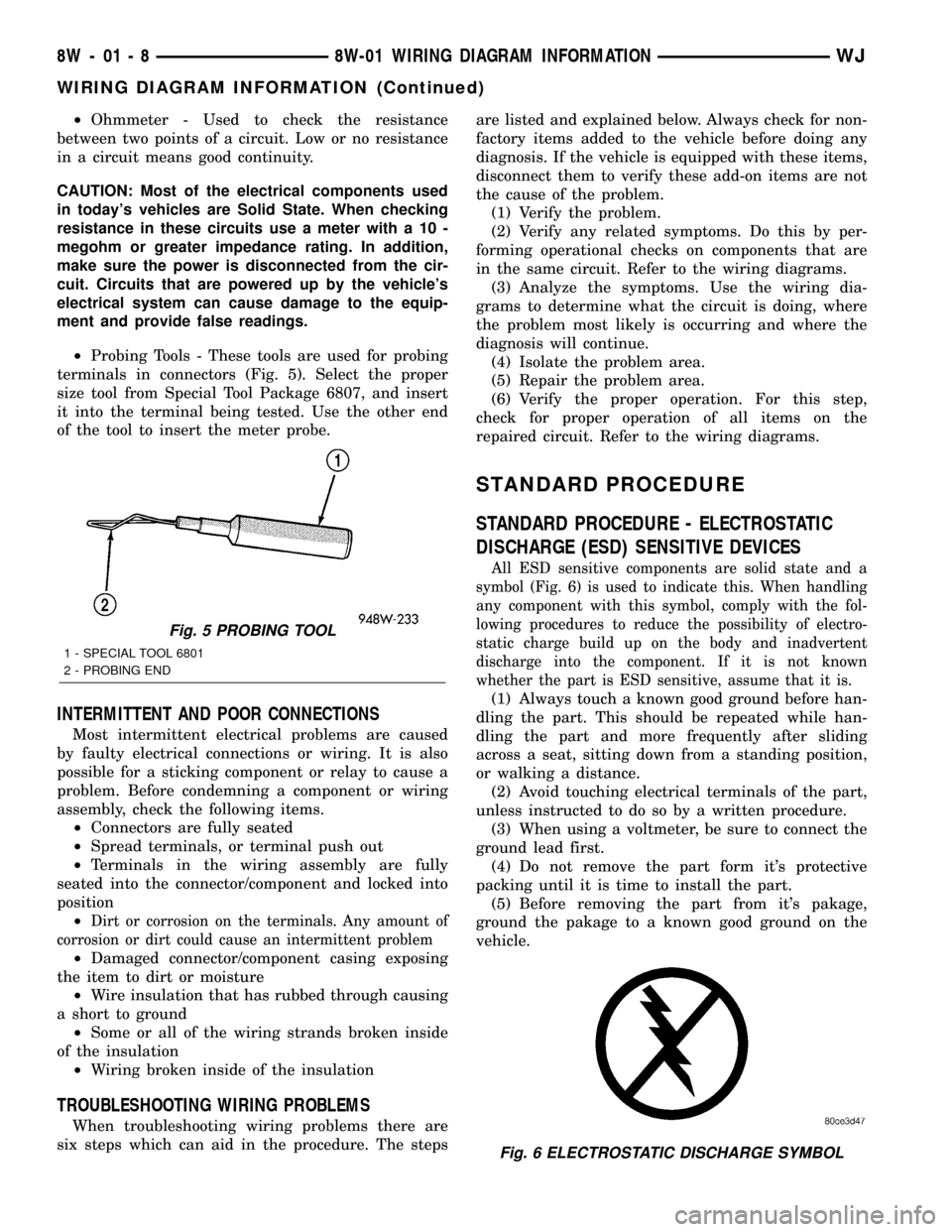
²Ohmmeter - Used to check the resistance
between two points of a circuit. Low or no resistance
in a circuit means good continuity.
CAUTION: Most of the electrical components used
in today's vehicles are Solid State. When checking
resistance in these circuits use a meter with a 10 -
megohm or greater impedance rating. In addition,
make sure the power is disconnected from the cir-
cuit. Circuits that are powered up by the vehicle's
electrical system can cause damage to the equip-
ment and provide false readings.
²Probing Tools - These tools are used for probing
terminals in connectors (Fig. 5). Select the proper
size tool from Special Tool Package 6807, and insert
it into the terminal being tested. Use the other end
of the tool to insert the meter probe.
INTERMITTENT AND POOR CONNECTIONS
Most intermittent electrical problems are caused
by faulty electrical connections or wiring. It is also
possible for a sticking component or relay to cause a
problem. Before condemning a component or wiring
assembly, check the following items.
²Connectors are fully seated
²Spread terminals, or terminal push out
²Terminals in the wiring assembly are fully
seated into the connector/component and locked into
position
²
Dirt or corrosion on the terminals. Any amount of
corrosion or dirt could cause an intermittent problem
²Damaged connector/component casing exposing
the item to dirt or moisture
²Wire insulation that has rubbed through causing
a short to ground
²Some or all of the wiring strands broken inside
of the insulation
²Wiring broken inside of the insulation
TROUBLESHOOTING WIRING PROBLEMS
When troubleshooting wiring problems there are
six steps which can aid in the procedure. The stepsare listed and explained below. Always check for non-
factory items added to the vehicle before doing any
diagnosis. If the vehicle is equipped with these items,
disconnect them to verify these add-on items are not
the cause of the problem.
(1) Verify the problem.
(2) Verify any related symptoms. Do this by per-
forming operational checks on components that are
in the same circuit. Refer to the wiring diagrams.
(3) Analyze the symptoms. Use the wiring dia-
grams to determine what the circuit is doing, where
the problem most likely is occurring and where the
diagnosis will continue.
(4) Isolate the problem area.
(5) Repair the problem area.
(6) Verify the proper operation. For this step,
check for proper operation of all items on the
repaired circuit. Refer to the wiring diagrams.
STANDARD PROCEDURE
STANDARD PROCEDURE - ELECTROSTATIC
DISCHARGE (ESD) SENSITIVE DEVICES
All ESD sensitive components are solid state and a
symbol (Fig. 6) is used to indicate this. When handling
any component with this symbol, comply with the fol-
lowing procedures to reduce the possibility of electro-
static charge build up on the body and inadvertent
discharge into the component. If it is not known
whether the part is ESD sensitive, assume that it is.
(1) Always touch a known good ground before han-
dling the part. This should be repeated while han-
dling the part and more frequently after sliding
across a seat, sitting down from a standing position,
or walking a distance.
(2) Avoid touching electrical terminals of the part,
unless instructed to do so by a written procedure.
(3) When using a voltmeter, be sure to connect the
ground lead first.
(4) Do not remove the part form it's protective
packing until it is time to install the part.
(5) Before removing the part from it's pakage,
ground the pakage to a known good ground on the
vehicle.
Fig. 5 PROBING TOOL
1 - SPECIAL TOOL 6801
2 - PROBING END
Fig. 6 ELECTROSTATIC DISCHARGE SYMBOL
8W - 01 - 8 8W-01 WIRING DIAGRAM INFORMATIONWJ
WIRING DIAGRAM INFORMATION (Continued)