hazard JEEP LIBERTY 2002 KJ / 1.G Workshop Manual
[x] Cancel search | Manufacturer: JEEP, Model Year: 2002, Model line: LIBERTY, Model: JEEP LIBERTY 2002 KJ / 1.GPages: 1803, PDF Size: 62.3 MB
Page 7 of 1803
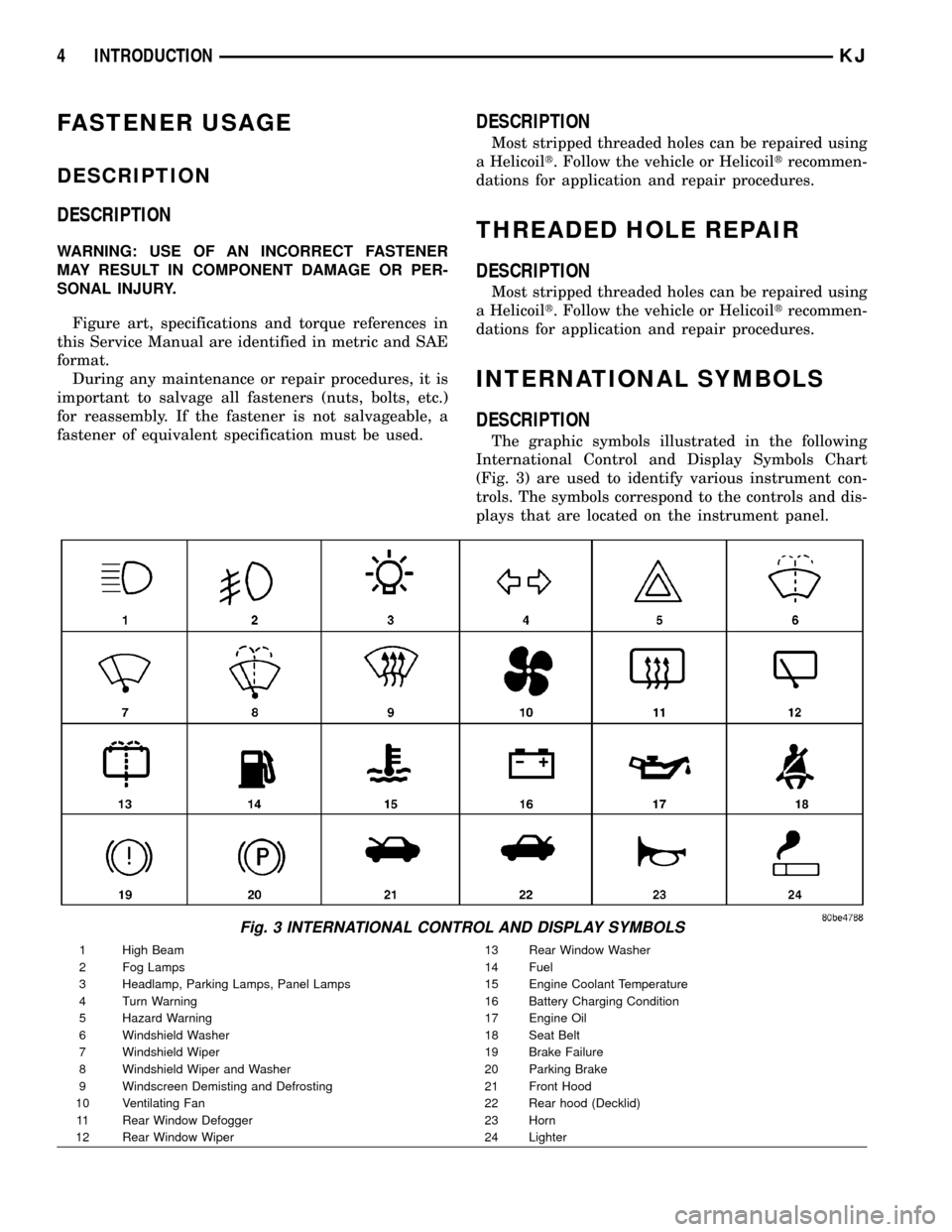
FASTENER USAGE
DESCRIPTION
DESCRIPTION
WARNING: USE OF AN INCORRECT FASTENER
MAY RESULT IN COMPONENT DAMAGE OR PER-
SONAL INJURY.
Figure art, specifications and torque references in
this Service Manual are identified in metric and SAE
format.
During any maintenance or repair procedures, it is
important to salvage all fasteners (nuts, bolts, etc.)
for reassembly. If the fastener is not salvageable, a
fastener of equivalent specification must be used.
DESCRIPTION
Most stripped threaded holes can be repaired using
a Helicoilt. Follow the vehicle or Helicoiltrecommen-
dations for application and repair procedures.
THREADED HOLE REPAIR
DESCRIPTION
Most stripped threaded holes can be repaired using
a Helicoilt. Follow the vehicle or Helicoiltrecommen-
dations for application and repair procedures.
INTERNATIONAL SYMBOLS
DESCRIPTION
The graphic symbols illustrated in the following
International Control and Display Symbols Chart
(Fig. 3) are used to identify various instrument con-
trols. The symbols correspond to the controls and dis-
plays that are located on the instrument panel.
Fig. 3 INTERNATIONAL CONTROL AND DISPLAY SYMBOLS
1 High Beam 13 Rear Window Washer
2 Fog Lamps 14 Fuel
3 Headlamp, Parking Lamps, Panel Lamps 15 Engine Coolant Temperature
4 Turn Warning 16 Battery Charging Condition
5 Hazard Warning 17 Engine Oil
6 Windshield Washer 18 Seat Belt
7 Windshield Wiper 19 Brake Failure
8 Windshield Wiper and Washer 20 Parking Brake
9 Windscreen Demisting and Defrosting 21 Front Hood
10 Ventilating Fan 22 Rear hood (Decklid)
11 Rear Window Defogger 23 Horn
12 Rear Window Wiper 24 Lighter
4 INTRODUCTIONKJ
Page 298 of 1803
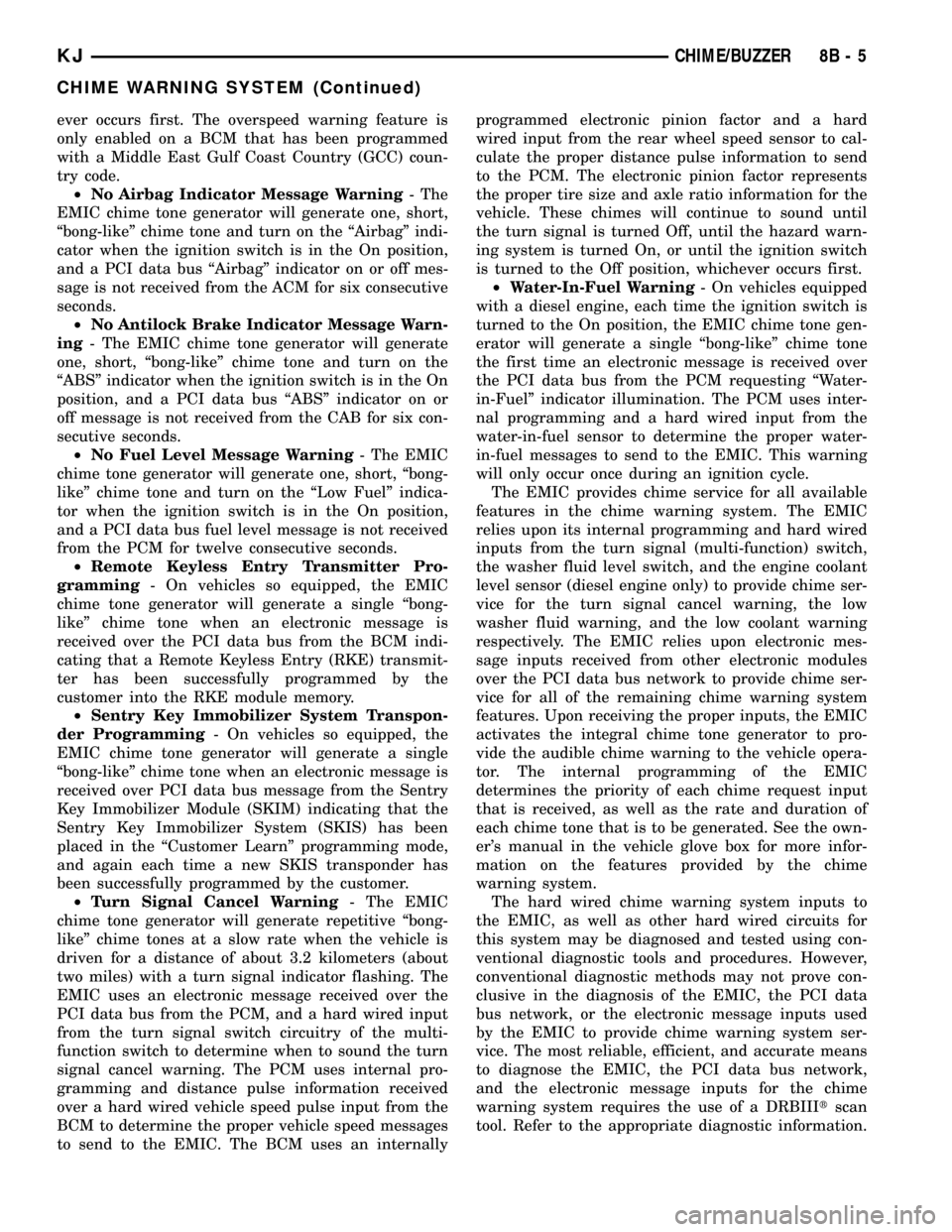
ever occurs first. The overspeed warning feature is
only enabled on a BCM that has been programmed
with a Middle East Gulf Coast Country (GCC) coun-
try code.
²No Airbag Indicator Message Warning- The
EMIC chime tone generator will generate one, short,
ªbong-likeº chime tone and turn on the ªAirbagº indi-
cator when the ignition switch is in the On position,
and a PCI data bus ªAirbagº indicator on or off mes-
sage is not received from the ACM for six consecutive
seconds.
²No Antilock Brake Indicator Message Warn-
ing- The EMIC chime tone generator will generate
one, short, ªbong-likeº chime tone and turn on the
ªABSº indicator when the ignition switch is in the On
position, and a PCI data bus ªABSº indicator on or
off message is not received from the CAB for six con-
secutive seconds.
²No Fuel Level Message Warning- The EMIC
chime tone generator will generate one, short, ªbong-
likeº chime tone and turn on the ªLow Fuelº indica-
tor when the ignition switch is in the On position,
and a PCI data bus fuel level message is not received
from the PCM for twelve consecutive seconds.
²Remote Keyless Entry Transmitter Pro-
gramming- On vehicles so equipped, the EMIC
chime tone generator will generate a single ªbong-
likeº chime tone when an electronic message is
received over the PCI data bus from the BCM indi-
cating that a Remote Keyless Entry (RKE) transmit-
ter has been successfully programmed by the
customer into the RKE module memory.
²Sentry Key Immobilizer System Transpon-
der Programming- On vehicles so equipped, the
EMIC chime tone generator will generate a single
ªbong-likeº chime tone when an electronic message is
received over PCI data bus message from the Sentry
Key Immobilizer Module (SKIM) indicating that the
Sentry Key Immobilizer System (SKIS) has been
placed in the ªCustomer Learnº programming mode,
and again each time a new SKIS transponder has
been successfully programmed by the customer.
²Turn Signal Cancel Warning- The EMIC
chime tone generator will generate repetitive ªbong-
likeº chime tones at a slow rate when the vehicle is
driven for a distance of about 3.2 kilometers (about
two miles) with a turn signal indicator flashing. The
EMIC uses an electronic message received over the
PCI data bus from the PCM, and a hard wired input
from the turn signal switch circuitry of the multi-
function switch to determine when to sound the turn
signal cancel warning. The PCM uses internal pro-
gramming and distance pulse information received
over a hard wired vehicle speed pulse input from the
BCM to determine the proper vehicle speed messages
to send to the EMIC. The BCM uses an internallyprogrammed electronic pinion factor and a hard
wired input from the rear wheel speed sensor to cal-
culate the proper distance pulse information to send
to the PCM. The electronic pinion factor represents
the proper tire size and axle ratio information for the
vehicle. These chimes will continue to sound until
the turn signal is turned Off, until the hazard warn-
ing system is turned On, or until the ignition switch
is turned to the Off position, whichever occurs first.
²Water-In-Fuel Warning- On vehicles equipped
with a diesel engine, each time the ignition switch is
turned to the On position, the EMIC chime tone gen-
erator will generate a single ªbong-likeº chime tone
the first time an electronic message is received over
the PCI data bus from the PCM requesting ªWater-
in-Fuelº indicator illumination. The PCM uses inter-
nal programming and a hard wired input from the
water-in-fuel sensor to determine the proper water-
in-fuel messages to send to the EMIC. This warning
will only occur once during an ignition cycle.
The EMIC provides chime service for all available
features in the chime warning system. The EMIC
relies upon its internal programming and hard wired
inputs from the turn signal (multi-function) switch,
the washer fluid level switch, and the engine coolant
level sensor (diesel engine only) to provide chime ser-
vice for the turn signal cancel warning, the low
washer fluid warning, and the low coolant warning
respectively. The EMIC relies upon electronic mes-
sage inputs received from other electronic modules
over the PCI data bus network to provide chime ser-
vice for all of the remaining chime warning system
features. Upon receiving the proper inputs, the EMIC
activates the integral chime tone generator to pro-
vide the audible chime warning to the vehicle opera-
tor. The internal programming of the EMIC
determines the priority of each chime request input
that is received, as well as the rate and duration of
each chime tone that is to be generated. See the own-
er's manual in the vehicle glove box for more infor-
mation on the features provided by the chime
warning system.
The hard wired chime warning system inputs to
the EMIC, as well as other hard wired circuits for
this system may be diagnosed and tested using con-
ventional diagnostic tools and procedures. However,
conventional diagnostic methods may not prove con-
clusive in the diagnosis of the EMIC, the PCI data
bus network, or the electronic message inputs used
by the EMIC to provide chime warning system ser-
vice. The most reliable, efficient, and accurate means
to diagnose the EMIC, the PCI data bus network,
and the electronic message inputs for the chime
warning system requires the use of a DRBIIItscan
tool. Refer to the appropriate diagnostic information.
KJCHIME/BUZZER 8B - 5
CHIME WARNING SYSTEM (Continued)
Page 305 of 1803
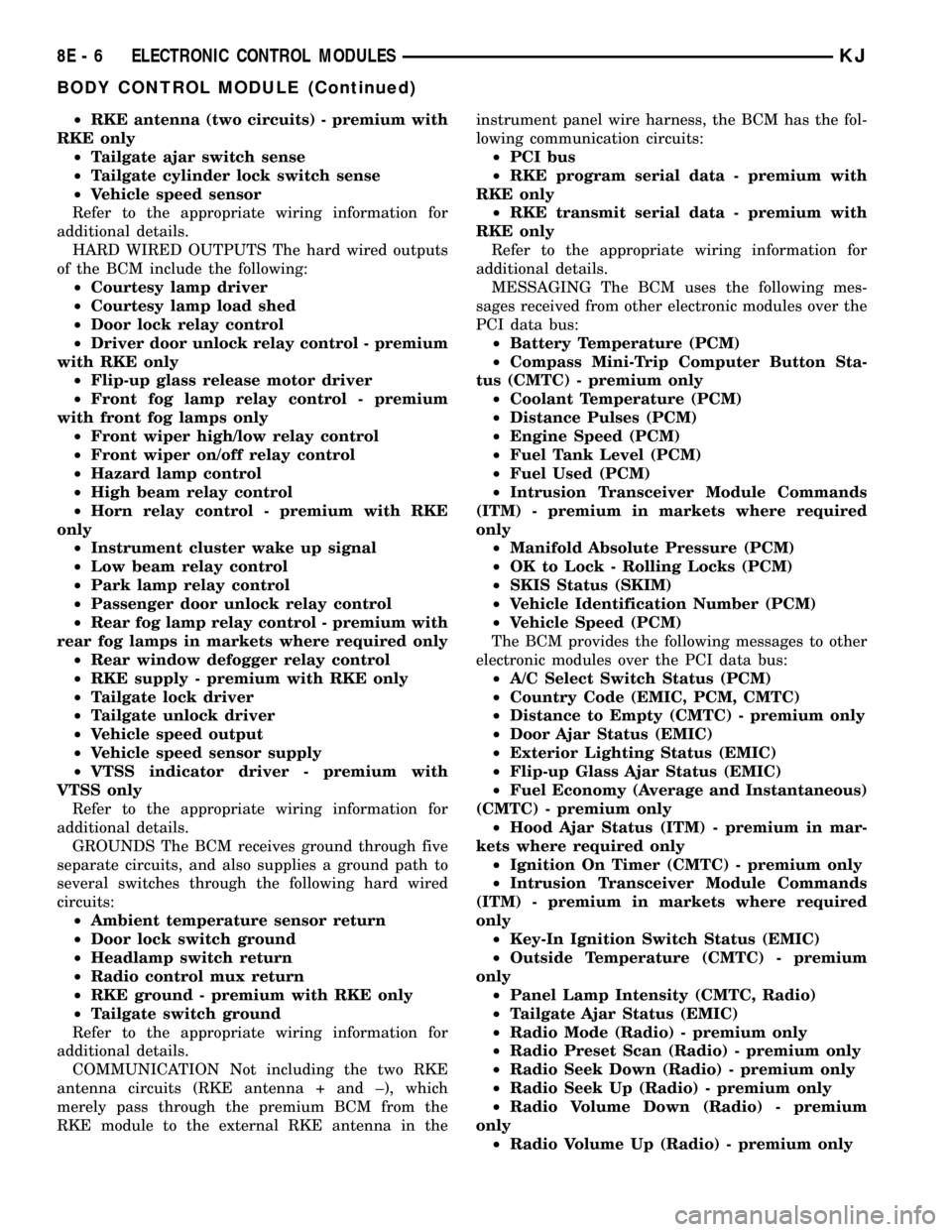
²RKE antenna (two circuits) - premium with
RKE only
²Tailgate ajar switch sense
²Tailgate cylinder lock switch sense
²Vehicle speed sensor
Refer to the appropriate wiring information for
additional details.
HARD WIRED OUTPUTS The hard wired outputs
of the BCM include the following:
²Courtesy lamp driver
²Courtesy lamp load shed
²Door lock relay control
²Driver door unlock relay control - premium
with RKE only
²Flip-up glass release motor driver
²Front fog lamp relay control - premium
with front fog lamps only
²Front wiper high/low relay control
²Front wiper on/off relay control
²Hazard lamp control
²High beam relay control
²Horn relay control - premium with RKE
only
²Instrument cluster wake up signal
²Low beam relay control
²Park lamp relay control
²Passenger door unlock relay control
²Rear fog lamp relay control - premium with
rear fog lamps in markets where required only
²Rear window defogger relay control
²RKE supply - premium with RKE only
²Tailgate lock driver
²Tailgate unlock driver
²Vehicle speed output
²Vehicle speed sensor supply
²VTSS indicator driver - premium with
VTSS only
Refer to the appropriate wiring information for
additional details.
GROUNDS The BCM receives ground through five
separate circuits, and also supplies a ground path to
several switches through the following hard wired
circuits:
²Ambient temperature sensor return
²Door lock switch ground
²Headlamp switch return
²Radio control mux return
²RKE ground - premium with RKE only
²Tailgate switch ground
Refer to the appropriate wiring information for
additional details.
COMMUNICATION Not including the two RKE
antenna circuits (RKE antenna + and ±), which
merely pass through the premium BCM from the
RKE module to the external RKE antenna in theinstrument panel wire harness, the BCM has the fol-
lowing communication circuits:
²PCI bus
²RKE program serial data - premium with
RKE only
²RKE transmit serial data - premium with
RKE only
Refer to the appropriate wiring information for
additional details.
MESSAGING The BCM uses the following mes-
sages received from other electronic modules over the
PCI data bus:
²Battery Temperature (PCM)
²Compass Mini-Trip Computer Button Sta-
tus (CMTC) - premium only
²Coolant Temperature (PCM)
²Distance Pulses (PCM)
²Engine Speed (PCM)
²Fuel Tank Level (PCM)
²Fuel Used (PCM)
²Intrusion Transceiver Module Commands
(ITM) - premium in markets where required
only
²Manifold Absolute Pressure (PCM)
²OK to Lock - Rolling Locks (PCM)
²SKIS Status (SKIM)
²Vehicle Identification Number (PCM)
²Vehicle Speed (PCM)
The BCM provides the following messages to other
electronic modules over the PCI data bus:
²A/C Select Switch Status (PCM)
²Country Code (EMIC, PCM, CMTC)
²Distance to Empty (CMTC) - premium only
²Door Ajar Status (EMIC)
²Exterior Lighting Status (EMIC)
²Flip-up Glass Ajar Status (EMIC)
²Fuel Economy (Average and Instantaneous)
(CMTC) - premium only
²Hood Ajar Status (ITM) - premium in mar-
kets where required only
²Ignition On Timer (CMTC) - premium only
²Intrusion Transceiver Module Commands
(ITM) - premium in markets where required
only
²Key-In Ignition Switch Status (EMIC)
²Outside Temperature (CMTC) - premium
only
²Panel Lamp Intensity (CMTC, Radio)
²Tailgate Ajar Status (EMIC)
²Radio Mode (Radio) - premium only
²Radio Preset Scan (Radio) - premium only
²Radio Seek Down (Radio) - premium only
²Radio Seek Up (Radio) - premium only
²Radio Volume Down (Radio) - premium
only
²Radio Volume Up (Radio) - premium only
8E - 6 ELECTRONIC CONTROL MODULESKJ
BODY CONTROL MODULE (Continued)
Page 437 of 1803
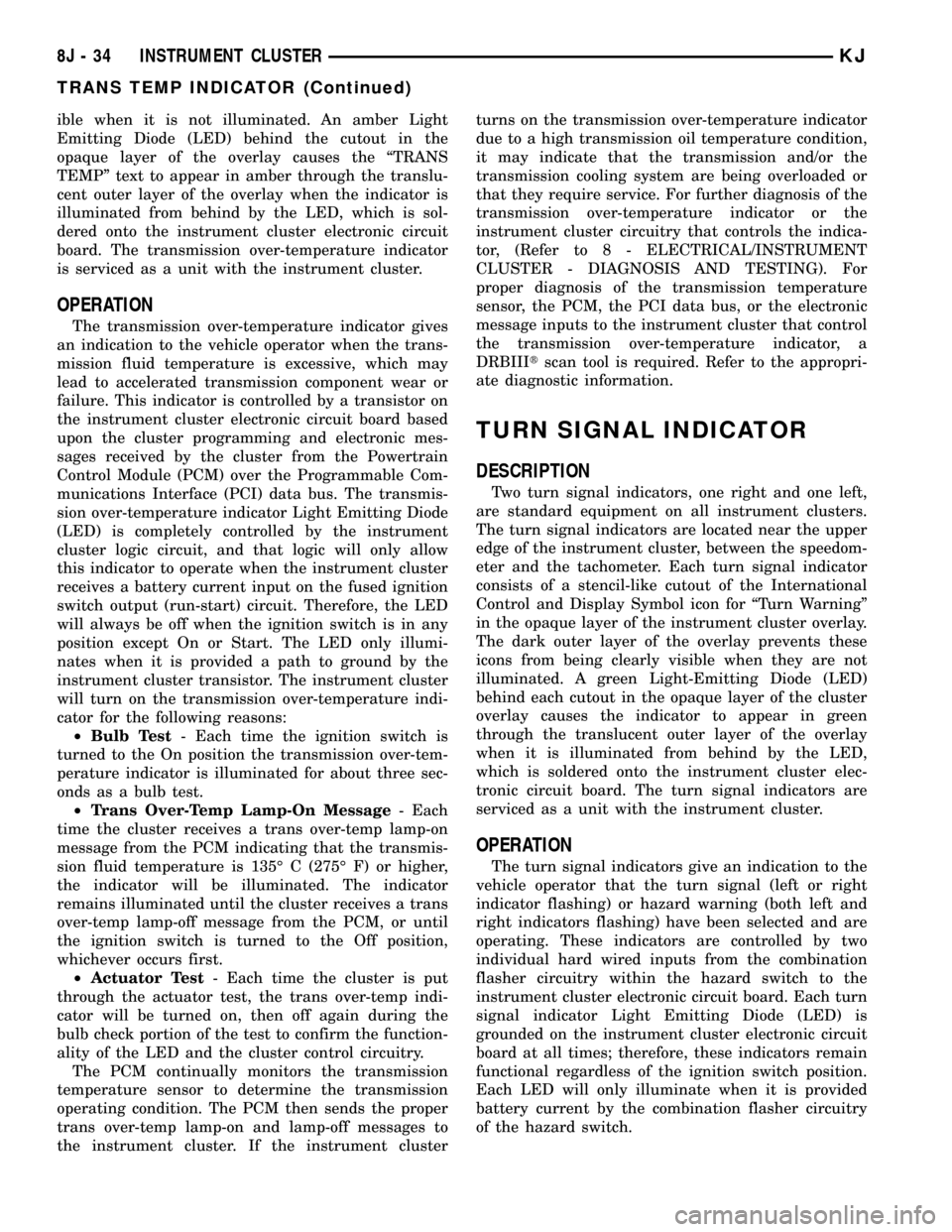
ible when it is not illuminated. An amber Light
Emitting Diode (LED) behind the cutout in the
opaque layer of the overlay causes the ªTRANS
TEMPº text to appear in amber through the translu-
cent outer layer of the overlay when the indicator is
illuminated from behind by the LED, which is sol-
dered onto the instrument cluster electronic circuit
board. The transmission over-temperature indicator
is serviced as a unit with the instrument cluster.
OPERATION
The transmission over-temperature indicator gives
an indication to the vehicle operator when the trans-
mission fluid temperature is excessive, which may
lead to accelerated transmission component wear or
failure. This indicator is controlled by a transistor on
the instrument cluster electronic circuit board based
upon the cluster programming and electronic mes-
sages received by the cluster from the Powertrain
Control Module (PCM) over the Programmable Com-
munications Interface (PCI) data bus. The transmis-
sion over-temperature indicator Light Emitting Diode
(LED) is completely controlled by the instrument
cluster logic circuit, and that logic will only allow
this indicator to operate when the instrument cluster
receives a battery current input on the fused ignition
switch output (run-start) circuit. Therefore, the LED
will always be off when the ignition switch is in any
position except On or Start. The LED only illumi-
nates when it is provided a path to ground by the
instrument cluster transistor. The instrument cluster
will turn on the transmission over-temperature indi-
cator for the following reasons:
²Bulb Test- Each time the ignition switch is
turned to the On position the transmission over-tem-
perature indicator is illuminated for about three sec-
onds as a bulb test.
²Trans Over-Temp Lamp-On Message- Each
time the cluster receives a trans over-temp lamp-on
message from the PCM indicating that the transmis-
sion fluid temperature is 135É C (275É F) or higher,
the indicator will be illuminated. The indicator
remains illuminated until the cluster receives a trans
over-temp lamp-off message from the PCM, or until
the ignition switch is turned to the Off position,
whichever occurs first.
²Actuator Test- Each time the cluster is put
through the actuator test, the trans over-temp indi-
cator will be turned on, then off again during the
bulb check portion of the test to confirm the function-
ality of the LED and the cluster control circuitry.
The PCM continually monitors the transmission
temperature sensor to determine the transmission
operating condition. The PCM then sends the proper
trans over-temp lamp-on and lamp-off messages to
the instrument cluster. If the instrument clusterturns on the transmission over-temperature indicator
due to a high transmission oil temperature condition,
it may indicate that the transmission and/or the
transmission cooling system are being overloaded or
that they require service. For further diagnosis of the
transmission over-temperature indicator or the
instrument cluster circuitry that controls the indica-
tor, (Refer to 8 - ELECTRICAL/INSTRUMENT
CLUSTER - DIAGNOSIS AND TESTING). For
proper diagnosis of the transmission temperature
sensor, the PCM, the PCI data bus, or the electronic
message inputs to the instrument cluster that control
the transmission over-temperature indicator, a
DRBIIItscan tool is required. Refer to the appropri-
ate diagnostic information.
TURN SIGNAL INDICATOR
DESCRIPTION
Two turn signal indicators, one right and one left,
are standard equipment on all instrument clusters.
The turn signal indicators are located near the upper
edge of the instrument cluster, between the speedom-
eter and the tachometer. Each turn signal indicator
consists of a stencil-like cutout of the International
Control and Display Symbol icon for ªTurn Warningº
in the opaque layer of the instrument cluster overlay.
The dark outer layer of the overlay prevents these
icons from being clearly visible when they are not
illuminated. A green Light-Emitting Diode (LED)
behind each cutout in the opaque layer of the cluster
overlay causes the indicator to appear in green
through the translucent outer layer of the overlay
when it is illuminated from behind by the LED,
which is soldered onto the instrument cluster elec-
tronic circuit board. The turn signal indicators are
serviced as a unit with the instrument cluster.
OPERATION
The turn signal indicators give an indication to the
vehicle operator that the turn signal (left or right
indicator flashing) or hazard warning (both left and
right indicators flashing) have been selected and are
operating. These indicators are controlled by two
individual hard wired inputs from the combination
flasher circuitry within the hazard switch to the
instrument cluster electronic circuit board. Each turn
signal indicator Light Emitting Diode (LED) is
grounded on the instrument cluster electronic circuit
board at all times; therefore, these indicators remain
functional regardless of the ignition switch position.
Each LED will only illuminate when it is provided
battery current by the combination flasher circuitry
of the hazard switch.
8J - 34 INSTRUMENT CLUSTERKJ
TRANS TEMP INDICATOR (Continued)
Page 438 of 1803
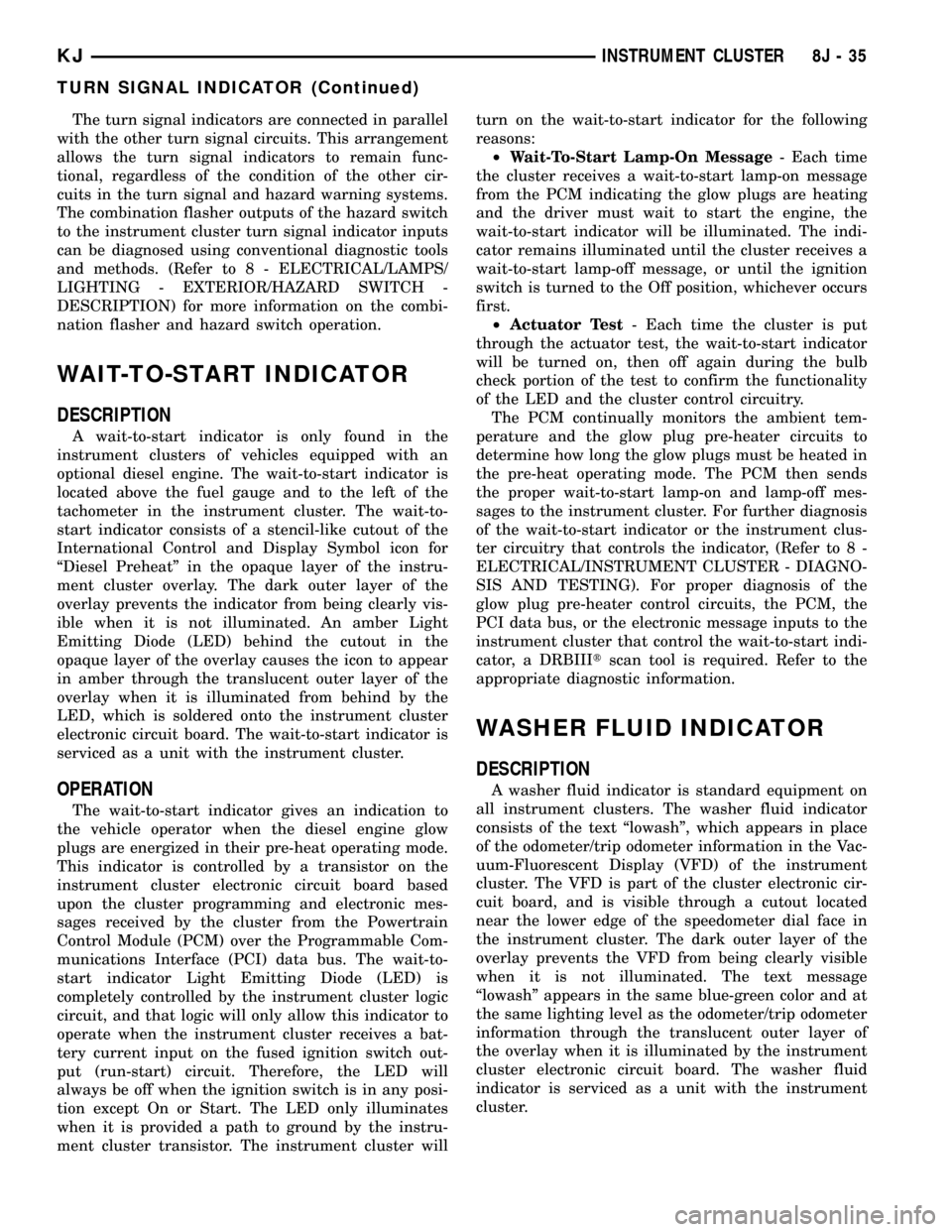
The turn signal indicators are connected in parallel
with the other turn signal circuits. This arrangement
allows the turn signal indicators to remain func-
tional, regardless of the condition of the other cir-
cuits in the turn signal and hazard warning systems.
The combination flasher outputs of the hazard switch
to the instrument cluster turn signal indicator inputs
can be diagnosed using conventional diagnostic tools
and methods. (Refer to 8 - ELECTRICAL/LAMPS/
LIGHTING - EXTERIOR/HAZARD SWITCH -
DESCRIPTION) for more information on the combi-
nation flasher and hazard switch operation.
WAIT-TO-START INDICATOR
DESCRIPTION
A wait-to-start indicator is only found in the
instrument clusters of vehicles equipped with an
optional diesel engine. The wait-to-start indicator is
located above the fuel gauge and to the left of the
tachometer in the instrument cluster. The wait-to-
start indicator consists of a stencil-like cutout of the
International Control and Display Symbol icon for
ªDiesel Preheatº in the opaque layer of the instru-
ment cluster overlay. The dark outer layer of the
overlay prevents the indicator from being clearly vis-
ible when it is not illuminated. An amber Light
Emitting Diode (LED) behind the cutout in the
opaque layer of the overlay causes the icon to appear
in amber through the translucent outer layer of the
overlay when it is illuminated from behind by the
LED, which is soldered onto the instrument cluster
electronic circuit board. The wait-to-start indicator is
serviced as a unit with the instrument cluster.
OPERATION
The wait-to-start indicator gives an indication to
the vehicle operator when the diesel engine glow
plugs are energized in their pre-heat operating mode.
This indicator is controlled by a transistor on the
instrument cluster electronic circuit board based
upon the cluster programming and electronic mes-
sages received by the cluster from the Powertrain
Control Module (PCM) over the Programmable Com-
munications Interface (PCI) data bus. The wait-to-
start indicator Light Emitting Diode (LED) is
completely controlled by the instrument cluster logic
circuit, and that logic will only allow this indicator to
operate when the instrument cluster receives a bat-
tery current input on the fused ignition switch out-
put (run-start) circuit. Therefore, the LED will
always be off when the ignition switch is in any posi-
tion except On or Start. The LED only illuminates
when it is provided a path to ground by the instru-
ment cluster transistor. The instrument cluster willturn on the wait-to-start indicator for the following
reasons:
²Wait-To-Start Lamp-On Message- Each time
the cluster receives a wait-to-start lamp-on message
from the PCM indicating the glow plugs are heating
and the driver must wait to start the engine, the
wait-to-start indicator will be illuminated. The indi-
cator remains illuminated until the cluster receives a
wait-to-start lamp-off message, or until the ignition
switch is turned to the Off position, whichever occurs
first.
²Actuator Test- Each time the cluster is put
through the actuator test, the wait-to-start indicator
will be turned on, then off again during the bulb
check portion of the test to confirm the functionality
of the LED and the cluster control circuitry.
The PCM continually monitors the ambient tem-
perature and the glow plug pre-heater circuits to
determine how long the glow plugs must be heated in
the pre-heat operating mode. The PCM then sends
the proper wait-to-start lamp-on and lamp-off mes-
sages to the instrument cluster. For further diagnosis
of the wait-to-start indicator or the instrument clus-
ter circuitry that controls the indicator, (Refer to 8 -
ELECTRICAL/INSTRUMENT CLUSTER - DIAGNO-
SIS AND TESTING). For proper diagnosis of the
glow plug pre-heater control circuits, the PCM, the
PCI data bus, or the electronic message inputs to the
instrument cluster that control the wait-to-start indi-
cator, a DRBIIItscan tool is required. Refer to the
appropriate diagnostic information.
WASHER FLUID INDICATOR
DESCRIPTION
A washer fluid indicator is standard equipment on
all instrument clusters. The washer fluid indicator
consists of the text ªlowashº, which appears in place
of the odometer/trip odometer information in the Vac-
uum-Fluorescent Display (VFD) of the instrument
cluster. The VFD is part of the cluster electronic cir-
cuit board, and is visible through a cutout located
near the lower edge of the speedometer dial face in
the instrument cluster. The dark outer layer of the
overlay prevents the VFD from being clearly visible
when it is not illuminated. The text message
ªlowashº appears in the same blue-green color and at
the same lighting level as the odometer/trip odometer
information through the translucent outer layer of
the overlay when it is illuminated by the instrument
cluster electronic circuit board. The washer fluid
indicator is serviced as a unit with the instrument
cluster.
KJINSTRUMENT CLUSTER 8J - 35
TURN SIGNAL INDICATOR (Continued)
Page 442 of 1803
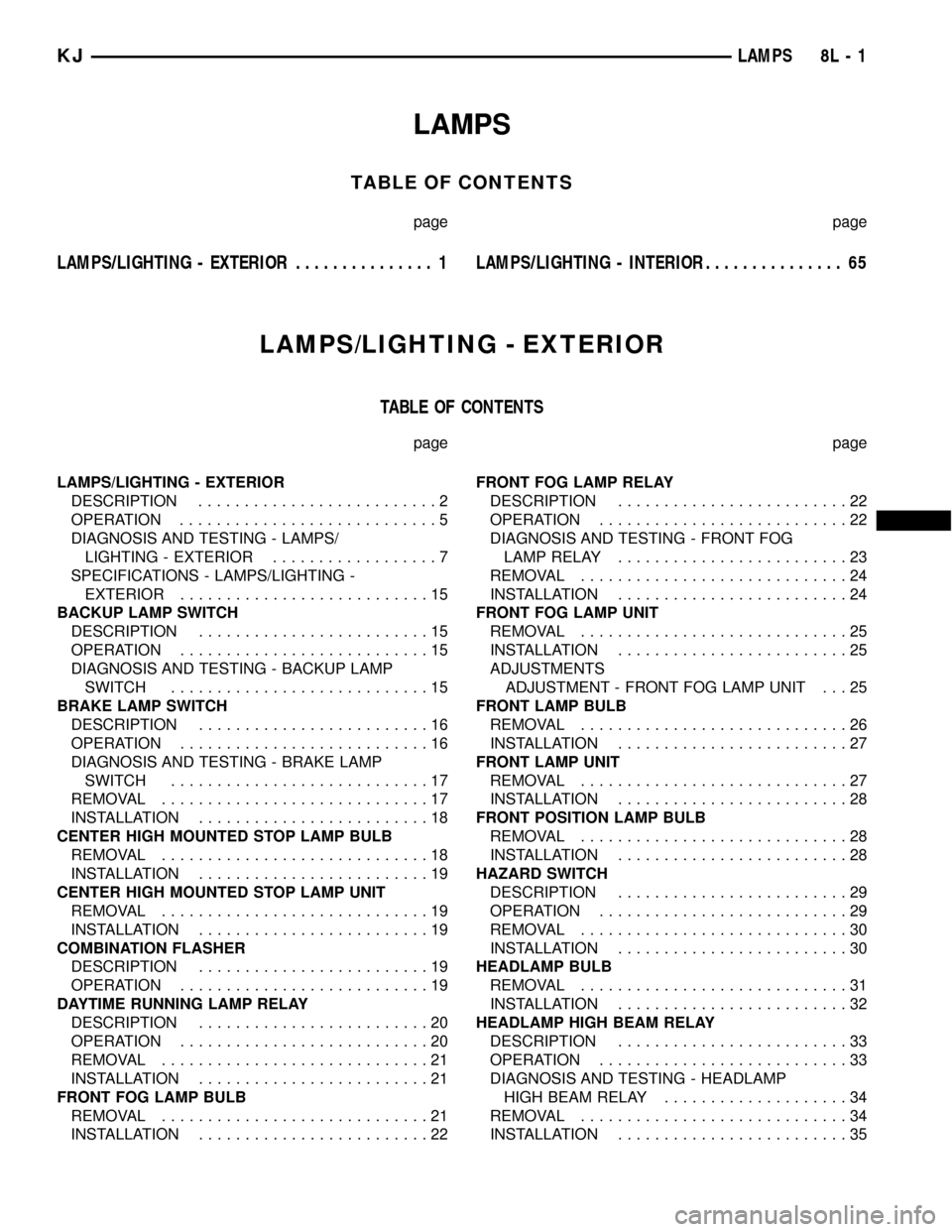
LAMPS
TABLE OF CONTENTS
page page
LAMPS/LIGHTING - EXTERIOR............... 1LAMPS/LIGHTING - INTERIOR............... 65
LAMPS/LIGHTING - EXTERIOR
TABLE OF CONTENTS
page page
LAMPS/LIGHTING - EXTERIOR
DESCRIPTION..........................2
OPERATION............................5
DIAGNOSIS AND TESTING - LAMPS/
LIGHTING - EXTERIOR..................7
SPECIFICATIONS - LAMPS/LIGHTING -
EXTERIOR...........................15
BACKUP LAMP SWITCH
DESCRIPTION.........................15
OPERATION...........................15
DIAGNOSIS AND TESTING - BACKUP LAMP
SWITCH............................15
BRAKE LAMP SWITCH
DESCRIPTION.........................16
OPERATION...........................16
DIAGNOSIS AND TESTING - BRAKE LAMP
SWITCH............................17
REMOVAL.............................17
INSTALLATION.........................18
CENTER HIGH MOUNTED STOP LAMP BULB
REMOVAL.............................18
INSTALLATION.........................19
CENTER HIGH MOUNTED STOP LAMP UNIT
REMOVAL.............................19
INSTALLATION.........................19
COMBINATION FLASHER
DESCRIPTION.........................19
OPERATION...........................19
DAYTIME RUNNING LAMP RELAY
DESCRIPTION.........................20
OPERATION...........................20
REMOVAL.............................21
INSTALLATION.........................21
FRONT FOG LAMP BULB
REMOVAL.............................21
INSTALLATION.........................22FRONT FOG LAMP RELAY
DESCRIPTION.........................22
OPERATION...........................22
DIAGNOSIS AND TESTING - FRONT FOG
LAMP RELAY.........................23
REMOVAL.............................24
INSTALLATION.........................24
FRONT FOG LAMP UNIT
REMOVAL.............................25
INSTALLATION.........................25
ADJUSTMENTS
ADJUSTMENT - FRONT FOG LAMP UNIT . . . 25
FRONT LAMP BULB
REMOVAL.............................26
INSTALLATION.........................27
FRONT LAMP UNIT
REMOVAL.............................27
INSTALLATION.........................28
FRONT POSITION LAMP BULB
REMOVAL.............................28
INSTALLATION.........................28
HAZARD SWITCH
DESCRIPTION.........................29
OPERATION...........................29
REMOVAL.............................30
INSTALLATION.........................30
HEADLAMP BULB
REMOVAL.............................31
INSTALLATION.........................32
HEADLAMP HIGH BEAM RELAY
DESCRIPTION.........................33
OPERATION...........................33
DIAGNOSIS AND TESTING - HEADLAMP
HIGH BEAM RELAY....................34
REMOVAL.............................34
INSTALLATION.........................35
KJLAMPS 8L - 1
Page 443 of 1803
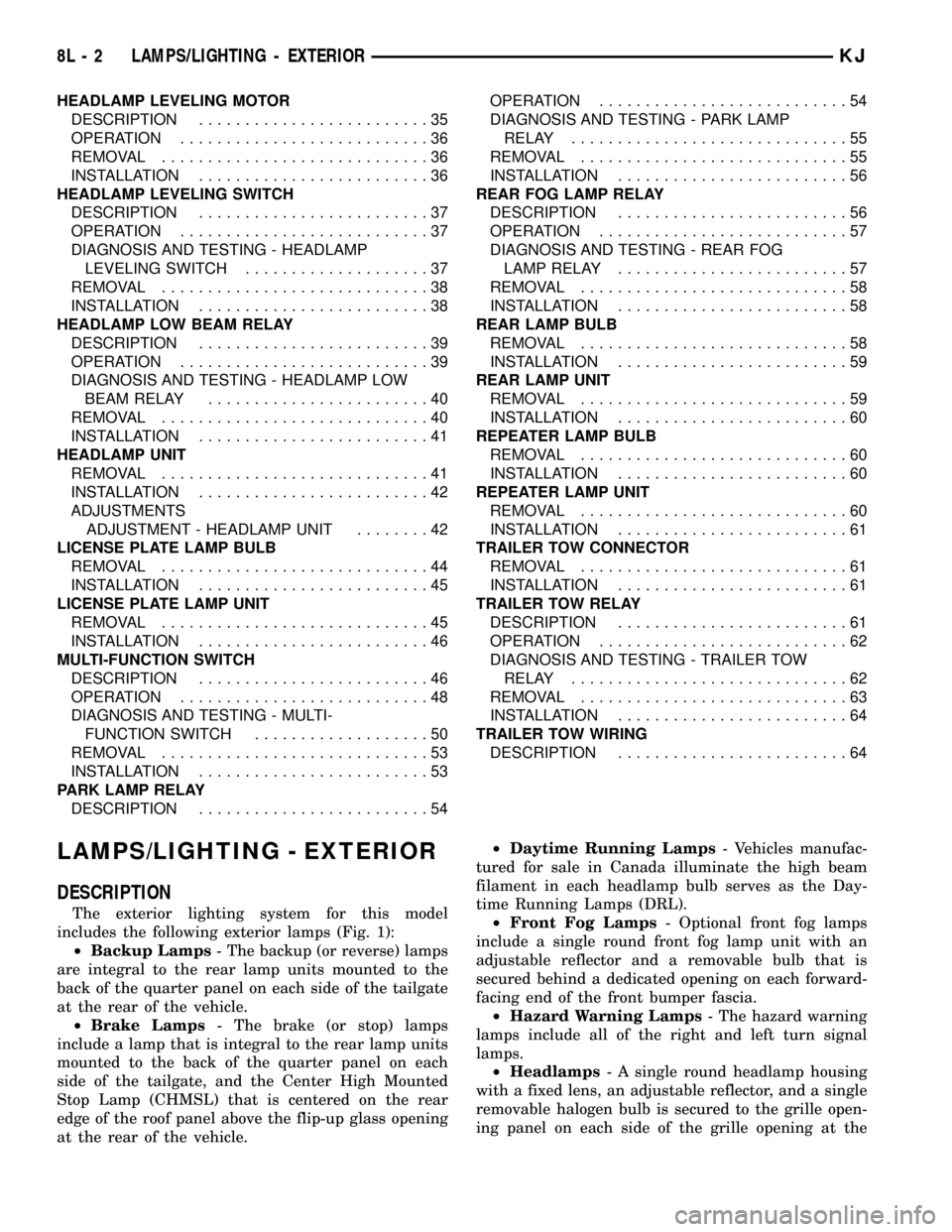
HEADLAMP LEVELING MOTOR
DESCRIPTION.........................35
OPERATION...........................36
REMOVAL.............................36
INSTALLATION.........................36
HEADLAMP LEVELING SWITCH
DESCRIPTION.........................37
OPERATION...........................37
DIAGNOSIS AND TESTING - HEADLAMP
LEVELING SWITCH....................37
REMOVAL.............................38
INSTALLATION.........................38
HEADLAMP LOW BEAM RELAY
DESCRIPTION.........................39
OPERATION...........................39
DIAGNOSIS AND TESTING - HEADLAMP LOW
BEAM RELAY........................40
REMOVAL.............................40
INSTALLATION.........................41
HEADLAMP UNIT
REMOVAL.............................41
INSTALLATION.........................42
ADJUSTMENTS
ADJUSTMENT - HEADLAMP UNIT........42
LICENSE PLATE LAMP BULB
REMOVAL.............................44
INSTALLATION.........................45
LICENSE PLATE LAMP UNIT
REMOVAL.............................45
INSTALLATION.........................46
MULTI-FUNCTION SWITCH
DESCRIPTION.........................46
OPERATION...........................48
DIAGNOSIS AND TESTING - MULTI-
FUNCTION SWITCH...................50
REMOVAL.............................53
INSTALLATION.........................53
PARK LAMP RELAY
DESCRIPTION.........................54OPERATION...........................54
DIAGNOSIS AND TESTING - PARK LAMP
RELAY..............................55
REMOVAL.............................55
INSTALLATION.........................56
REAR FOG LAMP RELAY
DESCRIPTION.........................56
OPERATION...........................57
DIAGNOSIS AND TESTING - REAR FOG
LAMP RELAY.........................57
REMOVAL.............................58
INSTALLATION.........................58
REAR LAMP BULB
REMOVAL.............................58
INSTALLATION.........................59
REAR LAMP UNIT
REMOVAL.............................59
INSTALLATION.........................60
REPEATER LAMP BULB
REMOVAL.............................60
INSTALLATION.........................60
REPEATER LAMP UNIT
REMOVAL.............................60
INSTALLATION.........................61
TRAILER TOW CONNECTOR
REMOVAL.............................61
INSTALLATION.........................61
TRAILER TOW RELAY
DESCRIPTION.........................61
OPERATION...........................62
DIAGNOSIS AND TESTING - TRAILER TOW
RELAY..............................62
REMOVAL.............................63
INSTALLATION.........................64
TRAILER TOW WIRING
DESCRIPTION.........................64
LAMPS/LIGHTING - EXTERIOR
DESCRIPTION
The exterior lighting system for this model
includes the following exterior lamps (Fig. 1):
²Backup Lamps- The backup (or reverse) lamps
are integral to the rear lamp units mounted to the
back of the quarter panel on each side of the tailgate
at the rear of the vehicle.
²Brake Lamps- The brake (or stop) lamps
include a lamp that is integral to the rear lamp units
mounted to the back of the quarter panel on each
side of the tailgate, and the Center High Mounted
Stop Lamp (CHMSL) that is centered on the rear
edge of the roof panel above the flip-up glass opening
at the rear of the vehicle.²Daytime Running Lamps- Vehicles manufac-
tured for sale in Canada illuminate the high beam
filament in each headlamp bulb serves as the Day-
time Running Lamps (DRL).
²Front Fog Lamps- Optional front fog lamps
include a single round front fog lamp unit with an
adjustable reflector and a removable bulb that is
secured behind a dedicated opening on each forward-
facing end of the front bumper fascia.
²Hazard Warning Lamps- The hazard warning
lamps include all of the right and left turn signal
lamps.
²Headlamps- A single round headlamp housing
with a fixed lens, an adjustable reflector, and a single
removable halogen bulb is secured to the grille open-
ing panel on each side of the grille opening at the
8L - 2 LAMPS/LIGHTING - EXTERIORKJ
Page 445 of 1803
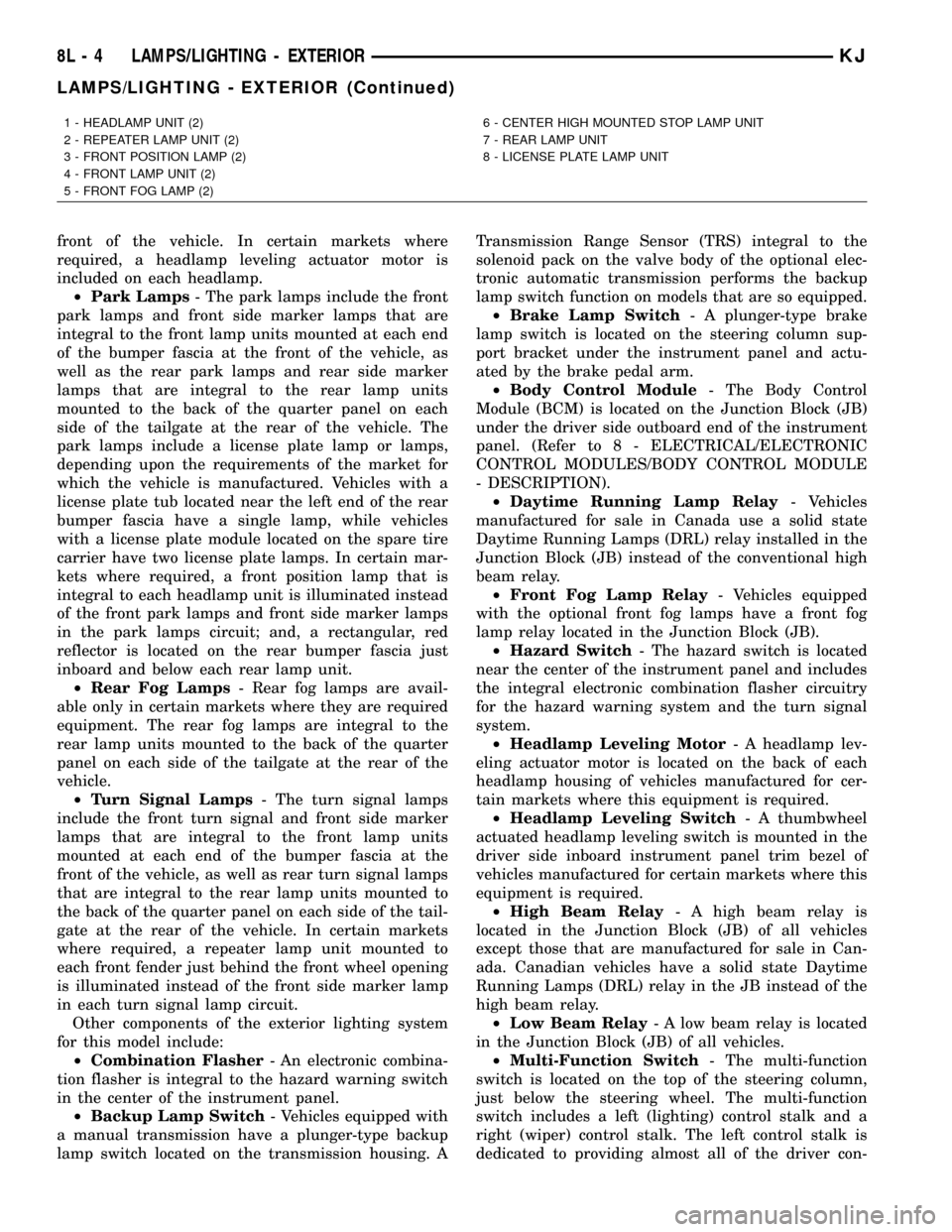
front of the vehicle. In certain markets where
required, a headlamp leveling actuator motor is
included on each headlamp.
²Park Lamps- The park lamps include the front
park lamps and front side marker lamps that are
integral to the front lamp units mounted at each end
of the bumper fascia at the front of the vehicle, as
well as the rear park lamps and rear side marker
lamps that are integral to the rear lamp units
mounted to the back of the quarter panel on each
side of the tailgate at the rear of the vehicle. The
park lamps include a license plate lamp or lamps,
depending upon the requirements of the market for
which the vehicle is manufactured. Vehicles with a
license plate tub located near the left end of the rear
bumper fascia have a single lamp, while vehicles
with a license plate module located on the spare tire
carrier have two license plate lamps. In certain mar-
kets where required, a front position lamp that is
integral to each headlamp unit is illuminated instead
of the front park lamps and front side marker lamps
in the park lamps circuit; and, a rectangular, red
reflector is located on the rear bumper fascia just
inboard and below each rear lamp unit.
²Rear Fog Lamps- Rear fog lamps are avail-
able only in certain markets where they are required
equipment. The rear fog lamps are integral to the
rear lamp units mounted to the back of the quarter
panel on each side of the tailgate at the rear of the
vehicle.
²Turn Signal Lamps- The turn signal lamps
include the front turn signal and front side marker
lamps that are integral to the front lamp units
mounted at each end of the bumper fascia at the
front of the vehicle, as well as rear turn signal lamps
that are integral to the rear lamp units mounted to
the back of the quarter panel on each side of the tail-
gate at the rear of the vehicle. In certain markets
where required, a repeater lamp unit mounted to
each front fender just behind the front wheel opening
is illuminated instead of the front side marker lamp
in each turn signal lamp circuit.
Other components of the exterior lighting system
for this model include:
²Combination Flasher- An electronic combina-
tion flasher is integral to the hazard warning switch
in the center of the instrument panel.
²Backup Lamp Switch- Vehicles equipped with
a manual transmission have a plunger-type backup
lamp switch located on the transmission housing. ATransmission Range Sensor (TRS) integral to the
solenoid pack on the valve body of the optional elec-
tronic automatic transmission performs the backup
lamp switch function on models that are so equipped.
²Brake Lamp Switch- A plunger-type brake
lamp switch is located on the steering column sup-
port bracket under the instrument panel and actu-
ated by the brake pedal arm.
²Body Control Module- The Body Control
Module (BCM) is located on the Junction Block (JB)
under the driver side outboard end of the instrument
panel. (Refer to 8 - ELECTRICAL/ELECTRONIC
CONTROL MODULES/BODY CONTROL MODULE
- DESCRIPTION).
²Daytime Running Lamp Relay- Vehicles
manufactured for sale in Canada use a solid state
Daytime Running Lamps (DRL) relay installed in the
Junction Block (JB) instead of the conventional high
beam relay.
²Front Fog Lamp Relay- Vehicles equipped
with the optional front fog lamps have a front fog
lamp relay located in the Junction Block (JB).
²Hazard Switch- The hazard switch is located
near the center of the instrument panel and includes
the integral electronic combination flasher circuitry
for the hazard warning system and the turn signal
system.
²Headlamp Leveling Motor- A headlamp lev-
eling actuator motor is located on the back of each
headlamp housing of vehicles manufactured for cer-
tain markets where this equipment is required.
²Headlamp Leveling Switch- A thumbwheel
actuated headlamp leveling switch is mounted in the
driver side inboard instrument panel trim bezel of
vehicles manufactured for certain markets where this
equipment is required.
²High Beam Relay- A high beam relay is
located in the Junction Block (JB) of all vehicles
except those that are manufactured for sale in Can-
ada. Canadian vehicles have a solid state Daytime
Running Lamps (DRL) relay in the JB instead of the
high beam relay.
²Low Beam Relay- A low beam relay is located
in the Junction Block (JB) of all vehicles.
²Multi-Function Switch- The multi-function
switch is located on the top of the steering column,
just below the steering wheel. The multi-function
switch includes a left (lighting) control stalk and a
right (wiper) control stalk. The left control stalk is
dedicated to providing almost all of the driver con-
1 - HEADLAMP UNIT (2)
2 - REPEATER LAMP UNIT (2)
3 - FRONT POSITION LAMP (2)
4 - FRONT LAMP UNIT (2)
5 - FRONT FOG LAMP (2)6 - CENTER HIGH MOUNTED STOP LAMP UNIT
7 - REAR LAMP UNIT
8 - LICENSE PLATE LAMP UNIT
8L - 4 LAMPS/LIGHTING - EXTERIORKJ
LAMPS/LIGHTING - EXTERIOR (Continued)
Page 447 of 1803
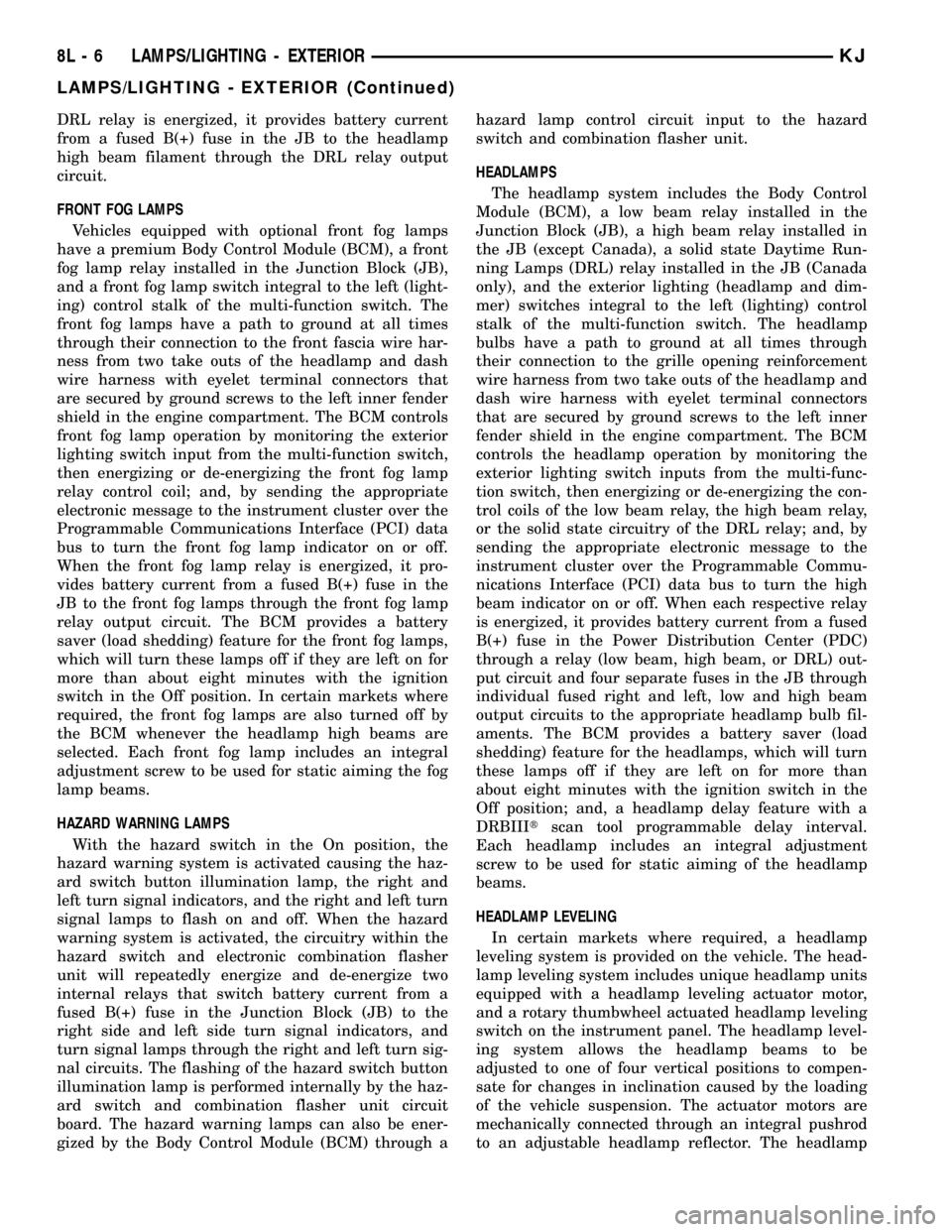
DRL relay is energized, it provides battery current
from a fused B(+) fuse in the JB to the headlamp
high beam filament through the DRL relay output
circuit.
FRONT FOG LAMPS
Vehicles equipped with optional front fog lamps
have a premium Body Control Module (BCM), a front
fog lamp relay installed in the Junction Block (JB),
and a front fog lamp switch integral to the left (light-
ing) control stalk of the multi-function switch. The
front fog lamps have a path to ground at all times
through their connection to the front fascia wire har-
ness from two take outs of the headlamp and dash
wire harness with eyelet terminal connectors that
are secured by ground screws to the left inner fender
shield in the engine compartment. The BCM controls
front fog lamp operation by monitoring the exterior
lighting switch input from the multi-function switch,
then energizing or de-energizing the front fog lamp
relay control coil; and, by sending the appropriate
electronic message to the instrument cluster over the
Programmable Communications Interface (PCI) data
bus to turn the front fog lamp indicator on or off.
When the front fog lamp relay is energized, it pro-
vides battery current from a fused B(+) fuse in the
JB to the front fog lamps through the front fog lamp
relay output circuit. The BCM provides a battery
saver (load shedding) feature for the front fog lamps,
which will turn these lamps off if they are left on for
more than about eight minutes with the ignition
switch in the Off position. In certain markets where
required, the front fog lamps are also turned off by
the BCM whenever the headlamp high beams are
selected. Each front fog lamp includes an integral
adjustment screw to be used for static aiming the fog
lamp beams.
HAZARD WARNING LAMPS
With the hazard switch in the On position, the
hazard warning system is activated causing the haz-
ard switch button illumination lamp, the right and
left turn signal indicators, and the right and left turn
signal lamps to flash on and off. When the hazard
warning system is activated, the circuitry within the
hazard switch and electronic combination flasher
unit will repeatedly energize and de-energize two
internal relays that switch battery current from a
fused B(+) fuse in the Junction Block (JB) to the
right side and left side turn signal indicators, and
turn signal lamps through the right and left turn sig-
nal circuits. The flashing of the hazard switch button
illumination lamp is performed internally by the haz-
ard switch and combination flasher unit circuit
board. The hazard warning lamps can also be ener-
gized by the Body Control Module (BCM) through ahazard lamp control circuit input to the hazard
switch and combination flasher unit.
HEADLAMPS
The headlamp system includes the Body Control
Module (BCM), a low beam relay installed in the
Junction Block (JB), a high beam relay installed in
the JB (except Canada), a solid state Daytime Run-
ning Lamps (DRL) relay installed in the JB (Canada
only), and the exterior lighting (headlamp and dim-
mer) switches integral to the left (lighting) control
stalk of the multi-function switch. The headlamp
bulbs have a path to ground at all times through
their connection to the grille opening reinforcement
wire harness from two take outs of the headlamp and
dash wire harness with eyelet terminal connectors
that are secured by ground screws to the left inner
fender shield in the engine compartment. The BCM
controls the headlamp operation by monitoring the
exterior lighting switch inputs from the multi-func-
tion switch, then energizing or de-energizing the con-
trol coils of the low beam relay, the high beam relay,
or the solid state circuitry of the DRL relay; and, by
sending the appropriate electronic message to the
instrument cluster over the Programmable Commu-
nications Interface (PCI) data bus to turn the high
beam indicator on or off. When each respective relay
is energized, it provides battery current from a fused
B(+) fuse in the Power Distribution Center (PDC)
through a relay (low beam, high beam, or DRL) out-
put circuit and four separate fuses in the JB through
individual fused right and left, low and high beam
output circuits to the appropriate headlamp bulb fil-
aments. The BCM provides a battery saver (load
shedding) feature for the headlamps, which will turn
these lamps off if they are left on for more than
about eight minutes with the ignition switch in the
Off position; and, a headlamp delay feature with a
DRBIIItscan tool programmable delay interval.
Each headlamp includes an integral adjustment
screw to be used for static aiming of the headlamp
beams.
HEADLAMP LEVELING
In certain markets where required, a headlamp
leveling system is provided on the vehicle. The head-
lamp leveling system includes unique headlamp units
equipped with a headlamp leveling actuator motor,
and a rotary thumbwheel actuated headlamp leveling
switch on the instrument panel. The headlamp level-
ing system allows the headlamp beams to be
adjusted to one of four vertical positions to compen-
sate for changes in inclination caused by the loading
of the vehicle suspension. The actuator motors are
mechanically connected through an integral pushrod
to an adjustable headlamp reflector. The headlamp
8L - 6 LAMPS/LIGHTING - EXTERIORKJ
LAMPS/LIGHTING - EXTERIOR (Continued)
Page 448 of 1803
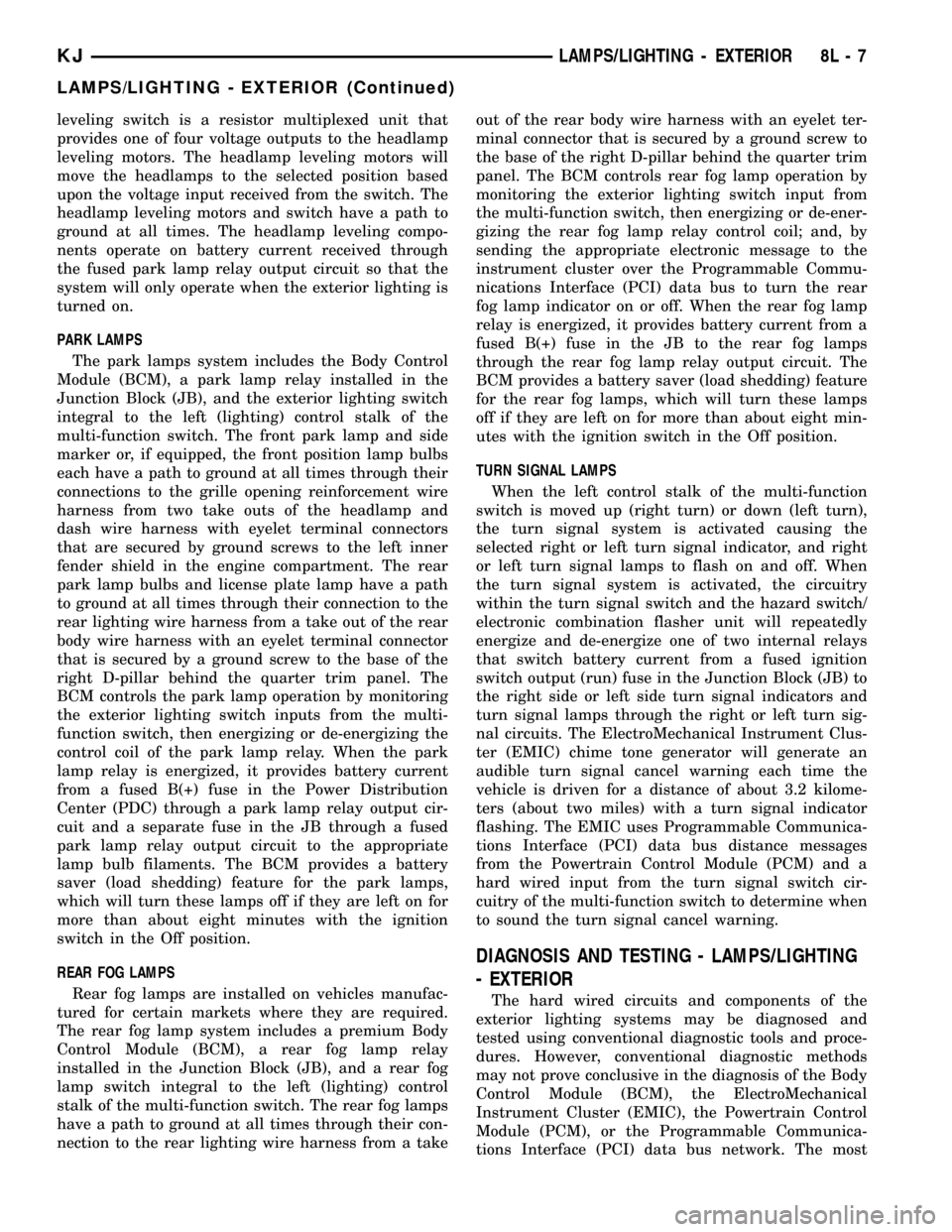
leveling switch is a resistor multiplexed unit that
provides one of four voltage outputs to the headlamp
leveling motors. The headlamp leveling motors will
move the headlamps to the selected position based
upon the voltage input received from the switch. The
headlamp leveling motors and switch have a path to
ground at all times. The headlamp leveling compo-
nents operate on battery current received through
the fused park lamp relay output circuit so that the
system will only operate when the exterior lighting is
turned on.
PARK LAMPS
The park lamps system includes the Body Control
Module (BCM), a park lamp relay installed in the
Junction Block (JB), and the exterior lighting switch
integral to the left (lighting) control stalk of the
multi-function switch. The front park lamp and side
marker or, if equipped, the front position lamp bulbs
each have a path to ground at all times through their
connections to the grille opening reinforcement wire
harness from two take outs of the headlamp and
dash wire harness with eyelet terminal connectors
that are secured by ground screws to the left inner
fender shield in the engine compartment. The rear
park lamp bulbs and license plate lamp have a path
to ground at all times through their connection to the
rear lighting wire harness from a take out of the rear
body wire harness with an eyelet terminal connector
that is secured by a ground screw to the base of the
right D-pillar behind the quarter trim panel. The
BCM controls the park lamp operation by monitoring
the exterior lighting switch inputs from the multi-
function switch, then energizing or de-energizing the
control coil of the park lamp relay. When the park
lamp relay is energized, it provides battery current
from a fused B(+) fuse in the Power Distribution
Center (PDC) through a park lamp relay output cir-
cuit and a separate fuse in the JB through a fused
park lamp relay output circuit to the appropriate
lamp bulb filaments. The BCM provides a battery
saver (load shedding) feature for the park lamps,
which will turn these lamps off if they are left on for
more than about eight minutes with the ignition
switch in the Off position.
REAR FOG LAMPS
Rear fog lamps are installed on vehicles manufac-
tured for certain markets where they are required.
The rear fog lamp system includes a premium Body
Control Module (BCM), a rear fog lamp relay
installed in the Junction Block (JB), and a rear fog
lamp switch integral to the left (lighting) control
stalk of the multi-function switch. The rear fog lamps
have a path to ground at all times through their con-
nection to the rear lighting wire harness from a takeout of the rear body wire harness with an eyelet ter-
minal connector that is secured by a ground screw to
the base of the right D-pillar behind the quarter trim
panel. The BCM controls rear fog lamp operation by
monitoring the exterior lighting switch input from
the multi-function switch, then energizing or de-ener-
gizing the rear fog lamp relay control coil; and, by
sending the appropriate electronic message to the
instrument cluster over the Programmable Commu-
nications Interface (PCI) data bus to turn the rear
fog lamp indicator on or off. When the rear fog lamp
relay is energized, it provides battery current from a
fused B(+) fuse in the JB to the rear fog lamps
through the rear fog lamp relay output circuit. The
BCM provides a battery saver (load shedding) feature
for the rear fog lamps, which will turn these lamps
off if they are left on for more than about eight min-
utes with the ignition switch in the Off position.
TURN SIGNAL LAMPS
When the left control stalk of the multi-function
switch is moved up (right turn) or down (left turn),
the turn signal system is activated causing the
selected right or left turn signal indicator, and right
or left turn signal lamps to flash on and off. When
the turn signal system is activated, the circuitry
within the turn signal switch and the hazard switch/
electronic combination flasher unit will repeatedly
energize and de-energize one of two internal relays
that switch battery current from a fused ignition
switch output (run) fuse in the Junction Block (JB) to
the right side or left side turn signal indicators and
turn signal lamps through the right or left turn sig-
nal circuits. The ElectroMechanical Instrument Clus-
ter (EMIC) chime tone generator will generate an
audible turn signal cancel warning each time the
vehicle is driven for a distance of about 3.2 kilome-
ters (about two miles) with a turn signal indicator
flashing. The EMIC uses Programmable Communica-
tions Interface (PCI) data bus distance messages
from the Powertrain Control Module (PCM) and a
hard wired input from the turn signal switch cir-
cuitry of the multi-function switch to determine when
to sound the turn signal cancel warning.
DIAGNOSIS AND TESTING - LAMPS/LIGHTING
- EXTERIOR
The hard wired circuits and components of the
exterior lighting systems may be diagnosed and
tested using conventional diagnostic tools and proce-
dures. However, conventional diagnostic methods
may not prove conclusive in the diagnosis of the Body
Control Module (BCM), the ElectroMechanical
Instrument Cluster (EMIC), the Powertrain Control
Module (PCM), or the Programmable Communica-
tions Interface (PCI) data bus network. The most
KJLAMPS/LIGHTING - EXTERIOR 8L - 7
LAMPS/LIGHTING - EXTERIOR (Continued)