JEEP XJ 1995 Service And Repair Manual
Manufacturer: JEEP, Model Year: 1995, Model line: XJ, Model: JEEP XJ 1995Pages: 2158, PDF Size: 81.9 MB
Page 1611 of 2158
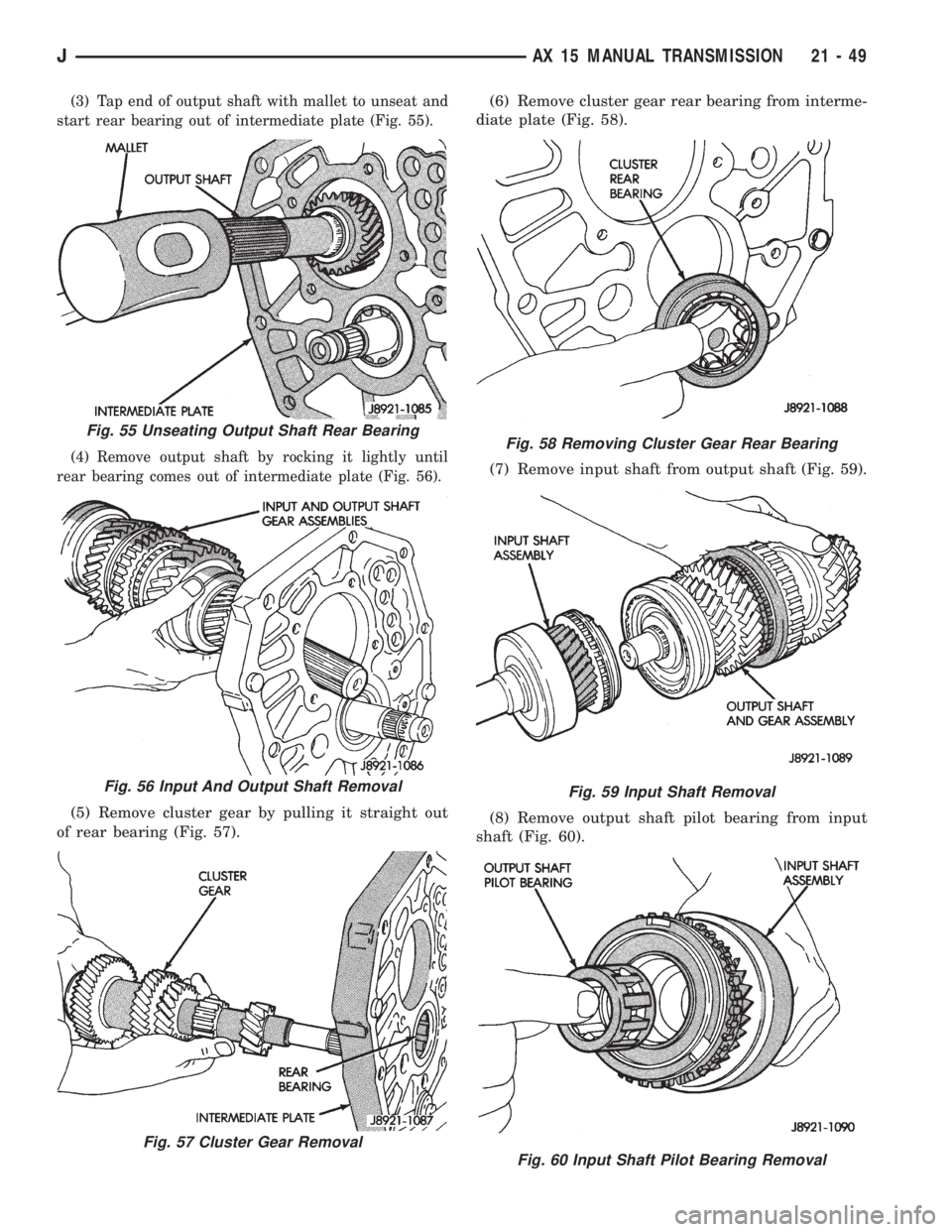
(3) Tap end of output shaft with mallet to unseat and
start rear bearing out of intermediate plate (Fig. 55).
(4) Remove output shaft by rocking it lightly until
rear bearing comes out of intermediate plate (Fig. 56).
(5) Remove cluster gear by pulling it straight out
of rear bearing (Fig. 57).(6) Remove cluster gear rear bearing from interme-
diate plate (Fig. 58).
(7) Remove input shaft from output shaft (Fig. 59).
(8) Remove output shaft pilot bearing from input
shaft (Fig. 60).
Fig. 55 Unseating Output Shaft Rear Bearing
Fig. 56 Input And Output Shaft Removal
Fig. 57 Cluster Gear Removal
Fig. 58 Removing Cluster Gear Rear Bearing
Fig. 59 Input Shaft Removal
Fig. 60 Input Shaft Pilot Bearing Removal
JAX 15 MANUAL TRANSMISSION 21 - 49
Page 1612 of 2158
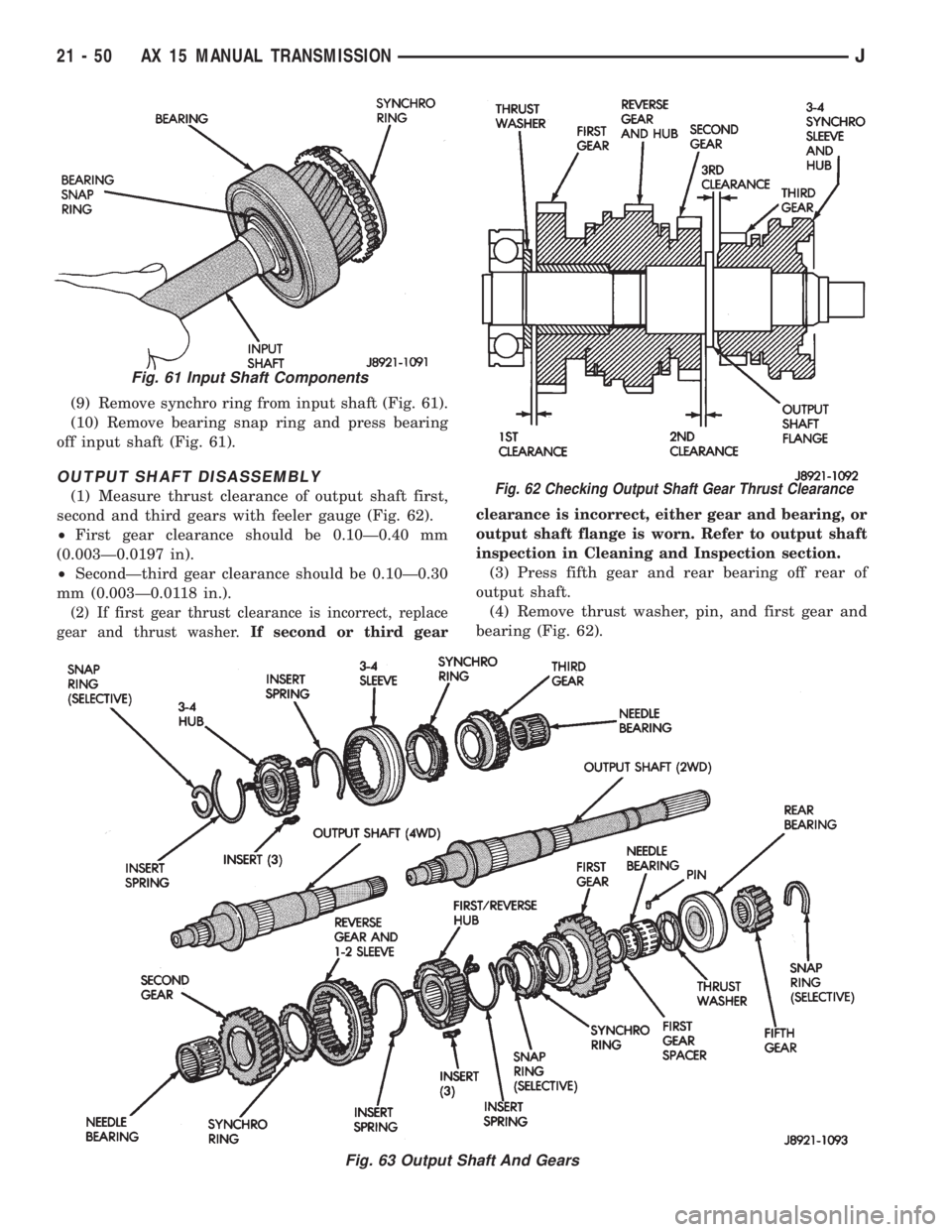
(9) Remove synchro ring from input shaft (Fig. 61).
(10) Remove bearing snap ring and press bearing
off input shaft (Fig. 61).
OUTPUT SHAFT DISASSEMBLY
(1) Measure thrust clearance of output shaft first,
second and third gears with feeler gauge (Fig. 62).
²First gear clearance should be 0.10Ð0.40 mm
(0.003Ð0.0197 in).
²SecondÐthird gear clearance should be 0.10Ð0.30
mm (0.003Ð0.0118 in.).
(2) If first gear thrust clearance is incorrect, replace
gear and thrust washer.If second or third gearclearance is incorrect, either gear and bearing, or
output shaft flange is worn. Refer to output shaft
inspection in Cleaning and Inspection section.
(3) Press fifth gear and rear bearing off rear of
output shaft.
(4) Remove thrust washer, pin, and first gear and
bearing (Fig. 62).
Fig. 61 Input Shaft Components
Fig. 62 Checking Output Shaft Gear Thrust Clearance
Fig. 63 Output Shaft And Gears
21 - 50 AX 15 MANUAL TRANSMISSIONJ
Page 1613 of 2158
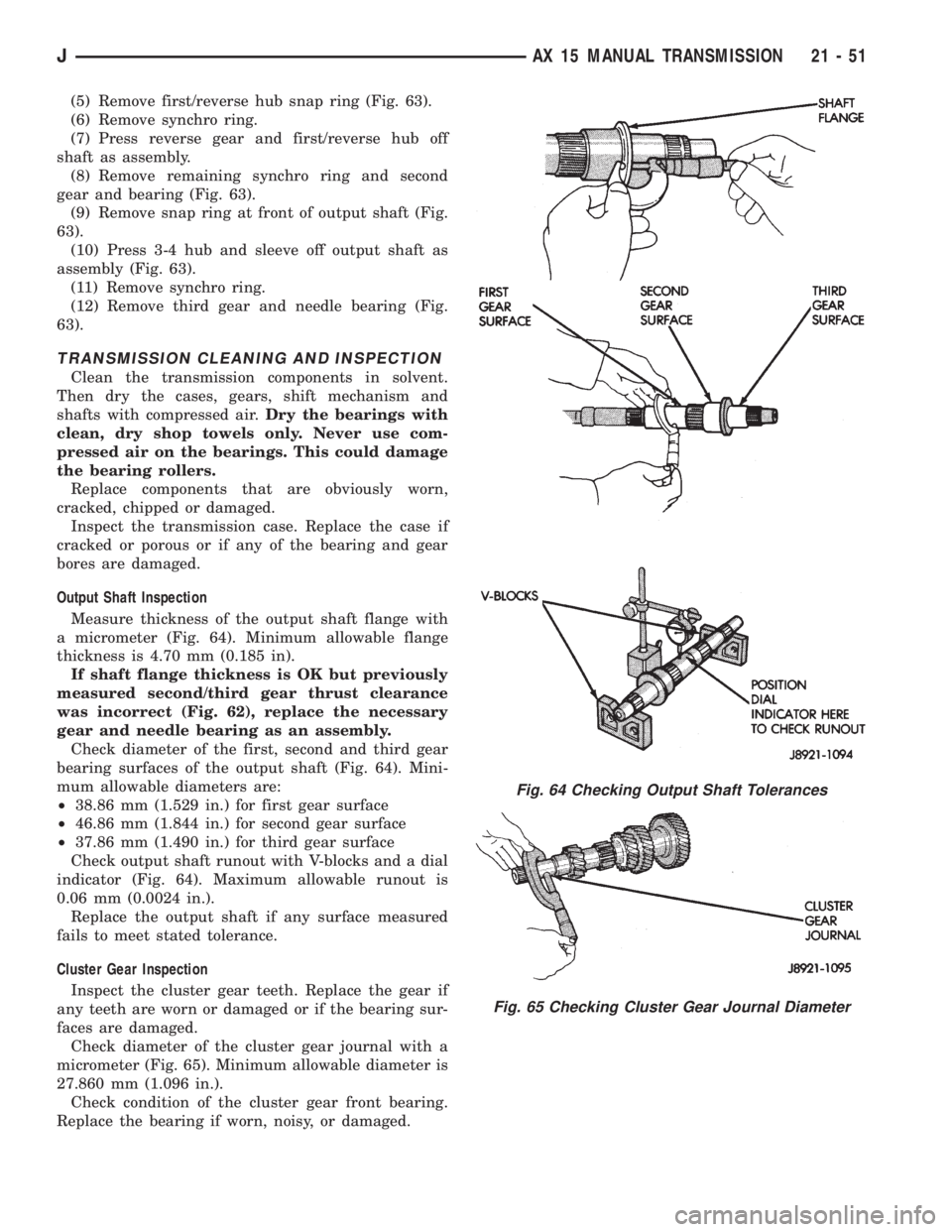
(5) Remove first/reverse hub snap ring (Fig. 63).
(6) Remove synchro ring.
(7) Press reverse gear and first/reverse hub off
shaft as assembly.
(8) Remove remaining synchro ring and second
gear and bearing (Fig. 63).
(9) Remove snap ring at front of output shaft (Fig.
63).
(10) Press 3-4 hub and sleeve off output shaft as
assembly (Fig. 63).
(11) Remove synchro ring.
(12) Remove third gear and needle bearing (Fig.
63).
TRANSMISSION CLEANING AND INSPECTION
Clean the transmission components in solvent.
Then dry the cases, gears, shift mechanism and
shafts with compressed air.Dry the bearings with
clean, dry shop towels only. Never use com-
pressed air on the bearings. This could damage
the bearing rollers.
Replace components that are obviously worn,
cracked, chipped or damaged.
Inspect the transmission case. Replace the case if
cracked or porous or if any of the bearing and gear
bores are damaged.
Output Shaft Inspection
Measure thickness of the output shaft flange with
a micrometer (Fig. 64). Minimum allowable flange
thickness is 4.70 mm (0.185 in).
If shaft flange thickness is OK but previously
measured second/third gear thrust clearance
was incorrect (Fig. 62), replace the necessary
gear and needle bearing as an assembly.
Check diameter of the first, second and third gear
bearing surfaces of the output shaft (Fig. 64). Mini-
mum allowable diameters are:
²38.86 mm (1.529 in.) for first gear surface
²46.86 mm (1.844 in.) for second gear surface
²37.86 mm (1.490 in.) for third gear surface
Check output shaft runout with V-blocks and a dial
indicator (Fig. 64). Maximum allowable runout is
0.06 mm (0.0024 in.).
Replace the output shaft if any surface measured
fails to meet stated tolerance.
Cluster Gear Inspection
Inspect the cluster gear teeth. Replace the gear if
any teeth are worn or damaged or if the bearing sur-
faces are damaged.
Check diameter of the cluster gear journal with a
micrometer (Fig. 65). Minimum allowable diameter is
27.860 mm (1.096 in.).
Check condition of the cluster gear front bearing.
Replace the bearing if worn, noisy, or damaged.
Fig. 64 Checking Output Shaft Tolerances
Fig. 65 Checking Cluster Gear Journal Diameter
JAX 15 MANUAL TRANSMISSION 21 - 51
Page 1614 of 2158
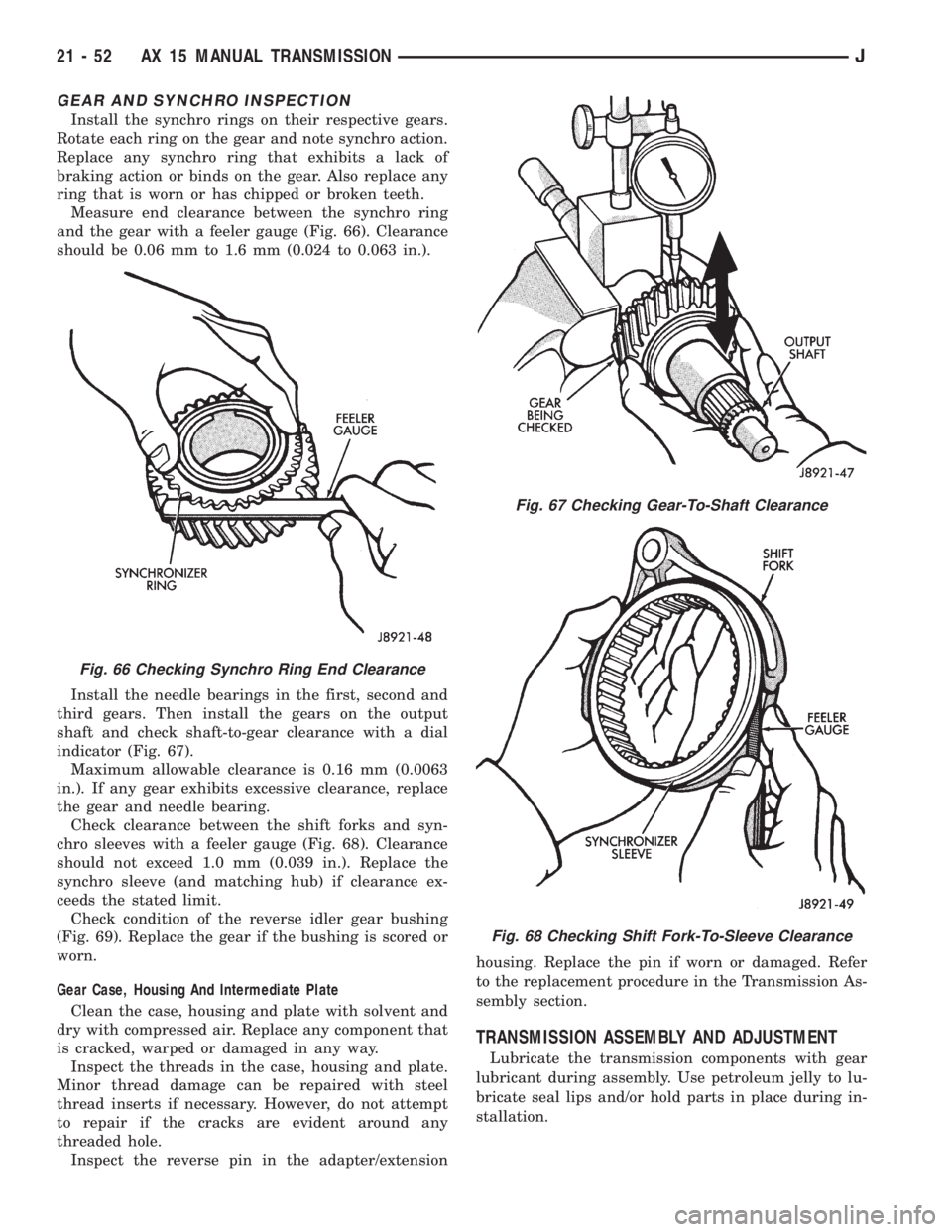
GEAR AND SYNCHRO INSPECTION
Install the synchro rings on their respective gears.
Rotate each ring on the gear and note synchro action.
Replace any synchro ring that exhibits a lack of
braking action or binds on the gear. Also replace any
ring that is worn or has chipped or broken teeth.
Measure end clearance between the synchro ring
and the gear with a feeler gauge (Fig. 66). Clearance
should be 0.06 mm to 1.6 mm (0.024 to 0.063 in.).
Install the needle bearings in the first, second and
third gears. Then install the gears on the output
shaft and check shaft-to-gear clearance with a dial
indicator (Fig. 67).
Maximum allowable clearance is 0.16 mm (0.0063
in.). If any gear exhibits excessive clearance, replace
the gear and needle bearing.
Check clearance between the shift forks and syn-
chro sleeves with a feeler gauge (Fig. 68). Clearance
should not exceed 1.0 mm (0.039 in.). Replace the
synchro sleeve (and matching hub) if clearance ex-
ceeds the stated limit.
Check condition of the reverse idler gear bushing
(Fig. 69). Replace the gear if the bushing is scored or
worn.
Gear Case, Housing And Intermediate Plate
Clean the case, housing and plate with solvent and
dry with compressed air. Replace any component that
is cracked, warped or damaged in any way.
Inspect the threads in the case, housing and plate.
Minor thread damage can be repaired with steel
thread inserts if necessary. However, do not attempt
to repair if the cracks are evident around any
threaded hole.
Inspect the reverse pin in the adapter/extensionhousing. Replace the pin if worn or damaged. Refer
to the replacement procedure in the Transmission As-
sembly section.
TRANSMISSION ASSEMBLY AND ADJUSTMENT
Lubricate the transmission components with gear
lubricant during assembly. Use petroleum jelly to lu-
bricate seal lips and/or hold parts in place during in-
stallation.
Fig. 66 Checking Synchro Ring End Clearance
Fig. 67 Checking Gear-To-Shaft Clearance
Fig. 68 Checking Shift Fork-To-Sleeve Clearance
21 - 52 AX 15 MANUAL TRANSMISSIONJ
Page 1615 of 2158
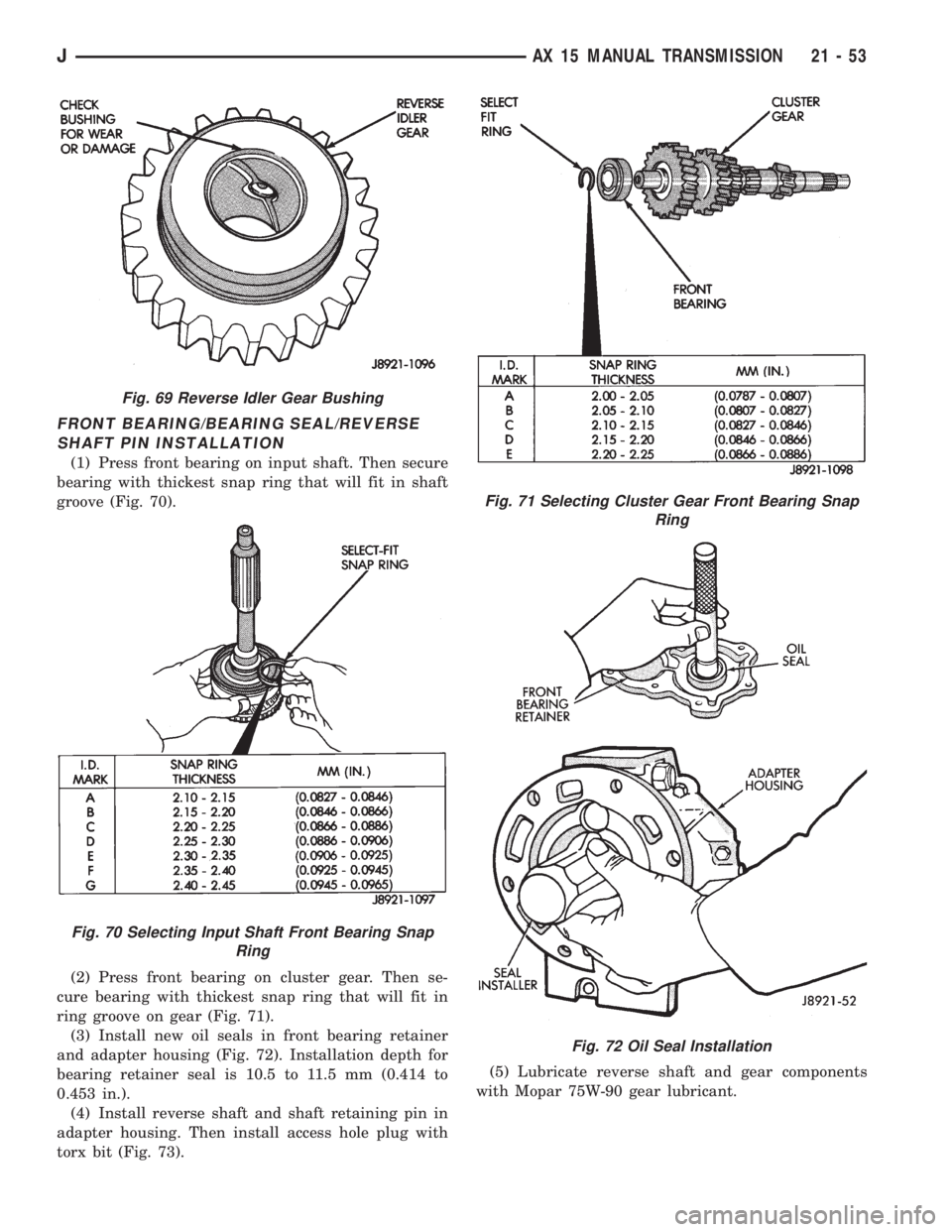
FRONT BEARING/BEARING SEAL/REVERSE
SHAFT PIN INSTALLATION
(1) Press front bearing on input shaft. Then secure
bearing with thickest snap ring that will fit in shaft
groove (Fig. 70).
(2) Press front bearing on cluster gear. Then se-
cure bearing with thickest snap ring that will fit in
ring groove on gear (Fig. 71).
(3) Install new oil seals in front bearing retainer
and adapter housing (Fig. 72). Installation depth for
bearing retainer seal is 10.5 to 11.5 mm (0.414 to
0.453 in.).
(4) Install reverse shaft and shaft retaining pin in
adapter housing. Then install access hole plug with
torx bit (Fig. 73).(5) Lubricate reverse shaft and gear components
with Mopar 75W-90 gear lubricant.
Fig. 69 Reverse Idler Gear Bushing
Fig. 70 Selecting Input Shaft Front Bearing Snap
Ring
Fig. 71 Selecting Cluster Gear Front Bearing Snap
Ring
Fig. 72 Oil Seal Installation
JAX 15 MANUAL TRANSMISSION 21 - 53
Page 1616 of 2158
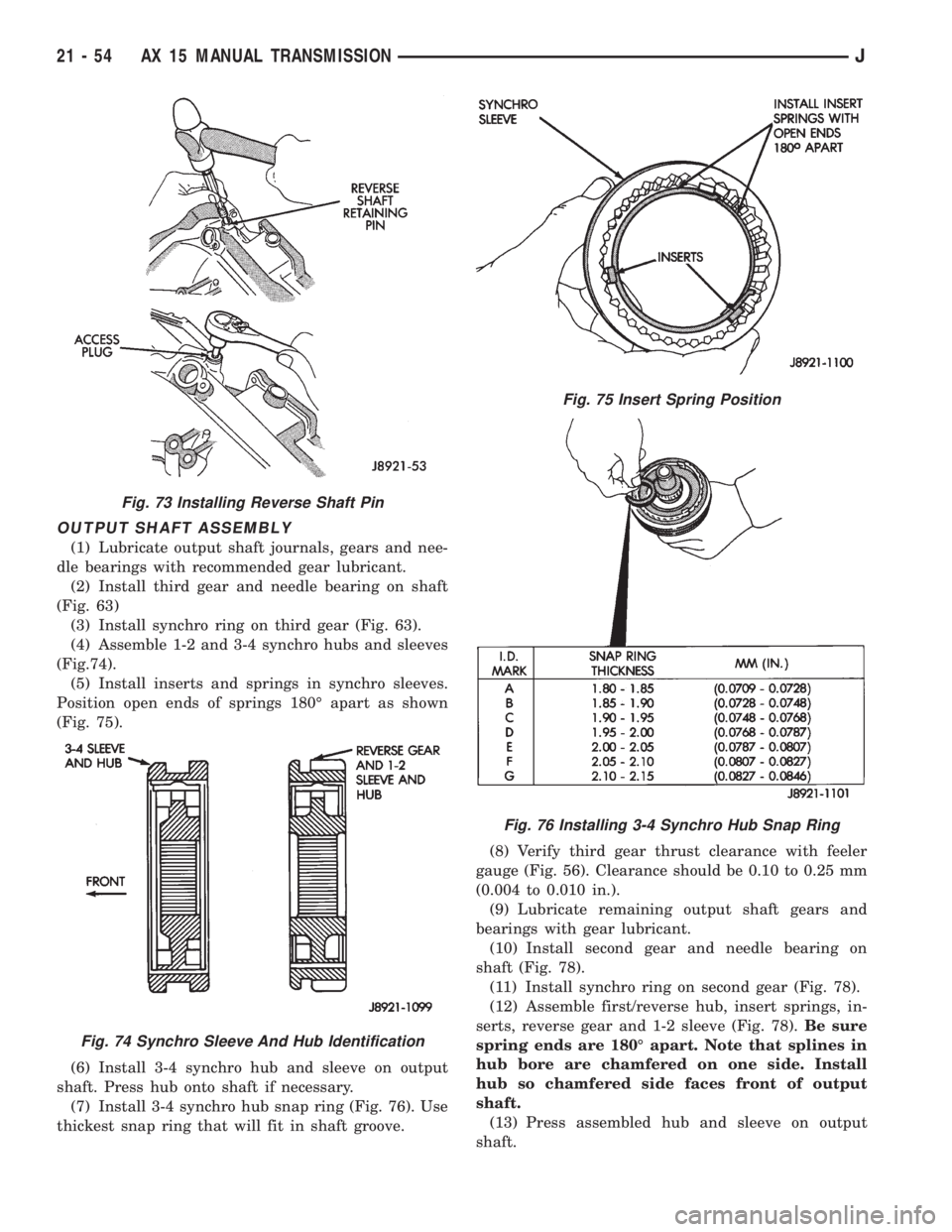
OUTPUT SHAFT ASSEMBLY
(1) Lubricate output shaft journals, gears and nee-
dle bearings with recommended gear lubricant.
(2) Install third gear and needle bearing on shaft
(Fig. 63)
(3) Install synchro ring on third gear (Fig. 63).
(4) Assemble 1-2 and 3-4 synchro hubs and sleeves
(Fig.74).
(5) Install inserts and springs in synchro sleeves.
Position open ends of springs 180É apart as shown
(Fig. 75).
(6) Install 3-4 synchro hub and sleeve on output
shaft. Press hub onto shaft if necessary.
(7) Install 3-4 synchro hub snap ring (Fig. 76). Use
thickest snap ring that will fit in shaft groove.(8) Verify third gear thrust clearance with feeler
gauge (Fig. 56). Clearance should be 0.10 to 0.25 mm
(0.004 to 0.010 in.).
(9) Lubricate remaining output shaft gears and
bearings with gear lubricant.
(10) Install second gear and needle bearing on
shaft (Fig. 78).
(11) Install synchro ring on second gear (Fig. 78).
(12) Assemble first/reverse hub, insert springs, in-
serts, reverse gear and 1-2 sleeve (Fig. 78).Be sure
spring ends are 180É apart. Note that splines in
hub bore are chamfered on one side. Install
hub so chamfered side faces front of output
shaft.
(13) Press assembled hub and sleeve on output
shaft.
Fig. 73 Installing Reverse Shaft Pin
Fig. 74 Synchro Sleeve And Hub Identification
Fig. 75 Insert Spring Position
Fig. 76 Installing 3-4 Synchro Hub Snap Ring
21 - 54 AX 15 MANUAL TRANSMISSIONJ
Page 1617 of 2158
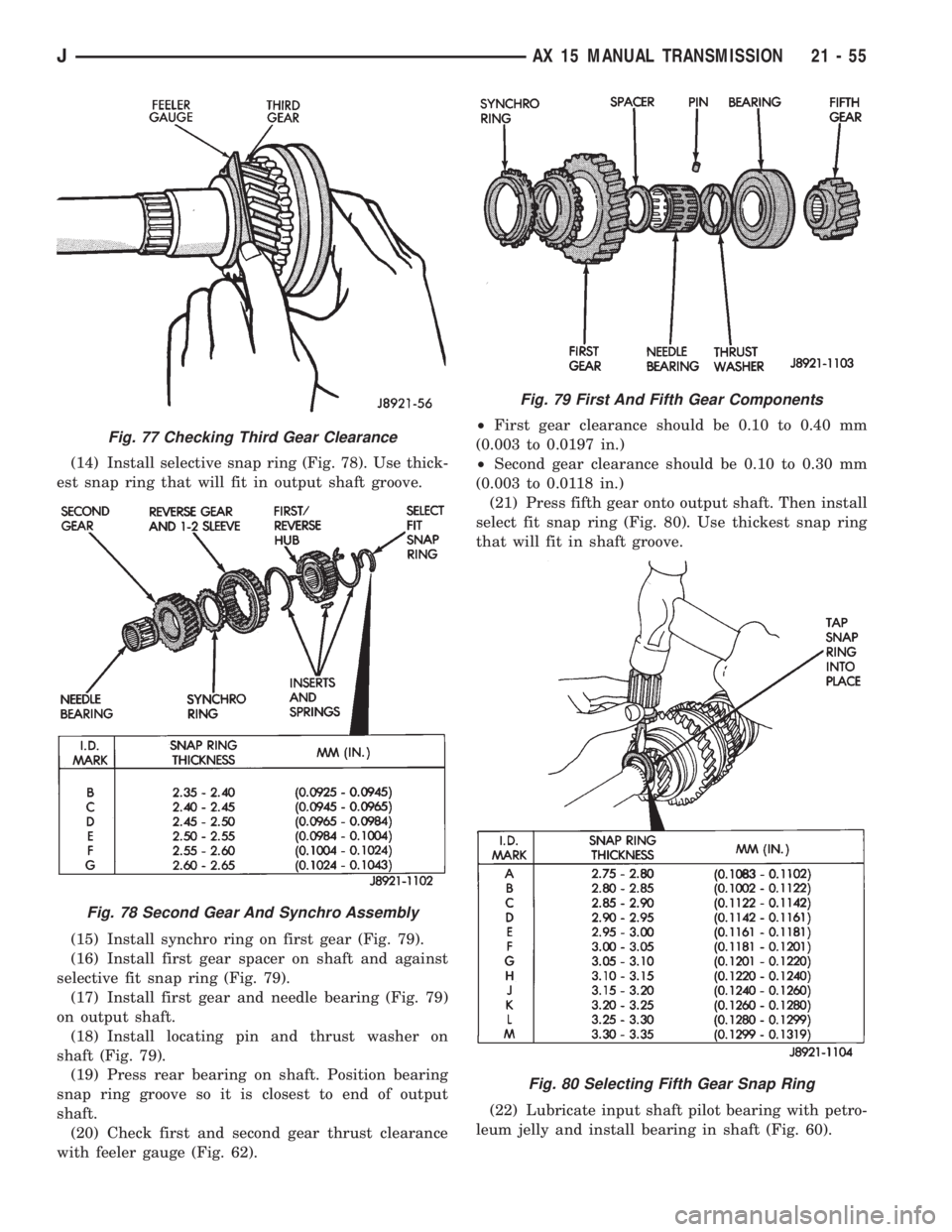
(14) Install selective snap ring (Fig. 78). Use thick-
est snap ring that will fit in output shaft groove.
(15) Install synchro ring on first gear (Fig. 79).
(16) Install first gear spacer on shaft and against
selective fit snap ring (Fig. 79).
(17) Install first gear and needle bearing (Fig. 79)
on output shaft.
(18) Install locating pin and thrust washer on
shaft (Fig. 79).
(19) Press rear bearing on shaft. Position bearing
snap ring groove so it is closest to end of output
shaft.
(20) Check first and second gear thrust clearance
with feeler gauge (Fig. 62).²First gear clearance should be 0.10 to 0.40 mm
(0.003 to 0.0197 in.)
²Second gear clearance should be 0.10 to 0.30 mm
(0.003 to 0.0118 in.)
(21) Press fifth gear onto output shaft. Then install
select fit snap ring (Fig. 80). Use thickest snap ring
that will fit in shaft groove.
(22) Lubricate input shaft pilot bearing with petro-
leum jelly and install bearing in shaft (Fig. 60).
Fig. 77 Checking Third Gear Clearance
Fig. 78 Second Gear And Synchro Assembly
Fig. 79 First And Fifth Gear Components
Fig. 80 Selecting Fifth Gear Snap Ring
JAX 15 MANUAL TRANSMISSION 21 - 55
Page 1618 of 2158
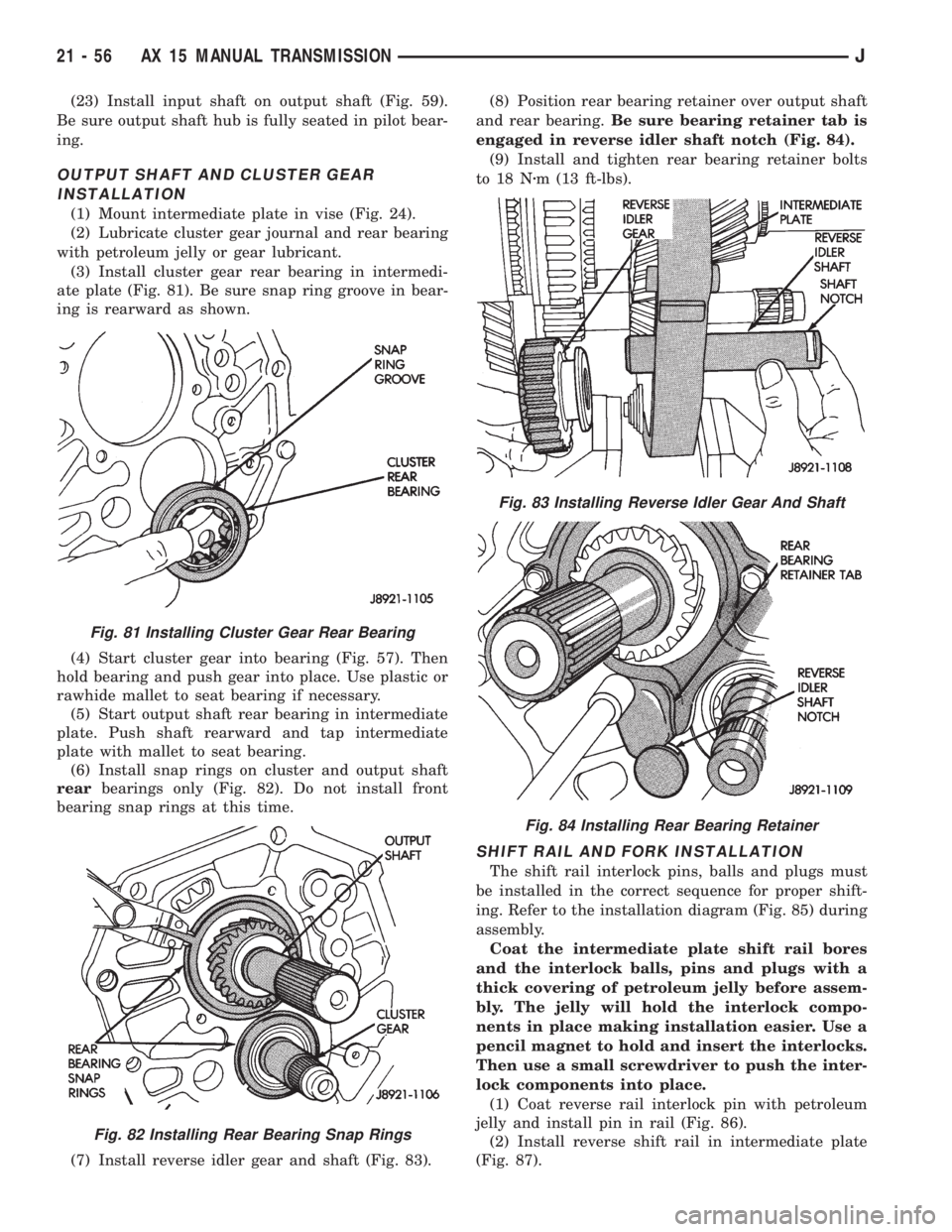
(23) Install input shaft on output shaft (Fig. 59).
Be sure output shaft hub is fully seated in pilot bear-
ing.
OUTPUT SHAFT AND CLUSTER GEAR
INSTALLATION
(1) Mount intermediate plate in vise (Fig. 24).
(2) Lubricate cluster gear journal and rear bearing
with petroleum jelly or gear lubricant.
(3) Install cluster gear rear bearing in intermedi-
ate plate (Fig. 81). Be sure snap ring groove in bear-
ing is rearward as shown.
(4) Start cluster gear into bearing (Fig. 57). Then
hold bearing and push gear into place. Use plastic or
rawhide mallet to seat bearing if necessary.
(5) Start output shaft rear bearing in intermediate
plate. Push shaft rearward and tap intermediate
plate with mallet to seat bearing.
(6) Install snap rings on cluster and output shaft
rearbearings only (Fig. 82). Do not install front
bearing snap rings at this time.
(7) Install reverse idler gear and shaft (Fig. 83).(8) Position rear bearing retainer over output shaft
and rear bearing.Be sure bearing retainer tab is
engaged in reverse idler shaft notch (Fig. 84).
(9) Install and tighten rear bearing retainer bolts
to 18 Nzm (13 ft-lbs).
SHIFT RAIL AND FORK INSTALLATION
The shift rail interlock pins, balls and plugs must
be installed in the correct sequence for proper shift-
ing. Refer to the installation diagram (Fig. 85) during
assembly.
Coat the intermediate plate shift rail bores
and the interlock balls, pins and plugs with a
thick covering of petroleum jelly before assem-
bly. The jelly will hold the interlock compo-
nents in place making installation easier. Use a
pencil magnet to hold and insert the interlocks.
Then use a small screwdriver to push the inter-
lock components into place.
(1) Coat reverse rail interlock pin with petroleum
jelly and install pin in rail (Fig. 86).
(2) Install reverse shift rail in intermediate plate
(Fig. 87).
Fig. 81 Installing Cluster Gear Rear Bearing
Fig. 82 Installing Rear Bearing Snap Rings
Fig. 83 Installing Reverse Idler Gear And Shaft
Fig. 84 Installing Rear Bearing Retainer
21 - 56 AX 15 MANUAL TRANSMISSIONJ
Page 1619 of 2158
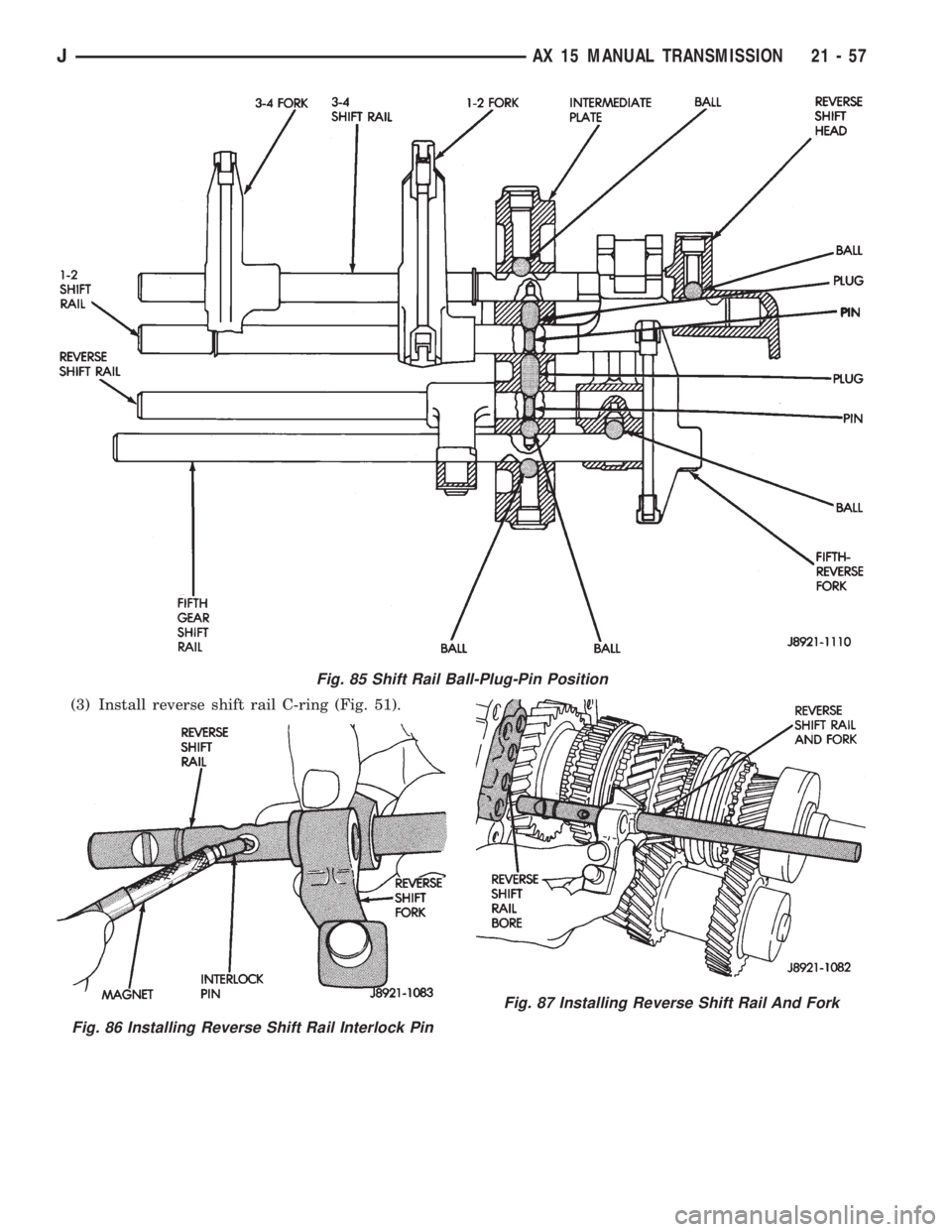
(3) Install reverse shift rail C-ring (Fig. 51).
Fig. 85 Shift Rail Ball-Plug-Pin Position
Fig. 86 Installing Reverse Shift Rail Interlock Pin
Fig. 87 Installing Reverse Shift Rail And Fork
JAX 15 MANUAL TRANSMISSION 21 - 57
Page 1620 of 2158
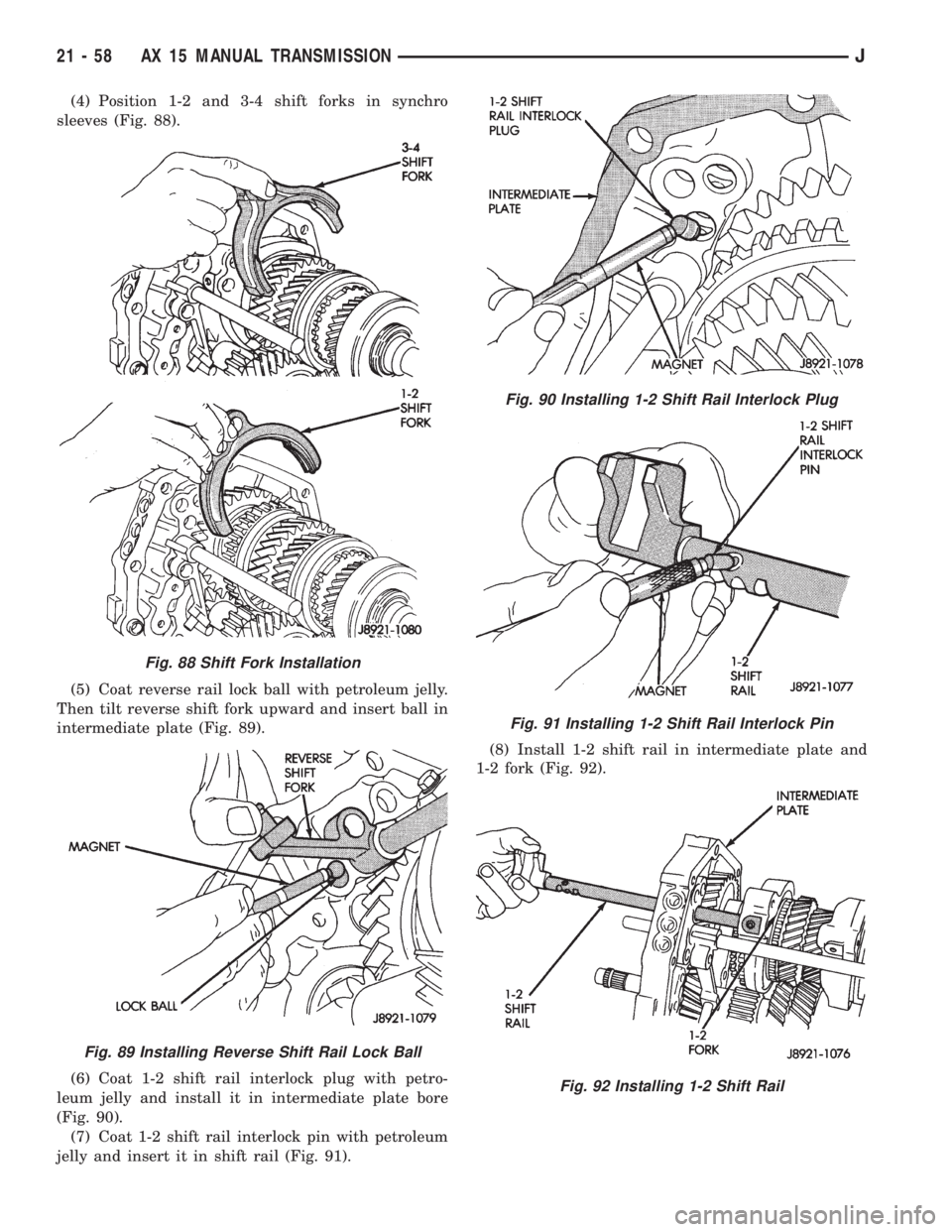
(4) Position 1-2 and 3-4 shift forks in synchro
sleeves (Fig. 88).
(5) Coat reverse rail lock ball with petroleum jelly.
Then tilt reverse shift fork upward and insert ball in
intermediate plate (Fig. 89).
(6) Coat 1-2 shift rail interlock plug with petro-
leum jelly and install it in intermediate plate bore
(Fig. 90).
(7) Coat 1-2 shift rail interlock pin with petroleum
jelly and insert it in shift rail (Fig. 91).(8) Install 1-2 shift rail in intermediate plate and
1-2 fork (Fig. 92).
Fig. 88 Shift Fork Installation
Fig. 89 Installing Reverse Shift Rail Lock Ball
Fig. 90 Installing 1-2 Shift Rail Interlock Plug
Fig. 91 Installing 1-2 Shift Rail Interlock Pin
Fig. 92 Installing 1-2 Shift Rail
21 - 58 AX 15 MANUAL TRANSMISSIONJ